Issues of the Gurgaon workers news letters with news, workers' reports and analysis from the Indian boom region.
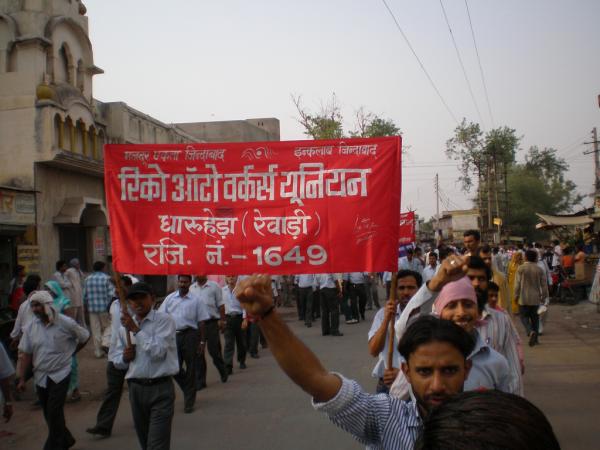
Attachments
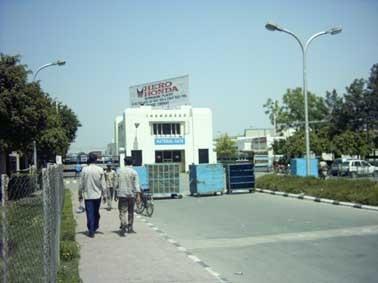
A brief introduction to the Gurgaon Workers News project.
Gurgaon Workers’ News is a project independent from political parties or unions, trying to support workers’ self-organisation in their struggle for a better life. One of the projects aim is to document the development and workers’ struggles in and around Gurgaon, one of the current boom regions of global capital. For this reason we publish a monthly electronic newsletter on our site.
GWS is not meant to be a purely documenting project, it is not supposed to be a one way street. We plan to distribute a regular newsletter/leaflet amongst workers in the area which, apart from local news, would contain workers` information of related industries, companies or boom regions from other places in the world. If you want to have your information distributed to workers of a specific company, see list of companies on the site, or if you would offer to do the same at your place, please get in touch.
web: http://gurgaonworkersnews.wordpress.com
e-mail: gurgaon_workers_news at yahoo.co.uk
Comments

English-language edition of the class struggle newspaper produced and distributed in Gurgaon, in the Indian state of Haryana. Contains workers' accounts of their experiences, reports of collective action, and analysis of the intense development of the city.
Gurgaon in Haryana is presented as the shining India, a symbol of capitalist success promising a better life for everyone behind the gateway of development. At a first glance the office towers and shopping malls reflect this chimera and even the facades of the garment factories look like three star hotels. Behind the facade, behind the factory walls and in the side streets of the industrial areas thousands of workers keep the rat-race going, producing cars and scooters for the middle-classes which end up in the traffic jam on the new highway between Delhi and Gurgaon. Thousands of young proletarianised middle class people lose time, energy and academic aspirations on night-shifts in call centres, selling loan schemes to working-class people in the US or pre-paid electricity schemes to the poor in the UK. Next door, thousands of rural-migrant workers uprooted by the agrarian crisis stitch and sew for export, competing with their angry brothers and sisters in Bangladesh or Vietnam. And the rat-race will not stop; on the outskirts of Gurgaon, Asia’s biggest Special Economic Zone is in the making. The following newsletter documents some of the developments in and around this miserable boom region. If you want to know more about working and struggling in Gurgaon, if you want more info about or even contribute to this project, please do so via:
www.gurgaonworkersnews.wordpress.com
gurgaon_workers_news[at]yahoo.co.uk
Comments
The following story has been published several years ago in the Hindi workers’ newspaper Faridabad Majdoor Samachar. We document it in the wider context of workers’ reports, demonstrating the hidden side of the factory world. Recently a new documentary on ‘house-workers’ in Delhi has been published, click here for the announcement.
I am not yet 35 years old. My husband and elder son both work. I look after the house and also earn some money from stitching and embroidery. Every day I get up at a.m. I have to go out for latrine in the open. It is dark. I fear pigs and dirty men. (Men sit and hide). It’s forced on us. I have to prepare for it. After coming back, I fill up water from the public tap. If it is not crowded, it takes twenty minutes, otherwise it takes an hour.
After bringing water, washing the dishes, cleaning the place then I cut the vegetables and grind the spices. I don’t use readymade spices. My husband works in Okhla now and he has to catch the 7:40 a.m. train. On one stove, I cook vegetables and on the other I make rotis (bread) after kneading the flour. Sometimes, on the kerosene stove, I have to heat up the water because my two kids have to get ready for school. After the vegetables are ready, I make tea. My husband has to leave home at 7:15 a.m. to catch the train. The children leave at 7:45. In the morning, they have breakfast of roti and vegetables and then drink tea. My husband also takes his rotis. The children come back at 1 p.m. and eat. After I’ve completed my work then if some tea is left, I drink that or I make another cup. I drink tea but I don’t feel like having breakfast. I heat up water and have a bath. Then I wash the dishes, broom the place, fold up the beds. I work very fast but still it is ten to 11 before it’s over and if some guests come in it takes more time. Then I take rest for an hour or two.
I again fill up water in the morning from the public tap. I have to collect water three times in a day. Then work for money. I stitch a pajama for ten rupees. An underwear for five. A petticoat for ten rupees. Contractors bring clothes from factories on which I do embroidery at piece rate. It is 4 to 5 p.m. By the time I bring milk and vegetables from the market, it is time to start preparing for dinner. Taking it all into consideration, it means that I cannot take care of my body. There is no time for myself.
My eldest son has night duty for 15 days in the month. Today he has night duty. He has to go at 8 p.m. from the house. I had prepared food by 7 because if he leaves immediately after a meal, then he’ll have a stomach. He eats one hour before and takes some rest. At this time, he is also ill. His duty is of 12 hours. From 8 p.m. till 8 a.m. tomorrow, the boy of 17 years old has to stand at a plastic-moulding machine for 12 hours every day. I feel a lot of pain. I wish he didn’t have to work but he is forced to. How can I have him sitting idle at home?
By 9:30 p.m., everyone is free and lies down for bed and watches T.V. Sometimes, I am not able to sleep the whole night because of worries. When I’ve fall ill, I worry about who will do my work as my son and husband go to work and my children go to school. If you take help from someone then one fears the false allegations by neighbors of having a ‘loose’ character. My daughter is getting older (she is 13) and I keep thinking about her. I have to carry so many burdens, yet have to still keep going. How can I go on? I have not even lived half of my life. My blood-pressure goes down very low and I have very bad thoughts. If I die, what will happen to my children? Now I don’t feel like meeting people whereas earlier I used to get-together a lot with people. Now my daughter has become a great support for me.
When I was 12 or 13 years old, I was married. And my husband and I stayed like two friends. Our children respect us. Again and again I try to convince myself that my children will support me. Like others’ children, my sons will not leave for their marriage. The fear of being left alone in old age…I cut down on meals to save some money so that at least their greed for money will make our children look after us in old age. When I get too tired then I become irritated and think why is this life being given to me? Death is better than this life.
Faridabad Majdoor Samachar, 2003
Comments
The distribution of Faridabad Majdoor Samachar has recently been extended to the new industrial area of Manesar, near Gurgaon, an area dominated by the automobile industry. We document short reports from automobile workers, mainly within the fractured cooperation of parts manufacturing. Recent struggles like at Rico, Denso, AG Industries or VXL, workers have not been able to extend their disputes along the arteries of this vast territorial assembly line.
Honda Motorcycle and Scooter Worker
(Plot 1 and 2, Sector 3, IMT Manesar)
There used to be joint buses for the 1,800 permanent and 5,500 workers hired through contractors – now they introduced separate bus transport. Both categories of workers used to use the same gate for entering and leaving the factory, now they introduced separate gates. Every worker used to have the right to 2 paid hours monthly for getting the gate pass, now this right has been reduced to the permanent workers – they say that there is too little admin staff, so they try to deprive the workers hired through of the gate pass. The management has recently increased the production target from 1,125 to 1,200 scooters. When workers met the new target the management distributed sweets – only to the permanents, not to the workers hired through contractors.
Munjal Showa Worker
(Sector III, IMT Manesar)
The factory runs on three shifts, manufacturing shocks and suspensions for Hero Honda, Honda, Yamaha. and for spare-part shops. There are only very few permanent workers. There are 500 casual ITI workers and 800 workers hired through four different contractors. They entice the casual workers by promising a permanent contract after five years – actually the workers are kept in a loop of ‘casual worker becoming trainee’ and ‘re-trainee becoming casual worker again’, no one gets a permanent contract. The workers hired through contractors are given enforced ‘breaks’ after six months of employment. The wages for the ITI worker is 4,500 Rs and for the workers hired through contractor 4,214 Rs. The wages are low… If you have to work in a standing position the whole time, then doing overtime means hell. We work 100 to 150 hours overtime, it is paid less than double rate, about 35 Rs per hour.
VG Industrial Worker
(Plot 26 F, Industrial Area, Faridabad)
We produce parts for export to Australia. In the plant only foremen, supervisor and managers are hired directly by the company, all workers are hired through contractors. The workers’ wages are 3,000 Rs, neither PF nor ESI. We work 12-hours shifts. On the obligatory weekly holiday we work 8 hours. Overtime is paid at single rate, wages are paid late. VG Industrial runs another factory on Plot 31 B in Industrial Area, a paint shop. The wages of the 25 workers hired through contractors is 3,000 Rs, neither ESI nor PF. In the GPS press-shop and the Model B press-shop they run two 12-hours shifts, day in, day out. The fixed production target is high, they pressure you a lot, the supervisor swears at you, there are accidents at the power-presses: in one year I have seen 10 workers cutting their hands. In the weld-shop and the packing department they make you work 4 hours extra, after a 12 hours shift. Every month 400 to 500 Rs get embezzled from your wages. The 300 Rs for DA in January 2010 was not paid yet (April 2010).
Haryana Industries Worker
(Plot 318, Udyog Vihar Phase II, Gurgaon)
In the factory about 2,500 to 3,000 workers produce parts for Maruti Suzuki. There is no day off. For 30 working days of 8 hours we get 3,500 Rs. Normal working-times are from 9 am till 8 pm, the second shift from 8:30 pm till 9 am. Overtime is paid single rate. On 22nd of April 2010 a worker cut off four of his fingers at a power-press. Workers don’t get ESI, if you cut your fingers, they make you pay for private treatment. The drinking water is bad, the toilets are normally locked – they open them only in the evening.
AG Industries
(Plot 8, Sector III, IMT)
The 100 permanent workers work on three 8-hours shifts, the 500 workers hired through four different contractors work on two 12-hours shifts. The factory runs 30 days a month. The factory manufactures fibre-side-covers for Hero Honda. The permanent workers get 7,000 to 10,000 Rs, the workers hired through contractors who run the moulding machines get 4,214 Rs. The permanent workers started to set-up a trade union, so the company sacked 5 and later on 13 permanent workers in January and February 2010. After back-and-forth workers laid down tools on 20th of March and gathered inside the factory premises. Permanent workers and workers hired through contractor stood side by side. The company called the police. They arrived in two buses, they first pushed workers out of the factory, then told them to keep a 200 meters distance to the company gate, and they attacked the workers with lathis in order to make themselves understood. One worker ended up with his hand broken, several others had bleeding heads. The police followed workers right into Sector V, beating them with lathis. Later on the police returned and smashed the window-pane of the companies’ security room and of their police car. On the very same 20th of March some workers turned up for the evening shift and started working – the management worked, too. On the next day, the 21st of March, two Hero Honda company buses from Gurgaon turned up, full with workers. They got paint-shop workers from Dharuhera and Gaziabad. New people were hired at the gate everyday… On the 26th of March, the union had a demonstration in Gurgaon. Over 10,000 people came, there was an assembly in Huda Park. They handed out food. But afterwards nothing. We kept on sitting 100 feet away from the company gate. Leaving their victimised 18 work-mates outside, the permanent workers decided to go back to work on 2nd and 3rd of April. The 500 workers hired through contractors pay for ESI and PF, but see neither card nor PF fund number.
VXL Worker
(20/3 Mathura Road, Faridabad)
The management had laid out a trap for yet another wave of redundancies. The number of permanent workers had already come down from 400 to 93, the management wanted to lay off another 46 employees. By instigating they created an atmosphere for a lock-out, which happened on the 6th of February 2010. Not surprisingly the management proclaimed that the workers were engaging in an illegal strike action. In order to move the demonstrating workers away from the factory gate the company cut the water supply on 2nd of April. During February, March and April both union and management had 15 to 20 separate meetings with the higher levels of labour commissioners, no joint meeting at all. The main outcome seemed to be that 7 workers would be sacked, 4 suspended and 41 transferred to other places, but the government official said that the company would not agree. After the 3rd of April even these type of meetings ceased… Therefore the union called for demonstrations on 20th of May to walk from the factory gate to Bata Chowk, on 21st of May to walk from the factory gate to Goodyear Chowk, on 24th of May to walk to the office of the labour commissioner. On 25th of May the labour official and labour inspector came to the workers and told them to stop the demonstrations, to stop causing public commotion and to talk again. On invitation from the management there were talks between company representatives and union leaders on 28th and 30th of May. Us workers still – today on 1st of June – don’t know what the outcome of these talks was. The company produces bomb-timers for the army and other electronic items. The management has replaced permanent workers with casuals and outsourced work to 50 suppliers.
Kiran Udyog Worker
(B-182, Okhla Phase I)
The 110 workers hired through three different contractors are paid 3,300 to 3,800 Rs. They get neither PF nor ESI. The 40 workers who are directly employed by the company get ESI and PF, but the helpers wage is below the minimum, they get 3,800 Rs, the operators get 4,300 to 4,800 Rs. You start working at 8:30 am and finish at 11 to 12 at night. There is a 12-hour night-shift, too. Overtime is paid at 12 to 16 Rs an hour, 100 to 200 Rs are embezzled each month. The factory produces parts for Honda and Denso in Noida. The drinking water is bad, there is only one toilet, people have to queue up. The bosses swear and sometimes hit workers. If you are 5 minutes late they cut one hour from your wages, but shift finishes 10 to 20 minutes late, which is not paid. Tea breaks are 5 instead of 15 minutes. There is a lot of pressure, lots of accidents – but workers have to pay for medical treatment themselves.
Micro Precision Worker
(Plot 96, Sector V, IMT)
They pay you the minimum wage, but instead of 8 hours they make you work 10.5 hours. We manufacture dies for Hero Honda, JBM, Neel Metal and other companies. There is also a lot of sheet-metal work, lots of workers get injured. The managing director swears a lot, sometimes he hits people. The shift runs from 8 am till 8 pm, sometimes you have to work till 1 am. Overtime is paid at single-rate.
Yamaha Motors Worker
(The factory is situated at Mathura Road, Faridabad)
The company hires young workers who have completed ITI as casual labourers. After seven and a half months of employment the companies sends workers on an enforced ‘break’. After that the company hands out ‘Vancancy’-leaflets and sends the former casual workers to a labour contractor. The former casual workers are now hired through contractor and work in the same department as before. The wages are the same, but the ESI and PF numbers have changed. After seven and a half months these workers are officially sacked by the contractor and re-hired as casual workers by Yamaha. Workers work since ten to twelve years in this ‘casual way’ at Yamaha. The work is permanent, the workers are non-permanent. The permanent workers get 25,000 Rs, doing the same work their casual/temp work-mates get 4,734 Rs. The helpers get 4,214 Rs and they have to pay a bribe for getting hired. Yamaha company only issues one T-Shirt for the casual workers, some of the contractors don’t even do that. There are three shifts, in the A-shift mainly permanents work, so in the C-shift mainly casuals are employed. The B-shift finishes at 2 am, that’s when the C-shift starts. There is a lot of trouble in these shifts – and once you are on C-shift you stay, shifts don’t change.
Oswal Electrics
(48-49 Industrial Area, Faridabad)
Around 1,200 workers are employed on 2×12 and 3×8-hours shifts, manufacturing parts for TVS Motorcycles and Orient Pankha. If they make you work double-shift, meaning 16-hours, they only give you 9 Rs extra-money for food – only few get 12 Rs. Overtime is paid at single rate. The machine operators are only paid the minimum wage for helpers.
Northern Tools and Gadgets Worker
(Plot 330, Sector-24, Faridabad)
Workers manufacture parts for Maruti Suzuki on 2×12-hour shifts. They force you to work overtime on Sundays – there is no day off, you work 30 days a month. The 90 casual workers are employed throughout the year, but they neither get ESI nor PF. Their March wage was 3,000 Rs. They said that wages would be increased to 3,500 Rs by April, but they paid only 3,000 Rs in April, too.
Super Age Worker
(Plot 109, Sector-6, Faridabad)
Workers work 150 to 200 hours overtime. Workers manufacture parts for two-wheelers of Yamaha, Bajaj, Hero Honda and parts for export to Dubai and Kuwait. Wages are paid with delay.
Pranav Vikas Worker
(45 – 46 Industrial Area, Faridabad)
The company employs 10 to 12 workers directly and 250 workers through 5 to 6 different contractors. They manufacture heating and cooling coils for Maruti Suzuki, Scorpio and Ambassador. Around 125 to 240 hours overtime, the permanents get double pay, the rest single. If you are forced to work 16 hours non-stop, they don’t even give you extra-money for food. The workers hired through contractors used to get two working uniforms per year, since three years there have been no uniforms at all. Money is cut for ESI and PF, but you will hardly get an ESI card and you have to pay 1,000 Rs bribe to the contractor in order to get the PF fund.
Comments
The international market pressure between low-wage regions like Vietnam, Cambodia, Bangladesh or India translates directly into excessive work-load on the shop-floor. Below you can find some reports, published in May 2010 issue of Faridabad Mazdoor Samachar under the title “Make it through the day… or Living life”. The monthly minimum wage (April 2010) at the times for unskilled workers in Haryana: 4,214 Rs (6-days week, 8-hours day), Delhi 5272 Rs. On 20th of August 2010 the Haryana minimum wage was increased slightly to 4348.21 RS per month for unskilled workers.
In terms of general wage development we quote from the article on mechanisation:
‘His job in the sampling department (which creates the first few samples of every new design) of a large garment manufacturer and exporter fetches him Rs5,700 per month.”That’s a Rs1,700 increase in 10 years,” he says despondently, “while the price of atta has gone from Rs8 to Rs18.”‘
The following article on increasing mechanisation is a good summary of current conditions, but in its predictions it is ideologically tinted. Obviously the spokes-people of capital want to make themselves believe that potentially they are able to replace workers with machines. Nevertheless, the article hints at some important changes within the organisation of garment production, e.g. the expansion of ‘chain-systems’, a more minute division of labour, and the introduction of computer-controlled machines for certain work tasks like thread cutting or embroidery. Often these work-steps have been undertaken by ‘helpers’ and/or female workers.
These Garment Factories Don’t Need Tailors
Live Mint By Akshai Jain (June 2010)
As garment units in Gurgaon scale up into mass manufacturing centres, machines are doing the trickiest work, cutting out the craftsman. When Santosh Kumar Kaushal came to Delhi from Allahabad 20 years ago, he found a job easily. He was a competent tailor, having worked in a small tailoring workshop back home for nearly a decade. After a few years in similar units in the neighbourhood, he settled down in a “fabricator” workshop, a 30-person unit where tailors lived and worked, being paid according to the number of pieces they produced. Till 10 years ago, says Kaushal, he’d make Rs150 a day tailoring coats. “We worked to our own schedules,” he says wistfully, “the atmosphere was friendly and newcomers learnt on the job.” But time and the garment factories of Udyog Vihar in Gurgaon, where he now works, have been cruel to him. His job in the sampling department (which creates the first few samples of every new design) of a large garment manufacturer and exporter fetches him Rs5,700 per month. “That’s a Rs1,700 increase in 10 years,” he says despondently, “while the price of atta has gone from Rs8 to Rs18.”
Ironically, business is better than ever before in Udyog Vihar, one of the largest garment manufacturing hubs in the country. Exports of readymade garments, the mainstay of the manufacturing here, are again on the rise. In 2009-10, India exported garments worth $10.64 billion (Rs50,008 crore today). This year the Apparel Export Promotion Council (AEPC), a trade body, expects growth of 10-15%. The garment industries of the National Capital Region, spread across Gurgaon, Faridabad and Noida, contribute more than 28% of India’s total exports; and of this the largest contribution is from the 2,500 manufacturing units of Udyog Vihar. These units, says Darlie Koshy, director general of AEPC, make higher-end “fashion” garments for companies such as Gap Inc., JCPenny Co. Inc., Ivy Co., etc. Among them they employ around 200,000 workers, and are always on the lookout for more.
A skilled tailor such as Kaushal should not find it difficult to get another job. But a series of changes in the manufacturing process over the last decade have made his skills as a tailor redundant. It started with the flood of readymade garments from China and South-East Asia. Fabricator workshops found themselves outpriced and started shutting down.
Manufacturing shifted to factories, where the tailor went from being a craftsman to an employee. Where once a tailor would work on a single garment at a time, now the work was split up among three or four tailors. Productivity went up, and though payment continued to be at “piece rate” or per piece, the charges dropped.
Then about six years ago came the assembly line or the “chain system”. Processes were standardized, and new machinery was brought in to do everything from cutting cloth to sewing on labels and buttons. An army of 30-40 workers would now work on a single garment. One would do just the hem, the other the zip and the third the collar, etc.
Manufacturing costs came down even further, and a flood of international orders started pouring in. Suddenly there was a huge demand for workers, but they didn’t need to be craftsmen. Skilled tailors were relegated to small sampling departments and a new kind of labour started taking over in the factories.
These were unskilled workers brought in by contractors from Uttar Pradesh, Bihar and West Bengal. While it would take a tailor a year to acquire the skill to stitch a “full piece” or entire garment, these workers were pushed onto the assembly line after two weeks of training. They settled in vast sprawling tenements in areas such as Kapashera, near Udyog Vihar.
The nali wali gali (street by the drain), which meanders off from the main Kapashera-Gurgaon road, is one such tailors colony in an area infamous for its filth. Local landowners here have created large compounds with hundreds of windowless, matchbox-sized brick rooms that they let out to the garment workers. In the heat of the Delhi summer, the rooms are baking and oppressive. The only access to the compounds is over a concrete beam that spans an open drain clogged with sewage and plastic bags. Four-five workers cram into each windowless room, for which they pay Rs1,000 a month.
In the warren of mud lanes, the conversation is about the wages being offered at different factories. The workers stay with a factory for five-six months, before returning home to their families. When they come back, they find work in another factory. Their wages are around Rs3,600, just above the minimum wage in Haryana. But the work hours are long, stretching at times to 15 hours. They’re paid overtime, they say, but only at their average hourly pay, not double that, as is customary.
Dozens of small “tailoring centres” have come up in these colonies to train workers for the assembly line. Zakir Siddiqui’s centre is a dusty room, open on two sides, with six electric sewing machines. His paan shop sits by the entrance. Siddiqui does not have time for ceremony. The rates for the tailoring courses are scribbled on the wall. A two-hours-a-day tailoring course that teaches workers just a little more than how to sew a straight line, but enough to get them into the factories, costs Rs300. The training for a “checker”, short for a garment inspector, costs Rs800. The centre currently has 80 students.
The tuition is brutal. Siddiqui paces between the machines shouting at the students, rapping them occasionally on the knuckles. “I need to train them with a stick,” he says, loud enough for all the students to hear. “If I train a student in 15 days, I make a profit of Rs100, if they take a month to learn, I make a loss.”
Malti, a middle-aged woman from Bihar, dressed in a bright polyester sari, is staring intently at her machine. She’s worked in Udyog Vihar before, but as a thread cutter. Now she wants to get on the tailoring assembly line. That she hopes will get her a better wage. Students at the centre are guaranteed a job with the caveat that they will only work for a single company that Siddiqui has an arrangement with. The agent from the company, he claims, gets Rs250 for every worker he brings. How much Siddiqui gets, he doesn’t want to disclose.
Virender Kumar, a worker from Uttar Pradesh, is the product of one such “tailoring centre”. He now works on the skirt manufacturing line of a company. Each individual assembly line has 42 workers, six helpers and one master craftsman. Kumar is responsible for the zips. In the years that he’s been working in Udyog Vihar, the number of machines on the assembly lines has gone up dramatically, as has the production. “Five years ago, a single assembly line would have put out 150 pieces a day,” he says. “Today we make 400.”
Kumar’s salary in the meantime has increased from Rs2,800 to Rs3,604. Unfortunately for him, while the minimum wage in Delhi was increased by 33% in February, wages in Gurgaon remain the same.
The increasing mechanization in the garment factories is being driven by clothing companies. In an effort to improve and standardize manufacture across units that are spread around the world, the companies have started stipulating the machinery a unit should use. “That way at least 70-80% of the quality is assured,” AEPC’s Koshy says.
Kaushal, meanwhile, has reconciled himself to becoming completely redundant. It’s only a matter of time before even the handful of skilled jobs in the sampling departments are taken away by sophisticated computer-controlled cutting, or CNC (computer numerical control) machines that have just started appearing in the factories.
“Soon there will be no difference between us and the assembly lines,” he says stoically. Would he join a tailoring shop? “There’s no work to be had there.” An assembly line? “Never.” “Gurgaon,” Kaushal says with a wide sweep of his hand as he prepares to leave, “is no place for tailors.”
———————–
The following is a main-stream newspaper article on Marks and Spencer’s and other multi-national’s take on the condition in Gurgaon.
Britain’s top labels thrive on Indian sweatshop labour
London, August 08, 2010
Britain’s best-known high street stores — Gap, Next and Marks and Spencer — have reportedly launched inquiries into abuse of working regulations at their Indian suppliers, which have resulted in children as young as six being left alone while their parents work in outlets in Delhi and in the satellite township of Gurgaon on its outskirts. According to the London Observer investigation, factories were using workers hired through middlemen, and paying them as little as 25 pence an hour, in the case of Gap and Next, and 26 pence an hour for Marks and Spencers. All three companies told The Observer that they are totally committed to ethical trading and will not tolerate abuses in their supply chain. All said their own auditing processes detected the problems and that they have taken swift action to tackle them. Gap, which uses the same factory as Next, confirmed it had found wage violations and gave its supplier a deadline of midnight last night to repay workers who lost out. Marks and Spencers said it has yet to see evidence to support the wage claims. Workers claimed that those who refused to work the extra hours have been told to find new jobs, a practice defined under international law as forced labour and outlawed around the world. The factory has pledged to apologise and reinstate anyone who lost their job. Next said it had found the situation to be “deplorable” and added the chairman of the Indian company it uses has apologised and promised to make amends, blaming demand for workers at the forthcoming Commonwealth Games in Delhi for leaving factories short of staff. Gap admitted wage and overtime violations and ordered its supplier to reduce working hours to within the legal limits and to refund workers who have been illegally underpaid. Marks and Spencer admitted its supplier had been operating excessive overtime, but said it had acted quickly to tackle the problem.
(London Observer)
———————-
While Marks and Spencer announced on 8th of August that they keep an eye on their suppliers in Gurgaon, on 21st and 23rd of August the very same suppliers sent armed thugs to attack workers at Viva Global. Following a press statement:
VIVA – GLOBAL (GURGAON) WORKERS BEATEN UP- HUNGER STRIKE BEGINS TODAY
MAZDOOR EKTA MANCH
Plot No. 48, First Floor, Opp. Maruti Gate No.2,
Old Delhi-Gurgaon Road, Gurgaon, Haryana
Phone No. 0124-4385478,9910159352,9958613761, 927828635.
Venue of the Hunger Strike: Viva Global Factory, 413, Udyog Vihar,
Phase – III, Gurgaon – 122 016, Haryana, INDIA
Workers including of the Viva Global Factory, including women were
brutally beaten up with hockey sticks and lathis by goons called in by
the Management of Viva Global, the Gurgaon based sweatshop apparel
house. The incident happened this morning between 9:30 and 10:00 AM
when workers were to enter the premises of the Factory, as part of a
tripartite agreement between the Management of Viva Global, the Labour
Department and the Garment and Allied Workers Union (GAWU). The
agreement was the outcome of a meeting between the three parties, held
on the 23rd of August 2010. The prevention of workers entering the
factory, is a serious violation of the above agreement. Besides being
beaten, a few workers were abducted in a vehicle by the goondas and
taken to an undisclosed destination. At least one worker is still
missing.
To protest against the high handedness of the Management of Viva
Global and its utter contempt for any laws, rules and rights of
workers, the workers of Viva Global have resolved that the President
of the GAWU, Ms. Anannya Bhattacharjee will be on an indefinite hunger
strike outside the gates of the Viva Global Factory. The hunger strike
began today after a notice to this effect was given to the Labour
Department. Our demands are :- 1) The abducted workers be immediately
brought back. 2) All workers be reinstated and 3) The Management of
the Viva Global apologise to the workers. Representatives of the
Mazdoor Ekta Manch have also lodged a police complaint against the
management for the unprovoked violence on workers and the abduction of
workers.
Viva Global is a major supplier of apparel to ‘reputed’ multinational
superbrands such as Marks and Spencer. There have been serious
violations of labour laws and human rights at the Viva Global Factory.
The Management has been using strong arm tactics against union
leaders, representatives of workers etc., each time that the workers
have demanded that basic amenities and legal wages be given to them.
On the 21st of Aug 2010, at 6.00 PM, contract workers were locked out
of the Factory in an attempt to illegally terminate them. Other
workers (non-contract workers) had then demanded that contract workers
be given their rights in terms of notice pay and the PF amount that
has already been deducted from their wages. Even on 23rd of August,
when workers reported at the gate for duty, they were allowed to to
enter the factory. About 15 local goons with pistols had threatened
the Union leaders and workers. A group of workers and union activists
had then complained about the incident to the Labour Department which
led to the tripartite agreement which had resolved : 1) That there
would be no goondagiri by the Viva Global Mangement whatsoever, 2) All
workers who were locked out would be taken back. Another tripartite
meeting is also scheduled for Thursday the 26th of August for further
discussions. However, the Management of the Viva Global has already
violated the agreement of the 23rd of August.
We would request you to spread the news of the workers struggle at
Viva Global. We would look forward to your solidarity and support!
With thanks // Rajeev Singh.
For the Mazdoor Ekta Manch, Gurgaon.
Media Contact: P. Saleena : 9 6 5 0 8 4 8 4 8 0 .
—————————————————–
Below the long list of workers’ reports from other factories in Gurgaon, showing that Viva Global is not a single ‘black sheep’.
Workers’ Reports – Faridabad Majdoor Samachar
24th of May 2010
Shahi Export, Plot 15a, Sector 28, Faridabad
…after days of overtime many workers collapse. on 24th of May 53 workers are brought to the nearby hospital. they have to be treated with oxygene. 41 workers remain in the hospital. most of the collapsed workers are women…
24th of May 2010
NTL Electronics, Plot F-28, Sector 6, Noida
…after days of overtime six female workers collapse and fall unconscious…
13th of May 2010
Palam Export, Plot A-205, Okhla Industrial Area Phase I
…after having worked 19.5 hours a day for several month a 22 years old worker suffers a heart attack and 50 female workers collapse at work…
13th of may 2010
Sargam Export, Plot 153, Udyog Vihar Phase I, Gurgaon
…during night-shift two workers collapse and fall unconscious…
Enexco Technology
(157 Nourangpur, Gurgaon)
There is money for ESI and PF cut from the 175 casual workers’ wages, but only 15 got an ESI card, and the card is temporary. If people leave the job PF is not paid – the PF form not given. After several years of employment a casual worker said: “Actually we are hired through a labour supplier, through a contractor”. In the factory there are another 125 workers hired through contractor and 40 permanent workers.
Orient Craft Worker
(Plot 15, Sector 5, IMT Manesar)
The 26 thread-cutting workers get 3,000 Rs per month, no ESI no PF. Official shift-times are from 9 am till 6 pm, but they make you work till 2 am. Only if clients/buyers come to the plant workers are let go at 6 pm. We work 60 to 70 hours overtime per month, but the pay-slip only shows 12 to 15 hours. Overtime is paid double rate, but on Sundays they are paid less than single rate. Some supervisors swear a lot at workers.
JNS Instruments Worker
(Plot 3, Sector 3, IMT Manesar)
There are 15 buses who bring and return people to and from work. They work from 8:30 am till 5:30 pm, those 200 who work till 8 pm are returned in smaller cars. The male workers work on two 12-hours shifts. The workers hired through contractors get less than single rate for overtime: 14 Rs per hours.
Kailash Ribbon Worker
(403, Udyog Vihar Phase III, Gurgaon)
The helpers among the 400 casual workers get 2,700 to 3,300 Rs, the skilled tailors get 3,500 to 3,900 Rs – neither ESI nor PF.
Eltex India Worker
(887 Udyog Vihar Phase V)
The workers employed in the plant work 200 to 250 hours overtime per month. Sometimes they make you work from 9 am till next day 9 am and then force you to work another whole shift. The overtime is paid single, and 500 to 800 Rs per month are embezzled. The helpers hired through contractors get 2,800 Rs, neither ESI nor PF. The wages are always delayed, we haven’t received our March 2010 wages yet (24th of April 2010).
Sargam Export Worker
(153 Udyog Vihar Phase I)
There are an abundance of little irregularities going on in this factory: there is always some overtime left unpaid; people who had worked January and February 2010 and left the job since then were not paid the 300 Rs DA; those who leave now are not paid the statutory bonus.
Dheer International Worker
(299 Udyog Vihar Phase II)
People work 250 to 300 hours overtime per month. The payment is at single rate and 50 to 60 hours get embezzled per month. Wages are paid delayed.
Cosmy Worker
(864 Udyog Vihar Phase V)
The helpers working in this factory get 3,000 Rs. The skilled tailors get 140 to 150 Rs per day. Wages are delayed. If you leave the job you have major trouble to get your outstanding wages. Workers who go to the local ESI office in Dundahera have to face a lot of trouble.
Mac Export Worker
(143 Udyog Vihar Phase I)
The 400 workers employed in the factory get neither ESI nor PF. The helpers get 3,500 Rs. When being hired the tailors are promised 175 Rs for an 8-hour day, actually they are paid 150 to 160 Rs. The normal shift runs from 9 am till 9 pm, but they make you work longer, till 1:30 am. Overtime is paid at single rate, every month 300 to 400 Rs get embezzled. Lack of drinking water is a major problem in the factory. The toilets are very dirty. The big boss swears a lot.
Asian Handycraft Worker
(310 Udyog Vihar Phase II)
The helpers are paid 3,300 Rs to 3,500 Rs, the skilled workers get 4,000 to 4,500 Rs.
Kis Export Worker
(871 Udyog Vihar Phase V)
In the factory 450 workers are employed through two different contractors, they get neither PF nor ESI. The tailor helpers get 3,914 Rs and the tailors get 156 Rs per day. The 300 Rs DA statutory from January 2010 has not been added to the monthly wages. The thread cutting and bead-stitching women workers are paid 3,600 Rs. The daily working-times are from 9 am till 10 pm – 18 to 20 days per month they make you work till 1 am. About 100 women workers are send home at 9 pm, but a third contractor supplies 20 female workers who work from 9 pm till 1 am. There is no monthly day off. The male workers work 160 to 200 hours overtime per month, about 200 Rs get embezzled. There is a lot of swearing on the shop-floor, there is a lack of drinking water.
Security Guard
The office of the company Swift Security is situated at Nihal Bhavan in Dundahera. The company employs 6,000 security guards, on 2×12-hours shifts. There is no weekly day off. If you work 30 days per month, 12 hours per day they pay you 4,000 Rs to 5,000 Rs. Even after three to four years of employment they don’t give you ESI. They cut 540 Rs in the name of PF – when people leave the job, some are paid double amount of the fund money, some are paid single, some are not paid out at all. Sometimes you have to work 36 hours on stretch – they won’t give you money for food, and the overtime is paid single. Wages are paid with delay. If we don’t have any security ourselves, so will we give anyone else security? We just wear uniforms and stand around.
Eastern Medikit Worker
(292 Udyog Vihar Phase II)
The 300 casual workers were paid their March wages late, on 20th of April. The company did not pay the new minimum wage, only 3,870 Rs. The April wages haven’t been paid yet – 15th of May. The company does not include the DA of July 2009 nor the DA of January 2010. The casual workers work on two 12-hours shifts, the overtime is paid at 14 Rs an hour – March overtime has not been paid yet either. The management would not let casual workers leave after 8-hours, no matter if the worker is ill, no matter if he or she might drop dead.
Bharat Export Overseas Worker
(493 Udyog Vihar Phase III)
Non of the 300 workers employed in the factory get ESI or PF. The helpers in the finishing department get 120 to 130 Rs for an 8-hours shift. Workers work 150 to 200 hours overtime per month, payment is at single rate. There are three faulty fridges for drinking water. The toilets are very dirty.
Oberoi Hotel Worker
(Shankar Chowk)
The workers employed through Starling Vilasan work on the construction site of the five-star Oberoi Hotel. The 300 workers get neither PF, nor ESI. Their wages are below the minimum wage: 3,600 Rs.
Pearl Worker
(446 Udyog Vihar Phase V)
Even if management makes you work till 1 am, they won’t give you extra-money for food. Only the first two hours overtime are paid at double rate – the rest single rate.
Radhnik Export Worker
(215 Udyog Vihar Phase I)
If you want to get drinking water or go to the toilet you have to take a token. If they make you work till 2:30 am they give you 30 Rs extra for food, though the food in the canteen is not good. We work 80 to 100 hours overtime per month, they pay single, but force us to sign double-rate. The 500 skilled tailors get neither ESI nor PF – officially they run as employees of Om Enterprise, but management says, that when clients/buyers come to the factory we are supposed to say we are Radhnik company workers.
Polypack Worker
(193 Udyog Vihar Phase I)
If you take one day of per month, they mark all four weekly days off as absent, even so you have worked. This means that you lose 720 Rs of your monthly wage. The daily shift times are from 8 am till 8:30 pm, they often make you work till midnight. They call any work after 12.5 hours shift ‘overtime’, and pay it less than single rate. The 50 workers hired through contractors are paid 5,400 Rs: for 26 days of 12.5 hours.
Taurus Home Furnishing
(418 Udyog Vihar Phase III)
The helpers are paid 3,000 Rs, the checkers 3,500 Rs and the tailors work on piece-rate. Out of 300 workers only 10 to 15 might get ESI and PF. The drinking water is bad. The toilets are dirty.
Countess Craft Worker
(6 Udyog Vihar Phase I)
The workers employed in the carpet show-room have not been paid February, March and April 2010. The company has not paid into the PF fund the last two years. Since three years the company has not paid the statutory bonus.
Crew Banks Worker
(199 Udyog Vihar Phase I)
Severe wage delays of two month now.
Gaurav International Worker
(198 Udyog Vihar Phase I)
The managers swear a lot at us. The femal thread-cutting workers are paid only 3,000 Rs, the male helpers 3,000 to 3,300 Rs, there is also physical abuse going on.
Comments
Gurgaon is one of the biggest call centre hubs of the globe, having been re-location destination for a lot of US call centre work. Now that the crisis hits the US wage level, calls might be re-routed back up to the global north. A short summary of a recent study and a short workers’ report about house-keeping work in an American Express call centre in Gurgaon.
US matches Indian call centre costs
(Financial Times, 17th of August 2010)
Call centre workers are becoming as cheap to hire in the US as they are in India, according to the head of the country’s largest business process outsourcing company. High unemployment levels have driven down wages for some low-skilled outsourcing services in some parts of the US, particularly among the Hispanic population. At the same time, wages in India’s outsourcing sector have risen by 10 per cent this year and senior outsourcing managers based in the country command salaries above global averages. Pramod Bhasin, the chief executive of Genpact, said his company expected to treble its workforce in the US over the next two years, from about 1,500 employees now. “We need to be very aware [of what's available] as people [in the US] are open to working at home and working at lower salaries than they were used to,” said Mr Bhasin. “We can hire some seasoned executives with experience in the US for less money.” The narrowing of the traditional cost advantage is also spurring other Indian outsourcers to hire more staff outside India. Wipro, the Bangalore-based IT outsourcing company, started to recruit workers in Europe, the Middle East and Africa during the global economic downturn. Suresh Vaswani, joint chief executive of Wipro Technologies, forecasts that half of his company’s overseas workforce will be non-Indians in two years, from the current 39 per cent. India is still expected to retain the overall cost advantage, particularly in more sophisticated software outsourcing. The move to expand operations in the US also comes as protectionist rhetoric against outsourcers rises in Washington. Last week, Charles Schumer, a US senator, described Indian IT outsourcing companies unflatteringly as “chop shops”, a term referring to places where stolen cars are dismantled for their parts.
If you can bare to scroll through various rather tedious semi-racist comments on the article mentioned above, please have a go and click here.
Call Center Worker
(226 Udyog Vihar Phase I)
The call center company is called FIS. About 1,500 to 2,000 workers phone for American Express.In the call center 22 house-keeping workers are emplyed through contractor. In January 2010 we were given 3,600 Rs and the contractor promised to increase the next wage by 300 Rs. In fact he paid 3,300 Rs in February. We work between 40 and 160 hours overtime, each hour overtime is paid 12.5 Rs. Money for ESI and PF is cut from the wages, but we are neither issued an ESI card, nor do we receive PF when we have to leave the job. Instead they cut 1,400 Rs from your last wage. Therefore most people leave after pay-day, which is around the 8th or 9th of the month. You ‘only’ lose 800 Rs outstanding wage this way.
Comments
(E-67, DDA Flats, Saket)
I work in the NGO. There are 30 of us employed here – doctors, drivers, cooks, helpers and office staff. The doctors get over 20,000 Rs per month for 8 hour days, the office staff gets 6,000 to 8,000 Rs. The drivers get 6,500 Rs for 12-hour duties. The cook and the helpers get between 3,000 and 5,500 Rs per month for 14-hours shifts. Non of the workers get ESI or PF. The NGO is engaged in a sterilisation scheme for street dogs – which is part of the street-dog eradication program run by the Delhi government. Although officially the government has assigned the MCD (Municipal Corporation of Delhi) for this task, but actually the big shots have decided to let cheap NGO workers complete the work. The MCD pays 445 Rs for the sterilisation of a dog, and besides provides other favours to the NGO management: the NGO gets water and electricity free. The vans are called ambulance and are in a bad condition – but because of the NGO name the police do intervene. The madam running the NGO swears at the workers and even lifts her sandal to threaten the helpers. The 15 workers who stay in the office take some of the restaurant food that was originally meant for the dogs, some of the donations meant for the dogs get messed with, too. The whole process of catching a dog, sterilising it and letting it free is very painful – several dogs die and are buried in the scrub-lands at night. But they are entered as completed sterilisations in the register. The two doctors have to perform 30 to 40 dog operations per day… a doctor let some younger helpers do the work. This increases pain for the animal and the likelihood of death.
Comments
We document six short reports by garment workers about seemingly spontaneous strikes to enforce higher wages, which took place in April 2010. The strikes have two parallels, one in space, the other in time. The strikes correspond with the more violent and widespread mobilisations of garment workers in Bangladesh and they continue the series of previous strikes during the last official increase of the minimum wage – click Gurgaon Workers News no.9.
The combination of the fact that companies do not passing on the wage hike and the fact of current inflation forces workers to react. One of the limitations of these struggles is the fact that mainly the skilled tailors get involved, while unskilled workers tend to remain outside. The struggles also depend on the enormous ups and downs of work/orders in the international garment industry.
Viva Global Worker / Marks and Spencer Worker
(413 Udyog Vihar Phase III)
The March 2010 wages did not contain the 300 Rs DA statutory since January 2010. The workers did not like that. On 8th of April 2010 600 skilled tailors stopped the machines and struck. On 9th of April the tailors continued the strike and some workers in the finishing and sampling department joint them. On the 10th of April the strike continued… when the management promised that the 300 Rs DA will be paid with the April wages the workers started work at 4 o’clock in the evening. Viva Global manufactures garments, among others, for Marks and Spencer. Non of the 200 workers in the finishing department get ESI or PF. Out of the 600 tailors only 150 get ESI and PF. Workers work 80 to 90 hours overtime per month, but payment is at single rate.
www.marksandspencer.com/
Fortune Garments Worker
(Plot 39, Sector IV, IMT)
The wages are delayed every month. On the 9th of April they told the skilled workers: “We will pay you after the lunch-break, now go back to work.” When wages were not given by 4 pm, the workers stopped the machines and went to the office of the general manager. At 6 pm the place was in chaos, the tables were over-turned, the window-panes broken, the company called the police. The skilled workers were given the March wages on 12th and 15th of April, the other workers were told that money will be given on the 17th of April. Then they said that wages will arrive on the 20th… On the 20th of April, after the meal-break, the workers in the finishing department stopped working, they continued their tool-down on the 21st and were paid a day later on the 22nd of April. The workers doing computer embroidery stopped working at 9 pm on the 24th of April and refused to do overtime on the following Sunday. On Monday the general manager told these workers that they will be paid by 2 pm, that they should go back to work… The workers continued working till 4 pm and then stopped the machines. The computer embroidery department was on strike Monday, Tuesday and Wednesday. On Wednesday they gave 20 workers their wages, but the machines continued to stand still. On Thursday the 29th of April, after all workers in the department had been paid, work was re-started at noon. The workers in the knitting department did not stop working – they were paid an advance of 3,000 Rs, but they haven’t seen their March wages by 1st of May 2010. At the moment there is little work, so there are only 600 workers – after August there will be more than 1,000 workers, but none of them will have PF or ESI. I don’t know whether the middle-management and supervisory staff gets ESI and PF. In the factories minors of 13 to 15 years of age are employed. The thread-cutters get 3,500 Rs for a 30-days month, 8-hours day. The drinking water is bad, the toilets are dirty.
Boutique International Worker
(B-246, Okhla Phase I)
Around 200 skilled tailors struck work on 28th of March 2010 in order to enforce the new minimum wage of 6448 Rs instead of the old wage of 4,370 Rs, which was still paid by the company. After management reassured workers about a wage increase, they started work on 29th of March. After the management did not publish a written notice about the wages work was stopped again on 30th of March, the management put up the notice and work started at 11 am. The workers in the second factory on plot D-80 stopped work on 29th of March, because the management did not pay the February DA. Since then the company started to sack the ‘old tailors’ and to hire fresh ones, paying them 5,850 Rs.
Wearwell Worker
(B-61 and B-134 Okhla Phase I)
Around 850 skilled workers in both factories struck work on 20th of March 2010, from 9 am till 9 pm. The next day work stopped again at 10:30 am. Work resumed only after the management put up a notice saying that the 400 permanent tailors will get 248 Rs for an 8-hours day and the 450 casual workers 225 Rs. Then the company started to kick out casual workers and hired new ones, paying them 203 Rs. Workers in the factory have to work from 9 am till 3 am on regular levels. The company used to provide transport for the female workers, but they have stopped the transport.
R.V. International Worker
(D-153, Okhla Phase I)
On 14th of March 2010 about 100 skilled tailors stopped work and demanded 248 Rs for an 8-hours day. So far they were paid 175 Rs and they were promised 225 Rs. After two hours of strike the management agreed to pay 248 Rs. The company started to lay off people – end of April about 30 tailors were left. The thread-cutting and stitching female workers get 2,400 to 2,500 Rs per month.
Orient Fashion Worker
(F-8, Okhla Phase I)
On 15th of March around 900 skilled workers stopped the sewing machines. After one hour of strike the company put up a notice announcing 248 Rs for 8 hours-day.
Comments
“There aren’t any students here, no teachers to suffer. It’s a school without rules out here”. (From movie-song, ‘Rang de Basanti’)
The relation between students’ and workers’ struggles used to be, if at all, a type of political alliance. Since the 1950s the relation changed, it increasingly became a social, rather than merely a political relation: more and more students were forced to see themselves as workers in the making. Whether a student will see her or himself as a worker while being at university roughly depends on six dimensions:
* young people from what kind of class background are able to enter university?
* how is the process of education in itself organised (division of learning, targets, hierarchies)?
* what is the relation between students and university staff and workers?
* do students have to work or do internship while studying?
* what is the influence of the wider (class) political situation and movement on the campus?
* what is the future prospect after leaving university, in terms of labour market, debts, position of intellectual labour in the social production process?
Like the society to which it has played the faithful servant, the university is bankrupt. This bankruptcy is not only financial. It is the index of a more fundamental insolvency, one both political and economic, which has been a long time in the making. No one knows what the university is for anymore. We feel this intuitively. Gone is the old project of creating a cultured and educated citizenry; gone, too, the special advantage the degree-holder once held on the job market. These are now fantasies, spectral residues that cling to the poorly maintained halls.
(From: “Communique from an Absent Future”, California Universities)
We neither have space nor knowledge to describe how these six dimensions have re-shuffled over time. Therefore just some general remarks. There are about 104 lakhs higher students in India, which is only around 7 per cent of the young population in ‘university age’. During recent years more semi-private colleges came up. Young, often working class youth entered these colleges – rather than the traditional universities and IIT’s – given that they promise a ‘more directly’ marketable degree. The perspective of these students and their families on ‘education’ is mainly one of future investment: debts for paying the fees most correspond to future job and wage perspectives. The pressure on students to pass the exam has aggravated, apart from a question of pride, prestige it became a more existential question of managing the debts. In December 2010, 20 students (in high school and college) committed suicide in Maharashtra; most due to intense fear of poor academic performance. India has the second highest suicide rate in the world and 40 per cent of the cases are in the adolescent age group. In 2006, 5,857 students, this is 16 a day, committed suicide across India – this number has increased drastically since then.
“One day this will all end. We’ll all go our separate ways. Life gets busy. Too many problems. After college we have to dance to fate’s tune. When I’m out on the streets… nameless, faceless, scared. Just walking the streets”.
(From dialogue, ‘Rang de Basanti’)
The process of education is changing. Professors at a meeting about ‘Democracy and University’, held in March 2010 complained about the increasing Taylorism of their work: students are given DVD’s for ‘e-learning’, as part of the planned shift to semester-system at Delhi University professors would have to correct 30 papers for marking a day, the time for revision has been cut down, teachers are now officially called ‘stakeholders’, which creates a kind of ‘client’ relation with the students. Professors and students fear that the planned opening of the education market for ‘foreign universities’ will foster this trend towards ‘universities becoming a market-place’. Another expression of the ‘neo-liberal’ university is the increase in casual work among the university staff. Most of the work like canteen, cleaning, security is now outsourced to contractors. There have been various struggles around this issue – see for example the report by PUDR jnu_workers_report
In addition to recent fee hikes and hikes in hostel rents the state intensifies repression against the more radical part of the student movement – under the pretext of ‘anti-Maoist’ anti-terrorism. There are ongoing protests about this issue, for more information click HERE
While most of the more radical student groups either solely focus on the campus or use the student world as ‘cadre-recruitment-base’ for the party, for example student unions like AISA, some students start to debate the question of the ‘historical material’ changes of the position of students within society and in relation to the working class, for example the group Correspondence – click HERE for their pamphlet.
Students protest fee hike
Greater Noida, August 17, 2010
Protesting against the fee hike, students of IEC College of Engineering & Management today boycotted classes and held demonstration outside the college. “Though the university registrar has informed that the fee approved by the fee fixation committee is applicable to the first year students only, the college is demanding the hiked fee from the second year students as well which is unjustified,” said the agitating students.
“We are also protesting against the fee hike for the first year students. The fee of Rs 75,000 was already high. Now, it has been hiked to about Rs 85,000 for B.Tech., MBA and MCA courses,” the students pointed out. “Since Friday, we have been protesting peacefully and requested the college management to resolve the issue. As it did not pay heed to our pleas, we were forced to demonstrate today. We have come here to study and not involve ourselves in any agitation,” they added.
Protest by teachers against semester system at Delhi University
New Delhi, August 17, 2010
As the Delhi University Teachers Association (DUTA) today held a massive demonstration outside the vice-chancellor’s office over the issue of intrroduction of semester system. DUTA today claimed that the tussle with the administration had strained its relationship with college principals. “Never before in the past have the principals and the DUTA come into conflict in this manner. The vice-chancellor is trying to create a rift between principals and the teachers to impose semester system in science courses. He is issuing them ‘orders’ to implement semester system,” said DUTA president, Aditya Narayan Mishra.
Rohtak University – Faridabad Majdoor Samachar
Maharshi Dayanand University Security Worker
(FMS January 2010)
In 2001 they started to hire guards through contractors. Because the minimum wage was not paid in 2002 the guards, the gardeners and cleaners went to an official who sent them to the labour department. Since then the number of workers hired through contractors has increased relative to the permenent workers and the labour law is violated openly. In 2005 workers started a sit-in protest and hungerstrike in front of the office of the principal. Workers gave a notification to members of parliament and even to the Prime Minister… In order to surpress the resistance they started to sack workers bit by bit. At that time only 18 guards out of 90 were paid the DC rate, the rest was paid 100 Rs for a 12-hours day. They don’t get ESI or PF. The guards come from nearby villages… When there was major construction work done at the university they brought workers from far away to do the job. The female workers carrying bricks, sand, cement they call coolies and they pay them only 82 Rs a day. The male workers are paid 92 Rs. There is a large number of 14 to 15 year old boys working, they are paid 82 Rs.
Comments
Please click here for the report on living and working conditions of construction workers on the Common Wealth Sites in Delhi. Below you can find a short note on a current strike of CWG construction workers. For more information check out following links:
NSI
Radicalnotes
Building workers on dharna
New Delhi, August 12
For the second time in the month, construction workers employed at the Miranda House Commonwealth Games site sat on a dharma outside the college. The workers, students and teachers, under the banner of the Delhi Nirman Mazdoor Sangharsh Samiti, were protesting against the non-payment of wages. The workers were supported by many Delhi University students, members of the Miranda House Staff Association, women’s and youth organizations like Centre for Struggling Women (CSW) and Krantikari Yuva Sangathan (KYS). They were also protesting against several other violations of labour laws. “The workers have not been paid for the entire one month and four days for which they have been working at the college. Furthermore, the rate of payment fixed by the contractor is well below the legal minimum wage rate. Unfortunately, despite the fact that the contractor has defaulted on paying the workers and violated several labour laws, the main employer, i.e. the college principal, Ms Pratibha Jolly has refused to step in and release the workers’ arrears,” said a member of the Mazdoor Sangharsh Samiti. “Since August 4, only a small part of the workers’ dues has been released with no further surety provided by the college administration to look into the other key demands of the workers,” he said.
Comments
The south of Delhi’s industrial belt is connected to the vast village hinterland of Haryana. And there is no calm in the hinterland. We spent some days in Mandkaula visiting friends – you can read the travel diary below. It is followed by news items about recent semi-rural unrest.
Mandkaula, Haryana, India
Mandkaula is a village near Bawal, with about 15,000 inhabitants. It borders poor Muslim dominated Mewat district, situated close to the planned Manesar-Kundli Expressway. Mandkaula is an ‘Ideal Village’ meaning that it is chosen by Haryana government to get several crore Rupees for investments into road works, street lamps and so on. Mandkaula is an ideal Indian village in many senses. It has been in the centre of the Green Revolution, it has ‘benefited’ early on from irrigation and electrification. It is within the catchment area of the industrial labour market of Faridabad. The land-holding is more or less equally distributed between those who have land. Despite, or may be because of, being an ideal village we can see the social death of peasantry. After hundreds of years of ‘agricultural tradition’ the current older generation of peasants in their 60s is probably the last ‘peasant generation’ of this village. Their are few families who might continue farming, but the social domination of field work is gone.
Out of 15,000 inhabitants about 7,000 are landless, mainly ‘castes’ engaged in handicrafts like pottery and weaving, some street cleaners. This is a quite typical ratio for India. Less typical is the quite equal land-distribution amongst the landed peasants, belonging to the Jat caste. About 80 per cent of them have around 5 acres. Out of the 250 potter families around five people still work with the stone-wheel and clay – they have no apprentices for the future. There are only one or two hand-looms left, the nearby industry has undermined the market position for hand-woven goods. There are about 400 acre common land, which basically means land taken-over and used by the state. The government built a stadium and a university department for agriculture studies on the common land.
Mandkaula was in the centre of the Green Revolution. Electricity arrived in 1964, largely replacing hand or bullock-driven wells with electrically operated borewells. Irrigation was improved through a nearby bigger canal. In the mid-1960s the government ordered a structural program to ‘unify’ land-holdings. Individual farmers used to own scattered land, after the reform most of them had a single unified piece of land. Then came the tractors. Nowadays there are more than 300 tractors in the village. Crop pattern changed since the 1950s and 1960s. Where there used to be millet and other rough crops, there is only wheat left. Rice production only started with the development of the canal and the tubewells. A lot of the harvest and wheat thrashing work is done by machines plus wage labourers. A gang of wheat thrashers from Rajasthan travel with their diesel-fuelled thrashing machine. They take about 800 to 900 Rs per acre. They provide the labour force, around ten workers. It usually takes them about one hour for an acre. After the wheat harvest in Haryana they drive on towards the soy bean harvest in Madhya Pradesh. Thanks to mechanisation, the wheat harvest takes about seven days, the rice harvest not longer than 15 days.
The living standard amongst the peasant is decent, much better than the living standards of industrial workers in town. The houses and inner-yards are airy, no feeling of crowdedness. You are more likely to find more televisions, coolers, fridges here, than in workers’ homes. But life is traditional. Women wear their faces covered when around strangers. The houses of the landed are spacially detached from the houses of the potters and the cleaners. ‘Caste’ live amongst ‘caste’. Without land and without jobs the former artisans are much harder hit. They complain that the National Rural Employment Guarantee Scheme (NREGS) is not implemented. There are about 150 people in the village who got a job card. There are 80 NREGS jobs, but they ran out. Instead of creating NREGS jobs, the panchayat engages outside contractors for road works and other infrastructural jobs, because he can cash in commission. Most of the farmers in Mandkaula are in debt, often for non-agricultural expenses like family houses, dowry or education.
The sons born in the 1970s and 1980s were not to become farmers. Most farmers tried to get them into government jobs: the police force, the army, the administration. The family of our comrade is no special case. His father owned 50 cows for diary production. In the early 1970s all his labourers left Mandkaula in order to work in the factories of nearby Faridabad. Contractors of Escort, Goodyear and other companies came to the village offering higher wages and a life in the urban. Our comrade himself left the village and worked in factories for some years. He returned to the village to keep the family farm going, but all his four sons have become office workers. Two of them commute every day between Faridabad and Mandkaula, which is about 40 minutes by train and another 30 minutes by three-wheeler. Living in the village is cheaper and better – but the younger sons want to leave the village soon.
If the Kundli-Manesar Expressway develops according to plan about 27 villages will disappear in the ‘special corridor’. Two kilometres on both sides of the expressway are dedicated for industry and real estate. The state starts to offer money to the land-owners, but people wait and see how prices develop. In that way the farmers always relate to the government: they need the government for jobs for their sons, they need it for the procurement of their harvest, for the subsidies and village development, for the final sale of their land.
————————
The longer lists about ‘village protests’ is random and arbitrary. The village is everything else, but not a ‘proletarian community’. We know to little about the background and class position of the farmers protesting against land acquisition for a nuclear power plant or against lack of electricity. We don’t know who blocked the street and attacked police posts. As we can see from the short report from Mandkaula – the villages are crisis ridden and they are divided. Social tension is increasing, and it finds many different channels, some of them seem to reflect the old inter-village oppression. For recent conflicts between Dalit and Jats in Mirchpur, a Haryana village please read HERE
Protesters halt traffic
Jind, July 28
The district witnessed traffic blockades at three places to highlight their grievances on various issues.
A large number of shopkeepers blocked traffic at Patiala Chowk by sitting on dharna on the main
crossing for an hour to express resentment over the increasing number of thefts in the locality in the past few days. The blockade was lifted after the intervention of the ASP, who assured them of a proper action.
Meanwhile, residents from Pouli village here blocked traffic on National Highway-71 linking Jind with Rohtak in protest against inadequate supply of drinking water in the village. The villagers claimed that there had been no water supply for the past three days. The third such incident was reported from Braha Khurd village located on the Jind-Gohana road. The villagers held protest after an elderly person was run over by a speeding vehicle this morning. Alleging delay and inaction on the part of the police to chase and arrest the accused driver, residents of the village blocked the traffic by laying down wooden logs and parking their vehicles across the road.-
Furious villagers attack police post
Sirsa, August 2
Irked at the merciless thrashing of a vendor by the police, villagers attacked a police post at Kulan village in this district last evening. Such was the fury of the mob that the in charge at the police post had to run for safety. The villagers, including women, later sat on dharna outside the post till senior officers reached there and made the policeman apologise for his act. The police had yesterday raided certain places to check gambling and rounded up five gamblers. Puran Singh, a vendor, out of sheer curiosity, went towards the police post to see what was happening. Prem Kumar, in charge of the police post, beat him up with a stick, dragging him inside the police post situated on the main crossing of Kulan village. The police action incensed the villagers and shopkeepers in the vicinity, who raised slogans and against the police and freed the victim. In the meantime, some women members of the family of the victim reached there with sticks and barged into the post, forcing the cop to flee. Additional police force from Tohana and brought the situationunder sat on dharna outside the police station with the victim and his wailing children. The villagers demanded an apology from Prem Kumar and that the police should bear the expenditure of victim’s medical treatment. They blocked the crossing halting traffic towards Bhuna, Ratia, Tohana and Jakhal.
Power Pangs – Villagers lock up school, anganwari
Sirsa, August 10
After the alleged beating up of a power nigam SDO by some villagers and subsequent arrest of an accused, residents of three villages today adopted a tough posture and decided to withdraw their children from schools and anganwaris. Villagers from Dhigtania, Chouburja and Rangrikhera today blocked traffic and locked the village school and the anganwari in protest against the erratic supply of power to their villages.
In Jind village, substation closed
Jind, August 10
Residents of at least three villages in the district locked a power substation and blocked traffic at two separate places here today to highlight their grievances over short supply of power in rural areas. The protests were lifted after intervention of the officials concerned. The villagers locked the 33 kV substation at Singhana village following an altercation with the staff posted there.
Irate villagers damage buses
Karnal, August 11
Incensed over the alleged failure of the authorities concerned to regulate power supply, residents of Tahkhana village blocked the National Highway No. 1 near Tarawari, 15 km from here, for about two hours today. The protesters, comprising mainly children and women, pulled down hoardings and went on the rampage, damaging three Haryana Roadways buses of the Panchkula, Ambala and Chandigarh depots. Hundreds of vehicles and commuters remained stranded on the road and foreigners, who were on their way to Chandigarh, got scared of the protest. The protesters alleged that power supply was erratic for the past over five months, but nothing had been done in this regard.
Gorakhpur farmers oppose acquisition
Fatehabad, August 17
Farmers from Gorakhpur village in this district, where the Nuclear Power Corporation of India Limited (NIPCL) is to set up a power plant soon, are up in arms against the government move to acquire their land. Hundreds of farmers met District Revenue Officer Om Prakash Verma today and submitted a memorandum asking the authorities to acquire alternative land for the plant. The villagers, whose land has come under this notification, have started filing individual objections with the authorities. They held a meeting in the village chaupal yesterday and decided to oppose the government move, threatening suicide if the government did not budge. The state government had recently issued a notification under Section 4 of the Land Acquisition Act-1894 for acquisition of 1,313 acres of the village for the plant. “We are not going to part with our agriculture land at any cost,” declared Dana Ram, a farmer, whose 52 acres fall under the land selected for acquisition. On 25th of August the media reported: The farmers’ agitation against the acquisition of their agriculture land for the proposed nuclear power plant at Gorakhpur has picked up momentum with villagers from 14 neighbouring villages coming out in their support.
For more: http://www.wsws.org/articles/2010/aug2010/indi-a26.shtml
Power-less, villagers clash with cops damage substation; police fires into air; sarpanch among 300 booked
Jind, August 19
Sans power for the past three days, hundreds of irate residents of Nagura village in the district resorted to violence, which lead to a clash between them and the police last night. The police fired several rounds into the air, besides resorting to a lathi charge, to disperse the mob. The violence resulted in heavy damage to the 132 kV substation and disruption of power supply to several villages in the region. Several persons, including some policemen, were injured when protesters resorted to throwing stones. A large number of policemen have been deputed at the substation and in the village. The police has booked about 300 persons, including the sarpanch of the village, Rajesh Kumar, in this connection. According to reports, hundreds of villagers assembled on the Jind-Assandh road last night in connection with the power supply problem. The police then opened fire into the air and resorted to a lathi charge to disperse the violent mob. At least six policemen, including Krishan Kumar, SHO of the Alewa police station, were injured in the violence. Property and machinery worth about Rs 8 lakh was damaged at the substation, said an official.
Villagers make team beat a hasty retreat
Fatehabad, August 22
A team of officials of the Food and Supplies Department from Fatehabad had to beat a hasty retreat when they went to Nadel village near Jakhal for “door-to-door checking” of some records of foodgrains supplied through the public distribution system (PDS). Villagers, who suspected that the officials had come to the village to tamper with the records, snatched ration cards from them when they were allegedly making some entries in the cards of the villagers. The Tribune had published a report, “Rotten wheat finds way through PDS”, in these columns yesterday and highlighted the fact as to how fungus-infested wheat was sold to poor families in the village. Gurjeet Singh, a former member of the village panchayat, entries in whose ration card was allegedly tampered with by the officials, called villagers, who asked the team to leave their village.
3 killed as farmers go on rampage near Aligarh
August 16, 2010
Three persons, including a PAC jawan, were killed and nine injured in a village near Aligarh when farmers, demanding higher compensation for land acquired for a township, fought pitched battles with police who opened fire to restore calm. The violence broke out last night in Jikarpur village when the farmers went on a rampage vandalising a police post, indulging in heavy brickbatting and setting afire a bus and another vehicle. The trouble erupted after rumours flew thick and fast that a farmer leader had been arrested near the village which lies close to Uttar Pradesh-Haryana border. Over 2,000 farmers on Sunday staged a sit-in at Jikarpur, the epicentre of yesterday’s violence. The protesters also tried to block traffic at several places on Aligarh-Tappal road. Vijay Prakash said the farmers this morning destroyed machinery for construction of the Expressway. The farmers are on the warpath demanding higher compensation for land acquired for a township project along the Delhi-Agra Taj Expressway.
Comments
Gurgaon is still an Eldorado for the international real estate business. In August 2010 the Hooda Haryana government was put into a no less dubious public spot-light for getting engaged in shady land-deals in Gurgaon. Farm land was turned into cheap property to build an amusement park. We summarised some news items on the matter.
Govt under fire over Gurgaon land deals
Tribune News Service
Gurgaon, August 10
The Haryana government has come under sharp criticism for the recent move of leasing out big chunks of prime public land in Gurgaon to a private party at rates much lower than the prevailing market price. The plots, located in Sector 29 and Sector 52 of Gurgaon, have been leased out for the development of amusement parks.While the local HUDA officials and other authorities concerned are tightlipped over the issue, all-out efforts are being made to hand over the said chunks of prime public land to the private player. So much so that a road passing through one such chunk of land is being covered with loose earth to facilitate the beneficiary. The front leaders of the Federation of Residents Welfare Associations (FORWA) and Gurgaon Citizens Council (GCC) maintained that the 25-acre plot in Sector 29 had been given on a 33-year lease at a nominal price of Rs 56.25 crore, as against the prevailing market price of Rs 2,016.67 crore for the purpose. “Similarly, the 17-acre plot in Sector 52, which could have been leased out for 33 years at Rs 548.53 crore as per the prevailing market price, has been given away for a meagre Rs 38.25 crore,” they asserted.”So many controversial land deals coming to light clearly vindicate our stance that the Hooda government is a regime of property dealers,” said an opposition party leader, adding that even the Punjab and Haryana High Court had also pointed out at the nexus between the state leadership and builders. Talking to The Tribune today, a front leader alleged that the Hooda regime eyed prime property in the National Capital Region (NCR), especially Gurgaon, and its single-point agenda was to grab farmers’ land in collusion with unscrupulous builders and colonisers.
Comments
This is an attempt to introduce a regular update on general tendencies of crisis development in India – motivated by Greek shock-waves, naked shorts and potential spillovers. Apart from short glimpses on the macro-level of things we focus on general trends in agriculture and automobile sector: the current demise of the past and the toxicity of the future.
The Crisis in July and August 2010 – A Summary
Tension between short-term influx and growing internal debts
The months of July and August 2010 confirmed the picture of the economy in India being in a waiting-loop of crisis. The government is able to announce that GDP growth is still on 8 percent-growth-path and that, after the massive outflow of 20 billion USD of short-term invested capital after the ‘Greek-Shockwaves’ in May 2010, money is flowing in again since June – mainly as short-term portfolio investment. These ‘good news’ are in contrast with the probably more substantial worries expressed during the last two months:
- the association of industrialists Assocham expects inflation to increase to 15 per cent in the coming months; the general inflation, which is in double digits for the fifth consecutive month, stood at 10.55 percent June – July 2010;
- the current trade deficit, which is a measure of higher imports of goods and services over exports, has already risen 50 per cent to 21.7 billion USD during April-May 2010 from around 14.4 billion USD a year ago; the trade deficit of the January – March quarter was the biggest since 1981;
- bank credit is growing at an annual pace of around 22 per cent while deposits grow at a 15 percent; the credit-deposit ratio has widened to 73.44 percent in July 2010 from around 70 percent at the start of this year, climbing above the monthly average of the past five years of 69 percent;
- 50 per cent of the 2009-10 foreign currency reserves growth is due to appreciation of the Rs in relation to the US-Dollar; the Rupee has proven to be a rather volatile currency, meaning that there is a big scope for depletion of the reserves in case the Rupee plunges
- according to a Reserve Bank of India report from August 2010, `total factor productivity’ has dropped from 2.6 per cent in ’92-97 to 1.7 per cent in ’97-2005; while productivity in agriculture has slipped from 3 per cent to -0 .2 per cent, that in industry has dropped from 3.1 per cent to 1.4 per cent
Total GDP 2009: 1,367 Billion USD
Total Export 2009: 165 Billion USD
Trade Deficit 2010-11: 120 Billion USD
Total FDI 2009: 39 Billion USD
External Debts 2009: around 200 Billion USD
Public debts of GDP 2009: 60 per cent
Fiscal Deficit: 5 per cent
Share in global merchandise trade in 2008: 1.5 per cent
Tension over Inflation between Finance and Fiscal Managers
The major concern, the high inflation, causes increasing tensions between the ‘political class’ and their financial managers, e.g. in the form of the Reserve Bank of India. While the government still claims that the general inflation is mainly due to high food prices and that ‘a good monsoon’ will sort things out, the Reserve Bank of India (RBI) announced in July that two-thirds of May inflation was contributed by non-food items. The RBI gives credits to the banking sector, the interest rates of these credits have been hiked four times since March 2010 in small steps of 25 basis points. Each of these interest hikes were accompanied by major public controversy whether the danger of inflation or the danger of ‘smothering the boom’ is more pronounced. “We will tell them [the government] that if inflation expectations solidify, it will push up government bond yields, loan rates will go up, and there will be a spiralling impact economy wide,” an RBI source said in August 2010. The interest hikes of the RBI have been passed on to consumers via the State Bank of India in August 2010. The SBI is the country’s largest lender. In August the SBI raised benchmark lending rate by 50 basis points to 12.25 per cent, making home, vehicle and other corporate loans linked with the rate costlier to middle-class consumers – and will very likely reverberate within the micro-finance sector of rural poverty, see below.
Tension between Central and State Government
The government’s take on the inflation problem is highly contradictive. After the central government has fuelled inflation by its reform to free-float petrol prices – causing considerable price hikes in June 2010 – Finance Minister Pranab Mukherjee now asks the state governments to cut taxes on petroleum products, “a move that would help tame the current double-digit inflation”. According to Rupe Report from August 2010 on subsidies – click HERE [http://www.rupe-india.org/49/subsidies.html] – state taxes on petrol in India are significantly higher than average: “While India’s petrol and diesel retail prices are lower than those in many developed countries, they are higher than US prices as of May 2010, solely on account of taxes. The ex-tax prices of petrol and diesel were, respectively, 7 cents and 11 cents lower in India than in the US; yet the retail prices of petrol and diesel in India (i.e., including tax) were, respectively, 36 cents and 6 cents higher than in the US.” So basically the ‘state subsidies’ for the petrol or fertilizer sector are actually a ‘ slight lowering of taxation from a very high basis’. A similar point of tension between central and state governments is the implementation of the new goods and services tax (GST) across the country next year. State governments fear that the new tax will shift taxation power further towards the centre – increasing the problems of the debt-ridden state budgets. Terming the new tax as “anti-democratic, anti-poor and anti-farmer,” Madhya Pradesh finance minister Raghavji said in August that the new tax regime is aimed at divesting the states of their financial freedom. The proposed new indirect tax, which will subsume all the major levies like excise, sales tax, VAT and other local levies like octroi, is anti-democratic as the proposed GST Council will not be accountable to Parliament as well as to the state assemblies and through it the power of the states to levy tax on sale and purchase will be taken away. After the implementation of the GST regime, Madhya Pradesh will lose revenue to the tune of 2,200-2,500 crore RS per year. The Finance Minister’s answer does not require any further comments: “The gain from GST will propel the country from one-trillion dollar economy to two trillion-dollar economy in a short span of time,” he said while addressing a meeting of the industry chamber Ficci.
Tension over International Markets
Apart from re-shifting debt burdens the state in India is up for selling more assets. This time we don’t talk about mobile-phone licenses, but about the real stuff: coal, oil. In August 2010 the central government announced plans to list its state-owned coal mining company Coal India by October 2010 and to sell an additional stake in its national oil company. The Indian government gave the mandate for the offering for Coal India shares to Deutsche Bank, Enam Securities, Morgan Stanley, Citigroup, Bank of America Merrill Lynch and Kotak Mahindra Capital. Coal India claims to be the largest coal producer in the world, accounting for 85 per cent of Indian output. Question remains if this partial opening will ease the general tension concerning foreign investment in the Indian market, particularly the retail, defence and agricultural sector. In August 2010 US Trade Representatives engaged in a diplomatic clash when announcing that they will be “exploring all options, including legal tools, to force India to open up its agriculture market”. “We are exceptionally frustrated. I will tell you it’s generally not our practice to comment publicly as to whether we are going to take legal action, but I would tell you we are exploring every alternative and every enforcement tool available to us to get India to open up their markets on a number of agriculture issues, the dairy sector in particular,” the US Trade Representative, Ron Kirk, told the US lawmakers in early August. During his visit to India in late July 2010 David Cameron aimed at a similar direction: Business Secretary Vince Cable has announced the government will allow the export of British civil nuclear technology to India for the first time. In return Mr Cameron is expected to call on India to reduce trade barriers in banking, insurance, defence manufacturing and legal services. A £500 million deal for BAE systems, Britain’s biggest defence contractor, to supply Hawk jet trainers to India is expected to be among “a string of high-profile contracts” to be signed during Prime Minister David Cameron’s visit. During the same visit immigration minister Damian Green made clear that in future only ‘high-class’-migration to the UK is wanted: “I’m convinced that we can achieve our objective of reducing migration to the UK, whilst driving forward our commitment to trade and inward investment. We can do both. We want to encourage to come the UK the brightest and most talented workers, entrepreneurs and investors”. He said Britain is now working more closely with Indian police and educational bodies to clamp down on unscrupulous agents who use fake qualifications to get student visas for customers and those behind bogus colleges.
Tension in some of the multi-national industrial core sectors
Obviously there are dozens of union mobilisations each day – click HERE for daily up-dates on LabourStart. At this point we only want to mention certain apparent parallels between mobilisations at multi-nationals in China and India. While the Honda strike in China was paralleled by a dispute at Hyundai in India in spring 2010, now Foxconn workers in India entered the sad stage of victimisation after their Chinese brothers and sisters. The strike at Hyundai was followed by a similar ‘open’ dispute at Volvo, while unions at Apollo tyre maker agreed to employment of temp-workers and workload increase after two months of lock-out.
- 500 Foxconn workers stage protest
July 2010
Workers who came under exposure of mysterious gas leak at Foxconn factory in Sriperumbudur were admitted to Hospital with complaints of giddiness, nausea and breathlessness. About 500 workers from the factory with the support of unions in neighbouring industrial units went on a sit-in protest in front of the Foxconn factory. However, the protest was called off later on as authorities and management promised action. Meanwhile, there was no operation in the company, which assembles handsets for Nokia.
- Employees at Indian Volvo bus plant strike over pay
August 2010
The two week long strike at Volvo Bus factory in Hoskote near Bangalore has ended with both the management and workers union coming to a mutual agreement on wage revision. Management has agreed to revise salaries of workers with retrospective effect from April 1 last for three years. Management, however, declined to reveal the exact rise in compensation for the workers. This was the first ever strike at Volvo’s bus plant in India. The strike lasted for two weeks, but a labour conflict which has slowed down production has been going on for about three months, he added. Four of the plant’s employees were suspended following a dispute at the plant in April, during which they allegedly physically assaulted a manager. During the three month labour conflict some employees have worked less or not at all in protest. The conflict has set the plant’s production pace back 60 buses, Johansson said. The factory rolled out 535 buses last year.
- Lockout at Apollo Tyre plant ends
End of August 2010
The two-month lockout at Apollo Tyres Ltd.’s Perambra, India, plant has ended as the company and two unions have come to a resolution. The parties have agreed to raise the plant’s daily capacity from 308 tons to 340 tons. Meanwhile, Apollo will hire an additional 200 people, and unions have conceded that the company can use “secondary manpower” at certain times. “The increase in capacity, manpower and the use of secondary labor are all progressive steps,” says Satish Sharma, chief of Apollo’s India operations. The Perambra factory produces light truck, medium truck, bus and agricultural tires.
The Rural Crisis
The news items we collected for July and August relate about growing farmers’ debts in Maharashtra and Punjab and the announcement of the state to claim land from bankrupt farmers, if necessary with the help of force. The rulers and their social managers also presented solutions to crisis-ridden farmers: the bad fix of micro-credits, micro-electronics, and, if necessary, re-location to African bloody soils of civil war. In the long-term the rural crisis might be fought out in the cities: “On a conservative estimate, 45 per cent of Indians would be living in towns and cities by 2050. This means that 379 million people may be added to the urban space over the next 40 years,” the National Council of Applied Economic Research (NCAER) said in its report ‘How India Earns Spends and Saves’ in August 2010. Urbanisation is a process of concentration: While nearly 25 per cent of urban population in India lived in cities with a population of one lakh in 1901, the number increased to 45 per cent in 1951 and 69 per cent in 2001.
To cater to this growth, India needs to invest $1.2 trillion in capital expenditure, mainly infrastructure, over that period, an eight-fold increase of current spending levels, MGI said. India now spends 17 USD per capita on urban infrastructure, compared to rival China’s 116 USD. What ‘state-management’ of urbanisation also means was revealed in mid-August in Bangalore: concentration-camps. From a BBC report: “Officials in the Indian city of Bangalore are investigating a spate of deaths at a camp for beggars. At least 100 inmates have died in the government-run camp on the outskirts of the southern city this year, 27 of them in the past week. Activists accuse the state government of negligence and say conditions in the camp are appalling. More than 2,500 inmates live in squalor at the camp and diseases there are rife, correspondents say. There are just two toilets for every 500 inmates.”
Foreclosures in Maharashtra
Scores of farmers mired in debt in the arid cotton belt of Vidarbha in Maharashtra are close to losing their property rights, as the state-controlled Land Development Bank has kick-started the process to recover dues from them. A top revenue ministry official said the process to recover loans by selling off land belonging to those farmers who have defaulted is “definitely on” and could start as early as July 23. It is now a well-accepted fact that mega loan amnesty schemes, such as the ` 71,000-crore waiver announced by the central government and the state’s ` 6,240-crore loan waiver, excluded many farmers in the state. The waiver was applicable only for loans contracted from a government-backed institution. But in the hinterland, most farmers borrow from money-lenders. Many of them could not avail of the amnesty schemes, as the eligibility was restricted to those having two hectares or below. More-than-half of Vidarbha’s 35-lakh farmers own more than two hectares and, therefore, according to the government scheme, can only obtain a loan waiver of 25 per cent of their outstanding loan instead of a total write-off. Now, the state government wants to recover the remaining 75% of the loans that have not been paid back until now. “According to rules, the Land Development Bank needs to recover loans within five years from disbursement. More delay than the stipulated time makes it mandatory for the bank to recover its dues by selling the immovable assets, in this case, the land,” an official associated with the exercise told ET. He said necessary orders to take over the properties of farmers have been issued and the powers to take possession of defaulters’ land have been vested with the respective district deputy registrars. “These officials have demanded police protection. This is being extended to complete the process,” a Nagpur-based government official said.
Debts in Punjab
Central Punjab has been the food basket of the state and the country since the 70s when the Green Revolution brought bumper wheat and paddy crops in its wake. A quarter century later, farmers of the area continue with the same foodgrain rotation but at a heavy price. A steep fall in water table is forcing farmers to dig deeper in search of water fanning the start of an agrarian crisis. Farmers of these districts are not only digging deeper borewells for water every few passing years but also digging themselves into debt from which they have a little hope of climbing out. Amar Singh from Khairpur Jattan village in the Ghanaur block of Patiala says 95 per cent of its residents are under debt. Amar Singh, who owns 16 acres of land and has two grown up sons and their extended families to feed, says 10 years ago, the family irrigated their land with 60-ft deep borewells. He says he dug his first deep borewell in 2002. At present, he is replacing an older borewell, which had become defunct with 375-ft deep borewell. Ironically, he has not struck sweet water even now. The story of Harmesh Singh of is similar. Harmesh’s march towards debt stated five years ago when he installed a 225-ft borewell. He took a loan of Rs 1.85 lakh from a bank to do so. He also purchased a tractor shortly afterwards so as to reap the rewards of mechanised farming. However, whatever he earned was offset by continuous expenditure on his borewell. The farmer started off with a 5-brake horsepower (bhp) motor, upgraded to 7.5 bhp and finally installed a 15 bhp motor over a year ago. With a debt of Rs 4 lakh now and minus the tractor that he has sold off, Harmesh is now indifferent towards life. When asked about his loan repayment schedule, he says, “Sometimes I give it (instalment), sometimes I don’t.”
Bad Fix One: Microcredits
Microcredits became big business in India. The sudden credit crunch after October 2008 global banking crisis has shown how close the remote Indian villages are to Bombay financial district or the Wall Street – in financial terms. According to their own sources the microfinance sector growth 80 to 100 per cent a year. Around 70 to 80 million small farmers depend on micro-credits. There are reports that small ‘self-aid groups, e.g. women who buy a hand-loom together, turn against their members once they are unable to pay back their share of instalment. The microfinance sector has to grow quickly in order to dish out credits, in order to grow. So far the microfinance companies had to take loans from normal banks, paying about 12.5 per cent interest. They passed the interest on to the small farmers, who have to pay around 25 per cent interest. These farmers cannot obtain credit from ‘normal banks’, because they cannot show the required securities. Microfinance is placed between the official financial sector and the money-lenders. While before the crash US banks used to grant people mortgages 120 per cent above what they were able to show as security, the microfinance institutes in India still lend credits around 150 per cent above the value of the small farmers’ property. In order to attract more capital from global streams they have to show growth rates of the mentioned 80 per cent – the sector is overheating. International Groups like the German Allianz or real estate developer Larsen and Toubro entered the market. Using the argument that the sector has to get financial sources independent from the official banks – in order to lower the interest rates for the farmers – microfinance companies started to issue shares on the stock-market. SKS Microfinance is one of these companies. Within three years this company increased the number of ‘clients’ 20-times – now around 5.3 million people depend on loans from SKS. In June 2010 188 million shares of SKS were sold on the market. A boom similar to the IT bubble, but the crash will have much more severe social consequences.
Bad Fix Two: Microelectronics
In the 1870s the colonial state promised that the telegraph system will prevent further famines in India, given that the information about the lack of foodgrain can be circulated quicker. The famines in the 1890s were even worse – partly because of the telegraph-system resulting in even quicker speculation. History does not repeat itself, it move in a social-technological spiral. A study about ‘agricultural productivity increase through mobile-phone services’ concludes in August 2010: “Among the states studied, small farmers from Maharashtra (income between Rs 12-17,000/month) reported the highest use of their phones to access information, leading to diverse benefits. These included yield improvements, price realisation and better adjustment of supply to market demand. Ideally, market price information is valuable in deciding where and when to sell, but also in deciding the cropping pattern. On the ground, there was some marginal evidence that the bargaining power with traders (who used mobile services widely) improved when farmes were armed with market price information”.
Bad Fix Three: Relocation
African nations offering land for free to Indian farmers
11 Aug 2010, 1551 hrs IST,PTI
Some African countries are offering land on lease for 99 years for free to overseas farmers and India should grab the opportunity, industry body Assocham said today. The countries that were in the forefront trying to attract agriculturists were Sudan and Ethopia, he said. Several Chinese farmers have already accepted the offer and begun cultivation of land, said Tyagi.
Bad Fix Four: Pre-emptive Counterinsurgency
Currently the state in India is undertaking a major operation to enforce identity cards, which means photographing, fingerprinting, and iris-scanning every resident of India, plus issuing of digital files, the so-called UID System. Combined with the ID-card is a supposed reform of the ‘Below-Poverty-Line’-food program. The idea is to not ‘guarantee’ minimum prices for the ‘officially poor’ anymore, but to issue food coupons. The definition of who is poor and changes in the households composition or income is supposed to be combined with the ID-drive. From an official document: “Since the Unique Identification will not, in itself, have information on people’s poverty status, these kinds of tailoring of information will need to be added to the UID System. Further, since households do move in and out of BPL status there has to be provision for updating of information.” This again is added to the ‘job-card-regime’ of the National Rural Employment Guarantee Scheme (NREGS), which only grants paid employment to locally registered people, often requiring a bank account. The state is blatant about the ‘counterinsurgency’-character of NREGS:
“India battles Maoist influence with jobs scheme – BBC July 2010
Also called the Mahatma Gandhi National Rural Employment Guarantee Act, it is being used to kick-start much needed development work in the area. Kaushik Lohar is a fortuitous beneficiary of a sudden rush of development work to keep the rebels away from his village. “If the Maoists were not at our door, all this wouldn’t have happened,” said Mr Lohar. “We have been waiting for development for decades.” He said he earns up to 3,000 rupees a month working on the dam, much more than what he used to earn as a daily wage worker.”
The “3,000 rupees a month” is the utter exemption. Not even 1 per cent households in Bengal got the promised 100 days’ work under the National Rural Employment Guarantee Act (NREGA) in 2009, the latest report of the rural development ministry has revealed in August 2010. Out of the total 31,15,422 households, only 19,163 got 100 days’ employment. Households on an average got 32 days of work. Seventy-two per cent of eligible households got merely 15 days of employment, the report said. The figure for most other states hovers around 5-6 per cent. Not only do people get less than 100 days, they also tend to get much less than the minimum wage. Reported in August 2010: “For 11 days, 99 people toiled to dig a check-dam under the Mahatma Gandhi National Rural Employment Guarantee Scheme (MGNREGS) in Tonk district of Rajasthan. But when it came to wages, they were paid only Rs 11 – Rs 1 for each day of labour. The Rs 11-payment was decided by a Junior Engineer who inspected the work site. Gudaliya residents protested, calling it a cruel joke, and appealed to the district administration. To no avail. For Gudaliya residents, this is not a lone case. For four jobs between April and June, they have reportedly been paid Re 1, Rs 7, Rs 12 and Rs 25. These wages have only increased their ire against the government. Incidentally, details of the payments are available on the MGNREGS website but have failed to move the authorities.”
Obviously, NREGS plays a role for poor people’s income, particularly for women – around 40 per cent of NREGS workers are women. A recent study – click HERE [upload pdf]- on NREGS impact on women says that although NREGS wages in the studied areas formed only 15 per cent of the total households income, it formed a significant income for the female members.
The state can not rely on the violence of structure and control alone, please read the fact-finding team’s press release about the killing of comrades Azad and Pandey from the 22nd of August 2010.
The Automobile Crisis
We have little to say about the automobile crisis this month, just three news article snippets about Maruti: More Sales, Less Profits, More Debts!
- “The country’s largest car maker, Maruti Suzuki India, reported 29.18 per cent jump in sales for July 2010 at 1,00,857 units.”
- “Maruti Suzuki’s July Profit Unexpectedly Falls 20 per cent as Raw Material Costs Swell”
- “Maruti Suzuki is among carmakers to have introduced waiting lists in India as a lack of parts including tires, bumpers and batteries damps vehicle production. Local components makers have struggled to expand because of debt levels that are twice as high as Asian suppliers. India’s 133 listed makers of components and tires have an average debt-to-equity ratio of 138 percent, according to data compiled by Bloomberg. The average for the 73 companies in the Bloomberg Asia Pacific Auto Parts & Equipment Index is 58 percent
Comments
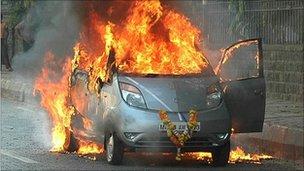
English Language edition of the class struggle newspaper produced in Gurgaon, in Haryana, India. The paper contains workers' enquiry and testimonials, collective action reports, theory and analysis.
Gurgaon in Haryana is presented as the shining India, a symbol of capitalist success promising a better life for everyone behind the gateway of development.
At a first glance the office towers and shopping malls reflect this chimera and even the facades of the garment factories look like three star hotels. Behind the facade, behind the factory walls and in the side streets of the industrial areas thousands of workers keep the rat-race going, producing cars and scooters for the middle-classes which end up in the traffic jam on the new highway between Delhi and Gurgaon. Thousands of young proletarianised middle class people lose time, energy and academic aspirations on night-shifts in call centres, selling loan schemes to working-class people in the US or pre-paid electricity schemes to the poor in the UK. Next door, thousands of rural-migrant workers up-rooted by the rural crisis stitch and sew for export, competing with their angry brothers and sisters in Bangladesh or Vietnam. And the rat-race will not stop; on the outskirts of Gurgaon, new industrial zones turn soil into over-capacities. The following newsletter documents some of the developments in and around this miserable boom region.
If you want to know more about working and struggling in Gurgaon, if you want more info about or even contribute to this project, please do so via:
www.gurgaonworkersnews.wordpress.com
gurgaon_workers_news[at]yahoo.co.uk
Comments
The Indian car industry is in a ‘sales boom’: all time record figures during the last months. But does the ‘sales growth’ translate into a ‘profit growth’?! The supplying industry complains about ‘squeezed margins’: the pressure on prices is so high that it hardly allows sufficient upgrading of capacities and future productive investments. They have difficulty to keep up with the demand in productive output. With dwindling profits per car the central assembly plants suck the supply chain dry: just-in-time, low inventory, low prices, full quality.
The 1st and 2nd tier suppliers are squeezed from two sides of capitalist contradiction, from both sides of the supply chain: from the down-stream side of capital-intensive manufacturing and from the up-stream side of workshop and slum production. The low wage regime of workshop and slum production hardly makes it profitable to invest in machinery. The workshop and slum production itself is part of a ‘human supply chain’ of cheap labour, reaching into the rural parts of society. The current conflicts about minimum wages for rural employment schemes will re-shape this supply – see ‘the Social Tsunami Impact’ in this newsletter.
Below we document some glimpses at different sections of the supply-chain: an article on ‘electronic flow-management’ at Suzuki Maruti in Gurgaon; articles on the situation of 1st tier suppliers and a worker’s report about conditions at ‘Wing Automobile’; and finally reports from workers employed in the workshop and slum production of the automobile industry in Faridabad.
The Electronic Flow
The ‘electronic flow’-management in central assembly plant symbolises the attempt of capital to get to grips with the flow of value. Their obsessive hope is that the ‘information’ passed on between assembly department and the scattered landscape of supplying industry can become the container of ‘value’ – ‘information’ being similarly immaterial and evasive. The ‘information-flow regime’ is their hope that a perfectly synchronized supply-chain will reconcile ‘technical productivity’ and ‘profitability’, by tuning the rhythms of welding-robots to those of the dexterous hands of child / slum labour.
“At Maruti Suzuki, electronic flow is a religion”
(Economic Times, 19th of November 2010)
At India’s largest carmaker, E. Nagare or ‘electronic flow’ is a religion. Simply put, this electronic flow is actually the sequence of production plans from the vendor [supplier] to Maruti’s shopfloor, which now sits at a two hour cycle from 30 days in the past. As S Maitra, Managing Executive Officer (Supply Chain) of Maruti Suzuki indicates, “E . Nagare has completely transformed the supply chain at Maruti over the last four years.” Across Maruti’s twin sprawling plants in Gurgaon and Manesar, multi-coloured bumpers arrive in mobile trolleys and components line up outside factory sheds directly feeding the ever-hungry , multitasked assembly lines. For the company’s 250-odd Tier I vendors and 20 global suppliers, supply is now a seamless activity. Maruti receives multiple supplies in a day within a slot of two hours based on the information given out to its vendors the previous night. That’s a far cry from the initial 30-day or subsequent 15-day cycles Maruti drove in years ago. And that’s what it takes to crank out 4,600 cars a day.
Along with processes like E. Nagare, new technologies and materials such as plastic instead of a metal fuel tank or light tinting of glass to keep the car cool, are now in the offing. Increased competition in the late 90s gave rise to global suppliers coming to India, like Delphi of GM. “Delphi came with a range of technologies, like wiring harnesses, chassis and powertrain components and AC components and they became our suppliers as well,” says Maitra. At that time, it was the ‘Materials’ division of Maruti that dealt with the supply side. Instead of price increase, which was the order of the day, Maruti called on its existing vendors to focus on cost reduction. Initially, the company could bring down the cost of production by 2-3 per cent and in 2006-07 , it even lowered that by 5%. “We had to induct many global suppliers in our vendor network, like Faurecia for seat mechanism, Bosch and some Japanese suppliers like Dentsu, Sumitomo Metals and Continental, all with a global footprint ,” elaborates Maitra.
The 1st tier squeeze
The profit squeeze of the wider industry appears as ‘unfair price policy’ to the supplying companies.
“Sales of passenger vehicles have set a scorching pace-25-27 per cent in the first half of the financial year-and auto component makers are struggling hard to catch up. Over the next few years, the vendors are expected to pump in at least Rs 2,000 crore to meet the demand. One factor that has enabled companies to make such high investments is the willingness on the part of original equipment manufacturers (OEMs) to re-negotiate contract prices. In the past ten months, the average contract prices have gone up by 5-10 per cent. As Ramesh Suri, chairman of the country’s largest car air-conditioning company Subros, which supplies air-conditioners to Maruti Suzuki, Tata Motors and Hyundai Motor, says, “We are going to invest up to Rs 200 crore for capacity enhancement,” adding that the only option left for his company is to constantly ramp up production to meet demand. Suri explains that while passenger vehicle makers constantly put pressure on component makers to cut costs, there is a limit to how much they can manage. He says while the company’s topline has been growing steadily, there is constant pressure on the bottomlines. “The average net profit per sale has certainly declined,” he claims, adding, “Auto firms have realised that they can’t continue to do business till the time they increase contract prices.”Managing director of Gurgaon-based auto component maker Omax Autos Jatender Mehta adds that his contracts with leading carmakers have increased 5 per cent in the past one year. “If we have to invest in our facilities, we cannot do it till we get more for our components,” he says. Mehta explains that high volatility in prices of key components like steel, copper, zinc and aluminum, which have increased 10-12 per cent since last year, has burnt a big hole in the budgets.”
The 1st tier workers’ anger
Wings Automobile Worker
(I-35, DLF Industrial Area Phase 1)
There are 25 permanent workers and 325 workers hired through contractor. They produce ignition coils for two-wheelers of Hero Honda, Bajaj, Yamaha, Honda, Hero Puch and Kinetic. They also produce parts for Maruti Suzuki. Officially workers are employed 8.5 hours per day, but actually they work 200 hours overtime per month, paid at single rate. If workers are made to work 20 hours non-stop, they get 20 Rs extra for food. There is a constant danger of cutting your hands – the production targets at the 12 power presses and the 10 moulding machines is too high. Even when the machines are faulty you have to run them. If one of your pieces is rejected (due to flaws) they cut one hour of your wages, they swear at you, they also push-beat you. Fingers are cut on a regular level. They don’t fill in the accident report. After an accident you are sent for private treatment and then you are dismissed. In an auxiliary of the company (Eden) 5 permanents and 70 workers hired through contractors produce horns for two-wheelers, cars and tractors. Recently, a newly hired worker was made working 26 hours non-stop on a power press, he had an accident and lost two fingers. The toilets are very dirty. There is no drinking water. Wages are paid delayed.
http://www.wingsauto.com/
(from: Faridabad Mazdoor Samachar no. 267)
The Automobile Slum-Production Workers
In the ‘industrial villages’ and slums of Faridabad more than 100,000 workers are employed in small workshops, which produce for the bigger industry on contract bases. Nearly all of them are ‘invisible’, they don’t show on any official documents. The workshop economy is an outcome of the 1980s restructuring process – see ‘Workers History’ on the GurgaonWorkersNews site. The 1980s and 1990s witnessed mass lay-offs of permanent workers. Some of them remained in touch with their former department managers and turned into their suppliers: they opened a workshop. The machinery of the workshop stems from a similar cycle of re-structuring: lathes, power presses and other machines replaced by micro-electronic revolution, often imported from Germany and Japan. New workers stream in from the countryside and find a job in the slum economy – in many cases they come from the workshop-owner’s villages. Below some voices from the low-wage labour-intensive regime.
Boxer India Worker
The workshop is situated near Industrial Area, 17 workers are employed. They work on six power presses, three lathes, one grinder and one reamer. They manufacture cycle clamps and other parts for JCB, Maruti Suzuki and RK Industries. The helpers are paid 2,500 to 3,000 Rs and the operators get 4,000 to 4500 Rs per month. The shift-times are from 8:30 am till 8 pm, but people are made to stay till midnight, too. Overtime is paid at single rate. Due to working too long hours, due to lack of maintenance and due to the fact that helpers are made to work on power-presses there are a lot of accidents: fingers get cut. Injured people are supposed to organise bandages through private channels. After being given 100 or 150 Rs by the boss they have to hear: if it does not get better through the bandages, why don’t you urinate on the wound. Even if you are still injured and bandaged you have to come to the workshop and do whatever work.
Aman Enterprises Worker
The workshop is in Saray Mohalla in Mujesar. There are two surface grinders, cylindrical grinders, internal grinders, a lathe machine, MNCR, a tool grinder, a drill, two generators – four workers, the workshop owner and his nephew use them in order to make dies for factories. The wages are between 2,500 Rs and 5,000 Rs. There is no toilet. Due to the surface grinder and the generators there is a lot of dust and exhaust in the air.
Lakshman Singh Mittal Industries Worker
The workshop is in Dabua, near the Sarvoday School. In the workshop 25 workers work on 12 power presses, on a surface grinder and a big drill, manufacturing parts for Whirlpool. Official shift times are from 8:30 am till 9 pm. The workshop owner knows all tasks, he does the setting – his son supervises the outsourced work. He is a senior die fitter, he does not work himself, he gets more than 5,000 Rs. The helpers and operators get 3,000 Rs to 3,500 Rs.
BS Enterprises Worker
The workshop is in Saray Mohalla in Mujesar. Three workers use a lathe, a surface grinder, a drill and a generator in order to do job work for bigger factories. Wages are about 3,500 Rs.
(from: Faridabad Mazdoor Samachar no. 267)
Comments
Really extraordinary interesting stuffs are provided here to know actual work of all workers associated with each and every automobiles industry and importance of electronic flow management which have been helping to growth rapidly.used truck parts
Short article on a rather dubious ‘technological fix’ for the Gurgaon call centre industry and an angry worker’s report from Sparsh BPO about working conditions, a strike and mass lay offs.
The Technological Fix
Finally an end to expensive office blocks and mingling of sexes: modern technology is supposed to enable ‘housewives’ to do the call centre job from their domestic sphere. “With just one laptop or desktop computer with internet and a phone connections, people could operate from their rooms, attend to inbound calls that otherwise land at the call centre. With this, housewives, who would never otherwise dream of joining a BPO, would be able to take jobs and do it from their homes,” said Mike Manson, director of the ‘innovative company’. “Virtualisation of voice technology would help setting up of one-seater or 3-5 seater micro BPOs in tier 3 and 4 cities from where the BPO companies are drawing talent pool,” said Sriram Srinivas, vice-president. “This would not only benefit the employee to save on overheads such as rentals and high cost of living in metros like Gurgaon but also helps the company reduce cost on things such as employee transportation expenses.” Experiences in the US and Western Europe taught us that even in call centres capitalist production is still mainly a ‘socially enforced’ type of productivity: despite rent costs the mass office is still more productive due to mass cooperation, flow of creativity, discipline and surveillance.
The Angry Worker
Sparsh BPO Service Worker
(409 Udyog Vihar Phase 3)
“We currently operate through 20 state-of-the art facilities across nine locations in India. Our dedicated workforce of over 16,000 motivated professionals provide qualitative solutions in the areas of transaction processing and call centre services, aiming to achieve excellence in every transaction.”
(from company web-site: http://www.sparshindia.com/)
The call centre is in a 12-floor building, several thousand workers are on the phone 24 hours on three shifts, phoning for BSNL, Airtel, Airsale, Reliance Com, Orient Bank of Commerce. For 26 working days per month they get 4,800 Rs. After 8-hours shift they are often made to stay two hours longer, which is not paid. The company does not pay for transport and those workers who use the ‘employee cabs’ have 1,000 Rs per month deducted from their wages. In addition 210 Rs is cut for PF and 80 Rs for ESI – but no ESI card is given. The food break is only 15 minutes – there are two 5 minutes breaks for tea. There is never enough time, but no matter what, you are supposed to work. You cannot make the customer wait, that’s what they say. Against this the workers stopped work at the end of March 2009, they stopped work for three days. They went inside the office, but they did not log in. The management reacted by smashing 4-5 computers and trying to blame the workers for it, saying that they will file a police case and send them to jail. Bit by bit they started to kick people out – in the end it must have been about 2,000 workers. Actually a lot of workers handed in their notice, but the company refused to take it – instead they said that the workers just left the job. After having worked there for more than two years I went to the office in order to make them sign my PF form. They just threw it away and said that I left the job without giving notice and that I won’t get the PF. The company keeps 200 workers for housekeeping. They work 12-hours shifts, 30 days per month and get only 4,887 Rs – no ESI and no PF. The company has another office at 195 Udyog Vihar Phase 1. There workers phone for Vodaphone, Shub Yatra, Bhartiy Jivan Bima Nigam and others.
(from: Faridabad Mazdoor Samachar no. 267)
Comments
GLOBAL CAPITALISM, WORKERS’ SPACES AND PROCESSES OF SELECTIVE INCLUSION/EXCLUSION
Findings from a Newly Industrialising Area in India
Anita Trivedi
August 2007
[We document an excerpt dealing with the living arrangements of migrant workers in NOIDA, a neighbouring industrial area to Gurgaon and Faridabad]
Material differences at the workplace and variation in work practices and responses were reflected in the living spaces of workers. Key findings reinforced the theme of variation observed in labour management practices and the responses of workers at the workplace. At the same time, while the strategy of control of workers and undermining the commonalities through differential employment contracts and remunerations was reflected in the hierarchy of the living spaces, it was also crosscut by a sense of unity among workers arising out of shared spaces, experiences and a sense of unfairness. The living spaces formed a significant dimension of social relations of production.
In the five residential areas a form of hierarchy originating from and akin to the one at the workplace could be observed, with the government-planned (Industrial Authority) sectors/colonies at the top and unauthorised slums at the bottom as shown in Table 2. In between, in descending order were the company colonies, unauthorised colonies, ‘urban’ villages and authorised slums. The areas towards the upper end of the hierarchy had access to better services and to the decision-making levels of the state; such access progressively declined as one moved down the ladder.
Type of residential area
Name & Location
Features
Planned colony
Gamma, Greater Noida
High level of public infrastructure, services and law and order
Authorised company colony
Y Nagar, Noida;
A Colony, Greater Noida
Slightly reduced scale and reach of public infrastructure and services
Unauthorised regularised colony
Harola, Noida
Come up through unauthorised sale or grab of land but regularised by government by providing some services
Authorised urban villages
Surajpur, Greater Noida
Villages surrounded by industrial and municipal urban settlements
Unauthorised slums
Khoda, Noida
Very little infrastructure / services
The processes of selective inclusion and exclusion extended here too. The ‘included’ permanent workers in the MNCs largely resided in well-developed and serviced areas; others ‘partly incorporated’, e.g. skilled migrant workers, apprentices, lived in company colonies, peri-urban areas and villages; and a majority of temporary and migrant workers, adversely incorporated or excluded, dwelt in the slums. Such scaling of the spaces resulted in further divisions among workers.
I admit we are better than others, especially the unauthorised ones, but not very good either. The light (electricity) doesn’t always come. The colonies of the Authority are much better. Why the difference?
(Union Functionary, J3, resident of a company colony)
Workplace injustices were overshadowed by demands for services and other issues in some areas. This continued the process of fragmenting the workers evident at the workplace and of weakening the formation of a collectivity.
However, on closer examination certain variations in the above scheme of things were observable. Not all ‘included’ workers resided in areas where they were expected to, i.e. well-developed and well-serviced residential areas. Some locals, who owned land and were economically and politically powerful continued to reside in or maintained strong links with villages, ‘urban’ villages and sometimes slums. This provided them with an opportunity to continue with an additional source of income (usually from agriculture or related activities); and allowed them to retain their dominant status (of class and/or caste) with its resultant social networks and benefits.
The ‘most included’ permanent workers, both in terms of employment status and also of the quality of the areas of residence and access to services, had the greatest fear of being ‘excluded’ from both. They suffered from a sense of insecurity similar to workers in other categories. At the other end, the ‘most excluded’ migrants who resided in slums exhibited no such fear and were resigned to workplace inequality and apathetic towards living conditions:
What is the point (of services)? We only come here to sleep. I am here to earn…and they will never give us a permanent job.
(Focus group of migrant workers, I1 and I2)
In between, there were many variations based on levels of inclusion and exclusion both at the workplace and in living areas. Many who were ‘more included’ at the workplace felt ‘excluded’ in the living spaces and vice versa. The skilled migrant workers (e.g. J2) who lived in the ‘urban villages’ experienced a greater sense of inclusion with respect to work but exclusion when it came to access to people of influence/ decision-making processes because they did not ‘know anyone’.
Yes, we live together but half of them are locals and they go home. The people (locals) understand our problems but they live here during the week and go to their villages over the weekend. They are different. We are different. We have skills and we held good jobs. They work at the firm only for the name. Pay and conditions don’t matter to them.
What can we do? Nobody listens to us…we are from different places. We don’t know anyone here and even if we ask for help, no one will stand by us, we are from outside.
(Focus group of migrant skilled apprentices, J2)
The reverse was true for many unskilled local workers (e.g. K1, J2) who lived in the surrounding villages and continued with the original agrarian pursuit (often as a fallback option during periods of unemployment). They drew confidence from local networks of community, village, and region and were vocal in their criticism of workplace practices and migrant workers for ‘putting up with them’:
I tell the security men who misbehave (manhandle, shout) with me…I will see you at the gate…
Others (migrant workers) who put up with it are not men.
(Local temporary worker, K1)
Many of the relatively prosperous and influential locals, who were excluded or partly included-excluded in the workplace as temporary workers in its various categories, often indulged in land grab in the slums and extended accommodation at high rents to migrant workers. The economic strength and political clout required for this originated from their insertion into channels of influence (access to officials and politicians through links of family, caste, village etc that are often drawn upon in times of crisis or during elections). They were most vocal in their demands for services and more hopeful of their fulfilment because of their social support systems.
I tell you it is a matter of time…we will get the recognition (thereby services in the unauthorised colony). They [the government] will have to do it. We are a solid vote bank for them.
(Local temporary worker, J1, Head of the residential committee)
In a way, their exclusion at the workplace was sought to be remedied by seeking greater inclusion in their other spaces. Despite the very evident divisions, the unintended outcomes of such structuring and reconfigurations were the coexistence of the workers in the living spaces, the urban-rural continuum and the overlap of spaces and issues in the physical and mental landscapes of workers. Shared spaces encouraged sharing of the experiences and injustices of the workplace. The empathy and the sympathy from the shared plight, or the fear of it, often overcame the divisions and hierarchy of both the workplace and living spaces.
The situation in those areas [Khoda and Harola] is bad. The workers there are mostly in export units and it is well known the kind of exploitation that goes on in such units. The government supports the owners of such units but ignores the terrible conditions that the workers live in… where else can they live on the pittance that they receive? As for us (in the MNCs), it is a different kind of exploitation. [Nods of approval by all]
(Union President, J1 during a mixed focus group)
A fragmented workforce from fragmented work organisation lived in hierarchical living spaces. Given their degree of fragmentation, sense of insecurity and spatial segmentation, one would expect to find a much weakened workforce with reduced avenues of organisation and representation. Yet, the politics of the workers displayed complexities that arose from their varied exclusion/inclusion at the workplace and in living spaces and the varied nature of interest articulation. The emphasis on the interests articulated differed on the basis of the place of residence (more service-oriented in the slums and completely work-related in the residential areas of the MNCs), or origin of workers (migrant or local), or skills of workers.
Variation of interests could be observed between the slums, where demands centred on better living conditions and services, and the well-serviced residential sector developed by the government, Gamma, where the permanent MNC workers were concentrated, where workplace and work related issues completely dominated. Again, service-related demands in slums were vocalized by influential local residents of the area and not the migrant workers. The urban village of Surajpur and the company colonies showed a mix of demands: the demands for services were not as strong as in the slums and were mixed with criticisms of work culture and practices.
While migrants and temporary workers in the slums displayed apathy towards their living conditions and towards the idea of political solutions to the same, and felt completely disempowered politically and economically, those in other areas, e.g. the migrant skilled workers working in the MNCs and residing in the ‘urban villages’, were more engaged. This stemmed from their sense of greater inclusion (however selective) at the workplace. However, it is significant that the engagement was not with the local politics but with the new economic policies of the state to attract MNCs and its impact on them, i.e. at the global-national level (the case of apprentices of J2 who spoke of workplace issues but disregarded the local ones).
Migrants, whether in temporary low paid employment or skilled, felt weaker on account of ‘not knowing anyone’ compared to the local workers who felt stronger because of their social support systems despite their insecure jobs. The presence of many well-placed permanent workers and entrepreneurs, mostly local, in the unauthorised slum of Khoda indicated both the operation of an ‘informal’ economy and the use of informal channels and mechanisms by the workers to gain economic strength and social status, and thereby access to the decision-making processes and institutions.
If they are going to take our land away, why wouldn’t we grab this land? We have to live and this is our place, our roots. [AT - But land grab is not good, surely?] No, it isn’t. But a man has to go up in life. Money talks, power matters.
None of the locals wanted to move and all felt that the migrants were unfortunate, thus manifesting the relationship between spatial mobility and social power.
Nobody wants to be rootless; I can’t imagine going somewhere else to live… it is sad to be a migrant.
This fractured politics with conflicting interests in the slums and the ‘urban villages’ reflected the inclusion-exclusion experienced by workers at the workplace. The local residents were ‘more included’ in the social processes of decision-making and power because of their origin (as compared to the migrants) but ‘more excluded’ than the permanent workers in the MNCs (who had access to better services). The latter, for their part, were not as concerned with the conditions of the slums (when asked about it) as with their own largely work related issues. The greater inclusion of the migrant skilled workers and exclusion of the local unskilled workers at the workplace reinforces Massey’s (1996) emphasis that space implies a co-existence of differences and multiple trajectories. Also, the preoccupation with service provisions in the slums was counterpoised by very powerful workplace and work-practices related responses in the company colonies and the residential sectors of the workers.
At the same time, the workers in the MNCs were as likely to exhibit a place-based politics in their villages.
I still have my land in the village…have bought some more too. This area is only going to grow more, not less. At the end of the day, it is family [extended family], community that matters…in times of need, marriage, troubles, and illnesses. Without your roots and links (in the village), a man is anchorless.
(Permanent worker, MNC)
Another example was found in interviews conducted with a local, permanent worker and a focus group of a mix of workers from the same organisation in one of the villages. When the interview was completed, I requested for all categories of temporary workers to be assembled. None of the temporary workers sat down and no response was forthcoming on any of the issues raised except from the permanent worker, who belonged to the dominant caste, was one of the rich men of the village, and was also instrumental in getting others employment. On being prompted, the permanent worker said ‘I am telling you, why do you need to ask them’ and the temporary workers said ‘we agree with what he says’.
Despite attempts by capital to undermine their commonalities, the possibility of a common consciousness emerging among workers, identified at the workplace, was also identifiable in the living spaces of workers. There was a keen awareness of trends and practices in other workplaces. Also, all along there was an emphasis on injustice and unfairness and a feeling of ‘us’ and ‘them’ among workers. Despite the divisions and conflicting interests there was a continued sense of awareness that such differences were largely work-mediated. This came through in almost all interviews and focus groups when workers, after initial scapegoating of other groups of workers, would end by attributing all their problems to the ‘MNCs, employers, state, new policies and changes’. Use of local networks were accepted by all and resented by some but always attributed as a counter to the prevalent ‘unfairness’.
It appeared that processes of exclusion-inclusion were multiple and interrelated and operated in all domains of workers. Although at some level the exclusions at workplace and living space were mutually reinforcing, in other respects and for some groups they were mutually compensating – e.g. exclusion at work can be offset by living space inclusion, and vice versa. The locational sources of power, i.e. those rooted in a place, local support structures and networks of influence that followed from it played a role. Also, though the fragmentation of both living space and workspace was a source of division, there were countervailing sources of solidarity deriving from a shared plight (or fear of it). Workers attempted to counter work-generated and spatial inequalities by demands for services, through recourse to formal as well as informal channels of influence and institutions of the state. What emerged was a lack of concordance between power location within the village or other living space, and power location in the company. Old social structures rooted in agrarian systems persist alongside new power relations in industrialised workplace settings.
Comments
Part of the international student protests? On 5th of October, students enrolled in Adarsh College of Education held a militant protest outside the college. They were protesting against the college authorities for forcing students to pay 40,600 Rs for the course offered. Read article by KYS (Revolutionary Youth Organisation).
KRANTIKARI YUVA SANGATHAN (KYS)
Haryana State Unit of All India Revolutionary Youth Organisation (AIRYO)
Munshi Premchand Library, Dharodi, District-Jind, Haryana
Email: kys.haryana@rediffmail.com, Ph. : 7876103701
On October 5, students enrolled in Adarsh College of Education, Shadipur (Julana), held a militant protest outside the college along with their parents and youth activists of Krantikari Yuva Sangathan (KYS). They were protesting against the college authorities for forcing students to pay Rs. 40,600 for the B.Ed course offered. This amount exceeded what the college had earlier advertised as the fee for the B.Ed course. The youth were also protesting the manhandling of students who tried to meet the college administration earlier and get an appraisal on the situation. The protest successfully drew working class youth from different districts in Haryana.
The protesters argued that as an ‘educational’ institute, it was expected that the college run on the basis of no-profit-no loss/minimal profit. They emphasised that even if the concerned college was a private institution it could not ignore the fact that education is a sector which is based on the notion of service to the society. When mobilising the affected students for the protest, KYS highlighted the fact that the declared fee for the course was already a very large amount and so the extra fees charged was completely unjustified. The fee structure was especially unwarranted considering the fact that most students enrolled were children of agrarian labourers and small peasants.
Indeed, this is no isolated incident, but one which is symptomatic of rampant privatisation of education in Haryana. It is a fact that the government has not been spending adequately on education and health. It is not, for example, creating more of its own institutes for B.Ed/JBT education. Rather than increasing the number of its own educational institutions the government has increasingly allowed private capital to enter the education field. It has been consistently doing this by giving recognition to private institutions that actually refuse to perceive education as a social service. Such private education institutes are well known for their profit-hungry mentality. In the interest of cutting costs to the minimum, these private institutes have no qualms functioning from small, cramped buildings, and in providing minimum teaching facilities. They are simply interested in manufacturing degrees, and are hence, characterised by the lack of teachers, regular lectures and classrooms/other infrastructure.
It is a shocking fact that in Haryana out of the total 459 B.Ed institutes only 19 are institutes funded and run by the Haryana government. Similarly, out of the 20,117 JBT institutes in Haryana only 2620 are government run institutes. Expectedly, in such a situation where government run educational institutions are scarce, the competition is very high and only those with good public schooling make it to the government colleges. On the other hand, students who have studied in badly run government schools due to their working class background are unable to make it to the few government run colleges. As a result, they are forced to enroll in expensive private colleges to pursue higher education. Clearly then, the nexus between the interests of private capital (in the education sector) and the government is a cause of much suffering to lakhs of students and their families.
Unfortunately, while the students were holding their peaceful protest outside the private B.Ed institute, the hired goons of the institution attacked the protest. Some of the protesters were struck by bricks and lathis. Many were bruised in the assault and four were seriously injured. Angered by the administration’s bullying tactics, the protesters decided to approach the District Commissioner. After being apprised of the situation and given a copy of the memorandum, the District Commissioner assured the youth of a positive intervention on his behalf.
Considering how the rampant privatisation of education in Haryana, KYS has decided to intensify its struggle on the issue and mobilise working class youth against the Haryana government’s measures to privatise education. It has been decided to launch a state-wide struggle so as to block the government’s openly capitalist education policy. Indeed, despite the fact that some of the protesting students were returned their money by the college principal on October 9, there remains a strong desire in them to take on the government on the issue of privatisation and commercialisation of education. This is best reflected in the fact that many of the affected youth refused to toe the line of the local panchayat (dominated by wealthy landed elements) which was suggesting a more amicable settlement of the issue. It is also reflected in their decision to march to Kurukshetra University (to which many of these private institutes are affiliated) so as to expose the nexus between the University and the education mafia.
Comments
In September 2008 an industrial dispute at Graziano car parts manufacturer in NOIDA ended in a manager’s death and subsequent victimisation of workers. Two years later, a different location in the wider Delhi industrial belt, a different automobile parts manufacturer, the same victimisation of workers after a violent dispute. Again the media worries about the ‘investment climate’. See link below for report by Bigul.
A report on the Sahibabad Allied Nippon incident
By Bigul Mazdoor Dasta
November 16, 2010
Sahibabad is amongst those industrial areas where there has been a glorious history of labour struggles. The martyrdom of Safdar Hashmi of Jan Natya Manch at this place is also a testimony of the labour struggle here. But, at a time when there has been an ever increasing onslaught on the rights of the workers in the era of liberalisation and privatisation and when the administration and industrialists are taking resort to authoritarian means to prevent the workers from getting organized, it is but natural that the workers’ anger would be vented at some or the other place. It is to be recalled that it was not without reason that the ex-president of India K.R.Narayanan had stated, “The patience of those who are suffering for long has got exhausted which can lead to an explosive situation”. If we look back, the reports of the simmering anger of the workers amidst the exploitation, repression, oppression and suffocation have been surfacing in the last decade (The recent labour struggles in Gurgaon, Ludhiana, Gorakhpur and Graziano are testimony to this fact). But this time the anger was released in Sahibabad Site-4.
On 13th November a bloody struggle took place between the management and the workers on the lawful demands of the workers of the Indo-Japanese Combo Allied Nippon Company situated in Sahibabad Site-4 in which the manager of the company Yogendra Chaudhary lost his life. Immediately after this episode the administration and the institutions of the industrialists were alerted to teach a lesson to the workers. The entire media with its clamouring tone is hell bent on terming the workers as murderers. Let us first learn the history of the conditions and struggles of the workers of the Allied Nippon Company before reaching to any conclusion.
What transpired on 13th November? - The Union had earlier declared a strike and the company management wanted to halt it. On the ill fated day at 2 o’clock in the afternoon the HR Head of the company Mahendra Chaudhary went to the two wheeler clutch wiring department along with Yogendra Chaudhary. Some altercation ensued with the workers there. After that Yogendra Chaudhary opened fire and in 4-5 rounds of fire a bullet hit a worker named Brijesh. Subsequently the angry workers valiantly fought with the officials and in an act of defence by the workers, the manager lost his life. Many people were injured from both the sides.
The real cause of the incident – There was a tension between the management and the union from last three months on the issues of contract, bonus and salary hike. Besides the demands of the permanent workers, there was a demand to make those workers as permanent on the priority basis who were working for last 6-8 years. The company had also kept 7 casual workers out of work and there were demands from the management regarding this and a concerned case was pending with the DLC. On the other hand the owner-management did not want to accept these demands. About six month ago the owner had secretly given lakhs of rupees to the so called management (in reality the white collared goons) – Yogendra Chaudhary and his colleagues Rajkumar, Omvir,Mahendra Singh Chaudhary and Narendra Dabas for breaking the union. Since then this so called management was arbitrarily running the factory. It was quite common for them to roam inside the factory openly carrying the guns in order to terrorise the workers. There was a surge in the incidents of threatening and intimidation to the workers, beating them and expelling them on the frivolous grounds so that the owner does not have to regularize any worker and a ground is prepared for not honouring the contract. Whoever was showing any sign of protest was shown the door at some pretext. All this caused enormous indignation among the workers. The workers were living in a condition of fear. If anyone dared to complain he was sure to lose his job. A worker was always living in a dilemma of his economic needs and fear. He was always fearful that if he would protest he would have to lose his job and face economic hassles. On the other hand he was also thinking of salvaging his dignity and self-esteem. This condition was gradually taking a dangerous turn and on 13th November it took an explosive form.
The reality of the so called management – After talking to the workers of the neighbouring locality we came to know that Yogendra Chaudhary used to utilize his influence and contacts to break the union and for intimidation. The workers told that he had earlier done this act of breaking the unions at Rama Steel, TCL and at other places. Yogendra’s wife Sheela Chaudhary is posted at Ghaziabad police department as sub-inspector and he had links with top shots in police, bureaucracy and politics owing to which he used to succeed in breaking the unions. He was running this kind of enterprise at other places as well. In the management of this company as well he had continued to recruit and retrench the people arbitrarily so that his purpose is served soon. But 4 years ago after the formation of the union, the owner had agreed to accept the demands of the workers. But there was a tussle between the management and the workers on the issue of implementation. There was a plan to organize a three day long strike from 16-17-18 November. But on 12th November the DLC ordered a stay on the strike by imposing rule-4 of the Industrial Dispute Act. The union got this information in the evening itself and gave its response on 13th.
Strength of the workers - There are around 300 permanent workers in the Allied Nippon Company and the same would be the approximate strength of the casual workers. Further around the same number of workers work on contract. The workers formed their union in 2006 against the increasing exploitation of the company.
The empire of the company – The workers tell that owner of the company has 4-5 other factories in Gurgaon and other places. There is a big show room in Delhi. The owner’s son’s name is Rohan Talwar.
