Fascinating pamphlet by Solidarity on the informal workers struggle against the frenetic pace of work at a General Motors plant, and the later co-optation of the struggle by the auto workers union.
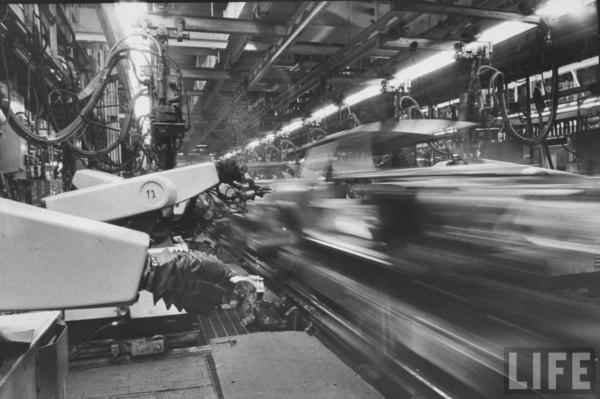
This pamphlet is an attempt to document some important tendencies developing in the motor car industry but which are relevant to modern production as a whole. We feel these trends have important political consequences for revolutionary socialists.
Although we will often refer to the car industry in general our main concern is to bring to industrial militants and others the specific example of what happened at the General Motors plant in Lordstown (Ohio) during 1971-72.
The Lordstown story is a clear example of working class resistance to work itself. This resistance, which we want to describe in some detail, is a very welcome tendency. It must be looked at in a very concrete way, if by socialism we mean something more than just a re-arrangement in the distribution of surplus value, which would leave the technological infrastructure of industry unchanged.
New Tendencies in Production
In the past workers have tended, like Oliver Twist, simply to ask for more. Now, on an increasing scale, they are moving away from traditional trade union demands. They are beginning to challenge some fundamental aspects of the work process. The old illusions about 'a fair day's work', about 'doing a good job' and about 'loyalty to the company' are happily dying.
At Lordstown wages were not an issue. Workers were used to regular wage increases. But despite these their life at work had deteriorated. But even if conditions remain the same workers themselves do not. They are increasingly rejecting the industrial prison.
This the real cause of the crisis in production today. It is an attitude which is beginning to question some of the underlying assumptions of modern society and several of its basic values and priorities. This is potentially a far more fruitful area for the development of socialist consciousness than the traditional marxist chimera of the great slump which, it is assumed, will somehow radicalise the workers and propel them, if not into socialism, at least into the arms of some vanguard party.
What we are witnessing today is something very different. The cultural attitudes brought about by a steady and sustained increase in the standard of living are proving most subversive to the smooth functioning of modern capitalism. The desire for more freedom is difficult to coopt. Having by and large secured the basic necessities of life, workers are beginning to think about a more human existence in work. Some are even beginning to question the present structure of work. How much work is necessary? Of what kind? Why? The system is still producing its own gravediggers but they are considerably plumper than envisaged by Marx, and are digging the system's grave in new .ways and with tools far more sophisticated than simple spades.
Lordstown was not unique. It was symptomatic of a process which is going on to a greater or lesser extent in all industrialised countries. This process has reached its most acute form in the motor industry. It does not express itself simply in the form of strikes but manifests itself over the whole range of relationships within the factory.
For years the motor industry has become increasingly dependent on migrant workers. These come either from abroad or from depressed areas within the same country. The migrant labour Force tends to be concentrated initially in the more unpleasant jobs, for example on the crucial assembly lines. Southern Italians, black workers in the USA, Finns, Yugoslavs, Turks, Portuguese and Spaniards are increasingly dominating the sharp end of motor manufacture. While this is an important fact, we do not share the divisive view - put forward by various maoid(maoist)tendencies - that immigrants are the 'new vanguard' of the working class. While it is true that on some issues migrant workers are in the lead, in other cases this is far from being the case. The real common denominator to the new types of struggle we will be describing is that it is the production workers-those on the line- who are showing the way, and doing this irrespective of their country of origin.
Sometimes, instead of using migrant workers, car companies move the factories-particularly assembly operations-to areas with high unemployment, or more importantly to regions with relatively low levels of job organisation. But this is just a palliative. It has not solved the main 'problem', namely that workers are less and less willing to accept the man-killing work pace. The resistance to production is shown by the universal tendency for an increasing proportion of strikes to be on issues other than wages, issues such as speed-up, victimisation of militants, and manning of machines .
Another way this tendency is expressing itself is in a very high, and escalating, rate of labour turnover According to official US Government statistics, workers in 1966 were staying an average of 4.2 years in each job. By 1969 this had fallen to 3.9 years. For young people under the age of 24 the average length of stay was 0.7 years (see 'The Prison Factory', New Left Review, May-June 1972). These figures have continued to drop.
