Beverly Silver traces the growth of workers power in the auto industry and the resultant outsourcing of industry to lower wage areas of the globe, where workers organised again and fought for better conditions, effectively spreading a militant workers' movement across the globe.
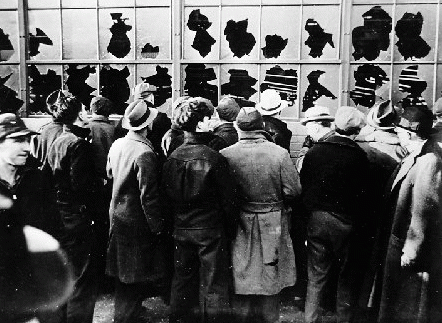
INTRODUCTION
The thesis of this paper is that the world automobile industry has been characterized by a half-century-long trajectory of labor militancy and capital relocation during which automobile production (in its "Fordist" incarnation) together with a characteristic corresponding form of labor militancy, have spread across the globe. This trajectory has been propelled by three major waves of militancy among the world's autoworkers: (1) the CIO struggles of the 1930s, (2) the "resurgence of class conflict" in Western Europe in the late 1960s, and (3) the emergence of "new union movements" in Brazil, South Korea and South Africa in the 1980s. Each of these rounds of labor struggles have prompted managerial responses, including the restructuring of production and the relocation of capital. And each round of restructuring and relocation has undermined workers' bargaining power in the sites of disinvestment/restructuring at the same time that it has created and strengthened new working classes in the sites of new investment.
The first section of this essay will trace the twentieth-century trajectory of global Fordism in the automobile industry from the CIO struggles of the 1930s to the recent labor upheavals in South Korea, South Africa and Brazil. It will be argued that this trajectory was driven forward by fundamental contradictions in the social relations of Fordist production. These contradictions reached crisis proportions in the 1980s as global Fordism found itself continuously reproducing militant and effective workers' movements in successively more peripheral geographical locations.
The greater success of Japanese-based corporations in containing the militancy and disruptive power of labor has allowed "Toyotism" to overtake Fordism in the global competition. While Fordism has been collapsing under the weight of its own contradictions, the competition from Toyotism delivered the coup de grace. Yet Toyotism itself is not a system without its own social contradictions--and its very success is likely to bring those contradictions to the fore. The final section of this essay will offer some speculations on the nature of those contradictions and their implications for the future of labor-capital relations in the world automobile industry.
I. THE FORDIST TRAJECTORY OF LABOR UNREST AND GEOGRAPHICAL RELOCATION: DEJA-VU IN MAJOR STRIKE WAVES FROM FLINT TO ULSAN
The complex division of labor characteristic of mass production in the automobile industry, beginning with Ford's introduction of the Model T, has produced a characteristic form of labor militancy. The strategic strike (especially the sit- down) targeted at a sensitive point within the automotive corporation's overall technical division of labor, has been the successful weapon of choice from Flint in 1936-37 to Turin in 1969-70 to Sao Paulo and Ulsan in the 1980s. In each case, workers quickly were able to force the acceptance of mass production unionism, major wage increases, and a degree of workers' control on to antagonistic employers.
The central characteristics of mass production in general, and the Fordist organization of production in the automobile industry in particular, has contradictory effects on the bargaining power of workers. On the one hand, continuous flow production and the assembly line increase labor-market competition through the homogenization/deskilling of industrial work roles and eliminate the market-based bargaining power of craftworkers. On the other hand, continuous flow production and the assembly line increase the vulnerability of capital to workers' direct action at the point of production. Likewise, although the concentration, centralization, and integration of capital give corporations formidable material resources with which to confront and oppose workers' struggles, these processes also increase the damage that can be done to an entire corporation by a strike in one of its key plants and the disruption that can be caused in the national economy by a strike in a key corporation or industry. This ability to cause costly disruptions as a result of one's location within a complex division of labor, we have called "workplace bargaining power" (Arrighi and Silver 1984: 193-5).
Automobile corporations have sought means to inhibit the use of this workplace bargaining power--through the promotion of "responsible unionism," through automation and through the relocation of production to regions with large supplies of semi- or newly-proletarianized cheap and/or repressed labor. However, these efforts have generally only succeeded in shifting the geographical location of this power over time.
A. Flint, Michigan:
On December 30, 1936, workers occupied General Motors' Fisher Body Plants No.1 and No.2 in Flint, Michigan. By March 12, 1937, General Motors (the US's largest industrial corporation with vast financial resources and a network of anti-union spies) was forced to capitulate and sign a contract with the United Auto Workers. This was the beginning of a flood of strikes which brought unionization to the mass production industries of the US.
A key to the UAW's success was the ability of the workers to exploit their position within the complex division of labor characteristic of mass production. The Flint sit-down strike that paralyzed GM's Fischer Body plant was planned and executed by a 'militant minority' of autoworkers who by 'unexpectedly stopping the assembly line and sitting down inside the plant . . . catalyzed pro-union sentiment among the vast majority of apathetic workers" (Dubofsky and Van Tine, 1977: 255). The strike wave demonstrated the limits of the assembly lines' technical control of the workforce: a relatively small number of activists could bring an entire plant's production to a halt. As Edwards (1979: 128) puts it, "[technical] control linked the entire plant's workforce, and when the line stopped, every worker necessarily joined the strike."