The authoritarian behavior of the administration with the workers – Yogendra’s relative and the security officer of the company Omvir Singh has lodged an F.I.R. in the Link Road police station against 377 people and by naming 27 workers this case. Police has arrested 8 persons in this connection. Right from the day of the incident, the SSP Raghuvir Lal has been saying that the clash was initiated from the workers’ side. On the other hand the labour department has already stayed the strike by the union by taking refuge to Industrial Dispute Act. The stand of the administration is very clear. The entire site-4 has been converted into a police cantonment and the police teams are conducting raids at different places in the workers bastis. On the other hand the leadership of CITU which claims to represent the interests of workers is maintaining a conspicuous silence over this issue.
Some questions which remain unanswered by the administration - Clearly the death of the manager cannot be justified but the question arises if the pistol is the way how the management wanted to hold a dialogue with the workers? If a case can be filed against 377 workers then why not against the management which carried out a fatal attack on the workers. Secondly if the management at the time of the formation of the union had promised to implement the demands of the workers and now when they have betrayed the promise and arbitrarily retrenching the workers, the union did not have any other means than to go on strike which is a constitutional right of every citizen.
377 workers guilty of murdering one manager – The incident of the site-4 Allied Nippon Company reminds one of the similar incident at Greater Noida’s Graziano in which 136 workers were sent to jail for the death of the CEO of the company and a case was filed under the National Security Act against 6 workers. The incident at the site-4 has once again shown that in the struggle between the owners of capital and the workers the capitalists and government, police, administration,courts, broker trade unions all are united against the workers. Nobody is punished for the death of the industrial accidents in India which are indirectly an outcome of the actions of the management. The murderers of the workers of Bhipal tragedy, Metro Rail Jamroodpur site or Korba episode are not punished till date. The blatant class prejudice of the so called independent and impartial judiciary is seen in this incident as well. When a person belonging to the propertied class is arrested in connection with a crime such as murder he gets bail immediately. On the other hand a case is filed against the workers without any proof of murder.
Comments
If we believe the wider media-coverage than the current boom sectors in Gurgaon are ‘indoor-golf’-facilities and eye-surgery or stem-cell treatment for US patients – at least most of the announcements of new investments concern decadent entertainment or medical tourism.
In November 2010 Harley Davidson announced to open an assembly plant in Gurgaon area, in order to avoid import duties. All parts will be manufactured in the US. Given the sales figures of 250 to 300 sold bikes in India per year, the factory is rather an extra-gimmick for the ‘indoor-golf’-palace anyway. A rather more serious investment: Panasonic announced to invest 2.5 billion Yen in a new washing machine factory in Gurgaon. Production is supposed to start in 2012 – annual manufacturing target 500,000 washing machines.
The power base of Haryana’s political class is the combination of big industry and local landowning class. Real estate rent and industrial profits transform into tax money – of which the local peasantry receives their share in form of compensation payment. In November 2010 the Haryana government announced to a Revised Land Acquisition Policy 2010, which basically means an increase in the state-fixed minimum land prices. For land situated within the notified limits of Gurgaon Municipal Corporation, the new MFR has been fixed at Rs 72 lakh per acre, including Rs 8 lakh as no litigation incentive. Earlier, the highest official acquisition rate in the state was Rs 22 lakh per acre. Hooda said the annuity for acquisition of land for private companies / initiatives would be Rs 42,000 per acre per annum with an annual increase at Rs 1500. The additional amount paid as annuity over 33 years worked out to Rs 21,78,000 per acre. Explaining the provision regarding giving jobs in government, the Chief Minister said that in cases where more than 75 per cent of land, subject to a minimum of two acres or above, was acquired for a public purpose other than that for HUDA/ HSIIDC/ HSAMB, one dependent from the land-owning family would be provided a job in the state government.
Comments
Debating the dimension of the micro-credit crisis in India we have to go beyond the old formula of ‘parasitic moneylenders in new disguise’. The growth of micro-credits is essentially part of the wider global development: credit money has to fill the gap between global over-capacities and subsequent under-consumption.
In this sense the growth of micro-credits can not be explained by general ‘greed of loan sharks’, but by, on one hand the global ‘hot money’ leaving the low interest regimes of the ‘over-accumulated’ developed states in order to invest in the interest-yielding industrial periphery, e.g. in growing sectors like micro-credits (2009 growth rate in India: 58 per cent); this ‘hot money’ then meets the ‘credit needs’ and ‘reproduction crisis’ of a large segment of semi-proletarianised population, which cannot survive as farmers, nor as small entrepreneurs, nor as fully proletarianised wage workers. Micro-credits are rarely ‘invested’ productively, they mainly serve as household income.
The current conflict about whether the wages for the rural employment scheme NREGS should be tied to the general minimum wage level, is part of the picture. Currently in most states the wages for NREGS are below the minimum wage. The central state fears that the fiscal deficit would expand even more once NREGS would be linked to minimum wage levels. It would be easy to counteract this argument by pointing at the planned four-year budget of 45 – 50 billion USD for acquisition of military hardware, but this would ignore the necessities of a ‘capitalist state’.
Fact is that despite the ‘hot money inflow’ the state deficit is increasing, that the current boom does not generate enough ‘employment’ and that the wage level of most of the new jobs can hardly be called a ‘family living wage’. The changes in the international migration regime will change the flow of remittance – last year India was the record receiver of remittance amounting to 55 billion USD – and will aggravate the social crisis in ‘emigrant-states’ like Punjab, already ridden by mass debts. The ‘micro-credit’ – as much as ‘subsidies’ or ‘farmers’ debt waivers’ – has therefore to be seen as the ‘grease’ in a troubled process of proletarianisation The Nobel Prize idyll of ‘small entrepreneur’-ship has capsized in the rough sea of global crisis.
In the following we summarise in a rather random fashion some general news relating to the development of social crisis.
a) inflation continues to stifle ‘industrial growth’
b) central state has subsequently increased its expenses beyond plan
c) nregs wages are supposed to remain below minimum wage levels
d) micro credit system threatens to default
e) tighter control of rural poor through electronic ID system
f) remittance on record high but threatened by changes in global migration regime
g) expansion of defence budget and US reiteration that China uses Pakistan to stifle India
h) increased investment of ‘Indian’ companies in Africa
i) towards a global class: recent workers’ strikes at Foxconn, BYD and General Motors India
a) inflation continues to stifle ‘industrial growth’
Garment industry suffers from Rupee appreciation. From April to August, exports were down 6.4 percent from a year earlier in the $10 billion Indian clothing industry. Although it represents only about 1 percent of the nation’s economy, the garment industry is India’s largest employer after agriculture. “Soaring inflation, rising input cost and slow growth in capacity addition are some of the reasons that are inhibiting growth in specific sectors,” Food inflation in mid-October stood at 13.75 per cent. Industrial output growth in August slowed to a 15-month low of 5.6 per cent from 15.2 per cent in July. While flows into the stock market have more than doubled, foreign direct investment into India fell more than 24 percent in the first seven months of the year, to $12.5 billion, compared with the comparable period a year earlier.
(1st of November 2010)
b) central state has subsequently increased its expenses beyond plan
The government is looking for approval to spend about $9.8 billion more than what was passed in its February budget, towards interest and subsidy payments.
(26th of November 2010)
c) nregs wages are supposed to remain below minimum wage levels
Fiscal experts are worried the government could be staring at a financial black hole if it agrees to the demands to provide minimum wages under the employment guarantee law. The spending on scheme is already one of the biggest item of expenditure for the government, budgeted at Rs 40,100 crore for the current fiscal. [But] “As per the latest figures, only about Rs. 17,000 crores has been spent – roughly 42% of the allocated budget. Immediately notifying the prevailing state minimum wage will have no impact on the Center’s fiscal budget,” said Roy, one of the founders of Mazdoor Kisan Shakti Sangathan.
(24th of November 2010)
d) micro credit system threatens to default
India’s rapidly growing private microcredit industry faces imminent collapse as almost all borrowers in one of India’s largest states have stopped repaying their loans. Sector’s leading company SKS Microfinance shares have lost 41 percent since Oct. 15. Lenders say that less than 10 percent of borrowers have made payments in the past couple of weeks. Indian banks, which put up about 80 percent of the money that the companies lent to poor consumers, are increasingly worried that after surviving the global financial crisis mostly unscathed, they could now face serious losses. Indian banks have about $4 billion tied up in the industry, banking officials say. Now some Indian officials fear that microfinance could become India’s version of the United States’ subprime mortgage debacle. Micro-finance company association demands a 200 million USD ‘state rescue package’ in case the crisis aggravates.
e) tighter control of rural poor through electronic ID system
The purpose of this exercise [current census] is to build the National Population Register (NPR). In due course, your UID (Unique Identity Number, or “Aadhaar”) will be added to it. This will make it possible to link the NPR with other Aadhaar-enabled databases, from tax returns to bank records and SIM (subscriber identity module) registers. Benefits and services that are linked to the UID will ensure demand for the number.” That UID is, in effect, going to be compulsory is clear from many other documents. For instance, the Planning Commission’s proposal for the National Food Security Act argues for “mandatory use of UID numbers which are expected to become operational by the end of 2010″ (note the optimistic time-frame). No UID, no food. Similarly, UIDAI’s concept note on the National Rural Employment Guarantee Act (NREGA) assumes that “each citizen needs to provide his UID before claiming employment.” [...] Take for instance Captain Raghu Raman (of the Mahindra Special Services Group), who is quietly building NATGRID on behalf of the Home Ministry. His columns in the business media make for chilling reading. Captain Raman believes that growing inequality is a “powder keg waiting for a spark,” and advocates corporate takeover of internal security (including a “private territorial army”), to enable the “commercial czars” to “protect their empires.”
(24th of November 2010)
f) remittance on record high but threatened by changes in global migration regime
Indian expatriates are expected to remit about $55 billion into the country this year as the number of emigrants from the nation is likely to clock 11.4 million, a new World Bank report said.
(24th of November 2010)
Offshore IT staff face new pay thresholds
UK migration officials said that non-EU entrants using intra-company transfers would need to earn at least £40,000 to work in the UK for more than 12 months.
(1st of November 2010)
India IT firms say US rejecting business visas
US is rejecting a growing number of visa applications and visa interviews are bordering on interrogations, Indian information technology companies say.
Also recently, the US Border Security Bill hiked the fees for H1B and L1 business visas, leading to protests from Indian IT firms.
(4th of November 2010)
With 5 mn pounds to invest, make UK your permanent residence
If you’re rich and ready to invest more than £5 million in Britain, you could now get permanent residence in two years and full citizenship in five. The UK government is easing immigration rules to woo millionaires to make England their home.
(6th of November 2010)
36 Indian illegal immigrants arrested in Britain
LONDON: Thirty-six Indian nationals have been arrested in Britain for working illegally in the country, while six other Indians were found hiding in a lorry in France, trying to enter Britain illegally, officials said on Wednesday. Since July, over 400 operations have taken place across Britain which resulted in arrests of more than 800 people from various countries.
(1st of December 2010)
India imports 15,000 Chinese laborers to build, teach infrastructure projects
“India may be an IT superpower and producing thousands of doctors, lawyers and MBAs every year. But the biggest gap is in the availability of skilled electricians, carpenters, welders, mechanics and masons who can build mega infrastructure projects,” said Raghav Gupta, president at Technopak. India’s demand for steel is growing exponentially, and steel production, now at 70 million tons a year, will need to grow 12 percent every year to keep up. “China is the only country in the world that has built so many new steel plants in the past decade, almost like assembly-line products, adding about 80 million tons of steel capacity each year. So we decided to get their technology and manpower,” said R.S. Singh, director of Electrosteel Steel Ltd., the company building a factory in Chandankyari. “This factory is a classroom for Indian workers and we will create a benchmark for speed, quality and cost,” Singh said. The Indian workers are learning a new work ethic from the Chinese and are now more punctual, not stopping work to take frequent tea-breaks or gossip, managers said.
(23rd of October 2010)
g) expansion of defense budget and US reiteration that China uses Pakistan to stifle India
During US-president Obama’s visit to India this autumn some 250 businessmen were traveling with him. American exports to India have doubled between 2005 and 2009. India plans to spend 45 yo 50 billion USD on military hardware during the next four years. The Indian state hopes that intensified economic relations will translate into formal political recognition: “Will he make a major push to support India’s hopes of becoming a permanent member of the UN Security Council? Unlikely, say most analysts. Though the Indo-US nuclear agreement sounded the death knell of the era of defence technology apartheid practised against India, it will still be a decade or more before the ghosts of technology denial regimes are finally buried. The deeply entrenched bureaucracies in the departments of state, defence and commerce around the Washington beltway will take quite some time to finally accept India as a co-equal partner with whom dual-use technologies can be shared to mutual advantage.”
In the meantime the US diplomacy prepares the atmosphere for future arms deals.
“Relations between India and China have deteriorated in last 18 months and is unlikely to get better”, Blackwill, a former US Ambassador to India. “The Indians have a long list of Chinese transgressions, which in my judgment are accurate, having to do with Chinese policy on Kashmir and on the border dispute between the two countries and the so-called ‘ring of pearls’ of Chinese quasi-military installations in Bangladesh and in Sri Lanka and in Pakistan and so forth,” he said. “In other words, China using Pakistan to slow India’s rise,” Blackwill said.
(4th of November 2010)
h) increased investment of ‘Indian’ companies in Africa
In the past 18 months India-based Essar group bought coal mines in Mozambique, half an oil refinery in Kenya and a call center in South Africa. Essar Energy Plc. plans to invest heavily in Nigeria’s power grid. “Africa looks remarkably similar to what India was 15 years ago,” said Firdhose Coovadia, director of Essar’s African operations. “We can’t lose this opportunity to replicate the low-cost, high-volume model we’ve perfected in India.” India-based Karuturi Global Ltd. leases 311,000 hectares of land — larger than the U.S. state of Rhode Island — in Ethiopia and Kenya, and sells more than half-a-billion roses a year.
i) recent workers’ strikes at Foxconn, BYD and General Motors India
* Government seeks to crush strike of Foxconn workers in India
Defying police repression, thousands of workers have been on strike since September 21 in the industrial city of Sriperumbudur. The more than 7,000 workers at the plant are demanding an increase in wages, increased health benefits, as well as recognition for the trade union Thozilalar Sangam (FITS), which is affiliated with the Stalinist Communist Party of India (Marxist). On October 9 police arrested several hundred Foxconn workers who, in defiance of repeated police attacks, have continued the strike. A total of 319 workers, identified as leading activists, were remanded into judicial custody and transferred to Vellore central jail. The remaining few hundred workers not arrested were laid off. After being held for four days in jail, 307 workers were released on bail on October 13. On October 10, the day after the mass arrests, over 3,000 workers staged protest demonstrations on the streets of Sriperumpudur. They have been staging ‘Dharna’ (sit in protests) near the District Collectors Office. Police are preventing workers from staging any protests in and around the Foxconn plant. Foxconn workers are paid 4,800 rupees ($US106) per month. The workers are demanding a basic pay of 10,000 rupees ($US221) and other additional bonuses, along with health checks and medical insurance. Foxconn management has contacted some workers from distant villages who live in the Sriperumbudur area and forced them to report back to work. However, most of them defied that order. Now the factory is staffed partly by workers brought from villages through labor contractors, along with some workers who have given into management threats. However, only a few hundred are working in the factory now. Even the vast majority of the 6,000 contract and trainee workers have joined the strike. On October 19, CITU General Secretary Tapan Sen sent a letter to Tamil Nadu Chief Minister Karunanidhi urging his “effective intervention to resolve the crisis” at Foxconn “in the best interest of the company and its 7,400 workers”. That is, the union leader is appealing to the chief minister of a government that has framed up striking Foxconn workers to intervene in the interest of the company.
(World Socialist Web-Site, 25th of October 2010)
* BYD Electronics fires most of its workforce, after police break up sit-in
The Indian subsidiary of the giant Chinese-based BYD Electronics has fired most of the workforce at its plant in Oragadom in the south Indian state of Tamil Nadu, after the workers staged a sit-in to press their demands for increased wages, an 8-hour work day, the regularization of contract employees, and recognition of their newly-formed union. BYD has now locked out the entire workforce at its Tamil Nadu plant and announced the dismissal of all 2500 contract workers. More than 3,000 of BYD’s 3,350 production workers participated in the plant occupation, which began on the night of October 28 and lasted for almost two days. The workers chose to end their sit-in on the evening of Saturday, October 30, after baton-wielding state police surrounded the plant and vowed to storm it if workers didn’t vacate the premises in 30 minutes. When the BYD workers returned to the plant on Monday, November 1, they found the gates shut, a heavy police presence, and a letter on the company notice board. The letter said BYD is dismissing all its “contract” workers-that is, 2,500 workers the company has hired through recruitment agencies so that it can pay them even less than its 850 “regular” workers.
The BYD notice also announced the firing of 60 regular workers and said 437 others will be required to sign a letter of apology for “misconduct,” i.e., for their participation in the occupation. The three-and-a-half-year-old plant is now closed, ostensibly for a snap week-long “holiday.” Management is using this time to plot with the state government to resume operations using other poor villagers, recruited through various labor contractors, as scabs. Workers at the plant, which produces parts for Nokia cell phones, are forced to work 12-hour shifts. A majority of them are young women. Those with four years’ experience earn just 5,400 rupees (about US $120) per month. Workers approached the Center of Indian Trade Unions (CITU), the union federation led by the Stalinist Communist Party of India (Marxist) or CPM, to form a union on October 9, after BYD announced the layoff of a hundred workers. The vast majority of the workers-regular and contract-soon joined. With the company refusing to negotiate, the workers staged an initial sit-in on October 21. Faced with this militant action, one moreover that united contract and regular workers, the company agreed to hold negotiations with 68 of the workers. But within a week the negotiations broke down because the company insisted that it would not discuss the grievances of the contract workers. Suriyadevi, a young woman worker, told the WSWS, “We don’t get proper food in the company canteen. That’s also run by contractors. During our occupation the management cut off the water supply so that we couldn’t even use the bathroom. There was no canteen facility. All of them were deliberately stopped to exert pressure on the workers to return to work. Now we have been locked out and are standing under the burning sun.”
(World Socialist Web-Site, 4th of November 2010)
* GM workers call off strike, work resumes at Halol plant
Around 450 [other sources say 900 worker] workers went on strike on 29th of October 2010, demanding hike in wages. The plant, which produces 150 vehicles per day, has 900 permanent workers distributed equally between two shifts. The Halol facility has an installed capacity to produce 85,000 units every year in three shifts. The strike was ended after three days. Management claims that the strike was called off unconditionally, while union leaders say that they have a written agreement to negotiate a wage deal.
Comments
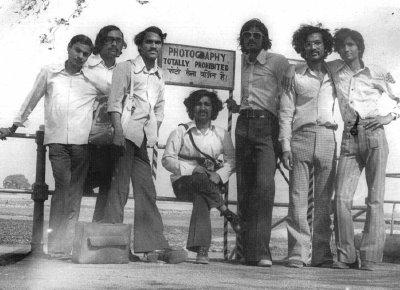
Below you can find various historical documents on working class experience in Faridabad in the 1970s and 1980s. Despite having been one of the largest industrial areas in India at the time and a hotspot of post-Emergency proletarian turmoil, the experience of workers in Faridabad rarely entered the realm of official labour history. For the current generation of workers and communists a critical engagement with the voices from the past is essential part of the search for new trajectories and new forms of organisation.
The material comprises translations of old articles from the still present local workers’ newspaper Faridabad Mazdoor Samachar; transcriptions of academic articles and other documents; and notes of ongoing conversations with workers about their past. The material is sketchy and the translations are not perfect – please see this as an open invitation to participate in the process.
In the near future we intend to bring more documents and voices back into our present discussions and extend the archive on this site. We will also try to debate some conclusions. At present we want to refer to the pamphlet on ‘Workers’ Self Activity’ by Faridabad Mazdoor Samachar, which you can find below.
Please get involved.
gurgaon_workers_news@yahoo.co.uk
List of Content
Sources:
Economic Political Weekly (EPW)
Faridabad Mazdoor Samachar (FMS)
Gurgaon Workers News (GWN)
/// 1970s ///
* Faridabad Workers’ Anger
EPW no.28, 1977: Report on mass strike and riots on 30th of June 1977 after death of worker Harnam Singh in police custody in Faridabad
* Capitalist Terror in Ghaziabad
EPW no.38, 1977: Report on industrial dispute and subsequent riot on 7th of September 1977 at Harig India, a company in Faridabad
* After CITU What?
EPW no.42, 1977: Analysis of workers’ discontent with union politics in Faridabad in 1977
* Anti-Worker Offensive in Haryana
EPW no.11, 1978: Analysis of post-Emergency repression of workers’ discontent in Faridabad
* Industrial Repression at Faridabad
EPW, 1978: Report on repression against workers, amongst others at company Autopin on 15th of February 1978 in Faridabad
* After the Massacre of Dalli Rajhara Mining Workers
EPW no. 24, 1977: Series of reports on contract mining workers struggle, the police massacre and the involvement of Congress and CPI
* Massacre of Kanpur Workers
EPW no.9, 1978: Report on police firings in Swadeshi Cotton Mills in Kanpur, on 6th of December 1977
* Police Massacre in Faridabad
EPW no.44, 1979: Report on police massacre and repression after general strike and demonstration in Faridabad, on 17th of October 1979
* From Emergency to Rural Maoism to Leninism in Faridabad
GWN Conversation, 2010
* Worker in Faridabad in early 1970s, Full Time Activist for CPI and later Naxalites, Sangarh Samiti 1979
GWN Conversation, 2010
* Escorts/Ford Worker in Faridabad in 1970s and 1980s
GWN, Conversation 2010
/// 1980s ///
* Revolutionary “Termites” in Faridabad
Loren Goldner, March 1998: Summary of important struggles in Faridabad in 1980s and 1990s
* Some Agitation in Faridabad
FMS, September 1983: Short news items on struggles in various companies (Biko Engineering, East India Textile Mill, Atul Glas, Usha Spinning Mills, JMA)
* Some Agitation in Faridabad II
FMS, October 1987: Short news items on struggles in various companies (HYDERABAD ASBESTOS LTD., Nukem Plastics, Autopin, Bombay Rubber, Metal Box, Escorts Anciliary, East India Textile Mill)
Escorts
* Escorts Intro
In 1980s Escorts was one of the ten biggest manufacturing companies in India. The Faridabad plants employed over 20,000 permanent workers, manufacturing tractors, motor-cycles, parts for the railways etc.
* “Interview with President of All Escorts Employees’ Union, Subhash Sethi”
by Journal of the Marxist Workers’ Tendency of the African National Congress (October 1981): Union leader who helped enforcing productivity scheme at Escorts portrays himself as anti-Stalinist revolutionary
* FMS – May 1983
Summary on powergame between old Escorts management faction Nanda and Indira Gandhi backed Swaraj Paul, from an internationalist Marxist perspective
* FMS – June 1983
Update on struggle about the Escorts ‘take-over’ through Gandhi – Swaraj Paul
* FMS – October 1983
Old Escorts union leadership breaks up workers’ protest and attacks new trade union leadership
* FMS – November 1983
Analysis on how both Nanda and Swaraj Paul make use of different trade union factions
* FMS – January 1987
Critique of Escorts Union president Subhash Sethi’s intimidating leaflet to the Escorts workers
* FMS – March 1987
Report on new agreement which settles a 50 to 80 per cent work-load increase
* FMS – December 1988
Report on how productivity bonus scheme has lead to productivity increase and piling up of inventory
* FMS – April 1989
Report on new agreement, which contains new work-load increase
* FMS – July 1989
Escort Union’s president resigns after only 17 workers turn up for 1st of May celebration
* FMS – February 1990
Report on introduction of compulsory pension scheme
* FMS – April 1990
Report on temporary closure of motor-cycle plant and mass lay-offs of temporary workers
* FMS – May 1990
Article on workers refusing the new agreement proposed by management and union
* FMS – July 1990
Article on reduction of over-time payment and the word-games attached to it
* FMS – November 1992
Article on the results of the formal breaking up of Escorts into various companies
* FMS – February 1993
Article on over-capacities and lay-offs in both motorcycle and tractor plant
* Escorts economic situation in 1998
News on take-over of motor-cycle division by Yamaha, of piston production by Mahle etc.
Gedore Jhalani Tools
* Self-Activity of Wage-Workers: Gedore Jhalani Tools
Kamunist Kranti / FMS, 1998: Summary of over a decade of practical involvement in Gedore Jhalani Tools dispute in Faridabad
* Revolutionary Termites: Gedore Jhalani Tools
Loren Goldner, 1998: Shorter version of the kamunist Kranti / FMS summary
* FMS – March 1983
Summary of 9 months of dispute previous to the tool down strike, which started on 12th of February 1983. The strike happens on the background of the threat of automation and mass lay-offs
* FMS – April 1983
Report on conflict between CITU and workers after workers’ rejection of agreement on 20th of March 1983, CITU leadership first tries to break strike, then has to resign
* FMS – May 1983
Short news item on union leader’s ‘excuse’ for signed agreement on 1st of May protest
* FMS – June 1983
First attempts of management to further delay wage payment and to provoke workers
* FMS – September 1983
Management pays outstanding wages to supervisors and staff after on one-day strike
* FMS – October 1983
Report that union leaders held plan for redundancies secret from workers
* FMS – November 1983
Short criticism of article on Gedore dispute published in the paper “April Kranti”
* FMS – January 1984
After having not been paid for three months staff of all three plants went on strike
* FMS – February 1984
Quarrel over minor issues between CITU and INTUC factions undermine workers’ unity
* FMS – March 1984
Lock-out at the third plant as first step for redundancy drive. CITU thugs start resisting workers (followed by summary of events between 1984 and 1988)
* FMS – December 1988
After having laid off over 1,500 workers in 1985-85 management started to loot the company – automation machinery has not been introduced
* FMS – May 1989
Several months of outstanding wages amount to 8,000 Rs per worker – the union suggests that the workers accept the companies’ ‘motor-cycle’-deal
* FMS – January 1990
Union leadership misinform workers about new agreement, workers confront them when they find out
* FMS – February 1992
Management cuts 800 Rs from monthly wage of some workers – according to the new agreement they have not met the production target
* FMS – July 1992
More arbitrary wage cuts based on ‘new agreement’, workers write collective letter
* FMS – March 1993
Wildcat strike and gathering against the new agreement on 9th and 10th February
* “The Company They Keep A Report on Workers of Jhalani Tools Ltd., Faridabad”
by Peoples Union for Democratic Rights, Delhi (November 1997): Longer report about dispute over outstanding wages – Jhalani Tools has not paid its workers wages due for the period March of 1996 to September 1997
/// 1990s ///
* “Dedicated to the Memoirs of Shankar Guha Niyogi”
FMS, October 1991: Memorial after murder of working class leader and review of struggles in Dalli Rajahara mining region since mid-1970s
* Police Firing on Striking Workers
EPW no.25, 1998: Report on police attack on protesting workers of the Pashupati Spinning and Weaving Mill at Dharuhera, Haryana, on 19th of February 1998
* Self-Activity of Wage Workers
FMS, April 1998: Political reflection on workers’ self-activity and the pitfalls of representation after nearly two decades of working class life and struggle in Faridabad
—————————–
* Faridabad Workers’ Anger
EPW 1977, No. 28
Ramnath Narayanaswamy
FARIDABAD is an industrial township, 20 kilometres from Delhi, with over 1,000 small-scale industries and a working class population exceeding four lakhs. On June 30, all activity in the township came to a standstill. Thousands of factory workers downed their tools in protest against the death in police custody of Harnam Singh, a maintenance foreman, working in one of the leading concerns of the area. Towards the afternoon, over 5,000 workers proceeded in trucks to Delhi to seek the intervention of the Union home minister, Charan Singh. Among the demands made to the minister were: a judicial probe into the alleged murder of Harnam Singh, immediate arrest of an inspector of the Haryana Central Investigation Agency and other police officials responsible for Harnam Singh’s death and the arrest of the owners of the factory where the deceased was employed.
Feelings ran so high that violence had erupted in many parts of Faridabad and vehicles proceeding to the capital were stoned, looted and burnt. Harnam Singh, it is alleged, had been tortured to death by the police on the factory premises in the presence of the managing director, a sub-inspector of police, and some other senior company officials. His co-workers allege that he was also administered some chemical and later taken to the hospital where he was declared dead. Harman Singh had been employed with the concern for the last 13 years. He resigned on June 13, when ‘the factory owners registered a case of theft where he and some of his co-workers were listed as the likely suspects. He was called to the police station on June 20 and after some preliminary interrogation permitted to leave. He was again called to the police station at 5 p m on the same day.
Balbir Singh, Harnam Singh’s brother, was called by the police on June 27 to Ballabhgarh where the CIA interrogation cell is located. According to him the CIA inspector systematically tortured his brother. Harnam Singh’s hands were tied and the other end of the rope was passed over the ceiling fan in the room. The fan was then switched on while the inspector kept asking Harnam Singh to confess. Lighted cigarette butts were applied to different parts of Harnam Singh’s body. Balbir Singh saw his brother for the last time on June 29. Harnam Singh was taken to the factory premises. After a cup of tea at the reception office, the police party proceeded to the electro-plating shop, beside which there was a well into which the stolen goods had been allegedly dumped. Harnam Singh breathed his last in the electro-plating shop allegedly in the presence of the managing director, assistant general manager and police officials. A brief view of the body at the mortuary revealed extensive torture marks. No part of the body had been spared and, according to one informant, the soles of Harnam Singh’s feet had been pierced with nails and subsequently burnt. While at Faridabad this writer also met Balbir Singh, who fully confirmed the reports of the torture of his brother.
On July 1, workers of the Okhla industrial estate observed a day’s strike to protest against the brutality of the police and the factory management that caused the death of Harnam Singh. The decision to go on strike was taken by over 2,000 workers in Okhla and a condolence resolution was adopted. The atmosphere was tense with rising anger at the police who the workers allege, are hand in glove with the management. Armed guards had become a common sight in Faridabad and armed police had been posted at various strategic places in anticipation of further disturbances. The same morning, an armed mob of over 50 persons, broke into the premises of the Presolite factory on Mathura Road and attempted to set it on fire. The security and accounts offices were set ablaze and a number of company records were damaged by the blaze. Local rumour has it that the fire was deliberately caused by one section of the management concerned in the Harnam Singh case. The fire, it seemed, was aimed at the location of the records that may have implicated the management.
A police camp and a special control room has been set up in Faridabad. Armed guards are on constant vigil while armed police who have been urgently summoned from Rohtak, Ambala and Karnal have been posted on Mathura Road to prevent further disturbances.
The police have registered 13 cases of rioting so far and made 158 arrests. On July 2, workers at Okhla decided to continue the solidarity strike the next day as a gesture of support to the workers at the Presolite factory. Some of the factories had begun to open their shutters while the Presolite factory remained closed. The Peoples’ Union for Civil Liberties and Democratic Rights has called a protest. The march will be sponsored by 12 trade unions and democratic rights organisations and will condemn the high-handedness of the police in the Harnam Singh case and also protest against the firing in the Dalli-Rajahara mines in Madhya Pradesh on June 3. Efforts are also being made to secure the release of workers arrested under section 144 and to ensure that there is no victimisation. The Haryana government has announced a grant of Rs 5,000 to the bereaved family. An inquiry by a sessions judge into the incident has been ordered and the superintendent of police of Gurgaon has been transferred. An inspector of the Haryana Central Investigation Agency, who had been suspended on June 30, was later arrested in connection with the death of Harnam Singh.
* Capitalist Terror in Ghaziabad
S K Rao
EPW 1977, No.38
On the morning of September 7, Harig India, a machine tool factory located in Mohan Nagar near Ghaziabad, was the scene of a violent confrontation between workers and the management, in which two persons died, 76 were hurt and the factory was gutted by fire. The events leading up to this violent incident add up to a dismal story of murky methods and goondaism in management-worker relationships.
Harig India is a 16-year old plant manufacturing surface grinders, cylindrical grinders and other such machine tools. It employs about 128 workers, of whom about half are unskilled and semi-skilled. The semi-skilled and the unskilled workers, it is reported, get a monthly pay of Rs 200 to Rs 300, while the skilled workers get from Rs 300 to Rs 900.
The events of the 7th morning seem to be a direct culmination of the efforts by the management to prevent workers from voicing their long-felt grievances through legitimate trade union activity. The management, it is alleged, had brought in goondas to suppress the workers’ trade union, which resulted in these violent incidents.
Ramu Roy, the President of the Harig India Workers’ Union, says that none of the workers have got appointment letters or identity cards; and while provident deductions are made, the management refuses to give them receipts for it.
The workers of this factory formed a union in January 1977 before the Emergency was lifted. All the workers joined the union. After the Emergency was lifted, in June this union sought affiliation with CITU which has become the major trade union force in this area. CITU has managed to double its strength after the Emergency – its membership has gone up from about 10,000 before the Emergency to about 20,000 after the Emergency. During the Emergency and even before it, the other trade unions had lost much of their credibility because of their soft-pedalling of workers grievances. After the Emergency, the CITU, because of its militant advocacy of workers’ rights in the past and the favourable political climate, has emerged as the most important trade union in this area. And, precisely for this reason, the industrialists of this area, where about 100,000 workers are employed, have been resenting the growth of this trade union. They have been adopting various tactics to keep the labour servile and underpaid: very often, it is alleged, that several workers are employed under the contract labour system, which denies them the usual privileges which go with regular employment; and often even the recommendations of the engineering wage board are not implemented. To this day, it is said, the recommendations of the engineering wage board, made as long back as 1969-70 and which could make a difference of as much as Rs 90 and more in the monthly pay of workers, have not been implemented. The growth of the militant trade union, CITU, in these circumstances has caused much apprehension and anxiety among the employers in this area.
What happened at Harig India should be seen in this context. When the newly-formed factory union got affiliation with CITU and demanded recognition from the management, the management refused it. Not only that, the workers allege that the management set in motion a train of events which culminated in the violence of the 7th. On June 28, the Union presented a charter of demands including bonus payment, variable dearness allowance, house rent, cycle stand, canteen for the workers, right to casual leave and facilities for drinking water which had all been denied to them so far. The management, instead of accepting or negotiating these demands, brought in four new security guards who carried guns, kirpans, etc. and allegedly lounged about the place making threatening noises against workers. The workers allege that these new security guards were known goondas whom the management hired on a contract basis to suppress the trade union; they were to receive, it is said, Rs 50,000 as hush money, of which Rs 15,000 was paid in advance. Suraj Bhan Bharadwaj, the chief organiser of CITU in Ghaziabad area, has alleged that some of these new security guards were employed earlier by another firm, Bramac Suri (Pvt) Ltd., to break an 108-day old strike. The management of this factory denied this. At any rate, the allegation calls for investigation into the antecedents of these four people. It is also alleged by the AITUC leaders that these same people were employed by Harig India earlier to scare away some villagers from whom the land had been acquired by the UP government on which this factory is located. These allegations of unsavoury background of these new security guards has not yet been denied by the management through detailed clarification of their earlier careers. The police say that they are looking into the antecedents of these people but nothing has yet come up which denies these allegations of the workers.
The management then inducted these disputed characters onto the scene when the workers were presenting their charter of demands through CITU. Moreover, the workers allege, the management in an attempt to get rid of the activist workers started denying raw materials to the sections where they were working and eventually laid off eight workers on August 10. After this, the management says that there was a tool down strike on August 17, 18 and 22; the workers’ representatives deny this. The management in any case cut 7 days’ wages even for a single day’s strike. But before the workers discovered this on September 6 when the pay packet arrived, on August 30 the central office of CITU in Ghaziabad submitted a memorandum to the Chief Minister of UP through the District Magistrate Ansari, in which among other things they pointed out that some managements, including that of Harig India, had been employing goondas to terrorise workers and that the authorities should take immediate steps. Bharadwaj says that he had even told the Police Superintendent verbally that an Assistant Inspector of Police was seen to be very friendly with the alleged goondas-cum-guards of Harig India and that the SD had assured him that he would look into this immediately.
Then came September 6 when the workers discovered that a week’s wages had been cut from their pay for the alleged tool down strike which, even according to the management, had lasted only three days. The workers, considerably incensed by this, refused to take any pay at all. The workers, according to Bharadwaj, decided on a strike following this and were planning to give notice of this to the management the next day in due manner. The next morning, that is on the fateful 7th, about 10 workers reached the factory gate by 7.00 am to put up posters and raise slogans. The new security guards, who were amusing themselves in a restaurant opposite the factory, it is alleged, advanced towards the factory workers with their kirpans. This confrontation immediately attracted some other workers and passers nearby. As the crowd grew in size, some of the guards allegedly opened fire; the pellets hit the crowd. The injured, among whom were Veer Singh, Nareshan and Dharm Vir Choudhary, were immediately rushed to hospital which was two minutes away. By 7.30 am the Shahibabad Police were informed; the police did not, however, come immediately because they were held up on the way by a crowd of students who held up the buses. According to Press reports, the Ghaziabad Police were also informed by 7.45 am and one industrialist even claims to have sent his own vehicle to fetch them. But they too did not come immediately. It is reported that by the time the first police party arrived it was 9.00 am.
But by 9.00 am a large crowd gathered numbering thousands. What happened that morning is reported in several contradictory ways, with different parties claiming different versions to be true. The first newspaper reports say, however, that by the time the police arrived the guards were on the roof firing gunshots into the crowd. About 70 people were indeed injured by pellets and other wounds – a fact that is not denied by anyone. The police, it is said, finding that the guards were firing dangerously into the crowd, ordered them to come down; when the guards refused to come down, the police made their way onto the roof and fired at the guards – a fact which again is not denied by the police. The guards when then disarmed and brought down by fire ladders – for the building had been set afire already. The workers say that the guards themselves had set the building on fire as they retreated onto the roof in the face of the surging crowd to prevent it from getting nearer; the management denies this saying that the crowd set it on fire. In any case, the first newspaper reports say that the police after firing at the guards on the roof disarmed them and brought them down. As they were being taken away, the police say, the crowd by now enraged asked the police to hand over the guards to them. The police refused, but the crowd seized two of them, Harbhajan Singh, a foreman, and Jeet Singh, allegedly a guard and lynched them to death. This is the police version. The workers say that while it is true that the crowd hit at these two people, they were already dead by the time they were brought down from the roof by the police; they say that the police in fact lowered them by ropes after tying them up, which shows that they were already dead. One should say, however, that this fact – that these two persons were lowered down by ropes by the police from the roof – is not reported in the news reports on the first day. However, the subsequent post-mortem reports on these two bodies say that while Harbhajan Singh died of multiple injuries, including damage to the vital organs, Jeet Singh’s death was caused among other things by a gunshot wound. As none of the reports say that anyone in the crowd was seen using a gun, who exactly fired the shot at Jeet Singh remains a mistery, for the police say that while admittedly they had fired at the guards on the roof, it was not a wound from a shot fired by them which was found on Jeet Singh.
Thus two people were dead; about 70, including some among the police, were hurt by pellet or other wounds. The whole event has enraged the workers in the area so much that most of the workers went on a snap strike that day, culminating in a public meeting in which about 20,000 people participated. Since then, Section 144 was imposed and several arrests were made, including those of Veer Singh and Nareshan, two workers, who, according to the workers’ representatives, had been wounded by the pellets and been taken to the nearby hospital much before the police came after which the alleged lynching took place. The workers are now demanding a judicial enquiry and release of all the arrested.
(…)
* After CITU What?
EPW 1977, No.42
ANS
An uneasy feeling of betrayal by the present political leadership is spontaneously manifesting itself among militant sections of the working class in and around the Capital. A great deal of the resentment bottled up during the Emergency, and quiescent for a period after, has begun to boil over in the manner witnessed at Faridabad in July and Ghaziabad last month.
For a brief period it was possible to argue that the ‘labour unrest’ was part of the post-Emergency euphoria. Not so any longer, as the frequent clashes in Faridabad, Ghaziabad and Sahibabad will testify. The cry for reinstatement of those sacked during the Emergency and restoration of rights and privileges is gradually giving way to resentment against the present “democratic excesses”, such as the UP government’s decision to ban strikes in a number of industrial units (private as well as public sector), the partiality of the Haryana police towards owners in Faridabad and the use of hired thugs by industrialists to terrorise workers at Pilakhua-Ghaziabad and Mohan Nagar.
The trade union movement in this region is itself in a state of flux. The unions have till now existed on the explicit understanding that the state had the right to formulate laws for all sections of society. Union struggles have, at their highest stage, been directed against particular laws and have not been part of a general struggle to recreate society itself. With the increasing inability of the unions to influence the government even as ‘pressure groups’ on behalf of labour, this role of the trade unions is being called into question by labour militants. Outside of the wage demands, there is a widening tendency for workers to “take the law into their own hands”. Trade unionists are forgotten, indeed they remain discreet bystanders, in direct confrontations between workers and managements. They often enter the scene after the event. In a confrontation between workers and some hired thugs in the pay of some Hapur industrialists in July, for instance, it fell upon local union leaders to play the role of “harvest brokers” to placate a 500-strong band of irate lathi-wielding workers. Similar confrontations have been reported from Pilakhua and Sonepat as well.
The major recent confrontations in Faridabad and Mohan Nagar (Ghaziabad) highlight this dichotomy between working class struggles and the trade union movement. At Faridabad, the confrontations reached the stage of an open battle against the government with the police emerging on the side of the owners. The entire working class upsurge at Faridabad in July had an element of spontaneity. Even the call for a general strike in Faridabad and neighbouring Badarpur came from the workers with the trade unionists lamely following behind. Indeed, most of the unions, including those of the left, were caught on the wrong foot. When irate workers stormed the Prostolite factory and set it on fire, the unionists were beseeching the workers not to destroy “national property”. Some unions, including those of the left, branded the destruction as the handiwork of outside saboteurs, thus disowning the working class they claimed to represent. It was only after workers in Badarpur joined the struggle that the unionists “rose to the occasion” by issuing statements of support and sympathy. They soon even claimed responsibility for a “successful general strike” which was not their doing.
At Mohan Nagar, resentment against the use of hired thugs by the managements had been building up since the early 1970s. Hired thugs are not new. The Emergency merely intensified such forms of coercion and the post-Emergency period has brought no let-up. Before the Harig India incident of September 8 (EPW, September 17, pp 1635-36), several other units had used thugs to break workers’ actions. A major textile plant in Modinagar nearby employed as many as 250 armed men to break up a strike which had been banned by the UP government a few days earlier.
When the hired goons of Harig India allegedly began firing on the workers, neither the trade unionists nor the police were much in evidence. The unit leader, Ramu Roy, was present, but he appeared to have very little to do with the developments. Once again the workers had reacted spontaneously. The general strike by workers, the processions and wearing of black arm-bands were decisions taken by the workers with the unionists endorsing them belatedly.
The present writer recalls a rather amusing meeting shortly after with an AITUC leader in the posh air-conditioned offices of a major liquor magnate in the neighbourhood. After some exchanges of compliments between the union leader and the industrialist, the former drew attention to the failure of the police to arrive on time and the resultant “sad loss of national property” (the factory was burnt by the workers). The union leader added, “there is no discipline left after the Emergency”.
Middle level trade union functionaries have had to face some difficult situations. One such left wing functionary in Faridabad was assaulted in early August by a 4,000 strong band of textile workers. The leadership of the union classified the event as a “plot” hatched by right-wing elements. The issue, however, goes much deeper than a right wing left wing confrontation and the hatching of “plots”, for, if there had been no initial resentment, it would have been difficult for agent provocateurs to forment a “plot” among workers who till the other day had enthusiastically accepted the leadership of the very unionist they later assaulted. The workers alleged that the assaulted unionist had been responsible for the arrest of numerous worker militants during the Emergency and was even in the pay of the mill management.
All this is not to say that the established central trade unions in the area are all on the wane. A shift is taking place. The INTUC and the AITUC are yielding place, mainly to the CITU – the fastest growing union in the area. In a few months, the CITU has taken over leadership of at least 70 units in the Ghaziabad area, creating alarm in political circles in UP. In fact there is every evidence of a concerted political drive by the UP and Haryana government to project the BMS (affiliated to the erstwhile Jan Sangh) and to stem the CITU advance.
Such shifts in alignment must, however, be viewed as temporary phenomena. The inability of trade unions to speak for labour as a whole is compounded by the fact that at no time does the total union membership of registered unions exceed 25 per cent of the total organised work force. The “peak periods” of trade union membership in the organised sector in recent times were in 1966 and 1971 when there were 4.08 million and 4.37 million union members (in central unions) out of an organised work force of 16.8 million and 17.49 million, respectively. If one were to take the unorganised sector, including the more than 100 million landless agricultural labourers into account, the performance of the trade unions would be seen to be pathetic. This trade union vacuum is especially felt in areas like Sahibabad, a fast developing industrial area in Ghaziabad district, and Hapur, a major foodgrain mandi in UP and also an expanding industrial town, both of which attract large numbers of seasonal labour from rural areas during slack periods in agriculture.
While all the central trade unions are, in one way or the other, linked to various political parties, the membership criteria is quite unambiguously non-political. Confronted by a wider choice of unions, labourers either continue to stick to the status quo or, if the present union should badly fail them, cynically shift over to the most likely to deliver the goods. Thus unions attached to the party in power may be preferred sometimes purely on the ground that demands made through them are more likely to be viewed favourably. The INTUC, for instance, registered a spectacular rise of 13 per cent in membership between 1975-76 and 1976-77 at the height of the Emergency. The AITUC and the HMS, on the other hand, registered increase of 3 per cent and 12 per cent, respectively in 1967-68 to 1968-69 which also saw the emergence of numerous united front governments all over the country. In this same period, INTUC membership fell by 8 per cent.
In this situation the failure of the central trade unions reflect not so much in the total decline in union membership as in their inability to induct new members (not yet unionised) into the sphere of union activity in keeping with the rising labour population. In and around the Union Territory of Delhi, such a situation has led to the growth, albeit still small, of ‘internal’ unions and of what are referred to as ‘Syndicalist’ tendencies on the part of the working class.
Another factor which is gradually becoming irrelevant are the ‘alternatives’ placed before the working class in the form of various unions. By now the organised sections of workers in Faridabad and Ghaziabad have gone through the whole gamut of unions and the sole ‘alternative’ left is the CITU. At each point of time, the shift has been leftwards to more militant unions, but disillusionment also has come faster. As Bhaskar, a militant worker in an oil mill in Ghaziabad said quite cynically, “they are all the same. The CITU talks of working class unity here while the CPI(M), its political leadership assures industrialists in Bengal that gheraos will not be tolerated. Leaders of the 1974 railway strike are ministers today and the same bonus demands of railway workers made then are no longer justifiable today. Such empty talk will not fill our stomachs.” Which still leaves us with the question, “After CITU what?”
* Anti-Worker Offensive in Haryana
EPW 1978, No.11
(…)
Since 1967 when the first united front government was formed in West Bengal followed by a spate of working class protest demonstrations, about 300 industrial units have shifted to the Haryana region from that state. One of the attractions in north India at the time was the ready availability on unorganised labour who were still unaware of the rights they enjoyed under the existing labour, and could therefore be made to work on subsistence wages.
But “the wind will not cease even if the trees want to rest”. Attempts to organise the workers into unions soon brought trade unionists into a direct confrontation with the employers. In 1973, during troubles at the Gedore Tools factory in Faridabad, a workers’ procession led by the Centre of Indian Trade Unions was fired upon by the police, and one worker was killed. Soon after this, a strike in the Usha Spinning mill fizzled out after police brutality and hunger had forced the workers to return to work without winning and concessions from their employers.
With the declaration of the Emergency, it became evident that labour in Haryana was more than ever at the mercy of the employer. The CITU was virtually banned since it was not allowed to function openly. The Trade Union Co-ordination Council consisting of CITU and AITUC, set up before the Emergency, became defunct.
Extreme Exploitation
A brief look at the working conditions in the industries in Haryana would reveal the extent of exploitation. Of the 100,000 odd workers in the area, more than half are unorganised. Although the minimum monthly wage fixed by the Haryana government is Rs 170, a large number of workers, particularly women, receive only Rs 70 to Rs 80 a month. It should be remembered that as far back as 1957, the 15th Labour Tripartite Conference held that a monthly wage of Rs 100 should be the minimum for a family of four. According to the present price index, trade unionists estimate, the minimum should be raised to Rs 350.
Quite a number of workers employed by the industries are what is known as “contract labourers”. They are not entitled to any casual or earned leave or any other facilities like provident fund. The employers’ rule of ‘hire-and-fire’ decides their working conditions. As soon as the Emergency was lifted, the accumulated grievances of the workers broke out into spontaneous protest demonstrations and charters of demands. Owners of at least 100 factories at the moment are facing charters of demand from their workers who mainly want the implementation of the minimum wages act and an end to contract labour and other unfair practices. (…)
Use of ‘Security Guards’
The industrialists of Faridabad, Ballabhgarh, Ghaziabad and other areas of Haryana have indeed begun to behave like the early American bourgeoisie. The latest feature of their labour policy is to hire so-called security guards to crush unions. One is reminded of the notorious US detective agencies – Pinkerton, Burns, Corporations Auxiliary Company – whose services were bought by American business firms to spy on employees’ associations, wreck them when they secured a foothold and destroy them when they tried out their strength. (…)
Something of the same sort is happening today in Haryana. The fact that some industrialists were maintaining a private army of their own to deal with recalcitrant workers came to light in October 1977 when ‘security guards’ shot down workers at the Harrig India factory in Faridabad. Since then the news of such mercenaries employed by several industrialists have been pouring in. The incidents at Auto Pins factory in Faridabad (on February 15) were sparked off by attacks of these ‘security guards’ hired by the owner on workers who were demanding a restoration of their wage-cut. According to later police inquiries, it was found that at least three of the 17 security guards were notorious criminals of Alwar. The Deputy Superintendent of Police of Haryana did not rule out the possibility of the remaining 14 having criminal records elsewhere.
That the owner of Auto Pins factory has been maintaining these guards on his pay roll for quite a number of years was revealed recently through the leakage of an old letter written by a fellow industrialist to another industrialist in Haryana. Piqued by abuses hurled by these guards when he came to attend a Rotary Club meeting at Faridabad, the writer of the letter dated November 22, 1974 complained that a “heinous atmosphere was being created by Mr Avtar Singh [owner of Auto Pins] and added: “25 to 30 goondas hired from Alwar have been retained by his group of industries and spread over the various associate concerns of M/s Auto Pins to be utilised as a terror at every eventual occasion to harras and horrify me”.
Avtar Singh has apparently given a lead to other industrialists in Haryana. It is estimated that as many as 15 agencies – the Indian counterparts of Pinkertons and Burns – are doing roaring business in recruiting and supplying ‘security guards’ to factory owners. The majority of these guards are recruited from professional criminals, and lumpen-proletariat from Muzaffarnagar and Alwar.
Pro-Employer Role of Government
The events at the Indian Dyes Chemical Organisation in Sunepta, which took place a few days before Auto Pins incidents, reveal not only the same pattern of hiring mercenaries to crush unions, but also the pro-employer role of the Haryana state government and the unfortunate contradiction between the unemployed and the organised labour force which is exploited by the employers. The management of the IDCO at first tried to prevent the workers from forming any union, notwithstanding which the CITU managed to organise a union and launch a strike demanding among other things implementation of the minimum wages act in August 1977. The then Haryana minister for Labour, Sushma Swaraj, asked the company to pay Rs 100 to each worker, which the company refused to do. Soon after this Sushma Swaraj was replaced by a new labour minister, Satwir Singh Mullik, who declared the strike illegal. The factory owners in the meantime succeeded in bringing in some villagers from nearby areas to replace the striking workers, who began a ‘dharna’ in front of the factory gates. On February 11 this year, the company director arrived on the scene and his ‘security guards’ demolished the workers’ tents and fired upon the workers killing a CITU office-bearer of the union.
There is a strong suspicion among many in Haryana that some of the leading members of the state cabinet have personal stakes in the industries, which explains the attitude of the state government. It is rumoured that the son of the labour minister is connected with agents who supply coal to the industry. The Home Minister, Mangal Sain, is reported to have shares in Auto Pins Ltd.
But it seems that the involvement of the politicians with the industrialists extends further up. When a calling attetion motion on the Haryana incidents was put up at the Rajya Sabha on February 21, the minister of state for labour, Ram Kripal Sinha, told the house that the law and order situation in Haryana was the responsibility of the state government and it would be desirable to leave it to the government of Haryana to sort it out.
False Propaganda
Utterances by various Central and State Ministers indicate that the authorities are going to be quite tough handling working class movements. To befuddle the public and alienate them from the workers, they are already harping on the theme of inter-union intra-union rivalries are the reasons for the industrial unrest. The President of the Employers’ Federation of India in a recent communication to the Union Minister has already given this cue which is likely to be followed by government spokesmen when called upon to inform the public about the growing labour troubles.
The facts of the cases in Haryana however contradict the version of the management. Also the Jan Sangh labour wing, the Bhartiya Mazdoor Sangh (BMS) and the Reddy Congress front, National Labour Organisation (NLO), are trying to make inroads into the industrial scene, they are still insignificant forces and the CPI(M)-dominated CITU is considered to be the main threat by the employers, some of whom have been known to have urged workers to join any union except the CITU. CITU spokesmen challenged the authorities to cite any single instance of clashes between their unions and BMS or NLO unions, and reject the management propaganda of inter-union clashes as causes for disturbances.
But it appears by default the CITU is assuming a political importance which is in no way commensurate with its organised strength in Haryana. By their own admission, the CITU has not yet been able to set up unions in the majority of the factories in the area, although they claim to be receiving invitations from workers from various units. But lack of organisers and a desire to concentrate on a few important units are probably the main two factors behind their present strategy.
Employers’ Calculations
The employers however are calculating on a long-term basis. The sudden surge of spontaneous militancy among the workers may force the hands of CITU or other trade unions to stage movements on demands like implementations of awards which the employers have been able to ignore all these years. In 1967 and 1969 movements on similar demands in West Bengal forced them to shift to unexploited areas like Haryana, Punjab or Uttar Pradesh. In 1978 however few such untapped areas are left. Although statistically industrial relations in 1977 was only marginally worse than that in 1976 (from January to October 1977 11.2 million mandays were lost on account of work stoppages against 10.2 million mandays for the corresponding period in 1976), the number of such stoppages increased in almost all the major states in India.
Such being the case, from the employers’ point of view, any manifestation of workers’ protest, however embryonic it might be, will have to be nipped in the bud. This explains the ruthless behaviour of the industrialists in Haryana.
It would be worth observing how in such a situation the CITU and other Leftist trade unions shape their strategy and tactics. The conventional form of struggle like ‘dharnas’, sit-down or tool-down strikes, or long-drawn-out strikes can sometimes be effective depending on the vulnerability of the employers and the tenacity of the workers.
(…)
* Industrial Repression at Faridabad
EPW, 1978
Ramnath Narayanswamy
VIOLENT clashes between management and labour have always characterised Faridabad, the industrial township of Haryana. On February 16, over 120 striking workers and 17 security guards of the Auto-Pin (India) were arrested in the evening on charges of rioting and arson. Over 17 people had sustained injuries – some of them, injuries on the chest and shoulders, caused by brickbats and lathis. The arrested were remanded into judicial custody by the sub-divisional magistrate at Ballabgarh. It is expected that AITUC and CITU will launch a series of demonstrations and gate-meetings to protest against the increasing industrial repression let loose by the managements of the leading concerns in Faridabad.
Management victimisation, non-payment of allowances, prevention of workers from forming unions, and low wages have continued to be the main grievance, of the workers in Faridabad. Refusal by managements to negotiate the question of forming unions has led to innumerable gate-meetings, tool-down strikes, and other forms of protest. Workers allege that it is common practice among concerns who have not allowed a union to be formed to employ ‘goondas’ to meet labour protest. The workers also allege that the police assiduously avoid interfering with the activities of the ‘management goondas’ who – well-armed with knives and in some cases even guns – are the primary forces of industrial repression against workers.
The February 16 incident centered around the strike which the workers of the Auto-Pin (India)- were waging against the company. Auto-Pin (India) manufactures leaf springs and bodies for tractors and defence vehicles. The workers were demanding negotiations on a charter of demands relating to increase in wages, bonus, incentives, and house rent.
Security guards (the workers allege they were ‘goondas’) were employed by the managing director about a fortnight earlier because he was apprehending “definite trouble”. It is significant that according to the managing director he had no knowledge of the past records of the ‘security men’ he employed where they came from. According to the workers, about three or four days before the strike began, they had begun to brandish knives and guns.
The trouble began when the tent in which the factory workers were lodged was ripped down at the orders of the management. When the workers resisted, the ‘security guards’ lathicharged the workers. The story was later confirmed by eye-witnesses who were present during the exchange between the workers and the ‘security guards’. The workers’ strength swelled, and the retaliation began when bricks were hurled at those inside the factory. Meanwhile brickbats continued to be thrown from inside the factory. How they got there remains unexplained. The workers insist that a day earlier they had been stored there by the management. There was an exchange of brickbats between the striking workers and those inside the factory. Several vehicles parked outside the factory premises were burnt and the windscreens of the cars smashed. The factory glass panes were also smashed, and the premises bore signs of wreckage.
The management has circulated a story that it was provocation by the workers that led to the violence on both sides. According to them, management personnel were prevented from entering the premises and the ‘security guards’ were “forced to act” when the striking workers refused entry to the management personnel and attempted to enter the premises.
When this writer visited the factory premises, there were a dozen armed policemen at the factory gate. According to some workers from the neighbouring concerns, the management was responsible for the destruction of the vehicles parked outside the factory, which they had caused in an attempt to rest the blame on the striking workers. According to both trade union leaders and workers, the employment of ‘goondas’ under the guise of security men by the management has become common practice in Faridabad. These ‘goondas’ are fully armed, and play a prominent role in breaking unions where unions exist, in preventing their formation. The managements employ them particularly when strikes are in progress.
According to the trade union leaders, the police in Faridabad turn a blind eye to the activities of the goondas even when acts of violence by them are brought to their notice. According to Sharms, secretary of the Faridabad unit of the CITU, three of the security guards of Auto Pin were well known thugs of Alwar. Consequently, the enormous arms build-up in the concerns at Faridabad and their free use by the goondas in times of industrial tension is not at all surprising. It is significant, too, that reportedly in the aftermath of the arrests at Auto Pin the security guards were released on bail whereas the 120 striking workers were not.
Indeed, incidents of victimisation, lay-offs, and management-hired goonda violence, have been increasing steadily over the recent past. Several instances can be cited. Among the most prominent of them was the case of Shiv Sharan, a worker, who was attacked en masse bv over 60 armed men at his residence in Ballabgarh. He was soon bullet-ridden, and succumbed to his injuries in the All India Institute of Medical Sciences in New Delhi. Among the others shot, were his wife, his 17-year-old daughter, his 80-year-old mother, and over 20 other workers of the same locality. In the midst of such violence, the Haryana Home Minister, Mangal Sein, has declared that the law and order situation was completely under control. He also added that the government was in favour of trade unionism and assertion of workers’ rights, but that the government would not ‘allow anyone to take the law into his own hands’. According to the honourable minister, the labour unrest was due to “elements that want to misuse the restoration of democracy”.
* After the Massacre of Workers of Dalli Rajhara Mines
EPW no.24, 1977
N K Singh
[We suggest as further reading the article by FMS, which was published after the murder of Niyogi in 1991 - see section on 1990s]
KILL ordinary workers fighting for their just demands and dub them Naxalites. The police firing on the striking workers of the Dilli-Rajahara mines, in which ten persons, including a woman and two children, were killed and at least 15 others received bullet injuries, smacks of a carefully-planned plot.
On June 2, the president of the recognised union of the mines, a CPI leader, tells a press conference that Naxalites have ‘struck a reign of terror’ in the area. Acting quickly, the same night the police goes to arrest the ‘Naxalite leader’, Shanker Guha Niyogi, who had been making allegedly ‘derogatory speeches’ and ‘instigating’ the workers to continue their agitation. Niyogi is the leader of a union, Chhatisgarh Shramik Sangh, which is not recognised by the Bhilai steel plant authorities who own the mines. Some two to three thousand workers assemble and resist the arrest of their leader.
They ‘turn violent’. The police ‘resorts to firing’. So runs the official story. When the first reports of the massacre arrive on the Samachar printer, it is given out that three workers had been killed. After some time comes another report, putting the number of the dead at five. Then comes a report that police had opened fire a second time, at noon, to ‘rescue’ some police-men allegedly held captive by the workers who were demanding the release of Niyogi. The toll goes up to seven. This time the report adds that among those killed were some police-men as well. By late night the figure mounts to nine. Samachar, which had failed to mention that among those killed were a woman and a 12-year-old boy, withdraws its earlier report that some policemen were in the casualty list. “No policeman was killed”, it now says. Next day yet another body of a 12-year-old boy is ‘discovered’ from the place where the firing took place, now under curfew. It is now disclosed that apart from the leader of the Chhatisgarh Shramik Sangh, Shanker Guha Niyogi, five other persons have been arrested; that the police are combing the area for more union leaders who are alleged to be Naxalites; however, the law and order situation was under control. Peace at last!
The Dilli-Rajahara iron ore mines in Durg district are the captive mines of the nearby Bhilai steel plant. While the, mechanised section of the mines is run departmentally, the manually-operated units are run by contractors, violating the government directive, issued way back in 1971, to take over all such units where the work was of a permanent nature. There is a big difference between the wages and service conditions of workers employed by the Bhilai steel plant and of those employed by the private contractors. The contractors, it is an open secret, resort to underhand methods and use of force they employ a private army of armed goondas – to suppress the restive workers. Since almost all the contractors are Congressmen, political patronage was never lacking. Coupled with the vested interest developed by the officials in the contract labour system, the political influence of the powerful contractors had thwarted all the attempts of the workers to force the government to implement its own six-year-old decision to abolish the contract labour system. The recognised AITUC union, the Samyukta Khadan Mazdoor Sangh, was only too happy’ to play ball with the contractors and the Bhilai Steel plant managenment. Shanker Guha Niyogi, today’s much-maligned Naxalite’, entered the labour force in the area as an ordinary mine-worker. Most of the labourers employed through contractors are local people, while the better-paid jobs in the mechanised mines have been cornered by outsiders. Niyogi took up the cause of the poorly-paid local workers and named his newly-formed union the Chhatisgarh Shramik Sangh. Although the union was not recognised by the management, Niyogi led many successful agitations and forced the contractors to accept a number of long-pending demands of the workers. Workers began to desert the recognised but inactive AITUC union and join Niyogi’s non-recognised but active union. At this point the authorities discovered that Niyogi was a ‘Naxalite’ and decided that his proper place was behind bars.
So in 1970 he was arrested and sent to prison, much to the relief of the contractors, the officials and the AITUC leaders. It was not till the Lok Sabha elections were announced in February this year that he was released along with other political prisoners. As was to be expected, during the Emergency the AITUC union had turned into a shameless lackey of the management. There was very strong discontentment among the workers and as soon as Niyogi reappeared on the scene a majority of the workers shifted their allegiance to the Chhatisgarh Shramik Sangh, which gave a call for strike in support of its demand for abolition of the contract labour system, payment of bonus, and allied issues. The two-week long strike was a complete success.
What was the AITUC’ attitude to this success of the workers? Homi Daji (1), general secretary of the Madhya Pradesh AITUC, declared that “Most of their [the workers'] demands were unrealistic, which could not be met”. Talking to this writer a couple of days after the Rajahara firing, which he condemned like all the other political leaders by issuing a statement, Daji said that Niyogi and his men ran a trade union in “a non-trade union manner”.”‘They soon started attacking our workers”, he alleged. On May 30, the workers led by Niyogi gheraoed the Assistant Labour Commissioner, the agent of the mines and three of the contractors for 27 hours. They were freed after police intervention. All these officials and the contractors lodged a complaint with the police that they were made to sign an agreement conceding the workers’ demands under duress. On May 31, the workers allegedly attacked the AITUC office and burnt its flag.
On June 1, the Chhatisgarh Shramik Sangh launched a strike, completely successful again. The contractors and the AITUC leaders were desperate. The CPI addressed a press conference at Raipuir urging the authorities to intervene in the ‘explosive situation’. The district administration duly intervened and arrested Niyogi and his associates for making “inflammatory speeches – and inciting the workers”. The arrests led to the massacre of Itajahata. The ^state government has ordered a judicial enquirv into the incident. The enquiry commission is expected to determine whether the firing was warranted or whether it could have been averted by more tactful handling of the situation. Was there really any danger to the lives of the six policemen gheraoed by the workers, as alleged by the authorities? However, the facts speak for themselves. Two among those killed by the police were children. Among the 18 hospitalised persons 15 are workers. And all the 15, including two women, have received bullet injuries. The condition of two of the injured workers is said to be critical. Meanwhile, the workers’ strike continues.
(1)
http://www.mail-archive.com/marxist-leninist-list@lists.econ.utah.edu/msg09000.html
After the Massacre
EPW no.25, 1977
N K Singh
ALTHOUGH the poor workers of the Dalli-Rajahara mines are literally starving as they have not received their wages for the last three weeks, their two-week old strike continues. And so does the curfew, clamped on June 3, when the police firing on agitating workers resulted in the death of ten persons, including a woman and two children, according to official figures. The toll went up to 11 later when one of the 15 wounded workers succumbed to bullet injuries in hospital. The situation in Rajahara is peaceful, says the government. As anyone can find out for himself, this is the peace of the graveyard. The sirens are silent. The heavy machines at the mining site are silent. Many workers have fled to the nearby villages to avoid harassment by the police and their dark and dingy huts, which are an apology for dwellings, are quiet. The deserted roads and markets of the curfew-clamped township are silent. A pall of gloom hangs over this mining colony of some 11,000 workers.
Considerate as the district administration is, it asked a local merchant to arrange for free rations for the starving families. The merchant promptly agreed and later reported full compliance with the request. Pleased with themselves, the authorities praised the merchant for his magnanimity. And of course the matter received wide publicity in the local press. A check with the recipients, however, later revealed that none had been given the full quantity of five kgs each of rice, one kg of pulses, wheat flour, potatoes and onions. In fact, a few workers had received only just one kg each of rice, two potatoes and two onions. No one in Rajahara is prepared to believe the authorities’ claim that only ten workers were killed in the two police firings. “Anyone who received bullet injury was picked up by the police”, said Gaya Ram, vice-president of the militant Chhattisgarh Shramik Sangh, whose office in the mazdoor basti was the starting point of the trouble. According to the Bhopal correspondent of the Times of India who visited the spot a week after the incident, there had been “apparently some random shooting. A bullet hit the cement wall of a tank far away from the scene of the trouble”. Some of the workers said there had been no warning, while others said that they had been given three minutes to ‘clear out’ before firing was resorted to for the second time at noon on June 3. A large number of bodies, the workers allege, were taken away in trucks soon after the second firing. However, as many of the workers have fled to the nearby villages in panic, the actual number of deaths can be assessed only after the curfew is lifted and all the labourers return. The police contention is that they resorted to firing both the times only when the workers held some policemen as hostages and refused to release them and “even tortured them”. The workers maintain that they held some policemen as hostages only after, and not before, the first firing in which four of their men and a woman had been killed.
Gaya Ram recalls the moonlit dark night: “As the strike was continuing, we could not take any rest. That night [June 2-3] we were discussing our struggle, formulating the strategy for the future, at the union office. About four to five hundred workers were camping outside the office .. . When a strike is going on how can anyone go to sleep? At about 2.30 about three dozen police-men led by the district collector arrived in a vehicle and dragged Shanker Guha Niyogi outside the office. We protested. Meanwhile about five thousand people, including women and children assembled. They started throwing stones at the police party. The police burst tear-gas shells. And then, without any warning, they opened fire. When it was all over, we collected our dead and injured as well as the six policemen who were left behind in the melee by their colleagues. They had taken Niyogi away. So we said, first release Niyogi and only then shall we release the six policemen. They did not release Niyogi and so we did not release the policemen. Now they say that we tortured the hostages, that two of them nearly died of thirst as drinking water was refused to them. In fact, the authorities had themselves cut off our water supply to make us surrender. Now tell us, when we ourselves had no water to drink, how could we give it to them? The workers were very angry, of course. Who would not be when their comrades and their womenfolk and children are killed just because they protested against an obviously illegal step of the police? Was not the arrest made to break our strike? And when they opened fire the second time in the noon of June 3, it was sudden, without any warning.”
Out of the total working force of 11,000, about 3,000 departmental labourers employed. by the Bhilai steel plant get Rs 9.80 per day. Under the rules, those hired through the contractors or the labour co-operatives should also receive the same wages. But they are paid only Rs 4.50 per day. And of course they are denied the other facilities available to the departmental workers. “I had never heard of fall-back’ wages till Niyogi told me about it recently”, said a worker working in these mines for the past eight years. The Bhilai steel plant has been patently guilty of doing nothing all these years to remove the causes of squalor and subhuman living conditions of the workers. For instance, the water mains run right through the cluster of hutments, but there is no water available for the workers. There is just one tap through which some water trickles for half-an-hour in the morning and evening for some 4,000 residents. The immediate demand of the workers is for an increase in the pre-monsoon allowance for repair of their huts (from Rs 20 to Rs 100), payment of ‘fall-back’ wages for enforced idleness during the rainy season and bonus comparable to that given to regular mine-workers of the Bhilai steel plant. The bonus had been reduced from Rs 308 to Rs 70 during the Emergency.
Victory for Workers
EPW no.28, 1977
N K Singh
THE martyrdom of the 12 workers of the Dalli-Rajahara iron ore mines killed in police firings on June 2 and 3 has not been in vain. The striking workers of the mines have emerged victorious in their struggle against the contractors, the co-operative tycoons, the top brass of the Bhilai steel plant and the unscrupulous leaders of the ‘recognised’ trade union – whose unholy alliance had thwarted the implementation of the recommendations of the iron ore wage board. The workers’ demands for bonus, fall-back wages and increase in the pre-monsoon allowance for repair of their huts have been conceded. The workers will receive a bonus of Rs 100 each – to be shared equally by the Bhilai steel plant and the contractors – and the hut-repair allowance has been raised from Rs 20 to Rs 100. A committee consisting of, among others, workers’ representatives has been constituted to fix the norms for fall-back wages for enforced idleness at work-sites. What is more significant, however, is that the agreement was reached with the non-recognised union, the Chhattisgarh Mines Shramik Sangh, whose leadership is drawn from the ranks of the workers themselves.
The recognised AITUC union was by-passed by the authorities, in effect conceding the workers’ plea that it had lost its representative character after the formation of the new union. With the settlement and the calling off of the strike, normalcy has been restored and the small industrial town-ship near Bhilai looks peaceful on the surface. But there was tension in the air still when this correspondent visited the area in the last week of June. The workers are particularly agitated over the fact that their leader, Shanker Guha Niyogi, whose arrest had sparked off the trouble, had not been released as yet, though there are no specific charges against him. Workers allege that the administration is using delaying tactics to prevent his release. Although Niyogi has been arrested under section 151, which relates to a relatively minor offence, a bail of Rs 1 lakh has been allegedly demanded. The CPI(M) MP, Ahilya Rangnekar, had visited the area a few days earlier and there was expectation that CITU may use its good offices to get Niyogi released on bail. What shocked this correspondent during his visit to the scene of the firing was the discovery that officials are tampering with and destroying evidence of the brutality of the police. A water tank far away from the scene of the trouble had received bullet marks, as testified by the Times of India’s Bhopal correspondent who had visited the spot a week after the trouble, suggesting the random nature of the shooting that had taken place. However, when this correspondent visited the place he found the walls of the tank all plastered up. It is to be hoped that the judicial commission appointed to probe into the incident will not ignore these pointers. Though the collector and the police superintendent were both transferred in the wake of the institution of the judicial enquiry, they are reportedly on 40 days’ leave and continue to live at Durg, the district headquarters. It is widely feared that they may use their influence to tamper with evidence which goes against the administration.
What marks the Rajahara workers’ agitation is the emergence of a leader-ship from among the workers. All the office-bearers of the Chhattisgarh Mines Shramik Sangh, the newly-formed militant union, belong to the working class. This is in sharp contrast to the other trade unions functioning in the area, whose leadership is provided by professional trade unionists from the middle class. The only person with a middle class background in the new union is Shanker Guha Niyogi, but he has been working as a farm hand and ordinary mazdoor for the last 10 years. There is no dearth of second-rank leadership in the new union. When Niyogi was arrested after the June 2 firing, the workers carried on their struggle successfully till June 17, when the management had to climb down. Ordinary mine-hands participated in the negotiations held with the contractors, the Bhilai steel plant officials and the Labour Department’s representatives and pleaded their case.
Another significant development is the radical role played by women workers in the agitation. A large chunk of the total labour force consists of women, who have occupied their due place in the new union. Quite a few women are in the executive and one of them, Durga Bai, an illiterate worker, has the reputation of being an excellent orator. Women workers braved police bullets as much as their menfolks (one of the workers killed was a woman). Last but not the least, though the majority of workers are illiterate – a few local educated unemployed persons have joined their ranks of late – the level of their consciousness has to be seen to be believed. It is, however, not political consciousness – the ‘Naxalite’ bogey has been raised by the management and government officials to divert attention from the real issue which is the ruthless exploitation of the workers – but class consciousness. The workers have become aware not only of their exploitation and their rights but also of the hypocrisy of their ‘leadership’ and the power of a
united working class.
“We toil all day long, and they [the contractors] have built up empires… While we get bullets in reward for our hard labour, those babus sitting in the Bhilai offices get high salaries and the benefits”, one worker told me in the shanty office of the Chhattisgarh Mines Shramik Sangh in the mazdoor basti which was dripping all over with the first onslaught of the monsoon. Another worker remarked, “it is we who are the real makers of steel. If we stop work there would be no steel”. When I told a worker that Prakash Roy, general secretary of the All-India Khadam Mazdoor Sangh (AITUC), says that it was his union which had been fighting for the workers’ rights for the last two decades and had secured many facilities for them, the worker retorted: “Yes, we know all about that. He has worked so much for us. And that is why he seems to have developed a disease which can be treated only in Russia. Every time he falls ill – and that happens so often – he takes the flight to Russia … He has the gumption to say that he has worked for us! They have worked for no one but themselves. Have you seen their office building in the main market here? [It is a huge building, whose value is estimated at over Rs 1 lakh. All of them arrived penniless in this town, and now they have purchased lands in the nearby villages, move about on motor-cycles. Where has this money come from?"
Both the government officials and the Bhilai management are afraid of the new militancy of the workers. "These same workers used to be so peaceful", said a high police official who has been camping at Rajahara since the firing. Manoharlal Jain, a contractor of the Rajahara mines and the treasurer of the Durg District Congress Committee, echoed him and lamented, "hardly a few months back the workers here were such an obedient lot that we used to raise our hands like this [precious stones set in half-a-dozen gold rings glitter in the air as the pot-bellied businessman raises his hands in a gesture of mock-offence] and the workers would flee from the spot. But this time … this time, we just could not believe it: their fellow-workers were dead, bodies were lying all over the place, but it looked as if they had lost all sense of fear. Instead of fleeing from the spot and taking shelter they fought ding-dong battles with the police.” The wealthy contractor confided to me, “they are not the same old workers. They have lost regard for the sanctity of the malik-mazdoor relationship”. “You know”, he whispered, “now they even say that it is we [workers] who labour and the contractors enjoy the fruits of our labour … Have you ever heard of any such thing?” The contractors are worried over this transformation and they blame Shanker Guha Niyogi for it.
But what about the old times, and the old union? “They were good chaps. AITUC used to raise only reasonable demands. They respected the rules, procedures and labour laws”, said Manoharlal Jain. In fact, the contractors and the representatives of the management whom I met were all ga-ga over the role of the old union. A spokesman of the Dalli-Rajahara Mines and Transporters, a private firm owned by Anupchand Jain, a big-wig of the area, told me that it was wrong on the part of the labour department to have by-passed the AITUC union in arriving at the agreement with the workers. “They were a responsible lot.” Most of the contractors asked me, “have you met Prakash Roy and other AITUC leaders? You must meet them”. A visit to both Prakash Roy and his union colleagues at Rajahara proved rewarding. Photographs of Lenin and Rabindranath Tagore hang side by side in Prakash Roy’s modest house in a lower middle class locality of Rainandgaon. He admitted that most of the workers have joined the new union, but contended that “they were forced to do so: coercion was used”. I gently pointed out that may be the workers deserted his union because it was not active enough to protect their interests. This provoked the ageing, veteran trade union leader, “What else we could do? It is obligatory for the recognised union to negotiate with the management. We can take to agitation only when the negotiations fail. This is the pre-condition of the recognised union.”
Roy’s comrades at Rajahara echoed him. “We follow the Industrial Disputes Act … We have also gone on illegal strikes, but never for more than one day. And these people – they are totally irresponsible. Ever since the new union was formed, there has been a spate of wild-cat strikes, gheraos, intimidation of loyal [sic!] workers and what not.” There is an INTUC union also working in the field, though its membership is limited to the co-operative societies that the union is running. The co-operative societies running the mines have a reputation of being as ruthless in their exploitation of the workers as the contractors. A spokesman of the INTUC union told me, “the leadership of the workers has gone into wrong hands. Shanker Guha Niyogi does not want to run the Chhattisgarh Mines Shramik Sangh on established trade union lines”. The contractors agree. A memorandum prepared by them urges that the problem can be solved only by a “change in the leadership. A stronger, dedicated leadership is required”. But dedicated to whom?
Trade Unionism with a Difference
EPW no.29, 1977
N K Singh
SHANKER GUHA NIYOGI, leader of the ‘Naxalite’ union of Dalli-Rajahara mine workers, has alleged that the police tried to kill him after his arrest in the night of June 2-3. Niyogi – whose midnight arrest had led to police firings in which 12 workers were killed – has alleged that while being taken to the jail at the subdivisional headquarter of Balod, a police official accompanying him stopped the jeep in a jungle and told him, “if you want to escape, you may just slip away: only assure us that you would never again step into this area”. Niyogi says that he was not taken in by “the police trick”. “I know all about encounters and the killed-while-escaping stuff.” Obviously, Niyogi is a dangerous man for the contractors and the authorities. That is perhaps why he has not been released even a month after his arrest, although the ‘offence’ is a bailable one, under section 151 of the IPC. An impossible bail of Rs 1 lakh has been demanded and, of course, the poor workers of Dalli-Rajahara simply cannot manage it. Although at the time of his arrest it was given out that Niyogi had been arrested for “making inflammatory speeches and inciting the workers”, the officials have now discovered that “had we not arrested that man, they could have burnt the entire town the next day”. “We have definite information”, a high police official, who did not want to be named “in view of the judicial enquiry”, confided to me by way of justifying Niyogi’s apparently unjustified arrest.
In fact, the authorities, the contractors, and the CPI have painted such a picture of ‘Naxalite’ violence engulfing the whole area that, while entering the mazdoor basti at Rajahara, this correspondent had almost expected to be accosted by gun-toting guerillas. Instead, he was greeted by a stray dog, some sick workers, and the closed doors of the hut housing the ‘Naxalite’ union. All the workers had left for work, including those whose dear ones had died in the police firing. Mourning is a luxury which the workers cannot afford. After a long wait by me, the union leaders arrived. Exhausted with my encounter with simple workers, who did not know the difference between the prime minister and the chief minister, I tried to strike up a dialogue with the union leaders in Marxist jargon, but drew a blank. There were also no photographs of Mao or Naxalite slogans within miles of the union office. Shanker Guha Niyogi has become a household name in this industrial area of Chhattisgarh. Every one talks about him – many with reverence and af-
fection, and some with hatred and fear. But they all – contractors, police, administration, trade union leaders, and the people of Rajahara – seem to agree on two points: Niyogi is the undisputed leader of about 8,000 workers of Rajahara; and his honesty, integrity and dedication is beyond question. “You can buy every one of these trade union leaders here, but not Niyogi”, a police official told this correspondent at Rajahara. “Niyogi is made of different stuff”, agreed a contractor. “The new union was formed with the backing of the contractors to break the unity of the workers”, alleged an AITUC leader. “Do you mean to say that Niyogi was the contractors’ man?” “No, no, not Niyogi”, the trade unionist hastily added, “It is the other leaders of that union who are dishonest.” Onkar Jaiswal, a local journalist said, “I know all the union leaders of this town, but I had never noticed Niyogi’s presence till May 31, when he led a huge procession of workers to celebrate the acceptance of their demands after a 27-hour gherao of the contractors and the officials. It was the biggest procession in the history of Rajahara.”
Shanker Guha Niyogi denies that he is a ‘Naxalite’. “I have no connection with the CPI(ML) or any of the Naxalite groups. In fact, I violently disagree with them on the issue of trade unions”, said Niyogi in the first interview given by him to a newsman after his arrest. Tall, lean and darkish, the 28-year-old Niyogi, clad in a pair of not-very-clean white pajamas and shirt, was at first a little reluctant to talk – after all, I could well have been an intelligence man – and what he said was mostly about the exploitation of the workers and the complicity of the CPI union. But, gradually, he began to talk about his work among the working class and peasantry during the last one decade. His mission, Niyogi said, was to educate the working class and make them conscious of their rights. “Once they are conscious, nothing can stop them.” “Why talk about me? I am immaterial. A new wave of awareness is sweeping through the people. If I had not gone to Rajahara, they would have got some other leader.” Niyogi comes from a lower middle class family of West Bengal. He came to Durg, where his uncle lived at the time, in the early sixties for studies. Since then, he has identified himself with Chhattisgarh. Though there is a trace of the Bengali accent in his speech, he fluently speaks Hindi and Chhattisgarhi, the local dialect.
Owing to poverty, Niyogi completed his B Sc with difficulty, doing various odd jobs to maintain himself. As a student, he was actively associated with the student movements. He was the joint secretary of the student wing of the CPI. After his graduation, Niyogi plunged into revolutionary politics in 1966-67, the year of ‘spring thunder’ over India. He left the CPI(M) to join the newly-formed Co-ordination Committee of Communist Revolutionaries. However, later he severed his connections with this splinter group of the CPI(M) too, unhappy with its stand on trade unionism – “they dubbed it as economism”. As a worker of the Bhilai steel plant, Niyogi helped organise the first militant trade union there – the blast furnace action committee. Soon, he was sacked from the plant on “security grounds”. His first arrest took place in 1968, when he started publishing a radical Hindi weekly from Jagdalpur, the heart of the adivasi belt. “Since then I have been arrested more than 20 times.” He has spent about five years in jail altogether, the longest term being 13 months during the Emergency.
Niyogi organised the workers of the Dai Tola mines, near Rajahara. He worked there as a daily, labourer, breaking stones in the quarry. “How can the workers treat you as their man, if you do not live as a worker, merge yourself with them, identify with their hopes and aspirations?” Niyogi also married a Chhattisgarhi mazdoor girl, Asha, working in the quarry. “She still works there.” At Dai Tola, as elsewhere in the area – “I know only about Chhattisgarh. I’ve worked in this region” the problem was the same. There was no honest trade union to protect the interests of the workers. Both the AITUC and the INTUC unions had become stooges of the management. They served the interests of the exploiter rather than the exploited. Niyogi first joined the AITUC union “all the workers were in their grip” and then, through dedicated work and persuasion, organised the workers under a new union. “It was not a difficult task. I was one among them, while the other leaders were outsiders, babu sahibs.” The contractors got worried over this new threat to their prosperity, and Niyogi was consequently arrested several times. Niyogi also tried to build up a peasant movement. He worked as a farm hand in Keri Jungata, a nearby village, and organised the agricultural labourers and landless peasants. “There is basically no difference between the peasants and the workers in the area. Both came from the same families. If the elder brother works in the farms, the younger one goes to the mines. If the father is a peasant, his son works as a miner to augment the family income.”
After the declaration of Emergency, there was a warrant of arrest under MISA for Niyogi. He managed to evade arrest for six months, but was then arrested and was released only at the time of the Lok Sabha election. Meanwhile, the workers of Dalli-Rajahara mines, dissatisfied with the agreement on bonus signed by their recognised trade union had started a spontaneous strike. The strike was also the product of grievances bottled up during the Emergency. The contractors and the trade union leaders thought that the disorganised movement would soon fizzle out. And so it did. On March 23, the workers ended their 19-day strike and signed an agreement for a bonus advance of Rs 50 as against Rs 70 earlier negotiated by the AITUC and the INTUC. Niyogi alleged that the workers were terrorised by the then Collector of Durg – now transferred after the institution of the judicial enquiry to sign this agreement. “He is known for his strong-armed tactics. Do you know, Durg ranked first in the country for the largest number of family planning operations performed? You can just imagine what he was like.”
Things changed radically when Niyogi was released and arrived on the scene. He organised the spontaneous movement of workers into a well-knit union. The contractors, who were initially happy at the recognised union losing its hold over the workers and the split among the workers, got seriously worried when almost all the 8,000 contract labourers joined the new union en bloc. The reason, Niyogi felt, was the same as in Dal Tola. The babu trade unionists had suddenly come into wealth. “What will illustrate the point better than the fact that many union men, like Jivan Mukherjee and Naseem, have left the party (CPI) to join the services of the contractors? The margin is so thin! The workers were becoming aware of this trend – the collusion of their ‘leaders’ with the management.” Niyogi maintains that he was arrested in order to break the morale of the workers, who were on strike at the time. He dismissed the allegation that the second firing in the noon of June 3 had become necessary because there was danger to the lives of the policemen held hostage by the workers. “Had they wanted to kill the policemen, they could have done it in the night, when five of their colleagues had already been killed in the firing.” The police were in a vindictive mood, enraged by the stone throwing of the workers. “All the injured workers have received bullet injuries – and that, too, above the waist.”
The Struggle Continues
EPW no.30, 1977
N K Singh
ON July 9 the pits of Dalli-Rajahara iron ore mines did not work because over 10,000 workers did not turn up. But they were not on strike; they had abstained from work because their leader, Shanker Guha Niyogi, had been released after 35-days’ illegal detention on the orders of the Durg sessions court and they wanted to accord him a heroic welcome. The acceptance of their immediate demands after a 19-day long successful strike which continued even after the police firing and large-scale arrests – an obvious attempt to break the strike – and the release of Niyogi has boosted the morale of the workers. Niyogi, whose arrest on June 2 last was followed by indiscrimninate police firing resulting the death of a dozen striking workers, had been ordered by the subdivisional magistrate of Balod to deposit a personal bond of Rs 25,000 with two sureties of like amount. Niyogi, a poor worker, was unable to manage this heavy bail of Rs 75,000. His lawyers, two CPI(M) sympathisers of Durg, challenged this order in the sessions court of Durg. On July 8, the sessions judge of Durg quashed the order of the subdivisional magistrate which was held “illegal and without jurisdiction”; the judge specifically held that the detention of Niyogi from June 3 to June 6 on the orders of the additional district magistrate was illegal.
Niyogi was initially arrested on June 2 under section 151 Cr PC and produced before the additional district magistrate of Durg who had remanded him to judicial custody till June 17. Meanwhile the subdivisional magistrate of Balod initiated proceedings under section 107 Cr P C on June 6. The case was again transferred to the additional district magistrate on June 13. On July 6, as soon as the section 144 imposed upon the township elapsed, over 10,000 workers brought out a procession to protest against police repression and in support of their demand for unconditional release of Niyogi, end of contract system in the mines and early implementation of the fallback wages envisaged by the wage board. The problem of fallback wages, denial of which means a saving of at least Rs 10 lakhs per year to the contractors and co-operative tycoons, has been hanging fire for the last several years. During the latest tripartite agreement between the workers, Bhilai steel plant, the master employer, and the contractors, the matter was referred to a committee to fix the norms of fallback wages. But if the past experience is any indication, it may take several more years before the contractors relent.
Before the formation of the new union, fallback wages for enforced idleness had never been an issue. The established unions, AITUC and INTUC, avoided the issue by saying that it was very difficult to fix the norms for wages for ‘not working’. The contractors as well as the Bhilai steel plant management were firm in their opinion that once fallback wages were enforced, workers would avoid work, for “who would like to work when one can get wages without working”. The real problem lies elsewhere. For instance, between May 27 and May 30 the contractors denied work to 669 persons on their regular roll as ‘blast’ had not taken place or because there was shortage of vehicles for loading and unloading operations. Such instances are not uncommon and fallback wages envisage payment of 80 per cent of the normal wages for such enforced idleness.
The management of the Bhilai steel plant has also its share of responsibility for the present labour unrest. Though the Bhilai steel plant is the master employer, the management has never cared for the labourers employed by the contractors and the co-operative society. For instance, over Rs 3 crores – half of which is contract workers’ share have accumulated in the welfare cess fund. However, although the departmental workers have been provided w[th quarters, the contract labourers have not received similar welfare benefits. The workers' money is lying idle, while they live in sub-human conditions. More recently, it was the Bhilai steel plant's decision to pay plant performance bonus to its departmental workers which sparked off the trouble. The contractual workers did not get their bonus. Unable to distinguish between the 'plant performance bonus' and 'bonus' - the regular Bhilai workers had not also received any bonus - they were angry that while they were engaged in the same work as the departmental workers, they were denied the facility given to the latter.
The contract system, continuing despite the seven-year-old Contract Labour (Regulation and Abolition) Act, seems to be at the root of all the trouble. Though a committee appointed by the steel ministry had unanimously recommended in December 1976, after two years' extensive study of the problem, immediate abolition of contract labour in all the mines except at the loading sites of the railways, the system still continues. One reason for not abolishing it may be that it is very cheap; the cost of mining iron ore in the manual mines run by the, contractors is about Rs 30 per tonne while the mechanised mining by the Bhilai Steel Limited costs around Rs 50 per tonne. Another reason could be 'the vested
interest developed by a section of Bhilai steel plant management in the contract system. Officials get their 'cuts'. And it is interesting to learn that the manager of Bhilai Steel Plant is a Jain belonging to Rajnandgaon. This piece of information becomes significant in view of the fact that the majority of contractors too are Jains belonging to the same place. And so the struggle continues.
Shanker Guha Niyogi gave assurance of that while addressing a press conference at Raipur after his release from jail. Niyogi, who said that he and other union leaders had been threatened with dire consequences for opposing the contractors, has demanded a re-election in the Balod and Gunderdehi assembly constituencies from where two-office-bearers of the Chhattisgarh Mines Shramik Sangh had contested' during last month's assembly election. Supporters of the two contestants were arrested while canvassing and the candidates had to go underground due to police terror. The Election Commission had been informed of these facts. Niyogi has also alleged that there was a conspiracy behind the firing. The contractors, police officials and leaders of the 'recognised' union had held a meeting for about two hours in a bar-cum-restaurant of the township in the evening of June 2. According to Niyogi, the police had made a special target of Anusuya, a 30-year-old activist and inspiring folk-singer of his union. The police bullet hit her right on the chest. "They aimed at her straight." The most nauseating aspect of the whole affair is the role of the CPI. Like many Congressmen, the CPI is now shedding crocodile tears; but it was CPI activists who had instigated the police to "take action against the Naxalite menance". In fact, on May 31 an AITUC procession of about 1,000 persons, mostly consisting of the departmental workers, had gheraoed the Rajahara police station to press its demand for the arrest of Niyogi.
* Massacre of Kanpur Workers - Government's Lies Nailed
EPW 1978, No.9
Nikhil Chakravartty, A. K. Roy and Satish Saberwal
The tragic events in Swadeshi Cotton Mills in Kanpur on December 6, 1977 attracted nation-wide attention. Though even according to the government's version 11 workers had been killed and 43 injured in the police firing, the government refused to order a judicial enquiry. In the circumstances, the Citizens' Committee for Enquiry into the Kanpur Massacre constituted a three-member group (...) to undertake an on-the-spot investigation into the incident. The report prepared by the group after its investigations exposes many lies in the government's version of the police firing on the workers of the Swadeshi Cotton Mills. Most important of all, the group's findings established that, contrary to the government's claim, the police firing did not start after the two officers of the mill, who had been gheraoed by the workers, had lost their lives, it started earlier when the Superintendent of the Police had been hit by some hard substance dropped from the roof of one of the buildings in the mill compound. This gives the lie to the official propaganda that the police had been forced to open fire because the workers had murdered the two officers. The full text of the group's report is printed below.
We visited Kanpur on February 7-9, 1978 for an on-the-spot investigation about what really happened on December 6, 1977 when a number of lives were lost following police firing within the precints of Swadeshi Cotton Mills in the city.
In the course of our investigation we had the opportunity of meeting a large number of persons including the District Magistrate and other government officials, some of the officers of management of the mill, as also a large number of workers. The cooperation, which we received from different sources helped us to get a clear picture of the happenings that led to the tragic loss of lives in the Swadeshi Cotton Mills on December 6.
The Swadeshi Cotton Mills Ltd. Controlled by the House of Jaipurias, has been passing through a period of crisis, according to the management. Originally the Swadeshi Cotton Mills was started in 1911 by Sir henry Horseman. He sold it in 1946 for Rs 2.10 crores to Mungtu Ram Jaipuria who happened to be his trading agent in Calcutta. It was claimed to be the biggest mill in North India having a labour force of over eight thousand.
This turned out to be such a profitable concern that, over the years, the Jaipurias were able to acquire or establish five textile mills in other parts of the country - at Pondicherry, Udaipur in Rajasthan and in UP at Naini, Maunath Bhanjan and finally at Rae Bareli (Initially a synthetic fibres millwas to be established at Rae Bareli, but the license for this was transferred to Ghaziabad.) The Rae Bareli unit of the Swadeshi Cotton Mills was set up for what the management euphemistically calls "political considerations" - - in other words, to placate former Prime Minister Indira Gandhi, whose constituency happened to be in Rae Bareli. In fact, quite considerable amount of machinery for the Rae Bareli unit was sent there from the Kanpur unit of Swadeshi Cotton Mills.
From this it is evident that the Swadeshi Cotton Mills, Kanpur, was for a long time fetching considerable profits for its owners so that they could set up five more profitable textile units apart from promoting the Swadeshi Polytex Ltd. In which it owns today 30 per cent of the shares with its block of one lakh shares originally priced Rs 10 each.
The trouble with the Swadeshi Cotton Mills started when the two brothers, Sita Ram and Raja Ram - the former adopted and the latter the real son of old Mungtu Ram - fell out. In November 1975 Raja Ram displaced Sita Ram as the Managing Director of the Swadeshi Cotton Mills while Sita Ram took over as the Managing Director of the profit-making Swadeshi Polytex Ltd. By March 1975, the company on paper showed loss. Meanwhile from 1974 onwards the management at Kanpur was found to be repeatedly defaulting in the matter of paying the workers' wages while at the same time it was not clearing its dues to the government. It has also eaten up the Provident Fund of the workers to the tune of over Rs 25 lakhs and the Employees' State Insurance accumulation to the extent of Rs 20 lakhs, both cognizable offence under law but the government did not bother to prosecute them.
From 1974, the workers of this mill had to resort to gherao to get their legitimate wages. This became regular practice from 1975. The state government, under Chief Ministership of N D Tiwari, arranged for the company a loan of Rs 1.50 crores in March 1976 from Punjab National Bank, underwriting the guarantee for it. But within a few months the company again started defaulting in the payment of wages. There are strong grounds for the presumption that this persistent defaulting arises from a sustained effort by the Swadeshi management to drain the company of its resources, possibly into unaccounted channels.
Why is the management creating this crisis? From all the circles we met in Kanpur - the management, the government and the workers - we formed the definite conclusion that the management is bent on pressurising the government to allow it to sell the Swadeshi Polytex shares at an inflated price; in addition, it seeks also to convert half of its capacity from cotton textile into synthetic textile in order to go in for large-scale profiteering.
The situation went from bad to worse last year and several gheraos had to be resorted to by the workers to secure their long-standing dues. In September 1977, the workers gheraoed the son and the son-in-law of one of the officers of the mill and only then the management could be forced to come out with a written assurance that they would disburse the wages long due by October 10. But nothing was done. The workers held a number of peaceful demonstrations including one before the luxuriously appointed Swadeshi House in the affluent part of the city. Meetings at the mill-gate followed in the next few days. Even the clerks of the establishment went on a strike on October 24.
On October 26, 1977, the workers gheraoed the Secretary of the mill, K P Agarwal, for a stretch of 54 hours. It may be noted here that the workers organised the gherao in such a way that production was not interrupted: those who were outside the shift took over, by turn, the task of keeping up the gherao. Agarwal was gheraod in anopen space near the cooling tank inside the mill. The next day the District Magistrate intervened and the state government hurriedly appointed a Receiver and at the same time arranged a loan of Rs 13.50 lakhs for immediate disbursement of the workers' wages which partly met the huge arrears due to them. During this gherao there was no question of the workers threatening the life of the gheraoed officer. Rather they even helped to instal a temporary telephone connection for the gheraoed officer so that he could speak to the mill authorities. At the end, when actually the cash was brought for immediate disbursement, the workers not only released but garlanded the gheraoed officer. So there was no question of menacing violence on the part of the workers.
The appointment of the Receiver naturally created a sense of expectation on the part of the workers and they rightly hoped that from now on they would be getting back not only their dues but also their wages regularly which were paid in fortnightly instalments. (...) [The Receiver] He was expected to supervise the sales of the products and to ensure the recovery of government dues “after the payment of labour dues and other essential items of the running of the mills”. What was interesting was that the Receiver was appointed “over the mills at Kanpur” and not over the company of the name of Swadeshi Cotton Mills Ltd. In other words, The Receiver was expected to oversee the financial position of only the Kanpur unit of Swadeshi Cotton Mills and had no jurisdiction over the other five thriving mills of the same Company located in different parts of the country. (…)
Towards the end of November it was clear from the testimony of the workers that they had the feeling that the Receiver was soon going to arrange for the payment of the dues by some means or other. But nothing of the sort happened. Even the officers began to disappear from the mill premises. The situation became desperate indeed for the workers whose wages for nearly two months were now overdue.
On the fateful December 6, two officers came to the mill premises on some other work: Iyenger, the Production Manager, and Sharma, the Accounts Officer were gheraoed by the workers roundabout 2 pm. It is to be noted here that on that day and for a few days preceeding there was power break-down in the mill due to a failure at the power station of Kanpur Electric Supply Authority. Most of the workers coming on shift duty were only signing for work were laid off. Only a few departments were functioning through the power supplied by the mill’s own generator.
The two mill officers were gheraoed exactly in the same way as it happened in the case of Agarwal on October 26. They were taken on the very same spot where Agarwal was confined in the open space in one of the yards near the cooling tank within the mill premises. Two police officers were also seen to be sitting near them and there was no sign of any menacing commotion.
From the evidence at our disposal it is clear that a large force of police turned up under the command of Superintendent of Police, Rai, somewhere after 3.30 pm, that is less than two hours of the start of the gherao. It may be noted here that no such force had been seen at such a short notice on October 26. The District Magistrate was on tour on December 6 and instead the Additional District Magistrate turned up, a man who is known to be very friendly to the Jaipurias.
From the evidence collected by us, it appears that the police started its operation first outside the mill premises on the main road and the lanes leading to the main road. There are reports of firing having begun in this area and we examined a number of spots inside the lanes in the crowded bustees opposite the mill gate – even bullet marks at a distance of more than 300 metres from the main road on which the mill stands. We also examined some people who were wounded by the police firing in this part of the town.
Meanwhile the police under the Superintendent of Police began to force its way within the mill compound. According to the version we got from the police, the SP as he was leading his force was wounded on the head by a hard substance (which might have been a brickbar or a piece of iron) dropped from the roof top adjoining one of the buildings within the mill compound. Since he was wounded the police which before that had tried teargas, began shooting.
The firing, according to the police, went on for twenty to twenty-five minutes. All other evidences, however, indicate that the firing lasted for nearly two hours. The police force not only went on charging while shooting but they climbed on the roof of one of the buildings from where they started firing indiscriminately on the workers. Rifles and muskets were both used liberally in this operation. With such large-scale firing most of the workers tried to escape from the backdoor, climbed over the wall at the rear of the factory, or tried to hide in the worksheds; and in course of it some of them broke their limbs also. We examined some of these workers including those who were wounded.
Meanwhile the workers who were still working in some of the departments which had power supply, did not realise that they would have to face the police attack. They were not participating in the gherao at all but they were forced by the police at bayonet point to come down and they were forced to run through two lines of armed policemen in course of which many of them had to suffer severe wounds. This was a totally unprovoked and calculatedly terror operation because these workers had nothing to do with the gherao.
The police rounded up nearly a thousand workers, those they could lay their hands on. Some of these were forced to load the wounded and the dead on the police trucks. After that the police left out the aged and put as many as 231 workers under arrest and sent them to the police lockup in different police stations in the city where in some cases they were beaten up and sent to prison next day.
As for the wounded who were taken to the hospital, most of them had to pay for their treatment and most of the wounded also were taken to prison as soon as they were discharged from hospitals.
What happened to the two gheraoed officers Lyenger and Sharma? A propaganda has been sedulously built up that the police shooting on the workers had to be resorted to because the workers had murdered the two officers. It is clear as daylight from the version we have heard from the authorities themselves that the police firing began when Superintendent of Police was wounded; there is not a shred of evidence of the two gheraoed mill officers having already been killed. The evidence that we have collected points to the fact that as soon as the indiscriminate firing was resorted to, the workers who were gheraoing the two officers ran away; and when these two were last seen they were standing under the portio leading to the building in which later on the police claimed that they found their battered corpses. The staircase leading to the room where the officers were found dead is such that nobody could be dragged through it. This leads to the reasonable inference that the two officers went up on their own for safety from police firing. (…)
In this context, it is worth noting that when the application was moved in court for the release on bail of the arrested workers who numbered over 230, the police at the beginning could not produce the FIR. (…) Most of the workers were released on bail only towards the end of January and the first week of February. We are informed that some of the workers are still in prison.
There is a wide margin of dispute over the casualty figures. The Government figure is that 11 workers were killed in police firing and 43 wounded and hospitalised. Many of the workers whom we examined claimed that a larger number were killed and some even said that they were forced to load the trucks with corpses which if counted would amount to a very large number. However, this requires further examination. What is clear is that the figure of killed in police firing must be more than 11. From the evidence that we collected in course of sixty hours, we could locate two cases in which the workers had not returned home nor could they be found in the hospitals nor in prison nor had gone back to their village homes. The obvious presumption is that they were killed in police firing. These two were Horilal, son of Mangali, living at the village of Macharia, PO Nauvasta (ESI No 237766; PF No UP 12/16367) and Gangaram, son of Narottam, living at 127/126 Juhi Bombaralaya. Both these names do not figure in the official list of the dead.
A lock-out had been declared at the mill since December 6. On January 7, 1978, the Company after getting a further loan of Rs 37.5 lakhs from the government cleared some of the arrears of wages to the workers. (…) Many of the workers, however, had left for their villages. From the side of the mill management we came to know that 267 workers had not turned up to take their wage dues. It is possible that these 267 had not got the information about disbursement of wages on that day. It is equally plausible that among these 267 missing, there might be a number of dead workers killed in the police firing. (…) During our on-the-spot investigation covering extensive talks with a very large number of workers, including trade union cadres of different affiliations, we could not help but realising that there has come about an erosion in the credibility of the trade union movement in Kanpur in the eyes of the working population, particularly at the Swadeshi Cotton where the trade union leadership proved to be ineffective in organising the workers’ struggle for securing the very basic demand of the workers, for their wages. (…)
* Police Massacre in Faridabad – Report of a Fact Finding Team
EPW, 1979, No.44
In one of the worst orgies of violence in recent times, Haryana police ran berserk and killed innocent people in Faridabad on October 17 and were engaged in concealing and destroying all evidence of their misdeeds, and in misleading the Press as to the actual nature of the incidents on that day. This is the finding of a three-member Fact Finding Team sponsored by the People’s Union of Civil Liberties and Democratic Rights, Delhi- Branch, which toured Faridabad on October 24, met victims of the police firing, visited the spots where the firing took place and talked to relations of those killed by the police and discovered that even though a week had passed since the incidents, the police were still persecuting innocent people. Contrary to what the police want to be believed, the Team found from its talks with those who had witnessed the police firing at Neelam Chowk’ on October 17, when a strike call had been given by different trade union organisations, that the provocation had come first from the police when Sub-Inspector Brahm Dutt opened fire on an unarmed demonstration of workers which reached Neelam Chowk. The Sub-Inspector had earlier given his policemen orders for a lathi charge to disperse the crowd which was not aware of the imposition of Section 144, promulgated by the police at 2 am on that day. No public announcement had been made. While some workers were engaged in an argument with the police, Brahm Dutt fired, killing one of the demonstrators on the spot. When the dead man’s comrades tried to lift the body, he fired again killing two more people. This enraged the crowd, who were reported to have pounced upon Brahm Dutt, who later succumbed to injuries inflicted by the mob.
The total indifference of the police and local administration towards basic human rights was described by the employees of a hotel at the Neelam Chowk, the epicentre of the incidents, in a statement made to the Fact Finding Team: When the trouble started, some policemen took up vantage positions above the building where the lime shop at Neelam Chowk is situated and started firing on the crowd in the streets. The policemen on the road started beating the people, including school children … The panic-stricken people moved to the railway bridge between Neelam Chowk and Mathura Road. Meanwhile a group of CRP men reached the Mathura side of the bridge to trap the crowd on the bridge between the two police forces. The police from both sides started attacking the crowd with gun shots. Many people jumped from the bridge down to a depth of between 25 and 40 feet. The policemen forced those who were dangling from the bridge to jump down by beating them on their knuckles. Also, some were physically lifted and thrown down from the bridge by the policemen. From the eye-witness reports that the Team heard from several sources, the lack of a properly organised labour force in Faridabad was evident. Those who were present at Neelam Chowk on the day of the incident reported that not a single leader of any union or political party was to be seen there before and after the incidents. This was corroborated by the CITU men whom the Team contacted at their office. Though various Haryana ministers have charged the CITU as having been responsible for the violence and disturbances, the CITU men appeared unaware of the number of dead, injured and missing and were generally ill-informed about the incidents of the17th.
On the other hand, police preparedness much before the trouble started was crystal clear. On the early morning of the bandh, Cr P C 144 was declared at 2 a m. According to the shopkeepers at Neelam Chowk, they were forced to close their’ shops and keep indoors by the policemen much before the trouble started. “The policemen themselves were preparing for a show-down” was how one shop-employee put it to the Team. Evidence suggests that after the death of the police officer, Brahm Dutt, the gun-carrying police force ran amuck, intent upon taking revenge. One engineer working in West Germany who is on a short leave to meet his relatives, told the Team that he saw a policeman stopping two young school children on their bicycles, returning from their school, unaware of the happenings. The school children were beaten mercilessly, although this was five hours after the morning incidents. Everyone in Neelam Chowk corroborated that the worst type of police raj prevailed in the whole area following the morning incidents. Policemen entered even shops and residences to beat up uninvolved and innocent people. One hotel employee showed the Team his right hand shoulder, which was difficult to move due to lathi-blows. He had been pounced upon by policemen while he was cooking inside the kitchen. Though the police and administration claim that no firing took place after 1 p m on the 17th, the gruesome incidents in the residential areas of Press Colony and Punjabi Colony speak otherwise.
The police did not stop at indiscriminately beating up and firing upon people who had either gathered in the demonstration or were watching as innocent by-standers at Neelam Chowk. They extended the range of their atrocities to areas far away from the scene of the demonstration, and to people who had nothing to do with the striking workers. The Team went to Punjabi Colony, 4 to 5 kms away from Neelam Chowk, and visited a house on the roof of which two of its residents, Kashmiri Lal Bali aged 42 and Jagdish Prasad aged 28, had been killed at point blank range by the police who had taken up positions at the landing of a stair-case of a house opposite the roof-top. Bali’s 12 year old son, Anil, who was shot in the abdomen, was still lying unconscious at the Safdarjung Hospital. Another boy, 16-year old Surendra Kumar, who was also standing on the roof-top was injured in the head and back by bullet splinters.
The story of Bali’s killing, as narrated to the Team by his brother-in-law and other relatives who were eye-witnesses to the incident, is pathetic. Bali was a printer at the Government of India Press. After his office closed at 4.30 pm, he came home and was told by his wife that -his eldest son Anil was playing on the roof. Asking his wife to prepare food, he went up-stairs to bring his son down. As he reached the roof, a bullet hit his head from across the road. Seeing him fall, Jagdish Prasad, who was staying in a room on the same terrace, came out to help him, but a bullet hit him in the waist and pierced his abdomen. He died in hospital. Bali’s son Anil was hit next, while the other boy Surendra Kumar, also a resident in the same neighbourhood, was injured by splinters from the bullet that had pierced Jagdish Prasad. This was a case of cold-blooded murder, as neither Bali nor Jagdish Prasad nor the two children were involved in strikes or demnonstrations on that day. That the police were keen on hiding all evidence of this murder was obvious from several facts. First, soon after the killing a police party came to Bali’s house and wanted to snatch away Bali’s dead body from his relatives. After they failed to take it away, a larger police party came headed by the DSP and forced the relatives to part with the body. But in the meantime, Bali’s relatives had managed to get a photographer to take pictures of Bali’s dead body and the scene of the killing.
Bali’s brother-in-law insisted on an inquiry into the killing, but the DSP said that the postmortem on the body would have to take place at Gurgaon on the orders of higher authorities. Bali’s brother-in-law then went to the Circuit House, where a meeting was in progress between a Haryana cabinet minister Khurshid Ahmed, high police officials and industrialists. When after an hour, the minister came out, the brother-in-law requested him to allow him to take Bali’s body and perform the last rites and cremate him. But both the minister and the industrialists who were present there rejected his request on the plea that “if the body was allowed to be cremated at Faridabad, it will further worsen industrial relations”. Finally, Bali’s relatives were allowed to accompany the dead body in a police van to the cremation ground at Gurgaon.
At the Gurgaon cremation ground, Bali’s relatives found that at least six more dead bodies were lying there to be cremated. The burning ghat people told them that the bodies had been brought by the police from Faridabad and were being secretly burnt there. They remained- unidentified. Bali’s brother-in-law told the Team that the same fate would have befallen Bali, had not his relatives insisted on getting back his body. The body of Jagdish Prasad was not handed over to his relatives after his death in hospital and no one still knew what happened to it. When relatives of the other dead people contacted the doctor at the Gurgaon Civil Hospital for post-mortem reports, he pleaded helplessness because of “limitations”. The relatives were in a state of utter desperation and helplessness. No one, including any political or trade union leader, had come to their rescue.
The story does not end here. On October 22, four days after Bali’s murder, a police party headed by an ASI visited the spot. Before killing Bali, the policemen who had aimed at him from the opposite house, had missed their target and one of the bullets had got lodged in the outer wall of the neighbouring house. To destroy this evidence, the police party which came on the 22nd climbed up the wall and with bayonets dislodged the bullet from inside the wall. The Team saw the original hole made by the bullet, further enlarged into a wide gap by the police team. The local people told the Team that the police were still on the prowl in the area to recover the cartridges of the bullets fired by them in the area on that day, so that they were not later produced by the residents to prove the misdeeds of the police. The police had also come to know of the photographs taken of Bali’s dead body. The photographer was being constantly harassed by the police. He told the Team that a senior police official had threatened him and even offered bribes to get back the film roll from him.
Thus, it was evident that the police were busy hiding and destroying all traces of their murderous activities of October 17. Plainclothesmen were prowling all over Faridabad, arresting people whom they suspected of giving out the real story. Reporters had not been allowed to enter the Badshah Khan Hospital where those injured on that day were being treated. The members of the Team managed to smuggle themselves into the male ward, and saw at least six persons with bullet injuries. They were shocked to see four of them – all with their hands or legs in plaster, and in no condition to move – chained to their beds in a separate corner of the ward and being guarded by armed police-men who were occupying some of the beds meant for patients. One of the injured was a post and telegraphs employee, who on the day of the firing was on duty on the bridge leading to Neelam Chowk. Hira Lal, Devi Lal, Jagdish K Pande and Tilak Kapoor (who is deaf and dumb) with bullet injuries on their bodies and chained to their beds, were workers who had been trapped in Neelam Chowk and shot at by the police. As they could not flee due to their injuries, the police arrested them and were planning to produce them as miscreants who had provoked the October 17 incidents. The Team also saw a 12-year old boy with bullet injuries under arrest. It came to know that at least three people who had been brought to the hospital on that day had succumbed to bullet injuries.
The Team also visited the neigh-bourhood of the bridge connecting Neelam Chowk with Mathura Road. During the day-long firing- and lathi charge, the police had spilled over into the outlying areas and beaten up innocent residents of the jhuggis and jhopris. One such victim was 60-year old Bishan Singh, a saintly looking Sardarji with white hair and beard. He showed the Team -the wall of his courtyard broken open by the police who entered the house as he was sitting on his charpoy and asked him to bring out those who were supposed to be hiding in his room. Bishan Singh said that no one was hiding, and offered to take the police to his room to prove the truth of what he was saying. Not satisfied, the policeman started beating him. With an injured leg, old Bishan Singh was now confined to bed. Children seemed ‘to have been a special target of the police. Wherever the Team went people complained that children were beaten up mercilessly.
The cases of Bali’s son and 16-year old Surendra of Punjabi Colony have already been mentioned. People with whom the Team talked at Faridabad estimated that from 50 to 120 people were still missing. Among them were a large number of children’. There was a widespread suspicion that the police had disposed of the dead bodies by burning them’ secretly – as evident from eyewitness accounts of the Gurgaon cremation ground – or by throwing them into the river. The Team found that there was widespread distrust among the people of Faridabad towards the local police force. For one thing, it was evident to all that the police had been giving out false reports. Immediately after the October 17 ‘incidents, they had said that firing had stopped at 1 pm on that day. But the Team was unanimously told by the people that at Neelam Chowk firing had continued till the evening. The killing of Kashmiri Lal Bali and Jagdish Prasad took place after Bali had returned from office, between 4.45 pm and 5.15 pm. As for the number of casualties also, the figure of eight given out by the police was dismissed as too small by the local people, many of whom were still searching for their missing relatives and friends who were suspected to have been killed. The people were further infuriated by the government’s immediate announcement of an award of Rs 15,000 to’ relatives of the dead sub-inspector. “What about the innocent people who were killed by him and his colleagues?” ask the people of Faridabad.
The Team was told that at every stage the local industrialists were influencing the police. At the Circuit House meeting where the industrialists, police officials and minister Khurshid Ahmed discussed the post-firing situation, it was the industrialists who had offered to pool the money and give the award to the dead policeman. It was they again who pressurised the Minister against giving Bali’s dead body to his relatives. There was a widespread feeling that the magisterial inquiry ordered into the October 17 police firing by the Haryana government would not lead anywhere, excepting defending the police. The people were demanding a judicial inquiry and suspension of the guilty policemen. The local people also complained that none of the major political parties or trade union leaders had bothered to visit the relatives of the dead or the injured. No help had been rendered to the victims in the hospital. The injured boy, Anil Bali, was lying alone in a critical condition when the Team visited him at the Safdarjung Hospital. In its report the Fact Finding Team has noted that the industrial climate at Faridabad had deteriorated over the years primarily because of the aggressive attitude of the local industrialists who habitually employ ‘goondas’ in the name of security guards to beat up workers active in the trade unions. For instance, it was alleged that on October 17, the ‘goondas’ employed by the management of a cotton mill near Press Colony, Faridabad, had chased workers belonging to the union. Eye witnesses told the Team that the police were protecting the goondas who hurled stones at the workers.
The Team has raised a number of questions in its report:
(1) Why is it that no arrests are made when organised goondas (working under the cover of security guards) attack workers whereas innocent victims of police firing are kept in chains in the hospital?
(2) Why is it that authorities in Faridabad impose Section 144 whenever there is even a notice of a strike in a single factory?
(3) Why is that compensations are paid by the government and the industrialists to the police personnel, while the victims of indiscriminate police firing are paid none?
(4) Why is it that seriously injured victims of police firing are kept in chains at the hospital with three armed guards? Summing up its findings about the events of October 17, the Fact Finding Team has stated that:
(1) Imposition of Sec 144 at 2 am, unannounced, was a deliberate provocative step.
(2) Disappearance of 150-200 men and children since October 17 was too much of a coincidence to be ignored.
(3) Threats, destruction of evidence and offer of bribes in some instances by the authorities proved their complicity in the incidents of the 17th.
(4) Disposal of dead bodies at Gurgaon without proper religious rites and the secrecy surrounding the act tended to suggest that the number of dead was much more than what the authorities want to be believed.
(5) People of Faridabad, workers, shopkeepers, housewives, children, etc., were all in fear of the police and critical of their acts.
(6) The reign of terror let loose by the authorities had to end before anything else could be done. A judicial inquiry must be held to inquire into the violent incidents of October 17 and the role of the police in them.
* From Emergency to Rural Maoism to Leninism in Faridabad
GWN conversation, 2010
We met some communist still active in Faridabad industrial area. Some of them entered reputable universities in the early 1970s, and spent their first years as ‘unpolitical’ students on the campus. Things changed during Emergency. Under the heavy atmosphere of the Emergency any kind of dissent obtained a new significance. Some of them had to leave university and joined a far-left organisation. The organisation sent these new recruits to work in the countryside, with Adivasis, the ‘indigenous population’. The Naxalite organisation had a kind of scale, there were class I areas, they were the poor Adivasi areas, class II for certain areas of poor peasantry, class III for urban working- class areas and so on. The Adivasi areas were not characterised by’ self-sustained communities’, most of them were wage workers for the timber industry. During these days these young comrades travelled from village to village, the organisation had contacts, often to village teachers or similar people. While being ‘underground’ the original organisation had split several times, but the young comrades were not aware of this. They continued their ‘organisational work’ for a non-existing organisation.
Some of them ended up in the ‘semi-tribal’ area of Mewat, a poor Muslim-dominated area in Haryana. They focused their activities less on the peasantry, but on the educated, unemployed poor youth. “We wanted to turn them into professional revolutionary cadres. We had some contacts within the Haryana electricity board. Some guys had been on strike in 1972, they knew people in various villages. In those days people liked revolutionaries, many people would help us and hide us from the state forces, give us food and shelter. Particularly in Mewat people were angry. The police had rounded up villages to enforce sterilisation – a sensitive issue particularly in the Muslim areas. We tried to break the encirclements, but this proved to be difficult. People were put into trucks and brought to the primary health centres. Each block and district local state officials were gratified for achieved numbers of sterilisation.”
The comrades met interested locals in B., a bigger village near Faridabad. They stayed with a mechanics and local teachers. Many underground revolutionaries arrived in B. after years of’ activities with the rural people’. There were CPI committees amongst peasants. Some clerk who had gone to Chandigarh to work had brought Marxist literature. “Although the official CPI line was against the Maoists and pro-Emergency, the CPI peasants in the village supported us. They were mainly from the Dagger tribe and had a history of resistance reaching back to feudal times. Every now and then the peasants of this village blocked power-stations, in order to protest against the lack of electricity. Police brutality in the area during Emergency had further radicalised them. A CPI official in the village had been to the Soviet Union as part of a party delegation. He was open towards the far-left, he managed to get people – who had returned from ‘activities’ in country-side – jobs in factories.”
Some of the peasants who had ‘joined the revolutionaries’ turned ‘workers’ for political reasons and went to work in factories in Faridabad during the late 1970s and early 1980s. “The factory was kind of a shock for the peasants. They were used to hard physical work, but not to having to stay in one place under surveillance and noise and the rhythm of the machines. Some of them wrote poems and songs about these experiences. Not just about the work, also about the ‘cultural changes’, e.g. at Bata shoe factory they found the village Pandits sewing leather sandals or Dalits in the restaurants serving food to the wider public, which was something unthinkable in the village. With the help of some of these ex-peasants we started our activities in Faridabad. We had broken with our Maoist heritage and had become urban Leninists.”
* Worker in Faridabad in early 1970s, Full Time Activist, Sangarh Samiti 1979
GWN conversation, 2010
I came to Faridabad in 1970. I got a job at Universal Electric Limited, a company manufacturing devices for the defence industry. There I worked for one year, I worked on a lathe machine. There was a strike by the union and in this I was thrown out.
Then I was employed at Porritts&Spencer Asia Limited, which was a British company, it still exists, but is now owned by Germany and America. In Porritts Spencer, I worked on the loom machine on which clothes are made. It was a factory where all the workers had to do all the jobs. They were trained in all jobs. So I was also trained in all the machines. At that time, in 1977, about 300 workers were employed. There was a strike in 1977. In that strike, I was the General Secretary of the union. Then I was thrown out.
Then I was fulltime with the CPI. Then I joined CPM full time. After that I worked for the Naxalite movement. In 1979 we formed the Sangharsh Samiti, the Struggle Committee. We brought the whole of Faridabad to a stop in 1979. Guns were fired in which many workers were killed. At that time, the Bhajanlal Congress government, ordered the gun fire. The guns were fired at the Neelam square which we today call the Martyr Square. The workers became martyrs. The government said 17 people had died. The workers and some police officers were hurt. The workers said that about 150-175 people had been killed. But the government made the dead bodies disappear. Because there were many arrests, in fear, the protest went down a little for some days. We could not find out whose dead bodies were missing.
Before that there were demonstrations in many different factories which the government could not control. At that time there were unions in about 50% of the factories and they helped one another. The police oppression was also very great, but the workers then were so militant that they used to fight with the police. This is the reason why in the Faridabad strike there was a struggle with the police, where the police fired guns and the workers were killed.
After that the workers movement declined, automation was introduced in the companies and the number of workers decreased. Many factories closed, a large number of textile factories closed and unemployment increased. Many factories were computerized and workers went back to their villages. The factories started outsourcing. Permanent work was reduced. People started to work on contracts. So the movement went back.
* Escorts/Ford Worker in Faridabad in 1970s and 1980s
GWN conversation, 2010
In the late 1970s and early 1980s trouble was brewing at Faridabad’s biggest company Escorts. The trouble was intensified and shaped by an internal fight between different management factions respectively supported by different political formations. In 1982 instigations against the old management started – a new management faction under Swaraj Paul and backed by Congress tried to ‘take over’. The emergence of a new union within Escorts was instrumentalised in order to attack the old management. After Indra Gandhis death in 1984, the new management under Swaraj Paul sold his shares. The old management and the old union were back in the seat. We mention these ‘power-games’ because they influenced and still influence any union formation in the bigger industry. We had a conversation with N., a comrade who worked at the Ford tractor department of Escorts in the 1970s and 1980s. N. got involved in union struggle on the side of ‘the new union’ – reading his story we have to see the double dynamic of workers’ unrest and internal management fights.
“I came to Faridabad from Kerala, in the early 1970s. In Kerala I had been engaged with the illegal CPI(ML), mainly struggling against land-lords. At the time it was not unusual for workers to come the long way from far – south Kerala, there must have been more than 20,000 of us working in Faridabad at the time. There was a huge demand for skilled workers which could not be satisfied from northern areas like Bihar or UP- that has changed quite a bit since then. In 1972 I got a job in the Ford tractor plant, where about 2,500 workers were employed. A comrade and me became elected as representatives of a left-wing union, which organised the vast majority of workers in the plant.
