A series of reports and accounts on casualisation and temporary work in Germany in 2007 by Prol-Position.
Misery is relative - Reports from temp workers in Germany, 2007
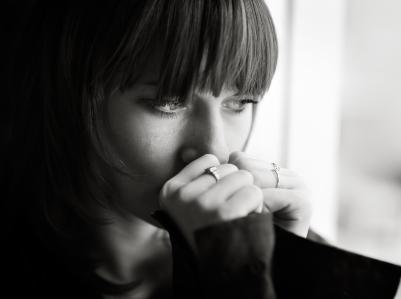
There have been many formal or campaign-like answers to the problem of 'precarity' and casualisation. Instead of relating to everyday proletarian anger and its potential collective expressions, many initiatives merely focus on a spectacle or event to convey general demands. Demands for guaranteed income or global rights and the way they are put forward often end up as alternative background music for the debate of those in power. Employers, state representatives and unions in Germany are currently debating the introduction of a general minimum wage. They see the introduction as a policy to regulate the low wage sector. The following text puts these debates in contrast to the experiences of those who are to be regulated, the experiences of low wage workers.
The first part summarises the quantitative and legal development of temp work in Germany and the official debate on minimum income. In the second part temp workers report from situations in following companies in 2006: General Motors (Bochum), Nokia (Bochum), Flextronics (Paderborn), Gate Gourmet (Düsseldorf), City Palais Construction (Duisburg). At the end you can find some preliminary conclusions. The text focuses on the new composition of temp workers in multinational companies, where temp work is not only used in order to accelerate the re-structuring process, but has become an un-temporary part of production. The quantitative growth of temp work has resulted in a new composition, bringing together young and often migrant workers on the one hand, and older workers who were formerly employed as permanent workers in the industrial core sector on the other. This composition of people circulates within the main core industries, without being too afraid of being unemployed again, without any bigger hope for a potential permanent contract and therefore without major illusions.
[prol-position news #8 | 4/2007] www.prol-position.net
Temp work and minimum income in Germany, 2007
Prol-Position on the extent of casualisation and the legal and contractual status of agency and temporary workers in Germany in 2007.
Temp work expands on a small scale
In mid-2006 about 500,000 people in Germany were employed by temp agencies. During the last decade the temp work sector has had an annual growth of about ten percent. In Germany, compared to other European countries, the share of temp work in relation to total employment is relatively small, about 1.7 per cent. In the UK for example that share is 4.7 per cent. The low number of temp contracts is less due to social conscience of German capitalists, but rather to the existing alternatives to temp work, e.g. temporary limited contracts, state subsidiaries for employing an unemployed person, special union bargained collective contracts which allow the employer to pay only 80 per cent of the wage if they hire a long term unemployed person. The manufacturing sector is the main area where temp work is implemented, and in particular in unskilled work in bigger companies of the electrical goods manufacturing and the metal industry. About one third of all temp workers work is found there, because there the re-structuring process is the most intensive and the wage differences between permanent staff and temps the biggest. The importance of temp-work for the re-structuring of certain industries becomes visible during the ongoing conflict about lay-offs at European Airbus. About 5 to 6,000 temp workers and 12,000 permanents are employed at the Airbus plant in Hamburg. In the manufacturing department the temps account for half of the staff and they are the first victims of the current crisis, March 2007. [see: http://www.wsws.org/articles/2007/mar2007/airb-m01.shtml]
In general, temp workers might earn 70 per cent of the average annual wage of a permanent worker, in cases such as GM (see reports) it might be slightly more than a third. Only about 2.4 per cent of German companies use temp work, but the usage of temp work differs according to size of the company. About 35 per cent of all companies employing more than 500 people make use of it. In other European countries where temp work is more common, the limitations of such contractual relations already show. For example in 2005 Spain got an official warning by the European Union because the share of temporary contracts was too high.
This warning was justified by the alleged impact of an disproportionate number of temp contracts on the general productivity. Modern industrial production depends on a certain identification of the worker with their workplace and with their future employment prospects. If temp contracts exceed a certain percentage the carrot of achieving a permanent contract seems out of reach. People loose their motivation, the sick leave rate increases, the productivity drops.
Temp workers get more mobile
Apart from the quantitative numbers, the employment biography of temp workers also changed. Particularly after the legal changes in 2003 (see appendix on legal changes), undertaken by the Social Democratic government, the average duration for which a temp worker is employed by the same temp agency decreases, as well as the duration for which the temp workers is hired to the client company. In 2003 only thirteen per cent of the temp workers were employed one year or longer by the same temp agency.
In addition to that the so-called chain contracts increased in numbers, meaning that the temp agency sacks the worker once there is no employment opportunity and re-hires them if necessary. This became possible only after the legal changes in 2003. This resulted in short-term contracts: in 2003 about 43 per cent of the temp workers had been unemployed before they got the temp-job. The average duration for which a temp would stay in one particular client company was 2.1 months in 2003, in 1997 it was 3.1 months. The increased mobility is also expressed in the fact that more often workers tend to be employed not according to their original qualification. In 2003 about two third of all temp workers had a professional qualification, but half of all workers were employed in 'unskilled' jobs.
The official debate on a minimum income is not about improving wages, but about how the low-wage sector will be regulated in future
The conflicting arguments in the German debate on a minimum wage are not about the wage level. Rather they are about how wide the wage gap between the official unemployment money, Arbeitslosengeld II (about 350 Euros plus rent), and the average wage has to be in order to make people take a low paid job and about how to control and enforce this wage difference.
With the Hartz IV reform [see prol-position news no. 1/2005 | 1, no. 1/2005 | 2 and no. 3/2005] the government already replaced income related unemployment money, which was based on the idea of an insurance, by unemployment money which is somehow a guaranteed minimum income which every unemployed person will get after one year of unemployment, regardless of their previous wage. Thus the first step was made towards a generalisation of proletarian income and the towards setting up the state as the official decision maker for the level of this income.
In most of the EU countries (18 of 25 of them have a minimum income) the ruling class expects the state to be the most capable body to regulate and officially enforce low wages in times of aggravated crisis. In Germany this is the center of the current debate on minimum income. The Social Democratic Party, SPD, and the union head-organisation, DGB, agreed in September 2006 on a two-phase plan to introduce the minimum income.
This plan expresses their will to sustain the alliance of government, employers association and unions and the official negotiation process regarding the low wage sector. After the 'political protests' against the Hartz IV-reform and more recently against the CPE in France the ruling class is afraid of 'politicising' the popular anger and of focusing it on the state. Their hope is that the state of the economy and of the workers struggles allows the holy trinity (state, capital, unions) to continue and to present the low wage outcome as a result of social partner-ship. In the first phase of the plan, employers and unions are supposed to negotiate a sector-related minimum income, which would then be legally founded by the state. This has already happened in the construction and cleaning sector. Only if this process fails, is the state supposed to fix a general minimum income.
Test-Tube Temp Work
The different capitalist fractions who participate in the debate about a minimum wage are still undecided whether and how regional or sector-related differences are taken into account when defining the minimum wage. Here the wage differences between east and west Germany still play a major role. The question is whether the advantage of having a collective contract in e.g. the hairdressing trade in Thueringen (East Germany) which allows hourly wages of less than 4 Euros before tax outweighs the advantage of having a state enforced general minimum wage of about 7 Euros or not. There are several union negotiated wages which are below the 7 Euros level, which is debated as a possible minimum wage, but of course there are several sectors and trades which pay more and which might adjust their wage level to the legal minimum.
Like the construction or cleaning sector temp work is a kind of test tube for the debate, given differences between areas and sectors are less distinct and given that the general wage level is very close to the debated level of a possible minimum income. Here the play-fight between the different institutions is the most intensive: after the government accepted the 'equal pay' directive of the EU in 2003 (see appendix on legal changes) the temp work companies reacted using a legal loophole. Basically they negotiated collective contracts with mainly smaller and so far irrelevant unions, exploiting the law that states that if a union agrees to unequal pay between temps and permanents, it is just. Before the legal change there were hardly any collective contracts in the temp work sector, today about 95 per cent of the workers are employed according to a union negotiated contract.
The first contracts were negotiated with the small Christian union PSA-CGZP. At first the main union head-organisation, DGB, refused to negotiate any contracts which would undermine the 'equal pay' directive and questioned the legitimacy of the smaller union to represent workers. After a short time the DGB too signed 'low wage contracts' for temp worker. They justified this step using the usual argumentation that otherwise the smaller union would sign even crappier contracts. Actually the wage difference between small and main union contracts are not that big (see below).
In May 2005 the DGB and the representatives of temp work companies agreed on a collective contract which might be taken on as a general minimum wage for the sector by the state. The main aim, which is to establish a permanent and regulated low wage segment, was achieved: the negotiated wage is only about 45 per cent of the median wage. Median wage means that 50 per cent of all wages are higher and 50 per cent lower. At the end of 2005 about two thirds of all temp workers were said to be paid according to the DGB signed collective contract.