Moreover, just as a militant minority could stop production in an entire plant, so if the plant was a key link in an integrated corporate empire, its occupation could paralyze the corporation. Such was the case when a group of union members stopped production and occupied one of the most critical plants in GM's entire empire: the Flint plant which produced the bulk of Chevrolet's engines. With the Fischer Body and Chevrolet engine factory occupations autoworkers succeeded in crippling General Motors' car production and the corporation's rate of output decreased from 50,000 cars per month in December to only 125 for the first week of February. GM was forced to abandon its uncompromisingly anti-union stance and negotiate a contract with the UAW covering workers in 20 plants in order to end the strike and resume production (see Arrighi and Silver 1984: 184-85, 194-95; Dubofsky and Van Tine 1977: 268-69; Rubenstein 1992: 235-7). According to Rubenstein (1992: 234), "avoiding concentrations of militant workers influenced locational decisions even in the early days of the automotive industry."
Among the many reasons why the automobile industry had centralized in the Detroit area in the early twentieth century was the anti-union environment successfully imposed through an 'open shop' campaign carried out by the Employers' Association of Detroit. "By 1914, when Ford's moving assembly line transformed automotive production from a skilled to an unskilled occupation, the open shop concept . . . had become strongly entrenched in Detroit and the automotive industry in particular" (Rubenstein 1992: 234-5). With the success of the UAW, relocation of production away from UAW strongholds became one of the consistent strategies followed by the auto companies over the next half- century. Immediately in 1937, GM acquired an engine plant in Buffalo to reduce its dependence on Flint, and shortly thereafter began to diffuse production sites to rural areas and the US South (Rubenstein 1992: 119, 240-1). But the geographical relocation of the automobile industry was not, in the post-world war period, primarily an intra-US phenomenon. The breakup of the world market from the crash of 1929 until the return to currency convertibility in Europe in 1958, had closed off capital's international escape route. But as soon as post-war Europe stabilized, and in particular, with the establishment of the Common Market and the restoration of currency convertibility, US multinationals (including US automakers) flooded Europe with investments.
For several decades following the CIO victories, three employer responses--disinvestment in union strongholds, automation and the promotion of "responsible unionism"-- progressively undermined the structural strength of US labor in general, and autoworkers in particular. When a new upsurge in rank-and-file unrest at the end of the 1960s (symbolized by the 'Lordstown Blues') pushed the UAW back toward confrontationist tactics (with 'Operation Apache'), the automakers abandoned the promotion of "responsible unionism" and pursued geographical relocation and automation of production with a new-found zeal. The bargaining power of US autoworkers, already weakened by decades of restructuring, collapsed in the 1970s and 1980s.
The other side of the coin, however, was the creation (and over time strengthening) of autoworkers' movements in the new sites of industrial expansion. This process was first felt in Western Europe in the 1950s and 1960s.
B. Western Europe:
In the interwar period, Western Europe lagged far behind the US in the extension of Fordist mass production techniques to automobile production. In the 1920s, the European industry was characterized by many small firms involved in the custom-manufacture of cars; none had the resources or sufficient market-share to make the huge investments in fixed plant and special-purpose machinery necessary to "catch up" with the US. In the 1930s, centralization of capital proceeded quickly with the support of governments, but the ability to take advantage of the economies of scale inherent in Fordist methods simply was lacking. The barriers to intra-European trade combined with generally low wages for workers meant than no true mass market existed. US autoworkers could afford to buy the product they were making (even in the 1920s), European workers could not (Landes 1969: 445-51; see also Tolliday 1987: 32-37).
But the center of growth in the world automobile industry shifted to Western Europe following the 1930s and 1940s upsurge of labor militancy among US autoworkers. For Altshuler et al. (1984: ch. 2) the first major wave of expansion of the auto industry lasted from 1910 to 1950 and was centered in the US. The second major wave of expansion occurred in the 1950s and 1960s and was centered in Western Europe. The production of automobiles in Western Europe increased fivefold during the 1950s, from 1.1 million in 1950 to 5.1 million in 1960; and it doubled in the 1960s to reach 10.4 million in 1970 (Altshuler et al. 1984: 19).
The dynamic behind this expansion was a combined "American challenge" and European response. US direct investment in the European automobile industry had begun in the 1920s as a way to avoid tariff barriers and save on transport and labor costs. But investment took-off in the 1950s and 1960s. GM invested over DM 100 million in a major expansion of Opel (Germany) between 1950 and 1955 and afterwards continued adding to its facilities every year. GM also invested 36 million pounds in Vauxhall between 1952 and 1956 to enlarge its Luton plant and build a new factory at Dunstable. Likewise, in the 1950s, Ford rapidly expanded its Dagenham facility in the UK and its Cologne factory in Germany (Dassbach 1988: 254-55; 296-300). A combined corporate-government response in Europe resulted in the rapid growth of European automobile corporations through consolidation and the introduction of the latest mass production techniques. Thus, for example, the automobile industry in Italy (which experienced little direct investment by foreign car manufacturers) more than tripled its output during the 1950s and then doubled it in the 1960s. By 1970 motor- vehicle production in Italy had reached almost 2 million with Fiat accounting for the vast majority of the output (Laux 1992: 178, 200).