These were rebellious times. Workers were questioning a lot. Take the example of a struggle lead by a marginal work-force in the factory: the cleaners. Take their example of struggle over a seemingly minor issue: canteen food. During these times workers’ desires turned badly cooked vegetables into social dynamite. There was a canteen for workers and a canteen for the management. The production workers were allowed to use the canteen first, when they left, the cleaners could eat. This was not because workers would not have sat together with cleaners, it was because the cleaners would work while machines stood still during the workers’ break. Nevertheless, when the cleaners came to the canteen there were little vegetables left, just rice or roti. The canteen might have cooked more veggies, but they were often half done or there were literally five minutes left of the cleaners’ break for having a meal. The cleaners were not happy about this. They complained. The management did not listen. They addressed the left-wing union and asked them to do something. The management ignored the union. The next day about 150 cleaners entered the management canteen in protest and ate all kind of nice food, fish, deserts and so on. This was not heard off before and the management was in shock. The shock-waves entered various levels. The first reaction was to purify the canteen with Ganga water, purify it from the spiritually dirty cleaners’ hands. The next reaction was an attempt to suspend not only some of the workers involved, but also some ‘ring-leaders’. This was not that easy…
The management tried to ignore our union in the Ford plant. The Escorts and Ford management and the main Escort union plotted all kinds of coups against us. But they basically tried to keep us away from any kind of negotiations. The workers were rather angry about that, they had voted for us, because they wanted us to do things. When a general negation between Escorts management and unions took place about 2,000 Ford workers gathered in front of the administration building. They demanded that their reps could be heard. The management refused. Workers wrote a demand notice: “Either the management talks to our representatives or they will be beaten with sandals”. The management remained deaf. Workers then pushed into the main building and surrounded the management, started beating it with sandals like promised. This was hot. In Kanpur, where a similar thing happened in 1977 the police shot and killed hundreds of workers in side a textile mill – that was after the Emergency, in the so-called’ new democratic phase’. The next day Faridabad was full of police looking for sandal-wearing workers…
The police-force itself was not too reliable at that time – a clear sign for the depth of social discontent. The lower ranks of the police were badly paid and had to work long hours. In Faridabad they went on strike. Some of them were from Kerala and we got in touch with them. In the end they had to bring in the special police force CRPF. They sacked half of the local police and the CRPF disarmed the other half. We put up posters “Police against Workers – CRPF against Police – Army against CRPF: This is Indian Socialism!”. The activities inside Ford got us more and more into the focus of repression. Escorts paid the police good money to find and beat us. During these days most of the arrests were unofficial and never documented. They would pick you up, take you to a faraway station and give you a good beating. The home guards, a rather poorly paid part of the police informed us about the police plans.
Finally they caught us and drove us to a station near Balabgarh. There, the night-shift guards knew us and refused to beat us up. In the end we got a thrashing in the police station in Sarai. It was dark, we could not see who thrashed us, but they always asked: “Will you know leave Haryana?!”, and unsatisfied with the answer they would continue. I was kicked out of the Ford plant, six years of legal battle followed…”
* Revolutionary “Termites” in Faridabad
Loren Goldner
For complete text see: http://libcom.org/library/revolutionary-termites-in-faridabad-a-proletarian-current-in-india-confronts-third-worldist-statism
1980′s Struggles in Faridabad
The CITU in 1983 was involved in another militant strike in Faridabad, this time at Lakhani Shoes, which then employed 500 workers and is now much larger. The CITU carried out physical attacks on managers and supervisors, but the strike, which lasted for months, ended in defeat. It later came out that Lakhani had paid 35,000 rupees to the Faridabad leader of the CITU. (Subsequently, the CITU was ousted and replaced by unions affiliated with the Congress Party and then with the JP.)
Such union activity is not merely limited to manipulating struggles with management while covertly collaborating with the latter. In 1983, Dewanchard Gandhi, a CITU leader in Faridabad, was involved in a brazen use of union goons for a real estate scam. People from nearby village had occupied land in Faridabad’s Sector 6 and had set up a tea shop, thereby becoming de facto owners. The owner of the land sold it to Gandhi and his brothers. The Gandhi brothers’ own goons would not vacate the land for them because some of them were from the same village as the occupiers. Thus Gandhi organized a union in a nearby factory of 300 young workers, and called a strike. While they were on strike, he used them to forcibly vacate the land and to wall it off, in one night, telling them it was to be the site of a union hall. This accomplished, the workers went back to their picket lines, but the union stopped food deliveries to strikers. The workers resumed work and left the CITU. Ghandi kept the land. In the same year, a militant CITU union at J.M.A. Industries called a strike. Bombs were thrown, and the state arrested and brought to trial four strike leaders. Regional CITU leaders came in to replace them and announced a deal. It later emerged that the company had built a new roof on the house of one of the regional leaders; meanwhile, the four local leaders stayed in jail, 18 militants were laid off, and management’s aim were imposed.
In 1988, a struggle began at the Bata Shoe Company, a Canadian-based firm also operating plants in Batanagar, near Calcutta, in Bihar, and in southern India. Bata Shoe launched a plan to restructure and diversify into marketing. The offensive began with a lock-out of the roughly 13,000 workers of the Batanagar plant, where both Communist Parties had unions. As part of the strategy, the management of the Faridabad plant went from a 5-day to a 7-day work week, with the cooperation of the CP unions there. A month later, an all-India one-day strike against Bata Shoe was called; two months later, this was followed by a 3-day all-India Bata strike. Four months after the management offensive began, it imposed all 37 of its restructuring demands. The union in the Faridabad plant called another strike in April 1989, and 10,000 workers went out, followed by further strikes later the same year. At the beginning of the management offensive, Bata Shoe in Batanagar had 13,000 workers; at the end, 7,000. (KK points out that at every turn the Indian media gave very favorable coverage to the unions’ toothless strike strategy.)
In 1989, at K.G. Khosla Compressors Ltd., a plant with 2,000 permanent workers and 350 casuals, the union signed an agreement with the company in which they gave away the workers’ dues (“dues” in India mean severance pay, outstanding wages, pension funs and bonuses. It is common for management to quietly loot these dues in anticipation of a plant closing.) (Six years earlier, in 1983, the INTUC had led a militant strike which was crushed, ending in layoffs. When confronted, the local INTUC leadership said they signed the contract because the national leadership signed, and the national leadership said they signed because the local leadership signed.
Things came to a head in August 1991 as Khosla management declared a lockout, terminating 250 casuals, announcing 326 layoffs of the permanent work force, and offering only the minimum annual bonus of 8.33%, threatening closure of the plant if these demands were not accepted. No wages were paid for August and the lockout began in early September, lasting 8 months and breaking worker resistance. A similar downsizing was pushed through at Thomson Press, a printing plant in Faridabad, which reduced its personnel from 1700 to 900 between June 1989 and June 1991.
In 1987, Thomson brought in a new manager, replacing one who had had a close working relationship with the Congress-affiliated INTUC. The new manager preferred to introduce the JP-Iinked HMS, to the relief of the workers, who hated the INTUC leader. The new HMS leader was himself a dismissed Thomson worker. To start off the new regime, the company agreed to make casuals permanent.
In 1989, however, Thomson demanded 200 layoffs and the new HMS leader signed a giveback agreement. In August 1990, the workers responded by bringing back the old deposed leader. In response to this, the company announced the closing of one of the plant’s printing operations, cutting jobs. Two factions of workers formed around the two leaders. The state government exacerbated the division by cultivating ties to the INTUC leader, and fights broke out between the two factions. In March 1991 management suspended all production because of the fighting. Whereas the media had given wide coverage to the situation up to that point because of the state’s ties to the INTUC leader, there was a complete blackout of news on this lockout. Both leaders convinced the Thomson workers to leave the factory during the lockout, and that night the management removed machinery from the plant. The lockout continued for 70 days, at the end of which the HMS leadership announced that the workers did not want a fight. The plant reopened, with a very bad agreement in effect, and over the next 4-5 months 800 workers were forced to resign.
Relevant Struggles Elsewhere In India
One icon of the official left in India is the worker buy-out of Kamani Tubes Ltd. in Bombay, the Indian variant of the French LIP strike of 1973 (8), or the more recent ESOP’s (Employee Stock Option Purchase) in the U.S. Kamani Tubes Ltd. was taken over in 1987 by its work force of 450, after 60 workers were laid off. The workers raised the buyout funds by taking out mortgages, and received support from the Bureau of Industrial Finance and Reconstruction. The Kamani Tubes experience of self-managed austerity is still used as a paradigm by India’s NGOs and official left, and has been copied in a few other well-publicized instances, such as the Kanoria Jute Mill in Calcutta after 1993.
Not all workers’ struggles in India, however, are successfully contained or manipulated by the unions. In 1989, 35,000 textile workers in Kanpur, an old industrial city in Uttar Pradesh, revolted against all local unions and blocked the railway lines through the city, taking turns by shift. 100 trains were cancelled, and the government conceded their demands in 5 days. In this case, in contrast to the nation-wide, union-controlled Bata Shoe strikes, government propaganda and the media weighed in heavily against the action, and trade union officials also attacked it. (In 1977, just after Indira Gandhi’s state of emergency had been lifted and the anti-emergency Janata Party had taken power, the government had fired on Kanpur textile workers inside the Swadeshi Cotton Mill, killing between 30 and 150 workers and running off all trade union leaders. The textile mill had been nationalized shortly after the shootings.) In 1989, however, an impending election year militated against government violence. Nonetheless, once the struggle had died down, the government announced a retrenchment program and pushed it through over the next 4 or 5 years.
Similarly, in December 1988, at the No.7 mining area at the Dhanbad Coal Mines in the state of Bihar, the piece-rate workers, fed up with the unions and their goon squads, revolted. They drafted demands and started a hunger strike at the union regional headquarters, and surrounded the regional management offices with slogans denouncing both corrupt management and corrupt unions.
In July 1990, another struggle outside and against union control erupted. 5,000 miners from the Munidih mines of the Bahrat Coking Coals Ltd. (BCCL) struck on their own. The police opened fire, killing two miners. All unions opposed the strike, and denounced the influence of “outsiders”. Management refused to negotiate, until Aug. 7, when 2,000 workers surrounded BCCL headquarters and forced talks, in which management persisted in pressing charges against the strikers. On Aug. 10, fighting erupted with police, and union goons threatened workers. Under this pressure, 50-60% went back to work, but after an Aug. 17 solidarity demonstration that mobilized 1,000 workers, management caved.
The workers at Bengal Jute, living under the “Marxist” state government of the CPI (M) in West Bengal, were not so fortunate. Bengal Jute operates 49 jute mills, in which the CPI (M)’s own union, the CITU, and the INTAC were dominant. In 1984, in a previous strike, management had agreed to no layoffs of 250,000 workers, but subsequently managed to retrench 110,000. In June 1992, the two unions launched a strike demanding the reinstatement of the laid-off workers; during the ensuing, failed strike by its own union, the CPI (M), with state power, said nothing.
1990′s Struggles in Faridabad
Lakhani Shoes, which currently operates 19 plants in Faridabad, had been the scene of mass layoffs in 1983 (described earlier) and 1988. By the mid-90′s, it had become a joint venture with Reebok, using a large number of casuals in very hard work with low pay, rapid aging on the job, and loss of fingers. Many workers are Nepali, with a young work force because of the previous mass layoffs.
In these conditions, in May-June 1996, the workers decided to organize and went to the Hind Majdoor Sabha (HMS), mentioned earlier as the union affiliate of the Janata Dal. In July-August 1996, management suspended the union activists, and in September the union called a strike. Permanent, casual and contracted workers all struck. The strike continued into the spring of 1997, when workers began to disperse. The management resumed work using new hires, with the ex-leaders from the HMS as the labor contractors. A court order demanded that strikers stay 100 yards from the gates, and all strikers were ultimately fired.
In June 1995, a new struggle erupted at the East India Cotton Mills in Faridabad, where the 1979 strike was one of KK’s first formative experiences in the working-class milieu. In 1995, the mills employed 3,000 workers in two factories. When some equipment was dismantled and workers complained, six of them were suspended. 2,500 workers walked out and the six were reinstated. Management, however, wanted 600 layoffs. Without leaders among the workers, they were unable to control the work force. In the run-up to a confrontation over the layoffs, hunger strikes took place, and a group of rank-and-file leaders, demanding a “good contract”, took over. In June-July 1996 295 workers were forced to resign. Management floated a voluntary retirement scheme which found no takers. On July 10, they declared a lockout. 18 days later, the lockout was lifted and an agreement to resume work was signed, with 18 days pay lost.
In August, management simply paid no wages, and on Sept. 12 declared a lockout in both plants, backed up by the arrival of the police. In an unusual move in a lockout situation, the rank-and-file leaders told the workers to leave the factories. The lockout continued into the fall, with the workers dispersed. The rank-and-file leaders threatened to close down Faridabad if the lockout did not end before Diwali (a Hindu festival). At the same time they avoided demonstrations because they were afraid of losing control. The leaders tried taking the case to the Supreme Court. In January 1997, the smaller plant reopened, but two months later resumed the lockout, with management still demanding 600 layoffs. As of December 1997, the lockout continued.
* Some Agitation in Faridabad
FMS, September 1983
* At Biko Engineering situated at Mathura Road the pressure from management increased after the issuing of a demand notice. Workers got suspended.
* After workers at Elson Cotton raised their voice against lay-offs, they got beaten up and some of them suspended. The bosses hired goons.
* At East India Textile Mill INTUC keeps beating the drum and the management cries about’ worsening situation’ for the company while at the same time sending lots of workers back home.
*At Atul Glas workers are determined in their battle for creating a union. Management and police try to suppress the workers by beatings and arrests.
* At Usha Spinning Mills the lay-offs of workers continue. Workers are laid off without being paid outstanding wages. Now the union leader says that he will do something about it.
* After Indian Aluminium and Mahindra and Mahindra have fused and the atmosphere amongst the Indian Aluminium workers is heating up.
* The back-and-forth between JMA management and workers continues. In order to break the union the management has kicked out four leaders and now talks about a contract/agreement.
* Five workers at the Electricity Board have been suspended. The processions and protest-meetings continue. There are a lot of posters-meetings-slogans etc. about forming this or that union, but most of it is the usual ritualistic procedure.
* Some Agitation in Faridabad II
FMS, October 1987
* The company HYDERABAD ASBESTOS LTD. has changed its name to Hyderabad Industries Ltd., but in the Faridabad factories, the company continues to use the asbestos material like before, causing fatal cancer and asbestosis lung disease. The infamous management is in the first line when it comes to make workers fight among themselves. During the last ten years, whenever the management saw that trouble is brewing amongst workers, it used incantation-bribery-threats-divisions in order to make the workers smash each others heads. After having seen this happening again and again, this time the workers countered the management at the very attempt. This time, on October 14, the police shot at the workers. After this the management enforced a lockout. Apart from enduring the usual back-and-forth of the INTUC-AITUC-BMS, this time the Hyderabad Asbestos workers also had to see the pretentiousness of the HMS.
* Nukem Plastics manufactures by using poisonous gas, putting at risk the health of workers and the wider population. In the course of conflicts among workers, incited by management and trade unions, a worker died in October 1987. In 1977, the management of this factory used the BMS as their weapon. Being squeezed between management and this union, the workers tried to turn sometimes INTUC, sometimes CITU, sometimes HMS into their vehicle of rescue. A lot of empty promises have been made, causing damage to the workers and usually ending in a sell-out. This time the HMS, while hailing the Lok Dal government, created a big fuss in order to take over the chair at the negotiation table from its relative, the BMS. In the course of the dispute the workers anger got vented, a worker died in action, the workers got locked out from the factory and finally the union sold out. The factory management first locked-out the troubled workers and then handed out food to them. Now it has restarted production and disseminates its poisonous gas again – and both BMS and HMS are looking out for new grazing grounds.
* After having suffered under CITU, the Autopin workers are now pretty fed-up with BMS. In order to take over another chair at the table, the HMS created a lot of fuzz – they tore the BMS flag from the gate pole. They workers got agitated, the management resorted to lock-out. After ten-twelve days the HMS showed its true colours – exactly the same as BMS. Thanks to the new agreement signed by HMS, the bonus has decreased from 16 to 10 per cent, the September wages were paid in November and god knows when the October wage will be paid.
* At Bombay Rubber plant the CITU makes fools out of the workers. After two months of strike against the dismissals of five workers, the CITU now has signed an agreement which accepts the dismissals and has taken aback the rest of the workers – while the management distributes sweets amongst the workers.
* At Metal Box many workers had been dismissed in the recent passed. Management started to pay the remaining workers wages which are relatively higher than in other factories. Some of the Metal Box workers then felt big and they saw themselves as being different from other workers. Now, as consequence of capitalist reality, Metal Box has to face a new round of redundancies and Metal Box demonstrates the workers their essential existence as workers. In order to enforce the redundancies, the management of Metal Box has issued a lock-out.
* At Escorts Anciliary the union HMS has negotiated such great agreement that the workers organised a tool-down strike against it. HSM’s plan to sweeten the increase in work-load with a little wage hike – the two results of the agreement – did not go down well with the workers. The HMS leaders reacted by turning an issue, which essentially only concerned workers at a different Escorts plant into a point of conflict. In return management was then able to announce a lock-out in order to break workers resistance. In this way union and management forced workers to accept the work-load increasing agreement.
* Since ten years the workers in East India Textile Mill are looking for a messianic-miraculous solution of their problems. They have seen one Messiah after the other trying to perform these miracles, but the workers are still not satisfied. After the Lok Dal took over government in Haryana, workers once more stare at the performance of the HMS leaders. A series of meetings and speeches has been put into motion… on the other side the management smears honey around the mouth of the union president and sends him off in a specially provided car…
* Intro Escorts
GWN, 2010
In the 1980s the Escorts Group belonged to the ten biggest manufacturing companies in India, an industrial giant active in various product segments, such as tractors and agricultural machines, motorcycles, cranes, earth moving machines, parts for the railways. Like Maruti Suzuki or Hero Honda, Escort collaborated with various international companies, such as JCB, Claas, Yamaha, Ford Motors. Till the mid-90s about 24,000 permanent workers worked directly for Escorts Group, the main company in Faridabad at the time, which had various plants in the area. Hundreds of smaller factories and work-shops still depend on Escorts as their main ‘client’. From the late 1980s onwards permanent workers were attacked by various management schemes to increase the work load and productivity, often in collaboration with the union leader-ship. The union leader at the time, Subhash Sethi, interestingly enough presented himself as an anti-Stalinist revolutionary – see interview with ANC journal below. The underlying battle about re-structuring went on during the early 1990s; management used various strategies, such as shutting down certain plants for one or two weeks, putting pressure on older workers to accept early retirement etc.. This process got aggravated by various market slumps, which management used as a pretext to threaten workers with job cuts. From 1996 onwards the re-structuring process made great leaps forward: JCB, Yamaha and Claas split off from Escorts, the telecom division was sold. From then on Escorts focussed on the agro-machinery sector, of 24,000 former permanent workers now only 6,000 are left. This is not only due to the carve up of the former Escorts Group, but also because permanents were increasingly replaced by casual workers or workers hired through contractors. Till 1992 the number of casual workers in production was less than two per cent, today it varies from 10 percent to 50 percent, as per demand, and whereas there used to be no workers hired through contractors in the immediate production, now their numbers increase significantly. For current conditions at Escorts see:
http://gurgaonworkersnews.wordpress.com/gurgaonworkersnews-no5/#fn1
* “Interview with President of All Escorts Employees’ Union”
Journal of the Marxist Workers’ Tendency of the African National Congress, October 1981
Inqaba interviews
SUBHASH SETHI,
President of All Escorts Employees’ Union,
Faridabad
India – ‘Workers must organise for Power’
India under capitalism is a giant In torment. With a population of 700 million (almost double that of Africa) and vast natural resources, India is potentially one of the most productive and wealthy countries in the world. Instead, after centuries of plunder by British imperialism, followed by the parasitic rule of the rotten Indian capitalist class, the country has been reduced to indescribable poverty and seething social tensions. Under the Impact of the mass struggle, India became politically Independent In 1947. British lmperialism handed power to the representatives of Indian capitalism. Though the trappings of a parliamentary system were established, for the mass of the people democracy does not exist. Enormous power has been concentrated fn the hands of Indira Gandhi and her corrupt family clique at the head of the Congress government. This power Is used In the most ruthless manner to enforce the interests of the big capitalists and landowners. Under their rule, over half the Indian people live below the official poverty line. 200 million working people survive on less than 20c a day. 100 000 children die of malnutrition every month. 80 % of children In the countryside will never go to school. The Indian workers and peasants struggle against these intolerable conditions. In every industrial city, heroic strikes have been fought in the face of murderous repression; in vast areas of the countryside, civil war reigns between landlords and landless peasants. In 1979, according to government calculations, there were 216 riots per day-nine riots every hour!
Pre-revolutionary turmoil
The capitalist class is completely incapable of solving the problems of the country. India has entered a period of pre-revolutionary turmoil. In the coming years the question of power will have to be decided-whether the present rulers will succeed in crushing the mass movement and stabilising their grip on the country, or whether their the only force capable of displacing them: the 21-million strong urban proletariat at the head of the countless rural masses. The most critical element in the workers’ struggle will be that of unity, leadership and programme. Thus far, the magnificent movement of the workers, in the towns and on the land, and the no less heroic struggles of the peasants, have been held back not by the power of the state, but by the failures of an utterly bankrupt and opportunist leadership. The leaders of the main organisations of the Indian working class-the Communist Party of India and the Communist Party of India (Marxist)-cling to the bankrupt position that India is not ripe for the overthrow of capitalism. Therefore the task, according to them, is to consolidate ‘democracy’ on a capitalist basis. In practice, this means a series of compromises with reactionary have increasingly been driven into nightmare regime will be broken by capitalist leaders, watering down their half-hearted reformist programmes even more, and losing further support among the working people. It is due to the failure of the workers’ leaders to provide a socialist alternative that Indira Gandhi-brought down by a wave of mass struggle in 1977-was replaced by an equally bankrupt capitalist regime, and was then able to return to office last year. But the election result itself revealed the isolation of the ‘victorious* Gandhi regime. According to the official figures (despite widespread vote-rigging in Mrs Gandhi’s favour) little more than half the electorate voted; in all, less than a quarter of Indian voters supported Mrs Gandhi! In office, the Gandhi clique have continued to enrich themselves while building up the machinery of a police state to protect themselves against the anger of the masses. Their latest reactionary measure has been to declare a total ban on strikes in the main sectors of the economy. A punishment of a year in prison is laid down for organising strikes, and 6 months for taking part in a strike! These attacks will spur the workers on to even more determined struggles. Country-wide protests are already taking place. Everything points at an explosive sharpening of the class struggle in the period ahead. The capitalist class has no answer to the struggles of the workers and peasants except increasingly barbarous repression. Already sections of the ruling class are calling up the dark forces of communalism (ultranationalist fascism) as a bludgeon against resistance among minority national groups. Nationalist movements in different stales of India, reflecting a mood of despair, are struggling lo break free from the hated regime In New Delhi. Under capitalism, India faces a nightmare future of ruin and disintegration. Only the development of a Marxist leadership within the mass organisations of the Indian working class can provide a rallying point for the workers and peasants in struggle and show a way out of the present crisis. Organised on a socialist programme, the Indian working class can draw behind it the mass of the people, demolish the capitalist system and, on the basis of nationalised production under democratic working-class control, develop the resources of the country to meet the need of the mass of the people. The fate of the Indian revolution is of vital concern to the workers of South Africa and the entire world. If successful, it would enormously strengthen the workers in every country; If crushed, it would be a demoralising blow to workers everywhere.
INQABA has discussed some of the crucial questions facing the Indian working class with Comrade Subhash Sethi, a union leader from the Delhi area and a supporter of the ideas of Marxism. Shortly after giving this interview, Comrade Subhash Sethi was a leader of a 30 000 strong demonstration of workers in Delhi against the antistrike legislation. Many of the tasks of the Indian workers-in particular, the building of a united national trade union movement-are similar to the tasks, which face us in South Africa today. Many lessons can be learned from the experience of the workers in India, which will assist us in carrying forward our work.
INQABA :
Workers in South Africa are eager for information about the pre-revolutionary movement of the Indian workers and peasants, which has brilliantly begun over the last period. Could you describe this movement?
Sethi:
Sixty per cent of the people in our country are living below the poverty line. That means earning less than two rupees a day (20c). 74% to 80% of the people are living in the villages. Some are peasants, some are landless labourers. But when they go to the cities they see the capitalists living like princes, with cars, big homes and servants. Due to all these social evils the masses want revolution, they want to change society. They realise they are working hard and getting nothing. But the main problem is the lack of revolutionary organisation, the lack of national leadership. The left in India is split into many parties like the Communist Party of India, the Communist Party of India (Marxist), the Communist Party of India (Marxist-Leninist), the Revolutionary Socialist Party. But none of them provide a real alternative, a revolutionary leadership for the struggling workers and peasants.
None of the political parties is working democratically. This is a big problem and that is why they are divided. Anyone who criticises the leadership is sent out of the party. Also if he wants any change in the policy or programme, he is sent out of the party. Most of the trade unions are controlled by political parties and work in the same undemocratic way. What we need is to build one country-wide trade union organisation that will work democratically and carry forward the struggle for change. In the meantime we will also be building a revolutionary political leadership.
INQABA :
The name of Gandhi is well known in South Africa since Mahatma Gandhi was active In South Africa as well. Can you tell us about the regime which Indira Gandhi has set up in India today?
Sethi:
No doubt Indira Gandhis’ family were involved in the fight for independence, but she was not elected for this reason. 60% of the people have voted against her, always. Indira Gandhi game back to power in 1980 because the previous Janata Party government did not give what they had promised, and because of the failure of the main workers’ parties to provide any clear alternative. Indira Gandhi’s Congress Party is a nationwide party, but the other parties are regional parties. The Communist Party of India (Marxist) is the biggest left party. It is the ruling party in three states – West Bengal, Kerala and Tripura. In other parts the Communist Party of India has a hold. If the left put up a united front nationally Indira Gandhi could not win. She has to use bribery and vote-rigging in order to stay in power. But the left parties don’t unite. They are Stalinist parties, by which I mean that the upper leadership are the bosses of the parties. They dictate, they don’t want democracy in the party, they don’t want to lead the revolutionary struggles of the masses. That is why Mrs Gandhi is able to stay in power. This government of Indira Gandhi is pro-capitalist, anti-trade union and anti-working class. A new law has just been passed to ban strikes. But I tell you, half a million workers will march on 17 August to say to Indira Gandhi, you shall not pass this law. We in Faridabad are planning a strike on that day. But Indira Gandhi knows that the national trade union leadership do not have the courage to fight. After passing this law repression will increase. After that some workers’ leaders will be forced to come out in opposition because of the pressure of the workers. The workers will demand of their leaders that they to organise a united struggle.
INQABA:
What has been your experience of the struggle to create a united trade union movement?
Sethi:
Until 1974 I was working at Escort in Faridabad, when I was sacked for trade union activities. There were six trade unions in Escort, in a workforce of 10 000. The strongest of those unions were led by the CPI (M), the CPI and the Congress Party (Indira). I said to the leaders of the unions, why are we divided into six parts? We are crying that the employers are exploiting us, but we are doing nothing for the workers. We can’t get anything until we unite. The leaders agreed and said we should form a front. I said no, we should form one organisation, one union, and the workers should elect the leadership. The leaders said no. Then I went to the workers directly. I told them of my discussion with the leaders and explained to them that if we are divided our demands will not be met. The workers agreed. Then I asked them, why don’t we form one union and leave those other leaders? So they all left their unions and we formed one union. For the last four years we have had elections every year, and I have been elected President every time. After we formed this union we had a strike. It involved 10 000 workers, and we won it in three days. At first the employer said he would kill me. He said he would fire his factory before he would talk to me. But after three days he agreed to talk. Then we had a meeting with the management and got an increase of 125 Rupees (R12,50) per month per worker. And within three years we got another increase of 350 Rupees (R35.00). In the history of India there have never been such increases in such a short period. On that basis I went to the workers of the whole region of Faridabad. I asked them, why are we divided, why should we not form one organisation as we have formed in Escort? The workers agreed. We organised 15 000 workers more. Now we are the strongest organisation, in Faridabad. Within the next two years our aim is to organise 100 000 workers into our organisation, out of 200 000 workers in the region. They will come into our organisation because all the workers can see we are following the right path, we are following the democratic path and we are fighting for the workers’ interests.
INQABA:
How does democracy operate inside your union?
Sethi:
Democracy means, the leadership must be elected by the workers, if the workers believe they are right. I may be the leader of our organisation, but the leadership can be changed if it is not working in the interest of the working class. So I am not saying that I should be the leader, but that the leader should be elected every year. Any leader who is not working for the interests of the workers should be dismissed by election, according to the will of the workers.
INQABA:
What are the prospects for building trade union unity in India as a whole?
Sethi:
On the basis of our work in Faridabad we will try to form one trade union organisation all over India. I am working around Delhi but other people are organising the workers in every other part of the country. They are many and they are militant, but they cannot fight if they are divided. They will come together because they have similar ideas. When that happens we will form one national trade union organisation. That will provide the basis for a united political leadership of the working class.
INQABA:
What is the role of the present political leadership of the workers?
Sethi:
All the workers and the left should be united on the basis of a program and policy that is decided democratically. Every leader should be elected, from the bottom, to the city committee, district committee, state committee or central committee of the organisation. But at present the left parties are run by a dictatorial system. That is why there are splits. If there had been democracy in the party, there would be no need for splits. With democracy, the reformist leaders will be sent out because the working class want a militant leadership, they do not want reformists who cooperate with the authorities. The CP leaders have had many opportunities to build a mass revolutionary movement in India. But because of their policies they have always thrown these opportunities away. Instead they have taken their line from Moscow and betrayed the struggles of the Indian workers and peasants. The most notorious betrayal was in 1942-1945. At that time there was the ‘Quit India* movement to drive British imperialism out of India. The CPI opposed that movement, it opposed it because of Russia- because the Stalinist regime was in alliance with the British imperialists against Germany at that time. Because of its attitude to the independence movement the CPI was held in low esteem by the masses of India. If the CPI had been willing to support the struggle for national independence, then the workers’ movement would have become very strong, it would have led the national struggle. Instead, the people saw that the CP went against the movement, it was helping British imperialism. People were being hanged, people were sacrificing, and the CP went against it. Today the workers are very militant but the leadership is leading a princely life. The poor people are not able to eat; 70 million people don’t have houses but the leaders live like princes. How can it be possible for the people to believe in such a leadership? I can give you an example. In 1979 there was a one-day strike in Faridabad. This call was supported by all the left trade unions, so there was a complete strike. Everything was closed. The police prohibited any assembly of workers. We had a meeting already arranged but the police said, the order has been made so you have to leave this place. The workers said no. Then one of the police inspectors fired and a worker was killed. The workers then dispersed, and two workers carried the body away. The police inspector said, don’t touch the body, but they ignored him. Then he fired again and both the workers were killed. The other workers were watching this. After the police inspector fired, they ran at him and killed him. Minutes later, huge contingents of police arrived. They fired at the workers and more than 50 were killed. The workers had the support of all the people in the area. There was a mood of militancy. But this situation was turned into defeat by the leadership of the CPI and the CPI (M). The workers wanted to stay out on strike the second day but the leaders in Delhi said no, no strike. So the workers went to work. We were forced to go underground for three months. The workers said to me, what kind of leader are you-you tell us to go to work after 50 of us have been killed? I said, can there be a complete strike if only our union calls it? If the CP leaders ask you to work, can I alone ask you to strike? The workers were betrayed, very much betrayed. From that day the workers have been thinking very carefully before taking any action- whether under this leadership we should fight, or not.
INQABA:
How do you think the task of building the workers’ organisation can be carried forward in the period ahead?
Sethi:
I am going to collect 200 000 Rupees (R20 000) from the Escort workers for the purpose of organising the exploited, unorganised workers. We will ask 30 Rupees (R3) from each worker. We will explain to them that the unorganised are getting only 200 Rupees (R20) a month, whereas we get 600 Rupees (R60). We will explain that unless we can organise the working class in millions, there can be no social change. If this money is collected we can take on at least 15 to 20 full-time organisers. At present we only have 8 to .10 cadres working full-time for the union. In India the financial problem is a very big problem of trade union organisation. This problem has been caused by our leaders. Many of them are very dishonest. They have used the workers’ money for themselves. You have mentioned the problem of money and financial control, which is crucial lo prevent corruption in the leadership.
INQABA:
How do you tackle this problem in the union?
Sethi:
Our union is one of the most organised and financially stable in North India because we account to the workers, and the workers have control over the union’s finances. We show the workers every month, this is the income, this is the expenditure, and this is in the bank and in cash. We cannot draw more than 1 000 Rupees (R100) from the bank at once, and we cannot draw more than
3 000 (R300) in a month. If we need to draw more than 10 000 Rupees, the whole of the Executive Committee has to meet; and we have to get permission from a general meeting of the workers to draw so much money for such and such work. Then, if they give permission, the whole Committee has to sign. All these instructions have been given to the bank. This is the system we have. In the coming years we will have a very strong financial position. With these resources we will be able to meet our target of organising 100 000 workers.
INQABA:
We would like to turn now to the relations between India and the surrounding countries. A lot is said about the conflict between India and Pakistan. Can you give us your views on that?
Sethi:
Indira Gandhi says that we have a danger from Pakistan, and Pakistan’s Zia says that he has a danger from India. But Indira Gandhi has no danger from Pakistan, not at all, she is only making excuses to divert the attention of the people. The people are not afraid of Pakistan. The only thing the people want is to change society, they want to throw out the capitalists. There are so many struggles in different corners of India. The peasants have been fighting in Maharashtra, in Karnataka, in Tamil Nadu, in Haryana. They want lower prices, cheaper fertilisers, lower electricity costs. At least 100 have been killed. In Bangalore, 130 000 public sector workers were on strike for 70 days. They were only defeated due to a weakness of leadership. All these struggles are against Indira Gandhi, not against Pakistan. We need a national organisation to expand these struggles all over the country. There is no danger at all from Pakistan or China. The people are not thinking about it at all, they are only thinking about changing society.
INQABA:
What has been the attitude of the Indian workers’ leaders towards the struggles of the workers in Sri Lanka and other countries?
Sethi:
The more militant workers* leaders know the history of the revolutionary Sri Lankan working class, and know how the general strike was defeated. But the mass of the workers are not yet very conscious of the working-class struggle internationally. That is due to the nationalist policies of the workers’ political leaders. The CPI (M) and the CPI (ML) gave no help to the Sri Lankan revolutionaries at all. As for the CPI, it takes its line mainly from Russia.
INQABA:
We often hear about the caste system in India, which splits up the people and harshly discriminates against those who are born into the lower castes. How do you fight against this system in the workers’ movement?
Sethi:
Under capitalism it is very, very difficult to overcome caste divisions. Society is in such a form that caste differences are linked to economic and social privilege and power – The harijans (the lowest caste; the so-called ‘untouchables’-Ed.), for example, have almost no land, while the highest caste, the Brahmins, have among them many landlords and capitalists. But the workers’ leaders have failed to campaign on these issues, and so there is no clarity among the masses about the way in which casteism and religion are being used to divide and oppress them. In our agitation we concentrate on speaking against capitalism, why the workers are being exploited and how we can overthrow the capitalist system. When the working class takes power, casteism will be eliminated. But among the cadres we should always discuss these questions. We need to be clear about it at all times or we will have problems in the future.
INQABA:
Some of our leaders in the South African liberation movement still regard Indira Gandhi as an ally. She even gives out medals for the struggle of the South African masses. What is your comment on this?
Sethi:
Indira Gandhi did not fight for the masses, either in India or in South Africa, not at all. The working people of India are against Indira Gandhi. The people of your country should know this.
INQABA:
What do you see as the prospects for the Indian workers’ struggle in the period ahead?
Sethi:
In the next elections Indira Gandhi will probably win again because no alternative is being provided by the leaders of the left. If she does not win, then other rightist parties will come to power. But in the election after that, definitely we can come to power. By “we” I mean our organisations, like the CPI (M) and the CPI, when we have reformed them. The people will demand a leadership and a government that will make an end to the oppressive conditions of the capitalist system. We must use the time now to build that leadership. The conditions are very favourable. Thousands and thousands of cadres in the CPI, the CPI (ML) and the CPI (M) want to bring in their own revolutionary policies instead of the reformist policies of the leaders. If we can unite these cadres on the basis of a revolutionary programme, we can establish democracy in the parties and replace any leaders who don’t want to struggle for the demands of the workers and peasants. If this kind of party is formed in India, the left will be united, and a socialist government will be elected. It is possible that the capitalists will not give up their power peacefully, they will end democracy if they see that the workers and peasants will put their own parties in power. In that case there will be a fight. But with the revolutionary cadre united, and with the trade unions united, the revolution will be successful. The consequences of the Indian revolution will be very great. India is a country with the second-largest population in the world. If the revolution comes to India and capitalism is thrown out, the whole of Asia and indeed the whole world will be affected.
The things you have explained will contribute an enormous enthusiasm to the South African workers. Like the workers in India, we have the task of building a mass united trade union movement on the basis of a Marxist programme. We must do everything possible to link our struggles together, and with those of workers throughout Africa and internationally.
Trade unionists in South Africa who would like to get in touch with Comrade Subhash’s union directly can write to:
Subhash Sethi, President, All Escorts Employees’ Union, Neelam Chowk, Faridabad, Haryana, India.
* FMS – May 1983
Mr. Swraj Paul (1), a London-based citizen close to Shrimati Indira Ghandi, has stirred up trouble amongst the circles of local industrialists. Having his roots in the wealthy Amichand Pyarelal family, Swaraj Paul has become an English citizen. He controls the Caparo Group. The Caparo Group also owns 16 tea plantations in Asam. Swaraj Paul’s brother runs the APJ Company here in Faridabad.
In the current budget the Indira Gandhi government has dished out many offerings to the NRI’s. These ‘friends in the distance’ have replied to these offerings in the appropriate manner… Swaraj Paul has bought company shares from share-holding members of Escorts and DCM management. In a state of agitation the group around Birla-Jain-Modi-Shriram-Nanda has met the Finance Minister on 20th of April requesting, that the right of NRI to vote in share-holder companies should be abolished! So to hell with “Vasudeva Kutumb (2)”, what has become of the “Indian-ness” of the Birla friends?!
On 22nd of April we could see the troubled face of the Escorts chairman HP Nanda in the Financial Express. He announced that he would buy Escorts shares at all costs… Mr. Nanda said that those people eager to take-over Escorts are nothing but “money bags” who want to “trouble” companies which are run according to the national customs. So, Mr. Nanda, the aversion against “money bags” has now also entered yourself?! The pot calls the kettle black! And in regard to the “trouble”, Mr. Nanda, this is still the issue of the working class movement, isn’t it?!
Well, so trouble has broken out between “foreigners” and “locals” – and what do insecure wrestlers tend to do: they scream out loud. The BJP party-leader Vajpayee (3) met the Finance Minister on behalf of Birla and Nanda. A member of the Congress (S) asked the government during a session in Parliament to stop Swaraj Paul creating trouble in 300 factories! The Haryana Government announced through a district judge that it will make use of the National Security Act against Mr. Paul – based on the fact that he is a social enemy, a national enemy… Mr. Nanda, why don’t you throw Mr. Swaraj Paul into jail under the National Security Act – after his leave for London he seems to have forgotten that there are laws allowing to lock people up without trial!
On the 30th of April the Economic Times printed the declaration of ten senior MP’s of Indira’s Congress – denouncing Mr. Swaraj Paul to spoil the game. Factions are competing, and the niggling continues. Rajeev Gandhi and the Central Finance Minister position themselves in the middle… In the meantime Mr. Paul said in an interview with a London-based newspaper that he has invested capital after having been instructed by important people in Delhi – ‘in the interest of Hindustan’. He will make use of his shares of Escorts and DMC in order to give a push to the big corporations in Hindustan, given that most of the owners of big companies in Hindustan have actually invested very little themselves. Mr. Swaraj Paul said that he will free those companies from their feudal roots…
Obviously, in the majority of companies, banks and insurance, ‘state capital’ has the dominant position. Nevertheless these companies are categorised as ‘private’. These companies are managed by Birla-Tata-Modi-Nanda tycoons, whose shares constitute only around 10 to 15 per cent of total capital. A company of one crore Rs share-capital takes out tens of crore Rs of credits from the banks. In this way, the money of Birla-Tata-Modi-Nanda will amount to less than one per cent of the total sum invested in the company (Sanjay Gandhi, who holds 3,000 Rs shares runs Maruti, a three crore Rs company).
Mr. Swaraj Paul has bought one or two per cent of the shares of Escorts and DMC and… he has become part of the management. If the state-leaders want him to, he will take-over the leading position. There is another clear issue. The managing figures within Escorts and DMC will – now more than ever – try to intensify their good relations with the Delhi political class… the financial offerings will increase. This is the actual meaning of Swaraj Paul’s ‘putting an end to feudalism in companies’. Mr. Swaraj Paul has made Birla-Tata and friends realise the power of state capital, the power of Indira-Rajeev Gandhi. This is the current motive behind the wrestling.
(1) http://en.wikipedia.org/wiki/Swraj_Paul (in October 2010 he was suspended from the British House of Lords for fraud)
(2) Hindu concept meaning that the world is one family
(3) http://en.wikipedia.org/wiki/Atal_Bihari_Vajpayee
* FMS – June 1983
From speculators at the Delhi Stock Exchange: Escorts chairman HP Nanda went to London to meet Mr. Swaraj Paul. Swaraj Paul bought thousands of 10 Rs-Escort-shares for 40 to 80 Rs each. Initially Nanda had offered the shares for 150 Rs each. Paul replied to Nanda by making following offer: Sell me all the shares you have for 200 Rs each. Given these large amounts of money, the Escorts workers are able to guess how much they are exploited. Swaraj Paul, a person close to Indira Gandhi, continues to put pressure on Escorts and DMC.
Nanda-Shriram and friends acknowledge the declarations of the government – Capitalists know their governments, therefore they don’t sit back and tighten their belts, no, they move their fat bellies and join the struggle over influence. Workers can take this as a lesson: they should give up their believe in the capitalist government’s promises. Obviously, behind all the chitter-chatter hides this main question: for whose private interest and to which extend is state capital employed. Therefore there is no clash between Birla-Tata-Modi-Nanda and Swaraj Paul. Their opponent is the head of state capital, Indira Gandhi. Nanda or Swaraj Paul? Whoever will benefit her more, will have Indira Gandhi’s hand in his back. Once either Escorts or DMC is handed over to Swaraj Paul there will be sweets in both of Indira Gandhi’s hands. From now on Birla-Tata-Nanda will be found more often in the palaces of state power – there will be more bribes changing hands.
Workers should take advantage of the in-fights between the different representatives of capital. This is a great opportunity for Escort workers to enforce their demands. Hence, it is time to put pressure on management through organised struggle, but the union leaders are entangled in a low level quarrel among themselves.
* FMS – October 1983
It has been an intensive week since the hunger strike of two dismissed Ford workers started on 23rd of September. The Ford workers have demonstrated a great unity and the workers in the second Ford plant have started to show on which side they are. But the Ford union leaders break the Ford workers’ eagerness to struggle by spreading the following wrong reasoning: if you fight back you might get hurt… so give up all this talk about struggle! On the eighth day of the hunger strike the leaders turned from being ‘peaceful’ to being ‘revolutionary’ – they stopped the demonstrations and the ‘lunch and tea’-boycott of the Ford workers! Instead of relying on the strength of the Ford workers the union leaders hope for miracles. And then suddenly they order to pack up the sleeping-mats of the hunger strikers on 3rd of October.
After having finished off the hunger strike, suddenly started to stir up trouble. Beatings in the Ford plant are followed by arrests of dozens of workers and the situation finally ends in a lockout.
Congress vultures turned all of a sudden pro-worker and bailed out the arrested Ford workers. The current situation, the conflict between Nanda management and other factions, are a golden opportunity for Congress to portraty themselves as ‘workers’ supporters’. These “workers’ supporter”-vultures of the Congress might bail out Ford workers, but are not bothered about the JMA workers being still in jail. How could they?! The order to put the JMA workers behind bars came from their INTUC [Congress Union} brothers.
DCS, PD, LC are experts in opportunism. In the current period the skills of these representatives of capital are coming into full bloom - the local lord is Nanda, but the main parental-power is Indira. Nanda's current interest is to keep 'peace' at Escorts, while Indira and Swaraj Paul are interested in 'trouble'. The bosses are solving this contradiction in an excellent manner. Presenting it as an 'external constrain' the 'peace-keepers' create 'controlled trouble'. The representative of the state are actually more 'militant' than both union leaderships: more than the leadership of the Escorts Union, who has been turned into Nanda's pawns and who preach that 'we have to keep the peace, because it is time for re-negotiating the agreement [collective contract]‘; and more than the leadership of the ‘troublemaking’ Ford leadership, who became pawns of Indira and Swaraj Paul.
Whoever portrays factions of the state as being ‘on the side of the workers’ has also to talk about the involvement of the state’s ‘law and order’… about the Atul Glas workers who have committed the crime to form a union have been stripped naked and beaten up in the police station; the lathi-attacks to prevent workers from holding meetings; the arrests of JMA Atul Glas workers, who were held in custody for four days without arrest notice. The police make sure that the Escort issue ‘is kept completely within the realm of the law’. To stick to the capitalist law in times when the bosses are in struggle with each other is hard work for the state representatives: “It is the order from above, what can we do, we are forced”…
* FMS – November 1983
In Faridabad, the struggle about the take-over of Escorts, which has erupted between the advancing Indira-Swaraj Paul faction and the Nanda clique, is heating up. Here the Indira – Swaraj Paul faction turns the Ford Workers Union leaders into their pawns, while Nanda does the same with the Escorts Employees’ Union leaders. At this point of time the main struggle at Escorts is not about the agreement. It is neither about the two leaders sacked at Ford. Neither is the struggle against the All Escorts Union leaders – so unpopular figures among the Ford workers – currently the main question at Escorts. Nevertheless, some stupid elements have used these questions to get workers entangled in a fight between each other: workers at the Ford plant on one side and workers of other Escort plants on the other side. At this point of time the struggle between Indira-Swaraj Paul and Nanda over Escorts is the central point of development and main concern at Escorts. To take advantage of the exploiters’ weakness – their factions being locked in a tug of war – is the workers’ task of the hour.
* FMS – January 1987
Leaflet of the Escorts Union Leader Subhash Sethi
When the struggle about the take-over of Escorts between Nanda and Swaraj Paul was still in full swing, the local trade union backed Nanda openly. During the peak-time of the tug-of-war over Escorts, the time came for a new three years agreement between management and union. The union presented a proposal to the workers: 20 per cent workload increase for a wage increment of 191 Rs per month. The workers ripped the proposal into pieces and demanded an agreement without inscribed workload increase. The union then proclaimed that they had achieved an agreement which would guarantee more money without higher workload – and they sold this to the workers as the most marvellous agreement under the sky of workers’ rights. Finally the Nanda management reclaimed the control over Escorts. Immediately after the successful re-instatement of Nanda management, both management and union told the workers to fulfil their part of the ‘whole agreement’: the wonderful agreement, which had guaranteed wage hike without asking for more work, contained I.E. Norms. And I.E. Norms meant that the workload of the Escort workers would be increased by 30 per cent. Facing this fraud, and given that they had turned a 20 per cent work-load increase agreement into shreds, the outburst of workers’ anger was not surprising. When the workers spat on an offered sweetener of 50 Rs wage increase, the union started to enforce the management’s policy by using threats and measures to create divisions among workers. When the workers faced a 30 per cent work-load increase the main union leader of Faridabad came out with a leaflet, with the headline “Two Issues”, which was distributed amongst the Escorts workers. The union leader’s [Subhash Sethi] leaflet reads:
“You can refuse the proposal for the agreement… but what right does exist to accuse leaders to have mingled with management… during the last negotiations the issue of 20 per cent production increase came up and you refused the issue, and we accepted your resistance. We then settled an agreement about the I.E. Norms and you were informed about this. Here and now we refer only to the decision about this issue, we don’t raise any new issues here.
It might well be that you have misunderstood things, we will have to explain to and understand from each other. “…but why all this general talk here”, you might think. “Why all this nonsense talk”, you might ask. “He is talking, but he does not say anything, and then he will complain again that all workers say that union leaders and management have mingled. Why all this double-faced attitude? Say what you want to say, speak straightforwardly. Unsubstantial nonsense-talk will not be tolerated. And we will have to find ways to deal with all this.”
Last year we have settled a mini-agreement. In this agreement the production increase was inscribed in ‘increase per cent’, but it failed. Now the management raised again the demand of production increase, again in terms of ‘percentage’. But one question comes up: if we apply a ‘percentage increase’ then those people who currently work 3 to 4 hours per shift will have to work only 40 to 45 minutes longer. Those who already work 6 to 6.5 hours will have to work 7.5 hours. The question has to be raised how this problem can be solved. One solution would be that those who work less will have to work the proper hours while those who work the full amount already, will not be bothered.
So now please tell us, should we have accepted the IE norms or not? Some were not accepting it. We – the union – thought that, alright, give us 50 Rs wage increase in the name of I.E. Norms. The management did not agree to this at all. Some people said at this point that “together with the I.E. Norms there will be a major increase in production targets”. Relating to this we told the management, that if there is a production increase, there should be a wage hike, too. So the management presented us this scheme. We did not agree to this scheme, but given that the I.E. Norms have to be introduced and that the workers should get something out of it, we thought that there will be no harm… Now, you will say: “this scheme is nothing else than the I.E. Norms in disguise”.
If you will not accept this agreement either, then you will have to accept that those people who work only 3 to 4 hours will continue to do so and those who work 6 to 6.5 hours will do so, too. Now you might reply that we should stop all the talk about I.E. Norms altogether, that the demands of the last settlement have been fulfilled from your side. The management will use this attitude of yours in order to obstruct the next settlement. To sort this out will take two months and the new settlement will be useless by then.
Now the question is: what are I.E. Norms? The management might have their position on this, but that does not mean that our union will have to agree. Our union delegates will see and find out how much work a worker is able to perform during 6.5 hours. Our union delegates and representatives of the management will meet and come to a decision about this. The norm that both sides agree on – which will have to be accepted by the workers – will be the I.E. Norm. You will receive 50 Rs wage hike for the I.E. Norm, if you will fetch more than that, that should be alright, and you should not worry about getting less than this. It is our task to establish the I.E. Norms, and in return there has to be a good settlement. Some people might now think that they could just work less during the I.E. Norms establishing process, or to create trouble. This was the case at Escorts plant in Bangalore – but go and ask the union leaders at plant 1 about the current conditions of the workers in Bangalore, these leaders have seen them with their own eyes. You will have to work double as much and will not get any wage increase at all – this is exactly what has happened in Bangalore.” [End of leaflet]
* FMS – March 1987
Three years agreement
At the beginning of every year Escorts management deducts the union dues from the wages of all workers and hands them over to the union – nowadays the annual dues amount to more than 200,000 Rupees. The last three years agreement between union and management is an example of how workers have to pay. Referring to the ‘last agreement’s conditions’ management and union asked workers to accept a 30 per cent increase of the work-load, which resulted in the workers becoming even more suspicious towards the union. Given this suspicion of the workers, the union did not manage to get the workers drawn into the whirls of their usual routine mobilisations, such as symbolic strikes “because the management is not willing to negotiate” – routine mobilisations, which, like at the moment, take place before the finalisation of a new agreement. When ordinary workers started to take the piss out of the union leaders cunning tricks, the union came up with their own remedy. Suddenly the union announced that in a struggle over life and death they have settled an agreement, which would guarantee the workers a 301 Rs increase of wages. For the desperate workers this was a rather surprising announcement – and the agreement received a nice applause.
But nowadays Nanda management is not engaged in any ‘internal’ struggle like during the last agreement, when the fight with Swaraj Paul was going on. Therefore it took less than a month before the workers had to face the truth of the current agreement. Shortly after the announcement workers were told that a further 50 to 80 per cent workload increase will be attached to the increase of wages. And the management in each plant made clear that the workers will have to meet the new targets first, before getting more money count in their leisure time.
The Escorts workers did not openly lament against this agreement, but in their groups they undertook steps against it. In all plants the maintenance workers strengthened their opposition against the agreement and formed collectives against it. In the third plant some department workers interrupted production and on the 28th of March in the Ford plant workers stopped the entire production acting against the agreement.
Here are some sections from the union-management agreement:
10. b) The union and the workmen agree that they will accept the production level defined by management and that they will undertake the effort to meet it.
c) If any workmen fail to meet the production level defined by management or are found being absent from their workplace, then the ‘no work no pay’ rule is applied.
e) …the union accepts that the company has the right to set time standards for different work tasks and methods. The workmen will deliver performance according the time standards defined by the company. The union also accepts that the time standard at one point defined by the company can be altered if there are changes in the production system, in the material or product, in machinery or tools or jig fixture, or any other factor which has an impact on the production system.
f) For production and productivity reasons a worker can be shifted from one machine or work station to another. If according to his skills the worker is able to run another or several other machines then the union will not interfere with or obstruct the worker being employed at this machine or these machines.
11. Whether the full amount of the wage is paid to the workmen will depend on the condition that the minimum production target is met, which is defined in the efficiency scheme.
* FMS – December 1988
Escorts: In Faridabad’s main company an incentive scheme has been introduced, based on last year’s agreement between management and union. Initially the workers were enraged about this work-load increasing scheme – but then, once earning two Paise extra, they only swore a bit and joined the scheme. Once the incentive scheme runs, the workers turn blind and drudge on. After only ten months the workers had already fulfilled the annual production target. At the beginning of November 5,500 Rajdoot motor-cycle stock started to pile up at the second plant. The situation is more or less the same at the tractor plant.
In this way ‘lay-offs’ entered the agenda of the management. The fact that now there is talk about a slow-down strike coming up, is not seen on the background of the looming lay offs. To suddenly come up with demands about pensions and to make workers engage in a slow-down can only be a measure to pull the wool over workers eyes. By having met the 12-months target in 10 months workers have handed over a sword to management, a sword to tackle and cut down 20 per cent of superfluous work-force.
* FMS – April 1989
Chess-Board Struggles
At the beginning of March, news about a “marvellous” agreement – all for the benefit of the Escorts workers – were published in the newspapers. In fact it was made to be published. But the Escorts workers were not too happy about this “marvellous” agreement, which the leaders had made ‘in the interest of the workers’. The same “marvellous” words were used during the 1986 agreement – which was forged in 1983 during the chess-board fights between Nanda and Swaraj Paul and which brought the I.E. Norms into effect.
Back then in 1986, the Escorts union president got enraged and threatened the Escorts workers in a leaflet named “Two Issues”. In the arbitrary name of I.E. Norms the work load of the Escorts workers had to be increased by 30 percent – and in the end the management and union leaders were able to force it upon the workers. The three-years agreement of 1987 again meant an increase of the workload for the workers – this time in the name of the incentive scheme. The Escorts workers verbally protested also against this agreement, but together the management and union were able to enforce it against the workers. For more and more incentives [productivity bonus] the Escorts workers started to speed up their work, exhausting themselves, shortening their lifetime. The workers, already running out of breath, had to face yet another “marvellous” agreement, which union and management put on their shoulders within less than a years time.
The incentive scheme ‘proved’ the management that the workers can easily work even more and that, up to now, they had intentionally worked less than they could. The Escorts union leader-ship agreed with the leading management – in their “Two Issues” leaflet distributed during the time of the I.E. Norms agreement they said: “Some people might think that they can work less and cause trouble… but in the end you will work double as much and will get nothing in return”. And the same union president, in order to enforce a 15 per cent work load increase, told the workers in March 1989 in a leaflet: “You will now say that we keep listening to the wrong advisors and that we should ensure that you will keep getting everything without being compelled to work a little bit: Then sorry! Such kind of leadership will not be given by Subhash Sethi!”
We actually do not know who is doing the wrong thing – the guy in the fine dress driving around in a car, agitating people; or the worker who uses the bike, wears blue-collar and drudges at his or her machine. But one thing is clear, that management and union have made the decision to threaten the Escorts workers. Having toughened the incentive norms, management will pay less for the workers, while at the same time they have increased the workload by another 15 per cent. In the last six-seven years again and again the Escorts workers and the union leaders have confronted each other over each and every main issues. It is clear that either the Escorts workers are to stupid to know their own interests; or the union leaders are wastrels who, in the name of the favour of the workers, do everything for the good of the management.
* FMS – July 1989
Union election
When out of the 12,000 members only 17 followed the call to come to the Mayday meeting, the union president made this the issue for his resignation. The actual issue is that during the last six to seven years the union has played a supervising and co-managing role when, under this pretext or the other, the work load of the workers has been increased. Therefore the union has lost its trust and credit amongst the workers. In the interest of the leadership of both union and management, something had to be done about this lack of credibility. The resignation was a step within the attempt to restore the credibility. The election of a new leader-ship was announced. During earlier elections it happened several times that the leadership had declare its resignation only in order withdraw it again shortly afterwards. This time they try to prevent this by ‘proper elections’, but actually the elections were hardly more than a drama. All leaders and their muscle men created a lot of pressure in order to prevent people from voting, and this actually made an impact. Nevertheless, 3,300 votes were counted and a new leader-ship elected.
* FMS – February 1990
Compulsory Pension Fund
The public workers got a little agitated about the current wage re-vision, they created a lot of fuss about the state’s announcement to transfer the outstanding wages – outstanding at the time of the wage re-vision – and the Dearness Allowance money into a compulsory public workers saving account. The government does not justify this compulsory saving scheme by saying that it is in the interest of the workers. The government says that it is forced to introduce it, it cries tears about having its hands tied. But look what’s going on here at Escorts.
In the name of the pension scheme the middle-men at Escorts do not just force the workers to pay into the scheme, but they directly cut money from their wages. Furthermore, this deed is portrayed as being a step in favour of the Escorts workers. This is published all over Faridabad. Lies don’t know any limits.
Every month Escorts deducts 125 Rs from each worker’s wage and pays it to the insurance. We do not know who will put commission-money from these crores Rs of insurance money into their own pockets, but fact is that the business of insurance companies is profit business and that in this case they extract this profit from the workers’ wages.
The Escorts pension scheme is actually a reduction of workers’ wages. Even according to the government’s own standards, a monthly wage of 3,000 Rs is hardly enough to fill the stomachs of a three-member family. Therefore, those who force us to cut money from a 1,500 Rs wage by beating the drum of a golden future actually make our black present even darker. And how should there be a golden future? One glimpse at the current Provident Fund policies is sufficient to see that if workers want to get their deposited money they have to pay bribes. In reality the Escorts pension scheme is a management scheme. Escorts biggest share-holder, the public company Indian Life Insurance Neegam (Bhartiy Jivan Bima Neegam) is already making money from the scheme, Escorts company also will use the gathered money of the workers, will invest for their own profit it and/or use it as credit.
* FMS – April 1990
Temporary plant closure
Since 23rd of March, production at the Escorts plants in Faridabad and the Yamaha plant in Surajpur has been stopped. On 23rd of March, 2,000 casual workers have been kicked out from their jobs. About 12,000 permanent workers will only get 22 days of wage paid for March. On 5th of April, the printing time of this issue, the production at the Faridabad plant was still down and the workers in a state of confusion. According to their business figures these are good times for the management – so why the production stop? In order to understand the management’s plot behind the decision to stop production for 14 days which produces more than 2.5 crore Rs per day, it is necessary to reflect on some facts in detail. The statistics we have taken from the management’s publication “Escorts News”.
In 1986 the production of Escorts was 382 crore Rs, in 1987 it was 482 crore Rs and in 1988 it was 600 crore Rs. Instead of taking January – December period as bases for their calculation of 1989 production they referred to the financial year period from April till 31st of March, meaning that they took a total of 15 month of production into account for 1989. From January 1988 to March 1989 the production was 783 Rs. The managing chairman told the share-holder meeting on 20th of September 1989 that production during the five months period between April to August 1989 was 308 crore Rs, which is a major jump compared to the 248 crore Rs during the same period in 1988. The profits in the April – August 1989 period were 80 per cent higher than those of the some period in 1988. And management and middle-men preach that Escorts workers work only four hours a day!
Given that their propaganda has an affect on some workers we refer to the figures given by management to the capitalist listeners, so that people can have a look at the bare facts. Obviously, from a superficial point of view in a production process, which runs in quick succession, any ‘resting’ workers look like they are idle. Actually, these workers subjected to the speed of work drown their mental and physical health – one expression is the increase in alcohol and gambling.
Well! In the Times of India of the 3rd of April 1989 it said that, according to a spokesperson of the chairman, the management proposed a 50 per cent increase in production – instead of a yearly production of 775 crore Rs an annual production of 1,200 crore. The management and the chief of their middle-men announced that he and his comrades are ready to increase the workload in order to obtain the 1,200 crore production… but management has to pour some sugar on this poison in order to enable the middle-men to get the 1,200 crore annual production down the workers’ throats.
After 18 years of increasing the work load, the collaborating union and their honoured management know very well that some minor incentives won’t do in order to further increase the work load: they will have to take more drastic measures against the workers. The current mini agreement which enforced 15 per cent workload increase and which was accompanied by speeches of the union middle-men, saying that there won’t be any further increases in the future, are recent events. Therefore, in order to grind workers down and to make them ready for the increased load, the management and middlemen arranged the drama of shutting down production on 23rd of March. Those 12,000 workers, who produce 20 per cent of all tractors and 40 per cent of all motor-cycles in India, have to face up to a serious issue.
* FMS – May 1990
Workers refuse agreement
The management and their middle-men announced the restart of production for the 20th of April, putting an end to their drama of shutting down production, which started on 23rd of March. In the last issues we had a look at the reasons behind this drama, based on the written announcements published by management and their middle-men: “In order to prepare workers for a 50 per cent workload increase, management and middle-men arrange this drama”. But this time the announcement that production would resume on the 20th of April, which was made by management middle-men during a meeting on the 19th of April, was torn to pieces by the Escorts workers. On 20th of April restarting production was not on the agenda, most of the Escorts plants were not even cleaned. It seems that the alliance of management and union middle-men, having their true pretensions revealed, will have to hurry up and get their own hands dirty.
Being irritated by the unaccomplished re-start of work the union middlemen called for another meeting on the 20th of April. Despite the drama staged by the union chief and his followers the workers could not be moved. For the first time since the events at Ford in 1983 the attempt of the union middle-men to silence the Escorts workers by threats and attacks failed. Despite being beaten and kicked the workers raised their hands against the 50 per cent work-load increasing agreement – those who raised their hands in favour of the agreement were mostly office staff who would not have been affected by the work load increase. The Escorts workers stand firm to oppose the workload increase. Having expressed their anger the workers also managed to extol money for the work (un)done in March.
* FMS – July 1990
Word games
The representatives of capital in India are experts in word games. English being the business language for the upper ruling layer, this game is their daily bread. In Faridabad there are two recent examples of how the representatives of capital use the ‘trap of words’ against workers.
In order to quell the initial collective steps of workers’ resistance at East India Cotton Mill, management suspended several workers in the power-loom department in December 1989. After six month of ‘investigation and inquiry’-drama around the question of suspension, management and workers were getting soft. Management told the suspended workers that they could be “dismissed”, but that they will actually be “discharged”. In this way, the power-loom workers at East India Cotton were sacked by management. In order to explain the mighty difference between ‘dismissed’ and ‘discharged’ capitalist scholars might meet you in that matter, but if you need a legal decision then please wait for the decision of the supreme court via high court via labour court – which, first of all, has to make a case concerning ‘dismissed in the name of being discharged’, which needs a decision of the supreme court and so on. Escorts management makes use of the mighty difference between ‘discharged-dismissed’, too.
At Escorts, nowadays workers do not work ‘over-time’, they do ‘over-stay’. You don’t need a Plato to explain the difference between ‘over-time’ and ‘over-stay’. For the Escorts workers the difference between these words is so big that an elephant could pass between them: for over-time double-rate was paid, while for over-stay only single-rate is given. Obviously, the law which fixes double rate for over-time is rather old. Most capitalists in Faridabad break this law without any shame – by changing hours in the over-time register etc.. But Escorts is a reputed and famous company and there are so many people employed in the middle-management strata that the top management does not dare to engage in such blunt swindles. But then Escorts is forced to make workers work over-time and they have to pay less for it – what has to be done? Together with the union the management made an agreement that at Escorts there will not be any over-time, instead workers will be stopped from leaving after their duty-time in order to work and they will do ‘over-stay’, paid at single rate.
* FMS – November 1992
In hundreds of small factories in Faridabad work for Escorts is done. Thousands of workers working in these factories are usually not paid according to the minimum wage fixed by the government. In the Escorts plant itself there is a notable amount of casual workers and workers hired through contractors who work extremely hard for very little money. And then there are 14,000 permanent workers, who have been subjected to a continuous series of workload increases issued by management-union agreements. These conditions have the combined effect that in the last ten years the business of Escorts has increased four fold, which amounts to an annual production of more than 1,200 crore Rs.
Normally the workload increase is accompanied by a nominal wage increase. But the real purchasing power is constantly falling. In this way the real wages of the permanent Escorts workers, like the wages of other workers in India, have fallen continuously. The reasons for taking an additional part-time job, to work over-time, to let children and wife run a shop, has to be found in the fall of wages. And concerning the right to leisure-time: workers would be shocked if they’d compare the official 60-70 years old laws and their reality.
Normally the statutory bonus is paid on company or factory level. Despite the fact that within Escorts there are various ‘Companies Ltd.’, bonus had been paid on the bases of the All Escorts Group as a whole. But this year there has been a change. ‘All Escorts’ is finished and the bonus payment on plant level has also ended up in the furnace. In the Escorts Plant I bonus is paid on department level. It was announced that workers in some departments get 20 per cent, while other get only 8.33 per cent annual bonus. Furthermore, while the 20 per cent bonus was paid on Diwali, the people who are paid 8.33 per cent received only 500 Rs as an advance payment. In the Motorcycle Division Rajdoot, Plant II) management announced the same thing: only 8.33 per cent, only 500 Rs advance. The Escorts management uses their union middle-men to whitewash these dangerous procedures.
Managements of other factories are not far from following the example given by Escorts: separate bonus for different departments. New machinery, difficult situation on the market, tight financial conditions: Escorts management plans some new and major attacks on the permanent workers at Escorts. To only swear at the union middle-men will not be a sufficient response, neither will a physical attack change anything.
* FMS – February 1993
Crisis kicks in
After the motorcycle department, now the tractor division is in trouble. The market slump gave Escorts a blow. The management reacts by cutting production, in one plant it is down to a half, in the other to a third of the normal level. Instead of two or three shifts only one shift is run. In addition to Sundays there are one or two more days off per week. The incentives [productivity bonus] drop. Permanent workers having to pay their instalments for their house-TV-fridge have to reduce their food to dal and roti. The supplying small factories and workshops are in trouble, too. There is less work and Escorts payments are delayed: Escorts pays only after six months, instead of every three months. The vendors at the Ford plant are only paid after 9 to 10 months. The situation of workers employed on 12-hours shifts in these smaller factories and workshops go from bad to worse.
Given the generally bad economic situation at Escorts, the internal wheeling and dealing of the Nanda management comes to the open more quickly. There are talks about the damaging impact of ‘corrupting relations’ on the company, e.g. there are fights between the sons of the chairman and other stories follow in rapid succession.
The situation in 1993 will be very complicated. The managers themselves don’t know what is going to happen. Insecurity is a normal atmosphere at Escorts. The sometimes 5,000, sometimes 8,000 casual workers know this atmosphere already, so do the workers hired through contractors; now 11,000 permanents and 3,000 staff and 800 managers know it, too. All Escorts Group wants to sacrifice 30 per cent of its work-force. On the Escort agenda is the dismissal of 3,300 permanent workers, 600 supervisors and staff and 240 managers. To blame this or that person for this situation only means to disguise the actual reasons.
Escorts is not an exception: in Italy thousands workers, managers and supervisors are laid off. It becomes necessary to look at the deeper reasons behind the possible lay-offs at Escorts. Individual workers have been replaceable and secondary, now managers and supervisors have become secondary, too. Nevertheless, managers and supervisors normally see the current system as being in their interest. Don’t the facts contradict this view? What does it mean that – once it becomes a ‘necessity’ – managers and supervisors are thrown on the scrap heap like unnecessary parts of the machine? Do these ‘necessities’ not increase on a world wide scale? And the issue does not confine itself to the workers. You might be a chairman, a managing director, a chancellor or prime minister: in front of the crisis of the industrial market system they are all helpless.
Having become parts of global competition means that in terms of their quality there is no difference between socialist, progressive, nationalist, culturally conservative or governments of other labels. There is only a formal difference: between the 60,000 lay offs at computer-giant IBM since 1986 (and the plan to sack another 30,000) on one side and the usage of armed police to quell workers resistance at Hyundai Heavy Industries in Korea on the other – the methods are different, the essence is the same. Behind their various veils the actual differences between Thatcher and Major, between Indira and Narasimha Rao, between ‘shining’ and CP political leaders are neglectable. So is the difference between the work of a highly paid genius, specially hired to run the company, and the old men of inherited family business with their rather general experience.
Production cuts, lay offs, reduction of wages and benefits, workload increase, continuous automation, growing numbers of unemployed – it might be Japan or America, Germany or Russia, Korea or India, the melody-rhythm of this lullaby-truncheon is present everywhere. General Motors is sacking 74,000 production workers in its global manufacturing units. There is the saying that what is good for General Motors is good for America (it is self-evident that workers are not part of this ‘America’). Having given the waking call of industrial revolution and it’s coal-steam force to spread around the globe, the English government has recently sacked 40,000 workers from the coal mines and moves heaven and earth to layoff another 30,000. Having used brute force to mitigate unemployment and to climb the ladder of development, Russia now makes big sacrifices to the crisis, which, apart from the usage of brute force, puts things topsy-turvy. The same process is happening in Vietnam and China. The seemingly solid foundation of the public sector has turned into a difficulty for the Indian government and the discussion about ‘privatisation as being the remedy or not’ continuous, despite the fact that it has ceased to say anything.
In this context of the fundamental issue the particularities become secondary. The company particularities become secondary. National particularities become secondary. In the times to come this fact will become more and more noticeable.
So should workers, should humans put their hope into ‘individual particularities’ when looking for a solution to their problems? Is there a solution on the level of ‘company particularities’? And can there be a solution to workers’ problems, to the problems of human-kind on a national level?
According to our understanding
After five hundred years of creating stronger ties and links day by day, the global market has now obtained a concrete form. Production for the market is now established on a world scale. All elements of human life are now controlled by the market or are affected by it.
Profit and competition are two essential elements of production for the market. Given that the market is now a global market, both profits and competition are now relating to a global level. It is for this reason that governments, which came to power because of their popular stance, might suddenly be forced to undertake unpopular measures. It is for this reason that companies – booming in terms of local competition and leading in terms of the national market – suddenly start to tremble. The new economic policies of the Narasimha Rao government and the collapse of Gedore Handtools company in 1982 to 1984 are current examples.
But to reduce production temporarily instead of increasing it; to take measures to cut losses instead of making profits; and to intensify the struggle over subsidies are becoming world-wide phenomena which make the fact more prominent that production for the market is prone to crisis. The path of fulfilling human needs through production for the market has become undermined. To leave human needs unsatisfied while cutting production at the same time… what is this about?
There is no lack of raw materials, no lack of machinery, no lack of people able to work… and reduce production! Lay people off! Cut wages! Drive forward automation!
America-Japan-Germany-Russia-England-India-China-Brazil-Egypt-South Africa: the wheels keep on turning faster and they run off track. The crisis is omnipresent and deepening. In order to overcome the crisis governments and managements in each country and company turn workers into offerings to be sacrified – as a result of which we seen two world wars and dozens of other wars in this century, killing 15 to 20 crore people. The devastating argument to save the hand by cutting off the fingers is established widely.
Today we do not face the problem of not being able to produce. The problem is that we produce for the market. From the issues mentioned above it becomes clear that the production for the market has entered a dead end and has turned increasingly anti-human. Therefore the search for an alternative to production for the market is an urgent agenda. This is where a solution to our problems can be found.
Once having broken the ties of production for the market and advanced on the path of a production for human needs, we will be able to build true relationships between individuals, as a society, with nature.
Be it the workers at Escorts, the mining workers in England, the General Motors workers in America or the steel workers in Brazil – the problem is identical. Not only that, the root problem of all workers is identical. Therefore we might struggle against the layoffs at Escorts or against wage cuts in Australia, the focus of our struggle should be to end the production for the market.
* Escorts economic situation 1998
EPW no. 4, 1998
With a view to concentrating on its core business of manufacturing and selling agri-machinery, the company undertook a major restructuring exercise during 1996-97 which involved divesting its piston and motorcycle businesses. The company’s automotive pistons business was divested to Escorts Mahle – an equal joint venture with Mahle GmbH (Germany) to enable this activity to access the latest technology vital for growth and expansion. The Rajdoot motorcycle manufacturing business too was transferred to Escorts Yamaha Motor on conclusion of negotiations with Yamaha Motor Co, Japan, while automotive shock absorbers will be transferred to a joint venture company with COFAP of Brazil. COFAP already has a large share of the international market in this field. The tractor market remained firm and Escort’s FARMTRAC brand maintained its leadership position in the market in the segment of 50 HP and above. While total vehicles sold increased from 2.28 lakh to 2.79 lakh vehicles, representing an increase of 22.3 per cent, sale of two-wheelers touched 2.36 lakh units while that of tractors touched 42,234 units as against 21,415 tractors sold last year. The company sold 4,349 more ESCORT brand tractors during 1996-97 than in the previous year, representing an increase of more than 20 per cent. With a view to upgrading the quality of its products to bring them on par with international standards, the company is now forging alliances with international industry majors in the field of engines, transmissions, hydraulics, etc. Escorts plans to set up a joint venture with Carraro SpA of Italy for manufacturing axles and transmissions for tractors, construction equipment, etc. In addition to introducing a special range of tractors from 60 to 85 HP, Carraro will support Escorts to upgrade its axles and transmissions for its full agri-machinery range including those that are currently being produced. The company fared well both in the domestic and export front. The export demand for tractors is expected to be in the region of 15,000 per annum, which is likely to materialise in the next three to four years. In order to meet this demand the company now plans to set up a new generation manufacturing unit near Pune at a cost of Rs 175 crore. This will be financed through internal resources. The company also plans to enhance the combined production volumes of all its tractor plants at Faridabad and Pune to 80,000 units per annum.
* Self-Activity of Wage-Workers: Gedore Jhalani Tools
Kamunist Kranti/FMS, 1998
Background Gedore Hand Tools, headquartered in Germany, had three plants in Faridabad exploiting 3500 wage-workers. U.S.A was a major market for its produce. Hand tools enterprises located in China and South Korea were Gedore’s market competitors. Shrinkage of production in the auto and engineering industries in the early 1980s sharpened the competition in the hand tools market. In this scenario, in order to maintain its competitiveness, Gedore management planned a major intensification of work through automation and large-scale retrenchment. For installation of an automatic plating plant Gedore management took a loan of Rs. 2.5 crores (~ $2.5 millions) from the Industrial Development Bank of India, a government of India enterprise.
The unfolding of events
In the beginning of 1982 incidents of chargesheeting, suspensions, transfers from one department to another, shifting workers from one job to another, wage-delays, downgradation in canteen quality, insistence on quality in production, strictness about production targets, time strictness, no rest during shift hours etc. increased noticeably.
In a gate meeting on June 7, 1982 union leaders spoke at length about capitalism, global crisis, company in crisis, and then asked the workers to make sacrifices in the larger interest. They put forward three alternatives to choose from:
- 25% reduction in wages.
- Go on special leave for six months at half wages.
- Retrenchment of 600 workers.
Workers rejected outright all these options put forth by the leaders. At this rejection, managements’ escalated their strong-arm tactics and instigation. Leaders and ex-leaders oiled their networks and accelerated mobilisations around caste and regional identities.
Workers disenchantment with leaders increased rapidly. Their self-activity became more pronounced. Large number of workers stopped paying union dues, attending union meetings, side-stepping leaders in day to day activity and began to deal directly with management individually and in small groups. Graffiti inside the plants increased. A group of workers belonging to, or influenced by, the fringe left posed inconvenient questions in a signed handbill on June 12, 1982. The handbill read “… management says that it does not have money even to buy raw materials – then where are the crores of rupees (millions of dollars) for automation coming from? Is it not because of automation that 600 workers are being told to resign? Soon, will you not talk of the need to retrench a thousand workers? Instead of struggling against it, haven’t union leaders become advocates of the management?”
The confidence of the leaders was shaken. Management was put on the defensive. Uneasy questions in the workers’ minds became points of widespread discussion. The tactic deployed by leaders and management – of announcing their attack in the gate meeting – had turned out to be a blunder. For damage control, the leaders adopted silence and the management took steps – show cause and advice l etters were issued to the signatories of the handbill. Through a circular, management warned workers to beware of disruptive forces. It said that automation was for the health of the workers. The management claimed that it had never had any intention of retrenching workers who would be made surplus by automation. If the management had wanted, it could have retrenched half the workers as it had been paying full wages to idle workers for one and half years. The circular ended with a rhetorical flourish: “Increase production OR perish!” A twisted version of the management slogan: “Increase production AND perish!” became popular amongst the workers.
The sequence of events at this point is as follows : there are prolonged delays in the payment of wages, machinery for automation reaches the plants, leaders maintain a strict silence, and ex-leaders attempt to form a rival union. There are physical attacks, by leaders and their network, on workers who still try to focus discussion on the looming retrenchment. To silence these voices, management uses suspensions. Besides the delay in wages, the issue of the annual bonus is used as another diversionary entanglement. Further on, the management goes for work suspension at half wages for three days and says that this may continue for quite some time.
Leaders complement these steps taken by the management for an open confrontation by ordering a tool down strike on February 12, 1983. Fiery speeches at gate meetings became a regular feature. Dissenting workers who have been trying to focus attention on looming retrenchment are denounced as disruptive elements and attacked. On February 21, 1983 leaders announce at a gate meeting that they have reached an agreement with the management. In the agreement it is agreed that no further work suspensions would take place but wages of January’83 would be paid in January’84. The workers reject this agreement. The management then tries, unsuccessfully, to instigate violent confrontations amongst workers through ex-leaders.
The same agreement is again put for approval at the gate meeting of February 28, 1983 after a number of thundering speeches challenging the management to lockout the factory if it wanted. The workers again reject the agreement. After the second rejection, the leaders announce that the way now is to go for an ‘open struggle’. A meeting of factory delegates (who had been elected in 1980) and other militant workers is called and suggestions asked for. Leaders then reject the suggestion for demonstrations on the plea that the conflict was with the Gedore management and not with the government. However, as soon as t he question of steps against the management comes into focus, the leaders somersault and announce a demonstration & a sit-down at the district administration chief’s office to be organised on Mar, 21.
On March 20, leaders call another gate meeting. Besides members of their network in the three plants, leaders bring their supporters from other factories and spread them out strategically. The same agreement is announced yet again. It is immediately hailed by the strategically placed supporters! And before the workers can react, leaders and their henchmen jump the factory gate and rush in to the plant to switch on the machines. The leaders had here used a time tested and most effective strategy. By switching on machines and restarting the plants, the workers would now be split into confronting groups, where one section would demand a continuation of the tool down strike while the other would be in favour of resuming work. This clash amongst the workers, and the concomitant unfolding of violence, would then facilitate large-scale retrenchment.
But in this case this strategy failed miserably. Enraged, the 3500 workers rush into the plant, shut down the machines and then beat up the leaders who are forced to run away. The President of the union who was also beaten and had to turn tail, had been the president of the union for ten years and was also the President of CITU, Faridabad district unit of the central trade union of Communist Party of India (Marxist). Production does not resume. There is now massive police deployment. Leaders again try to start the machines at night. They are again forced to retreat. Tool down continues.
Some workers belonging to the fringe left call a general body meeting on 23rd March, the weekly rest day. All the workers attend it. A committee proposed by militant, articulate workers and ex-leaders to obtain the resignation of leaders is not opposed. In view of the mounting discontent of workers, the leaders have to resign. After the resignations, the struggle committee, however, does not materialize and the ex-leaders take over. Tool down continues till April 14, 1983. The workers reluctantly accept the agreement that they had rejected earlier.
Stalemate. The issue of retrenchment has got bogged down.
The cycle of shopfloor instigation and wage-delays reemerges as a part of renewed attempts to retrench workers. Police are now posted inside one of the plants. Mobilisations being made on the basis of region and caste come to the fore. There is now a delay in the payment of wages to supervisory and clerical staff.
The management obtains government approval for retrenchment of 300 workers. Leaders hide the list and deny that there is any retrenchment on the cards. They start talking about a new long-term agreement and preparation of a demand charter for it.
At this juncture, management steps up attempts at violent confrontations amongst workers. Old leaders form a committee with the claim that they will negotiate a good agreement with the management. Mobilisation by the two lead-ry networks on the basis of caste, region and plant identity became frantic. The management flames the fire by locking out the third Gedore plant in February 1984. Enraged workers attack the existing leaders and the committee of old leaders uses this opportunity to take over leadership. Lockout in the third plant is lifted.
The finishing off And then began joint action by the management, leaders, police, state administration and the media, to retrench workers in Gedore Hand Tools. A gang of 15 to 20 leaders and their musclemen freely roam the three plants. They pick workers from their machines, take them to the plant time-office and force them, through physical violence and threats, to sign resignation letters. In this way, up to 50 workers are forced to resign in a single day. Workers coming to factory for work and those leaving after shift hours are attacked on the roads and forced to resign. Workers are threatened at their homes and forced to resign. Workers who had lodged complaints with the police find that the police have framed cases against them. Government administration merely files away the complaints made at the District Administration office. Newspapers do not print any news of these events. Not even letters about a fellow worker who committed suicide on the rail tracks after he was forced to resign.
In these circumstances hundreds of workers sought shelter in their villages for months. And the environment at Gedore? Armed police in tents inside the factory, armed police in trucks making rounds of the three plants. This is how the stalemate was broken and retrenchment implemented. Even then, it took one more year to retrench 1500 workers out of the 3500 in Gedore Hand Tools, Faridabad.
*** SELF-ACTIVITY OF WAGE-WORKERS AGAINST POLITICS OF CLOSURE DEFINING CLOSURE
A viable enterprise means that enough surplus is being extracted and realised in order to be appropriated as taxes, interest payments, cuts & commissions, managerial life-style and dividends. For financial institutions, management & state apparatus, a company becomes non-viable & sick when the extracted and realised surplus is not sufficient to meet the existing levels of taxes, interest rates, cuts & commissions, managerial life-style and dividends.
It is not uncommon to find that state apparatuses, financial institutions and management are sometimes forced to reduce their amounts of surplus appropriation to keep an enterprise running. But the overriding tendency, of course, remains one of perpetually increasing the amounts that are appropriated, resulting in increasing “sickness” and “unviability”. The dominant propaganda and media, however, all the while speaks of “sickness” and “closure” in terms of either mismanagement or lack of profitability (i.e. inability to pay dividends). This screens the fact that the major portion of extraction from wage-workers is appropriated as taxes, interest payments, cuts & commissions and managerial lifestyle.
POLITICS OF CLOSURE
The common interests of management, financial institutions and state apparatus dictate the survival, running and growth of an enterprise. In their common interest, they collaborate to increase intensity of work & workload, decrease wages, retrench workers and create techniques to counter wage-workers’ self-activity.
Despite all the cunning and guile, force and deception used to keep an enterprise viable, when an enterprise “becomes unviable”, then it is in the management’s interest to swindle as much as it possibly can of the company’s assets. When a goose no longer lays golden eggs, wisdom advises – ‘Cut and Eat the Goose’.
There is a well-tried out management method to grab as much as is possible of wage-workers’ legal dues before the closure of a factory. Along with the months of outstanding wages, years of provident funds/ pension funds, gratuity/ retirement benefits, years of bonus and leave travel allowances, etc. are also not paid. Company properties are then sold off with the management taking large cuts & commissions. This has been a routine exercise in a large number of factories which have been closed in Faridabad and other places. The dominant schema is:
When a factory “becomes sick”, and closure has been decided, management – through union leaders – instigates strikes, and/or violent incidents to create conditions for lockouts. This facilitates the dispersal of workers. In these situations, management stops coming to the factory and wage workers are channelised into long drawn out civil and criminal court cases – fifteen years is very common. During all this, closure is very actively camouflaged. In the rare cases where the court cases are finally decided in favour of the workers, and the workers are at hand to take their legal dues, there is no property in the company’s name to pay. Banks’ and state apparatuses’ dues (taxes and other bills) gulp most of the little that remains.
A BREACH IN THE POLITICS OF CLOSURE
This is the scenario that is being tried out in Jhalani Tools Limited, Faridabad. But the wage-workers in Jhalani Tools are actively countering this management-leaders-state administration schema to gobble-up workers dues through various modes of self-activity. These steps of self-activity, in our opinion, have wider ramifications for wage-workers. Management of Jhalani Tools stopped paying wages to workers from Mar’96. The past experiences of wage-workers in Faridabad and specifically in Jhalani Tools, have thoroughly discredited leaders amongst wage-workers. Through silence and passivity, the 2,000 workers countered leaders’ and management’s methods of instigation around tangential issues. No heed was paid to grand agreements, identity politics, change of union affiliation, change of leaders, provocation by transfers, instigation to violence etc. Four groups of leaders have come (have been brought) and gone, banging their heads against this wall of ‘dull and dumb’ silence.
With mounting legal dues and increasing hardships, workers had hesitatingly started looking for alternative courses of action. Initially a small group of workers in Sept.’96 had on their own demanded back wages from the state labour department officers. Slowly, in affinity groups of 5-8, workers complaints to the state officials increased. And very soon the working of the labour department and district administration was almost jammed when 300 small groups of workers separately started approaching the officers. Legal obligations of separate dates and hearings were done away with, but then talking to hundreds of workers at the same time was another impossibility. Like the management, the district officials desperately tried to foist leaders on workers, but failed. Faced by this stubborn refusal to accept anyone as leaders, district officials then tried their best toinstigate workers to violence. They failed again.
Another facet of this incident is that collecting a crowd by giving a single date to 300 affinity groups facilitates the spread and legitimization of the ageless rhetoric of unity and delegation (for negotiation with management and administration). This was attempted by the district administration. But an interesting metaphor to counter this arose from within the crowd outside the administration office. A worker responded to the call for “unity and delegation” by calling out that – “Bees united in a hive can easily be smoked off and their honey taken away. But if affinity groups of bees swarm about, no one dares to touch their honey”.
Then the management tried to create leaders and instigate strikes through summary dismissals of workers. But even when the number of dismissals reached a hundred, the workers neither made leaders nor took to violence.
With this stepping up of pressure by management, leaders and state officials, the workers of Jhalani Tools in August’97 started taking very simple steps to take their predicament to more than 300,000 co-workers in Faridabad & Delhi. Overcoming hesitation, fear & shame, some workers in small groups of 8-10 started standing along various roads during morning and evening shift hours with hand written placards. This was done to engage in discussions with workers of other factories without any intermediaries. They have been doing this daily since Aug’97.
On the placards is written:
“We are from the 2000 workers who have not been paid their wages for (so many) months”;
“What is to be done when management does not pay wages?”;
“We have changed leaders four times and union flags three times, but each time it has been from the frying pan into the fire”;
“We have made many complaints to govt. officials and ministers but conditions have gone from bad to worse”;
“Metal Box, Delta Tools, Electronics Ltd. and now Jhalani Tools workers. Whose turn tomorrow?”; etc.
Everyday they space themselves along a different road. Along each route that they stand on, workers from hundreds of factories pass by. The response of workers at large has been tremendous. Dispersed, multi-nodal conversations without intermediaries are emerging about the urgent need for new modes of self-activity of workers. Over this period of eleven months, more than 200,000 workers have read these placards and thousands of workers have stopped to have extensive conversations with them. In almost all factories of Faridabad (and large number of factories & offices in Delhi) questions posed by these workers are being debated.
What is being discussed by an ever-increasing number of wage-workers is how to act on their own strength against the triumvirate of state, management and representatives. It is a constant process of conversation, argument and counter-argument as to the ‘Whats’ and ‘Hows’ of steps of self-activity. There is awareness that the charted out paths and networks of representatives, leaders and their organisations are all geared to subvert this process.
Management, leaders and state officials are finding it difficult to instill fear in workers at large as they can find no appropriate targets for their terror tactics. More difficult than the small numbers of workers on the roads, is the problem that the straight and silent faces of workers are posing for the bosses. An additional difficulty for the bosses is the workers’ refusal to go to court despite all the advice that the specialists have been doling out wholesale.
More and deeper discussions have been taking place amongst Jhalani Tool factory workers. These have found visible expression in forms like wall letters and graffiti, but a truly significant fallout has been that workers have innumerable and extended conversations within and outside the factory premises and with co-workers as well as workers from all other factories. From being a problem of one fac tory, it has now become a problem of all workers.
To counter the increasing self-activity of wage-workers, the provincial government organised elections, in Oct’ 97 in order to establish a new leadership in the factory. From Dec’ 97 the management started paying wages. However, these steps failed to put a brake on the workers’ self-activity. Neither the issue of back wages & other dues could be side tracked, nor could the management sell the IIIrd plant of the factory, nor could it make leadership credible amongst workers.
In this situation, in Apr’ 98, the management resorted to massive wage-cuts in order to instigate workers. Failing again, the management then created an atmosphere of fear & violence and threw out the elected leaders – replacing them with its hand picked works committee in the first week of June’98. This hand picked committee has resorted to direct physical attack and identity politics. But the continuous rise in workers’ self-activity has put a hold on this.
Small groups of workers with placards standing on the roads have increased and are increasing in number and so are the workers in conversations with them. Thereby not only creating problems for Jhalani Tools management, which has not been able to close the factory, but also for managements of thousands of factories.
KK / Collectivities, June, 1998. Majdoor Library, Autopin Jhuggi, N.I.T. Faridabad, 121001, India
* Revolutionary Termites: Gedore Jhalani Tools
Loren Goldner
For complete text see: http://libcom.org/library/revolutionary-termites-in-faridabad-a-proletarian-current-in-india-confronts-third-worldist-statism
The extracts from Goldner’s article below can serve as a summary of the various articles in FMS covering the dispute.
In 1982, a struggle erupted at the German-owned Gedore Hand Tools works, consisting of three plants and employing 3,500. The dominant union was the CITU, the affiliate of the CPI (M). Gedore management demanded 600 “resignations” (6) and a 25% pay cut or six months of “special terms” for pay. All demands were rejected. Management attempted a “pinprick” strategy, to which the union responded with a “tools down” strike. Management attempted a lockout, and the union struck. As is often the case, the union called the strike just before payday, ensuring that the workers would go into the strike with the least possible financial cushion. A month passed, and two contracts were rejected; with a third offer, the union packed the strike meeting and ordered a return to work. The strike continued nonetheless, as strikers occupied their own union hall and demanded the resignation of the leadership, which took place, after which a new leadership took over the CITU. The strikers returned to work, but nine months later management locked out one of the three plants. A “Committee of 15″ was formed to get a better agreement, but it was then learned that the new leadership which had taken over in the original ouster had collaborated with management in the lockout, which brought the “Committee of 15″, which had ties to the original leadership, to power in the union. The “Committee of 15″ in turn began forcing people to resign by force. Armed police and police trucks were posted inside the plants. On some days as many as 50 workers were forced to resign and beaten by union goons. Many workers went back to their villages to avoid being forced to resign. In this conditions, it took a year to force 1,500 resignations (7), and in May 1985 the struggle was over. Later, the German management sold off the company, which became Jhalani Tools.
The (ongoing) struggle at Jhalani Tools Ltd. is one of the most recent struggles in which Kamunist Kranti has been involved, one of the most dramatic, and the one about which I have the most documentation so, at the risk of overkill I will give it more space. Jhalani Tools provides an unusually clear illustration of what Faridabad workers (and workers in other parts of India) are up against. Workers everywhere are familiar with asset-stripping by management. But most workers in Europe and America, when their company goes bankrupt or is absorbed in a leveraged buyout, at least expect to be laid off with a final paycheck, collect some unemployment compensation, and perhaps eventually some part of a pension. Of course in the fly-by-night sweatshops of Los Angeles and New York, as in similar maquiladora operations on the US-Mexican border, there are constant cases of companies folding up and disappearing while owing workers weeks of pay. But there have to date been few cases of decades-old, well-known “mainstream” companies operating for nearly two years without paying any wages.
Not so in Faridabad. Jhalani Tools Ltd. (9), the successor to Gedore Hand Tools (cf. above for the account of the 1982-85 struggle there) has not paid wages to 2183 workers since March 1996. Since there has been no hiring at Jhalani since 1978, (and the forcible “downsizing” of the work force in 1984) these 2183 employees have been at Gedore/Jhalani for a minimum of 20 years. They are the target of an asset-stripping strategy that is not uncommon among Indian firms. Jhalani Tools is not merely attempting to loot two years of back wages; it is also looting money owed workers for two annual bonuses, three years of “leave-travel” allowance, 3 years’ payments to the group medical plan, and other “contracted” benefits. It is able to blackmail workers in this way because of the difficulty, not to say impossibility, for them to find other jobs by walking away from their “legally guaranteed” employment.
After reducing staff almost by half by goon terror in 1984, as described earlier, Jhalani in 1989 colluded with the union to ram through a contract containing three secret clauses that were withheld from workers (the contract was read aloud, minus these clauses, at a gate meeting). The clauses linked wages to production targets (requiring a minimum of 200 tons before any wages would be paid), absolved the company of the obligation to pay workers when production was impossible because of electricity blackouts or raw materials shortages, and gave the company the right to assign work irrespective of job classification. Even after pay had been docked for electric outages and materials shortages, these clauses remained in a new contract pushed through in 1993. Pleading poverty from various causes, Jhalani Tools in December 1995 got an “ad hoc committee” to agree to a 50% pay cut until further notice. The company began paying wages months in arrears and finally, in March 1996, stopped paying wages altogether, largely blaming work stoppages and indiscipline for the company’s problems, using further endless salami tactics and manoeuvres, and blithely ignoring the occasional labour board and court decisions in the workers’ favour (the latter hardly being news).
Seasoned by decades of these tactics by management and the unions, Jhalani workers refused to be provoked into a set-up strike or other easily-targeted actions and instead took their case to the Faridabad working class as a whole with roadside informational pickets. (For further details cf. KK’s response to this article published in CAN, Fall 1998). As of this writing (March 1998), the standoff remains unresolved.
* FMS – March 1983
Since 12th of February 1983, Gedore workers in the three plants are engaged in a tool down strike against the enforced two days layoff per week. Without understanding the root of an illness it is impossible to cure it. This is why a report about the events of the last 8 to 9 months is necessary. The plans of the Gedore management to go ahead with mass redundancy were made public during a [union] gate meeting on 7th of June 1982. Please read the leaflet distributed in the name of six workers shortly after the meeting, on 12th of June 1982:
“At the gate meeting of the 7th of June 1982, the union leaders advocated following measures of the management: wage cuts of 25 per cent; lay offs; dismissals of 600 workers; workload increase. But the workers scolded their leaders. Let’s have a deeper look at the arguments presented by management and their advocating union leaders. The management and leaders claim that currently the bosses don’t have the money to pay for the raw materials. Therefore it is necessary to cut wages in order to be able to run the factory. Why don’t they take the money they spoil on air-conditioning, cars, bungalows and other luxuries? Moreover, the management drives forward automation and both management and union now say that the workload will have to be increased. Therefore additional raw materials will become necessary. So it seems that these people tell us that in order to keep the factory running we are supposed to work for free and that, apart from our last shirt, are supposed to hand over our money to the bosses – the January 1983 wages are now supposed to be paid in January 1984!
The situation of the bosses is bad. This is the argument of the bosses and their drum beating leaders for why the dismissal of 600 workers is necessary. To increase production through automation and thereby to create a surplus of workers is a common issue in capitalism. This is why workers fight against capitalism. But these leaders give support to the bosses, they became advocates for class collaboration. Even the INTUC leaders barely conceal their open advocacy for wage cuts. According to their argument it is necessary to cut wages in order to save the Gedore bosses in the current crisis of global capitalism: so that the workers still find work and their daily bread. The fact that these leaders not only put forward this line of argumentation, but at the same time shout slogans denouncing CPI(M) and CITU of ‘collaboration’ with the capitalists’, have crossed all the boundaries of shamelessness.
We ask the management and their advocate leaders: Where did the crores of Rupees for automation come from? Although it was not openly mentioned, wasn’t it clear already when automation started that 600 workers would become superfluous? Will you not very soon say that actually 1,000 workers have to go? Work-mates and comrades, it is a fact that in order to introduce automation a quarter of the work-force will have to go. This is why management cries about how bad their economic situation is. The management’s current trajectory is to incite us by paying wages late, by dishing out charge sheets at the smallest occasion.”
This was written in the leaflet from 12th of June 1982. After that the CP(M) – CITU leaders turned into silent ascetics. The reply to the leaflet was issued by the general manager (personnel and administration). He replied on behalf of these leaders and the Gedore management. He circulated a two-and-a-half page leaflet in English on 14th of June 1982. Some days later the Hindi translation was circulated amongst the workers. On 17th of June 1982, the management issued a letter [official warning] to those workers who had distributed the initial leaflet – on 16th of July 1982 management issued an advance letter to the same workers, making clear that they want to silence the whole dispute. In July 1982, in issue no.4 of our publication, we expressed some thoughts about the reply of the Gedore manager. Please consider some excerpts:
“On 4th of June 1982 the General Manager, Personnel and Administration, Gedore Tools announced following ‘facts’, in order for the Gedore workers to receive ‘information for finding a true position’, who ‘had been let astray by troublemakers’.
“1. Automation in the plating plant is being introduced for the benefit of workers’ health. It was never management’s intention to sack those workers who have become superfluous as a result of the automation. If the management had intended to sack workers, they would have been able to sack half of the workforce already. Management has paid the full wage to all those workers who sat idle during the last one and a half years.”
Capitalism obviously considers workers’ health a lot! And obviously you did not intend to lay off workers! We accept your words, but… the rule of capital does not function according to your will. So what will you do? It is a very good deed to pay full wages to those workers who sit idle – but how many unemployed are included in your royal court? Your endowments are also paid in order to save taxes and to give workers their bit of opium to smoke. In the current system we live in, every new machinery embodies both, the workload increase for some, the lay off for other workers. Therefore the managers, in the end, have to give out the slogan ‘increase the workload or be destroyed’, which obviously means ‘increase the workload and be destroyed’.
This was on 1st of July 1982. We ask the management: when you stopped paying wages to workers in January and February 1983, the time when they suffered hunger, you only had their health in mind, didn’t you? The CITU / CP(M) leaders kept on remaining silent, now the Gedore management, as well, retreated into convenient silence. In this situation we wrote in the issue no.5 on 7th of August 1982:
“At Gedore, the production runs on full steam now. But workers should not fool themselves by adhering to false hopes… machinery for automation has arrived in heavy trucks. The Gedore management is wielding the blank sword to sack at least 600 workers. On the bases of a proper understanding of the situation, the Gedore workers’ unity can secure workers’ own interests.”
This was on 7th of August 1982. In order to diffuse the workers’ attention regarding the threatening mass redundancies, the Gedore management resorted to the manoeuvre of delaying payment of wages. The CITU leaders, during the gate meeting on 7th of June 1982, did not open their mouth about this issue. In issue no.6 on 7th of September 1982 we wrote:
“The August 1982 wages of the Gedore workers are again delayed. In order to debate about the current threat of automation and dismissals, 200 workers asked the union leaders to call for a general union body meeting on 20th of August 1982 – they confirmed this demand with their signature.”
But why should the CITU leader get involved in a general body meeting? What kind of value should workers’ signatures have for them? In the meantime the Gedore management arranges religious ceremonies and offerings inside the plant in order to fool the workers. In issue no.8 on 7th of November 1982 we commented:
“And regarding the question of fear, you keep the sword of mass redundancies above of the heads of your (Gedore management) workers.”
After that the Gedore management tried to entangle the workers into the issue of bonus payment, while the attempt to form a second trade union inside the company failed. The CITU leaders escaped from the elections – everyone was now able to see them as what they are. In order to obstruct the elections they grabbed for the brought up issue of bonus payment. From the management’s perspective the redundancy program started to get more pressing. The Gedore management started to put pressure on the CITU leaders. This is when the leaders, trained by the CP(M), revealed their true character. While previously the CITU leaders used paid thugs, they now themselves beat up those leading workers who had showed opposition towards the collaboration between Gedore management and CITU leaders. The Gedore management fulfilled their part of the job by suspending one of the leading workers.
But the situation at Gedore developed in quite a different direction from what management and leaders had expected. Instead of being intimidated and silenced the leading workers stood firm on the side of their co-workers. At this point the Gedore management withdrew their believe that the CITU leaders will be able to arrange a ‘silent process of redundancies’. The management forged a new scheme. They suddenly enforced lay-offs [lay off meaning that people were not dismissed, but forced to stay at home or idle]. The CITU leaders saw no other chance but to call for a tool-down strike. After having been fooled around for months, the Gedore workers were now determined to fight back. After having called for the strike, the CITU leaders withdrew into their usual business. As a worker in the third plant put it: “At Gedore, the leaders don’t get engaged in struggle, it’s the workers who fight”.
Previously the conflict between workers and CITU leaders had never been as open as now. After having torn to pieces the agreement between Gedore management and leaders of the 21st of February 1983, the workers also rendered useless the management’s attempts to break them. On 28th of February 1983, the workers turned into shreds another agreement proposed by the CITU leaders, which would have meant that current January wages would have been paid in January the following year. The leaders also said: if the management wants to lay-off, they will do so, there is nothing we can do to stop them.
* FMS – April 1983
Since the 12th of February a tool down strike is on in three Gedore plants. A summary of the events in March: After the workers rejected their negotiated deal on 28th of February, the CITU leaders announced to ‘fight’. Those leaders elected as delegates in 1980 (and some others) called for a meeting and demanded suggestions. The CITU leaders refused to call for a demonstration, saying that the struggle is with the management, not with the government. Then the question was put in front of them to undertake steps against the management. In response to this question the CITU leaders made a u-turn and suddenly announced a protest and procession on 21st of March in front of the DC office. The CITU leaders started to plan their manoeuvring.
On 20th of March they held a gate meeting. They secretly placed external lumpen-elements in the meeting… and the CITU leaders announced that they have come to an agreement with management. The workers shouted enraged. The CITU leaders escaped and started the machines in the second plant. But… the Gedore workers taught the CITU president of Faridabad and the president of the Gedore Workers Union a little lesson. Work in the factory was not resumed. The CITU leaders disappeared. The police arrived. During the night the CITU leaders again tried to start running the machines. Again the leaders were forced to run from the scene. The tool-down continued. In fear, the CITU leaders tried to break the strike.
On 23rd of March, a bank holiday, the Gedore Workers Union called for a general body meeting. Having seen the strike-breaking role of the leaders, the general body meeting decided to make them resign from their posts. In order to enforce the resignation a committee was formed and the decision was made that after the resignation of the leaders another general body meeting would be called and that a struggle committee elected. Neither on 24th nor 25th of March the CITU leaders announced that they would resign. The discontent amongst the workers started to increase. On 26th of March a meeting was called for the morning and the CITU leaders were finally forced to resign. The tool-down strike in three plants continued. On 26th of March a faction of INTUC took over the leadership of the Gedore Workers Union and during the gate meeting on 1st of April they revealed their true nature to a lot of workers. They focussed the hope of some workers on a meeting with the Prime Minister of India on the 6th of April.
* FMS – May 1983
The same eminent leader, who had praised the agreement of the 14th of April as “a marvellous agreement”, said on the occasion of the 1st of May that “we ourselves have not been too happy with the decision [regarding the agreement]“. We see the same helpless state of being. But yes, it has helped the Gedore Workers to understand: ‘Neither the prime minister, nor the minister, neither the DS, PD, nor the LC will act in the interest of the workers, because they are all representatives of capital’. This is the outcome of two months of tool-down strike.
* FMS – June 1983
The 15th of May was fixed as the payday for the February-March-April wages. Management paid some wages between 20th and 25th of May. In any case, in front of some well-known people the INTUC-Leaders have settled the date for payment of salary and of the bonus. They have ‘settled’ dates before, why should the problem of payment suddenly disappear? And the management has put up a notice saying that the workers do not work properly! In order to prepare dismissals on a larger scale management is busy making use of lumpen-elements for provocations.
* FMS – September 1983
From the leaflet of the Gedore general manager, published on 14th of June 1982:
“Don’t be lead astray by instigating forces! The automation is implemented in order to benefit the health of the workers. The management does not intend to make workers redundant.
In the meantime, on 2nd of September 1983, the circular of the general manager reads: “The company can not be run with the current number of workers. We have to reduce the work-force by at least twenty per cent.”
The management cries about lack of money. “We nevertheless spend the little amount of money that we have. What can we do, we are forced by the circumstances”. In the first and third plant, the staff [middle management] engaged in a one-day strike. The following day management paid out the total bonus to staff of all three plants and sacked eight people. Suddenly there was money available, wherever it came from! The staff in the third plant showed their courage and went on strike against the dismissal of their eight colleagues. Management paid the first and second plant staff the June wages, as well. Where have they kept the money? After the staff of the third plant stayed determined, staff in the other two plants went on strike in solidarity – the management bowed a little. The strike of the staff has stripped the management plans for mass redundancies.
* FMS – October 1983
Since 16 months now, everyone who warns Gedore workers about redundancies is denounced as ‘misleading’. Some of those people who were busy denouncing the ‘misleading troublemakers’ had actually received lists with details about imminent redundancies. Hiding these lists from the workers they asked: what do you mean by redundancies? Now these friends of indecency themselves say that there will be redundancies. Redundancies are on the agenda, but the recently published demand notice of the INTUC faction does not even mention them. Let’s not believe in the reassurances of the state representatives; those representatives, who, while trying to appear as being on the side of the workers, set up police posts inside the plants.
* FMS – November 1983
“This is not a sweet agreement after all… there is no mentioning of the bonus anymore… and the management does not talk about the agreement anymore – they say that we first have to talk about redundancies! In fact, the issue of redundancies is nonsense talk.” This is how the current situation is portrayed by the ‘watch-guards’ of ‘April Kranti’. To cling to power they should lie upon lie. But the Managment is shameless. After all, how long can these ‘watch-guards’ keep telling lies ?
* FMS – January 1984
The management has not paid the staff the wages for three months. On top of that management started to threaten the staff. In response the staff in the three plants went on strike for their rights. The staff cooperated with the workers during the time of the workers’ tool-down strike. Management eagerly tries to break workers of the first-second-third plant, using the issue of the 75 per cent [bonus?].
* FMS – February 1984
The management has started again to lay off staff. In order to go forward with the lay offs, the management encourages the middlemen to break up workers unity. Sometimes the hand of the management is in the back of the INTUC faction, sometimes in the back of the former leaders belonging to the CITU. These leaders suddenly started a minor row about the 200 Rs agreement. They showed themselves outraged. They brought up the issue of union elections. The INTUC faction raises the issue of the 75 per cent and the bonus in order to prevent new elections. On 21st of January a decision was supposed to be made during a gate meeting. But on 20th of January the former leaders belonging to the CITU – who had raised the demand for union election – organised a separate meeting and instead of elections decided that their committee will recognise the 200 Rs agreement. On the 21st of January the CITU leaders created clamour. The police, the DLC and the management [mathadhisha] all showed full support to the CITU leaders. Since then there are two adhoc committees who claim to represent the majority – one of the INTUC faction the other of the CITU – both work day and night in order to undermine workers unity.
* FMS – March 1984
With the help of their middlemen the management has been successful to break the unity of workers. With the lock-out at the third plant management has given the scheme of mass redundancies a final form. In order to foster workers’ unity, individual workers of the first, second and third plant have gone on hunger strike at the gates. The middlemen try with all might to prevent these steps, which have been taken by workers. Thugs of the CITU have used brute physical violence to drive away the hunger-striking workers.
(Due to the fact that the newspaper ceased to be published between May 1984 and January 1987 there is a gap in the coverage of the events at Gedore. Given the importance of the events we summarise them in the following.)
Instrumentalising the anger of the locked-out workers of the third plant, the clique around the Faridabad CITU president beat up and chased away the leader of the CITU recognised Gedore Workers Union. Having started, the CITU and their thugs joined the ranks of Gedore management, the police, the state administration and the press in their effort to enforce the lay offs against the Gedore workers.
The management walked around the factories unrestrained in groups of 15 to 20 men. The workers were forcefully taken from the work-place to the time-office, they were beaten and threatened by groups of CITU thugs and forced to sign their notice letters. In this way they managed to force 50 workers per day to resign. They stopped workers on their way to or from work, beat them up on the street and forced them to sign their notice. They went to works homes, and forced them to resign through beatings and threatening. If workers went to the police in order to complain, the police filed a case against these very workers instead. The state administration piled up the workers’ complains untouched in a remote and forgotten corner. The daily newspapers refused to publish any reports about these incidents. After a worker – who had been forced to resign – committed suicide on the rail-tracks his work-mates wrote a letter about this: which the big daily newspapers refused to print. In this social atmosphere dozens of workers decided to leave Faridabad and go back to their villages. On the premises of the factory, inside the company gate, the armed police put up tents. The armed police patrolled the three Jhalani factories in trucks. The management unleashed an open regime of violent intimidation inside the factories. The labour department, the state administration and the press were their silent henchmen.
In this atmosphere Gedore management put into effect their redundancy policy. Nevertheless, it took them one year to lay off 1,500 out of 4,500 workers. This noteworthy chain of events at Gedore, which took place between 1982 and 1985, confront the workers’ movement with some serious questions. Can workers wage struggles over important issues successfully if the struggle is limited to the level of a single factory? Are unions still organisations on the side of the workers?
* FMS – December 1988
The company name is now Jhalani Tools. Seven years ago the management took out a 2.5 crore bank loan and installed machinery for automation. After violent repression 1,500 workers left their jobs in 1984. But five years later the automation machinery still waits to be switched on and used for production. It seems that in 1985 management realised that even after mass redundancies of 1,500 workers and introduction of automation the business will not yield too great a profit – since then management started to fill their pockets individually. Be it the money from the service and PF of workers or the money put in the pockets of managers in the name of loans for the company – from wherever it is possible Managment is busy collecting money.In the last three years the company stumbled and teetered. The root of the struggles around this or that director lies in this wider condition of the company. The company has already been declared as sick. The management is now engaged in looting before the company is declared bankrupt and finally closed.
* FMS – May 1989
Don’t ask for outstanding wages – take the motorcycle offer instead!
The Gedore management has been engaged in various rip-offs during the last four years: they did not pay the statutory contributions to the Provident Fund; they did not return the money taken from workers for a housing scheme even after having sold the housing plot; they did not account for the money collected for a company society. After four years of promises-postponements they have now taken seven months of outstanding wages from the workers. About eight to ten months ago management said that they will pay the outstanding wages in 200 Rs monthly instalments. But they even messed with the payment of the 200 Rs, so that now they owe each worker around 8,000 Rs to 10,000 Rs of unpaid wages. The union leaders gave a hand to the company in order to reduce the workers’ discontent – they suggested that instead of the wages the workers should take a motorcycle or scooter. Please be informed that the current union leader is the president of the CITU gangs of thugs who engaged in the beatings of workers in 1984, when Gedore management started their lay-off policy; the beatings resulted in 1,500 workers signing their notice letters. After the dirty involvement of the CITU president made too wide rounds, the Delhi CITU committee dismissed him and the Faridabad branch joint secretary from the CITU in 1987.
Currently a lot of workers think that in a situation where everything and nothing can be expected of the Gedore management, it might be better to take the offer of the motorcycle and sell it quickly. The workers have to understand that if the motorcycle-scheme comes into effect the actual bank loan will be in the name of the workers, the management will only give their name as security. The actual documents of the vehicle will stay with the bank, which therefore has the final word about selling it. There is another serious issue: if the worker does not pay the instalments in time the bank can fine the worker, who him/herself might not be aware of it, thinking that the management is responsible. A management, which evades paying the instalments for outstanding wages and does so openly in front of all workers, if such a management pays even one monthly instalment as a result of a bank letter demanding the instalments of the last six months – workers could count themselves lucky. The fine will be paid by the worker and together with the interests, the bank will cut the money for the fine from the workers’ service or seniority bonus etc.. In 1976 Gedore management took over a similar role as ‘guarantee for security’, when some workers were encouraged to take out a 2,000 Rs housing loan from the New Bank. Management deducted the monthly instalments from the monthly workers’ wages, but transferred this money only with three months delay to the New Bank. In the end the bank fined the workers – not the management – for not keeping up with the due payments.
* FMS – January 1990
The methods of the middle-men
At Gedore alias Jhalani Tools, union leaders called for a meeting on 20th of December in order to announce the next three years agreement. Workers from all plants and all three shifts came along. The leaders started their speech with the complain that once meetings concern issues of interest for the workers, thousand arrives – but that when the AITUC calls for a union meeting not even hundred workers attend. Then the leaders announced the agreement and repeated several times to the workers that they should accept it. Having heard this, the workers thought that the agreement will be alright.
Then union leaders went to plants separately and told single groups of workers that there have been wrong information in the announcement of the agreement. The union leader said that they were forced to speak untruthfully, because if they had announced the correct content of the agreement they would have been attacked – facing thousands of assembled workers. As a result of this betrayal a wave of workers’ anger surged in the three plants. The union president, once encircled by workers of the first plant, said: “The mistake has happened, now do what you want!”
The next day the union leaders announced that the reason for having lied is that otherwise – given the general chaotic situation – the ‘evil’ former Faridabad CITU president, who had just been expelled by the union, would have returned. Now the current CITU union leaders, who were goons of the former CITU president, have adopted the same attitude of 1984, when they compelled 1500 workers to sign an agreement: an agreement about which the workers had not been informed beforehand – just like today.
* FMS – February 1992
On 10th of January the workers of the second plant were thrown into confusion. Management had cut 800 to 900 Rs of the December 1991 wages of many workers. The wage cut was also documented on the pay-slip.
The management and their middlemen at Gedore alias Jhalani Tools are ill-reputed in the whole of Faridabad. After major efforts to lay-off workers failed in 1982-83, management and middlemen forced 1,500 workers to re-sign in 1984 by brute physical and mental violence. After the redundancies the remaining 2,500 workers stirred every now and then, but most of the time they kept being silent and afraid.
The wages of the 150 workers in the second plant have been cut. With the spreading of the news, the workers’ anger erupted and replaced the previously pre-dominant fear. Facing this anger the management and middle started whispering and finally paid out the missing amount to the workers. The issue over the wage cut calmed down, but workers’ worries increased. Some workers, who asked the middle-men for the reasons behind the wage cuts, were intimidated in response and the middle-men tried to silence them – but the workers did not keep silent about this. After consulting each other, workers decided to ask management in written form about the reasons for the wage cuts. The management refused to take the workers’ letter. If a worker would refuse to receive a document issued by management, this worker would be accused of and officially warned for not following orders. So, Jhalani Tools workers sent the letter by UPC post and informed the DLC of the issue.
Obviously, the cutting of wages of workers of the second plant was a way for management and middle-men to instil fear among workers and to find out how they would react. The management and middle-men came to the important decision to enforce the collective agreement upon the workers. Please have a look at the details of this agreement:
“Eight hours work performed by workers will be counted as four hours of production. The management will not be responsible for supplying workers with material and electricity. Any worker can be employed at any machine, for any job or task.”
It becomes clear that the issue is not about some workers at the second plant, but that we have to deal with a general attack on workers of all three Jhalani Tools factories in Faridabad. This is a serious issue for the Jhalani Tools workers. Only the collective strength of the workers will be able to take care of the workers’ interests. The Jhalani workers should remember that in 1983 their collective power made the chief of middle-men, the Faridabad CITU president, bite the dust. Their collective power also made Gedore management feel rather uneasy. But it was the united strength of management and middle-men and state together which the Jhalani Tool workers alone were not able to come up against. Workers managed to deal with the thugs of the CITU president in 1984 as long as it was just them. If Jhalani Tool workers continue to establish and strengthen the unity with workers of other factories they will manage to deal with the unity of management, middle-men and state. Courage and tenacity will be necessary.
* FMS – July 1992
In May, for the duration of a week, each worker of the rough grinding department (in the second plant) was given a letter – one on every single day of this week. The letters were written by management and written in English. The workers went to the union leaders in order to show them the letters. The leaders said: “This doesn’t mean anything, the management has always issued this type of letters.”
When May wages were paid, management had cut 100 to 150 Rs of the wages. After a lot of running about, workers found out that management’s letters stated that workers had not met the production target and had remained idle despite having been told to perform their duty. In fact, during the respective period there had been power cuts for two and a half hours each day and the electricity from the generators had not been supplied to the rough grinding department.
The workers reported this fact to both management and middle-men, but were only told that “we will see” – nothing else. Actually the CITU union and Jhalani Tools had just signed an agreement saying that wage levels depend on production levels… and that the supply of material and electricity is not part of the responsibility of the management. In June workers received another letter, similar to the May ones. This time workers replied to the management, but management refused to take the workers’ reply. The fact that workers showed resistance will surely have had an impact, given that the management refrained from sending a second, third, fourth, … letter like in May.
* FMS – March 1993
The management and leaders are very happy about their three years agreement. After announcing the agreement during a gate meeting on 6th of February, the leaders said that the first shift can take the rest working day off and management did not cut wages for these four hours of extra-holiday. The production target fixed in the previous agreement had already been difficult to meet. Stating that production levels were too low, management had sent various letters and cut wages of workers of all three plants several times, by in total around 800 to 900 Rs. After back-and-forth the deducted amounts were paid later on. In the new agreement production targets were raised by 25 per cent!
During the 6th of February meeting, some people who don’t have to work but nevertheless get the productivity incentives for ‘topping the target; plus some people who are close to the leaders; and some workers of departments where wages had not been cut, raised their hands in support of the agreement. These workers accounted for about 20 per cent of the total workforce. The leaders did not even come to their usual tricks of asking if there is anyone opposing the agreement. No one will speak against the agreement at this meeting – this is what leaders repeatedly said on 6th of February. One worker asked about the wage cuts, but his question was smothered by general racket and the announcement of the half-day holiday. Then the meeting was over.
Eighty per cent of the workers, those workers opposed to the increase of work-load – they kept silent during the meeting. Those workers whose wages had been cut under the pretext of ‘too little production performance’ – they, too, kept silent. This is not all: without even knowing its full content, workers signed a blank document in support of the agreement. For the last agreement it took groups of ten to fifteen musclemen to surround single workers at their machine in order to make them sign a blank document. “I signed because these hooligans forced me to.” This time no worker was surrounded and forced to sign, nevertheless they gave their signature? Why? What reason for?
On 9th and 10th of February wages of many workers were cut by 800 to 900 Rs – because “production was to low”. In the morning of the 11th of February – on the initiative of the workers of the grinding and forging department – workers of the first plant stopped production and gathered in front of the administrative block. The workers of the packing department acknowledged the fact that raising their hands in support of the agreement had been a mistake.
Union leaders came running from their office. One of them tried to appear commanding and to intimidate workers. The result of giving this guy a beating was that the president, the secretary and the cashier turned all soft. Facing the open and fierce opposition towards the agreement, the union leaders announced that they had not signed the agreement yet. The leaders gave their assurance that they would call for a meeting and only once all workers agreed they would sign the agreement.
The production was put to a halt from 8 to 11 o’clock – management put up a notice saying that three hours would be cut from wages. Not only this, seeing their plan going down the drain the management called the DLC. Within four hours after production was resumed, management and union signed an agreement in the presence of an official from the Haryana State Labour Department. In the end… union leaders are also entitled to democratic rights!
* The Company They Keep A Report on Workers of Jhalani Tools Ltd., Faridabad
Peoples Union for Democratic Rights, November 1997
JHALANI TOOLS LTD. is a well known company which makes hand tools such as spanners, wrenches, pliers, screwdrivers, etc. It is a reputed exporter and has six plants in India 2 in Aurangabad (Maharashtra), 1 in Sonepat and 3 in Faridabad (Haryana). The company started its Faridabad operations in 1960 as a German collaboration project called Gedore Hand Tools. When Gedore withdrew from the company in 1985, it came to be known as Jhalani Tools. In 1986 Jhalani Tools had been declared a sick company but its process of recovery started by 1992 and currently it is no longer considered sick.
Today, at New Industrial Town, Faridabad only 2 plants are functioning. The third plant was shut down in 1984 but the workforce was absorbed in the other two. Through the decades of the sixties and the seventies the workforce had built upto about 4000. However, following mass retrenchment in 1984 this number today stands at 2183. All these workers are registered, permanent workers of the company. There has been no new recruitment since 1978, which means that almost all of these 2183 workers have served the company for at least 19 years. This report concerns such workers who have not been paid any wages for the last 19 months; who have been reduced to pulling rickshaws, setting up thelas of petty merchandise, or depending insecurely for survival on other family members.
Jhalani Tools has not paid its workers wages due for the period March of 1996 to September 1997. The company also owes its workers many other dues. For the last two years no bonus has been given, for three years no Leave Transport Allowance; and no dues for uniforms, shoes, soap or saafi (protective head gear) for a similar period. Further, the company has not paid its Employees State Insurance (ESI) dues for more than three years, and Provident Fund amounts have not been deposited since May 1994 (see Box-1).
However, it is the issue of non-payment of wages that is central to the current deadlock prevailing in the Faridabad plants. It is also the issue that brings out the complex role played by various mechanisms of governance and justice, including even trade unions, in helping the company to extract the maximum possible from its workers. And what’s more, to justify that extraction. In its investigation, PUDR team spoke to many company workers, the current workers union, the senior management of Jhalani Tools, the Deputy Commissioner (Faridabad), the Deputy Labour Commissioner (Faridabad), and other functionaries of the Labour Department.
Background
The history of the relationships between workers and management, workers and their unions, since the early eighties, seems to have been problematic. The company has played a visible role furthering, manipulating and gaining from this.
Over the years the unions in Jhalani Tools have not been chosen through election. Instead, barring the odd exception, groups have staked their claim to leadership by collecting in their favour signatures of a simply majority of workers, and sometimes by sheer muscle power. The groups that thus come to power are called “ad hoc committees”. It is such groups that negotiate with the management on behalf of workers and formalise labour-management agreements. The Gedore/Jhalani ad hoc committees have mostly been affiliated with CITU (Centre of Indian Trade Unions) and sometimes with INTUC (Indian National Trade Union Congress). An example of the manipulative role that Jhalani Tools management has played in the functioning of these ad hoc committees is in the matter of union chanda (contribution). The management deducts the chanda directly out of the workers salaries and hands over a lumpsum to the committee in charge.