Another yardstick of changing attitudes to work is provided by the figures for absenteeism At GM absenteeism jumped from 2% in 1960 to 6% in 1970 ('GM:The Price of Being Responsible', Fortune, January 1972). It rose another 11%, in 5 months, in early 1972. According to Malcolm L. Denise, Vice President of Labour Relations at Ford Motor Company, the rate of absenteeism for hourly-rated workers at Ford in the USA 'more than doubled' between 1960 and 1968. Every day at GM 5% of workers are absent 'with no explanation whatsoever' - On Mondays and Fridays the percentage doubles, 10% are out (Fortune, June, 1970). The Wall Street Journal of September 29, 1970 quoted a GM statement: 'many workers who become ill in midweek don't come back to work till the following Monday. Now it's just not normal that everybody should recover the same day!' At Chrysler absenteeism has reached 18.6%. During the summer months, at Lordstown, it had reached as high as 20%. When a worker at Lords town was asked 'What is it like on a Monday, in summer, then?', he replied, 'I don't know, I've never been in for one'. (Sunday Telegraph, December 2, 1973) Another worker, when asked 'how come you're only working four days a week?' replied, 'because I can't make enough money in three'. (Newsweek February 7, 1973)
Absenteeism has important effects on production. A local Lordstown official put it this way: 'When absenteeism gets really high, they go on general break and bring in the relief men. If that's not enough they pull in everybody they can get--cleaners, drivers, maintenance men, anybody. They're supposed to have 3 days' training, but they just shove them in as welders, though they may never have held a gun before in their lives. Then, of course, the vehicle is garbage.' This kind of thing can happen 'a couple of times a week or more'. (Sunday Telegraph, December 2,1973)
The same problems exist in other parts of the world. Fiat in Italy admits to an absentee rate of 18% (see 'The 30,000 spanners in Mr Fiat's works' by Mary Kenny, Evening Standard, March 7,1973). At Volvo in Sweden absenteeism is 15%. At Saab- Scania it is 25% (BBC-2, 'Money at Work', February 9, 1973). And it was these latter figures which were the specific reason for these Swedish firms to turn towards 'job enrichment'. In Britain the figures 50 far tend to be lower - about 6% - although at one unnamed motor plant it is as high as 30% (BBC-2, op. cit.). The situation is rapidly getting 'worse' - or 'better' - depending of which way you look at it.
The cost of all this to management is enormous. For example in 1971, in the Oldsmobile Division of GM alone, the cost of absenteeism (considering only fringe benefits) was about $50 million. Turnover costs were another $29 million (Detroit Free Tress, November 12, 1972, quoting from 'GM Personnel Development Bulletin'). GM's labour costs rose from 29.5% of sales in 1962 to 33% in 1972 ('GM: the Price of Being Responsible', Fortune, January 1972). The firm's investment per worker rose from $5,000 in 1950 to $24,000 in 1969. James Roche, Chairman of GM, commenting on these figures, said: 'tools and technology mean nothing if the worker is absent from his job' and went on to stress the domino effect of absenteeism on co-workers, on quality and efficiency, and on other GM plants with related production. 'We must receive a fair day's work for which we pay a fair day's pay' ('Blue Collar Blues', Fortune, July 1970).
Even politicians are becoming aware of the problem. Senator Edward Kennedy commented on 'the effect that worker discontent has on productivity.' The National Commission on Productivity states that in at least one major industry, absenteeism increased by 50%, worker turnover by 70%, worker grievances by 38% 1 , and disciplinary lay-offs by 44% in a period of 5 years. How much does that cost the economy in terms of low productivity?' (Minutes of Senate Subcommittee on Employment, Manpower and Poverty, July 25,1972).
Absenteeism and labour turnover are simply the statistically quantifiable tip of a vast iceberg. They are associated with 'tardyness in starting work', shoddy work, bloody-mindedness, and a simple lack of enthusiasm for production. What happened at Lordstown was a symptom of a far wider and growing problem of capitalism: the fact that more and more people are questioning established authority relations. This situation was nowhere more clearly shown than by the struggle of workers against the General Motors Assembly Division (GMAD).
Lordstown: the Plant
In 1970, the re-equipped General Motors car assembly plant at Lordstown (Ohio) started producing the sub-compact Vega model, aimed to compete with imported cars. 2
The plant had a target production of 400,000 vehicles a year-Because of the success of the Vega, a new assembly plant (with a planned capacity of 150,000 vehicles per year) was later built at Sainte-Therese, Quebec, Canada.
When completed Lordstown was the world's most automated motor plant. 3 It had 26 ##unimate industrial robots for welding operations. These perform about 520 welds on each car. (Time Magazine, February 7, 1972). There are only some 800 machines of the type in the USA. Britain has 50, West Germany only 20 (Times Business News, March 30, 1973) There are 18 of these machines in the Mirafiore plant of Fiat in Turin. 4
Sub-assembly areas, conveyor belts and quality control at Lordstown are all computer directed; this results in an estimated saving of final assembly labour costs of 10% ('GM: The Price of Being Responsible', Fortune, January 1 972). Investment totalled over 100 million dollars. At the same time the Company incorporated enormous design rationalizations in the new model. For example the Vega body is assembled from only 578 parts, compared with the average for American cars of 996: a 43% reduction. ('The Men Won't toe the Vega Line', BJ. Widick, The Nation, March 27, 1972).
The result of this investment and rationalization was a track speed of 101.6 cars per hour: one vehicle produced every 36 seconds, by far the fastest rate in the world. For comparison the Cortina line at Dagenham, at just over 70 cars per hour, is the fastest in Britain. Ford (Cologne) has the highest track speed in Germany with 72 cars per hour, compared with 36 cars per hour. off each line at Volkswagen. And the Lansing (Michigan) GM plant turns out 91 Oldsmobiles an hour, the second highest rate in the world.
The consequences of this high track speed are worth looking at. Instead of the 'normal' minute to complete an operation, which is bad enough, the worker has only 36 seconds.