The following numbers show that the wage levels do not really differ much whether they are negotiated or proposed by the little Christian 'bosses' union', the DGB or the state officials. In the west (east) of Germany the Christian unions contract pays 6,80 Euros (5,60) per hour before tax, the DGB contract 7,00 Euros (6,00) and the proposed minimum wage for the sector is 7,15 Euros (6,20). For the individual low-wage worker these differences might not be tangible given that in many cases people can apply for social benefit money which is paid by the state to top up low wages. In September 2005 about 906,000 working people received these social benefits, 280,000 of them worked full-time. In this sense a minimum wage would not change much for most workers in low-wage jobs, it would just change the 'wage transfer' between capital and state.
Appendix: Legal changes in the labour law concerning temp contracts
1994 Temp workers can be employed continually in one client company for nine months instead of six. After this period they have to be made permanent. People who were long term unemployed (more than a year) can now be sacked from the temp agency once the job at the client company is over. In all the other cases employment has to be continued for a certain period, i.e. about 25 per cent of the duration for which the temp worker stayed at the client company.
1997 Temp workers can be employed continually in one client company for twelve months instead of nine, before having to be made permanent. Temp companies are now allowed to give people a series of timely limited contracts in succession.
2002 Temp Workers can be employed continually in one client company for twenty four months instead of twelve, before having to be made permanent.
2003 People can now be employed in the client company for an unlimited period without having to be made permanent. People can now be fired and re-hired by the temp agency. Before the legal change people could not be rehired within the following three months after being sacked. The German government implemented the EU labour law according to which all 'employees are equal'. Theoretically, temp workers could now demand equal pay and conditions. The government left a legal loop-hole, which allows the 'equality law' to be undermine. If employers and union agree on a collective contract then its terms and conditions apply, even if they mean that temp workers earn less and work under worse conditions than permanents. Consequently, nearly all temp-agencies now employ people on a collective contract basis.
[Sources: Dr. Claudia Weinkopf, Mindestbedingungen für die Zeitarbeitsbranche?, Expertise im Auftrag des Interessenverbandes Deutscher Zeitarbeitsunternehmen (iGZ e.V.) (Aktuelle Analysen aus dem Institut für Arbeitsmarkt- und Berufsforschung der Bundesagentur für Arbeit, Ausgabe Nr. 14 / 19.9.2006]
[prol-position news #8 | 4/2007] www.prol-position.net
Comments
Temp work at Flextronics, Paderborn, 2007
Prol-Position on casualisation and agency working at a large German electronics manufacturer.
The company
Alongside Solectron [see prol-position news no. 2/2005] and Celestica, Flextronics is the biggest 'non-brand manufacturer' for electronic goods. Flextronics is a contract manufacturer among others for Sony, Ericsson, Microsoft and Siemens, producing and labeling their play-stations, mobile phones or TV-satellite receivers. In the US about 70 per cent of all electronic goods are already produced by 'sub-contractors' like Flextronics; in Europe it is about 20 per cent. In China a single sub-contractor factory produces half of the world markets' demand and three quarters of the European demand for microwaves, just to give a picture about dimensions and productivity of this sector. And these companies play an important role in the re-structuring process of multinational manufacturers, e.g. in 2000 Siemens contracted Flextronics to produce 33 million mobile phones. Shortly after this Siemens sold the rest of the mobile phone branch to BenQ.
BenQ liquidated the remaining factories soon after the take-over [see prol-position news no. 3/2005 'On German anti-capitalism']. Like most of the companies of the sector in 2001 Flextronics was hit by a severe slump, worldwide 10,000 of the 80,000 employees were dismissed. The high competitiveness of the contract manufacturer is not only based on low wages, but on economy of scale, a high rate of machinery utilization and a worldwide network which is able to order the cheapest components at a given point in time and which coordinates the company internal division of labour on a global scale. A particularly close cooperation exists between the plant in Guadalajara, Mexico and Sarva, Hungary. These plants are identical in their outlay and organisation and they both produce a play station for Microsoft. In Hungary they adjust the production to seasonal up and downs of the market: during the summer some departments produce single-use cameras for Kodak and in autumn they manufacture parts for DVD-recorders for Philips and Panasonic.
The backbone of this kind of flexible production is a new generation of machines that put the electronic components on the circuit-board. They can be set-up for different series of circuit-boards in shorter time. At this point we still have to be careful and distinguish between official ideology of 'production on demand' and the reality on the shop floor. The management of the plant in Paderborn state that only 8 eight per cent of all manufactured models (of identical circuit boards) are produced in series of 1,000 or more and that the average series comprise only about 200 pieces (i.e. claiming that it is not mass production). According to official company statements the plant is able to fit 165,000 components per hour, on seven different production lines, for 15 different clients and in total 500 different products. On the line people say that the number of 500 different models is extremely exaggerated. The plant in Paderborn, a small town in the west of Germany, belongs to the SBS-branch of Flextronics (Special business Solution, meaning that the focus is on middle-sized contracts). The clients are, amongst others, Macro System, PWB Technologies, TRW Automotive, Aastra, Wincor Nixdorf, Blaupunkt, Conrad, Fujitsu Siemens, Hella, Bintec Funkwerk, ADVA – optical Network, SUN Microsystems, Siemens, Data Display, KBA and SINN. Flextronics took over the plant from the computer-server manufacturer Fujitsu Siemens. In the 90s Fujitsu-Siemens itself was outsourced from the bigger computer plant of Siemens-Nixdorf, the main employer in Paderborn at this time. The 630 workers who were employed at Fujitsu-Siemens got new contracts with Flextronics. Apart from the server manufacturing Flextronics started to get other contracts. Once a new contract is obtained the achievement is presented to the employees in a general assembly, in English and with colourful screenings. The individual location is portrayed to be in fierce competition with the other global locations, but the example of the computer manufacturer SUN shows, that the competition is 'artificial company policy' of Flextronics. SUN wanted the computer parts to be produced in the plant in Hungary, but out of company strategy reasons Flextronics agreed on paying the wage difference themselves, in order to be able to produce them in the plant in Paderborn. [http://www.flextronics.com/Contacts/GlobalLocations/paderborn.asp]
The Composition of the (Temp-) Workers
In addition to the 600 permanents, Flextronics employs about 60 temp workers from two smaller local temp-agencies (PPS and Heuer und Koenig). Workers from the big agency Randstad are only hired for the neighbouring plant of Wincor Nixdorf. According to the companies' collective contract only 45 temp workers are supposed to be employed, but the actual numbers are higher. In the production unit half of the permanent workers are migrants, some came from Turkey other from Poland during the 80s or from the former Soviet Union during the 90s. Half of the total workforce are women. In the huge logistics department the composition might be different. Some of the permanents took part in a kind of unpaid apprenticeship that the job centre organised at Nixdorf, the former mother company. Some of them got a proper contract afterwards. Nixdorf still used to train apprentices; some of them now work as mechanics or electricians in the production unit. Most of the permanents have worked in the plant for the last 10, 15, 20 years, but no one has been made permanent for the last five years. The company puts big announcements on the notice board promising leaving pay for any permanent workers who quit the job voluntarily, disregarding the current boom and the lack of experienced workforce. A lot of the temp workers are from migrant background, too, a lot of them are so-called 'Aussiedler', people who were born in the former Soviet Union but have German ancestors. Particularly at weekends there are also a lot of student temp workers employed. Some of the temps have worked at Flextronics before, only for a period of a few months each year, for the last three or four years. All in all the permanents are much more relaxed, they ask the temps to take a coffee break every now and then.
Work Organisation
There are seven production lines, two of them dedicated to 'mass-production' for the bigger contracts, mainly audio-circuit boards for Blaupunkt. Until last year Blaupunkt manufactured these boards in France, but then stopped the production. Flextronics bought the machines and started producing the same circuit boards as a contractor for Blaupunkt. The work at the Blaupunkt lines is very standardised and they have a high output. At the smaller lines the output is less, e.g. after 400 circuit boards the machines have to be re-set for a different model. These lines produce about 30 to 150 circuit boards per hour, depending on the model. Apart from filling the machines with electronic components the main task is the setting and re-adjustment of the machines. There are only few women doing this job, most of them work in the department where circuit boards and components are soldered by hand and in the quality department. According to the management you need one month of training at these smaller lines, but actually it is more like two or three months, given the complexity of these machines. At the mass-producing lines the training period is only one week. If these lines are under full steam, the work is quite stressful. Blaupunkt intervened in the production process: at the mass-lines only permanent workers are supposed to do the quality check. Those temp workers who did the job already for half a year had to be given a different job. The control and so-called quality check was intensified. Hourly all workers on the lines are supposed to fill in the number of produced pieces and their efficiency into a spreadsheet and a graph. At the computer at the line you can check these figures. It might say:
Production Line Hanover
Type KGBA938177439
Order 10056
Target: 40 circuit boards
Actual boards produced: 30
Efficiency: 75 per cent
Everyone has to fill in their figures into the chart at their machine. Most people do this, but only reluctantly and in a rather sloppy way. Everyone knows that this measure is only meant to give people a bad conscience, given that the figures are in the computer anyway and that the bosses could just check them their. If your efficiency rate is under 80 per cent you are also supposed to give reasons. But this measure is not yet completely enforced; a lot of people just forget to fill in the chart. The already mentioned company internal network, which Flextronics uses in order to integrate the various production locations, is to a certain degree also used by the production workers. You might use this intranet, e.g. if you search for a particular stencil which is used for marking the board with soldering paste. You type in a product code and then you can see the location of the stencil in the storage department. You can also see for which company a certain model is produced, how many are ordered and what the price of the product is.