The most controversial year in the company’s history was probably 1984. In its drive towards automation the management decided on massive retrenchment. In Faridabad as many as 1500 workers were retrenched in one year. According to the company these workers had opted for the Voluntary Retirement Scheme (VRS). But according to the workers and the press, the company used brute force, the complicity of the then CITU union and the help of armed police to terrorise the workers into resigning. The presence of a police chowki within factory gates in 1984 speaks for itself. Union leaders are alleged to have been directly involved in drawing up lists of workers to be targeted and in aggressive tactics used against the workers. (The President and General Secretary of this union were eventually expelled by CITU’s Delhi Committee in l985.) Notably, the company, having gained its ends in l984, today in all its statements and letters to authorities, glosses over that year as the year of “Voluntary Retirement”.
Another instance of management-union leaders collusion appears to be the 1989 long term agreement which workers today describe as a “terrible agreement”. At that time they were given no idea as to the specific clauses it contained. After the agreement had been signed, at a gate meeting, the leaders read out a certain version of the agreement. The very next day they confessed to individual workers that they had withheld information about three crucial clauses so as to avoid the eruption of workers protest. These 1989 clauses set the precedent for all later settlements. The main point was the linkage of wages to production targets. In 1989 it was agreed that the workers would be given wages only after they produced 200 tons of goods. Secondly, the company refused to take responsibility if there was shortfall in production due to shortage of raw materials and electricity. Thirdly, the company could switch around workers from one job to another, irrespective of their skills.
The impact of the first and second clauses proved to be lethal to workers interests. For example, in May 1992 wages were reduced for non-achievement of targeted production, even though this was due to erratic electric supply. Electricity shortage in effect thus became workers responsibility! The electricity problem grew to such an extent that, according to the management [letter to Deputy Commissioner, 17 October 1986], “there had been long periods of 100% power cuts from 1993 onwards”. Yet in the agreement signed in 1993, there was no attempt to take into account the electricity problem. At the same time the production targets were extended by 25%.
The latest agreement signed on 6th June 1997 once again links wages to production but it nowhere takes into account the lack of raw materials. At the time of signing, the ad hoc committee showed the Deputy Labour Commissioner (DLC) authorising signatures from workers in what the DLC calls “an irregular format”. Later he received complaint letters from as many as 1600 workers denying that they backed this agreement. The DLC formally declared it null and void (circular, 30 July 1997). The Jhalani Tools management, however, is still trying to uphold this officially invalidated agreement. In a notice signed Yogesh Jhalani 26 September 1997, workers are told “your agreement has taken place…under the care of CITU’s national Joint Secretary who has the trust of 20-25 lakh workers”. The invalidation of the agreement is explained away as the “pressurising” of the DLC by a few disruptive workers.
An important facet in the company’s history has been its `sickness’. In 1986 the company was declared sick under the Sick Industrial Companies Act, 1985. According to the management this was because a steep rise in the price of steel in 1981 made the company unviable in the international market. From 1989 remedial measures could be implemented as the government started providing steel at international prices. The management states that the next few years, till 1992-93, showed substantial improvement and the company started implementing a rehabilitation package approved by the Board for Industrial and Financial Reconstruction. The Annual Report for 1996 states that the company has been consistently earning profits for the last six years and that the net worth of the company is now positive.
Today whenever the Jhalani Tools management has to answer for its workers’ problems this background of sickness is heavily invoked. The management admits that its problems have been mainly due to factors such as competitive international markets, the price of steel and, in the 1990s, massive power cuts, difficulties with creditors, postal and transporters’ strikes etc. Nevertheless, in dealing with the current problem it insists that the workers are mainly responsible for the company’s losses and cites go slows, stoppage of despatch and carelessness in handling material by workers as a cause of heavy damages.
The logic of the financial crisis is used to compel workers into agreements such as that of December 1995, in which the ad hoc committee agreed that workers would accept only 50% wages till conditions improved. And, as we shall now discuss, by explaining the present crisis in terms of workers `non-co-operation’ and misdeeds the management absolves itself of all responsibility for giving workers their dues.
The Current Problem
“Today the world is one of competition and no company can exist without productivity. Therefore every agreement is linked to production. In future too, any agreement, of any kind, at any time, will be linked to production.”
Translation of a Hindi notice to workers, signed Y.C. Jhalani, 19 September l997
The three agreements of 1989, 1993 and 1996 (and various interim mini agreements) established the linkage of payment of wages to specified production targets. Simultaneously, by 1996, lack of electricity or generated power, of raw material, and non-maintenance of old machinery were entrenched problems. So was the tradition of late wage payments. For example, wages given in March 1996 were for work done in November l995. Similarly wages given in May 1996 were for work done in January 1996. The current problem relates to wages for the period March 1996 to September 1997 which, on various grounds, the company refuses to pay.
March 1996 and part of May 1996 were times of no production because of intermittent work stoppage due to workers’ anger with the then ad hoc committees. There were resultant leadership changes. Workers did report for duty in April, part of May, and June to August. Lack of raw material remained a serious problem. In this period the management made statements that they had no cash to disburse. In July a date was announced, hopes were raised but no wages were paid.
According to the current ad hoc committee, in August 1996, production upto 200 tons was ready, with only 5 tons or so lacking. But the management contends that the shortfall was actually of 50 tons. With the management refusing to pay six month due wages, on the grounds of this shortage, the workers committee decided to stop despatch of goods at the beginning of September 1996. In retaliation, the management got the electricity connection cut so that no production could take place anyway. This stalemate lasted from September 1996 to January 1997.
Work was resumed in January 1997 after a settlement was reached between the ad hoc committee and the management via an interim memorandum of understanding. Instead of wages, this settlement announced “advance payment” for the next four months. About Rs.8000/-was given to each worker as advance. This was cold comfort to workers as the management announced that losses of the company from September to January would be `recovered’ from workers’ back wages and that this `recovery’ would continue till the loss was compensated. The recovery was thus to be effected from wages that had not been paid in the first place and from allowances and benefits that had not been paid for years. For workers, it meant that there was no hope of subsequent wages either. For the management, the issue of wages seemed to be taken care of.
Thus, barring the advance, no wages were paid throughout 1997 even though the workers reported for duty. (In fact a management notice of 3 July 1997 takes cognisance of the good work being done by the workers). On 6th June l997 another agreement was negotiated demanding a minimum 100 hours worth of production before wages would be paid. As noted above, this was invalidated by the DLC. Matters reached a stalemate as the management’s proposals continued to revolve around this agreement. In August the company tried to give another Rs.1000/- as advance, but the workers refused and demanded their back wages.
Meanwhile from 24th July to end of August 1997, the management illegally terminated the jobs of about 100 workers. The mandatory enquiry into the charges against them was not conducted. The dismissal notices cite “serious misconduct” and state that “since the atmosphere in and around the factories is totally surcharged it is not possible to conduct any enquiry against you…you are dismissed with immediate effect.” Through this tactic it appears that the management has simultaneously got rid of the more vocal workers and created an atmosphere of insecurity to pressurise the rest of them.
The Management
“Management advises all workmen….to accord top most priority, over their own payments, to inputs and to outside commitments to suppliers and bankers… You are however free to continue your present stand and jeopardise your own jobs.”
Notice to workers, signed by the entire top management, 28 October 1996
The nature of the agreements signed by the management and the unions, and unwillingly borne by the workers, lies at the centre of the problem for the past two years (see Box-2). It is clear that under the norm of wages linked to specific production targets, there is the potential situation of production shortfalls due to external factors. And the responsibility for external factors has been shifted onto the workers.
This has meant that the workers spend months without wages. It becomes possible for a permanent worker with 20 years of service behind him to not even get the statutory minimum wages. This situation is sometimes explained by the management, and even by the Deputy Labour Commissioner, in terms of “no work-no pay”. But the truth is that the workers have been reporting for work and producing as much as external conditions allow. Thus a recent production report signed by a supervisor shows in an 8 hour shift, most workers have put in 2 hours of work and for the remaining 6 hours there was “lack of material”. This is a situation more akin to “no production targets-no pay”.
Another attempt to shift responsibility for external factors onto the workers is evident from the interim memo of understanding of January l997, according to which it was agreed that workers would be paid in terms of despatch. While `production’ refers to the goods produced, `despatch’ refers to goods actually taken out of the factory for sale. Thus it is possible that only a part of the production is despatched in a given period of time. According to the agreement 17% of the despatch value was to be distributed among the workers. This distances wages from the actual amount of work put in by the workers. The agreement went even further than linking wage payment to production targets and sought to link wage payment to the ability of the company to sell its goods.
Wages have not been paid not only to workers but also to staff members. According to workers, staff salaries have not been paid for 19 months. The situation is not very clear, but salaries have definitely not been paid since September l996. In a letter to the Deputy Commissioner (17 October 1996), the management has offered this explanation for its conduct: “We do not wish to believe that the staff members have instigated workmen for negative activities… However, there appears to be no inclination on their part to make efforts to increase productivity or to guide workmen away from negative activities….and if assuming they are inclined to do this they are not effective at all”. These reasons are patently absurd not to mention illegal. For example, a telephone operator’s duty is not to persuade protesting workers. Nor can the company in such an arbitrary fashion thus deny wages to the staff for not being “effective” in curbing worker protest.
Administrative Response
According to the Deputy Commissioner (D.C) the Jhalani Tools issue deserves consideration on humanitarian grounds. He believes that the Jhalani family want to make money by selling property and wants “to get out of Faridabad”. He states that the company would not be allowed to sell any immovable property without paying the workers’ dues. However the D.C. sees no point in dealing with the middle level management and is waiting for the senior Vice President (who was in Germany at the time of the interview) to return to Faridabad.
The chief labour officer dealing with this issue in Faridabad is the Deputy Labour Commissioner. According to him such a problem can be dealt with in two ways. First, there is the Payment of Wages Act, 1936, under which a company can be fined for not paying wages to its workers. However, this Act applies only to those companies whose workers earn less than Rs.1600 per month and the Jhalani workers do not fall into this category. (On the other hand the Jhalani Tools workers point out the case of another company, Hitkari Potteries, that was `challaned’ for non-payment despite its workers earning more than Rs.1600 a month. This is confirmed at the DLC’s office and provides a clear instance of differential application of the law).
A second possibility is for the workers to formally make a `dispute’ of the matter and approach a labour court under the Industrial Disputes Act. The DLC says he cannot help in this matter since the contesting versions given by different parties necessitate the gathering of proper evidence, which only a court can do.
The bottomline in every statement of various officials involved is that the workers must move the labour court. They even give off-the-record assurances that the court verdict would certainly be in the workers’ favour. An unavoidable question arises. Why has the Jhalani management, who is said to be sure to lose in a labour court, not faced any punitive action from the labour department (except challans from the Provident Fund department) for all of 19 months? The workers disbelieve such assurances and understand them as the bureaucracy’s attempts to avoid having to deal with their case. This is not surprising since over the last few months these authorities have sent the workers to seek help from sources as diverse as the General Manager of the District Industrial Centre, Faridabad, and the local Grievance Committee constituted by the town’s eminent persons.
While officials ascribe the reluctance of workers to move court to their illiteracy and ignorance, workers themselves point out the countless examples of litigation that they have observed around them in Faridabad. The average worker cannot afford the time, money and energy that he must invest, from the labour court in Faridabad, to the High Court in Chandigarh to Supreme Court in New Delhi. Workers pointed out the case of the East India Cotton Company in Faridabad as an example of the near irrelevance of the legal machinery to their cause. The Jute Mills of this company were closed in 1983. Despite a prolonged court case the 900 workers retrenched at that time have still not managed to retrieve their due wages and gratuity in 1997. In August this year, they went back to sitting in demonstration outside company gates.
Conclusion
“…ration shops do not give us food on credit any more…electricity connections are getting cut…children’s education is in jeopardy…our daughters are of marriageable age…please do get our husbands their wages or we will be forced to commit suicide.”
letter to D.C signed ‘wives of workers of Jhalani Tools’, August 1997
Over a long period of time the Jhalani Tools management has deprived its 2000 workers of their wages and other rightful dues for no fault of theirs. In a vicious cycle, the management first created (and allowed to exist) such conditions that work could not efficiently take place. Then, the workers were denied remuneration on the grounds that no work had taken place. And when the workers protested against this injustice, remuneration was further cut in terms of fines and `recovery’. Moreover, they have had to face arbitrary dismissals, without any right of reply, from their 20 years of service.
In such a context many workers are being forced to seek new sources of livelihood, however ad hoc and insecure these may be, and are unable to pursue the matter of their dues any further. It is possible that some would accept a pittance from the management and in return forsake their rights to much larger dues. Thus, while the management has already laid off its workers without giving the situation its correct name (see Box on page 8), it is further, effectively creating a situation of retrenchment without having to bear the responsibility of calling it retrenchment.
Today, the fear of the workers is that the management does not wish to run the company any more but is not openly saying so. Jhalani Tool’s background of sickness in the 1980s and, even today, the management’s constant references to paucity of funds for paying wages, and to a backlog of problems, make workers apprehend that the management would prefer to close down the company and is trying to extract all that it can from various sources, before closure. The workers dues provide a large number of such sources to the management.
Many instances discussed in this report support such an argument. First, it is not just workers’ monthly wages that are in dispute. The crores of rupees involved in unpaid Provident Fund, E.S.I, gratuity etc. take this issue far beyond the realm of controversial agreements and disputes over work done or not done. Second, arbitrary non-payment of staff salaries also adds to the suspicion that the management is fomenting problems with the workers, to not only save on their dues, but also to appropriate money from other sources. Another pointer is the management’s attempts to sell the third plant which was closed in 1984. Questions are particularly raised about the closure of this plant, when of the three plants, it was in best running condition. The workers have petitioned the Deputy Commissioner to prevent this eventuality since, according to them, this would foreclose any possibility of third plant workers getting their wages and gratuity. Finally, even the Deputy Commissioner’s reading of the situation is the same. He asserts that the owners want to close the plant, sell and withdraw from Faridabad.
As things stand today the Jhalani Tools workers find themselves in a beleaguered state. Yet another ad hoc committee has been formed recently which is waiting for the management to initiate a fresh round of negotiations. The administrative machinery claims not to be able to respond to their problem and pushes them towards court. And courts provide an expensive, time consuming option that seems to be no option at all. For Jhalani Tools workers, will a backlog of unpaid wages, an absence of Provident Fund or gratuity to on and prolonged litigation with no guarantee of results, ever compensate for a lifetime of labour?
BOX-1
Saving on the Workers’ Bill
“The gain of the company is our collective gain. In its realisation some delay may take place. But it is an unbreakable law that when we gain from something [i.e. the company], or may gain from it sometime in the future, then it is essential that we have reverence and gratitude towards it”.
Translation of a Hindi notice to workers
sd/- Y.C. Jhalani and P.C. Jhalani, 27 December 1996
Non-payment of wages: Wages have not be paid to 2183 workers between March 1996 and September l997. According to the workers their salary ranges from Rs.2800/- to Rs.3200/-. Taking Rs.3000/- as a rough average the amount gained by the company at the workers’ expense adds up to 12 crore 44 lakhs and 31 thousand rupees.
Non-payment of bonus: 2183 workers have not been bonus for 2 years. At about Rs.800/- per worker, per month, this amount is 34 lakhs 92 thousand rupees.
Non-payment of Leave Transport Allowance : LTA is Rs.1500 per worker per year and has not been paid for 3 years. This works out to 98 lakhs 23 thousand rupees saved by the company.
The loss to each worker on account of the above three categories amounts to approximately Rs.60,000. However, the workers have also been denied other dues, of a qualitatively different nature.
Non-payment of ESI dues: The workers have complained to the Regional Director, Employees State Insurance Corporation that despite having ESI cards they get no medical facilities at ESI hospitals for 3 years now. “On being asked the officials say that the company has not deposited dues”.
Non-payment of P.F.: The current union calculates that Provident Fund amounts have not been deposited since May 1994. P.F dues are also missing for 5 years in the mid-eighties. (This is partially confirmed by the company’s annual report for 1995-96). According to Labour Department officials, challans have been issued against Jhalani Tools in this regard.
Non-payment of Gratuity: Workers allege that the company has not paid service gratuity due to them for many years. This too has been confirmed by Labour Department officials.
BOX-2
Relevant Legal Provisions
Minimum Wages Act, 1948: Under Section 25, “any contract or agreement whereby an employee either relinquishes / reduces his rights to a minimum rate of wages, or any privilege or concession accruing to him under this Act, shall be null and void in so far as it purports to reduce the minimum rate of wages fixed under this act”.
Indian Contract Act, 1872: Under Section 23 ,”the considerations of or object of an agreement is lawful, unless it is of such a nature that if permitted it would defeat the provisions of any law or the court considers it opposed to public policy”
Industrial Disputes Act, 1947: Under Section 2 (kkk), ‘lay off’ is a failure, refusal or inability of the employer on account of shortage of coal, power or raw material, or the accumulation of stock, or breakdown of machinery, or for any other reason, to give employment to the workmen.
Under Section 25-M lay off is prohibited:
sub-section (1) no workman in an establishment employing 100 or more workers are to be laid off except with prior permission of the government, unless lay off is due to shortage of power or natural calamity.
sub-section (2) a copy of the application for permission is to be served on the workmen.
sub-section (8) lay off without adequate permission is illegal and workmen are entitled to all benefits as if they had not been laid off.
Section 25-C entitles workmen who have been laid off (with adequate permission) to 50% of the total of their basic wages and dearness allowance.
Further, under the Provident Fund Act, (Section 14, Section 14A, Section 14 AB) non-payment of Provident Fund deposits and under the Employees State Insurance Act, (Section 85) non-payment of P.F. and ESI contributions are punishable offences. Criminal cases can be instituted, responsible persons arrested and prosecuted to ensure compliance. Payment of Bonus Act (Section 28) similarly makes the non-payment of Bonus an offence.
* Dedicated to the Memoirs of Shankar Guha Niyogi
* FMS – October 1991
On 28th of September 1991, the central figure of the Chattisgarh Mines Shramik Sangh – Shankar Guha Niyogi – was killed through gunshot. With the explicit intention to quell the workers’ movement in the Bhilai area he was shot dead at three to four o’clock in the morning, in his house, asleep. This murder took the workers’ movement, which had been influenced by Niyogi during the last 15 years, to an important turn on its way. While the account of these 15 years is, above all, of utmost significance for the Bhilai area, its importance is true for the workers’ movement as a whole. Following we try to give a wider account.
The setting-up of the Bhilai steel plant forms an important link in the collaboration between Russian and Indian capitalists. Manufacturing hundreds of thousand tons of steel, the factory requires an immense supply of raw material. About eighty to ninety kilometres from Bhilai are the iron ore mines of Dalli Rajhara, source of the main raw material. In these mines about 12,000 male and female workers hired through contractor are engaged in bone-breaking work for 5 Rs a day. In 1977 these workers started a strike for bonus payment under the joint leadership of INTUC and AITUC. Seeing that the strike increased in might, the INTUC-AITUC leadership announced the end of the dispute, saying that the bonus has always been an exclusive entitlement of the permanent work-force alone and that the workers hired through contractors have no right to it. The striking workers reacted by chasing the INTUC-AITUC leaders away. They formed a strike committee and continued the struggle. Finally they chose the recently released Shankar Guha Niyogi as their strike leader – Niyogi had been accused of being a Naxalite and put into jail during Emergency. The strike carried on.
In 1977 the Janata Party Government – in an attempt to break this strike – managed to arrest Niyogi in a swift-raid, but the police unit did not manage to break through the subsequent encirclement formed by ten thousand workers. Under the pretext of freeing the trapped police unit a huge deployment of police started shooting on the assembled workers. The shooting continued throughout a day-long operation, killing eleven male and female workers. Even after the killings and the following wave of state repression the workers did not budge. After four month the strike forced the government to give in and the Bhilai Steel management had to offer a deal to the striking contract workers. In this way the Chattisgarh Mines Shramik Sangh obtained its concrete foundation and Shankar Guha Niyogi came to the fore as its central figure.
The 1977 incidents of the Bhilai iron ore mining area Dalli Rajhara and the person of Shankar Guha Niyogi became of importance for the manoeuvres of the Indian political landscape – the Indian state being situated between the capitalist blocs of America and Russia. The CPI, for example, presented Niyogi as an agent of the CIA. The liberal and patriotic factions of capital started to get excited by Niyogi’s private life and by what they portrayed as his reformist efforts. For the section supporting ‘national capital’ – under the cloak of Naxalism – Niyogi became a bone in their throat, which they were neither able to swallow, nor to spit out. In Madhya Pradesh Niyogi was made into a part-taker in the in-fights between factions within the Congress Party and in the regional capitalist election politics. In the current elections he was a member of the Indira cabinet and he supported openly the Congress candidate for the Kanker (Chattisgarh) regional constituency, Arvind Netam, and the Janata Party candidate from Bhopal, Svami Agnivesh… but we think that the important fact remains that Niyogi has played a central role in starting a continuing workers’ struggle in the Bhilai area.
In 1977 the contract workers in the mining areas of Dalli Rajhara had been paid 5 Rs per day. Today they get 80 Rs daily wage. Since 1977 they are paid stand-by wages – before that they used to be sent back home unpaid once there was no work available. The workers were successful in halting a major redundancy drive, attempted by the management through mechanisation. Although only few people are able to get permanent job, the contract workers managed to enforce gratuity bonus (service) and 7 days casual and 5 days paid annual leave – a certain degree of job security. The workers fought a long and hard battle for this. In 1981 the struggle for job security and against mechanisation turned into a strike – Niyogi and Sahdev Sahu were arrested. During the long strike each demonstration of the workers in Dalli Rajhara got lathi-charged by the police and each following day the strikers returned and demonstrated in front of the main administration of Durga district. Nevertheless, over time mechanisation increased and numbers of workers fell due to, among other reasons, a stop in hiring – both diminished the power of the Dalli Rajhara contract workers. In the meantime Niyogi made a noteworthy active effort to foster the emergence of workers’ movements in the factories neighbouring the Byhilai Steel plant. The successful outcome of the three-month long struggle of contract workers at ACC Cement factory in July 1990 was the first gain of Niyogi’s union in this area.
According to the enforced contract at ACC Cement the contract workers were entitled to 20 days guaranteed work per month, provident fund, paid and casual leave, medical treatment and school education for children paid for by the company management. This agreement had an immediate effect on the workers in Bhilai industrial area. Only very few workers employed in the 105 factories of the area were permanent. The management in the area would not even stick to the capitalist labour laws. In the majority of the factories there were recognised unions affiliated to the two central trade union organisations, but instead of working in the interest of the workers they rendered their service to the management. Motivated by the success at ACC Cement tens of thousand workers started to get organised towards this new direction. A workers’ movement erupted in the area demanding higher wages, better working-conditions and 20 per cent bonus. In order to change the situation and calm things down the government tried to detain the general assembly of Niyogi’s union in Bhilai.
Despite the management’s unity, alertness and open intimidations a strike started under the lead of Niyogi’s union in the four Simplex factories – Bhilai’s biggest industrial complex. After attempts of bribery, threats, framing and arrests of 800 workers by the police did not prove successful in stopping the movement, the government came forward with an ancient legal case against Shankar Guha Niyogi and arrested him on 4th of February 1991. After two month he had to be released on bail. The workers’ struggle expanded and gained in strength. On 25th of June 1991 the demonstration of Chattisgarh Distilleries workers was attacked by police with lathis and gunshots – 150 workers were injured, 107 workers were arrested. In response to this attack workers in 1,000 factories of the area stooped work an demonstrations started in Dalli Rajhara and other places. Seeing that they could not control the workers the government tried to ban Shankar Guha Niyogi from the area of Bilaspur-Raypur-Durga-Rajanandgaon-Bastar – the High Court (only) officially put a halt to this ban. At the beginning of September 1991 hundreds of workers followed Niyogi to Dehli and protested in numerous places.
To keep the struggles in Bhilai Steel Plant area running, the support of the Dalli Rajhara mining workers 80 kilometres away played an important role. The Shahid Hospital in Dalli Rajhara – founded and run by the mining workers in memory of the victims of the 1977 police-attack – gave treatment to those Bhilai workers injured by goons and police during the dispute. Once a week a doctor from Shahid Hospital would go to the bastis of the striking workers for medical treatment. Despite having to be cautious given the running bail-cases, Niyogi’s union kept on supporting the striking workers with rice-dal and financial support. After ten months of strike a worker from one of the factories said in his own words: “This is a union of a different kind.”
To put it brief: in this situation, where many attempts to get workers back under control had failed, certain capitalist factions decided to have Niyogi murdered. In the current situation it is necessary to have a look at the weaknesses of the workers’ movement under Niyogi’s leadership, too. The importance of the permanent workers employed in both the mines and in Bhilai Steel plant has been neglected: this is to a significant extent due to Niyogi’s ‘ideology’. At times ‘tactics’ can be important, but in the attempt to ‘forge a unity at all costs’ the importance of individuals-particularities can grow in result. The way that Niyogi has operated in the area contributed to this tendency. In 1981 the workers hailed the Bharatiya Janata Party after the party gave some speeches against the arrest of Niyogi, after that the workers applauded the Janata Dal, they asked to vote for the Congress candidate, they praised Mohandas Karmchand Gandhi… this did not contribute to the development of a revolutionary workers’ movement. Once in this position it is not too difficult to turn workers into pawns for the various capitalist groupings. Today the Chattisgarh Mines Shramik Sangh is pretty much in a similar situation to 1981, after Niyogi’s arrest. At that time a striking worker said: “Shankar Guha Niyogi is our eye, without him we are blind,” a meaningful comment then and still. Currently the the workers’ movement in Bhilai-Dalli stands at crossroads, the active people within the movement are confronted with a decisive moment. The swamp of liberal capitalists, the whirlpool of militant national-capitalists or revolutionary workers’ movement: the time has come to chose. The murder of Niyogi has made matters urgent.
[The movement in Chattigarh continued after Niyogi's death. The strike for better conditions continued till July 1992, attacks from state and companies increased, various parties tried to jump on the movement and at the same time tried to prevent a called for general strike, 800 workers were kicked out of Chattisgarh Distilleries in 24th of January 1992 by mass police force. In mid-June workers started rail-road blocks, e.g. the Calcutta-Bombay lines, In July 1992 police opened fire on a protest of 5,000 male-female workers, killing 16 people. A curfew was imposed in the area]
http://www.questia.com/googleScholar.qst;jsessionid=M02JB6WZmKkgF5BNPH1tJmFN1G6j6sX2GPJbFmgf6kPpJZyLpylr!1896127874!1380883283?docId=98203572
[EPW Files]
* Police Firing on Striking Workers
EPW no.25, 1998
Striking workers of a textile mill were fired upon by the police, workers’ houses and property destroyed and residents of the colony beaten up. What led to this brutal attack?
ON February 19, a contingent of the Haryana police fired upon protesting workers of the Pashupati Spinning and Weaving Mill at Dharuhera, Rewari district, Haryana. Four workers were killed in the firing and five others received bullet injures. The workers then blocked National Highway 8 (on which the factory is situated) through the night. In order to remove them the police carried out a lathi-charge on the morning of February 20. In the course of this operation, they entered workers’ houses, destroyed household goods, smashed doors and windows,and beat up the residents, including women and others who were not associated with the mill. Twenty-one people were seriously injured in the process, and many others received minor injuries.
The Pashupati Spinning and Weaving Mill is part of a nationwide group of 50 companies, controlled by the Jain Shudh Group. It is a public limited concern, in commercial operation since 1981. It had a turnover of Rs 103 crore in 1997. The Mill is part of the Dharuhera Industrial area about 20 km away from the district headquarters at Rewari, and about 60 km from Delhi. The highway in front of the factory is the main trunk route between Delhi and Jaipur. There are four plants in the Mill, which operate on 3 shifts – A, B and C, each of eight hours duration, starting at 8 am, 4 pm, and 12 midnight respectively. In all, there are 3,000 workers in the factory. There are very few women workers. Most of the workers are migrants from eastern UP and Bihar and live in rented tenements owned by local residents next to the factory or in the nearby Kapdiwas village. About 200 labour quarters are provided by the management behind the factory. In the factory, workers are divided into unskilled, semi-skilled and skilled categories. While the nature of jobs vary, there is comparatively little variation in the wages received by them. These amount to about Rs 2,200 per month, for skilled workers while those in the semi and unskilled categories get somewhat less. None of the workers get proper appointment letters or proof of employment. Nor do they have attendance cards or leave cards guaranteed to them by the Factory Act (1948). The management therefore conveniently shifts permanent workers who go on legitimate leave for a short period into the temporary category when they return. There are at least 1,000 temporary workers in the factory at any given time. Many remain in this capacity even after working for several years. Such action by the management is violative of the right of the worker to be considered to be in continuous service if he goes on legitimate leave (under Section 25 B of the Industrial Disputes Act) and thus get their due wages. While the management claims that Provident Fund is being deducted from the salaries of the workers, no records to this effect have been maintained for a number of years. Some of the workers have not been covered under the Employees State Insurance (ESI) scheme and cannot avail the benefits of the ESI dispensary at Dharuhera. Non-payment of PF deposits and not giving ESI benefits are offences punishable under S 14, 14 A and 14 A-B of the PF Act and S 85 of the ESI Act. Compliance to these norms can be enforced by the labour court.
Union-building efforts had been started in 1987 under the Haryana-based trade union, Lok Hit Mazdoor Sangathan and its leader Sukhbir Singh Arya. This was smashed soon afterwards by the general manager, J S Marattha. The Lok Hit Mazdoor Sangathan, however, remains the official union in the factory. In October 1997, after a conciliation process, the management arrived at a 3-year wage settlement with this union before the deputy labour commissioner (DLC) at Gurgaon. The issues raised by workers were annual increment, issue of attendance cards, leave cards, maintenance of PF records and covering all workers under the ESI scheme apart from appropriate wage revision. None of the general demands were addressed by the settlement, and the wage revision too was an inadequate one. The DLC was guilty of not ensuring that the settlement was done with a union that genuinely represented the workers. Workers were not satisfied with the limited settlement. Subsequently another union, the AllIndia Textile
Mazdoor Janta Union (AITMJU), affiliated to the ANURAG Federation and headed by K K Shukla, started organising the workers around the same issues raised in the settlement. The workers under the new union also demanded that though inadequate, the conditions of the earlier settlement be implemented immediately. The agitation intensified in January 1998, and large meetings of the workers were held. The dispute between the workers, the new union and the management at the DLC’s court continued. The management on the other hand claimed that the settlement made in October had stated that no fresh demands would be made for three years, so the demands for PF records, employment proof, etc, were illegitimate. It also failed to implement the existing settlement. In February, workers launched a go-slow agitation over the same issues. The management then arbitrarily suspended one of the most active and articulate protesting workers on the grounds of deliberately preventing production and inciting workers. This amounts to an ‘unfair labour practice’ punishable under S 25 U of the Industrial Disputes Act.
Whatever may be the case the management had kept the police informed and demanded police assistance to put a stop to union activity from January onwards. The police were called during each of the meetings of the union. In February, the management, determined to break the union and to bring ‘indisciplined’ workers to heel, called upon the SP and the DC to give them extra policemen to deal with the go-slow agitation, which had been leading to loss of production and profits for the management. Industrial disputes do not fall under the jurisdiction of the district police. However this was not the reason given by the administration’s inability to aid the management in early February. It was said that the police were required for conducting the forthcoming national elections and would be able to assist only afterwards. And on February 19 therefore, the police served the ends of the Pashupati management and fired upon the workers.
At about 5.45 pm on February 19 (about a week after the go-slow agitation had been launched) soon after the second shift (B shift) workers had started work, most of them were ordered to go outside the factory by an enraged management, on the ground that if they were not interested in carrying out production work then they should leave the premises.
The management was assisted in carrying out this illegal lock-out by its own goons and policemen of the Dharuhera P S. The lathi-wielding police and goons numbering about 50 in all, roughly pushed workers out. About 200 workers were kept inside. As second shift workers were thrown out, other workers came out of their houses in the vicinity of the factory and joined them. All of them together demanded that the workers still confined inside by police and management should be allowed to come out. The police, having helped the management in throwing out workers, stationed themselves inside the factory gates. Instead of complying with the workers’ demand for the release of their fellows they ordered the 500-strong crowd of workers to vacate the area outside the factory. The SHO called the SP Rao Sohan Lal and SDM Roop Singh. They reached at about 7 pm. Tear-gassing was started by the SDM’s orders. According to the police, about 50 tear-gas shells were fired. However workers insist that tear-gassing lasted for a very short while. The police, under the SDM’s instructions, started firing even as the tear-gas shells were exploding. Approximately 50 rounds were fired. No warning of firing was heard. According to some of the injured, firing occurred in spurts. This is borne out by the accounts of two workers who have bullet wounds. Thinking that the firing had stopped, they went forward to help a fellow worker Pramod, when they themselves were shot. Two workers, Pankaj and Sardaru Singh, died on the spot, while Pramod and Vinod were seriously injured, and later died. Some of the workers also sustained injuries from country weapons fired by goons of the management working in concert with the police. The firing stopped at about 8.30 pm. The workers locked inside were allowed to leave the factory only at night. Many workers then blocked the highway in front of the factory and sat there guarding the two dead bodies till the morning. Reinforcements of police started arriving from 4 am on February 20 from the neighbouring districts of Mahendragarh, Faridabad and Gurgaon to clear the highway, under the orders of the DC. Over 200 policemen removed the protesting workers from the highway by lathi-charging them. What was described by the DC as a ‘mild lathi-charge’ led to several workers sustaining severe and multiple fractures. As workers ran off to safety into the nearby Lal Singh and Roshan Lal colonies, the police followed them. Long after their objective of clearing the highway had been achieved, the police continued to break down doors, window grills and locks, and even thrashed sleeping women, children and others not associated with the Mill. When our team went to Dharuhera on February 22, we saw broken doors hanging on hinges and bent and twisted window grills. After this assault, over 150 workers were rounded up and taken for ‘questioning’ to the police station. Eighty-six of them were brought back to Dharuhera at about 2 am on February 22, after pressure was exerted by workers of nearby factories, as they were found to be ‘innocent’. Seventy-one workers were found to be ‘guilty’ and arrested. Out of these 33 were arrested for the incident on the 19th (FIR No 100/98, Dharuhera P S) and sent to Rohtak jail, and 38 were arrested for the incident on February 20 (FIR No 101/ 98) and sent to the jail at Bhiwani. They were arrested under Sections 148, 149, 307,436, 341, 332, 353, 186, 283,506,450 of the IPC (for rioting, unlawful assembly, attempt to murder, arson, wrongful restraint, injuring and obtructing public servants, obstructing roads, trespassing and criminal intimidation). Those arrested for the incident on the 19th were also charged under S 25, 54, 61 Arms Act, solely on the basis of a police claim of having recovered a bullet casing of a country weapon from the spot. In fact (as mentioned earlier), it was the goons of the management who were wielding and firing country guns at the workers.
It is not clearon what grounds some workers were identified as guilty and others treated as innocent. The workers or their union were not given list of those picked up and arrested. This aggravated the atmosphere of fear and uncertainty as workers were unaware of the whereabouts of their fellows. In addition, after the lathi-charge on the 20th, the workers who used to occupy the few labour quarters provided by the factory were also forced to vacate by the management, and their property thrown out. Mostly migrants, some of the injured workers had no families at Dharuhera nor any alternative support system, and were dependent on their co-workers for medicines and money. Of those lying injured in the hospitals, some workers had families living near the factory, but were not aware of the condition of their families.
OFFICIAL STORIES
The police account states that they had gone to the factory on February 19 in response to an earlier complaint by the management. The management had accused some workers of breaking machinery and assaulting a supervisor. The police say that the workers voluntarily walked out in protest against the suspension of their colleagues and started throwing stones, after which they shut the factory gates in order to protect the machinery and the remaining workers inside. After appropriately warning the workers, the police fired from inside the gates. However, the police and the DC say that this was directed at the air, and not at the workers. Since workers were standing on roofs of nearby houses and trees in front of the factory, they got hit and some got killed. Three policemen were injured but none seriously. It is important to note here that there are no buildings in front of the factory gates, and the nearest houses are low roofed tenements located at a considerable distance on one side of the factory walls. The trees in front of the factory are of the tall, smooth-trunk variety, with very few branches. The workers continued to pelt stones even as some of them were getting injured and killed. According to the DC, they would break up into groups, collect stones, re-group to throw stones at the police, ‘like guerillas’. Although she was not herself present at the time, she felt that the response of the police was justified under such fierce resistance. The DC’s explanation for the attack on people on the morning of February 20 is that the workers who had been blocking the highway were given shelter by the residents in the colonies. Many of these residents were also fellow workers and guilty of stone- throwing the previous evening. According to her, women and non-workers had to be beaten to catch the ‘guilty’ workers. The workers had clung to the window grills, and had to be prised apart from them by the police, causing the grills to get bent and twisted. While maintaining that they had summoned the police because the workers had walked out voluntarily and started throwing stones at the factory, the management stated that the entire incident took place outside the factory gates, which allows them to disclaim all responsibility.
Treatment of those injured in the police firing and assault, a legal right of the injured was completely denied to the victims at Dharuhera. On February 19 night, five of the more seriously injured workers were brought by other workers and local residents to the Rewari Civil Hospital. One of them 20-year old Pramod Kumar, was referred from there to Safdarjung Hospital in Delhi, where he died. Another, Vinod died soon after he was taken to Gurgaon Civil Hospital. The remaining four in Rewari Hospital had not even been x-rayed till February 21, and their bullet wounds had merely been sown over. On February 21, three of them were sent to the government hospital at Bawal, about 25 km away, to be x-rayed. Most of the expense for this had to be borne by the workers themselves. Even at the government hospital every x-ray exposure costs Rs 60, instead of which the doctor at Bawal asked for Rs 110 each. The DC finally intervened on February 22 and two workers got x-rays through the Red Cross. Twenty workers had been admitted to Rewari Hospital on February 20, all with injuries sustained in the lathi-charge. Again, they were brought in by the co-workers and not by the police. One of the patients who had been sleeping in his room when the police raided,
said the police repeatedly tried to hit him on the head. He managed to fend the blows off with his arms and hands, which bore the marks of severe beating. The DC has persuaded the management to declare compensation of Rs I lakh to the families of the dead; Rs 20,000 for seriously injured and Rs 10,000 for simple injuries. The DC was trying unsuccesfully to get the management to give at least part of the money as a ‘gesture of goodwill’ to the workers on February 22 itself so that they could use it for their treatment. The management is clear that this is not ‘compensation’ since they bear no responsibility for the firing, but merely an act of largesse. The union has demanded Rs 5 lakh per deceased victim, which was refused by the management. No compensation has been declared by the state, in clear violation of the right of citizens to compensation when the state kills and injuries in blatantly unjustified firing.
The firing at the Pashupati Mill shows the way in which the law and order machinery was used to serve the interests of the Jain group. While The SP and SDM gave the actual order for firing, knowing well that the police were being used as a private army of the management, while the DC justified the firing and the lathi-charge. However, now that the police have served their purpose, the management is trying to distance itself from the firing and lay the entire blame on the police and the workers.
The NHRC is currently conducting an inquiry into this case. The agitation of the workers is now temporarily stalled. The same policemen continue to operate at the Dharuhera P S. Workers with fractured limbs and injured heads have used up savings to get themselves treated at private hospitals and some have gone back home. Ironically, through this one-sided intervention of the state, it is workers who were denied their rights, thrown out of the factory, fired upon, beaten up and are now in jail under grave charges punishable with terms up to life imprisonment.
A joint action committee (JAC) of representatives of workers and unions of different factories as well as 10 representatives of the AITMJU was set up on February 21 and a large demonstration of workers numbering between 5,000-10,000 was held. It demanded arrest of the GM, payment of due compensation and meeting all earlier demands of workers. The GM was arrested to humour the workers, under a minor charge (S 216, IPC harbouring criminals) for apparently giving shelter to the goons who he had engaged to break the union. He is out on bail. Through continuous meetings before the DLC between February 27 and March 6, a temporary agreement was reached between the management and the union regarding compensation. It finally agreed to a compensation of Rs 1.75 lakh for death. Moreover it promised to extend ESI facilities to all workers and also provide a job for one member of the family of each worker killed. The JAC meanwhile held another large public demonstration on March 5, and continues to push ahead with its demands. In the firing at Pashupati Mill both the state and the management stand completely exposed by the management agreeing to pay compensation for firing actually executed by the police. Instead of ceding the workers’ demands earlier, or even negotiating with workers the management decided to end the workers’ agitation by declaring an illegal lock-out without any prior notice. This led to the police firing. The brutal fact remains finally that the management agreed to a few of the reasonable and legitimate demands of the workers only after four workers were killed. Several demands have still not been agreed to.
[This is a slightly condensed version of a report on the incident. The People's Union for Democratic Rights (PUDR) which sent a five-member fact finding team to Dharuhera and Rewari on February 22. The team met the factory workers, Navraj Sandhu, the deputy commissioner at Rewari, Ram Kumar, the SHO of the Dharuhera PS and Ramesh Jain of the Pashupati Mills management at Delhi.]
* Self-Activity of Wage Workers
Theories and practices of representation & delegation are a stumbling block in the self-activity of wage-workers. They hinder wage-workers’ resistances, refusals and steps of change. What follows is a part of a larger critique of representation & delegation that we are engaged in. We invite you to join us in this attempt.
CONTENTS
*** Lead-ry
*** Routine lead-ry
*** Lead-ry – Department of conflict management
*** Self-activities of wage-workers
*** Activities of a fringe left
*** A critique of a fringe left
*** A preliminary sum-up
*** Self-activity of wage-workers against Politics of Closure
KK/ Collectivities, April, 1998 Majdoor Library, Autopin Jhuggi, N.I.T. Faridabad, 121001, India
*** Lead-ry
For over four years now we have encountered numerous arguments and counter-arguments in conversations amongst wage-workers on the role of leaders in routine factory life. The backdrop to these conversations has been the unfolding of events in factories where workers find themselves trapped. What is attempted here is a systematization of numerous experiences and observations to obtain a better understanding of shop-floor life in order to confront it more effectively.
“On the shopfloor we are at all times in direct antagonism with the supervisor/ foreman. This antagonism is because of the supervisor’s constant attempt to maintain work flow.”
“Supervisors constantly keep their eyes on us. They threaten us with charges, threets & suspension, placate us with overtime & advance payments and use outright deceptions to keep us in check.”
“Supervisors constantly nag us to fulfill production quotas and maintain quality. They perpetually hassle us to ensure a minimal rejection of products. Raw material utilization is another never-ending bone of contention.”
“We never tell supervisors what is in our hearts. No supervisors can know what we are thinking and planning. They are actually in constant fear of us.”
“Routinely we engage in slowdowns, quality slackening, wastage, breakage and clogging. Breakage and clogging are what we all do, all the time – but never talk about it, even with each other. We never even voice our appreciation or acknowledgment of what someone has done … its an open secret.”
“Whenever the discontent on the shopfloor becomes very sharp and the atmosphere surcharged, supervisors lose their voice.”
*** Routine Lead-ry
“Leaders are from amongst us. We have an ambivalent relationship with them.”
“Because they are from amongst us, leaders know a lot about us, about our inclinations and our thoughts. Leaders do not work themselves. They tell us to ensure that production does not fall and promise to take care of the rest as they claim to be our watchdogs (pahredar).”
“Leaders have financial clout. This is not just from union dues & other collections. A lot of money comes from cuts & commissions in the purchase of uniforms, shoes, festival sweets, festival gifts like blankets, almirahs, suitcases, watches and kitchenware. Cuts from canteen contractors and scrap-dealers. Lumpsums from managements for long term agreements. Control of cooperative societies and welfare funds.”
“Contenders for leadership spend a lot of money during elections (in the factory). Because leadership means financial clout.”
“Being a leader entails no work in the factory and much money. This is enough to sway a lot of workers.”
On small benefit networks
“Leaders, ex-leaders and potential leaders create and maintain intricate networks spread throughout the factory through incentives like advances, loans, lighter jobs, preferable shifts, employment to kith & kin, gate passes, tours, better food from the canteen without any payment, grants from welfare, first preference.” Networking by leaders also uses caste and regional identities.
“Leaders and ex-leaders are often found ensconced in the offices of the personnel manager or some other official. Persons with close links to this or that managerial faction can provide facilities to their close followers (laguea-bhaguea). Leaders and their camp-followers makeup ten to fifteen percent of the factory’s workers.”
“Those who constitute the networks are articulate in various ways from muscle power to slippery tongues.”
“These networks which are constituted on the basis of material incentives and favours are very intricate. They make a “tantra” and “jaal” (apparatus and mesh) to keep constant tabs on, as well as affect the weather and temperature on the shopfloor.”
“Those who constitute the networks are conduits for the circulation of rumours, baits, airy-fairy promises, and even lies. These networks make constant efforts to justify and valorize leaders and their powerful social & political links.”
“Leaders are basically middle-persons. And like all middle-persons they sometimes get small things done for us on an individual basis.”
“We have everyday fears of disciplinary actions, chargesheets, suspensions and physical attacks. Leaders’ networks routinely highlight, heighten and exaggerate these fears to keep us pacified.”
During shopfloor confrontations
“Supervisors run away from the shopfloor whenever worker discontent grows and workers take an openly confrontationist stance. In such cases management refuses to talk to workers directly. It sends leaders to the shopfloor.”
“Most of us weigh the situation again and again, and hesitatingly take steps back and forth on contentious issues. Leaders’ networks try to pacify us by exaggerating our fears. Meanwhile, the networks of ex-leaders and potential leaders try and instigate us to an openly confrontationist stance in an attempt to establish their leaderships.”
“Leaders’ pet rant to pacify us is that ‘you start the work, we’ll take care of the matter’. When workers refuse to listen and open confrontation continues, selective suspensions and dismissals begin.”
“In such situations, suspensions and dismissals force workers to talk to the leaders. The leaders then scold workers for having taken steps without their advice. They present the suspensions and dismissals as a consequence of not heeding them.”
“The issues of contention are effectively sidelined by the leaders. They shift the focus to suspensions and dismissals.”
“Routinely, when workers demand small relief on individual or group basis, the management does not act. When leaders say the same thing, the management acts. This increases the power of the leaders.”
Some conclusions
“We used to give union dues on the understanding that we would get benefits in exchange. Wages will increase and our jobs will be safe. But during the past twenty years things have been just the opposite.”
“For twenty-eight years I have been witnessing a reduction in the number of workers and an increase in production.”
“Earlier we used to give union dues but now the management deducts union dues from our salary.”
“Trapped by one assurance or another, we contribute union dues. It is only later that we find that all these assurances were hollow.”
*** Lead-ry: Department of conflict management
Lead-ry is an art and a science, mastered only by a few, and used to sit on our heads. It requires:
· Sharp skills in discontent measurement and the ability to arrive at swift quantitative solutions i.e. ‘at what’ and ‘at how much’ will the workers accept the disagreeable. This involves a wide spectrum of activities ranging from passing on sums of money to slapping a supervisor’s face.
· Highly developed rhetorical skills, which are used to sway, to create prejudice and to convince.
· Organising skills, which are used to build and sustain well-oiled networks at minimal cost. These skills involve astute psychological reading of individuals and groups of individuals. They also require a down to earth grasp of identity politics and maneuvers.
Managements’ regime of work, productivity and discipline is routinely confronted and opposed by wage-workers. Routine activity of lead-ry is to coax, cajole and threaten wage-workers into accepting these regimes. Lead-ry routinely negotiates agreements with management and attempts to implement them by overcoming wage-workers’ opposition. “Whenever a new machine or fixture is brought workers refuse to work on them. Leaders are the main instruments to implement these changes. Placation, suspension and fear are used by leaders for this.”
The main activity of lead-ry is to actively discourage the routine self-activity of wage-workers. Individually and in small groups, workers are always taking steps on their own that disrupt the work-routine. These seemingly minor irritants are a major threat to production and discipline. Leaders and their networks, i.e. lead-ry, is constantly engaged in hindering, devaluing and hijacking the self-activity of wage-workers.
To put it bluntly: higher management makes strategies, leaders & personnel managers act as tacticians, and supervisors & leaders’ networks execute these strategies.
*** Self-activities of wage-workers
Perhaps not universal, it is still true that most people have the capacity as well as the ability to act and participate as “NOT AS UNEQUALS” in small informal groups. The layering of experience, the excitement and the unpredictability associated with what takes place each day is not because we participate as ‘equals’. Instead, it is because each of us carries our individuality and is able to express it freely in such groups. This participation as “NOT AS UNEQUALS” is spread over various facets of life and an individual is often a participant in more than one informal group at most times. The wider implications of these informal groups of “NOT AS UNEQUALS” stand out clearly when we look at their play in some detail in institutional structures, whether factories, offices, banks or the media.
The moment of entry into a factory is the moment of entry into the disciplinary grid of work & productivity, as well as a jungle of informal groups. Strict entry schedules set up by managements are transformed into stretchable entry times. The act of punching-in is often put into disarray by proxy-punching or transformed by kicks that literalize the machine into a punching bag. ‘Entry time’ is made distinct from ‘commencement of work’ by long handshakes – backslaps – chitchat. It is often that work commences after 9 o’clock tea in an 8 A.M. shift. Management strategies like changing the placement of the ‘punch-in’ from factory gate to departments, the imposition of fines, like a fifteen minute wage-cut for being late by one minute, are visible signs of managerial desperation.
Proxy-punching in the Goodyear Tyre factory has forced the management to issue identity cards containing computer floppies, even though it has meant an increase in cost. Workers’ kicks in the Bata Shoe factory repeatedly dysfunctionalized the punching machine and forced the management to appoint an attendance clerk to go to each department and mark workers’ attendance.
Using lead-ry networks, management conducts time studies to work out grids of intensification. These are the periods when the wink of an eye and the utterance of a phrase put into practice well thought-out schemes involving co-ordinated steps by small affinity groups of seven-eight workers. And, whether they are premised on time studies or on agreements with leaders, the biggest stumbling block to increases in the workload are the informal groups of workers.
Keeping the immediate supervisor in check is a task that all workers have to take up. It is a very common sight to find five-six workers heckling a supervisor when s/he is trying to boss over some worker. Immediate supervisors are often nervous, tense and anxious despite the brave face they put up. In a hand tools factory, a supervisor who bullied and humiliated workers was lucky to survive. On a cold winter night shift, the machines lay idle because of shortage of material and the supervisor went to sleep in his cabin with a coal fire to keep him warm. Workers slept on as a factory ghost locked the supervisor’s cabin door. It was the routine round of security personnel that led to the breaking open of the door and the saving of the supervisor’s life.
Helping one-another does not remain confined to affairs dealing with the company. Discussions of events in one-another’s residential locality, schools, hospitals, etc. are very common amongst groups of workers during breaks which are often extended, to the constant chagrin of managements. Intricate inter-linking amongst workers coagulates them into entities where a member is never alone. This plays a major role in keeping the bossism of management or the goonery of lead-ry in check, whether in the factory, on the road or in residential localities. Anyone mistaking an individual to be only an individual is immediately shown the real side of things. In fact, the affinity groups in factories are a continuation of affinity groups at large in society.
Innumerable actions, immense diversity and an extremely high unpredictability of affinity groups keep management and leaders in check. A phrase often floating in management-lead-ry negotiations is “Will the workers accept this?” Rules and regulations are easily made. Agreements can easily be signed. Workers not accepting or fulfilling given production targets can have their services terminated. Given the universal co-option of unions and leaders by managements, there seems to be nothing stopping managements from doing what they want. Then, why the ever-present, ever-troubling question “Will the workers accept this?”
In a factory manufacturing wires, management stream-rolled workers from one job to another. Anyone saying ‘NO’ was shown the gate. The coolness and quietness with which small groups of workers accepted this and interchanged operations, from acid to water to oil back to water, oil and acid, only infuriated the management when they discovered that ninety tonnes of wire was sent back by a consignee as being defective. Arbitrary job changes came to an abrupt end. To counter the delay in wage-payment, a handful of workers working for a contractor in a textile factory simply went to the canteen and sat there. The workers’ silence in response to the haranguing of the chief executive completely unnerved the management.
A management of a tractor factory increased production quotas using agreements with the union. Workers operating computerised machines responded by changing around the tapes that governed work sequences. The management had to very quickly replace the machines.
Anyone blowing the whistle is shown his or her place. In a hand tool-manufacturing factory, new machinery even further cut down the time between two operations. In order to obtain some breathing space, two cranes were made to move from opposite sides, clash and cause a breakdown. A maintenance worker complained to the management. One day, cranes were in operation but were said to be not working. The maintenance worker was called for repair. He climbed a crane and when he was checking it, the other crane began moving towards his crane. His shouts for mercy braked the other crane, but they proved to be a brake for management schemes as well.
And then, things like not greeting a boss. The management of a factory stopped overtime payments to pay clerks. The five pay clerks responded to this loss of dues by moving like automatons whenever they came across their boss. The silence of the clerks got on his nerves and the management had a nervous breakdown. Overtime dues were restarted.
It is these constant innumerable, insidious, unpredictable activities by small groups of workers that underlie the stress that managements give to representation – articulation – long term agreements. Representation – articulation – unity – long-term agreements versus wage-workers’ silences – mumbling – incoherence – constantly nagging non-unitary demands are expressions of the functioning of a large number of small informal groups in an institution. They are the signs of expressions of the individualities of workers.
In a factory, workers in small groups would often go to the general manager to put up their grievances or seek relief. The harassed manager met this self-expression of workers by posting a guard in front of his office and issuing explicit instructions that workers would not to be allowed to enter his office in groups and only one worker would be allowed to go in along with a leader. In this way, not only was his paternal mask shattered but also the upkeep of his position demanded new costs. Management responds to the adamancy of these small groups of workers by harping on the threat to harmonious industrial relations. Lead-ry denounces the actions and demands of these small groups as a selfishness that poses a threat to workers’ unity.
Sixteen hot chamber workers in a factory left their place of work on a hot summer day complaining of excessive heat. Operations involving five hundred workers came to a standstill. Hot chamber workers had been demanding relief during summers through a lowering of temperature, but the management was not willing to agree, as this would lessen the pace of drying and therefore slow down the chain of work. Assurances had been aplenty and many a long-term agreement had completed its tenure. This step of the hot chamber workers was met by the leaders with such epithets: “All these years they did not feel the heat, it is only today that they have acquired this delicacy. They want to spoil our relation with the management. Wheat advance is around the corner – now the management will refuse to give it. They only look at themselves. Their selfishness is harming all the other workers. The management listens to us because we represent you. But if small groups do not listen to us and take steps on their own, then why will the management talk to us? It is only our unity that is holding back the management, otherwise it will do whatever it wants. These hot chamber workers are harming our unity, and if tomorrow the management takes action against anyone we will not be responsible.”
In the Escorts Yamaha motorcycle manufacturing factory, disenchantment with and denunciation of leaders was similar to innumerable other places. In a confrontation with the management, 300 workers on the assembly line refused to have anything to do with leaders and jammed the assembly line on their own. Leaders denounced these workers and reciprocated by saying that they would not intervene on their behalf – this would teach them a lesson. Workers in other departments did not lay down their tools in sympathy with the assembly line workers. Instead, what was observed was that management and leaders were conspiring for a lockout/strike to launch a major attack on the workers. There are two thousand five hundred workers in the factory. All the workers side-stepped the leaders and decided to continue production in other departments while the assembly line workers would keep the line jammed. Meanwhile, money would be collected department-wise to compensate their financial loss. As the assembly of a motorcycle per two minutes stood still, management and leaders bid their time, confident that the past would repeat itself and workers would have to accept the mediation of leaders. A week after the jam, overtime payments of the previous month were made. One hundred rupees was contributed by each worker, and collected in a rota department-wise. It was decided that a like amount would be contributed when monthly wages were to be paid. This step of the workers unnerved the management as well as the lead-ry. Leaders on their own started holding talks with the management and an ex-partie agreement fulfilling the assembly line workers’ demands was made to get the assembly line moving.
Refusals
Self-activities of wage-workers also encompass layers and layers of routine refusals. A few such refusals are:
“Never make a complaint against a co-worker to a supervisor or to a manager.”
“Never to give evidence in favour of management against a co-worker.”
“Not to get entangled in competition. To give more production in competition with co-workers is unacceptable.”
“Refuse to be carried away by managerial appreciation & recognition to give more production.”
“Even the shadow of money is unacceptable in inter-personal relations.”
Seismic lead-ry
It is not un-often that competitiveness in the market demands sharp rise in productivity. This entails a major attack on wage-workers. Major attack means large-scale retrenchment, big increase in work intensity, sharp cuts in wages besides other cost cutting and efficiency drives.
In these conditions managements plan new strategies and lead-ry adopts new tactics. The unfolding of events is very intricate. To discern the intricate web of strategy and tactics we take as an illustration the unfolding of events in Gedore Hand Tools, Faridabad in 1982-1984 of which we have a first hand experience.
Background Gedore Hand Tools, headquartered in Germany, had three plants in Faridabad exploiting 3500 wage-workers. U.S.A was a major market for its produce. Hand tools enterprises located in China and South Korea were Gedore’s market competitors. Shrinkage of production in the auto and engineering industries in the early 1980s sharpened the competition in the hand tools market. In this scenario, in order to maintain its competitiveness, Gedore management planned a major intensification of work through automation and large-scale retrenchment. For installation of an automatic plating plant Gedore management took a loan of Rs. 2.5 crores (~ $2.5 millions) from the Industrial Development Bank of India, a government of India enterprise.
The unfolding of events
In the beginning of 1982 incidents of chargesheeting, suspensions, transfers from one department to another, shifting workers from one job to another, wage-delays, downgradation in canteen quality, insistence on quality in production, strictness about production targets, time strictness, no rest during shift hours etc. increased noticeably.
In a gate meeting on June 7, 1982 union leaders spoke at length about capitalism, global crisis, company in crisis, and then asked the workers to make sacrifices in the larger interest. They put forward three alternatives to choose from:
- 25% reduction in wages.
- Go on special leave for six months at half wages.
- Retrenchment of 600 workers.
Workers rejected outright all these options put forth by the leaders. At this rejection, managements’ escalated their strong-arm tactics and instigation. Leaders and ex-leaders oiled their networks and accelerated mobilisations around caste and regional identities.
Workers disenchantment with leaders increased rapidly. Their self-activity became more pronounced. Large number of workers stopped paying union dues, attending union meetings, side-stepping leaders in day to day activity and began to deal directly with management individually and in small groups. Graffiti inside the plants increased. A group of workers belonging to, or influenced by, the fringe left posed inconvenient questions in a signed handbill on June 12, 1982. The handbill read “… management says that it does not have money even to buy raw materials – then where are the crores of rupees (millions of dollars) for automation coming from? Is it not because of automation that 600 workers are being told to resign? Soon, will you not talk of the need to retrench a thousand workers? Instead of struggling against it, haven’t union leaders become advocates of the management?”
The confidence of the leaders was shaken. Management was put on the defensive. Uneasy questions in the workers’ minds became points of widespread discussion. The tactic deployed by leaders and management – of announcing their attack in the gate meeting – had turned out to be a blunder. For damage control, the leaders adopted silence and the management took steps – show cause and advice l etters were issued to the signatories of the handbill. Through a circular, management warned workers to beware of disruptive forces. It said that automation was for the health of the workers. The management claimed that it had never had any intention of retrenching workers who would be made surplus by automation. If the management had wanted, it could have retrenched half the workers as it had been paying full wages to idle workers for one and half years. The circular ended with a rhetorical flourish: “Increase production OR perish!” A twisted version of the management slogan: “Increase production AND perish!” became popular amongst the workers.
The sequence of events at this point is as follows : there are prolonged delays in the payment of wages, machinery for automation reaches the plants, leaders maintain a strict silence, and ex-leaders attempt to form a rival union. There are physical attacks, by leaders and their network, on workers who still try to focus discussion on the looming retrenchment. To silence these voices, management uses suspensions. Besides the delay in wages, the issue of the annual bonus is used as another diversionary entanglement. Further on, the management goes for work suspension at half wages for three days and says that this may continue for quite some time.
Leaders complement these steps taken by the management for an open confrontation by ordering a tool down strike on February 12, 1983. Fiery speeches at gate meetings became a regular feature. Dissenting workers who have been trying to focus attention on looming retrenchment are denounced as disruptive elements and attacked. On February 21, 1983 leaders announce at a gate meeting that they have reached an agreement with the management. In the agreement it is agreed that no further work suspensions would take place but wages of January’83 would be paid in January’84. The workers reject this agreement. The management then tries, unsuccessfully, to instigate violent confrontations amongst workers through ex-leaders.
The same agreement is again put for approval at the gate meeting of February 28, 1983 after a number of thundering speeches challenging the management to lockout the factory if it wanted. The workers again reject the agreement. After the second rejection, the leaders announce that the way now is to go for an ‘open struggle’. A meeting of factory delegates (who had been elected in 1980) and other militant workers is called and suggestions asked for. Leaders then reject the suggestion for demonstrations on the plea that the conflict was with the Gedore management and not with the government. However, as soon as t he question of steps against the management comes into focus, the leaders somersault and announce a demonstration & a sit-down at the district administration chief’s office to be organised on Mar, 21.
On March 20, leaders call another gate meeting. Besides members of their network in the three plants, leaders bring their supporters from other factories and spread them out strategically. The same agreement is announced yet again. It is immediately hailed by the strategically placed supporters! And before the workers can react, leaders and their henchmen jump the factory gate and rush in to the plant to switch on the machines. The leaders had here used a time tested and most effective strategy. By switching on machines and restarting the plants, the workers would now be split into confronting groups, where one section would demand a continuation of the tool down strike while the other would be in favour of resuming work. This clash amongst the workers, and the concomitant unfolding of violence, would then facilitate large-scale retrenchment.
But in this case this strategy failed miserably. Enraged, the 3500 workers rush into the plant, shut down the machines and then beat up the leaders who are forced to run away. The President of the union who was also beaten and had to turn tail, had been the president of the union for ten years and was also the President of CITU, Faridabad district unit of the central trade union of Communist Party of India (Marxist). Production does not resume. There is now massive police deployment. Leaders again try to start the machines at night. They are again forced to retreat. Tool down continues.
Some workers belonging to the fringe left call a general body meeting on 23rd March, the weekly rest day. All the workers attend it. A committee proposed by militant, articulate workers and ex-leaders to obtain the resignation of leaders is not opposed. In view of the mounting discontent of workers, the leaders have to resign. After the resignations, the struggle committee, however, does not materialize and the ex-leaders take over. Tool down continues till April 14, 1983. The workers reluctantly accept the agreement that they had rejected earlier.
Stalemate. The issue of retrenchment has got bogged down.
The cycle of shopfloor instigation and wage-delays reemerges as a part of renewed attempts to retrench workers. Police are now posted inside one of the plants. Mobilisations being made on the basis of region and caste come to the fore. There is now a delay in the payment of wages to supervisory and clerical staff.
The management obtains government approval for retrenchment of 300 workers. Leaders hide the list and deny that there is any retrenchment on the cards. They start talking about a new long-term agreement and preparation of a demand charter for it.
At this juncture, management steps up attempts at violent confrontations amongst workers. Old leaders form a committee with the claim that they will negotiate a good agreement with the management. Mobilisation by the two lead-ry networks on the basis of caste, region and plant identity became frantic. The management flames the fire by locking out the third Gedore plant in February 1984. Enraged workers attack the existing leaders and the committee of old leaders uses this opportunity to take over leadership. Lockout in the third plant is lifted.
The finishing off And then began joint action by the management, leaders, police, state administration and the media, to retrench workers in Gedore Hand Tools. A gang of 15 to 20 leaders and their musclemen freely roam the three plants. They pick workers from their machines, take them to the plant time-office and force them, through physical violence and threats, to sign resignation letters. In this way, up to 50 workers are forced to resign in a single day. Workers coming to factory for work and those leaving after shift hours are attacked on the roads and forced to resign. Workers are threatened at their homes and forced to resign. Workers who had lodged complaints with the police find that the police have framed cases against them. Government administration merely files away the complaints made at the District Administration office. Newspapers do not print any news of these events. Not even letters about a fellow worker who committed suicide on the rail tracks after he was forced to resign.
In these circumstances hundreds of workers sought shelter in their villages for months. And the environment at Gedore? Armed police in tents inside the factory, armed police in trucks making rounds of the three plants.
This is how the stalemate was broken and retrenchment implemented. Even then, it took one more year to retrench 1500 workers out of the 3500 in Gedore Hand Tools, Faridabad.
Fallout
The inability of the management, lead-ry and state administration to entrap wage-workers in time tested snares, forced them to divest themselves of their constitutional garbs as well as leader militancy. They had to resort to brute force to implement their policies. This repression, however, could not bring with it the myth of “glorious defeat” with its martyrs and heroes as well as the attendant mortgaging of wage-workers’ critical evaluation.
But not getting trapped was not sufficient for the workers and they were disabled by the methodical repression of the management. This could happen, fundamentally, because management repression did not create sufficient ripples and repercussions amongst other wage-workers. Workers’ self-activities had remained disjointed, unlinked and uncoordinated even within the enterprise. A dynamic expansion of wage-workers’ self-activities is critical for linking wage-workers of one enterprise with those of other enterprises. But the unfolding of workers’ self-activity was impeded by their not questioning of representation & delegation.
Seismic lead-ry – at a higher level The frequency of extensive area-wide, region-wide, nation-wide attacks on wage-workers, compressed in ever-shortening periods of time is increasing. The attacks entail huge wage-cuts, enormous increase in work-load and mass scale retrenchments. And they are implemented, primarily, in two ways.
One: through instigation to mass violence by playing the politics of identity, and
Two: through the foisting of credible, militant leaders.
In Indonesia, 1997-98, through the massive attacks on wage-workers, one can see these strategies being played out:
I. Media highlighted riots between ‘ethnic Indonesians’ and ‘migrant Chinese’;
II. “Confirmed reports say that the US has been pressuring Jakarta to release one of the top political dissenters from imprisonment. ‘The US move is to enable Jakarta to cool the rising temperature down to some extent’, say sources”. [HT, Delhi 29 March 1998]
*** Activities of a fringe left
The fringe left that was a participant in the events in Gedore Hand Tools in 1982-84 existed around a monthly workers newspaper. Some workers of Gedore were members of this fringe left and we have emerged from this background.The activities of this fringe left had been geared:
- to unmask the collaboration of leaders with managements.
- to keep in focus the issues that managements and leaders seek to hide.
- to unmask formal and phoney steps like one-day token strikes, token demonstrations and formal mass meetings that are organised by leaders.
- to create and establish an effective alternate leadership to be constituted by militant, credible leaders from amongst the workers.
- to unify workers around this alternate leadership.
- to launch organised, conscious struggles under this alternate leadership.
- to push for demonstrations, mass meetings & strikes.
*** A critique of a fringe left
The process of unmasking management-leader collaborations brought into focus contentious issues that management and leaders seek to hide. This centre-staging of otherwise hidden agendas helped unleash the self-activity of wage-workers. Management notices and leaders rhetoric, demand charters and agreements, all came under constant scrutiny by wage-workers. “What to do?” and “How to do? ” became topics of routine discussion. Routine self-activity of workers as individuals and in small groups increased.
The medium of circulation of information around these activities was through a regular monthly newspaper, frequent handbills, wall-letters and conversations. These simple acts created considerable hurdles in the implementation of the retrenchment policy at Gedore Tools.
But it is the alternative proposed by fringe left that is problematic, in fact, fatal. The mobilisation of wage-workers envisaged by the fringe left, in fact, is premised on the erasure of the self expressions and self-activities of wage-workers at large.
The problem of militant and credible leaders
In the latter half of the 19th century and the first quarter of the 20th century, fierce polemics raged on the question of real and phoney representations/ representatives of the interests of wage-workers. The polemics spanned ideology, strategy and tactics. ‘Reform or Revolution’ was often the high point of the debate. The reality that has unfolded since has, however, made the very premises of this debate redundant. Towards the last quarter of the 19th century, requirements of production enterprises for accumulated labour reached such dimensions that individual ownership of production enterprises became unfeasible. to to as the major source of funding for production enterprises are what has unfolded in these one hundred years. Individuals as owners/ part owners of production enterprises have increasingly become insignificant. Acts forcing bankruptcies of individual owners have lost their cutting edge. Enterprises have acquired institutional forms. With enterprises becoming monoliths of massive amounts of accumulated labour, head-on collisions of living labour with these institutional monsters are counter productive for living labour, whether in the form of an individual wage-worker, a group of wage-workers or a mass of wage-workers. And, working for head-on collisions is the raison d’etre of the fringe left.
In this scenario, the blurred boundaries between phoney, formal and real struggles have melted, become indistinguishable, giving way to a continuum. Formal-token, phoney-instigated-provoked, militant struggles, despite some differences of form, have in essence become indistinguishable. It is through repeated experiences that large numbers of wage-workers have learnt that these are harmful for them. It is this that underlies the unwillingness of workers to struggle – the word ‘struggle’ is here being used in the sense of the dominant meaning s that it has come to have. And it is this that underlies the fringe left’s activities to ‘agitate workers’ in order to overcome what it decries as the apathy and passivity of wage-workers. It is in this context that the fringe left creates the polemics of militant & credible leaders.
In general, the alternate leadership, the militant & credible leaders for whose creation the fringe left is geared, is a fringe phenomenon like itself. It is only in the event of major attacks on wage-workers that the alternate leadership of militant & credible leaders can and often does acquire leverage amongst large numbers of workers. And it is only then that the ‘dead-endness’ of militancy, and the fact that it actually causes serious damage, becomes obvious.
Unity and unifocality are the mantras of state and proto-state apparatuses. Even those fringe left groups that are explicitly anti-state have as their axis activities that are geared to unity and unifocal forms. This is what makes even such fringe left groups proto-states.
In fact, it must be stated that it is very doubtful if representation was at any time in the interest of wage-workers. A hundred years compel us to engage in a critical retrospective analysis. With all that wage-workers have experienced in this time, history proves that any and every representation is counter-productive for wage-workers.
Demonstrations, mass meetings and strikes are all events premised on unity and unifocality, and implicit in them are both representation and delegation. The logic for these events is that these are shows of strength and thus in the interest of wage-workers. Facts, however, point to the contrary.
Demonstrations Demonstrations involve an elaborate plan of date, time, route, destination, pace, slogans, demands, those to lead, those to maintain order, those to address and those to talk ‘on behalf’. Organisational infrastructure is a prerequisite for a demonstration. Ninety-five percent of wage-workers cannot organise demonstrations themselves, they can only join in as followers. For a worker to become a part of a demonstration, the worker has to in effect erase any idea of self-activity and self-expression, or, has to deceive him or herself by parroting the pre-written script as self-expression.
Demonstrations
Demonstrations are means and occasions for displaying the strength of organisations and leaders. The index of strength is numbers and the index of militancy is the number & intensity of skirmishes with the police, which range from charges by mounted police, water cannon charges, tear gas shelling, arrests, and firing. The success of a demonstration is measured by the grandiosity of the spectacle it provides to the media. What are erased are the injuries and the long court cases inflicted on wage-workers. Those who are killed are made into martyrs and transformed into icons to shackle any criticism or questioning. Workers, by and large, are aware that demonstrations make them easy targets for police attacks besides gagging their self-expression. This is evident from the distance that workers maintain from demonstrations. In fact demonstrations often have to be organised during shift hours with the connivance of managements.
Mass Meetings
Mass meetings Most frequently, mass meetings that wage-workers have to encounter are gate meetings at the factory and office. Gate meetings are held by leaders. The rule is that only leaders will speak in the gate meetings. The logic put forward is that any other vocalization will show disunity amongst workers to the management and weaken bargaining power. To see to it that the rule is implemented, lead-ry musclemen are strategically placed in gate meetings in order to summarily deal with any worker who tries to speak. Recognition of a new leadership hap pens with the successful holding of a gate meeting, because holding a gate meeting constitutes a challenge to the existing leadership.
The most encountered mass meetings, i.e. gate-meetings, exclude wage-workers self-expression both by logic and force. The fringe left often called for general body meetings (GBM) away from the factory premises in order to overcome the prohibition of any expression of dissent at gate-meetings. However, an elaborate organisational apparatus is also a prerequisite for holding general body meetings. These are occasions that require venues, agendas, stages, stage-managers, order keepers and elaborate time management. By their very nature, general body meetings are arenas for fights between leaders, ex-leaders and potential leaders with their lists of articulate speakers and cheer groups.
General body meetings demand from wage-workers time bound (two to three minutes) coherent presentations on specific agenda. These presentations have to be speeches to audiences of hundreds or thousands. This demand on the workers by itself excludes most workers from expressing themselves in general body meetings. Those who are not thus excluded have to filter through the lists of speakers of contending lead-ry networks. Workers have seen through general body meetings for what they are. Now the norm is that out of a thousand workers, approximately 150 will attend them.
There are other kinds of mass meetings that play on higher scales of representation. An illustrative example: From 1977 to 1979 in Faridabad, there were sporadic multi-nodal outbursts of workers discontent in hundreds of factories. In October 1979 unions jointly called a mass meeting. Around 100,000 workers assembled and the atmosphere was very charged. The huge number of workers spilled out of the meeting ground and road and rail traffic was forced to halt. Well-prepared police and paramilitary forces then began indiscriminate firing. Factories functioned normally from the next day. This incident ensured a smoother functioning in the industrial b elt for the next few years. And a martyrs’ column was duly erected.
Strikes
This fringe left’s activity regarding strikes was on two planes. One – phoney strikes called by leaders for the implementation of management policies and formal strikes to make their presence felt, were denounced. Two – The call was given for real strikes, and for militancy in real strikes.
Denunciation of phoney and formal strikes opens greater possibilities for workers self-activity as questions regarding what to do, what not to do, how to do, how not to do are unleashed. However, calling for real, militant strikes has disastrous consequences for wage-workers.
Vis-a-vis management, work stoppage at either factory or larger levels is no longer a powerful weapon of wage-workers. On the contrary, lockouts by managements and strikes by leaders are powerful instruments used to launch major attacks on wage-workers. In the last twenty years we have not come across any strikes, anywhere in the world, that have not resulted in large-scale wage cuts, retrenchments, work intensification or closures.
A few illustrative examples:
Bombay Textile Strike of 1982-83 in 60 textile mills. 250,000 workers unified under a militant leadership on a charter of demands. Management policy was to retrench 90,000 workers and close down old mills & sell the premium land. Under normal circumstances, such large-scale retrenchment would have taken more than ten years. Through the strike, however, this policy was implemented in one year.
East India Cotton Mills, Faridabad, 1979. Automation was to be implemented. Management needed to retrench 3000 out of 6000 workers. A strike was called by the union for a one-percent increase in bonus. Militant strike, and a lot of violence. Three thousand workers dismissed. Lakhani Shoes, Faridabad, 1983,1988,1996. Three major strikes by three different unions. Each time there is violence and militancy. Each time all workers are dismissed. Lakhani Shoes has registered a very fast growth rate in output. Number of factories of the company has increased from 3 in 1983 to 22 in 1997.
Requirements of a strike
The requirements of a strike are factory-wide issues and an elaborate organisational structure. Also, mobilisation of workers through persuasions, deceptions, hopes and threats. The activity of fringe groups during strikes that are not organised by them is geared to make the strikes increasingly militant. In factories where they have a physical presence and they are able to get an echo they may be able to take over the leadership of the strike by forming struggle committees of militant workers. What are the courses open to these struggle committees?
Prolongation of the strike does not help. Rather, the longer the strike is stretched, the weaker becomes the strength of the workers vis-a-vis management. Such being the reality, struggle committees are forced to resort to:
· Direct confrontations with state administration to pressurize the state-apparatus to act on the management. The steps are big and volatile, be they demonstrations, mass meetings, road jams and railway stoppage. These steps provide easy and visible targets to repressive organs of the state-apparatus. Given past experience, workers rarely follow those advocating these steps.
· Mobilisation of media, artists, stars, influential persons, other representatives, parliamentarians, grass-root activists to persuade state administrations to act on management.
Wage-workers are initially hopeful spectators to these performances and then slowly disperse as disenchantment sets in.
Both these action-courses lead to an immobilization and dispersion of workers and ensure an implementation of management policy.
Unified militant struggles, whether in the form of demonstrations, mass meetings or strikes, are akin to military operations with their generals, captains, sergeants and, of course, foot soldiers. Organisations linked to the management or organisations that are proto-states are alone capable of running such operations.
*** A Preliminary Sum-up
In general, when wage-workers resistances, refusals and steps of change are discussed, the imagery that crop up is that of mass demonstrations, mass meetings, strikes, pitched battles, insurrections. The corollaries to these are the non-mundane qualities of heroism, sacrifice, bravery, martyrdom, courage, wisdom, articulation, discipline and unity. By these very definitions, the self-activities of most wage-workers are excluded. This imagery inherently posits a spectacular arena for lead-ry to deprive the wage-workers of their voices. More painful still is that big, mass, spectacular movements make easy targets of wage-workers for managerial apparatuses to control, manage and, if necessary, crush.
Big implies mobilisation on a mass scale. Conducting and directing committees are intrinsic to such events. Seemingly a large number of people become active, but actually it is representatives and leaders who think, decide and issue orders whereas numbers at large have to march to the tunes trumpeted. Mobilisations by representatives are for representatives. Defeats are camouflaged as victories in order to legitimize the re-creations of these representational forms. Repeated experiences with ‘big’ have led wage-workers at large to keep aloof from them. This is often characterized as passivity and apathy of wage-workers.
When wage-workers daily routine oppositions become too much for a management or when a management has to go in for a major restructuring, retrenchment, wage-cut or intensification, it often resorts to spectacular work stoppage. Since production enterprise is no longer the private property of individuals (i.e. capitalist), prolonged stoppage of production is no longer a question of life and death for a management as it was for a capitalist. When necessary, managements resort to strikes, lockouts, work suspensions, suspension of operations by creating big factory-wide, area-wide issues with the help of representatives.With strikes becoming the weapon of managements, those attempting to genuinely represent wage-workers’ interests are crushed. Furthermore, individuals have become so insignificant vis-a-vis institutional structures that commitments or personalities hardly make any difference.
For all of us self-activity of wage-workers is of paramount importance. It is this area that we want to open out for discussion and debate. As wage-workers we know that all of us, everyday and at everyplace, have to contend with oppressive and exploitative conditions around us. Individually and in small groups we take steps on our own. In small groups, we interact with each other ‘not as unequals’ ensuring the self-expression and self-activity of each one of us. Confining ourselves to workplace experiences we can say that each one of us has an affinity group of half a dozen or so amongst whom all participate ‘not as unequals’. In these affinity groups a lot of premeditation and co-ordination takes place. The activities of affinity groups span from mutual help to routine resistances against productivity and discipline, along with refusals and steps of change that question and challenge hierarchy, competition, money relations and wage slavery. The problems as we see them are:
I. The importance of self-activity as reflected in these steps taken by affinity groups is denied. The steps by themselves are small and thus belittled. When they are talked about, they are derisively characterized as insignificant workplace skirmishes, or merely survival calisthenics.
II. Constant attempts are made by managements to suppress these self-activities through representation.
III. Wage-workers often do not give much importance to their self activity because of the invisibility of the social effects of the small steps engendered by their self-activities.
IV. There is a tremendous lack of linkages between affinity groups (which can only be horizontal and multi-nodal). This lack makes wage-workers vulnerable to getting coagulated into a mass whenever wider level issues are forced or arise. This coagulation if not created by representatives (which is ofttn the case), then in itself engenders representation.
V. More importantly, co-ordination between affinity groups is hampered by a lack of discussion on experiences of affinity groups.
Lest we be misunderstood, we would like to make it clear that we are not for small steps per se but our concern, rather, is for self-activity. Self-activity in terms of routine resistances, refusals and steps of change by wage-workers at large on a sustained, extended and expansive scale, encompassing a multifaceted global reality.
*** SELF-ACTIVITY OF WAGE-WORKERS AGAINST POLITICS OF CLOSURE DEFINING CLOSURE
A viable enterprise means that enough surplus is being extracted and realised in order to be appropriated as taxes, interest payments, cuts & commissions, managerial life-style and dividends. For financial institutions, management & state apparatus, a company becomes non-viable & sick when the extracted and realised surplus is not sufficient to meet the existing levels of taxes, interest rates, cuts & commissions, managerial life-style and dividends.
It is not uncommon to find that state apparatuses, financial institutions and management are sometimes forced to reduce their amounts of surplus appropriation to keep an enterprise running. But the overriding tendency, of course, remains one of perpetually increasing the amounts that are appropriated, resulting in increasing “sickness” and “unviability”. The dominant propaganda and media, however, all the while speaks of “sickness” and “closure” in terms of either mismanagement or lack of profitability (i.e. inability to pay dividends). This screens the fact that the major portion of extraction from wage-workers is appropriated as taxes, interest payments, cuts & commissions and managerial lifestyle.
POLITICS OF CLOSURE
The common interests of management, financial institutions and state apparatus dictate the survival, running and growth of an enterprise. In their common interest, they collaborate to increase intensity of work & workload, decrease wages, retrench workers and create techniques to counter wage-workers’ self-activity.
Despite all the cunning and guile, force and deception used to keep an enterprise viable, when an enterprise “becomes unviable”, then it is in the management’s interest to swindle as much as it possibly can of the company’s assets. When a goose no longer lays golden eggs, wisdom advises – ‘Cut and Eat the Goose’.
There is a well-tried out management method to grab as much as is possible of wage-workers’ legal dues before the closure of a factory. Along with the months of outstanding wages, years of provident funds/ pension funds, gratuity/ retirement benefits, years of bonus and leave travel allowances, etc. are also not paid. Company properties are then sold off with the management taking large cuts & commissions. This has been a routine exercise in a large number of factories which have been closed in Faridabad and other places. The dominant schema is:
When a factory “becomes sick”, and closure has been decided, management – through union leaders – instigates strikes, and/or violent incidents to create conditions for lockouts. This facilitates the dispersal of workers. In these situations, management stops coming to the factory and wage workers are channelised into long drawn out civil and criminal court cases – fifteen years is very common. During all this, closure is very actively camouflaged. In the rare cases where the court cases are finally decided in favour of the workers, and the workers are at hand to take their legal dues, there is no property in the company’s name to pay. Banks’ and state apparatuses’ dues (taxes and other bills) gulp most of the little that remains.
A BREACH IN THE POLITICS OF CLOSURE
This is the scenario that is being tried out in Jhalani Tools Limited, Faridabad. But the wage-workers in Jhalani Tools are actively countering this management-leaders-state administration schema to gobble-up workers dues through various modes of self-activity. These steps of self-activity, in our opinion, have wider ramifications for wage-workers. Management of Jhalani Tools stopped paying wages to workers from Mar’96. The past experiences of wage-workers in Faridabad and specifically in Jhalani Tools, have thoroughly discredited leaders amongst wage-workers. Through silence and passivity, the 2,000 workers countered leaders’ and management’s methods of instigation around tangential issues. No heed was paid to grand agreements, identity politics, change of union affiliation, change of leaders, provocation by transfers, instigation to violence etc. Four groups of leaders have come (have been brought) and gone, banging their heads against this wall of ‘dull and dumb’ silence.
With mounting legal dues and increasing hardships, workers had hesitatingly started looking for alternative courses of action. Initially a small group of workers in Sept.’96 had on their own demanded back wages from the state labour department officers. Slowly, in affinity groups of 5-8, workers complaints to the state officials increased. And very soon the working of the labour department and district administration was almost jammed when 300 small groups of workers separately started approaching the officers. Legal obligations of separate dates and hearings were done away with, but then talking to hundreds of workers at the same time was another impossibility. Like the management, the district officials desperately tried to foist leaders on workers, but failed. Faced by this stubborn refusal to accept anyone as leaders, district officials then tried their best toinstigate workers to violence. They failed again.
Another facet of this incident is that collecting a crowd by giving a single date to 300 affinity groups facilitates the spread and legitimization of the ageless rhetoric of unity and delegation (for negotiation with management and administration). This was attempted by the district administration. But an interesting metaphor to counter this arose from within the crowd outside the administration office. A worker responded to the call for “unity and delegation” by calling out that – “Bees united in a hive can easily be smoked off and their honey taken away. But if affinity groups of bees swarm about, no one dares to touch their honey”.
Then the management tried to create leaders and instigate strikes through summary dismissals of workers. But even when the number of dismissals reached a hundred, the workers neither made leaders nor took to violence.
With this stepping up of pressure by management, leaders and state officials, the workers of Jhalani Tools in August’97 started taking very simple steps to take their predicament to more than 300,000 co-workers in Faridabad & Delhi. Overcoming hesitation, fear & shame, some workers in small groups of 8-10 started standing along various roads during morning and evening shift hours with hand written placards. This was done to engage in discussions with workers of other factories without any intermediaries. They have been doing this daily since Aug’97.
On the placards is written:
“We are from the 2000 workers who have not been paid their wages for (so many) months”;
“What is to be done when management does not pay wages?”;
“We have changed leaders four times and union flags three times, but each time it has been from the frying pan into the fire”;
“We have made many complaints to govt. officials and ministers but conditions have gone from bad to worse”;
“Metal Box, Delta Tools, Electronics Ltd. and now Jhalani Tools workers. Whose turn tomorrow?”; etc.
Everyday they space themselves along a different road. Along each route that they stand on, workers from hundreds of factories pass by. The response of workers at large has been tremendous. Dispersed, multi-nodal conversations without intermediaries are emerging about the urgent need for new modes of self-activity of workers. Over this period of eleven months, more than 200,000 workers have read these placards and thousands of workers have stopped to have extensive conversations with them. In almost all factories of Faridabad (and large number of factories & offices in Delhi) questions posed by these workers are being debated.
What is being discussed by an ever-increasing number of wage-workers is how to act on their own strength against the triumvirate of state, management and representatives. It is a constant process of conversation, argument and counter-argument as to the ‘Whats’ and ‘Hows’ of steps of self-activity. There is awareness that the charted out paths and networks of representatives, leaders and their organisations are all geared to subvert this process.
Management, leaders and state officials are finding it difficult to instill fear in workers at large as they can find no appropriate targets for their terror tactics. More difficult than the small numbers of workers on the roads, is the problem that the straight and silent faces of workers are posing for the bosses. An additional difficulty for the bosses is the workers’ refusal to go to court despite all the advice that the specialists have been doling out wholesale.
More and deeper discussions have been taking place amongst Jhalani Tool factory workers. These have found visible expression in forms like wall letters and graffiti, but a truly significant fallout has been that workers have innumerable and extended conversations within and outside the factory premises and with co-workers as well as workers from all other factories. From being a problem of one fac tory, it has now become a problem of all workers.
To counter the increasing self-activity of wage-workers, the provincial government organised elections, in Oct’ 97 in order to establish a new leadership in the factory. From Dec’ 97 the management started paying wages. However, these steps failed to put a brake on the workers’ self-activity. Neither the issue of back wages & other dues could be side tracked, nor could the management sell the IIIrd plant of the factory, nor could it make leadership credible amongst workers.
In this situation, in Apr’ 98, the management resorted to massive wage-cuts in order to instigate workers. Failing again, the management then created an atmosphere of fear & violence and threw out the elected leaders – replacing them with its hand picked works committee in the first week of June’98. This hand picked committee has resorted to direct physical attack and identity politics. But the continuous rise in workers’ self-activity has put a hold on this.
Small groups of workers with placards standing on the roads have increased and are increasing in number and so are the workers in conversations with them. Thereby not only creating problems for Jhalani Tools management, which has not been able to close the factory, but also for managements of thousands of factories.
KK / Collectivities, June, 1998. Majdoor Library, Autopin Jhuggi, N.I.T. Faridabad, 121001, India
Comments
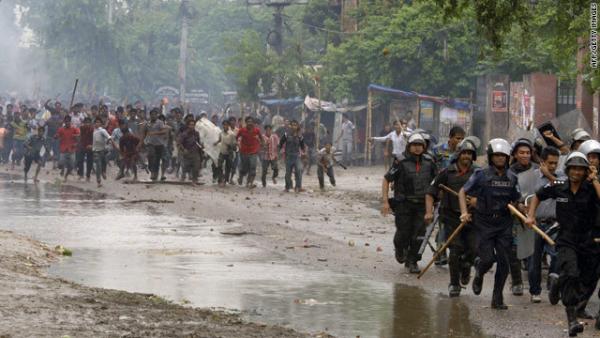
English Language edition of the class struggle newspaper produced in Gurgaon, in Haryana, India. The paper contains workers' enquiry and testimonials, collective action reports, theory and analysis.
Gurgaon in Haryana is presented as the shining India, a symbol of capitalist success promising a better life for everyone behind the gateway of development.
At a first glance the office towers and shopping malls reflect this chimera and even the facades of the garment factories look like three star hotels. Behind the facade, behind the factory walls and in the side streets of the industrial areas thousands of workers keep the rat-race going, producing cars and scooters for the middle-classes which end up in the traffic jam on the new highway between Delhi and Gurgaon. Thousands of young proletarianised middle class people lose time, energy and academic aspirations on night-shifts in call centres, selling loan schemes to working-class people in the US or pre-paid electricity schemes to the poor in the UK. Next door, thousands of rural-migrant workers up-rooted by the rural crisis stitch and sew for export, competing with their angry brothers and sisters in Bangladesh or Vietnam. And the rat-race will not stop; on the outskirts of Gurgaon, new industrial zones turn soil into over-capacities. The following newsletter documents some of the developments in and around this miserable boom region.
If you want to know more about working and struggling in Gurgaon, if you want more info about or even contribute to this project, please do so via:
www.gurgaonworkersnews.wordpress.com
gurgaon_workers_news[at]yahoo.co.uk
Comments
This doesn't say anything other than a headline. Wonder if any contacts in India know what's happening.
And this AJ report, to which this headline is linked, doesn't show anything about a riot:
(not sure if this has come out properly - never tried to embed any video before, and preview shows only html code, so won't know until I save it; if it doesn't come out, can someone tell me what to do in future?)
And just seen this, from Gurgaon Workers' News from a month ago (apologies if this has already been posted up):
On 1st of February 2011 – while riots rocked the Kasbah and downtown Cairo – around 150,000 young people arrived in Bareilly, near Shahajanpur in Uttar Pradesh, India. They came in order to apply for 416 vacancies at the Indo-Tibetan Border Police (ITBP). Facing the enormous mass of applicants the local administration called off the hiring procedure. The angry youth started smashing the place up, burnt cars, pelted government and media buildings. The trains heading home were overcrowded, people had to sit on the engine and wagon roofs. Crashing into a bridge more than a dozen young people died. Desperation and anger of the youth spreads from the ‘illegal’ vegetable markets of Tunis, to the Parisian banlieus, to the textile industrial suburbs of Mahalla… across this world of widening contradictions between what is and what could be.
We met a 20 years old worker who lives and works in Manesar, near Gurgaon. It is his individual story, but it is at the same time the story of a dominant part of global working class today: the migration between village and town, the wandering between different jobs and sectors, the dissolution of old social structures, the necessity to form new ones. Their existence bridges the knowledge of agricultural work, the knowledge about the misery of village life, the skills of modern industry and industrial struggle, the anger towards the urban betrayal. Seen on its collective and antagonistic background their story smashes all antiquated, but re-animated concepts of the ‘peasant-workers alliance’ – a concept, which essentially upholds the ‘mediating and allying role’ of the ‘left-wing of bourgeoisie’. Any attempts of professional and institutional trade unionism will fail their meandering workforce shifting between textile, automobile, printing or whatever production. In the face of their social experience, any claim that workers’ consciousness is necessarily reduced to the ‘economic dimension’ will be doomed to wither in the shadow of irrelevance. So far the temporary falling-back into the village might have prevented a mass confrontation with the real-existing conditions in the urban world: a settled existence as an urban wage worker is utopian and nightmarish at the same time. The ‘falling back’ becomes untenable, so does the ‘leap ahead’ into the urban whirlpool. The whirl’s centre is formed of mainly temporary employment in core industries, connected to both, global production-chains and the large fringes of slum economy. The centrifugal forces are growing and hardly allow a settled existence. The new desires and collectivity emerge from the central point and are washed into the periphery. Only if future working class movements are able to keep the social connection between urban industrial centres and periphery will they be able to express a communist tendency. The current social connection is on the shoulders of the migrating workers. The Pearl River generation of migrating workers has become the pendulum of global capital. Their pushs-and-pulls between southern hinterland and global workbench and the rushes of northern austerity crisis will have to crack the systemic borderline of under/development and reiterate the necessity to make the step beyond.
Twenty years old worker
(FMS New Series No. 268)
I get up at five o’clock in the morning, in the middle of sleep…
Since I was 12 or 13 years old, I always got up at five in morning to milk the cows. We had two cows. Then I went three and a half kilometres on my bicycle to deliver the milk to a place outside of our village. Back at home, I would eat and then go and graze the cattle. After having washed and returned the cows, I went to school at about ten o’clock. My parents fought a lot with each other. Since I was in seventh class, my father stopped sending money to us. We lived in Eastern Uttar Pradesh. My father worked in Pehowa, Haryana, painting and plastering houses. For one month, I worked as a helper for the manager of a brick kiln. But selling milk was our profession. When my father did not send any money during all of 2004, I left school. Everyone said, “How long will you survive by grassing cattle, go and learn some work…”
In 2005, I arrived in Gurgaon. I stayed with the son of a relative. I was 15 years old then. For ten days, I had to sit idle. I learned how to make rotis and started to make food for those who went to work at four in the morning. I found my first job in N.K. Rubber factory in Nakhrola. The personnel manager interviewed me. The contractor said that I was still young, but that it would work out. The workers -who had come from Orissa to find a job – filled out my job card, stating that I was 18 years old.
I had to get up at half past four in the morning. I prepared food. Then I went one kilometer on foot. I began work in the factory at eight o’clock. They ran two 12hour shifts. We manufactured soles for shoes. It was assembly line work. You had to stand upright for 12 hours, only half an hour meal break. I hardly managed to keep up. The supervisor got angry. My feet would swell up from all the standing.
During nightshift, you get very tired. I snuck away to get some sleep. The supervisor screamed and the guard went to find and wake me up. Although I had already worked six hours at that point, they cut 12 hours from my wages. I had difficulties sleeping during the day. During the nightshift week, I used to get so very tired by Wednesdays… Now on nightshift week, I often take Wednesday off.
There are six people now sharing the room. From my first wages, I used 1,000 rupees to pay the food bill. With 250 rupees, I bought a thin mat and blanket. With 300 rupees, a gas cooker and some cooking utensils. Then I went to get a different room in Nakhrola. With another one of the guys, I paid 700 rupees rent. The guy left and I spent two months on my own.
The winter began. You leave at half past seven in the morning and return at eight o’clock at night. For fifteen days, you do not see the sun. A thin mat, a blanket, a sheet – I had no proper bed, I slept on the floor. I also had no sweater, so I slept with my jacket on… I could not get any sleep at night. When the morning came…I can still remember how cold it was during winter in 2005. In the factory, it smelled really bad, but it was warm…There, sleep came very easily.
I had been working at N.K. Rubber for four months when the message of the death of my grandmother arrived. I went back to the village. Cutting wheat, thrashing wheat, storing the straw. Cutting arhar, digging out garlic, cutting coriander. Preparing the paddy field, preparing the rice plants and planting them. Go and fetch the cows for grazing, grazing them. At home, there was a lot of difficulty because of the heavy burden of all the work. But if you don’t do it, what will you eat? Suffering at home continued. There was a lot of fighting between my uncle and my father. Because my mother had been staying in the village, we got hold of three bighas of land during the re-distribution.
My earliest memories are from Pehowa in Haryana. They sent my older sisters to a government school and me to a private school. After a year, my sisters returned to the village to stay with my mother. I stayed back with my father. After having prepared food in the morning, my father went to work and I went to school. One day on the playing field, a kid threw a stone and it hit my head. I bled a lot, but there wasn’t anyone to put a bandage on, so I kept my head in some cloth. When my father came from work at eight o’clock, he bandaged my head. I was very sad. I was alone. I missed my mother and my older sisters. My father went back to the village. I had my exam coming up. He had left me in Pehowa, so the neighbors gave me food. I developed a fever – now I think it was because of the stress. I was good at math. My father wanted me to keep on studying in Pehowa. I would go back to the village during holidays. It was a private school so, the holidays were very short. After the marriage of my two older sisters, my mother was left only with my younger sister. I went back to the village and my mother would not let me go back…
When I arrived at Gurgaon the second time, I started again working at N.K. Rubber – this time in the packing department, where I stayed for four months. I also went to Perfecti factory, but nothing came out of it. In order to learn how to run CNC machines, I started at Moog Automotive for a low wage. The supervisor was a cousin of mine. I stopped after twelve days. There was too much quarreling because the cousin kept on screaming at me. I went back to the village. In 2006, I spent the whole winter in the village. Then I went back to Gurgaon. It took 15 days to find a job. I spent a lot of time running around IMT Manesar. I had job interviews at many places.
They hired me at Vishal Retail factory (Plot 16-17, Sector 5). They hired me as a press man – it was the first time that I worked at a steam press. I became a record keeper and then a small supervisor. I learned how to sew. Wages were delayed. The first day after the supposed pay-day, workers stopped working for a while. The next day workers stopped working at eleven o’clock. The general manager said that wages would arrive at three o’clock. Workers started working. The wages did not arrive. Workers stopped again. At eight o’clock at night, people were finally paid. I worked there for a year. Then the factory closed. The contractor disappeared. One year of contributions to the PF lost…
I was ill for 15 days. I had chicken pox. I did not eat, I could not walk, neither sleep. Because he was afraid of infection, one of the roommates left. I was upset about that. I used to cook for him. The other roommate took 15 days off. He cooked food, prepared the medicine, and washed the clothes.
After Vishal retail had closed down, I started at Orient Craft (Plot 15, Sector 5) as a tailor. You had to work from half past nine in the morning till one o’clock at night every day. On Sundays, they made you work from half past nine in the morning till four o’clock the next morning. They paid double for overtime. They sacked me because I took a Sunday off. They said that data was lost on the computer. I had to go to the office again and again to get my outstanding wages. After twelve days working at Orient Craft, I worked seven days at Gulati Export (Sector 4).
Then I started at STI Zenho (161, Sector 40). The company manufactures break pipes for Maruti, Suzuki, and Honda cars. I learned how to operate a bending machine. Most of the supervisors there were women. The behavior of our supervisor was not good. You had to ask in order to go to the toilet. Even after having finished the target, you had to keep the machines running, making extra-pieces. You were not supposed to make pieces which would be ‘rejected’. You were supposed to work eight hours daily overtime. For two or three days, I was concerned with the fact that a woman was my supervisor, then I got used to it. You are forced to work, so you have to listen. After seven months, I took holiday and returned to the village. My sister was ill. At the time of return, I also got news about the work accident of my supervisor cousin. He was kept in the Delhi Jay Prakash Trauma center, got a blood infusion and had to stay for fifteen days. He then had to be looked after by relatives for another ten to fifteen days. After all this, I started again at STI Zenho. After five months, they gave me an enforced ‘break’.
I started at AG Industries (Plot 8, Sector 3). About 100 permanent workers work on three shifts and another 500 workers hired through contractors work on two 12 hour shifts. They manufacture fiber side-covers for Hero Honda motorcycles. The permanent workers wanted to establish a union. So, in January-February 2010, the company kicked out eighteen of them. On March 20th, all workers gathered and stopped working. The police came in two bus loads, they entered the factory, started beating us with lathis and kicked the workers out. One had his hand broken, several others had bleeding heads. At six in the morning, some workers went back inside and started working. The managers also worked. Workers were brought in Hero Honda buses from Gurgaon, from Dharuhera and also from Ghaziabad. New people were hired at the gate. On March 26th, the unions had a demonstration in Gurgaon, with ten thousand people, with speeches. Then again, nothing. After signing the ‘good conduct conditions’, the permanent workers went back inside on the 2nd and 3rd of April, leaving the eighteen other workers outside. After four months of working there, I had an argument with the supervisor. I left the job and went back to the village.
When I told them that I would go back to Gurgaon, my mother and sister cried. I stayed for three more days. When I left, I didn’t tell them. I borrowed money for the travel from a friend. I looked for a job for eight days. I started at Kumar printers (24 Sector 5). Two 12 hour shifts. At every machine, at every corner cameras. There are 50 permanents and 225 workers hired through two different contractors. They do industrial printing. During the Commonwealth Games trouble, 50 to 60 workers left because they were afraid of being harassed by the police. Due to the lack of workers, the remaining workers had to work from eight in the morning till one at night. They also brought 30 workers from Bhiwadi in a bus every day. I haven’t fixed a date yet, but I will go back to the village…
Comments
We translated and summarised an article about the conditions in the factory of a Tata Motors supplier based in the state of Uttarakhand. The article was published in the Marxist-Leninist revolutionary journal Nagrik, issue 23, 1 – 15 December 2010. Tata Motors claims to represent the ‘new people’s car’-industry, with cheap cars like the Nano. ‘People’s Cars’ are built with workers’ blood. The state of Uttarakhand attracts investment by massive tax benefits. A fair share of factories has been re-located from other states towards this northern state. SIDCUL, the State Industrial Development Corporation of Uttaranchal [Uttarakhand] has established seven industrial estates which, according to the SIDCUL website provide a “Peaceful and Secure Industrial Environment”. Read about the war behind the peace yourself…
The mutilating factory – Rojitasha Company
http://www.sidcul.com/sidculweb/home.aspx
http://www.tatamotors.com/nag
sptripathi@sidcul.com
Rojitasha is a supplier for Tata Motors. The factory is situated in Sidkul, Sector 11, an industrial area in Pantnagar, Uttarakhand. Metal chassis for Tata’s mini truck ‘Chota Hathi” are produced here. The factory used to produce in Poona and has been re-located to Pantnagar, an industrial area of the Sidkul. The factory employs 500 workers out of which 50 are permanent, the rest hired through contractor. The company established the factory as part of the Engineering Industry agreement, but nevertheless openly makes use of the contract system. Apart form this work-force there are about 150 staff employed at Rojitasha. Formal owners are S.D. Gange and R.D. Gange. Tushar Kumble is the plant manager and Pradeep Barik is the production manager. The company manufactures metal bodies for 750 mini trucks a day, using sheet metal and form-giving machinery.
Open violation of health and safety standards and measures
The workers in the area call the Rojitasha factory the ‘scrubby factory’. In the inner yard of the factory scrub and bushes grow, the imported sheet metal for the chassis is also kept in the undergrowth, next to all kinds of rubbish and dirt. In the factory the sheet metal is cut, bent and welded. The noise pollution is extreme. A lot of metal dust and gas from the welding is in the air. Despite the accidents and the dangers neither masks, nor helmets, nor safety glasses, nor ear plugs are handed out to the workers. The factory is therefore also known as the ‘mutilating factory’. The workers are afraid of permanent damage to eyes, lungs, … to their body.
The company runs on two 12-hours shifts, overtime is paid at single rate. The workers receive 247.50 Rs per 12-hours shift. The legal minimum wage for an 8-hours shift is 165 Rs, and it is a crime to force people work longer than these 8 hours. If required the workers are also made to stay 24 hours or 36 hours on stretch. The long working-hours tire the workers out, more accidents happen, more hands get cut, most accidents happen in the 11th and 12th hour of the shift. Everyday workers are hurt, three to four workers become permanently disabled each month. The management and contractors give private treatment to these workers, they try to emotionally blackmail the workers or promise them compensation and permanent employment in the company – in order to prevent the workers from taking legal steps against the company. When things have cooled down these workers are kicked out of the company. Because the workers hired through contractors are not on record they can hardly prove that they have been employed at Rojitasha.
We tell the story of the worker Vikas from Visalpur, who started working at Rojitasha on 27th of September 2010. The worker’s parents are ill, they are not able to do hard work. Vikas’s wife only sometimes finds work on other people’s fields in the villages. He is the oldest of six siblings, so when he was 20 years he left the village to look for a job in factories like Rojitasha. On 16th of November at 3 am in the Rojitasha factory the worker’s hand gets into the metal cutter. Five fingers of his left hand are severed. The contractor first sends him to the private Shubham Surgical Centre in Rudrapur, then to a private nursing home. The worker also goes to a hospital, but his fingers are lost. The contractor puts pressure on Vikas, so that the story cools down and Vikas will meet the same sad fate like the other workers. Rojitasha did not contribute neither to PF nor ESI, neither did the contractor. If Vikas had been registered with the ESI, as according to law, he would now get a pension. Vikas was not aware that the care and compensation after a work accident was not a merciful act of management towards the worker, but a right of the worker which as been fought for.
Apart from that there are only six toilets for 500 workers, out of which two toilets are not usable. According to law one toilet has to be provided for 20 workers. Workers say that they have never seen so dirty toilets before. There is only one tap with drinking water for 500 workers. The food in the canteen is very expensive, about 35 Rs per meal. Wages are paid late, instead of the 7th of the month they are paid between the 15th and the 22nd.
Every second month workers go on sudden strike because of delayed wages. Only if wages are paid or the management assures that wages will be paid soon, the workers would start working again. In October 2010 workers stopped work for four to five hours and only started again once wages were paid. In November, when the question of bonus payment came up, all workers stopped work and gathered at the gate. The supervisors, contractors and managers threatened and scared the workers, the workers then went inside to work. The manager threatened that if he would be made to pay for ESI, PF, company bus etc., he would close and shift the factory. During the night of the 23rd of November the management illegally removed a welding machine, shifted and kicked out 21 workers hired through contractor.
Comments
A report of a wildcat strike at Honda in Gurgaon, India in December 2010.
On 17th of December 2010 a security personnel at Honda factory misbehaved with a temporary worker. In response temporary workers – not represented by the union – went on a wildcat strike, which brought production to a halt. The temporary workers raised demands concerning their precarious work-contract. The established union asked them to get back to work and promised that things will be taken care of. The strike continued for 24 hours, the security personnel had to apologise in front of the workers. Since the police attack on Honda HMSI workers and the registration of the Honda union in 2005 there have been several incidents of wildcat action. Most of these actions originate in the discontent of the casual and temporary workforce. Their situation has not improved since the establishment of the union, the material divisions between permanent and temporary workforce in terms of wages and conditions have widened since 2005. When they go on wildcat action the union leadership speaks of ‘instigation by pro-management forces’.
Honda Struggle 2005:
http://gurgaonworkersnews.wordpress.com/gurgaonworkersnews-no7/#fn4
Wildcat Strike 2007:
http://gurgaonworkersnews.wordpress.com/gurgaonworkersnews-no913/#fn5
Working Conditions 2010:
http://gurgaonworkersnews.wordpress.com/gurgaonworkersnews-no-930/#fn2
Working Conditions 2010:
http://gurgaonworkersnews.wordpress.com/gurgaonworkersnews-no-932/#fn1
According to some friends who visited the factory during the strike:
“On 17th of December 2010 at around 1 pm a temporary worker, who had been employed at the plant for a while was asked by his supervisor to perform duties outside the factory. He reported to the supervisor that he has not been issued a company ID, which is required when entering the premises individually. He was nevertheless sent outside. When the security personnel found out he swore at the worker and made him perform exercise as a form of punishment. The worker was upset and complained to his work-mates. They stopped working. The work stoppage spread to the other part of the plant. Finally the whole production came to a halt. The workers went to the union office, the representatives told them to wait for the union president who would come back at 5 pm. When he arrived he listened and told workers to go back to work. He promised them that the security guard would be suspended. The workers replied that they also demanded that the temporary workers were not given a break of employment after one year – the company resorts to these breaks in oder to avoid to have to give them permanent employment. The president asked workers to return to work. The permanent workers tried to resume work, but the temporary workers prevented them from doing so. During the night union representatives said that management spread the word that they would engage in a lock-out if work would not restart next day. This increased the division between permanent and temporary workers. Of the arriving early shift only the permanent workers were allowed to enter the factory. The security guard were made to apologize in front of the workers, but the other issues (break of employment) were ‘taken care of’, as said by the union representatives. To outsiders the union president said that apart from the issue of misbehaviour by security personnel there was no ‘other issue’. The company organised extra buses to get the workers back home. The next day, on the 19th of December the factory was closed for an early weekend. The temporary workers left with a general feeling of anger.”
We met a canteen worker some days after the strike. He said:
“After the incident with the security guard small groups wandered around the premises. When the second shift arrived at 2 pm, all workers gathered and encircled the management building to shout slogans. At that point the permanent workers were still with the casual and temp workers. Only after the security guard apologized and the temp workers still maintained their demand concerning the enforced break of employment, the permanent workers left the action. There were no leaders among the temporary workers – but the fact that there will be union elections at the end of January and the fact that there is an opposition within the union will have played a role. The numbers of workers on the premises came down. At the end about 250 workers stayed in the canteen over night. The management did not try to intervene, but there were about 150 police on the factory premises. Some managers say that the action has caused a loss of 7 crore Rs.”
According to the media:
“The workers at Honda Motorcycles & Scooters India (HMSI) plant in IMT Manesar, called off their strike following the suspension of one of the security personnel. The end came about only after Haryana labour department officials and leaders of the HMSI Workers Union intervened. The HMSI management suspended the services of the guard. They also advanced the Sunday weekly off to Saturday, to soothe tempers. According to the workers, the security guard insulted one of the casual workers by asking him to hold his ears as punishment for trying to enter the factory without his identity card, which he forgot to bring. In a written statement, the HMSI termed the affair a ‘small incident of indiscipline between security personnel and casual workers’. Senior HMSI official Harbhajan Singh said the workers had been instigated by a group of trade union members. Workers sources, said there was still uncertainty and the production shutdown has resulted in a loss of about 5000 units since yesterday. The workers claimed that about 2,500 casual labourers went on a flash strike. Singh said the guard was suspended from work pending investigations and labour leaders had addressed workers on Saturday to bring the situation under control. With two groups of trade unions operating, there was a chance for ‘trivial issues’ being blown out of proportion, Singh said. The Manesar factory produces 1.6 million two-wheelers per annum with a daily production of 5,500 units. The company is building another R500-crore plant at Tapukara in Rajasthan with a capacity of 600,000 per annum. Last year HMSI suffered a loss of over Rs. 300 crore after workers went on a go-slow strike that had resulted in production dipping by over 50 per cent for nearly three months. The strike, which the company says was a minor incident, happened a day after Honda announced it will sell off its 26 per cent stake in world’s largest two-wheeler company, Hero Honda Motors Ltd. It symbolised the Japanese firm’s problems in managing industrial relations in India.”
Comments
We have documented reports about the dispute at the garments export factory Viva Global before – see GurgaonWorkersNews no.32
The struggle has been lost in an objective sense: the workers engaged in the trade union lead dispute are now unemployed and the factory has been closed. The buyer ‘Marks&Spencer’, which has been in the focus of the media campaign and petitions, denies that it has received goods from Viva Global during the months before the dispute. The struggle has been lost despite the fact that it has been ‘promoted’ by international media campaigns and activities.
The local revolutionary left target the ‘easily identifiable weak spots’ when criticising the organisation behind the strike: the union is part of a NGO-set-up, which, through mediation, is funded by the US-based Ford-foundation. The resources have been used to recruit ‘organisers’ among students and workers and to ‘drive for union registration’. We think that the criticism should go a step further and raise the question of how ‘victorious’ struggles are imaginable in a globally squeezed and structurally weak industry like the garment sector. It will not be enough to replace the ‘NGO’-union with a ‘revolutionary’-union and the ‘paid organisers’ with ‘professional cadres’. From the IWW strikes in the US at the threshold of the 19th to the 20th century to the garment workers riots in Bangladesh today: the strikes in the textile industry have always involved a level of mass violence if they did not manage to spread beyond their ‘structurally weak foundation’ – it is relatively easy to shut and re-open a garment factory.
We have no practical alternative on offer, but to learn from the ‘many defeats’ of individual struggles for union recognition in the garment sector of Delhi’s industrial areas and the few example of very short, but temporary successful ‘direct action’ of workers, mainly during the time when new orders came in or when shipping dates had to be met. You will find many examples in previous issues. It requires deep understanding of daily factory reality and global industrial structures in order to find the form of struggle appropriate to the specific material conditions. Only based on the insight of the ‘immediate production process’, forms of organisation can be determined which allow the workers the highest degree of control over their struggle. Many ‘revolutionaries’ and ‘well meaning people’ lack this knowledge. ‘The registered union’ is their external way to relate to workers’ reality, a way which reserves a role for them as middle-class people: spokesperson, legal advisors, negotiators, agitators. If they refuse to reflect their social position and consequently present ‘the trade union’ as the ‘organic workers’ organisation’ and ‘all-time solution’, they create traps for the workers and unnecessary limitations to future movements. The following report is by a worker employed at Viva Global. In the case that it is not accurate, please get in touch.
Viva Global Worker
(413 Udyog Vihar Phase 3)
About 30 of us were hired through contractor in March 2010, we were working on piece rate. On 25th of August 2010 we were stopped at the gate and asked to request the outstanding final wages from the contractor. The wages for August – around 125,000 Rs – we have still not received, it is now the 26th of October. The company says that it won’t pay wages, because we went on strike, which has caused the break-up with the buyer [Marks&Spencer]. They say that, but it was the company management itself which had kicked us out. The dispute had involved 100 permanent workers who had been hired by the company directly. From 23rd August onwards 100 permanent workers staged a protest sit-in in front of the company, while 40 permanent workers were working inside. Now that there is a case running with the labour department, the protest has been called off. Those 40 workers who had remained inside were given their final wages on 1st of October. Out of the 100 workers who had been involved with the union 35 workers took an extra of 10,000 Rs as a final payment. 30 women workers and 35 male workers are still with the union. The production department has been closed. Some office employees are still working.
Comments
Updated version of the Glossary: things that you always wanted to know, but could never be bothered to google. Now even in alphabetical order.
AITUC
BPO
CITU
Casual Workers
Contract Workers
Crore
DA
DC
ESI
Exchange Rate
HSIIDC
ITI
Jhuggi
Lakh (see Crore)
Lay off
Minimum Wage
Panchayat
PF
Ration Card
SP
Staff
Trainees
VRS
Wages and Prices
Workers hired through contractors
AITUC
The All India Trade Union Congress (AITUC) is the oldest trade union federation in India and one of the five largest. It was founded in 1919 and until 1945, when unions became organised along party lines, it was the central trade union organisation in India. Since then it has been affiliated with the Communist Party of India.
BPO
Business Process Outsourcing: for example of call centre work, market research, sales.
CITU
Centre of Indian Trade Unions, a national central trade union federation in India. Politically attached to CPI(M), Communist Party of India (Marxist). Founded in 1970, membership of 2.8 million.
Casual Workers
Workers hired by the company for a limited period of time.
Contract Workers
Workers hired for a specific performance, paid for the performance.
Crore
1 Crore = 10,000,000
1 Lakh = 100,000
DA (Dearness Allowance):
An inflation compensation. Each three to six months the state government checks the general price development and accordingly pays an allowance on top of wages.
DC
Deputy Commissioner, Head of the District Administration.
ESI (Employee’s State Insurance):
Introduced in 1948, meant to secure employee in case of illness, long-term sickness, industrial accidents and to provide medical facilities (ESI Hospitals) to insured people. Officially the law is applicable to factories employing 10 or more people. Employers have to contribute 4.75 percent of the wage paid to the worker, the employee 1.75 percent of their wage. Officially casual workers or workers hired through contractors who work in the factory (even if it is for construction, maintenance or cleaning work on the premises) are entitled to ESI, as well. Self-employment is often used to undermine ESI payment.
Exchange Rate:
1 US-Dollar = 43 Rs (July 2008)
1 Euro = 68 Rs (July 2008)
HSIIDC
Haryana State Industrial and Infrastructure Development Corporation
ITI
Industrial training, e.g. as electrician or mechanic. Two years of (technical school), one year of apprentice-ship in a company. During the two years at school the young workers receive no money, but they have to pay school fees. A lot of the bigger companies ask for ITI qualification.
Jhuggi
Slum Hut
Lakh
see Crore
Lay off
Lay off in the Indian context means that workers have to mark attendance, but they actually do not work and receive only half of the wage.
Minimum Wage:
Official minimum wage in Haryana in June 2007 is 3,510 Rs per month for an unskilled worker, based on an 8-hour day and 4 days off per month. But hardly any workers get this wage.
Panchayat
A locally elected village administrative body in charge of village-level issues.
PF (Employee’s Provident Fund):
Introduced in 1952, meant to provide a pension to workers. Officially applicable to all companies employing more than 20 people. Official retirement age is 58 years. Given that most of the casual workers belong to the regular workforce of a factory, they are entitled to the Provident Fund, as well. So are workers employed by contractors. If workers receive neither PF nor ESI they also do not show up in the official documents, meaning that officially they do not exist.
Ration Card
Officially the so called ‘governmental fair price shops’ are shops were ‘officially poor’ people can buy basic items (wheat, rice, kerosene etc.) for fixed and allegedly lower prices. In order to be able to buy in the shops you need a ration card. The ration card is also necessary as a proof of residency, but in order to obtain the ration card you have to proof your residency. Catch 22. Local politics use the ration depots and cards as a power tool that reaches far into the working class communities. Depot holders’ jobs are normally in the hands of local political leaders. In return they receive this privileged position, which often enable them to make money on the side.
SP
Superintendent of Police, Head of the District Police.
Staff
In India staff includes managers, supervisors, security personnel and white-collar workers.
Trainees
In general trainees work as normal production workers, they might have a six-month up to two-year contract. Depending on the company they are promised permanent employment after passing the trainee period. Their wages are often only slightly higher than those of workers hired through contractors.
VRS (Voluntary Retirement Scheme):
Often a rather involuntary scheme to get rid of permanent workers. Particularly the VRS at Maruti in Gurgaon made this clear, when 35 year olds were sent in early retirement.
Wages and Prices:
When we hear that a cleaner in a call centre in Gurgaon, an industrial worker in Faridabad or a rikshaw-driver in Delhi earns 2,000 Rs for a 70 hour week, which is about the average normal worker’s wage, we have to bear in mind that they often came from West Bengal, Bihar or other remote place in order to get this job. In order to put 2,000 Rs into a daily context here are some prices of goods and services – based on Summer 2006 prices. Inflation levels have been high since then. Fort more recent prices see:
http://gurgaonworkersnews.wordpress.com/gurgaonworkersnews-no-928/
Housing:
- Monthly rent for a plastic-tarpaulin hut shared by two people in Gurgaon: 800 Rs
- Monthly rent for a small room in Gurgaon (without kitchen), toilet and bathroom shared by five families: 1,300 Rs
- Monthly rent for a small room in a new building in central Gurgaon, single toilet and bathroom: 4,500 Rs to 8,000 Rs
Food:
- Half a kilo red lentils on the local market: 25 Rs
- Kilo rice on local market: 14 Rs
- 1 Kilo Onions and 1 Kilo carrots on local market: 25 to 30 Rs
- McChicken: 40 Rs
- Bottle (0,7l) of beer at Haryana Wine and Beer shop: 50 to 70 Rs
- Cigarettes (10), cheapest local brand: 25 Rs
- Starbucks Coffee (Latte Medium) in Shopping Mall: 59 Rs
Utensils:
- Faulty shirt on Faridabad local market: 40 Rs
- Single gas cooker plus new 2 litre gas cylinder: 720 Rs
- Re-fill gas (2 litres – once every month and a half): 100Rs
- Second-hand bicycle: 600 to 1,000 Rs
- Two simple steel pots: 250 Rs
Transport and Communication:
- Bus ticket to nearest bigger bus stop in South Delhi: 14 Rs
- Daily Newspaper: 3 Rs
- One hour internet in a cafe: 20 Rs
- Cinema (new) ticket Saturday night: 160 Rs
- Single entry for swimming pool: 100 Rs
- One litre Diesel: 30 Rs
- Driving license in Haryana: 2,000 to 2,500 Rs
- Start package pre-paid mobile phone (without the phone) 300 Rs
- Phone call to other mobile phones: 1 Rs
- One month mobile phone flat rate: 1,500 Rs
Luxuries:
- Minimum dowry poor workers have to pay for the marriage of their daughter: about 30,000 Rs (80,000 Rs more likely)
- Money given to poor labourers for their kidney: about 40,000 Rs
- Compaq Laptop: 50,000 Rs
- Flight Delhi to London: 28,000 Rs
- Cheapest Hero Honda motorbike (150 cc): around 40,000 Rs
- Ford Fiesta: 587,000 Rs
- Four hours on Gurgaon golf course: 800 Rs (info from golf course worker earning 2,400 Rs monthly)
- Two-Bedroom Apartment in Gurgaon: 10,000,000 to 50,000,000 Rs
Workers hired through contractors
Similar to temporary workers, meaning that they work (often for long periods) in one company but are officially employed by a contractor from whom they also receive their wages. Are supposed to be made permanent after 240 days of continuous employment in the company, according to the law. A lot of companies only have a licence for employing workers in auxiliary departments, such as canteen or cleaning.
Comments
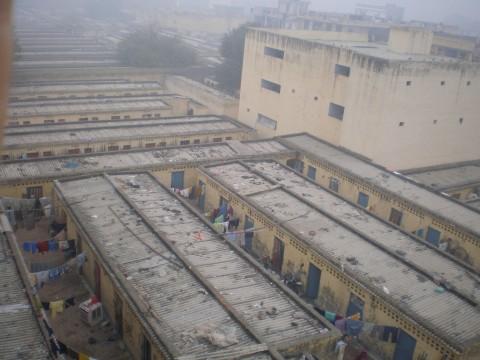
Gurgaon workers newsletter issue 35, with news, reports and analysis from India's special exploitation zone.
Comments
Detailed additional information, including participants' reports about the wildcat strike of Honda workers in Gurgaon, India in December 2010.
The short wildcat strike at Honda HMSI on 17th of December 2010 has to be seen on the background of growing anger of a casualised workforce in the main industries of the global south. Be it temporary workers at Hyundai in South Korea, Honda supplying workers in China or Nokia workers in Chennai, in the shade of a minoritarian ‘permanent’ work-force – which bourgeois media focuses on when reporting about gains of development – the unrest increases. We first document additional information on the strike based on Honda HMSI temporary workers reports; we then have a short look at recent international conflicts which bear an systemic semblance to the Honda Gurgaon strike and conclude with some preliminary thoughts on ‘What could be done?’ on an immediate and local level.
The Wildcat Strike at Honda HMSI in Gurgaon
After publishing a first general report in the last issue of GWN we spoke to workers hired through contractor employed at Honda who took part in the strike. The report is being circulated in the January/February issue of Faridabad Mazdoor Samachar.
