The following article documents material concerning eighteen factory struggles in Delhi’s industrial belt between early 2014 and mid-2015.
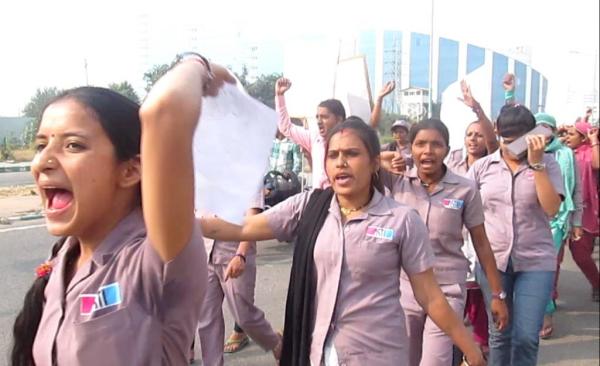
--- January 2014: marauding workers in Faridabad shut down dozens of factories demanding minimum wage increases --- February 2014: wildcat gatherings of over 2,000 female auto-electronics workers at Jai Ushin in Manesar enforce pay hikes --- April 2014: male and female workers of two Napino factories occupy their plants for ten days --- May 2014: police evict over 1,000 workers from Shriram Piston factory using tear gas and live ammunition --- February 2015: after management injures a worker several thousand workers start attacking their factories and bosses’ cars ---
(The text will be published as part of GurgaonWorkersNews no.64 / www.gurgaonworkersnews.wordpress.com)
We focus on a series of riots around garment factories and a cycle of factory occupations, largely in the automobile sector, which took place in early 2014 in close geographical proximity, involving a new generation of female workers. This short cycle of struggles had the potential to make a qualitative leap into new forms of workers’ organisation.
Most of the struggles became known to the public only at a point when either violence occurred or workers were engaging in longer protests outside the factory – which means that struggles often become visible at a moment when workers are on the back-foot [perhaps this needs to be explained?]. If the prelude to the struggles is not revealed, our understanding of the strong and weak points of current workers’ unrest will remain skewed. The prelude and underlying tendencies don’t reveal themselves easily – and we would not have known about them were it not for the continuous and regular efforts of comrades of Faridabad Majdoor Samachar [1], an independent workers’ newspaper, to listen to workers and to circulate their experiences. The material provided in this article is largely based on translations of Faridabad Majdoor Samachar.
Firstly, we will explain the extent to which the local series of struggles in Delhi form part of the emerging ‘global strike wave’. We then look briefly at the general economic background of the struggles, namely the wage pressure from above and below, and the political situation, namely the parliamentary integration of the anti-corruption movement.
This is followed by a brief comparison of the garment workers’ riots in Delhi with those of their co-workers in Bangladesh and of the automobile wildcat strikes in Delhi with the struggles of Honda and other automobile workers in China 2010. Bangladesh and China were outstanding examples of workers being on the offensive so we make the comparison to see what common tendencies exist between them and the situation of workers in the same sectors in India.
We then look at the specific composition of the factory occupations in terms of permanent and temporary workers and emphasise the importance of the emergence of female workers’ autonomy. Finally we analyse the relation between workers’ actions on the shop floor and the formation process of company unions, in order to question the general assumption that trade union federations help workers overcome the ‘cellular’ or company-limited character of their struggles. We end with a critical reflection of the common (far-) left interpretation of both the ‘unlawful’ character of current workers’ struggles and government attempts to change the labour and trade union law.
Riots and spontaneous mass-protests:
* Riots in NOIDA and Okhla industrial areas, February 2013
* Spontaneous mass-factory shutdown, Faridabad, January 2014
* Orient Craft Riot, Gurgaon, March 2014
* Spontaneous mass-protests at Northern Complex Industrial Zone, Faridabad,
September 2014
* Udyog Vihar Riot, Gurgaon, February 2015
* Orient Craft Riot, Gurgaon, June 2015
Factory occupations and wildcats:
* Napino Auto Dispute, Manesar, 2010 to April 2014
* Munjal Kiriu, Manesar, December 2013 - January 2015
* Shriram Piston, Pathredi, January 2014 – May 2014
* Jay Ushin / JNS, Manesar, February 2014 - September 2014
* Asti Electronics, Manesar, February 2014
* Baxter, Manesar, February 2014
* Bajaj Auto, Gurgaon, February 2014
* Track Components, Manesar, April 2014
* Subros, Manesar, May 2014
* Autoliv, Manesar, June 2014
* Wearwell, Okhla, September 201
* Orient Electric, Faridabad, October 2014
* Premium Moulding, Gurgaon, October 2014 to June 2015
You can find both shorter summaries of each dispute and longer chronologies after the footnotes of this text. We particularly recommend reading the longer chronologies of Napino Auto, Asti Electronics and Jai Ushin disputes for understanding the general contradictions of current disputes.
CONTEXT OF THE STRUGGLES IN DELHI
*** The cycle of struggles of a new generation of factory workers in Delhi emerged synchronous to the global intensification of class struggle, also termed, ‘the global strike wave’. [2]
During the onset of the 2008 financial crisis, many speculated about a possible ‘de-coupling’ of the Indian economy [3]. But it quickly turned out that despite India having only a relatively small share in total global trade, the impact of the crisis was pretty immediate, e.g. micro-credits for small peasants dried up, wages in call centres were cut, garment exports came down. The situation in India is closely related to wider global developments not only regarding the circulation of capital, also in terms of the circulation of struggles. In India’s industrial areas a new cycle of struggle started around 2005, while on a global scale workers’ struggles started to culminate simultaneously, building up to a ‘global strike wave’ around 2011. In the Delhi area the stages leading to the new cycle can be roughly described as follows:
a) Like in most ‘developing countries’ the mid-1970s were characterised by draconic state measures, culminating in violent attacks on workers’ militancy in the late 1970s, e.g. the Faridabad Nilaam Chowk massacre in 1979. In the 1980s the introduction of electronics and new (synthetic) raw materials in, amongst others, metal and textile, contributed to the de-composition of this older workforce [4]; the Bombay textile mill strike in 1982 bears resemblance with many defensive mass struggles of this decade e.g. of the miners in Britain.
b) The global crash of 1990/91 resulted in a foreign debt crisis in India, which accelerated the restructuring process in industries. From then on mainly temporary workers were hired, to much worse conditions – again, a global phenomenon.
c) The dispute at Maruti Gurgaon plant in 2000/01 [5], which ended up with around 2,000 permanent workers being dismissed and replaced by casual staff. This marked a final point of this decade’s development of casualisation; since then temporary workers form between 50 and 80 per cent of the workforce in the ‘organised’ manufacturing sector.
d) It took the working class more than a decade to re-compose itself. The new generation of permanent and temporary workers entered the stage during the 2005 Honda HMSI conflict in Gurgaon [6]; at the time, given the composition of the workforce, permanent workers were already dependent on temporary workers joining their struggle in order to put pressure on management. Given the continuing ‘boom’ period in the sector the company was able to offer significantly higher wages to the newly formed permanent workers’ union, mainly through productivity incentives, which relied on the increased exploitation of temporary staff, and thereby managed to re-divide permanent and temporary workers. A year after the dispute the permanents earned four to five times as much as their harder-working temporary colleagues.
e) During the factory dispute at Hero Honda motorcycle plant in 2007 [7], for the first time temporary workers appeared with a new and necessary form of struggle: the ‘spontaneous’ occupation. However, given the wage differences the occupation remained limited to the temporary workers and given their inexperience they did not manage to sustain the occupation through support from outside.
f) The 2008 crisis changed companies’ abilities, particularly in the automobile sector, to finance significantly higher wages for the 30 to 40 per cent permanent workers amongst their workforce. In many situations, for example in the new Maruti Manesar plant (built in 2007), permanents initially earned only around one and a half times as much as the temps. This was only a third of what permanents earned in the older Maruti Gurgaon plant. The factory occupation of both permanent and temporary workers at Napino Auto in 2010 and especially the two occupations at Maruti Manesar in 2011 [8] expressed this underlying similarity in material conditions. From then on it became much more difficult for management to divide the workforce. These struggles can be compared to the series of wildcat struggles in the Honda and other automobile plants in China 2010 – see below.
g) The series of struggles in 2014 and 2015 that this article deals with are an extension of the Maruti Manesar experience. Struggles were directly and indirectly affected by the Maruti struggles e.g. through changes in production if they were part of the Maruti supply-chain or in terms of management’s responses with the violence at Maruti lurking in the back of their minds. The new quality of this series of struggles since 2014 is the participation of female factory workers, largely in the automobile electronics factories.
Relating these local developments back to the question of the global strike wave we can say that the synchronous character is partly based on a more short-term and regional commonality of neoliberal boom and bust (in particular within the BRIC states). But more generally and long-term we can say that globally it took the working class over a decade to discover how to struggle under the new conditions of a casualised and generally very mobile workforces, new supply-chains and ‘lean-and-mean’ factory regimes with new modes of (technological) control.
*** The current struggles take place against the background of a concerted wage freeze from above and a continuing wage pressure from below, where the general economic conditions still allow for a workers’ offensive.
The garment export sector and the automobile sector have been affected by the global slump, but so far there haven’t been mass lay-offs. The growth rate of passenger cars sales has come down, but sales have not yet declined. [9] Friends employed in the supply-sector told us that since end of 2014 there is less overtime in their factories, working hours have come down from 72 hours per week to 58 hours. The Indian Automobile Employers’ Association announced that in 2014 there were 200,000 job cuts in the sector, out of a total 19 million people employed. According to a recent survey these job cuts are largely due to an increase in automation, claiming that foreign direct investment in the sector rose from $200 million in 2009/10 to $646 million in 2013/14, mainly in automation technology, not in new capacities. In 2014/15 garment exports from India still grew by around 13 per cent compared to the previous year. All in all, profit margins have come down, but workers are not threatened with dismissals due to lack of work – which allows them to express their discontent about depressed wages.
Accounting for inflation, calculating in 2011/12 prices, if a worker earned Rs 8,154 per month in 1990/91, she earned only Rs 7,972 per month in 2011/12. In real terms, workers today earn less than they did in 1990. This mirrors a global trend. At the end of 2013 the chief minister of Haryana – the state where Faridabad, Gurgaon and Manesar are located - announced a substantial increase of the local minimum wage from around Rs 5,500 Rs to over Rs 8,000, but this did not materialise. In January 2015 the government met with leaders of all established trade union confederations and representatives from companies to debate an increase to Rs 7,400, but again no result. Minimum wages for unskilled workers in July 2015 were still below Rs 6,000. The central state knows that wages have to stay low and so do the companies: there has been a concerted effort within the automobile sector to fight any wage increase for permanent workers above Rs 7,000 over a three- year period or Rs 3,000 for temporary staff. Maruti or Honda would accept weeklong production stoppages at their suppliers, as long as workers are not successful in imposing higher wage hikes – and thereby giving encouraging signals to their workmates.
*** The struggles take place against the background of the political degeneration of the ‘anti-corruption’ movement and its parliamentary wing. In 2014, with BJP in central state government and the AAP (Aam Admi Party) [10] in Delhi, parts of the local working class experienced a ‘Syriza’ (or ANC, Partido dos Trabalhadores (PT) Brazil, Muslim Brotherhood, Obama etc.) effect.
The global integration of class relations in India is also reflected in developments within the political sphere. The 2008 crisis destroyed neoliberal liquidity and revealed the personal power relations behind the scene: who profits from so-called ‘privatisation’, what kind of personal relations it needs to progress up the career ladder etc. Popular movements against ‘corruption’ and ‘lack of democracy’ emerged in many countries after 2009, from Spain to Turkey to South Africa to India.
In India Anna Hazare and Ram Dev were prominent figures of a movement of mainly lower-middle class people protesting against those in parliamentary power, but also Maruti workers during the Manesar dispute expressed the hope that these ‘extra-parliamentary’ mobilisations could change the political landscape. Apart from a few ‘local’ industrial workers and certain Delhi ‘professional’ groups, such as inner-city auto-drivers, most workers are completely outside of the electoral sphere – not mainly because they are registered on the electoral roll only in their far-away village, which they hardly visit, but because their general proletarian condition relates little to the political circus. The middle-strata movement institutionalised itself as the AAP and became a government force in Delhi state – and quickly revealed itself to be unable to offer much to the common people: in actual fact, it repressed the strike of temporary bus conductors in Delhi, who were demanding the permanent contracts that had been promised to them prior to the elections; in June 2015 rubbish collectors had to strike for weeks in order to get paid; and hundreds of health workers launched an indefinite strike, staging a protest outside Chief Minister Arvind Kejriwal's (AAP) residence demanding regularisation of services and fixation of minimum wages. On the central state level the BJP faces similar problems, having won the election mainly on the ‘anti-corruption’ ticket. Workers globally face the problem of how to interpret this demise of the ‘popular movements’ post-2009 and what it means for the political generalisation of their own struggles.
GENERAL TENDENCIES WITHIN THE STRUGGLES
*** The two main new tendencies within current struggles in the Delhi area we can schematically distinguish in garment workers’ riots and automobile workers’ factory occupations.
Since 2010 we’ve seen an increase in industrial area riots and factory occupations as two forms of workers’ struggles.
a) While not exclusively, riots erupted mainly in industrial areas dominated by garment industries (or construction) [11]. The way the industry is organised is based on there being irregular busy periods e.g. lots of overtime when new orders come in; there being lots of temporary under-employment after orders are finished; a high level of capital flight potential because it is easier to relocate garment factories due to a lesser degree of machine investment; and disputes tend to evolve around individual skill levels as skilled tailors can negotiate piece-rates according to their professional groupings. We can state that this more irregular, mobile and individual character of the garment industry forces workers to act more quickly and opportunistically. This is also a reason why hardly any trade union manages to establish a permanent basis in the garment sector – in contrast to the more ‘industrial’ textile mills in the 1980s.
b) The factory occupations emerged as a necessary measure to counteract managements’ strategy to lockout workers and replace them with newly hired people. Due to the extensive division of labour, people can be trained and put to work fairly quickly. Therefore occupations mainly happen in factories with a more regular production process where workers cooperate within a more sophisticated division of labour, e.g. in the automobile sector. They only tend to be successful in situations where two shifts remain inside the plant while the third shift supports from outside. If more than 200 – 300 workers are inside the plant the police tend to be more cautious concerning evictions, or at least it takes them longer to prepare for it.
*** The riots, mainly by garment workers in Delhi, are less extensive compared to those in Bangladesh. [12] This is largely due to the lesser significance of the sector for the national (political) economy.
When we analyse the garment workers riots in the Delhi area it makes sense to contrast them with the recent garment workers struggles in the neighbouring country Bangladesh, where, unlike garment workers in India, workers have managed to enforce significant wage increases since the mid-2000s.
Looking firstly a bit closer at the six riots/mass protests in Delhi mentioned in this article, we see that two remained limited to the factory that employed the disgruntled rioters. They occurred after work accidents and involved around 1,000 workers. Two riots spread mainly against the background of a ‘symbolic’ general strike called for by otherwise minoritarian trade union federations. The workers involved in the riot were neither union members nor part of the mobilised sectors, nevertheless between 5,000 and 10,000 workers took part. One mass protest was a collective response to a common but temporary problem (accumulated sewage water) and involved 3,000 workers. And only one riot was in response to management harassment and went beyond the company boundary, involving between ten to twenty times as many workers as in the originally affected factory, a total of 10,000 to 20,000 workers.
Apart from two riots, which happened at the same factory ground, all the others happened at different industrial areas – meaning that it is unlikely that individual (groups of) workers were involved or experiencing it twice – another major difference to Bangladesh. The riots also took place in industrial areas (Okhla, Gurgaon Udyog Vihar), which are in different areas from those that became centres for factory occupations (Manesar). This does not mean that they were not felt in other areas, e.g. in the case of the riot in Okhla managements of various companies in Manesar decided to send workers on holiday the following day, fearing copy-cat effects.
Each riot only lasted for several hours. The main targets were the factories themselves plus (bosses’) cars. While police was fought initially, workers retreated once the police deployment became overbearing. There were very few arrests on any of the occasions. During the riot in Gurgaon Udyog Vihar, workers made sure to destroy CCTV cameras and recorders. As far as we know there were generally no attempts at looting.
While the two riots/mass protests that took place against the background of the trade union mobilisations raised demands of minimum wage hikes, the other riots/mass protests remained without clear demands. In Bangladesh it seems that riots are more extensive, regular, organised and – at least in hindsight – connected to general demands. These demands don’t have to be raised explicitly by the workers; rather the ruling class in Bangladesh interpret them as such. In India though, this does not happen so explicitly.
What explains the difference?
While the average factory size, sizes of industrial areas, wages and working times are fairly similar in both countries, the first obvious difference is the workforce: in Delhi mainly ‘skilled’ men work in the garment factories, male workers comprising around 70 per cent of the workforce, while in Bangladesh, the majority female workforce are mainly seen as ‘unskilled’ workers. In Delhi the industry still relies on male workers who have learned the skill from older family members in the village. The fact that companies can integrate these artisanal skills without major training costs means that in many factories workers still produce full garments or at least bigger parts of it, whereas newly trained younger workers are generally employed in ‘chain-systems’ with a more minute division of labour, e.g. sewing on single collars or pockets. In this situation of skilled-worker-dominated industries, wage disputes tend to be more individualised. Because a lot of the ‘skilled’ male workers are on piece-rate wages, they tend to negotiate individually or as groups and relate less to the general minimum wage. This individualisation or professional basis of the industry might also account for the fact that riots tend to spread less extensively and regularly as in Bangladesh.
The more important difference is the significance of the garment export sector for the national economy and differences in the general political landscape. In Bangladesh the garment export sector constitutes around 12 to 13 per cent of GDP, 80 per cent of total export and employs 4 out of 160 million people, whereas in India garments and textiles (!) together make up 4 per cent of GDP, garments constitute 12 per cent of total export and the sector employs around 8 million out of 1.3 billion people. [13] This means that first of all workers in Bangladesh know that they have bigger economical and political clout, but it also means that various opposing political forces, NGOs and trade unions are interested in developing influence amongst the workers. Rioting workers in Bangladesh know that the political class will hear them, whereas in Delhi the riots were portrayed as mere ‘hooliganism’. There is no, or hardly any trade union organising amongst garment workers in Delhi and most attempts to establish unions failed either due to workers disinterest or repression of employers. Similarly, none of the political parties would address the largely ‘migrant’ garment workers in Delhi, partly because they are not on the voting register anyway. The situation in India is politically more stable than in Bangladesh, workers are less seen as a necessary force to gain political influence vis-à-vis a police state.
*** The automobile factory struggles in Delhi have similar features to the Honda strikes in China in 2010. [14] Although the automobile struggles in India are more extensive in scope, more frequent and in some cases more severely attack management power over the factory, due to their democratic and trade union mediation, they don’t seem to pose a similar ‘political’ potential to generalise and to pose a threat to the ruling class.
The wildcat strike wave in the automobile industry in China in 2010 – first of all the strike at the Honda gearbox factory in Nanhai - got a lot of public attention, in the global north in particular. Compared to the (automobile) factory struggles in India we can say that a very similar generation of workers is involved: young workers in their twenties, coming from a semi-rural background, but often with technical qualifications, working on casualised contracts, e.g. as workers hired through contractors, as company casuals or trainees, comparing their conditions to an older permanent workforce who do similar work in the main plants of Honda or Maruti Suzuki (or even to those wages and conditions of car workers in Japan or US/Europe). They manufacture cars for the middle class, which they themselves cannot buy - while their parents might still own a tiny patch of land in the countryside, which won’t feed anyone anymore. The urban promise is not kept, workers can’t go back, but they also can’t properly arrive.
In the 1970 and 1980s industrial workers around Delhi were able to buy an (‘illegal’) plot of land and build a slum-house on it and wages were high enough to raise a family ‘in town’. Partly due to the land price development, partly due to relative wage decline, this has become largely impossible. Where in China ‘rural-urban migration laws’ and a dormitory system regulates the precarious living conditions of migrant workers, in India it is the more subtle force of the market: state and capitalists plan industrial areas, but they leave workers’ accommodation to the local ex-peasantry, who build blocks of small rooms and become landlords. Reproduction costs of the workers are lowered and the local population is integrated through taking part in the exploitation through rent.
Inside the factories, workers face more similar situations. During the (initial) dispute they are not represented by the existing union structures, they engage in wildcat actions, largely confined to their immediate factory surroundings, though news of the struggles spread further, often through making use of mobile phone / social media technology. Their strikes tend to threaten the wider production chain, meaning that often the main automobile companies intervene in the dispute. In some cases workers put forward their own representatives when dealing with the company; in some cases the existing unions get engaged during a later stage of the dispute, brokering between workers and management; in many cases workers don’t send any formal representation. In many cases management reacts with concessions to the initial dispute. These are some similarities.
The differences mainly concern a) the position of Indian and Chinese manufacturing on a global scale; b) the relation between workers’ struggle and the state form; c) and therefore the democratic mediation of struggles through the unions and the possibility for workers in India to set up their own union and/or to affiliate to different union federations.
The first two points are fairly obvious.
With regards to the position of Indian and Chinese manufacturing on a global scale, we can see that the difference in importance of the national economy explains partly why the series of struggles in China got more public (global) attention: unlike India, China is the ‘factory of the world’. In 2013, India’s share of global manufacturing stood at just above 2 per cent, while China accounts for 22.4 per cent. World consumption depends on workers’ behaviour in China, which alone explains why struggles attract more attention.
In terms of the relation between workers’ struggle and the state form, we can see that in India the state itself rarely feels politically threatened by workers’ mobilisation: democracy provides various ways to channel workers’ discontent, through parliamentary representation, the right to have toothless protests at the parliament itself, through year-long court cases, through the paralysing bureaucracies of the trade union apparatus and their symbolic marches and general strikes etc. While at the same time the state locks workers up in jail for years without trial, such as in the case of 150 Maruti Suzuki workers after the struggle in July 2012. Or the state shoots workers with live ammunition, as seen in hundreds of cases over the years, e.g. in the example of Shriram Pistons mentioned in this article. These regular ‘exceptions’ of democratic rule are obviously followed by official inquiries and public blaming of the responsible political/police representatives, with little to no general consequence. In this sense in many incidents of discontent, ‘democracy’ allows the state to act more brutally.
