Gurgaon workers newsletter issue 35, with news, reports and analysis from India's special exploitation zone.
Gurgaon Workers News #35 - February 2011
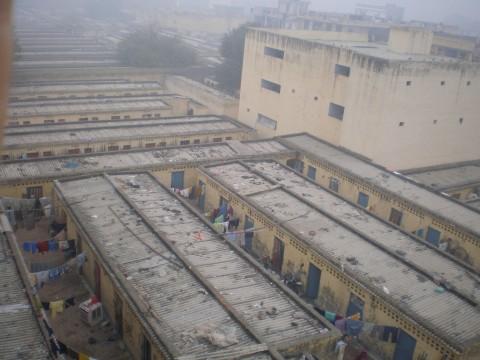
After the Wildcat: Another Report by Honda HMSI Worker
Detailed additional information, including participants' reports about the wildcat strike of Honda workers in Gurgaon, India in December 2010.
The short wildcat strike at Honda HMSI on 17th of December 2010 has to be seen on the background of growing anger of a casualised workforce in the main industries of the global south. Be it temporary workers at Hyundai in South Korea, Honda supplying workers in China or Nokia workers in Chennai, in the shade of a minoritarian ‘permanent’ work-force – which bourgeois media focuses on when reporting about gains of development – the unrest increases. We first document additional information on the strike based on Honda HMSI temporary workers reports; we then have a short look at recent international conflicts which bear an systemic semblance to the Honda Gurgaon strike and conclude with some preliminary thoughts on ‘What could be done?’ on an immediate and local level.
The Wildcat Strike at Honda HMSI in Gurgaon
After publishing a first general report in the last issue of GWN we spoke to workers hired through contractor employed at Honda who took part in the strike. The report is being circulated in the January/February issue of Faridabad Mazdoor Samachar.
HMSI Worker
(Plot 1, Sector 3, IMT Manesar)
On Friday 17th of December, after having worked for about two hours, the A-shift workers at the scooter line suddenly stopped work, they went in groups to the other departments of the factory, where they were joint by the rest of the workers. The arriving B-shift joined them, they did not start working. At 11:30 pm management suddenly announced that the weekly day off would be shifted from Sunday to Saturday – the following day. The A-shift workers, who arrived ay 5:30 – 6 am at the bus stops waited in vain for the company buses, they then found out by phoning work-mates and supervisors that the day would be off. On 19th of December the A-shift resumed production, the factory then ran continuously till 27th of December, the time between 27th of December and 2nd of January is the annual maintenance time off… On Friday, the 17th of December, a worker hired through contractor told his work-mates that he had been mistreated by a security guard. The workers immediately stopped working. Permanent workers, casual workers and workers hired through contractor were together in this… The strike spread from the scooter line to the motorcycle lines to the weld- and machine shop to the PI department… the entire work-force was involved. Both A and B-shift workers joined. It was the first time since 2005 that the entire work-force would be in action together, 1,800 permanent and 6,500 workers hired through contractor together. Under the impact of wildcat action of 8,000 workers the management was shaken. “Keep calm, the union president is currently not here, he will be coming at 5 pm”, the workers were told. The main manager for plant security apologised in front of the workers and told them that the security guard would be kicked out. A senior member of management said that he has come all the way from Jaipur to sort out the issue. Workers showed their anger: “We don’t want your apologies, bring the security guard, he should apologise. And you could have come from Japan instead from Jaipur, we don’t care. We want that you stop the clearance.” 1 At 3:15 pm the busses of the A-shift left the plant and quite a few permanent workers left the factory. At 4:30 to 5 pm the union president arrived and said that everything will be arranged in favour of the workers, but that they should go back to work. The permanent workers retreated, but the workers hired through contractor catcalled the union president and accused him to have done nothing about the ill-treatment and discrimination of workers hired through contractors. Had the workers started the wildcat shouting “Down with management, long live the union”, these workers shouted some hours later “Down with management, down with the union”. The rumours spread that management would resort to a lock-out, which caused the permanent workers to withdraw further, but which did not result in controlling the workers hired through contractor. The union president requested several times to resume work, the workers ignored the requests and the union president left the scene angry. The B-shift did not start working – without the workers hired through contractors production could not have been started. The company then announced that Saturday would be off. After A-shift did not arrive at the factory and after 150 to 200 police turned up, workers left the factory on Saturday at 11:30 am. The shaken management did not put up any notice in reaction to the strike. The company did not undertake any open repression apart from suspending a permanent worker, accusing him of instigation. There is talk about 170 workers hired through contractors having been put on a list in order to kick them out ‘secretly’. When workers were assembled together it was mentioned several times that a similar strike had happened in 2004. Back then a group of five workers hired through contractors had been sent to negotiate with management, they left in a company car and disappeared from the scene without workers knowing what had happened to them. It was also said that this time workers should be careful not to expose themselves.”
We want to give some additional information concerning the general background of the strike and encourage you to read the reports from Honda HMSI predating the dispute. In these reports the general day-to-day divide between permanent and temporary workforce becomes clear.
The permanent workers earn up to 31,000 Rs per month, while temporary workers earn around 6,500 Rs. The wage divide has been growing since the establishment of the union in 2005, so has the relative numbers of temporary workers and their work-load. Permanent workers are mainly employed in supervising positions and departments like maintenance, welding, machine shop, final quality check. The line-leaders are permanent workers who have been employed for a minimum of two years and who underwent extra-training. Each of the three main assembly lines is segmented into three-four zones, line-leaders are in charge of these zones where between 25 and 60 workers work. The assembly lines themselves are spacially separated in two main halls. Below the ‘line leader’ there is a supervisor, who normally reports for 8 to 10 workers, The supervisor tends to be a worker hired through contractor himself. A temporary worker reported that while a permanent ‘line leader’ initially supported the strike, the temporary worker himself was rather anxious to be seen taking ‘actively part’, because his supervisor was standing close by – who was a temporary worker, too.