HMSI Worker
(Plot 1, Sector 3, IMT Manesar)
On Friday 17th of December, after having worked for about two hours, the A-shift workers at the scooter line suddenly stopped work, they went in groups to the other departments of the factory, where they were joint by the rest of the workers. The arriving B-shift joined them, they did not start working. At 11:30 pm management suddenly announced that the weekly day off would be shifted from Sunday to Saturday – the following day. The A-shift workers, who arrived ay 5:30 – 6 am at the bus stops waited in vain for the company buses, they then found out by phoning work-mates and supervisors that the day would be off. On 19th of December the A-shift resumed production, the factory then ran continuously till 27th of December, the time between 27th of December and 2nd of January is the annual maintenance time off… On Friday, the 17th of December, a worker hired through contractor told his work-mates that he had been mistreated by a security guard. The workers immediately stopped working. Permanent workers, casual workers and workers hired through contractor were together in this… The strike spread from the scooter line to the motorcycle lines to the weld- and machine shop to the PI department… the entire work-force was involved. Both A and B-shift workers joined. It was the first time since 2005 that the entire work-force would be in action together, 1,800 permanent and 6,500 workers hired through contractor together. Under the impact of wildcat action of 8,000 workers the management was shaken. “Keep calm, the union president is currently not here, he will be coming at 5 pm”, the workers were told. The main manager for plant security apologised in front of the workers and told them that the security guard would be kicked out. A senior member of management said that he has come all the way from Jaipur to sort out the issue. Workers showed their anger: “We don’t want your apologies, bring the security guard, he should apologise. And you could have come from Japan instead from Jaipur, we don’t care. We want that you stop the clearance.” 1 At 3:15 pm the busses of the A-shift left the plant and quite a few permanent workers left the factory. At 4:30 to 5 pm the union president arrived and said that everything will be arranged in favour of the workers, but that they should go back to work. The permanent workers retreated, but the workers hired through contractor catcalled the union president and accused him to have done nothing about the ill-treatment and discrimination of workers hired through contractors. Had the workers started the wildcat shouting “Down with management, long live the union”, these workers shouted some hours later “Down with management, down with the union”. The rumours spread that management would resort to a lock-out, which caused the permanent workers to withdraw further, but which did not result in controlling the workers hired through contractor. The union president requested several times to resume work, the workers ignored the requests and the union president left the scene angry. The B-shift did not start working – without the workers hired through contractors production could not have been started. The company then announced that Saturday would be off. After A-shift did not arrive at the factory and after 150 to 200 police turned up, workers left the factory on Saturday at 11:30 am. The shaken management did not put up any notice in reaction to the strike. The company did not undertake any open repression apart from suspending a permanent worker, accusing him of instigation. There is talk about 170 workers hired through contractors having been put on a list in order to kick them out ‘secretly’. When workers were assembled together it was mentioned several times that a similar strike had happened in 2004. Back then a group of five workers hired through contractors had been sent to negotiate with management, they left in a company car and disappeared from the scene without workers knowing what had happened to them. It was also said that this time workers should be careful not to expose themselves.”
We want to give some additional information concerning the general background of the strike and encourage you to read the reports from Honda HMSI predating the dispute. In these reports the general day-to-day divide between permanent and temporary workforce becomes clear.
The permanent workers earn up to 31,000 Rs per month, while temporary workers earn around 6,500 Rs. The wage divide has been growing since the establishment of the union in 2005, so has the relative numbers of temporary workers and their work-load. Permanent workers are mainly employed in supervising positions and departments like maintenance, welding, machine shop, final quality check. The line-leaders are permanent workers who have been employed for a minimum of two years and who underwent extra-training. Each of the three main assembly lines is segmented into three-four zones, line-leaders are in charge of these zones where between 25 and 60 workers work. The assembly lines themselves are spacially separated in two main halls. Below the ‘line leader’ there is a supervisor, who normally reports for 8 to 10 workers, The supervisor tends to be a worker hired through contractor himself. A temporary worker reported that while a permanent ‘line leader’ initially supported the strike, the temporary worker himself was rather anxious to be seen taking ‘actively part’, because his supervisor was standing close by – who was a temporary worker, too.
In general temporary workers did not show too much fear, despite the fact that one of the managers present during the dispute was the manager who runs the ‘tests’ of temporary workers. The test is the only chance for temporary workers to become a casual company worker. The next test will be in February 2011 – allegedly around 1,200 temporary workers will take part and 80 will have the ‘chance’ to become a casual worker. The test contains – apart from general questions of production details, such as colour of electrical connection used for this or that vehicle part – the name of the Japanese capital or the Indian Minister for Industry. During the last years less than 80 temporary workers were are made ‘company casual’. The fact that this year the number increased is – according to rumours – due to the opening of the second Honda HMSI plant in nearby Bhiwadi, which is approximately 40km from the existing plant and approximately 90km from Delhi.. Production there is supposed to start in April. According to other sources no workers are transferred from Manesar plant to Bhiwadi, only some middle managers are shifted. Officially there is no ‘production’ shift planned, the capacities in Bhiwadi are additional to those in Manesar.
We finally want to say a few words about the question whether the coming union election played a major role in the dispute – as stated by a Honda manager. The fact that the suspended permanent worker belongs to the oppositional AITUC faction indicates that the ‘faction’ struggle has some influence. The AITUC faction is the original union faction, which fought for recognition in 2005. The current leading faction – which took over two years ago – is portrayed as a ‘management friendly’ faction of mainly ‘local workers’. The current union leadership put up a notice immediately after the strike saying that they regard the dispute as trivial – which was a blunt sign for management that they would not oppose a suspension. The management in due course suspended the permanent worker on 20th of December.
When using phrases like ‘management friendly faction’ etc. we would ask you to bear in mind that during the wildcat strike of temporary workers in October 2006 [http://gurgaonworkersnews.wordpress.com/gurgaonworkersnews-no7/#fn43], the now opposition AITUC faction was the leading union body and they denounced the strike as ‘instigated and anti-union’, as much as the current leadership denounced the December 2010 strike. The conditions of temporary workers has not only declined since the last two years of ‘new union leadership’, the wage gap and work load started to increase before that. The temporary workers demonstrate that they are more than mere pawns of this faction or the other. Historical experiences, e.g. during the 1980s restructuring period in nearby Faridabad, show that the last straw of management, when having to deal with mass-level of unrest, is to turn it into a representative/factional struggle. If necessary they are happy to accept a ‘management hostile’ faction, too, as long as they have at least someone to talk to.
The International Character of the Dispute
In the Faridabad Mazdoor Samachar issue distributed in Delhi industrial areas in January/February 2011 we concluded the report – see translation above – with an example of the recent strike of automobile workers at Denso in China. Facing management and state repression these workers had refused to put forward ‘delegates’ for negotiations and instead confronted management with anonymously written demand letters. Here we don’t want to go deeper into the question of ‘potentials and limitations’ of ‘anonymous struggle’, but rather stress the point that the Honda HMSI dispute has a wider international background. We picked three examples of recent struggles of a casualised workforce; a workforce outside of the ‘recognised’ employment and union status, but right at the core of the new global workbench which emerged after the mass-relocation of industry and casualisation of work-force during the 1990s.
Hyundai/South Korea
The wildcat strike of temporary workers at Hyundai in Ulsan (South Korea), began on 15th of November 2010. Around 570 out of 2,000 temp workers stopped assembly lines, demanding permanent contracts – according to Korean law they would have to be made permanent after two years of employment. They occupied a factory department which links the automatised storage halls and assembly lines of the factory. They resisted police attacks and harsh conditions – but by 6th of December technicians managed to bypass the occupied part of the factory, numbers of occupiers came down to 260 by that time. On 9th of December they evicted the building. During the dispute they received no solidarity from permanent workers unions: three days after occupation 600 permanent workers and middle management organised protest against strikers. In a formal spectacle FKTU union asked members whether to join the strike, but 77 per cent members voted against joined action.
Honda/China
The morning of 17th of May 2010 workers in the automatic transmission department halted the assembly line by pushing the red stop button, normally used for emergency shutdowns over quality problems. The company offered various raises in bonuses and subsidies for different groups of workers, but the workers insisted on a general raise in the base wage. The company fired two workers who had initially stopped the line. The harsh reactions of management galvanized the workers.
On 24th of May, the strike became indefinite, soon affecting Honda’s main assembly plants in Guangzhou and in Wuhan in central China. Both factories had to stop production on 26th and 27th of May. The local government, along with the union and management, took a more and more aggressive stance, resulting in the mobilization of a group of about 100 thugs clad in union uniforms, who confronted the workers physically.
http://www.labornotes.org/2010/12/auto-worker-strikes-china-what-did-they-win
http://chinastrikes.crowdmap.com/
Honda/Mexico
Since December 2010, after sacking of an active worker, struggle at the Honda plant in El Salto, Jalisco intensified. Twenty-one hundred workers on two shifts assemble 5,000 trucks a month, most of them exported to the United States. Since 2009 workers have been resisting and have held several work stoppages to demand that management modify its demands and its attitude. In every case management has responded with repression and firings of the workers it saw as leader. Management maintains a “protection union,” the CTM (Central de Trabajadores de Mexico, the largest official union in the country). The atmosphere at Honda is one of constant hostility and contempt for the dignity of the workers on the part of the foremen. Meanwhile, Honda’s logo reads “The Power of Dreams.” This charro union, as Mexicans call unions that serve the employers, plays the role of formally complying with Mexican law, but in reality it is an instrument that management uses to keep salaries the lowest of all assembly plants in the country. The daily wage is $10-$12.30 per day.
What Could be Done?
There are a few things which any small group of workers/activists can do. Situations like on 17th of December will emerge again and again, question will be whether workers a) will be able to enforce their demands because they actually hit the company; b) they manage to avoid giving management opportunity for open repression as far as possible c) develop stronger organisational links within and beyond the Honda factory as a result of the dispute. We can do out bit to help, which could mean:
* keeping in touch with workers directly – not only their official representatives – in order to follow general developments in the factory (individual repression etc.)…
* finding out whether the information of the 24 hours strike has spread to workers in the surrounding/supplying industry and through which means (through room-mates, security guards, actual production-stops, by seeing police etc.); this would tell us something about to which extend workers can rely on ‘organic forms of industrial and proletarian communication’ and how we can intensify it…
* analyzing current economic situation and production system at Honda with workers, if possible by facilitating regular meetings between Honda workers and workers in the nearby supplying industry (see reports of automobile workers in this issue)…
* arguing for both, need for avoiding traps (‘faction union struggle’, ‘making delegates’, unnecessary physical confrontations, lock-outs, left isolated during factory occupation etc.) and the necessity of extension of future struggles,
* making sure that these positions find a voice and practical support in future struggles…
* looking for acquaintances among workers in the new Honda plant as quickly as possible and inform new workers about experiences of struggles at Manesar plant since early 2000s…
* encouraging flow of information between workers in similar situations on local, regional (Chennai etc.), international level…
- 1 Management kicks out workers hired through contractors once they have completed a year of employment and often re-hire them two weeks later. They do this in order to prevent the workers gaining legal right to permanent status.
Comments
In a report on the death at work of a textile factory worker and subsequent strike in Gurgaon, India.
The following report about the sad death of a garment worker at Modelama factory in Gurgaon was sent by a friend of Gurgaon workers news.
Since then the death of a worker seems to turn into a back-and-forth between different interest groups about the question of compensation. A former MP from Maharashtra, who belongs to the same village as the worker, took a middle-man role.
“At around 3am on the morning of 16th January or, the 15th night’s overtime, 17 and-a-half hours into continuous sewing and stitching for the 21hour shift, sitting on his iron stool, Md. Rabban, died instantly of electrocution through one of the live wires protruding out of the production line in the garment factory, Modelama Exports in Plot no.105-106, Phase 1, Udyog Vihar, Gurgaon.
Md. Rabban, who had been working, sampling, stitching, sewing, washing, ironing and producing clothes for Modelama, for the past more than 7 years and in the 105 unit since its production started three and-half years back, hailed from Muzaffarpur, Bihar, and was paid the measly minimum wage of Rs.4200 (after the cuts for ESI, PF, and the ‘breaks’, from Rs. 4800). As usual, on 15 January also, Rabban reached in the morning 9.30 am shift to start his day on the production line to work till 6.30am the next day, to resume work again at 9.30am. There were two breaks of half-hour each at 1.30-2pm, and then again at 6.30-7 (which workers pay for themselves, and for which wage is deducted from the workers themselves), a dinner break from 8.30-9.30pm (tasteless stale food in the canteen, for which the company pays a mere Rs.20), and then a next chai break at 2.30-3am. Ten minutes later into resuming work, at around 3.10am, in the overtime and already 17 hours into work, one of the live wires protruding out in front of his machine, electrocuted Rabban as his hand was caught in between the line. A number of complaints were regularly made about the safety conditions and specially about the leak in the current in the electric machines in the production line, and nothing as would cost the company was done about it. The usual thing that does get done in such situations by the management is the ‘management’ of the body, i.e. to wipe it out of sight, as workers recall earlier incidents of the sweeper in the morning sweeping out litres of blood on occasions of the death of workers due to over-work, clash with management etc. However, before any such ‘cleansing’ attempt, the around 80 workers in the production line who witnessed the incident, made an uproar, and tried to help their saathi/work-mate. There was a cry for immediately taking Rabban to the hospital, and because the company had neither doctors nor an ambulance for such (frequently occuring) situation, and was also unwilling to spare its own cars, the workers offered to take him themselves to the hospital in a hired car in front of the company and were pooling in the Rs.1500 required for the transport. Sensing the workers reaction, the management (the supervisor and other staff) shut production immediately, took possession of the body, and took him to the hospital where he was declared brought dead, and then to the morgue after post-mortem, and with an rapidity which only came later, also took the body to the Nizamuddin cemetry and buried him. The police was informed and an F.I.R registered under Sec.304-A which declared it a freak ‘accident’.
Meanwhile the workers of the production line, were joined by those coming in for the morning shift, and anger erupted outside the closed gates of the factory, with over a thousand workers pelting stones and breaking the sleek glass front of the company. The low pay, the single overtime, the non-payment of back wages, the no-offs strictness, the continued and regular harassment in the form of abuse and even slaps and beatings, the strong surveillance in the from of finger-print/biometric entry and the CCTV cameras at every nook and line with the suspicion of workers-as-thieves while clearly it is the other way round, all took form in this solidarity action. Workers of other companies in the area going for their morning shifts also joined in to express their solidarity and anger. Police was employed to control the anger, and disperse the angry workers who demanded justice for Rabban.
The company however came out much later, and made an oral statement about the promised payment of Rs. 1lakh to the family of the deceased. And by around 2pm on the 16th, the spontaneous wave of anger was stifled with the threat of police, targetting-and-possible-suspension and management-through-the-family. The next day’s newspapers reported in an insignificant column, an accident in the Modelama company which was resolved. Work remained suspended on the 16th. /on the 17th morning, when workers got back to the company, after some initial tension at the gates, work was resumed. however soon after, in many departments, many workers again took up the previous day’s incident and its sham resolution in a general uproar, which the management stifled with selective representation of some workers, and a promised 50-50 joint-fund of workers and the company’s contribution which will be paid to the family of Rabban. That it was a direct case of negligence of the company was skirted and work was resumed again, not after a fire broke out (it was unclear how, or by whom) in one of the departments which took some time to be doused.
The Modelama Exports unit situated in plot 105-106 in Phase 1, has around 4500 workers, and it is one of its several units in operation in Haryana, Delhi and Chennai. (Plot nos. 105, 106, 184, 200, 201, 204 in Udyog Vihar, Phase-I, 660 in Phase-II, plot nos. 5, 7, 18, 89 in IMT Manesar, one each in Sonipat and Rewari, two- B-33 and B-57 in Okhla Phase-I, and one in Chennai). Selling “the mystifying aura of fashion”, it is a big name in the ready-made garment industry besides expanding into home furnishing, jewellery, energy and real estate. Its chairman, Lalit Gulati was the president of the owners’s association, Apparel Exporters and Manufacturers’ Association. Its production units cover 400,000 sq. feet area, and has a production capacity of 6 million garments per year and a turn over of US $ 60 million. Its ‘vision’ statement says that it seeks to maintain a balance between “ethical values and corporate objectives” and that it “takes pride in the human resource” that it has. It counts its buyers from the US, UK, Canada, Europe and Australia, among them being big corporate players like Gap, Banana Republic, Marks &Spencer, Abercrombie &Fitch, and Country Road. Its main buyer, Gap is a leading member of the ‘Ethical Trading Initiative’ body of Companies, NGOs and trade unions, which ‘promotes ethical trading’ and ’3rd party auditing’ (an industry which recent estimates show has grown to a staggering US $50billion!) and is supposed to have been specifically ‘monitoring’ the 105 unit for ‘workers rights violation’ with a number of complaints earlier. It is another classic case of the exploiter making the rules of violation and monitoring.
Comments
While workers in the global north are with their backs to the wall of crisis – see current dispute at FIAT Mirafiori – the automobile workers in the global south suffer for a pathetic ‘boom’.
We document 17 short reports from automobile workers, employed up and down the supply-chain: from work-shops with a couple of machines and half a dozen (child) labourers to the first-tier suppliers and the assembly plants employing thousands. In the Delhi region the supply-chain is stretched out over a hundred or more kilometres, the current effort to turn the country-road between Faridabad and Gurgaon into a six-lane highway has to be interpreted in terms of automobile crisis: the slow traffic impacts on the production process as much as on the use(less) value of the final product, with average car travel speed often hardly exceeding the velocity of a cycle or bullock cart. The current petrol price hikes add financial pressure.
Due to the fact that the supply-chain is formally divided up into different company units, the internal contradictions within the industry surface as ‘different private interests’. The main automobile companies try to outsource not only stock and certain production steps, but also the financial risks. Component producing suppliers complain about financial squeeze: there is increasing price pressure from both sides (steel and rubber prices are increasing and final assembling companies asking for lower prices) and the current hike in interest rates as part of ‘anti-inflationary measures’ make investments in capacity expansion more costly. Final assembling companies ‘take informal credit’ from suppliers by paying for parts, not in advance, but with increasing delay of up to 180 days. The final assembling plants are compelled to increase capacities and to run the capital-intensive plants 24 hours, while the rest of the supply-chain is dragged deeper into the squeeze.
The wildcat strike at central assembly plant of Honda HMSI on 17th of December has demonstrated that ‘labour costs’ are not a mere figure in the overall calculation, but an angry soul in a heartless machinery – see report in this issue of GurgaonWorkersNews. Any revolutionary effort will depend on turning the supply-chain into the radical chains, which we will have to lose: re-composing working class from the assembling centres to the labour intensive peripheries.
The following reports have been gathered and re-distributed with Faridabad Mazdoor Samachar in November/December 2010.
Boxer India Worker
(Milhard Colony, New Town Station, Faridabad)
The workshop employs nine workers. Wages are 3,000 to 3,500 Rs for helpers. Overtime is paid at single rate.
Karma Engineering Worker
(Sector 22, next to Rachna Cinema)
The workshop employs 25 people. They produce car parts on 12-hours shifts. There is no weekly day off. The helpers get 3,000 Rs and the machine operators get 4,000 Rs to 4,200 Rs.
Hanu Industries Worker
(Plot 152, Hridaykund Colony, Mujesar)
The 20 workers get between 3,000 and 4,000 Rs per month. The work-shop runs on two-12-hours shifts. There are two rubber mixing rollers, nine extruder machines, a boiler, three moulds and a generator. For production rubber and carbon is used, the air pollution is bad. Workers get ESI and bonus is given.
Akma Auto Worker
(Barkhal Gaon, Sector 49)
Around 150 workers are employed to manufacture axles for motorcycles. A lot of children between 12 and 14 years are employed. They receive 1,000 to 1,200 Rs per month, the older workers get 2,500 to 3,000 Rs. No ESI, no PF.
Varun Precision Components Worker
(Plot 220, Sector 59, Faridabad)
We work on two 12-hours shifts, we produce parts for Hero Honda two-wheeler gear. The parts we produce are sent to Shivam Autotech, from there they go to Hero Honda. The 40 workers hired through two different contractors get 4,200 Rs for 30 days of 12-hours shifts. The permanent helpers get 4,200 to 4,400 Rs for 26 days, the operators get 7,000 to 8,000 Rs. There are no toilets, you have to go to the railway lines nearby. The drinking water is outside of the factory in a barrel. If there is an accident, they don’t fill in the accident form. If you take a day off, they cut two days from your wages. There is swearing and slapping from ‘superiors’.
India Forging Worker
(Plot 28, Sector 6, Faridabad)
There are more than 1,000 workers employed on two 12 hours shifts. We manufacture axles and hubs for Maruti Suzuki and various tractor parts. Only the 50 people of the middle management and administration are permanent. There are 50 company casual workers, who are employed since years – they are neither kicked out, nor made permanent. Only those 100 workers get ESI and PF. The helpers hired through contractor get 3,000 Rs to 3,500 Rs, the operators get 4,500 Rs to 5,000 Rs. Around 500 workers work on piece rate system. There is metal scrap laying around everywhere in the factory – but you won’t get gloves or safety boots. If you hurt yourself you won’t find bandage in the company, you have to get private treatment. There used to be a canteen, but now there’s not. Even if you have to work 36-hours on stretch there is hassle to get extra money for food. You have to write down overtime and pieces worked, otherwise 500 to 600 Rs get embezzled.
SPM Auto Worker
(Sector 59, next to JCB)
Around 200 workers manufacture axles and gears for Tata Motors, Maruti Suzuki and export on two 12-hours shifts. They are often forced to work 36 hours on stretch – the gates are locked and the helpers are given 20 Rs for food. The helpers get 5,200 Rs for 30 days of 12-hours shifts. It is heavy work, a lot of accidents, people have to pay for treatment themselves. The toilets are defunct since years, you have to go outside, but you are supposed to be back within 5 minutes.
Oswal Diecaster Worker
(Plot 48, Industrial Area, Faridabad)
The 1,500 workers hired through contractor did not receive the obligatory annual bonus. In the diecasting department workers manufacture parts for TVS, Hero Honda and others. Workers do not get days off, even when ill. They are told: Take some pills and work.
JNS Industries Worker
(Plot 4, Sector 3, IMT Manesar)
The printing department runs on two 12-hour shifts, the other departments on 8-hours shifts. We manufacture metres, starting keys and other parts for Hero Honda, Yamaha, Suzuki, Bajaj, Maruti Suzuki and Mahindra. It is a big factory, the women workers are transported to and back from the plant in 19 buses. They work only day-shifts. Most of the workers are hired through contractors. The wages of permanent workers and staff are delayed, their July and August wages were paid on 15th of September. The manager of the printing department swears a lot and slaps people. During meal breaks machines continue running, people have to take their break in turns. The food is of low quality. BUT on 18th and 19th of October the food was really good: there was butter with the bread, Coriander leaves and tomatoes in the vegetables. The big shots from Japan came for a visit! The whole factory was clean and even defunct machines were run for show…
E.R. Automotives Worker
(Plot 184, Sector 4, IMT Manesar)
500 workers are employed on 12-hours shifts. We manufacture gears for the Sonalika tractor, the sheet-pipe for Hero Honda Motorcycles and hydraulic bolts for export to England. People work everyday, though only 8-hours shifts on Sundays. Overtime is paid at single rate. When we are forced to stay longer, they give you 50 Rs extra for food for a continuous 36-hours shift. There are 50 to 60 permanent workers and 450 workers hired through three different contractors. The company did not pay the obligatory inflation compensation (July) of 134 Rs. Drinking water is a big problem. The toilets are dirty.
Pacman Worker
(Plot 28-29, Sector 7, IMT Manesar)
The factory runs on two 12-hours shifts, the main work is injection moulding. Machines runs through the meal breaks, day and night, all days through the month. Overtime is paid single rate, though shown is double rate. We manufacture parts for Honda, and through the company ‘Sandhar Locking Devices’, we also produce for Hero Honda. They cut wages in the name of PF, but when you send the PF form after leaving the job the PF office sends it back saying that no money has been paid into the PF account.
Endurance Technology Worker
(Plot 400, Sector 8, IMT Manesar)
There are more than 1,000 workers employed through three different contractors, manufacturing parts for Honda, Suzuki, Mico and Bosch. Last year, permanent workers gave 1,000 Rs each and workers hired through contractor gave 599 Rs each as contribution for a union. The union was formed. The wages of permanent workers increased by 3,600 Rs and they received a canteen voucher of 17 Rs, instead of 11 Rs. The workers hired through contractor received only safety boots. After establishment of the union the company increased production by increase of line-speed. The speed-up falls on the shoulders of workers hired through contractor. The 150 permanents rather make work, they work less themselves.
http://www.endurancegroup.com/plant-address.htm
Hero Motors Worker
(Plot 61, Sector 3, IMT Manesar)
Two 12-hour shifts, work on power-presses and MIC welding. The power-press operators get 4,500 Rs, overtime is paid single. The work pressure is high. The company was previously called Repro Auto, workers used to be paid bonuses, there used to be a weekly holiday and if you had to work longer than 12 hours you used to receive 30 Rs extra for food. With the change of the company name all this has been stopped.
Talbros Worker
(Plot 51, Sector 3, IMT Manesar)
There are 80 permanents and more than 400 workers hired through four different contractors. Permanents get double rate overtime payment, the rest single. Money is cut for ESI and PF, but no money paid when you leave the job.
Track Components Worker
(Plot 21, Sector 7, IMT Mensar)
During the Common Wealth Games the pressure to provide ‘Proof of ID’ increased. The workers would have needed at least fifteen days to go back to the village in order to get the required documents. This would have meant that the factory had to be closed during their absence. In order to stop workers from ‘escaping’ the security regime during the Common Wealth Games, companies found all kind of by-passes: deals with the police that a ‘Company ID’ would do etc.. In the power press department an ‘official’ takes ‘credit’ from workers for a financial scheme, but the money gets embezzled. The company always ‘demands’ that the health and safety devices at the power presses should be used, but they actually do not install these devices. There is always the danger of cutting your hand. They used to give you 20 Rs extra for food if you had to work longer than 10.5 hours, but they have stopped this. There are less workers nowadays, therefore people are made to work longer, most of the time 14 hours, sometimes 17 to 19 hours on stretch. You would stop at 2 am at night, sleep in the factory and start again at 7 am. There is no stock of material, the machines keep on running, even on Sundays.
Munjal Showa Worker
(Plot 26, Sector 3, IMT Manesar)
There are three shifts, employed are 15 permanents, 400 trainees, 400 casuals and 1,000 workers hired through three different contractors. We manufacture shockers for Hero Honda, Yamaha and Honda two-wheelers. The trainees are given a break after one year, then re-hired as trainee. They are not made permanent, even after five years they say: if you want a permanent job, look somewhere else. The casuals are given a break after six months and then re-hired. For overtime, the trainees get 35 Rs per hour, the casuals 20 and the workers hired through contractor 40 Rs. They make you work longer by locking the gates. The workers hired through contractor are afraid that if they refuse overtime, they are made ‘casual workers’. The trainees and workers hired through contractor work 150 to 200 hours overtime per month, the casuals 60 to 70 hours. You have to stand upright all the time, no time to go to the toilet, no ‘reliever’, who would do your job while you are away. After working 16 hours constantly on the line, on 27th of November a worker at the rear-shocker line collapsed. Only the 15 permanent workers receive ESI cards. The obligatory annual bonus is also only paid to the 15 permanent workers.
Honda Motorcycle and Scooter India
(plot 1, Sector 3, IMT Manesar)
In October 2010 the company announced that till January 2011 the B-shift would have to work overtime each Monday till 1:30 am. Management cut 475 Rs from August wages of the workers hired through contractor and 2,500 Rs from permanent workers for not meeting the fixed production target. We could not meet the target, because production stopped frequently due to lack of parts. The company busses have become a ground of bitterness between permanent and temporary workers. The temp workers are made to stand up and leave the seat to a permanent workers, sometime they are made to get off the bus, they are ‘fined’ 200 to 400 Rs or threatened to ‘have them kicked out from the company’. The temp workers have to do the heavier work, they receive much lower wages, have to endure all kinds of mistreatment from the ‘permanent’ team leaders. The two-tier division exists even during Divali: the permanent workers received one kilo dried fruit each, while workers hired through contractor received only half a kilo.
Comments
Indian electronics workers strike for a meal break.
The Maxx Mobile company is situated in Haridvar, Sahadarabad. The factory produces mobile phones and their batteries. The company breaks the labour law, it does not provide a lunch break during the 8.5 hours shift. On 27th of November workers acted against this. All workers left their work and assembled at the gate. Workers demanded that the lunch break should be included into the working-day. The management refused to accept the demand. The workers started a protest sit-in at the gate. On 28th of November the company was shut for the regular Sunday day off. On 29th of November the workers continued their strike. A representative of the workers went to the labour department. The representative was assured by the officials that the demand would be met by the 7th of December – and he was sent back. In this way the labour department ‘dealt’ with the transgression of the labour law. In order to spread fear amongst the workers the management has locked-out all workers hired through contractor. All workers now wait for the 7th of December. To hope for the labour department to sort things out will be a self-betrayal and will end in workers’ passivity.
Comments
Reports from Indian garment workers on their conditions, February 2011.
We translated reports from Lakhani workers in Faridabad and Uttaranchal – a state further north of Delhi/Haryana. Lakhani is a major company engaged in garments, plastic and rubber manufacturing – from sandals, shoes (AllStars, Puma, Adidas) to car parts. Lakhani has recently opened factories in Uttaranchal, in addition to the long-time established and often conflict ridden factories in Faridabad. In some cases a division of labour and mutual dependency has been created between the two industrial centres. The reports from Uttranchal are translated from the Marxist-Leninist journal Nagrik.
Lakhani Apparels Worker
(Plot 136-b, Sector 24, Faridabad)
After July wages had not been paid by 20th of August workers stopped working. After four hours the production manager said that wages will arrive tomorrow, so people should go back to work. We started working… the July wages were paid on 2nd to 5th of September, but the August wages were not paid. Now 350 workers are left, about 400 to 500 workers have left the job. We manufacture garments, amongst others for Motherhood and Global. Up until July there was a lot of work. The daily working-times were from 9:30 am till 1 am, they often made you work till 4 am. They give you vouchers for the canteen, but the food is of low quality and won’t fill your stomach. When they force you to work Sundays, it is shown as worked on saturdays. Those workers directly hired by the company get the minimum wage. The other workers work on piece rate and/or a paid by one of the four contractors: 3,000 to 3,500 Rs per month, no ESI, no PF. The permanents are supposed to get PF, but when they leave the job they find that no money has been put into the fund. Once the buyers come, the factory is clean and workers get masks and so on.
Lakhani Footwear (Adidas, All Star)
(Plot 130, Sector 24, Faridabad)
There is one line manufacturing for Adidas, one for AllStar and two for Lakhani Shoes. At the Adidas line 500 pairs of shoes are manufactured per shift, once a representative of Adidas arrives the number is reduced to 250 pairs – they want to show how much they care for quality. The same happens at the AllStar line: normally 800 pairs, during visits 400 pairs. At the Lakhani line things are different, one line churns out 2,400 pairs per shift. While there are stools to sit at the Adidas and AllStar line, there aren’t any at Lakhani line. No time for toilet, the feet swell up. Once a representative of the buyers comes, management hands out ear plugs, masks, aprons, gloves etc., but they take it back once the visitor has left. The lines are right next to each other, but the buyer’s representatives won’t even look at the Lakhani line. When the inflation compensation of 134 Rs had to be paid according to law, they immediately increased the price for tea in the canteen, from 2 to 3 Rs. Money is cut for ESI and PF, but the 1,400 casual workers don’t get an ESI card.
Lakhani India Worker (Puma)
(Plot 265, Sector 24, Faridabad)
We worked 150 to 200 hours overtime in May, we received the payment as late as October. June and July over-time was not paid – no money. They say that overtime is paid one and a half-rate, but actually people get only 25 or 27 Rs per hour. For three months there were less orders, there was less work here. Now work has started again, amongst others for Puma. The company demands over-time from us, but we say that they should pay the outstanding wages first – we refuse to work overtime. They also did not pay the July inflation compensation of 134 Rs. In this factory 1,500 male and 1,500 female workers manufacture sandals and shoes.
Lakhani Factory -, Haridva Sidkul, Uttranchal
(from: Nagrik, 16 – 31 December 2010)
The Lakhani Vardan Group runs three factories in Haridvar Sidkul, Sector 4, Plot 20, 21, and 22. The first plant runs under the name of Lakhani India Ltd. In this plant shoes are manufactured, amongst others, for Puma, Canvass and Woodland . The second plant runs under the name of Lakhani Auto Privat Ltd. In this factory soles for shoes are manufactured. The third plant runs under the name of Lakhani Detergent and Soap. The Lakhani Vardan Group has started production in Haridvar in 2005. The following report concerns the Lakhani Auto factory.
The hall is 130 feet long and 120 feet wide. Currently they use three lines (conveyor belts), one chiller machine, three – four different kinds of grinders, in total about 22 to 24 machines. various chemicals are used for raw materials to produce the layer, the mid and the sole – and to glue them together. The material comes from Lakhani’s main plant in Faridabad. As a first work-step the layer and the mid are roughened with the buffing machine and the sole is worked with a hand-grinder. The chemicals 5050 / 6316 RC, Hardener ARF, 948/24 B, P-300 are used to clean and roughly glue the different layers, which are then put on the conveyor belt. On the lines the three layer, mid and sole are put together and proceed to the heater, the press and the chiller. Around 50 workers are employed for this stage of production. The finished pieces are then put into size-frames and the outlines are marked. The soles then process to the side-grinding machine, the quality check and the packing station, where a pair of soles is put into a plastic bag. Around 15 to 20 workers perform this work-step. At the three lines workers manufacture between 1,400 and 1,700 pair of soles per day, the final side grinding machine has a capacity of 1,500 soles per day. The production costs for these soles are about 125 Rs per paid, the 5 Rs wage costs are included. Lakhani India Ltd. pays about 150 Rs per pair.
For a six-days week the workers receive a monthly wage of 3,632 Rs plus 300 Rs incentive bonus. Out of the 70 workers working in the plant no worker is employed as an operator, all are employed and paid as helpers, although actually they operate machines. The main problem for the workers is the fact that the chemicals stick to the hands and clothes of the line workers. The clothes are destroyed and workers develop allergies. The gases trouble lungs and eyes. The halls are filled with rubber dust, floating in the air like fog. The company issues no masks. If people complain they are threatened with dismissal, some workers who talked about these problems were forced to sign their ‘own’ notice letter. The wages tend to be paid delayed. Because of this workers have engaged in sudden stoppage of work several times.
The sole production has started this year in April. Before that Lakhani had produced auto parts in this plant, but the production has been shifted to Faridabad. Only 25 to 30 workers in the plant have worked there for more than six month, about 15 to 20 for four months and the rest for less time. Most workers are from Bijnour and Shahjahanpur. The workers are not issued the obligatory company documents (work contract, company ID) or ESI cards. Although half of the workforce are women, the management does not provide the obligatory facilities (separate restroom, toilets, health care, creche for children). The canteen is only called canteen, no food is provided, it is only a place to sit. There is a guest house provided for management.
Comments
Reports from textile workers in India in February 2011.
While automobile workers fight mainly within/against the ‘flow’ of a vast production system, garment workers fight with the ‘rushes’ of the market in a more mobile and less ‘mutually integrated’ industry – the form of struggle reflect these conditions.
While struggles in the automobile sector tend to have a higher degree of ‘coordination’, the structure of garment industry forces workers to ‘grasp the instantaneous chance of irruption’. The industrial relations are characterised by enormous pressure on global prices, sudden income of orders followed by slack period, dead-lines which require to make workers work 16 hours or more in order to be met. The big industry can rely on patriarchal family structures, small workshop industry and village systems to produce the necessary skilled tailors – the industry has little costs for training, but the workforce comes with it a certain professional pride. Major companies like Modelama try to undermine the bargaining position by ‘chain systems’ and ‘one-week-free-training’ offers…
Modelama Worker (GAP, Old Navy)
(105, Udyog Vihar Phase 1, Gurgaon)
We have started working yesterday, on 27th of November 2010 at 9 am. Some of the guys are still working now, 28th of November at 4 pm, they will go home at 8 pm… It is ‘urgent shipment’ time and the master said at about 1:30 am last night that ‘crores of Rupees could be lost’. Since three months, after the arrival of a ‘Madam’ [female manager?], the physical and mental torture has eased a bit, but it is still quite a lot. On 27th of November seven women workers were verbally abused nastily and they were kicked out from the factory. On the same day an ‘incharge’ beat a master and swore at a ‘piece leader’ and slapped him. The factory employs 500 female workers, they have to work on Sundays, too. The guys on piece rate work very fast, the company asks the same output from the workers on monthly wages. There is a chain system (several workers work on one piece of garment in division of labour) even for the piece rate workers. Instead of full piece rate (payment for one piece which is the same for all workers), they have part rate (people are paid different rates, e.g. for sewing a collar, a sleeves etc.), which makes it more difficult for workers to link up for higher rates. Management doesn’t count – and pay – all garments you have produced and they pay less than the previously fixed rate. Modelama offers ‘one week of free training’ to new workers every month, with the ‘possibility of later employment’.
Edigear International Worker (Adidas, Reebok, Puma)
(Plot 150 and 189, Sector 4 and Plot 235, Sector 6, IMT Manesar)
We manufacture garments for Adidas, Reebok and Puma. On plot 150 around 300 permanent and 650 workers hired through contractor tailor jackets, track suits and T-Shirts. We work 150 to 180 hours overtime per month. The pay slip shows only 50 hours. Between 22nd of November and 27th of November we worked three days from 9:30 am in the morning till next day 5 am. The same happens on plot 189. On plot 253 around 500 workers do leather work. They used to pay 50 Rs extra when you had to work till next morning 5 am, this has been reduced to 40 Rs. There is a ‘complain box’ near the toilets, a lot of people complained about the 10 Rs cut and put their complain flyer in the box, but nothing happened. The representatives of the buyers arrive once a month, then all three factories are nice and clean.
Kalamkari Worker
(383, Udyog Vihar Phase 2, Gurgaon)
If you arrive five minutes late, they send you back home unpaid. They cut money for ESI and PF from your wages, but even after years of employment you won’t get an ESI card. In the personnel department they always tell you: no time. I was ill and got a holiday application signed by the department manager – in the personnel department they threw the application away and said that there is only one and a half day holiday per month. When they hire you you have to sign 15 papers, but you they won’t give you any document as proof of employment. They say that shift times are from 9 am till 5:30 pm, but actually you work till 9 pm, often till 2 am.
Jyoti Apparels
(158, Udyog Vihar Phase 1)
In the sewing department workers work 120 to 150 hours overtime per month, in the finishing department 200 hours. Paid single rate. Only 25 out of 350 workers get ESI and PF. Currently there is a lack of tailors, so the bosses don’t bother us too much.
Ventage Workers
(Plot 5, Sector 7, IMT Manesar)
The twelve women workers doing thread-cutting get 4,000 to 4,300 Rs for a month of 9 to 10-hours days. The 90 male workers douing stitching work either by hand or by computer work 12-hours shifts. They get 4,800 Rs to 5,200 Rs. Wages are paid delayed, there is no ESI and no PF.
Mac Export Worker
(Plot 143, Udyog Vihar Phase I, Gurgaon)
The helpers are paid 3,600 to 3,800 Rs, no ESI or PF is given. Working-times are from 8 am, to 10 pm. The managers swear at workers, sometimes slap workers.
Chelsea Mills / GAP Worker
(Plot 360, Udyog Vihar Phase IV, Gurgaon)
Shift starts at 9 am and finishes at 9 pm, overtime is paid single rate. Workers get the minimum wage, but it is paid delayed. If you arrive half an hour late they cut 4 hours from your wage. Out of 450 workers only 100 get ESI and PF. GAP is the main buyer of this factory.
S and B Worker
(Plot 669, Udyog Vihar Phase V, Gurgaon)
There are 150 workers employed, out of which only 30 get ESI and PF. We work 70 to 80 hours overtime per month, one to two daily wages get embezzled from overtime.
Bharat Enterprises Worker
(Plot 189, Udyog Vihar Phase I, Gurgaon)
There are 60 permanent and 150 workers hired through contractors manufacturing leather jackets. The helpers are paid 3,300 to 3,500 Rs, the operators 4,000 Rs.
MIC Filter Worker
(Plot 88, Udyog Vihar Phase I, Gurgaon)
There are 500 workers employed in the factory, working 12 hours shifts. The security guards have not received their August and September wages (26th of October). They are employed through Asmat Security.
Eastern Medikit Worker
(Plot 195 – 205, Udyog Vihar Phase I, and Plot 292, Phase II, Gurgaon)
Wages for casual workers are delayed. Over-time payment is less than single rate, between 11 and 16 Rs an hour. September overtime has not been paid yet (26th of October 2010). Without bribe neither permanent nor casual workers get their PF money.
Comments
A report on the security industry and conditions for security workers in Gurgaon, India in February 2011.
There are tens of thousand security guards employed in Gurgaon. There is security technology and architecture, there is a system of supervision, but the system is fragile in its inner self.
The watching eye is tired, turning watchtowers and CCTV circuits into an eternal void. Those who are supposed to supervise and secure are too precarious to care.
“We are watch men. Our job is to watch the factory burn. It is not our job to douse the fire. Our job is to guard the ashes, once the factory has burnt down. If someone asks about the whereabouts of the company, we have to provide information: this is where the factory used to stand, it has gone to ashes. This is our job, nothing more. It is our job to guard the factory, not to save it. We don’t manage to save ourselves, how are we supposed to save the factory”
(Conversation with a security guard)
Balaji Security Worker
(Branch Office, Kapashera)
We work 12-hours shifts, no weekly day off. For 30 days of 12 hours shifts we get 5,000 Rs. They take 500 Rs from you even before they hire you. Then they cut 2,000 Rs from your first wage for the uniform. Even if you have stood upright during the 12-hour day-shift all the time, if they catch you sitting down during night-shift they cut 200 Rs from your wage. If the guard from the other shift is ill or off, you have to work 36-hours on stretch – they might give you 30 Rs extra for food then. No ESI, no PF. It feels bad to search the pockets of the factory workers when they leave the factory.
Scientific Management Services (SSS) Worker
(U-28, DLF Phase 3, Gurgaon)
For 30 days of 12-hours shift we are supposed to get 6,100 Rs, but only 5,200 Rs are paid. They first said that 650 Rs are cut for uniform and boots, but then they cut 100 Rs every month extra. They cut money for ESI and PF, but neither is given.
Massive Security Workers
(Branch Office, Manesar – Main Office Nehru Place)
Even if you have to work 36-hours on stretch they won’t give you extra money for food. For 30 days of 12 hours shift they pay 5,000 Rs.
Om Security Worker
(Satvari, Chattarpur, Delhi Office)
They pay 5,000 Rs for 30 days of 12 hours shifts and wages are delayed. No ESI, no PF.
Comments

Gurgaon workers newsletter issue 36, with news, reports and analysis from India's special exploitation zone.
Comments
There is no lack of triggers, there is no lack of social explosives…
Rising ‘graduate unemployment’, massive hike in food prices, increasing signs of capitalist decadence in the form of rapidly aggravating ‘inequality’ and its symbolisation in a rich new oligarchy with strong links to the political class (corruption)… if these were the basic ingredients of the popular uprisings in North Africa, we find the same social explosives here in India. Both regions also share similar rhythms of debt crisis, (IMF) credit regimes and popular discontent: 1974 (“Bihar Movement”), 1981 (IMF loan and re-structuring), 1991 (external debt crisis). The rhythm becomes global. Desperation and anger of the youth spreads from the ‘illegal’ vegetable markets of Tunis, to the Parisian banlieus, to the textile industrial suburbs of Mahalla… across this world of widening contradictions between what is and what could be. The Shahajanpur accident – see below – could have been a sad trigger, there are hundreds of triggers every day. If we had to name the two main social aspects distinguishing the current social situation in India from the conditions in Egypt or Tunisia we would come up with:
a) a still more dynamic tri-angle relation between temporary village fall-back, rural industry / seasonal labour and scattered attracting/ejecting industrial boom regions; the rural-urban-rural migration, the back-and-forth between short stays in the village and another round of job hunts still expresses and diffuses the vast amount of social unrest – see report of village visit in this issue of GurgaonWorkersNews; the fact that labour migration from North Africa to the Euro-zone has become more difficult, crisis and all, has contributed to the explosion;
b) a still more dynamic economic and political middlemen culture; this culture reaches from modern ‘democratic’ and legal mediation of industrial disputes, to frequent usage of paid thugs to quell workers’ discontent; the local state in form of the modern ‘village council’ combined with ‘old’ forms of caste dominance and micro-credit liquidity; the state in form of middlemen in each slum and ‘state run ration shops’ (subsidised food shops); a vast ‘entrepreneurial’ and ‘empowering’ NGO sector and liberal ‘civil society’ sphere in combination with mass bases of paramilitary forces and ‘fake encounter culture’; a multi-layered ‘contract system’ which enables many permanent factory workers to become ‘small contractors’ themselves, or turns ‘local peasantry’ into landlords for migrant workers; a state-defined ‘reservation/promotion’ for middle(wo)men of all castes and gender; in summary: the ‘individualisation’ of misery here in India, e.g. in the form of mass suicides of small peasants, has little to do with the ‘cultural heritage of fate-obeying Hinduism’, but a lot to do with the brutal internalisation of ‘liberal democratic individual freedom’ in an ‘upwardly/downwardly mobile’ modern market society, which leaves us isolated when facing the systemic crisis;
In the following we summarise the news on the Shahajanpur ‘accident’:
“On 1st of February 2011 – while riots rocked the Kasbah and downtown Cairo – around 150,000 young people arrived in Bareilly, near Shahajanpur in Uttar Pradesh, India. They came in order to apply for 416 vacancies at the Indo-Tibetan Border Police (ITBP). Facing the enormous mass of applicants the local administration called off the hiring procedure. The angry youth started smashing the place up, burnt cars, government and media buildings. Around six state-owned buses and several other vehicles were set on fire and several shops were damaged and looted by them. The agitating youths also pelted stones at AIR and Doordarshan offices (public media). They then tried to return home. “The Railway staff were taken by surprise when they found the station swarmed by thousands of young men, who looked very agitated,” a senior Railway official said on condition of anonymity from Bareilly. “We promptly got the Railway police into action, but the station was jam-packed with these young men who went about damaging Railway property while raising anti-ITBP slogans,” he said. “No sooner did the Himgiri Express roll into the station than a large group climbed over it, clutching on to all sides of the train, including the rooftop and the engine. There was no way the youth could have been prevented from crowding the train and no one realised that barely 60 km ahead they would fatally encounter a low overbridge,” the official added. Many young people died when the train hit the bridge. The accident triggered violent protests as angry youths torched the train and attacked the station.”
Facing the Uprising, Facing the Daily Accident – What to be done?
The insurrection is permanent – from Argentina to Egypt we see that it does not take much to chase away the police or management, to take the things we need (homes, food, items), to break out of prisons or to fraternise with soldiers, in short, it does not take much to overthrow a government, but what comes next? The uprising asks the question whether we will we continue to live and work in a way, which leaves us having to buy the products we produce, which separates us from bread and roses by price; in a way, which puts a price tag on our time and energy itself and forces us to sell it on the market, competing with others; in a way, which leaves it to the development of prices whether a ‘we are pushed into a job’ or whether a factory is closed; in a way, which – in the end – will force us to call for the ‘good politicians’ to do something about the ‘bad market’: the very same politicians we have just chased away because they are useless – confronted with the global crisis of a system…
It is ironic to see how the regime – be it in Greece, the UK or in Egypt – uses the ‘democratic appeal’ in order to contain social discontent. While in Egypt the uprising is publicly reduced to ‘strife for democracy’ and rulers and twitter rulers to be call for a ‘return to work and return to the ballot box’… in Greece, in the UK or in other ‘democratic’ states the anti-government protests against the austerity measures are told that they will have to let the ‘elected parliament do their work, in the spirit of the democratic process’ – hinting at the fact that otherwise there are other forms of rule waiting in the back rooms…
The uprising, the strike waves have to become the process of discovery of our social cooperation; a cooperation, which so far has been organised as the fragmented ensemble of the ‘capitalist social production process’. The discovery will be both, appropriation for immediate needs and material transformation of production itself. Each struggle will meet the limits of imposed capitalist division of labour: in form of company walls, sector boundaries, ‘institutionalised’ knowledge separation, ‘political’ division between rural and urban. Each struggle will cause its unexpected chain-reactions, will cause shortages and ruptures of social life beyond their ‘capitalist’ boundaries, as proof of its previously hidden social dimension. The struggles will raise the question of direct, instead of mediated cooperation in order to overcome shortages and to make plans for the new day – the economic and political social separation dissolves. The extension of struggles along these lines of social cooperation might take violent forms, but given the historic degree of socialisation of labour (intertwinement of ‘science’ and industry, of ‘administration’ and production’, of agriculture and the industrial complex/market), ‘separate power’ has turned into a mere obstacle which has to be pushed aside; it has lost its productive function and is not worth fighting over.
The managers of capital can only succeed in ‘legitimating their power’ as long as they are able to make ‘capital’ appear as the pre-condition of social cooperation, as long as they are able to separate the social experience of over-productive labour from the poverty of un-/underemployment. Obviously this separation does not take a pure form of working-class on one side, proletariat on the other. This separation appears in its various shades of development and underdevelopment, of high-tech and labour intensity, of regional deprivation and boom centres, of respectable workmen and lumpen, of hire and fire. This separation will appear in all imaginable ethnic colours. With the disappearance of the old buffer-classes, with the social death of peasantry and artisans in the global South, the demise of the self-employed educated middle-classes and petty bourgeoisie, capital has to face up to it’s living self. While being in it’s essence the violent coordinator of social labour – globalisation, international supply-chains etc. – in this crisis more than ever capital has to hide and segment the global character of social cooperation from the emerging global working class. In the attempt to segment and re-combinate capital becomes a burden to social cooperation. It gets in its own way.
Therefore the challenge for working-class communists is to discover and point-out this ‘general global character’ of labour in the concrete local disputes, to discover and point-out the ‘political separation’ of development and underdevelopment, the potential of abundance in the face of stark misery. That means to argue not from the abstract level of ‘class consciousness’, but from the perspective of the collective worker. The challenge for ‘communists’ is not separate from what workers’ themselves are forced to do: As we can see in front of our eyes, most current workers’ struggles have to find answers to their own global dimensions – not to proclaim their communist demands – but to simply avoid being defeated.
Comments
Impressions from a visit to Babripur Village, connected to the Delhi industrial belt by two generations of labour migration.
Some Aspects of Agricultural Investment in India II
There are lot of ‘village case studies’ being published, contributing to the debate on ‘class stratification’ and general changes of the old village structure. There is less debate – and less empirical work – on the question of how urban wage work impacts on village conditions and vice versa. Based on his research in Gujarat, Breman states that ‘the landless lack resources in order to make the jump into urban wage work’, but this might not be the general case.
A classical position states that the ‘landed’ worker, who comes to the urban industrial landscape and shares the same experience of work with his landless co-worker, will mentally and materially relate to the wage as ‘future capital’. He acts in the hope that the urban wages will help him to secure his social position back in the village – as a peasant or petty bourgeois engaging in trade or other business. He will be less inclined to ‘act as a worker’, he has more to lose, he doesn’t depend solely on ‘better wages’ in order to survive.
This position – although sound from a materialistic point of view – seems to lack the ‘historic dynamic element’. It reduces the experience of factory work to the relation of the worker towards his monthly payment and it does not take into account the changes within the village and the changing aspirations of ‘peasant-workers’ after the urban experience.
With similar questions we went to visit our friends village in the North-East of Uttar Pradesh, Babripur near Kadipur, about 80km from Sultanpur. The following is a rather impressionistic account between ganna harvest and buffalo grazing, less of an empirical study.
There are about 5,000 people living in Babripur. Around half of the village population own around 0.5 hectar, there are few ‘landless’. Electricity and tube wells arrived around 20 years ago, there are only three to four tractors in Babripur. Most peasants engage in multiple agricultural production: sugar cane, pulses, wheat, potatoes, mustard, vegetables. Although Delhi is quite far away – around 800 km or 14 hours by train – labour migration from Babripur area towards Delhi and Faridabad started in the mid-1960s and has been passed on to the next generation. We met two old workers who both left Babripur area in order to work in Faridabad factories in the 1970s. One worker belongs to the Brahmin caste, the other to the ‘Scheduled Caste’ (Dalit).
“My grandfather – besides working as an artisan – had an additional income as an exorcist. This had been a family tradition for some 150 years or so. As a kid I would gather people around him, sometimes up to 100, and he would perform his miracles. On his deathbed he told us that we should not continue this family tradition, that it was useless work. My father had too little land to work on, he got engaged in leather contract work. I myself managed to get a government job, I would go around and collect certain kinds of taxes. I then worked as a bus conductor. There were problems – a lot of wheeling and dealing connected to this types of jobs – so I decided to go to Faridabad to work. Initially I was rather na•ve, I thought that I would not have to stick to one job too long, because there seemed to be many jobs on offer. I had a dozen different jobs during the first years. Then Emergency came, they erased the slum settlement where I used to live. We built a new place a bit further out. At that time it was not too expensive to ‘but some unauthorised land’ and to build a small house. I got a permanent job and stuck with it till the company closed in the 1990s. I am retired now, I still live in Faridabad, we have two small houses here. My children had a good education, they now all work, one is an engineer, the other runs a shop”.
“My grandfather performed religious ceremonies, he was also the head of the village council of Babripur after 1947. He implemented the land reform, some land was redistributed. Before the land reform hardly any of the Scheduled Caste members had land, after the reform around 60 per cent had at least some land. My father did farming. He built the house we now live in. He had three sons, there were about eight hectares of land. I decided to leave the village and work in Faridabad. I started working in a plastic factory. In the late 1980s I returned. My daughter got married, both sons live in Delhi. What is our situation now? We have four buffalos to take care of, they give us milk and we can sell some. We have four hectares of land, some potato, some rice, some sugar cane and so on. Most of our food comes from the fields – what we don’t consume, we sell. The money income from agriculture is unstable. Take the example of a 0.5 hectare potato field. A good harvest will provide you with 10 to 12 tons of potatoes. You might manage two harvests a year, depending on weather. Production costs are around 20,000 Rs, this includes the labour we hire, the seeds, the fertilizer, the petrol for the tube well and so on. You can imagine the market rate for a kilo of potato? It will hardly be more than 3 Rs. So this is our basic situation: there is little surplus, my wife and me still work either around the house or taking care of the machinery and organise the field-work. The actual field-work is done by wage workers. We pay them 100 Rs a day. We used to pay them 50 Rs, but when NREGA came in, they demanded 100 Rs and we paid them. They obviously live in worse conditions here in the village, in smaller huts – and they depend on wage work, having little land themselves. Our situation as small peasants depends on previous wage work: some of the machinery has been bought be wage savings. If prices change – either of produce or of wages of the rural labourers – we might be forced to either reduce hired labour or to compensate the loss by our own wage work. Our condition is the suicidal condition of millions”.
The routes of labour migration have been inherited by the next generation. By chance, during a stroll through the fields, we met several ‘(ex-)workers’ from Gurgaon and Delhi.
“I am from the same (Brahmin) family. I worked seven-eight years as a metal polisher in an export company based in Okhla. I came back to the village two years ago, I think I came back for good. I am 28 years old now and I run this mobile phone shop.”
“I belong to the same caste. I left Babripur in 2000 and started working as a supervisor at FCI. I came back last year, I bought some extra-land. I don’t think I will go back to Gurgaon.”
“I normally work at Orient Craft in Gurgaon. I am here for a short visit, my family has little land in Babripur, I help with the harvest, although it does not amount to much. I also do some extra-work repairing machines for other people in the village.”
“I worked as a temporary worker at Honda HMSI in Manesar. The company interrupted my employment two months ago – they enforced a break of one, two months in order not to have to grant permanent employment. I will stay here for another month or so and then go back to my uncle in Manesar. I might try to get a job at Honda again.”
While the old ‘peasant’ comrade says that the ‘progressive’ industrial workers’ consciousness is wiped out as soon as workers get back to their village and re-enter the old village hierarchies, we think it is quite astonishing how direct the exchange between the village and the industrial zones have become. We can also see that ‘the land question’ clutches the new generation of workers from two sides and defines the more precarious status compared to their fore-mothers-and-fathers: it is not only more difficult to survive as a small scale peasant, it is also near to impossible to buy land in Delhi-Faridabad-Gurgaon area in order to ‘settle down’ in a family home. Wages are relatively lower and land prices have gone up.
A week after the return from Babripur we distributed Faridabad Majdoor Samachar in Manesar and asked workers whether they have heard of the 24 hours wildcat strike at Honda HMSI in December. Most workers haven’t heard of the incident, even those workers who work in the main supplier just across the road from Honda factory. It seems that proletarian organisation will not only have to be based – and can be based! – on the urban and rural exchange, but that it sometimes will have to help crossing the street…
Comments
We incarnate the global division of labour: private clinics in India cooperate with NHS hospitals in the UK in order to reduce ‘waiting-lists’, labs in Gurgaon process material for the medical complex in the US, patients fly in for final operation in Gurgaon due to lower local costs, organ trade is the scandalised warehouse of this boom sector. While the public focuses on price comparison for services of expert doctors, they often neglect the low-wage service regime, which provides the material foundation for the hospital complex. A general overview and two reports by workers from the Medical Industrial Complex.
Medical tourism and global outsourcing of medical services (laboratory services, telemedicine etc.) is one of the few remaining boom sectors. On the bases of new technologies, oversupply of skilled labour in the global south, relatively cheap transport costs and dismantling of ‘public health services’ in the global north, we can see the establishment of a ‘global body’, which is worked upon in an international division of labour. According to mainstream statistics medical tourism to India has witnessed an annual growth rate of 20 to 30 per cent during the last years. Treatment costs for, e.g. hip replacement or heart surgery are said to be 20 per cent of the costs compared to US standards. The medical tourism business in Asia has grown to 4 billion US Dollar. Not only patients from ‘the north’ but upper-class patience from the Gulf countries, Pakistan, Bangladesh etc. come to India for treatment. Gurgaon has become one of the centres for medical tourism in India. Direct international flights to the nearby Delhi airport, special medical visa service, a sophisticated local service sector are the necessary infrastructural back-bone for an assembly-line type of industry: in Apollo hospital in Delhi doctors performed 4,200 heart operations in 2010. Critical voices point out that a lot of the ‘experts’ have been trained by public sector institutions, but now provide treatment for upper-class patients in private hospitals. While the working class – particularly in rural areas – face a lack of medical support, the material and labour forces are concentrated in the profitable ‘upper-class’ medical complex.
One of the centres of local medical industrial complex is Medanta Medicity, according to company website “one of India’s largest multi-super specialty institutes located in Gurgaon”. Spread across 43 acres, the institute includes a research center, medical and nursing school, 45 operation theatres catering to over 20 specialties. We met a housekeeping worker employed at The Medicity.
Medanta / The Medicity Worker
(Jharsa Road, Rajiv Chowk)
The building has four underground floors, it is 16 floors high and has 1250 beds. The housekeeping workers, general duty assistants, security guards, drivers, barbers, washing workers are all hired through contractor. They say that housekeeping is done in three 8 hours shifts, but most housekeeping workers work 16 hours shifts, they receive 4,348 Rs per month, their overtime is paid at single rate. The general duty assistants and the security guards work two 12 hours shifts. There are about 500 general duty assistants – they are paid 7,500 Rs for 30 days of 12 hours shifts. There are two canteens – the workers hired through contractor have a hard time there. For 20 Rs you get hardly enough to fill your stomach. Even if you work 12 hours shifts you won’t get a free cup of tea. The doctors, technicians and nurses are hired directly by the company. The nurses are paid 14,000 Rs, the technicians 22,000 Rs and the junior doctors get 50,000 Rs. They work on two 6-hours day shifts and one 12 hour night-shift. One nurse cares for three patients during a shift. The patient fees for a single-room is 5,000 Rs a day, for a double-room 3,000 Rs.
Down the supply-chain works a friend, manufacturing medical equipment. We regularly report about conditions and struggles of his co-workers at Eastern Medikit, casual workers occupied their factory some years ago in order to enforce payment of outstanding wages.
Harsurya Healthcare Worker
(110 Udyog Vihar Phase 4)
Around 900 workers manufacture IV syringes. We are paid single rate for overtime. Due to the high production targets there are a lot of accidents with the syringes. We are supposed to quickly tape the wounds and go back to the machines. You can only go to the toilet twice during a 12 hours shift and you have to fill in a register for that. If you need longer than 5 minutes you have to face being told off. In the canteen there is not enough space for sitting down during meal time. It is near to impossible to finish your meal during the 30 minutes, and you are told off if you are 2 minutes late. They have installed cameras everywhere. Wages are paid late. In order to overcome these problems a union has been formed three month ago. Since then management swears less at workers, but the company casual workers have been degraded and are now hired through contractor. Before you sign your new work-contract with the contractor he forces you to sign your notice letter – for the future. The union president has spoken out against this, so on 11th of December he was suspended. Since then production has come down and the company started to kick out workers bit by bit. The company has also put up two guys with rifles at the factory gate.
Comments
In January 2011 automobile manufacturers in India announced both, record sales and plans to expand future capacities on one hand, and a drop in net profits on the other. We briefly summarise a report on Maruti Suzuki and add two reports by workers employed in the supply-chain.
Maruti Suzuki to raise output
ET, Jan 30 2011
The carmaker plans to raise annual manufacturing output to 1.4 million units starting April 2011. Maruti has been selling whatever it produces this financial year with the car market growing at 27 per cent due to strong economic fundamentals. Between April and December, Maruti Suzuki produced 924,103 units and sold 927,665 units, a growth of 31 per cent, according to Siam (Society of Indian Automobile Manufacturers). Meanwhile, the company reported an 18 per cent decline in net profit for the third quarter ended December 2010.
Shivam Autotech Worker
(58 Kilometer Stone, NH8, Binoula)
In 2007 workers at Shivam Autotech plant in Gurgaon occupied their factory and demanded ‘same conditions’ like their colleagues in nearby Binola. Following report is from Binola, four years later.
We manufacture parts for Hero Honda, Mico and Bosch. There are 750 workers hired through three different contractors, they work on 12 hours shifts. Their overtime is paid single rate. When the factory opened in September 1999 the majority of workers were permanent, their wages were very low, they were forced to work overtime, they were sworn at and insulted… in 2005 just when the Honda struggle took place management started religious offerings in the factory and increased wages by 900 Rs… the discontent remained and the permanent workers gave 1,100 Rs each in order to form an AITUC union. Workers went on five days strike after a colleague was mistreated, then AITUC and management came to a three-years agreement. Increase of monthly wages by 2,700 Rs in three instalments, an end to enforced overtime, no further verbal abuses, introduction of a group incentive scheme… and increased in the numbers of workers hired through contractor. Initially the permanent workers were satisfied, but this did not last for too long… Now half of the work-force is hired through contractor, their wages are between 4,348 and 5,600 Rs, whereas the permanents get 10,000 to 19,000 Rs. The permanent workers are afraid. Every year a union election, internal faction fights, the seven union leaders don’t work, or only pretend to do so. Every month the permanent workers give 20 Rs union dues. The management does not agree to let the union install an office inside the company and gives the union 2,000 Rs per month instead. The incentive scheme is a lollipop.
Neolight Worker
(396 Udyog Vihar Phase 3, Gurgaon)
Around 500 workers manufacture light-systems for vehicles on two 12-hours shifts. The day-shift workers are made to work 16 hours every second day, they then receive 30 Rs extra for food. On Sundays we also work 12 hours. We work 150 to 200 hours over-time per month.
Track Auto Components Worker
(Plot 21, Sector 7, IMT Manesar)
Demand for production is very high, therefore safety devices are removed from the power-presses – both of old machines and newly installed machines. There are a lot of accidents because of that. Fingers are cut off.
V.G. Precision Components Worker
(Plot 327, Sector 24, Faridabad)
We manufacture parts for Maruti Suzuki. Even the company casual workers don’t get ESI or PF. Due to a lot of accidents the workers hired through contractors get ESI, but no PF. Out of 70 workers 55 workers get around 3,000 to 4,000 Rs per month. We work 12 hours shifts, but overtime is paid single rate. Even after seven, eight years of employment your are still a casual worker. Due to iron casting and finishing work there is a lot of pollution in the plant.
G.L. Auto Worker
(14-b, Industrial Area, Faridabad)
The 25 female workers get 2,700 to 3,000 Rs per month, the 500 to 600 male workers get 3,000 to 3,500 Rs. No ESI, no PF. There are few permanent workers, and six or seven of them have become company-internal contractors. There are three external contractor4s. We work two 12.5 hours shifts, sometimes they force us to work longer. Overtime is paid single rate, Sundays they pay double. Wage are paid late. There are only three toilets for the male workers.
Marshal Group Worker
(Plot 390, Sector 24, Faridabad)
There is not even one permanent worker employed. There are 11 CNC operators, 20 dispatch and packing workers and 120 helpers hired through contractor. We manufacture parts for Escorts, Honda, TVS and for export. The helpers get 3,200 to 3,500 Rs. The dispatch guys get 3,500 Rs and the operators get 4,000 to 4,500 Rs. A lot of pollution, and the bosses swear a lot.
Nova Pack / Hella Worker
(Northern Complex, Mathura Road, Faridabad)
The helpers get 3,500 Rs, the operators get 4,300 to 4,400 Rs. We work on two 12 hours shifts. On Sundays we work 9 hours. We work for Hella Light.
Lakhani Rubber Worker
(Plot 262, Sector 24, Faridabad)
We produce hose pipes etc. for Maruti Suzuki. It’s rubber work, it’s dirty. When the Maruti representatives come, workers are given gloves and masks. Maruti stops production after 24th of December for the annual revision. Therefore there is little production, but normally we work on two 12 hours shifts. Since two months the company hires workers through contractors. These workers get single rate overtime payment, while the older workers get one and a half.
Castmaster Worker
(Plot 46, Sector 6, Faridabad)
There are 500 workers hired through three different contractors, manufacturing metal parts for the automobile industry. Overtime is paid at single rate. If they force you to work longer than 12 hours they give only 20 Rs extra for food. Wages are 2,700 – 3,200 – 3,700 Rs. The contractors who pay 3,700 Rs also cut money for ESI and PF from wages. Wages get embezzled, one or two day-wages from the overtime money. Production targets are very high. They won’t grant you a 5 min tea break during the 12 hours shift. Drinking water is bad, toilets are dirty.
Comments
We translated workers’ reports from two Marxist-Leninist journals Nagrik and Mazdoor Bigul, both reports dealing with current ‘company struggles’ in electronics and footwear manufacturing.
International Electro Devices Ltd. Worker (NOIDA): The Mutilating Factory and the Betrayal by CITU
From: Mazdoor Bigul, December 2010
http://sites.google.com/site/bigulakhbar/
The companies Samtel and International Electro Devices (IED) Ltd. – owned by Sudheer Kora and family – are situated in the Lalkuan area of NOIDA. Samtel manufactures computer monitors and other devices, IED Ltd. supplies Samtel with parts. In the name of these two companies, a large area of both government and non-government land has been obtained by the owners – after having delivered little favour to the people in the public administration. Samtel and IED sell parts, monitors and other electronic devices to leading international companies, but at the assembly lines the workers exist in situation of dreadful darkness. In the last eight years near about 300 workers have lost fingers to the machines in the IED Ltd. factory. Management removed obligatory safety sensors from machines in order to increase work speed. The production target given by management so high, that they cannot be achieved if safety measures are applied. They told workers that if they don’t meet the target, they can look for a different job. This forced machine operators to disregard safety measures themselves. During the last eight years hands of 300 workers have been mutilated in result – despite the fact that there is a union operating in the factory. A CITU union has been registered two years ago. CITU did not organise any resistance, so management is able to degrade mutilated workers from machine men to helpers or to sack them from the job completely. CITU did not even demand compensation for these workers. The opposite is true, the CITU leadership emphasises the fact that management – in some cases -would continue employing mutilated skilled workers as helpers, and portrays it as an act of charity. Around 1,200 workers have to work under these conditions at IED Ltd.. Some workers had started to organise themselves in meetings and raised various demands. During this struggle they established contact with CITU. CITU negotiated with management and ‘achieved’ to enforce some minor demands, whereas the important demands were ignored: same wage and bonus as workers at Samtel, reduction of production targets to speed which allows application of sensors, compensation for injured workers. These demands do not show up in the demand notice issued by CITU. Despite this workers started their struggle and even occupied the factory. In response management raised false accusation against six workers and spread the rumours that a legal case had been filed against them – which was not true. CITU used these rumours in order to convince workers to stop the strike and end the occupation. CITU said that due to the factory having five different gates, an occupation was not sustainable and that workers should stop the struggle until the ‘cases’ against the six workers would be withdrawn, and only then to start the fight again. Apart from those six workers, additional 40 workers had been kicked out by management during the agitation. Workers should regroup around a new demand notice which includes all important demands and continue the struggle and occupation.
Ongoing unrest in Sidkul
From : Nagrik, 1 – 15 January 2011
Contact: nagriknews@gmail.com
The Markson factory is situated on Plot 11 and 11e in Sector 6a in Haridvar Sidkul. On 21st of December 2010 around 200 workers – at Markson around 100 to 120 female workers are employed – went on strike and started slogans against the contractor and management at the factory gate. The main reason for the strike was the fact that November wages had not been paid. The Deepvali bonus had also not been paid and the PF contribution of the company was not correct.
There are three contractors operating in the factory. Only 15 to 20 workers are hired directly by the company. Company management told workers to complain to their respective contractors about wage delays, but workers put pressure on both, contractor and company management: “We work for the company and it is the supervisor and company management who drive us to work harder – so who should we ask to pay us if not those who constantly demand more work”?
The factory manufactures electronic devices: TV’s, DVD and LCD players. This type of manufacturing has to be seen as ‘permanent production’, in contrast to seasonal work, and according to law the company would not be allowed to use contractors for employment in the production department. On 23rd of December the strike was lifted and workers resumed work. Wages were not paid to all of them, but small groups of two to four workers received their wages. Management tries to break the unity of workers by, for example, threatening workers with withdrawing the company bus service.
Lakhani Worker
(Haridvar, Sidkul)
Wages are usually paid delayed at Lakhani Vardan Group. Apart from that the company does not provide appropriate means – masks, gloves, clothes – which would protect workers from the chemicals used at work. Like other companies Lakhani gave workers a bonus and sweets for Dipvali, but only 1,000 Rs bonus and 100 Rs worth of sweets, and the rest of the wages were paid delayed. When November 2010 wages were not paid by 13th of December, workers stopped working after the tea break at 3 pm and started asking the supervisor about the outstanding payment. The supervisor first tried to explain and re-conciliate , but when workers did not accept this he called the plant manager. As soon as the manager arrived he started shouting at workers: “Do your work or go and leave the factory”! During previous occasions only a few workers resisted the threatening behaviour and refused to go back to work, this time about half of the work-force refused to go back. The manager started to call workers singly, he threatened them and he expressed his sadness about the pitiful state of the company:
“We have to work, so do your work, otherwise the situation will remain like this.” “We did not call you to come to work here, you did come on your own accords”. “In other factories the contractors take their share of your wages, here you get your full wages, only a little late” “We can find a lot of other workers and you can find a different job, so there is no shortage neither on our nor on your side”.
The following day the manager continued to preach to the workers:
“If any of you has a problem he can meet us alone and we will find a solution for his problems. If you gather like this in a crowd and stop working, then you will find no worse person than me. If anyone dares to do so, we will have him beaten up, kick him out and make sure that he won’t find any other job in Sidkul. Go back to work, we don’t appreciate these agitations”. The following day, on 15th of December at 4:30 pm wages were paid, but the outstanding overtime money was not paid.
Comments
During the last months several ‘land scandals’ have entered the public stage in Gurgaon. The state industrial development agency HSIIDC is accused of having sold land dedicated for ‘public purposes’ to private firms, which then used the land for commercial purposes. The immediate reaction is to complain about the obvious rampant ‘corruption’ connected to the land deals. A deeper analysis would be necessary which would have to locate the ‘corruption’ within the formation and re-formation process of a ‘local ruling class’.
Obviously there are the local landed classes involved, who are supposed to sell their land to the state or private companies. The price of land determines whether they will make the jump from peasantry into ‘petty bourgeoisie’ and how high or low this jump will be. Given the vast amount of migrant labour exploited in Gurgaon industries, the local landed class is a necessary social back-bone of the ruling class. They have to be compensated for their loss of land and obtain middlemen functions either as labour contractors, landlords, local politicians, union leaders or other trading positions.
The price of land is of immediate importance for commercial traders of land and private developers like DLF. These companies have been not only important developers of (industrial) infrastructure, they also have been one main entry door of global financial streams into Gurgaon, which then re-diverted from real estate into other sectors. The multinational industrial managing class has similar interest in ‘cheap land’, but depends on ‘good relations’ with the local landed classes to a higher degree than the ‘real estate capital’. Recently the ‘industrial class’ started to complain about a ‘burocratisation’ within the Haryana state apparatus, in the form of increasing power monopoly of the HSIIDC and cases of double taxation.
‘Corruption’ in this sense has a ‘productive function’ – in capitalist terms – beyond the individual forms of embezzlement. It functions as ‘grease’ within the re-shifting of different sections of ruling class and re-distribution process of different incomes in form of land revenue, rent, profit, taxes. The larger picture of extended capitalist cycle shows that despite the initial importance of land prices the main ‘grease’ stems from the exploitation of the industrial working class. The following news snippets can give an idea of the various layers and interests – the true common interest ‘as representatives of capital’ will be revealed during times of social turmoil alone.
Land Scandal – 5th of February 2011
DLF plans to appeal in the Supreme Court against a Punjab & Haryana High Court order to demolish properties on a land owned by the country’s largest realtor in Gurgaon. In September 1995, the state government had sold 30 acres to East India Hotels that runs Oberoi group of hotels to develop a hospital and hotel management institute for the public. The hospitality firm sold the land to DLF. DLF converted the land into special economic zone and took necessary approvals from the central and state governments. The High Court has termed the transfer of land by the Haryana government to the private firms as illegal: “Facts alone are enough to establish the nexus of M/s DLF Ltd with the government to grab the property in question… subsequent facts of granting necessary approvals for setting up a SEZ etc. was an attempt to cover the malafide action of Haryana government.”
Land Grab in Rewari and Manesar
Finance Minister, Capt Ajay Singh Yadav, comes out strongly in defence of Rewari’s aggrieved farmers facing a threat of land acquisition. The farmers, in their memorandum, have mentioned that the HSIIDC has issued a notification for acquiring 500 acres in Dharuhera. He is learnt to have added that the industrial town at Bawal and Manesar are a stone’s throw from Dharuhera where plots can be given to boost industrialisation. “Therefore, I feel that acquiring more land around Dharuhera for the industrialists is of no point as, in this way, no agricultural land would be left for farmers and their livelihood. As of now, there is a saturation point of urbanisation and industrialisation in Bawal and Rewari blocks,” the letter says. HSIIDCs expansions plans are the talk of the town this year, on the list are several villages near the Manesar IMT. Development plans might soon be rolling out for the 1800 acres of land earmarked for large scale industrial and commercial setup by the government. The state is also supposed to make sure that the villagers, who own this chunk of land, get handsome compensation, at the going price of more than Rs 50 lakh per acre.
Farmers Protests Concerning Land Grab – 15th of February 2011
The Bhupinder Singh Hooda-led Congress government in Haryana is under attack from various quarters over its land acquisition policy, converting agricultural land into industrial or commercial property. The Opposition is trying to make the most of the situation. The INLD has already announced a state-wide agitation against the ‘pro-builder and anti-farmer’ stance of the government. Farmers of Pachgaon, Kasan, Mokalwas, Baaslambi, Kharkhari, Sehrawan, Kukrola, Pukharpur and Fazilwaas villages have already held two mahaypanchyats and blocked the Delhi-Jaipur National Highway-8 in protest against the government’s move to acquire their land. The protesters soon blocked the highway, refused to talk to the SDM and demanded that either the Divisional Commissioner or the Additional Deputy Commissioner (ADC) be sent to accept their memorandum. Meanwhile, an anti-riot squad of the police force was deployed at the blockade site as a preventive measure. Ultimately, Gurgaon ADC VS Hooda and SDM Satender Duhan went to the farmers’ leaders and accepted their memorandum.
Industrialists complain about HSDIIC
The industrialists of Gurgaon and Manesar claim that the new industrial policy of Haryana grants unprecedented powers to HSIIDC. According to them, besides getting away with a rather lopsided estate management policy, HSIIDC has also acquired chunky portions of industrial land all over the state. Industrial areas in Gurgaon, previously under HUDA or the department of industry, according to the 2011 policy, are to be duly handed over to the HSIIDC this year. But this transfer of jurisdiction is being contested by the industrialists of these areas unanimously. The Gurgaon Industrial Association announced that they are going to ask the Chief Minister to intervene and stop the transfer forthwith. The general concern of the industrialists is that a transfer to the HSIIDC ambit would entail double taxation.
Haryana sets up ‘Japanese Township’
Japanese investment constitutes more than 33 per cent of the total Foreign Direct Investment (FDI) received in the state so far: Suzuki, Honda, Canon, Yakult, Denso, Mitsubishi, Toyo, Daikin, Yokohama, Showa, Nippon, Kansai Paints, Asahi and Stanley. There are about 2,000 Japanese nationals working in such these companies. Some of them shuttle between Japan and India. Now, the Haryana government is planning to set up a Japanese township. The Japanese township would be set up near Madina village in Rohtak district, 60 km from New Delhi, along National Highway 10.
Comments
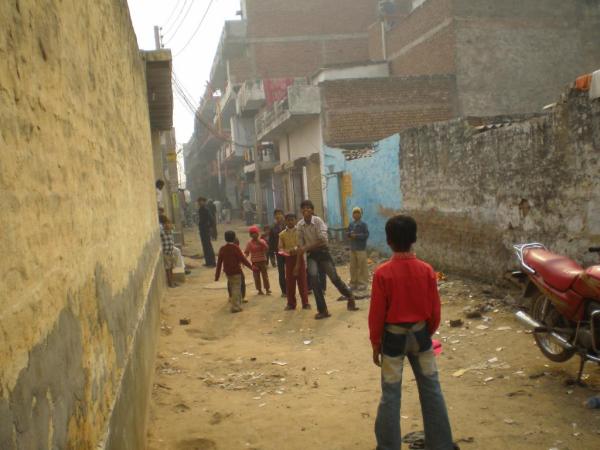
Gurgaon workers newsletter issue 38, with news, reports and analysis from India's special exploitation zone.
Comments
Short reports collected and distributed in Faridabad Majdoor Samachar in early 2011.
Gaurav International Worker
(198, Udyog Vihar Phase 1)
Management forces women workers to come to the factory at 6 am in the morning and makes them stay till 10 pm. There is a high work load – Management swears a lot at the women workers, they say:”Why do we pay double for overtime?!” – when actually only the first two hours are paid double. Male workers work from 9 am till 10:45 pm, and they often have to stay till 6 am next day.
Pearl Global Worker
(446, Udyog Vihar Phase 5)
Most of the 1,500 to 2,00 workers are hired through contractor. Work starts at 9 am and they make you work till 4 am next morning. Only two hours overtime are paid double. If there is less work, they kick you out. They cut ESI and PF money, but workers get only old ESI cards and no fund money when they leave the job.
Richa and Company
(193, Udyog Vihar Phase 1)
Every Saturday you have to work from 9 am till next day 6 am. Even if you have to work 21 hours on stretch they don’y pay extra for food. Only first two hours overtime at double rate.
RK Footwear Components
(529 and 549, Sector 37)
Only 25 out of 250 workers get ESI and PF, They manufacture soles and heels for the shoe industry. The 25 workers get 7,000 to 8,000 Rs, the rest get 3,600 to 4,000 Rs. Monthly 100 to 125 hours overtime paid single rate. management swears a lot, sometimes beats people.
Indian Hand Fab Worker
(92, Udyog Vihar Phase 1)
Helpers wages are 3,500 to 4,000 Rs. The skilled tailors work on piece rate. Daily working time is from 9:30 am till 9 pm, often till 1 am. Wages are delayed. Theb toilets are very dirty. The 30 to 35 senior workers and the supervisors are allowed to go outside, the rest of the workers have to use the dirty toilets inside.
Shivang Export Worker
(Plot 146, Udyog Vihar Phase 1, Gurgaon)
You normally work from 9 am till 11 pm, but they often make you work till next day 8 am. There is a fixed time when you have to arrive at the factory, but there is no fixed time when you can leave it. On Sundays they make you work till 2 am, too. We work 150 to 250 hours overtime, money gets embezzled, around 200 to 500 Rs each month. If you work from 9 am till 11 pm they give you 15 Rs extra for food. There is no canteen and they won’t let you go outside. They tell you that you can go and eat at home once you have finished work. If you have to work till 8 am, they give you 20 Rs extra and they let you leave the factory for an hour between 8 am and 9 am – but they cut this hour from your overtime. Even if you work 14 or 23 hour on stretch you won’t get a free cup of tea. There are more than 1,000 workers in the factory – but not a single one gets ESI or PF. The thread-cutting female workers get 3,800 to 4,000 Rs, the packing helpers get 4,200 to 4,300 Rs. The tailors get 170 to 175 Rs per 8-hours day. There are a lot of troubles to get drinking water. The toilets are dirty. The situation in the other factory of the company on plot 669 in Udyog Vihar Phase 5 is the same.
Enrich Agro Food Products Worker
(Plot 277, Udyog Vihar Phase 2, Gurgaon)
This is a bottling plant for Coca Cola. The 125 workers hired through two different contractors get 3,000 to 3,200 Rs. December to February there is less work to do, the rest of the year we work 12 to 14 hours a day.
Rolex Worker
(695 Udyog Vihar Phase 3, Gurgaon)
If you leave the job, you have major difficulties to get your outstanding wages. Sometimes they say that there is no money, sometimes they say that they have sent it somewhere, sometimes they tell you to come back another time…
Chelsea Mills Worker
(360 Udyog Vihar Phase 4, Gurgaon)
You work from 8 am till 10 pm, then from 1 am again till 6 am. They give you 20 Rs extra if they make you work full nights. here are 800 male and 200 female workers. The bosses swear and sometimes beat people.
Spark Worker
(166 Udyog Vihar Phase 1)
There are 400 workers hired through the contractor ‘MR Stitchwell’ in the factory. When you leave the job and go to the PF office they say that for the last four to five years no PF money has been paid into the account.
Marks Export Worker
(370 Udyog Vihar Phase 2)
The thread cutting workers get 3,500 Rs, the skilled tailors and checker get 4,864 Rs. The make you work from 9:30 am till 11 pm. We manufacture garments for Chicos. Whenever a representative of the buyer [client] turns up, around 50 to 60 out of the 500 workers are kept outside of the factory and are not paid for the dat.
RK Footwear Components
(787 Udyog Vihar Phase 5)
Normal working-times are from 8 am till 8 pm, but 15 to 20 days a month you work till 2 am – they pay you 20 Rs extra for food then. You also work on Sundays. The helpers are paid between 3,600 rs and 4,000 Rs, the operators between 4,000 and 4,500 Rs. Only 10 out of 50 workers get ESI and PF. We manufacture heels and soles for Lakhani (Faridabad), Amar Shoes (NOIDA), Liner (Agra), Liberty (Karnal), Goodladder (Chennai). There is verbal and physical mistreatment from management.
Casual Wear / GAP Worker
(263 Udyog Vihar Phase 4)
About 150 male and 50 female workers work from 9 am till 9 pm, often till 1 am. The company pays only 20 Rs extra for food. We manufacture garments for GAP.
EEL Worker
(401 and 510, Udyog Vihar Phase 3)
There are 40 permenent and 500 temporary workers, manufacturing machines for cement factories on 12-hours shifts. Overtime rate single. Around 300 temporary workers get 4,000 Rs per month. PF is cut from wages, but when you leave the job after three, four month of employment, you won’t get the fund money.
News from Faridabad
ESKO Die-Casting / Phillips Worker
(Ploy 37, Sector 27a, Faridabad)
Around 100 workers assemble Phillips halogen lighting on two 12-hours shifts. Sunday is a working day, too. After workers raised demand for higher wages, double rate for overtime as per law, minimum wages for the 65 workers hired through contractors, ESI and PF – management suspended one of the 35 permanent workers. The company has recently opened a third plant in sector 58.
Kunj Bihari Textiles Worker
(Plot 95, Sector 25, Faridabad)
Out of the 2,500 to 3,000 workers olnly 50 to 60 get ESI and PF. There are two `12-hours shifts. If you work every day, 12-hours a day, you’ll get 4,800 Rs per month. If the reliever does not turn up, they make you stay longer – even if the reliever does turn up they sometimes force you to work beyond your 12-hours. If they force you to work 36 hours they will only give you 25 Rs extra for food. If you work 12 hours they won’t give you a free cup of tea either. The drinking water is bad. There are only six toilets for 3,000 workers.
Colour Line Worker
(151, DLF Phase 1, Faridabad)
About 150 workers dye textiles on two 12 hours shifts. No weekly day off. For a 30-days month of 12-hours days the helpers get 4,500 Rs, the operators get 5,000 Rs. Wages are delayed. Only two or three workers get ESI or PF.
Alpia Paramounts Worker
(Plot 60, Sector 25, Faridabad)
There are 300 workers on two 12-hours shifts. We manufacture plastic parts for Whirlpool, Samsung, LG fridges. We also have to work on Sundays. Only 20 workers get ESI and PF. The helpers get 3,500 Rs. Drinking water is bad. The toilets are dirty.
City Textile Industries Worker
(18, DLF Phase 2, Faridabad)
Around 150 workers on two 12-hours shifts, dyeing textiles. The helpers get 2,960 Rs, the operators get 3,200 to 3,400 Rs. The 20 workers who get ESI and PF are forced to sign that they receive the minimum wage, actually they get the same wages as everyone else. The drains get blocked all the time, the factory overflows with chemical-water. If you have to stand in this water, you get ill. There is also fear of electric shocks.
STL Global Worker
(Plot 4, Sector 6, Faridabad)
Two 12-hours shifts of textile dyeing. helpers get 4,500 Rs, operators get 6,000 Rs. Wages are delayed. Only 12 out of 700 workers get ESI and PF.
Deepak Enterprises
(25/7 Industrial Area, Faridabad)
The helpers hired through contractor get 3,000 Rs, the operators get 4,000 Rs. No ESI, no PF. Sundays 5-hours shift, all other days 12-hours.
News from Manesar
Vatika India Next Worker
For their construction site close to Rampura on National Highway 8, Vatika Company has hired building workers through contractors. Around 500 women workers are employed to transport bricks and mortar. They are paid 110 to 130 Rs for an 8-hours day.
Kumar Printers Worker
(Plot 24 and 38, Sector 5, IMT Manesar)
Management has put up a notice inside the factory that for the support of the family of a company worker who has died after a work accident, a daily 12-hours wage will cut from each workers’ wage. The notice does not say how much money the company will pay to the deceased employee. In the meantime, on 30th of December 2010 a worker who had already worked 12-hours in the factory on plot 38 was told to work another 12-hours shift in the plant on plot 24. The worker refused, so management told the supervisor to dismiss the worker.
Crewbos Production Worker
(Plot 12, Sector 5, IMT Manesar)
Around 5,000 workers are employed, manufacturing leather bags and boots for Fossil and Next. They work from 9 am till midnight, often till 4 am next day. The 100 to 125 hours monthly overtime is paid at 33 Rs per hour. Since January 250 workers are send home at 8 pm. Their overtime is not paid. They have been set a production target for these 11 hours which would need 12 hours to achieve. For 26 days they receive 6,000 to 6,500 Rs. The rest of the workers have not been paid their January wages yet – it’s now the 25th of February. December overtime has not been paid either. In the company factory on plot 8 in sector 7 around 2,000 more workers manufacture leather belts and purses.
http://www.crewbos.com/factories.html
News from NOIDA
JPC Worker
(A-45, Sector 83, NOIDA)
Around 300 workers are employed on two 12-hours shifts, they dye textiles. There is no weekly day off. Only 50 workers get ESI and PF, these workers are paid 5,500 Rs for a 30-days month of 12-hours shifts. The rest get 4,500 Rs for the same working-time. management cuts 500 Rs for ESI and PF from their wages, but they don’t get neither ESI nor PF. Drinking water is bad. The toilets are dirty. The supervisors swear a lot.
[h4]News from Biwari[/h3]
Jaguar Worker
The factory is near Rico and Nilam Chowk. Around 2,700 workers are employed on two 12-hours shifts, they manufactur copper fittings. Overtime is paid at single rate – overtime is not shown on the pay slip. Helpers are paid 3,300 Rs and skilled workers 4,300 to 4,500 Rs.
http://www.indiamart.com/jaguar-international/
Comments
Below you can find an interview and translations relating to the history of workers’ struggles at the still existing Thomson Press in Faridabad, near Delhi.
Comments
ciao,
it is no.39 - we had problems with wordpress putting pages in funny orders, therefore the confusing numbering system. thanks loads for putting up the old newsletters!
AngryWorkersWorld
ciao,
it is no.39 - we had problems with wordpress putting pages in funny orders, therefore the confusing numbering system. thanks loads for putting up the old newsletters!
great, thanks for the clarification.
(I have renamed this so it matches the style of the others)
sorry, I am going to put them all up eventually but I became confused as some newsletters have already been put up, whilst articles from other newsletters have already been put up as stand alone articles and i'm not sure whether to duplicate.
I have also put up your fantastic WWW newsletters, http://libcom.org/library/workers-wild-west
A short interview with a union official of HMS in Faridabad. He arrived in Faridabad in 1973, worked as a printer at Thomson Press (1) and became the union president there. He covers the events at Nilam Chowk in October 1979 and the turmoil during Devi Lal take-over of Haryana government in the late 1980s early 1990s. Like the main local HMS union leader Sethi, he was invited by the international Trotzkyte movement to speak as an ‘independent’ workers’ leader at various international gatherings. We suggest to read his account together with the Faridabad Majdoor Samachar reports, in particular about the developments at East India Cotton, at Escorts and Thomson Press itself.
I arrived in Faridabad in April 1973 and started working as an apprentice at Thompsen Press India Ltd. Around 250 to 300 workers were employed, most of them permanent workers.
At the time I didn’t know much about trade unions, there was no union at Thomson. But in 1973 workers went on strike for higher wages at Escorts company, Faridabad’s main company, and the police attacked them badly. They arrested workers as soon as they could. It was not possible to hold a meeting in Faridabad, you had to go to Badarpur-Delhi border. At the time there was AITUC, BMS and INTUC union at Escorts, in each of the eight plants here in Faridabad there were different unions. In 1973 there was also a violent incident in front of the Goodyear factory, one worker was shot by the police. But I don’t know too much about this event.
Then came the Emergency 1975. Work-pressure in the factories increased and less bonus was paid. Outside the factories there was the issue of enforced sterilisation and demolitions of slums. AITUC was predominant in Faridabad at the time, AITUC is affiliated to the CP, which had supported the Emergency. Therefore there was silence in Faridabad during this period.
In 1977-78, after the lifting of the Emergency, CITU became more powerful, given that the CPM had opposed Emergency. The National Labour Organisation (NLO) also became stronger, but our leaders had to leave the NLO and formed the Haryana Labour Union (HLU) instead. They met with union leaders of seven, eight factories. At that time our comrade Mr. Sethi started his work as union leader at Escorts. He called various unions and asked: “Why do you work seperately, in this way the bosses won’t be effected and you won’t achieve anything”. He suggested a general union election and contacted workers in all eight plants. A year later secret elections were held at Escorts and he was elected union president in 1978.
After Emergency AITUC was replaced by BMS as the main union at East India Cotton Mill, one of the major textile companies in Faridabad at the time. The workers did not support the new union, they wanted elections, they supported the HLU. A struggle broke out around this issue, this was in 1979. The three HLU leaders got kicked out by East India management, workers opposed this. Unions in Faridabad reacted by forming a Sangarsh Samiti (Struggle Committee) and called for a huge rally, nearby Nilam Chowk.
All main union leaders came, even the AITUC ones. They announced to the government that if it would not give those workers their right to elect their union there would be a general strike on 17th of October. East India Cotton still refused negotiations, so the general strike went ahead and the whole of Faridabad’s industry came to a halt. The union committee had to go underground on the 16th of October in order to avoid being arrested, so there were hardly any union leaders around the next day.
On 17th of October masses of workers came from both directions towards Nilam Chowk, a huge mass of Escorts workers from one side, other from the other side. The police got caught in between. People started shouting slogans. One police officer started shooting and was subsequently killed by the masses. A huge contingent of special police then started firing and chasing people, the terror spread to all areas of Faridabad. A lot of people went hiding, active workers had to hide. The majority of workers went to work next day. During the following days the police continued to arrest individual workers, around 150 to 200 in total. They were charged with 202 or 207, with murder of the police officer or attempted murder. The government had imposed a 144 the day before the general strike.
At that time I was still working at Thomson Press and we were thinking about establishing a union there, we had set-up a committee already. At the time we had no famous leader, it was a small union. The management told my name to the police and ten days after the Nilam Chowk incident I was arrested. The workers at Thomson stopped work in response, for four hours. The management talked to them and promised them to get me out. They denied that they had anything to do with the arrest and accused us of telling lies. They said that they will pay for my court case, give me full facilities, “but please go back to work now”. Management and some of their men then came to the police station and spoke to me: “It was the police, not us, who got you here”.
After Nilam Chowk they also arrested a lot of local peasants who had come out in support of the workers. They had also suffered under Emergency. There was no jail, so we were first sent to Rohtak and then to Bhiwani. The workers at Thomson Press thought that if the general strike scares the management then we might get something out of it. That was there attitude towards the strike.
On 5th of December 1979 I was released from jail, on bail. The workers at Thomson welcomed me, the management joined them. The manager said: “Go, meet the boss. You can stay off work, outside the factory, and he will pay you”. I said that there is no need to meet the boss. We then tried to continue rallying in front of East India Cotton factory, but the police had barricaded the whole area off. They stopped people. It was not a lock-out, production was running, but they did not let the old workers go back inside, neither did they get compensation for redundancy.
At Thomson the union was established in 1980. When I was out in 1979 the workers had elected me as general secretary of the union. The management was not in favor, but they were not too aggressive. Things changed in 1981, when management became rather aggressive towards the union. Because we raised the question of payment for the casual workers, who were paid less than the permanents. The other point of conflict was a three and a half years agreement which had been forged with some “leaders” about one year previous. According to the agreement there was hardly any wage increase, only increase of the housing allowance. This agreement was still pending when I became union leader.
I opposed this agreement, so the management organised a different union group against me, an INTUC union. They called for a gate meeting in order to set-up this union. Local MLAs, ministers, they all came. We also went, we wanted to go to work, but we were stopped at the gate. As long as the meeting went on, we listened. Shift normally starts at 8 am, the meeting went till 9 am. After their gathering was over I called workers over and asked them to listen what I had to say. I asked them: “What need was there for a meeting? Why have you been stopped at the gate? All this is a conspiracy to weaken our union. Let’s go inside now and stop work when we are inside. Let’s demand from management that they should recognise our union and only if they do so, we go back to work”. The workers did this, they went inside and sat down. The police arrived. At that time the casual workers were not members of the union, but they were with the union. They were a minority at the time, hardly ten per cent of the workforce. The production was stopped for the whole day. The labour commissioner arrived. A meeting between the conflicting parties took place. They said that they would increase the basic wage by 30 Rs. So we went back to work. They also started paying minimum wages to the casual workers, which they had not done before.
The management then targeted three of our comrades, who had been active during the dispute. They laid a trap and then suspended them and finally kicked them out. At the time I was still inside. We assembled the workers, took the flag and supported the three suspended comrades. This went on for six months. Then the 13th of March 1981 came. Management sent some thugs in order to attack one of the suspended comrades at the factory gate. We thought that this was a provocation and that we should avoid a confrontation, but people pushed forward. We stopped working after the lunch break and people left the factory in order to assemble at the gate in support. There I was attacked by thugs, the beat me with clubs. Police arrived, I was taken to hospital, but a case was registered against me. They said that I started a fight, that I called for strike – there was no case filed against the thugs. A minister intervened in support of the management, while a high-rank police officer asked me whether I knew the thugs. I confirmed and told him who it was. They arrested them shortly after, but I was not taken back on duty.
Management set-up their INTUC union inside the factory. A few workers benefitted from the subsequent settlements and agreements between INTUC and management, but the number of workers hired through contractors and casual workers increased rapidly, from around 300 in 1981 to about 1,000 workers in 1987 – in 1987 there were around 500 permanents employed, by then a minority. In 1987 the Haryana government changed. The Devi Lal / Chautala (2) government replaced the Congress government. Given that we were opposed to the Congress, Devi Lal gave us some support, not much, but some. We called all workers together, after change of government, I was again attacked by thugs. It was actually those guys close to the INTUC leaders, they broke my nose. In reaction to this attack the Escorts workers laid down tools. Our union was the main union at Escorts and at about 70 to 80 other local companies , they shut down the whole of Faridabad in support for us at Thomson. The DC arrived and said that he will set-up elections, to decide whether it should be INTUC or HMS. We received 99 per cent of the votes. Then Chautala saw that unions can be a good support for political parties, so he set-up his own union, the Lok Majdoor Sangh (LMS). They first invited us to join them, when we refused, they started to contest us (1).
After 1990 re-structuring accelerated, now there are hardly 400 permanent workers left. This is the general trend – therefore the union movement has been seriously undermined.
(1)
http://www.thomsonpress.com/international-business.asp
(2)
http://en.wikipedia.org/wiki/Chaudhary_Devi_Lal
http://en.wikipedia.org/wiki/Om_Prakash_Chautala
Comments
(June 1989)
After both the General manager and the (INTUC) union leader attached to him got discharged in 1987, the Thomson Press workers gained some short relief – when recently management started to put pressure on workers again. The capitalist law says without any doubt that after 240 days of constant employment casual workers have to be made permanent – now the management has settled an agreement with the new (HMS) union that all those casual workers will be made permanent who have worked at Thomson for more than four years. After some time of pending this agreement was nullified again on 15th of May. There are still 100 casual workers – with over four years seniority – who wait to be made permanent, plus 65 to 70 casuals who should be made permanent according to law. Now Thomson Press says that there is not enough work and that either 200 workers leave voluntarily or the 1,700 workers, who are now employed on two shifts, are supposed to work on three shifts – or in more straightforward words: the management is eager to increase the work-load by 30 to 35 per cent. The current changes imposed by management correspond with this aim: reduction of last year’s bonus payment of 20 per cent to 10.37 per cent; stopping the process of making casual workers with four years seniority permanent; giving the sack to 40 workers after closing two departments; suspending two workers after minor incidents and threatening them with shift to recently relocated composing department in Okhla.
(August 1990)
Three years ago management withdrew the general manager. Management also replaced the very unpopular old (INTUC) union leader with a new one. Despite the fact that the new (HMS) leader openly receives 2,000 Rs monthly payment from management, the fact that the old leader got discharged gave some respite to workers. In exchange for his 2,000 Rs and other crumbs the new (HMS) leader supported management in “getting the company out of its troublesome condition” by cutting down annual company benefits: the annual three-four days company tour got cut, the annual picnic got cancelled, the annual ‘open-day’ and program at the factory, as well. Together with these measures the new (HMS) leader inscribed a work-load increase in the new collective agreement. After having signed the agreement, the union leadership called the workers during a side meeting to stop these measures – a proof of the leadership’s juggling performance. In this way the situation at Thomson Press has aggravated to an extend that some workers started to run back to the old (INTUC) union leader. These developments are part of the reason behind the current beatings and fights within Thomson Press.
But the main reason behind the internal fights is the management’s policy to put their support behind the back of both sides. Thomson Press management is also affected by the intensifying blows of capitalist crisis. Management states that it is difficult to obtain orders and that the company is in trouble due to fierce competition. After having increased the work-load and cut certain company benefits, management now says that either the lottery department is shifted to Okhla or 200 to 250 workers have to go – otherwise the company would get into economic trouble. Workers assume that management wants to get rid offf a total of 500 workers. Speculation increases with aggravating capitalist crisis – the lottery business is booming – but the current management’s schemes to steer the company out of the waters of crisis are little more than speculation themselves. In order to fortify their strategy, management now – after having divided up workers between the increasingly disgraced new union leader and the already disgraced old union leader – prepares their agreeing/favoured workers to offer sacrifice for the company.
(January 1991) (1)
In the August 1990 issue we stated the management policy of putting their hands behind the back of the two conflicting parties as the main reason for the current physical confrontations between groups of workers at Thomson Press. This evaluation was wrong. At that time we saw the events only related to Thomson Press itself. We did not take into account the links between management of Thomson Press, India Today, News Track and the influence of the local capitalist politics. This is why we were wrong then. The agitations of the 6th of December 1990 made this quite clear. Nevertheless, the workers at Thomson Press still try to understand these events on the limited bases of their own company grounds. Workers have been turned into pawns in the struggle between different capitalist leaders – 150 workers cause trouble for the Devi Lal / Chautala government, so 1,500 workers pose a threat to the Thomson Press management. The whole issue is of importance for the workers at Thomson Press, but other workers can also learn a fair share from these developments – let’s therefore consider the whole issue more thoroughly. In a capitalist democracy the big newspapers and publishers play an influential part – their influence even increased when, together with the elections in November 1989, the theatre play of local capitalist parliamentary politics turned into a full-on drama. Concerned about their image, political leaders try to make themselves ‘popular’, while the big publishing houses and daily newspapers use columns like ‘The Nation wants’, ‘The country speaks out’ or ‘India demands’ in order to dictate the political leaders their aims and wants. On this background, after having put a lot of effort into becoming part of the central political machinery, various big capitalist newspapers and publishers started attacking Devi Lal and Chautala, aiming to extend their influence within the political machinery. During election times these attacks became more fierce. Devi Lal / Chautala retaliated, e.g. by verbally abusing newspaper publishers in their speeches.
The owners of Thomson Press, India Today and Newstrack were at the forefront of attacks against Devi Lal / Chautala government. The attacks in India Today and through video in Newstrack were publicly debated issues. The Hindi and English version of India Today is printed by Thomson Press in Faridabad, Haryana. Devi Lal / Chautala are in control of the government apparatus in Haryana and, in the name of trade unionism, the LMS is their hooligan organisation. It was therefore easy for Devi Lal / Chautala to take steps against their opponents in Haryana. In July 1990 the struggle between Devi Lal and the publishers emerged and expressed itself through the violent confrontations between groups of workers at Thomson Press.
In 1987 Thomson management replaced the old general manager and the old union leader attached to him. The HMS leader took his position. After his take-over workers felt some relieve and did not object to the HMS leader openly receiving a monthly payment of 2,000 Rs from management. Discontent grew after the union leader helped management to cut three lakh Rs for annual company-provided conviniences and to increase work-load. Their discontent came together with the start of Devi Lal’s intervention at Thomson Press through his union LMS and the old union leader. Despite their discontent with the HMS leader, the majority of workers refrained from re-grouping around the re-emerging old leader. In July 1990 the series of violent clashes started. Through the middlemen of HMS and LMS the struggle between Devi Lal and the publishers has turned into a struggle between workers.
The struggle was still in full swing when Devi Lal, after having been pushed out of the centre of power in August, re-entered the central power in November. Their efforts to obtain control over the publishers intensified. As part of this chain of events the LMS put up their flag at Thomson Press on 6th of December 1990. The stir caused by Chautala and his men cause trouble in the management departments of companies in Faridabad. Escort management fears that after having done so at Thomson Press, Chautala could post the LMS flag at Escorts, too – a fiery former Escorts leader, who had been kicked out of the Ford plant (part of Escorts), is with Chautala. Here Mr. Sethi, the main HMS leader in Faridabad also plays his role. As president of the Escorts workers union he openly supported the Nanda management in the struggle with Swaraj Paul over Escorts take-over in 1983. He also helped enforcing increased work-loads. Having been a follower of Devi Lal this main HMS leader has recently left him and started to support the Janata Dal. In this way the front against Devi Lal / Chautala has been fortified behind the leadership of Thomson Press management. The Faridabad Industries Association has expressed its support of the Thomson Press management against Devi Lal in front of the SP – DC. On 6th of December Escorts management ordered ‘a strike’ for the first shift in all Escorts plants against the setting up of the LMS flag at the Thomson Press gate. On the background of all these facts it seems that this ‘strike’ happened after a signal of the SP – DC, and on the very same 6th of December at 2pm the HMS leaders uprooted the LMS flag from the Thomson Press gate. The police just watched. In order to demonstrate their loyality towards Chautala and Devi Lal the SP – DC removed the HMS flag again later at night of the 6th of December. The capitalist factions opposed to Chautala and Devi Lal took further steps. The HMS leaders staged a gate meeting at Thomson Press assembling central leaders of the Janata Dal. All this resulted in Devi Lal and Chautala withdrawing slightly from the attack.
Lock-Out at Thomson Press
(April 1991)
After having instigated clashes within the factory on 21st of March, management has imposed a lock-out under the name of ‘suspension of production’. The lock-out continued at least till the 4th of April, the time we received our latest news. But this time neither the big newspapers issued big headlines about it, nor did the big party leaders arrived at the gate in order to deliver big speeches, nor did the management association raise their voice, nor did any middlemen come to agitate. This time the atmosphere is absolutely different from the one in december 1990, when the struggle between Chautala / Devi Lal and the publishers were in full swing. It seems that this time the issue is between management and workers alone.
(May 1991)
Thomson Press in Faridabad, employing 1,700 workers, belongs to the most important printing presses of India. Since 21st of March a lock-out continues, labelled as ‘suspension of production’. The wages for the first 21 days of March had not been paid by beginning of May. It seems that management’s plan consists in imposing their conditions on starving workers. And the complete silence by all those capitalist elements, which in December 1990 stirred up a huge noise around the conflicts at Thomson Press, plays in the hand of management plans. To consider this issue in more depth might also be useful for other workers.
Currently thirty big printing presses in India are declared as ‘sick units’. Thomson Press is one of them, but up to this point has been able to hide their crisis behind the ‘booming condition’ of India Today. According to the opinion of some experts working in the printing industry the main reason for the ‘sickness’ of Thomson Press is located in the confusion within management. The printing of lottery tickets and other security relevant documents required investment of large sums in machinery, but Thomson Press seems to have difficulties to establish themselves in the market, both in terms of quality and price. The Thomson Press policy is to employ highly qualified workers at high-tech machinery, but to pay them very little. When economic trouble started at Thomson Press around six, seven years ago the owners sacked some low-skilled managers and instead put high-degreed managers in charge of leading the business. These managers got involved in large-scale irregularities and in order to cover them up they declared that Thomson’s ailment was due to superfluous work-force. The current events are part of their plan to enforce large-scale retrenchments. Recently 50 workers were dismissed under allegations that they had been involved in fights. It is obvious that the main ‘sickness’ is the capitalist system in itself, where the main daily work of the representatives of capital is to play poker with workers income, subsistence and life. Let us have a look at the events of the 21st of March and the subsequent developments. It looks like the event of the 21st of March has been result of an instigated conflict in the factory. And given that the outcome of the fight plays in the higher management, it seems that the instigation had its origin in Thomson management itself. At about 4:30 pm, after the fight, two shifts of total 1,500 workers were inside the factory. One Escorts union leader, who is attached to HMS, and the Thomson Press union leader told the workers that management will lock-up the factory and that all workers should come to the union office at 10 am the next day for a meeting. On the 22nd of March the union leadership said that on the previous night management had started to remove material from the factory and that therefor workers should encircle the factory in order to prevent management from taking away stuff. Between 21st of March and the beginning of May there had been no demonstrations/processions or public gathering about this matter. These events express the non-understanding of the Thomson workers and the collusion of management and middlemen.
(June 1991)
The main HMS leader in Faridabad, who had helped management to enforce their lock-out on 21st of March and had then given full support to maintain the lock-out for 70 days, now claims on a printed leaflet that the “Thomson Press workers are not ready to fight”. Workers should know the truth in order to be able to learn from the painful experience of the Thomson Press workers and to escape the clasp of the management-middlemen alliance. Here, as well, management keeps Dal Fry-type of gangs; here, as well, in the name of INTUC-AITUC-CITU-HMS-BMS-LMS middlemen practice every day to enforce management policies. Again and again workers in Faridabad reject these shopkeepers of various colored flags, but given the lack of alternatives, workers get caught in the tread-mill of choosing ‘the lesser of two evil’. In order to prevent the return of the old infamous LMS leader, even Thomson Press workers who are dissatisfied with the HMS rally around them. During the battle between Thomson Press management and Chautala the HMS leaders made use of the workers to take sides of management, and afterwards, when they helped to fulfill management’s plan of attacking workers. On 21st of March the HMS leaders helped to get the assembled two shifts of workers out of the factory, so that management was able to implement their lock-out. Following the example of CITU at Gedore, which physically attacked workers and made 1,500 workers sign their resignation, HMS established their role at Thomson Press during the lock-out. Between the beginning of the lock-out on 21st of March and the re-opening of the factory on 31st of May the HMS leaders did not organise even one protest march, not even one public gathering. It seems too remote to even think about stopping work at Escorts in solidarity or to take other measures of struggle. After two months of lock-out around 80 per cent of the Thomson Press workers have returned home to their villages: to sit and sit in front of the factory doing nothing had caused too much trouble for them. And then the HMS leaders came to ‘an agreement’ with Thomson management. The ‘agreement’ was so bad that the remaining workers openly opposed it. This discontent was then covered with the veil of democracy by making even less than the remaining twenty per cent of the work-force take part in a secret ballot – in order for the main middleman to be able to shout about that the Thomson Press workers are not willing to fight.
(1)
Chautala’s men attack Press workers again
The Telegraph, 21-01-1991
Chautala’s men attack Press workers again
Faridabad, Jan. 22: After a brief lull, violence erupted once again at the Thompson Press here when five employees owing allegiance to the Chautala-backed Lok Mazdoor Sangh (LMS) alongwith two outsiders fired at point blank range upon the vicepresident of the elected Hind Mazdoor Sabha (HMS), Mr Ashok Kumar, yesterday morning. Mr Kumar escaped by running into the factory premises.
The LMS, which has been creating trouble at a number of factories in the industrial township here in order to establish itself as the recognised union without facing an election, has since the middle of last year injured 22 employees of the Thompson Press in various attacks. No arrests have been made against the FIRs registered at the police stations by the HMS. The police have consistently turned a blind eye to these incidents of violence. In this case also, the HMS has registered an FIR naming some of the alleged attackers but no action has been taken so far.
The HMS union, which was being strongly backed by the management of the Thompson Press so far, is now alleging that the management too is trying to shield the culprits in order to weaken their elected union. The Thompson Press management had put up a notice in the factory earlier this month saying that any employee indulging in violence on or outside the premises will be suspended. Citing this, the HMS president, Mr R.D. Yadav, has been demanding suspension of the five employees who indulged in yesterday’s attack.
A senior manager of the Thompson Press admitted putting up the notice but he did not want to implement the warning because, in that case, the HMS employees, who had attacked LMS men on December 29, will also have to be suspended. Requesting anonymity, the manager said the HMS was free to make any allegations it liked.
However, the fact that the Thompson Press management had changed its tune was evident as it had not admitted that the HMS men had beaten the LMS boys on December 29 till now. In fact, they had been saying just the contrary and blaming the LMS men for the attack.
The manager also said that whether it was the LMS or the HMS, they were both harmful to the Thompson Press as the continuing violence had affected their work badly. “The HMS employees resorted to work stoppage for one hour each on January 15 and 17 and for five hours on January 20 when LMS men, who had earlier incited violence, reported for duty.”
The continuing violence at the Thompson Press by the LMS so far was alleged to have been inspired by the Janata Dal (S) secretary, Mr Om Prakash Chautala, who was said to be settling scores for exposing the violence during the Mehem byelection in the India Today magazine which is printed here. But neither the management nor the HMS union has made any mention of Mr Chautala in this round of violence.
* Faridabad Mazdoor Samachar: January 1989 to February 1997
Articles covering re-structuring process and struggles in jute mill, powerloom department and table-printing department of Faridabad’s major company.
East India Cotton
FMS
(January 1989)
Nowadays Chhotelal cycles a rickshaw. He had been hired at the Jute Mill of East India Cotton Company in 1974. In 1983 the mill was suddenly closed. Since then Chhotelal stays in Faridabad in the hope that he will get his outstanding wages, his PF money and seniority bonus. In order to survive he cycles rickshaw in the meantime. Five years have passed, but Chhotelal hasn’t seen any money yet. Chhotelal is one of 900 workers, out of which 200 to 300 are still in Faridabad – waiting like him. The rest could not make ends meet, they have disappeared. There are many factories like the Jute Mill in Faridabad, closed factories. There are thousand workers like Chhotelal who wait for outstanding wages, which are due to them according to capitalist law.
Jute Mill, Powerloom, Dabar, Ajanta are the names given to the different departments of Eastern India Cotton company. Apart from the jute mill, the rest still exists within Eastern India Cotton. When the dismissed jute mill workers asked for their money the management refused to have anything to do with the workers. They said that the workers belong to Fibre Processors Limited. Whenever necessary the Eastern India management creates new companies within the company. This happens in many other factories in Faridabad. When workers – hidden behind the many company names within the factory premises – want to file a case against management, their lawyer will say that the management actually belongs to a different company.
In September 1983 the jute mill management laid off workers for a months – they said that this was due to lack of raw materials. At this point the company owed workers two months of outstanding wages. Workers were given 200 Rs and told that they should go back home until the necessary raw material arrives. By October no jute was to be seen. Eastern India management closed the factory and only left their security guards sitting at the gates. Through some middle-men workers filed a case in 1983, but nothing came out of it. In the meantime banks also filed a case in order to get back their money and in 1986 the jute mill machines were auctioned. When machines were about to be retrieved from the factory, workers became agitated. New middle-men entered the stage. The new middle-men took 50 to 100 Rs from each mill worker still hanging out in Faridabad and they filed a case. At this point the machines had not been taken from the factory yet and the middlemen delivered endless and promising speeches. After the machines were taken from the factory in December 1988, the middlemen would not be seen at the gates of East India jute mill anymore. Till today the 900 workers of the jute mill haven’t received their final pay.
Kanpur – Textile Workers blockade railtracks
FMS
(March 1989)
The developments at East India in Faridabad cannot be seen isolated from the wider development of textile industry in India. Below you can find a short article relating to the struggle of textile workers in Kanpur, which took place at the same time.
On 22nd of February around 35,000 textile workers blocked the main railtracks in Kanpur. Every day, after end of their shift, around 10,000 workers met and blocked the tracks. Only once the other shift had arrived at the tracks, the workers would get up and leave. Only after the government accepted their demands, the workers gave the tracks free on 27th of February. For five days the workers did not let any train pass through Kanpur. The government had to cancel 100 trains every day. Please read the article published in Indian Express on 27th of February:
“The railtrack-blockade movement of the textile workers is exceptional in many ways. The workers have become leaders themselves, and the old trade union leaders are left standing aside.”
We can learn some valuable lessons from the marvellous movement of the Kanpur workers. We will talk about some aspects here and hope that we will be able to provide more material in the next issue. The Kanpur textile workers have clearly demonstrated that the whole capitalist machinery is nothing but a thing and that during struggle workers can harm this machinery in sensitive and important spots. The Ministry of Railroads has announced in thir propaganda, that the struggle of the Kanpur textile workers is between the workers and the management of the textile mills, and that the workers should not draw the railways into this conflict. The workers refused this capitalist nonsense-talk and as a result, they won. Police, army, court, parliament, village council: this whole machinery is the workers’ enemy.
The Kanpur workers have chosen the right time to start their struggle. On 6th of December 1977 the Janata Partty government sent police into the Swadeshi Cotton Mills in Kanpur, where subsequently more than 150 workers were killed in a police firing. The Janata Party had just got to power and thousands of workers did not create to much commotion around these deads. This time the government did not put into action their action plan to evict the workers from the tracks. The ruling Congress Party has no problem with spilling workers’ blood, but it is election year and in the vote-games the party might have to pay a high price for a bloodbath. Instead of applauding to the election circus, the workers should accelerate the struggle for their demands.
East India Cotton
FMS
(April 1989)
In order to suppress the 1979 strike, the East India management mobilised the infamous Dal Fry goons [a union section]. Even after the open mobilisation of goons became unnecessary the management continued to make use of them. The DC tried several times to explain to the management that their behaviour was rather unintelligent. Seeing that the anger amongst the provoked workers increased and re-calculating the expenses for the goons, the management finally understood what the DC had try to explain. Suddenly, on 28th of February, the management announced union election for the 4th of March. The agitation among workers was considerable. Although they knew that the elections will not change anything, they got tied up in the hope that something will change. The Dal Fry goons and some others ‘got elected’.
East India Cotton
FMS
(July 1989)
On 8th of June the workers at East India Cotton achieved their first victory over the alliance of management and goons in ten years. This victory happened after a sad incident.
At East India, particularly in the printing and processing department, the capitalist health and safety rules are ignored to such an extend that, if the system was not as rotten as it is and the makers of the rules did not break their own creation, the company would have to be closed for security reasons. But it is the worker, who dies in accidents, while management can claim some money from insurances for ‘damage’. Therefore the company keeps on running – after putting some money into this or that official’s pocket.
On the 8th of June at 1 am a worker died in an accident. The corpse was sent to hospital, where the doctors announced death and immediately sent the corpse on to the mortuary. So far this would have been a common event at East India. It seems that the Dal Fry goons tried to get 5,000 to 10,000 Rs out of the worker’s death. Instead to the mortuary the corpse arrived in the factory at 4 am. All workers assembled around the dead worker. The workers of the 6:30 am early shift joined them. The news spread and the workers of the powerloom and dabar department also arrived, so did the next 8 am shift – in the end about 3,000 to 4,000 workers gathered. The Dal Fry goons and people of minor importance staged a drama of negotiations with management. Up to this point the game of the Dal Fry goons seemed to go according to plan, the workers were a mass, but only a mass. Then a worker from the powerloom department arrived and gave the silent mass a voice. The speech of this worker spoilt the game for the Dal Fry goons. Thousands of worker raised the demand of 1 lakh Rs compensation for the family of the dead worker. The district president of the LMS, who is also the legal advisor of the Dal Fry-union, tried to rescue things for the Dal Fry. The workers gave him a good beating. At this point the 100 to 150 Dal Fry goons, who had been well fed over years, also lost their good senses. A leader among them threatened the powerloom worker when police was already about to arrive – the angry response of thousands of workers shook both management and the arriving police. The things had gone out of hand of the Dal Fry and their ally from the personnel management – so the main company management took over. As soon as the management accepted to pay the due compensation to the relatives of the dead workers, apart from 100 – 150 individuals, all workers left the factory together. The relatives haven’t received any money yet.
East India Cotton
FMS
(September 1989)
On 12th of August the union leaders hold a gate meeting. At the meeting workers complained about the fact that workers were laid off, while leaders were paid the full 30 days without having worked. The leaders were stunned at these signs of workers’ resistance against the leader-management alliance. On 13th of August a worker who had raised his voice during the gate meeting was refused entry to the factory. It is the rule at East India Cotton that workers who are refused entry are not given the obligatory charge sheet or any other written reason for the refusal. The capitalist rules are broken by the representatives of capital themselves. Knowing that East India Cotton normally undertakes steps against those workers who oppose the union leaders, the powerloom workers had been expecting the move. Up to this point the steps taken by management had frightened the workers, this time they organised a counter-move. In protest against their work-mate having been kicked out, the night-shift of the power-loom department refused to leave and the early shift did not start working. Within an hour management and leaders started to run around. No one wanted to be responsible for the decision to refuse the worker entry, everyone said that the worker should start working and that everything will be fine. After the reassurances by management and leaders the workers started working after one and a half hour strike, and the night-shift said that in case the worker is not taken back as promised, they would undertake steps during the next shift. The worker was taken back on the 13th, during morning shift.
The power-loom workers learned quite a lot from this incident. Having examined the situation, they did not engage in an ‘all out’-struggle. The workers did not say: “Take the worker back on, then we will work”. The workers have given the management both, a blow and time to think about the damaging consequences. And the workers were successful.
In general workers tend to engage in an ‘all out’-struggle even when it concerns small daily conflicts. It has turned into an ideology that, disregarding the impact of the blow, the struggle has to be advanced to the outmost degree. As long as the factory was owned by an individual person, who had invested their private money, this way of struggle had usually increased the strength of the workers. The greater the impact of their attack, the higher the possibility that workers would win the struggle. A long strike used to be able to force a capitalist to his knees. But over time important changes have taken place concerning the ownership of capital. Nowadays individual persons or families do not tend to invest to much of their private money into a single factory. This is obvious when looking at state-owned factories, but the relation is not much different in the private sector. Today, workers face a management, instead of a boss. Management are representatives of capital and ministers-DC-SP-judges -generals are their colleagues. Given that management has invested only little money themselves, a long strike does not impact on their individual condition much. Therefore, an ‘all-out’-struggle in a single factory tends to first of all harm the workers. At the printing and processing plant of East India Cotton, as well, a worker was refused entry due to having opposed the leaders. There, as well, workers were rather angry, but this anger was vented by merely engaging in verbal cannonades. The workers did not undertake any steps for their work-mate. This worker is still struggling to get his job back.
In the dabar plant, East India management has removed 400 permanent workers and hired worker through contractors. On the first working day of the workers hired through contractors, the management made sure that police was around. The fact that the workers did not raise their voice against the shift from permanent to contract work, reveals the weakness of the workers.
Workers in Faridabad undertake some steps during the drama of capitalist elections
FMS
(December 1989)
During the times of election the whole capitalist regime spreads their illusionary net in order to entangle workers. But it seems that the workers in Faridabad have learnt their bit during the last years. This has become obvious during the current elections in various forms.
Firstly, the fact that AITUC-CITU-HMS-LMS-BMS unions call workers to support the candidate of the Janata Dal does not seem to have much of an impact on the workers. This might be because the current Congress candidate was the chief minister of the Haryana Janata Party government in 1979 and the current Janata Dal candidate was a minister in his cabinet at the time – a time when in October 1979 the police firing on workers in Faridabad took place and killed many. Many workers remember this. The unions fail in covering up the current regime of hooliganism and looting of the Janata Dal. More important than the disillusion towards the elections are the steps, which workers currently take in their own interest.
The steps undertaken by East India Cotton workers for the 800 Rs rate are worth mentioning. During his election campaign the chief minister of the Janata Dal had announced in April that the minimum wage in Haryana will be 800 Rs. The Janata Dal and their big-mouthed chief minister spread this promise everywhere, but nowhere in Haryana it has been turned into reality. After six months the Haryana government hasn’t even published the new wage in its newsletter. AITUC-CITU-HMS-BMS-LMS-Bank Employees Federation praised the chief minister Devilal on 13th of June for his wage announcement. The announcement of the new wage has been published in the government newspaper’s in due time before the parliamentary elections, but there wasn’t any factory in Haryana, where the new wage would have been paid on payday in November. At this time the union of the Janata Dal LMS was the leading union at East India Cotton. At the gate meeting on 3rd of November the Haryana president of the LMS beat the drum against the current Congress candidate and his involvement in the police massacre of 1979. One of the reasons for the 1979 firing was – apart from the quelling of general discontent – the long strike of workers at East India Cotton. In the period and in the shadow of the 1979 strike the East India management implemented their automation scheme and made 3,000 workers redundant. The LMS president whole-heartedly reassured the workers about the 800 Rs rate and in return asked the workers to vote for the Janata Dal.