The state in China however, has less of these channels available, or at least they are less flexible, when trying to insulate workers’ discontent. In many cases company management is forced to give concessions to workers just in order to avoid workers’ dispute becoming more publically visible. As far as we are aware, one of the main tools of management in India to deal with workers’ unrest, namely the lockout, is less used by management in China because of that reason: it is a bigger political risk to have workers sitting and demonstrating ‘in public’ for months and possibly accumulating in some sort of ‘Tahrir’ effect. To sum it up, the higher degree of attention workers’ struggles in China attract is partly explained by the spectators’ expectation that they might play a catalyst role in some sort of regime change. Here the third point, the trade union question comes into play.
In China the trade union federation ACFTU is the official state union, most workers’ ‘representatives’ are members of company management, the right to engage in labour disputes are restricted. Looking to the last point about the democratic mediation of struggles through the unions, in China, most labour activists and left-leaning academics think that the forming of ‘independent union structures’ would be the precondition of a) overcoming the ‘cellular character’ of the factory struggles, meaning, bringing workers of different companies and sectors together and b) challenging the undemocratic form of the regime. The latter point is historically founded: in most cases of ‘regime change’ from formal dictatorship to ‘democracy’ trade unions played a major role as transmission belts between ‘mass power’ and ‘political representation’: from Spain 1975 to Poland 1981 to Brazil 1985 to South Korea 1987 to South Africa 1994, but also in the post-Morsi government in Egypt.
The question remains why in all these cases the working class let themselves be betrayed by ‘their own representatives’ as soon as (or at least shortly after) they or their political wing got into state power. Although in most debates the role of unions in overcoming factory boundaries and their role in regime change are kept slightly separate or seen as a ‘two-stage’ model (‘unions as the school of workers’), we think that looking closer at how trade unions ‘overcome’ the factory boundaries of workers’ struggles and how they ‘connect’ individual company workforces is the key to understand why the ‘regime changes’ have historically ended in ‘letting workers down’. This is mainly because of trade unions introducing and/or strengthening the rules and laws of bourgeois forms of representation and segmentation of economic and political struggle within workers’ struggles. This is not surprising when we see how the union form and rules from the very start of a struggle use segmentations and hierarchies to their advantage.
But even if we don’t address the question of the relationship between the two stages in the ‘two-stage model’ mentioned above (between union organisation ‘as school’ and regime change), we still think that looking at the role of trade unions in the disputes in recent Delhi struggles might be fruitful. This is primarily to add to the debate about whether independent trade union representations, ‘collective bargaining’ or a democratisation of the ACFTU in China could solve the problem of the allegedly ‘cellular’ character of struggles there.
In China we can see how management and GDFTU (regional trade union federation branch) reacted to the wildcat strikes in 2010: they collected ‘concrete demands’ from workers through union surveys, they tried to involve workers’ representatives in the negotiation process without handing over control, they established a type of regional ‘collective bargaining’ in the affected industrial areas (“Guangdong Provincial Regulations on Collective Contracts in Enterprises” (GPRCC)) in order to curb the spreading of unrest from individual company to company etc., meaning, they actually implemented a lot of the mechanisms which are generally seen as features of ‘democratic industrial bargaining’. The ‘collective bargaining’ basically brought about a more systematic communication and collaboration between union representatives from various companies, local authorities and an emerging association of management in various supply-chain companies.
A closer look at the inner composition of the struggles in Delhi will further reveal that workers have little to gain from state-recognised national trade union federations with ‘democratic structures’ and will have to depend on setting up their own struggle coordination if they want to overcome the limits of their struggles so far.
*** How representative are the examples from Delhi for struggles in (automobile) industries in the rest of India?
Before looking at the individual disputes and their composition we have to ask how representative they are for the situation in general. Out of the thirteen factory struggles listed below, around half of them made it into the public spotlight, mainly because they were drawn-out and took place outside the factory gates. The way these struggles played out are representative of struggles that make it to the media/the left’s attention. Four of the struggles listed below were more ‘low key’ and less visible (workers stayed inside the factory or came outside only for a short for meetings and protests). But they were generally more ‘successful’ in terms of getting some concessions from management. In this sense we have to deal with a certain problem: struggles that enter the public debate do not necessarily represent examples of workers’ current power vis-à-vis the bosses.
Three companies out of thirteen are not part of the automobile supply chain (a major fan and light bulb manufacturer, an international pharmaceutical company, a significant garment export company). All the others are part of, amongst others, the first-tier Maruti Suzuki and/or Hero Motorcycles supply chain, which are the main local (and Indian) automobile companies. Most of the companies employ between 500 and 1,000 workers. Seven of them have joint ventures (or formed corporate groups) with ‘foreign’ companies, mainly from Japan, which does not impact much on workers’ conditions. In most of them production levels were high at the time of the dispute, meaning companies did not plan to lay-off workers. All of these aspects are fairly representative of the general (automobile) industrial structure across India.
Eight of the factories are located in IMT Manesar, an industrial zone 30 km from Gurgaon and 60 km from Faridabad, with around 800 factories and up to 150,000 workers. Although this might not be representative in terms of the size of IMT Manesar compared to Faridabad or Gurgaon industrial areas, it hints at struggles being concentrated within a certain area. We can say that this concentration happened neither due to the mere fact of workers being part of the same supply chain (which reaches into all corners of Delhi, UP and Haryana) nor due to formal organisational links between them, but because of the mutual influence of workers who live and work in the same area and under similar conditions. Workers recognise these similarities and learn from each other.
*** Under similar sectorial conditions the form and course of current struggles is mainly determined by the specific composition of firstly, permanent and temporary workers; secondly ‘local’ and ‘migrant’ workers.
In nine of the factories, workers hired through contractors (temporary workers) account for more than 60 per cent of the staff, which is representative of the general situation. The temp/permanent workers ratio/relation is the main line of division within the workforce.
In most cases permanent workers earn considerably more than their temporary workmates, in particular if we take various bonuses and allowances into account. While permanents in the (older) main assembly plants of Maruti or Honda can earn up to four to five times as much as their temporary colleagues, since 2009/10 the newly hired permanents are less well paid and the wage gap shrank. Apart from the pay gap, differences on the shop floor might mean workers wearing different uniforms, or permanents getting easier jobs or better treatment in general.
In legal terms temporary workers are not treated as ‘workmen’ of the company they are employed at, which means, amongst other things, that they cannot become members of the same trade union as the permanents. This fact becomes one of the main stumbling blocks in workers’ struggles and, in many cases, a handy tool in the hand of management to divide workers’ collectivity – see point on the role of the unions below. Here the seniority of temp workers also plays a role: in many of the factories concerned, a considerable share of temp workers had been employed at the company for several years. These workers were more prone to support the process of permanent workers’ union formation.
Apart from the ratio between permanent and temporary workers, the division between ‘local’ (meaning workers from Haryana) and ‘migrant’ workers (meaning, from Bihar or other states) can play a role. While it was the case that companies were reluctant to hire local workers, they now form a considerable share of the workforce, in particular in companies located outside of Manesar, closer to the Rajasthan border. The main difference is that ‘local’ workers can fall back on their families or their own house more easily, e.g. during time of unemployment or longer dispute, whereas the ‘migrant’ workers have to pay rent and their families are much further away. The other difference is workers’ connection to local authorities, such as the village councils – in some cases workers on strike appealed to these authorities, asking them for support or to play the role of arbitrators. In most cases these local authorities take management’s side and even threaten workers to stop their agitation. In regards to the thirteen disputes dealt with here only in one case did the ‘local’/’migrant’ question seem to have played a role.
*** We see a new quality of female worker involvement in factory struggles and occupations, mainly in automobile electronics factories, which questions the gender regime.
In three of the factories women workers formed the majority within the workforce and in one they formed a considerable minority.
In general, female employment rates in urban-industrial areas are low, between 10 to 20 per cent in North India. This is a major difference to the situation in China and Bangladesh. These differences cannot mainly be explained by referring to a more conservative culture or the composition of the industry, e.g. there being only a small electronic consumer goods manufacturing industry in North India. The main reason is that employment in more seasonal agriculture, where many women were employed before, is decreasing faster than jobs are created in the urban industrial sphere. An urban wage is not a household wage, meaning it hardly sustains the urban reproduction of a partner and children. [15] Women and children therefore tend to stay in the village, women might work the household field (which is too small to farm for a living, but too big to be left alone), are transferred into rural employment schemes, or find seasonal employment. [16]
Urban ‘industrial’ female employment in Delhi area was therefore largely confined to either small-scale household industries, helper jobs in the garment or construction industry and more recently, though from a different class background, call centres. [17] However, this is changing. There are an increasing number of young, single women coming to work in the modern industrial areas. In all these workplaces though, there are attempts to enforce a ‘moral code’ and certain gender relations e.g. within the electronics and pharmaceutical plants where women now form a significant share of the workforce, management imposes separate seating arrangements in the canteen or company buses or transfers young men and women from their workplace if they talk too much to each other. The clash between the moral code and the larger number of women being in positions of industrial waged work opens up a space of contestation. A number of things can be called into question on a larger scale e.g. the share of the responsibility of reproductive work. These ‘private’ conflicts also have a dynamic relationship to the more public social movements that have rocked India in recent years, focusing as they have on sexual violence and women’s wider role as oppressed subjects within society. These movements may have had an impact on how these working class women see their ‘role’ as potential subjects of protest.
Many of the women workers are single, often migrants from other states in North India (Uttranchal, Himanchal Pradesh, but also Nepal), but some are married, in particular women from the local area (Haryana) who are pushed into work because of low wages for the men. They find that in many cases the ‘crèche arrangement’ in the factory is just for show or that shift-times make it hard to arrange childcare. In that regard it is interesting to note that the current government labour law amendments, which are criticised as an ‘attack on workers’ rights’ from the left and trade unions, contain an increase in paid maternity leave from three to six months. Although we know that most legal rights are equally just for show, it nevertheless hints at the fact that the state has to address the problem of ‘fully proletarianised shrinking households’ and the social significance of female employment.
Their employment in modern industry is fairly new, but we can already see qualitative changes in the way women workers participate in struggles and in the gender relations. For example, while in 2010 during the first occupation at Napino Auto women left the factory overnight, in 2014 they stayed inside with their male workmates for the whole duration of ten days and nights. During the Jai Ushin / JNS dispute it was the women workers who started the wildcat gatherings, the male workers only joined them on the second day. Also during the struggle at Asti [18], women workers stayed at the protest camp in the industrial area overnight, which they had to fight over – not only with the female riot cops but also with their families. In that sense the participation of ‘local’ women is of particular importance, also given the general level of gender violence in the Haryana hinterland. [19]
*** The new composition of temporary and permanent workers forces them to take an initial step together, while management’s strategies to deal with unrest forces workers to occupy or take other ‘spontaneous’ actions.
In most factories we can assume a similar material pre-condition for struggles. We can see that:
a) Permanent workers account for only 30 to 40 per cent of the total workforce. This means that it would not be easy to take steps alone - either for the permanents or for the temporary workers. The fact that wage differences are less severe and work on the shop-floor similarly hard is more conducive to workers’ taking an initial action together – which is the case in most of the respective thirteen factories where the ratio of permanents and temps is around 1:3;
b) Over the last decade, in particular after 2010, workers have learned to deal with management’s usual strategy for industrial dispute: management builds up their stock reserves by ordering stock from other companies (either locally, sometimes from ‘mother companies’ abroad) and/or let workers work overtime; management starts hiring new people, either from regional technical colleges or contractors; management provokes a situation which allows them to suspend a few ‘leading’ workers (if they have their names e.g. through a union register, the easier it is to get the names); the bosses force the rest of the workers to stay outside through ‘good conduct’ undertaking [20] and/or through a police presence; in many cases management has already got hold of a court order which forces workers to stay a certain distance away from the factory gate; in some cases management has prepared food and accommodation for new workers which allows them to stay in the factory for 24 hours; this managerial strategy can hardly be challenged legally, which forces workers to take swift action through occupation to circumvent it: usually the A-shift refuses to leave once the B-shift is inside, while the C-shift workers support from outside.
The struggles themselves transform these material pre-conditions for collectivity and necessities for occupation into something more: in particular after the Maruti Manesar struggle it became a kind of moral duty of all workers, and also their official representatives, to emphasise the need for a unity between temp workers and permanents. Similarly, the occupations became more than a functional counter-strategy, but workers involved said that for the first time they were able to breath freely inside the factory and that for the first time they really recognised the other people they had been working side-by-side with.
What kind of ‘direct actions’ by both temp and permanent workers did we see? At Napino Auto workers occupied the plant at first for four, then for ten days; at Munjal workers occupied for several hours, were kicked out and continued the protest outside for 25 days, while production was down; at Shriram Piston workers occupied the plant twice and were only evicted through a massive police attack; at Jai Ushin/JNS over 2,000 female workers refused to enter the factory, gathered outside and demanded more money; at Asti workers reacted with joint wildcat strikes to dismissals and forced management to take them back; workers at Baxter went on an unannounced slow-down strike; at Track Components two wildcat strikes enforced bonus payments; wildcat strikes stopped both Wearwell factories and workers increased bonus payments; at Orient Electric hundreds of temp workers gathered in a park and demanded bonus payments; similarly Premium Moulding workers stopped work collectively for higher annual bonuses.
It is not easy for management to deal with such a scenario. The financial clout for major monetary concessions to the permanent workers to ‘buy them off’ has been increasingly restricted because of the general economic downturn and increased competition. The use of brute police force for evictions contains major material risks to plant and machinery and risks of political repercussions. Management prevention strategies seem helpless, e.g. since the series of occupations in many companies management will only let the B-shift enter the factory once the A-shift has left. This causes significant loss of production, but is a political price they have to pay. Therefore management’s major challenge is to undermine the developed organic unity of workers, to make it easier to prepare for and pre-empt workers’ actions and to keep them isolated and harmless once (parts of) the workforce ends up outside the factory. In this situation workers’ trust in the law and legal procedures, in representation, in the strength of trade unions as institutions and the union’s ability to organise wider solidarity actually play into the management’s hands. Workers know how to organise on the shop floor level, but their experiences of organising coordinated efforts beyond their company are still limited. As soon as workers leave the factory, bourgeois society comes down on them heavily in the forms of legal authorities and regulations.
*** The role of trade unions in the disputes: Where permanent workers and temp workers are divided, management will fight against the establishment of a trade union inside the plant. Where management faces collective actions of both permanents and temp workers, trade union formation either becomes a stumbling block for workers or a tool for management to undermine their collectivity.
The dynamic between workers’ unrest inside the plant, the formation of a company union and the trade union federations is complex. Even a close look at the respective chronologies doesn’t always reveal the concrete relations easily. First of all we can state that in ten out of our thirteen examples (some) workers formed a company union during the process of struggle, nearly all of them affiliated themselves either to HMS [21] or AITUC [22] trade union federations. These two unions have established around 60 company unions in Gurgaon/Manesar area, in total around 20 to 30,000 members – out of a total workforce of around 400 to 500,000 industrial workers. Most of the wildcat actions took place before the union was officially recognised, a few of them in order to protest against potential union representatives who had been sacked; some actions took place after the union recognition, e.g. in the case of Napino the union itself instructed the ten-day wildcat occupations, while at Asti the union ordered an unofficial slow-down strike under the pressure of impatient workers – who had expected that with the registration of the union concessions by management would follow automatically.
Below we summarise the general dynamic between workers’ aspirations, divisions between workers, the initial process of union formation and management’s reactions. We state the legal or formal reasons why forming a company union in most cases will hinder the development of collectivity between permanents and temps and makes it easier for management to foresee and counteract workers’ activities.
* Even before the question of union formation emerges, there is general discontent amongst workers and smaller collective steps are daily occurrences. So are repressive counter-measures by management. Workers know that they have to be organised together – and they can.
For example: In three of the thirteen examples (Wearwell, Jai Ushin, Orient Electrics) no union formation was taking place, but workers’ took wildcat actions, which all ended with management giving material concessions.
* In this situation (some) permanent workers compare their wages and conditions to those working at the central assembly plants, where a union has previously been established (and has been able to sharply increase the wage gap between permanents and temps), e.g. Honda or Maruti Gurgaon. So some permanents take steps to set up a union, but because the numbers of permanent workers has come down over the years, they need to incorporate the temporary workers.
For example: In most cases temps and permanents struggle together during the initial process, so at Asti, the union collected union dues from the temps up to the time when it was officially recognized even though they knew that they could not represent them in future – and betrayed them in the end.
* For most workers, in particular temp workers, ‘the union’ is still a symbol of workers’ strength and unity, but also contains a certain power-fetish: the union leaders are educated, workers are not; they have political links, which workers need; once a union is established there will be automatic improvements of wages in future; only improvements negotiated and settled on paper count, management won’t give anything without official agreement etc. These (mis-)conceptions are still widespread – and workers literally pay for it: The myth of the trade union as a guarantor for improvement also helps people to make money. Although the costs of registering a union is no more than Rs 500, workers often collect between Rs 200,000 to Rs 900,000, which ends up either in the coffers of the trade union federations, the lawyers or in some cases the permanent workers who started the registration process.
For example: In the cases of Subros and Track Components money disappeared without workers seeing results. In the case of Subros it seems that the union president embezzled the union funds.
* Though permanent workers depend on the temps, the union form itself questions their collectivity: only permanent employees can become members of the company union, temporary workers can only form a separate union, which rarely happens.
For example: In most cases the permanent workers appealed to the temporary workers to support formation of the union and to pay union dues, promising to take temp workers issues on board, but as in the case of Napino Auto and Asti, they were left in the lurch.
* Another reason temporary workers don’t often actively support union formations is the fact that the usual three-year wage agreements are less attractive for temporary workers, because they might not stay in the plant for that long.
For example: At Munjal Kiriu the permanent and older temporary workers did not manage to integrate the newly hired temporary workers, partly because their demands were mainly focused on seniority issues.
* For the application of union registration the names of members and representatives have to be given, which usually end up in the hands of the bosses; the representatives become pawns, who are either crushed or instrumentalised.
For example: At Shriram Piston the union president was suspended while union registration was pending; at Baxter management transferred the workers who had applied for union registration; at Napino Auto management was able to use the twelve representatives after they were first fired and then re-hired to broker a divisive wage agreement. The prime example in the area is the ‘sell-out’ of the early union body during the 2011 Maruti Manesar struggle.
* During this process wildcat actions and union formation can go hand in hand. Workers’ actions often lead to concessions and wage increases, even without written settlements.
For example: Of those ten companies that witnessed union registration/recognition processes at least eight saw initial wildcat actions of all workers (with concessions) before the union was formed.
* At this point it depends on the general situation and composition of the workforce: if permanent workers are isolated from the temporary workers and if management does not face wider trouble, the bosses will oppose the union formation. If management cannot break the collective dynamic and control the situation they might help setting up the union, as happened in the case of Asti or Maruti Manesar plant.
* Once the union is registered, officially strikes or other actions have to be announced, which allows the employers to prepare themselves, e.g. through hiring new people. Even when actions are not announced, the negotiation process around the demand notice makes it easier for management to control the pace of events.
For example: In particular at Asti it became clear during the slow-down strike that the union was not able or willing to counteract management’s strategy to undermine workers’ action, e.g. by hiring new people or by subcontracting work. The main argument was that it was the legal right of the company to do so.
* The certain formalization of dispute makes it easier for management to calculate certain risks and to prepare steps. The chance to divide workers and/or remove them from the factory increases:
For example: In seven of the cases either permanents (Baxter), temps who took part in the struggle (Asti) or both (Munjal, Shriram, Bajaj, Autoliv, Premium) ended up being ‘locked-out’ and in some cases dismissed. Only in the case of Shriram and Premium we can say that it was mainly police repression that caused both temps and permanents to end up outside, though ‘trust in the law(yer)’ was a more significant reason in the Premium case. And in the other cases, the existing division between temps and permanents and/or management’s ‘good-conduct’ strategy and the unions’ response to it forced workers outside. In the case of Subros the company dismissed nearly all temps and permanent workers in small groups and the union president disappeared with the union dues.
* In order to maintain their influence, trade unions propose steps to workers which makes them dependent on the apparatus, e.g. when management asks workers to sign a ‘good conduct’ undertaking as a precondition to go back to work, the union would advise workers not to sign it, even if their position is weak, e.g. production is running.
For example: In the case of Autoliv and Bajaj this led to a slow degeneration of workers’ strength. While Autoliv management used skilled workers and products from other plants and companies (Maruti workers, skilled workers from France etc.) to get production going, workers remained isolated.
* In this situation where workers are outside the factory and visible, the form of the company union tends to emphasise the company-specific conditions and steps and does not relate to the more general proletarian conditions. The division between (legally qualified, eloquent etc.) union leaders and workers generally results in workers becoming more passive and waiting for instructions and leaving it to the representatives to contact other ‘workers’ (usually only other union representatives). Once workers are protesting outside, the main course of actions that unions propose are legal procedures (labour court meetings), which take a long time, or symbolic actions, often away from the actual industrial areas or other workers; in most cases workers who don’t break this dynamic through self-activity end up getting tired and isolated.
For example: At Baxter, Subros, Bajaj and Autoliv workers sat outside in protest for several weeks in struggle for ‘their union’, but only on few occasions addressed workers in the wider industrial area directly.
* Union federations generally help little to create solidarity amongst workers. This is true locally, but even more so on a nation-wide level.
For example: HMS discouraged the Munjal workers to engage in common actions with the dismissed Asti temp workers who were protesting nearby. There are only a few examples where the union federation actually called for ‘solidarity strikes’. During the Rico ‘lock-out’ in 2009 [23] AITUC called for a one-day ‘general strike’ in Gurgaon, but this only led to workers thinking that ‘something was happening’ on their behalf. In the end they remained outside and the majority of them took their final dues.
* The links between the union federation and their respective political parties (less formal in the case of HMS) results in fostering illusions amongst workers about possible support from the political class.
For example: At Asti various political leaders turned up such as the president of the BJP’s women’s wing, but instead, this contributed to workers’ feeling even more let-down after politicians either siding with management or merely dishing out empty promises.