Even if the amount of work to be done is reduced, the job is intolerable, It is even impossible for the worker to pace himself and 'save up' a few seconds by working flat out, so he can scratch himself or whatever, which is sometimes possible on a slower track. The addition of a single spot weld, nut, bolt, or washer to an operation cycle can be the last straw. Adequate manning is essential to make this sort of tempo remotely bearable. Relatively minor changes of job-mix or workload can lead to explosive situations. 5
An example of the amount of work required at Lordstown was given by Stanley Aronowitz in his book False Promises. Within a minute on the line, a worker in the trim department had to walk about 20 feet to a conveyor belt transporting parts to the line, pick up a front seat weighing 30 pounds, carry it back to his work station, place the seat on the chassis and put in four bolts to fasten it down by first hand-starting the bolts and then using an air gun to tighten them according to standards. It was steady work when the line moved at 60 cars an hour. When it increased to more than 100 cars an hour, the number of operations on this job were not reduced and the pace became almost maddening. In 36 seconds the worker had to perform at least eight different operations including walking, lifting, hauling, replacing the carpet, bending to fasten the bolts by hand, fastening them by air gun, replacing the carpet again and putting a sticker on the hood. Sometimes the bolts fail to fit into the holes; the gun refuses to function at the required torque; the seats are defective or the threads are bare on the bolt. But the line does not stop. Under these circumstances the workers often find themselves 'in the hole', which means that they have fallen behind the line. 'You really have to run like hell to catch up, if you're gonna do the whole job right', said one operator named Jerry. 'They had the wrong sized bolt on the job for a whole year. A lot of times we just miss a bolt to keep up with the line.'
To get this sort of productivity, supervision has to be intense. For example, a worker describes how you go to the bog. 'You just about need a pass to piss. That ain't no joke. You raise your little hand if you waist to go wee-wee. Then wait maybe half an hour 'till they find a relief man. And they write it down every time too cause you're supposed to} do it in your time, not theirs. Try it too often and you'll get a week off (Barbara Jarson, 'Luddites in Lordstown,' Harper's Magazine, June 1972).
Lordstown: the Workers
General Motors selected the Lordstown site carefully. As one commentator put it: 'It became obvious why GM picked Lordstown for their super production plant. Although Lordstown is in the centre of a heavily industrialized area (to the West is Cleveland, to the East is steel-making at Youngstown. And across Lake Erie is the automaking centre at Detroit) there is no actual working class community. Many of the workers, 500 of them women, commute from as far away as Cleveland and Pittsburgh.' (Industrial Worker, April 1972). Many of GM's plants throughout the world seem to be sited in the same sort of isolated location.
GM carefully screened its new work force. This was not only younger than average (to keep up with the man- and woman-killing pace) but also rather better educated than usual. A very large majority of workers came from rural areas. Derogatory remarks about 'Hillbillies' occur again and again ('Swedebasher' is the nearest British equivalent). Yet it was precisely this group which in many ways spearheaded the struggle, when it came.
Because the plant started more or less from scratch. seven years ago, the work force was, from the onset, relatively young. The average age was about 25 (various sources gave the average as being between 23 and 28). Much has been made of this but in fact there is an increasing tendency in all the industrialised countries for the age of workers in mass production industries to decline. For example, the median age of hourly employees of the Ford Motor Company in the USA, in 1968, was 35.4. This was 3.5 years less than the median age in 1964 (Speech by Malcolm L. Denise. Vice President of Labour Relations for the Ford Motor Company. November 10, 1969). Much has been made by left-wing commentators of the fact that Gary Bryner the president of local 1112 of the UAW which covers Lordstown was only 29 - as if youth were some sort of guarantee against bureaucracy!
The rigid seniority system which they have in the USA means that longer established workers get the better and higher paid jobs as well as a number of other privileges. They feel they have something to defend against other employees. Young, black and immigrant workers, whose numbers are rapidly increasing due to a soaring rate of labour turnover, tend to be concentrated on the less pleasant but often crucial jobs. Many work on the assembly lines, often on the second shift. This explains the often marked difference between shifts almost amounting at some plants - but not at Lordstown - to 'civil war'.
This new type of worker is creating serious problems for both bosses and union leaders. The views of management were expressed in a very perceptive way by Malcolm L. Denise, Vice President of Labour Relations for the Ford Motor Company at a meeting of Executives on November 10, 1969:
'A few years ago Reuther and his Executive Board (the leadership of the United Auto Workers) could map the union's course with confidence. Today they seem uncertain. The reason is a big influx of a new breed of union member - a younger, more impatient, less homogeneous, more racially assertive and less manipulable member whose attitudes and desires admittedly are not easily read by a sixty-two-year-old labour leader.
For that matter, those attitudes and desires are not always so easily understood by many of us here, either. While some of the problem-employees have come to us through our efforts to hire the so-called hard-core unemployables, most of them are simply a reflection of the labour market we've been drawing from, for our normal hiring, during recent years.
The other root cause of our present difficulties with the workforce might be termed a general lowering of employees' frustration tolerance.
Many employees, particularly the younger ones, are increasingly reluctant to put up with factory conditions. Despite the significant improvements we've made in the physical environment of our plants. Because they are unfamiliar with the harsh economic facts of earlier years, they have little regard for the consequences if they take a day or two off.
For many, the traditional motivations of job security, money rewards, and opportunity for personal advancement are proving insufficient.
Large numbers of those we hire find factory life so distasteful they quit after only brief exposure to it. The general increase in real wage levels in our economy has afforded more alternatives for satisfying economic needs.
There is also, again especially among the younger employees, a growing reluctance to accept a strict authoritarian shop discipline. This is not just a shop phenomenon, rather is a manifestation in our shops of a trend we see all about us among today's youth.
As many of you are only too aware, the new work-force has had a costly and unsettling impact on our operations.
More money,time and effort than ever before must now be expended in recruiting and acclimatising our quality control programs have been put to severe tests; large numbers of employees remain unmoved by all attempts to motivate them; and order in the plants is being maintained with rising difficulty.’
It is amazing how much more perceptive management is to the real problems of modern industry than are the traditional revolutionaries, who can only think of the working class in terms of wages and consumption. Modern capitalism can, by and large, cope with the traditional type of economic problem, for instance those dealt with by Marx, it can continue to develop production. It is in difficulties, however, when confronted with a massive resistance to its values, priorities and whole pattern of authority. Such a resistance can have both economic and other repercussions.
