A follow up to shop talk.
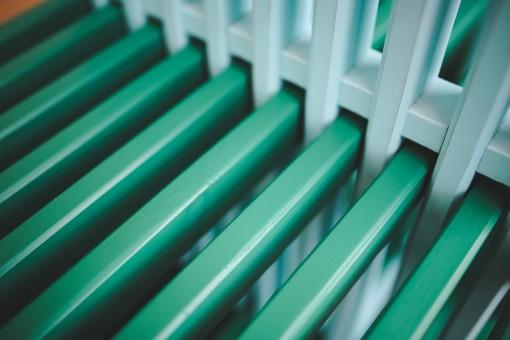
I've been moved around the factory a bit last week. I spent two relaxing shifts in what appears to be the company's loading bay of broken toys. But sadly it didn't last, I was moved back to the fast paced sections. In shop talk, I briefly mentioned that factory work is the area with the highest number of disabled and English second language workers I've encountered in my work life. This impression has been confirmed, and it's also the only workplace I've been employed at where migrant workers can be found in some roles of responsibility. Very few were in the higher paid more respected, looks good on the CV and attracts the headhunters positions. Mostly they're in positions of seniority that don't really have any perks other than respect from the rest of the line, so I don't want to give the false impression that it's meritocratic, but it was a little surprising to me at first.
Haven't seen many disabled workers in those positions, though. In fact, looking back, the only times I've encountered a disabled worker in a position of some authority it's someone with mobility issues in a clerical role, admin or payroll usually. There is also a degree of well-intentioned humouring of the more obviously disabled staff, which well isn't great, but I haven't seen any of the warning signs of more vicious and aggressive attitudes that I've encountered in other work places.
I may have more thoughts on these as I go on, or I may not, we'll see.
I did a shift on one of the premium lines, I said in shop talk that I was able to roughly calculate how much labour I needed to accomplish to be profitable for my employer, and it wasn't much. Well, a friendly acquaintance who'd been on the premium lines before told me that the stuff we were making that day routinely sells for £20. Now I can't confirm that, I guess I go to the wrong shops, but I have no reason to doubt him. So, again factoring costs, let's estimate about £10 or so of each sale goes into the pockets of the company which owns the factory. So, within 10 minutes of clocking in, I had been a profitable resource for the company.
The pace was very fast, so fast in fact that even in overalls and nets I was obviously struggling to keep up, so the supervisor put me on another station on the line. My job without going into detail1 was to feed the containers into the line. So again, very easy stuff, though there were knacks2 , but without this easy step, no product could be assembled and nothing could be sold for profit.
The national minimum wage has risen in the UK recently, I remember employers were complaining, but once the deadline passed they all adapted pretty quickly. I can't think of a large employer that went under or noticeably downsized because of the increase. When I worked on the docks, a similar thing happened with workers militancy. The companies would keep trying to enforce new conditions on the densely unionised workforces, and it would pretty close to strike action sometimes, but it never did get far because the companies stood down, and within a week or two had somehow found the money to pay for wage rises and spending on workplace improvements that they were swearing blind could not be found and bankruptcy would follow.
This isn't news to anyone really, but I remembered reading that traditionally the number one demand a workforce could make that would practically guarantee the most violent strong arm tactics from the employers wasn't wage increases (no matter how high) or improvements or even changes to hiring practices, it was reductions in work days and shift lengths. And, I can see why that's the case. Even though in terms of real sums for the workers the money is negligible, reduction in work hours cut into the ratio of profit from labour.
On this premium line, in order for the company to break even on its costs, I'd go home after half an hour tops. I shudder to think how much they'd make off of me after twelve hours on that line.
Addendum-
Anyone can do this pal
I was talking to a friend who has moved to London and had a bit of a turbulent job history in the month or so since the move. She has had to bounce from multiple jobs. She has no issue getting them, the problem is they're very casual, short term or just abruptly announce they won't be extending contracts. There is more stable work with a much greater probability of long term employment, but a lot of it is factory work similar to what I've been doing. The issue is that she can do most of the work in the roles available, most people are capable of at least some position or role in a modern factory setting, but there's a difference between being capable and being profitably capable.
I think I've shown just how quickly most productive enterprises cover their costs and make a profit off their workforce, but it's not enough to be profitable, they want the maximum amount of profitability feasible. This is the root of a lot of the workplace difficulties in manufacturing stem from. From feelings of isolation in the very layout of the workspace, to exhaustion and even injury preforming your duties. You may well have doubled the companies' investment in you after an hour of work, but the lines don't stop then, you have to keep up the pace for hour after hour.
That's a big sacrifice, it's difficult to explain what this constant and unrelenting demand has on those who haven't experienced it. I find it to be another example of a key problem with the capitalist system of work, it's not interested in fulfilling any genuine needs it just maximizes potentials for profit regardless of the costs to people, the environment or even its own viability in the long term. It's wasteful in the extreme.
Comments
Just to say finding these…
Just to say finding these write-ups really interesting, thanks
Steven. wrote: Just to say…
Thank you, though I thought I'd saved this to drafts as I wanted to give it another pass.