But on 7th of November management paid the old rate. In response the 4,000 East India workers of the powerloom and Ajanta department displayed great unity and refused to take the old rate wages. The workers demanded the new 800 Rs rate. Seeing the unity of the workers, the LMS leaders became confused. Given that it was election period the whole situation was rather tricky, therefore East India management hesitated to make use of its goons. Shortly before the East India workers had given the LMS regional president a beating while the Dal Fry goons stood and stared. Seeing that the election harvest might get spoilt, the LMS Haryana president was given the role to entice the workers. On 8th of November this leader held another gate meeting. During this gate meeting the leader reassured the workers that before election the new rate would be paid, and he tried to convince the workers to accept the old rate this time and take their wage. But the workers were not be moved. After he did not succeed during the gate meeting the leader organised a side meeting, but even after hours of bullshitting the workers insisted on the 800 Rs rate. The leader got very agitated and left in his Maruti, while the workers shouted slogans containing his name and ‘down with’.
The East India workers continued working peacefully, but they refused to take the old rate wages. During the next days four thousand workers resisted the pressure in this way. The workers had only started to debate amongst themselves about possible further steps, such as demonstrations to the DC after shift, when the management made a full-force attack and broke the workers unity. The management was successful due to the stay notice drama, usage of the Dal Fry goons and the hesitations of the workers to take next steps. On 14th and 15th of November all workers had taken the old rate wages. During the movement of these four thousand workers it became clear for everyone that in no factory in Haryana the new rate was paid.
Workers at Gedore alias Jhalani Tools could also not be bothered to take part in the election theatre. Workers took part in a gate meeting, because they thought that it was about the demand notice. But the leader of the CITU in Faridabad started talking about support for the Janata Dal candidate. The workers told him to say something about the demand notice, otherwise they would go, because they had nothing to do with the elections. Then management and union put up a notice saying that workers should come to work on Sunday in order to take Wednesday off to cast their vote on the election day. In the first plant workers encircled the manager and told him that they will keep the Sunday as rest day. They told him that the workers had nothing to do with the vote, if management want, they can take the Wednesday off, but we will come to work. After having been encircled for one and a half our the manager withdrew the notice. At Gedore, workers took Sunday off and worked on election day. But in most of the other factories in Faridabad management and union forced workers to shift their rest day to Wednesday.
East India Cotton
FMS
(January 1990)
After having been shaken by the demonstrated unity of the 4,000 workers during the 800 Rs conflict, on 10th of December management decided to stop one power-loom worker at the gate and refuse to let him go to work. They just stopped him, they did not issue any charge sheet or any other written paper explaining the reason. This time the power-loom workers made a collective step in response. When they heard that their work-mate was kicked out, they stopped working. After machines stood for two hour the management gave the worker a one line letter, saying: “You have been suspended. The charge sheet will be issued later”. On 10th of December, East India management suspended five workers in response to the displayed unity of the workers.
East India Cotton
FMS
(October 1990)
It has been 15 months now since the announcement of 800 Rs minimum wage by the Haryana government, but in the majority of factories in Faridabad the new obligatory wage is not paid. In those big factories where permanent workers have been able to enforce the new wage, management engages in all kind of crooked ways to undermine it. Workers in the power-loom department of East India undertook a collective step against one of these crooked attempts. According to the state’s own definition, workers operating ‘Two-Loom-Drawbacks’ are graded as ‘highly skilled’. The minimum wage for these workers is 975 Rs per month, but East India pays them 910 Rs. Again and again workers have individually tried to enlighten management about this issue, but management did not bother too much. As a result workers operating the ‘Two-Loomk-Drawbacks’ decided to undertake a collective step in order to make management understand. The letter signed by all East India workers caused some commotion within company management.
East India Cotton
FMS
(August 1991)
East India Cotton Mills is a well-known Faridabad based company, engaged in cloth weaving, pressing, printing and sewing. The company operates under various names and in different official branches. During the times of workers’ uprising in 1977 – 1979 the East India workers were in the frontline. In order to quell the workers’ discontent East India management made use of the system of goons which made it infamous all over Faridabad. In October 1979 the police managed to suppress the unrest by firing and massacre. East India company established the Dal Fry gang of goons, which, during the last 12 to 13 years, have used all kind of ways and means to crush workers’ actions. In 1983 East India closed its Jute Mill, and years later the 900 dismissed workers still haven’t received their wages and pensions. Against this infamous management the power-loom workers have recently obtained a victory. The workers have been able to get out of the grip of management to a certain extend and open space for their fellow workers.
East India management – amongst many other local company managements – have filed a case at the high court against the new minimum wage grades, which have been announced in June 1989. In May 1990 the high court came to a verdict: The Haryana government and the company lawyers came to the agreement that the new grade would be put into practice not from June 1989 onwards, but from January 1990. many unions had collected money from workers in order to send their own lawyer to the court case, but in the end they did not. In this way several crore Rs endced in the pockets of management and ruling party leaders and several lakh Rs in the pockets of union middlemen. After the court case some power-loom workers realised that they were not paid according the new pay scale. Around 100 workers went – rather hesitantly – to meet management officials and union leaders, but their voice was not heard. In October 1990 these 100 workers sent a signed letter to management, that they are paid 65 Rs too little. Management did not respond. After a month union leaders told workers that they will be paid according to ‘fixed standard’.
After 12-13 years of company-organised violence these scared workers collectively signed their protest letter in order to demand their full wage from management. The workers undertook a second step. In November 1990 these 100 workers sent an application to the DLC. East India management swung into action. The advance payment and the ration and the cooperative store were cancelled for these workers. The intimidations started, but the workers did not bow. Management usually did not attend the meeting the DLC invited them to – and if they attended, then their representative said openly that according to the new rate those workers should receive 65 Rs more, but that management won’t pay them more, because the main issue was not concerning those 100 workers, but how to control 5,000 workers. The fact that these workers undertook steps themselves and put forward demands, this fact could not be accepted by the management. The management representatives said openly that the company would take the case up to the supreme court, but they would not pay. The resposibility of the DLC and the labour inspector was to make sure that minimum wages are paid according to the legal norm and to enforce this against management – but they did not. The DLC issued a request to management and the labour inspector kept on extending the request period.
East India Worker
FMS
(April 1996)
After management had not paid February wages by 13th of March workers gathered and demanded payment from management, they also gave a beating to one of the union leaders. Management consequently suspended two workers. On 14th of March the night-shift stopped at the gate after shift and the morning shift decided not to start working. They demanded that the suspended workers should be taken back on and the wages should be paid. The police arrived. The management promised to take the workers back and pay wages by 2:30 pm.
But since seven to eight months it is number one on the East India management’s agenda to replace the table printing by Tex Print machines and to sack 500 workers from the Ajanta department. Therefore the management started to stop people at the gate, to announce lay-offs and to refuse to give a job to the 500 casual workers, who had been employed as ‘badlis’ on a constant basis since eight to ten years. In order to diffuse the resulting collective anger, management obtained a court order saying that workers’ protest has to keep a distance of 100 metres from the company gates – but given the current election time the DC enforced that the whole conflict should be postponed. The old union leaders were kept away from it all.
Eight months earlier the East India workers had elected the last leader as their saviour, but soon enough tasted his betrayal. This time workers abstained from chosing leaders, but for some people it is necessary to look out for leadership. This time there were no ready-made leaders to buy off, therefore the East India management will be forced to practice how to produce leaders in advance. In this context an East India worker said: “We will not let them continue in the old style. We have challenged them by having beaten up an old leader. Let them run their case about union contributions [?], if they won’t work at the machines next to us, we will give them another beating. Today no one will be able to push workers around.” Another worker said that based on the last collective agreement a wage increase of 500 Rs is legally obligatory. However, we have to bear in mind that the aim of East India management is the dismissal of 500 to 600 workers.
East India Worker
FMS
(August 1996)
On 1st of July management put up a notice saying that any worker who leave the job voluntarily by 10th of July will get extra-money. In times when you need all kinds of personal connections and bribes to get a job, who would voluntarily leave? Voluntarily or not, in order to make people resign East India Cotton Mill management locked out the workers of the Ajanta Table Printing department and the colour room on 11th of July, and they did not pay the June wages. The fact that despite the lock-out production continued in the rest of the factory made management more than happy. Having stolen ten days of wages from the workers in the Ajanta department, after the meeting between management and leaders at the labour commissioner in Chandigarh on 18th of July the lock-out was lifted on the 19th of July and management put up a notice saying that the scheme for voluntary resignation would be extended to the 31st of July.
Since about a year the management aims at finishing off the table printing department and to kick out 600 to 700 workers. The initial scheme of large-scale retrenchment by locking out the complete factory – through attempted provocation pf mistreating one of the leaders – failed. Now management has brought up new leaders and prepared the trap for the lay-off of 600 workers. After management of Calvinators succeeded to lay off 2,500 workers with the help of the ‘great agreement’ facilitated by the Chandigarh officials, now East India management might well repeat this success. In 1979, on the background of automation, East India had to lay off 2,500 to 3,000 workers. Back then leaders could say whatever, the workers would follow. The workers suffered a lot, but the outcome was rather tragic. The fact that workers stand up-sit down-walk-stop on command makes things easy for the management. The East India workers can stop the redundancy drive if they think and decide together. Currently the main aim of East India are redundancies. Currently the new [wage] agreement is not the main concern. In 1979 redundancies were also the main point on the agenda, while the strike was initiated about bonuses.
East India Worker
FMS
(September 1996)
In June 1995 management stopped two workers from entering the factory. When their work-mates arrived at their workplaces, they laid down tools. After four hours management bowed down and only after letting the two workers get back to their job, production resumed. Some days later management stopped five workers at the gate. Again a sudden strike, again management bowed down.
The reason?
During these days the workers at East India did not listen to any of the union leaders. Workers took steps according to collective discussion and decision. To continue this process was in the interest of every worker, while it was a necessity for management to break it. Management brought forth new leqaders and workers – instead of continuing to make their own decision – started to stare at the mouth of the new leadership.
One year later, in July and August 1996:
The management locked out workers in the Ajanta Table Printing department on 11th of July and did not pay June wages. In the rest of the factory production kept running and workers took their June wages – ignoring what was happening in the department next door. In August 1996 management produced a list with the names of 90 workers who were supposed to be made redundant. After five, six years of employment these workers were suddenly kicked out. The production in the rest of the factory continued and workers kept silent about the enforced redundancies – instead they focused on the play-fight of the collective [wage] agreement dispute. Another list with names of 65 workers was produced, again silence from the rest of the work-force. A list with 140 names appeared, workers were kicked out, while the [wage] agreement drama continued.
The reason?
Currently workers listen to what the leaders say, they sit down – stand up, when they are told to. The leaders keep quiet about the dismissals and create a drama about the [wage] agreement. Following their example, workers also keep quiet about the lay offs and joined the drama.
“The leaders work very hard for the agreement, they are busy day and night, run back and forth, but they are not heard. What more can they do, we ask from them? The management is behaving very badly.”
And the East India management is able to lay off people, as they are pleased. Could anything better happen to management? Currently management breaks one finger of the hand, while the remaining keep silent. Workers hope that someone else should think for them and make decisions. We wish that someone else would find a solution for us. As a result leaders spring up like mushrooms. It will not change much if we later on cry about mushroom poising if we don’t change our state of inertia.
East India Worker
FMS
(October 1996)
In August East India management sacked 300 workers in three batches. On 2nd of September management put up a notice at the gate saying that the table printing department is closed due to running losses. The 600 remaining Ajanta printing workers were told to do this or that useless work in other parts of the factory. Anyone can predict that this increased the discontent amongst workers. Management announced on flyers that August wages would be paid on 8th and 9th of September, but by 10th of September wages were not paid. People kept silent about the redundancies , but got agitated about the [wage] agreement and announced the decision for a tool down strike. On 12th of September management of the East India Group enforced a lock-out at the printing and processing plant based in Faridabad Industrial Area and at the power-loom section based in Sector 24. The late shift was stopped by police at the factory gate at 2:30 pm, the early and general shift was slowly released from the factories by 10 pm. Management used to lock-out workers on their weekly day off, because it was hard work to get them out of the factory – whereas it has become rare that workers enforce entry to the factory against a lock-out, given the entanglement in legal procedures. East India management made the decision to lock-out workers while the whole shift was still inside the factory, in believe that they will not face major difficulties to get them out. Given that August wages were not paid, for the workers the lock-out essentially started not on 12th of September, but 10th of August – the original pay date. From 12th of September till 30th of September about 3,000 workers sat together during lock-out, but they did not use the time to debate and decide amongst each other, which would have been the necessary thing to do – during the whole time leaders gave only two speeches. From 12th September onwards a daily demonstration should have been organised in the morning and in the evening, but till 30th of September not a single protest-march was organised. This means that the workers did not undertake any step to increase their strength. What is the reason for this? “The leaders are very busy and if the workers do something without telling the leaders this could cause problems. The leaders are so busy, but what should we do, the police and administration have all sold out.” If the East India workers lose their strength in this way and hand over control to others, than management will impose their conditions. Three thousand workers are not a piece of straw that could be easily chewed by anyone. If workers would decide together, if they would organise protests marches, they strength would increase.
East India Worker
FMS
(November 1996)
After the lock-out in September workers were sitting together, but they were losing strength day by day. No protest march was organised in September, neither in October – which could have changed the balance of forces. The 3,000 workers dispersed bit by bit. After having been let out of the factory and made to sit inactive until most workers left the protest, the workers were preached from above that ‘Workers have to stay firm’. Apart from protest marches workers should try to enforce entry to the closed factories. In this context it is important to focus on the fact that in the powerloom factory redundancies are not on the agenda – management therefore tries to keep the powerloom production running. The redundancies concern the printing and processing plants in Industrial Area, these workers should undertake the first step to get entry to the factories. Breaking through the inertia of police and administration, workers could succeed in forcing government and management into retreat.
East India Worker
FMS
(February 1997)
After four and a half month of lock-out leaders came to an agreement with the management on 20th of January. According to the agreement 350 workers started production in the powerloom plant on 21st of January. Management reassured the remaining 2,100 workers of the printing and processing factories that the lock-out will be lifted on 3rd of February and that before that a good agreement would be found… aim at the end of the process will be the redundancy of the superfluous 600 workers. Roaming around during the months of lock-out, looking for work and being refused – workers at East India found out that it is difficult to find a job nowadays…
Comments
The mining industry and miners' struggles in India
https://libcom.org/library/mining-industry-miners-struggles-india
Comments
Preliminary Balance Sheet of the 13-Days Sit-Down Strike at Maruti Suzuki Factory in Manesar/Gurgaon, India
http://libcom.org/library/balance-sheet-maruti-suzuki-workers-strike
Comments
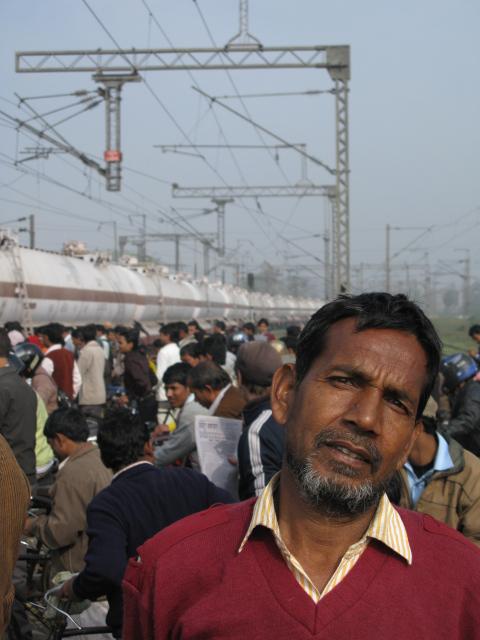
Faridabad-Gurgaon, India – Three Workers’ Stories and Thirty Workers’ Photographs
We want to change this society, not only because under current conditions our social productivity turns into the alien and destructive forces of war and environmental disaster; not only because in a money/market system, over-production means misery and hunger; but mainly because in the present system our potentially joyful social life is boxed up in daily routines, nuclear households, shift rhythms, loneliness amongst the masses…
Apart from reports on workers’ experiences in factories and struggles Faridabad Majdoor Samachar regularly publishes daily life stories of workers on its front-page. Workers of different generations, professions, gender, … talk about what we do every day. It is a mirror, sometimes we might not like what we see, but it is a starting point for all of us to think about a fundamental collective change…
Friends translated three daily reports: from a 34 Year Old Casual Worker, a 42 Year Old Government Employee and 50 Year Old Electricity Board Worker. A friend of Faridabad Majdoor Samachar took photographs during a visit in the area. They cover the way to work and the living area of workers in Faridabad, Manesar and Gurgaon. We document them together with the three stories…
To abolish the global work/war house will take more than informative exercise! If you live in Delhi area, please be welcomed to take part in Faridabad Majdoor Talmel – a workers’ coordination. We distribute Faridabad Majdoor Samachar on ten days each month in various industrial areas around Delhi – some of the photographs in this collage are taken during time of distribution. You can also participate in the workers’ meeting places which have been opened in various workers’ areas. If you are interested, please get in touch.
34 Year Old Casual/ Temporary Worker: I came to Faridabad for the first time in 1997. First, I joined Autopin factory through a contractor. In the first month, for 13 to 14 days, I worked for 16 hours each day. (I was seventeen at the time.) I worked there for nine months. In later months, I worked 16 hours a day for six, seven, eight days.
Through another contractor, I joined Talbross factory. Here also for six days in a month, they used to force us to work for 16 hours. During winters, going to and from the factory was very problematic given the fog at the railway crossing and crossing the National Highway Mathura Road. I saw three, four accidents where blood was all over the place. I felt sick. Because of the accidents and night duty during winter, I left Talbross after four months.
Then through an acquaintance, I joined Anil Rubber factory. Here for the first time, they had me sign on blank papers at the time of employment. I had also heard that employment officers take a 200 rupee bribe. In Anil Rubber, I worked sixteen hours a day only four days in a month. After six months, I was given a ‘break’, meaning termination of services.
I joined Expro factory. Here we have to work for 16 hours a day, five days in the month. And there was no chance of leaving after 12 hours of work. While working in Expro factory, I had heard about ITI (Industrial Training Institute). After six months, I was again given a ‘break’. In June 1998, I left for my village. That year I could not get admission in ITI. I got admisson in 2000. After completing ITI in 2002, I came back to Faridabad and I am now a temporary worker in Oswal Electricals.
At this time, I am on night shift. In the factory, I go to the latrine. (If I don’t go in the factory, then I have to go out in the open near my shanty.) I walk back to my room. I wash up and then have a bath. I don’t drink tea. By this time, it’s 9 a.m. And for breakfeast, I make roti, and fry potatoes, peas, or cauliflower. Sometimes, when I am too tired, I straightaway prepare my meal- rice, lentils, and something else with it. Normally, I sleep at 11 a.m. and get up at 4:30, 4:45 p.m. If I sleep after breakfast, then I miss out on lunch. After washing up, I go to the vegetable market and have a light snack there. At most, I spend 5 rupees on it. I buy vegetables for another 5 rupees and on returning I sit in a barbershop and read the newspaper there for an hour or two. Then for an hour or two, I study in the room- general knowledge, general science, and about my subject of refrigeration. At night by 9 p.m., I make dinner. Then I rest for an hour before leaving for work.
On arrival, attendance is marked at the factory gate. In the department, the supervisor tells us the work to be done and issues gloves and a pencil. I have to check the production of three operators. I have to check for fissures, indents, fault in the sites etc. There is pressure from the operators that I should hold back from finding faults. Yet, the responsibility of the job is that I do it according to the norms. This work continues into the night until 7:30 a.m. In Oswal electricals, there is no break for a meal and even for tea. Constant work for 8 hours! There is no question of sleep. (In some factories, workers work quickly and sleep after their work.) If the material is bad, then you can’t even take out ten to fifteen minutes for yourself and the material piles up. If the material is good, then we can rest for five, ten minutes and dring this time, we go to the latrine. Otherwise, we go to the toilet after the shift is over.
There are 500 workers in Oswal Electrical factory, but there is no canteen. (The law says if there are more than 300 workers, there has to be a canteen.) We are banned from leaving the factory to have tea. Three, four of us have to get together and obtain a gate pass for one person from the supervisor and send him to the East India Crossing open shops to get tea. Even supervisors cannot go out to have tea. This was the situation in the night-shift of Talbross Factory also- no break for meal, no break for tea, and there was a canteen, but it used to be closed at night.
Shifts change every week. Last week I worked the morning shift. Then I used to get up at 5 a.m. I had to go out in the open to defecate. Then make breakfast and lunch. Eat two rotis and fold four to take with me. During winters, I don’t bathe in the morning. From 7:30 a.m., I work in the factory. In the day shift, there is lunch break from 11:30 to 12 noon.
After the shift is over at 3:30, I come straight back to my room. I bring water and have a bath- supply water is not too cold. If something is left over, then I have that, or I prepare something small to eat. Then I read for awhile. I go to the library in NH1 (a locality) and for an hour, I skim through both English and Hindi newspapers. And return by 7 p.m. I’ll read books for an hour or two. I prepare my dinner at 9 p.m. and sleep by 11 p.m.
For these 15 days, I have to do all the work myself. Earlier I used to give an acquaintance, 600 rupees per month for my meal. The most problemtic is B shift duty. Now I will have to bear this all by myself. In B shift, I return from the factory 12 at night. At that point, it is very difficult to eat the 9 p.m. prepared cold food. It is 1 a.m. by the time I finish eating. I can’t fall asleep until 2 a.m. In the morning, I awake at 7, 7:30 a.m. and because of lateness, going out in the open for latrine is an additional problem. By the time I have my bath, it is 10 a.m. After breakfeast, I feel drowsy and sleep for another hour and a half. After getting up, I have my meal at 12:30 to 1 p.m. and just wile away time. Everything goes topsy-turvy in B shift. I feel loose, without energy. This laziness remains till 4:30, 5:30 p.m. After we have been working for an hour, then the body becomes alert. In B shift, leisurely roaming and reading stops.
I really dislike being in the factory. There is too much fault-finding and lecturing by the supervisor. I feel bad when co-workers refuse to answer a question or talk back rudely- they don’t even consider us human beings. They want to get work out of us at a faster speed than CNC (computerized) machines.
Outside there are also problems upon problems. Water problem, problem in the post office, problem at the railway station…everywhere there is a line. I dislike lines. Right now, I have no friends here. They are all temporary. A little acquaintance, some conversation. Sometimes, I feel extremely lonely.
I like interesting work, where there are things to be learned. I like to roam about and gather information. But in this age, where are such things?…
A 42 Year Old Gov’t Employee: I have been in central government service for twenty years. Before this, I did other jobs for 5 years. To earn some money, I had begun tutoring from the time I was in 8th standard. After I had finished 11th standard, I joined a factory. I worked in different factories- Hindustan Syringe, Escorts first plant, Unimax lab, Belmont Rubber, and Steadchem. (After every six months, I was thrown out). While working in the factories, I continued my studies through correspondence and completed a Bachelors in Commerce. Then I became a teacher in a school and while I was teaching there I got a job in the Central Government.
My husband is also in government service. We have one son. Because of Board Examinations, after 12, he doesn’t go to school these days, and my health is also not well. Therefore, in the morning I get up late- 6:45, 7 a.m. For the past 7 years, I have had breathing problems. For over a year now, a major operation was postponed for medical reasons and then I avoided it because of my son’s exam.
Even in gov’t service, for years it was routine to wake up at 5 in the morning. After making breakfeast and lunch, I sent my son to school at 7. The fridge made it possible to knead the flour for rotis at night and cut vegetables beforehand. So instead of getting up at 5, I could get up at 5:30. After getting my son ready, I would broom and mop the floor and wash the dishes. Then get ready for work. Because of breathing problems, increasing from the dust, for the past three years a woman comes and does the household work. Whether I am awake or asleep, work is on the mind all the time. I don’t feel like getting up in the morning, but I have to work. My husband brings milk and makes tea for us in the morning. I make breakfast and lunch. After getting ready by 8:45, I leave for the office. Work is work. There’s nothing to like about it. Even if there is a problem in the house or I’m not feeling well, I still have to go to work.
Work is from 9 a.m. to 5:30 p.m. First of all, we have to sign in. Then begin your work and keep at it. Earlier I was dealing with the public, but now I only work behind a desk. Because of this, I can be a bit flexible with the work. If I don’t feel like it today, I’ll do it tomorrow, but I can’t postpone it too much longer. There are no constraints on drinking tea in the office from your own money, but I don’t have an habit of drinking tea. Lunch is from 1 to 1:30 and during that time, men and women sit separately. Such is the tradition. In the women’s section, we talk about children, family matters, the rising prices of everyday expense. Someone sings a devotional song. But 80% of us lie down for twenty minutes. Some even take a nap. In these twenty years, I haven’t faced any difficulty as a woman employee. Now in the office there are many women working, but when I was dealing with the public, I was the only woman amongst male co-workers. Instead of facing problems as a woman, I got special attention. After 1:30, office work continues till 5:30. Because I have to sit in a chair all day, I get tired. From the office, straightaway I come home. I’m dead-tired and my husband makes a cup of tea for me. I make dinner and prepare things for tomorrow’s meals. By 10 p.m., we have had our meals and are free. Then we watch t.v.
From childhood itself, I haven’t had time for any interest to develop. Everything is so tied up by routine. If there is an holiday for a day or two, I can do the pending household work, but any time more than that and I wouldn’t know what to do.
My attempt has been that my son shouldn’t have to face the difficulties we have faced. We live an extremely simple life. My husband and I are both government servants and we have only one son, but still we are in debt. We are worried about our son’s exams, but we are even more worried about his admission. What if we have to pay for a slot in a university? To take a loan, we would spend our whole life repaying it. And then my operation!
There are problems. But I consider only those as problems for which I cannot see a solution. In my life, I have had problems at each step. Therefore, I do not consider routine problems as problems. I did not bother about my health- for my job, I have done overtime, and on holidays instead of taking rest, I take care of household tasks. Because of these reasons probably, there have been too much mental pressures. Taking it all into consideration, I am worried about my health.
From my childhood, I liked helping others and my own people. I don’t know why I liked to. Instead of sitting in a chair and doing office work, I like live relations instead. It has been almost my nature that I should not hold back anyone’s papers and no one should have problems because of me. It has never entered my mind that people whose work I do should pay me something in return. In twenty years, I hav not taken a cent from anyone for doing his or her work. And because of this, I have gotten great satisfaction. But in dealing with the public, you need a lot of energy. Of course, you have to talk a lot. You also meet many such people who simply do not accept that you want to help them. In such a situation, one gets tense. Because of illness, now I am doing a deskjob. And here also I don’t want to see anyone face a problem because of me. But government itself is a problem…
A 50 Year Old Electricity Board Worker: Right now my shift is from 11 p.m. to 7 a.m., but I am only really off-duty at 9 a.m. because early in the morning, there is a lot of load on the electrical line and some mishap is bound to occur. There is not enough staff there, so we have to stay back and I get home late.
I am tired when I get home. I don’t feel like doing anything. At this age, physical fatigue is natural. But nowadays, mental stress is greater. These days my family is with me so when I get home, I get a cup of tea. After having tea, I rest for an hour or two. Then after a bath and my meal, I go to sleep around 1 p.m.
Of course, I don’t feel like I have to get up around 3 to 4 p.m. Sometimes, it is because noise in the house or noise outside. But I don’t get enough sleep. Because of this, my heart and mind are restless… After getting up, I go and get the vegetables or some other household things. If I leave, I have to go here and there at 6 p.m. It’s 8 by the time I return. These days I get my meals cooked,so I don’t have the additional burden of having to cook my own food. But still there is usually there is something or the other to deal with.
Sometimes, I am ill or my kids are ill and we have to go to the doctor. Depending on the season, there is some illness or the other. On the days I have to go for treatment for myself or the kids, then I have to squeeze in all the other things I have to do. I don’t get a chance to rest. One has to be on duty during the prescribed shift hours. If there is any work on the electric line, then one has to go. Otherwise one has to stay at the Complaint Center. As soon as some break-down takes place, one has to inform the officer.
During summers, there is a lot of power failure. Because of dust storms and winds, there are breakdowns on the line. There is also too much load on the line because of people running fans, coolers, leading to breakdowns. Even at 1 or 2 in the night, the public will come to the Complaint Center. It is because those who come in and complain give us an helping hand with the manual work that we are even able to work. Otherwise, there is too much staff shortage.
During winters, there are less power failures, but when they do happen it is difficult to search them out. Because of fog, there are additional problems. A ten minute task takes half an hour. And sometimes, it is even difficult to locate the reason for the failure at all. During the rainy season, the transformers get burnt. Cables get burnt. Trees fall and wires are broken. The danger of accidents is high. Most workers are busy. Conversations are few. Discussions only take place when people are happy.
When my family is not with me and they return to the village, then life becomes very difficult. Before I come home, I have tea at a shop somewhere. After coming home in the morning, I have to clean the place. Mop the floor, dust, wash the clothes, wash the dishes. I have to collect water from the public tap. Then I cook my lunch and dinner. Sometimes, I make vegetables with bread or rice and lentils or bring curd from the shop and eat it with bread. It gets to be 1 to 1:30 p.m. once I complete all this. Then I rest for an hour or two. After getting up, I clean the utensils and get vegetables from the market…Sometimes, my bicycle needs repairs and sometimes my body needs repairs. By this time, it’s already 8 p.m. And then I have to get ready for the night shift
Life alone is very difficult to handle, whatever be the shift. For the morning shift at 7 o’clock, I get up at 5 a.m. When I am alone, then for half of the week, I am not able to make food for myself. I have to go for duty without tea or breakfast and there is not enough time to prepare a lunch to take with me. One reason for this is the laziness that come in the body with age. Even if one does not get meals, one still has to work. I have to either eat in the hotel or share whatever co-workers have brought. When the family is with me, I get home-cooked food. During the morning shift, there is more work. Instead of 3 p.m., we get off at 4, 5, 6 p.m. Some work or the other comes up so that we can’t leave yet. But we don’t get overtime payment for staying back.
Comments
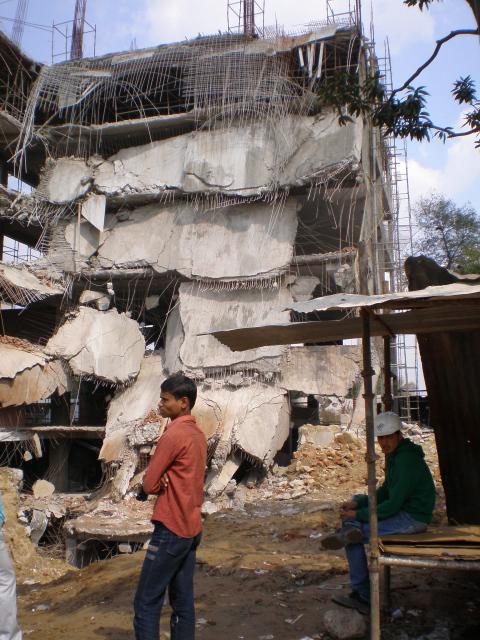
Gurgaon in Haryana is presented as the shining India, a symbol of capitalist success promising a better life for everyone behind the gateway of development. At a first glance the office towers and shopping malls reflect this chimera and even the facades of the garment factories look like three star hotels. Behind the facade, behind the factory walls and in the side streets of the industrial areas thousands of workers keep the rat-race going, producing cars and scooters which end up in the traffic jam on the new highway between Delhi and Gurgaon. Thousands of young people lose time, energy and academic aspirations on night-shifts in call centres, selling loan schemes to working-class people in the US or pre-paid electricity schemes to the poor in the UK. Next door, thousands of rural-migrant workers uprooted by the agrarian crisis stitch and sew for export, competing with their angry brothers and sisters in Bangladesh or Vietnam.
In the September 2011 issue you can find:
1) Proletarian Experiences –
Daily life stories and reports from a workers’ perspective
*** Workers’ Reports from Gurgaon/Faridabad Factories –
Short reports given to and further distributed by Faridabad Majdoor Samachar in spring 2011. Most of the accounts are from workers in the garment export industry based in Gurgaon
*** Systemic Collapse or Emancipation? On Accidents –
Commemorations for victims of two ‘accidents’ in Gurgaon and Okhla and further political questions
2) Collective Action –
Reports on proletarian struggles in the area
*** Small Upsurge of ‘Spontaneous’ Collective Actions by Garment Export Workers in Okhla, Gurgaon, Manesar –
Seven reports on direct collective actions in the garment export industry in March 2011. In order to enforce the payment of the (new) minimum wage, workers in several factories went on short wildcat strikes.
3) According to Plan –
General information on the development of the region or on certain company
policies
*** Shifts in the Call Centre Industry: Gurgaon Tata Workers’ Report and Global Re-Locations –
We look briefly at local and global changes in the call centre industry in relation to the current crisis. We document a call centre workers’ report from Gurgaon.
*** A Prelude? Current Problems of the Real Estate Giant DLF –
DLF was the main private company ‘which built the new Gurgaon’. This was before the global real estate bubble burst. Currently the fundaments of DLF are shaky.
4) About the Project –
Updates on Gurgaon Workers News
*** Suggested Readings: A Few Texts for the International Revolutionary Debate –
The global and historical character of the current crisis forces us to coordinate both debate and practice ‘for workers self-emancipation’ on an international scale. Following texts are selective, but we think that they can stand as examples for ‘general theses’, ‘concrete analysis’ and ‘historical debate’ of class struggle and revolutionary movement.
On the current and historical crisis of capitalism
On capitalist crisis and challenge for communist movement
Theses on proletarianisation, food production and (food) crisis
On recent uprising in Egypt
On recent uprising in Tunisia
On recent movement in Spain
Recent contribution for revolutionary debate on Russian Revolution
Last, but not least!
To abolish the global work/war house will take more than informative exercise! If you live in Delhi area, please be welcomed to take part in Faridabad Majdoor Talmel – a workers’ coordination. We distribute Faridabad Majdoor Samachar on ten days each month in various industrial areas around Delhi. You can also participate in the workers’ meeting places which have been opened in various workers’ areas. If you are interested, please get in touch. For more background on Faridabad Majdoor Talmel:
http://faridabadmajdoorsamachar.blogspot.com/p/fms-talmel.html
Comments
1) Proletarian Experiences –
Daily life stories and reports from a workers’ perspective
*** Workers’ Reports from Gurgaon/Faridabad Factories –
Shahi Export Worker
(15/1 Mathura Road, Faridabad)
The main problem in this factory is production, production, production. The production targets are way too high. At the feeder each worker has to give his production results to the foremen once every hour. If the production target is not met every hour the supervisor shouts at the workers and threatens them with dismissal. In the sewing departments, in the finishing department… at any place the targets are fixed. There is a lot of pressure, no one wants to sworn at. On 16th and 17th March, when the thread cutting workers did not meet their target before the meal break the supervisor did not allow them take the break. In the second finishing department, which is under the corrugated iron roof, a woman worker fell unconscious on 18th of March, because it was too hot and she was over-worked. How will things look like in the summer months? Last year in summer on one day 50 workers fell unconscious. On 5th of March a supervisor swore at a pressman for not having met the target – other press men surrounded the supervisor and threw him on the floor. On 12th of March the production manager slapped a supervisor for not having achieved the production target. Currently there is less work in the sewing department, but male workers in the finishing department start shift at 9 am and work till 1 am. In February the company ordered overtime on three Sundays. There is a canteen in the factory, by they offer neither meals nor tea. Most of the 2,000 workers employed here are female. If you arrive a minute late or punch out a minute too early they cut 50 Rs to 80 Rs from your wages.
Eastern Medikit Worker
Eastern Medikit has several factories in Udyog Vihar, Gurgaon. The wages of the casual workers are always paid delayed. In the factory on Plot 205 in Phase I the casual workers refused to start working on 17th of March 2011, because they had not been paid their February wages. After two hours of ‘work stoppage’ the manager said that wages will be paid the next day. The company plan was to pay an advance of 500 to 1,000 Rs before Holi and the rest of the February wages after Holi, but they had to pay the whole wage on 18th of March.
Gaurav International Worker (Garments)
(Plot 236, Udyog Vihar)
Every month between 400 Rs to 500 Rs get embezzled from workers’ wages. When eight to ten workers went together to the personnel department they were told: why do you come together, come one after the other. When you go on your own they swear at you and ask you: why do you come and make a fuzz about 100 Rs or 200 Rs? Two or four of the old workers were paid the outstanding money, but the rest of us were not paid. Working times are from 9 am to 10:30 pm every day – they hold you back in order to make you work longer. Only the first two hours overtime are paid double, the rest single. We manufacture garments for GAP, Asmara and Dealers. The bosses say that when the representatives of the clients come to visit the factory we should say that there is no overtime, only one or two hours here and there and that we eat our meals at home in the evening. Apart from the 2,000 to 3,000 workers hired directly by the company there are 400 to 500 workers hired through contractor in the finishing department. They don’t get ESI or PF.
Kalamkari Worker (Garments)
(Plot 280, Udyog Vihar Phase II)
Here 400 permanent workers and 1,600 workers hired through contractors are employed. The company does not hand out a pay-slip. We work 125 hours overtime per month, the permanents are paid one and a half, the rest of the workers are paid single rate. The workers stay the same, but after six months they are put on a different pay-roll and the cards are changed in order to avoid having to make them permanent or pay them seniority bonus. The toilets are dirty.
Modelama Worker (Garments)
(Plot 417, Udyog Vihar Phase III)
Daily working time is from 9:30 am till 10:30 pm and at least 12 days per months we are held back and we work till 1 am. For the tailors and the checkers the first two hours of overtime are paid double, the rest at single rate. The other categories of workers are paid only single rate. If you take leave at 6 pm and go home, the next day you have to face verbal abuse. They only start ESI and PF once you have worked for the company for three months. If you leave the job, in order to get the PF form filled in by the company it takes a lot of running around. The helpers received 4,350 Rs in February 2011, meaning that the 155 Rs DA from January was not paid.
Stickpen Worker
(Plot 318, Udyog Vihar Phase IV)
In this factory us 150 workers produce writing pens on two 12 hours shifts. On Sundays the day-shift works 9 hours, the night shift 12 hours as usual. Overtime is paid at single rate. The helpers receive 3,200 Rs per month. Only 2 – 4 workers get ESI and PF, these are the permanent workers, the rest are casuals. The drinking water is bad. The toilets are dirty.
S.A.N. International Worker (Garments)
(Plot 203, Udyog Vihar Phase I)
We work from 9:30 am to 10:30 pm every day. Then we might have half and hour or an hour off, then again work till 1:30 am. Often, when we are caught up in work pressure they don’t even grant this break for taking meals. Then we work till 6 am the next day. On Sundays they let us go at 5 pm. The tailors work 125 hours overtime a month, the guys in the finishing department 200 hours, paid single rate. If they make you work till 1:30 am they pay 25 Rs extra for food. If you have to stay till 6 am, they pay 50 Rs. There are about 700 workers in the factory, but there is no canteen. The tailors don’t get ESI or PF. There is a lot of dirt in the drinking water. The doors of the toilets are broken. We are hired through contractor, but we don’t know who it is – it’s possible that the general manager himself is the contractor.
Sherry Clothing Worker
(Plot 400, Udyog Vihar Phase IV)
If you take one day off they cut two days from your wage. The management swears at us. The helpers are paid 4,200 Rs, the tailors are on piece-rate. The toilets are dirty.
Aaina Fashion Worker
(Plot 893, Udyog Vihar Phase I)
The helpers are paid 3,500 Rs, the tailors are on piece rate. Of 200 workers only 4 are permanents, the rest are casual workers. The boss tells us that he will close the factory, that he will shut it on the 31st of March, he tells us to look for a different job, that we should leave now and come back on the 7th of April to get our final payment. One of us went and asked: “If we lose the job, why don’t you pay us now?”, but the accountant got angry and hit him. After that the worker went to see the manager of the plant, then the director, but then the big wigs kicked him out from the factory.
Vodafon Worker
(Plot 102, Udyog Vihar Phase I)
For running their company office Vodafon has subcontracted cars and drivers. The drivers have to wait outside of the gate by day and night, during summer, winter and monsoon. Vodafon hasn’t installed a rest room for the drivers.
*** Systemic Collapse or Emancipation? On Accidents –
Two accidents in Gurgaon area earlier this year pushed the ‘constant emergency’ and the ‘fragile temporary absence of accidents’ back into our heads.
On 25th of January in Okhla industrial area a fire broke out on the fourth floor of a arment export factory. Thirty workers in the finishing department died. Most (garment) factories there operate with boilers, solvents or other chemicals. Most factories are crammed with people, most factories only have one entrance/exit, which, in many cases, is locked during working time. After the accident ‘concerned’ journalists reported: “It is surprising that despite occurrence of such a major mishap in the area, no step has been taken so far by the concerned civic agency to stop the illegal and dangerous business in the area, which the owners cannot run without having nexus with the local police. “The business at the factory resumed just a day after the mishap,” said a worker, adding, “there are more than 100 illegal garment manufacturing units in the area which are still operating without any disturbance.” “Instead of standing with us, the police is making their all possible efforts to save the owner of the factory. More than 20 people from our locality have lost their lives, but the police’s count is less than 10,” said Hamid Ali (50), who lost his 18-year-old daughter in the boiler blast.
On the 17th of February an under-construction 6-storey building collapsed on Plot 100 of Udyog Vihar Phase I Gurgaon. It took 24 hours to get the right machinery to search for victims. The road was closed till the 22nd of February and people were obstructed from observing the ‘rescue operations’. Officially two security guards were declared dead. Rumurs spread that several families had slept in the construction site that night. The construction company Millenium Construction Private Limted built a factory for Unitech Infosys. The media: “Though the officials were not certain as to what could have led to the structure’s collapse, use of sub-standard material is being investigated.”
The incidents of ‘accidents’ are neither accidental nor isolated. Regarding the question of accidents we think that systemic problems require a systemic analysis – we therefore encourage to read the following article by Amadeo Bordiga concerning the question of ‘capitalist catastrophes’:
http://libcom.org/library/murdering-dead-amadeo-bordiga-capitalism-other-disasters-antagonism
http://libcom.org/library/murder-bordiga
Comments
*** Small Upsurge of ‘Spontaneous’ Collective Actions by Garment Export Workers in Okhla, Gurgaon, Manesar –
In the following we document seven short reports on collective wildcat action by workers in the garment export industry in March 2011. The strikes happened on the background of the Delhi government having increased the minimum wage on 1st of February 2011: from 5,200 Rs to the new Delhi minimum wage of 6,084 Rs for helpers, and from 6,000 to 7,410 for skilled workers. We can briefly derive three conclusions: workers don’t have and do not need an institutional union frame work to impose themselves; the structural weakness of the sector leads to a quick lash-back from the employers which can only be countered by coordinated organised efforts, e.g. when the company relocates work; piece-workers have frequently been able to impose higher rates by strike action, but we have only witnessed strikes of (monthly/daily) waged workers ‘on a mass scale’ when the official minimum wage has been increased; so far there hasn’t been a general ‘wage strike’ of that dimension without the impulse of the government increasing the rate; to our knowledge (monthly/daily) waged workers had to rely either on frequent job changes or sporadic strikes to ‘improve’ conditions; the general tendency is: increasing pressure on wages through global competition and introduction of ‘chain system’ (division of labour and mechanisation).
Om Jyoti Apparels Worker
(B-241, Okhla Phase I)
When the company gave out the two slips with overtime and attendance on 4th of March we became aware of the fact that the company will pay according to the old rate of 5,278 Rs (6,448 Rs). We demanded to be paid the new rate of 6,084 Rs (7,410 Rs). The management kicked out four workers from the factory. The mood was down… On 5th of March after the noon break we stopped production in the factory. In the finishing department there are 4 – 5 ‘incharges’ (department foremen), we encircled them and in order to escape from our anger they took refuge in the general managers office. The son of the chairman, he is the director, then said that the government had not sent the documents with the new pay rate yet and that the company will pay the new rate in March and also the area bonus for February. The company started relocation production work to NOIDA (a close by industrial area, but part of Uttar Pradesh, where the minimum wage is considerably lower). Saying that there is no more work the company dismissed 35 tailors on 15th of March and 16 workers of the cutting and finishing department on the 23rd of March… there are 250 workers left at Om Jyoti Apparels, out of which only 50 get ESI and PF.
Wearwell Worker
(B-61, Okhla Phase I)
The company paid the old minimum wage rate in February. On 11th of March workers stopped work for half an hour in order to protest. On 12th of march, when workers again stopped production after two hours the management put up a notice saying that in March the new rate will be paid and that the February area bonus will also be paid.
Orient House
(F-8, Okhla Phase I)
On 28th of February during the lunch break all workers assembled in front of the factory. They started shouting that they want to be paid the new rate. The management arrived at the gate and gave assurances that the new rate will be paid. Workers said that instead of some verbal assurances they wanted something in written. The bosses demanded that some representatives should come forward in order to negotiate. Us 700 workers said that we don’t have any representatives. The workers did not take up work… After one hour the company put up a notice saying that it will pay the new rate. (Translation from ‘Nagrik’ 16 – 31 March issue)
Shahi Export Worker
(F-88, Okhla Phase I)
In the factory there are more than 5,000 sewing machines. Most of the workers are female. When they announced the new rate the commotion amongst the workers increased. The company then put up a notice saying that the new rate will be paid.
Details Worker
(D-30, Okhla Phase I)
The company kicked out a few tailors on 25th of March after 15 days of employment. There was resistance. They then were paid their outstanding wage according to the new rate of 7,410 Rs.
Edigear International – Adidas, Reebok, Puma, Benetton Worker (Garments)
(Plot 150, sector IV, IMT Manesar)
We start working at 9:30 am and punch out at 6 pm ‘for show’ and for the official documents, actually work continues. At night from 8:45 to 9:00 pm there is a meal break, then we work till 1 am, often till 5 am. During January, February till the 18th of March 650 tailors, 100 cutters and 350 workers in the finishing department turned day and night into one. The tailors work till 1 am every other day, the 80 women workers stay from 9:30 am till 8 pm and Sundays from 8 am till 6 pm. In the finishing department the male workers worked till 1 am every night, on 14 days per months they worked till next day 5 am. In January the pressmen worked from 9:30 am till 5 am next day on 26 days. You have to turn up after your 4 1/2 hours break and start again at 9:30 am. After Holi only 11 out of 19 pressmen returned, some had fallen ill. After Holi 300 tailors, 100 finishing department worker and 40 cutters did not come back to work. We manufacture stuff for Adidas, Puma, Reebok and Benetton and there is a great demand, but currently a great lack of workers. There is no canteen in the factory. If we work till 1 am we are paid only 25 Rs extra for food, if till 5 am only 40 Rs. They should pay at least 50 Rs and 100 Rs for full-night food money. Workers currently refuse overtime and they say that the company should increase the wages, so that more workers will come and work. The workload is enormous and wages are paid delayed. On 14th of March, after February wages had not been paid, workers went inside the factory, to their workplaces, but workers did not start work, in any department. They had agreed on that amongst each other. On the next day, the 15th of March, workers again went inside, but did not move a finger. The general manager and the managing director promised that wages would be paid by the 18th of March, so work was resumed on the 16th. The bosses were told that if wages would be delayed again, people would look for a different job and they would have to find new workers. Now they said that they will pay punctually on the 7th of the month.
Sargam Worker
(Udyog Vihar, Gurgaon)
One month before Diwali the company dismissed 90 per cent of all workers in the factories on Plot 153 and 210 in Phase I, on Plot 224 in Phase IV and Plot 540 in Phase V, Gurgaon. In this way the company managed since 2008 not to pay the annual statutory bonus to 90 per cent of the workforce. In response on 14th, 15th and 16th of March workers in the Sargam factories stopped working and demanded the bonus. In the plant on Plot 210 on 16th of March at 1:30 to 2:30 pm, when production was still interrupted, management said that it will give a written announcement for the payment of the bonus. Now, on 24th of March the bosses say that they will kick everyone out tomorrow, on the 25th of March…
Comments
*** Shifts in the Call Centre Industry: Gurgaon Tata Workers’ Report and Global Re-Locations –
Call centres can be seen as ‘the industry of globalisation’. The came up in the 1990s as a product of Taylorisation of office work: information technology enabled to undermine the ‘individual skills’ of accountants, bank and other office workers. Contrary to what a lot of lefty ideologist thought the technological restructuring lead to a massification and concentration of work-force. By the end of the 1990s call centres went global, jumped the English speaking global wage scales from the global north to south. The patriotic populism of most of the trade unions proved helpless facing global relocations. India became the global back-office and call centre. Call centres combined ‘excess capital’ (finance, dubious personal services etc.) with an excess educated working class (students, graduates etc.). Unemployed post-graduates in Tunisia phoned for French Telecom, their Indian work-mates did the same for British Telecom. With the crisis one of the main pillars of call centre industry – the finance sector and personal services – came under pressure, so did wages in the global north. Currently we can witness rapid changes and shifts within global call centre work. In the following we give a sketchy overview on recent trends. Gurgaon is probably still the biggest call centre hub world-wide, so we are glad to document a short letter by a worker at Tata Consultancy Services based in Gurgaon.
a) Re-relocation back to the US and UK – Falling wage levels and populism
b) ‘Indian’ call centre companies opening call centres in the global north – Investing in the industrial decay (Manchester)
c) Call centre industry shifting further into the lowest wage regions, example Kashmir and Bhutan
d) Strike by call centre workers at Sparsh after relocation to small Indian town
e) Intensified outsourcing of accountancy and personnel departments and supply-chain management by major corporations
f) Squeezing space in ‘Indian call’ centres to counteract rising rent prices
g) Foreign workers in Indian call centres – Report of a worker from the USA
h) Strike by workers at Verizon in the US
i) Worker’s report from Tata Consultancy, Gurgaon
a) Re-relocation back to the US and UK – Falling wage levels and populism
There is a lot of talk about ‘on-shoring’, meaning that US or UK companies would close their call centres in India and re-open it in the US/UK. Most of these cases are actually blown up and don’t represent a major trend. The reasons given are often populist to both the patriotic sentiments and the ‘client pride’ (local accents, ‘good quality’ etc.). In general the share of IT-BPO service work done in India still increased, the global market share stood at about 55 per cent in 2010. Nevertheless there are some shifts taking place. We document some of them:
Indian call centres: not as cheap as the UK
(4th of July 2011, ET)
“But with Indian salaries expected to rise 13 per cent this year, at least one UK company has decided it’s cheaper to operate out of northern England than in Mumbai. According to a report in the Daily Telegraph, New Call Telecom said it was leaving Mumbai to open a call centre in Burnley, Lancashire after being attracted by low commercial rents and cheap labour costs there. Salaries in India aren’t that cheap any more. Add to that the costs of us flying out there, hotels and software, and the costs are at an absolute parity. Mr Eastwood added he also expected to save money through better staff retention in Burnley. In the UK we will pay workers the minimum wage. Given the current economic environment, we will get good “sticky” employees who will also receive bonuses linked to performance. The new call centre will operate out of rented property and employ up to 100 people. Some days later banking giant Santander announced to bring its call centres ‘back’ to the UK: 500 jobs would be created by the switch of call centre work from India to staff based in the UK cities of Glasgow, Leicester and Liverpool from this month. This year, BT has also created several hundreds of jobs in the West Midlands through the opening of a new call centre in Sandwell in the West Midlands. That investment follows a decision announced at its annual meeting two years ago that it too would be moving some offshored customer support jobs from India back the the UK. UK insurer Aviva moved back some jobs from its Indian BPO partner WNS to Norwich, UK, earlier this year. Although it did not give a reason, people familiar with the matter said it was facing quality issues.”
The following example demonstrates the ironic side of things: banking call centre relocation back from Asia because local workers are better in putting pressures of local workers in debt:
“The decision to bring the work – which had been handled from the Philippines under contract by Accenture has boosted employment at United’s offices in Warrington and Whitehaven in north-west England.
Russ Houlden, chief financial officer, said a review of United’s debt collection strategy had prompted the move – and a recognition that local staff were best positioned to deal efficiently with customers with genuine problems in meeting their bills.”
b) ‘Indian’ call centre companies opening call centres in the global north – Investing in the industrial decay (Manchester)
“On 14th of July 2011 the Indian firm Aegis announced to create 600 jobs by opening call centre in Manchester, UK. The contact centre will handle calls on behalf of Aegis clients, most of which are blue chip companies in sectors like healthcare, travel and hospitality, retail and technology.”
“As Indian companies grow in the U.S., outsourcing comes home
By Paul Glader, 20th of May 2011
New York – Ray Capuana paces the rows of cubicles in a haggard high-rise a stone’s throw from Wall Street as his people hustle the phones and hope for a bonus check. His employees are not bond traders, though. They are call center workers. Many are African Americans without college degrees. Some lack high school diplomas. They work for a Mumbai-based company called Aegis Communications. India’s outsourcing giants – faced with rising wages at home – have looked for growth opportunities in the United States. In this evolution, outsourcing has come home. The pay runs $12 to $14 an hour, with bonus checks of up to $730 a month. At $12 to $14 an hour with possible monthly bonuses, workers can make four times what call center workers in India do. But Essar executives say it’s worth paying more in wages to leverage a large U.S. presence to gain contracts with banks, health-care companies and governments that require the work to be done here.”
Importing cheap labour
Actually at least in the US most of the ‘Indian’ companies import some of their work-force and undermine local wage levels.
“In the past, if, say, BNY Mellon inked an IT contract with Infosys, Infosys would handle 70 percent of the work in India and send 30 percent of its project staff to the United States on temporary work visas. These Indian workers often live in ethnic enclaves on the outskirts of a city, work long hours and earn less than an American would for the same work. Companies such as Tata Consultancy Services, Genpact and Infosys are the largest users of the H-1B visa program and have collectively brought as many as 30,000 workers into the country in a year on H-1B or other visas. The workers are often paid “home-country wages” in America. “That’s as low as $8,000 a year” with housing allowances, he says. The employers own the visas – so the workers can’t bargain for wages, and if they lose their job they have to leave the country.”
c) Call centre industry shifting further into the lowest wage regions, example Kashmir and Bhutan
In the end it’s a question of wages, and wages are low when workers conditions are miserable. Aegis not only opens call centres in Manchester, they and companies like Genpact are the global tracker dogs for an ‘educated low waged work-force’. They have to enter the fields of social disintegration and decaying dictatorships:
Kashmiri call centre gives flicker of hope to a bleak future
(12th of August 2011 ET)
IS one of the world’s most volatile regions – a flashpoint between two nuclear-armed states that has become an economic backwater.
Now, India’s IT revolution has arrived in Kashmir with the opening of the state’s first call centre, in the city of Srinagar. The 230-seat centre, which handles calls mostly from customers in other parts of India. The call centre is operated by Aegis, an outsourcing company owned by Essar Group. Much of its work involves handling calls from customers in India’s booming mobile phone market, which is adding 15 million subscribers a month. With 500,000 unemployed, there is no shortage of willing job applicants, while wages in Kashmir are among the lowest in India.
Despite slowdown, BPOs look for expansion in Bhutan
(24th of August 2011, FE)
While the industry body, Nasscom, sticks to its projection of 16-18 per cent growth in IT exports in 2011-12, industry leader Genpact is all set to foray into Bhutan. “We are all set to open our office in Bhutan and we hope to start the operations soon. Tiger (NV Tyagarajan) and his team are already working on it,” said Pramod Bhasin, vice-chairman Genpact. “We believe that our country is an ideal destination to start a BPO because of the conducive atmosphere we have. To begin with, we have a stable government that is eager to set up an outsourcing industry. Apart from Genpact, we are also in talks with Wipro and few other players to start their operations in Bhutan,” said Kezang, executive director, ministry of information and communications, government of Bhutan.
d) Sparsh workers strike again!
In March 2009 workers at Sparsh call centre went on strike against low wages.
https://gurgaonworkersnews.wordpress.com/gurgaonworkersnews-no-933/#fn2
The call centre closed and a smaller call centre was opened in a small town in Rajasthan. About two years later and several hundred kilometres in distance Sparsh again faced workers’ anger:
BSNL call centre employees on strike
(22nd of June 2011, Times of India)
AJMER: Employees of state’s first call centre – BSNL – went on strike alleging the organization for illegal deduction of money. They said they got payments lower than what was promised to them during their appointment. The management was in touch with the employees but no solution came until the evening. The call center was inaugurated by union IT and telecom state minister Sachin Pilot. About thirty people working with call centre ‘Sparsh’ walked out of the office on Friday morning. They shouted slogan against the officials. “They promised to pay Rs 5,500 at the time of appointment but they are paying us Rs 3, 700 only,” Minali, an employee, said. They also accused the HR and operation officials of harassment , “They have zero tolerance . Even when the system fails they deduct half day’s salary,” another employee said. When contacted, the officials refused to talk and said there was some misunderstanding , which they were trying to solve.
e) Intensified outsourcing of accountancy and personnel departments and supply-chain management by major corporations
Obviously it becomes more interesting when global call centre agents or back-office workers not only handle ‘global clients’ but form part of an actual global productive cooperation. For example a back-office in Gurgaon organises all shift-shedules for the German railways Deutsche Bahn. Some recent examples from Gurgaon:
“Capgemini inaugurated its new Business Process Outsourcing (BPO) centre in Gurgaon, its first BPO centre in North India and sixth in India
(23rd of July 2011, FT)
Spread across an area of 35000 sq. ft, the new BPO facility in Gurgaon will increase Capgemini’s BPO’s total capacity in India to over 4500 seats. The existing BPO staff in Gurgaon will deliver Global Order Management services to Nokia Siemens Networks, a leading global enabler of communications services, to support the company’s global Supply Chain Management.”
“Genpact acquires Nissan’s HR operations
(2nd of June 2011, ET)
India’s largest BPO firm, Genpact, on Monday bagged a seven-year HR outsourcing contract from its existing client Nissan by acquiring its shared services center for human resources in Yokohama , Japan. The acquisition will boost Genpact’s presence in Japan and the center ( Nissan Human Information Service )) will be renamed as Genpact Japan Service . The amount paid for acquisition was not disclosed by Genpact. Genpact will provide payroll, benefits, staffing, training and other key HR services to Nissan’s 54,000 employees. Genpact already manages procurement for Nissan from its offices in Gurgaon and Dalian.”
f) Squeezing space in ‘Indian call’ centres to counteract rising rent prices
Apart from cutting wages, free food, bonuses etc. a lot of call centres in India, particularly in high-rent urban areas, start to reduce the work and breathing space of their workers.
“IT, ITeS firms pack more employees in confined work space to save on real estate costs
3rd of August 2011)
“Under pressure from their clients, or parent organisations, to reduce bills amid increasing rentals and employee salaries, these IT-enabled services (ITeS) firms are taking stringent measures to cut costs. They are reducing space per employee, and decreasing the size of common areas like cafeterias and conference rooms. At a clutch of ITeS companies, office space is being shared between IT workers and the call centre workforce (as the latter work the late shift to synchronise with US timings). And a few firms have even been asking employees to work out of the library. At the Gurgaon offshore office mentioned above, space per employee has been reduced to 60 sq ft from 100 sq ft; at large IT companies, 125 sq ft per employee is a standard. Workstation width has dropped from 3-4 feet earlier to 2 feet. All this is leading to severe workrelated stress. “I can’t move my hands in the fear of hurting someone. And all day one has to hear colleagues talking about issues from boyfriends to food recipes to childcare, which is not just distracting, but irritating,” says Rajsekhar. A Kumar, an employee at one Gurgaon ITeS centre, adds: “In the morning, the lifts are so packed it feels like you are travelling in a Mumbai local train.” “In the West, people come out on the street to protest when governments allow higher bird density in poultry farms. Over the past five years, rentals for IT and ITeS firms in the main metros have gone up by between 20% and 90%, according to real estate consultant Jones Lang LaSalle India. Salaries, on the other hand, have seen a 15-20% growth year-on-year. A junior employee with generic skills in India costs about $20 an hour, or $40,000 a year. An equivalent resource in the US comes for $60,000. A senior executive resource in India costs $30 an hour, or $60,000 a year, while an employee with a similar experience and skill in the US costs $90,000 annually. The result? Margins in business process outsourcing (BPO) have been stagnating at 18% for the past years even as revenues declined in 2011. For IT services the drop in profitability is worse: margins have plunged from 32% in 2006 to 18% in fiscal year 2011.”
g) Foreign workers in Indian call centres – Report of a worker from the USA
And obviously there are quite a few foreign workers employed in Indian call centres now. A readable account of a US based worker from Gurgaon:
http://motherjones.com/politics/2011/05/indian-call-center-americanization
h) Strike by workers at Verizon in the US
They have been one of the proletarian back-bones of global communication workers and one of the first call centre workers who went on a mass strike in 2000.
http://libcom.org/library/6-confrontations-pulse-collective-struggle
They had to go on strike again this year in August, after Verizon announced to cut health care and pension. We know little about whether this strike had repercussions within the global telephone lines, whether Verizon call centre work was done by invisible (and probably unknowing) ‘scabs’ at the other line. This mass work-force which is still semi-integrated with the ‘hard-ware’ workers like electricians or line-maintenance could have reached out to a global work-force. We know too little about the strike and given the lack of first-hand accounts or reports by comrades we document the conclusion of the WSWS:
http://www.wsws.org/articles/2011/aug2011/pers-a22.shtml
i) Worker’s report from Tata Consultancy, Gurgaon
“Two brief accounts from Gurgaon where call centres continue with their exploitative practices
Tata, the salt to software conglomerate is no stranger to controversies. From the killing fields of Nandigram to driving the endangered Olive Ridley turtles to near extinction the Tatas have seen them and done them all. Outsourcing behemoth, Tata Consultancy Services (TCS), which operates in both information technology and business processing outsourcing (BPO) domains, has kept alive the age old Tata tradition of exploitation of workers – this time in Gurgaon call centres. As an employee of TCS, I have documented two such practices.
One of them relates to increasing the notice period. A notice period is the time which the employee must serve on resignation before he is relieved from company services. As per labour laws these are a part of the employment contract and cannot be increased to the disadvantage of the employees without employee consent. Rachel, an agent with TCS, narrated an incident when she found a better offer with a rival call centre and resigned from TCS. To her consternation, she was informed that her notice period had been unilaterally increased by TCS from two (as was mentioned in her employment contract with TCS) to three months. She was not informed of this change in the terms of her employment (which is completely illegal in the first place) and she came to know about it only when she had resigned. Since she had already committed on a joining date to the rival call centre – which she was unable to meet – she was left with no choice but to take back her resignation and continue working with TCS. On the first glance this may not appear to be a serious violation of employee rights. Reality however is different. Since call centres are not unionised the agents have no negotiating power. This creates fertile conditions for exploitation by the management all of which is well documented in call centre literature. The only real power that an employee possesses is to resign. By depriving the employees of this power they are further subjugated to management whims leading to possibility for pervasive exploitation.
Timesheets are meant to document the man-hours logged by agents at work. Agents fill them at the end of a day’s work. Call centres extensively use them to determine the salary payout to the agents. Abhishek, an agent with a voice based process for domestic client narrates that their team was asked to fill 8 working hours of work even as they were asked to put in 10 hours. What it meant was that they were paid for 8 hours work while they were putting 10 hours. What is more interesting is that there virtually no protests on what was a patently exploitative mandate. As Abhishek notes, the typical reaction of an agent was of docile acceptance coupled with the acknowledgement of lack of negotiating power vis-a-vis the employers.
These two instances only go to reveal the extent of exploitation of the workforce and an urgent need for unionisation in the call centre space.
PS- Some names have been changed in order to prevent the victimisation of my sources. Again this goes to show the oppressive nature of neo-liberal global capitalism that is pervasive in Gurgaon.”
*** A Prelude? Current Problems of the Real Estate Giant DLF –
The real estate company DLF was the symbol of the ‘Shining India’ of the post-1990 period, the shooting star on the stock-markets and the builder of neoliberal city Gurgaon. The most recent news about DLF might be an indicator of the current condition of the ‘Indian boom’ and will have an impact on the local (political) ruling class, which has been forged in the gold rush of ‘land deals’. We should keep an open eye at further developments.
DLF to sell 13-acre Gurgaon plot for Rs 300 crore to ease debt burden
(19th of August 2011, ET)
India’s largest developer DLF is selling a 13-acre plot in Gurgaon, Haryana, as part of its plan to ease its debt burden through asset sales. About 1 million sq ft of commercial space can be built on the plot, which is expected to fetch Rs 300 crore for the realty firm. DLF’s net debt increased by Rs 100 crore during the April-June quarter to Rs 21,524 crore. The firm had said that it plans to sell developed assets, including IT parks and its hotels business as well as hotel plots to raise Rs 7,000 crore over the next two years. The company reported that the money from the sale of non-core assets was Rs 165 crore in April-June quarter. The company is also trying to sell land in other cities such as Hyderabad, Kolkata, and Chennai. DLF has also appointed Goldman Sachs as an advisor to sell Aman Resorts, a luxury hotel chain of 23 hotels across 12 countries it had acquired in November 2007 for $400 million. Real estate giant DLF may have to pay Rs 900 crore extra penalty if the Competition Commission of India (CCI) finds it guilty of abusing its dominant market position in three more projects in Gurgaon.
Comments
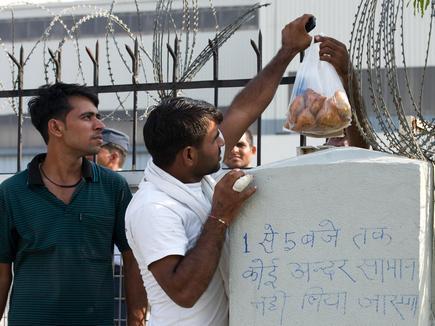
Wildcat strikes, factory occupations and protest camps
Since June 2011 around 3,500 workers at Maruti Suzuki car plant openly confront the factory regime and its institutional allies in Manesar, in the south of Delhi. [1] Their struggle leaped over to other automobile factories in the industrial corridor, which brought the world’s third largest automobile assembly plant in nearby Gurgaon to a halt. While in the US automobile workers have to confront the introduction of a union sanctioned “Two Tier”-wage system, which enforces a dramatic (global) wage drop and generational division, the Maruti Suzuki workers refuse the status as cheap labour.
In the most significant workers’ struggle in India in the last two decades the young workers managed to undermine the companies’ attempts to divide them along the lines of temporary and permanent contracts. The struggle attacked the core of the Indian development model and puts it into question: integration into global markets and production structures on the highest technological level combined with harshest casualisation of the workforce. While waves of protest against the impacts of the crisis rock the globe, their occupations and protest camps are an angry exclamation that this system is in crisis even when it is ‘booming’. In its potential their struggle is a chain in the missing link between the strike waves at Honda in China in 2010 and the mass mobilisations against corrupt austerity regimes during the ‘Spring Uprisings’ and in the global North in 2011.
We hope to be able to provide some material and thoughts for the necessary debate about this dispute and the general question of ‘how to organise for the self-emancipation of the working class’.
*** Collection of Quotes from the Front-Line –
*** Summary of the Struggle from June to October 2011 –
*** Chronology –
*** General Political Thesis for the Debate –
*** Further Material –
* Links, Videos and Documents (Written Agreements) –
* Contribution for the Debate: A Critique of the ‘Balance-Sheet of the Maruti Suzuki Struggle’ in GurgaonWorkersNews no.41 –
* Article in Faridabad Majdoor Samachar with Workers’ Reports after the first Factory Occupation in June –
* Short Reports by Workers in Automobile Factories in Manesar/Faridabad, Distributed by FMS Shortly before Dispute at Maruti Suzuki Broke Out –
Comments
“When we went home finally after a long stint occupying the factory, we saw how fast the world is changing on television, there are hundreds and thousands of people like us, working people, young people, out on the streets, occupying so many cities, New York, London, Rome…, we realized that we are not alone…that makes us feel very happy…that is why you see so many of us smiling here…we are angry, but we are not beaten, we are out here, and we will not give in now easily…the whole world is watching the whole world.”
(Maruti worker after the end of the second occupation)
“Indisciplined workers inside the plant can cause an even greater loss'”
(Maruti Suzuki chairman R.C. Bhargava, after decision for ‘lock-out’)
“But we are not donkeys. We cannot work like slaves. The problem is the immense pressure. They are extracting the work of 5,000 from half that number. We cannot go to the washroom during any other time, and in case we do, we have to give an unconditional apology letter. We are giving our best to the company, but what are we getting in turn? The production capacity of Maruti has gone up from 10 lakh units to 12.7 lakh units in during the last two years, but our salary has not gone up at all. Where is the incentive for hard work?”
(Maruti worker)
“A process of healing had to begin, and it was clear from the amount of feedback we received from that exercise that we had been somewhat cut off from how they [the workers] were feeling.”
(Maruti official after the first occupation and the decision to engage Brahmakumaris spiritual organisation for ‘re-conciliation’)
“My wife and I talked it over. We decided we’re young enough to fight this. What do we have to lose? If we win, we don’t have to be slaves any anymore. If we lose, I’ll find work somewhere else.”
(Maruti worker on strike after second occupation)
“Global investors are watching this very closely. India’s low-cost manufacturing growth story is built upon labour stability.”
(Stock-market trader SMC Global Securities)
“We would not call it a strike as there is no labour union at Munjal Showa. It is a fallout of whatever is happening at Maruti’s plant. The protesting workers from Maruti’s plant joined people here at our plant last evening.”
(C.M. Midha, general manager at Munjal Showa after wildcat strike at his factory)
“These hands have worked so hard that had I put them to use in my family farm in Hisar, my folks would have been very happy. We have delivered 2 lakh cars when the management wanted it, working overtime and breathlessly and we have been taken for granted.” Asked why he does not go back home to work on his farm, he shoots back: “I wanted to be something else.”
(Maruti worker)
“We are on strike in support of the Manesar workers. Once they are issues are resolved then we will raise our demands. Our workers are paid less than what the company pays the Manesar workers. We want the same pay for all workers.”
(Powertrain Union official, 21st of October)
“When you look at this entire situation, then we admit that there is a need for us to bring in adaptability in a young population that is very, very young. I think definitely, it must be somewhere more from the side of the young inexperienced workers and I think it is typically a question of capability to adjust and adapt and have some respect for law”
(Maruti Suzuki India (MSI) Managing Executive Officer, after the start of the second occupation)
“Once a problem starts, it does not just go away.”
(Maruti chairman R.C. Bhargava after the ‘lock-out’ started)
Comments
Please feel free to correct and add to this chronology. We need a collective memory for the struggles to come.
The First Occupation: 4th of June to 17th of June 2011
3rd of June
Representatives of the MSEU meet the Labour Department to complete the formalities regarding registration of the union. The same day the labour department officials inform Maruti management about the issue. The management begins forcing workers to sign blank papers in order to be able to sabotage the union formation.
4th of June
Start of the 13 days of the first occupation. After the union reps try to retrieve some of the blank signed papers, management resorts to dismissals and suspensions. Workers start a sit-down strike in the afternoon and occupy the factory.
5th of June
The management starts to seal the factory gates and placed a row of security guards in front of them in order to prevent exchange between workers inside and outside, between workers and supporters and media. In nearby Delhi the police attacks the mass protest of ‘anti-corruption Guru’ Ramdev brutally.
6th of June
Only after a demonstration outside the gate, the food supply through family and friends is permitted again. Police is deployed both inside and outside the premises, they remove some tents, which supporters had put up.
8th of June
The main unions AITUC, CITU, HMS, INTUC, UTUC form a ‘joint action committee’ to ‘support’ the strike.
9th of June
The ‘joint action committee’ mobilises “workers of 50 to 60 factories in Gurgaon”, around 1,000 to 2,000 union members gather in front of the Maruti factory gates.
10th of June
The strike is declared illegal by Haryana government. Two truckloads additional police arrive on the factory premises. Under pressure 250 workers decide to leave the occupation. Due to lack of storage space around 200 to 250 of the suppliers, most of them located in the proximity of the plant, have to reduce or stop production.
12th of June
The Maruti Suzuki management offers to take back 5 of the 11 sacked workers, but the union refuses. The main unions announce a two-hour solidarity strike for the 14th of June 2011.
13th of June
The management announces that it would accept a separate union for the Manesar plant, but under the umbrella of the company council, which would be responsible for wage revisions and other general issues – a fake offer.
14th of June
AITUC secretary Sachdev first announces that the two-hours solidarity strike is on, only to proclaim that it is called off ‘due to negotiations’.
16th of June
The management tells the media that it would try to ‘revive’ production lines in the Gurgaon plant for models, which had been moved to Manesar.
17th of June
End of the first occupation. The dispute is settled with help of main trade unions and MUKU (Gurgaon plant union). Maruti promises to turn the dismissals into suspension. Union reps accept ‘no work, no pay’ plus penalty wage reduction. Maruti says that the occupation has caused 93 million USD loss. Maruti Suzuki brings in external trainers and the spiritual organisation Brahmakumaris to organise sessions with the workers, where they were encouraged to speak about their problems. After lock-out at Denso in 2010 the same ‘spiritual organisation’ had to heal the ‘industrial relations’.
The Underground: 18th of June to 28th of August
18th to 25th of June
According to management sources the output of the Manesar factory during that period was only 1,100 cars per day instead of the usual 1,200. Workers report that most supervisors, who had been high-handed, now treat them with a certain awe.
16th of July
After 11 years the MUKU holds elections. Workers in Manesar boycott the stage show. Only a dozen votes were polled.
26th of July
The application to register Maruti Suzuki Employees’ Union (MSEU) is rejected by the state authorities for formal reasons (illegal strike, faulty signatures).
27th of July
A group of workers hired through contractors complain about the work load and demand more workers to be hired for the job. The department supervisor verbally abuses one of the workers. His workmates support him and the supervisor is forced to apologise in front of the workers.
28th of July
Police enters the factory and take away four workers from their work-places and announce six suspensions. In response workers in the whole plant stop working and gather. The company is forced to ‘show’ that the four workers have not been arrested. The company orders that no buses are sent out to collect the B-shift. Workers arrive by their own means, but Maruti refuses them entry. The A-shift workers refuse to leave the factory. After a short stale-mate the company lets the B-shift workers enter.
8th to 17th of August
Although the management promised to withdraw the suspensions if ‘normality returns to the factory’, management refuses to do so. Instead the company continues hiring new ITI workers from Kanpur and other colleges. The company also fences of all grass and outside areas on the premises, which have been used by workers during the occupation. Supervisors start using their previous high-handedness towards the workers again.
23rd to 24th of August
Four more workers suspended. The company complains about production loss due to go slow and sabotage. “On August 24, 1,230 cars were planned to be produced, but only 437 were assembled. Out of which, just 96 cars could pass quality check”.
The Protestcamp / Lock-Out: 28th of August to 30th of September
28th of August
Start of the 33 days of lock-out / protest camp. During the night, when only a few hundred workers and supervisors on overtime are in the plant a 300 to 400 strong police force in riot gear enter the factory and establish themselves there.
29th of August
The management refuses to let any worker enter the factory without signing the ‘good-conduct undertaking’. Only 18 workers sign. A nearly 500-metre-long aluminium wall is put up covering the service lane, blocking the view from both inside and outside. Notices announce dismissal of 11 workers and 10 suspensions.
30th of August
The company claims to have started ‘production’ in the highly automated areas (weld-, press-, paint-shop) and announces to ‘have found 200 potential ITI workers who will be hired on contract basis in the next 2-3 days’. 12 more workers sacked and 16 more suspended – allegedly all office-bearers of the MSEU.
31st of August
“The company brought in 120 ITI-trained workers this morning to the plant on a contract basis to strengthen manpower for assembly operations”. In addition, 50 engineers from the Gurgaon factory and 290 supervisors are working at the Manesar plant. The company claims to have 500 trained and experienced people available for production. Only 36 workers have signed the bond so far.
1st of September
Nearly 3,000 members from 35 unions in the region assemble in front of the Manesar plant to express solidarity with the protesting workers. The unions announce to go on a tool-down strike the following week if the management declines to negotiate.
2nd of September
Some contractors and Maruti middle-management round up around 150 Maruti workers in Aliyar village near the Maruti plant in Manesar. The workers are threatened and some are beaten. After workers resist the contractors/thugs, the police arrive and arrest some of the Maruti workers. Meanwhile the employers’ association ASSOCHAM asks the Haryana government “to take firm action against those who are trying for sometime to malign the name of Gurgaon, which has become destination for many Indian and global companies.” The company claims to have produced 125 Swift cars from Manesar Plant A and Plant B this day. Normal production in Manesar: 1,200 cars (150 SX4, 300 to 400 A Stars, 650 to 750 Swift).
3rd of September
Some 70 students from Delhi universities visit the Maruti workers. Towards evening, workers have to shift their protest-tent across the road, as the management obtained a court injunction against any protest within 100 metres of the factory. The company claims the current strength of people available for production to be around 800 (90 engineers from Gurgaon, 290 supervisors and 425 new manual workers). The new workers have to stay inside the factory day and night. This workforce is supposed to have produced 150 Swift.
5th of September
The MSEU publishes a communiqué: “The production was at a total halt in the beginning of last week, and in the last 2-3 days, a meagre 8-10 cars were produced in the plant, which are all faulty models somehow clubbed together.” The company claims that so far 63 permanent workers have signed the ‘good conduct bond’.
11th of September
The MSEU meets with representatives from around thirty trade unions and repeats its demand of the right to organise and unionise, to withdraw the charge-sheet, termination and suspension of 57 workers. In turn Maruti announces: “From Tuesday onwards the company will start hiring trained technicians, who will be on the permanent rolls, to replace the current workers who refuse to sign the bond.”
12th of September
Wildcat strike at automobile supplier Munjal Showa in Manesar, which spreads to the companies’ Gurgaon and Haridwar plant. The 1,200 workers in Manesar are hired on temporary basis and are not unionised, they produce around 60,000 shock-absorbers per day. They demand permanent contracts and the company to stop shifting workers between plants. The production at motorcycle factories of Honda and Hero Honda is threatened due to lack of supply.
13th of September
The wildcat strike at Munjal Showa ends. The management agrees to make 125 workers permanent, and to promise that after completion of 3 [5?] years of training, all workers will be made permanent. The management complains about ‘negative influence from Maruti Suzuki workers’. AITUC, CITU, HMS and 11 members of independent unions revive the ‘Joint Action Committee’. In Gurgaon around 1,500 union members and students demonstrate in support of Maruti workers. Maruti claims to have 1,100 work-force in Manesar, after having hired additional 100 ITI workers today.
14th of September
Strike at Suzuki Powertrain Ltd. and Suzuki Castings in Manesar and workers at Suzuki Motorcycle India Ltd. in nearby Kherki Dhaula in solidarity with Maruti Suzuki workers and for own demands. More than 4,000 workers are involved. When asked for support MUKU at Gurgaon plant talks about ‘potential of a hunger strike next week’. Around 350 workers hired through contractor engaged with loading and unloading at Maruti Manesar plant also go on strike and demand driver instead of helper grade. Suzuki announces to locate a planned $1.3 billion passenger car factory in the western Indian state of Gujarat.
15th of September
Negotiations at Suzuki Powertrain, Casting and Motorcycles. Scuffles at gates of Maruti Manesar plant when the company tries to force three buses with temp workers inside the plant. Four strikers injured and arrested. The media reports about 11 injured supervisors.
16th of September
While Maruti announces to close the Gurgaon plant due to lack of parts from Suzuki Powertrain, the union HMS negotiates an end of strike at Suzuki Powertrain and Motorcycles, the workers at Suzuki castings also call off their strike. Gurgaon plant operational again on 18th of September. Meanwhile the “Joint Action Committee” calls for demonstration in Gurgaon, but after the district president of the AITUC was arrested (‘risk of ‘breach of peace’) the demonstration is postponed.
17th of September
Short strike Manesar Honda HMSI plant in order to get the AITUC officer out, at 2pm he is released against bail. At the stock markets analysts downgraded their call on MSIL shares from ‘buy’ to ‘accumulate’.
18th of September
Police arrests three MSEU leaders when they come out from negotiations with management and state administration on basis of phoney charges.
19th of September
The three MSEU leaders are released. Meeting of worried company leaders (Maruti, Bony Polymers, Honda, Rico Auto) to discuss the industrial dispute’. Maruti announces that they will ask 350 trainees to resume duty within next three days and claims to have produced 600 Swift from Gurgaon and Manesar plant (no separate figures for Manesar available). HMS leader proclaim that workers are ready to sign ‘good conduct bonds’, but insist on taking back all suspended and dismissed.
20th of Sep
Maruti dismisses five more workers in connection with the alleged scuffles at the gate.
21st of September
“After exceeding the normal production levels for the Swift, the company is planning to start production of the SX4 and A-star models at Manesar plant,” Maruti claims in a statement and announces to have hired 100 more regular workers. 104 workers at the Manesar plant are said to have signed the ‘Good Conduct Bond’ since the start of the dispute.
22nd of September
Day of solidarity: Demonstration by section of railway union in Japan against arrest of Maruti union leaders. About a dozen trade unions demonstrate in various places across India. More than 100 people protest in front of Haryana Bhawan in Delhi and at a Maruti Suzuki showroom near Connaught Place. Meanwhile the media announces that the total workforce at Manesar has increased to more than 1,300.
23rd of September
Company sends individual SMS to permanent workers mobile phones and asks them to go back to work. Workers’ families in villages are also contacted to ‘convince’ their sons/husbands to resume their duty.
24th of September
Maruti claims to have produced a total of 700 Swift, out of which 400 in Manesar, no other models. 116 workers are said to have signed the bond.
26th of September
Maruti claims that in total 1,400 workers are working at Manesar factory, out of which around 800 newly hired.
27th of September
Talks fail, workers in Manesar accept MUKU (Gurgaon plant union) as negotiator. MUKU announces a ‘hunger strike’ for the 28th of September, in case the management will not move. The AITUC indicates it will press for an immediate return to work if the company agrees to place about half of 62 workers it has fired for “indiscipline and insubordination” on suspension instead. The Economic Times claims that total work-force is at 1,500 and that Maruti started producing the second (out of three) model in Manesar.
29th of September
Two weeks of lock-out of 2,500 Bosch automobile workers in Bangalore begins after tool-down strike. Bosch wanted to outsource certain work-steps and started to dismantle machinery.
30th of September
Agreement and end of lock-out / protest camp. Workers sign bond; 18 trainees are taken back; 15 dismissals revoked and turned into suspension; total 44 permanent workers now still suspended. ‘No work, no pay’ plus one daily wage per day wage reduction as penalty. Maruti says that the 33 days lock-out created 150 million USD loss (22,000 cars).
The Second Occupation: 7th of October to 14th of October
3rd of October
On the first day of work after the lock-out / protest camp Maruti management refuses entry to the 1,200 workers hired through contractor who took part in the protest and previous occupation. Inside the factory Maruti decided to shift a lot of workers from one work-station to the other, which caused discontent, so did the company move to suspend the company bus service, which fetches workers who live further away.
3rd to 7th of October
In frustration and at the end of financial resources around 100 workers hired through contractor take their final dues, while the rest puts pressure on company and fellow workers inside the plant. Contractors try to prevent workers to get to the Maruti gates by threatening them with violence.
7th of October
Workers inside Maruti Suzuki Manesar plant, Suzuki Powertrain, Suzuki Castings and Suzuki Motorcycles occupy their factories in support of the ‘locked-out’ temporary workers at Maruti. Workers at Omax Auto, Lumax DT, HiLex, Lumax, Endurance Technologies, Degania Medical Devices, FCC Rico, Satyam Auto go on solidarity strike, a total of more than 10,000 workers.
There are an estimated 2,000 workers inside the Maruti Suzuki Manesar factory. This includes about 700 regular workers and also the workers newly hired during the 33 days of lock-out.
8th of October
The company uses the media to claim that the workers are indulging “in several random acts of violence and damaged property inside the factory premises.” “The agitating workers attacked co-workers, supervisors and executives in multiple incidents of violence.” They claim to have ‘rescued’ 350 workers from the factory with the help of the police.
9th of October
Maruti Suzuki India dismisses 10 workers, terminates five trainees, suspends 10 and ‘rescues’ another 100 employees from the plant. Still around 1,500 workers inside and over 1,000 workers outside the factory. Newly hired workers inside the plant ‘fraternise’ with strikers. Meanwhile armed labour contractors (Tirupati Enterprises) fire gun-shots and throw bottles at striking workers outside the Suzuki Motorcycle plant. At least three workers get injured. Police lets attackers get off.
10th of October
Occupations at Powertrain, Motorcycles and Maruti Suzuki continue. Maruti officials announce, that they ‘will need the police to evict the workers”. Police is overstretched due to election time in Hirsa, another district in Haryana, ‘private bouncers’ are hired to keep people out of the industrial area of Manesar – comrades say that the ‘atmosphere is tense’. The Haryana labour department issues a ‘breach of settlement’ notice on striking workers.
11th of October
Due to the halt in supply of diesel engines and transmissions from Suzuki Powertrain India, the production at Maruti’s Gurgaon plant falls to 1,000 units against a normal daily production of 2,800 units. The local class of land-lords and village hierarchy mobilises against the strike: village councils in four villages around Manesar write to the state authorities to ‘find a quick resolution to the strike’. More physical threats from local contractors / village leaders on striking workers.
12th of October
Production in Gurgaon plant falls to 600 units.
13th of October
Maruti announces to shut Gurgaon plant due to lack of parts after five days of strike at Suzuki Powertrain. Some models (M800, Omni, Eeco and Gypsy) do not need parts from Suzuki Powertrain, but their production volume accounts only for a small share. Maruti Suzuki suppliers in turn start to shut their plants, for example Sona Koyo. The elections in Hirsa district are over. At a gate meeting main trade union leaders announce that they will bring the whole of Gurgaon to a stand-still if the police touches the workers inside the factory.
14th of October
Prime Minister Manmohan Singh observes regarding Maruti, ” Labor unrest is a matter of serious concerns, we need to address it efficiently.” 18 workers at Powertrain and 10 at Motorcycle plant are dismissed in the morning. One office member of the MSEU union arrested from his house at 2 am. Raids also take place at houses of other MSEU representatives. More cops enter Manesar, they take down the workers’ food-kitchen, which had supplied around 4,000 workers at Powertrain and Maruti Suzuki plant. There are said to be around 1,500 to 2,500 cops inside the Maruti factory now, they shut down access to water, canteen and toilets. Late at night workers decide to leave the factory and continue strike outside. Maruti complains that some ‘robots have been damaged and machine settings altered’. Earlier the day, according to the media, over 100 analysts, investors and fund managers of Maruti Suzuki participated in a conference call with Sonu Gujjar, president of Maruti Suzuki Employees Union, to ‘talk about the situation’. No leaders of the main trade unions around.
15th of October
Workers at Powertrain and Motorcycles decide to end their occupation and continue strike outside. The MSEU publishes a communiqué saying that they stick to the unity between temp workers and permanents and that they call all trade unions to show support. The AITUC says: “We will observe a solidarity day on October 17”.
The Second Protest-Camp / Strike: 16th of October to 21st of October
16th of October
Maruti workers decide to celebrate Diwali as a black day if demands not met. Maruti announces that “Production has started in a limited way at the company’s plant in Manesar. To start with, the weld shop has been made operational.” Production in Gurgaon resumes, too, although only those models which do not need parts from Powertrain Suzuki Powertrain. Meanwhile in nearby NOIDA several hundred workers at solar-panel and optical disc factory of the multi-national Moser Baer go on strike and demand higher wages.
17th of October
Talks at Maruti between management and union reps fail. The trade union ‘day of solidarity’ takes place: an afternoon (and after work) rally in Gurgaon, several thousand union members from Gurgaon factories and students attend.
18th of October
The company claims that now 400 workers work in the Manesar plant and that 1,700 cars have been produced in Gurgaon. An two-hour tool-down strike announced by the main trade unions were called off, because ‘management entered negotiations again’.
19th of October
Maruti announced that work-force in Manesar is at 600 and that they rolled out 200 cars. Suzuki also claims that production has been started at Powertrain, but the president of the Suzuki Powertrain India Employee Union says that no work happens at the plant apart from cleaning.
20th of October
A dozen unions in Kolkata announce solidarity rallies for the Maruti workers. Labourstart campaign delivers more than 4200 letters to local management in less than 24 hours, complaining about the repression.
21st of October
Agreement in Manesar: the management agrees to take back 64 permanent workers, but another 33 will remain suspended (30 from Maruti, 3 from Powertrain). The 1,200 workers hired through contractors are supposed to be taken back on. Bus service is supposed to be provided again. Instead of recognising MSEU the company will set up a ‘grievance committee’ and ‘labour welfare committee’ with “equal representation from the management and the workers . Presence of a Labour Officer from the state government will be a key comforting factor”. Strikes at Suzuki Powertrain and Suzuki Motorcycles are also called off. The negotiations are said to have been a 42 hours marathon during which workers representatives were put under pressure of ‘pending arrests’ and ‘no permission to leave the venue of negotiations’.
22nd of October
Production resumes in Manesar.
Comments
* Links, Videos and Documents –
* Links for the Debate
http://www.radicalnotes.com
http://www.facebook.com/groups/WithMarutiWorkers/?ref=ts
http://kafila.org/2011/09/06/speed-and-control-at-manesar-why-is-the-maruti-suzuki-management-keeping-workers-out-of-its-factory/
* Videos
http://www.ndtv.com/video/player/news/truth-vs-hype-maruti-trouble-at-the-plant/214402
http://www.radicalnotes.com/journal/2011/10/21/working-conditions-maruti-suzuki-english-subtitles/
http://www.radicalnotes.com/journal/2011/10/20/video-maruti-suzukis-attempt-to-suppress-workers-struggle-subtitled/
http://www.radicalnotes.com/journal/2011/10/18/october-17-gurgaon-rally-in-support-of-maruti-suzuki-workers/
* Documents
17th of June Agreement
The 11 terminated workers will be taken back, but enquiry proceedings will be initiated against them and “appropriate disciplinary action” will be taken. Regular employees will be considered to have resumed work on June 17th, but actual shifts will resume from midnight on June 18th. An extra day of work on June 19th will be required to compensate for not working on June 17th.
In accordance with the provisions of the Payment of Wages Act, 1936 and the standing orders of the company, workers participating in the strike are liable to a fine of three days wages for every day of work lost. However, it was agreed that, for the moment, only ten days’ wages will be deducted (ie one day’s wage for each day of the strike). The remaining amount of the fine will be waived if, and only if, the workers maintain good behaviour and discipline, and abide by the rules of the company.
In accordance with the principle of “no work, no pay”, the workers will not be paid for the days they were on strike.
The workers agreed to maintain discipline, ensure expected levels of production and not indulge in any individual or collective activities that would hamper the normal functioning of the factory. The management also agreed not to behave badly or hold a grudge against the workers.
The agreement will be taken as a final resolution of all disputes between the workers and the management.
30th of October Agreement
The details of the settlement are as below:
1. 15 workmen who have been dismissed shall be reinstated and placed under suspension and impartial inquiry will be initiated against them.
2. 18 trainees who have been terminated will be reinstated.
3. 29 workmen placed under suspension will remain under suspension and face impartial inquiry.
4. On the principle of “no work, no pay”, no workman shall be eligible for wages from August 29 until the day of reporting for duties. In addition, a penalty of “deduction of wage for one day” shall be imposed upon them.
5. All workmen shall sign the revised good conduct bond and join duties with effect from October 3.
Good Conduct Bond*
In Terms of Clause 25(3) of the Certified Standing Orders
I,………………………. S/o…………………………. Staff
no…………. do hereby execute and sign this good conduct bond
voluntarily in my own volition in accordance with Clause 25(3) of the
Certified Standing Orders. I undertake that upon joining my duties I shall give normal production in disciplined manner and that I shall not resort to go slow, intermittent stoppage of work, stay-in strike, work to rule, sabotage or otherwise indulge in any activity, which would hamper the normal production in the factory. I am aware that resorting to go slow, intermittent stoppage of work, stay-in strike, or indulging in any other activity having adverse effect on the normal production constitutes a major misconduct under the Certified Standing Orders and the punishment provided for committing such acts of misconducts includes dismissal from service without notice, under clause 30 of the Certified Standing Orders. I, therefore, do hereby agree that if, upon joining my duties, I am found
indulging in any activity such as go slow, intermittent stoppage of work, stay-in strike, work to rule, sabotage or any other activity having the effect of hampering normal production, I shall be liable to be dismissed from service as provided under the Certified Standing Orders.
Date:……………………
Signature of the workman.
“I agree that if on joining duty I am found indulging in go-slow, intermittent stoppage of work, stay-in strike, work to rule, sabotage or otherwise indulge in any activity which would hamper the normal production in the factory, I will be liable to be dismissed from service without notice, as provided under the certified standing orders.”
(i) Apply or obtain leave on a false pretext.
(ii) Lack of proper personal appearance, sanitation and cleanliness including proper grooming.
(iii) Conduct in private life prejudicial to the reputation of the company.
(iv) Remaining in a toilet for a substantially long period of time.
(v) Habitual neglect of cleanliness.
* Contribution for the Debate: A Critique of the ‘Balance-Sheet of the Maruti Suzuki Struggle’ in GurgaonWorkersNews no.41 –
We thank the comrades who took the time to write down a contribution to the debate. We did not yet find the time for a proper reply, but hope that a reply can partly be found in the political thesis of this newsletter and the Faridabad Majdoor Samachar article, following their contribution below.
ARE THE MARUTI WORKERS REALLY DEFEATED?
A DISCUSSION ON “BALANCE SHEET OF MARUTI SUZUKI WORKERS STRIKE”
Published in GurgaonWorkerNews No 41 July 9, 2011
1. We think that this is very unfortunate that the comrades who have drawn up the “balance sheet” have termed this struggle as a defeat. We have been told that “Despite the young workers’ courage and the fact that the company was hit at times of full-capacity the strike ended in a defeat for the mass of workers.” Why? They continued in that line, “They did not enforce any betterment of conditions and wages, which was their main concern.” Is it really a fact that the Maruti workers started this strike for “betterment of conditions and wages” as has been told by the comrades. No, the comrades have completely overlooked the fact that the workers did not start the strike with any such demands. The strike started spontaneously because the management started to coerce the workers to join the management controlled union. It is also a fact that the workers, either a section or whole of them, were trying to organise themselves in a separate, fighting union. Even if it is true that only a section of workers were active in organizing this new union, the fact that the new union had the backing of overwhelming majority of workmen had become evident from later facts. So, actually the strike was not at all for any demands, like wage revision or improvement of their service conditions as has been assumed by the GurgaonWorkerNews. The workers went for a strike to foil the conspiracy of the management to force them into joining the management-controlled union; the workers went for the strike to preserve their right to form their own union, they fought for their control over their own struggle. Had they achieved their demand? Definitely not completely. But, definitely they have foiled the plan of the management and they have done it by fighting alone against such a mighty management like Suzuki management and who had the complete backing of the Government of Haryana, and definitely we can well assume, the overt and covert backing of the Central Government also, which is very likely in this era of Globalisation. Yes, it is fact that the workers could not force the management to recognize the new union. Actually they did not wage their strike to do that. They did not heighten the movement for recognition of their union by management. They kept themselves within the limit to foil the conspiracy of management. They have done it and the workers are not only still organised, they have consolidated their strength and basically they have formed their union through the strike, whether they have got the formal registration or not is immaterial to us. We have seen in the meeting held just after the withdrawal of the strike, the workers themselves could recognize and appreciate this fact that not the registration, but this unity shown and achieved during this 11 day is the real union. But, unfortunately our comrades could not appreciate it. It is obvious that the struggle between the workmen and the management will continue regarding the organisation of the workers, the result of which will decide the fate of their next struggle, struggle for their economic demands. However, for the present the workers have foiled the conspiracy of the mighty Maruti management, they are still united and organised, consolidated their strength and trying to launch their next battle. These achievements are no mean achievement, considering the disintegrated, unorganized state of the working class movement through which we are passing now. The representatives of big bourgeoisie will definitely try to belittle the achievement. Should we also do likewise?
2. Another important achievement of the workers is that they have forced the management to take back the dismissed workmen. It is important because it will help to retain their strength. Had the management been able to dismiss the leadership it would have helped them to advance in their conspiracy to break the unity of the workmen, conversely by forcing the management to take back the dismissed workmen, the workers have been able to advance in the direction of organisation and also future struggle.
3. Even if the workers had not achieved anything palpable (“material gain”), even if they had to go down fighting, would their struggle lose all significance? Should the real representatives of working class think in that way? For one moment remember how many struggles of historic significance had been actually defeated in terms of achievements. No, do not think at all that we are comparing this struggle with any such struggle of historic significance. What we are trying to impress is simply the fact that for anybody who is fighting not for any improvement of the condition of working class keeping the system of exploitation intact but for the abolition of the system of exploitation as a whole, it is not important at all what gains in wages or service conditions the workers are now achieving, the only important thing to them should be whether the workers are uniting and organizing themselves more and more, whether their struggling unity and organisation is preparing them to fight the capitalists, helping them to discover their real strength, helping them to stand on their feet, build their own, independent organisation which will lead them in their struggle for the complete emancipation from the exploitation of the capitalist class. Definitely, these spontaneous, economic struggles of the workmen, especially in the narrow factory plane will not itself advance to the struggle of working class for complete emancipation. But, definitely, through these struggles the workers are awakening and from among these fighting workmen, will awaken the advance, class conscious workers of future working class struggle. Those, who are fighting for the complete emancipation of working class, should not evaluate any struggle of workers from what material gains in terms of improvements in the condition of the workers the struggle could achieve or not, but whether the struggle will help the workers to advance in the long path of struggle for complete emancipation.
4. Undoubtedly there is a tendency among the workers in general to rely on the formal recognition or registration from the Government. Definitely, it is a sign of their backwardness, which we have seen amongst the fighting workmen of different factories, that too, of different areas of the country, who think that the formal registration will help them to maintain their union, will help them to resist the attacks of the management to break their union. We know very well that the real strength of the workers lies in their struggling unity, not in any formal registration or recognition and so the workers should not have depended so much on the registration of the union. However, is it not natural that the workers will display such examples of backwardness, considering the state of the working class movement in which they are in. Is there any real Working Class party to help? To educate these fighting workers? Are there any working class organisations which have the real organic link with the masses of workers, upon whom the workers can depend and also depend in reality? No. There is no force to educate, to guide the fighting workers in their struggle, no force to develop the workers struggle into a real struggle for the complete emancipation from exploitation. The workers are struggling and also learning from the experience of their struggle and life on their own. So, in this process it is very likely that they will make mistakes, but we must keep faith on them and help them. Can we help them by belittling their achievements and inflating their weaknesses, backwardness etc?
5. The workers are learning through their experiences of struggle. Summing up their experiences of the betrayal of established parties, especially the left parties, the workmen are trying to establish their control on their organisation and struggle. The Maruti workers are also showing such signs in their struggle. They have depended somewhat on some establish parties to get the registration, but in essence maintained their independence over their struggle. This is the most significant feature in this struggle. However, the Gurgaon Workers News has rightly pointed out that “is naïve to repeat the phrase of ‘betrayal’ of the main unions.”, the workers should free themselves from any dependence on the established parties and more and more depend on their own strength. We do not know what they meant by ” ‘political’ experience of self-organisation”, but it is undoubtedly true that political consciousness of workers would have helped the workers not only to free them from the influences of the old established parties but also to free themselves from the influences of the reformist politics of these parties. In fact, the dependence of the workers on the legal structures is an apt example of such pernicious influences of reformist politics practiced by the established parties, especially the so-called ‘left’ parties. The political consciousness, more correctly, class consciousness of the workers will help them to free themselves of the pernicious influences of the politics of the establish parties. Not only will it help them to build their struggle for complete emancipation, but also help them to develop the present economic struggles. Once the workers will become conscious about the real class character of the present legal structures, the class character of the established parties, especially the so-called left parties, It will help them to free themselves from dependence on the legal structures ( like dependence on the formal recognition of the union as shown by the Maruti workmen ), to understand the conspiracy of the established parties, and also help them to form and develop their independent organisation, free from the control and influence of the established parties. But how this political consciousness will grow among the workers? Here, we face a paradox. To make the workers really politically conscious we need a real working class party. But, how can a real working class party develop without a substantial segment of class conscious workers, especially in the present situation of defeat of working class movement? So, it is very natural that the workers will fight on their own strength, with the instruments of struggle which they are building up from their past experience and they will also learn from their present experience, from the weaknesses, defeats of the present struggle. Definitely it is tortuous path, but probably inevitable also. Maruti workers are part of this struggle, part of the process of new awakening of working class, who are awakening not only in our country, but in different countries throughout the world. We must help them in this process and to do that definitely we should criticize their weaknesses, but we shall have to do that from a class point of view and obviously upholding advancements they are making. We shall have to understand the real condition of present working class movement, analyse the strength and weaknesses of their movement against this backdrop and understand the achievements and weaknesses of the workers. Otherwise, we will not be able to really help the workers in their struggle.
———
* Article in Faridabad Majdoor Samachar with Workers’ Reports after the first Factory Occupation in June –
FROM HONDA TO MARUTI SUZUKI: A WIDE ANGLE VIEW OF CORPORATE STRATEGIES
(New Series No. 277, July 2011)
WHAT THE MARUTI BALANCE SHEET SHOWS
The 300-acre Maruti Suzuki factory in Gurgaon houses three plants and produces 7 lakh cars a year. The engine plant alone has a manufacturing capacity of 7.5 lakh engines a year.
The 600-acre Maruti-Suzuki plant in Manesar started production in February 2007. This factory houses Maruti’s newest assembly plant with a capacity of 3 lakh cars a year.
Another assembly plant in this factory will begin production in March 2012 and will have a capacity of 2.5 lakh cars a year. The Suzuki Powertrain Diesel Engine factory adjoins Maruti’s Manesar factory. This is a joint venture of Suzuki Motors (70%) and Maruti-Suzuki (30%) and has a capacity of 3 lakh engines a year.
12.7 lakh Maruti-Suzuki cars were produced in 2010-11 – 2.7 lakh units more than the installed capacity of its plants – and representing almost half of all cars produced in India.
Around 1.4 lakh Maruti-Suzuki cars were exported to 120 countries in 2010-11.Maruti earned slightly more than Rs.40,419 crores from sale of its cars during 2010-11.
Maruti-Suzuki contributed a total of Rs.4290.81 crores to the national exchequer by way of excise duties, and paid Rs.820.11 crores in taxes to the Haryana Government in 2010-11.
The company declared a total share capital of Rs.144.46 crores. The value of a Rs.5/- share went up to Rs.79.22 during 2010-11.
After deducting payments to employees (Rs.703.62 crores), bank interest payments (Rs.24.41 crores), costs of raw materials and plant maintenance (Rs.27,576.13 crores) and other expenses, the company declared a net profit of Rs.2288.64 crores.
WHAT THE BALANCE SHEET DOESN’T SHOW
Maruti-Suzuki had 8,500 employees as of March 31, 2011. Only 3,200 of the total of 8,500 employees are factory workers – 2,300 at the Gurgaon factory and 950 at the Manesar factory.
Apart from these 3,200 regular workers, every other worker in the Maruti factories is a contract worker, hired through a labour contractor.
Maruti first started hiring contract workers in 1977. In 2001, after a strike at the Gurgaon factory which was probably engineered by the management and was ruthlessly crushed, 1250 regular workers were laid off. Another 1250 workers were laid off in 2003. As of 2007, the Gurgaon factory had 1,800 regular workers and 4000 contract workers. The number of contract workers at the present date is not known.
According to figures from the ILO, regular workers comprise only 15% of the Maruti-Suzuki factory workforce – 85% are contract workers. This is a much lower proportion of regular workers than in companies such as Nokia (50% regular workers) and Ford (25% regular workers).
Regular workers in the Maruti-Suzuki factory are paid an average monthly basic salary of Rs.5,300/- and an “attendance allowance” of Rs.8,900/-. An amount of Rs.2,500/- is deducted from the salary for every day of non-attendance other than earned leave.
Contract workers hired through a labour contractor are paid an average monthly wage of Rs.7,200/- (for those with an ITI diploma) and Rs.6,200/- (for those who do not have an ITI diploma). There is no provision for leave, and an amount of Rs.2,000/- per day is deducted for absence from work.
THE ARITHMETIC OF PROFIT
Assuming that none of the workers took leave, the total amount paid out by Maruti-Suzuki to their regular factory employees during 2010-11 is Rs.54.52 crores. Assuming that the number of contract workers today is 8,000 (twice that in 2007) and calculating at the higher rate (Rs.7,200/- per month) the total amount paid to the contract workers in 2010-11 is Rs.69.12 crores. The total amount paid to factory workers (Rs.123.64 crores) represents 5.4% of the profits of Rs.2,288.64 crore made by Maruti-Suzuki in the same period.
THE MARUTI FORMULA- “LEAN MANUFACTURING”
One year ago, it took a herculean effort for the Manesar plant, working two shifts on the main (automated) production line, to make 1,100 cars a day. Today, the plant rolls out 1,200 cars every day from the main line and another 150 from the manual line. How has the pace of production has been stepped up?
Maruti Production System or MPS draws learnings from its parent company Suzuki Motor Corporation’s concepts on `lean manufacturing’ under Suzuki Production System (SPS).
Setting trends in new products and achieving customer delight starts with Manufacturing Excellence and Maruti’s manufacturing excellence hinges around four important pillars-Cost, Quality, Safety and Productivity.
Every employee working on the line is ‘cost sensitive’ and functions in capacity of a Cost Manager. He is a key contributor in suggesting how to keep costs of production under control.
A product of poor quality requires repeated inspections, entails wastage in terms of repairs and replacements. “Do it right first time,” is the principle followed to avoid wastage. To ensure quality, robots were devices and deployed, especially where they reduced worker fatigue and were critical in delivering consistent quality. With consistent improvements in the plant the company was able to manufacture over 600,000 vehicles in 2006-07 with an installed capacity of just 350,000 vehicles per year.
“Home or work place; Safety takes First Place”. This has been the motto of the company where safety is concerned. Maruti attaches great significance to safety of its people and strongly advocates that safety at work place adds to quality of the products and improves productivity of the plant significantly.
In the Japanese manufacturing system, the central role is accorded, not so much to Quality, Productivity or Cost, but to Safety. When process flow, lay-out and systems are designed for maximum safety, they automatically contribute to better quality and productivity.
– from http://www.marutisuzuki.com/lean-manufacturing.aspx
The deepening economic crisis is justification enough for companies like Maruti to push even harder to cut costs and increase production. Shorn of jargon, Maruti’s much-lauded lean manufacturing system is the tried-and-tested traditional system of squeezing the workers through increasing workloads, cutting wages and benefits, undercutting investments in safety and increased casualisation of the workforce.
Here’s what lean manufacturing looks like on the factory floor.
The paintshop at the Manesar plant is a schizophrenic combination of cutting-edge robotic technology and brute physical labour. One one side are 12 painting robots. On the other, are workers carrying 25 kilo headloads of used screens up two flights of stairs and returning with a 30 kilo load of clean screens. Each worker has to carry 70-80 screens up and down the stairs, working an extra hour without pay if the job is not done by the end of the shift. The lunch-break (30 minutes) and tea break (15 minutes) are not counted as part of the working time on the shift.
The Quality Maintenance Unit employs 95 workers hired through a labour contractor. Their job includes cleaning out the tanks that hold thinners and solvents. They are always on the C-shift – from 12.30 in the night to 8.30 the next morning. Workers on the C-shift work non-stop. There are no breaks for food or tea. The food allowance of Rs.44/- that they used to be given has now been slashed to half. By the end of the shift, they are exhausted, giddy and nauseous from the chemical fumes they inhale. Workers in the Quality Maintenance Unit put in 32 to 192 hours of overtime every month, for which they are paid only Rs.28/- per hour, well short of the legal minimum of 1.5 times the normal wage. For many of these workers, the shift can extend to 17.5 hours of non-stop work without breaks or food.
“The tea break is seven minutes long. In that time, we have to run to the canteen, line up for tea and a snack, use the toilet and get back to the assembly line – and they expect us to be back with a minute to spare.”
“The line moves so fast that there’s no time even to scratch an itch…”
“The company gave us all mobiles as gifts to celebrate reaching the one crore production mark, but what’s the use – we don’t have the time to call anyone.”
WORKERS AT THE MANESAR PLANT, SPEAKING TO FMS
Casual workers hired through a labour contractor are paid an average monthly wage of Rs.7,200/- (for those with an ITI diploma) and Rs.6,200/- (for those who do not have an ITI diploma). Casual workers on the A and B shifts are entitled to free meals at the canteen. There is no provision for leave. Wages for the day, and an extra penalty of Rs.2,000/- are deducted for every absence from work. Any protests or arguments with the contractor are dealt with by immediate dismissal.
Regular workers are not much better off. Their package consists of a basic pay of Rs.5,300/-, an incentive/attendance allowance of Rs.8,900/-, a house rent allowance of Rs.1,600/-, a Dearness Allowance and an allowance for children’s education, adding up to between Rs.17,000 and 18,000/- a month. Although their contracts include provisions for paid leave and casual leaves, each day off work results in a deduction of Rs.2,200/- from the incentive allowance. The entire amount of Rs.8,900/- is forfeited if a worker takes more than four days off in a month.
Regular workers cannot be threatened by dismissal, but are harassed and humiliated by supervisors who abuse and manhandle them, arbitrarily move them from one assembly line to another, and report them to managers or the HR Unit for concocted offences.
THE STRIKE
The workers at the Manesar factory started a new union in April 2011. The membership included both regular workers and casual workers hired through labour contractors. The management refused to recognize this union. On June 4, 2011, the workers stopped work. The A shift was just ending and the workers on the B shift had all come in. Workers on the C-shift were quickly contacted over the phone and asked to join the strike. Before the management realised what was happening, more than 2,000 men – regular workers, apprentices, trainees and contract workers from all three shifts – had occupied the factory, sending the management into a complete panic.
As the strike went into its second week, the Haryana Government declared it illegal, but was unwilling to intervene as they had done in the Honda strike. Although police were stationed in the factory premises, the management was reluctant to force the workers out of the factory, given the the risk of damage to the equipment. Equally, the workers were determined to hold their ground inside the factory – everyone was aware that being forced or persuaded to vacate the premises would be the beginning of the end, as it had been for striking workers in Rico Auto, Denso, Viva Global, Harsurya Healthcare, Senden Vikas …. crushed protests that left workers far more vulnerable than before.
By the time the strike entered its tenth day, the factory had lost Rs.600 crores and Maruti shares had plummeted in value. It was obvious that the Maruti management and the government were helpless in the face of the workers’ determined refusal to surrender.
The agreement between the workers and the management that ended the strike on June 16th does not reflect this situation. No one reading this extraordinary document would guess that the workers were in a strong bargaining position while the management and the government had their backs to the wall. Instead, those who brokered this “return to normalcy” created a scenario that disempowered the workers and made it seem as if it was their inability to hold out any longer that brought them to the negotiating table.
THE AGREEMENT
The signing of the agreement and the fact that the management agreed to take back the 11 office-bearers of the new union who had been dismissed on 6 June, has been hailed as a victory for the workers by some commentators.
But the terms of the agreement suggest otherwise.
A bitter “victory”
The 11 terminated workers will be taken back, but enquiry proceedings will be initiated against them and “appropriate disciplinary action” will be taken. Regular employees will be considered to have resumed work on June 17th, but actual shifts will resume from midnight on June 18th. An extra day of work on June 19th will be required to compensate for not working on June 17th.
In accordance with the provisions of the Payment of Wages Act, 1936 and the standing orders of the company, workers participating in the strike are liable to a fine of three days wages for every day of work lost. However, it was agreed that, for the moment, only ten days’ wages will be deducted (ie one day’s wage for each day of the strike). The remaining amount of the fine will be waived if, and only if, the workers maintain good behaviour and discipline, and abide by the rules of the company.
In accordance with the principle of “no work, no pay”, the workers will not be paid for the days they were on strike.
The workers agreed to maintain discipline, ensure expected levels of production and not indulge in any individual or collective activities that would hamper the normal functioning of the factory. The management also agreed not to behave badly or hold a grudge against the workers.
The agreement will be taken as a final resolution of all disputes between the workers and the management.
The story of the Maruti Suzuki strike of 2011 is very similar to that of the Honda strike of 2005. The Honda workers were persuaded by the so-called negotiators to come out of the factory. Once they did, they were mercilessly beaten by the police. By brokering this agreement, the self-appointed negotiators in the Maruti case have dealt an even more lethal blow to the workers’ struggle. The Maruti Suzuki management is exhibiting care and concern for workers’ welfare in the immediate aftermath of the strike. If the Honda case is anything to go by, this phase will be short-lived, and will be followed by a further tightening of the screws.
The 1,700 Honda regular employees who launched the strike in 2005 were workers on the factory floor. Of the 1,800 regular workers on the Honda rolls today, a large segment works as supervisors of contract workers hired through labour contractors. For instance, the motorcycle engine assembly plant at the Honda factory in Manesar is run by 4 engineers, 12 regular workers and 110 casual workers hired through a labour contracting company. Each shift in the assembly line in the no.2 motorcycle plant has 8 staff, 3 line leaders, 4 regular workers, 4 casual workers hired directly by the company and 101 contract workers hired through a labour contractor. Workers hired through labour contractors are responsible for the bulk of the production in the Honda plant. There are 6,500 such workers on the production line, and another 1500 in ancillary departments.
THE ISSUE IS GLOBAL
Regular workers and irregular workers. Casual workers employed directly by the company and contract workers employed through a labour contractor. Registered contractors and unregistered contractors. Workers who are entitled to PF and ESI, and workers who are not entitled to these benefits….
As many as 75% of the factory workers workers in Delhi, Noida, Gurgaon and Faridabad are invisible in government statistics. The vast majority – over 80% – of these workers are paid less than the statutory minimum wage. Shifts of 12 to 18 hours are the norm, and overtime is compensated at the same rate as regular duty and not at twice the regular rate as required by law.
The situation of workers in Maruti Suzuki and Honda is mirrored in thousands of small and medium factories operating within the 300 or so square kilometres of Delhi and the NCR, that are connected to other such operations in other cities thousands of kilometres away. All of them are struggling against similar strategies of exploitation and resisting attempts to undermine solidarity and unity.
Yet, it is this globalisation of oppression that is creating the conditions for solidarity across boundaries of race and nation, across different industries, different sectors, different companies.
————-
* Short Reports by Workers in Automobile Factories in Manesar/Faridabad, Distributed by FMS Shortly before Dispute at Maruti Suzuki Broke Out –
Factory Reports – FMS no. 274, April 2011
Flash Electronics (Automobile Parts Manufacturer)
(Plot 3, 8, 9, Sector 27 B, Faridabad)
Together with the general shift of 12.5 hours there is a day shift and night shift of 12 hours each. Those workers who start at 8 am in the morning are supposed to finish at 8 pm, but often they are made to work till 1 am or 5 am next morning. On Sundays workers have to work 8 to 10 hours. There is a lot of pressure to meet production targets. The foremen, supervisors and manager swear at the helpers amongst the casual workers, the general manager also slaps them. In order to meet production targets the general manager also slapped a permanent worker. There are 60 to 70 power presses from 20 to 1,000 tons. Most of the presses are old and there are no safety devices. Most of the presses are run by helpers. On the presses, too, workers have to stay longer after 12 hours shifts, up to 21 hours. The daily pressure, the little space etc. results in many accidents. Parts break, people accidentally press the pedal while hastily taking out finished parts, pressure from the supervisor… one-two-three fingers, thumbs, fingers of both hands get cut off. Each months two-three-four workers cut their hands. If this happens the company does not bring the worker to the (official) ESI hospital, they don’t fill in the accident form, they send the worker to a private hospital in Sector 16. The tools of the power presses weigh 50 to 80 kilos and have to be removed by hand. Hands and feet get squashed. The supervisor swears at the injured worker that the injuries are his/her own fault of having been careless. The injured workers do not receive wages during time of treatment and when not able to work. The company does not pay compensation for lost fingers. When workers want to go to the ESI hospital after first treatment in the private hospital, they demand the accident report, but neither doctor nor company provide this. They also don’t provide the necessary documents for the ESI smart card. On 28th of April a worker operating a power press cut off three of his fingers. He was sent to a private hospital in sector 16 for treatment… We work 100 to 225 hours of overtime each month, paid single rate. From overtime each month 400 to 500 Rs get embezzled. Last year’s DA (inflation compensation) of July was not paid before October and this year’s January DA has not been added to wages yet (March wages). Casual workers received pay-slips in January 2011, but the overtime was not mentioned, no ESI number or PF number given. Casual workers are dismissed after seven months of employment and are rehired after two months of break. There are workers who work continuously in the factory, but their contributions for PF and ESI are not deducted for these two months (meaning that they are officially not employed). There are 100 permanent workers and 1,000 to 1,200 casual workers employed. We produce parts for two and three wheelers. There are 300 to 350 operators amongst the casual workers, the rest are hired and paid as helpers. The operators get 15 Rs per 12 hours shift for tea, 30 Rs for a 17 hours shift and 50 Rs for a 21 hours shift. The helpers get nothing. In Badarpur there is another Flash Electronics factory manufacturing auto meters and they are about to open another plant in Faridabad DLF Industrial Area.
Omega Auto Worker
(Alley no.2, Krishna Colony, Sector 25, Faridabad)
The female workers in this workshop are paid 3,500 Rs, the male workers 3,800 Rs. There is a drill, a welding machine, a lathe, a power press and three CNC machines. Women workers are also employed at the CNC machines. No ESI, no PF for the workers. We work from 8:30 am to 8:00 pm. We manufacture small metal pipes which are used as engine parts for oil and air supply. Our pipes go to Imperial Auto, a different supplier, and from there to Honda, Hero Honda and Maruti Suzuki.
Munjal Showa Worker
(Plot 26, Sector III, IMT Manesar)
There are three 8-hours shifts. After Holi there was a lack of workers. So since 21st of March workers are forced to work double-shifts of 16 hours. They don’t let workers leave, they use physical force to keep people from leaving. We manufacture shockers for Honda, Hero Honda and Yamaha. If you have to stand upright for 16 hours and handle these shockers, this causes great pain. They don’t pay extra for food. The overtime payment is 38 to 43 Rs per hour.
Track Auto Components
(Plot 21, Sector VII, IMT Manesar)
Some power presses are equipped with security devices for health and safety, but some operate with double stroke. Due to the heavy vibrations from the presses a metal part fell from some storage space and hit a worker. The injured worker had to wait, because the van which is usually meant for ambulance transport was used to transport work materials. They had to mend his foot with 12 stitches. On 18th of April a worker cut off four of his finger at a power press. If you have to start working at 7 am you have trouble to prepare your meals. In January they said that they will open a canteen on the third floor, but now they installed a sheet rolling machine there instead. The company hired 30 to 40 staff directly, 600 workers are hired through five different contractors. We manufacture parts for Maruti Suzuki, Honda and Hero Honda. The drinking water is not alright. The filter machines has been faulty for the last 8 months. The workers of the upper floors have to come to the ground floor if they need a toilet – there are always queues. On the upper floor under the roof there are 18 power presses, but not a single fan. On 26th of April Maruti Suzuki sent an audit. Those workers who operate the 160 ton power presses for Maruti parts were given ear plugs and helmets – after the Maruti reps had left the Track Auto managers took the helmets away again. The workers in the press shop often demanded ear protection, but the company does not give out any.
Honda Motorcycles and Scooter (HMSI) Worker
(Plot 1 and 2, Sector 3, IMT)
After increasing production in December last year the company again increased it in April 2011. In the motorcycle plant we had to produce 1,025 instead of 1,000 vehicles, now fixed production target is 1,100. The company swalloed the time to drink water, go to the toilet and get a breath in. Most of the production increase is enforced onto the backs of the 8,000 workers hired through contractors (this includes drivers, canteen staff), and they don’t see a paisa more for it. The illusion that some of the workers hired through contractor employed in the Manesar plant would be hired as permanents in the new Bhivari plant has imploded. The company policy of: “Use the workers and then throw them away” has proven itself clearly. The annual production target of 1.8 million bikes in 2010 has been brought to 2 million bikes in 2011. Neither the union nor the management has an open ear for the problems of the workers hired through contractor. The assembly lines are stopped by workers, sometimes here, sometimes there. On the 16th of April one production line came to a stand-still several times, instead of 1,100 bikes only 950 were produced.
SKH Worker
(Sector 8, IMT)
This factory is situated on the Maruti Suzuki premises, near the fourth gate. Around 300 workers work on two 12-hours shifts. On Sundays, too, 12-hours shifts. The company pays the overtime at single rate. They have Vishal Power Presses (800 ton model) set up in a production line, with separate die casting tools. If the first press does 1,700 piece, then the last one has to do the same amount. The machines are not supposed to stop. The ‘line must be clear’ all the time [no pieces piled up anywhere, the line moving]. There is no time for getting and drinking water or go for a piss. It’s heavy work, you have to lift the 15 kilo sheet metal by hand. If one piece gets rejected [by quality check], hell breaks lose.
Comments
The following thoughts remain on a rather superficial level due to lack of opportunity for first-hand exchange with workers during the struggle. They are at the same time a call to intensify the debate on an international level.
1) The struggle at Maruti Suzuki was the most important workers’ struggle in India since two decades. For the first time on mass scale the new composition of a young industrial work-force came to itself by confronting the factory regime. They undermined the division in temporary and permanent workers, which had been imposed as a main line of division within industrial working class in India – and not only in India – since the early 1990s. The workers hit the core of the Indian regime’s developmental model, which consists of the integration into the global market and production structure at the highest level of technology and ‘productive cooperation’ – combined with the severe suppression of the aspirations of the work-force, which emerge with this integration.
We say ‘most important struggle’ less because of its quantitative scale, or militancy, or result, but because of its structural character. The struggle brought together the subjective anger of a new workforce with its objective position in the core of the current developmental cycle. Since three decades we witnessed the dismantling of old workers’ core centres, the main struggles evolved as defensive struggles. The centres moved from the textile mill strikes in the mid-1980s (which were undermined by new division of labour between automatised spinning and informalised weaving processes). Throughout the 1990s, the centre shifted to the struggles in the major (automobile) manufacturing companies (Escorts, Maruti Suzuki) [1] against capital’s attack in form of ‘privatisation’, outsourcing, casualisation. These were decades of major defeats of the old trade union movement, which was only able to compensate for their decline by co-managing the emerging class division between a mass of casualised workers and a core of permanents.
We currently see a reversal of the historical trend in automobile manufacturing. From Detroit at the beginning of the 20th century to the Midlands in the UK, to FIATs Turin and Toyota’s factories in the 1950/60s to South Korea and Brazil in the 1970s: while the first generation of car workers produced cars for the middle-classes, the workers of the second generation – through struggles and general productivity increases – were able to afford the product they produce themselves. In India, if at all, this trend has reversed itself, the second generation of car workers is worse off. They are also less attached to company spirits and the automobile dream. At Maruti the various carrots and waiting-loops have lost their gripping effects. The ladder from apprentice, trainee, temp worker, “junior workman” “associate workman”, to the Nirvana of a permanent status or even an award as employee of the year has been broken, the level of casualisation is too high in order to mobilise workers’ illusions. Similarly the patriarchal whip of ‘warning letters’ – three times too late, too slow, too ill and you are out – and other threats have become blunt. Maruti wants to copy the paternalistic ‘Fordist model’ of interference in workers ‘private life’ – workers are supposed to abstain from public activities harmful to the reputation of the company, they have to announce once they are in debts – without being able or willing to pay them the ‘Ford wage’.