* Where the final outcome leads to material concessions the agreement tends to increase the wage gap. The three-year agreements make it easier for management to plan ahead and the wage gap undermines workers’ collectivity in future:
For example: Both permanent and temporary workers at Napino got a wage increase as the result of union-management negotiations. But permanents got a raise nearly three times higher than the temps, which led to major discontent. The prime example regarding this issue is Honda HMSI, where the union was established in 2005 through joint struggle. Management accepted the union, but refused to let temporary workers re-enter the factory. Since then the share of permanent workers to the total workforce has come down from 50 to 20 per cent through expansion of the temp workforce, while permanent workers’ wages increased from one and a half the temporary workers pay to five times their pay. The wage increases are also based on productivity bonuses, which only permanent workers are entitled to: the permanent workers have largely supervisory positions and have a material interest to make the temporary workers work harder.
To sum up, we hope to have been able to demonstrate the following:
- Collective direct actions exist before and during union formation processes and they deliver results without the necessity of formal settlements;
- The union as a from mainly appeals to permanent workers, and though they depend on temporary workers support, the legal union framework undermines workers’ collectivity;
- Workers still have many legal and formal illusions regarding the necessity of legal expertise and the potential to use the law against the bosses; the union apparatus still seems the main way to connect to both resources and (organised) workers in other companies;
- Management rejects the unions if they don’t face collective trouble; in case of joint-actions they try to make use of unions and formal procedures to control the workforce; this mainly depends on the ‘integration’ of the permanent workers;
- Although able to organise collective steps on the shop floor, workers haven’t found alternative organisational forms to coordinate beyond the company boundary – a necessity to fight back against the inevitable counter-attacks by management; this lack explains the persistence of trade union influence despite their obviously undermined material basis and despite often having interests that contradict those of the workers.
This brings us back to the initial question of whether ‘independent trade unions’ and ‘collective bargaining’ are the way out to overcome the ‘cellular character’ of workers’ struggles, e.g. in China. We think that the examples from Delhi demonstrate that workers’ direct actions are able to force bosses to pay up and that a formalisation of this process does not improve workers’ position. In actual fact, there are many examples to show it makes things worse. We can see that once workers are forced into a defensive position – for whatever reason – being affiliated to a trade union federation does not increase their strength, but rather contributes to the winding down of the disputes through legal channels. The examples from Delhi make it clear that so far, an independent workers’ coordination beyond the shop floor boundary has only existed as temporary and limited efforts – see below.
*** The factory struggles ‘communicate’ with each other, but they don’t yet coordinate amongst themselves. Workers still leave it largely to the unions to organise beyond the company level, which in most cases means that struggles remain isolated.
What kind of indicators or examples do we have of workers’ struggles overcoming company boundaries?
* The most obvious question will be: have the struggles at the suppliers impacted on production at Maruti Suzuki? And here we are at a certain loss, because we lack information from Maruti workers themselves. While the dispute at Maruti caused many of the suppliers to close down or reduce production, it seems that at least when it comes to smaller parts like AC components etc. the supply-chain is fairly flexible and necessary parts can be sourced from other local companies.
* The fact that struggles concentrated in time and space in IMT Manesar during early 2014 means that although there is no formal link between them, the fact that workers live and work closely together influences their struggles. To a certain extent, experiences are passed on informally, e.g. workers at Asti could tell the AITUC leader about how his union had treated workers at other factories nearby. News about struggles tends to spread quickly e.g. through mobile phone messaging.
* Certain struggles change the atmosphere in companies around them, e.g. after the Maruti Manesar riot in 2012 many company managements in the area gave concessions to their workers, similarly the riots in Noida and Okhla led to companies sending their workers home the following day.
* During the Maruti Manesar struggle a former Maruti worker managed to mobilise 200 Maruti workers to protest in front of a supplier company to force management to give treatment and a job guarantee to a worker injured after a work accident. On a different occasion Maruti workers supported locked-out Senior Flextronics workers in 2012 [24] by turning up and shouting slogans in front of their factory – which scared both management and police. There are several examples of such type of ‘solidarity actions’, but they rely largely on personal contacts.
* The high point in terms of coordination of struggles happened during the second occupation of the Maruti Manesar plant in 2011, when workers of eleven factories occupied at the same time. We assume the coordination was established through the rank-and-file contacts between different HMS shop floor workers, given the fact that most of the factories had HMS representation and, more decisively, after HMS regional and national hierarchy intervened and reduced the occupations to the four factories of the Suzuki group.
* During the Asti and Jai Ushin protests outside the factories the workers camp temporarily turned into a wider proletarian public sphere, e.g. struggling workers talked to other workers who were going to or coming back from work. Students came to support the workers. The idea to have a ‘mobile’ protest camp and to circulate within the industrial areas came up, but was not executed. Similarly, Premium Moulding workers started to address other workers through self-made placards, but their focus of activity remained on the developments at the labour court.
* After the Asti dispute, dismissed workers aimed at setting up an independent committee to ‘coordinate’ between colleagues who had started working in other factories in the area. They planned to meet regularly and to support each other in the new jobs. As far as we know though, the committee still tends to focus on the court cases of a minority of workers.
* We heard of an ‘independent struggle coordination’ between different factories in the Bawal area, closer to the Rajasthan border area, where mainly local factory workers linked up with local small peasants in struggle. We know about a series of factory struggles in that area, but little about the influence or role of the struggle coordination.
* The coordination of dismissed permanent Maruti workers unfortunately focused largely on the legal case and attempts to mobilise local ‘political’ support in the dismissed workers’ villages, as well as to influence the trade union elections in the Manesar plant. As far as we know there were little efforts to use the time and collective energy to set up a wider general workers’ coordination beyond the rather minoritarian union representatives.
We can see that coordination’ takes place on a rather random and informal level. Efforts to build more consistent structures are often sucked up into the power games of the existing trade union federations – which leads us to the question of the role of working class activists.
RESPONSES OF THE LEFT
*** We witness tragic misconceptions on the far-left: at times where management and trade union apparatuses have difficulties keeping class struggle under control, (rioting) workers are portrayed as victims, while trade unions and the labour law are defended against ‘Modi’s fascism’.
The left and ‘far-left’ reacts with a certain ‘anti-fascist’ reflex to the Modi government’s proposed labour law amendments: “the political right attacks the ‘labour movement’, we have to defend it”. The changes basically propose to narrow down the conditions for the registration of a trade union and redefine the strike laws. [25] The leftist response tragically ends up re-focusing workers attention back to the framework of the law, just at the moment where ‘wildcat occupations’ as an unlawful, but the only effective practice of workers’ struggle, have started to proliferate. Similarly, instead of supporting workers’ agency in their discontent as they attack ‘their own’ factories during riots, most leftists declare angry workers to be the sad victims of ‘management conspiracies’.
First of all we have to state that the labour law does not play a role for most of the workers, be it in the so-called informal or in the organised sector: they are not paid the minimum wage; they don’t appear on company books, as they are hired through contractors; they can’t become members of the company unions. Even though the ‘registration of a trade union’ under current law is supposed to be just a minor formal act, in reality it depends not on the law, but the will of the administration, political class and management if a union is registered, and more importantly, recognised. The proposed changes in the labour law won’t change this dynamic. The only way to curb the disrespect for the law emerging amongst the casualised mass of workers is through linking the permanent workers to the labour law and the companies’ future. Under the conditions of crisis the latter becomes increasingly difficult.
Trade unions themselves, similar to the unions in the UK or in Germany where currently governments are also launching rather symbolic ‘attacks’ on the unions, present themselves as the guarantors of law and order: “Trade unions across India see a grave threat in these changes. Tapan Sen, a Rajya Sabha member and vice president of the Centre of Indian Trade Unions, said that by enforcing a law that restricts workers’ participation in unions, the government is taking away all their outlets for grievances, pushing them towards more militancy. “If you push someone against the wall, what will they do?” asked Sen. “They will hit back at you.”” [26]
Here we have to ask what the political motivation behind the reaction of the (far-) left is. It might be a mere naïve reflex to defend whatever a right-wing government seem to attack. Or it might be a tactical decision to defend the union bureaucracy as the main organised form, which could guarantee a small, mainly middle-class left access to, and political influence over, the working class. From a similar perspective we can question the motivation of the political left, leftist academics and NGOs of establishing independent trade unions in China: is it actually ‘in the interests of the working class’ or in the interests of their own political trajectories?
The challenge for us lies in taking account of all the experiences of independent shop floor actions and their relation to efforts in building wider co-ordinations. This requires a daily engagement with workers’ reality in a concrete form, e.g. in the form of newspapers like Faridabad Majdoor Samachar. But it also requires proposing bold initiatives at the various isolated protest camps in order to transform them into permanent workers’ bodies, open for other workers’ in struggle – and an organised national and international debate of workers’ experiences.
--------
Footnotes:
[1]
FMS:
http://faridabadmajdoorsamachar.blogspot.in/p/about-fms.html
[2]
Global strike wave:
http://www.wildcat-www.de/en/wildcat/90/w90_in_our_hands_en.htm
[3]
'De-coupling' was the term economists used to describe their hope that the national economy in India and China will not be affected too harshly by the global financial crisis due to a bigger internal market.
https://libcom.org/library/global-crisis-india
[4]
Class relations in 1970/80s
https://gurgaonworkersnews.wordpress.com/workers-history/
[5]
Maruti strike, 2000/01:
https://gurgaonworkersnews.wordpress.com/gurgaonworkersnews-no8/#fn5
[6]
Honda, 2005:
https://gurgaonworkersnews.wordpress.com/gurgaonworkersnews-no7/#fn4
[7]
Hero, 2007:
https://gurgaonworkersnews.wordpress.com/gurgaonworkersnews-no4/#fn2
[8]
Maruti Manesar, 2011:
https://gurgaonworkersnews.wordpress.com/gurgaonworkersnews-no-941/
https://gurgaonworkersnews.wordpress.com/gurgaonworkersnews-no-944/
https://gurgaonworkersnews.wordpress.com/gurgaonworkersnews-no-945/
https://gurgaonworkersnews.wordpress.com/gurgaonworkersnews-no-948/#fn1
https://gurgaonworkersnews.wordpress.com/gurgaonworkersnews-no-951/
[9]
Car crisis:
https://gurgaonworkersnews.wordpress.com/gurgaonworkersnews-no-961/#fn2
[10]
AAP:
https://en.wikipedia.org/wiki/Aam_Aadmi_Party
http://radicalnotes.com/tag/aam-aadmi-party/
[11]
Construction riots:
https://gurgaonworkersnews.wordpress.com/gurgaonworkersnews-no-950/#fn3
[12]
Bangladesh:
https://libcom.org/tags/bangladeshi-garment-workers
[13]
Exports:
http://www.cleanclothes.org/resources/publications/factsheets/india-factsheet-february-2015.pdf
http://www.cleanclothes.org/resources/publications/factsheets/bangladesh-factsheet-2-2015.pdf
http://www.tradingeconomics.com/india/exports
[14]
China 2010:
http://www.gongchao.org/en/texts/2010/auto-industry-strikes-in-china
[15]
Women workers:
https://gurgaonworkersnews.wordpress.com/gurgaonworkersnews-no-963/#fn1
[16]
Mnrega:
https://gurgaonworkersnews.wordpress.com/gurgaonworkersnews-no-949/
[17]
Call centres:
https://gurgaonworkersnews.wordpress.com/gurgaonworkersnews-no1/
https://gurgaonworkersnews.wordpress.com/gurgaonworkersnews-no-952/
[18]
Asti dispute:
http://kafila.org/2014/12/03/days-and-nights-in-manesar-reflecting-on-the-asti-workers-struggle-anshita-arya/
[19]
Gender violence:
http://sanhati.com/wp-content/uploads/2014/07/wss-haryana-report-compiled.pdf
[20]
Good conduct undertaking:
Employers ask workers to sign individual agreements as a precondition to be allowed back to work, stating, e.g. that workers won’t engage in indiscipline, such as slow-downs, or raise further demands
[21]
HMS
Independent trade union federation, 3.3 million members in India
https://en.wikipedia.org/wiki/Hind_Mazdoor_Sabha
[22]
AITUC
Trade union federation of the Communist Party, around 2.2 million members
https://en.wikipedia.org/wiki/All_India_Trade_Union_Congress
[23]
Rico:
https://gurgaonworkersnews.wordpress.com/gurgaonworkersnews-no-921/#fn26
[24]
Senior Flextronics:
https://gurgaonworkersnews.wordpress.com/gurgaonworkersnews-no-950/#fn2
[25]
Labour law amendments:
http://www.catchnews.com/india-news/split-wide-open-industry-experts-and-insiders-debate-proposed-labour-reforms-1434976389.html
http://www.india-seminar.com/2015/669/669_gautam_mody.htm
http://www.epw.in/commentary/protecting-employers-against-workers-and-trade-unions.html
[26]
Trade unions on law changes:
http://scroll.in/article/736208/workers-get-more-militant-as-space-for-unionisation-shrinks
--------
Shorter Summaries:
1* Riots in NOIDA and Okhla industrial areas
When? 20th and 21st February 2013 during all-India ‘general strike’
What happened? Workers started attacking factories in NOIDA during an otherwise minoritarian ‘general strike’. The attacks were broadcast on television. In Okhla, an industrial zone around 15km away, only 200-300 union demonstrators assembled to try to persuade workers to stop work, but without success. On the following day, workers went to work in the morning, but stayed outside after the lunch break and started to shout strike slogans. A group of 5,000 to 8,000 workers gathered and took over the union demonstration, walking around randomly. They started pelting stones at expensive cars and factories and were joined by school students – it had more of a carnival atmosphere.
Outcome: Police retreated and there were hardly any arrests. Company management in Manesar, 30km away, gave their workers a holiday, fearing copycat actions.
2* Spontaneous mass factory shut-down, Faridabad
When? 22nd January 2014
What happened? Against the backdrop of a symbolic Haryana-wide public sector strike, a bigger group of factory workers in an industrial area in Faridabad – not connected in any (formal) way to the strike - walked from one plant to the other and called on workers to walk out. Around a dozen companies were affected. Workers shouted slogans for an increase of the minimum wage, which the Haryana government had announced on 1st of January 2014, but which was never implemented.
Outcome: Traffic on the highway clogged up. The following day management in that area called a holiday and many factories remained shut. The following day a huge police presence was noticed in the area.
3* Riot, Orient Craft, Gurgaon
When? 28th March 2014
What happened? A tailor died of an electric shock from a machine in the Orient Craft factory, a big garment exporter. 1200 women and men workers of the factory rebelled – first inside the factory, then out on the streets. Workers from other factories joined them. Police arrived from various stations and set up barricades against the assembling workers. Workers responded with throwing stones, both against the police and factory. The police reacted with lathi-charges, tear gas, and fired live ammunition. 40 vehicles got damaged in the riot. Many workers and hawkers were injured.
Outcome: Police registered cases against thousands of workers. Many workers got arrested.
4* Spontaneous mass-protests at Northern Complex Industrial Zone, Faridabad
When? 26th September 2014
What happened? There are about 25 to 30 medium-sized factories in this zone, built on the grounds of the former Northern India Iron and Steel factory. On 26th of September the early shifts assembled outside, while the night shifts waited inside the complex because they were angry about the terrible sewage system - sewage water had accumulated for months during the rainy season. The management was helpless and the police arrived. The situation remained this way till 1:30 pm. 3,000 to 4,000 workers of 25 - 30 factories had assembled and stopped work together.
Outcome: The following day the sewage system had been de-blocked and the streets were clean.
5* Udyog Vihar Riot, Gurgaon
When? 12th February 2015
What happened? This industrial area is spread out over more than 2000 acres and mainly consists of garment factories and some metal factories and call centres, in total around 800 - 900 plants, employing 200,000 plus workers. Rumours first circulated on 11th of February that managers and security guards had beaten and/or killed a worker at the Gaurav factory. The next day, unrest and violence spread from one factory to the other (maybe a dozen). An extra battalion of 500 police arrived, but facing 20 to 30,000 angry workers they had to retreat. Then 1,500 special police arrived, plus 500 police from Mewat and Faridabad. Workers attacked factories, machines and damaged 100 cars. The police managed to establish a curfew. By evening, things were peaceful again.
Outcome: No one was arrested immediately, though some were in the aftermath. Five workers are currently in prison.
6* Orient Craft Riot, Gurgaon
When? 19th June 2015
What happened? There had been earlier riots at this Orient Craft factory in Sector 37 in 2012. Rumours spread that a worker had been killed by electrocution - it later turned out that he had 'only' been injured. More than 3,000 factory workers started a riot: they set fire to a fabric store inside the plant, overturned at least a dozen vehicles around it and set them alight. Hundreds of policemen had to keep guard at the factory for the next few days before the company could resume production.
Outcome: Orient Craft management had asked the police not to arrest any workers because they feared that it would have further impact on production either due to lack of workers or due to workers getting angrier.
7* Napino Auto Dispute, Manesar,
When? 2010 to April 2014
What do they manufacture? Main wire harnesses for Hero motorcycles and Maruti Suzuki cars and electronic parts for Hero and electronic parts for export.
Workforce: There are 800 workers employed working on three shifts, out of which 100 are women workers.
What happened?
In May 2010, 800 workers occupied the plant for four days after a worker had been mistreated. They also raised discontent about wages. The 100 female workers took part in the occupation, but left the factory overnight. Management increased wages by Rs 3,500 over three years, attached to a productivity target.
In May 2011, management went for a counter-attack: they hired 400 new people, provoked the workers to go on strike, they used the police to remove the workers from the plant and kept production running. Workers sat outside for eight days, then 150 outspoken temporary and permanent workers were sacked, most permanent workers took final dues of Rs 20 to 25,000. Twelve fired workers filed an application for union registration.
Since March 2012, 631 out of 800 workers had been paying 100 Rs monthly to the union. The 325 workers hired through contractors also paid, but they were not given union membership.
In May 2012 around 90% of the workers started an overtime strike to get the 12 sacked workers (who put in the union application) back into the factory.
In July 2012, after the riot at the nearby Maruti factory, management decided to re-hire the twelve sacked workers and also re-hired 50 former temporary workers as trainees.
In October 2012 the union was registered and gave a demand notice to management. The union promised workers equal pay increases of Rs 25,000 over three years and temporary workers to be made permanent.
By March 2014 management still had not responded to the demand notice and workers got increasingly angry.
From 24th March - 3rd of April 2014 three Napino factories in the area were occupied by both permanents and temp workers under instruction of the union. This time female workers stayed inside the plant overnight.
Outcome: The union negotiated with management and agreed to Rs 8,100 for permanents and Rs 3,100 for temps over the next three years. Most workers were angry and threatened to beat up the union reps, but in the end accepted the deal.
8* Munjal Kiriu, Manesar
When? 18th of December 2013 - January 2015
What do they manufacture? Brake discs and drums for Maruti Suzuki, Nissan, General Motors, Hyundai, Toyota and Honda.
Workforce: Around 550 workers, 250 of whom are permanent and around 300 temporary workers.
What happened?
On 18th of December 2013 permanents occupied the plant after trainees were not made permanent. Police managed to kick them out the same day. Production stopped for 25 days, 100 newly hired workers could not start production.
In September 2014 a second strike/occupation attempt failed and was followed by a several month-long protest camp outside, this time with little impact, as production was running with temp workers and some loyal permanents. It is unclear when divisions between permanents and temps deepened, probably after the management-union agreement discarded the demand for regularisation – and after the 100 newly hired workers were not integrated in workers’ collectivity. Also, the union-management deal after the first occupation left a loophole regarding dismissals. Workers left HMS and joined AITUC after that. AITUC representatives seemed to have brokered a deal behind workers backs during the second occupation, which caused the several month-long protest camp and workers to rejoin HMS. HMS did not prove to be too supportive after workers sat outside for three months and discouraged Munjal workers to link up with sacked Asti temp workers.
Outcome: Arbitrary. 200 temps were made permanent during the course of the struggle and although general wage increases were low, the wages for these new permanents increased considerably. Permanent workers were not able to enforce the withdrawal of dismissals and suspensions of several colleagues
9* Shriram Piston, Pathredi
When? January 2014 – May 2014
What do they manufacture? Pistons and engine valves for most local automobile companies, e.g. Maruti Suzuki and for export, e.g. Ford (Germany), Renault (France) Honda (USA).
Workforce: 1,900 workers: 560 permanents, the rest are trainees or on 'fixed term contracts'.
What happened?
While the application process for union registration was pending, the union president was suspended. So on 24th March 2014 around 1,000 workers occupied the plant for five days, supported by 800 outside after management had refused entry to workers who did not want to work overtime. Management said they would take suspended workers back, but didn't.
On 15th of April workers occupied the plant again.
Outcome: On 26th of April police evicted workers, using teargas and live ammunition. Workers continued to protest outside.
10* Jay Ushin / JNS, Manesar
When? February - September 2014
What do they manufacture? JNS manufactures speedometers for Honda, Bajaj, Hero, Suzuki, Yamaha two-wheelers and Maruti Suzuki and Honda cars. Jay Ushin manufactures keys and locking devices for the automobile industry.
Workforce: The total of all three factories is around 3,500, out of which around 2,500 are female workers.
What happened?
In February 2014 three wildcat gatherings and strikes from workers of all three factories took place. The management responded by giving a Rs 1,000 wage increase and overtime bonus. But the management also prepares for further dispute e.g. by hiring new workers .
In September 2014 around 400 workers of the Jai Ushin factory go on a wildcat strike for higher wages. They leave the factory when the police arrive, but stay at the factory gate overnight. It is unclear why Jay Ushin workers stayed alone during the protest and JNS did not join.
A couple of days later they try to blockade the gates to stop other workers from going in or parts from going out, but they are attacked by police and the blockades fail. Union leaders start negotiating with/for them, although workers are temps and not in a union. The protests continue until 24th of September.
Outcome: Management increased wages by Rs 2,000 without any paperwork having had to be done.
11* Asti Electronics, Manesar,
When? 18th February 2014
What do they manufacture? Amongst other things, electronic equipment and cable harnesses for the automobile industry.
Workforce: Out of the 500 workers employed around 80% are women in their 20s. Roughly 125 are permanent and 350 are hired through contractors.
What happened?