The rapid extension of mass production techniques in Western Europe had contradictory effects on the labor force, similar to those experienced by US autoworkers in the early twentieth century. On the one hand, craft workers (and their unions) were marginalized from production. On the other hand, the expansion and transformation of the industry created a semi-skilled working class composed of newly proletarianized migrant workers. In the case of the early twentieth century US, the immigrants had been from Eastern and Southern Europe. In the case of Western Europe in the 1950s and 1960s the immigrants came from the peripheral regions of Europe (southern Italy, Spain, Portugal, Turkey and Yugoslavia). In both cases the first generation of migrant workers generally did not protest against the harsh conditions of work and life. Unions were weak and the arbitrary power of management over issues such as hiring, firing, promotion, and job assignments, was unchallenged in the automobile factories. But in both cases, the second generation became the backbone of militant struggles that succeeded in radically transforming relationships within the factory and within society.
The strike wave which spread across Western Europe from the late sixties through the early 1970s caught unions, management, and states by surprise. In these strikes, mass production workers, like their US counterparts in the 1930s, were able to exploit the bargaining power that accrued to them as a result of their location within a complex division of labor. Autoworkers in plants across Western Europe came to realize that strategically located and timed strikes could do great damage to a corporation, while minimizing the sacrifice made by the workers themselves. Perhaps the most dramatic example was the "hot autumn" of 1969 at Fiat: "For Italian strikers, coordinated dispute activity within a large-scale production unit [was] undertaken with a view to paralysing production at the least cost to the workers. A judicious application of strike action a singhiozzo (shop-floor strikes) and a scacchiera (coordinated in-plant stoppages) soon leads to production chaos." (Dubois 1978:9)
Spot strikes, rolling strikes, and lightening strikes were designed to create the maximum disruption to the flow of production by targeting the most sensitive links in the productive chain. Similar tactics were employed by autoworkers throughout Europe in the late-1960s and early 1970s (see, e.g., Crouch and Pizzorno, eds., 1978).
The successful exploitation of such tactics resulted in a rapid expansion of the role of unions and workers' control on the shopfloor and an unprecedented explosion of wages in the 1970s. Major limits on managements' prerogatives were imposed. For example, at Fiat "consigli dei delegati" (workers' delegates committees) were set up at the factory-level, with the goal of providing workers (through their delegates) with some direct control over the organization of production and with a say in the day-to-day exercise of what had heretofore been fundamental managerial prerogatives: e.g., assigning work tasks, loads and speed, changes in the organization of production and the introduction of new technology. Management was required to inform, consult and negotiate with workers' delegates on all decisions relating to the organization of the shop floor (Silver 1992: 29-30; Rollier 1986).
The response of automakers producing in Western Europe to the startling successes of the workers' movements was analogous to the US corporate response to the CIO victories of the 1930s and 1940s: intensive restructuring of production (including the rapid robotization of labor-intensive tasks), attempts to promote "responsible unionism," and the relocation of production. For Volkswagen a strategy of shifting investments to more peripheral locations in Southern Europe (especially Spain) and South America (especially Brazil and Mexico) took precedence. Overall, foreign direct investment from Germany increased fivefold between 1967 and 1975 (OECD 1981, Ross 1982, Silver 1992: 80). At Fiat, on the other hand, massive robotization projects were pursued, including the complete automation of engine assembly (Volpato 1987: 218).
The effect on the bargaining power of workers was also analogous to the US case. By the early 1980s labor movements in Western Europe (including auto workers) were generally on the defensive and the promotion of "responsible unionism" was abandoned. By 1980, Fiat was able to bypass the workers' councils and unilaterally implement a policy of aggressive automation and rationalization that reduced the number of employees from 140,000 to 90,000 (Rollier 1986: 117, 129). The gains of the late 1960s had been largely overturned.
The other side of the coin, however, was the creation (and strengthening) of new automobile proletariats in the favored sites for industry expansion in the 1970s and 1980s. Production expanded in low-wage semiperipheral locations with authoritarian regimes, as the auto corporations sought to escape militant workers at home, and as semiperipheral governments "seized the chance" afforded by the global competitive conjuncture to lure capital investment and promote export-oriented industrialization. Large mass production sectors were created and successive semiperipheral "economic miracles" were heralded in the 1970s.
C. Sao Paulo, Brazil:
The Brazilian economic miracle from 1968-1974 corresponded precisely to the period in which core capitalists increasingly sought to escape militant workers' struggles at home. Brazil provided a seemingly perfect site for investment: the 1964 military coup installed an extremely repressive regime which succeeded in smashing the old corporatist trade union movement and in effectively eliminating any working class opposition at both the plant-level and national political level. The Brazilian automobile industry experienced very rapid expansion in the 1970s. By 1974 Brazil was among the world's top ten vehicle producers. From 1969-1974 vehicle output increased by an average annual rate of 20.7 percent; and from 1974-1979 (while vehicle output collapsed throughout the core in response to the oil crisis and labor militancy) the Brazilian industry continued to grow at 4.5% per year (Humphrey 1982: 48-50). While retrenching their operations in core countries, multinationals invested heavily in Brazil in the 1970s: Ford, for example, invested over US$ 300 million and increased plant capacity by 100 per cent (Humphrey 1987: 129).