In general temporary workers did not show too much fear, despite the fact that one of the managers present during the dispute was the manager who runs the ‘tests’ of temporary workers. The test is the only chance for temporary workers to become a casual company worker. The next test will be in February 2011 – allegedly around 1,200 temporary workers will take part and 80 will have the ‘chance’ to become a casual worker. The test contains – apart from general questions of production details, such as colour of electrical connection used for this or that vehicle part – the name of the Japanese capital or the Indian Minister for Industry. During the last years less than 80 temporary workers were are made ‘company casual’. The fact that this year the number increased is – according to rumours – due to the opening of the second Honda HMSI plant in nearby Bhiwadi, which is approximately 40km from the existing plant and approximately 90km from Delhi.. Production there is supposed to start in April. According to other sources no workers are transferred from Manesar plant to Bhiwadi, only some middle managers are shifted. Officially there is no ‘production’ shift planned, the capacities in Bhiwadi are additional to those in Manesar.
We finally want to say a few words about the question whether the coming union election played a major role in the dispute – as stated by a Honda manager. The fact that the suspended permanent worker belongs to the oppositional AITUC faction indicates that the ‘faction’ struggle has some influence. The AITUC faction is the original union faction, which fought for recognition in 2005. The current leading faction – which took over two years ago – is portrayed as a ‘management friendly’ faction of mainly ‘local workers’. The current union leadership put up a notice immediately after the strike saying that they regard the dispute as trivial – which was a blunt sign for management that they would not oppose a suspension. The management in due course suspended the permanent worker on 20th of December.
When using phrases like ‘management friendly faction’ etc. we would ask you to bear in mind that during the wildcat strike of temporary workers in October 2006 [http://gurgaonworkersnews.wordpress.com/gurgaonworkersnews-no7/#fn43], the now opposition AITUC faction was the leading union body and they denounced the strike as ‘instigated and anti-union’, as much as the current leadership denounced the December 2010 strike. The conditions of temporary workers has not only declined since the last two years of ‘new union leadership’, the wage gap and work load started to increase before that. The temporary workers demonstrate that they are more than mere pawns of this faction or the other. Historical experiences, e.g. during the 1980s restructuring period in nearby Faridabad, show that the last straw of management, when having to deal with mass-level of unrest, is to turn it into a representative/factional struggle. If necessary they are happy to accept a ‘management hostile’ faction, too, as long as they have at least someone to talk to.
The International Character of the Dispute
In the Faridabad Mazdoor Samachar issue distributed in Delhi industrial areas in January/February 2011 we concluded the report – see translation above – with an example of the recent strike of automobile workers at Denso in China. Facing management and state repression these workers had refused to put forward ‘delegates’ for negotiations and instead confronted management with anonymously written demand letters. Here we don’t want to go deeper into the question of ‘potentials and limitations’ of ‘anonymous struggle’, but rather stress the point that the Honda HMSI dispute has a wider international background. We picked three examples of recent struggles of a casualised workforce; a workforce outside of the ‘recognised’ employment and union status, but right at the core of the new global workbench which emerged after the mass-relocation of industry and casualisation of work-force during the 1990s.
Hyundai/South Korea
The wildcat strike of temporary workers at Hyundai in Ulsan (South Korea), began on 15th of November 2010. Around 570 out of 2,000 temp workers stopped assembly lines, demanding permanent contracts – according to Korean law they would have to be made permanent after two years of employment. They occupied a factory department which links the automatised storage halls and assembly lines of the factory. They resisted police attacks and harsh conditions – but by 6th of December technicians managed to bypass the occupied part of the factory, numbers of occupiers came down to 260 by that time. On 9th of December they evicted the building. During the dispute they received no solidarity from permanent workers unions: three days after occupation 600 permanent workers and middle management organised protest against strikers. In a formal spectacle FKTU union asked members whether to join the strike, but 77 per cent members voted against joined action.
Honda/China
The morning of 17th of May 2010 workers in the automatic transmission department halted the assembly line by pushing the red stop button, normally used for emergency shutdowns over quality problems. The company offered various raises in bonuses and subsidies for different groups of workers, but the workers insisted on a general raise in the base wage. The company fired two workers who had initially stopped the line. The harsh reactions of management galvanized the workers.
On 24th of May, the strike became indefinite, soon affecting Honda’s main assembly plants in Guangzhou and in Wuhan in central China. Both factories had to stop production on 26th and 27th of May. The local government, along with the union and management, took a more and more aggressive stance, resulting in the mobilization of a group of about 100 thugs clad in union uniforms, who confronted the workers physically.
http://www.labornotes.org/2010/12/auto-worker-strikes-china-what-did-they-win
http://chinastrikes.crowdmap.com/
Honda/Mexico
Since December 2010, after sacking of an active worker, struggle at the Honda plant in El Salto, Jalisco intensified. Twenty-one hundred workers on two shifts assemble 5,000 trucks a month, most of them exported to the United States. Since 2009 workers have been resisting and have held several work stoppages to demand that management modify its demands and its attitude. In every case management has responded with repression and firings of the workers it saw as leader. Management maintains a “protection union,” the CTM (Central de Trabajadores de Mexico, the largest official union in the country). The atmosphere at Honda is one of constant hostility and contempt for the dignity of the workers on the part of the foremen. Meanwhile, Honda’s logo reads “The Power of Dreams.” This charro union, as Mexicans call unions that serve the employers, plays the role of formally complying with Mexican law, but in reality it is an instrument that management uses to keep salaries the lowest of all assembly plants in the country. The daily wage is $10-$12.30 per day.
What Could be Done?