Some male permanent workers were promised wages of Rs 8,000 to 10,000 once a union had been set up. They collected between Rs 1,000 to 2,000 from every worker in early 2014. In March 2014 there was around Rs 900,000 with the union.
On 18th of February 2014 all workers went on a wildcat strike in response to dismissals. They were successful on the same day.
At the end of May 2014 the union sent a demand letter to management and called for a ten-day long slow-down. This was undermined by management hiring new people.
On 1st of November 2014 temporary workers attempted to occupy the factory after being fired. The police stopped them. The following protest camp and actions (hunger strike, demonstrations) lasted till end of January 2015, but without a larger impact.
In May 2014 management was successful in dividing workers by giving special training to permanents only.
In July/August 2014 management and the union forged an agreement that deepened the wage gap between permanents and temps. The fact that management dared to kick out the 310 temp workers in one go in October 2014 was based on the trust management had in the union and the permanent workers. After they were kicked out the temp workers undertook various efforts to talk and meet the permanents, the factory union, the main union federation HMS - but to no avail. The permanents continued to work inside the plant. The temps relied on their own force.
Outcome: As a result of their struggle Asti workers said that they would form a committee to keep in touch – they started working in various factories in the area – and to organise outside of the union framework.
12* Baxter, Manesar
When? 19th February 2014
What do they manufacture? Medical and pharmaceutical products.
Workforce: Approximately 49,700 employees worldwide. It has production units in 27 countries, three of them in India. At the time of the dispute there were 300 permanent workers inside the factory, plus 100 trainees, 150 staff and workers hired through contractor, initially only for loading work. Around 70 per cent of the workers are female.
What happened?
On 15th of May 2013 workers engaged in a slow-down ‘wildcat’ strike, to which management responded with concessions. After management transferred several people in response to the union formation process on 18th of February 2014 workers engaged in a factory occupation – motivated by the strike at Asti Electronics nearby, which started on the same day. Male and female workers stayed in the factory overnight. Management promised to take the transferred workers back (some sources say 15, others 45 workers). Workers left the factory. Management prepared itself e.g. through hiring additional people and forced the permanent workers to stay outside the factory on 26th of May 2014. Protest sit-ins started and workers remain outside until August 2014. It is unclear whether both permanents and temporary workers took part in the 2013 slow-down and the short factory occupation on the 18th of February 2014. It is clear that only the permanent workers remained outside after the suspensions in May 2014.
Outcome: The union was neither able to force management to negotiate on the 56-demand notice, nor to maintain (or establish) the unity of temp and permanent workers (only permanent workers became union members, as per the law).
13* Bajaj Motors, Gurgaon
When? 24th February 2014
What do they manufacture? Engine parts for the automobile industry, around 65% of production is for Hero two-wheelers, some parts are exported to car plants in Turkey and France.
Workforce: There are 300 permanent workers and 1,500 workers hired through 8 - 9 different contractors; plus 300 middle-management.
What happened?
There had been various conflicts on the shop-floor in 2012 and 2013, some of them brought police inside the plant. A union was formed.
On 24th of February 2014 all workers, both permanent and temporary, stayed outside the plant after management asked them to sign individual ‘good conduct papers’. At the same time production kept running (on lower levels) with the help of additional temp workers, a few loyal permanent workers and management staff. The company had prepared itself for this attack e.g. through having let workers work overtime, but the workers were not. Staying outside they relied on the usual formal and symbolic forms of struggle, e.g. letters to the authorities, hunger strikes, which did not lead anywhere.
Outcome: On 30th April they were forced to accept the conditions of management and returned to work.
14* Track Components, Manesar
When? April 2014
What do they manufacture? Sheet metal parts for Maruti Suzuki, Honda and BMW.
Workforce: Around 1,000 workers, most of them temporary.
What happened?
There are only very few permanent workers in the factory, but management promised to make 15% of the temp workers permanent in January 2014. At various times workers had demonstrated that they could stop work collectively, e.g. after an accident on 17th of February 2014 or during two wildcat strikes in April and May 2014 for overtime bonus and DA (inflation compensation) payments. A union registration process was going on at the same time, but management got hold of the application and the signature list and dismissed eight permanent workers.
Outcome: The union collected a lot of money from both permanents and temporary workers (although the temps would not be able to join the union) and later on left workers in the lurch.
15* Subros, Manesar
When? May 2014
What do they manufacture? Air-conditioning systems for Maruti Suzuki.
Workforce: There were 300 permanents, 500 temporary, 300 to 400 trainees and 300 engineers were employed until April 2014, less after that date.
What happened?
At the end of 2013 an AITUC union was established at Subros and in April 2014 they arranged a slow-down, which led to a few dismissals and management asking workers to sign a 'good conduct'-undertaking. After that, over a period of time most old workers, both temps and permanents were dismissed, while the union president and leading figures of the union seemed to have been paid off and disappeared.
Outcome: In August 2014 a group of new workers nevertheless managed to fight back a wage deduction through spontaneous collective work stoppage.
16* Autoliv, Manesar
When? June 2014
Workforce: 60,000 workers in 80 plants in 28 countries. In Manesar there are 54 permanent workers, 12 trainees and 130 workers hired through three different contractors.
What do they manufacture? Parts for Maruti Suzuki and Mahindra Bolero.
What happened?
The company felt the pressure of deepening bonds between permanent and temporary workers and conceded some concessions: a wage increase for everyone, 20% bonus payments.
When management saw its control undermined they started to take repressive steps. In May 2014 they started to hire new workers through contractors. They transferred 40 skilled workers from the company's factory in Bangalore. Similar to the Bajaj Motors case, Autoliv systematically prepared itself for an attack on the permanent and temporary workers by hiring new people, transferring skilled workers from other plants of the company, by getting skilled staff from the main client-company Maruti Suzuki and by even flying in skilled workers from Autoliv France.
The company was able to use the usual trap: on 4th of June 2014 they sacked a small number of people and asked the rest to sign 'good conduct' letters. Workers, likely advised by the union, refused to sign, although they could see that management was able to run production. While staying outside, their main form of struggle remained symbolic and addressing the authorities.
Outcome: In the end they lost and the union brokered the redundancies.
17* Wearwell, Okhla
When? September 2014
Workforce: The dispute concerned two factories in Okhla. In factory 1 there are 380 tailors. In factory 2 there are 225 tailors, 70 finishing workers and 40 female workers who cut threads.
What do they manufacture? Garments, all for export - the company used to supply M&S.
What happened?
On 1st of September workers at both factories went on a five-day wildcat strike. A similar dispute about bonus payments took place in 2013, but in 2014 the strike included workers of both factories.
Outcome: Workers were able to increase the bonus payments by Rs 1,000. A later attempt by management to victimise single workers failed, facing the anger of co-workers.
18* Orient Electric, Faridabad
When? 20th October 2014
What do they manufacture? Around 8 to 9 million fans per year and also light bulbs.
Workforce: 1,163 workers, out of which 52 are permanent.
What happened?
On 29th October 2014 a significant minority of 350 temp workers stopped work and gathered in a park outside, demanding the statutory bonus payment. They were joint by cleaning workers. Older workers gave in to the pleas of management to resume work and a chance to join up with workers of other departments was missed.
Outcome: In November 2014 management offered an attendance incentive of Rs 700 per month (a 15% wage increase), having to deal with the problem that lots of temp workers were staying away from work regularly.
19* Premium Moulding, Gurgaon
When? October 2014 to June 2015
Workforce: Around 200 permanent and 50 temporary workers
What do they manufacture? Steering wheels and other parts for the automobile industry, in Gurgaon mainly for Maruti Suzuki but also for Hyundai and Ford.
What happened?
In October 2014 workers managed to enforce a bonus payment through a short work stoppage.
But in June 2015 they are less prepared to oppose management’s strategy to remove machines from the plant and shift work to Dharuhera. Workers relied too much on their lawyer and legal appeals
Outcome: Workers continued to be outside the factory.
------
Chronology of disputes:
1* Riots in Okhla during ‘general strike’
When? 21st February 2013
There are about 4,000 factories in Okhla industrial area, employing around 500,000 workers. The quotes below are from Okhla. The two-day 'all-India' general strike that was called for by the unions (against food price inflation and ‘privatisation’ policies of the government) as the background to this riot was largely symbolic: in Okhla itself on the first day, nobody really took part. In spite of unionists blocking roads, trying to stop workers from going to work, many of them bypassed them and went to work anyway. There was a demonstration attended by 200-300 people, an assembly, some speeches. In Faridabad and Gurgaon, production kept running although some public sector workers went on strike and many buses stopped running.
20th of February 2013
"The factories in Okhla phase I F–block all kept running, the garment factories Boutique International, Orient Craft, Shahi Export, Orient Fashion, Ditel and workers at Vodaphone and all printing presses were working. But after the lunch-break workers in one factory refused to go back to work. Five of us workers started to take a stroll in the area. People worked till nine o’clock at night. The night-shift workers arrived. In Phase I, management at Maya and at five plants of SMS in Phase II told workers to go home at 11 pm, production stopped.”
21st of February 2013
Union guys were out again, trying to put pressure on people to stop work but like the day before, they didn't listen.
Then things started to heat up. A local worker said:
"A few workers of a factory walked out at 10am saying that ‘today is the strike’. They shouted slogans. From a neighbouring factory 40 to 50 workers came out. From two lines of factories around 1,200 workers came out. Management started to be afraid, so around 10:30am to 11am management in 24 surrounding factories announced a holiday for the workers. In phase I, II and III workers started to walk out and by 10:30am the whole of Okhla industrial area stuttered into a standstill. Many workers went home, many workers kept on standing in front of the factories, many people joined the demonstrations… It grew to a demonstration of 8,000 to 10,000 people. Police retreated behind the police station when we passed. Then in phase I, after an attack with lathis (long sticks) the police retreated. In the whole area factories got pelted with stones."
“Workers did not seem to be angry, they were laughing.”
“The women workers who came out of the factories first threw more stones than the male workers and then went home to their rooms.”
“An expensive Audi car got smashed. Suzuki Swift cars got smashed and filled up with stones and rubbish.”
"The fourth and fifth class kids coming out of the public school threw a lot of stones at the factories."
"In the evening I saw that the windows of four factories behind the power station in phase II had smashed in windows. All workers were happy about it, they said it was great and that they should be burnt down."
"People started talking about seven arrested workers. We know one of these workers. We start talking that if they put him in jail, we will collect money between us to get him out. But in the end he has not been arrested. He is outside and no case has been filed against him. He is back at work.”
As well as the riots in Okhla, there was also unrest in NOIDA on the 20th February, to which the managements of Maruti Suzuki, Honda HMSI, Endurance, Satyam Auto and Hero responded by declaring a holiday for workers the next day.
22nd of February 2013
FMS: "When we distribute the newspaper at Okhla railway crossing near Sarita Vihar the faces of most workers are shining. Workers seem hopeful and excited. Thousands of workers are smiling."
"One can understand if workers get violent out of anger. If you give concessions, this violence can be kept under control. But the workers in NOIDA and Okhla did not portray any anger. They seemed to enjoy the violence. This is a very troublesome issue.” Publicised academic
2* Spontaneous mass factory shut-down, Faridabad
When? January 2014
The strike of Haryana state public workers on 21st, 22nd and 23rd of January had encouraged these factory workers to stop work. They were mainly angry about the fact that the rise in the minimum wage (by around 2,500 Rs to 8,100 Rs), announced on the January 1st 2014, had not yet materialised.
On the 22nd of January groups of factory workers had started walking from one factory to the other, calling on workers there to join them in a walkout. A mix of garment, auto and pharmaceutical companies like Vishani Lux, Boya Medical, Haryana Wire, Mahindra, Varmani Overseas, SKH, Mahrani Paints and Auto Ignition were shut down. Workers had also entered the offices of the factory bosses and told them to leave. Permanent and temporary workers, middle-management and management all stood in front of the Auto Ignition factory when, at about 10:30 am, a police jeep arrived and the policemen told the crowd to go back in and that they would see to it. After that 850 people went back inside. After the police jeep had left at about 11:15 am a group of 250 workers turned up again in the factory and told everyone to come out again. A local trade union leader also turned up. Management told the workers that a union rep had arrived and that they should listen to him. All people gathered on a grassy area on the factory premises. The leader said that everyone should remain peaceful and that he would talk to the management.
After a meeting between management and the leader the company announced that the 23rd of January would be a day off. In the whole area factories remained shut down on the 23rd. On the 23rd no workers was arrested during the protests, which resulted in 14 mile-long traffic jams
There was talk of keeping the factories closed for four days. On the 24th from early morning onwards there was a huge police presence in the area.
“When the factory bus arrived at the factory on the 24th there were four jeeps and one police bus waiting. During the meal breaks there were also a lot of police around. The Senior Superintendent of the Police (SSP) from Palwal arrived at the factories in order to reassure management that things are under control. The factories were running.”
(Local worker)
The Faridabad Industries Association complained to the state government. They said that unruly elements had entered the factories and caused trouble and mayhem. If the police could, they would turn up, but facing the rebel crowd they would silently withdraw. They said that these workers had come in, armed with sticks, and said that the factory was not supposed to run until Monday. This group of workers had not previously contacted the trade unions or organisations. None of the trade unions had ordered the factories to be shut down. Under these circumstances it is difficult for the managers to keep production running. According to the joint secretary of the Industries Association the police filed a case against 10 unknown youths and arrested 18 workers.
The atmosphere in the area remained tense e.g. at Indo Autotech in Faridabad management announced that new shift times, from 8 am till 8 pm. On 31st of January workers wanted to leave at the usual time of 5 pm, but management shut the gates and called the police. Lots of police arrived and were stationed at every exit. At this point workers said that they didn’t care whether management let them go or not, that in any case they would not work. For three hours workers strolled around in the factory, but the machines did not run.
3* Riot, Orient Craft, Gurgaon
When? 28th March 2014
On 28th March, between 11:30 and 11:45 am, Sunil Pushkar, a worker in the tailoring department of the factory, suddenly collapsed on his seat in front of the electronic sewing machine.
"Orient Craft workers had gathered in large numbers outside the factory gate after Sunil was taken away to the hospital. ASI Jaipal Singh told us that the police received information of workers gathering around 12 noon and they sent 65 policemen from different stations to the factory gate “in order to avert any trouble”. Workers were furious on hearing this and got into a scuffle with management officials. The police responded with a lathi charge and teargas shells and workers pelted bricks and stones at the police officials. Workers were chased back to their residential quarters in Sarhaul village, and police broke into some rooms and beat up the occupants. According to newspaper reports, nearly two dozen people, including workers as well as policemen, were injured in clashes that day.”
(Report fact finding team - see www.sanhati.com)
Orient Craft had the second highest export turnover among all apparel export companies in India in 2011-12 (Rs. 958.75 crore) and officially employed 29,300 people on its payroll. According to the Outlook Business magazine, the company earned revenues of Rs. 1,151 crores in the financial year 2013 and was the second largest employer in the Indian garment industry. It supplies to well-known international brands like Ralph Lauren, Banana Republic, Gap, Nike and Levi’s.
From only four factories in Okhla in 1993, the company has grown to operate 22 manufacturing units in the NCR region where between 150,000 and 200,000 garments are made in a day. The factory unit of Orient Craft, where the incident occurred, is located at Plot No. 7D, Sector 18, Udyog Vihar, a fifteen-minute walk from the manufacturing unit of Maruti Suzuki. Although the number of workers employed in this unit is not clear, it is anywhere between 5000 and 7500. According to one worker, around 3000 workers are permanent while the rest are hired on a contract basis through big labour contracting companies operating in the area. While the permanent workers are paid Rs. 5900 (they get Rs. 5100 after Rs. 800 is deducted towards PF), the contract workers get around Rs. 5700 per month. “No one ever earns more than Rs. 12000 after working for 12 to 14 hours in a day, irrespective of seniority or experience”, one worker told us.
We were told that 3-4 years ago, Orient Craft started the practice of monitoring individual tailors with stopwatches in order to calculate the amount of time taken to stitch a piece of garment. This practice was further refined 1-2 years ago with the introduction of magnetic card readers. Now, every bundle of cloth that arrives at the tailor’s desk is accompanied by a magnetic card. Every tailor has to punch this card on the card-reading machine at the beginning and conclusion of operations, which relays data regarding how many seconds each worker takes per task, and how many pieces he/she has finished in a day. Since the installation of these machines, work intensity has increased markedly.
(Factfinding report)
It is worth mentioning that Orient Craft also runs factories in Bangladesh. Management said that they shifted production there due to generally lower wages.
In the Delhi area, workers' discontent at Orient Craft is not confined to a single factory and it goes beyond rioting, as the following examples demonstrate.
Orient Craft Okhla:
In February 2014 at the Orient Craft factory in Okhla (30 km from Gurgaon) the company tried to stop four workers at the gate and refused them entry. Inside workers stopped production for two days in response. Management then let the four workers back in.
Orient Craft Manesar:
At the Orient Craft factory in Manesar (20 km from Gurgaon) shifts run from 9am till 0:45am, but the food provided by the company is insufficient. Workers complained to the general manager. In June-July 2013 the workers spoke amongst themselves. One day the 1,000 permanents and 1,000 temporary tailors did not stay for overtime. At 5:45pm the whole production floor was empty. The general manager said again, that he was not able to change anything about the food situation. The following day the tailors walked out after their 8-hour shift. The general manager said: okay, start doing overtime again, you will get 5 instead of 3 roti and 3 instead of 2 spoons of rice. Then the company kicked the general manager out of his job. In January 2014 the company declared new regular shift times: 9:00am to 8:45pm and changed the break-times, which caused major queues in the canteen. One day a security guard slapped one of the workers. The following day on 17th of January 2014 all the tailors assembled at the gate and refused to go inside. Management staff tried to put pressure on them, but workers refused. This continued for a while. As a result of the commotions the company kicked out the next general manager...
4* Spontaneous mass protests at Northern Complex Industrial Zone, Faridabad
When? 26th of September 2014
There are about 25 to 30 medium-sized factories in this zone, built on the grounds of the former Northern India Iron and Steel factory. The sewage system is bad, so sewage water accumulated over months during the rainy season. On 26th of September the early shifts assembled outside, while the night-shifts waited inside the complex. The management was helpless and the police arrived. The situation remained this way till 1;30 pm. 3,000 to 4,000 workers of 25 - 30 factories had assembled and stopped work together. The following day the sewage system had been de-blocked and the streets were clean.
5* Udyog Vihar Riot
When? 12th of February 2015
The industrial area is spread out over more than 2000 acres and mainly consists of garment factories and some metal factories and call centres, in total around 800 - 900 plants, employing 200,000 plus workers. The area borders the Maruti Suzuki Gurgaon plant in the southwest and the highway NH8 in the southeast, where large office towers and some shopping malls are located.
On 11th of February rumours first circulated that managers and security guards had beaten and/or killed a worker at Gaurav/Richa factory. On 12th of February unrest and violence spread from one factory to the other (may be a dozen). The local Gurgaon police could not deal with the situation. An extra battalion of 500 police arrived, but facing 20 to 30,000 angry workers they had to retreat. Then 1,500 special police arrived, plus 500 police from Mewat and Faridabad. The industrial zone had turned into a war zone, with companies and the state on one side, workers on the other. Workers attacked factories, machines and damaged 100 cars. In the targeted factories workers destroyed CCTV cameras and recorders. Traffic was blocked along the Delhi-Gurgaon Expressway, IFFCO Chowk, MG Road, too (main local traffic arteries), but not due to a workers’ invasion, rather police efforts to insulate the privileged from the insurgents. Then the police established a curfew. By evening, things were peaceful again. No one got arrested immediately, though some were afterwards. Currently five workers are in prison.
In the aftermath the representatives of local companies said in the press that the riot will give Udyog Vihar and Gurgaon a bad name and that industry might relocate. The police commissioner called it a pre-planned riot and blamed 200 ringleaders for it - whereas other media sources said that 10 to 20,000 were involved without ringleaders and that in future arrests people will face long prison sentences.
From a local media report:
"Our findings have shown that the episode was orchestrated as hundreds of protestors were already gathered at the spot well before the violence actually started. Also, we have found that a fictitious organization had requested the labour department to be registered as a labour union. But since it showed only 100 enlisted workers, the application for registration was rejected," the official added. The report also mentioned that due to sporadic unrest in the garment industry over the last three-five years, some industries had shifted to Bangladesh, taking an estimated Rs 160 crore worth of exports with them. Seeking an in-depth investigation into the Udyog Vihar violence, the report urged the state government to take this up with the Centre."
During the following distribution of FMS in Udyog Vihar workers were smiling and 2,700 copies were distributed within no time, there were not enough newspapers.
6* Orient Craft Riot
When? 19th of June 2015
There had been earlier riots at this Orient Craft factory in Sector 37, Gurgaon in 2012. On 19th of June 2015 rumours spread that a worker had been killed by electrocution - it later turned out that he had been 'only' injured. More than 3,000 factory workers started a riot: they set fire to a fabric store inside the plant, overturned at least a dozen vehicles around it and set them alight. Hundreds of policemen had to keep guard at the factory for the next few days before the company could resume production. Orient Craft management had asked the police not to arrest any workers because they feared that it would have further impact on production either due to lack of workers or due workers getting angrier.
7* Napino Auto Dispute, Manesar
When? 2010 to April 2014
*** Company:
Napino Auto and Electronics in Manesar produces main wire harnesses for Hero motorcycles and Maruti Suzuki cars and electronic parts for Hero and electronic parts for export. They are second tier suppliers for Audi, Magna, GM, PSA, VW.
http://www.napino.com/
*** Workforce:
There are 800 workers employed working on three shifts, out of which 100 women workers.
*** Chronology:
May - June 2010 - Factory Occupation in response to mistreatment and ow wages:
In May – June 2010 during the A-shift, after having made a small mistake, a worker was forced to stand for a long time in the heat and a manager pulled his ear to make him squat. In response the workers in the main harness department on the ground-floor stopped work and went upstairs to the electronics department, where workers also laid down tools. All workers stopped work and sat down. The company closed the canteen. At 2:30 pm, the A-shift workers refused to leave the factory at the usual end of working-time. After half of the B-shift workers had arrived management stopped the other workers from entering. The workers remained inside the factory for four days. Around 100 female workers of the A-shift stayed together with their male co-workers. The female workers did not stay over night, they brought in food in the mornings, which had been cooked by people outside. The workers shared it amongst themselves and ate together. After four days people of the labour department arrived and asked the workers to sent five representatives. The company chairman promised that in future such misbehaviour won’t take place. When workers said that the wage is too low and that the company should increase it the chairman said that he’d rather close the factory, but that he won’t give a paisa more. Workers insisted, so an agreement was made that the wage will be raised by 3,500 Rs over three years, but at the same time the production target was also increased a lot. Actually, up to today the production target fixed in the agreement has not been met.