Whether the production of small series is profitable for an industrial company like Flextronics, depends on the time spent on resetting the machines and on changing the work organisation. From my own experience and after talking to other workers the average time to restart the production of a model which has already been produced in the plant previously - not a prototype - takes about a week: from resetting the machines, re-organising the storage department etc. to full production capacity. The management says that the time necessary to re-set machines from one model too the other is supposed to take twelve minutes. This is under the condition that the machines and storage is already adjusted to these models, that is not a complete start from scratch. In fact the time needed is more like two hours. Sometimes there are problems with lack of components, e.g. last week we produced telephones, but there were parts missing. I only produced 750 instead of 1,000. We will have to make up for it once the components are delivered. Sometimes lines are shut down completely for a period of time.
Wage and Working Time
The permanent workers' wages start from 12.50 Euros per hour before tax for 'unskilled' production workers. The temp workers get between 7.50 Euros for 'unskilled' and 10.50 Euros for 'skilled' workers, though 'skilled' only means that they have a contract with the temp agency as a qualified worker, not that their actual work in the plant differs in required skills. After Flextronics took over the plant, and after a new collective contract has been agreed on, a so-called Haustarifvertrag [in-house wage and conditions contract], which is limited to the company instead of the whole sector, the permanent workers had to put up with a monthly wage loss of about 200 to 300 Euros. In addition to that there is fear amongst the staff that the new ERA wage assessment model, which was agreed on by the union and which will be implemented in the whole metal sector, will lead to further wage cuts. ERA triggers anger in a lot of companies (see report on Nokia). Despite this fact, or maybe because of it, only few production workers took part in demonstrations during the last collective contract campaign of the metal union IG Metall. There are three rotating shifts which one week start on Sunday at 10pm, the next week on Monday 10pm, meaning that you work early shift one week, late-shift the following week and night-shift the week after.
For one cycle the night-shift starts on Sunday, the next cycle on Monday. In that way each worker on a Monday cycle has to work three weeks in a row on Saturdays. This model also allows for extending the working week to six days if necessary. The consequence of this model is that on Mondays and Saturdays there are only half of the staff working. The company uses student temp workers to fill the gap. During a five days week we work 37 and a half hours, the temp workers get 25 per cent extra for night-shifts, it might be more for the permanents.
Conflicts
A lot of temp workers leave the company after a short stay and there are arguments concerning the low wages. The students asked why there is a three Euros wage difference between 'skilled' and 'unskilled' temp workers although they do the same work. The students in the quality department got a 50 cents per hour 'quality-bonus', the other workers of the same temp agency did not. In contrast to that a lot of workers at the mass-lines, mainly students, are fired more quickly. You cannot follow it up, people just disappear, only days later you notice or hear that another three students have been kicked out. A lot of people quit because of stress, there is a very tight technological control, e.g. no product must leave your machine unregistered and there are very heavy production targets. Often there are no foremen around for hours, then they appear and ask you: "What is wrong with your efficiency?!". Workers have to sign all sorts of shit, without knowing why. If you manage to stay longer than half a year you are the king of seniority amongst the temps.
[prol-position news #8 | 4/2007] www.prol-position.net
Comments
Temp work at Gate Gourmet Germany, 2007
Prol-Position on agency work at catering firm Gate Gourmet in Germany in 2007, following the strike of 2005-6.
The Company
A lot has been written about the six months of strike at the airline catering company Gate Gourmet at Duesseldorf airport in 2005-2006 , therefore only a brief introduction. The following report from a temp worker is based on a very short work experience inside the plant, about three months after the end of the strike. A strike which was mainly defeated because of the scab-work of temp workers.
Gate Gourmet is one of the world's biggest airline catering companies. In Germany Gate Gourmet took over the catering branch of the airline LTU. Temp workers had been employed at Düsseldorf airport before the strike, but mainly on the basis of actually temporary employment, e.g. students during holidays or on part-time. During the strike, temp work was drastically increased and due to a lot of permanents leaving after the dispute, now most of the workers in the logistics department and the kitchen are temps. There are three different temp agencies, the local agency Avci mainly recruits Turkish workers, whose conditions are even worse than the other temps. It was a challenge for the management to join ex-strikers, scabs and new temp workers in the production process.
The Hiring Process
Apart from the usual hiring ceremony Gate Gourmet demands that the agencies ask the civil aeronautics security board to check possible candidates and their addresses of the last ten years. After the short interview all three candidates who took part got the job, two of them were older than 45 years. The manager of the temp agency Mumme announced that Gate Gourmet plans on establishing a 'permanent team' of temporary workers. Like the manager at Wico/GM he seems to think that the prospect of a permanently temporary status is an incentive to take the job. They don't even need to promise a possible permanent contract anymore.
Work Organisation
The work at Gate Gourmet is divided into four different departments: kitchen (about 30 people), storage for customs warehouse (about 20 people), general warehouse (about 25 people) and the lorry drivers (about 10 people). The kitchen and the customs warehouse are separated units, and mainly Turkish workers from Avci temp agency are employed in the customs warehouse. They have the worst conditions; they don't get bonuses for night-shift work and unlike all the others they have to pay for the food (it is not allowed to bring one's own food). The supervisors in the warehouse are permanents, mainly former scabs. The 'organic' informal foremen are either permanents who have been shifted from LTU during the strike or temp workers who worked as scabs. The permanents at LTU used to only get short contracts and often there was not enough work, so somehow only the scab-job seemed to provide safe full-time employment. All the drivers are permanents.
The management offered a lorry driver's job to a temp worker, but although it would have paid better, about 10 Euros before tax instead of 6.50 Euros, he refused the job after dong it for one day, due to the higher stress-level. Before the strike the drivers used to help loading the trucks, now they are only supposed to drive. The assembling of the load (magazines, newspapers, bog-rolls, drinks, meals etc.) and the actual loading of the trucks is now done by temp workers, most of them hired after the strike. The result of this restructuring is that now more than half of the work-force at Gate Gourmet are temps, most of them earning about 6.50 Euros per hour. If we take all annual extra-payments into account, the temps earn about 40 percent less than the permanents. However, the main motivation for Gate Gourmet is not the immediate wage costs, but the more flexible employment of the temps: particularly after the strike and during the phase of re-structuring they wanted people that they could get rid of more easily. In addition to that the ups and downs on the catering market intensified, demanding a more adjustable total workforce. The other side of the flexible coin is the high turnover amongst the temps. People often quit after a week or less. Especially for the work in the warehouse you need experience of at least two to three weeks. You have to know a lot of minor details: How many tabloids are provided on an inter-European flight? On which side of the lorry do you have to put the trolleys with uneven numbers? How many puke-bags for a trip to the US? The management and the supervisors complain about an increase of delays and wrongly packed trolleys. They blame fresh temps or pissed-off ex-strikers. On the noticeboard they condemn the 'sabotage'. The delays are a real problem, the time-schedule is tight, if a truck leaves the warehouse ten minutes late it might cost Gate Gourmet thousands of Euros of penalty.
After the Strike
There are no visual remnants of the strike, therefore it is interesting to see how a newly hired temp worker would get to know about a six months long dispute about three months after it finished, without asking about it. As early as during the first day at work another temp worker answers the unintentional question of how long he already works at Gate Gourmet: 'I have been working here since February. I am one of the strike-breakers'. Two days later in the canteen some permanents talk about the time 'before the strike', the harassments and the cost-cutting threats. Apart from that the atmosphere is neither tense nor relaxed, you cannot 'feel' an underlying tension, which might be due to the strike; there are no open disputes between ex-strikers and ex-scabs, at least not during the six working days of this report.