There are a few things which any small group of workers/activists can do. Situations like on 17th of December will emerge again and again, question will be whether workers a) will be able to enforce their demands because they actually hit the company; b) they manage to avoid giving management opportunity for open repression as far as possible c) develop stronger organisational links within and beyond the Honda factory as a result of the dispute. We can do out bit to help, which could mean:
* keeping in touch with workers directly – not only their official representatives – in order to follow general developments in the factory (individual repression etc.)…
* finding out whether the information of the 24 hours strike has spread to workers in the surrounding/supplying industry and through which means (through room-mates, security guards, actual production-stops, by seeing police etc.); this would tell us something about to which extend workers can rely on ‘organic forms of industrial and proletarian communication’ and how we can intensify it…
* analyzing current economic situation and production system at Honda with workers, if possible by facilitating regular meetings between Honda workers and workers in the nearby supplying industry (see reports of automobile workers in this issue)…
* arguing for both, need for avoiding traps (‘faction union struggle’, ‘making delegates’, unnecessary physical confrontations, lock-outs, left isolated during factory occupation etc.) and the necessity of extension of future struggles,
* making sure that these positions find a voice and practical support in future struggles…
* looking for acquaintances among workers in the new Honda plant as quickly as possible and inform new workers about experiences of struggles at Manesar plant since early 2000s…
* encouraging flow of information between workers in similar situations on local, regional (Chennai etc.), international level…
- 1 Management kicks out workers hired through contractors once they have completed a year of employment and often re-hire them two weeks later. They do this in order to prevent the workers gaining legal right to permanent status.
Comments
Death of a Worker: Work Kills at Modelama Textile Factory
In a report on the death at work of a textile factory worker and subsequent strike in Gurgaon, India.
The following report about the sad death of a garment worker at Modelama factory in Gurgaon was sent by a friend of Gurgaon workers news.
Since then the death of a worker seems to turn into a back-and-forth between different interest groups about the question of compensation. A former MP from Maharashtra, who belongs to the same village as the worker, took a middle-man role.
“At around 3am on the morning of 16th January or, the 15th night’s overtime, 17 and-a-half hours into continuous sewing and stitching for the 21hour shift, sitting on his iron stool, Md. Rabban, died instantly of electrocution through one of the live wires protruding out of the production line in the garment factory, Modelama Exports in Plot no.105-106, Phase 1, Udyog Vihar, Gurgaon.
Md. Rabban, who had been working, sampling, stitching, sewing, washing, ironing and producing clothes for Modelama, for the past more than 7 years and in the 105 unit since its production started three and-half years back, hailed from Muzaffarpur, Bihar, and was paid the measly minimum wage of Rs.4200 (after the cuts for ESI, PF, and the ‘breaks’, from Rs. 4800). As usual, on 15 January also, Rabban reached in the morning 9.30 am shift to start his day on the production line to work till 6.30am the next day, to resume work again at 9.30am. There were two breaks of half-hour each at 1.30-2pm, and then again at 6.30-7 (which workers pay for themselves, and for which wage is deducted from the workers themselves), a dinner break from 8.30-9.30pm (tasteless stale food in the canteen, for which the company pays a mere Rs.20), and then a next chai break at 2.30-3am. Ten minutes later into resuming work, at around 3.10am, in the overtime and already 17 hours into work, one of the live wires protruding out in front of his machine, electrocuted Rabban as his hand was caught in between the line. A number of complaints were regularly made about the safety conditions and specially about the leak in the current in the electric machines in the production line, and nothing as would cost the company was done about it. The usual thing that does get done in such situations by the management is the ‘management’ of the body, i.e. to wipe it out of sight, as workers recall earlier incidents of the sweeper in the morning sweeping out litres of blood on occasions of the death of workers due to over-work, clash with management etc. However, before any such ‘cleansing’ attempt, the around 80 workers in the production line who witnessed the incident, made an uproar, and tried to help their saathi/work-mate. There was a cry for immediately taking Rabban to the hospital, and because the company had neither doctors nor an ambulance for such (frequently occuring) situation, and was also unwilling to spare its own cars, the workers offered to take him themselves to the hospital in a hired car in front of the company and were pooling in the Rs.1500 required for the transport. Sensing the workers reaction, the management (the supervisor and other staff) shut production immediately, took possession of the body, and took him to the hospital where he was declared brought dead, and then to the morgue after post-mortem, and with an rapidity which only came later, also took the body to the Nizamuddin cemetry and buried him. The police was informed and an F.I.R registered under Sec.304-A which declared it a freak ‘accident’.
Meanwhile the workers of the production line, were joined by those coming in for the morning shift, and anger erupted outside the closed gates of the factory, with over a thousand workers pelting stones and breaking the sleek glass front of the company. The low pay, the single overtime, the non-payment of back wages, the no-offs strictness, the continued and regular harassment in the form of abuse and even slaps and beatings, the strong surveillance in the from of finger-print/biometric entry and the CCTV cameras at every nook and line with the suspicion of workers-as-thieves while clearly it is the other way round, all took form in this solidarity action. Workers of other companies in the area going for their morning shifts also joined in to express their solidarity and anger. Police was employed to control the anger, and disperse the angry workers who demanded justice for Rabban.
The company however came out much later, and made an oral statement about the promised payment of Rs. 1lakh to the family of the deceased. And by around 2pm on the 16th, the spontaneous wave of anger was stifled with the threat of police, targetting-and-possible-suspension and management-through-the-family. The next day’s newspapers reported in an insignificant column, an accident in the Modelama company which was resolved. Work remained suspended on the 16th. /on the 17th morning, when workers got back to the company, after some initial tension at the gates, work was resumed. however soon after, in many departments, many workers again took up the previous day’s incident and its sham resolution in a general uproar, which the management stifled with selective representation of some workers, and a promised 50-50 joint-fund of workers and the company’s contribution which will be paid to the family of Rabban. That it was a direct case of negligence of the company was skirted and work was resumed again, not after a fire broke out (it was unclear how, or by whom) in one of the departments which took some time to be doused.