May 2011 - Provoked strike and lock-out, mass-dismissals
The company prepared itself for a counter-step. Management gave a 500 Rs wage increase to some individual workers. Some workers were promised to be made permanent. Management prepared to hire 400 new workers from outside. The police settled down near the premises. After a minor issue was blown up 100 workers agitated to take a step, so in May 2011 workers of the A-shift went on strike (or were agitated to go on strike). The police arrived and used force to kick workers out of the factory. Management stopped the B-shift from entering the plant. The 400 workers were brought in and hired on the spot. Workers continued the strike for eight, nine days from the outside. Around 150 permanent and temporary workers who had been most outspoken were sacked. Most of the permanent workers took 20 to 25,000 Rs final dues and also left the job. Most of the 400 newly hired workers were also sacked again.
June 2011 - Napino closes during Maruti occupation, some workers try to form a union:
During the 13 days factory occupation of the Maruti Suzuki Manesar workers in June 2011 Napino Auto closed its plant. Twelve Napino Auto permanent workers who had not taken their final dues went to the labour department to object the dismissal. There they met a union leader who told them to register a union at Napino Auto. Secret meetings started with workers who were still employed inside. When 90 per cent of these workers agreed to the registration plan the twelve workers filed an application in Chandigarh. Management said that these twelve workers had been terminated and had the registration file closed.
September 2011 - Napino workers meet Maruti workers at their protest camp
When the Maruti Suzuki struggle intensified in September and October 2011, around 400 female and male Napino Auto workers went three, four times to meet the Maruti workers at their factory gate. In March 2012 the twelve workers again opened a new union registration file.
May 2012 - Over-time strike and protest to re-instate 12 workers:
In May 2012 90 per cent of the workers started to wear black arm-bands in order to demand the re-hiring of the twelve workers. They refused working over-time – they used to work 150 hours over-time per month, paid single instead of statutory double rate.
18th of July 2012 - The impact of the Maruti violence on Napino - management re-hires sacked workers:
Again, on 18th of July 2012 the situation at Maruti culminated, 100 managers were admitted to hospital and the factory was closed. The Napino Auto management was very afraid, negotiations re-started. After July 2012 management stopped threatening workers in the plant. In August 2012 all twelve workers who had been sacked in May 2011 were taken back on in the factory. In addition, Napino Auto management called 50 to 60 temporary workers, who had been working in various production positions and who had been kicked out, and re-hired them for one year as trainees. Fifteen of the workers hired through contractors working at Napino at the time were hired as trainees for three years.
October 2012 to August 2013 - Union registration and back-and-forth over demand notice
In October 2012 the union was registered. The union gave a demand notice to the company. For two, three months management did not reply. In November 2012 the company made 51 workers hired through contractor permanent. In preparation for the India-wide general strike, 500 Napino Auto workers took part in a trade union event in Faridabad on 6th of February 2013, handing over a memorandum to the labour minister. But on 20th of February 2013 production kept running in the factory. When workers’ riots kicked off in NOIDA the company sent workers on holiday on 21st of February 2013 and told them to work on Sunday instead. The workers refused. The union said that union and company are in a formal dispute and that therefore workers should come to work on a Sunday, making up for the 21st of February. Negotiations started between union and management at the labour department. After eight to ten days the issue was not settled. The union asked workers to wear black arm-bands from 26th of August 2013 onwards. This did not have any impact. The appointment at the labour department on 29th of August also remained without result. On 30th of August the union gave the company 5 days ultimatum.
A temporary worker: “Since March 2012 out of 800 workers 631 workers paid 100 Rs monthly to the union. The 325 workers hired through contractors had also paid 100 Rs per month to the union, but they were not given membership. Only 306 workers are members of the union, amongst them the union leadership. The union leader said that everyone will get the same wage increase and that everyone will be made permanent, that the negotiations were positive. But the actual leadership regarding negotiations at Napino is with a Honda union leader and everyone knows about the relation between permanent workers and workers hired through contractor at Honda. We know what the Honda union does in the factory. At Napino the management fears some of the permanents, but the workers hired through contractor specifically. The demand notice states 25,000 Rs wage increase over three years, but we have heard that the management so far agrees only to 8,200 Rs. The workers hired through contractors know that their increase will be less, so they told the union leaders that if it will be much less, if it will be less than 7,000 Rs, then they can get lost with their union and the company will have to pay in this way or the other.”
March 2014 – Prelude to the factory occupations:
After months of fruitless waiting for negotiation results workers, in particular temporary workers started urging the union for action. Since September 2013 the union did not have the courage to call for general meetings of all workers. Out of the twelve members of the union body six are on the shop-floor, but they don't work. When workers went up to them and urged them for action they said: "Go back to work!". By March 2014 there was an atmosphere in the factory in which anything would have been possible. If anything had started management and union would not have been in control. Meanwhile, in the company's new factory in Sector-8, where only temporary workers are employed, the workers are out of control of management.
24th of March 2014 – Three Napino Auto factories occupied in Manesar and Gurgaon:
Then, on 24th of March, the union undertook a step without previously mentioning it to the workers, they undertook a step according to today's necessities of workers' struggles:
Plot 7, Sector 3, IMT Manesar, Nippon Auto and Electronics; On 24th of March the general shift, a- and b-shift stay inside; at the same day on Plot 131 in sector 8 workers of the same company sit-down and stop working; the same happened on Plot 753 in Udyog Vihar Phase 5 in Gurgaon; in all of the three factories women workers don't leave the plant over night, but stay at the occupation – which is a major difference to the 2010 occupation, when women left the plant over-night; the workers stay inside from 24th of March till 2nd of April; the company had closed the canteens from day one; the c-shift workers supply their work-mates inside with food; workers from other factories support them; the occupations took place on instruction of the union.
28th of March 2014 – Negotiations between union and management without result:
On 28th of March management called the union leaders for negotiations to Delhi. The leaders came back and said that they did refuse the conditions imposed by management during negotiations.
2nd/3rd of April 2014 – End of occupation and betrayal of temp workers:
On 2nd of April management called the union leaders again. Negotiations took place inside the factory between factory management and union. The union leaders reassured workers that the wage increase will lead to equal wages and that it will be a ground-breaking outcome.
On 3rd of April management arrived and told workers to dispatch parts from the storage of the factory, because a settlement had been reached. The same was repeated by the union leaders. In the afternoon the workers left the factory and assembled at the gate. The outcome of the negotiations had been leaked. Instead of an equal wage increase the permanent workers were given Rs 8,100 over three years, while the temporary workers were paid only Rs 3,100 more over the same period... There were no speeches and the union leaders did not dare to announce the result. Scuffles broke out with the few who were in favour of the agreement. The majority of workers expressed their anger against the unequal outcome. In order to save the twelve members of the union body from being beaten up they were put in a jeep and driven away. The regional leader of the union did not dare to come to the factory, he held a meeting with few supporters in a distant park. Discussions amongst workers continue...
8* Munjal Kiriu Dispute, 18th of December 2013 – January 2015
*** Company:
Munjal Kiriu in IMT Manesar produces brake discs and drums for Maruti Suzuki, Nissan, General Motors, Hyundai, Toyota and Honda.
http://www.munjalkiriu.co.in/
*** Workforce:
1,000 workers out of which 400 temp workers employed on 12-hour shifts, sometimes they have to work 24 hours on stretch. Other sources: Around 550 workers, 238 of whom are permanent, 6 TT (technician trainee) and around 300 temporary workers
*** Prelude:
There had been small collective protest sit-ins of both permanent and temporary workers in 2013 - see:
https://gurgaonworkersnews.wordpress.com/gurgaonworkersnews-no-961/#fn6
*** Chronology:
22nd of February 2013:
Some workers file an application for union registration. Management react by terminating 5 out of 7 of the union body members whose names appear in the application letter.
12th of June 2013:
(Permanent) workers get their union registration and affiliation with HMS. They present a demand letter to management.
26th of November 2013 – Four-year agreement:
After some back-and-forth a four-year agreement is signed. Most of the demands, including regularisation of contract workers, are disregarded. The wage increase is only Rs 4,500 to 7,200 Rs. over a period of four years. Four of the suspended union members are taken back, one remains suspended.
18th December 2013 – Occupation after trainees not made permanent:
Less than a month after this binding agreement was signed, the permanent workers stop work because three guys were not made permanent after they finished their training. Both A and B shift workers, numbering around 300, later joined by C shift workers, start a sit-in strike or occupation at around 2pm. At 9pm 1,000 Haryana police personnel (who entered the factory at around 4.30pm) kick them out. Workers start a protest camp near the factory gate.
January 2014 – Protest camp:
Production stood still for 25 days. The company suspended 64 workers as result of the occupation. Around a 100 new contract workers have been brought in to resume production, which turned out to be difficult.
15th of January 2014 – Agreement to take back suspended workers:
An agreement was reached on 15th of January 2014 saying that the suspension decision concerning 49 were taken back and 15 workers will be subjected to an inquiry process - and the company and union agreed that even if they are found guilty they won't be 'dismissed' ("it will have a consequence less drastic than 'dismissal'). There are speeches by the union leaders proclaiming victory.
April 2014:
In April 2014 the company asks rhetorically why the agreement should not allow them to 'discharge' the workers (which according to them is less drastic than 'dismissal') under scrutiny, in case they are found guilty. At that point the permanent workers leave HMS union who they blame to have left this loophole, and join AITUC.
June 2014:
Under some pressure 200 temps were made permanent, the wage for the new permanents was increased from Rs 7,000 to 12,000. The workers still don't get ESI or PF, though money for that is cut from their wages.
26th of August 2014 – 9 workers ‘discharged’:
9 workers who had been suspended after the occupation are 'discharged'. The permanent workers give notice to the deputy labour official and the DC about the dismiss-discharge farce and start to wear black armbands at work.
22nd of September 2014:
The company breaks open the lockers of 25 workers and accuses them of theft.
23rd of September 2014:
Management declares that an agreement has been forged with some permanent workers who acted as representatives, but once asked, the respective workers deny this.
24th of September 2014 – Start of protest camp:
Those seven workers who allegedly signed an agreement sit down together with other workers of the early shift in the utility plant. Production stops. 50 to 60 police arrive at the factory. The workers hired through contractors are threatened and put to work. After a short while those workers who allegedly signed an agreement with management start to put pressure on the rest of the workers and start to work themselves. After five hours production starts again.
When the A-shift leaves the factory at 2pm the B- and C-shift workers are already waiting for them. (Nowadays the A-shift workers have to leave the factory before the B-shift workers are allowed in - management knows from examples of many recent factory struggles that once A- and B-shift workers are together inside and decide to take actions, there is trouble.) The other workers hear the bad news from inside and decide that neither B- nor C-shift would go to work. After 2pm the Munjal Kiriu workers sit outside. Inside workers hired through contractors work on two 12-hour shifts, plus 100 trainees and a few permanent workers. Production is running.
25th of September 2014
The Munjal Kiriu workers leave the trade union AITUC after this event and go back to HMS.
30th of September 2014
At a gate meeting HMS union leaders announce that a meeting with the labour official will take place on 1st of October, that 40 permanents have been suspended and that two more have been 'discharged'.
4th of January 2015
Workers are still outside. It is cold, workers sit on plastic sheets day and night, their positions has been weakened, but they are still determined. There are debates about a moving protest camp to overcome the isolation: in front of other Munjal factories, of suppliers, of client factories, at bus stops, colleges etc.
15th of January 2015
At first HMS leaders were very active but after three months outside, they have given up on the workers. Workers accept the conditions imposed by management. They accept that 9 workers will remain dismissed and 20 will remain suspended and go back inside the factory.
9* Shriram Piston and Rings Ltd. Dispute, 23rd of March 2014 – end of April 2014
*** Company:
Shriram Pistons and Rings Ltd., located in Pathredi Industrial Area on the Haryana-Rajashan border, around 20 km from IMT Manesar. Production started in March 2011. They manufacture pistons and engine valves for most local automobile companies, e.g. Maruti Suzuki and for export, e.g. Ford (Germany), Renault (France) Honda (USA).
https://www.shrirampistons.com/
*** Workforce:
1,900 workers: 560 permanents, rest trainees or on 'fixed term contracts'.
*** Chronology:
November 2013:
Some workers filed an application for union registration.
6th of January 2014:
The union president got suspended by management.
31st of January 2014:
Second application with AITUC was issued by workers.
1st March 2014:
Management puts a legal halt on the application process.
2nd March 2014:
Meeting of 1,600 workers, including temporary workers.
8th of March 2014:
Workers put forward demand letter, including wage increase demand.
24th of March 2014 – Dismissals and plant occupation:
The management asked the workers to do overtime on Sunday, 23rd March. Those who refused to do overtime were not allowed to enter the plant on the following day. The workers decided to occupy the plant premises and stop production. For the next five days, around 1,000 workers were on sit-in strike inside the plant, and 800 workers sat outside the plant.
28th of March 2014:
Management agreed to take back all 22 suspended workers, including the president of the union within the next ten days. But after that management showed no intention of taking the workers back.
15th of April 2014 – Second occupation:
1,800 workers went on strike and occupied again - 1,200 workers remained inside and 600 workers outside the factory. A negotiation meeting was agreed for on 28th of April 2014.
26th of April 2014 - Eviction:
At 5am around 2,000 policemen and 200 bouncers attacked workers with lathis, water cannon, and teargas. Workers resisted by pelting stones and burning four cars. They only dispersed when police fired rounds of live ammunition. From news reports it is unclear whether workers sat inside or outside or both at that point. 79 workers have been hospitalized, 4 with serious injuries, 26 workers arrested on attempted murder charges. Workers continued their protest at a 500-metre distance.
10* Jay Ushin / JNS, Manesar, 10th of February 2014 - September 2014
*** Company:
There are three companies located on the same premises, initially using one entrance/exit-gate: JNS, Jay Ushin, Jay Auto. They all belong to the JPM Group. The group claims that 9 in 10 cars manufactured in India contains parts of the JPM Group. JNS manufactures speedo-meters for Honda, Bajaj, Hero, Suzuki, Yamaha two-wheelers and Maruti Suzuki and Honda cars. Jay Ushin manufactures keys and locking devices for the automobile industry.
http://jpmgroup.co.in/jns-instruments-limited.html
*** Work-Force:
The total work-force of all three factories is around 3,500, out of which around 2,500 are female workers.
At Jai Ushin there are around 1,115 workers, 600 of them permanents, the rest hired through 8 to 12 different contractors. The factory has three floors: 390 women workers in the lock-set department, 350 in the switch department, 50 on the third floor in the lock-department for four-wheelers plus 25 in moulding department. The women workers arrive in buses from Delhi, Gurgaon plus from the Haryana hinterland. The male workers work on two 12-hour shifts, the shifts change every 15 days, on that day they have to work16-hour shifts.
10th of February 2014 - Women of all three plants assemble before shift and refuse to enter:
Before the start of the early shift, more than 2,000 women workers assemble. The factories use the same gate and start at same time. The women don't go inside. For two hours they raise the issue of the government's promise to increase the minimum wage (1st of January 2014) from Rs 5,500 to Rs 8,100. The police arrives. Women go to work after a while.
12th and 13th of February 2014 - Women workers repeat assembly and are joined by male colleagues:
The women workers repeat the gathering on the 12th of February and were joined by their male colleagues on the 13th. Inside the JNS factory the KWS line, which manufactures speedo-metres for the Hero Fashion Pro motorcycle-model runs only for two hours on the 12th and not at all on the 13th. This affects production in the press-shop, the printing department, the 'movement line' and the 'auto line'. In order to undermine these efforts of the workers management decide that instead of letting the workers off the buses outside the gate, where they can assemble more easily, they will ask the drivers to park the 6am buses on the factory premises. Some women workers are then forced to enter the factories. Many male workers of the 6am shift do not enter the factories. The bus of the women workers that arrives for the 9am shift is stopped 2 miles away at IMT Chowk, the women workers walk the rest to work. In the evening the company announces that the wages will be increased by Rs 1,000 and over-time will be paid double - "now go to work!".
28th of April 2014 - Confirmation of wage increase:
On 28th of April JNS workers confirm that wages have been increased and over-time is paid double now, though while previously the company counted 4 out of 12 hours of a day shift as over-time, now after the change they count 3.5 hours. Workers also report about various previous small protests of women workers who had left the job and not been paid their outstanding wages. They gathered at the gate and verbally and physically attacked senior staff.
12th of September 2014 - Wildcat-strike at Jai Ushin:
300 women who arrive at 9am at the Jay Ushin factory go inside the factory, but do not start to work. 100 male workers join them. The managers say that they need more time to increase pay, "give us three, give us two months…". After one hour a bus and two mini-buses with female and male police-officers arrive. Only then the managers say: go to work or leave the factory. All workers leave the factory and sit down outside. When the company buses arrive at 6:30pm the female workers took them to go home.
13th of September 2014 - Protest sit-in at Jai Ushin factory:
The following morning the women workers arrive at the plant again. Again they went inside, but did not start working and go outside again. When the buses come at 6:30pm the women do not take them, but stay at the factory gate over night. One of the few women who worked during the 12th and 13th says that management was in panic, they did not let women go and have tea downstairs, they made them stay till 8pm and then drove them out through the JNS gate. The company starts hiring young male workers with ITI qualification. But that does not turn out to be so easy, some guys leave the job as soon as they see the women workers sitting outside.
14th of September 2014 - Failed attempt to blockade the gates:
When the company wants to bring in workers with buses, the women workers storm forward and try to blockade the gate. The female police officers respond with a lathi charge. When the workers try to stop material from leaving the factory the male and female police again respond with lathi attacks. The conditions are hard: the company has stopped water-supply to the workers outside, a lot of mosquitos and drunken lumpen-elements at night. Where the Jay Ushin workers sit in front of the gate tens of thousand of workers walk by day and night to get to their factories. Conversations with many of them start. The media also arrives. Some union reps arrive from other factories in order to offer support. Seeing that there are only workers hired through contractors employed, the union reps realise that there is no chance to establish a union at this company. Nevertheless, the leaders try to summarise the various issues that streamed towards them from workers' mouth in a demand notice. A demonstration is called in Gurgaon for the 18th of September.
19th of Septemer 2014 - Negotiations in Gurgaon:
Some union leaders take some workers to a meeting with management in Gurgaon. Management give a list of names of 12 male and 25 female workers and say that apart from these workers everyone else should come back to work. The 400 workers sitting outside the gate rip the list to pieces as soon as they got hold of it. Students from Delhi's universities start to arrive. Because there is no leader to stop them from doing so, workers talk openly and widely with everyone. Drinking water and food has been organised and the female workers go to rooms of their work-mates in nearby Narsinghpur in order to have a wash.
24th of September 2014 - Jai Ushin management gives concessions:
The company cannot understand what's going on. They give some concessions and let all workers go back to work on the 24th of September. No written statement has been given, but one contractor says that wages have been increased by Rs 2,000. Up to now the company refused holidays on festivals... but now they have announced holidays for two important festivals.
Post-24th of September 2014 - Management tries to regain control:
Between 12th and 23rd of September management was able to hire 170 women extra. When the women workers go back inside management tries to take back control: a high company official starts walking around in the factory with a rifle. A supervisor is posted at the door that leads to the toilets, to see who is coming and going. Before the end of shift managers position themselves near the lockers, to stand and watch. They try to stop conversations between the 170 workers who have been inside during the dispute and the rest.
The workers were supposed to be paid their overtime money from the period 1st of September to 11th of September on the 27th of September. When workers demand their pay the bosses say: "First shout some slogans, then you get your money". Workers assemble four times to demand the money, then they are paid. The female workers are paid double rate (which is exceptional), the male workers a bit less. Also: the factory runs since ten years but management has never paid the statutory annual bonus. This year, after the walk-out, management paid the bonus before Diwali in October.
10th of October 2014 - Dispute about delayed wages:
The September wages are supposed to be paid on the 7th of October. Workers assemble and go together to the HR department on 10th of October. The boss says that "someone else" will give you the money, so workers replied that "'this someone else' might then also have to do their work for them, if he does not pay quickly". The boss gets slightly nervous and calls the contractor and wages are handed out the following day.
19th of October 2014 - Further small conflict regarding day-off
On Sunday, 19th of October workers work on their usual day off, because they want the 22nd off (Diwali) instead. Management says that on the 21st there will be a program in the factory, women are allowed to wear Saris, there will be dance and food and presents. On the 21st, after the party, the company puts up a notice that the 22nd will be a normal working day. Workers are angry and tear down the paper. They go to the HR and request their Diwali presents immediately - he replies that the presents will be given on the 22nd at 1pm and that the whole day will be counted as overtime. On the 22nd the workers go to the factory, take their presents and leave again.
27th/28th of October 2014 - Single workers sacked
A manager starts an argument with some women. The following day three women are not allowed to go to work. They are told: "You have caused Rs 60,000,000 damage to the company, you can't go back". Workers inside stop work till 11am in angry response. On the following day the company bus don't pick up one of the women, whereas the two other women are made to leave the bus on the way to work. For the following four days after the three women were stopped from coming to work workers inside assemble and go to HR every day, on the fifth day they go straight to factory management. Management says: "We won't take them back, if you want, you can go, too". In order to stop women from using their mobile-phones management also installed 'jammers' (electronic signal blocking devices).