Denise's speech has never been officially published. Our text is drawn in part from an internal document called 'Democratising the Workplace' produced by the UAW. It was written by Irving Bluestone, the Union's Vice-President Significantly, Bluestone omits the first section dealing with the UAW itself! This part came from Stanley Aronowitz's book, False Promises. 6
That this is not simply a bosses' problem was expressed by youthful Gary Bryner, President of the main Lordstown local of the UAW, in his evidence to the US Senate Sub-Committee on Employment, Manpower and Poverty on July 25, 1972 (Senator Edward Kennedy was presiding):
'There are symptoms of the alienated worker in our plant - - - Absentee rate, as you said, has gone continually higher. Turnover rate is enormous. The use of alcohol and drugs is becoming a bigger and bigger problem. So has apathy within our union movement towards union leaders and towards the Government ... (The worker) has become alienated to the point where he casts off the leadership of his union, his Government... He is disassociated with the whole establishment. That is going to lead to chaos
Bryner went on to describe how he saw the role of the union:
'We have got to take the quality of life issue, we have got to meet it head on. and we have got to reach out to the people of this country who are the mainstream of our economy who do take the tax burden. And if we alienate them to government, to the union leadership, where in the hell are they going to go? They are going to go with a radical group. They are going to throw off every part of the establishment and some place else'
This wasn't a Solidarity meeting where these developments were being welcomed, as a vindication of our whole analysis. It was an official US Senate Committee, recording the facts with obvious concern!
Lordstown: the Local Union
The Lordstown facility originally consisted of two separate GM plants - the Fisher Body Plant and the Chevrolet Assembly Division Plant. Each was organised by separate UAW locals: local 1112 with 6,800 members and local 1714 with 1,800. Each local had separate agreements with GM.
The first major difference with Britain is factory organisation. There is no autonomous shop stewards set-up as such in the US motor industry. Instead of stewards, there is a system of full-time committee-men, in a ratio of about 1 committee-man to 250 workers. These committee-men are generally completely integrated into the local union hierarchy, which in turn, within narrow limits, is under the thumb of the international union. There are 34 full-time committee-men at Lordstown. This doesn't include those officials directly employed by the local. These union retainers form the core of the unions goon squads, which have been increasingly used against the left. The Chairman of the Lordstown Works Committee, Barker, was an ex-marine prison guard.
Autonomous combine committees are unknown in the American motor industry. Everything is done through the UAW (or to give it its full name the United Automobile, Aerospace and Agricultural Implements Workers of America). The union 'organises' everyone, including skilled workers and white collar workers. Industrial unionism in this context means that workers are faced with a single powerful bureaucracy. Those who continue to parrot earlier calls for ‘industrial unionism' would do well to ponder this fact.
Union dues are paid through the check-off system. They are deducted from the pay packet by the company. There is a closed shop. Union dues are two hours pay per month. In the case of Lordstown, until mid-1973, there was another dollar a month towards the locals building fund. Worker participation in the affairs of the local is as low as it is in Britain. The fact that 250 out of 7,000 attended a monthly meeting was specially noted as being exceptional in the local's journal (See Here, February 1973). Attendance at this meeting was much higher than usual because there was a protest turn out, which ended the dollar-a-month payment to the building fund!
There are several 'rank and file' caucuses of various types and political complexion. The most important of these are generally oriented to capturing positions and passing resolutions. They are consequently not going to endanger their candidates by extra-union activities, like creating alternative rank and file links, or developing a serious critique of trade unionism as such, or drawing any real lessons from Lordstown.
The most significant of these caucuses in the UAW is the United National Caucus (UNC), led by a triumvirate of Art Fox, Jordan Sims, and Pete Kelley. The UNC is a united front of a number of smaller caucuses. Several 'radical' groups participate in it. Its programme is a rag-bag of wishy-washy, opportunist, lowest-common-denominator demands, salted with vague appeals for 'union democracy' through a system of referendum elections of UAW officials. Sims, co-Chairman of the UNC, is quoted as saying 'to make your America great, to make it productive, to make it serve you and benefit you, you're not going any place without me or something like me (1972). Art Fox said, 'We are fighting to save our union, and in a broadest sense, to save our Country. (1972) (Quoted from Workers Vanguard, June 1972) Such people see themselves as alternative 'left-wing' trade union leadership.
The role of the various 'radical' groups is worth looking at in this context. The main Trotskyist groups (SWP, WL, IS) have, incredibly, as their main demand the creation of an American Labor Party, led by the union bosses, rather on the pattern of its British equivalent! This, of course, parallels their British fellow-thinkers' support for the Labour Party. Most of them have a perspective of reforming the UAW - a very unlikely prospect. Meanwhile back inside the factories, each struggle takes place in isolation and without preparation.7 Another aspect of the American industrial scene is the extreme emphasis on seniority. Everything, from laying off to promotion, from better jobs to overtime, is determined by length of service. This often creates a core of privileged workers within the plant, who have been through it all themselves and who feel they have something to protect against other workers.
Another appalling aspect of the UAW agreements is compulsory overtime. In fact the current local agreement at Lordstown (local agreements between GM Assembly Division and Local 1112, March 24, 1972) states that 'any hours beyond eleven, will be on a voluntary basis. In the event that it is necessary for management to schedule or work beyond eleven hours and cannot obtain the required manpower on a voluntary basis, management can require the low men on each Equalisation Group to work.' Massive amounts of overtime are in fact worked - well over 20 hours a week on some cases. The 10 hour day was normal practice. Failure to work overtime, for example to come in on a weekend, counts as absence and the worker is subject to disciplinary action.