The rapid expansion of manufacturing in general, and the automobile industry in particular, created a new working class: new in size and in experience. From 1970 to 1980 employment in manufacturing doubled (Humphrey 1987: 120). In the industrial suburb of Sao Bernardo do Campo where the automobile industry concentrated, the number of workers employed in manufacturing increased from 4,030 in 1950 to 20,039 in 1960 to 75,118 in 1970 (Humphrey 1982: 128-9). This new working class tended to be concentrated in plants of enormous size. The Volkswagen, Mercedes and Ford plants in Sao Bernardo each employed over 60,000 people (Humphrey 1982: 137).
Like the protagonists of the CIO struggles of the 1930s and the strike waves in the core of the late 1960s, Brazil's auto workers were strategically located within a complex technical division of labor within the Brazilian factories. But this new working class was also strategically situated in what was now the key export sector of the Brazilian economy: in 1988 transport equipment was Brazil's largest export, worth $3.9 billion (Economist Intelligence Unit, No.1, 1990, p.3). Strikes and militancy in the automobile industry would affect not only the profitability of the specific firms involved, but also the ability of the Brazilian government to service its enormous debt to private multinational banks.
In the closing years of the 1970s, as labor movements were experiencing decisive defeats throughout the core, a new trade union movement burst onto the scene in Brazil, bringing to an end almost one and a half decades of worker quiescence. Brazil's auto workers formed the central core of this new labor movement. An intense strike wave in 1978 inaugurated a period of activism which survived (even flourished) through a decade of repression and recession in the 1980s.
On May 12, 1978, the day shift workers entered the Saab-Scania plant's tool room in Sao Bernardo, but refused to start up their machines. The strike quickly spread to the whole plant with thousands of workers standing by their machines in silence with their arms crossed. From Scania, the stoppages spread to other auto plants--Mercedes, Ford, Volkswagen, and Chrysler. Within a few days, workers were crossing their arms and refusing to work in all the major plants. Reminiscent of the US strikes of the 1930s and the Western European strike waves of the late 1960s, these were mainly conducted as sit- down strikes, with workers reporting to work each day, eating in the canteen, but refusing to work (Moreira Alves 1989: 51-2; Humphrey 1982: 166). The strikes resulted in major worker victories, including substantial wage increases and the recognition of new, independent trade unions (not linked to the official state-sponsored trade unions). Implacably anti-union employers had been forced to negotiate with new independent unions and to sign collective contracts.
The automobile multinationals did not accept this defeat and carried on a battle to repress strikes and eliminate the unions from the plants. They believed that the victory of the workers in 1978 resulted from their own lack of preparation, rather than from any inherent strength of the workers. But repression only resulted in a change of tactics from large-scale confrontations to smaller-scale (but very disruptive) protests on the shopfloor (slowdowns, spot strikes, and general non- cooperation with management) reminiscent of the tactics used in the Western European strike wave of the late 1960s and early 1970s to maximize the disruption while minimizing the costs to the workforce.
By 1982 the major employers had accepted the inevitability of unionization, union involvement in shopfloor management, and rising wages. Ford was the first to come to believe that the maintenance of discipline on the shopfloor required the promotion of "responsible unionism." In 1981, Ford recognized plant-level committees made up of workers elected at the shop floor level, and linked to the independent unions, as having the right to negotiate with management over workers' concerns and grievances (Humphrey 1987: 125). VW held out longer, but by 1982 VW was forced to recognize the independent unions, and accept factory committees similar to those that had been introduced at Ford. Unrest continued at the plant-level and in the nation as a whole. Strike activity in Brazil reached a peak of nine million workers involved in 1987 (Moreira Alves 1989: 67). During the four years from 1985 to 1988, real industrial wages in Greater Sao Paulo grew by an average of 10% per year (Economist Intelligence Unit Country Profile, Brazil, 1989-90).
By the late 1980s, Brazil was no longer a favored site for investment by the automobile multinational corporations. New investments promised by the auto multinationals in the late 1980s never materialized, and the Brazilian auto industry is becoming technologically obsolete (Gwynne 1991: 75-78).
D. Port Elizabeth:
Like Brazil, although on a less spectacular scale, South Africa became a favored site for investment by the automobile multinational corporations as they fled militant labor movements at home. During the late 1950s and early 1960s, foreign capital had shied away from South Africa. The strength of the national liberation movements was peaking across the continent, and massive protests against the implementation of apartheid laws within South Africa were spreading--including nationwide stayaways organized in 1957, 1958, 1960 and 1961 by the South African Congress of Trade Unions (SACTU). However, foreign investment boomed in the late sixties, once the Nationalist government showed that it could successfully smash the opposition, and moreover, institute repressive and racist legislation which ensured a steady flow of cheap labor.