The current composition of the workforce at companies like Maruti Manesar plant is the outcome of the defeats and restructuring of the 1980s and 1990s and the further integration into the global production system. It took the working class two decades to ‘find itself’ and turn this ‘precarious, but central structure’ into a more radical basis for its struggle. Current struggles at Bosch in Bangalore or wildcats at General Motors in Gujarat are other indicators that the conflict has returned to the centre again. Here we can see parallels to the strike wave in automobile factories in China in summer 2010. [2]
2) During the last years the divisions between permanent and temporary workers in Gurgaon area deepened. In many cases ‘union recognition’ was enforced by joint-struggles of both categories of workers, but once established, the trade unions could not reverse this trend of increasing separation.
In the few cases where trade unions were established in modern manufacturing industries in Gurgaon area during the last decade this lead to an ‘improvement’ of the position of union members, wage levels rose up to 25,000 to 30,000 Rs, management was able to offer these unionised permanent workers some stability, three-years agreements, regular productivity/sales-related wage hikes. But this ‘improvement’ was paralleled by the reduction of the permanent unionised work-force to about 30 per cent of the total staff. In many cases these workers were granted if not supervisory, but ‘privileged’ position in relation to the increasing mass of temporary workers within the production process, whose wage levels dropped in real terms and hover at about 5,000 Rs. For them ‘three years wage agreements’ have little to do with the reality of frequent job changes and mobility. In many cases the ‘enforcement’ of trade union recognition against the company was only achievable by ‘struggling in unity’ by both permanent and temporary workers, but tragically after establishment the (permanent) workers did not find ways to bridge the widening gap between ‘represented minority’ and ‘marginalised majority’ – see development of the union at Honda HMSI in Manesar. [3]
During the last years, the ‘casualised majority’ of workers appeared several times on the stage of workers’ struggle in Gurgaon and Manesar, e.g. during factory occupations at Hero Honda or Delphi by thousands of temporary workers [4], but in these struggles ‘permanent and temporary’ workers had remained being separated. This was not the case during the current Maruti Suzuki struggle. The material division (quantitative ratio on the shop floor, wages, qualification, origin etc.) between permanent and temporary workers have been less pronounced in the first place. Furthermore, Maruti Suzuki does not seem willing or able to ‘offer’ the young permanent workers a similar ‘privileged’ position (managed by a respectable union body) which permanent workers had been offered during the last two decades. They know that the standards at the central assembly set the standards elsewhere. Both, the objective factors (“ability to finance a division”) and subjective response (“acceptance of division” by workers) were not given at Maruti Suzuki. This is why the struggle carried on.
3) The situation of the global automobile industry makes it difficult Maruti Suzuki to ‘finance’ a class division by granting the permanent workers a privileged position through trade union management. It forces the company to casualise the workforce in the new plants. A draconic disciplinary regime is supposed to impose a more intense combination of underdevelopment (‘speed-up without investment’ of manual work, extension of working hours) and development (automatisation in upstream departments etc.) within the factory. All this fuelled the collective anger.
The conditions have changed quite fundamentally since 2000/2001, when Maruti enforced a major split within the geology of the work-force in Gurgaon or even since 2005, when Honda in Manesar did the same. The global pressure on wages and conditions increased fundamentally with the contraction of markets since the crisis 2008. Due to the lock-out Maruti started production at Manesar ‘Plant B’ three month earlier than planned – a more automatised plant, which was presented as the technological fix to workers’ unrest. Here in an direct sense workers’ struggle pushes capital into aggravation of its contradictions, expansion of productive capacities while reducing its living (and consuming) self. Including the two Manesar plants and the Gurgaon plant Maruti Suzuki’s capacity will be around 1.7 million cars a year, this is nearly as much as the current total domestic Indian market. In July Ford and PSA had announced to each open new assembly plants in Sanand, Gujarat – the market pressure is increasing through overcapacity and potentially swindling demand. The cheap cash for consumers crunches. The Reserve Bank of India has raised interest rates 12 times since mid-March 2010 to rein in inflation, driving down demand for cars. In India about 80 percent of purchases are funded by loans.
The crisis has proven that there is no ‘de-coupling’, meaning that there is no national market or sector or company, which could remain unaffected by the general conditions. ‘Suzuki’ is not a ‘Japanese’ company anymore, the Indian subsidiary accounts for 55 per cent of Suzuki’s global operating income. At the same time its not solely an ‘automobile manufacturer’, which would only depend on car sales. Life Insurance Corporation, ICICI Prudential Life and Bajaj Allianz are among the major shareholders of Maruti Suzuki and the pressure on banking and insurance markets will reverberate within the assembly lines.
Behind the surface of ‘market’ pressures the core of ‘wage’ pressure reveals itself more blatantly on a global level. In September 2011 – while the struggle at Maruti was still intense – the United Auto Workers union in the US agreed on the ‘Two-Tier’-wage-system, which means that newly hired workers will earn only half the wage of the older workers, which will cause an enormous downward pressure on the global wage cascade from the North to the South. These wage pressures are not mediated anymore, with the integration of ‘Indian’ car production into global markets it becomes an ‘immediate’ global wage. Manesar is Maruti Suzuki’s sole global manufacturing base for the A-Star, which exports the compact car to various markets in Western and Eastern Europe, South America, Africa and other parts of Asia. In Europe, Suzuki sells this car as ‘Alto’ and Nissan as ‘Pixo’ – around 9 per cent of Maruti Suzuki’s revenue comes from export.
The squeeze is not solely on wages, but on workers’ brains and muscles. Under these conditions ‘capital has to eat itself’, it has to squeeze workers beyond physical capacities, without re-investments. Within the factory the split (and combination) between development (automatisation) and under-development (manual speed-up, double-shifts) aggravated. After 2008 the work pressure in Manesar increased considerably. Instead of investing into separate production lines, different models were produced at the same ‘flexi-line’, increasing work stress. With an official capacity of 250000 cars, Manesar manufactured 350000 in 2010. Certain departments of the plant, particularly in Plant B, became more automatised after 2010, while the manual operations were simply ‘sped-up’. Workers were more frequently forced to work double-shifts and Sundays, the whole ‘disciplinary regime’ has to be seen on this background.
“The paintshop at the Manesar plant is a schizophrenic combination of cutting-edge robotic technology and brute physical labour. One one side are 12 painting robots. On the other, are workers carrying 25 kilo headloads of used screens up two flights of stairs and returning with a 30 kilo load of clean screens. Each worker has to carry 70-80 screens up and down the stairs, working an extra hour without pay if the job is not done by the end of the shift.”
(FMS, July 2011)
4) If Maruti had calculated to ‘save the investment on a separate trade union’, the actual course of the struggle forced them to accept major losses in order to smash the emerging workers’ collective and to re-impose their regime. In a wider sense it was a ‘political price’ to pay, in defence of the ‘developmental model’ of the ruling class.
The dispute inflicted major losses on Maruti Suzuki at a time when according company claims ‘there are 100,000 open orders for the Maruti Suzuki Swift’ and waiting-times of more than four months. If we leave out all extra-costs (resting capital and capacities, payment for extra-security, bribes, legal and propaganda work etc.) and calculate an average price of a Maruti Suzuki Swift at 400,000 Rs [8,000 USD or 5,800 Euro] when sold to the traders, then a loss of 1,200 cars per day in Manesar amounts to 48 crore Rs [9,600,000 USD or 7,000,000 Euro]. A total loss of 75,000 units, as Maruti claims to have lost between June and October 2011, would amount to 3000 crore Rs [600 million USD or 435 million Euro]. Also Maruti Suzuki’s share-values have suffered, between June and mid-October the share price fell by 16 per cent.
A lot of the business media people wonder about the seemingly ‘irrational stubbornness’ of Maruti to rather swallow such kind of losses than accepting ‘the workers’ right’ to a separate trade union – quite a lot of leftist might have shared this view. We think it is less about the ‘violation of workers’ rights’, but about Maruti Suzuki having to confront developments during the course of the struggle, which forced them to ‘fight it out’. It became a question of who rules on the shop-floor. It became a question of whether capital let workers undermine the core of the current developmental regime by joint unlawful direct action.
5) During the last three decades the local industrial ruling class developed a fairly repetitive manual in order to transform workers’ unrest into leaps of re-structuring. This strategy was able to integrate trade union forms of struggle as long as it stuck to the rules of representation, labour law and/or other calculable forms of struggle. The workers’ actions at Maruti broke the master-plan at several points.
The use of ‘good conduct bonds’ or ‘lock-outs’ in order to tire out struggling workers is no new development. [5] We have seen hundred of times how this strategy in combination of ‘company’-focussed trade union struggle ended in hundreds of defeats. If the management is not able to get the general situation on the shop-floor under control – or if the general conditions force them into re-structuring – they prepare themselves for a ‘showdown’. Often they try to focus on the question of representation, either by crushing the workers’ representatives or by promoting and co-opting them, in order not to have to deal with an unruly and inadressable mass. If that proves to be difficult management prepares for a lock-out (impose overtime to fill stocks, arrange alternative sourcing of extra-parts, start to arrange supply of ‘new workers’). Depending on the economic climate they might announce to ‘close the whole factory’.
The management provokes the workers, e.g. by suspending their representatives. In order to circumvent the accusation of an illegal lock-out management issues ‘good conduct bonds’, hoping that the main trade unions stick to the ‘traditional ways’ of struggle, which means: refusal to sign, confining the struggle to the company gate and occasional demonstrations, reducing the conflict to the question of ‘our victimised leaders’ and thereby making it an individual issue which has little danger to explode into the wider proletarian area. At the same time management tries to keep up production, partly in order to avoid losses, but mainly in order to demoralise the workers. In the meantime they attack the workers outside by all means necessary (thugs, cops, boredom).
After some weeks there is an agreement, which normally results in severe re-structuring and re-placement. The trade union leaders can proclaim ‘a victory’ (“We got our representatives back on” or “We prevented the closure of the company”). The formerly combative collective is dismantled, e.g. by taking back only the permanent workers, or by shifting workers around within the plant. In this way most struggles in recent years got lost and re-structuring boosted. The fact that this set-up has repeated itself so many times is not mainly due to the cunning plans of management or the ‘compliancy’ of the main trade unions, but because of a specific configuration between general economic situation, composition of the workforce and blockades in the re-structuring process.
These conditions have changed. Maruti Suzuki was not able to enforce the usual strategy to deal with industrial unrest. This is mainly due to the unlawful collective action of the workers by occupying the plant and by the threat of spreading wildcat strikes. Instead of sticking to ‘legal campaigns’ ‘and well-meaning symbolic protests’ for their union rights, workers went into an offensive, which gave them an advantage position and raised the stakes. The fact that Maruti Suzuki could not undermine the workers collectivity neither by severe repression nor by replacing them during the lock-out is partly due to the specific nature of the industry and partly due to the general social atmosphere.
6) The decision of workers not to sign the ‘good conduct bond’ and to hand over the factory floor as the main ground for collective struggle to management was a tricky one. Maruti Suzuki did not manage to get full production going during the 33 days of lock-out, but they came close enough in order for the lock-out to become effective as a means of demoralisation.
If it had not been a central assembly plant – an integrated production process requiring the cooperation of hundreds, thousands of workers inside the plant and in combination with the suppliers – the struggle would very likely have been lost during the time of the ‘lock-out’. The company would have managed to demoralise the workers by being able to return to ‘normal’ production with some of the supervisors and newly hired staff. The ‘combative’ stance ‘not to sign the bonds’ would have turned into a ‘voluntary defeat’, because workers would have renounced to stay in the heart of the beast, where they have a faceless collective power: within the production process.
We should critically examine how close the Maruti management came to actually being able to get production going again – with the help of supervisors, engineers from the Manesar and Gurgaon plant and hundreds of newly hired ITI workers. Maruti Suzuki limited the attempt to get production going to only one of the three models manufactured in Manesar. On 31st of August, the third day of the lock-out, the company started production with 50 engineers and 290 supervisors, who had partly been shifted from Gurgaon, and 120 newly hired manual workers. They said that these 460 workers managed to produce 60 cars. Concerned about the companies’ share price development, Maruti Suzuki from then on announced new ‘production records’ on a daily level. On the 3rd of September 840 workers are supposed to have produced 200 cars. On 5th of September the MSEU declared in a communiqué that these figures are more or less bad propaganda, and that not more than a couple of cars are produced per day. Maruti claimed that at the end of the lock-out 1,400 workers produced around 400 Swift a day (normal output around 650) and that they had started to produce the A Star.
They surely did not manage to get production going within a month time, but they came close enough. This forces us in future struggles to make sure to a) not leave the terrain of the factory ‘completely’ to the management, even if there is great unity amongst the workers and b) not to think to be able to rely ‘on ones own strength alone’ even if this strength is as quantitatively massive as in the case of central assembly plants. The collective stance “We all stay out”, “We will not give in into their good conduct bullshit” is definitely an expression of ‘collective will’ – but if not combined with a major effort to actively connect with other workers in the area in order to spread the conflict it might be a step into a swampy ground.
7) Manesar could have turned into India’s Mahalla. [6] The Occupation at Maruti Suzuki took place while the populist ‘anti-corruption’-movement was attacked brutally in nearby Delhi. The social atmosphere (disillusion with corrupt political class, food price development, ‘desperate’ expressions of discontent) is shared with the countries of the ‘Spring Uprisings’ in Northern Africa. Previous to these uprisings, repression triggered unrest and explosive fusions rather than quelling them.
If the extreme poles of managements strategy to defeat a workers’ collective is to either replace them as collective producers or to repress them with brute force then both poles have proven fragile during the Maruti dispute. In 2005 we witnessed that neither Honda management nor the Indian state has major problems with crushing heads of hundreds of workers if it seems like a good way to return to ‘harmonious industrial relations’. This did not happen this time. There are various reasons why Maruti did not consider a violent eviction at the time. Obviously there is the danger of damaging machinery (and the cooperative will of hundreds of skilled workers!) and the possibility that an eviction will not go down well with the other workers of more than 500 factories in Industrial Model Town Manesar.
But we think that there are more specific reasons for why the ruling class is very cautious to make use of mass repression in current times, and these seem to be global reasons: in the current social atmosphere repression does not seem to instil mainly fear, but could create incalculable trigger effects of unrest. We have witnessed this during the recent uprisings in Northern Africa, from Tunisia to Egypt. The parallel to the situation in India is not a mere abstraction. The time of occupation coincided with the rather populist ‘anti-corruption movement’ (Ramdev, Harare), there were the violent attacks of the state on the Ramdev followers in Delhi in early June. There have been ‘suicide attempts’ of followers in desperate acts of ‘solidarity’. An attack on the occupation only miles away could have sparked all kinds of fusions and reactions – some of the Maruti workers had referred positively to the anti-corruption movement. This is understandable giving general situation and the concrete ‘corruption’ at Maruti Suzuki, e.g. at the annual remuneration of the CEO has increased by 419 per cent between 2007 and 2011, while workers’ real wages (and general profitability) dropped. Similarly the allegation that high-rank manager in Maruti’s HR department are personally involved in labour contracting business. This ‘corruption’ is obviously ‘unfair’, but just a drop in the sea of crisis. We have to see the ‘corruption’ primarily as an expression of the current instability of the system: future (profitable) prospects are bleak, the ruling class looks for immediate ‘personal gains’, instead of long-term investment.
During the course of the dispute the area around the Maruti factory turned into something like a ‘proletarian protest-camp’, various political groups turned up, students, family members. It expressed a certain need for spaces to come together in support and debate about what is happening in this world, a need which we can see spreading from Tahrir, to the Spanish square occupations to Wall Street. Manesar could have turned into an Indian Mahalla, where the repression of an organically very organised industrial working class could have given a whole different framework and impetus to a general ‘populist anti-government’ sentiment. We don’t advise workers to look for ‘formal alliances’ with these type of movements, but we should be aware of the general fragile social fabric.
In this social atmosphere the ‘means of repression’ had to be more subtle, but they revealed the wide social front-line which workers have to face: from the desks of the state administration to the metal barriers set-up by the company and staffed with private security guards, from the riot cops to the individual sms send by management to workers’ company phones, calling them back to work – these mobile phones had been a company present for 10 million produced Marutis. From the drunken land-lord thugs and local labour contractors attacking them in their ‘villages’ or in front of the factory with guns to the ‘soothing’ spiritual brain-wash of Brahmakumaris, hired by Human resource management to ‘heal’ the workers from their anger after the occupation. From the ‘panchayat’ leaders of the Manesar villages, linking up with the multi-national Haryana regime, to the investment fund advisors asking for ‘de-risking’ of Maruti’s production location. From the media regime, which portrays them as villains or victims to the production manager who orders to shift them away from their old work-mates to other lines and departments. And last but not least all those institutionalised leaders of trade union apparatuses who promise and postpone and mobilise and call off, all rather in the interest of their own organisations than to strengthen the collective power of the workers.
But we think that all these ‘cogs of the system’ can not explain the paradox that although Maruti’s position had been difficult and the losses significant, the workers did not manage to turn the (company) regime’s weaknesses into their own victory.
8. Despite the unity and sacrifice, despite the 100,000 open orders for Swift cars, despite having imposed full(-stop!) control over the factory… in many ways the workers lost, without having been defeated. We cannot ignore the material wage losses and glorify the struggle for ‘dignity’ and union ideals.
To ask about ‘victory’ and ‘defeat’ and ‘true demands’ of workers’ struggles is obviously an awkward matter – see contribution to debate on first Maruti occupation in this newsletter. Let’s start with the official demands and the gains and losses of workers as a result of the struggle. The initial official demand – the recognition of a separate union – has not been enforced, the company and administration offered a watered-down version of a welfare-board. If we just look at the ‘black on white’-results in form of wage slips, termination/suspension letters and agreements, then the workers paid a rather high price for this. Several dozen workers have been suspended, more than 100 temporary workers left the job at Maruti out of frustration – particularly after they were not taken back on 3rd of October. All agreements had an element of ‘moral punishment’ for the workers, either in form of penalty wage cuts or in form of the ‘good conduct bond’, which ‘on paper’ prohibits them to gossip or sing on the job or spend too much time on the toilet. The wage losses are considerably: the sole wage loss amounts to more than 50 days wages, if Maruti actually imposes the penalty wage cuts on the permanents then we talk about a total of about 130 daily wages loss. [7] The media likes to emphasise that these young workers a often unmarried and son’s of small peasants with brothers working somewhere in the army, and that therefore they are able to stick it out ‘with family support’, but anyone can imagine that this is a heavy loss to take, which definitely sets a limit to the participation of poorer and/or temporary workers.
This ‘material’ defeat is contrasted by something like a ‘moral victory’, in the sense that workers fought together for a common aim in form of ‘the union’, symbol for of their unity, for their own interest opposed to the interest of the company and for their hope in future betterment through union representation. They stood up for those who got suspended or terminated throughout the struggle (mainly representatives and office bearers of the union) and – and this is one of most significant decisions a collective of workers took in recent history of class struggle – for their ‘excluded’ temporary co-workers. This is their victory. We can go even further and say that although workers’ struggles tend to have ‘demands’ for betterment of their material situation, in many ways the collective struggle in itself is what we want and what in the end will improve the situation – with or without prove on paper in form of an agreement. We want to say “Enough!” together with others, link up, create a moment where everything is put into question, where we learn new things and where ‘their haughty power’ is broken. This is the political content of any struggle. And the Maruti workers did it! If all this happens around the ‘demand for a union’, let it be, but…
9) It was a tragic short-coming on the side of the workers not too put their concrete necessities into the foreground of the struggle: “More Money, Less Work” – because these had been general necessities of the mass of workers in Industrial Model Town Maneser. If combined with concrete steps ‘from group of workers to group of workers’ to actively generalise, this could have given an additional forceful dynamic to the struggle.
It is useless to debate whether the ‘demand for union recognition’ – reduced later on to the sole demand of ‘withdrawal of termination and suspension’ – has actually been the only demand of the workers. It has been the official demand and leaders like AITUC-president Sachdev have made clear a thousand times that this should be the focus. The initial demands of temporary workers for fixed contracts had disappeared early on.
As workers we cannot allow ourselves to postpone concrete demands and hope that they will be solved at future negotiation tables – particularly not if our general status is temporary anyway. Not only for the immediate sake, for ‘bread and butter’, but also in relation to other workers. The demand for ‘a company union and re-instatement of leaders’ creates less common grounds and potentials for generalisation than a concrete demand of, for example, 500 Rs for 8 hours, stop to double-shift and weekend work, … and all the other common problems of workers in Manesar and beyond. The likeliness of contagion will be higher in the latter. It also makes a difference if workers in a ‘privileged position’ like a booming assembly plant say that after weeks of full-on struggle they got something materially out of their enemy’s hands – or if they have to admit that they have lost a lot of money and only been offered a welfare board.
The ‘generalisation’ of a struggle obviously depends less on ‘the right demands’, but on its form: whether it leads to wider participation and active engagement of a mass of workers. Like demands, the decision about this form of struggle should not be delegated. Here, again, the formal constitution of institutionalised trade unions rather hinder ‘mass participation’ and ‘unity’ (beyond one-day shows) than encourage them. We cannot say much about the relation between the MSEU and the wider mass of Maruti workers. Facing the severe repression and general pressure we can understand that workers have the urge to defend those ‘who stick their neck out’. We don’t criticise the ‘representatives’, we question institutionalised representation and delegation. We have to ask whether ‘formal representation’ actually leads to both ‘immediate workers’ power to enforce our needs’ and to a political mass experience of workers deciding and doing themselves. We have to see that Maruti and the state operated very strategically with their arrests, suspensions and terminations (or withdrawals of them) of the representatives – and by doing so they were able to focus and ‘reign in’ the struggle around this question.
The ‘joint action committee’ which was set up first in June and was then revived during the ‘lock-out’ comprised only few Maruti workers, and if so, then the leaders of the MSEU. In June, out of a meeting of 100 in Manesar, there were only five Maruti workers, the rest were either union officials of the main trade unions or leftist supporters. Comrades noted that often there was little engagement of Maruti workers in the decisions of the ‘official steps of the struggle’ (when to demonstrate) or that in most cases the ‘agreements’ were settled without wider debate amongst the workers. Comrades noted that as long as the relation between Maruti Suzuki Manesar workers and Powertrain workers was mediated through the main union bodies, the different interests of AITUC, HMS and other institutions were actually hindering the coming together – e.g. Powertrain workers not taking parts in the early demonstrations of the Maruti workers in Manesar. Only once workers actually made contact, particularly the casual workers of both plants, they were able to push things to ‘common action’, in particular the second occupation.
10) The most ‘offensive’ and ‘potentially generalising’ leaps within the dispute, which actually questioned Marutis strategy to insulate and choke the struggle, were taken without major decrees and without following the pre-described formula of the labour laws. While officially and formally workers wanted legal recognition, their actual practice went way beyond this. Not the ‘betrayal’ of the main trade unions, but the fact that workers did not develop strong enough independent coordination during the struggle can explain its arbitrary outcome.
There were moments were workers – as part of the union or not – were able to put Maruti and the state on the back-foot. For us these leaps were:
* the first occupation in June, stopping or impacting on production of 200 nearby suppliers within weeks (a major potential, but largely missed chance for getting in touch with these workers);
* followed by the unrest ‘back at work’ in July and August, e.g. the wildcat strike on 28th of August;
* during ‘the lock-out’: the wildcat strike of casual workers at Munjal Showa on the 12th of September (which spread to the companies Gurgaon and Haridwar plants), the strike at Suzuki Powertrain and Motorcycles on the 14th of September;
* the decision to occupy again on 7th of October – not at last due to the pressure of 1,000 angry ‘locked-out’ temporary workers.
These were the moments were ‘things could have gone out of hand’ of the (state) management.
It is easy to discard the main trade union leadership for ‘betraying’ the unity, which they claim to symbolise:
* trade union leaders told everyone and the workers that ‘workers are victimised’ and ‘workers are in a bad spot’, while they were on occupation in June and were actually in a rather strong position
* AITUC called off the solidarity strike in June last minute;
* HMS called off the strike at Powertrain in September as soon as it hit the Gurgaon plant;
* regional AITUC president at nearby Honda plant said “We are waiting for the authorities to take initiative to resolve the issue.”, when Maruti workers occupied again in October and were actually threatened by eviction.
We think it is less about ‘betrayal’, but about a general problem with ‘trade union form of struggle’ in times of crisis. If under the general conditions trade unions confine themselves to their set limitations (within legal boundaries, confined to sector or company, based on formal representation and settlements), they will remain largely toothless. If they are toothless, the ‘improvements’ for their members will be counterweighted by the deterioration of conditions of a growing mass of other workers: all those, who remain outside of the formal boundaries which legal trade union struggle can act within. The rapid changes of the social production process (globalisation, new technologies) undermine institutionalised forms of workers organisations further. If unions decide to actually go beyond their limitations, they will face the full brunt of repression and they will have to question their very formal premises. At Maruti Suzuki workers reached this point. So instead of barking about betrayal, let’s focus on the essentials instead: independent organisation of workers. [8]
11) What could be done?
We cannot come up with any master key or all time solutions, but rather some general day-to-day considerations and suggestions. As we wrote in April 2011:
“We will put forward the issue “500 Rs for an 8-hours day – We can’t do it for less’ in Manesar Industrial Model Town. We openly say that such a slogan alone will neither free us from looking at our department or company specific conditions, nor do we have the illusion of a ‘final settlement’. It can help us to debate about concrete steps. Which steps will be specific, which steps can be common? What can we do inside the factory, what in the wider area? We have discussed the issue with some workers employed in different companies. We will put it forward both in form of hand-written posters in the area and inside these companies. We will decide about further steps according to the debate, which hopefully will emerge amongst workers in different factories.” [9]
* Let’s not delegate and postpone our concrete needs! Let’s start formulating with our co-workers what we want and look for commonalities with others. Let’s not go for promises and future settlements, enforce ‘less work, more money’ if we can, here and now.
* Let’s start with collective steps on the level of our day-to-day existence as cooperating workers or neighbours. Let’s share your experiences and debate them with other groups (in other departments, factories, sectors) and find ways to join up in common steps.
* Let’s not give out of our hands the weapon of the collective producer. Don’t let them blind you by all their talk about ‘indiscipline’ and ‘unlawfulness’. Collective ‘indiscipline’ doesn’t cost much, doesn’t need experts, hurts the management and can provide immediate relieve for us.
* Let’s try to find forms of struggle, which do not require individual people sticking their heads out too much, without leaders to be corrupted or squashed.
* Let’s create means of communication and spaces in the wider area to meet and coordinate practical activities on a larger scale, linking up with the experiences on a day-to-day group / factory level.
* Let’s find forms of collective debate and decision making during mass mobilisations or meetings. Don’t wait for calls, plans or decisions from above. Make any effort to spread ‘company struggles’ to other workers, relating to them as co-workers.
* Let’s not give the state or management too much chance to predict our next moves – break their strategy of ‘good conduct bonds’ or other traps. Don’t go for set-up provocations. Don’t stick to their normal procedures.
* Let’s not rely on the spectacle of the middle-class playgrounds (legal proceedings, media, NGO campaigners, political leaders). We should find forms of struggle and communication, which remain independent.
* Let’s make an effort to learn from the current explosion of struggle around the world (occupations of squares, strike waves, riots etc.) – let’s not treat them as ‘glorious’, but examine critically whether new forms of working class organisation and perspectives emerge. Let’s share our experiences with them in a global discussion.
* On the bases of the experiences of the global working class – as producers and as groups in struggle – let’s debate about a social alternative to car production, traffic jams, mega-cities, villages, peak oil, bio-fuels, war machines, the permanent crisis and this failing system.
Friends of Faridabad Majdoor Samachar try to support this process of working class self-organisation by taking part in the discussions amongst striking workers during the Maruti strike, by publishing a monthly workers’ newspaper and by taking part in Faridabad Majdoor Talmel, an effort of workers’ coordination in the industrial belt of Delhi. If you live in Delhi area, please be welcomed to take part. We distribute Faridabad Majdoor Samachar on ten days each month in various industrial areas around Delhi. If you are interested, please get in touch.
For more background on Faridabad Majdoor Talmel:
http://faridabadmajdoorsamachar.blogspot.com/p/fms-talmel.html
Footnotes:
[1]
Extensive material by Faridabad Majdoor Samachar on the re-structuring process at Escorts and the role of the HMS union:
https://gurgaonworkersnews.wordpress.com/workers-history/#fn131
Overview on the 2000/2001 dispute at Maruti Suzuki Gurgaon plant:
https://gurgaonworkersnews.wordpress.com/gurgaonworkersnews-no8/
[2]
See comprehensive analysis by Mouvement Communiste:
http://mouvement-communiste.com/documents/MC/Booklets/BR1_China_EN_vF_Complete.pdf
[3]
Documentation of the struggle for union recognition at Honda HMSI in 2005:
https://gurgaonworkersnews.wordpress.com/gurgaonworkersnews-no7/#fn4
[4]
Documentation of wildcat strikes / factory occupations of temporary workers at Hero Honda and Delphi:
https://gurgaonworkersnews.wordpress.com/gurgaonworkersnews-no4/#fn2 https://gurgaonworkersnews.wordpress.com/gurgaonworkersnews-no8/#fn4
[5]
Documentation of ‘management’s strategies’ at Faridabad Gedore Handtools factory:
https://gurgaonworkersnews.wordpress.com/workers-history/#fn292
[6]
Industrial town in Egypt. Mass strikes in 2005 and 2008 provided impetus and organisational focus for the ‘popular movements’ emerging around Tahrir Square in 2011:
http://www.klassenlos.tk/data/pdf/egypt_interview.pdf
[7]
If we count full days of strike as full working days: 14 days occupation, 33 days of lock-out/protest camp, 14 days of 2nd occupation and strike; plus 28 days penalty wage cut for first occupation, 33 days for lock-out, 14 days for 2nd occupation
[8]
For the historical debate on the question of ‘economic’ and ‘political’ struggle of the working class:
http://libcom.org/library/class-composition-sergio-bologna
[9]
Paper on potential for wage struggles in Manesar, April 2011:
https://gurgaonworkersnews.wordpress.com/gurgaonworkersnews-no-937/
Comments
Struggle at Maruti Suzuki in India:
Wildcat strikes, factory occupations and protest camps
Since June 2011 around 3,500 workers at Maruti Suzuki car plant are confronting the factory regime and its institutional allies in Manesar, in the south of Delhi – also see GurgaonWorkersNews no. 41. Their struggle leaped over to other automobile factories in the industrial corridor, which brought the world’s third largest automobile assembly plant in nearby Gurgaon to a halt. In the most significant workers’ struggle in India in the last two decades the young workers managed to undermine the companies’ attempts to divide them along the lines of temporary and permanent contracts. The struggle attacked the core of the Indian development model and puts it into question: integration into global markets and production structures on the highest technological level combined with harshest casualisation of the workforce. This casualisation is enforced by various means, ranging from the use of country rifles by local labour contractors to sending individual text messages to the workers company mobile phone (a ‘company present’ for the production of 10 million Maruti cars), calling them back to work. The dispute developed in four phases.
The First Occupation
From 4th to 17th of June the workers occupied the assembly plant after management had tried to sabotage their attempt to form an independent union Maruti Suzuki Employees Union(MSEU). Friends, co-workers, family, supporters provided them with food and other necessities. Casual workers engaged in loading finished Maruti cars joined their strike and demanded the same wage rate as the truck drivers. The main trade union centres called for a solidarity strike on 14th of June, but called it off again last minute. The occupation ended with the management offering only a ‘faked’ recognition of the union as part of a ‘company committee’, while penalising the workers with wage reductions of two daily wages per day of strike.
The Underground
From the 17th of June till 28th of August the dispute continued underground. Workers said that after the occupation foremen and management treated them with slightly more respect than usual. During the first weeks only 1,100 instead of 1,200 cars were produced per day. End of June the state authorities refused the application for union registration for formal reasons. The workers refused to take part in the elections of the ‘company union’ Maruti Udyog Kamgar Union (MUKU), which is based in the Gurgaon plant and which was set up after a major defeat of workers in 2000/2001, after a long lock-out. The company started hiring new manual workers for assembly line positions from Kanpur and other Industrial Training Institutes (ITI), at the same time they fenced of the grassy and open areas inside the premises, which had served the workers as assembly places during the occupation – which can be seen as preparations for a possible lock-out. On 28th of July the police arrived and took four workers from their work-places to the management offices – the management talked about ‘incidences of violence against superiors’. In protest, workers in the whole plant laid down tools and assembled. The company stopped the buses for the B-shift and refused entry to the arriving workers. The A-shift refused to leave the factory. After about an hour management agreed on letting the B-shift start working. At the beginning of August some workers hired through contractor (temporary workers) complained about the work load and demanded that more workers should be hired for the job. The line manager abused one of these workers, the other workers at the line stood up for him – in the end the line manager had to apologize in front of the gathered workers. The company started to complain about go-slows and According to company sources on 24th of August only 437 of the planned 1,230 cars were produced, out of which only 96 made it through quality check. During this period four workers were suspended and around 40 temp workers sent home.
The Lock-out / Protest-Camp
During the night of the 28th of August around 400 riot cops entered the factory and established themselves there. The company erected a metal barrier around the entrance of the plant and demanded from each worker to sign a ‘good conduct bond’ (no go slows, no sabotage, no singing during work, shave regularly etc.). Only twenty or so workers signed, the others set up a protest camp in front of the factory. Maruti Suzuki transferred engineers and supervisors from Gurgaon to Manesar and started to hire new skilled workers on temporary basis. Till the end of the 33 days of lock-out the numbers of workers inside the plant increased to about 1300, 800 of which had been hired fresh.
On 12th of September around 1200 temp workers at neighbouring Munjal Showa factory went on wildcat strike. Munjal Showa manufactures around 60,000 shock absorbers for two-wheelers a day – the tool-down threatened the production at the local Honda and Hero Honda plants. The next day the Munjal management promised to make 125 workers permanent and complained about the negative influence of the Maruti workers.
On 14th of September several thousand workers at Suzuki Powertrain, Suzuki castings and Suzuki Motorcycles in Manesar area went on strike. [1] The HMS union at Castings and Powertrain had been recognised under the pressure of the first occupation at Maruti Suzuki – while at the time AITUC still made major efforts to control the MSEU at Maruti Suzuki. The workers at Powertrain etc. raised their own demands (wages, regularisation of casual workers), but also demanded the end of the ‘good conduct’ lock-out and withdrawal of the suspensions at Maruti Suzuki. Apart from the Maruti Manesar plant, Suzuki Powertrain also supplies the bigger Maruti Gurgaon plant with engines, gear-boxes and axles. After one day of strike management at Gurgaon plant announced to close the factory due to lack of parts for certain models. This is also of importance because Maruti had threatened to ‘re-relocate’ certain models from Manesar back to Gurgaon in order to compensate for the impact of the lock-out. On 16th of September the HMS union called off the strike, after management had considered some of the ‘company internal demands’.
The lock-out continued till 30th of September, in the end the main trade unions advised the workers to sign the ‘bond’, in turn management took back on 18 trainees and converted 44 terminations into suspensions. Both sides declared to take care for harmonious work relations.
The Second Occupation
On 3rd of October production in Manesar was supposed to resume. The management allowed the permanent workers to enter the factory, but refused entry to about 1,200 temporary workers who had taken part in the occupation and protest camp. Management also shifted a lot of permanent workers between departments and production lines, which caused discontent. The wage loss had been a drain on workers scarce resources. Between 3rd and 7th of October around 100 frustrated temp workers took their final dues. The others went to the factory gate put pressure on management (and on their permanent co-workers). On 7th of October the workers inside the Maruti factory occupied the plant again, together with them, workers at Suzuki Powertrain, Castings and Suzuki Motorcycles took the same step: they responded to the attempt of the Maruti management to divide the workers into temps and permanents by engaging in a sit-down strike. They demanded to take back the temps and to re-install the company bus service, which had been cancelled since early October. There were short solidarity strikes in eight more (mainly) automobile factories in the industrial area. At least half of those workers who had been hired during the lock-out and who were now inside the Maruti plant joint the occupation in support of the temporary workers outside.
On 9th of October local labour contractors appear in front of the Suzuki Motorcycle factory, they throw beer bottles and shoot and threatened the striking workers. The Haryana state accused the striking workers to have broken the agreement and gave them 48 hours notice. On 10th of October the Gurgaon plant manufactured only 1,000, instead of 2,800 cars due to lack of parts from Suzuki Powertrain. Two days later management announced closure of the Gurgaon factory.
On 14th of October, after district elections finished and more police force was available, the cops evicted the workers’ make-shift kitchen in the industrial area, which had provided food for around 4000 workers in occupation. Around 2,000 cops were now in the Manesar plant, they started to shut down the canteen, the water supply and the toilets. During the night workers decided to leave the occupation, the next morning the other two occupations ended, too. The strikes continued outside the factories, on the 16th of October Maruti announced that production in Manesar had started on ‘low levels’ with about 800 workers. The same day around 1500 workers at multi-national solar-panel and optical discs manufacturer Moser Baer in nearby NOIDA went on strike for higher wages. The strike at the Maruti Suzuki and the other three Suzuki plants lasted till the 21st of October. In the end management agreed to take back on the 1200 temps and take back some of the terminated and suspended workers. The MSEU is not recognised, but a ‘company welfare board’ is set up, with participation of representatives of both workers and management.
Who are these workers and what do they want?
The pyramid of valorisation
The assembly plant in Manesar was opened in 2007, Maruti hired young skilled workers from various ITIs in Northern India. The majority of workers in their mid 20s. Originally from the hinterland of Haryana or Uttar Pradesh they now live in the industrial dormitory villages around Manesar and Gurgaon, often sharing rooms. Around 1,000 workers are permanents, around 800 are trainees, 400 are apprentices (who work full-time as normal production workers) and 1,200 are temporary workers, hired through contractors. The permanents earn around 13,000 to 17,000 Rs, the trainees around 8,000, the temp workers 6,500 and the apprentices around 4,000. The wage of the permanent workers is composed of a basic wage of around 5,000 Rs (the minimum wage in Haryana) and 8,000 Rs of various bonuses (attendance etc.). This means that the young permanent workers earn considerably less than the permanent workers in the older Gurgaon plant in around 20 km distance or the neighbouring Honda motorcycle plant in Manesar, who both earn around 30,000 Rs. The Maruti factory in Gurgaon was opened in the early 1980s. In 2000/2001 the Gurgaon workers were confronted with a long lock-out of several weeks, similar to the Manesar workers today. Back then the company used the defeat of the workers in order to enforce a Voluntary Retirement Scheme and replaced around half of the permanent workers with temp workers. Today the majority in Gurgaon are temp workers, the severe wage difference – or class division – is managed by the trade union MUKU. The young workers in Manesar did not feel represented by this union and hoped for a solution to their problems by forming their own union.
The new anger, the new aspirations
The young workers have concrete desires: more money and less work and an end to the disciplinary factory regime. They compare their wages to those in other car plants. They complain, that Maruti cuts their bonus payments for any minor delay or as soon as they take a day off, up to 2,200 Rs wage reductions for a day off. They express their discontent about the workload, which does not leave time to get a breath in. The break time does not suffice to walk 400 metres to the canteen and take your meal. You need permission in order to go to the loo. They are angry about the never ending waiting-loops before you get a proper contract. But they did not put these aspirations – more money, less work – in the foreground of the struggle. This could have built a bridge to the 150,000 other workers in Manesar industrial area, because these are common problems and aspirations. Instead they demanded recognition of their union, and later on: re-instatement of the suspended and terminated representatives. They struggle hard and bear huge wage losses for a piece of paper, which they see as a symbol of their unity, as a thorn in the flesh of the hated factory regime and as a hope, that they can establish, solidify or delegate their gains and collective power to a permanent body of representation.
[1]
Suzuki Powertrain India Ltd employs over 2,000 (1,300 – 3,000, 1250 trainee and permanent and over 600 contract workers) workers at its Manesar plant, where it manufactures diesel engines (300,000 per year) and transmissions for supplies to Maruti Suzuki. Suzuki Castings has nearly 700 workers (375-400 trainee and permanent and over 500 contract workers). Suzuki Motorcycles India has 1,400 workers at its plant near Manesar and rolls out about 1,200 motorcycles and scooters a day.
German Translation:
http://www.wildcat-www.de/aktuell/a092_indien_maruti.html
Comments
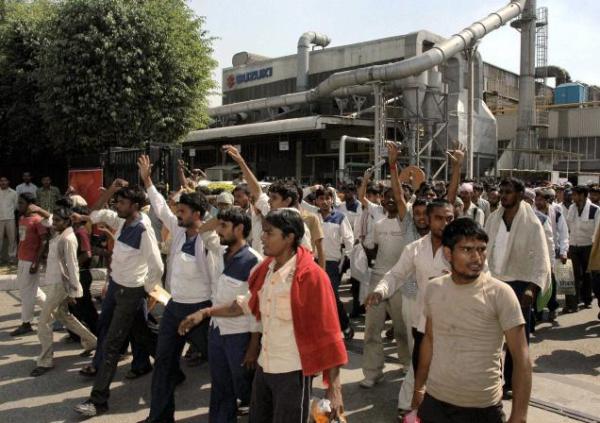
GurgaonWorkersNews – Newsletter 45 (December 2011)
Gurgaon in the industrial belt of Delhi is presented as the shining India, a symbol of capitalist success promising a better life for everyone behind the gateway of development. At a first glance the office towers and shopping malls reflect this chimera and even the facades of the garment factories look like three star hotels. Behind the facade, behind the factory walls and in the side streets of the industrial areas thousands of workers keep the rat-race going, producing cars and scooters for the middle-classes which end up in the traffic jam on the new highway between Delhi and Gurgaon. Thousands of young proletarianised middle class people lose time, energy and academic aspirations on night-shifts in call centres, selling loan schemes to working-class people in the US or pre-paid electricity schemes to the poor in the UK. Next door, thousands of rural-migrant workers up-rooted by the rural crisis stitch and sew for export, competing with their angry brothers and sisters in Bangladesh, China or Vietnam. And the rat-race will not stop; on the outskirts of Gurgaon, new industrial zones turn soil into over-capacities. The following newsletter documents some of the developments in and around this miserable boom region. If you want to know more about working and struggling in Gurgaon, if you want more info about or even contribute to this project, please do so via:
http://www.gurgaonworkersnews.wordpress.com
gurgaon_workers_news@yahoo.co.uk
In the December 2011 issue you can find:
1) Proletarian Experiences –
Daily life stories and reports from a workers’ perspective
*** Story by Proletarian Tenant on Landlordism in Tekhand, Okhla Industrial Area –
A working class tenant describes how landlords in Tekhand try to squeeze extra money by using the tenants’ dependency on water and electricity – and how collective steps of tenants can undermine this.
*** Workers’ Reports from (Garment) Factories in Gurgaon and Manesar –
Eleven short workers’ reports on conditions in Gurgaon’s factories, amongst others at Adigear (Puma, Adidas), House of Pearl (JC Penny), Modelama (GAP, Old Navy).
2) Collective Action –
Reports on proletarian struggles in the area
*** IMPORTANT Unfinished Business: Further Material for Debate on Maruti Suzuki Workers’ Struggle –
Between June and October 2011 thousands of workers took part in factory occupations, wildcat strikes and protest camps at Maruti Suzuki and other automobile factories in Manesar, near Gurgaon. We document further material on this important strike and call for an open debate about the lessons of this dispute. We translated two long articles published in Faridabad Majdoor Samachar providing important new details and summarised some material about the general context of the struggle.
*** Delayed Notes on Harsoria Healthcare Workers’ Strike in Gurgaon –
In April 2011 a dispute erupted at the factory of the health equipment manufacturer Harsoria. After initial collective steps on the shop-floor and a 72 hours factory occupation, workers followed the legal order and union advice to leave the factory. They were attacked by the police and had difficulties not to get entangled in conflicts of factory union representatives, regional union leaders and company management.
3) According to Plan –
General information on the development of the region or on certain company policies
*** The “Spiritual”-Industrial Complex: Involvement of Brahmakumaris and Radha Soami Panth in Industrial Management in Gurgaon –
Religious sects like Brahmakumaris and Radha Soami Panth not only engage in commodity production by selling products for ‘spiritual tourism’, they get directly involved in management of industrial relations and education of manual workforce. After lockouts at Denso in 2010 and Maruti Suzuki in 2011, the multi-national management engaged Brahmakumaris to deal with the agitated ‘human capital’, while the Radha Soami Panth supplies semi-skilled young workers to companies like Honda Motorcycle and Scooter India (HMSI) in Manesar. A workers’ report describes the ‘spiritual-industrial’ connection.
4) About the Project –
Updates on Gurgaon Workers News
*** Suggested Reading: Contributions to the Global Overthrow –
The global and historical character of the current crisis forces us to coordinate both debate and practice ‘for workers self-emancipation’ on an international scale. Following texts are selective, but we think that they can stand as examples for ‘general theses’, ‘concrete analysis’ and ‘historical debate’ of class struggle and revolutionary movement.
Leaflet by InsurgentNotes on the Occupy Movement in the USA
New Magazine from the US focusing on the Proletarian Tendencies within the Occupy Movement
Article from Wildcat on Rural Class Relations in Indonesia
Article from Wildcat on Migrant Agricultural Workers Strike in Southern Italy
*** GurgaonWorkersHistory: Voices from the Local Working Class History –
We translated an article published in the Hindi magazine ‘Militant Worker’, Sangharshrat Mehantkash no.3, dealing with the history of working class struggle in Dharuhera, near Gurgaon. The first industrial area was set up in 1977, the first official movement kicked off at East India textile company in 1984. The article describes the Radhu Yadav’s Unemployed Army in 1985 and the first strikes at Omax Auto in 1986. Both in regards to the debate on the struggle at Maruti Suzuki and the importance of a workers’ historiography, we suggest reading Sergio Bologna’s article on the emergence of industrial history and workers’ research around the automobile industry in Italy. We converted the article into a text-file and published it here:
http://libcom.org/library/theory-history-mass-worker-italy-sergio-bologna
*** Delhi Calling: Get Involved in Faridabad Majdoor Talmel –
To abolish the global work/war house will take more than informative exercise! If you live in Delhi area, please be welcomed to take part in Faridabad Majdoor Talmel – a workers’ coordination. We distribute around 9,000 copies of Faridabad Majdoor Samachar on ten days each month in various industrial areas around Delhi. You can also participate in the workers’ meeting places which have been opened in various workers’ areas. If you are interested, please get in touch. For more background on Faridabad Majdoor Talmel:
http://faridabadmajdoorsamachar.blogspot.com/p/fms-talmel.html
Comments
*** Story by Proletarian Tenant on Landlordism in Tekhand, Okhla Industrial Area –
A proletarian tenant in Tekhand, near Okhla Industrial Area
(Distributed in Hindi in FMS 275/276 May/June 2011)
In order to get drinking water in Tekhand (a ‘village’ near Okhla industrial area) you have to run a motor pump. On two floor there are about 22 rooms occupied by tenants. Since six months the landlord runs the motor pump only every second day for each floor. This could mean that you won’t have water to wash your clothes on Sunday. You are also not allowed to keep too many canisters or other kind of water containers. In this way the landlord can save one or two units for his electricity bill, may be 10 Rs here and there. It does not matter that this causes a lot of problems for the tenants. When the motor pump got stolen the landlord asked for 150 Rs extra from each room. If you refused to pay, he would have kicked you out, he says that there are a lot of tenants queuing up for rooms.
When a tenant wants to give up his or her room in Tekhand, some landlords, under this or that pretext, demand the payment of 2,000 Rs, 3,000 Rs extra. When a tenant wanted to leave his room on 10th of April 2011, the landlord said that for one and a half months of electricity and cleaning charges he should first pay 2,050 Rs. The whole thing was a complete con and the landlord went so far as to use open threats and finally he called the cops. After the word about this conflict spread amongst the tenants of the 70 rooms of the landlord and the neighbouring rooms and people started discussing, the thuggish behaviour of the landlord stopped. The tenant cleared his room in front of the landlord’s eyes… without paying him the 2,050 Rs.
*** Workers’ Reports from (Garment) Factories in Gurgaon –
NIIT Technologies Worker
(Plot 223, Udyog Vihar Phase I)
This IT company employs around six to seven thousand workers. We 33 housekeeping workers on plot 223 are not even paid the minimum wage. In March we were paid 3,850 Rs for 31 days of work, 8 hours a day. Now, since 13th of April we are supposed to work on two 12-hours shifts and they say that for 31 days of 12-hours shifts we will be paid 5,800 Rs. None of us gets ESI or PF.
Modelama Worker
(Plot 105, Udyog Vihar Phase I)
We work from 9:30 am till 8 pm, often 2 am or even 6 am the next day. There are 4,000 workers employed, manufacturing for GAP, Old Navy, AMC, DKNY etc.. The 600 to 700 female workers in the finishing department are paid 3,600 Rs to 4,000 Rs, they often have to work till 10:30 pm at night. The male workers are paid 4,200 Rs to 4,300 Rs. In the production department there are 3,000 tailors (200 female), out of which 1,000 are on piece rates and the rest on monthly wages of 4,400 Rs to 4,500 Rs. The 250 workers in the sampling department are paid 4,893 Rs. We work 100 to 150 hours overtime per month. Only the permanent workers are paid double rate, but only the first two hours of daily overtime. Even after five years of employment some workers to get the PF form. A lot of swearing from the bosses, bad drinking water, dirty toilets.
Eastern Medikit
(Plot 195 and 205, Udyog Vihar Phase I and Plot 292, Phase II)
Wages were delayed. The casual workers of the company started to go on strike on 20th of April, the company then paid the March wages on 22nd of April. The casual workers work on two 12-hours shifts, they get 18 Rs per hour overtime. The payment for February overtime was delayed, on 10th of April workers at Medikit stopped work in order to move the company to pay, on 12th of April they did.
SLV Security Worker
(Office of the company is near Ghora Farm, Sector 23)
The company employs 27,000 to 28,000 guards, they all work on two 12-hours shifts. There is no weekly day off. They pay 6,000 Rs for 12 hours, 31 days – cash in hand. If they see you dozing off they cut 300 Rs from your wages.
Grand Printers Worker
(134, Udyog Vihar Phase IV)
We work from 9 am till 8 pm on one day, from 9 am till 2 am the other. This is an industrial print-shop for cigarette packs, medical packaging and so on. They pay double rate for overtime… but the helpers are paid only 2,200 to 2,800 Rs per month and the operators 4,000 to 5,000 Rs. Only 50 out of 300 workers get ESI and PF.
Neelam International Worker
(556, Udyog Vihar Phase V)
The female workers (also the 12 to 15 year old girls) have work till late at night, sometimes till 6 am the other day. Overtime is paid single rate. The female workers who work by hand get 4,200 Rs the tailors get 5,500 Rs. None of the 500 workers get ESI or PF. Male and female workers have to share the same toilets. The factory has three floors, but only on the ground floor there are two toilets. There is always a queue. If you leave the job you have to fight hard in order to get your outstanding wages.
Jyoti Apparels Worker
(158, Udyog Vihar Phase I)
In the finishing department around 50 to 60 women workers work from 9:30 am till 9 pm, and 150 male workers work till 1 am. The monthly overtime of 150 to 200 hours is paid single rate. The tailors are sometimes paid piece rate, sometimes daily wages, sometimes monthly. None of the 450 to 500 workers get ESI or PF, may be the 50 staff get it. The general manager swears at workers. There is no canteen. The drinking water is crap. The toilets dirty. The situation in the factory next door is the same.
House of Pearl Worker
(446, Udyog Vihar Phase 5)
Around 3,000 workers produce stuff for JC Penny and Impulse. Daily shifts are from 9 am to 9 pm, often till 1 am. Only half of the workers get ESI and PF. The ‘incharges’ swear at workers a lot. Even during meal breaks you won’t find drinking water in this factory.
IMT Manesar
Kumar Printers Worker
(Plot 24, Sector 5, IMT)
In order to earn some money a worker worked 16 hours a day for 10 days in a row. He went to work even when his appetite went. He fell ill… On the 11th day he had to quit the job. The company paid him single rate for his overtime.
Crewboks Worker
(Plot 153, Sector 4, IMT)
The wages are delayed. The February wages were paid on 15th of April 2011, the March wages have not been paid (30th of April). Workers stopped working on 24th and 25th of April because December 2010 overtime had not been paid yet. The company kicked out three workers who stood in front and talked [talked to the management, talked openly]. The overtime money was then paid on 27th of April. On 25th of March 250 workers who had worked for the company since one and a half to two years were shifted to the plant on plot 12 in sector 5. Their PF numbers were changed.
Adigear Worker
(Plot 150, Sector 4, IMT)
In April the factory was swarming with representatives of the ‘buyers’. PUMA wants 25,000 pieces every week. JAMBUREE wants jeans for Australia. RSS orders uniforms. ADIDAS sent their representatives. The workers had stopped work for two days in March, because wages were delayed. The company reassured that wages will now be paid punctually on the 7th of each month. The problem in April was that because there were so many representatives running about the company did not want to be the last month wages in order to avoid the representatives seeing the large [and formally illegal] amount of overtime we work. They turned the 150 to 180 hours of overtime from March into 30 hours, documented on the pay slip. The bosses said: “Take your wages now, we will pay the remaining overtime later”. The workers said: “No way, pay both now”. They then paid both, March wages and overtime, around 17th to 21st of April. There is a huge work load due to the increased demand. Most of the 300 guys in the finishing department work from Saturday 9:30 am till Sunday 1:00 in the afternoon, that’s a 27.5 hours shift. On 27th of April the company dismissed the ‘incharge’ of the finishing department because he refused to work that long.
http://www.adigear.com/clients.html
Comments
*** Unfinished Business: Further Material for Debate on Maruti Suzuki Workers’ Struggle –
Between June and October 2011 around 3,500 workers at Maruti Suzuki car plant openly confront the factory regime and its institutional allies in Manesar, in the south of Delhi. Their struggle leaped over to other automobile factories in the industrial corridor, which brought the world’s third largest automobile assembly plant in nearby Gurgaon to a halt. In the most significant workers’ struggle in India in the last two decades the young workers managed to undermine the companies’ attempts to divide them along the lines of temporary and permanent contracts. We wrote two longer texts summarising material about this important experience and tried to formulate preliminary conclusions for a necessary open debate.
https://gurgaonworkersnews.wordpress.com/gurgaonworkersnews-no-944/
https://gurgaonworkersnews.wordpress.com/gurgaonworkersnews-no-941/
In the following we want to give a short up-date on what has happened since the official end of the dispute in October 2011. As part of the ‘updates’ we also try to relate the dispute at Maruti Suzuki to the current ‘second-crisis-blow’, the global automobile industry has to confront since 2008. The growth in car sales in China and India is slowing down rapidly, while wage levels drop sharply in the US and it becomes clearer that they will try to close assembly plants in Europe in the near future. The re-structuring in the global car industry will still be the determining axis for the ‘capitalist re-covery’, the industry will still determine the centres and peripheries of global supply-chains and wage hierarchies for the wider social production. It will also depend on the workers’ struggles in this sector whether the working class can liberate society from the straight jacket of austerity, sales figures and assembly chains.
Jump Ahead: Up-Date on Maruti Suzuki Workers’ Dispute
More importantly than the brief update: we publish a rough translation of two articles written and distributed in Faridabad Majdoor Samachar in October and November 2011. The articles provide important details based on conversations with Maruti Suzuki workers during the dispute, in particular about the relationship between central trade unions, factory union and Maruti Suzuki workers. The articles not only ‘document’, they formulate practical suggestions of how to increase the workers’ collective power during the dispute. Friends put these suggestions to debate during conversations with workers at the occupation and protest camps and in form of a workers’ manifesto – poster. These suggestions should form part of the debate about lessons – from a perspective of workers’ self-emancipation.
Jump Ahead: Articles by Faridabad Majdoor Samachar On Maruti Struggle, October/November 2011
Last, but not least you can read six reports by automobile workers living in dormitory villages, employed in the Maruti Suzuki supply-chain. Two reports are from mainstream newspapers, but we found them interesting nevertheless. The other reports were given to and distributed by Faridabad Majdoor Samachar.
Jump Ahead: Automobile Workers’ Reports from Faridabad, Gurgaon, Manesar
——————-
* Up-Date on Maruti Suzuki Workers’ Dispute
There is an official and an unofficial aftermath of the Maruti Suzuki dispute. The official outcome seems devastating to many who have followed the struggle, while we are only able to see fragments of the unofficial results, which seem to reflect more of the collective power developed during the dispute. Unofficial results which we still have to discover together with other workers.
The official aftermaths
The official result can be summarised in the picture of golden hand-shakes. Shortly after it became known that all of the 30 suspended trade union leaders of the unrecognised MSEU have resigned from their jobs for an individual payment between 4 million rupees (USD 81,000) and 1.6 million rupees (USD 32,500), Mr RC Bhargava, chairman Maruti Suzuki was awarded with the ‘The Order of the Rising Sun, Gold and Silver Star’ by The Emperor of Japan for “his contribution to the strengthening of economic and bilateral relations between India and Japan”.
For all those who focussed on the ‘new leadership’ of the workers, their ‘betrayal’, their ‘sell-out’ must have been a blow. Sachdeva, general secretary of the All India Trade Union Congress: “These 30 workers were the most active in the formation of a union. Their loss means a new leadership needs to be developed. But, it will take workers time to put their faith in the new leaders”. It will also have been a blow to many workers, who have lost a large amount of money due to wage loss and penalty wage reductions and who see that ‘their leaders’ got out of it with a fair sum of money.
Obviously this is not a new phaenomena. After the Rico strike in October 2009 around 125 ‘leaders’ took a one-off payment and left the factory: https://gurgaonworkersnews.wordpress.com/gurgaonworkersnews-no-932/#fn1
Instead of lamenting about betrayal we should ask about the structural problems emerging from formal representation and organisational forms, which produce an institutionalised or personalised leadership. Unlike bourgeois forms of struggle the struggle of an industrial working class in itself does not need individual heroes, which tend to become either traitors or martyrs.
In the meantime a ‘new leadership’ has emerged to form a trade union. The character of both leadership and trade union is obscure. Friends wrote that it seems to be based much more on ‘regionalistic’ divisions within the work-force. A lawyer who represented the MSEU so far said: “I feel the new union leaders are hand-in-glove with the management. I asked them to include a provision in their union application that in the case of dispute, a settlement will only be reached with the management once it has been ratified by a two-third majority. But the union leaders refused to include any such democratic provision.” An application was filed early November, but the Haryana administration denied having received any application. The company also announced that people who underwent any disciplinary proceedings (suspensions etc.) during the time from June to October 2011 will not be able to become elected to the ‘company board’ – the ‘management’s alternative’ to union recognition.
Maruti management Mr S. Y. Siddiqui, Managing Executive Officer, told a business paper in early November “that the Department of Labour, Haryana and some management-level employees are explaining the process of setting up the union to the workers and it was likely to be completed in four months. The company has also created an email id through which any employee can communicate directly with the top management any time he/ she wants.” “My impression of the boys when I started interacting with them was that they are just kids. They have zero experience of industry and zero maturity.” This is one definite outcome, management is cautious with these young workers, they try by all means necessary to ‘understand them’ and to created new channels of ‘conflict management’. The unofficial outcomes, see below, are definitely due to this cold fear on the top.
In the meantime we should not forget that the dispute has not been resolved at Suzuki Powertrain India (SPIL). During November output levels were said to have dropped to 60 per cent – result of a go-slow protest. Focus of this protest has narrowed down to the demand of re-instatement of three trade union representatives who had been sacked during the June – October struggle. Protest meetings took place on 9th of November 2011. Subey Singh, the president of the Suzuki Powertrain Workers Union on 12th of November: “The management has been pressuring me to accept a payout many times higher than that offered to Maruti’s labour leaders. I have been offered money. They have been asking me what is it that I want (to resign). However, I have refused to accept any payout. I will not become a traitor to the labour workforce that has elected me their leader.”
The unofficial aftermath
There are two sides to the unofficial aftermath, one side relates to the wider changes the strike enforced on management and industry, the other side on how workers re-organise themselves after this experience. In the following we are only able to hint at some of the changes, which the struggle imposed; changes which did not make it into official agreements. Immediately after the dispute ended Maruti management called workers for a company meeting. “The factory manager said that it has been mentioned that a share of the profit will be distributed to the workers. The wages of the trainees and the workers hired through contractors will be increased. The wage agreement for the permanent workers runs till April 2012, so their wages will currently not be increased. You will get 16 days of paid holiday per year. There will be more company buses and their route will be extended. You can form a work committee. A worker: “For how long will this committee last?” (FMS). The wages of the apprentices were increased from 4,700 Rs to 6,200 Rs in October 2011. Apart from higher wages workers say that the middle-management and supervisors are much more respectful towards them. Also the work load seems to have eased a bit. Mr Roy, production manager in Manesar said in an interview in the The Hindu that the plant was configured to work as a ’50 second line,’ to produce a maximum of about 1,152 cars a day over two shifts of 8 hours each. This summer the company hoped to produce about 1,200 cars a day, or a 48 second line. “Prior to the troubles we were making about 1070 cars a day,” said Mr. Roy, “At present we are making about 800 cars a day.” (6th of November 2011)
The unofficial outcomes are not confined to Maruti Suzuki itself. On 24th of November motorcycle manufacturer Hero announced wage increases ‘across the board’ – menaing for their permanent employees. “For white-collar employees, the pay has been raised as much as 30 per cent, while workers at the Dharuhera plant have got a monthly increase of Rs 6,500 each. The pay increase for blue-collar workers will be spread over three years depending on their staying with Hero. “No company wants to go through what Maruti Suzuki India Ltd, the country’s biggest car maker, had to endure in the past few months. Hero’s wage increase will help ensure that there’s no disaffection among workers.” If we assume a monthly wage for permanent workers of around 30,000 Rs per month, than we talk about an annual wage increase of about 7 per cent – at a current annual inflation rate of around 10 per cent (which is only partly compensated for by Dearness Allowance). More importantly than the rather ‘relative’ wage increase is the fact that the wage difference between permanent and temporary workers is very likely to have increased, too. Hero has a specific history of division between permanent and temporary workers, backed by the permanent workers union, in particular at the Dharuhera plant.
Factory Occupation at Hero in Gurgaon, 2007
https://gurgaonworkersnews.wordpress.com/gurgaonworkersnews-no4/#fn2
Lock-out of Temporary Workers at Hero in nearby Dharuhera, 2008
https://gurgaonworkersnews.wordpress.com/gurgaonworkersnews-no-919/#fn6
The Second Blow of Crisis for the Global Automobile Industry
The strike had a significant, though temporary impact on Maruti Suzuki’s profits and sales. On 20th of October 2011 Maruti management announced that the half-year profits (Q2) were down by 60 per cent and that the market share shrunk to 39.5 percent, from around 48 per cent. These figures must be terribly worrying for management and share-holders, but even more worrying for the gentlemen are the global long-term trends.
In India and China the impact of the crisis 2008 did not affect sales figures too much, partly because of the cheap money policy of the governments. Shrinking profit margins were still counteracted by increasing sales. Based on the growth figures all car manufacturers opened extra capacities, e.g. Maruti started to buy land for a third plant in Gujarat, claiming to set-up capacities for another 2 million vehicles per year. Shrinking profit margins cannot be explained by increasing wages of workers, wages of workers fell relatively, even in the ‘well-paid’ car industry. Maruti’s labour cost was 1.91 per cent of its net sales in the financial year 2011 compared to 3.21 per cent in financial year 2002. During this period, sales have increased by five times to Rs 37,500 crore [one crore = 10 million] from Rs 7,500 crore while labour cost moved up from Rs 227 crore to just Rs 694 crore.
The workers’ wages are already squeezed to the limit, and although they cannot account for decline of profitability, the workers’ pockets and bodies are the only source to be squeezed more. In particular after sales figures in India and China have started to follow the global downward trend. In the last year a combination of general economic slow-down, increasing interest rates to tackle inflation, rising petrol prices have put pressure on sales. In October car sales in India suffered their sharpest decline in over a decade, a fall of 24 per cent compared to the previous year. The fourth consecutive month of decline for the car industry. The Society of Indian Automobile Manufacturers (SIAM) started lobbying for measures such as scrapping all vehicles manufactured before 2000 – to copy the eco-packaged subsidy model of the German government. In October Siam slashed its sales growth forecast for the current financial year to 2-4 per cent, the second cut in estimates from an initial forecast of 16 to 18 per cent. In China, the other ‘last resort of automobile capitalism’ the car market grew about 48 per cent in 2009, 34 per cent in 2010 and 4 per cent in 2011. The state subsidies ran out. While we still speak about ‘growths’ in Asia, we speak about absolute decline in Europe. In 2012 the European car market is supposed to shrink by over 5 per cent, this are about 600,000 cars, meaning the annual production of two assembly plants.
The immediate reaction by capital is to further reduce labour costs, either by reducing wages, lay offs or plant closures. Lay offs and the threat of closures is largely used to coerce workers to accept lower wages. In the USA, while Maruti workers in Manesar striked for better conditions, the UAW trade union accepted 50 per cent wage cuts for newly hired workers, a major generational division in the plants. In Italy FIAT announced in October 2011 that all collective contracts for the 70,000 FIAT workers will be terminated in 2012 and wage cuts will be cut in result. In October FIAT closed the plant Termini Imerese, a smaller factory manufacturing for Lancia. The factory is supposed to continue running under management of Chinese companies (Chery, Gonow). At the same time Maruti Suzuki announced a new joint-venture with FIAT in Italy concerning common engine manufacturing, and Maruti supplier Talbros engaged in a closer collaboration with FIAT’s supplier Magneti Marelli – see workers reports below.
Capital will only be able to drop labour costs on a global level if it ‘globalises’ wage levels in relates different wage levels directly. The car export from Asia to the global North increases, but export of car parts increased more significantly than ‘ready-made’-cars export – meaning that an actual global cooperation between automobile workers is taking shape. In the future two aspects will be decisive for working class struggle: will workers be able to turn the ‘global integration of markets and production’ into a global strike-front; and will we be able to use the togetherness and creativity brought to the fore during struggles to imagine and experiment with a different concept of mobility – beyond the car. Following text can serve for debate – against the automobile nightmare, from the perspective of an automobile worker:
http://www.wildcat-www.de/en/wildcat/83/w83_auto_en.htm
In the meantime disputes continue. On 19th of November workers at Hyundai Motor India protested against increased work load on the shop floor. Representatives of the HMIEU said that the car manufacturer has hiked the work load without consulting with the union. In the assembly shop, for instance, the work done by 30 workers is expected to be done by 25. Workers at the factory in Sriperumbudur, near Chennai, have boycotted the canteen facilities in protest.
* Articles by Faridabad Majdoor Samachar On Maruti Struggle, October/November 2011
Faridabad Majdoor Samachar no.280 – October 2011
Maruti Suzuki Manesar – Disciplinary Regime from Head to Toe
* A worker sitting outside the Maruti Suzuki Manesar factory during the time of protest, on 29th of August 2011: “We have to think about life beyond the routine of shifts and job, We have to think properly about it once we find the time.”
* A young workers hired through contractor at the Maruti Suzuki Gurgaon plant: “In the bumper shop the supervisors swear at you openly. The permanent workers, as well, do not respect us. It is us who are forced to do most of the work. The work load at the bumper assembly is extreme, and you won’t find any permanent workers there. There are five stations and 15-16 workers hired through contractors work on each shift. I want that in this world everyone can live, everyone can live happily.”
* A worker who got dismissed from Maruti Suzuki in 2000: “These boys are no losers. These guys from the Manesar factory have both energy and passion to fight.”
The collectivity amongst permanent and temporary workers has grown after June 2011. The sudden occupation of the factory in June was a glorious beginning. On 27th and 28th of July the collectivity of temporary and permanent workers forced the company and state to retreat: the standing together of both categories of workers forced the police, who came to arrest workers from the plant, to leave empty handed. The youthful energy softened the rigidness and became a container for laughter and happiness…
From the companies’ side the united voices of the well-dressed walking corpses say: “Indiscipline will not be tolerated!” The noisy answer of young workers, expressing the force of life: “Authoritarianism will not be endured.”
The tune and collectivity of the young workers which shook Maruti Suzuki Manesar is part of the young energy which sends ripples across the globe. The youth in Tunisia, Egypt, Yemen buried state leaders who had been unmovable for decades. In Greece, France, Spain and England the undisciplined youth started to blockade the system of wage labour. In Afghanistan, Pakistan, Jharkhand, Chattisgarh, Orissa artisans, peasants and rural poor revolt against social death and murder. In one of the main financial centres on Wall Street in New York in America, every day thousands of people assemble in order to oppose the global money system.
This is why Maruti Suzuki and the state had to launch a direct attack on the workers on 29th of August [lock-out, good conduct bill]. Secret plans forged behind closed doors, concealed preparations… be it army officials, company officials or their special advisors, all these people have become trapped in their formula that two and two equals four. The fact that two and two always equals four on paper has increased the force of the bosses, but in society, in practice, two and two can sometimes be fifty, sometimes zero, sometimes even minus twenty. According to the habitual drill of the governments’ armies and their allies two and two is always four… …but in practice ,instead of delivering any solution through their many attacks around the world, the armies joint in the NATO only increase the crisis. Amongst the leaders of this world this is no one who can make sense of their situation. The planned and prepared attack of Maruti Suzuki and the state on the workers did not have the desired result…
Walls Replace the Tarps
The factory area stretches out on 600 acres. In order block the view and to demonstrate their strength the company put up tarpaulin behind the fence barb-wire fence surrounding the factory area. After the weakness of the company manifested itself during the struggle, management started in October to build a high wall around the plant. The first coal and steam based factories 200 years ago were forced to take the shape of fortresses, because at night they were attacked by scores of artisans (black-smiths, weavers etc.). Now the process of turning factories into fortresses started again. This time the bosses nightmare has come true: the workers are both inside and outside of the factory. They can see nothing but enemies, both inside and outside the fortresses walls, The security guards they hire through contractors have to work 12-hours a day, 30 days a month – more potential enemies…
In Germany people’s protest forces the government to shut down nuclear power stations. The party and government in China, armed with science, fears the youthful force of turmoil amongst peasants and workers. In Bangladesh, when workers revolt, they burn dozens of factories down.
Pieces of Paper
Maruti Suzuki, the state and the middlemen had hard work to forge the ‘agreement’ in June [ending the occupation]. But the workers treated the agreement as mere pieces of paper. The bosses, who break their own laws and rules on large scale day by day, could not stop lamenting about the ‘murder of law and order’. On 30th of September, after a long tormenting process, the bosses again signed an agreement [to end the ‘lock-out]. And on 7th of October, by occupying the factory, workers again called a piece of paper by its name: a mere piece of paper. Those leaders and officers whose daily job it is to break the sacredness of words and promises now call for the defence of the ‘sacredness of the agreement’.
Sweet Force of the Youth
They run from one crisis to the next in a desperate race to manage one after the other. The key solution of the experts is: to squeezed the common people even more. The experts then cannot understand why in result the crisis depends and gives birth to new crisis, instead of solving them. In the meantime the permanent workers and trainees occupied the factory on 7th of October in protest against the companies refusal to let the workers hired through contractors back inside the factory. This time the force of the youth was not limited to Maruti Suzuki, on the 7th of October 11 factories in Manesar were occupied.
This is the time to develop a collectivity amongst permanent and temporary workers, unemployed, the rural and urban poor. This is the time to replace ‘mine-yours’ with ‘ours’. This is the time to occupy factories and to bury them. It is time to build a new society, which replaces the today of money and competition, the present of markets and opponents with a togetherness of people and the acceptance that the human species forms a part of nature.
Points for the conversation with workers who sit outside the Maruti Suzuki factory gate since 29th of August 2011
1. We cannot turn back time. Therefore it is important to focus on the now and the near future, when deciding about next steps.
2. Maruti Suzuki company and the state have launched a prepared attack on the workers in the early morning of the 29th of August. It is obvious that we have to resist this attack, therefore we should make those steps our common focus which increase our strength.
3. It is agreed fact that the permanent Maruti Suzuki workers have decided not to sign the ‘good conduct conditions’. Therefore, if this conflict remains limited to Maruti Suzuki then another painful outcome is awaiting us. In the recent past sporadic support rallies and demonstrations and short-lived strikes in single factories did not manage to change things.
4.In order to widen the collectivity against the attack of the company and government we have to take the whole of IMT Manesar as our initial place of activity.
5. As long as we treat it only as an issue of the Maruti Suzuki workers it will be naive to expect more than compassion from others. This is why we should see the main problems and worries of the workers in IMT Manesar as of common importance.
6. High work-loads, at each step humiliations, very low wages, fear due to not knowing when they will kick you out again, being forced to work 12 to 16 hours a day… this is the reality which the worker faces in anger and helplessness. This is why in a first step we can join up in collectivity to turn the question of how to put an end of the contract system and how to enforce a wage of at least 100 Rs per hour into a common issue.
7. At this time it would be easy for the Maruti workers to go in small groups of 10-20-50 and to talk to other workers employed in factories in IMT Manesar. In this way it seems viable that the 2,500 Maruti workers can join up with 10,000, 20,000, 50,000 or 100,000 other workers and undermine the attack by company and state.
8. Parallel to spreading the word in IMT Manesar it won’t be too difficult to undertake collective steps together with workers in nearby Gurgaon. On this background it should not take too much time until workers in the Delhi area (Gurgaon, Delhi, Faridabad, NOIDA, Gaziabad, Bahadurgarh, Sonipat) are able to undertake practical steps.
9. The setting up of a workers struggle committee could happen be based on a brief and swift agenda.
10. Nowadays it seems very easy to create a coordination/collectivity with students.
11. It does not seem to be in too distant future to raise the question of (or to put into question) the wage system as such… within the worldwide churning and emerging coordinations lies the possibility to find significant support and inspirations.
The impact of the Maruti Suzuki workers’ movement can be seen amongst the Munjal Showa workers on the 12th of September. Workers in this factory in sector III stopped work at 3 pm in order to protest against the employment of temporary workers for permanent work. The workers at neighbouring Satyam Auto company immediately started coming and going to and from Munjal Showa. The workers at Munjal Showa Gurgaon and Haridwar plant also stopped working. On 13th of September at 8 pm management immediately made 155 workers permanent and after having given reassurances , management had to catch their agitated breath.
On 14th of September at 4 pm workers of two shifts at at Suzuki Casting, Suzuki Powertrain and Suzuki Motorcycles stopped work, started demonstrations inside the plants, shouted slogans. The production stopped and the gathered workers inside the factories demanded that the Maruti Suzuki Manesar workers should be taken back and the good conduct bond should be withdrawn.
On the 15th of September the production in these three factories was still halted and very animated workers still inside the plants. In front of the Maruti Suzuki factory young workers, laughing and making jokes. They marched to the occupied Powertrain factory, shouted slogans in support, gave speeches, sung songs, distributed flyers. Beautiful words, interesting discussions. The drivers of the sale and dispatch department stopped working in the C-shift. On 15th of September the A and B-shift of he 350 drivers hired through contractor gathered in front of the SND gate of Maruti Suzuki, even in the heavy rain, taking cover under trees and bushes.
“Hoo!-Hoo!-Hoo!” – this growing noise from the workers means that the media guys gave arrived. Once the news made the round that people form the media have arrived the workers sitting in front of the Maruti factory started to shout rounds of “Hoo!” noises. During the course of the struggle childhood illusions have evaporated. “When I was in the 11th class I still believed in what The Times of India was saying… The fact that this newspaper printed the whole speeches made by the Maruti Suzuki chairman has opened our eyes.”
On 16th of September production was made to be resumed at Suzuki Casting, Engine and Motorcycles. The company was willing to enter negotiations, but put the condition to it that work should first resume at the three factories. The middlemen were compliant. The union rally was cancelled. Obviously, having witnessed the general atmosphere even the traditional steps (like rallies) have scared the state, company and middlemen several times.
In the night of the 18th of December negotiations between labour department, company and workers took place. There was no scope for an agreement. Ending unsuccessful, the police arrested three workers right from the venue of negotiations. The hope of the bosses was that in reaction the workers would cause trouble, which would have given more chances for in the state and companies’ plan to succeed.
Despite this instigation the Maruti Suzuki workers did not run riot. The kept calm. Steps were undertaken to bail out the arrested workmates. They were released on the 19th instead of the 20th of September.
The company made it an exercise to use the mobile phone, which was given to workers for 10 million manufactured Suzuki cars, as a management tool against the workers. While the three workers were in jail, the company phoned up the trainees. “Why don’t you go inside? We had put up a notice saying that you the trainees don’t return to work by 19th of September you can see yourselves as fired. You have been fired, but nevertheless, now you still can come back to work.”
Maruti sent 4 to 6 letters to the home of each employee. They sent text-messages to their phones. On 20th of September: “Dear employee”, on 21st of September: “Dear friend of the Maruti family”, then “Dear fellow workmen”. They sent a help-line number, a link where workers could watch a video about the ‘true situation’. They sent quotations from Vivekanand and Napoleon. The company send managers to the villages and homes of workers (in order to speak to their families). When workers sitting in front of the factory heard from their families about it they said: “Don’t ask him questions. Keep cool and give the gentlemen food and drink and say farewell to him with respect.”
The company said (during the lock-out / protest-camp): Today we have produced 670 cars. A manager then said: On the day we manage to manufacture 1,000 cars you will all be fired.
The company assembled some village chiefs of the villages Aliyar, Dhana, Baas, Mangrola against the workers: “Go inside the factory, otherwise leave this area.” In the night some of the villagers drove around in cars, drunk. Some increased the room rents of workers. They threaten the workers at night, speak with soft voices the next day and greet the Maruti Suzuki workers in villages a bit further away from the scene.
The company plan gut stuck, the workers obstructed it. The company changed its tactics. The middlemen were again been activated. In the meantime the workers had realised that sitting in front of the gate and merely hearing talks about support and help wouldn’t move things forward. So on 23rd of September the factory union leader of the Gurgaon plant arrived with three bus loads full of workers. Union leaders of the three other Suzuki Group factories also arrived. Speeches and discussions. Around 250 permanent workers of the Maruti Manesar factory gave their signature to an agreement saying that the Gurgaon factory leader should take part in negotiations on their behalf.
After it seemed that a frontal attack on the workers would turn out unsuccessful, state, company and middlemen started to act from a new angle. A long process of ‘explaining-advising’ took place. A lot of phoney reassurances were dished out as usual, but some genuine reassurances were given by young workers from other factories in IMT Manesar. On the 30th of September, late at night, an agreement was signed.
Conditions of the Agreement
1. Both sides accept that the termination of those 15 workers who were dismissed by management between 29th of August 2011 and 15th of September will be revoked and turned into a suspension. But they will undergo an independent investigation according to the legal procedures and future steps will be decided based on the outcome. Whatever is the outcome, both sides will accept it.
2. Both sides also accept that those 18 trainees who had been dismissed between 29th of August to 30th of August will be reinstated from 1st of October onwards.
3. The 29 workers who had been suspended between 1st of July and 17th of September 2011 will remain suspended. A charge sheet will be issued against them and an independent investigation will take place. Both sides will accept the outcome of the investigation.
4. Both sides accept that from 29th of August the ‘no work, no pay’-rule applies and that as penalty one day wage extra will be cut from wages per one day of no work.
5. Both sides agree that workers will take a day off tomorrow, 1st of October, and resume work on 3rd of October after having signed the good conduct bond as wished by management. The day off on 1st of October will be compensated for in the near future by working during a bank holiday (day off).
6. Both sides accept that workers will keep discipline, will not obstruct production neither collectively nor individually. The management promises not to act against workers scornfully.
7. Both sides agree that in case of future disputes both sides will try to solve it by conversation amongst each other.
8. Both sides will not abuse the fundamental rights of the other and based on this agreement they will not hold scornful feelings for the other, but act in full loyalty.
9. After the agreement both sides accept that all disputes between the parties have been solved.
On the 3rd of October permanent workers and trainees went inside the factory. Around 1,200 workers hired through contractors where not let inside the plant. On 4th and 5th of October these workers were still refused entry. The anger grew. People who were on the side of the company irritated (bullied) and agitated these workers. The company had given a clear order to the contractors not to let these workers return to work at the Maruti factory.The company saw the growing collectivity amongst permanent and temporary workers as their main source of trouble. Out of anger around 100 temporary workers left, but the rest kept on putting pressure on the permanent workers. The temporary workers put pressure on the 44 suspended workers to take things forward.
After Dusshera (festival), at 10 am in the morning of the 7th of October the workers hired through contractor arrived at the factory gate. Thugs turned up to threaten them. A suspended worker, who was also a member of the factory committee, interrupted the bouncer and gave him something to chew on by saying that the workers hired through contractors had also signed the agreement – the bouncer then dragged his tail and left. The workers of other IMT factories who had reassured the workers offered support. Workers gathered at the factory and at 1 pm it was decided that at 4 pm, when both B and C shift are inside the factory, workers would stop working and occupy the factory.
On 7th of October at 4 pm the permanent workers occupied the factory, demanding to take back the workers hired through contractors. At Suzuki Engine, Suzuki casting, Suzuki Motorcycle, Satyam Auto, Bajaj Motor, Endurance, Hi-Lax, Lumax DK and other factories workers stopped work, started demonstrations inside the plant, occupied it and demanded the taking back of the temp workers at Maruti. The state sent more than 200 police men into the Maruti plant. They stayed established themselves there.
On the 8th of October the occupations at the four Suzuki factories (not the Gurgaon plant) were kept up. The company had closed the canteen, therefore the workers themselves organised the food. Under pressure the workers at the other factories had restarted work. The other four factories maintained the protest for the 44 suspended and the workers hired through contractor.
On this background remember the poster which was put up at the Maruti Suzuki gate on 30th of September…
About how to increase the power of and with the Maruti Suzuki Manesar Workers
*Company and state have executed a pre-planned and prepared attack on the workers on 29th of August.
* The workers’ collectivity has resisted this attack successfully for one month now. Their mutual help and care provides strength for the workers.
* The collectivity amongst permanent workers, trainees, apprentices, workers hired through contractors has put a halt to Maruti Suzuki management and the state’s attack. It has pushed the attackers back.
* How can workers increase their strength? This has become an important question.
* For the Maruti Suzuki workers and the workers in IMT manesar to join up seems like an easy and simple first step.
* In order to come closer and to extend support and mutual care it seems necessary to raise common questions.
* The very low wages and the fact that temporary workers are employed for permanent work and similar issues seem to provide a common ground. If we look at the price increases wages in IMT should be at least 800 Rs for an 8-hours day. On this bases and the goal to put a stop on the contract system the Maruti Suzuki workers can link up with workers in hundreds of factories in Manesar.
* There is time. And there is young energy. Going out in groups of 5 to 10 the Maruti Suzuki workers can quickly reach other workers in Sector 8,7,6,5,4,3 and talk to them about the 800 Rs for 8 hours question, the question of putting an end to contract system.
* Turn the Maruti Suzuki issue into an IMT Manesar issue – this can push back the attack.
———-
Faridabad Majdoor Samachar no.281 – November 2011
Maruti Suzuki Diary
* On the 7th of October at 4 pm eleven workers in IMT Manesar occupied eleven factories. The issue has spread beyond Maruti Suzuki, following its essential character, which is not confined to one company. The speed with which is spread puts in front of us the potential and reality of the turmoil in thousands of factories.
* Under the pressure of the state, companies and middlemen on 8th of October the occupations were reduced to the four plants of the Suzuki group. The Maruti factory in Gurgaon was not occupied, but the middlemen were unsuccessful to make workers go back to work at Suzuki Powertrain, castings and Motorcycle. These workers had made the experience of how middlemen call for and call off strikes on 14th to 16th of September.
* At Maruti Suzuki Manesar the issues of taking back the 44 suspended permanent and allowing the 1,200 to 1,400 workers hired through contractors to re-enter production became one. At Suzuki Powertrain and Motorcycles permanents and workers hired through contractor joint together and turned the issue into a common issue of the four plants.
* The central government was entangled and preoccupied with the regional elections in Hisar and therefore not able to intervene. The general atmosphere during the period of the four factory occupations between the 7th and the 13th of October was one of commonality and easiness. The company did not have any clue how to solve the issue. The bosses did not know what these workers wanted.
* Conversation amongst workers in one factory: “Previously one would leave the factory during strike, now we stay inside. To leave the factory means to hand it over to the company and gives them more scope to act. To stay inside means to keep the control over the factory.” But… but to be kept outside the factory or to stay outside of the factory gives us the immediate chance to create links with workers of other factories and to join up. Yes, to only sit in front of the gate and blow hot air means to have become trapped.
* The problem which the Maruti Suzuki workers face is the problem of all of us and in October the solution was amongst the workers in IMT Manesar coming together and building a big damn by helping and supporting each other. The position that the power of the workers in the four factories alone was sufficient was dwindling. .
* The propaganda churned out by radio-TV-newspapers did not have any effects: Maruti will close down the plant and go to Gujarat, two hundred thousand jobs will be lost here, the strike causes huge losses for the tax revenue of the Haryana and central government, we have to accept factories as means of provision, they are a way out after the collapse of the workshops, the wages of the Maruti workers are high and they just think about themselves… all this talk was pushed into the background by the questions of ‘how to survive’ and ‘how to live a good life’ which emerged during the struggle.
* The Maruti Suzuki workers listened to everyone, but acted according to what they thought right – this is why they did not end up in the fist of the middlemen. The unions set up a committee to support the strike, composed by seven members. Amongst them the leaders who came to give speeches during the general assembly on 13th of October in front of Maruti Suzuki. The elections in Hisar were on the 13th of October and the Haryana-Punjab high court had ordered to leave the factory on the 13th of October… the union leaders said that if the government uses force, we will take action all over IMT manesar, all over Haryana, all over India.
* On the night of the 13th the police took the communal kitchen from the Powertrain gate. In Aliyar village a new kitchen to supply workers with food was set up. Huge numbers of police gathered at Manesar police station. In front of the office of the district administration a long queue of empty Haryana Roadways buses formed. On the 14th the Gurgaon DC went inside the factory and conveyed the high court order to the workers, told them to leave the factory and to enter into negotiations.
* The union committee phone the union leaders and told them to call for strike and to support the Maruti Suzuki workers. The leaders said that they will call for a meeting at noon that day. Work was not interrupted in any factory and none of the small and big leaders turned up at the Maruti factory. The police stopped the food supply to the workers inside. The factory committee said that it was ready to leave the factory by 7:30 pm. At 8 pm a leader arrived at the factory and told the committee to tell the workers to leave the plant. The leader spoke to the workers inside by using a mic. There was resistance. In the end the workers left the factory.
* On the 15th of October a huge police force gathered inside and outside the Suzuki Powertrain factory – according to a correspondent of a Punjab newspaper about 4,000 cops. The 2,000 workers refused to leave the factory. A demonstration of 2,000 workers arrived from the Maruti Suzuki plant and sat down in front of the Powertrain factory. The tension rose. Some middlemen turned up. The powertrain workers left the plant. A joint demonstration went back to the Maruti Suzuki gate.
* On the 17th of October a rally-demonstration-handing over of a memorandum took place in Gurgaon, called for by the unions. Two hours of speeches, but no action plan was announced. Tripartite negotiations started at the Huda guest house. Maruti published again figures after figures about how many cars they were able to produce. Some workers went back inside the factory to resume work.
* On 19th of October three Powertrain workers who took part in the tripartite negotiations were separated from the negotiations, seated in a separate room and their mobile phones were taken away. On the 19th of October Maruti Suzuki signed the agreement. The Powertrain agreement was signed on the 21st of October – workers who took part in the negotiations were not allowed to leave the site of negotiations during all that time. They did not allow anyone to support them (with advice), when they went smoking or to the toilet, policemen were always with them. It is said that it was an oder by the government that until there is an agreement no worker should be allowed to leave. Accoring to clause 6 of the Suzuki production was supposed to be resumed by B-shift on the 20th of October… but production was not resumed by early evening on the 21st of October…
The Agreement
1. Both sides agree that out of the 44 employees who were suspended according to the agreement on 30th of September 2011, 22 employees will be subjected to thorough investigation. The investigation should take place within the next ten days. Whatever the investigation will come up with will be accepted by the employees. If the investigations turns out to be in disadvantage to any employee, the employees agree to abstain from any protests, such as tool-down strike, sit-in strike, protest rallies and so on. The remaining 25 employees will undergo an initial investigation and according to decision, will return to their work on 20th of October 2011. Those employees who had been suspended earlier (case 807222) will undergo a thorough investigation. If the decision turns out as disadvantageous for the employees, no employee will resort to any protest, such as tool-down strike, sit-in strike and so on. The remaining 9 employees will undergo an initial investigation and according to outcome will return on the 20th of October 2011.
3. Both sides agree that from the 7th of October onwards the rule ‘no work no pay’ applies and that as penalty one day’s wage per day of strike will be reduced from the salary.
6. Both sides agree that production resumes immediately with the B-shift on 20th of October 2011.
10. From 30th of September onwards the company bus services for employees will be re-installed.
11. Both sides agree that the management of the company will request the contractors to accept the conditions which had been given for the contract workers on 29th of August 2011.
* On the evening of the 21st of October the Maruti Suzuki workers were happy, they were shouting slogans. They believed that the 30 suspended will return within the next 10 days. But the union president was nervous, words were spread. People who haven’t read the agreement, said what they had heard about it. When the union general secretary did not appear on the platform, the workers put up pressure and let him be called to speak. In the speeches of the leaders there was no force, the speakers to not shout any slogans or encouraged workers to do so.
* On the 22nd of October the A-shift went inside the factory, but neither in the morning nor the evening any of the committee members turned up. Why did they not turn up? People from the media turned up.
* On the 22nd of October the factory manager called for a meeting. Small groups of more silent workers were called from each department. The factory manager put on a very serious face. He said: “Why are you guys down? Come on, be happy.” A worker: “Even when we are angry, we are still happy.” The factory manager said that it has been mentioned that a share of the profit will be distributed to the workers. The wages of the trainees and the workers hired through contractors will be increased. The wage agreement for the permanent workers runs till April 2012, so their wages will currently not be increased. You will get 16 days of paid holiday per year. There will be more company buses and their route will be extended. You can form a work committee. A worker: “For how long will this committee last?”
* On the 23rd of October it has reached the ears of all workers that something was wrong. The union president and general secretary had secretly resigned from their job. The union president had disappeared after announcing the agreement. When called the general secretary only spoke hot air. The factory union committee has been made defunct. News make the round that 5, 10, 15 of the suspended have resigned from their jobs.
* In the factory none of the workers speak about the agreement – those who made the agreement have nothing to do with us anymore. There are preoccupations, but there is no fear. The fear had been expelled. People ask themselves what could be done now? Now that neither the management nor the workers rule in the factory. On Sunday, 24th of October workers talked about the fact that the current payslip shows that 10 Rs has been deducted as contributions for the old union. The company became anxious and stopped handing out the payslips. They said that they will issue new ones, that the 10 Rs will not be deducted, that the new ones will be out by 30th of October.
* The situation that has emerged has forced Maruti Suzuki to take back the 1,200 temporary workers. Given that the issue has become reduced to the Suzuki factories the workers there depend more and more on support and cooperation of other workers.
* The bosses are not able to understand social processes. This is why they make individuals or small groups responsible for a situation and use all force to deal with them. This is why state and company feel relieved after Maruti Suzuki has dealt with the 30 leaders at their plant and the 3 leaders at Powertrain. Whereas, during the last five months these workers have been brought into a position where they were able to play an important role to keep the workers under control. It is the twist of these times that the government and company in their agitated state have thrown away their well suited tools by making these workers resign from their jobs.
Today, from a new angle, and at a new level, life has surfaced again.
* Automobile Workers’ Reports from Faridabad, Gurgaon, Manesar
Following six reports concerning workers in the local automobile industry. The first two are from mainstream newspapers, the following four were told to Faridabad Majdoor Samachar.
Living Conditions in Caterpuri
“Roughly 70 per cent of the residents of Carterpuri-named after the former US president Jimmy Carter, who came calling in 1978-work in Maruti Suzuki and other factories. “We hardly go to the malls. It makes us feel low, it’s frustrating,” says 24-year-old Dharminder Singh, a contract worker at Maruti and a resident of Carterpuri. “When you earn Rs. 6,700 a month, you cannot eat out, visit malls and, of course, feel on a par with others.” There’s a story behind the name. It used to be called Daulatpur Nasirabad before the 39th president of the US came calling in 1978. Jimmy Carter was looking for the area in which his mother Lillian had worked as a nursing volunteer in the 1960s. A name change seemed propitious.”We thought the renaming of the village will change our fortunes but Gurgaon became a city and we stayed where we were,” says Attar Singh, a resident of Carterpuri, now in his late 60s. Carterpuri is a low-lying area that gets flooded with sewage from the private colonies around it. Flies and an overpowering stench of open drains hangs in the air. Ironically, while part of Maruti’s corporate social responsibility (CSR) initiatives involve welfare programmes in and around areas close to its plants, Carterpuri has never figured in them. “We have adopted four-five villages in Manesar where we try to improve the living conditions,” says a company spokesperson. “Our workers may be living there as the village (Carterpuri) is in the vicinity of our plant but living conditions in that village never came to our notice.” “The company considers the local community an important stakeholder.”
We find this ‘local community’ concern of Maruti particularly ironic given that one of the forces used by management against the strikers was ‘the local community’ – bought by Maruti money – in form of landlords, panchayats and thugs.
Working Conditions at Maruti
“When I first began working for Maruti, assembly lines used to run right through my dreams,” said a worker with a laugh, “These days I suppose I’m so tired that I don’t get dreams anymore.”
In Manesar, Maruti produces about 180 variants of three basic models. When a car rolls in, the worker looks at a large matrix pasted on the vehicle that indicates if the car is a left or right hand drive, powered by petrol, diesel or compressed natural gas engines intended for the domestic, European or general export market. Depending on his work station the worker chooses from 32 different upholstered seats, 90 tyre and wheel assemblies, and innumerable kinds of wire-harnesses, air conditioning tubes, steering wheels, dashboard trims, gearboxes, switches, locks, and door trims, in an average time of 50 seconds per car. For parts like air conditioning tubes, the worker stands between a set of parts racks. As a particular car variant rolls in, a light above the corresponding parts rack blinks with increasing urgency as the worker runs to it, grabs a part and pulls a cord to acknowledge he has chosen the right part. He then steps onto the conveyor belt, fits the part and rushes back to match the next car to the next blinking parts rack before an alarm rings. If the line halts, signboards across the shop floor light up – flashing the number of the workstation where the line has stopped and the duration of the stoppage. Another board displays the total time ‘lost’ during the shift; a scrolling ticker lists the production targets at a given time of the day, the actual cars produced and the variance. “For every fault, the feedback is recorded and the worker has to sign against it… it goes into his record,” said a worker, speaking on condition of anonymity as every Maruti worker must sign ‘Standing Orders’ that, among 100 other conditions, bar them from slowing down work, singing, gossiping, spreading rumours and making derogatory statements against the company and management. The work record is examined during yearly appraisals. (Gone in 50 seconds, Aman Sethi, The Hindu)
Omax Auto Worker
(Plot 6, Sector III, IMT Manesar)
There are two 10.5 hours shifts, 200 permanent worker and 1,200 to 1,300 workers hired through six different contractors. They manufacture motorcycle parts for Honda, hero Honda, Suzuki and Minda. Per month workers work 60 to 84 hours of overtime, the payment is less than single rate, around 16 to 20 Rs per hour. Of the 800 newly hired workers each month 10 to 15 hours overtime get embezzled. The helpers are paid 4,214 Rs. From these wages contributions for ESI and PF are cut, but only some workers receive the PF money when leaving the job. The highest pressure is on the welding workers, the air pollution is unbearable.
QH Talbros Worker
(Plot 51, Sector III, IMT Manesar)
In the factory 100 permanent workers, 50 casuals and 300 workers hired through contractors produce steering rods for Maruti Suzuki, Tata, Escorts, Sona Steering and for export. The permanent workers work on 8 hours shifts, the rest of the work-force on two 12-hours shifts. The permanents get double rate for overtime, the rest single rate. After paying initially 1,500 Rs each and then 100 Rs monthly, the permanent workers joined a union about a year ago. Many other workers initially also gave 200 Rs for the union. At the beginning of May management suspended one worker accusing him of stirring up trouble. After coming back from leave the company refused to take back four workers hired through contractor – they were accused of having taken part in hoisting the union flag. The company has hired 60 to 70 trainees for two years, after their training they were supposed to be made permanent – but so far out of 18 trainees who passed the training 4 were dismissed. In order to put up resistance against all this, the INTUC union gave a strike notive to management for the 5th of May. Since the 20th of May all workers sit outside of the factory in protest. On the 23rd of May nothing came out of the negotiations between management and union at the labour department.
Talbros Automotive Components and Magneti Marelli signed agreements on November 16th 2011, for formation of a 50:50 joint venture to manufacture suspension systems and modules. The JV will start its operations in Faridabad, Haryana, and will manufacture various components including control arms, knuckles, and front axlesand rear axles for automobile applications. Mr Eugenio Razelli CEO of Magneti Marelli stated that “The JV agreement with Talbros allows us to further extend our presence and footprint in India, adding a business area the suspension systems in which we have consolidated know-how and long-time industrial experience. We applied once again our strategy of partnering with Indian leading companies, that up to now has brought good result in our process of localization in the country and that enables us to add value to local clients and major transnational carmakers in the country.”
http://www.talbrosit.com/comp_QH.htm
Clutch Auto Worker
(12/4 Mathura Road, Faridabad)
For their April wages management paid the permanent workers 1,800 Rs less than usual. As an act of resistance the permanent workers refused to take the wages on 12th of May. The company claims that according to the 2006 agreement between trade union and management the company can cut wages if productivity targets are not met. This is a trap… There is talk about the company opening a new factory in Rewari and so the management wants the workers to leave the job ‘on their own accord’.
Premium Moulding and Pressing Worker
(185 Udyog Vihar, Phase I, Gurgaon)
In this factory 100 permanent workers and 200 temporary workers are employed on two 12-hours shifts. They manufacture steering wheels, horns, dumpers, radiator fans for Maruti Suzuki, Tata, Tata Nano, Mahindra, Ford, Punjab Tractor. The workers hired through contractors are paid only 3,500 Rs and only 6 Rs per hour of overtime. The wages are paid delayed. The drinking water in the plant is bad.
*** Delayed Notes on Harsoria Healthcare Workers’ Strike in Gurgaon –
We already published a short note and call for solidarity in a previous newsletter.
https://gurgaonworkersnews.wordpress.com/gurgaonworkersnews-no-938/#fn4
The following is a more detailed report published and distributed in Hindi in Faridabad majdoor Samachar.
Harsoria Healthcare Workers’ Strike
(Plot 110, Udyog Vihar Phase IV, Gurgaon)
There are about 650 to 700 workers in our factory, we work on two 12-hours shifts, we manufacture IV’s and medical cannula. Due to extreme work loads the hands are always pricked by the needles we manufacture, we are told to tape our hands and continue working, the machines are not supposed to stand still. In the factories there are cameras everywhere. Wages are paid late. We receive a lot of swearing from the managers.
In order to find some relieve we joint a union in September – October 2010. The permanent workers paid 2,000 Rs each contribution, the casual workers and those hired through contractor paid 1,000 Rs each. In this way the union gathered more than 450,000 Rs.
The company turned the casual workers into workers hired through contractor, which made their situation worse. Because he objected this, the company suspended the union president on 11th of December 2010. In resistance the production output suffered, people worked slow. The company sacked individual workers, bit by bit, and put two guys with rifles at the gate. But they stopped to swear at us and the wages were not delayed anymore.
In March 2011 the company and the union had to settled their three year agreement. In consequence the workers found a little relieve… but they had hardly time to catch their breath when the company provoked the workers on 8th of April. A guy from the middle-management [staff] told workers that the union president in the factory had sold out. The union president hit the guy. Trouble. The company suspended the president and another worker.
In response the workers on night-shift stopped working on the very same day. When the management refused entry to the morning shift, the workers on night-shift stayed inside the factory. There is no canteen in the plant, so the 300 to 350 workers inside got their food passed over the fence by their co-workers. Inside and outside the factory the workers kept the noise up for 72 hours. The legal order arrived: “Get out of the plant!”. After the union told them the workers left the factory after 72 hours.
The company suspended first 5 more workers, then another 7 and finally another 4 workers. The workers staged a protest sit-in in a nearby park. Some dates for meetings with the labour department circulated. The management said that everyone apart from 7 suspended can go inside and work. On the 25th of April negotiations started between company and union in the office of the labour deputy. Around 150 workers waited for the settlement in front of the office. At 6 pm two lorries arrived – accompanied by the police – and started loading finished goods from the factory. The workers who were sitting in the nearby park came running and arrived at the gate. The police started an attack with their batons. The workers sat down on the road. The union leader arrived. He told the workers to clear the street and sit down in the park again. “The union will have a meeting and take action”.
On the 26th of April 300 workers arrived and waited for a decision from 10 am onwards. At 2 pm around 40 union leaders arrived. They gave speeches. They said that once a decision is made it has to be followed. On the 27th of April, company and union came to an agreement. At 2:30 pm a top union leader announced the result: Apart from the 7 suspended, all the other workers should go inside and work. The 250 workers who were present became very angry. The top union leader was driven away while he was still trying to continue with his speech. Another big union guy made another attempt, but was also sworn at by the workers and finally chased away. The factory union leaders and the workers organised a separate meeting. We got trapped – it became absolutely clear that we had been trapped. Leaving the 7 suspended outside the rest of the workers entered the plant on 28th of April.
Comments
*** The “Spiritual”-Industrial Complex: Involvement of Brahmakumaris and Radha Soami Panth in Industrial Management in Gurgaon –
To cooperate with hundreds of other workers (and supervisors, middle-managers) under the conditions of a modern autombile regime requires as much emotional, affective, intellectual labour as manual skills. During times of discontent this effort of affective labour, often invisible in daily life, turns into collective anger. All of a sudden management has to rediscover the ‘human dimension’ of the assembly line workers. They engage in human resource studies, participatory grievance workshops in order to win back the ‘mind,hearts (and muscles) of their workers. The following quote from a Maruti advisor after the strikes and occupations is a good example of how the representatives of capital address the contradictions their system brings forth:
“For lasting cooperation, Maruti needs to train its line managers not just in grievance redressal, but in caring for and communicating with each worker from their heart so as to develop among them a sense of ownership. That would help strengthen a workplace culture that restores the workers’ pride and dignity. This task cannot be just episodic and left to the HR department alone. The company needs to build a psychological connect with each employee, and internalise a great deal of passion in its employee care programme so as to move away from any symbolism or neglect. It must have a comprehensive communication and human relations agenda touching most aspects of the workers’ lives and their families so as to bring the alienated workers back into the mainstream and on a path of commonality of objectives as a way of life. However, nothing can replace the mantra of ‘communicate, communicate and communicate’.”
(www.business-standard.com/india/news/lessonsmaruti/454670)
All of a sudden the ‘human appendixes of the machinery’, the ‘global assembly line coolies’ have a mind and heart to care about – and obviously a soul. After the lockout at Denso in 2010, management invited the permanent workers to a week at the Brahmakumaris resort near Manesar.
https://gurgaonworkersnews.wordpress.com/gurgaonworkersnews-no-924/#fn5
Similarly Maruti Suzuki engaged Brahmakumaris ‘scientological’ advisors to take care of industrial relations after the recent lockout in summer 2011. But as you can read below, the involvement of religious sects in industrial management is not only confined to ‘post-dispute healing’, but comprises ‘pre-work education’ of manual workers.
Honda Motorcycle and Scooter (HMSI) Worker
(Plot 1/2, Sector III, IMT Manesar)
Since four years one of the managers maintains relations with the Dayalbagh Educational Institute (DEI), which is part of the Radha Soami Panth, a religious sect. The institute collaborates, amongst others, with the University of Maryland, College Park, in the USA. The manager hires (through contractors) young skilled workers from the 76 branches of the institute, who are then employed in the HMSI factory. In many districts, next to the centres of the Radha Soami Satsang there are DEI run educational institutes, which train wiring operatives and motor mechanics for four-wheelers. After the one year course they are supplied Honda, Mahindra, Tata etc.. According to the rule of ‘use and throw’, Honda uses these workers for three or four years and then kicks them out.
http://www.dei.ac.in/ssi/Home.htm
(Faridabad Majdoor Samachar – June 2011)
4) About the Project –
Updates on Gurgaon Workers News
*** Suggested Reading: Contributions to the Global Overthrow –
The global and historical character of the current crisis forces us to coordinate both debate and practice ‘for workers self-emancipation’ on an international scale. Following texts are selective, but we think that they can stand as examples for ‘general theses’, ‘concrete analysis’ and ‘historical debate’ of class struggle and revolutionary movement.
Leaflet by InsurgentNotes on the Occupy Movement in the USA:
http://insurgentnotes.com/2011/11/the-next-step-for-ows/
New Magazine from the US focusing on the Proletarian Tendencies within the Occupy Movement:
http://viewpointmag.com/
Article from Wildcat on Rural Class Relations in Indonesia:
http://www.wildcat-www.de/en/wildcat/90/e_w90_indonesien.html
Article from Wildcat on Migrant Agricultural Workers Strike in Southern Italy:
http://www.wildcat-www.de/en/wildcat/91/e_w91_nardo.html
*** GurgaonWorkersHistory: Voices from the Local Working Class History –
Sangharshrat Mehantkash no.3, 2011
The Workers Movement in the Industrial Area of Dharuhera – by Bhoop Singh
In 1977 Dharuhera was declared an industrial area by the government of Haryana. At that time Banarsi Das Gupta was prime minister. For the industrial area the government alloted thousands of acres. At that time there were already some production units situated in Dharuhera, for example Sehgal Paper, which claimed to produce ‘carbonless paper’ in India. Other units were of Suri Paper, Haryana Detergent, Multitech, Dharuhera Chemicals and East India Synthetics. At around 1981 a huge plant with the name Pashupati Spinning and Weaving. To that date the Haryana State Industrial Development Corporation (HSIDC) did not exist yet, so these industrial areas were developed by Haryana Urban Development Authority (HUDA).
With the time some of the famous industries like Sehgal Papers closed – these companies had been given cheap land by the government, which they still owned. But the name of Seghal Papers turned Dharuhera into a landmark on the map of India. In the 1980s the mentioned companies ran well – during that time the factory bosses linked up with local thugs, this is why during this period no worker in no company was able to raise their voice for their demands. Up to 1984 there was no movement in this industrial region.
Dharuhera’s first workers’ movement
The first movement was kicked off by the East India workers in June 1984. The workers were fully organised but given the lack of a proper leadership and future perspective the company bosses were a able to suppress them with the help of local leaders, one of them a member of the national cabinet, and state machinery. At the time Choudary Bhajanlal was chief minister of Haryana. His government was completely immersed in corruption. In the whole of the nation the corruption of Bhajanlal was the word of the day. Up to June 1986, as long as Bhajanlal was in government, the exploitation of workers was the most blatant. In Haryana the condition of the Congress government had become merciless. The government ministers didn’t even let the village meetings being taken place. When a minister who had a different post in the Haryana cabinet entered the village meeting of the village Bharouda (Rohtak), he was chased away together with his staff. In consequence, the state ministers ordered to ban the village meetings and stopped visiting the villages [of the state Haryana]. As a result Indira Gandhi central government revoked Bhajanlal from his position and chief minister and made him a minister in the central government and installed Bansilal as chief of state.
Radhu Yadav’s Unemployed Army
In 1985 Radhu Yadav organised the Unemployed Army [Berojgar Sena]. This organisation called for a huge rally during the same year, calling people in the area reaching from Rewari to Dharuhera. When they heard this all the industrialists and their middle-men became alarmed. They started preaching that Radhu would loot and burn the entire region. It was the plan to stop the demonstration at the Sahbi river. The leading figures behind this conspiracy were members of a Dharuhera based ziledar [superintendent] family. Not by chance these people were agents of the Pashupati Mill. As little by chance as the fact that it was well known that the exploitation was worst in the Pashupati Mill – this company paid the most meagre wages in Haryana. The owner Jain was in cahoots with the local council leaders. The Unemployed Army arrived at the planned day in Dharuhera and held an enormous mass meeting – in this way the demonstration was successful and the local conspiracy did not manage to obstruct. On that day the nephew of Lilu Kutbi – who was part of the industrialists middlemen – received a beating. He had tried to obstruct the rally in Dharuhera.
Hero Honda Group establishes industrial units
In 1985 Hero Honda opened its motorcycle plant in Dharuhera. The partts supplying auxiliaries also opened factories, such as Omax Auto, Rico Auto or KJ Auto. For one or two years exploitation was going on in these plants. No workers raised his voice. In October 1986 the workers at Omax Auto started a mobilisation. For their interested they set up a union, the “Omax Auto Workers Union”, whose presidents were comrade Surat Singh and Sachiv Raj Singh. The workers presented their demands to management and in order to enforce them they went on strike. After a few days of strike and after the SDM in Revari had given his signature the strike was ended. This was an organised movement and in this way workers’ unions started here. After a few days the Omax Auto workers again struck over a certain issue. The entire workforce set up a tent in front of the company gate and stopped production. This continued for some days when during night the police arrived, they loaded the workers into buses and threw them into Mehandrgarh jail, I can remember very well when we went to SDM court in Rewari in order to bail them out the police started beating the hand-cuffed workers. Some of them got injured. I opposed this together with some lawyers. All this reminded me of the atrocities and abuse of the English which they inflicted upon Lala Lajpat Rai. This type of abuse was contemptible in a free India. But the workers here are still not fully organised, this is why they can still be abused. After a few days of back-and-forth the good son of Choudhray Bansilal intervened, he made the company take the Omax workers back on duty and a union under the name of “Dharihera Kamgar Union” was registered. The leadership was with CITU. By this time the workers in Dharuhera were awakened. The workers at KJ Auto also set up a union. (To be continued)
Comments
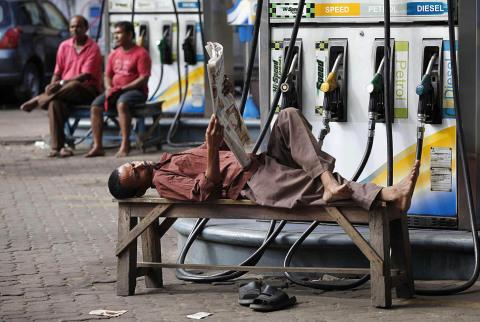
GurgaonWorkersNews – Newsletter 46 (January 2012)
Gurgaon in the industrial belt of Delhi is presented as the shining India, a symbol of capitalist success promising a better life for everyone behind the gateway of development. At a first glance the office towers and shopping malls reflect this chimera and even the facades of the garment factories look like three star hotels. Behind the facade, behind the factory walls and in the side streets of the industrial areas thousands of workers keep the rat-race going, producing cars and scooters for the middle-classes which end up in the traffic jam on the new highway between Delhi and Gurgaon. Thousands of young proletarianised middle class people lose time, energy and academic aspirations on night-shifts in call centres, selling loan schemes to working-class people in the US or pre-paid electricity schemes to the poor in the UK. Next door, thousands of rural-migrant workers up-rooted by the rural crisis stitch and sew for export, competing with their angry brothers and sisters in Bangladesh, China or Vietnam. And the rat-race will not stop; on the outskirts of Gurgaon, new industrial zones turn soil into over-capacities. The following newsletter documents some of the developments in and around this miserable boom region. If you want to know more about working and struggling in Gurgaon, if you want more info about or even contribute to this project, please do so via:
http://www.gurgaonworkersnews.wordpress.com
gurgaon_workers_news@yahoo.co.uk
———-
The Different Faces of Crisis – January 2012 Issue
*** I / We in Crisis – A Workers’ Life and Day
On its front-page, Faridabad Majdoor Samachar frequently publishes workers’ stories, relating both to their daily experiences and their life. This is less about ‘story-telling’ and ‘personal accounts’ as such, but about a collective process of discovering not only how the current system shapes our ‘private’ life according to its inner structure, but also how in seemingly ‘individual’ workers’ experiences lies a creative, productive and antagonistic wealth of the working class – the experiences of having worked in rural and urban areas, in various industries, in households and factories; of having gone through the systemic repressive institutions of family and school; of having found ways to survive and undermine the structural pressures. We translated the story of a 37 years old worker.
*** We are the Crisis – Struggles of Teacher Trainees
In most of the recent larger working class mobilisations teachers played a prominent role – from protests against austerity in Spain to the revolt against the regime in Egypt. There are various reasons for this prominent role. There is the obvious trend of proletarianisation of the profession ‘teacher’. The casualisation of ‘semi-skilled’ teaching staff (assistant teachers), the standardisation of work (teaching modules), the austerity measures in the public sector, have eroded the status and conditions of teachers. In many cases teachers become low paid social security guards who are supposed not only to take care of pre-unemployed youth, but also provide them with an illusion of a future. We document the recent struggle of BTC trainees (Basic Training Certificate: basic teaching in primary schools) in Dehradun. The BTC teachers are low paid teachers to teach mainly in poorer areas. They struggled against having to work unpaid for months on so-called ‘practical training’.
*** The Global Crisis Re-Surfaces in India
In autumn 2008 the capitalist strategists still talked about the potential for a ‘decoupling’ of the ’emerging markets’ (China, India, Brazil etc.) from the global crisis. It was clear from the start that the ‘decoupling’ was a myth, a wishful thinking. We summarised some basic figures showing the link: on the impact of the slump 2008, on the national and global bail-out in 2009, on the currency war and state of inflation in 2010, and finally on the Indo-Euro crisis in the second half of 2011.
*** Suggested Reading: Contributions to the Global Overthrow
The global and historical character of the current crisis forces us to coordinate both debate and practice ‘for workers self-emancipation’ on an international scale.
An illustrated book by prole.info, which takes one seemingly simple thing – a house – and examines the social relations around it. From the construction site to the city, from gender roles to trade unions.
The Housing Monster
Blog for the exchange of experiences concerning organising at the workplace.
Re-Composition
*** Delhi Calling: Get Involved in Faridabad Majdoor Talmel
To abolish the global work/war house will take more than informative exercise! If you live in Delhi area, please be welcomed to take part in Faridabad Majdoor Talmel – a workers’ coordination. We distribute around 9,000 copies of Faridabad Majdoor Samachar on ten days each month in various industrial areas around Delhi. You can also participate in the workers’ meeting places which have been opened in various workers’ areas. If you are interested, please get in touch. For more background on Faridabad Majdoor Talmel:
Faridabad Majdoor Talmel
Comments
In autumn 2008 the capitalist strategists still talked about the potential for a ‘decoupling’ of the ’emerging markets’ (China, India, Brazil etc.) from the global crisis. It was clear from the start that the ‘decoupling’ was a myth, a wishful thinking.
The Impact of the Slump 2008
The impact was immediate. The main stock-market index (Sensex) fell by more than 50 percent during the year 2008, from 20,800 in January 2008 to under 10,000 in mid-October. The mass-sales of shares and securities held by foreign investors and the subsequent massive US Dollars outflow resulted in the largest fall of the foreign exchange reserves in eight years. While in July 2008 the reserves stood still at 300 billion US Dollars, by November 2008 they had plunged down to 258 billion. The withdrawal of capital from the Rupee caused a massive devaluation of the currency. Early 2008 the Rupee stood at 39.25 US Dollars, by end of November 2008 it had depreciated to 50.5 US Dollars. In October 2008 for the first time in more than a decade the manufacturing output of the Indian industry declined.
The National and Global Bail-Out 2009
In 2009, the state in India induced money into the markets, which postponed the impact of the crisis and shifted its focus to the question of state debts. “We had to inject Rs 80,000 crores as stimulus package to overcome the crisis, which helped arrest further deterioration of the Indian economy,” finance minister Mukherjee said in April 2010. These policies, like in the rest of the world, increased state debts. India’s public debt was at 78 per cent of GDP in 2008/09 and increased to 82 per cent in 2010. Despite the global stimulus packages, foreign direct investment inflows into India dipped 5.16 per cent to USD 25.89 billion in 2009-10. India’s exports declined 4.7 per cent to USD 176.5 billion in 2009-10. Export forms a fair chunk of the GDP (1988: 6 per cent / 2008: around 20 per cent). The fiscal deficit increased by 25 per cent in 2009 to 2010.
The Currency War and Inflation in 2010
The low interest rate policies in the Global North – meaning: the attempt by the states to provide cheap money as investment incentive to corporations – sent off a wave of ‘hot money’ to the emerging markets, where investors hoped to be able to find a profitable short-term investment. This caused inflation rates to rise dramatically. Indian inflation hit double digits in May 2010, the highest in any G20 nation. The Indian reserve bank had to raise interest rates again and again in order to curb inflation, which forced a lot of companies to lend money on the international markets, increasing the (corporate) foreign debts – between March 2009 and March 2010 external debts increased by 16.5 per cent to 261.5 billion USD. The ‘fluctuating’ character of investments revealed itself when the state debt crisis in Greece sent shocks through the global markets in May 2010 – 20 billion USD short-term invested capital was extracted from ‘Indian’ markets within a couple of months.
The Indo-Euro Crisis in 2011
The Euro-crisis – the running out of the stimulating impact of state credits induced in 2009 and the hitting home of state debts – reached India in the last quarter of 2011 and fortified the general trend towards a further downturn. Between August and December 2011 the Indian Sensex (main stock market) lost 18 per cent. In November 2011 alone, 600 million USD ‘foreign short-term investment’ was withdrawn from the Indian securities market. The ‘hot money’ of 2010 cooled down – in summer 2011, when the Euro crisis threatened to trigger a second global slump worse than the one in late 2008, the ‘hot money’ streamed back from the ‘insecure’ emerging markets to the USD markets. This caused massive depreciations of local currencies. Between July and December 2011, the price of the Indian Rupee fell by more than 16 percent, to a rate Rs 53.80 to the USD – a record low.
The persistent fall of the rupee has also added to the burden on the trade deficit, which in October 2011 widened to a 17-year high of $19.6bn. The total trade deficit for 2011/12 is expected to widen sharply to between $155 billion and $160 billion from $104.4 billion a year ago. As a consequence of the weak Rupee the petrol prices are supposed to rise by 1 Rs per litre from January 2012 – around 80 per cent of the petrol in India has to be imported. In 2010 the government changed the legal framework for oil price regulations, an act to make ‘the people’ pay for the state’s ‘corporate stimulation’ – since then petrol prices have been hiked several times. Higher petrol prices will keep inflation up. India’s headline inflation has been above 9 per cent during 2011 despite 13 rate increases since March 2010 that have lifted the repo rate to a three-year high of 8.5 per cent from 4.75 per cent. The high interest rates choke investments.
The government lowered the GDP growth forecast for 2011 to below 7 per cent, compared to 8.5 per cent in 2010. In October 2011 industrial output fell for the first time in more than two years. Capital goods production, considered a barometer of investment sentiment in the country, fell 25.5 per cent. In 2011 car sales in India posted the steepest fall in nearly 11 years.
Consequently the state has trouble meeting its crisis budget. Net tax revenues have grown just 7.3 per cent in the first seven months of 2011-12, while state expenditure has jumped by about 10 per cent during the same period. Some economists are now projecting that the fiscal deficit by the end of the financial year could be as high as 5.7 per cent of GDP. The state had calculated to re-finance its debts by selling state assets, but the economic slump foiled the plan: only one public sector undertaking (PSU) hit the capital market in 2011 raising only Rs 1,145 crore, the plan had aimed at several ‘privatisations’ which were supposed to raise Rs 40,000 crore.
Is a re-make of the 1991 foreign debt default possible? The Indian (state) banks have 314 billion USD of foreign currency reserves. Outstanding foreign debts, which will have to be repaid within a year, stand at about half of this amount. The recent deal with Japan of a 15 billion USD currency swap can be seen as a sign that liquidity problems are severe. With the value of the Rupee declining, it will become costlier to repay the debts.
The figures above confirm that there is no ‘decoupling’, but rather a very immediate relation between the ‘continental markets’. Austerity measures or monetary policies in the north almost immediately impact the situation in the ’emerging markets’. It also shows that despite a seemingly huge ‘internal market’ – 800 million people living in India’s semi-rural areas – this ‘internal market’ has little weight once it comes to the question of capitalist boom or demise. The regime in India will have to follow its counterparts in the north and push through with ‘unpopular’ decisions.
The back-and-forth concerning the question whether foreign direct investment should be allowed in retail sector (allowing Walmart, Tesco, Carrefour etc. to open supermarkets directly) can be seen as a symbol of the dilemma the regime is facing: economically the regime is in dire need for further capital inflows, socially it does not want a head-on confrontation with a social strata (medium and small traders) which quantitatively and qualitatively might prove to be the last stable ‘popular’ barrier between the regime and the rural and urban proletarian poor.
The ‘political expression’ of this strata, in the form of the anti-corruption movement Hazare’s, although ‘annoying’, manages to channel wider ‘popular discontent’ and re-focus it on the political-parliamentary arena. They thereby provide an invaluable service of social counter-insurgency for the ruling class, which weights as heavy as the pressure from the ‘economic’ figures above. Economic and social figures, which, let’s be honest, resemble scarily the figurations of recently toppled regimes in northern Africa (food price developments, foreign debts, graduate unemployment, historical parallels of IMF enforced adjustments etc.). The decision to post-pone the opening of the retail market has to be seen as a state of economic-political paralysis of the regime, facing the social abyss. Let’s help the regime with a little push.
Comments
In most of the recent larger working class mobilisations teachers played a prominent role – from protests against austerity in Spain to the revolt against the regime in Egypt. There are various reasons for this prominent role. There is the obvious trend of proletarianisation of the profession ‘teacher’. The casualisation of ‘semi-skilled’ teaching staff (assistant teachers), the standardisation of work (teaching modules), the austerity measures in the public sector, have eroded the status and conditions of teachers. In many cases teachers become low paid social security guards who are supposed not only to take care of pre-unemployed youth, but also provide them with an illusion of a future. In this sense the demand for teachers increased. The fact that teachers are often at the forefront of current public protests has two main reasons, both reflecting the arbitrary position of teaching work. Firstly, the cohesion amongst teachers is less constituted through the work process, therefore the greater need for a ‘formal’ organisation, which tends to be more visible. Secondly, in many cases teachers still appeal to their social status as ‘providers of education’, which gives them the credibility to protest, not only in their own interest, but a wider interest. As we can see, both reasons have an arbitrary element regarding to the possible generalisation of teachers’ struggles as ‘struggles of workers’. These arbitrary tendencies will surface first of all in conflicts within the ‘education sector’, once the divisions between various grades of ‘teaching staff’ (assistant, casuals, trainees etc.) impose themselves as essential problems for a ‘common’ struggle. We document the recent struggle of BTC trainees (Basic Training Certificate: basic teaching in primary schools) in Dehradun. The BTC teachers are low paid teachers to teach mainly in poorer areas. They struggled against having to work unpaid for months on so-called ‘practical training’.