Wage rates were not at issue at Lordstown during the GMAD dispute. The hourly rates being paid between November 1972 and September 1973 were:
Job Title - $ - £ 8
- Vauxhall(UK) Equivalent
Janitors 4.22 1.74 80p
Most production workers 4.62 1.90 90½p
Production repairmen & inspectors 4.72 1.95 93p
Dingmen 4.99 2.06 93p
Millwrights, pipefitters, carpenters 5.65 2.33 97/102½p
Electricians, fully skilled welders 5.81 2.40 97/102p
Average earnings can be high. In one case James Edwards, aged 26, worked 12 hours a day, 7 days a week, right up to the GMAD takeover. His take-home pay for the year was $15,000 (Militant, March 31, 1972). While this figure was well above the norm, many workers earned $13,000.
The Coming of GMAD
From June 1970 to July 1971 GM's profits on invested capital was 'only' 9.8%, having fallen from 16.9% in 1969. This was far below the record year of 1965, when GM had a 25% return. 9
GM decided to take advantage of the 'recession' to introduce a massive 'rationalisation' and cost-cutting programme. In October 1971 GM consolidated its auto assembly plants into the General Motors Assembly Division - GMAD for short. Until then the various divisions (Buick, Cadillac, Oldsmobile and Pontiac) had been autonomous. The UAW gave prior agreement both to GMAD and to a reduction of the work force. 10
GMAD took over 18 assembly plants, leaving only the 4 'home' plants at Detroit untouched. The new division, which was described by Leonard Woodcock, President of the UAW, as 'the roughest and toughest in GM', immediately embarked on a brutal campaign to increase productivity. Aiming at a massive increase of production, with an actual reduction in the number of workers, GM employed 422,000 men in the first quarter of 1972. This was down from 443,000 in 1971. 11
On a plant level GM's tactics meant a massive reduction in the number of production workers. At the Norwood (Ohio) plant nearly a third of the workforce were laid off But the track speed remained the same. At the St. Louis plant the number of workers was reduced from 8,200 to 6,500 while the line speed was increased from 35 to 45-47 cars per hour (On the Line, a rank and file paper, no. 9). 12 Lordstown was no exception. When GMAD took over, all previous agreements were nullified. The two plants were amalgamated. 800 workers were laid off (about 10% of the total work force). 13 The speed of the line remained the same. GM justified this with one of the most cynical explanations ever. The firm claimed it had added operations to men's work 'in the hope of alleviating the mind-numbing boredom of endlessly doing just one task' (Times, February 7, 1972). Job enrichment, as usual, really means boss enrichment. An example of the sort of savings that GM aimed to get out of the Lordstown operation was given by Jim Jacobs (Cleveland Plain Dealer January 23, 1972) 'GM calculated that if each worker at Lordstown worked one half of a second more each hour, the Company would save one million dollars a year, or 0.05 per cent of its annual profit after taxes.' The charming way UMAD operates was described in a letter to a British trade unionist by Frank James, Administrative Assistant to Irving Bluestone (dated March 22, 1973) (see also Newsweek, October 23, 1972)
'In the General Motors Assembly Division there are eighteen plants and the plant manager who ranks no. 18 has a poor and short life expectancy. He must better his position or else he is replaced.
Even if the plant ranks no.10 but a department such as the Paint Department ranks no.18 among all the Paint Departments, then the Superintendent of the Paint Department is not a good risk for a real estate mortgage. He too, must better his position or else. He must eliminate manpower and cut costs.
This fierce competitive drive extends all through the assembly chain. Ultimately the assembly line worker catches the brunt of this never-ending cycle of "improve or else".'
The situation at Lordstown had been bad enough already. The offensive by GMAD brought to the boil one of the most sustained campaigns of informal in-plant resistance ever to have been documented.
Workers Playtime
In the winter and spring of 1971-72, under the pressure of increased workloads, workers (often the usually compliant 'hiilbillies') began to pass cars down the line with the odd bolt or minor part missing. The movement rapidly gained momentum. In one case a car came down the line with the body shelf neatly covering a pile of unassembled parts. Alvin B. Anderson, Manager of Lordstown, stated 'we've had cases of engine blocks passing 40 men without them doing their work.' (Cleveland Plain Dealer, January 23, 1972)
At this stage workers left out one car in 10, or one car in 20.This meant a reduction of 5 or 10 cars per hour. Fortunately the situation is not quite as simple as that, for what we have described assumes that all workers are co-operative enough to pick the same vehicle not to complete their operation on. Any reasonable well-run campaign should leave at least 80% of cars incomplete. And that's not counting those which have had secondary operations completed when the primary job isn't completed, which of course means that the 'completed' job has to be taken to pieces again.
The situation developed rapidly. The company started suspending and disciplining men right and left and generally tightening up. Many suspected that the company was attempting to provoke a strike to lance the boil (see UAW Local 1112 leaflet, dated January 18, 1972). The struggle inside the plant escalated. Soon Time magazine was alleging (February 7, 1972) that ...
'somebody deliberately set fire to an assembly line control-box shed, causing the line to shut down. Autos regularly roll of the line with slit upholstery, scratched paint, dented bodies, bent gear-shift levers, cut ignition wires, and loose or missing bolts. In some cars. the trunk key is broken off right in the lock, thereby jamming it. The plant's repair ht has space for 2.000 ant its. but often becomes too crowded to accept more. When that happens, as it did last week, the assembly line is stopped and the workers are sent home, payless.'