11* Asti Electronics Ltd. Dispute, Manesar, 18th of February 2014 - January 2015
*** Company:
Asti Electronics Ltd in Manesar manufactures electronic equipment and cable harnesses for the automobile industry, but also for white goods, circuit boards for mobile phones, control systems for robots etc. in six factories in Japan, two in China, two in Vietnam and one in Manesar, India. Asti supplies, amongst others, Suzuki, Yamaha, Panasonic, Toyota, Kawasaki, Honda, Hitachi, Sanyo, Canon. Production in Manesar started in 2005.
http://www.astiindia.com/
*** Workforce:
Out of the 500 workers employed around 80 per cent are women in their 20s. Roughly 125 are permanent and 350 are hired through contractors. The wages are very low, between Rs 5,500 and 6,000, both of temporary and permanent workers. Most of these young women are migrant workers from Nepal, Arunachal, Assam, Jharkhand, most of them unmarried - some are 'locals' from the hinterland of Haryana. The shift times are random: the B-shift starts at 5pm and finishes at 2am and the C-shift runs from 2am till 8am. Women workers do the most tedious work of cable harness assembling.
*** Chronology:
12th of January 2014:
Some workers file an application for union registration.
25th of January 2014:
Management dismisses two workers whose names appear in the list of union representatives. A temporary worker is sacked some days later for protesting against behaviour of a supervisor. (other sources state that they were sacked two days before the strike).
18th/19th of February 2014:
All workers stop work inside the plant. Work stops from 8am till 3pm, then an agreement is reached: the two will be taken back and they will be paid for the days they were stopped from working.
7th of March 2014:
After February wages are paid the union reps try to collect Rs 500 from each worker. A female office worker protests against this, saying that the dues are too high, but union reps silence her by threatening a strike against her.
17th of May - Company helps with union registration:
Management changes their strategy. Talks with the union body take place and two members of the union body ware taken in the car of the plant manager to Chandigarh to register the union. The registration is confirmed on 17th of May 2014. After the union is registered dues are only collected from permanent workers.
Mid-May 2014 – The union hands demand notice to management:
Shortly after the union is registered a demand notice to management is issued – to which management does not reply.
Second half of May 2014 - Company training for permanent workers:
In May the company employs three trainers to give training to the permanent workers. Every one of the trainers is paid Rs 150,000 for the fifteen days training. They teach: how to improve your lives, how you can proceed; how should the relation between workers and management look like. In the end they say: for you own development you have to be able to use the carrot and the stick - like Chanakya used to say (a Machiavelli-type Brahmin advisor to the rulers 350 BCE). The temporary workers voice their discontent with the fact that the permanents got trained. They say that this is brainwash and to create divisions. The union leader says that this is company policy and that the union could do nothing about it. When the temps ask to get the training themselves they say that it was not available for them.
End of May 2014 - Slow-down strike:
Shortly after the demand letter was given the union orders a slow-down strike. Workers reduce the production of cable-harnesses for the automobile industry by around 40 to 50 per cent. The company hires 150 new workers hired through contractor. These new workers and some old workers are put on 12-hour shifts. People complain that in this way the slow-down won't have any effect - but the union leaders state that it is the right of the company to hire new people.
9th of June 2014 - End of slow-down:
After the end of the slow-down 45 of the newly hired workers are kept, still working 12 hour shifts. The managing director says to people: fulfill the normal production target and within a week, by beginning of June everything will be arranged. The union leader says: stop the slow-down, there will be an agreement soon. The slow-down lasted for ten days. In the meantime management also accumulated a bigger stock of parts by ordering from outside companies, some abroad, some local, e.g. Anu Auto, Bhagvati Auto, Mothersons, Dut Wire. There is stock for four months in the company's warehouse. Workers complain about this, but the union leaders say that it is the company's right to order extra-parts from other factories.
June/July 2014 - No agreement:
There was no agreement in early June. The union leader said that he will announce the agreement on 20th of June. But June passed and in early July there was still no agreement. There is still talk about: we will force them to make the temps permanent or at least the wage will be the same. We will change the odd shift times.
August 2014 - Agreement:
The wages for the permanents will increase by Rs 10,000 over the next three years (Rs 4,700, 2,650, 2,650) - up to that point wages had not been increased by more than Rs 1,500 per year. The wages of the temporary workers will increase by Rs 3,900 (Rs 1,300, 1,300, 1,300) - up to now wage increases were around Rs 500 to 1,000. It also says that every year 35 temps are supposed to be made permanent. After hearing the result the temporary workers are dissatisfied, but not too much so. Unlike at Napino Auto the union leaders do not have to escape in order to save themselves from being beaten up. Management meets in secret and prepares itself.
October 2014 – Rumours that temps will be dismissed:
At the beginning of October rumours spread inside the plant that the temporary workers are going to be dismissed. The temps go to the union body and asked for information. The leaders say that these are false rumours and that before any of the temps would be kicked out the union body would be kicked out first.
31st of October 2014:
During the night-shift on 31st of October: people talk that at some point 310 temps will be kicked out. In the morning a union leader stopped one of the workers and said that all the talk about dismissals are lies and that the union is on their side.
1st of November 2014 – Dismissal of all temps, occupation and end of occupation:
In the morning of the 1st of November the permanent workers get to know that the temps will be kicked out, but they are told: stay alert, don't get involved in their issue, after shift just go home. When words spread to the temps some go to see the union body and some of the outspoken permanent workers. The permanents say that all will be fine, don't get too worked up. When workers come out of the A-shift, management hung up a notice saying that 310 workers hired through contractor will be dismissed "Due to lack of work all temporary workers will be sent into paid holiday for one week and on the eighth day have to report to their contractor to collect final dues". Feeling betrayed a bigger group of temp workers go to finish off the union body, but other temps come to rescue and tell the union representatives to talk to management. They leave, but never return.
A worker gets hold of a written agreement:
"Today, on 1st of November 2014 representatives of the trade union and company made and agreed on the following points:
1. 1. 1. Due to lack of work and lack of orders from clients it has become necessary to end the employment of all temporary work-force. None of the union representatives object this.
2. 2. 2. ... (Signature)
Management refuses to let the B-shift enter the plant. All permanent workers of the A-shift silently leave the factory, while the temporary workers stay inside. At the main production line 180 female and 70 male workers sst down. One hour later the police chief and the contractor arrives. They tell workers that it is a crime to sit next to the machines and that they should shift to the canteen. The workers do not move. Then 25 to 30 police officers with lathis arrive. All workers get up and go to sit down in the canteen. Five temp workers go to speak to management - but no one listens. "It turned 9 pm and we had no future plans and there were many police - we decided to leave the factory." The company prepared busses to bring the women workers to their respective homes.
2nd and 3rd of November 2014 – Meetings with left-fringe groups and labour department:
The kicked out temp workers had links to some (over-active people (of the 'radical left' fringe). "On Sunday, 2nd of November we had debates amongst ourselves, the temp workers. A small group of the fringe left egged us on: 'The unions are made to improve workers' conditions, continue to support the union'. They called the union leaders. They were afraid that they would be beaten. The left group reassured them. When the unionists came the left group made them write a complaint letter to the labour department. When the letter was supposed to be handed over, the labour department gave the straight-forward answer that the company is closed and refused to take it. Only after arguments they took the letter and promised an inquiry.”
On Monday, the 3rd of November the temp-workers see that the company prepared itself: there are 500 to 600 male and female police at the factory. The temps stay home.
4th of November 2014 – Start of protest camp:
All temporary workers assemble at the factory, while all permanent workers under union leadership work inside. Police, bouncers, contractors and company officials move the temps away from the gate. Workers set up a tent in some distance. The company shows a court ruling saying that workers have to stay in 150 metres distance - it is invalid and management obtained it already on the 21st of October. The police push the workers and they go to sit in 150 metres distance. The lawyers ask for Rs 25,000 in order to challenge the ruling. AITUC and CITU leaders come to hold speeches, but workers cut them short.
November 2014 – Actions and waiting for negotiation dates at labour department:
Waiting for dates at the labour department start: 11th of November, 14, 17, 24, ... 1st of December. In the meantime management manages to break some older temp workers and take them inside the factory, while some others take a 'tin hand-shake' and quit the job. Most of the temps though stay put. The company reps start talking about giving workers one month wages as leaving due, the labour department talks about two or three months wages...
On 12th of November the Asti workers and the Munjal Kiriu permanent workers, who have been sitting outside for two months by that time, have a common demonstration in IMT Manesar.
On 18th of November the Asti workers distribute their leaflets at various places and meet various union leaders.
On 19th of November a meeting at the factory takes place and union leaders delivered a lot of speeches. The Asti union leaders don’t take part in this meeting and they state clearly on the 22nd of November that they won't be able to give any support. Another gate meeting on the 28th, again the same spiel. Some students and youth start to come to the factory and stay with the workers, also over night. After demonstrations, leafletting, gate meetings, dates at the labour department things don’t go forward... so workers decided to go on hunger-strike.
25th of November 2014 – Start of hunger strike:
Two male and three female workers go on indeterminate hunger-strike on 25th of November. In support five to ten other people would join them for 24 hours each day. No support from DC in Gurgaon or other political leaders: the president of the BJP women's wing comes to the protestors. She goes inside the factory in order to speak for the temporary workers. When she comes out again she says: "There is not enough work, but I will talk to people in the higher ranks."
December 2014 – End of hunger-strike:
After 16 days the hunger-strike is aborted without there having been any response from management.
23rd of December2014 – Meeting with village councils:
In hope for support the temp workers call village council chiefs from 4 to 5 surrounding villages as mediators. "How can companies in our area dare to kick out so many workers?", they say and go inside. When they come back out they say: "When there is no work, how do you want to give work? Now get up and leave from here, otherwise we will make you move."
Workers: "Three days later some lumpen-elements tore down the tent. Then we went to start a sit-in protest at the ALC department in Gurgaon. After a day the police came and made us move."
The Asti workers have another demonstration with the Munjal Kiriu workers, who have been outside since three months by that point. But HMS leaders tell the Munjal workers that they should not get engaged with the Asti workers, because no one listens to them.
20th of January 2015 – End of the protest camp:
The company increases their final pay offer from Rs 5,000 to 15,000 to 25,000. Workers: “On 20th of January 2015 we decided together that 250 will take the final payment and quit the job. And 22 female and 13 male workers will continue to fight the court case. For the case we have advisors from two left-fringe groups and also a lawyer, who is not good, but who sticks things out.
18th of March 2015:
At a meeting at the labour department a company official says: "Come to an agreement and take Rs 40,000 final dues. If you don't take that offer the case will drag on for years...". Workers: “Let it go on...”
12* Baxter Dispute, Manesar, 19th February 2014 – August 2014
*** Company:
Baxter India Ltd. in Manesar manufactures medical and pharmaceutical products. Baxter has approximately 49,700 employees worldwide, has production units in 27 countries, three of them in India. The factory in Manesar was opened in 2002.
http://www.baxter.in/
*** Work-Force:
At the time of the dispute there were 300 permanent workers inside the factory, plus 100 trainees, 150 staff and workers hired through contractor, initially only for loading work. Around 70 per cent of the workers are female. When the factory opened management hired people from polytechnic colleges, promised them Rs 10,000, paid that wage for a month and then said that the company policy had changed and reduced wage to Rs 5,000. They have installed a creche, but just for show. If workers object to arbitrary management behavior, such as refusing toilet breaks, they are shifted to other departments or refused day off for 14 days.
*** Chronology:
November 2012 - Collective pay hike demand:
All workers go together to the HR department and demand a pay increase. The boss says that people should come individually. When in the following days people go individually they receive threats and the pay demand is forgotten.
10th of May 2013 - Permanent workers demand pay hike:
All permanent workers and trainees go to management and raise the pay increase issue again, but management refuses.
15th of May 2013 - Slow-down strike:
Workers agree amongst themselves to start a slow-down, working 30 to 40 per cent of the usual production. After a debate in the works committee management says that they would increase the pay by Rs 2,717 in return for a productivity bonus, an attendance bonus, in case accidents were low and product rejections would decrease. They also say that they would pay over-time and give biscuits for tea. Although management does not really grant a wage increase workers decide to end the slow-down. The company implement their proposal from 1st of June 2013, but they do not pay Rs 2,717, but Rs 1,700 to 1,800. At that point there are no leaders involved in the dispute.
May to September 2013 – Union registration in process:
Around 45 permanent workers start meeting and collecting union dues, later on they start collecting money from all workers.
24th of September 2013 – Workers are transferred and dismissed:
Under the pretext of having given falsified documents to management two workers are dismissed on the 24th of September and on 25th of September management starts transfering certain workers to other factories of the company, as far as Maharashtra. Abuses towards women workers increase inside the factory, so do threats against male workers. Management also starts to hire workers through contractor for the immediate production process.
15th of October 2013 – Demand notice and delayed negotiations:
Workers talk about doing something, but the leader of the union tells them to be patient. When the number of transfers reached 23 on 15th of October, the union files a complaint at the labour department.
On 17th of October the union hands in their demand notice with 56 demands. From then on the two issues are negotiated during dates after dates at the labour department. After 20 meetings still no solution. The union is still not officially registered. By January 2014 44 workers have been transferred and 12 are dismissed. Workers decide to break out of the hamster-wheel of court dates and to do something.
18th of February 2014 – 24-hour occupation by male and female workers:
Workers receive the news that the negotiation at the DLC about the fate of the transferred and suspended work-mates has been postponed to the 22nd of April. At the same time they hear about the strike at Asti Electronics nearby. The A-shift does not leave the factory and the B-shift does not start to work. 140 male and 110 female workers sit down inside - the C-shift workers gather outside. The company calls the police and officials from the labour department. Two vans with female and four vans with male police officers arrive. Inside and outside of the plant there is police over police. Police and management ask workers to send a representative outside for talks, but workers refuse. Management leave the factory, the police stay. The 250 work-mates stay inside. The workers inside do not engage in a hunger strike, but they say that they would not touch company food, only food from friends outside. Management does not let any food be delivered inside, the same the following morning. The company has provided thin mattresses for the female police and chairs for the male police. Female and male workers lay down on the floor. Male and female workers workers stay inside for the night of the 18th and only leave on the 19th at 10:30 pm.
19th of February 2014 – Leaving the plant:
On the 19th of February union leaders start to give speeches at the gate. A situation arises which could have create major disturbances in the wider industrial area. But things are not pushed forward. At the 2pm meeting with the assistant labour official some of the leaders are present. Some back-and-forth and reassurances, then at 10:30pm workers are called out of the factory. Leaders say that 15 of the transferred workers would be taken back within 15 days, plus they would get some wage compensation. When people demand that everyone should be called to a meeting and hear about the agreement the leaders refuse.
20th to 28th of February – Work resumes, but no production
On 20th of February regular duty starts again - though there is no production. Management say that till 28th of February there would be only cleaning operations and training.
End of April 2014 – Management starts to provoke
By end of April 2014 it seems that management feels more self-assured again. They provoke workers with 'training and exams', they make the workers hired through contractor work sometimes 8 hours, sometimes 12 to 16 hours and threaten those who refuse over-time with dismissal. They open lockers of workers to confiscate biscuits, which members of management had left behind after tea break. The 56 demand-letter is still with the labour department and the dates for negotiation meetings were continuously postponed.
21st of May 2014 – Show-down after worker is kicked out
An outspoken worker is kicked out of the factory by security guards and receives injuries. Workers complain about it to the police and assemble inside the factory. The company put red tape around the machines, which is supposed to stop workers from using them. The police arrive. The workers say that they are willing to work. Management respond saying that they won't run the plant. Management decides not to send the buses for the B-shift. People who arrive to work on foot were not let inside. When the A-shift workers refuse to leave at 2pm the official from the labour department arrived. An agreement is reached at 8pm... The outspoken worker will remain suspended, an inquiry will be started, the factory will shut for cleaning process, the workers will be sent into paid holiday and management will inform them once production starts again.
26th of May 2014 – Suspension notice
Workers receive a text telling them to come to work on the following day. When the A-shift arrives they find a notice saying that 17 female and male workers are suspended for 'serious reasons' and that a proper 'accusation letter' will be issued shortly. Workers tell management that the 17 would remain outside, but that they will go in, but management refused to let them enter. An inspector from the labour department arrives. Workers tell him that they are willing to sign 'conditions' put forward by management to go in. Management say that they will present a letter with conditions to resume work at the meeting on the 28th, a meeting which was originally set up to negotiate the 56 demand notice of the union.
27th of May 2014 – Union meeting and announcement of registration
A meeting of 200 union members and leaders takes place. Big union leaders promise big steps and great news. The news was that the union had received its registration number.
28th of May 2014 – Protest at the labour department
300 male and female permanent Baxter workers are at a protest sit-in in front of the labour department, while the general shift starts production inside the factory. 150 workers hired through contractor and 60-70 staff are at work. New workers have been put up in guest houses in Gurgaon and are driven from there to the factory, through the back-gate. Police is around. 30 to 40 workers in the dispatch and unloading department stay inside the factory 24 hours, management provides for them. It becomes clear that the company had prepared itself for this attack.
June and July 2014 – Workers remain outside
There is not much support for the Baxter workers. The union leaders blame the production stop at Maruti and Honda (due to annual maintenance) for it, because not much work is happening in the entire belt of auxiliary companies. A union meeting is called for 3rd of July. No steps are undertaken. Again, big things are announced for July, but on 3rd of August workers are still sitting outside.
13* Bajaj Motors Dispute, near Manesar, 24th of February 2014
*** Company:
The Bajaj Motors factory is located on the Delhi - Jaipur highway NH-8 in Narsinghpur, close to Manesar. Workers manufacture engine parts for the automobile industry, around 65 per cent of production is for Hero two-wheelers (the Hero factory is located 15 km down the highway by in Dharuhera). Bajaj Motors also produces parts for Harley Davidson and BMW. Some parts are exported to car plants in Turkey and France. The factory was opened in 1992. The Bajaj Motors Group has 8 - 10 other factories in the region.
http://www.bajajmotors.com/
*** Work-Force:
There are 300 permanent workers and 1,500 workers hired through 8 - 9 different contractors; plus 300 middle-management.
*** Prelude:
To attract workers hired through contractor Bajaj paid them the statutory double-rate for over-time, which is very rare; nevertheless workers didn't stay long, the hiring process was continuous. The production targets were very high and had to be fulfilled, come what may. There was over-time even on Sundays. Workers worked 70 to 200 hours over-time per month (which is illegal). They were employed at CNC or VMC machines, but graded and paid as 'helpers'. The workers hired through contractor were not kicked out and re-hired after six months (to avoid having to make them permanent, as per law), but they had to sign a resignation letter, which the company kept in case of future claims. Four - five years ago the unrest amongst workers grew and the company saw it as a relief when the permanent workers registered a union and affiliated to one of the big trade union federations. During the Maruti Manesar struggles management became very nervous and they issued a disciplinary notice to one of the outspoken workers - an inquiry process against him followed, which took till March 2013. In 2011 and 2012 it became obvious that the relationships between permanent and temporary workers deepened.
*** Chronology:
2012 to February 2014 - Simmering dispute after dismissal of worker:
In 2012 a security guard mistreated one of the temporary workers and the permanent workers had a go at the guard. The following day management sent for the police, the police arrested one of the outspoken permanent workers on the shop-floor. In reaction both permanents and temp-workers stopped production. Management started a quarrel with some of the permanent workers and used it as a pretext to suspend five of them. This time the company did not engage in an inquiry process, but negotiations started with regional and national union leaders. There were a lot of speeches, saying "Keep patient, keep calm". After that negotiations with regional and local leaders followed. By that time the previous 2011 inquiry declared that the worker was guilty. They sacked the worker without any written reason or dismissal paper. Seeing workers' anger the union leaders said that they will talk to the managing director about it and gave assurances about the progress of negotiations (later on it turned out that these were lies). While workers kept hoping that the negotiations between management and leaders would be fruitful the company prepared itself in the meantime. They filled the plant with extra-stock of parts. Once workers realised that without pressure things would not move forward, it was to late.
24th of February 2014 - A prepared attack leads to workers being kicked out:
On 21st of February management complaint at the labour department about workers engaging in a slow-down, though they themselves were prepared. On 24th of February, when workers arrived for the A-shift they found a notice saying that 15 permanent workers had been suspended and a request that all other workers should fill in a 'good conduct form'. They also found 200 police in and outside the factory. 300 permanent and 1,500 temporary workers refused to go inside the factory. On the day before the company had run two 12 hours shift over-time on Sunday. On the 24th of February 50 trainees, 15 permanent workers, 300 workers hired through contractor and 300 staff were inside the factory. The company had food, alcohol, TV, soap, tooth-paste stocked for them. The factory ran 24 hours. The workers inside suffered, but management did not allow them to leave their workplace. Police and musclemen were around the plant 24 hours. The Bajaj managing director was at the time also president of Gurgaon's Industries Association. The union complained about the situation at the labour department. Since then there have been various negotiations, without results. On 5th of March leaders of 38 unions in Gurgaon held speeches in front of the gate and started a hunger-strike on the 14th. Since then negotiation dates and meetings are drawn out... One, two months went on like this... having got tired the permanent workers accepted the conditions set by the company in an agreement on the 30th of April.
14* Track Components Dispute, Manesar, April 2014
*** Company:
Track Components in Manesar manufactures sheet-metal parts for Maruti Suzuki, Honda and BMW. It must be a fairly 'informal' company, as they don't have a company web-page.
*** Work-Force:
Around 1,000 workers, most of them temporary.
*** Chronology:
January 2014 - Management promises some permanent jobs:
In January 2014 the manager said that an information has arrived from head-office that 152 workers should be made permanent. The did not show that list and kept silent about it afterwards.
17th of February 2014 - Spontaneous strike after accident in press-shop:
On 17th of February a worker was seriously injured after a machine accident. The company tried to forge the accident report by entering an earlier dismissal time and declaring that the accident had happened on his way home. All workers in the press-shop stopped working on the 19th of February and demanded compensation and a permanent job for the worker. After one and a half hours the HR boss came and said that the company also hired supervisors and engineers through contractors, so how can they give a simple worker a permanent job?
End of May 2014 - Attempt of union registration:
Eight permanent workers joined HMS. They went to those temps who had been in the factory for eight to ten years and collected 187 signatures off them between 28th and 30th of May. On 6th of June 2014 the letter with the registration application was sent to Chandigarh. After the letter was sent of the temp workers had meetings amongst themselves. They met twice and collected another 500 to 600 signatures from temps who had been in the company for two to four years.