The Modelama Exports unit situated in plot 105-106 in Phase 1, has around 4500 workers, and it is one of its several units in operation in Haryana, Delhi and Chennai. (Plot nos. 105, 106, 184, 200, 201, 204 in Udyog Vihar, Phase-I, 660 in Phase-II, plot nos. 5, 7, 18, 89 in IMT Manesar, one each in Sonipat and Rewari, two- B-33 and B-57 in Okhla Phase-I, and one in Chennai). Selling “the mystifying aura of fashion”, it is a big name in the ready-made garment industry besides expanding into home furnishing, jewellery, energy and real estate. Its chairman, Lalit Gulati was the president of the owners’s association, Apparel Exporters and Manufacturers’ Association. Its production units cover 400,000 sq. feet area, and has a production capacity of 6 million garments per year and a turn over of US $ 60 million. Its ‘vision’ statement says that it seeks to maintain a balance between “ethical values and corporate objectives” and that it “takes pride in the human resource” that it has. It counts its buyers from the US, UK, Canada, Europe and Australia, among them being big corporate players like Gap, Banana Republic, Marks &Spencer, Abercrombie &Fitch, and Country Road. Its main buyer, Gap is a leading member of the ‘Ethical Trading Initiative’ body of Companies, NGOs and trade unions, which ‘promotes ethical trading’ and ’3rd party auditing’ (an industry which recent estimates show has grown to a staggering US $50billion!) and is supposed to have been specifically ‘monitoring’ the 105 unit for ‘workers rights violation’ with a number of complaints earlier. It is another classic case of the exploiter making the rules of violation and monitoring.
Comments
From Supply-Chains to Radical-Chains: Reports from Automobile Workers
While workers in the global north are with their backs to the wall of crisis – see current dispute at FIAT Mirafiori – the automobile workers in the global south suffer for a pathetic ‘boom’.
We document 17 short reports from automobile workers, employed up and down the supply-chain: from work-shops with a couple of machines and half a dozen (child) labourers to the first-tier suppliers and the assembly plants employing thousands. In the Delhi region the supply-chain is stretched out over a hundred or more kilometres, the current effort to turn the country-road between Faridabad and Gurgaon into a six-lane highway has to be interpreted in terms of automobile crisis: the slow traffic impacts on the production process as much as on the use(less) value of the final product, with average car travel speed often hardly exceeding the velocity of a cycle or bullock cart. The current petrol price hikes add financial pressure.
Due to the fact that the supply-chain is formally divided up into different company units, the internal contradictions within the industry surface as ‘different private interests’. The main automobile companies try to outsource not only stock and certain production steps, but also the financial risks. Component producing suppliers complain about financial squeeze: there is increasing price pressure from both sides (steel and rubber prices are increasing and final assembling companies asking for lower prices) and the current hike in interest rates as part of ‘anti-inflationary measures’ make investments in capacity expansion more costly. Final assembling companies ‘take informal credit’ from suppliers by paying for parts, not in advance, but with increasing delay of up to 180 days. The final assembling plants are compelled to increase capacities and to run the capital-intensive plants 24 hours, while the rest of the supply-chain is dragged deeper into the squeeze.
The wildcat strike at central assembly plant of Honda HMSI on 17th of December has demonstrated that ‘labour costs’ are not a mere figure in the overall calculation, but an angry soul in a heartless machinery – see report in this issue of GurgaonWorkersNews. Any revolutionary effort will depend on turning the supply-chain into the radical chains, which we will have to lose: re-composing working class from the assembling centres to the labour intensive peripheries.
The following reports have been gathered and re-distributed with Faridabad Mazdoor Samachar in November/December 2010.
Boxer India Worker
(Milhard Colony, New Town Station, Faridabad)
The workshop employs nine workers. Wages are 3,000 to 3,500 Rs for helpers. Overtime is paid at single rate.
Karma Engineering Worker
(Sector 22, next to Rachna Cinema)
The workshop employs 25 people. They produce car parts on 12-hours shifts. There is no weekly day off. The helpers get 3,000 Rs and the machine operators get 4,000 Rs to 4,200 Rs.
Hanu Industries Worker
(Plot 152, Hridaykund Colony, Mujesar)
The 20 workers get between 3,000 and 4,000 Rs per month. The work-shop runs on two-12-hours shifts. There are two rubber mixing rollers, nine extruder machines, a boiler, three moulds and a generator. For production rubber and carbon is used, the air pollution is bad. Workers get ESI and bonus is given.
Akma Auto Worker
(Barkhal Gaon, Sector 49)
Around 150 workers are employed to manufacture axles for motorcycles. A lot of children between 12 and 14 years are employed. They receive 1,000 to 1,200 Rs per month, the older workers get 2,500 to 3,000 Rs. No ESI, no PF.
Varun Precision Components Worker
(Plot 220, Sector 59, Faridabad)
We work on two 12-hours shifts, we produce parts for Hero Honda two-wheeler gear. The parts we produce are sent to Shivam Autotech, from there they go to Hero Honda. The 40 workers hired through two different contractors get 4,200 Rs for 30 days of 12-hours shifts. The permanent helpers get 4,200 to 4,400 Rs for 26 days, the operators get 7,000 to 8,000 Rs. There are no toilets, you have to go to the railway lines nearby. The drinking water is outside of the factory in a barrel. If there is an accident, they don’t fill in the accident form. If you take a day off, they cut two days from your wages. There is swearing and slapping from ‘superiors’.