Anderson, GM's Lordstown manager, gave some further examples of sabotage (The Times, March 1 6, 1 972) such as caving-in of radios, scratching of instruments in the instrument panels... tearing glove-box doors, etc.' 14
But this management-inspired hysteria was not the whole story. There was no doubt that they were boosting the sabotage' aspect of the struggle inside the plant. for public relations purposes. For example, simply missing an operation was described as 'sabotage'. Modern Times, a rank and file paper from Cleveland, had an interview with several Lords-town workers (February 1972).
MT: 'What about the sabotage charges?'
Don: 'I've had a buddy come up and tell me that the parts have come in packed but already broken, and this foreman just went up and tagged them "sabotage". The part had already been broken.'
On the other hand another Lordstown worker was quoted as follows in a sympathetic article by Barbara Garson (op.cit.):
'Sabotage? Just a way of letting off steam. You can't keep up with the car so you scratch it on le way past. I once saw a hillbilly drop an ignition key down the gas tank. Last week I watched a guy light a glove and lock it in the trunk. We all wanted to sec how far down the line they'd discover it ... If you miss a car they call that sabotage. They expect the 60 second minute. Even a machine has to sneeze. Look how they call us in weekends, hold us extra, send us on and off.
The struggle really began to bite. Substandard Vegas began to reach the dealers who screamed like stuck pigs. The media got hold of the story (Cleveland Plain Dealer February 20. 1972). By January, GM estimated that they had lost production of 1 2,000 Vegas and 4,000 Chevrolet trucks, worth 45 million dollars. On the other hand the men had gone for weeks without full wage packets or even without a full day's work having been sent home early when the 2,000 space car park was full of uncompleted vehicles. Nine hundred men had been disciplined. There were 5.000 unprocessed grievances (failures to agree). Discipline was intense. A worker was sent home for being one minute late (Newsweek,Febuary 7. 1972). Another was suspended for farting in a car. Yet another for yodelling ( Barbara Garson, op. cit.). Yet another was sent home for going for a drink of Tensions had reached fever pitch.
The Union Takes Over
On February 1 the local held a strike ballot. Eighty-five per cent of the membership voted, of which 6,350 (97%) voted for the strike and 203 against. The strike started on March 2, 1972. Unlike the foregoing struggle it was completely dominated by the UAW national leadership.
One of the 3% who voted against the strike-an older man who had worked at other car factories-put it prophetically:
'I seen it before. The international (union) is just giving them enough rope to hang themselves. They don't ever take on speed-up or safety. And they don't ever help with any strike they didn't call. Like I was saying, they see a kicky young local, so they go along. They authorize the strike But it's just giving you enough rope to hang yourself. So they let 'em go ahead. But they don't give 'em no help. They don't give 'em no funds. They don't even let the other locals come out with you. When it conies to humanizing working conditions you might as well be back before there was any unions. So the strike drags on. It's lost. Or they 'settle' in Detroit. Everybody says: "there, it didn't pay."
(Barbara Garson, op. cit.)
The strike lasted 22 days. It was exactly like most other strikes: a couple of pickets on the gate, the rest of the work force following it all on the TV. With 'task forces' of officials, moved in from outside, making sure that things stayed under control.
One commentator put it as follows:
We approached two workers on the picket line when a union bureaucrat drove up. He immediately told us "no pictures" and that we should leave. We tried to explain that we drove down from Chicago, and that many people were concerned about the strike. It was obvious, though, that his orders came from the top. It was ironic that fur 362 days a year GM pushed this union bureaucrat around. On those rare times his workers stopped production he acted like he owned the plant.
(Industrial Worker, April 1972)
These visitors were lucky. Later in 1972 at a strike at a GM plant in St. Louis, members of the local Rank and File caucus were set upon by a squad of 20 UAW goons on three separate occasions, and a member of the American I.S. was beaten with a lead pipe when he tried to sell the paper Workers Power.
More recently, at the large Chrysler Mack Avenue stamping plant at Detroit, a black militant called William Gilbreth was sacked. He returned to the shop and sat down on the assembly line (a technique of struggle worth considering). Two security guards tried to throw him out. In the ensuing fight they were injured. As a result the plant was closed down for 2 days and nearly 70 other workers were sacked.
When the plant reopened unofficial pickets attempted to close the plant. But Douglas Fraser, head of the UAW's Chrysler department, brought in about 1,000 UAW thugs armed with baseball bats to keep the plant open. 'These aren't union goons' said a Chrysler official 'these are labour statesmen.'(Newsweek, September 3, 1973) (For a detailed report on this struggle see Solidarity, vol Vll, no.9)
The actions of these gangs of 'labour statesmen' closely parallels the role of the Stalinist hacks of the CGT in France in 1968. Which only goes to show the universal role of trade union bureaucrats, whether Communist or business, in splitting and dividing workers.
When the settlement came the UAW claimed it as a complete victory. All but 130 of the 670 men laid off were reinstated. Eight hundred of the 1,200 disciplinary suspensions were cancelled. And the workers involved were paid for the lost time. Twelve hundred of the outstanding grievances-mostly about works standards-were settled. Inverse Seniority was introduced, which meant that high seniority employees could opt for lay-off (at 95% of their basic weekly wage) in the place of a worker of lower seniority. But all the fundamental issues about which the struggle had started (speed of the track, the work load and related questions) were left fundamentally as before. On March 27 1972 2,040 workers voted to return to work. Nine hundred and forty voted against. The struggle inside the factory went on.
One worker commented bitterly:
Before the strike the union local was in favour of not working faster than you could. Now people are afraid not to work. The union and the Company say everything's settled. But we had a strike. What did we achieve for it? We got the shaft in the last strike. We didn't know what we won and what we lost. When we asked the union we wouldn't get answers.
(Aronowitz, op. cit.)