17th of April and 12th of May 2014 - Collective wildcat strikes for bonus payments
The company did not pay the statutory inflation compensations announced in January and July 2013, neither the one announced in January 2014. The workers talked amongst themselves and on 17th of April workers of all three floors assembled and stopped work. After one and a half hours the HR said that they will pay the statutory payments and that they will also pay the statutory double-rate for overtime - workers are on two 12-hour shifts. On 12th of May when workers saw that the April wages did not contain the increment, they stopped work again on all floors. The production manager asked the workers to go back, he would talk with everyone, from HR to managing director about the issue. Workers went back to work - and kept waiting.
1st of July 2014 - Over-time strike, management reacts with new shift system and slight increase in bonus payments
They agreed that if overtime payment was not increased by 30th of June they would stop working overtime from 1st of July onwards. On the 1st of July all workers left the factory after eight hours. Till 10th of July the company officials didn't say a word. On 11th of July management put up a notice. Despite management's refusal to pay and their threats workers continued to work only 8 hours. From 13th of July they started operating a three 8-hour shift-system and together with the repression also increased the bonus by Rs 300 to Rs 1,500. In May the permanent workers had been stopped at the gate and refused entry. When they went to the labour department the company provided documents saying that they had been transferred to the company's factory in Bangalore. They kept on sitting in front of the gate. During the following month also some temps were stopped and they joined the sit-in of the 7-8 permanents at the gate. Since June around 50 workers...
July 2014 - Second attempt of union registration:
The few permanent workers sent a second file for union registration in July 2014. The company got to know about this. The company had given Rs 500,000 bribe to officials in Chandigarh and got hold of the list with the 187 signatures. They called them in individually or in pairs and threatened them. Management called the eight permanent workers who were official representatives and both threatened and lured them, offering between Rs 3 and 5 million. The company did not let these eight workers go to work between 15th of July and end of October 2014. During the time the permanents were not at work some temporary workers had four meetings in the hills of Manesar. There were about 600 to 700 workers. HMS leaders from Gurgaon delivered speeches: keep the unity! you all will be made permanent! the wages will be good; everything will be fine. In July and August 2014 union dues were collected. The 25 to 30 old helpers gave Rs 1,000 each, the 400 operators Rs 2,000 and the 200 foremen also Rs 2,000 each. After the eight permanents returned to work there was silence from the union...
15* Subros Dispute, Manesar, May 2014
*** Company:
Subros Auto in Manesar manufactures air-conditioning systems for Maruti Suzuki. The company runs six plants in India, with a total annual capacity of 1.5 million AC systems.
http://www.subros.com/
*** Work-Force:
There were 300 permanents, 500 temporary, 300 to 400 trainees and 300 engineers employed till April 2014, less after that date.
*** Prelude:
Secretly Rs 4,000 were collected from each permanent worker to register a union. The president took 15 days off (saying that his wife was ill) and went to Chandigarh. End of 2013 an AITUC union was established at Subros.
In March 2014 the union said that they would increase the wages for everyone and called people to a meeting in Gurgaon. Company buses brought people to a central park. Leaders gave speeches, workers clapped. The union decreased production, instead of increasing it. Where people used to produce 1,100 air-conditioning modules in April 2014 they only finished 850. At the beginning of May 2014 they started to take Rs 100 for union membership from trainees and from old temporary workers with ITI qualification.
*** Chronology:
14th of May 2014 - Company does not send buses, workers remain outside:
Suddenly, on Sunday 14th of May 2014 the company buses did not arrive to pick up workers for their shift. 250 workers who live near the factory walked there and arrived at 7 am. The company buses brought in workers from the Subros factory in NOIDA, around 60 kilometres away. All IMT Manesar workers remained outside. The union president went inside and came back at 9 pm. All workers were waiting for him. The company had put up a notice saying that for 27 old temps with ITI and trainees the gate of the factory will remain closed. The union president said that he will make the company take them back and he himself will stay outside for 45 days. Don't give any signatures on blank pieces of paper. Whatever we have to do, we will do after 45 days. On 15th of May 2014 the buses arrived on time. The production had been increased, now 1,200 AC components were manufactured.
28th of May to end of June 2014 - 400 temp workers dismissed in small groups, while the union president has disappeared:
Then again, on 28th of May after the A-shift 37 temp workers' company-ID-cards were taken. From then on every day this happened to another 30 to 40 workers. Within one month 400 workers who had been in the plant the last three, four years had been kicked out. The workers tried to meet the union president, but could not find him. His phone was switched off. On 25th of May there had been rumours that the union president had disappeared after having taken Rs 6,000,000. Also the four other union leaders close to the president had not been seen since 15th of May. No AITUC leader had approached the factory since the dismissals started. The union president was from Aliyar village in IMT Manesar. His family members said that he had sold everything and left.
Within six to seven months Subros had also kicked out 300 permanent workers. The factory had been opened in 2007, but now no old workers works here anymore. Now most workers are 'under training'. They are hired from technical colleges in Jharkhand, Bihar, Uttar Pradesh, Rajasthan - as trainees. Even the engineers are hired as trainees. 400 workers through contractor are employed as helpers, they get Rs 6760. Those with ITI qualification get Rs 7,200. The engineer trainees (around 70 of them) get Rs 11 to 12,000. The work pressure is enormous, the managers shout at people...
August 2014 - Collective wildcat action to get proper wages paid
In August 2014 management cut two supervisors' wages by Rs 8,000, because a die-casting part had been faulty. When they cut Rs 3,000 from workers operating a pressure die-casting machine they refused to take the money and workers in the department stopped all nine machines. After the machines had been idle for an hour the HR head himself handed out the proper wages without the reduction. Workers started working again. Nearly all workers are temporary, in total 150.
16* Autoliv Dispute, IMT Manesar, June 2014
*** Company:
Autoliv in Manesar manufactures parts for Maruti Suzuki and Mahindra Bolero. Autoliv employs 60,000 workers in 80 plants in 28 countries, one third of sales in each of the three regions Europe, Americas and Asia including Japan. They manufacture seat-belts, steering-wheels, airbags and other safety-equipment for all major car companies.
http://www.autoliv.com/Pages/default.aspx
*** Work-Force:
In Manesar there are 54 permanent workers, 12 trainees and 130 workers hired through three different contractors.
*** Chronology:
1st of June 2014 - Management runs factory with new workers while old workers are on day off:
On Sunday, 1st of June, the weekly day off for the old workers, the factory was running with the recently hired work-force. When the old workers arrived on Monday they found a notice saying that they are supposed to take two days holiday. Inside the factory production was running.
4th of June 2014 - Dismissal of 17 workers and demand to sign 'good conduct'-undertaking
On the 4th of June workers found a notice that 17 permanent workers were dismissed, that all the other permanents have to sign a 'good conduct undertaking', while the old workers hired through contractor were sent on another week holiday. In addition to the notice there were two police buses, one jeep and ten bouncers stationed at the factory. Workers issued a complain at the labour department through the union. Waiting for dates with the officials. A demonstration was called for the 18th of June in Gurgaon and a notice was given to the DC. Apart from meetings at the labour department management had arranged three meetings with five representatives at a local hotel.
1st of July 28th of July 2014 - Workers stay outside, while production runs inside:
On 1st of July a handful of union leaders held speeches at a gate meeting at the factory. On 2nd of July the union gave another notice to the labour department. On 3rd of July the company gave a 72-hour ultimatum to 27 permanent workers to come to take up work again. The process of hiring new people throughout June was stopped from 1st of July. Up to the 10th of June there were a lot of rejections of parts. Six skilled female workers from the Autoliv factory in France were brought over to Manesar. Skilled workers from another local company also came over to train the new workers. They got the quality/rejection problems under control. Most of the 40 workers who had been transferred from Bangalore were slowly sent back after the 15th of June, only two of the remained. Maruti Manesar management has agreed to keep 20 of their workers available for helping out at Autoliv.
29th of July 2014 - Union negotiates resignation of workers
On 29th of July the union secretly moved 54 workers to sign their resignation letters. When the 130 workers hired through contractor refused to move from the gate management offered to pay each of them Rs 10,000 as leaving dues.
17* Wearwell Dispute, Okhla, September 2014
*** Company:
Wearwell is a garment manufacturer, all garments are for export - the company used to supply M&S. The dispute concerned two factories in Okhla.
http://www.indiamart.com/wwi-pvtltd/
*** Work-Force:
In factory 1 there are 380 tailors. In factory 2 there are 225 tailors, 70 finishing workers and 40 female workers who cut threads.
*** Chronology:
1st of September to 5th of September 2014 - Wildcat strike in both Wearwell factories in Okhla:
In both of the company's factories in Okhla Wearwell garment workers stopped work between 1st of September and 5th of September 2014. Wear Well factory manager Nishchal Kumar says the company suffered a loss of Rs 11 lakh. The year before there had been a dispute about the yearly bonus payments, workers had refused the low bonus payments and stopped work in only one of the factories. Management then tried to trick workers by transferring their bonus payments straight into people's bank accounts - undermining the collective refusal to accept the payment. Therefore this year workers of both factories addressed managers directly before the bonus payments. Management said that they would need one week time, but there was still no reply after three weeks. The workers then stopped production on 1st of September and sat down inside the two factories. The managing director came and said that the bonus will be Rs 5,280 (the usual monthly payment), but machines kept on standing still. Workers stayed inside, although drinking water was cut on 2nd of September. On 5th of September the managing director came again and said that he would pay Rs 1,000 more. Then workers in both factories started working again. Ten days later the company tried to kick out ten workers using CCTV pictures as excuse, but facing workers' anger they withdrew their attack.
18* Orient Electric Dispute, Faridabad, 20th of October 2014
*** Company:
Manufacturer of fans, home appliances and light bulbs with factories in Faridabad and Kolkata. Part of the BC Birla Group. The factory in Faridabad manufactures around 8 to 9 million fans per year and also light bulbs.
http://www.orientelectric.com/about/about-orient.aspx
*** Work-Force:
In the fan plant there are 1,163 workers, out of which 52 are permanent. The permanents get a basic wage of Rs 13 to 14,000, plus housing allowance Rs 2,150 plus Rs 500 cycle allowance plus Rs 50 for soap. They also get Rs 17 for each working day for tea and a growth incentive of Rs 400 to 500 each day. This amounts to a monthly wage of Rs 28 to 30,000 per month. When the factory manufactured 1.1 million fans they made a 20 per cent bonus agreement. The bonus payment is still the same, although they now produce 8 to 9 million. The annual bonus is Rs 8,400. The canteen only provides food for the permanents. The factory runs 24 hours, but the permanents don't work nights. The wage for the temporary workers is Rs 5,640, they don't get allowances, incentives or bonus, neither food. Because the temporary workers started to become a bit agitated the company then paid them double-rate for overtime (as it is statutory according to the law).
*** Chronology:
20th of October 2014 - Wildcat sit-in outside the plant by 350 temp-workers:
On 20th of October after the 11am tea-break the 350 workers hired through contractor did not start work, but sat down in a nearby park. The three assembly lines for rotor-fans stood still. The 15 to 20 permanent workers sat down at the lines. The 10 to 12 company officials came to the park. Why did you stop work? - We want to be paid the bonus, too. - You have not raised this issue the last ten years. - But we do it now. - The general manager has gone to a meeting in Gurgaon, I am new here, I don't know about the issue, please go back to work and we talk about it this evening. - None of the workers got up. In the meantime 20 cleaning workers from the factory had joined the others outside. The bosses gave the reassurances and moved them to get up. Workers of the nearby CFL (light-bulbs manufactured by Orient Electric) factory started to assemble at their gate and checked out what was happening in the park - and the idea arose to go and meet up with them. But an older worker seemed to have accepted the bosses pleas, got up and walked back to the factory - bit by bit other workers followed him. During the food-break some of the cleaning workers had an argument with the new boss and at 1pm all of them walked out again. The dirt and rubbish had started to pile up around the assembly lines, when at 4:30pm they came back in. A young worker's thought about all of this: It is difficult to stop work at the assembly-line, because the bosses can single out those at the beginning of the line and put pressure on them: "You, start work. We will see who will stop the work next!" It seems better to assemble somewhere away from the lines - the boss will not be able to single people out.
November 2014 - Management offers attendance incentive
The November passed without bonus payment. The problem for management is that the temporary workers come to work or stay away from work as they are pleased. Absence is a huge problem for the company. The new production manager called all temporary workers in the fan plant to a meeting on 29th of November. In order to stop people from taking days off they will pay an attendance incentive of Rs 700 per month (plus Rs 300 for those who work only nights). When workers started to raise other issue in the meeting the manager quickly left the place. Another thing is that due to too many rejections and quality problems management has put additional people at the lines, so that now two workers do the work of one worker.
19* Premium Moulding Dispute , Gurgaon, October 2014 – June 2015
*** Company:
Premium Moulding manufactures steering-wheels and other parts for the automobile industry, in Gurgaon mainly for Maruti Suzuki, but also for Hyundai, Ford. The company has factories in Gurgaon, Baddi, Dharuhera, Chennai
*** Work-Force:
185 permanent workers in Gurgaon, many of them have been shifted from the Delhi factory when it closed in the early 2000s. Around 50 temporary workers. Workers used to work on two 12-hour shifts, over-time is paid Rs 6 per hour for helpers, Rs 8 for operators. The over-time has been cut seven months ago (December 2014), now workers are on two 8-hour shifts.
*** Prelude:
In 2013 workers still received Rs 8,400 Diwali bonus plus presents, in 2014 only Rs 2,000.
Initially management said that due to a slump they won't pay the Diwali bonus. After Diwali on 28th of October workers stopped work in the morning. By 3pm management had paid the bonus and work started again. When the company tried to take four molding machines from the Gurgaon factory to Dharuhera in January 2015 the workers objected. The ten workers who worked on these machines were then sent on holiday, when they came back, no work was given to them…
*** Chronology:
March 2015 - New HR manager threatens workers to shift them to Dharuhera plant:
The new HR says that workers will have to move and transfer on their own costs. Workers engage a lawyer in order to oppose the transferral of machines and the threat of being kicked out. The lawyers says that he has received a ‘stay order’ for the machines from the court.
April-May 2015 - The company kicks out 50 workers:
Without stating proper reasons the company kicks out 50 workers who had worked at the plant for 8 or more years.
6th of June – The company orders workers to take holiday:
management tells workers that due to plant closure for annual maintenance at Maruti from 7th of June to 14th of June the Premium Moulding factory will remain closed on 8th and 9th of June. This never happened before. Workers are alert.
7th of June – Bouncers, police and management arrives at factory:
At 10pm eight cars full of bouncers, plus the chief of the local police station arrive at the plant together with management representatives. Around 35 workers who live nearby also come to the plant. The workers oppose the bouncers in their attempt to take the machines and they tell the police officers that they have a stay order from the court. The police does not accept the document and tells workers to leave.
8th of June – Workers meet police commissioner:
The workers meet the police commissioner but he also refuses to accept the stay order from the court. Under protection from the police and bouncers management continues shifting machines to Dharuhera: The lawyer’s stay order only concerned the dismissal of workers, not the removal of machinery. Management took all necessary machines and the lawyer only then applied for a stay order to keep the remaining machines, which workers called ‘scrap-metal’.
10th of June – Workers arrive at factory, but are sent back
When workers arrive at the plant after their ‘holiday’, they are told to go back home and come back later.
14th of June – A transfer notice to Tamil Nadu
When workers arrive at the gate they find a notice of management sating that workers will be shifted to the Tamil Nadu plant. Both permanent and temporary workers remain outside the factory. The deputy labour commissioner accuses workers in a letter to ‘engage in a strike’, while the court issues an order that workers have to stay in 25 metres distance from the factory gate.
June – 2015 – Workers unpaid and trapped?
In order to increase the pressure the company does not pay workers’ May wages. After a complaint at the labour department the company promises to pay on 22nd of June, then 26th of June, then they say that they will cut 8 days from the wages ‘due to strike’, then say that they will pay on 1st of July. Permanent workers demand that the temporary workers should be paid first – they receive a cheque on 2nd of July… Workers also contact a union, but many other examples show (Eastern Medikit, Bajaj Motors, Baxter etc.) that the drawn-out legal process will end up weaken workers and make them accept managements conditions. Workers start to address other workers in the industrial area by holding self-made placards at main roads…
Comments
Interesting & informative
Interesting & informative article.
article
On the topic of unions and regime change;
Quote: "which means that
, this probably means, in cricket terms (which Indians use a lot), when workers were in defensive situation or when workers had no control over situation. I am not sure if it fits the description but what happens in India is like many other countries media pays zero attention to workers actions. And when some violence occurs they start blaming the workers - how they are all uneducated and stupid, they don't know how to live and so on and also advocating the official line, of the factory owners. All of this usually without giving any context.
A very long article of which
A very long article of which I have only scratched the surface. One point I did pick up was the disparity between Unionised labor and day laborers, an issue on which the onus lies on Unionised workers to address.
Debate continues between
Debate continues between comrades in India
https://viewpointmag.com/2017/01/23/autonomy-in-india-tactical-and-strategic-considerations-on-the-new-wave-of-workers-struggles/
Reply to Viewpoint Mag article by comrade close to Faridabad Majdoor Samachar / Kamunist Kranti
A response to ‘Autonomy in India: Tactical and Strategic Considerations in the New Wave of Workers’ Struggles’
I help a few friends in publishing and distributing every month a newspaper – Faridabad Majdoor Samachar – in the Delhi-NCR area, in which we try to present to workers an image of their own activities which we think are of transformative possibilities. We also keep these activities of workers at the center of our discussions by consistently trying to interpret their implications anew. What we see the workers doing, and what we hear of from other places today, gives the impression that a great churning is taking place which we dare not try to fit into existing moulds bequeathed by past experience without a thorough look.
It is in this context that I place this response to the article that appeared on 23rd January, 2017 on your magazine. The major criticism against it would be that, apart from the many erroneous commissions and ommissions, it presents workers as a “fragmented”, hapless lot, and by trying to place them in bygone frameworks, completely misses their present radical potential. This essay will point out how, in their characterization of workers today, the authors of ‘Autonomy in India’ place the irrelevant in their spotlight, exceptionalize the normal, and thus manage to get away with presenting an image of workers which is, even by the examples it invokes, less representative of their activities.
Making the irrelevant relevant
1.“State’s machinery to protect the rights of unorganized workers”
The authors inform us that “the state is now trying to find ways to normalize the figure of the unorganized worker through social measures, while allowing – and in fact facilitating – the uncertain conditions of work in the wake of globalization.” Whatever the “normalization” of 80%-90% of the workforce means, we find that this age-old distinction between “organized-unorganized” workers is coming into question in churnings in the factory mode today, along with making laws, legal redress, labour commissions, etc. increasingly irrelevant. This is amply evident when we consider even the cases of “organized” workers today, as at Munjal Kiriyu (Sec-4, IMT Manesar),
“.. A union was established in the Munjal Kiriyu factory at the beginning of 2013. As per law, only the permanents took membership of the same. In present conditions, actual workers' organization is made possible by the inter-mixing between permanents, trainees, apprentices and temps. On 26.11.13, the union signed an three-year agreement with the management that sought to weaken and break this actual workers' organization. But the bonds between permanents, trainees and temps proved resilient, and even before a month was over since the legal agreement was signed, all workers stopped production on 18.11.13 in favor of three trainees (?). After production was stalled for 25 days, the union and the management made an agreement with elusive traps involving provisions for dismissal and discharge..... The real face of the “victory” of the union-management agreement of 15.1.14 after 25 days of stalling production was revealed to the permanents later in April that year. Permanents broke ties for the first time from a big union in May to join hands with another big union. At that time, the company straight away attacked the permanents, whose collective strength was already depleted by weakening of their ties with the temps due to management-union interventions. 195 permanents were removed from the factory on 24.9.14, as 400 temps, 100 diploma trainees, and 43 permanents continued production within. The debarred permanent workers then, on 25th September, returned to take shelter under the roof of the former big union. A month, two months, three months passed since the 195 workers debarred from the factory were sitting outside it. Hearings-after-hearings took place at the Labour Department. Initially, big unions were very active, but then grew lax, and finally became completely distant from the workers. Apart from removing them from work, the company put a few more outside the factory. Workers sitting-in at the factory gates since 25th September accepted the management's conditions on 15.1.15 when they saw that resistance wasn't bearing fruit. Leaving the 9 who were terminated, and 20 who were suspended, the rest of the workers returned inside the factory. Reports about Munjal Kiriyu workers will be found in the 2014 September, October, November and January 2015 newspapers of Majdoor Samachar...” (FMS, Feb 2015)
Or, if we look at the more recent case of the Honda (Tapukara) factory,
“.. On 16th February, in order to stem the upsurge of temporary and permanent workers, the workers were evicted from the factory by means of police action. Following that, a huge number of new temporary workers were recruited, and the factory was kept operational through them and a few permanent workers. Meanwhile, the workers evicted from the factory were made to run around Gurgaon, Jaipur, Alwar by middlepersons for obtaining relief.
On 6th June, there was a settlement between the Honda management and unions in the presence of the Labour Commissioner of Rajasthan government. Out of more than 4000 workers evicted from the factory, 256 permanent workers were to go back to work at the factory starting 8 June. As for the rest, it was decided to have talks on 13 June at the Labour Department.
The union thanked the Honda management and Labour Department of Rajasthan Government in press releases. On 8 June, the permanent workers went into the factory to work in accordance with the settlement.
And then, come 13th June, the Honda management never showed up for the talks scheduled at the Labour department. The company bluntly said that it would not recall even a single worker of the thousands of temporary workers evicted from the factory. 102 permanent workers of Honda Tapukara have been dismissed and 47 have been suspended.