India Forging Worker
(Plot 28, Sector 6, Faridabad)
There are more than 1,000 workers employed on two 12 hours shifts. We manufacture axles and hubs for Maruti Suzuki and various tractor parts. Only the 50 people of the middle management and administration are permanent. There are 50 company casual workers, who are employed since years – they are neither kicked out, nor made permanent. Only those 100 workers get ESI and PF. The helpers hired through contractor get 3,000 Rs to 3,500 Rs, the operators get 4,500 Rs to 5,000 Rs. Around 500 workers work on piece rate system. There is metal scrap laying around everywhere in the factory – but you won’t get gloves or safety boots. If you hurt yourself you won’t find bandage in the company, you have to get private treatment. There used to be a canteen, but now there’s not. Even if you have to work 36-hours on stretch there is hassle to get extra money for food. You have to write down overtime and pieces worked, otherwise 500 to 600 Rs get embezzled.
SPM Auto Worker
(Sector 59, next to JCB)
Around 200 workers manufacture axles and gears for Tata Motors, Maruti Suzuki and export on two 12-hours shifts. They are often forced to work 36 hours on stretch – the gates are locked and the helpers are given 20 Rs for food. The helpers get 5,200 Rs for 30 days of 12-hours shifts. It is heavy work, a lot of accidents, people have to pay for treatment themselves. The toilets are defunct since years, you have to go outside, but you are supposed to be back within 5 minutes.
Oswal Diecaster Worker
(Plot 48, Industrial Area, Faridabad)
The 1,500 workers hired through contractor did not receive the obligatory annual bonus. In the diecasting department workers manufacture parts for TVS, Hero Honda and others. Workers do not get days off, even when ill. They are told: Take some pills and work.
JNS Industries Worker
(Plot 4, Sector 3, IMT Manesar)
The printing department runs on two 12-hour shifts, the other departments on 8-hours shifts. We manufacture metres, starting keys and other parts for Hero Honda, Yamaha, Suzuki, Bajaj, Maruti Suzuki and Mahindra. It is a big factory, the women workers are transported to and back from the plant in 19 buses. They work only day-shifts. Most of the workers are hired through contractors. The wages of permanent workers and staff are delayed, their July and August wages were paid on 15th of September. The manager of the printing department swears a lot and slaps people. During meal breaks machines continue running, people have to take their break in turns. The food is of low quality. BUT on 18th and 19th of October the food was really good: there was butter with the bread, Coriander leaves and tomatoes in the vegetables. The big shots from Japan came for a visit! The whole factory was clean and even defunct machines were run for show…
E.R. Automotives Worker
(Plot 184, Sector 4, IMT Manesar)
500 workers are employed on 12-hours shifts. We manufacture gears for the Sonalika tractor, the sheet-pipe for Hero Honda Motorcycles and hydraulic bolts for export to England. People work everyday, though only 8-hours shifts on Sundays. Overtime is paid at single rate. When we are forced to stay longer, they give you 50 Rs extra for food for a continuous 36-hours shift. There are 50 to 60 permanent workers and 450 workers hired through three different contractors. The company did not pay the obligatory inflation compensation (July) of 134 Rs. Drinking water is a big problem. The toilets are dirty.
Pacman Worker
(Plot 28-29, Sector 7, IMT Manesar)
The factory runs on two 12-hours shifts, the main work is injection moulding. Machines runs through the meal breaks, day and night, all days through the month. Overtime is paid single rate, though shown is double rate. We manufacture parts for Honda, and through the company ‘Sandhar Locking Devices’, we also produce for Hero Honda. They cut wages in the name of PF, but when you send the PF form after leaving the job the PF office sends it back saying that no money has been paid into the PF account.
Endurance Technology Worker
(Plot 400, Sector 8, IMT Manesar)
There are more than 1,000 workers employed through three different contractors, manufacturing parts for Honda, Suzuki, Mico and Bosch. Last year, permanent workers gave 1,000 Rs each and workers hired through contractor gave 599 Rs each as contribution for a union. The union was formed. The wages of permanent workers increased by 3,600 Rs and they received a canteen voucher of 17 Rs, instead of 11 Rs. The workers hired through contractor received only safety boots. After establishment of the union the company increased production by increase of line-speed. The speed-up falls on the shoulders of workers hired through contractor. The 150 permanents rather make work, they work less themselves.
http://www.endurancegroup.com/plant-address.htm
Hero Motors Worker
(Plot 61, Sector 3, IMT Manesar)
Two 12-hour shifts, work on power-presses and MIC welding. The power-press operators get 4,500 Rs, overtime is paid single. The work pressure is high. The company was previously called Repro Auto, workers used to be paid bonuses, there used to be a weekly holiday and if you had to work longer than 12 hours you used to receive 30 Rs extra for food. With the change of the company name all this has been stopped.
Talbros Worker
(Plot 51, Sector 3, IMT Manesar)
There are 80 permanents and more than 400 workers hired through four different contractors. Permanents get double rate overtime payment, the rest single. Money is cut for ESI and PF, but no money paid when you leave the job.
Track Components Worker
(Plot 21, Sector 7, IMT Mensar)
During the Common Wealth Games the pressure to provide ‘Proof of ID’ increased. The workers would have needed at least fifteen days to go back to the village in order to get the required documents. This would have meant that the factory had to be closed during their absence. In order to stop workers from ‘escaping’ the security regime during the Common Wealth Games, companies found all kind of by-passes: deals with the police that a ‘Company ID’ would do etc.. In the power press department an ‘official’ takes ‘credit’ from workers for a financial scheme, but the money gets embezzled. The company always ‘demands’ that the health and safety devices at the power presses should be used, but they actually do not install these devices. There is always the danger of cutting your hand. They used to give you 20 Rs extra for food if you had to work longer than 10.5 hours, but they have stopped this. There are less workers nowadays, therefore people are made to work longer, most of the time 14 hours, sometimes 17 to 19 hours on stretch. You would stop at 2 am at night, sleep in the factory and start again at 7 am. There is no stock of material, the machines keep on running, even on Sundays.