Following the Lordstown struggle there were a series of isolated struggles at other GM plants. Out of the first 10 GMAD plant takeovers, only one was achieved without a strike. All of these struggles were on the same issues as at Lordstown. All proved ineffective. One of the most interesting of these was the 1 74 day strike of 4,000 workers at the militant GM plant at Norwood (Ohio) which manufactures the ailing Camaro, Firebird and Nova models. The strike ended in early October 1972. It was criticised by some militants because CM was in a position to let the strike go on, because of its advanced production schedule, and the pallid sales reports on the models to be built at Norwood.' (Business Week, October 7, 1972) Norwood was the longest strike in the history of GM.
As the rank and file paper Moving on Up, published in Cincinatti (near the Norwood plant) put it:
Now that the strike is over, many workers at the plant here feel that the strike was a set-up and that the UAW international joined with the Company to "make an example" out of Norwood. For years the Norwood local has been one of the most militant in the UAW. In 1970 the local stayed out for two months following the national strike settlement with GM, greatly embarrassing Woodcock and throwing into doubt his ability to control the locals to the satisfaction of GM management.
It was a different story in October 1972 when 2,300 men at the Fisher Body plant at Mansfield (also in Ohio) struck. This facility is the sole source of parts for every GM model. A strike there could have crippled GM within days (Business Week, October 28,1972) The day after the plant struck Woodcock, President of the UAW, announced that they must end the strike within the week. And so they did without any settlement. In other words workers can stay out for 1 74 days at a plant where it does not matter, but 5 days is the maximum at a plant which can really hit the boss. The role of the UAW leadership was clear. There were a series of 5-day stoppages at various plants, usually preceded and succeeded by massive compulsory overtime working. This meant that actual loss in production was minimal.
The policy of the UAW was clearly stated by Woodcock when he stated that the aim of the strikes was to force 'GM to crack down on GMAD'. He claimed that the division's policies were being promoted by 'corporation hawks, carrying out a policy which might not be pleasing to higher ups, but they let them get away with it.' (Business Week, October 28, 1 972) In other words, GMAD was all a ghastly mistake and the job of the union was to bring the matter to the attention of the GM top brass. Meanwhile, back in the factories, the speed-up continues.
Conclusions
The role of the union during the Lords town events was typical of the role of unions, whether 'right' or 'left', in modern capitalist societies. It divided and isolated workers When it did mobilise them it did so either to 'let off steam' or to struggle for meaningless objectives. The union made a major contribution to the workers' defeat.
Trade unions, in advanced industrial societies, are increasingly being shown up as one of the main obstacles workers have to face when struggling for their justified demands. When we say this we don't just mean that they have 'bad' leaderships or 'wrong' policies. We mean that their whole structure now mirrors the structure of the system. They are part of the prison, not part of the way out of it - struggles to 'change the union' or to elect 'left' officials have again and again just recreated the same situation. This needs to be stated unambiguously.
To struggle effectively workers will need to build alternative channels of communication and coordination, rank-and-file committees that cut across formal union boundaries, linking together various crafts, the skilled and the unskilled, the employed and the unemployed, women and men, the young and the not so young.
This will need tremendous effort. Firstly an effort of imagination. We will have to break free of the ideological grip of traditional modes of thinking about how we organise and work together. Secondly it will require the ability to be self-active. Workers will have to directly dominate their own organisations and struggles, to break with all the old attitudes of 'leaving it to others'. Self-management is like a hot potato - when it comes our way we all have a tendency to 'hand it over to others', usually self-appointed, and part of either the Establishment or of some 'revolutionary' vanguard or other. We do so because we are not yet used to thinking in terms of self-activity, because we are insufficiently confident of our own strengths and abilities and because we still think that others are more 'experienced' in matters of organisation and decision-taking. Herein lies the seed of repeated defeats. There can be no substitute for a self-conscious, autonomous rank-and-file movement, built op of self-conscious, autonomous human beings. It is not enough to question the work ethic, or to fight for more freedom in production. If the fight is conceived of as something which, either at its crucial stages or in its day-to-day implications, can he left to others. In this field there were clearly shortcomings in the Lordstown struggle, shortcomings which are still widespread throughout industry.
These things must be honestly discussed. They must be grappled with, however 'remote' they may seem from the, preoccupations and everyday concerns of ordinary workers. They cannot be left to 'look after themselves'. This is as essential a component of the struggle for a self-managed socialist Society as is the questioning of the work ethic or the fight for freedom within the work process itself, Workers have from time to time taken tentative steps in this direction. In this particular field working people are not only up against the dominant ideas of the society, as voiced by those who own or man age the means of production. They are also up against the echoes of these ideas, as expressed by the trade union bureaucracy and most political tendencies on the left. In fact these are more than echoes. They are deeply internalised patterns of thought and behaviour.
Revolutionaries can only help mass socialist consciousness emerge from industrial struggle if they see the struggle as it really is. Unfortunately most are so obsessed with what their textbooks tell them about capitalism and socialism and about what the struggle ought to be about that they fail to see the new-and inherently far more revolutionary-tendencies emerging under their very eyes. Moreover many sections of the radical movement have consciously or unconsciously deeply absorbed many of the values of the system, such as the fore-mentioned needs for institutionalised leadership and for discipline imposed from outside. They have a deeply economistic view of life. In fact at a deep level they fundamentally accept and reflect much of the structure and ideology of capitalist production. One has only to look at the pattern of production in Russia (whether under Lenin, Trotsky or Stalin), at Castro's Cuba, at Tito's Yugoslavia or at Mao's China to see this being worked out in practice. Everywhere there is the same attack on anyone who dares question the work ethic or who preaches resistance to production. It is only those revolutionaries (inside or outside of industry) who are prepared to look at what the working class is already beginning to do and to place it in the context of a different vision of socialism who will be able to contribute in a positive way to the revolutionary developments now taking place.