If you ask the temps openly about the strike, most of them will tell you that they didn't feel that it addressed them; that the aim and organisation had nothing to do with them. Three guys say independently from each other that the demands of the strike were on a different league: even if the wage-cuts would have been enforced, the income of the permanents would still have been considerably higher, their workplace still much safer. Practically, the strike was not able to build a bridge to the temps, nor to build up enough force to prevent scabs from working. The current problems at work are more pressing than the history of the strike. A lot of the temps come from the rural areas in the north-west, close to the Dutch border, they have to travel up to 80 kilometres to work. The shift-times are murderous, e.g. six days from 3am to 12am (early shift), then two days off, then six days from 7pm to 4am (night-shift). If not enough people turn up for their shift, workers have to stay longer, up to two hours, which is particularly tiresome after night-shifts. The management announces extra shifts, only giving very short notice.
Facing these kind of working-times and the low wages people often quit spontaneously, e.g. the two older guys from the job interview disappeared after three days. Some people have to stay, e.g. an African guy, who obviously has a bad conscience for having done scab-work, who arrived illegally in Spain, worked in the harvest, made his way working through France and now ended up at Düsseldorf airport loading trucks. The management watches the whole scene with a kind of paranoiac mistrust. After some leaflets with the title 'Against the Exploitation of the Temp Workers' appeared in trolleys, under meal trays, in water crates and Playboy magazines, they got nervous. Even more so after some leaflets actually made their way to the passengers in the aeroplanes. The management called the criminal investigation department and created a big fuss. The enormous stamina of the strikers, who occupied the strike-tent during six cold German winter-months, the spontaneous piqueteros, who blocked the lorries, the alleged acts of sabotage inside the plant, the destruction of a temp agencies' office during the dispute… must have fucked up their nerves considerably.
[prol-position news #8 | 4/2007] www.prol-position.net
Comments
Temp work at General Motors Opel Bochum, 2007
Prol-Position on casualisation and agency working at General Motors in Germany in 2007.
The Company
Since the wildcat strike in 2004 about 3,000 workers have left the plant in Bochum, nearly all of them 'voluntarily', cashing in up to 180,000 Euros severance pay. In August 2006 there are 6,799 permanent workers still employed. The strike managed to prevent a radical re-structuring process, since then this process continued, but at a slower pace and targeting only one department at a time.
The complete plant 3 (storage and logistics for spare-parts) was outsourced to Caterpillar, the production department for exhausts and axles was sub-contracted to the US company Magna. GM refuses to give permanent contracts to its apprentices in the manufacturing departments. Once they finish their apprenticeship they have to accept a contract with the temp agency Adecco; they get the basic wage of 13,50 Euros before tax and a guarantee of staying in the plant for half a year. After that they are only 'normal' temp workers at Adecco, their wage is reduced to 10 Euros and they can be sent anywhere in Germany.
In addition to that the management threatens with various smaller outsourcing measures, such as the security service. The following report describes the situation in plant 1 (final assembly of the models Astra and Zafira) in summer 2006. All GM plants in Europe are supposed to compete for the order to produce the Astra follower model (Delta II). In addition to the closure of the plant in Portugal and the cut of the entire night-shift in England, the outcome of the decision about Delta II would be another plant closing. In plant 1 of GM in Bochum the management demands severe wage cuts and the outsourcing of the entire internal logistic department (which employs about 550 people), a crucial department which delivers the assembly lines with parts. In 1999 the workers prevented the outsourcing by going on wildcat strike. In 2004 the plant in Bochum was cursed as too expensive, in summer 2006 it is hailed as one of the most productive in Europe. The atmosphere inside the plant is rather bad. The collective feeling of workers' power was weakened by the way the strike ended and fades further due to the individual poker-game around leaving pay ('people are being bought out') and the daily announcements of undermining the remaining collectivity by outsourcing.
The temp workers in the final assembly department are hired by an already outsourced company, called SCB (Sils Center Bochum GmbH). SCB is a subsidiary of Ferrostaal, which in turn is a subsidiary of the truck manufacturer MAN. In the GM plant in Bochum SCB has the order to pre-assemble certain parts (the inner lining, the glove compartment, parts of the dash board etc.) and to supply the assembly line just-in-time. In Cologne SCK assembles the front and rear bumper for Ford and SCR in the GM plant in Russelsheim pre-assembles engine parts. The pre-assembly department which SCB took-over in Bochum used to be a so-called convalescent department, meaning that it used to comprise easier work for people who were not able to work directly on the assembly line anymore or not yet, e.g. after recovering from an illness. People were blackmailed with the closure of the convalescent department and told that their only chance to keep their job was to shift to the outsourced company SCB. When they shifted to SCB those people kept the conditions inscribed in their GM contracts. This has the result that at SCB there are three different legal conditions for the same work: old GM contracts, SCB contracts and temp work. Even the hourly wage before tax differs considerably: according to GM contract it is about 16.50 Euro, SCB 13.50 Euro and temp contract 7.00 Euro. Along with the outsourcing of SCB the conditions of Adecco temp workers who were previously working in the department deteriorated drastically: GM used to pay a bonus for all temp workers, so that their hourly wage was topped up to 13.50 Euros, the lowest hourly wage a permanent worker would get. With the take-over in April 2006 SCB scrapped this bonus and 150 Adecco workers saw their wage cut by 50 per cent, resulting in 149 workers leaving the job or being kicked out after taking collective sick-leave. The huge wage differences between GM and temp workers become even more blatant if we take holiday pay, various bonuses and extra paid breaks for assembly line work into account, extra payments which the temps do not receive. The annual total wage of a temp amounts to about one third of a permanent workers wage. In the period from the second world war to the present day such an extreme wage difference only seemed to be enforceable along of racial or gender lines. In the main industries the struggles of the 60s and 70s washed these severe differences away, now they have returned and they are imposed by 'merely' legal divisions. In addition to the wage gap there are further disadvantages the temp workers have to face, e.g. during the three weeks of company holiday the temp workers were dismissed and had to apply for unemployment benefit; after the holiday not all temps got their job back. Or another small example: if people do not turn up for their shift it is the temp workers of the previous shift who have to stay until the management finds replacement, for up to two hours. Another disadvantage and difficulty on a daily level is the fact that the temps can be kicked out from GM immediately, from one minute to the other. At the moment there are only about 400 temps working in the plant, including, for example, canteen staff.
Compared to, e.g. the new plant of BMW in Leipzig in the east of Germany, this is not very many. At BMW 1,000 of the 3,400 employees are temps, many them have been working as temps at BMW for three years. Due to the combative history of the GM workers there are only a few temps at Bochum, but they are highly concentrated, e.g. in the assembly department nearly half of all fork-lift drivers on night-shift are temps. In contrast to GM the 150 outsourced companies that operate on the GM premises do not have legal constrictions as to how many temp workers they are allowed to employ. As part of the competition for the Delta II the GM management demands that GM itself should be allowed to increase the share of temps from five to fifteen percent.
The temp agency Wico employs about 35 people per shift, only for SCB in the pre-assembly department. After a lot of Adecco people quit, Wico got a big chunk of the order, so most of the Wico temps have only been in the plant since May 2006. Compared to Adecco it is a minor agency with about 150 employees in total, most of them are hired to companies of the automobile sector. Wico temps work at GM, at Ford in Cologne, at Tower Automotive in Duisburg (doors for Mercedes Sprinter and VW T5) and for Nobel in Essen (breaking-systems). During the job interview the Wico manager tells you that you might be hired to any of the above companies.
Hiring Process
GM and Ford demand that the temp agency subjects the job candidate to a German test, a second hurdle for immigrants. Apart from that no other formal qualification is required, although the agency prefers people who have assembly work experience. The job interview took about two minutes and ended with the manager saying: 'You are now on the list, please be available, we might phone you in the afternoon and ask you to do the next night-shift'. And this is more or less how it happened. During the interview the manager emphasized that SCB wants to recruit 'a permanent pool of temporary workers'. He said that it could be a long stay at GM, but did not promise a permanent contract with SCB, did not even mentioned the prospect. He also warned about the bad influence of the old GM workers in the department who do not accept the new work standards and quality measures of SCB. He made clear that they can get away with it, but that we would not. The temp agency Wico has their own office on the GM premises, a supervisor who visits the temps before or after shift, who takes care of complaints of either side. If you are five minutes late, at 5:50 am this is, he would phone you and inquire about your whereabouts.
The Composition of the (Temp-) Workers
Most of the temps are young, half of them from migrant families, about three quarters are male. Most of them have a formal qualification in an unfashionable profession, such as mechanic in the mining industry or building fitter. They are younger than the average GM worker by about ten years, but apart from that their composition is almost identical (in terms of qualification, migrant background, gender etc.). In the small department that pre-assembles the inner lining we are eight workers, four temps and four permanents. Apart from the foreman only temps do the night shift. A female work-mate used to work at GM with a permanent contract. She did an apprenticeship at GM, her mother had a corner-shop on the premises and knew the works councils, which helped her to get the job. She was then dismissed due to down-sizing of the paint-shop, worked at the counter of a bakery for a while, was unemployed and then got back to GM, this time as a temp, earning half her previous wage. A Turkish and an Albanian temp worked at Nokia mobile-phone plant before and were both kicked out because of problems with the foreman. The permanents at GM radiate a certain coolness, a certain tired self-confidence. Towards the temps they are friendly, mixed with pity. The temps who just started to work at GM are impressed by the dimensions of the plant, the masses of people, the huge locker-rooms, the info-board of the workers' motorcycle-club. There are remnants of the old political workers' fortress, which the plant used to be. Displayed in the plant there are quite a lot of union info-boards, shop-steward news, calls for demonstrations and meetings by the MLPD (Marxist-Leninist Party of Germany). People rant a lot against 'them up there', but at the same time most of them think that the plant will be down-sized bit by bit and close at some point.