From 1965 to 1969, the average annual net inflow of foreign capital was $308 million per year; and between 1970 and 1976, the inflow mushroomed to an average of $1 billion per year (Litvak et al., 1978: 40). The motor vehicle industry was one of the main targets of these inflows of capital. From 1967 to 1975 the motor vehicle industry grew by 10.3 percent annually (Litvak 1978: 24, Myers 1980: 256).
A large, urban, Black proletariat was formed, concentrated in semiskilled positions in mass production industries. And as in Brazil, this new proletariat became the backbone of a wave of labor militancy in the late 1970s and early 1980s. And as in Brazil, the wave of militancy was successful in gaining recognition for independent unions and advances in both wages and working conditions.
Autoworkers formed the frontline of the industrial class battle in the early 1980s. As in the other cases described above, they were able to effectively exploit their position within a complex technical division of labor. Mass militancy took a variety of forms: some were large-scale conflicts involving thousands of striking workers (e.g., in 1980 at Ford, VW, Datsun and BMW; in 1981 at Leyland; and in 1982 at Ford and GM); others involved the use of disruptive but low-key tactics such as slow-downs and small strikes limited to key departments within plants. For example, in an August 1984 strike at Volkswagen, the workers limited their stoppage to the paint shop, but because of the latter's strategic location within the factory's division of labor, the entire plant was forced to shut down for five days. The plant reopened when management agreed to union demands (Southall 1985: 321, 329).
By the end of the 1980s automobile multinationals had largely divested from South Africa. As Gwynne (1991:50) noted: "While political factors [anti-apartheid campaign] have been emphasized, the recent withdrawal of Ford and General Motors from South Africa has a significant economic basis."
E. Seoul/Ulsan:
The fading of the Brazilian and South African "economic miracles" overlapped with the emergence of the South Korean "economic miracle." In 1973 the South Korean government targeted automobiles as one of the priority industries for development. But the take-off of the South Korean automobile industry only took place in the early 1980s-- that is, during the years in which labor militancy, unionization and rising wages had come to characterize the Brazilian and South African industries. Like Brazil and South Africa at the time of their big spurts in automobile production, a labor-repressive regime in South Korea banned independent trade unions and strike activity, and helped keep wages abysmally low. The environment proved attractive for the three domestic conglomerates that had been given governmental permission to produce automobiles (Hyundai, Kia and Daewoo), as well as for their multinational corporate partners (Mitsubishi, Ford/Mazda, and GM/Isuzu, respectively) (Wade 1990: 309- 312; Deyo 1987).
South Korean vehicle output increased almost twelve-fold between 1977 and 1987 from 83,000 units to 980,000 units (Bloomfield 1991:29). Both US and Japanese multinationals moved into Korea through joint ventures. In 1981 GM obtained a 50 percent stake in Daewoo. Through this joint venture, GM began selling a cheap Korean-made car in North America as the Pontiac Le Mans. A 1985 agreement between GM and Daewoo calls for the latter to supply starter motors and alternators for GM's worldwide operations. In 1986, Ford paid US $30 million for a 10 percent shareholding in Kia and opened a Korean branch office of Ford International Business Development in order to develop sources of automotive components in South Korea (Gwynne 1991: 73-4).
As South Korean production reached one million automobiles annually (and surpassed Brazilian output), The New York Times filed the following report on August 12, 1987: "A wave of labor unrest is sweeping through this country . . . The unrest has shut plants in the nation's largest conglomerates, including Hyundai, Daewoo, Samsung, Lucky-Goldstar. Hyundai Motors, which manufactures the popular Excel, settled a dispute that had shut its factory but said labor troubles at its suppliers had forced the company to suspend car exports for now."
On August 18, 1987 the New York Times headline read "Workers Seize Hyundai plants in South Korea." And it was reported that: "More than 20,000 workers climbed over a barricade and occupied factory buildings and a shipyard operated by the Hyundai Group . . . Hyundai has been the most badly hit of the large conglomerates. At the heart of the struggle is the demand by Hyundai's workers to form their own unions. Hyundai has long taken a tough anti-union stance, and until the recent turmoil, Hyundai employees had no union." Then, on August 20, 1987, only eight days after the initial report, the Times carried a photograph with the caption: "Chung Ju Yung, in white suit, founder and honorary chairman of the Hyundai Group, toasting the agreement with leaders of the newly formed labor union in Seoul yesterday." The accompanying article was entitled "South Korean Company Agrees to Recognize Union."
Additional strikes in 1988 and 1990 confirmed the transition of the South Korean automobile industry to a new stage. With real wages rising at an average annual rate of 20% since 1987, and given the small size of the domestic market, it is not at all clear that the US and Japanese corporations on whom Korea depends for technology and investment, will continue to choose South Korea as a favored site for expansion. Recent moves (especially by Japan) into the ASEAN countries and China may be taken as further evidence for doubts about the South Korean industry's future.
F. The Trajectory of Global Fordism-- A Summary:
The global automobile industry has been characterized by a half-century-long trajectory in which mass production techniques and a characteristic form of mass production labor militancy has spread across the globe, from the US, to Western Europe, to rapidly industrializing semiperipheral states.