First Published by Solidarity as Solidarity pamphlet #45. (Circa 1973)
- 1 The number of grievances at General Motors itself rose from 106,000 in 1960 to 256,000 in 1969 (The Company and the Union by William Serrin, Knopf 1973, p.39). The nearest British equivalent to these 'grievances' would be the well known 'failures to agree' .
- 2 Production in the world motor industry has accelerated rapidly. Sales outside the US are growing at twice the rate of sales on the home market. GM is only the fifth largest motor manufacturer outside the US and Canada. Fiat, Toyota, Volkswagen and Ford tin that order) lead GM in sales ('GM: The Price of Being Responsible', Fortune, January 1972).
- 3 It is symptomatic of the rapid development of technology that Lordstown has now been put into the shade by recent 'advances' in Japan. For example, 40,000 Toyota workers produce 2 million vehicles (50 per worker, or about fire times the output of British Ford workers, themselves the most productive in Britain). This has been achieved by a massive investment in new technology. The new plant at Takaoka is far in advance of Lordstown (see Sun, May 24, 1973).
- 4 These industrial robots have been defined as 'easily reprogrammable, operatorless, handling devices, that perform simply repetitive jobs that require few alternative actions and minimum communications with the work environment' (Times; March 30, 1973). Sounds just like the ideal worker!
- 5 An extreme example of what can happen took place in October 1969, at the Chrysler Eldon Axle Plant. James Johnson, a black production worker with a 'low frustration tolerance' was sacked. He went home, got his gun, came back and killed two foremen and a UAW Committee man. The following day, workers all over Detroit stuck the press cuttings on the Johnson ease on their foremen's desks. At his trial Johnson defended himself He claimed insanity brought about by working in the noise, filth and danger of the plant. The judge and jury visited the plant. The verdict was unanimous: acquittal Since then there have been a large and growing number of assaults and killings of supervisors. The recent Williams case at Ford (Dagenham) shows that this tendency is developing here too (see Solidarity, vol vIl, no.8)
- 6 I would like to thank the author for access to the first chapter - which deals with Lordstown. This section contains a mass of information, based on interviews with Lordstown workers.
- 7 The traditional lefts are, in many respects, the last repositories of workers' illusions. In America they want a Labour Party. In Britain it is common to hear socialists arguing for a union on the pattern of the UAW. We hope this pamphlet contributes towards dispelling these illusions, at least in the British motor industry. It is an interesting fact that virtually the entire leadership of the UAW, like numerous British trade union bureaucrats, went through the 'left' on its way to the top. All three of the Reuther brothers were members of the Socialist Party. Emil Mazey, the union's secretary-treasurer was for many years a member of the Proletarian Party and later of the Socialist Party, and even led some G.I. struggles inside the Army during World War II. Leonard Woodcock, the union's President, was brought up in Britain - -- and was a member of the ILP!(Independent Labour Party) He later joined the Socialist Party in the USA. So much for 'lefts' capturing positions!
- 8 Calculations based on exchange rate of $2.45 to the pound, which was operative at time of writing this article.
- 9 This decline was only temporary. The rare of profit rose to 17.6% in 1972.For the last quarter of 1972 profits were the highest ever:
8667 million, compared with the previous best of 8590 million Wall Street Journal, February 2, 1973). These figures were achieved in spite of a series of stoppages including Lordstown which had cost GM about 200.000 units in lost production. - 10 This is consistent with the long-term strategy of the UAW of trading higher wages for productivity, in the belief that this is the way to beat back foreign competition and save jobs. The idea was that high wages and security will keep workers satisfied. This myth has been destroyed.
- 11 Ford got into the act as well. It was able to produce 194,210 more vehicles in the first 5 months of 1972, with only 4,273 more workers. See article by Jim Jacobs in Cleveland Plain Dealer
- 12 One of the benefits of 'recessions' for the employers is the opportunity to increase productivity, when the balance of power in the factory swings their way. This is shown in the following statistics:
Increase in output per man-hour
1949 Recession 3.1%
1950 Recovery 8.2%
1954 Recession 2.4%
1955 Recovery 4.4%
1957,1958 Recession 3.07
1959 Recovery 3.6%
1960 Recession 1.5%
1961 Recovery 3.4%
1967 'Mini-recession' 2.1%
1968 Recovery 2.9%
(Source: Workers Power January 19, 1973)
It is worth while considering how all the 'crying wolf about slumps indulged in by the traditional left has actually helped employers step up productivity. The system gains from these periodical 'shake-outs' which help it function more efficiently. In a situation where the mass of the working class still accept this rotten system, each time the traditional left utters its perennial (and false) prophesies of impending doom, the only result is to ensure that workers are conned into tightening their belts in its defence. Fortunately the prophets of crisis are losing their credibility and the workers' activity (and the class struggle) continue unabated. - 13 There was some dispute about this total. The Company estimated those laid off at 400, presumably not counting those who left and were not replaced.
- 14 Sabotage is not unique to Lordstown. It is as old as industrial production. A detailed examination of what happened in another auto plant in Detroit in 1968 is given in 'Counterplanning on the Shop Floor,' by Bill Watson, published by Radical America, 1878 Massachusetts Avenue, Cambridge, Mass. 01140(10 cents + postage). We recommend this pamphlet. It is available on libcom here: http://libcom.org/library/counter-planning-shop-floor-bill-watson
Comments
Bump, updated with new
Bump, updated with new formatting, lots of corrections, picture, proper footnotes etc.