Work-Organisation
We work five meters away from the line, preparing the inner lining for the assembly. We can see if the line is moving and we can hear if there are any problems. If there is any problem at any section of the line people can press a button and then a tune is played from loudspeakers positioned at the line. There are different tunes for different sections, so the department manager or the maintenance crew know where to go. Most of the time these tunes play at the same time, badly composed electronic versions of old-fashioned children songs. Psycho. The work is simple; it takes about two hours to learn it and probably four days to find your rhythm. The temp workers are trained by temp workers. Once you got the rhythm the work is not too stressful, unless there are problems with the supply of parts or with the transport to the line. This is often the case. Meaning that you work more or less constantly. You take the inner lining for the roof, make sure that it is the right one (there are six different types), then you take cables, the spot-lights, foamy positioners and the electronic-parking-aid and stick it all on with masking tape. If you are stressed, the masking tape can get you into a comical fuck-up, a sticky situation, so to speak. You normally need three minutes per inner lining. Every fifteen minutes a work mate with an electric lorry will drive a wagon with ten inner linings to the assembly line, about 200 meters upstream. We are supposed to have two wagons full of inner linings prepared at any given moment, in order to be on the safe side. Because if no wagon reaches the line for ten minutes, the line would stop. This should not happen. There shouldn't be a wrong inner lining model on the wagon neither, nor parts missing, because things get pear-shaped otherwise, people have to run or cycle through the plant and supply the line with the correct item. This is why one person in the team is always supposed to check the wagon and sign for the correct content.
This job rotates with each wagon. After this worker the driver will check the wagon again and then an older GM worker stands at the line and triple checks it. They want to get rid off this worker, but that will be a tough job. There are rumours that the old bugger rejected a 150,000 Euros leaving package. SCB gets in trouble with GM for any mistakes, this is why they increase the pressure on the team; we are held responsible for the quality. To give the wagon a good check and to assemble new linings at the same time is stressful. But it is even more stressful if you don't notice that a work mate in the team forgot to stick on a foamy positioner, because he will be screwed by the foreman and then screw you. The SCB foreman tries to threaten us with the sheer mass of capital involved: 'We are supposed to assemble 370 cars per shift, so if you guys cause the line to stop for a minute, it will cost us 15,000 Euros. You don't really want to deal with that, do you?!'. Answer of a temp worker: 'If I actually have such a responsible position in this company you'd better pay me more than seven Euros before tax'. Even a straightforward inner lining, whose production price will hardly amount to more than ten Euros, is the product of an extended international cooperation. The actual lining has left the factory (supplier: Faurecia Sia), in Poland one week ago, the spotlights were supplied by a manufacturer from the South of France and the cable is from the Czech Republic. Interestingly enough Faurecia has a plant in Leipzig, as well, supplying the BMW plant. There the union officially states that it was able to make 20 temp workers permanent and to convert all short-term contracts into permanent ones.
SCB plans to train all temp workers to drive the electric lorries, to organise the supply for the assembly line. The job is dull and you rarely have time to chat with anyone. The workers on the assembly line (who are all permanent workers) are not really up for chatting, which might be due to the work load, but also because the e-lorry drivers change every other day. And what kind of conversation can you have during one minute of handing-over the parts and fetching the empty wagon?! The temps are also supposed to go to an unpaid one-day training for fork-lift driving. May be once the internal logistics is outsourced they will want the temps to take over these jobs. We have to sign a paper that we have to pay back the costs of the training, about 150 Euros, if we leave the job within the next three months. The high turnover is a problem and this may be a way of trying to tackle the problem.
The fact of producing cars, an alleged mass-product, without being able to afford to buy one, is strange in itself. The temps' wages are so low that probably even a ten years credit would not be enough to pay for a new car. This fact becomes even more absurd if you know that the automobile giants have to struggle with huge overcapacities; they produce too many cars.
At the same time we are supposed to work extra-shifts on Saturday twice a month and 30 minutes overtime every day. And for January 2007 the management announces reducing the working week to four days, which would mean the sack for some of the temps. Most of us are gutted: the job is shit, but you can count yourself lucky if you have one. It is surreal that grown up (wo)men who keep the biggest industrial giant of the world running have to be scared of these daft foamy positioners. In our team six people assemble inner linings for the roof-part. The new model needs four foamy positioners less. The older GM workers are seriously worried; they know where it's at. Four foamy cubes less means 30 seconds time saved per inner lining. If we assume a daily output of 400 cars, it would add up to about three and a half hours per working day.
For some Mc Kinsey bastard this would be enough to kick one of us out. As if the alienation of the work process wouldn't be enough, the management invents extra-alienations. Right next to the assembly line there is a 'wounded car', it is bandaged and a huge sign says 'mutilation parcour'. You first think that it is a kind of health and safety measure or a warning for future street accidents, but it is actually about the car and in which parts you might hurt it. Every day an old fork-lift driver rattles past this bloody 'mutilation parcour', his neck and spine full of metal screws, he literally broke his neck at work and is still waiting for compensation from GM.
Conflicts
The permanents and temps take their break together, we sit at the same table, there aren't any animosities, but our problems are of different kind of intensity. The main worry for the permanents is the future of the plant, the threat of dismissals and the question of the leaving pay. For the temps these conversations are a lesson in modern company management. They rarely talk about the wildcat strike of 2004, but when they mention it then they describe it as the main answer which they found to managements policy. The next sentence is usually about the fact that since the strike ended, about 3,000 workers left the plant, that therefore the situation today is different. The permanents have their coffee/fag-break together with their worst-case-scenario, with the next generation of industrial workers. The temps can tell them how life is on unemployment benefit, how the situation is on other shitty shop-floors and how to manage your life with 850 Euros per month when additionally to this problem you have a full-time shift-job in the German car industry. The permanents are estranged from the 'don't-give-a-toss'-attitude of the temps towards the company and the future of the plant. The main problem of the temps is of a straightforward financial nature, the low wages. At the moment there seems to be a kind of material and moral limit of about 10 Euros per hour before tax for young industrial workers. If the wage is lower, it becomes the main concern. If you earn 850 Euros per month like we do, you have only about 150 Euros more than on the dole, of which most is spent on petrol and increased drug consumption. And then the growing uncertainty of if and where you will actually work next month. The rumours about the enforced four-day working-week and unpaid holiday hit the temps harder than the permanents. And the management would not call the permanents at five o'clock in the morning on a personal holiday and ask them if they could come to the shift and replace an ill colleague, as does happen to the temps. And they don't phone the permanents early in the morning when they are five minutes late, which makes coming too late to GM feel like this…
…this sensation, still dozy in bed, the first attempt to open your eyes, still frazzled and able to into the soothing abyss when you realize that the time-keeper next to you is right, that shift will start in five minutes and you are a naked twenty minutes bike ride and three dream-lands far away from work, a lot of things happen at the same time, various pictures, sensations, thoughts, disbelieve, and then five seconds of panic: an industrial giant with scrap-metal edges gears up, comes ploughing through your puffy downy cosy world, through the scent and touch of the other, the picture of the cars' carcasses lining up to be filled with meat, the rattling chain and a tiny link missing which is you still in bed, a missing link with ripple effects, the debts of the worlds biggest car manufacturer surge to a menacing wave of dollar-bills, a black-hole of uncovered pension funds, the general motor starts to stutter and screech, asking for more human energy, for the missing link, sends the foreman to the department manager to the greasy temp agency amoeba who slobs towards the phone in order to sneak into the warmth of your blankets, naw! 'blow the job, man, get some sleep!', but behind him threatens the sack, the job centre, another dozen of job interviews with similar sticky personalities. Humiliation, silky muscles turning to sour flesh during the race to the plant, running through huge industrial halls, the assembly line moves in the opposite direction, nightmare sensation, you can run, but you will not get anywhere, mocking smiles of already working men, 'this time it's you, buddy', patronizing wagging finger from your foreman, acrid smell of mercy, the shrugging shoulders of your mates and your early morning knees shake for five euro an hour…
All this results in a really bad mood amongst the temps. The rumour that all Adecco temps are about to be kicked out is the last straw. The permanents, even the foreman, suggest that we should ask SCB for permanent contracts. Or at least ask about what is actually going on concerning the Adecco people.