Munjal Showa Worker
(Plot 26, Sector 3, IMT Manesar)
There are three shifts, employed are 15 permanents, 400 trainees, 400 casuals and 1,000 workers hired through three different contractors. We manufacture shockers for Hero Honda, Yamaha and Honda two-wheelers. The trainees are given a break after one year, then re-hired as trainee. They are not made permanent, even after five years they say: if you want a permanent job, look somewhere else. The casuals are given a break after six months and then re-hired. For overtime, the trainees get 35 Rs per hour, the casuals 20 and the workers hired through contractor 40 Rs. They make you work longer by locking the gates. The workers hired through contractor are afraid that if they refuse overtime, they are made ‘casual workers’. The trainees and workers hired through contractor work 150 to 200 hours overtime per month, the casuals 60 to 70 hours. You have to stand upright all the time, no time to go to the toilet, no ‘reliever’, who would do your job while you are away. After working 16 hours constantly on the line, on 27th of November a worker at the rear-shocker line collapsed. Only the 15 permanent workers receive ESI cards. The obligatory annual bonus is also only paid to the 15 permanent workers.
Honda Motorcycle and Scooter India
(plot 1, Sector 3, IMT Manesar)
In October 2010 the company announced that till January 2011 the B-shift would have to work overtime each Monday till 1:30 am. Management cut 475 Rs from August wages of the workers hired through contractor and 2,500 Rs from permanent workers for not meeting the fixed production target. We could not meet the target, because production stopped frequently due to lack of parts. The company busses have become a ground of bitterness between permanent and temporary workers. The temp workers are made to stand up and leave the seat to a permanent workers, sometime they are made to get off the bus, they are ‘fined’ 200 to 400 Rs or threatened to ‘have them kicked out from the company’. The temp workers have to do the heavier work, they receive much lower wages, have to endure all kinds of mistreatment from the ‘permanent’ team leaders. The two-tier division exists even during Divali: the permanent workers received one kilo dried fruit each, while workers hired through contractor received only half a kilo.
Comments
Mobile Phone Factory Maxx in Haridvar, Sahadarabad – Struggle for Regular Meal Break
Indian electronics workers strike for a meal break.
The Maxx Mobile company is situated in Haridvar, Sahadarabad. The factory produces mobile phones and their batteries. The company breaks the labour law, it does not provide a lunch break during the 8.5 hours shift. On 27th of November workers acted against this. All workers left their work and assembled at the gate. Workers demanded that the lunch break should be included into the working-day. The management refused to accept the demand. The workers started a protest sit-in at the gate. On 28th of November the company was shut for the regular Sunday day off. On 29th of November the workers continued their strike. A representative of the workers went to the labour department. The representative was assured by the officials that the demand would be met by the 7th of December – and he was sent back. In this way the labour department ‘dealt’ with the transgression of the labour law. In order to spread fear amongst the workers the management has locked-out all workers hired through contractor. All workers now wait for the 7th of December. To hope for the labour department to sort things out will be a self-betrayal and will end in workers’ passivity.
Comments
Step Across the Border: Lakhani Workers in Faridabad and in Uttaranchal
Reports from Indian garment workers on their conditions, February 2011.
We translated reports from Lakhani workers in Faridabad and Uttaranchal – a state further north of Delhi/Haryana. Lakhani is a major company engaged in garments, plastic and rubber manufacturing – from sandals, shoes (AllStars, Puma, Adidas) to car parts. Lakhani has recently opened factories in Uttaranchal, in addition to the long-time established and often conflict ridden factories in Faridabad. In some cases a division of labour and mutual dependency has been created between the two industrial centres. The reports from Uttranchal are translated from the Marxist-Leninist journal Nagrik.
Lakhani Apparels Worker
(Plot 136-b, Sector 24, Faridabad)
After July wages had not been paid by 20th of August workers stopped working. After four hours the production manager said that wages will arrive tomorrow, so people should go back to work. We started working… the July wages were paid on 2nd to 5th of September, but the August wages were not paid. Now 350 workers are left, about 400 to 500 workers have left the job. We manufacture garments, amongst others for Motherhood and Global. Up until July there was a lot of work. The daily working-times were from 9:30 am till 1 am, they often made you work till 4 am. They give you vouchers for the canteen, but the food is of low quality and won’t fill your stomach. When they force you to work Sundays, it is shown as worked on saturdays. Those workers directly hired by the company get the minimum wage. The other workers work on piece rate and/or a paid by one of the four contractors: 3,000 to 3,500 Rs per month, no ESI, no PF. The permanents are supposed to get PF, but when they leave the job they find that no money has been put into the fund. Once the buyers come, the factory is clean and workers get masks and so on.
Lakhani Footwear (Adidas, All Star)
(Plot 130, Sector 24, Faridabad)
There is one line manufacturing for Adidas, one for AllStar and two for Lakhani Shoes. At the Adidas line 500 pairs of shoes are manufactured per shift, once a representative of Adidas arrives the number is reduced to 250 pairs – they want to show how much they care for quality. The same happens at the AllStar line: normally 800 pairs, during visits 400 pairs. At the Lakhani line things are different, one line churns out 2,400 pairs per shift. While there are stools to sit at the Adidas and AllStar line, there aren’t any at Lakhani line. No time for toilet, the feet swell up. Once a representative of the buyers comes, management hands out ear plugs, masks, aprons, gloves etc., but they take it back once the visitor has left. The lines are right next to each other, but the buyer’s representatives won’t even look at the Lakhani line. When the inflation compensation of 134 Rs had to be paid according to law, they immediately increased the price for tea in the canteen, from 2 to 3 Rs. Money is cut for ESI and PF, but the 1,400 casual workers don’t get an ESI card.