With the Honda management “going back on its words”, the union has once more started a series of protest-demonstration-appeals since 20th June.” (FMS, July 2016)
And from recent events at the Bellsonica factory in Sec-8, IMT Manesar,
“The union has kept saying : workers will benefit from peacefully keeping up regular production at the factory, abiding by the Labour department and the Courts. Far from the workers gaining anything through these proceedings going on since one and a half years, the company has instead fired many permanents, trainees and workers hired through contractor companies.” (FMS, July 2016)
These are only a few cases among many – Bridgestone IMT Manesar (Hindi report in FMS, Nov 2015), Napino Auto IMT Manesar (Hindi report in FMS, May 2016), Omax Auto IMT Manesar (Hindi report in FMS, May 2016), and so on – in which: first, the “organized- unorganized” distiction proves unhelpful and a hindrance in workers’ activities vis a vis managements and work, and second, “organized” workers bear witness to the breakdown of the “state machinery” that is supposed to “ensure their rights,” to say nothing about the vast majority of cases in which “unorganized” workers are testament to this breakdown. We observe, rather, that laws, legal redress, the rights-framework have become irrelevant for workers, and any mediating that channelizes workers’ activities through these means is all the more harmful for workers’ expressions of agency. In contradistinction to this, consider the possibilities thrown out of workers organizing themselves beyond this statized “organized- unorganized” distinction, as seen in Maruti Suzuki, for example,
“.. In 2011, in the factory in Manesar, there were 950 permanent workers, 500 trainees, 200 apprentices, 1200 workers hired through contractors for work in the direct production process, and around 1500 workers hired through contractors for various auxiliary functions. The pace of work was such that a car was being assembled in 45 seconds. Some permanent workers attempted to organise another union against the existing union. Strong arm tactics of the management to make permanent workers (most of whom were not even aware of the attempt at another union formation) accept the existing union gave rise to a surcharged atmosphere. All around discontent coalesced into a sudden stoppage of work. On 4 June 2011 when A and B shift workers were together in the factory, they took over the entry and exit points. Most workers in factories today in the subcontinent are temporary workers — the percentage of permanent workers varies from 0 to 5 to 25% of the work force. On 4 June permanent workers, trainees, apprentices, and workers hired through contractors came together, and in this way a workers’ organisation appropriate in the current conditions took shape, transcending the legal framework wherein only permanent workers can be members of the factory trade union. What started on 4 June and continued for 13 days should be termed a ‘deoccupation’ of the factory. Around 3000 workers stayed in an atmosphere of freedom inside the factory premises during those days.
The company and the government were taken aback. During the deoccupation many more bonds developed between the various categories of workers. The company was forced to take a step backwards and revoke the termination of 11 workers, for production to restart.
There was a dramatic change in the atmosphere in the factory. The bonds between workers continued to grow and management officials were increasingly on the defensive. The company was forced to plan and prepare to re-establish its control. It went to far away industrial training institutes and secretly recruited hundreds of young boys. On 28 August, a weekly day off, 400 police men came at night to the factory. Company staff had arrived earlier. With metal sheets, the factory was secured in military fashion. On the 29th morning when workers arrived for their 7 am shift, there were notices announcing dismissals and suspensions, and entry premised on signing of good conduct bonds for permanent workers.
All the workers, both permanent and temporary, stayed out of the factory. Inside the factory were the new hires and workers brought from the company’s Gurgaon factory, with a few permanent workers from Manesar plant itself. Arrangements for their stay inside the factory
had been made. Managerial and supervisory staff members also had to work in the production process with the workers in 12 hour shifts. This was a well rehearsed chess game of managements to soften workers and impose major conditions.
Repeated attempts were made to instigate workers to violence. The workers refused to be instigated, even when some of them were called by the state government for negotiations and were arrested there. 3000 plus workers self-organised themselves in two 12 hour shifts outside the factory. At any time, there were more than 1500 workers spread out near the workers’ entry gate. This continued for the whole of September 2011. Many kinds of discussions took place. Bonding between different categories of workers acquired new dimensions.” (For the entire report ‘An Account of Factory Workers Today”, see http://faridabadmajdoorsamachar.blogspot.in/2014/11/an-account-of-factory-workers.html)
Workers’ activities run opposite to the discourse on dwindling rights; rather, we note that the weakness of workers lies not in “precariousness” due to ineffective labour regimes, but rather in holding their activities hostage to those labour regimes. We need only recall the mass upsurge among workers in Bangalore, in which the role of the state-machinery became more than clear: suppression, or diffusion by giving concessions, of workers’ activities. This was also seen in the recent mass-absence of workers from factories in Bangladesh.
2. “How do the workers mobilize and organize? What methods or approaches will be adopted by the political organizers?.. This is a vital supplement to the Maruti case, which demonstrated that even in the organized sector – at the cutting edge of technological innovation in the workplace – the radical Left has an important role to play. With the rise of casualization of labor, it is true that workers have become more geographically mobile and contractually flexible; but the upshot may be that they are now more amenable to the kind of politics articulated by the radical Left... Who organizes the workers at sites that have not been previously organized or where trade union influence has been minimal?”
What the authors present as a victory of Maruti Suzuki workers in 2000 (victory in the form of a tripartite negotiation) seems reminiscent of the “organized” workers-unions- organizations’ appeals in 2016 from Jantar Mantar to parliamentary conscience for the workers of Honda Tapukara, which was followed by a photo-op with Delhi’s Labour Minister, a continuing court case, and a dead end which wasn’t even spoken about.
At a time when it has become amply evident that representative frameworks are dysfunctional in supporting workers’ organization, is there any case for the good vs. bad representative argument? Is there any case for the “radical Left” better than the “classical Left” idea? We can ask workers from ASTI Electronics (Sec-8, IMT Manesar),
“Temporary workers braced the situation by the strength of their backs. They were approached by all – IMK, KNS, Bigul Mazdoor Dasta – to hijack our struggle, but we didn't let them. We agreed that they could give us suggestions, and we did take suggestions, but made it clear from the first day onwards that acting or not acting upon suggestions was up to us. A leader from AITUC said the HMS does this kind of politics every time, you should trust us, we will fight your struggle. A temporary worker replied, It was good of you to come, but we've seen what you did in Napino Auto. You may leave, thank you. A CITU leader then said many things against Modi, that he is bringing laws that will spoil the workers' future, that we have to stop those laws from coming into action. A temporary worker replied, You are now in senility, have gained immense knowledge, but this is not a platform for electioneering. It is a platform of workers; the laws you speak of haven't yet come, and already we are doomed. You haven't been able to implement laws presently in place, but still speak of a future. When somebody from Bigul came to speak, IMK protested, demanding they not be permitted to speak. They were told thatthis platform isn't IMK's, but of the contract workers. It is our decision whom to allow or disallow to speak.” (FMS, April 2015)
Or we could also test the validity of these claims against certain “militant” tactics of the Bellsonica Union:
“In June, workers at the factory bluntly told the union leaders that the union right away do something for immediate relief, failing which the workers would act on their own. The union which had been holding out hopes since months for the decisive date of 12 July at the High Court, taxed its brains and made a plan : as the saying goes, kill the snake without breaking the stick. To ensure that the production does not suffer, the company does not face losses, the company does not get annoyed – the weekly off day in the factory was chosen. A lot of thought also went into the “action” to be taken - to act without putting the government authorities under pressure, or tension, without being a bother, without angering them. A Sunday was found to be the best choice. 6000 handbills were printed for distribution. 1500 posters were printed for putting up in Dharuhera, Bawal, Gurgaon, Faridabad, Delhi University and IMT Manesar. Towards the end of June, the union kept busy many workers working in Bellsonica factory and their colleagues outside the factory.
Sunday is a holiday at the factory. Government offices are closed on Sundays. Hence, the middlepersons calling for revolution-vevolution announce “Program : Collective Hunger Strike Venue : Mini Secretariat, Gurgaon Time : 9 AM – 5 PM
Date : July 3 2016”” (FMS, July 2016)
The bankruptcies of radical Left politics were visible already in the events around the Maruti Suzuki de-occupation, of which the authors of the article in question only present incomplete fragments, through the same obfuscating lens. A more detailed account:
“Permanent workers, trainees, apprentices, workers hired through contractor companies, new workers who had been hired to run the second assembly plant — all these workers, around 4000 workers, in a meticulous operation on the evening of 18 July 2012 attacked two symbols of the wages system : managers and factory buildings. It was not this or that bad manager who became the target but rather any and every manager; hundreds of managers, MANAGERS AS SUCH WERE A TARGET. It is this that makes happenings in the Maruti Suzuki Manesar factory one of global importance. Suppression that triggers explosion is well known, but concessions being rejected en masse is a new phenomenon. It is a radical point of departure. Maruti Suzuki Manesar is a good example, but what is more important is that amongst factory workers in the national capital region in India, similar things at different stages and levels are gaining currency.
In the following days, the two thousand factories in IMT Manesar offered a significant ground for workers to meet other workers and to bond with them. In place of that...central trade unions acted fast and shifted the venue 25 km away to Gurgaon by constituting a committee of 16 trade union leaders who would decide what steps are to be taken. Of the discharged permanent workers numbering 546, those remaining outside the jail were pushed into becoming an audience for this committee. Other workers’ representatives/supporters, critical of central trade unions, but who also see workers as victims and as lacking consciousness, erased the active role of the workers on 18th July. They made out the company to be the active force that had conspired and hired bouncers to attack workers to instigate them. Poor workers only reacted to the bouncers’ attack and so were caught in the management’s trap. 60-70 thousand leaflets with these falsehoods were distributed amongst workers in IMT Manesar, Gurgaon, Delhi and Faridabad. Knowingly or unknowingly these do-gooders encouraged the workers to set out on paths that were tiresome and exhausting. Petitions, demonstrations, protests by the family members of the jailed and sacked workers; hunger strikes, bicycle protest tours...steps which gave some support to the workers’ cause, but which, if relied upon solely, only made workers tired and exhausted. Because of the ineffectiveness of the committee of 16, those more to the left gained ground. And the venue was shifted 200 km away to a peasant dominated area.
By July 2013 the complete bankruptcy of all those who considered workers as poor, exploited victims, had reached a stage where these ‘struggles’ came to an ignominious end — on 18 July 2013 in a candlelight protest in daylight in a park provided by the government, a portrait of the manager who died in 2012 was carried...” (From ‘An Account of Factory Workers Today’ cited above)
To suggest that a tendency working against the direction of workers’ activities ought to play a decisive role in mediation, and even organization of workers follows the same line of argument by which a dysfunctional state machinery is sought to become functional again in regulating workers’ activities. The significance of this line of thinking lies in how regulation and organization of workers act complementary to each other.
3. “The rural rich gentry, the upper caste kulaks, and the wise elders of the nearby settlements all supported the company bosses....Perhaps the postcolonial condition not only does not completely transform peasants into workers at least for now, but in this condition the workers have to traverse both spheres. In the case of Maruti the workers who were part of the struggle were only the first generation who had given up farming and taken up technical education to become part of the skilled workforce. Maybe that is the reason that forced them to look for succour in their villages rather than in their so-called autonomous self.”
Having seen that presentation of all workers as “precarious,” “fragmented,” or otherwise weakened by “globalization” is inadequate as a characterization, the authors turn to add more “local” qualifications pertaining to remnants (or fables) of earlier social structures (e.g., the management vs. the Dalit worker; the local contractor vs. the migrant labourer;
“Taking into account that many of these workers belonged to villages around Gurgaon- Manesar, their impulse led them to fall back on the community organization of the khap panchayat.” and so on).
Notwithstanding the absence in history of a worker completely bereft of baggages, whether of past identities, or of present links to non-worker habitats (e.g., to a rural community), this approach fails to look at the factory (or the neighborhoods) as a space in which churning takes place between people of very varied such experiences, under very new, unprecedented conditions. Rather than look at the links and discussions that emerge between workers in a new space like this, the authors construe it as just another playground for baggages of the past to play out. Thus, they fail to even imagine the possibility of something new and different to emerge from workers’ activities.
“Maxop, Sec-6, IMT Manesar: 12 hour shifts for the manufacture of automobile parts for export. .. Work load is a lot, workers keep leaving, there are always vacancies.. High temperatures in the factory.. On the night shift of 16th January, Kaleem Ansari was working on a pressure die casting machine. At 2:10am in the night, a casting part got stuck in the machine. When Kaleem attempted to remove the part from the machine, it suddenly sprung into action due to being on auto-plan. His head got sucked into the casting machine, and he died immediately. Workers stopped work. Left the factory premises. The factory was shut on the 17th, on the 18th January too. Work commenced on the 19th.” (FMS, February 2015)
We find among factory workers a trend wherein even one person on the factory floor becomes a focal point of concern for every other worker. In this process, the force of past identities, or specific differences, to set apart collectivities is challenged by the workers’ reading of their common situations. This trend is repeated again and again, in the events at Udyog Vihar in February 2015 at the area-level, with a beating given to a garment worker becoming a trigger for spilling of widespread anger against many factories and cars of management. More than 2000 policemen refused to act on seeing the volume of workers having a go at the factories (FMS, March 2015). We also heard from workers of a Micromax factory at Mayapuri, Delhi (FMS, December 2016), where
“There are about 450 workers in the Mayapuri Micromax factory, with 9 hours long duty in a day, paid 9000 (after deduction of esi/pf) rupees a month. As soon as workers spend sometime in the factory, they refuse to do overtime. Hence, the Micromax management is concerned at all times with enlisting new workers. In Novermber 2016, the management removed 4 workers from 13 in a small department from work. The 9 remaining workers in the department halted work. The management had to take back the four removed workers.”
Where even one worker becomes a focal point of discussion among tens of thousands, an invitation for collective action, we infer that many differences and specificities, and many baggages that come along with the same, are put into questioning, and this is a starting point to look at workers’ activities as something radically different from earlier social markings.
This emergence of new tendencies is particularly marked in how the gender question manifests itself among workers. More than half the participants among events such those witnessed in Bengaluru (Jan 2016), Udyog Vihar (Feb 2015), Okhla Industrial Area (Feb 2013), and so on were, firstly, women, and secondly, migrants. Both these categories are considered, in dominant and counter-dominant discourses, as socially weak and vulnerable. In this context, consider this about the workers’ sit-in at ASTI electronics:
“from the 4 th November, 60 male and 250 female workers began a continuous sit-in outside the factory...” (FMS, Dec 2014)
Or from JNS & Jay Ushin (Sec 3, IMT Manesar):
“Women wage-workers from all over Gurgaon, Jhajjar, Rewari, Pataudiin packed buses. Many also walk down to work daily from Manesar, Kasan, Khoh, Naharpur. Like on other days, on 10 th February too – a Monday – women workers coming by buses and on foot gathered outside the factories at 8:45 am. Entry into both factories is through one gate alone and duty begins at 9 am. However, on 10 th February, the gathered women workers refused to enter the factories. For about two whole hours they stood outside the factory gate and discussed promises by the Haryana Chief Minister to raise the minimum wage to Rs. 8100. The police arrived. In buses, senior staff accompanies the women workers as informers, so the women don't talk as freely. Despite all this, the company didn't have a clue when on the 10 th February more that 2000 women workers acted collectively. JNS Instruments is a strong initiative between Nippon Seiki, Japan and J P Minda from India. Autometers for Honda, Bajaj, Hero, Suzuki, Yamaha two-wheelers and Maruti Suzuki and Honda cars are manufactured here. Jay Ushin is a joint-venture between Ushin Ltd., Japan and J P Minda. It manufactures car-keys and automatic-locksets. JNS annually produces goods worth about Rs. 5 billion, while Jay Ushin produces goods worth Rs. 6 billion annually. Male wage-workers working in these factories work for two shifts of 12 hours each. Shifts change every 15 days, whereupon workers from the first shift work 16 hours straight. The factories run 24 hours a
day, every day of the month. The only holiday is on 26 th January (National Republic Day). Overtime rates are below single-rate: Rs. 22 for male and Rs. 23 for female workers per hour. Those directly employed on the company rolls are given their salaries directly in their bank accounts, they number 500-600; their role is to get work done by the contract workers, and they boss around inside the factories. Men and women contract workers are hired through eight to twelve contractors.
Workers are told about their wages around the 9 th of every month, but they are only paid around the 20 th . Workers who have quit are made to dance around for long to get their dues, women workers often enter arguments at gates, swear at the management, even pick up their footwear to thrash somebody when they come to collect their dues.” (FMS, Mar 2014)
Clearly, new kinds of relationships are taking shape between the men and women who share factory spaces, who stop work together, pelt stones together, share neighborhoods. As more households become multiple-earning, what becomes of the gender hierarchies within households that are part of the “social factory” that the authors point to? If we return to some scenes from the Maruti Suzuki de-occupation in this light (of which our authors inform us that workers, being tied to local villages, “sought succor” outside “their autonomous self,”
“It has been observed that important questions dealing with life, time, relations, representation, articulation and factory life were brought to the fore by the deoccupations of June and October 2011. In the words of a worker:
‘Inside the Maruti Suzuki factory, 7-14 October was the best time. No tension of work. No agonizing about the hours of entry and exit. No stress over catching a ride in a bus. No fretting about what to cook. No sweating over whether dinner has to be eaten at 7 or at 9 pm today. No anguishing over what day or date it is. We talked a lot with each other about things that were personal. All of us drew closer to each other than we have ever been before, during these seven days.’
In the same vein, when the issue of 30 workers being bought made the rounds in end October, a worker said:
‘Earlier we used to pass on the issues to the president, general secretary, department coordinator — that they will tell. But now every worker himself answers. On every issue, every one gives his opinion. The atmosphere has changed.’” (An Account of Workers’ Activities)
Exceptionalizing the norm
1. “There have also been attempts to invent and improvise methods of organizing workers in these changed conditions, where the organized sector is supposedly being increasingly fragmented, with lean production or just-in-time production becoming the norm, and shop floors becoming increasingly redundant as a site of both production and mobilization. Even where the shop floor continues to be important, as in the automobile sector, the worker is now a mere appendage of the machine and has to tune their self to the iron rhythm of the robot. The ideal worker, it seems, is one who can transform into one of the cogs of the huge machine... transforming the shopfloor into a site of precarity”
In the above section, the authors have merged multiple claims in a rather complicated unity: one claim is that due to production techniques now in motion, workers’ have become bootstrapped in acting at the site of production; then there is the claim that the shop-floor’s importance today remains only in the automobile sector, which, too, shows this helpless existence of the worker. And in order to challenge this, there “have been attempts” to improvise methods, which are obviously not the methods “improvised” by workers, since they are “a mere appendage of the machine.”
This view would prevent us from understanding a large number of workers’ activities vis a vis the factory mode today. Let us look at some instances:
“Sebros Auto (Sec-5, IMT Manesar): Due to the breaking of a die-part of the die-casting machine, while being paid wages on 11th July, they were deducting Rs. 3000 from the salaries of the pressure die-casting workers. Workers refused to take wages, and 9 machines in the department were shut...” (FMS, Sep 2014)
“At Munjal Kiriyu... all workers stopped production on 18.11.13 in favor of three trainees who were removed. After production was stalled for 25 days, the union and the management made an agreement with elusive traps involving provisions for dismissal and discharge.” (FMS, Feb 2015)
“JNS Instruments (Sec-3, IMT Manesar): Line leader, in a school-like fashion, orders a worker to stand in place for 10-20 minutes. What shame in standing in place? Gets some relief from work. Older workers disclose to new ones how to deal with supervisors and line leaders. Girls from two lines got together to beat up a line leader. The supervisor had to come to secure release.” (FMS, Apr 2015)
And so on. An interesting trend seen in garments factories is product rejection. Pants manufactured in Indo-British Garments had legs of different sizes; 32,000 pants returned to the factory, without anybody getting a whiff of how this happened (FMS, Sep 2014). Similar rejections were produced by workers at Modelama and Precision Prints. Workers of the two factories of Wearwell in Okhla Industrial Area kept machines shut for several days over non- payment of wages, and stayed in de-occupied factories in September 2014 (FMS, Oct 2014). And there are numerous instances of workers having clashes at the factory site; in many cases, such as Udyog Vihar (Feb, 2015) and Orient Craft, Manesar (Oct, 2015) for example, these happened in the middle of a shift. One then looks at garments workers’ activities in Bangalore in January, 2016, and more recently in Bangladesh in December 2016. Further off, one recalls collective fainting by garments workers in Cambodia, and so on.
2. “this unruly, often militant, population working in extremely uncertain conditions. Every other day we hear news of workers murdering a factory official, workers raiding a company or plant office, or the sudden disappearance of a worker, or a laborer in a precarious work condition committing suicide.”
This “unruly, often militant” worker, for the authors, is a by-product of “unorganized” “precarity” that is at the same time a liability for everyone from the state to the management, and simultaneously contributes nothing to the “struggle.” This upstart, in all manifestations of this syndrome, is capable only of sporadic acts, bordering on pathology. Even when in a group, their acts have nothing to do with the pace of factory production, or a hindrance to the same. It is to “govern” this “unorganized subject without producing a subject called the organized worker” that is the task of regulation as well as organization. We shall leave this wild claim unresponded.
3. The Struggle of Forms Glides By
The authors of the article submit their analysis, broadly outlined and discussed above, to a rigmarole of forms from the world history of the left, and to its more localized Indian counterpart: from the party, to the union, to the autonomous organizational form (as epitomized by the Italian theoreticians of workers’ movement). They find that “Every instance of worker-led resistance has shown strong marks of autonomy, a swell of consciousness on the ground, and a large degree of spontaneity. At the same time, every uprising of workers has demonstrated features of strategic leadership, effective organization, wide social networks, and a strong transformational desire.” Apart from the fact that neither has their discussion about the wage-worker today given any scope for workers’ autonomous activities to be understood in any meaningful sense, nor have their notions about organization and autonomy left any clear clues about how the two mesh together, we find that workers’ activities elude any attempts to fit them in such forms. Sometimes this rejection is immediate, as during an ongoing gathering or a sit-in where existing organizations of various hues often arrive; this is also because the results of deciding in favor or against are immediate too. But in a large measure, it is also the subtle avoidance of the temporary worker who knows he/she is outside the legal framework.
Conclusion
In “normalizing” or conceiving the image of the wage-worker today from the lens of organization of bygone times, an inversion takes place: the worker appears as a weak entity, a mere “cog in the machine.” This inversion is only achieved by emphasizing the most irrelevant aspects of the workers’ being and doing, and by circumscribing their regular frictions with the production process, and how they learn and act upon the same. Thus, a Left that considers itself theoreticians of workers arrives at the problem from leagues behind where the workers have already reached.
[The translations from the originally Hindi reports have been made available due to the participation of a number of friends. For other reports mentioned which haven’t been translated, we will be happy to get back if you write back to us.]
Hey, so I've now added both
Hey, so I've now added both those article to the site as they're really interesting (especially when read together). Here's the Viewpoint article and the response.
In future though, when you see stuff like that, feel free to upload it to the site directly as it's all stuff that would be of interest!