Kick Out
Various factors lead to a rash action, which end in a temp guy being sacked. The atmosphere is bad, people talk about quitting the job, the same talk in the glove-compartment department. When the management sent us to the benefit office during the company holiday they promised that we would all be back on board in three weeks time. Actually a very sound work-mate is not on board now, he is still at home, the management says that he is not wanted because he comes late and sometimes drunk. So somehow they don’t give a shit about us and we don't about their jobs, or at least not at any cost.
Really, it is like having to pay for having a job. A common action seems to be more plausible than leaving or being made to leave. The idea crops up that we could all go to the SCB office during the fifteen minutes break and ask about the future of the Adeccos and for permanent contracts, at least a bit more money. We tell people in other departments about it, the electric lorry-job comes quite handy for that. Most of the people think it is a good idea, some of them go straight to others, spreading the word, some boast about bringing fourteen people to the date. It is two days before the date and the Wico supervisor snoops the thing out, starts to threaten people individually, saying that the action endangers all the temps jobs, suggests that we should talk to him and leave the Adecco guys alone. Because we work all quite spread out and are more or less chained to the workstation there is no way to get together quickly, to find some common answer. He asks for ringleaders, he really panics, and finally it is the electric-lorry driver who is on number one of his list. Although even the SCB foremen speak in his favour, the guy has to leave the plant and is not allowed to return. This result is even more demoralising because it confirms the opinion of the permanents that the temps are victims who can be kicked out in no time and who cannot stick together long enough in order to get something going. A successful action, however small, of temp workers who know about their position in the final assembly would have been an important answer against the general trend and a possible sign for others in less 'privileged' work situations.
[prol-position news #8 | 4/2007] www.prol-position.net
Comments
Temp work at Nokia Bochum, 2007
Prol-Position on casualisation, work and agency staff at the Bochum Nokia plant in Germany, 2007.
The company
Nokia has been producing mobile phones in Bochum since 1989. In 2005 the plant manufactured 100,000 to 150,000 mobile phones per day for the global market. About 2,500 permanents are employed, over 500 less than four or five years ago. The screen-production was shut down and the complete logistic was outsourced to the company Exel, which now organises the delivery for the production lines and the storage. In addition there are many temp workers from various agencies in the plant (Adecco, Randstad, WIR, Allbecon, Persona).
Like most of the other companies of the sector (see Flextronics) Nokia cut many jobs in 2001 and re-located many jobs within the plant. There have been various 'political' labour court cases, because permanent workers accused the company that they sacked people, when they already knew that temp work would be increased on a constant basis. Left-wing or critical unionists complain about the fact that so far it has not been possible to establish a union or workers group inside the plant which could have an oppositional position against the management. The existing workers' representation usually retreats when attacked or else collaborates with the management. For example the chairman of the works council, Hammer, boasts that the works council tried to win over the Nokia management for Nokia to become the first company which implements the ERA wage scheme. ERA means that each individual work place is re-assessed and assigned to a new wage band. Most of the 'unskilled' production workers would have to put up with wage cuts and at Nokia most of the jobs fall under this category. About the severely controlled and pre-described work organisation and the very flexible working time Hammer says: "The creativity of our product has to be reflected in the creative solutions found for our work conditions".
At the notice board the union group at Nokia informs about re-structuring measures demanded by the management, allegedly necessary in order to secure jobs. Some of them had already been implemented: the number of temp workers agreed on in the collective contract has been increased from 550 to 800 and starting from autumn 2005, to 1,200. This means that more or less every second worker in the production department is a temp. All extra payments that exceed the general collective contract for the metal sector are cut, which is supposed to result in a 20 per cent drop in labour costs.
For a permanent production worker this would mean a monthly wage cut of about 70 to 120 Euros. The total monthly wage before tax is between 1,600 and 2,200 Euros. The working-time is planned to be increased from 33.5 hours to 35 hours, although due to overtime and extra-shifts people usually work longer hours anyway. The works council asks the workers to refuse to cash in holidays: because of the low market activity last year a lot of people have 'minus-hours' in their working time accounts.
The company is asking to compensate these minus-hours with holidays. The management threatens with official negotiations with the metal union about a 40-hours week without wage compensation (five hours longer working-time per week) in case that there will be resistance against further cuts from the local workers representatives. The works council informs that due to its allegedly weak position it will refer to the worse general collective contract, as well, instead of trying to defend the better 'in-house' contract. A very interesting, recent and detailed study on the impact of global mobile phone production on workers and environment can be found here: http://www.somo.nl/html/paginas/pdf/High_Cost_of_Calling_nov_2006_EN.pdf
Hiring Process
The local temp agency WIR advertised that they would hire people for a company assembling locks for the car industry. In the office a lot of Iranian, Pakistani and Syrian students are waiting, the agency has sent them to work at Nokia. At 2pm the temp manager signs your work contract and you can start working at Nokia the same night. When you listen to his phone calls or the conversations of the students you soon find out that a lot of people did not come to work today, that they have difficulties to find replacements. This might be due to the low wages; you get 6.80 Euro per hour before tax and no extra money for travel expenses. Fifteen years ago a helper on the construction site would not have received a lower wage, but general living costs were probably 30 to 40 per cent lower. WIR employs about 80 people per shift at Nokia, in total 240.
The Composition of the (Temp-) Workers
A lot of the permanents are female, in their forties and from eastern European countries. No-one has been made permanent for years. The temp workers are younger and mostly from Turkish backgrounds, or students from even further south. The permanents have a Nokia patch stuck to their working jackets, the temps don't. I would guess that 60 per cent of the production workers are female and 70 per cent with a migrant background. German men mainly drive forklifts. The temp workers have various working experiences: a single mum who worked on the assembly line at Hella (supplier for the automobile industry) before having the baby, or a young bloke whose parents are from Iran and who just finished an apprenticeship as a mechanic in a nearby coal-mine. The permanents refer to 'permanent temp workers', people who work at Nokia for quite a while, but who now are on holiday. The 'temp-temp workers' have to jump in, mainly students on university holiday.
Work organisation
The factory is well guarded. There are special entrance doors for temp workers, where they have to sign for new company ID cards every morning. The management allots them special locker rooms; each temp agency gets a different one. The control when leaving after work is also rigid. People have to queue up in order to return their company ID, some have to open their bags, and every fourth worker is subjected to an airport-like body search. These measures extend the unpaid daily working-time. We have to be at the gates half an hour before shift starts and we wait another half an hour after work to pass the checkpoint.
Inside the plant there are several huge halls. In the departments there are stalls for the various temp-agencies, the managers sit behind them and tell their people where to go. In the production hall the so-called engines are manufactured, the heart-piece of the mobile. The circuit boards have already been assembled somewhere else; the cardboard boxes with plastic parts have Chinese or Taiwanese signs on them. Compared to the assembly and storage hall this hall is nearly empty of people and full of machines. In the assembly hall the so-called SOP (supply operations) take place, there are dozens of production islands, an electrician who works in maintenance says that there are 50 of them. The various elements of the production island (a scanner, an air-pistol, a testing device, an automatic screw-driver, a packaging machine etc.) are fixed on two meters high racks on wheels. These racks are positioned in a square, inside this square - people here call it 'the cell' - we work. Permanents say that the company experiments a lot with the positioning of the racks. They used to have a straightforward assembly line, but in June 2006 the management introduced these production islands. In the company magazine they call it 'pretzel-like production lay-out', maybe because people choke on it, more likely because people run in a pretzel-shaped circle when they shift from work-station to work-station. Usually there are six people working on one production island, three permanents and three temps. Above their heads there is a screen with numbers for the production target, for the already produced mobile phones and the efficiency rate. Most of the time these numbers are on a red background, only rarely on a green one. The production target per island per each seven-and-a-half hours shift is 1,000 assembled mobile phones. The target cannot be achieved without major stress, the ten square meters small pretzel-laid-out cell-structure is supposed to make people generate this stress amongst themselves. Roughly there are about a dozen single work-steps, from single parts to a packaged cardboard parcel with five smaller mobile phone boxes inside.
1) put three small plastic lids onto the 'engine' and the digital camera, check for possible gaps
2) press the created unit onto the key board, check for possible gaps
3) put the joined unit into the automatic screwer and take it out after two seconds
4) put the mobile phone into a testing device and take it out after ten seconds
5) put a label on the mobile and on its plastic bag
6) examine the mobile for scratches, put on the battery cover
7) put the mobile into the plastic bag
8) put batteries, head-set, power-lead into a cardboard box ('inner pulp')
9) put mobile, user manual, two flyers and a CD in the right order into the box
10) scan the label on the mobile phones plastic bag and on the cardboard box
11) weight the box and put another label on it
12) put five boxes into a bigger box and label it.