This trajectory has been characterized by successive cycles during which: (1) production concentrates in areas that are both close to large consumer markets for the industry's final product and that offer large supplies of relatively cheap and disciplined labor; (2) large, new working classes with extensive bargaining power form in these areas; (3) the workers use their disruptive power in an explosion of militancy that successfully gains union representation, rising wages and a degree of worker control on the shopfloor; and (4) management responds, in part, by reorienting investments toward new sites presumed to offer cheap and disciplined labor. This relocation weakens the labor movement in the sites of disinvestment, but strengthens labor movements in the new favored sites of investment, preparing the ground for a new wave of militancy, followed by another round of restructuring and geographical relocation.
US- and West-European-based automobile multinationals have been chasing the specter of cheap and disciplined labor around the world, only to find themselves continuously recreating militant labor movements in the new locations. And while following this strategy, they have been dramatically losing market shares to Japanese automakers. Have we reached, then, the historical limits of the trajectory of global Fordism?
On the one hand, the recent rapid expansion of automobile production in northern Mexico--where independent unions are not recognized and wage levels are far below those now paid in South Korea--could be interpreted as evidence suggesting a continuation of the dynamic of militancy and relocation. The approach followed here would lead us to expect a strengthening of independent workers' movements in Mexico, with a strong base in the auto industry in the north during the coming decade. (The first visible signs in support of this conjecture were the Ford strike at Hermosillo in 1990 and the VW strike at Puebla in 1992.)
On the other hand, a second trend has emerged in the late 1980s and 1990s that appears to be stronger and to point toward an exhaustion of the trajectory. That is, the automobile multinationals have begun to recentralize production in the core regions from which they had fled in the 1950s, 1960s (US) and 1970s (US and Western Europe.) In the case of the US, the southern Great Lakes states are once again a site of concentration of production for both the automotive assembly and automotive components industries--although former union strongholds are avoided and small towns with no automotive production history are preferred (Rubenstein 1992: 171-182). This trend toward a recentralization of production has been associated with the rise of "global Toyotism." Japanese automobile firms have been the leading agency in this transformation through a major wave of direct investment in the US in the 1980s (and to a lesser extent, in Western Europe.) This recentralization in the core has also been accompanied by transformations in labor-capital relations associated with "Toyotism," including the introduction of flexible work rules, just-in-time delivery systems and multi- layered subcontracting. And in both the US and Western Europe, these major changes in work rules and productive organization have been possible to implement thanks to the weakening of formerly militant auto worker unions through the relocation of capital and restructuring processes of the 1970s and 1980s.
This reconcentration in the core could be interpreted as the beginnings of a second long trajectory of militancy and relocation: that is, as mass production unions have been undermined in the core by the disinvestment of the previous decades, producers are once again choosing to relocate in an area of weak labor movements (e.g., small towns in the southern Great Lakes region.) However, the fact that this recentralization in the core has been accompanied by the introduction of new "post-Fordist" techniques of production raises doubts about whether we are witnessing the reinitiation of a similar long cycle, or a process of fundamental transformation--that is, a transition from global Fordism to global Toyotism.
II. LABOR UNREST UNDER GLOBAL TOYOTISM
The question is, how different are the dynamics of global Fordism and global Toyotism?
The fledgling Japanese automobile industry in the 1930s attempted to follow the essential principles laid out by the United States example: mass production techniques were introduced and a strategy of vertical integration of operations within the major automotive assembly firms was pursued. Toyota, Nissan and Isuzu made their own brakes, castings, and other subassemblies and critical components, as well as many simple parts; while Toyota and Nissan both set up captive suppliers of specialty steel (Smitka 1991: 6-7).
In the aftermath of the Japanese defeat in the Second World War, a continued strategy of vertical integration proved impossible. The automobile assemblers faced financial constraints that limited their ability to enlarge and expand their facilities. Equally, if not more important, the automobile assemblers faced militant workers' movements. In the late 1940s and early 1950s, layoffs of workers were frequent triggers for bitter strikes and other forms of unrest, while employment security and wage equality became central workers' demands (Okayama 1987).
Thus, when output began to expand in the 1950s, the assemblers avoided hiring new permanent workers, and instead adopted a policy of shifting work out to suppliers. "The primary reason for [this shift to] subcontracting," according to Smitka (1991:7), was "to avoid renewed conflict with militant labor unions . . ." By following a strategy of expanding output, not through vertical integration, but through a widening reliance on subcontracting, Toyota increased output fivefold during 1952-57 while its workforce rose only 15%. (Smitka 1991: 2). This reliance on outside suppliers allowed the automobile assemblers to guarantee permanent employment to their own workers.
At first, the workers (and profits) at subcontracting firms provided the buffer that protected workers (and profits) at the main assembly firms. However, by the 1960s, the contracting system had grown into a multilayered pyramid in which the primary subcontractors (those who sold directly to the assemblers) resembled the assemblers themselves, in terms of the use of advanced technology and the wage levels and employment security offered to their workers. The role of "buffer" in recession fell to a larger group of secondary suppliers (who sold to the primary suppliers) and tertiary suppliers (who sold to the secondary suppliers) (Smitka 1991).