Lakhani India Worker (Puma)
(Plot 265, Sector 24, Faridabad)
We worked 150 to 200 hours overtime in May, we received the payment as late as October. June and July over-time was not paid – no money. They say that overtime is paid one and a half-rate, but actually people get only 25 or 27 Rs per hour. For three months there were less orders, there was less work here. Now work has started again, amongst others for Puma. The company demands over-time from us, but we say that they should pay the outstanding wages first – we refuse to work overtime. They also did not pay the July inflation compensation of 134 Rs. In this factory 1,500 male and 1,500 female workers manufacture sandals and shoes.
Lakhani Factory -, Haridva Sidkul, Uttranchal
(from: Nagrik, 16 – 31 December 2010)
The Lakhani Vardan Group runs three factories in Haridvar Sidkul, Sector 4, Plot 20, 21, and 22. The first plant runs under the name of Lakhani India Ltd. In this plant shoes are manufactured, amongst others, for Puma, Canvass and Woodland . The second plant runs under the name of Lakhani Auto Privat Ltd. In this factory soles for shoes are manufactured. The third plant runs under the name of Lakhani Detergent and Soap. The Lakhani Vardan Group has started production in Haridvar in 2005. The following report concerns the Lakhani Auto factory.
The hall is 130 feet long and 120 feet wide. Currently they use three lines (conveyor belts), one chiller machine, three – four different kinds of grinders, in total about 22 to 24 machines. various chemicals are used for raw materials to produce the layer, the mid and the sole – and to glue them together. The material comes from Lakhani’s main plant in Faridabad. As a first work-step the layer and the mid are roughened with the buffing machine and the sole is worked with a hand-grinder. The chemicals 5050 / 6316 RC, Hardener ARF, 948/24 B, P-300 are used to clean and roughly glue the different layers, which are then put on the conveyor belt. On the lines the three layer, mid and sole are put together and proceed to the heater, the press and the chiller. Around 50 workers are employed for this stage of production. The finished pieces are then put into size-frames and the outlines are marked. The soles then process to the side-grinding machine, the quality check and the packing station, where a pair of soles is put into a plastic bag. Around 15 to 20 workers perform this work-step. At the three lines workers manufacture between 1,400 and 1,700 pair of soles per day, the final side grinding machine has a capacity of 1,500 soles per day. The production costs for these soles are about 125 Rs per paid, the 5 Rs wage costs are included. Lakhani India Ltd. pays about 150 Rs per pair.
For a six-days week the workers receive a monthly wage of 3,632 Rs plus 300 Rs incentive bonus. Out of the 70 workers working in the plant no worker is employed as an operator, all are employed and paid as helpers, although actually they operate machines. The main problem for the workers is the fact that the chemicals stick to the hands and clothes of the line workers. The clothes are destroyed and workers develop allergies. The gases trouble lungs and eyes. The halls are filled with rubber dust, floating in the air like fog. The company issues no masks. If people complain they are threatened with dismissal, some workers who talked about these problems were forced to sign their ‘own’ notice letter. The wages tend to be paid delayed. Because of this workers have engaged in sudden stoppage of work several times.
The sole production has started this year in April. Before that Lakhani had produced auto parts in this plant, but the production has been shifted to Faridabad. Only 25 to 30 workers in the plant have worked there for more than six month, about 15 to 20 for four months and the rest for less time. Most workers are from Bijnour and Shahjahanpur. The workers are not issued the obligatory company documents (work contract, company ID) or ESI cards. Although half of the workforce are women, the management does not provide the obligatory facilities (separate restroom, toilets, health care, creche for children). The canteen is only called canteen, no food is provided, it is only a place to sit. There is a guest house provided for management.
Comments
The Empire’s New Clothes: Reports from Textile Workers
Reports from textile workers in India in February 2011.
While automobile workers fight mainly within/against the ‘flow’ of a vast production system, garment workers fight with the ‘rushes’ of the market in a more mobile and less ‘mutually integrated’ industry – the form of struggle reflect these conditions.
While struggles in the automobile sector tend to have a higher degree of ‘coordination’, the structure of garment industry forces workers to ‘grasp the instantaneous chance of irruption’. The industrial relations are characterised by enormous pressure on global prices, sudden income of orders followed by slack period, dead-lines which require to make workers work 16 hours or more in order to be met. The big industry can rely on patriarchal family structures, small workshop industry and village systems to produce the necessary skilled tailors – the industry has little costs for training, but the workforce comes with it a certain professional pride. Major companies like Modelama try to undermine the bargaining position by ‘chain systems’ and ‘one-week-free-training’ offers…
Modelama Worker (GAP, Old Navy)
(105, Udyog Vihar Phase 1, Gurgaon)
We have started working yesterday, on 27th of November 2010 at 9 am. Some of the guys are still working now, 28th of November at 4 pm, they will go home at 8 pm… It is ‘urgent shipment’ time and the master said at about 1:30 am last night that ‘crores of Rupees could be lost’. Since three months, after the arrival of a ‘Madam’ [female manager?], the physical and mental torture has eased a bit, but it is still quite a lot. On 27th of November seven women workers were verbally abused nastily and they were kicked out from the factory. On the same day an ‘incharge’ beat a master and swore at a ‘piece leader’ and slapped him. The factory employs 500 female workers, they have to work on Sundays, too. The guys on piece rate work very fast, the company asks the same output from the workers on monthly wages. There is a chain system (several workers work on one piece of garment in division of labour) even for the piece rate workers. Instead of full piece rate (payment for one piece which is the same for all workers), they have part rate (people are paid different rates, e.g. for sewing a collar, a sleeves etc.), which makes it more difficult for workers to link up for higher rates. Management doesn’t count – and pay – all garments you have produced and they pay less than the previously fixed rate. Modelama offers ‘one week of free training’ to new workers every month, with the ‘possibility of later employment’.