These work-steps are supposed to be shared out and combined freely amongst the six workers. If you have a short break at your station, go and help out at another one. If the already labeled mobile phones pile up, you are supposed to help packaging. The model looks similar to the work-organisation at McDonald's. The company magazine puts it like this: 'At the end of the day everyone is responsible for the continuity of the process (…) and everyone in the assembly department has to concentrate on the one-piece-flow' (Nokia People, 02/06). And it works, the people stress themselves out. While working together under such conditions with people from different backgrounds, origins and gender I develop an aversion against those people who talk about cognitive or affective work e.g. in call centres opposed to the rather unemotional manual work of the 'Fordist period'. To create human relationships and to maintain ones own emotional balance under such stress is one of the biggest affective challenges I ever managed to fuck up. As a reminder the foreman visits the cell every now and then and checks or complains about the achieved numbers. He also checks the toilet list, which everybody has to sign in and out from, and please only one person a time. If there is a lot of work to do, and there usually is, people are not allowed to have breaks together, only individually, while the others keep on working. Once a month a manager visits the cell, she stands in the middle for half an hour, observes the work-flow and ticks invisible criteria on her sheet. Some people would name this behaviour ('the henchman is snooping around'), others turn it into philosophy: 'Since March Nokia organises regular Kaizen-Events (original in English - Japanese) in the plant in Bochum. The idea originates in the Japanese production philosophy. It is all about avoiding Muda (waste) in the Gemba (place of valorisation)' (Nokia People, 02/06).
In addition to the manual stress of assembling 1,000 mobile per shift there is a lot of stress because of quality checks, re-adjustment of the machines and paper work for the packaging. If you see a little piece of dust under the display or detect a little scratch on a plastic part then you have to replace it. The flyers have to face a certain direction, the manual a different one. You risk an official warning if the label does not correspond with the boxes content. If you get three warnings you are out. It happens regularly that dozens of big parcels are re-opened again, because something 'went wrong', e.g. the CD cover was put in upside down. There are only two electricians/mechanics for 50 production islands. People complain about the fact that they are shifted to a different job in the assembly department without notice, that things change constantly, about the feeling of drowning in the one-piece-flow. After the experience of such stress and of handling such enormous quantities the fetish character of a camera mobile phone turns into scrap plastic. It is not only the work organisation that changes constantly, so does the working time. People are only told on Thursdays if there will be a Saturday shift or not. Two Saturday shifts per month are normal. At the moment there is a constant night shift and an alternating early/late-shift, but the management is debating a new model: two days early, two late, two night, two free. The temp workers are handled even more flexibly. At the beginning of each shift the list of temp workers is checked, if there are too many, more humans than the 'client has ordered', people are sent home again, sometimes in the middle of the night. Or the temp agency phones people in the afternoon, telling them that they do not have to come to the late-shift as planed, but to the early-shift next morning, because necessary parts have not reached the plant.
Kick out
Two female permanent workers were kind of alpha-females of the cell; they were addressed by the foreman as the responsible people. They had the main influence on the pace of work, due to experience and their position. Those temps who worked too slowly or had problems with the quality requirements were told off, always with reference to the general production target or possible formal warnings for quality flaws. A student from Syria was kicked out of the cell only after half an hour. It was not possible to behave according to something like a general workers' standard, e.g. when the target screen changed to green I ask one of the alpha-female who kept on pushing people: 'Is it not time to relax a little bit? Otherwise you will have to produce 1,200 mobiles a shift soon'. 'Whaaat?!', she answers in Bulgarian accent. We keep on arguing a little bit, then I go to the loo. When I come back the Finish manager is already waiting in the cell. 'You think you can ask people to work slower when the target screen is green?'. 'Nope, of course not. But maybe we breath a bit, just for a change'. When the manager is gone I ask the woman if she always tells him about what we say inside our cell. Another little argument. 'We have to make up for the low production numbers of last week'. After the break the temp agency manager arrests me and I have to leave the plant. In the temp agencies' office they offer a kind of penalty job in a small metal workshop somewhere in the fields, about 40 kilometres away. Thanks, but no thanks.
[prol-position news #8 | 4/2007] www.prol-position.net
Comments
Temp work at a shopping mall construction site, 2007
Prol-Position on casualisation and agency work on a German building site in 2007.
The Company
The City-Palais is a major construction project in the inner city of Duisburg, comprising of a shopping mall, a concert hall, a conference centre and a casino. Right in front of the City Palais another construction is about to be started, the Forum, another shopping mall. Germany's biggest inner city shopping mall is in the process of being built in Essen, which is only 25 kilometers away. In the late 90s the CentrO was opened in Oberhausen, situated between Duisburg and Essen. It is a huge shopping complex where about 4,000 people are employed. It was the biggest single investment in the whole Ruhrarea since the GM plant in Bochum. The decision to build the City Palais triggered the usual (petty) bourgeois critique lamenting about the consequences of for the small shop-owners and about the obvious links of corruption between the planning commission, construction companies and the local political class. More interesting is the question of why there is so much liquid capital flowing in such kind of rather prestigious projects and of the conditions under which workers build and run such new palaces.
The initial estimation for the total investment sum was 160 Million Euros, of which the LEG (Landesentwicklungsgesellschaft, Development Society of North-Rhine Westfalia, a kind of development and housing association) paid 90 Million. The remaining costs for the completion are supposed to be paid by the future tenants of the City Palais. The LEG is one of German biggest real estate companies. It owns about 110,000 flats in North-Rhine Westfalia and 1,200 acres of commercial land. In October 2005 the LEG announced privatisation of all flats, to put them on the market for international investment funds, a current trend in Germany, where thousands of flats are bought by mainly US hedge funds. This decision triggered some verbal protest by tenant unions. In October 2006 the LEG found a buyer for the City Palais, which was still a construction site at his point. The investment fund Hannover Leasing paid 100 Million Euro. Hannover Leasing invests in the international real estate market, in major infrastructure projects, the aviation, rail and shipping industries and in the movies. The fund has an investment pool of about 7.5 Billion Euros and it manages investment projects worth 11.5 Billion Euros. At this point LEG announced that about 85 percent of the total 35,400 square meters commercial area had already been rented out. The biggest tenant is Germany's biggest casino operator, West-Spiel.
The main construction company is Bilfinger and Berger, they also build the shopping mall in Essen, and the main local company is Hitzbleck. During the early stages about 200 workers were on the site, during the completion phase up to 700. After the police organised a raid on the site during summer 2006 the newspapers reported that some companies employ workers illegally and pay less than the minimum wage. In October 2006, half a year after the construction started, the project lagged four weeks behind the schedule, and the town administrations agreed to extend the working shifts. It also became clear that the costs for the concert hall and the congress centre covered by the City Council would be considerably higher than expected. The town parliament voted for a 3.6 Million Euros top-up in addition to the already allotted 35 Million Euros. The PDS (Party of Democratic Socialism) explained the rather swift decision by the fact that the SPD (Social-Democratic Party) town director Brand is at the same time the City Palais project-manager in charge of the completion work. The following report describes the working condition during the completion phase of the project. [http://www.citypalais.de/index.php?typ=html&content=Story&sub=1]
Hiring Process
Tremonia, a German-wide operating temp agency, looks for electricians to wire fire-alarm systems, video cameras and door-contact systems on the City Palais site. You can start working the next day. Tremonia has a collective contract with the small Christian union (see first part of article), which pays 9,80 Euro per hour before tax. They don't pay any money for travel costs, no other extras. Tremonia employs five temps on the site.
The Composition of the (Temp) Workers
Three of the Tremonia workers are in their mid-40s, experienced electricians. They have been unemployed for about a year before they took the job at Tremonia, mainly because the benefit office started to hassle them and the Hartz IV unemployment benefit was too low an income in the long run. One of them has been working for temp agencies for a long time, he worked as a maintenance electrician in coal mines, in the automobile industry, he loaded trucks for supermarkets, he renovated shops in Spain and wired up the lion cage in the zoo of Wuppertal. He is the typical hooligan-type from Essen, a full-monty Ruhrarea prole. The second story he tells you is about his worries: it is his first trip to Nigeria next January, his wife and he will celebrate their marriage ceremony in her Nigerian village and he is a bit concerned about the dancing. This is one of the great things about the Ruhrarea, where unlike in a lot of more metropolitan areas people tend to mix more. The two other workers are in their early thirties. Since the start of the construction work four months ago, five Tremonia workers have already left the site, two because of the long working-hours, the others were sent back home because the client (hiring) company was not happy with them.
The client company is called Heinrich, a bigger handicraft company specialising in electrical installations. The company is from Leipzig, a bigger town in the east of Germany, about 500 kilometers from Duisburg. There are five permanent workers from Heinrich on the City Palais site, although the number varies given that Heinrich has more people employed on a hospital building site ten kilometres away, people sometimes have to work there, others are coming over.