This multilayered subcontracting system has allowed the Japanese automobile assemblers and their primary suppliers to develop relatively cooperative relationships with their employees, based on a commitment to lifetime employment and rising wages with age and tenure. They have therefore been able to minimize the costs associated with labor unrest since the upheavals of the early 1950s. This, in turn, has been a central component explaining the competitive success of the Japanese automobile industry on a world-scale since the late- 1960s.
In response to the competitive success of the Japanese, US-based and Western-European based automotive firms have attempted to selectively imitate Japanese methods--for example, by adopting the just-in-time system and flexible work rules but without employment guarantees at the assembly firms or primary suppliers. The results of these efforts to date show that the lower levels of labor militancy in Japan cannot be explained by lower levels of workplace bargaining power. In fact, the just-in-time system puts enormous, and perhaps even greater disruptive power in the hands of the workforce, as production becomes extremely vulnerable to strikes at suppliers as well as in transportation.
Indeed, where just-in-time methods have been adopted, without the adoption of employment guarantees and other concessions, the vulnerabilities of the system have been well demonstrated. As an October 8, 1992 (page 5) New York Times article noted: "Because the [US] automobile industry has largely adopted the Japanese system of keeping production inventories low, strikes at part plants have a much broader impact than in the past . . . The ability of the union to cripple production by putting only a few thousand workers on strike is a way of imposing costs on the company that may outweigh the savings from job cuts [through automation, outsourcing, etc.]" There are already numerous cases where transport strikes and supplier strikes have led to widespread assembly plant closings in the southern Great Lakes states under the just-in-time system. For example, "on the first day of a nationwide walkout by rail engineers in September 1982, GM was forced to close its St. Louis assembly plant because of lack of parts. By the third day, Janesville, Leeds, Lordstown, and Wilmington were operating on half days, and Chrysler president Iacocca wired the White House to urge intervention. On the fourth day, the US Congress [intervened and] ended the strike . . . " (Rubenstein 1992: 198).
Strikes at suppliers can lead to equally rapid disruption of production. For example: "When workers at Delco Electronics plant in Kokomo, Indiana, went on strike in November 1986, GM assembly plants around the country were closed. Because radios from the plant were being shipped on a just-in-time basis, assembly plants had little inventory on hand with which to work once the strike began. The strike was called to protest Delco's sourcing of some work to a plant in Mexico. GM felt compelled to return the work to Kokomo in order to get a supply of radios flowing into the assembly line plants again." (Rubenstein 1992: 198)
In sum, the just-in-time system continues to put as much--or more--disruptive power in the hands of workers as the more traditional Fordist organization of production. On the other hand, in Japan, where these methods were pioneered and have been developed to their fullest, workers have not routinely exercised these powers. The key seems to be the guarantee of lifetime employment to the upper rungs of the workforce (those with the most disruptive power) and a concentration of the pressures of low wages and insecure employment on the lower rungs of the workforce (those without significant disruptive power). However, can this process be maintained in the coming decades?
The success of the Japanese automobile industry has been founded on a Japan-based (rather than transnational) system of production. But as "Toyotism" achieved phenomenal success on a world-scale, it has been forced to convert itself into "global Toyotism." In response to protectionist measures in the US, as well as rising costs in Japan, the leading automobile assemblers and their suppliers have begun production in the US in the 1980s (Rubenstein 1992). At the same time, many of the firms (and/or functions) being performed by the lowest rungs of the Japanese subcontracting pyramid were moved off shore to low-wage countries in South East Asia (Machado 1992).
As production has moved off-shore, the post-war employment and wage system in Japan is coming under attack. Major corporations are attempting to reduce costs and increase efficiency in Japan by making merit pay a major component of total income. This will have several important consequences including, undermining the relatively egalitarian internal pay structure of the firms, eliminating the guarantee of upward movement in wages with increasing length of tenure, and introducing a divisive issue over which management exercises a subjective judgment (whose work merits more/less pay). At the same time, "Japan's most famous labor institution, lifetime employment," is also coming under attack.
"Companies are finding it hard to continue to keep 'window sitters', people who are given no useful work to do but collect a salary . . . More people are being asked to retire early, and some analysts expect that if the current slump continues large companies will announce sweeping layoffs, as in the United States" (New York Times, "Japanese Starting to Link Pay to Performance, Not Tenure," October 2, 1993, A1).
In sum, Japanese corporations may be moving their employment practices in the direction of the kind of Fordist practices that provoked major waves of labor militancy from the CIO struggles of the 1930s to the more recent labor upheavals in Brazil, South Korea and South Africa--and the late 1940s and early 1950s strike wave in Japan itself. The contradictions of success for "global Toyotism" are now showing on the horizon, and raise a number of questions about the future. First, can the automobile industry retain harmonious labor-capital relations in the face of wage freezes, merit pay distinctions and layoffs, or will the mid-1990s for the Japanese industry resemble the mid-1930s for the US industry? Second, as the Japanese automobile corporations decentralize production in an effort to lower costs and be close to large markets, will they be able to recreate the elements that fostered relative industrial peace in Japan from the mid-1950s to the present? Or, will they retrace the long trajectory of global Fordism by creating and strengthening new working classes in each new favored site of investment?