Edigear International Worker (Adidas, Reebok, Puma)
(Plot 150 and 189, Sector 4 and Plot 235, Sector 6, IMT Manesar)
We manufacture garments for Adidas, Reebok and Puma. On plot 150 around 300 permanent and 650 workers hired through contractor tailor jackets, track suits and T-Shirts. We work 150 to 180 hours overtime per month. The pay slip shows only 50 hours. Between 22nd of November and 27th of November we worked three days from 9:30 am in the morning till next day 5 am. The same happens on plot 189. On plot 253 around 500 workers do leather work. They used to pay 50 Rs extra when you had to work till next morning 5 am, this has been reduced to 40 Rs. There is a ‘complain box’ near the toilets, a lot of people complained about the 10 Rs cut and put their complain flyer in the box, but nothing happened. The representatives of the buyers arrive once a month, then all three factories are nice and clean.
Kalamkari Worker
(383, Udyog Vihar Phase 2, Gurgaon)
If you arrive five minutes late, they send you back home unpaid. They cut money for ESI and PF from your wages, but even after years of employment you won’t get an ESI card. In the personnel department they always tell you: no time. I was ill and got a holiday application signed by the department manager – in the personnel department they threw the application away and said that there is only one and a half day holiday per month. When they hire you you have to sign 15 papers, but you they won’t give you any document as proof of employment. They say that shift times are from 9 am till 5:30 pm, but actually you work till 9 pm, often till 2 am.
Jyoti Apparels
(158, Udyog Vihar Phase 1)
In the sewing department workers work 120 to 150 hours overtime per month, in the finishing department 200 hours. Paid single rate. Only 25 out of 350 workers get ESI and PF. Currently there is a lack of tailors, so the bosses don’t bother us too much.
Ventage Workers
(Plot 5, Sector 7, IMT Manesar)
The twelve women workers doing thread-cutting get 4,000 to 4,300 Rs for a month of 9 to 10-hours days. The 90 male workers douing stitching work either by hand or by computer work 12-hours shifts. They get 4,800 Rs to 5,200 Rs. Wages are paid delayed, there is no ESI and no PF.
Mac Export Worker
(Plot 143, Udyog Vihar Phase I, Gurgaon)
The helpers are paid 3,600 to 3,800 Rs, no ESI or PF is given. Working-times are from 8 am, to 10 pm. The managers swear at workers, sometimes slap workers.
Chelsea Mills / GAP Worker
(Plot 360, Udyog Vihar Phase IV, Gurgaon)
Shift starts at 9 am and finishes at 9 pm, overtime is paid single rate. Workers get the minimum wage, but it is paid delayed. If you arrive half an hour late they cut 4 hours from your wage. Out of 450 workers only 100 get ESI and PF. GAP is the main buyer of this factory.
S and B Worker
(Plot 669, Udyog Vihar Phase V, Gurgaon)
There are 150 workers employed, out of which only 30 get ESI and PF. We work 70 to 80 hours overtime per month, one to two daily wages get embezzled from overtime.
Bharat Enterprises Worker
(Plot 189, Udyog Vihar Phase I, Gurgaon)
There are 60 permanent and 150 workers hired through contractors manufacturing leather jackets. The helpers are paid 3,300 to 3,500 Rs, the operators 4,000 Rs.
MIC Filter Worker
(Plot 88, Udyog Vihar Phase I, Gurgaon)
There are 500 workers employed in the factory, working 12 hours shifts. The security guards have not received their August and September wages (26th of October). They are employed through Asmat Security.
Eastern Medikit Worker
(Plot 195 – 205, Udyog Vihar Phase I, and Plot 292, Phase II, Gurgaon)
Wages for casual workers are delayed. Over-time payment is less than single rate, between 11 and 16 Rs an hour. September overtime has not been paid yet (26th of October 2010). Without bribe neither permanent nor casual workers get their PF money.
Comments
Turn a Blind Tired Eye: Security Guards from Gurgaon
A report on the security industry and conditions for security workers in Gurgaon, India in February 2011.
There are tens of thousand security guards employed in Gurgaon. There is security technology and architecture, there is a system of supervision, but the system is fragile in its inner self.
The watching eye is tired, turning watchtowers and CCTV circuits into an eternal void. Those who are supposed to supervise and secure are too precarious to care.
“We are watch men. Our job is to watch the factory burn. It is not our job to douse the fire. Our job is to guard the ashes, once the factory has burnt down. If someone asks about the whereabouts of the company, we have to provide information: this is where the factory used to stand, it has gone to ashes. This is our job, nothing more. It is our job to guard the factory, not to save it. We don’t manage to save ourselves, how are we supposed to save the factory”
(Conversation with a security guard)
Balaji Security Worker
(Branch Office, Kapashera)
We work 12-hours shifts, no weekly day off. For 30 days of 12 hours shifts we get 5,000 Rs. They take 500 Rs from you even before they hire you. Then they cut 2,000 Rs from your first wage for the uniform. Even if you have stood upright during the 12-hour day-shift all the time, if they catch you sitting down during night-shift they cut 200 Rs from your wage. If the guard from the other shift is ill or off, you have to work 36-hours on stretch – they might give you 30 Rs extra for food then. No ESI, no PF. It feels bad to search the pockets of the factory workers when they leave the factory.
Scientific Management Services (SSS) Worker
(U-28, DLF Phase 3, Gurgaon)
For 30 days of 12-hours shift we are supposed to get 6,100 Rs, but only 5,200 Rs are paid. They first said that 650 Rs are cut for uniform and boots, but then they cut 100 Rs every month extra. They cut money for ESI and PF, but neither is given.
Massive Security Workers
(Branch Office, Manesar – Main Office Nehru Place)
Even if you have to work 36-hours on stretch they won’t give you extra money for food. For 30 days of 12 hours shift they pay 5,000 Rs.
Om Security Worker
(Satvari, Chattarpur, Delhi Office)
They pay 5,000 Rs for 30 days of 12 hours shifts and wages are delayed. No ESI, no PF.
Comments