There are two more Tremonia people on the hospital site, one of them used to work as a temp worker in the famous BenQ mobile phone plant near Duisburg, but was kicked out after the dismissals started [see prol-position news no. 3/2005]. The ten workers from Leipzig share two small flats in an empty nurses' dormitory on the hospital premises. They drive back to Leipzig on Thursday night or, which is normally the case, on Friday afternoon. They have to return to Duisburg on Sunday early afternoon. According to traffic they need about six to nine hours for their journey back home. They say that there isn't much work for electricians around Leipzig.
One work-mate from Leipzig used to work in an automobile supplier. (There is a booming Porsche and BMW factory in Leipzig. In the whole of East Germany there are three German car manufacturing plants, and two of them are in Leipzig.) But the supplier demanded CNC skills from him, and although he was employed as an unskilled worker, they wanted him to work Saturday and Sunday shifts without extra-pay. The stress-level was high. This fifty-year-old worker quit the job and as a result the unemployment office cut his benefit money for eight weeks. Another work-mate became unemployed after the small handicraft workshop went bankrupt. He still fights a legal case for unpaid wages. All the workers have been unemployed for a while, half of them for longer than a year, long enough to get your benefit reduced to the Hartz IV minimum. The company Heinrich got a sub-contract from the company Imtech. Imtech in turn got the contract from Siemens. Siemens now only supplies the engineers who manage the technical coordination between the various sub-contractors. The fire-alarm system is installed by several smaller companies, which got individual contracts, e.g. to wire the parking garage.
The minority of workers on the site are from West Germany. The west Germans tend to be the managers, engineers or foremen from the main construction company; managers of the Turkish cleaning gang; temps like us; or some specialists crane drivers or maintenance crew for the machinery. The big chunk of people come from East-Germany, Poland, Bulgaria. Most of the companies are very small, often self-employed gangs, so you might find four or five companies working on the installation of the video cameras, or a dozen companies putting up plasterboard-walls.
Work Organisation
There is a turnstile at the entrance of the site, which you can only pass with a special ID-card. There is a lot of valuable stuff on site, and things do get stolen. Sometimes this is rather uncool, given that a lot of the tools and material belong to the self-employed workers. On the site you are supposed to wear your helmet and the ID-card with a digital-picture of yourself, otherwise they fine you 50 Euros. As a temp worker you get this ID-card too, but no tools to work with. We asked Tremonia several times to give us some smaller basic hand-tools, screw-drivers and stuff, but they found all kind of excuses.
Finally some of us bring their own tools, something that becomes negatively trendy for wage-workers. Others refuse to do that and use tools of the Heinrich company, meaning that they have to uselessly run around a lot. After the shell has been completed the main building company only does little supervising and coordinating work, they organise the site control, the transport of material, the cranes, they allot porter cabins and hassle the thirty Turkish cleaners who have to sweep the site twelve hours a day. The coordination of the different crafts is divided up, e.g. the Siemens engineers command all the smaller companies and work gangs doing electrical work, often mediated by the direct contractors, in our case Imtech. They also pass the installation plans on to Heinrich and the Heinrich coordinating worker hands them out to us. Usually a Heinrich worker and a temp then leave together and start working, at least the big boss in Leipzig wants that the temp is always with a permanent, but he is in Leipzig and often people prefer to choose their immediate workmates. The main work is to install cables for the fire-system and the cameras, to put them into an already fixed rail if possible, or to drill and hammer in new rails. There are literally thousands of kilometres of cable running through the site, and most of them run at seven metres high. The site is huge, three football fields plus three major sub-terrain garages for about 700 cars.
So most of the time you run around or wobble on mobile scaffolding, banging steel anchors for the rails into the concrete over your head. The time pressure, the hierarchical work organisation and the divisions into dozens of single companies not only creates stress, but unnecessary extra-work and delays, as well. For example often the guys who build the structure for the double ceiling start their work before we manage to get to the cable-rail. It is a real bugger, because you then have to kind of snake-dance yourself and the 500 metres long cable through the metal frames. Or you drive the hired mobile scaffolding to the other end of site, which takes about 40 minutes, destroys various cables on the floor and the already started marble work only to find out that there are already five unused scaffoldings waiting. But they belong to other companies and some people take that fact very seriously.
The main engineers wanted to change two walls in the car garage, which had the domino effect of changing the entire fire-safety zones, which annoyed the Siemens engineers, but they passed the changes and costs on to Heinrich and we then had to rip out cables which took two men one and a half months to install. All this creates the typical construction-site quarrels, mainly between Prussians (big lads from East Berlin) and Saxons (rather skinny moustached guys from Leipzig), which might still be some kind of conflict from times of socialism. But disputes can be settled in comradely manners, even with Albanian marble-stone masons, once you start cursing the general building project's management. There is no arrogance or rivalry between temps and permanents, mainly because the conditions for the east-German permanent workers is equally shitty or even relatively worse and because the building trade is somehow temporary anyway, meaning that the Leipzig guys cannot be sure if there is work after the project is finished.
Wage and Working Time
Compared to the permanents, from Leipzig the temps from the Ruhrarea earn more and work less. We get about 10 Euros per hour while the east-German get about 8 Euros, we work about 40 hours per week, they work up to sixty. They have to be away from home during the week, they don't get any extra money for that, they often arrive home late Friday night and half of the Sunday they spend on the Autobahn. An experienced electrician and proper family father, a work-mate from Leipzig tells us that since 1992 he has never earned more than 7.50 Euros an hour before tax and that he is therefore trying to keep this bloody job he has.
He even puts up with the other guys drinking and gambling half the night while he tries to get some sleep on the living room sofa. He also puts up with delays of the wage payment; in October the Heinrich workers had to wait two weeks. A workmate from the Ruhr area slips the collective contract for building workers to the guys from Leipzig. If their company had been in the employer's association they would have got a nice 40 per cent wage rise, or the sack. All in all there are only few discussions about the possibility of improving the situation. The conditions and relationships seem somehow temporary.
Rien ne va plus
The work ends with an accident, the scaffolding collapsed, it belonged to an unknown work-gang, no one to sue, the wrist collapsed, as well. The doctor, who is in charge of the site says that he gets quite regular visits from injured workers from the City Palais. Broken bones for Starbucks and the roulette. One month later all the temps got fired, Heinrich could not pay Tremonia anymore, the City Palais chaos busted their budged. Tremonia had no other jobs for the temps, so we all got laid off. We don't know what happened to the permanents from Leipzig.
[prol-position news #8 | 4/2007] www.prol-position.net
Comments
Conclusions
The different reports show clearly that we will not be able to derive a radical and generalising political line from the sheer precariousness of the jobs, from the legal contract relations of temp work. The possibilities and material starting-points for initiatives vary, particularly if we take into account that unlike in the examples above, a lot of the temp work is not done in major companies or industrial surroundings. Very interesting front lines could appear where, due to regional or industrial concentration, (temp) workers come together in a tangible context of common experiences which goes beyond company boundaries. In the Ruhr area this could be the case, e.g. at Gate Gourmet and at GM there were temps who had common experiences with working at Nokia, at GM some temps previously worked in various automobile suppliers.
It would also be important to analyse the political potentials of the fact that hundreds of foreign student-workers are exploited at Nokia in Bochum while at the same time there are various activities and a long occupation at the university in Bochum, against fees and the increasing pressure on students. Contrary to common opinion, it is possible (for people between aged 20 to 45) to get a job in the core industries within a short period of time, but for wages that motivate half the people to leave the job after a similarly short period. This might be an important background situation for possible initiatives. Another parallel between the above examples is the temp agencies using union negotiated collective contracts to justify the low wages. In all four industrial companies the temps are lured with the 'promise' of a long-term stay as temporary workers, the possibility of getting a permanent contract after a certain probation time was never even mentioned.
At Nokia it was clear that the management is able to extend the number of temp workers to over one thousand so that half of the staff in the production department are not really attached to the company. All this in a world-market factory for mobile phones which is situated less than an hours drive away from BenQ, another big mobile phone plant where workers gave a good example of how to loose a struggle by not even starting it. At GM the precarious experiences of the temps mix with the experiences of a combative industrial stronghold under attack. Thanks to the still effective resistance of the permanent workers, temporary work is still a minor factor there, but highly concentrated, particularly in the pre-assembling departments and in logistics.
One of the other tragic results of the long strike at Gate Gourmet is the fact that temp work, which was one of the main levers to undermine and finally break the strike, is now used in order to restructure the work-organisation. The main weakness of the strike was, that it was neither able to prevent scabbing nor was it able to build a bridge to the temps which would have allowed them to join the dispute. The failed little action at GM shows that at least during an embryonic stage of struggle, the legal right of the bosses to kick people out from one minute to the other poses a serious problem. The example of the major construction project made clear that 'precarious conditions' and low wages are not only a concern for temp workers, young folks or the creative self employed, but became part of daily life experience for the family-father-type handicraft-worker, as well. Let's see who moves first.
[prol-position news #8 | 4/2007] www.prol-position.net
Comments