Beverly J. Silver
Department of Sociology
The Johns Hopkins University
3400 North Charles Street
Baltimore, MD 21218-2685
REFERENCES
Altshuler, Alan et al. (1984). The Future of the Automobile: The Report of MIT's International Automobile Program. Cambridge, MA: MIT Press.
Arrighi, Giovanni and Beverly Silver (1984). "Labor Movements and Capital Migration: The US and Western Europe in World-Historical Perspective," in Charles Bergquist (ed) Labor in the Capitalist World- Economy. Beverly Hills, CA: Sage.
Bloomfield, Gerald T. (1991). "The World Automobile Industry in Transition," in Christopher M. Law, ed., Restructuring the Global Automobile Industry. London: Routledge.
Crouch, Colin and Alessandro Pizzorno, eds. (1978). The Resurgence of Class Conflict in Western Europe Since 1968. (2 volumes) New York: Holmes & Meier.
Dassbach, Carl (1988). Global Enterprises and the World Economy: Ford, General Motors and IBM, The Emergence of the Transnational Enterprise. Ph.D Dissertation, SUNY-Binghamton.
Dubois, Pierre (1978). "New Forms of Industrial Conflict 1960- 1974," in Crouch and Pizzorno, eds., volume 2.
Dubofsky, Melvyn and W. Van Tine (1977). John L. Lewis: A Biography. Chicago: Quadrangle.
Economist Intelligence Unit (1990). Country Profile: Brazil, # 1.
Edwards, Richard (1979). Contested Terrain: The Transformation of the Workplace in the Twentieth Century. New York: Basic Books.
Gwynne, Robert (1991). "New Horizons? The Third World Motor Vehicle Industry in an International Framework," in Christopher M. Law, ed., Restructuring the Global Automobile Industry. London: Routledge.
Humphrey, John (1982) Capitalist Control and Workers' Struggle in the Brazilian Auto Industry. Princeton: Princeton University Press.
__________ (1987) "Economic Crisis and Stability of Employment in the Brazilian Motor Industry," chapter 7 in William Brierley, ed., Trade Unions and the Economic Crisis of the 1980's. Gower: Aldershot, pages 119-131.
Landes, David (1969). The Unbound Prometheus. Cambridge: Cambridge University Press.
Laux, James M. (1992). The European Automobile Industry. New York: Twayne Publishers.
Litvak, Lawrence et al. (1978). South Africa: Foreign Investment and Apartheid. Washington D.C.: Institute for Policy Studies.
Machado, Kit G. (1992). "ASEAN State Industrial Policies and Japanese Regional Production Strategies: The Case of Malaysia's Motor Vehicle Industry," in Cal Clark and Steve Chan, eds., The Evolving Pacific Basin in the Global Political Economy. Boulder: Lynne Rienner Publishers.
Moreira Alves, Maria Helena (1989). "Trade Unions in Brazil: A Search for Autonomy and Organization," in Edward C. Epstein (ed.), Labor Autonomy and the State in Latin America. Boston: Unwin Hyman, pages 39-72.
Myers III, Desaix et al. (1980). US Business in South Africa: The Economic, Political and Moral Issues. Bloomington: Indiana University Press.
Okayama, Reiko (1987). "Industrial Relations in the Japanese Automobile Industry 1945-70: the Case of Toyota," in Tolliday and Zeitlin, eds., pages 168-189.
OECD (1981). International Investment and Multinational Enterprises: Recent International Direct Investment Trends. Paris.
Pollack, Andrew (1993). "Japanese Starting to Link Pay to Performance, Not Tenure," New York Times, October 2, 1993, A1.
Rollier, Matteo (1986). "Changes in Industrial Relations at Fiat" in Otto Jacobi et al. (eds.), Technological Change, Rationalisation and Industrial Relations. London: Croom Helm.
Ross, Robert J.S. (1982). "Capital Mobility, Branch Plant Location and Class Power," paper presented at the Annual Meeting of the Society for the Study of Social Problems, San Francisco, September.
Rubenstein, James M. (1992) The Changing US Auto Industry: A Geographical Analysis. London: Routledge.
Silver, Beverly (1992). Labor Unrest and Capital Accumulation on a World Scale. Ph.D Dissertation, SUNY- Binghamton.
Smitka, Michael J. (1991). Competitive Ties: Subcontracting in the Japanese Automotive Industry. New York: Columbia University Press.
Southall, Roger (1985) "Monopoly Capitalism and Industrial Unionism in the South African Motor Industry," Labour, Capital and Society 18:2, November, 304-42.
Tolliday, Steven (1987). "Management and Labour in Britain, 1896-1939," in Tolliday and Zeitlin, eds., pages 29-56.
Tolliday, Steven and Jonathan Zeitlin, eds. (1987). The Automobile Industry and Its Workers: Between Fordism and Flexibility. New York: St. Martin's Press.
Volpato, Giuseppe (1987). "The Automobile Industry in Transition: Product Market Changes and Firm Strategies in the 1970s and 1980s," in Tolliday and Zeitlin, eds., pages 193-223.
Wade, Robert (1990). Governing the Market: Economic Theory and the Role of Government in East Asian Industrialization. Princeton: Princeton University Press.
Comments
Silver's always a good read.
Silver's always a good read. Thanks for posting!