Struggles of BTC Trainees in Dehradun
(www.nagrik.com)
On 22nd of November 2011, demanding direct recruitment in the state government service during their third semester of the Basic Training Certificate (BTC), hundreds of teachers undergoing training in different districts of the state, protested in front of the civil secretariat in Dehradun. The protesters burnt their clothes to register their protest against the alleged step-motherly attitude of the administration. When they tried to get to the administration building, they were attacked by the police. Twelve trainees, including one female trainee, were injured and 200 were arrested. After two days they were released without charges. The ‘crime’ they had committed was to resist being sent to work (under the name of ‘practical training’) to remote areas of the state without permanent contract and without wage.
These trainees had not passed yet the exam of the third semester – so for the government they were officially unskilled. The government cajoled them by saying that if they would accept to work in formerly closed schools in remote areas they might get a permanent contract even if their training had not been completed. They were reassured that they would be called back for exams after three months. BTC trainees said that the last batch of trainees had not been called back from ‘practical training’ for one and a half years! In addition, the government did not want to pay them a single Paisa for these one and a half years of work. The BTC trainees started their movement in order to get an answer to their question about their future – after having paid from their own pockets to go to remote areas and still not knowing how things will turn out. The government wants to profit from these trainees by re-opening schools in remote areas during the time of elections – but they don’t want to give them a permanent status.
After the attack on 22nd of November the order to start ‘practical training’ was revoked and postponed to the 15th of December. On 28th of November a meeting was supposed to take place. The trainees who were released from jail confirmed their resolution to demand an answer and called for a protest sit-in at the education directorate in Nanurkheda. The issue is that in the 13 districts of the state around 1267 trainees of education and training institutes are kept in a cloud of uncertainty. According to a government order they can be sent to ‘practical training’ in other districts even before completing their training. Their fellow trainees of other institutes are paid 6,000 Rs honorarium for the last six months of similar ‘practical training’, those BTC trainees on correspondence courses got 7,500 Rs – the BTC trainees find themselves in the dilemma that the competition for permanent jobs increases – should they demand from the government to tell them for which position they will be hired and for which wage?
The true stance of the state government revealed itself when an office bearer of the BTC trainee union came to Dehradun to meet the Minister for Education – and the Minister refused to meet the representative. Instead the education secretary told the trainee union officer that they have to follow the government orders. In the first week of November the BTC trainees returned to Dehradun in form of a movement – to wake the government who had refused any talks. Trainees from 13 different BTC institutes assembled on the Parade Maidan in Dehradun. A workers’ representative said that on 21st of November the ministry called and promised that if the trainees would stop their protest assembly they could meet the central minister. So they went back to Nanurkheda and encircled the education secretariat instead. The central minister phoned the next day and said that the exams for the third semester will take place soon, but he did not agree to the main demand. The education secretary repeated this – the dissatisfied trainees intensified the protest in front of the secretariat. On the same day in the evening the patience of the trainees found an end, they started to tear down the police barricades around the secretariat. The police answered with a baton charge and arrested 199 trainees, 80 of them women. After verbal support of all opposition parties the trainees were released after two days. The released trainees reassembled on Parade Maidan and said that they keep up the protest till 28th of November, the date of the promised meeting with government representatives. They say that if the meeting won’t take place they will encircle the residence of the central minister. The education ministry sent out a letter to all district education officers saying that BTC trainees are not supposed to be sent to remote districts, but to schools were there are either too many pupils or to few teachers.
The state minister for education informed that there are 2,720 vacant posts in primary schools – at the same time the minister tells the trainees that they will hire the 3367 BTC trainees once they have finished their exams plus 2,200 trainees on special BTC courses, a total of 5,000 posts – these are empty promises. Out of 882 trainees on special BTC courses around 60 per cent work as teaching staff in RSS (Hindu Nationalists) run Shishu Mandirs – the government is under pressure to give jobs to these trainees once they have finished their courses. The opposition parties officially support the agitation, trying to convert the teachers to foot-soldiers of their respective parties.
On 18th of December 2011 members of Uttarakhand BTC Trainee Shiksha Mitra Federation staged another protest at Parade Ground and later took out a rally to the residence of the Education Minster in Dehradun. The demands include appointment of BTC Trainees to the posts of assistant teacher after their completion of BTC training and allowance of `10,000 Rs to Shiksha Mitra during training.
Comments
On its front-page, Faridabad Majdoor Samachar frequently publishes workers’ stories, relating both to their daily experiences and their life. This is less about ‘story-telling’ and ‘personal accounts’ as such, but about a collective process of discovering not only how the current system shapes our ‘private’ life according to its inner structure, but also how in seemingly ‘individual’ workers’ experiences lies a creative and productive wealth of the working class – the experiences of having worked in rural and urban areas, in various industries, in households and factories; of having gone through the systemic repressive institutions of family and school; of having found ways to survive and undermine the structural pressures.
We have translated and published workers’ his/her-stories in following earlier newsletters:
no.17
no.24
no.31
no.34
no.42
A 37 years old worker – FMS no.276 – June 2011
I get up at 5 o’clock in the morning. There is no toilet, one has to go to the open space next to the rail-tracks. You have to be careful, I have seen two people being killed by trains – one of them was a relative of mine. After having washed, I prepare food together with my mate. In the morning we make vegetables and roti. The water comes from a private borewell, this is why we have to pay 150 Rs for water per month. We have finished preparing the food by 7:30 am. Washing, eating and then at 8:15 you have to leave for the factory.
Some things come up in the mind again and again. When Indira Gandhi died there was holiday at school. I was eight, nine years old then. I saw how, at the station, three wagons of a train were set on fire. After having dragged Sikhs out of the wagons, one after the other, the police beat them up. The crowd kept standing at a distance. They brought one Sikh and tied him up in a sack. When the policemen asked for petrol from people in the nearby shanties, I kept on standing to see what they would do. The policemen sprinkled the sack with petrol and set fire to it. I ran away in fear. There was a curfew for three days. When I think about it now, it seems strange to me – how was this possible?
The shift starts at 8:30am . At the moment I work in the New Industrial Area in Faridabad, in a company called Sisaudia Engineering. I work here in the Honda department, I operate an industrial drill, even though I have ITI (Industrial Training Institute) training in refridgeration and air-conditioning. Currently the minimum wage for unskilled workers is 4,503 Rs per month, but in this factory I earn 3,500 Rs.
I finished my ITI training in 2000. Our village is in East Uttar Pradesh and the ITI is about 20 kilometres away from our place – I cycled back and forth every day. I received 700 Rs student allowance per year. I also worked on the fields. My father was employed as a permanent worker at Gedore-Jhalani Tools factory in Faridabad, but for several years they had hardly been paid any wages. I arrived in Delhi to do my apprenticeship. The widowed mother-in-law had a house in Trilokpuri, but there were expenses for three young brother-in-laws and two sister-in-laws. Instead of doing an apprenticeship I started working as a security guard in Nanj Supermarket in Greater Kailash (South Delhi). I was working for Gajraj Securities, but hired through a contractor from NOIDA, who paid 3,800 Rs. I worked there for three and a half months, then the job was finished – a manager had embezzled three to four crore Rs. After looking for work for ten days I found a job at Kapeel Export factory in NOIDA Sector 11, they paid 1,200 Rs. I learned how to print and embroider clothes with machines. After having worked for some time the piece-rate wages went up to 4 to 6,000 Rs. I worked there for two years. Then my father fell ill and I returned to the village.
When we arrive at the factory we have to carry the raw material, which is stored outside the factory, to the machines. In 8 hours you have to drill 1800 pieces. I don’t have a particular fear of accidents. While working, you think about all kind of things.
After I had finished my eighth class in Faridabad I went back to the village. My grandfather had become old. I started to plough the fields with the bullocks and did other work. I finished the tenth class in a school three miles away. I enrolled in the Intercollege in Pratapgarh and lived in the student hostel there. They paid 50 Rs per month student allowance. I went back to the village only at weekends – I worked on the fields there, and when there was too much work, I took days off at the college. My mother went to Faridabad in order to have an eye surgery, around this time I failed my eleventh class. Because of mental pressure I also failed once in the twelfth class – my wife died after a miscarriage. We had lived together for many days, we were married when I was in the ninth class. I finished the twelfth class in a private college. When my neighbour – who taught in a neighbouring village – opened a school in our village, I joined him. When we had enrolled 250 children, each of us four teachers would earn around 500 Rs. I stopped teaching when I had to both study for ITI and do the work on the fields.
At 12:30 there is a lunch break. There are 400 workers in the factory, but there is no canteen. There is no place to sit and eat. I go to our shanty and eat there. And at 1 o’clock you have to be back at the drill.
In 1993, after having finished my tenth class I was trying hard to find a job. I filled in many application forms. I went to Bophal, Buvaneshvar, Jodhpur in order to apply for jobs as a gangman for the railways. Then on the bases of the ITI I went to Mumbai, Ilahabad, Lakhnow, Kolkata in order to get a job as an assistant driver. In 1998, I went to an interview for a job at the Uttar Pradesh Irrigation department. A lot of job seeking people came at the same day. Seeing this, the administrators said that the interviews were cancelled and that we would receive further information by letter. People started throwing stones. The place was closed down, people left. This letter never arrived. After having finished the ITI I put my name down on the list of the employment office in Pratapgarh. They never sent anything. I renewed the enrolment in 2003 and 2006. Again nothing. In 2006, they told me not to put my name down again in future. I got furious. In the meantime I had seen governments changing from Congress, BJP, SP, BSP…
At 2:30 the contractor provides tea. The wages are low, but there is no particular atmosphere of complaining here. I know some of the people who work here from before, acquaintances, friends…
In 2009 the village council leader himself issued a job card under the MNREGA (Rural Employment Scheme). In 2010 during the monsoon the village leader said: “Your money has arrived for the 25 days of work that you have done. Open an account and you can get the money.” I did not even work under this scheme… figure that out. I then met a lot of other people who had not worked, but in whose name money was drawn for MNREGA. The village leader called the bank manager to his home and asked him to open accounts. When it? was to get the money from the bank the village leader said I should go to the bank and that the contractor (who was supposed to have undertaken the work under MNREGA) has already taken the pass book there. I went to the bank, I withdrew 2,500 Rs from the account, out of which 1,700 Rs was taken by the contractor… the village leader is illiterate and he once received a reward from the prime minister.
No one stops working at 5 o’clock in the afternoon. The overtime is only paid at single rate, but nevertheless, no one could make ends meet if they did not work 12 hours a day. Some workers work 200 hours overtime per month.
I married again in 1997. We had children. My father did not receive his outstanding wages from his company. Even in the village they sell packaged goods nowadays (everything becomes more expensive). The bullocks have been sold and 1.5 bigha are now ploughed by tractor. The school fees are 800 Rs per month. My wife works as a domestic nurse, but she does not get a fixed salary, nor a honorarium, she works piece-rate: for a childbirth 600 Rs, a vaccination 50 Rs, a sterilisation 150 Rs. But she also has to pay, e.g. 200 Rs for the room for a monthly meeting – it is difficult to earn enough to cover expenses. We wanted to form a Dr. Ambedkar Self-Aid Group, but there is no space, where would you keep the goats? What will you give the buffalos to eat? There is no hay. The chicken spread their dirt everywhere. I thought about starting sewing, but I didn’t know how to. I tried to learn, but was not too successful. I thought again about an apprenticeship, after the CTI I could then complete my ITI master. I arrived again in Faridabad, to do an apprenticeship in refridgeration and air-conditioning at Whirlpool company, but they said that they wouldn’t take anyone who comes from a different state. So I then started to work as a casual worker at Whirlpool. At the cabinet line there were three permanent workers, six casuals and two workers hired through contractors – their wages were 20,000 Rs, 4,200 Rs and 3,500 to 4,000 Rs respectively. Because there was too much work to be done back home on the field I left this job in August 2010 and went back to the village.
We finish working at 8 or 9 o’clock and buy vegetables on the way back to the shanty. Between my mate and myself, whoever comes home first starts to prepare dinner. We make dal, rice and roti – all in all this takes about two hours. We go to sleep around 11 o’clock or midnight. I cannot sleep… I really can’t stand the noise around, the trains which pass nearby really disturb you. You never get a good night’s sleep. The head becomes heavy.
Comments
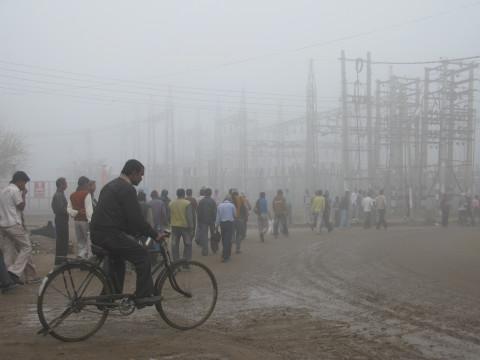
GurgaonWorkersNews – Newsletter 47 (February 2012)
Gurgaon in the industrial belt of Delhi is presented as the shining India, a symbol of capitalist success promising a better life for everyone behind the gateway of development. At a first glance the office towers and shopping malls reflect this chimera and even the facades of the garment factories look like three star hotels. Behind the facade, behind the factory walls and in the side streets of the industrial areas thousands of workers keep the rat-race going, producing cars and scooters for the middle-waged classes which end up in the traffic jam on the new highway between Delhi and Gurgaon. Thousands of young proletarianised post-graduates lose time, energy and academic aspirations on night-shifts in call centres, selling loan schemes to working-class people in the US or pre-paid electricity schemes to the poor in the UK. Next door, thousands of rural-migrant workers up-rooted by the rural crisis stitch and sew for export, competing with their angry brothers and sisters in Bangladesh, China or Vietnam. And the rat-race will not stop; on the outskirts of Gurgaon, new industrial zones turn soil into over-capacities. The following newsletter documents some of the developments in and around this miserable boom region. If you want to know more about working and struggling in Gurgaon, if you want more info about or even contribute to this project, please do so via:
http://www.gurgaonworkersnews.wordpress.com
gurgaon_workers_news@yahoo.co.uk
In the February 2012 issue you can read
Comments
1) Proletarian Experiences –
Daily life stories and reports from a workers’ perspective
*** Everything but Accidental – Report by an Omega Construction Equipment Worker and on fatal Accident at Machino Plastics Ltd. –
Accidents are a daily routine (not only) for workers in the Delhi industrial belts. Not only the factories are slaughterhouses, the way to work itself is murderous. Between January and December 2011 officially (!) 163 people were killed in road accidents on the short Gurgaon-stretch of the National Highway 8, most of them workers crossing the highway on foot…
Two Workers Killed at Machino Plastics, Manesar
21st of January 2012
At least two workers were killed and several injured when a temporary roof-structure collapsed at Machino Plastics Ltd., a supplier for Maruti India Ltd’s in IMT Manesar. “There was a huge machine setup which suddenly fell along with the pillars and roof,” investigation officer Surender Singh said. “The victims were rushed to hospital where two workers were declared dead on arrival. Situation of four workers is stated to be critical.” Those killed were identified as Bhagirath and Naresh Kumar. Bhagirath hails from Uttar Pradesh’s Faizabad and Naresh from Rajasthan.
Omega Construction Equipment Worker
(FMS 2011)
A work accident in the Faridabad plant of Omega Construction Equipment nearly killed Dinesh Kumar. Although he worked for the company since 25 years as a permanent employee and despite the fact that – unlike the majority of workers in Delhi-Faridabad-Gurgaon – he had an ESI medical insurance card, the post-accident treatment by both company and medical system turned out to be a nightmare. http://www.omega.org.in/fabrication/facilities.htm
Omega Construction Equipment manufactures special machinery and heavy fabrications (hydraulic cranes, storage tanks) for the local and global large-scale industry (petrochemical, power, cement, paper, sugar, textile, steel industries). Me, Dinesh Kumar, worked at this factory (Plot 262 M, Sector 24, Faridabad) for 25 years as a permanent employee. On 15th of September 2009 I had an accident at an hydraulic press, which cut my complete face. One jaw bone was cut, I lost all teeth and my nose was cut. I spent one month in the Escorts Fortis Hospital, then 15 days in the Metro Hospital, then 10 days at the ESI Hospital – I was unconscious for the whole time, I then opened my eyes. The mouth area was stitched up, I was fed through a plastic tube inserted into my throat. I was sent to Safdarjung Hospital in Delhi, but then turned back to the ESI Hospital. The nose needed a plastic surgery and the mouth also another operation. I was transferred back to the Escorts Hospital, there they told my family to bring medicine, which cost about 18 to 20,000 Rs, which was not paid for by the ESI… the ESI said that everything will be provided by Escorts Hospital, “so why do you buy the medication yourself?” The doctors at Escorts Hospital later on said that they don’t know about the legal ins and outs. My brother had admitted me to the Metro Hospital, so the 56,000 Rs will have to be paid by my family. From the ESI I received 148 Rs a day from 15th September 2009 to 27th of July 2010. The expenditures were considerable… On 28th of July an ESI doctor attested that I was fit to work. I went to the factory. They sent me back and forth, told me to take my final dues and quit the job. I went to the labour department, through a trade union. There the company agreed in writing that they would take me back on duty. I worked the last three days in September and seven days in October, on pay day I asked for my wages, but the factory director swore at me and threatened me. I went back to the labour department. The company lawyer said that I should take my final dues and quit. I refused. The whole issue went to Chandigarh, to the labour court, the court date is on 1st of July 2011. Again, quite a lot of expenditures… my brother, nephew and my older daughter (my wife has just died) tell me that I should not think too much, that my mind has gone slightly bad, that I therefore should not think too much. As a consequence of the accident I am forced to a certain diet, I have to suck water through my nose regularly, my mouth and head hurts… I will have to go to the ESI medical board in order to get a compensation.
*** The Guns of Manesar and the Return of Patriarchal Corporatism: Wage Revision at Maruti Suzuki and Reports from Mars Associates and Motherson Sumi Workers –
We included a short note on the upcoming pay revision in the Maruti Suzuki plant in Manesar, which has turned into a stage-show for management propaganda. According to the head of Maruti Suzuki’s human resource department, the pay revision “will help stabilize the situation not only at Maruti, but the entire industrial belt in Haryana”. He continues wisely: “Twenty years back, the profile of workers was different. Now, almost 70 per cent of our workforce is in the age group of 24-26 years. These young guns always look for improvements.” Following the note on the wage revision are two reports of ‘young guns’ employed in Maruti’s supply-chain, at Mars Associates Ltd. and Motherson Sumi Systems.
Maruti likely to revise pay structure
7th of January 2012 – Times of India
“The move will help stabilize the situation not only at Maruti, but the entire industrial belt in Haryana, which is home to several auto companies. Their pay revision is due. We have set up a committee, which would evaluate their demands and negotiate those with the company management,” said S.Y. Siddiqui, managing executive officer (human resources and administration). “The wage settlement process will begin in March and it is expected to be completed by April-May.” The company has agreed to the demand of the Manesar workers for a union, separate from those of their colleagues at the company’s Gurgaon plant. Both Gurgaon and Manesar are located in Haryana. “It’s their right to form a union and nobody can stop them from doing that,” Siddiqui said. “We are really happy for them.” Siddiqui said the company has a lot of young workers at both plants and it has understood that it needs to respect their demands. “Twenty years back, the profile of workers was different. Now, almost 70 per cent of our workforce is in the age group of 24-26 years. These young guns always look for improvements.” Siddiqui admitted that “overwork” last year triggered workers to go on strike. “There was a huge demand in the market last year, especially for models like the DZire and the Swift,” he said. “There were occasions when there was a need for extra work. There was a huge pressure on production. Better communication with the workers should have avoided these strikes.” The company will hire 365 workers in this fiscal and at least 750 in the next one, Siddiqui said. A decision on whether to delay the Gujarat plant opening will be taken at the board meeting on 23 January, he added. Maruti Suzuki India Ltd reported a 63.6 per cent drop in net profit for the quarter ended 31 December 2011 from a year earlier. Maruti will seek to increase the proportion of locally made parts to minimize the impact of currency changes. Imports currently constitute 12 per cent of net revenue and vendors import the equivalent of another 10 per cent of net revenue.
Motherson Sumi Systems Worker
(Plot 21, Sector 18, Gurgaon)
The shift officially starts at 6 am, but the company buses arrive as early as 5:30 am. Even the workers who live in Gurgaon have to get up at 4 to 4:30 am to arrive ‘on time’, the workers living in Delhi get up at 3 or 3:30 am. The various assembly lines for electrical (car) harnesses are given names of different flowers in order to distinguish them, but the workload is heavy and less flowery. In the Gurgaon factory most of the work is done for Maruti Suzuki. Because of the unrest the production at the Maruti Suzuki factory in Manesar has been low during the summer months – the ready harnesses piled up in our plant, in the packaging area, in the canteen, next to our machines.
MARS ASSOCIATES PVT. LTD. Worker
(Plot 23, Sector III, IMT Manesar)
The company employs 20 permanent workers and 80 workers hired through contractors. We work on two 12-hours shifts, manufacturing parts for Honda, Hero Honda, Maruti Suzuki. There are no days off, we work on Sundays, even on festival days. The overtime is paid at single rate. Out of the eight pressure die-casting machines four remain defunct since three months. The machines run, though they are faulty – but it is the worker who operates the faulty machine who is sworn at, sometimes beaten. Accidents are frequent, this year two workers have cut their hands. The company does not fill in accident forms, workers are sent to private hospitals, money for treatment is cut from their wages and in the end they are sacked from the job. 650 Rs are cut from wages for ESI and PF, but the workers hired through contractors receive neither card nor PF form. Mars operates another factory in D-166, Okhla Industrial Area, Phase-I, Delhi.
Comments
*** Two Decades of Unrest at Clutch Auto in Faridabad
Clutch Auto belongs to the first industrial companies in Faridabad. The first factory was opened in 1971, in the mid-1980s the company shifted to a new plant at Mathura Road, now Clutch Auto is about to open a factory in Rewari, near Manesar, which might result in down-sizing or closure of the Faridabad plant. The company is India’s largest clutch manufacturer, around 2 million per year, for the automobile industry, for agricultural machines and army tanks. In June 2011 about 350 permanent workers at Clutch Auto went on a 11-days strike. At the time the dispute at Maruti Suzuki in Manesar, about 50 km from Faridabad, was in full swing. The strike officially concerned wages and a ‘wage agreement’, but the relocation of the factory is looming in the background. We document a workers’ report published in Faridabad Majdoor Samachar. We also translated an older article relating the story of a strike at Clutch Auto two decades earlier in 1992, after 250 casual workers were sacked from the plant.
http://www.clutchauto.com/
Faridabad Majdoor Samachar – July 2011
Clutch Auto Worker
(12/4 Mathura Road, Faridabad)
Every month 100 Rs is cut from the 350 permanent workers wages and paid annually in form of LTC [Leave Travel Concessions] – the bosses say that this is inscribed in the agreement with the trade union. By June 2011, this money accumulated from 2010 had not been paid to the workers yet. The company had also put up a notice in the past, which said that workers are not supposed to take their paid holiday, that they will be compensated. Since 2006 there has been not paid holiday and people who ask for holiday are not granted any. Now, in May 2011 the company put up a notice saying that for any holiday taken the company will cut two day’s wages. In addition, management cut 1,800 Rs from the April wages of workers, saying that according to the wage agreement with the trade union they can cut wages if production targets are not met. On 12th of May 2011 the permanent workers refused to take the reduced wages… on 20th of May the company paid the wages without any reductions. The company opens a new factory in Rewari (around 40 km from Faridabad), they take machinery from the Faridabad plant, they hire new people for training… it looks like they want to get rid off the 350 permanent workers here. On 3rd of June the permanent workers engaged in a tool-down strike, they came to work, but did not start working. On 12th of June negotiations between management and union took place at the office of the Ministry of Labour. The permanent workers and their families ‘encircled’ (protest form) the house of the labour minister, the Clutch Auto workers live in his election constituency. The workers will get wages paid for the ten days of strike, five days are paid by the company and for the other five days workers will work from 20th to 30th of June for 12 hours instead of 8 hours per day. Apart from that a lot of reassurances are given. Production started again on 13th of June.
Faridabad Majdoor Samachar – May 1992
On 4th of April 1992, 250 casual workers were kicked out from this factory, situated at 12/4 Mathura Road. They were employed in the factory for eight to ten years continuously, and during this time the workers had been squeezed to the max. They had to jump from one machine to the other, relentlessly. They were not paid the minimum wage. They did not receive ESI. They worked 30 days a month and if they left work to go and drink water, smoke a bidi or go to the toilet, they were marked as ‘absent’ for half of the day and their wages were cut accordingly. Now, at Clutch Auto like at Universal Engineering or other factories, the conditions of the casual workers come to the fore. In July 1991, management and trade union negotiate a new three years wage agreement. The agreement concerned only the 500 permanent workers, the 250 casuals were not even mentioned. According to the current agreement the workers would have received a 150 Rs wage increase combined with an increase in work load – but management was not able to increase production to the extend they had wanted to. This is why they refused to increase the wages by 150 Rs. Under these conditions it was only natural that dissatisfaction amongst the permanent workers towards the trade union leaders grew. It seems that the union leaders, who are affiliated to the HMS, pushed forward the demand to give all casual workers a permanent status. The fact that management kicked out all casual workers on 4th of April is a link in this chain of events. The fact that management suspended 12 ‘prominent’ permanent workers on 27th of April and the subsequent back-and-forth is another link. In the factory production runs as normal. The casual workers, who had been sacked all of a sudden, are angry and they started to organise themselves. Against their protest management obtained a court rule saying that they have to stay in 50 feet distance from the factory gate. On 26th of April thugs paid by the management started to threaten these workers and ‘prominent’ casual workers were followed back to their homes, where the thugs also threatened their families. One problem is that the casual workers – following the advice of some people who want to turn themselves into prophets – started to put their hope in procedures at the labour department and other paper-tigers. A whole month has already been spoiled while waiting for the date of a hearing. Here we have to remember that in 1983 – 1984, during the period when Clutch Auto shifted the factory from sector 6 to Mathura Road, management sacked hundreds of permanent workers with the help of the CITU. At Mathura road INTUC staged the show the drama, and now it is HMS’s turn to continue the drama.
The back-and-forth heated up and on 11th of May 1992 workers at Clutch Auto went on strike. Workers stare at faces of the union leaders and wait what they have to say – the harmful consequence of which becomes visible. With having forced 100 of the casual workers to resign by end of May, management has sealed the fate of the demand to make all casuals permanent. And at Clutch Auto workers still sit in front of the gate, playing cards, putting their hope in leaders who run back-and-forth between labour department and other officers.
*** Green/Nano-Technology, the Long Shadow of the 20th/US-century and the Local Regime: A workers’ Report from Usha Amorphous Metals Ltd. –
Worker’s report on a dispute at Usha Amorphous Metals Ltd., in Gurgaon, in summer 2011. Workers had recently formed a trade union, which raised the demand for higher wages and permanent contracts for the casual workers. In response Usha management sacked all casual workers – followed by police repression and entanglement in the net of the labour law. The company Usha Amorphous Metals Ltd. is an interesting example for the close connection between so-called ‘green’ and ‘nano-technology’ and the large scale industries (automobile, aerospace, military-complex). The company history also shows the formation process of ‘global corporations’. Behind the formal display of joint-ventures (in Usha’s case with Honeywell, US; Siemens, Germany; Hitachi, Japan) and ‘capital and technology transfer’ we can see how these corporations grew as part of the state regimes and their ‘opening of markets’.
http://uaml.in/contact-us/
Usha Amorphous Metals Ltd. (UAML) manufactures ‘nano crystalline cores’ (amorphous alloy) for electrical switches used in solar inverters, wind generators, in automobiles, rail traction, aerospace and military technology. Usha Amorphous Metal Ltd. came out of a joint-venture with the US multi-national Honeywell. A Usha subsidiary linked up with the German equivalent Siemens. Both Honeywell and Siemens manufacture for the energy and military complex and the development of the corporation is very closely linked to the ‘expansive’ policies of their respective state regimes. Or as Honeywell management puts it: “Honeywell is a Fortune 100 company that invents and manufactures technologies to address tough challenges linked to global macrotrends such as safety, security, and energy”. Honeywell employs around 122,000 workers worldwide, including 19,000 ‘engineers and scientists’. Honeywell is a company of the 20th ‘US-century’, based in the oil and gas sector, expanding into automobile and military sector. “By 1941, the company was present in Chile, Panama, Trinidad, New Zealand, Argentina, and South Africa. By 1998, the company had operations in 95 countries through 83 wholly-owned subsidiaries and 13 joint ventures.”
http://www.missionready.com/
http://honeywell.com/About/Pages/our-history.aspx
Honeywell started to sell amorphous metal products on the Indian market in the 1980s. At the time the state in India curbed the possibility for ‘foreign’ companies to set-up ‘their own’ subsidiaries in India, instead they were ‘forced’ to engage in joint-ventures with ‘local’ companies. The distribution of shares amongst the factions of capital and the question of technology-transfer was given a formal frame-work. In 1987, Honeywell agreed with Usha India to create an Indian-based joint venture, UAML, to make and sell amorphous metal products. Usha India agreed to contribute real estate in exchange for more UAML shares – the family behind Usha India owns large pieces of land in Delhi area and in other regions. Honeywell agreed to contribute technology in exchange. This agreement was memorialized in a “Technology Transfer Agreement”, executed in February 1994. In 1995 the laws for foreign direct investment changed, also as part of the post-1990/91 crisis management and ‘structural re-adjustment – and allowed to set up 100 per cent ‘foreign-owned’ companies in manufacturing. Honeywell set up their ‘own’ unit and the joint-venture with Usha India finally broke up in 2008 – not without a long legal case about ‘monopolising knowledge’ and ‘active sabotage’ of the joint-venture. As we can read in the following, for workers it does not matter too much who their bosses are…
Usha Amorphous Metal Worker
(Plot 487 – 487, Udyog Vihar Phase III, Gurgaon)
In the factory 32 permanent workers and 100 casual workers manufacture parts for electrical transformers. The work load is high, there is hardly time to go on the toilet or drink water. People work 125 to 190 hours overtime per month, which is illegal, payment is 31 Rs per hour overtime, which is also illegal. Each month around three to four day wages get embezzled. After 10 – 20 years of employment the wages of the permanent workers are still only 6,000 to 7,000 Rs. In order to find some relieve workers joined a trade union. In March 2011 workers gave a demand notice to management, demanding a wage increase and permanent contracts for the casuals. In response to this management sacked all casual workers on 28th of April. The workers handed in a complaint at the labour office and started a protest camp in front of the factory. On 11th of May the police arrived, they started to threaten workers, “what are you doing here, go to the labour court”, and chased them away. An appointment was given at the labour department on 18th of May: the management claimed that the casual workers were not casuals, but workers hired through contractor and that currently there is no work at the factory. They said this while hiring new people on a daily level. The April wages were paid to the sacked 100 casual workers on the 18th of May, but the overtime money for March and April has not been paid.
*** Caparo Automobile Workers in Chennai: Short and Succesful Strike against Casualisation and Low Wages –
On 1st of December 2011, 500 workers in the stamping and foundry units of the automobile parts manufacturer Caparo (Sriperumbudur/Chennai plant) went on strike. After two days, management agreed to raise wages and to make 110 workers permanent. We document our rather limited information and ask friends and comrades in Chennai to supply further insights on this important struggle. The strike has to be seen as a continuation of the unrest at Maruti Suzuki or Munjal Showa in Manesar, Gurgaon – the unrest of a new generation of workers.
http://www.caparo.co.in/global_presence.html
The information on the numbers of workers who took part in the dispute differs. Some sources state that there are 800 workers employed at the plant, out of which 500 are ‘company trainees’, the rest workers hired through contractors. According to this source only the ‘company trainees’ took part in the dispute. Other sources claim that 500 out of 800 ‘company staff’ laid down tools and were joint by 600 workers hired through contractors. It would be important to know which version comes closer to truth.
Workers struck on Thursday, 1st of December 2011. On Saturday, 3rd of December, the Caparo management arrived from Delhi for negotiations. After management agreed on certain demands raised by the workers, work resumed on Sunday morning, 4th of December. “The training period is for about 1-1.5 years. But many of the workers have been here for three to four years without getting confirmed,” said Mr E. Muthukumar, union leader at Caparo. “The management has given confirmation order to 110 workers belonging to C3 grade. The rest of the workers will be made permanent over a period of time,” said Muthukumar. “There has also been a salary increase – from Rs 7,200 gross to Rs 10,200. The management has promised us that the other issue of recognition of our union will be taken up later”.
Caparo India is part of the UK-based Caparo group let up by Swraj Paul. Whoever is interested in the history of this ‘industrial captain’ should read about his involvement in the back-and-forth over the management leadership at Escorts in Faridabad during the early 1980s:
https://gurgaonworkersnews.wordpress.com/workers-history/#fn141
The plant near Chennai supplies stampings, aluminium die-castings and forgings Nissan and Ford. Caparo India basically supplies parts to all major car manufacturers in India and for export, for example:
* Caparo Maruti Limited produces sheet metal and door-parts to Maruti Suzuki and General Motors from factories in Gurgaon, Halol and Bawal;
* A different plant in Halol manufactures axle and suspension systems for GM and for export to Thailand and Mexico;
* The plant in Pune manufactures stamped components for Tata Motors;
* There is a fastener manufacturing unit in Chopanki, another stampings facility in Greater Noida and Caparo aluminium foundry, Chennai.
http://www.caparo.co.in/global_presence.html
http://www.caparo.com/en-gb/worldwide/worldwide.aspx
Comments
*** The Failing ‘Kingdom of Dreams’: The Global Crunch and the Local Crisis of Real Estate –
In the last month we could observe how two very ‘finance’ sensitive sectors slowly, but surely crunched under lack of liquidity – the airlines and the real estate sector. These are ‘early symptoms’, hinting at the condition of the general economy, the root of the problem lying not in ‘sector specific issues’, but in the general squeeze: rising costs of credits vs. lower expectations of future profits.
The fiscal deficit of the state in India increased after the 2008 bail-out, subsequently the state finances its debts by selling state bonds to ‘private local’ banks (‘domestic market borrowing’). The share of ‘domestic market borrowing’ in financing the federal states’ fiscal deficits increased from around 15 per cent in the 1990s to around 75 per cent today – the ‘domestic market’ share for the central state’s borrowing is currently at about 85 per cent. Like in the global north we can see a close interdependence between ‘state’ and ‘financial sector’: the state bails-out ‘the banks’, not in order to ‘stuff the bankers’, but because its own deficit largely depends on ‘market borrowings’. Behind this we can see the need of the ruling class to ‘centralise’ the global command over the credit system, BUT to maintain the bourgeois appearance of separate economic and political spheres – they have seen how quickly ‘state power’ gets under fire nowadays once it is seen not only as a form of political oppression, but also the source of economic misery.
Through the ‘bailout’ the fiscal deficit increases. The regime forecasts a fiscal deficit of 4.6 per cent of GDP for this fiscal year, but their own officials question this: “It is quite clear that it will be very significantly worse. I can’t quantify,” Montek Singh Ahluwalia, deputy chairman of planning commission, said in an interview in mid January. Conservative estimates foresee a deficit of 6 per cent plus – in 1990, before the declaration of state bankruptcy, the fiscal deficit was around 3 per cent. The ‘trust’ in the government as a guarantor for financial stability is eroded: Indian government bonds are among the 10 riskiest in the world, according to a study issued by BlackRock in December 2011. Thereby the ‘general costs’ for borrowing increases: interests on the benchmark 10-year ‘Indian’ government securities jumped to above 9 per cent by end of 2011, an annual increase of more than 1 per cent. These costs trickle down into the wider economy.
At the same time the ‘expectations of future profits’ on the global markets look rather bleak – a global market which the ‘Indian economy’ is increasingly integrated in: India’s (foreign) trade to GDP ratio increased from 20 per cent in 1993 to 45 per cent in 2007; ratio of foreign assets and liabilities to GDP increased from 43 per cent in 1993 to 85 per cent in 2007. The global slow down translates directly into a slow down in the ‘Indian’ market. The request by the Indian government that the state-owned companies should stop “sitting on piles of cash”, and instead spend it on investment in ‘infrastructure’ seems like a rather helpless appeal.
The ‘credit crunch’ at this point leaves the sphere of figures and percentages, the realm of mathematics and regulations, and reveals its origin: the ‘real antagonism’ in the ‘the real capitalist world’. Here certain ‘finance’ sensitive sectors become ‘precursors’, e.g. airlines (global situation, oil prices, ‘state finance’) and real estate sector.
In autumn 2008, the financial trouble of ‘Indian Airlines’ – treated as a symbol of the booming subcontinent – became the stage-show for the state bail-out, a ‘proof of trust’. In October 2008 Jet Airlines had announced the dismissal of 1,900 workers. We then were shown some symbolic protests by the unions, fiery speeches by various political representatives, a state intervention, a repenting general manager and the public reinstatement of the workers. The state guaranteed financial support. Three years later the trouble returns. Kingfisher Airline is close to bankrupt, five of six main Indian Airlines declared losses in 2011. In mid-January 2012, pilots and cabin crews of Air India went on a wildcat one-day strike, protesting non-payment of their wages. The back-log of allowance payments had reached four months.
The situation is similar in the real estate sector, which makes up around 10 per cent of the Indian GDP (including construction, real estate related financial services etc.). Interest rates for mortgages and other real estate credits are high: The central bank’s repurchase rate, currently 8.5 per cent, is the highest level since 2008. The costs for interest payments for real estate developers increased by around 10 per cent on average during 2011, e.g. India’s biggest developer and ‘neo-liberal founder’ of New Gurgaon, DLF paid a record 5.26 billion Rs of interest in the third quarter of 2011, up from 4.96 billion Rs in the prior period. Combined net debt of the 11 biggest Indian developers rose 19 per cent in 2011. The pace of new project launches has severely been crippled in 2011 – a decline of about 50 per cent. Of the total housing inventory pertaining to the under construction projects, 39 per cent are lying unsold. Of the total office stock of 367 million square feet in the major cities, around a quarter remains vacant at the end of 2011.
The credit crunch translates itself back into the ‘real world’ in form of urban deserts – in particular in Gurgaon. The pillars of three symbols of the neo-liberal boom in Gurgaon are shaken: DLF itself, the Reliance SEZ and the ‘Kingdom of Dreams’. DLF stared a sell-out of assets to bring down its debt of Rs 22,500 crore in September 2011. In December 2011, DLF sold its 60 per cent share in a Pune SEZ, DLF also exited from Noida IT Park and sold real estate land in Gurgaon.
In January 2012 the Haryana government announced that it would take back 1,383 acres previously sold to Reliance Industries in Gurgaon. RIL and the Haryana government had entered into a deal in 2006 for setting up the multi-product SEZ, at the time hailed as ‘Asia’s biggest SEZ’ and showcased as a key achievement of the Congress government in the state. Chief Minister Hooda had, on the day of the signing, claimed that the project would create jobs for 500,000 people and that the state would earn Rs 10000 crore from the projects. Six years later, in January 2012 he said: “Yes, we are in talks with Reliance (with regard to handover of the Gurgaon land to the state government) because it has not been able to set up the SEZ.
In January 2012, also the ‘Kingdom of Dreams’, a Bollywood entertainment mall, in Gurgaon started failing. The Haryana Urban Development Authority (HUDA) announced “to give one last chance to the city’s entertainment hub, Kingdom of Dreams (KoD), to pay up the Rs 9 crore it owes to HUDA. If KoD fails to comply this time, it faces closure.” HUDA and Great Indian Nautanki Company had signed an agreement in February 2008. According to the agreement, the firm had to pay Rs 36 lakh per month as rent. The first two notices were issued in June 2011 – the pending rent amount increased to Rs 7.63 crore by November.
We will see how the crisis of the ‘kingdom of nightmares’ will impact on the wider working class reality, on the industrial companies closely linked to the real estate bubble…
*** Middle-Class is Revolting –
The fact that the iron fix-points of society – money, commodity, state power, professional advancement etc. – slowly turn into sand-castles, leaves its impact on the mind not only of workers, but also of the middle-waged classes. Recently Gurgaon witnessed some outbreaks of ‘middle class anger’ towards the commodity-form. ‘Middle class’ people who lose more time in traffic jams on the National Highway, than the new highway would allow them to ‘win’ by speed, forcibly opened the toll gates which are meant to ‘finance’ the highway. Young ‘middle-class’ people came to see ‘Metallica’ in Gurgaon – a band, which is known for their arsehole attitude towards ‘free music downloads or sharing’ on the data highway. After the announcement that the concert would be postponed, people smashed the concert venue. Two short news items on pent-up anger…
On 28th of October 2011 Metallica was supposed to play in Gurgaon. More than 25,000 fans flocked to the venue ‘Leisure Valley’, with some paying more than 10,000 Rs for tickets (current monthly average wage for industrial workers around 5,000 Rs). After the news of postponement was announced on stage, disappointed fans vandalised the venue ‘Leisure Valley’, which can seat around 30,000 people. They broke barriers, climbed on stage and tore posters, smashed loudspeakers and equipment. “The show was cancelled with no prior information to the ticket buyers or [to] the district administration – which could have caused [a] law and order problem,” explained a government spokesman.
On 2nd of January 2012, protesters, who have been demanding the removal of two toll plazas on Gurgaon Expressway, forcibly opened the toll gates at Kherki Dhaula plaza for an hour or longer. The incident took place after villagers from nearby areas held a meeting to plan their future course of action. Almost a month ago, on December 4, the same group had forcibly opened the toll gates of the 32-lane plaza. On Monday, the demonstration by the Toll Hatao Samiti and some of the residents’ organizations also received support from the local Hindu-Nationalist BJP and INLD. “Gurgaon is the only city where two toll plazas have been allowed within 20km of municipal limits. The private company is doing nothing to improve road infrastructure,” said one of the ‘leaders’. The private developer, Delhi-Gurgaon Super Connectivity Limited (DGSCL), has sought financial compensation from the Haryana. At least 190,000 cars pass through the 32-lane toll plaza every working day.
Comments
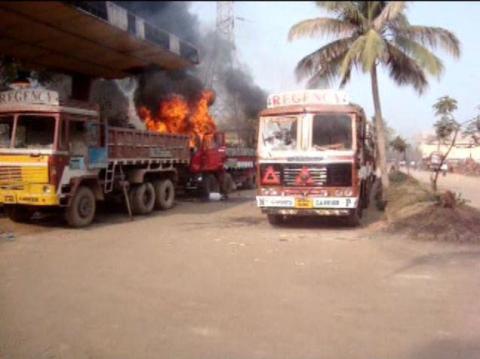
GurgaonWorkersNews – Newsletter 48 (March 2012)
Gurgaon in the industrial belt of Delhi is presented as the shining India, a symbol of capitalist success promising a better life for everyone behind the gateway of development. At a first glance the office towers and shopping malls reflect this chimera and even the facades of the garment factories look like three star hotels. Behind the facade, behind the factory walls and in the side streets of the industrial areas thousands of workers keep the rat-race going, producing cars and scooters for the middle-waged classes which end up in the traffic jam on the new highway between Delhi and Gurgaon. Thousands of young proletarianised post-graduates lose time, energy and academic aspirations on night-shifts in call centres, selling loan schemes to working-class people in the US or pre-paid electricity schemes to the poor in the UK. Next door, thousands of rural-migrant workers up-rooted by the rural crisis stitch and sew for export, competing with their angry brothers and sisters in Bangladesh, China or Vietnam. And the rat-race will not stop; on the outskirts of Gurgaon, new industrial zones turn soil into over-capacities. The following newsletter documents some of the developments in and around this miserable boom region. If you want to know more about working and struggling in Gurgaon, if you want more info about or even contribute to this project, please do so via:
http://www.gurgaonworkersnews.wordpress.com
gurgaon_workers_news@yahoo.co.uk
In the March 2012 issue you can read
Comments
*** Further Material on Struggle at Maruti Suzuki, Manesar –
We translated two ‘Maruti Suzuki Workers’ Diaries’, published in Faridabad Majdoor Samachar in December 2011 and January 2012. The diaries demonstrate that negotiations, formally elected leaders or legal agreements are not needed in order for workers to improve their conditions. As a result of the unrest Maruti Suzuki offered higher wages, more holiday and much lower work loads. Not because they faced a negotiation partner who had a disciplined mass behind them; but because of the opposite, the management faced a confrontation with what appeared to them to be a rather unruly mass whose next step was not predictable. The Maruti Suzuki dispute also shows that the long-term result of the struggle depends on the ability of workers to go beyond the immediate sphere of their factory, without losing this base of daily relationships. The more recent wildcat support action of Maruti and Suzuki Powertrain workers for a workmate employed and injured at a supplier (see report) indicates that the Maruti struggle has changed the atmosphere amongst workers in Manesar in general. How closely related the conditions in Manesar are to those in automobile centres across the globe becomes visible in the current debates about EU-India trade pacts and discussions about automatisation in the industry in India (see summary).
*** Yanam is Everywhere: Trouble at Adidas/Reebock/Puma manufacturer Adigear, Manesar –
On 27th of January the police killed a worker at Regency Ceramics in Yanam, Andhra Pradesh, during a conflict with the locked-out workforce in a dispute over wages and regularisation of workers hired through contractors. In response workers attacked the factory and managements’ houses, during which a top manager was killed. Workers burnt down parts of the plant, the company college, lorries and other equipment. Workers living in the area used the opportunity to loot neighbouring companies, e.g. a cooking-gas bottle supplier. Yanam is potentially everywhere. Below you can find a short report about current disputes at Adigear in Manesar, a textile manufacturer for Adidas and other international sportswear brands. During one of the conflicts a top manager got beaten up. We see these incidents as an expression of the increasing pressure of crisis. You can find a short summary concerning the current threat of mass loan default of textile companies in India – and the utter perplexity of the representatives of capital – leaving the representatives of capital at a loss.
*** Delhi Calling: Get Involved in Faridabad Majdoor Talmel
To abolish the global work/war house will take more than informative exercise! If you live in Delhi area, please be welcomed to take part in Faridabad Majdoor Talmel – a workers’ coordination. We distribute around 9,000 copies of Faridabad Majdoor Samachar on ten days each month in various industrial areas around Delhi. You can also participate in the workers’ meeting places which have been opened in various workers’ areas. If you are interested, please get in touch. For more background on Faridabad Majdoor Talmel:
http://faridabadmajdoorsamachar.blogspot.com/p/fms-talmel.html
*** Further Material on Struggle at Maruti Suzuki, Manesar –
Between June and October 2011 around 3,500 workers at Maruti Suzuki car plant openly confront the factory regime and its institutional allies in Manesar, in the south of Delhi. Their struggle leaped over to other automobile factories in the industrial corridor, which brought the world’s third largest automobile assembly plant in nearby Gurgaon to a halt. In the most significant workers’ struggle in India in the last two decades the young workers managed to undermine the companies’ attempts to divide them along the lines of temporary and permanent contracts. So far we published three longer texts about this important experience and tried to formulate preliminary conclusions for a necessary open debate.
GWN no.45
GWN no.44
GWN no.41
In this newsletter you can find further material, mainly two ‘Maruti Suzuki Workers’ Diaries’ , published in Faridabad Majdoor Samachar in December 2011 and January 2012. The friends of Faridabad Majdoor Samachar take it seriously to discover and circulate this important experience, even if the official dispute is over. It lays outside of our capacity to summarise the slowly condensing experience into a comprehensive article. We can only generally state that the Maruti Suzuki dispute confirmed the importance of the ‘centrality of the factory’, as a place of direct confrontation between the essence of capitalist relations and workers’ collective power, as a place where the antagonistic elements of the productive cooperation (‘working together under capitalist division of labour’) of workers is concentrated: productive cooperation as the main source of capitalist productivity and power and at the same time the material bases for workers’ self-organisation as an ‘proletarian inversion of cooperation’. The workers at Maruti themselves are not different from the migrant workers in hundreds and thousands of other factories in Gurgaon or Faridabad, and they themselves have been working in these factories. Therefore it is not their particularly ‘advanced consciousness’, which developed a struggle with the most advanced forms of collective activity, questioning of legality etc., but their specific condition in the centre of production.
We have also seen that it does not need negotiations, formally elected leaders or legal agreements in order to translate workers’ unrest into material improvements. Maruti Suzuki offered higher wages, more holiday and much lower work loads, not because they faced a negotiation partner who had a disciplined mass behind him (sic!), but because of the opposite, the confrontation with a – seemingly from the perspective of management – rather unruly mass whose next step was not predictable. The Maruti Suzuki dispute also shows that the long-term result of the struggle depends on the ability of workers to go beyond the immediate sphere of their factory, without losing the base of daily relationships. Their often temporary status forces them to act towards this direction. The example of the wildcat support action of Maruti and Suzuki Powertrain workers for a work-mate employed at a supplier on 13th of January 2012 – see below – shows that the Maruti struggle has changed the atmosphere amongst workers in Manesar in general. How closely related the conditions in Manesar are to those in automobile centres across the globe becomes visible in the current debates about EU-India trade pacts and discussions about automatisation in the industry in India.
*** Maruti Suzuki Manesar Workers’ Diary – December 2011 –
*** Maruti Suzuki Manesar Workers’ Diary – January 2012 –
*** Wildcat Solidarity Action for Injured Automobile Worker –
*** Update on General Situation of Automobile Industry in India –
*** Maruti Suzuki Manesar Workers’ Diary – December 2011 –
* Before June 2011 the A-shift had to start work at 6 am, instead of 7 am, and the B-shift had to work till 1:40 am, instead till midnight. These daily two hours overtime were not officially recorded by Maruti Suzuki management and the overtime was paid at single rate, instead of the statutory double rate. Maruti’s official production capacity was 1 million per year, produced and sold were 1.27 million cars last year. After the 13-days occupation of the factory in June the workers stopped working overtime.
* A supervisor said: “After the workers had occupied the factory for a second time they forced the company to reinstall the company bus transport. This was good, it was an enormous effort to get to work without the busses.
* After the second agreement was settled workers signed the good-conduct undertaking and went inside the factory on the 3rd of October. We were scared of re-entering the factory, but the supervisors and management were twice as scared. In all the departments workers first listened to the sermons of the leading management and then arrived at the production lines at 9 am. Around 30 per cent of workers were shifted from their previous work-station to a new one. Then phone calls of workers hired through contractors came in saying that although permanent workers and trainees were taken back in, the workers hired through contractors were denied entry and told to take their final dues from the contractor. People trusted the (non-recognised) union committee, whose members had been suspended and kept outside, people listened to their instructions. The committee said that they gave management two to three days to take the workers hired through contractor back on.
* On the 7th of October, when the B-shift entered the factory, people said that “something is going to happen”. Suddenly at 3:30 pm we assembled, the decision was made to get people together from all departments as quickly as possible and not to leave a single person there. All workers from the ‘old’ assembly line gathered together. In addition there were around 170 permanent workers from the Manesar factory, around 700 workers from the Maruti Gurgaon plant and more than 600 newly hired workers from ITI’s in Kanpur, Riwa, Himanchal, Bihar, Delhi, who management had all kept inside the plant since beginning of September. Of these workers many had been employed at the ‘new’ assembly line. Most of these workers left the factory at that point on their own accord. The workers immediately formed chains at all entries and exists of the factory.
* At that point there had already been 400 police on the factory premises. At 8 pm the chief of the local police station arrived and said: “Those people who you force to stay, let them go”. People from management stood further away and called individual workers by name to come forward. Some of the workers refused to leave the factory out of fear. The next morning the police chief returned together with contractors and made 30 to 40 rounds on the premises.
* On the night of the 7th of October we prepared ourselves to sleep – we gathered together all blankets and pillows and distributed them. The company had provided these pillows and blankets for those ‘working’ workers, who stayed inside the factory 24 hours during the ‘lock-out’ in September. We found some papers with a list of names of all those workers, in front of each name they had written a column saying ‘pillow’, ‘vest’, ‘loin cloth’, ‘soap’, ‘tooth paste and brush’, ‘sandals’, cigarettes’. In September, apart from these workers who stayed inside for 24 hours, busses arrived from Gurgaon plant every day, with bouncers and workers. Management had ‘promoted’ workers hired through contractors from Gurgaon plant to trainees and used them for production in Manesar.
* During the time of the lock-out supervisors and managers also had trouble over trouble. They feared for their security: would the guys storm inside the factory and start trashing? would the guys catch you outside and trash you? would they trash you once normality has returned? The work-load was also extreme: they extended shifts to 12-hours, they had to produce with new guys they did not know – so they themselves also had to work. A line supervisor who had been brought in asked: “How do the guys who normally work here manage to churn out so many cars? They were also worried about their jobs.
* During the time of the occupation management ordered to retrieve a huge die from the press shop in order to stir things up a bit and worry us. They came with a big trailer and 100 police. We discussed: if we actively try to hold them back, they will start beating us up. Let’s lie down in front of the truck. So 50 of us lied down in front of it. The police chief stopped the truck by hand signal and said to management: if you want we will get it out by running over them. The truck remained where it was – the driver had left.
* In addition to the 400 cops, on 13th of October 200 more police arrived inside the plant. At night after 10 pm a chain of workers stopped an official of the local administration, who had arrived with cameramen and 30 to 40 helmet wearing cops. The official came in order to put up the high court order to leave the factory. After discussion the factory committee gave their permission to put up the court order. Things were very chaotic at that point – when the official put up the document they shot photos, when they spoke to the committee they took photos. After we read the order there first was a bit of confusion, but then the decision was made not to leave the factory. Also the decision to keep calm. The police had stopped any food or other things from entering the factory since the afternoon. During the night of the 13th of October we were hungry, we passed the night by talking. The left-over chana we distributed amongst the apprentices in the morning. In the morning the company stopped the water supply to the toilets. We gathered the rest of the drinking water.
* The news made rounds that the police chief would come in order to search workers. There were around 1,600 permanent workers, trainees and apprentices inside the plant – the police searched us one by one. Then suddenly the DC and 20 to 25 administration officials arrived in the plant, surrounded by cops with guns. They walked around a bit, then stopped in one place and started talking – he had no microphone, so the workers gave him a mic. At the beginning he spoke exactly like a (union) leader: that we were good workers, that we were educated, that we did a great job since five years now, that we achieved such high production levels, that this grants so much tax for the government. he then said that our wages were higher than those of others, that the management is good, that we have been seduced by some people, that we have illegally occupied the factory, that we should follow the orders of the high court, that we have to follow the order to leave the plant, that there wasn’t any other option, that playing with the law will not be tolerated, that since the erring of the Rico Auto workers law and order has been in dire straits, that if Maruti Suzuki will move the factory, our jobs would also go, but why should the government have to bear the losses.
* The workers listened to these words of the DC attentively for half an hour. Then the DC started to tell a tale, the tale which Maruti Suzuki management kept on telling: the race of the turtle and the rabbit, which ends with the morale that if sometimes the rabbit carries the turtle, and sometimes the turtle the rabbit, both win. Team-work! Workers and management should join and go together. But soon after the DC had started his story, the workers stretched out, many fell asleep, others started talking amongst themselves. End the end the DC said that he will quickly move management to enter negotiations for a settlement, and that we should now please follow the order. Another official spoke again about the law, that the occupation is illegal, that we had to go. When the DC was about to leave a worker took the mic: “We have now listened to your words, now listen to ours.” The DC stopped, but when one worker after the other started questions, he left. When workers started to shout slogans, with rather load voices, the DC and the other officials fled the factory more or less running.
* After talks between management and some workers on 22nd of October, an high official of the company, the managing executive officer, made a straight intervention in the Manesar factory. In an expensive restaurant on National Highway 8 a two-day meeting with 60 to 70 ‘representatives’ of workers and managers took place. They negotiated around the question of holidays: management offered that some of the holidays could be fixed, others could be flexible. Management said that they will give us 16 days annual leave. They said that our parents will be covered by the company health system, that this will become easier and more straightforward. “We will see about company transport, too”. They said: “Form a union, we will not object.” When the company wanted workers to form a company committee and workers objected, management said: “Okay, don’t form a committee then, that’s fine.” They also said: “There will be a good wage increase, just wait for three months”. “We will pay you more than the workers at Powertrain (Suzuki Powertrain had an 11,500 Rs monthly increase over three years: 6,500 – 2,500 – 2-500). And the bosses themselves said that the work-load was to high and that as soon as B-plant has started operation the line speed will be reduced from 45 seconds per car to 1 min per car.
* The fact that workers hadn’t put forward any (wage) demands led the bosses to wonder about the ‘policies’ behind the dispute. They said: Tell us, haven’t all the issues relating to your mates been resolved after the 13-days occupation in June? We don’t understand why things flared up again – have you been seduced or what happened? Some high official within Maruti Suzuki belong to the same party as a certain section within leading management in Hyundai, Honda, Volkswagen, Mercedes, Ford – and some of these high officials had recently left Maruti Suzuki in order to get jobs at other car manufacturers. Who knows, may be they arranged all this trouble at Maruti in order to benefit their current employer?
* On 3rd of November A-shift and B-shift stopped work for an hour each and their were department meetings. The big bosses repeated what they had said already. In November management had put up a notice saying that the formation of a works committee has been rejected.
* The Manesar A-plant produced 1,150 cars in two shifts in November. Working overtime is strictly forbidden. The manual line has been idle. Instead there are still 70 to 80 police staying there. Up to now, the end of November, you can see them in the morning, with their wrapped up towels, brushing their teeth.
* When the bought-sold issue (‘golden hand-shake’) of 30 workers (union representatives) made the rounds after the end of the dispute, a Maruti-Suzuki worker said, “Earlier we used to pass on the issues to the president, general secretary, department co-ordinator – they will tell. But now every worker himself answers. On every issue, everyone gives his opinion. The atmosphere has changed.”
* All in all: “The time in Maruti-Suzuki factory during October 7-14 was extremely good. There was no tension of work, there was no tension of coming to the factory and going back, there was no tension of catching the bus, there was no tension of cooking, there was no tension that food has to be eaten only at 7 o’clock or only at 9 o’clock, there was no tension as to what day or date was that day. Lots of personal conversation took place. We had never come so close to one another as we came in these seven days.”
*** Maruti Suzuki Manesar Workers’ Diary – January 2012 –
* The assembly-line speed used to be a car per 45 seconds, they have now reduced speed to a car per 1 minute.
* The police have left the factory in December.
* The company management does not understand what really happened during the last months and why. Therefore they are afraid of pushing things too far with workers. Management has started to pat us on the shoulder, to give us concessions.
* There is a distance. There keeps being a distance between management and workers. The bosses say: the distance has been created, let it be closed. The big bosses said to the department managers that they should establish direct relationships with the permanent workers and technical trainees. Through the executive officers, management has issued two new email IDs for workers to contact and communicate with the company management directly.
* Being alarmed by the many debates and wide-reaching discussions amongst workers some elements started to spread the rumour that the company would tap workers’ phones. If company and state are afraid of us talking to each other, and therefore spread these rumours, we should increase doing so, increase talking, increase their fear. In September – October, when large numbers of Maruti Suzuki Manesar workers spoke to each other in an open way, spreading rumours about conspiracies of management or state played an important role when it came to stirring up some dust in order to cloud things again. Company and state are very weak, this is why they have a lot of fear of workers conversing.
* After the (union) president and secretary and then the other 28 suspended took their final dues and left, the process of union registration continues. First they tried to appoint union officials on the base of ‘regions of origin’. This got entangled in inner-disputes. New union officials were appointed. The company knows about this – it is all in full knowledge of the company. Workers had trusted the president and secretary way too much. Now, when there is talk about the question of the president election, we only come and see who they want to make president. Now we won’t just close our eyes and trust anyone. Obviously, if the company wants to, a strike can always happen, but now we will make our decisions only after proper thinking and discussing. The company has not paid money to all those 30 guys who left the job in order to make them leave from here. They gave them money so that they would always intervene on the side of the company. The sphere of union and officials is still the chosen arena of the company.
* Debates. “You should put pressure on the administration in Chandigarh in order for the labour commissioner to register your union.” “What will a registration change? Why would you need it? You have seen that the labour commissioner came all the way from Chandigarh to the factory gate when the dispute was on – and you have seen what his role was.” “That’s correct. But nevertheless, if the government accepts you, you will get some help from it.” “But what kind of help? You have seen the kind of help the company and government has to offer. Why do you want to reduce your strength from 3,500 workers to 950 workers?” “No, we should remain together as 3,500 workers.” “But how? Only the permanent workers can become member of the union. According to the legislation trainees, apprentices and workers hired through contractors cannot become members. By forming collectivity amongst all workers in the factory and beyond the factory you have shaken company and government. Why do you now want to shrink again?” “Currently there is no one who would engage in talks with the company. The company started to give you this and that concession, because they are afraid that you have joined together amongst 3,500 and might join with the 100,000s around you. They have increased the wages of the apprentices, trainees and workers hired through contractor. They have reduced line speed from 45 sec to 1 min a car. The company official told that there will be a considerable wage increase for the permanent workers. So, what kind of interest could you have in a 950-member union which has negotiations between company, president and secretary? At the moment the company hasn’t got anyone for settling an agreement with, this is why they are forced to make concessions to all workers. This is why the company is actually in need for a union and union leaders. The conditions nowadays are such that – even if you intend a thousand times to achieve the opposite – starting from the fact that union registration and acceptance is limited to the permanent workers, the leaders will be reduced to a small circle and thereby become a tool in the hand of the company. You just have to look at the example of the Honda union. In 2005 permanent workers, trainees, workers hired through contractors fought together. Now most of the 1,800 permanent workers have supervisory jobs. The company has stopped to keep trainees. Please speak to the 6,500 workers hired through contractor about their view on the union – the workers who do most of the production work at Honda – and then think about it again.”
*** Wildcat Solidarity Action for Injured Automobile Worker –
On 13th of January a worker hired through contractor employed in the factory of the car parts (break shoes) manufacturer Allied Nippon received serious chemical burn injuries during a work accident. The company brought the worker to a private nursing home, instead of an ESI hospital, in order to keep the accident ‘unofficial’. Seven friends of the worker, living in the same dormitory villages in Manesar and employed mainly as temporary workers at Maruti Suzuki, visited him at the nursing home. The friends first contacted the supervisor of the contractor which employed the injured worker. The contractor said that he had no information about the issue – the worker also has not been issued an ESI card, although he had been employed since early December 2011. The seven friends then went directly to the Allied Nippon factory, but the factory manager refused to see them. The friends then decided to call other friends for help. Within half an hour 70 to 80 workers employed through contractor in different departments of Maruti Suzuki and Suzuki Powertrain gathered in front of the Allied Nippon factory. The factory manager felt threatened, and stayed behind the factory fence. The assembled workers said that he would not even have to bother with paying for the hospital fees, that the workers themselves would pay for that, but that he has to pay the worker until he is better and get his job back. He should also inform the parents of the worker. “We got a lot of support during the time when we occupied the factory. Now it’s time that we support others”, said one of them.
http://www.alliednippon.com/manufacturing-facilities.html
*** Update on General Situation of Automobile Industry in India –
In the last month there was a fair bit of back and forth around the question of the EU – India free trade agreement and how it would impact on the automobile industry in both regions. The back and forth does not primarily express conflicting interests between different car manufacturers, given that most companies now have plants both in Asia and Europe. The conflict evolves rather around the question how to balance the global movement of production – not necessarily only from north to south – and the regional framework of state revenues and labour markets. Currently the EU imports around 250,000 cars from India annually, that’s more than from South Korea – Hyundai, itself a ‘South Korean’ company is one of the main exporters from India. The Indian market ‘only’ imported around 4,000 cars from the EU in 2011, this does not include automobile related commodities (parts, machinery for production etc.). The free trade talks on 10th of February haven’t determined yet whether the 60 per cent Indian import tariffs on cars manufactured in the EU will be dropped to 30 per cent, or whether the 6.5 per cent EU import tariffs for ‘Indian’ cars will be dropped to zero, as demanded by the Indian state delegation. It is for sure that general market pressure will increase, not mainly because of tariff policies, but due to the general dynamic of capitalist production – and both regional state and the global manufacturers will try to translate this pressure into pressure on workers everywhere – General Motors in the US currently announces ‘record profits’, as one of the results of sharp real wage decline in the US car industry.
After the increased unrest in the automobile industry in India the management publicly muses about ‘automatisation’. “Three hundred robots whirr to life every morning all over Hyundai’s Sriperumbudur plant near Chennai, rubbing shoulders with 1,500 employees and 7,000 contract workers. Together, man and machine churn out one car in less than a minute; over 600,000 cars roll out of the factory every year. The number of robots inhabiting the factory has increased more than 10-fold in a decade. Car companies directly or indirectly employ over five workers for every car produced. All automobile and component companies together employ over 1.3 crore workers directly and indirectly. At Hyundai, gone are the part-bypart way of putting together a car; today, 40 per cent of the value of the car comes to Hyundai by way of pre-arranged modules, de-skilling the job at the shop floor. The Indian auto shop floor isn’t as automated as those in the more mature markets. So, while German carmaker Volkswagen’s Chakan plant has an automation of 30% in its body shop, the comparative number back home would be 90%.”
Obviously there is ‘automatisation’ happening in the main assembly plants, at the same time there is also outsourcing to labour-intensive first and second tier suppliers going on. The talk about ‘automatisation’ is mainly ideological talk, which expresses itself nicely in the following quote by tyre-manufacturer Apollo’s top-manager Sharma: “We do not have what has traditionally been referred to as ‘workers’ at the Chennai plant.” Apollo, instead, has shop floor engineers who are not just in charge of running machinery but also its upkeep, maintenance and effecting innovation. In order to see more clearly how much of this talk is ‘propagandistic’ it might be worth having a look at the developments in the global north, where the peak of ‘automatisation’ and ‘skill-enrichment’ in the car industry was probably reached around 1990, and since then – mainly as a result of stagnating wage levels – has basically reversed to rather ‘traditional’ means of industrial production.
In this regard we suggest greatly to read following account “At some point you are not interested in technology anymore”, by a Volkswagen worker in Germany:
http://www.wildcat-www.de/en/wildcat/79/w79_auto5000_en.htm
Comments
On 27th of January the police killed a worker at Regency Ceramics in Yanam, Andhra Pradesh, during a conflict with the locked-out work-force, in dispute over wages and regularisation of workers hired through contractors. Workers in response attacked the factory and managements’ houses, during which a top-manager was killed. Workers burnt down parts of the plant, the company college, lorries and other equipment, workers in the surrounding neighbourhood used the opportunity to loot neighbouring companies, e.g. a cooking-gas bottle supplier.
Yanam is potentially everywhere. Below you can find a short report about current disputes at Adigear in Manesar, a manufacturer for Adidas and other international sports gear brands. During one of the conflicts a top-manager got beaten up. The ‘textile’ sector in India is not excepted from the general tendency of crisis. On 6th of February we could read in the Economic Times:
“Yarn, fabric and clothing companies are in a sweet spot. They owe banks so much that now it is their lenders’ job to ensure they survive. With wild enthusiasm, banks have lent the textile industry Rs 2,50,000 crore in the last 12 years. Now companies say they can’t even pay interest on Rs 50,000 crore in working capital loans. Up to 15 per cent of loans to this industry are stressed and the number is rising fast. In today’s precarious times, such a gaping hole could be the last straw for banks. Most of these loans have already been ‘restructured’ once. If payments fall behind a second time, the account has to be classified as a ‘Non Performing Asset’ on the bank’s balance sheet. In December, a dozen banks asked the RBI to relax the rules on declaring bad loans and let these twice restructured loans remain standard. Because such relaxation flouts international prudential and accounting norms, quite sensibly, RBI refused.
The biggest players, with enough backward and forward integration to ride out the storms, continue to make money. Those in distress today were clearly unworthy of large loans in the first place and should now be written off. The real issue is that Indian textile companies are small, labour-intensive, non-integrated spinning, weaving, finishing and apparel-making outfits. Only 3% are large composite mills. Today’s world demands economies of scale. Indiscriminate government subsidies in the name of job creation further encouraged promoters to use public money for creating more such fragmented capacities that are inevitably idled at first signs of trouble. It is a mirage that the textiles industry is too big to fail. On the contrary, its myriad small units have outlived their utility. Their exit will occur only when banks face the consequences of their actions. And subsidy schemes should stop. Individual livelihoods can’t be protected by industrial dinosaurs.”
We remember the attack on the huge composite mills in Bombay in the mid-1980s, when the representatives of capital proclaimed that this ‘large-scale’-form of production is outdated and small, flexible units are supposed to be the future. We remember the recent mass waves of strikes and riots in the textile export zones in Bangladesh, where, according to this view, capital found better investment options. We are reminded that the problem of profit-margins, over-production, 16-24-36 hours shifts paralleled by rising unemployment is an universal problem. The crisis, and the ‘solutions’ proposed in the article above (the only solution the current system can provide), will create one, two, three, …many Yanams.
Adigear International Worker
(Manufacturer for Adidas, Reebok, Puma, FILA etc.)
(Plot 253, Sector VI, IMT Manesar)
Shift starts at 9:30 am in the morning. The 100 female workers finish work at 8 pm and the 800 male workers work till 1 am, sometimes till 6 am the next morning. On Sundays workers work till 6 pm, sometimes till 1 am. The male workers work 180 to 240 hours of overtime per month, paid at single rate. Wages are paid delayed, the August wages were paid in small installments from 20th of September onwards. On the 20th of September at 11 am, when wages were handed out, there was a lot of commotion. The six-foot personal security officer of the company director slapped one of the workers. Why did he hit him? The workers wanted to know, but the security officer had left the place. During meal break workers left the factory and started to question the security officer, but he escaped with the help of another security officer. The workers then met the general manager outside the plant and the workers treated him as the due representative of the security officer. He was then admitted to the ESI hospital. The company has close relations to the district police, so they acted immediately. The police arrived and arrested 42 workers, whose names were given by management, and brought them to the Manesar police station. In protest all remaining workers stopped working and left the factory. In return 21 workers were released, but the others remained locked-up. The workers did not re-start work, the factory remained idle from 23rd to 25th of September. Workers said: Release all of the arrested, withdraw the cases filed and pay compensation for lost wages… if you want the next orders to be shipped in time, fulfil these demands. Conflicts continued since then. On 3rd of December, when workers who had been sacked came to get their August wages, management called the cops again. We don’t know whether these workers got their wages in the end. When our October and November wages were still not paid on 15th of December, we stopped working at 9:30 am. When work was still not resumed at 1 pm the company send seven bouncers who started hassling workers. In response all of us left the factory…
http://www.adigear.com/clients.html
Comments
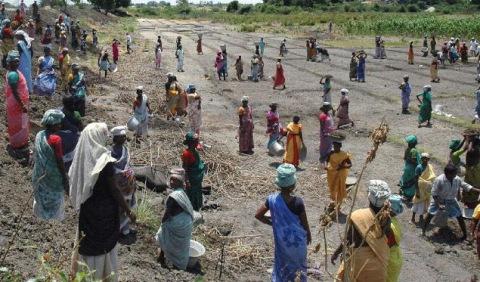
Breaking Rocks as ‘Social Empowerment’? –
Thoughts on the Rural Employment Scheme MGNREGS, India –
For the International Debate on Work Schemes and Crisis Regimes
Breaking Rocks as ‘Social Empowerment’? –
Thoughts on the Rural Employment Scheme MGNREGS, India –
For the International Debate on Work Schemes and Crisis Regimes
*** Intro
*** General Information on MGNREGS
*** MGNREGS on the Background of (Rural) Crisis in India
*** (Re-)Productive Functions of MGNREGS
* Reproduction of Labour Force
* Reproduction of Rural Class Divisions
* Regulation of General Wage Levels
* Regulation of Migration
* Integration of Proletarians as Individual ‘Citizens’
* Internal Re-figuration of the Global and Local State
* Invigorating the Dialog between Rural Proletariat and State
*** Current Struggles within MGNREGS and Preliminary Conclusions for the Communist Movement
Introduction
The Mahatma Gandhi National Rural Employment Guarantee Scheme (MGNREGS) in India is the world’s largest public work scheme. [1] In 2011 around 45 million workers were directly employed, half of them women. By decree, the scheme consists of labour intensive work, e.g. breaking rocks and digging earth for rural road construction.
With the deepening of the global crisis, the debate about ‘state-managed work schemes’ acquires a relevance, which goes beyond the national framework. [2] In symbolic terms the ‘multi-national’ character of MGNREGS was expressed during a recent G20 summit, when labour ministers applauded the ‘Indian’ work-scheme as an example of ‘innovative legislation’.
One of the features of modern work-schemes, which distinguishes them from labour schemes of the past, is the claim that they will strengthen the ‘community’, rather than being a mere work-house for the poor. Centrally designed work schemes are supposed to invigorate the local state and local ‘civil society’ structures – this reaches from the idea of the ‘Big Society’ community initiatives in the UK, to the gram panchayat (village council) and ‘social audit’ projects in India.
Whether seeing the scheme ‘as a battlefield for a rights-based movement’ or ‘critically co-managing’ them – there is a lack of debate on the left. I.e. one which could locate these schemes within wider capitalist re-production, the current crisis and unrest, and the state’s attempt to deal with the latter.
The starting point of a critique of the work scheme has to be the experience of workers themselves – and their fluid existence between being both ‘surplus population’ and ‘productive work-force’. In the following we summarise some material for the wider debate.
*** General Information on MGNREGS
MNREGS is not the first employment scheme in India. The announcements of ‘poverty alleviating’ schemes, such as the Employment Assurance Scheme (EAS), Jawahar Rozgar Yojana (JRY) and National Food for Work Programme, followed more or less synchronously the cycles of (global) crisis: from the first dent in the early 1960s to the early 1970s, when the ‘garibi hatao’-campaign Indira Gandhi’s preceded the more drastic ‘poverty eradication’ schemes of the State of Emergency in form of mass slum evictions and (forced) sterilisation schemes, particularly targeting the rural poor. Since the 1970s the ’employment schemes’ grew in size, due to an increase of a rural population mainly dependent on wage work and a parallel reduction of labour input necessary for agricultural production as a result of mechanisation etc..
It is no coincidence that the introduction of MGNREGS in 2006 was paralleled by a similarly far-reaching ‘welfare reform’ in Brazil. The Bolsa Familia, a type of social benefit payment for ‘the poor’, is said to be the world largest ‘conditional cash transfer program’. It is less important that both schemes were announced by ‘labour’-governments (PT/UPA), but rather that they have a similar origin in the particular character of the BRIC (Brazil, Russia, India, China) boom at the time. This boom saw on one hand a considerable influx of foreign cash (through ‘liberalisation’ of investment regulations etc.), boosting state budgets and nominal GDP; but on the other hand it was described as ‘jobless growth’, increasing the number of under/unemployed in need of state benefits.
Under MGNREGS every ‘officially poor’ family in rural India is entitled to 100 days of paid work – for one family member. According to law, employment is supposed to start 15 days after handing in of an application, under condition that a defined number of people (currently between 20 and 50) are enrolled in the scheme in the local village. In order to apply for the scheme there are certain formal requirements (registration in the village, job card, in some cases a bank account). If the local village council is not able to provide work after 15 days the applicants are entitled to unemployment allowance. It is up to the (individual federal) state government to decide the amount of unemployment allowance, but it must not be less than 1/4 of the minimum wage for the first 30 days, and not less than 1/2 the minimum wage thereafter.
In 2010-11, officially between 40 and 45 million people were employed on MGNREGS worksites. Since the introduction in 2006, the share of women increased from around 40 to now 50 per cent – which indicates that MGNREGS is mainly an ‘additional income’, an extra-wage for the household. According to a survey in around 1,000 villages in 2011, MGNREGS contribution to household income through wages was 16.5 per cent in Rajasthan, 9.62 per cent in Andhra and 8.39 per cent in Bihar. If we assume an average of six members per household and take the household as a basic economic/wage unit, than MGNREGS entered into the income of around 250 million people, out of a total rural population of somewhere around 800 million. In 2011, the central state allocated around 8,9 billion USD of its budget for MGNREGS, 3.7 per cent out of a total budget of 240 billion.
Currently, the official daily wage under MGNREGS is 120 Rs per day, around 2.7 USD. The central government pays the wages and 3/4 of material cost and some percentage of administrative cost. The federal state governments meet the cost of unemployment allowance and 1/4 of material cost. In most Indian states the MGNREGS wage lies above the minimum wage fixed by the individual states, in about half a dozen states the local minimum wage is higher. There is an ongoing constitutional back and forth about this fact. There are other legally fixed conditions, such as a crèche for children of MGNREGS workers, transport facilities etc..
MGNREGS is supposed to be labour intensive, and it is so by decree. For the scheme a 60:40 wage and material ratio has been legally fixed and the usage of machinery is banned, so is (officially) the use of contractors as middlemen. The work performed is supposed to be ‘developmentally’ beneficial to ‘the village’, in form of road works, irrigation infrastructure like wells, canals, ponds etc.. The main work performed is road construction. MGNREGS work is allowed on private land of small and middle peasants. The management of the scheme lies mainly in the hands of the gram panchayat (village council), the lowest level of state power. There is a formally described role of so-called social audits, composed of administration and ‘civil society organisations’, which are supposed to check the correct implementation of MGNREGS. The following report of a MGNREGS worker summarises well the main social aspects of the scheme:
NREGS Worker
(Faridabad Majdoor Samachar – March 2009)
“I am from an artisan family from a village in Mathura district. I have an ITI qualification (two-three years of technical apprenticeship). I have done my internship. In order to find work I roamed Mathura, Agra, Ahmedabad, Gurgaon and Faridabad. I started work in a factory in Faridabad, but I was ‘given a break’ (kicked out in order to avoid having to give a permanent contract) after six months. After the lessons of having been unemployed for some time and the trouble it means, when I got unemployed again, I was ready to apply for a job with the NREGS.
The first work started in July 2008: digging earth out of a pond for the agriculture panchayat (village council/authority). The second job was in August and September: digging earth out from an irrigation canal of the irrigation department. In total I worked for 21 days, the documents showed 22 days. The work was done by 35 workers, but the documents showed 50 workers – the other 15 were sitting at home and faked attendance. A lot of earth moving work, all measured in cubic meters – done by us 35 workers instead of the shown 50 workers. No payment in November and December. They said that they will open a giro bank account for transferral. They took 20 to 50 Rs in order to open this account. When the first payment was due they kept the 200 Rs in this account. At the time of the second payment they also kept the 200 Rs “for keeping it in the account” – as some kind of fee.
After a significant delay our wages ‘arrived’. We had to sign with our finger-print and money was given to the local temporary school teacher and the official from Gram Vikas (Agriculture Institution). From that money 800 was paid to us 35 and 400 to those who stayed at home. The same happened with the second payment, just that this time they asked for 50 Rs instead of 20 Rs for expenses. When we resisted they started to threaten us – “you will come here again and want to work, and then we will see”. Our pay roll was kept with the guy from the bank, our job card was with the school teacher.
We had been promised a daily wage of 100 Rs, we were actually paid 70 Rs and only after several months of hassle. In the meantime we all took time off from the NREGS work, so that when there was gardening work offered in January, no worker in the village would lay their hands on it. The school-teacher and the official from Gram Vikas gave us to understand that we should give money to the area, district and block officials, because they have to drive around a lot on the motorcycles in order to arrange things for us – which obviously costs money. In December, when our wages were distributed, the school-teacher received his outstanding wages from the government – he had not been paid for the last ten months.”
The fact that the scheme had to be ‘enforced’ against the opposition of ‘neo-liberal hardliners within the political class and that, although legally sanctioned, hardly any of the legally determined conditions are met – e.g. that the average amount of days of labour in 2011 was not 100 (as legally statutory), but merely around 40 days – also contributes to the prevailing view amongst the left, that MGNREGS is a question of ‘proper implementation’, of ‘defending entitlements’. Before analysing this view, we first have to see MGNREGS in the wider context of capitalist development and the crisis management by the state.
*** MGNREGS on the Background of (Rural) Crisis in India
If we see the actual form and content of MGNREGS, the actual work performed (labour intensive construction of infrastructure), it resembles very much situations, which in other times of capitalist history required rather unfree forms of mediation, e.g. in form of semi-bonded labour or actually forced labour. The fact that MGNREGS (breaking rocks for wages which hardly guarantee reproduction) does not need armed guards or barbed-wire and can appear as a ‘welfare benefit’ and a ‘legal right or entitlement’ says much about the enormous brutality of rural poverty in India in 21st century capitalism. No one will deny the fact that the rural crisis in India is aggravating. According to official figures 238 million proletarians in India are undernourished, the majority of the rural poor has to survive on less than 20 RS a day. Since 1995, more than 253,000 farmers have committed suicide.
In order to determine the quality of MGNREGS we would first have to determine the origin of modern rural poverty in India. The question is whether ‘the misery’ on the countryside is result of an insufficient ‘productivity’ in terms of material production of goods (material output) or rather an expression of a ‘produced crisis’ in capitalist terms: increased general dependency on market and money economy (commodities, wages), increase in productivity of social labour, declining prices due to relative overproduction, further rationalisation (use of machinery etc.) leading to an increase in ‘relative surplus population’ (unemployment) and therefore to aggravated poverty.
If we look at both urban and rural relations in the ‘global north’, then the current global crisis openly questions a ‘developmentalist view’: everyone can see that falling living standards in the global north are not due to a lack of productivity, but due to a crisis of profitability (and therefore of employment) due to an increase of productivity (‘rationalisation’). If, in the face of this crisis, developmentalist in South Asia still uphold that a further integration into the market (‘diversification’, small business models, micro-finance etc.) and an increase in productivity (either through more elaborate agro-technology or through sustainable empowerment of ‘female resources’ on eco-cooperatives) will alleviate rural poverty, they do this by referring to the specific difference between agricultural development in the north and south.
We want to have a look at this question, because essentially, the idea that the rural poor will be able to make use of MGNREGS in order to return to ‘small scale market farming’ or ‘small scale artisan work’ is the main ‘progressive’ gloss on MGNREGS. Or in other words: MGNREGS can only be portrayed as ‘progressive’ by both state and civil-society leftists if the reason for the brutal poverty is seen in a ‘lack of development’ and MGNREGS not as a ‘permanent workhouse’ for the poor, but as part of ‘productivity development’ which eventually will alleviate poverty and make MGNREGS redundant.
Small Scale Farming and Capitalist Productivity
So what is portrayed as the main peculiarity of (agricultural) development in South Asia? The fact that unlike in the global north average land-holding decreased. During the three decades after 1970, farm size in the United States (US) from 157 to 178 ha. Farm size in India in the same period has declined from 1.84 ha to 1.32 ha (other figures say 1.08 ha). [3] Around 87 per cent of global small land-holdings (below 2 ha) are located in Asia. The two questions which arise consequently are: a) are small land-holdings under given local conditions less productive than large land holdings; b) would an increase in productivity under given conditions (market economy) be a way out of crisis for everyone?
We would claim that the market pressure on small peasants actually has increased productivity above the level of bigger land-holdings and intensified their adaptation to ‘market trends’. “Dyer (1997) argued that the inverse relationship [per hectar productivity increases the smaller the land holding is] is neither a product of superior efficiency on the part of small farms nor is it due to better quality land on the small farms but arises from the desperate struggle of poor peasants for survival” – leading to long-term drop in productivity, because soil gets exhausted by the desperate attempt to squeeze more from it.
In order to do this, small peasants have to invest heavily, double the amount of small land holdings have irrigation facilities (borewells etc.) compared to bigger land holdings. During 2001-02 marginal farmers used 2.6 times the fertiliser used by large farmers. On large farms HYVs (high-yielding varieties) occupied 42 per cent of the area. In the next five years the HYV coverage on marginal and smallholdings increased to 72 per cent and 68 per cent, but their coverage on large farms remained below 50 per cent. In 2001 the per hectare value of crop output was Rs 25,173 at holdings below 0.4 ha. As the farm size increased towards 2 ha, productivity declined to less than Rs 17,000 per hectare. In large farms (4 ha to 10 ha) the value of aggregate crop production declined to Rs 13,500 per hectare.” (Chand etc., EPW June 2011)
Small peasants are also much more desperate to satisfy the needs of the market by ‘diversification’ (horticulture etc.). Does this ‘market adaptation’ save the small peasants? The opposite is true: “the crop that witnessed the most rapid growth in yield in 1990s and 2000s was cotton (ECONOMIC SURVEY, 2010-11). But, ironically, this crop is also the one that led to the largest number of farmer suicides.” (Sanhati) The price decline in cotton and the subsequent bankruptcy of small peasants can also not easily explained by ‘influx of subsidised US cotton’, India has been one of the main exporters to China in recent years: the crisis is largely ‘home grown’, an expression of a contradiction which is as much global as local.
What about general productivity: is there hunger in India because the agricultural production is particularly unproductive? Despite the diversion from food-grain production to non-food cash-crop over the last decades – to a point where in 2007 around 40 per cent of land in India is used for non-food commercial crop – the actual food-grain production still increased:
1960 – 1975 100 million tonnes
1991 – 2009 228 million tonnes
This is confirmed by figures demonstrating that neither the per hectare productivity is particularly low in India (2001):
Rice (kg/ha): 3,370 (India), 4,309 (world average)
Wheat (kg/ha): 2,802 (India), 3,086 (world average)
We can summarise that the rural crisis in India is a capitalist crisis, a crisis of commodity production, not of absolute productivity. The small land holdings are ‘too small’ in terms of market survival, the (total) land is not ‘too small’ in terms of producing goods for (all) people. On this background the developmentalist propaganda that raising productivity and market adaptation will provide a way out for the impoverished masses only speaks the word for an acceleration of the suicidal wheel of ‘individual survival on the market’. Obviously, the very uneven land distribution still remains a field of struggle [4], but it can be seen more as a result of the general problem of commodity production.
What we can see in general terms is a combination of, on one side, a very desperate labour and input intensive ‘market-oriented family farming’ [5], which mainly continues due to the enormous level of self-exploitation; and, on the other side, the further ‘rationalisation’ of large-scale ‘agro and food chains’ (contract farming, sophisticated cooling and transport chains, large-scale retail distribution) as we can in formation in Punjab. [6]
On this background, the current ‘re-discovery’ of small scale farming by the institutions of global governance with the help of NGOs, seems either absurd/helpless or cunning. The revival of ‘small peasantry’ has to be seen in the context of the general crisis: rising unemployment, declining wages, volatile food prices and dwindling state budgets. It only exists as a sub-category of the failing existence as wage workers. It is the regime’s hope that people ‘farm their individual way through the crisis’ – that they stay hungry on their piece of land, blaming themselves and nature, instead of relating to the stark contrast of general global potentials of wealth production and mass misery. Small market peasants tend to kill themselves, while hungry proletarians tend to cause riot – this fact is very much in front of our and their eyes.
We have to see that the contradiction of ‘capitalist productivity’ is even more pronounced in the urban and urban-industrial area – which is supposed to provide an outlet for the impoverished rural masses. The IT-related services in India might create 20 per cent plus of the total income from exports, but they create 0.01 per cent in employment; all major automobile companies in India announced to step up automation in 2012; CNC-computer controlled stitching machines replace the remains of artisan labour all over India – just to name some symbolic examples.
We see an ever-increasing output of commodities requiring a decreasing amount of labour input, leading to mass underemployment and impoverishment – in the face of potential abundance. This is a rather unsophisticated ABC of ‘capitalist contradictions’ and it might seem abstract; but it is this contradiction as an underlying force, which has recently blown up the regimes in Northern Africa and is currently raging in Europe. The unemployed in Egypt or Tunisia had neither possibility to migrate ‘outwards’ nor to ‘fall-back’ into a ‘rural economy. It is on this background of the ‘historical character of poverty’ that we have to debate both the current attempts to revive ‘small scale farming’ and MGNREGS. [7]
*** (Re-)Productive Functions of MGNREGS
Rather than as a jumping board into a better existence as small scale market producer, MGNREGS can be seen as a social valve situated between the market pressure on the agricultural and wider rural sector, which ruins and expels increasing numbers of small peasants and artisans (proletarianisation), and the ‘labour expelling’ pressure of profit production resting on the rural and urban labour market (surplus population). It is a security valve in the sense that it is meant to control proletarian migration and is strategically placed in areas of rural unrest. But it is more than a mere valve, it acts at the same time as a pressure chamber which intends to keep up the pressure on rural and urban labour markets, by making clear that ‘surplus labour’ has to ‘toil hard for a minimal existence’ even in times of overproduction.
In this sense it is not an ‘evil scheme’, but an expression of the absurdity of capitalist productivity and wage labour: a huge modern apparatus, comprising all state levels, supranational developmental institutions, NGOs and other civil society organisations; an apparatus, which uses the most modern technologies (e-government, IT-integrated pay rolls and bio-metric ID-cards) of the current ‘productive forces’, in order to make poor women and men breaking rocks, using – by decree! – the most primitive tools, which have been around for thousands of years. And this absurd fact itself is portrayed as ‘welfare’ as ‘grassroots empowerment’, as a chance for ‘community based democracy’ and as a potential starting point for ‘building an existence’ as peasant or artisan. Back to start.
MGNREGS has a ‘productive function’, the creation of so-called ‘assets’ (rural infrastructure), but this aspect is not in the centre of MGNREGS. The scheme first of all is a scheme of social management. The productive element itself, the actual constructed infrastructure, has also the function of re-imposing divisional lines within the rural class relations. We see following general functions of the scheme:
* Reproduction of Labour Force
* Reproduction of Rural Class Divisions
* Regulation of General Wage Levels
* Regulation of Migration
* Integration of Proletarians as Individual ‘Citizens’
* Internal Re-figuration of the Global and Local State
* Invigorating the Dialog between Rural Proletariat and State
* Reproduction of Labour Force
First of all the existence of the MGNREGS is a proof of the demise of subsistence farming and the level of proletarianisation in rural India. Around 40 per cent of the rural population is landless, around 65 per cent of the income of ‘small peasant” household depend on ‘non-agricultural’ sources (wage work). Under the current condition of underemployment and food price inflation millions are facing starvation.
In the past masses of people actually starved to death in India and they still do in other areas of the world, despite the ability of the ruling elite to prevent this. The major difference between past and present is neither the intrusion of humanism into the minds of the ruling class nor the ‘achievement’ of a ‘right to work’ or ‘right to food’ etc., but that rural India is obviously less isolated from the systemic centres: family members of rural poor work in urban areas, there is a fair amount of rural industrial investment, there are means of communication and transport. Millions of desperate people cannot be just ‘locked away’ in the countryside. The ‘surplus population’ is intertwined with the productive working class, it does not exist in isolation. Last, but not least, the last wave of mass starvation in the 1960s was followed by the emergence of armed insurrection (Naxalites), driven by an alliance of rural poverty and urban class politics.
‘Counter-insurgency’ is not just an abstract or potential aspect of MGNREGS. Politicians don’t get tired of emphasising that the scheme is a direct answer to the ‘biggest internal threat’ – the Maoist uprising in the so-called red corridor, stretching from West-Bengal to Maharashtra. The scheme is over-proportionally located in Jharkhand, Chhattisgarh, Orissa – the main areas of rural unrest. The proto-state Maoist guerillas or parties relate differently to MGNREGS and similar state-run schemes, depending on the area of operation. Whereas in areas such as Telangana the Maoists were one of the few institutions which actually enforced central state programs against the local state representatives, in other areas, where their alliance with the ‘local bourgeoisie’ (construction contractors etc.) was more developed, they opposed the program, justifying their opposition by stating ‘military’ or even more obscure reasons. [8]
To summarise, the fact that starvation exists today is due to the increase of wage/market dependency at a time of over-accumulation related underemployment; the fact that the state sees itself obliged to save the poor from starving is due to the fact that poverty exists very closely linked to the centres of accumulation. But the state does not just want to prevent the poor from starving, the state wants to reproduce the poor as wage labourers and want to reproduce the general conditions of wage labour. Therefore the state does not just ‘pay for the poor’, the poor are supposed to work hard for their minimum wages. Small peasants who barely make ends meet by market farming have to be encouraged to continue to do so by demonstrating that if they join the proletarianised poor, they have to beg to be allowed to break rocks in the heat. Similarly, the rural labourer, who travels from harvest to harvest, working for low wages, has to be shown that the basic principle of capitalism is still based on the compulsion to sell one’s labour power – even if this labour power is as over-abundant as most other commodities.
Obviously, the general contradiction of wage labour does not stop at the door of a ‘state run’ work-scheme – as it didn’t stop at the border of ‘state socialist/capitalist’ regimes either. The fact that workers are surely forced to sell their labour power does not automatically mean that they are then happy to work hard for their meagre income. Subsequently, most state governments in India have shifted the MGNREGS wages to a piece rate system, which is supposed to enforce the desired work discipline – a measure which was also very well known amongst the ‘managing comrades’ of the ‘real socialism’. In Rajasthan, the state with one of the highest degree of implementation and ‘social audit’ (control through NGOs), the government introduced piece rate wage as early as February 2006. The contradiction subsequently changes its form: the struggle now evolves around the question of the definition of rates. [9] Rates have to be defined for different type of soil, tools, workers – and ‘objectiveness’ becomes very blurry, e.g. the official standard rate for excavation in soft soil for 1 cubic metre with a lead of 50 m and a lift of 2 m was 0.2 person days in Tamil Nadu and 0.75 person days in Andhra Pradesh.
If the whole scheme is an expression of absurdity, of the imposition of “primitive labour intensive wage work” in times of underemployment and over-productivity, then the absurdity continues through the ‘burocratization’ of the scheme: in order to administer wage payments, to engage in ever more minute mechanisms of ‘piece rate settings’ and supervision, large amounts of ‘burocratic’ labour emerges in order to rescue the wage form, a whole pyramid of admin-workers, time-keepers, NGO-controlers piles up on the shoulders of the shovel-swinging proletarian woman. On the lowest panchayat state level alone, 10 per cent of the ‘costs’ of MGNREGS go into administration. Here we can see that ‘burocratization’ is not primarily a result of mismanagement or ‘development of a self-interest of the burocrats’, but of ‘social management of wage labour’ itself. If you want to get an impression of this ‘pyramid of labour’, check out this government document on MGNREGS management: gwn48_nrega.
* Reproduction of Rural Class Divisions
The reproduction as reproduction of labour force includes the reproduction of the relation to other classes in the rural areas. Here we focus less on the question of ‘profiteers’ of MGNREGS in from of middlemen, e.g. local politicians or construction contractors, who, in many cases, are one and the same. We refer to the fact that ‘asset creation’ – the construction of roads or irrigation facilities – is more beneficial to the ‘landed’ than to the ‘landless’, the roads are more valuable to the local traders, than to the poor who walk on them.
We can see that, consciously intended by the regime or not, MGNREGS will confirm, if not fortify, the class distinction between those who already have’ assets’, and those who don’t. The small traders and small peasantry, who themselves are under huge systemic pressure (Second Green Revolution, concentration process in local and global retail) see that the state let’s the poor work and create infrastructure which has a at least short-term positive impact on their existence. We can assume that the state is not unaware of this dimension of ‘pleasing the middle-strata’ by making the poor work. This is confirmed by a recent change in the legislation, which now allows MGNREGS work to be performed on private land directly, in particular on cash-crop (horticulture etc.) of small peasants (general section). In other cases the MGNREGS work directly benefits the large-scale capitalist farmers.
Let’s look at the example of the Kalchini Tea Garden, West Bengal. Under the scheme for revival of closed tea garden, MGNREGS jobs were issued to all workers in the closed gardens in late 2010. The work included land development, drainage, irrigation channel, connectivity. From 13 December 2010 to 31 March 2011, all 2003 permanent workers of were put to work under the MGNREGS within the confines of the garden, to construct drainage systems. Workers at the various sites have been paid daily wages ranging between Rs. 30 and 50 on an average – the base wage as tea garden workers had been 65 Rs a day. (source: http://www.radicalsocialist.in)
* Regulation of General Wage Levels
The wage-levels of a state-run employment scheme, which comprises nearly 250 million rural households, will have some kind of impact on the general wage levels, even if it is just in a rather symbolic way of an ‘approximating/regulating guideline’. Advocates of the scheme claim that “As a result of NREGA, market wages increased everywhere as employers had to raise labor rates to keep up with NREGA wages”.
(http://eprints.soas.ac.uk/7832/1/Nayak_womenworkersinindia.pdf)
This claim seems to be confirmed by the complaint of farmers in areas of migrant labour dependent harvests, that due to MGNREGS fewer seasonal migrants make the trip to work in the harvest and that therefore a seasonal shortage of labour arises. The actual numbers (actual total amount of days allocated per year, actual wage levels etc.) question that MGNREGS practically push up wages: in most areas the days allocated will only supplement the ever decreasing days of paid labour people can find during harvest time due to increase of mechanisation or other ‘labour-saving’ mechanisms. On average male rural wage workers find between 100 and 150 days of paid work in the rural areas, which includes seasonal migration – with decreasing tendency. In this sense MGNREGS is rather a supplement. MGNREGS wages may lie above the payment small local peasants pay their agricultural labourers, but the official MGNREGS guideline also states that the work in the scheme is not supposed to clash with harvest and other labour intensive agricultural seasons. Many local studies revealed that MGNREGS jobs are more the bottom-line, if there is actually no other monetary income available:
“Initiated in Raichur in April 2006, the Mahatma Gandhi National Rural Employment Guarantee Scheme (NREGS) was intended to provide each household with 100 days of employment (…). Eleven group interviews and surveys of 81 households in six local villages in 2008 and 2010 revealed that each household had received on average slightly less than four days work per annum. Payments were routinely delayed for up to three months (surpassing delays in the payment of agricultural wages), and were often below the stipulated rate. In addition, NREGS work was routinely more intensive and for longer hours than was the norm for casual agricultural labour.” (Pattenden: Migrating Between Rural Raichur and Boomtown Bangalore)
The debate about the wage level of MGNREGS reflect the attempt of the state to establish a ‘dynamic’ minimum wage to a) understand minimum reproduction levels and varies sources of income of the rural poor; b) negotiate different wage levels paid by small and large peasants, also regulating the demise of small peasantry; c) establish wages in relation to different regions in India d) attempt to regulate labour migration. If the current ‘census’ is an attempt to establish a political-sociological overview of the vast proletarian masses in India, then the wage negotiations around MGNREGS can be seen as an attempt to establish an ‘economic’ census of proletarian rural India today.
Here the ‘central state’ acts as the ‘ideal general capitalist’ and finds itself in legal conflict with federal state governments and farmers’ lobbies. Currently the triangle of high-courts, federal and central state has to figure out whether a) there can be a difference between ‘centrally fixed minimum MGNREGS wage’ and ‘regional minimum wage fixed by the individual federal states’; and b) if formally there cannot be a difference, who would have to pay for the consequent regional increase of MGNREGS wages. So far the centre pays MGNREGS wages and regional states would have to prop up these wages if there minimum wages are higher – the limit here being also the considerable indebtedness of the federal states. The legal back-and-forth around this question has to be seen a) as a state-internal argument around the question of control over general and regional economic planning and b) as an expression of the increase of uneven development within India itself.
* Regulation of Migration
“One of the significant objectives of the NREGA is to arrest out-migration of unskilled, landless labour force from the rural areas to urban areas,” Mihir Shah, member of the governmental planning commission. “Where durable assets are created, water conservation happens, agriculture productivity is raised and all this is dovetailed with micro-finance, then out-migration from the area is reduced and people go back to farming or other livelihood created by NREGS.” As we have seen above, the ‘developmental’ capacity of MGNREGS, the possibility to inverse the trends of market farming and to create assets for a new layer of successful market participants, have to be put into question – what remains is the regime’s aim to regulate migration.
Despite relative early emergence of capitalist relations, the rural-urban migration in India happened at much slower pace than in other countries of the global south, even during the first decades after the end of colonial rule. Unlike in China there is no formal restriction of movement as such. Slow pace of rural-urban migration was rather due to the particular integration of the ‘village economy’, which also included forms of unfree labour (debt bondage) intertwined with caste-hierarchies, which prevailed to a significant degree until the 1970s and still persist.
Additionally, rural-urban migration had been curbed by the question of ‘land’: the landless often lacked resources to engage in long-term and long-distance migration and those who still owned land saw this as both reason and viable option not to leave for good. Throughout the 1970s the combination of struggle against the old village hierarchies and the further introduction of ‘Green Revolution’ technologies in agriculture, which shortened the need for hired labour, ‘casualised’ the conditions on the countryside. [10]
On this background of an ‘untied labour force’, we can see that cheaper means of transport and communication lead to an accelerated migration – to a point where due to ‘lack of absorption’ in the urban areas it threatens to undermine social stability. The ‘political’ (registered citizenship, fortification of village administration) and ‘economical’ (wage levels) aspects of MGNREGS have to be seen on this background to ‘re-tie’ the mobility of labour to the current needs and limitations of the regime. This does not mean that the aim is to ‘make people stay’ on the countryside, but to discourage permanent urban settlement and to foster – or at least allow – the continuation of the ‘migrating status’. The ‘migrant status’ of labour forms the backbone of most industrial and agricultural centres in India.
* Integration of Proletarians as Individual ‘Citizens’
Reproduction of a modern proletariat is not merely a reproduction of their labour force and their class position, it also entails the reproduction as a citizen – as an individual with a legal or illegal relationship with the political body of class relations, with the state. It is therefore not surprising that in India the world largest employment scheme MGNREGS is paralleled by and intertwined with the world largest census and biometric data-collection through introduction of the ‘unique identity scheme’ (UID), the issuing of a modern biometric ID-card.
The Census and the UID Scheme [11]
In January 2012 around 200 million people have been registered in the UID scheme. There has been a lot of debate about the political content of both current census and introduction of the ‘unique identity scheme’ (UID). The justification for gathering this data and its electronic combination in a database is that in future, the availability of this data for all kind of state (welfare) institutions (vaccination, health care, food aid, social benefits etc.) will deliver ‘better services’ and prevent corruption – ‘corruption’ in the sense of the state also means any ‘illegal’ appropriations by the working class. The UID scheme combines work by central and state governments and private companies which got sub-contracted to undertake the biometric-datacollection, amongst others Accenture and L-1 Identity Solutions (USA), Morpho (France) and Wipro (India). Wipro is paid 26 Rs by the state for each registration, the registration workers are supposed to register 40 to 50 people a day. The state allocated 614 million USD for the first five years of the scheme ending 2012, the budget for the next phase has more than doubled.
One of the criticism of the current census was that for the first tie since independence the questions of caste belonging was re-incorporated in the questions asked, in addition to general questions of the household income, seize, means of reproduction of the rural proletariat. In times of crisis, where ‘identity (caste) politics’ are less a means of upward mobility, but of ‘divide and rule’, such a formal and socially integrated official registration of caste is a potentially fatal information in the hands of our enemy. Whoever maintains the idea that the database is in ‘neutral democratic’ hands should remember the last time when the state ‘systematically’ dealt with rural and urban poverty after the major global crisis of 1973: despite their brutal consequences, the lists for (enforced) sterilisation programs, slum demolition/relocations and arrests during the Emergency (1975) seem scarily sketchy compared to the current integrated data-management of the state.
The link between ‘formalised citizenship’ and MGNREGS is direct in the sense that in order to enrol in MGNREGS you need to be registered in your village, you need an ID in order to get a job card or to open bank accounts. In general this combination of MGNREGS and ID-politics does not only allow the state more insight into the reproduction of the rural proletariat and increases the economic and political dependency of the ‘poor’, it also facilitates their further monetary/market integration, e.g. through shift from material entitlements (subsidised food, gas etc.) to cash transfers thanks to bank accounts. MGNREGS is the capitalist utopia of combining an ultra-light IT-based administration of proletarians as ‘transparent’ and participating citizens with their most labour intensive exploitation. [12]
* Internal Re-figuration of the Global and Local State
Obviously, the actual strength and stability of a class society is not measured in the degree of state control over individual proletarians, but rather whether it does not need to make use of too much force and control mechanisms in order to reproduce itself. In this sense the degree of ‘participation’ of wider layers of society (and working class) in the management of social labour (exploitation) can be seen as a much more decisive indicator for the condition of a class society. In this sense MGNREGS has another (re-)productive function, which is a) re-shaping the inter-state relations and b) invigorating the ideology and practice of ‘democratic participation’, meaning, strengthening the ties between state and society. First of all we can see how around MGNREGS – around the management of largely female rural labour in the poorest areas of the globe – it reveals itself what ‘the state’ is today; state not in a formal sense of ‘Indian public administration’, but ‘state’ in the sense of political coordinator and regulator of proletarian reproduction.
The Pyramid of the MGNREGS State Management
Who participates in shaping and managing the scheme? We clearly see that it starts on a supra-national level of ‘global governance’, the advisory function of developmental institutions of UN and World Bank and of the large global NGOs is direct, the financial involvement mediated. On the central and federal state level there exists a close cooperation between the governmental institutions, ‘civil society’ and academic apparatus in the development of the scheme.
Abstracted from the wider social context of the scheme, abstracted from the social pressure of thousands of suicides in the cotton zones of India and the dire prospect of millions of urban slum dwellings, MGNREGS becomes a playfield of ideologies and institutions who want to use the ‘human capital’ of (female) labour in order to save the planet or empower women (significant involvement of eco and women NGOs), or re-vive the Indian village community with their Gandhian thoughts. These organisations can only play out their well-intended ideas if they actually take part in management of the scheme and directly or not, in the financial resources attached to it. In this sense, from a systematic and not moralistic point of view, we can call this the actually most blatant form of ‘corruption’: a large amount of fairly cushy jobs, research careers etc. on the back of the rural proletariat. To get an impression: gwn48_manrega
From a systemic point of view, the productive function of this ‘managing strata’ is to deliver an ideological and practical framework for the ‘participation’ of the rural poor in the scheme – or at least to foster the participation of an emerging new layer of representatives on village level. Crucially, this ‘higher strata of stata/NGO management’ emphasises that for political reasons MGNREGS should based on and fortify the institution of the ‘gram panchayat’, the village council – in cooperation with ‘social audits’ of civil society organisations.
The Role of the Panchayat (Village Council)…
The focus of the central state machinery on these ‘village councils’ is not new. In India there are currently around 230,000 elected village councils. During colonial times these village councils’ relation with the central state was mainly characterised by tax transfer, not by direct political control – in many areas this did not change fundamentally during the first decades after ‘independence’. After the waves of rural turmoil of the 1970s the central state launched a campaign to intensify the central state’s control over the rural sphere by strengthening the ‘gram panchayat raj’. This was officially justified by saying that the ‘democratic panchayat’ would break the old patriarchal caste rule, which the ‘old panchayat’ was said to represent. Actually this old ‘caste rule’ had been put into question by struggle and changing rural economy previously – the state’s campaign to ‘democratize’ the village sphere was in this regard more a reaction to this turmoil and an attempt to re-integrate discontent into state politics.
Laws were passed which guaranteed women and members of lower castes half the seats in the council, certain elements of state decision were ‘handed over’ to the panchayat level. Many people, and many leftist, saw this as a move towards decentralisation and a return to ‘old (Gandhian) local egalitarianism’, when actually the ‘decentralisation went intertwined with an actual centralisation of control over village politics and economy (large agro-business, fiscal transfers etc.) and the integration into state machinery of a new layer of ‘representatives’ of the ‘lower castes’. It’s not by chance that this ‘(de)centralisation’ intensified after the 1990 crisis and subsequent ‘neoliberal reforms’.
…in the Management of Crisis
MGNREGS can be seen as a kind of ‘economic’ complement to this ‘political’ attempt to ‘grass-root’ state power. We can see the same combination of centralisation and decentralisation taking place. Today, the official justification and progressive gloss is not to break the stronghold of the upper-caste rule, but rather the rule of the ‘local corruption’, the alliance of local politicians, contractors, larger landholders. The management of MGNREGS is handed over to the panchayat – while the actual framework of the scheme, it’s narrow confinements, are set by the central state and the general conditions of capitalist crisis. This ‘handing down’ of the responsibility to self-manage the effects of crisis to ‘the local community’ has its counterparts all over the globe, e.g. in the ideology of the Big Society in the UK. [13]
Over the last years the central Indian state has cut money for both general rural/agricultural development schemes and public food distribution systems. MGNREGS can be seen as a partly substitute for these investments: the central state pays minimum wages for work-scheme, the gram panchayat is forced to use ‘it’s local labour’ to accomplish necessary ‘infrastructural development’ instead of relying on central state funding. The crisis should be managed on low-investment levels, in a combination of labour intensity, ‘voluntary sector activities’ and other forms of self-regulation and initiatives. Conflicts, which emerge due to general global contradictions, are supposed to be solved within the formal and financial frame-work of the ‘local community’.
* Invigorating the Dialog between Rural Proletariat and State
We have many examples of how MGNREGS is ‘corrupted’ by the alliance of local power (political caste, land-owners, contractors) in order to fortify their position to the disadvantage of the rural poor. [14] This gives reason and credibility to the struggle for the ‘proper implementation’ of MGNREGS. While the struggle against the local elite is obviously necessary, the problem arising is two-fold: a) focussing on the ‘legal framework’ of MGNREGS will not manage to understand the ‘systemic’ implication of central state in local power, it will burn itself out in the attempt of appealing to ‘central law’ against ‘local rule’, thereby creating unnecessary illusions within the rural proletariat; b) it will, wanted or not, provide MGNREGS with a ‘progressive’ aura, which objectively, as a hard labour scheme in late capitalism, it does not have.
To a certain extend the prescribed framework of MGNREGS encourages ‘disputes’ on the local state level, in order to re-balance the relation between general reproduction of the rural proletariat, general state crisis regime and interests of the local bourgeoisie. The state is aware that a ‘corrupt’ local elite would be overwhelmed with the task to socially manage the enormous pressures of rural crisis. In this sense MGNREGS and legal changes such as the ‘Right to Information Act’ can be seen as a kind of ‘cultural revolution’ – a re-structuring from above which takes the form of ‘controlled dispute’.
“Typically conducted in partnership with a local “people’s organisation”, a social audit involves the systematic review of documents related to NREGA works in a given locality. Files are scoured by teams of volunteer-auditors trained and overseen by facilitators with experience of similar audits elsewhere. Forms containing administrative clearances and technical sanctions are reviewed for procedural lapses. Financial records (muster rolls, job cards, material vouchers, expense ledgers, bank statements) are examined for inconsistencies. The audits culminate in public meetings where local people (particularly NREGA workers) are invited to comment orally on specific issues raised by the audit teams. Testimonies are based on their direct experience as workers or supervisors on NREGA projects or suppliers to particular worksites. Discrepancies between government records and oral accounts are scrutinised. Officials are asked to offer explanations for apparent violations of procedural norms. These meetings are held either as an extension to or, where local authorities are uncooperative, in lieu of – the gram sabha [village council assembly].” (EPW, March 2012)
The legally set boundaries of this ‘arena of struggle’ are able to contain most of the current ‘MGNREGS activism’. Following some quotations, which reflect the attitude of ‘critical participation’ on the left.
“I believe the primary stakeholder of NREGA has to be a social movement which organizes the end beneficiary (rural communities) around their right to work. If the political will is assumed to stay, we should start treating the government resources like venture capital for socio-political entrepreneurship by all the strategic stakeholders of NREGS.”
(http://nrega.nic.in/circular/So_Audit_I.pdf)
“Turning the mai-baap State on its head, holding it accountable to its people, rights-based legislations have the ability to politicize the population for a truly functional democracy. Already NREGA workers across the country are registering trade unions to mobilize and fight for their rights. There is immense potential in these unions – traditionally mobilization has taken place along divisive (and dead-end) issues like caste and religion – for political gain of vested interests but not politicization of the individual.”
(Ruchi Gupta: http://www.hardnewsmedia.com/2011/01/3799)
“It is important that programs meant for the disadvantaged, the marginalized, the poor be monitored by Civil Society Organisations (CSO). Monitoring Reports with advocacy for change can generate pressure for corrective measures. But this depends on the initiative of the CSO. CSOs with required resources and commitment can make NREGA a great success.”
(http://www.ohchr.org/documents/publications/goodgovernance.pdf)
“The State provides employment, and by virtue of its scale effectively raises wage rates in the labor market. Finally through built-in transparency and penal provisions, the government is held accountable for both performance (timely employment, payment) and accounting (open muster rolls, social audit). This form of governance – large role of State, redistributive stance, grassroots political activism for state accountability – is firmly on the far left of the ideological divide.”
“NREGA In West Bengal: How To Ruin A Working Class Programme
On 2nd February 2006, the National Rural Employment Guarantee Act (NREGA) finally became operational. It was the fruit of three decades of struggle by unions, political parties and people’s organisations all over the country. What actually underlies the non-performance of West Bengal in NREGA is the class character of the Government that we have. The Left Front may call itself a working class government; it has however become a government of the rich and powerful. Radicalization of NREGA is one of those many cumbersome mechanisms of extra-parliamentary democratic institutions in which left must intervene and play an active role.”
(http://khetmajoorsamity.blogspot.com)
*** Current Struggles within MGNREGS and Preliminary Conclusions for the Communist Movement
Most official struggles within MGNREGS we hear about are waged by trade unions [15] for the proper implementation of MGNREGS. A ‘trade union’ view imposes itself rather automatically, given the extreme ‘rights violations’ within the scheme: corruption through middle-men or faked job cards, non-implementation of the scheme or only little amount of days, wages not paid fully and delayed, wages based on piece rate which does not allow to earn minimum wage, non-payment of unemployment allowance in case scheme is delayed, work not within 5 km radius, no facilities (creche, toilets), not work according to physical abilities, sidelining of community and grassroot organisations when it comes to decision making etc.
There are large amounts of small scale actions, in particular about non-payment or low payment of wages.
In early 2011, in Keshabpur village in West Bengal workers started a dharna in front of the Panchayat office after having not been paid wages for 24 days of work for over two months. After staying there overnight, on the next day, they were informed that wages would be paid immediately – at the rate of Rs.22 per day for 8 hours of hard labour. When the workers refused to take such low payment, a revision of the piece rate took place – they were offered Rs.48 per day. The workers have still refused to take these low wages and have asked for a third count – in their presence.
In July 2011, 100 workers from Sewapuri block of Varanasi district in Uttar Pradesh got unemployment allowance under NREGA after a two year long struggle. After several protest demonstrations, the government was forced to order an enquiry into the matter, and finally gave orders for the payment of unemployment allowance to 107 workers. The workers who received an amount of approx Rs. 1400 individually were paid after they declared they would sit on an indefinite dharna.
On 22nd of September 2011, three members of Uttarakhand MNREGS Contract Employees Union have climbed on top of a telecommunication tower in Dehradun. One of them claimed that the junior engineer, computer operators and accountants are being provided jobs on contract through NGOs under MNREGS, but that these employees are not being paid whatever promised by the NGO officials. They demanded that junior engineer, accountants and computer operators should be considered as employee of DRDA (District Rural Development Agency), as public sector workers.
In December 2011, after 47 days of a protest sit-in in Jaipur by workers employed under MGNREGS the Rajasthan state government acceded to the worker’s demands on five issues, principal amongst which was payment of state minimum wages and inflation compensation.
Mass actions organised by established institutions tend to have rather symbolic character and address mainly the upper-level of the political class.
In February 2011, MGNREGA workers in West Bengal protested to draw attention to non-implementation issues. The protests held were part of a national programme organised by the New Trade Union Initiative, a national centre of independent trade unions. Nearly 150 members of the PBKMS and Shramajivi Mahila Samity (SMS) blocked the offices of the Minister of Panchayat and Rural Development and demanded better implementation of the programme.
On 12th of June 2011, several thousand NREGA workers crossed the borders of Punjab to demand work in the neighbouring state Haryana. They thereby protested against the lower MGNREGS wages in Punjab and wanted to show that there is not enough work under the scheme in Punjab.
What means do MGNREGS workers have in order to enforce their demand, apart from pressurising the political class to ‘stick to their own laws’? From general experience we can derive that it is not the ‘appeal to the law’ or the astute work of lawyers which ‘make the rulers stick to their rules’, but actual pressure and the threat that unrest in whatever form might spread from clearly defined boundaries of a welfare scheme into the wider sphere of rural production.
We can assume that ‘going on strike’ in classical terms will be more difficult in a work scheme, where ‘paid work’ is presented as a welfare benefit – though we should not exclude the possibility that under specific conditions local and wider ruling class might actually depend on MGNREGS work-force. A concrete analysis of the actual work performed under MGNREGS is a pre-condition for finding ways and means to fight back. Of equal significance is the analysis how workers in a MGNREGS scheme have other seasonal rural or urban labour experiences in common and whether struggle within MGNREGS can be based on this wider experience. We have to see whether proletarians can make use of the fact that during other times of the year their collective work-force is needed in harvests, brick-kilns, constructions sides or factories. We have to analyse whether the pressure which they are able to exert there can somehow be extended into the situation within MGNREGS – where larger numbers of people tend to work together on the same sites.
This is not completely abstract, given that workers act this way on an individual and perhaps more passive level. They quit MGNREGS jobs as soon as they find other work which is slightly higher paid. The fact that in most regions the regime was forced to introduce piece-rate systems also indicates at the fact that workers are not merely grateful receivers of benefits, but subjects, who are able to withhold their labour power.
Therefore the main problem with the ‘official trade union’ struggle is not so much that they ‘focus on the law’ and come up with mainly symbolic activities, but that they confine the arena of struggle very formally to the scheme itself, where the ability for workers to develop their full potential of collectivity and power is necessarily limited. This is also partly due to the fact that for the trade unions, to organise ‘MGNREGS workers as MGNREGS workers’ allows them to build up a mass base of rather dependent members in a short time – similar to many NGO’s within the scheme these representative institutions develop their own interest in keeping things running and keep the workers in the position they are in. Part of this separate logic of organisation is the propagandistic presentation of the scheme as ‘an achievement’ of struggles – which mystifies its actual content as part of the crisis regime. These organisations will not analyse and turn into a weapon the total experience and practice of the rural proletarians engaged in MGNREGS – from their experience of seasonal migration to acts of individual and collective sabotage and absenteeism.
To sum up, a communist position towards MGNREGS would mean to first of all call MGNREGS by its name, instead of disguising it as an achievement for the proletariat. It would mean to clearly abstain from any participation in designing or promoting the scheme or co-management. It would secondly mean to support practically any struggle for higher wages and less work within the scheme, by all means necessary, without restricting it to the symbolic or legal terrain and without developing a separate organisational interest from the workers. It would finally mean to analyse the organisational potential of workers’ actual movement between seasonal rural and urban labour, the experience of migration and the work within MGNREGS. Here the usual interpretation of ‘state run work-schemes’ prevailing on the left, which either demonise them as a ‘return to unfree forms of labour’ (prison economy) or mystify them as ‘a chance for non-market form of labour’, have to be overcome – through analytical and practical reference to the dimension of the ‘collective worker’.
Footnotes
[1]
If you happen to have the means and time you can watch the following documentary on the scheme, supported by the development organisation of the UN and the Indian Ministry for Rural Development, which provides a propagandistic, but fairly comprehensive overview.
http://www.cultureunplugged.com/documentary/watch-online/play/7585/NREGA-Reforms—Building-Rural-India
[2]
Some contributions to the debate about work-schemes in the UK.
http://libcom.org/blog/new-social-workhouse-16022012
http://thethirdestate.net/2012/02/workfare-in-context/
[3]
Exception here is the Punjab, the most advanced agricultural region, where the number and proportion of small-holdings has been declining over time. During the last decade, 1,28,000 small-holders leased out their land to larger holders and operators and opted out of farming. In addition, 72,000 sold their land to larger farmers. Of these 2,00,000 smallholders, about 22 per cent joined the ranks of agricultural or other labourers.
[4]
According to a NSS survey for the year 2003-04 , the top 5.2 per cent of rural households own 42.8 per cent of agricultural land, and the top 9.5 per cent own 56.6 per cent.
[5]
Agriculture, then, seems to be particularly ‘productive’ only when it is performed as a family enterprise and/or by employing migrant seasonal workers. Actually they are highly specialised – and only nominally ‘self-employed’ – as independent producers in the agro-processing industry. They form part of a very finely calibrated division of labour; the work methods they apply are prescribed by the processing industry, but they have to bear the entrepreneurial risk themselves.
http://www.wildcat-www.de/en/wildcat/89/e_w89_nahrungsmittel.html
[6]
Punjab has been corporatising its farming sector since the 1990s. Field Fresh – an equal partnership venture between Bharti Enterprises and Rothschild – has leased 4,000 acres of land and employs the former owner-cultivators as farm managers. Fresh fruits and vegetables from Field Fresh are exported to the European Union, eastern Europe, Asia. The company claims that the livelihoods of its lessors have improved compared to when they were owner-cultivators as it pays a minimum wage of Rs 80 a day.
Another example are the ‘Punjab potato kings’, who include three families who cultivate seed potato on 12,000 acres of leased land and have cold storage facilities that can store their entire produce. The largest of these three potato kings cultivates 5,500 acres and employs 5,000 labourers during peak periods, mostly migrant workers from Bihar who live in makeshift tents next to the potato fields. They are recruited through “contractors” and supervised by mangers specially hired for the purpose (Witsoe 2006).
More recently, the state government announced a subsidy for farmers for the purchase of transplantation machines. Based on recommendations of the farmers’ commission, it extended a subsidy of Rs 75,000 for each transplantation machine. With the help of these machines, about 5 acres can be planted in a day compared to five persons taking a day to plant one acre. (Singh)
[7]
As an example of a ‘developmentalist’ view on MGNREGS:
“What we need is a livelihood focus in NREGA and creation of livelihood opportunities in the local economy using NREGA funds. NREGA projects should not merely generate wages but should build livelihood assets for the community as well as the individual families that will make them self reliant over the short to medium term rather than be dependent on State doles year after year.”
http://sapplpp.org/openforum/developing-block-level-plans-for-livelihood-promotion-through-nrega-examples-advice
[8]
One of the reasons given for why the Maoists oppose MGNREGS is that further construction of roads will facilitate the mobility of the Indian army in the area. In case of the killing of Niyamat Ansari, a MGNREGS activist the statemen issued by South Latehar Sub-zonal Committee of CPI (Maoist) not only claims the responsibility of the murder but also provides a motive for the act. According to the statement, Niyamat was killed because he did not report for a “people’s trial” conducted by CPI (Maoist) and turned police informer. There is actually more evidence for the case that local construction contractors close to the Maoists felt bothered by Ansari’s activities.
[9]
See following example from a MGNREGS report:
Deepening of village pond (NREGA)
in Thandrampattu
This work was sanctioned for an amount of Rs 50,000. the work involved excavation of earth. It was estimated that a total quantity of 1657 cubic metres of earth has to be excavated @Rs 25 per cubic metre. Including some other minor items the total estimate for the work was worked out at Rs 50,000 based on PWD schedule of rate. The work started on 17-2-06. The first measurement of work was carried out on 27-2-06. At that time it was recorded that 207 cubic metres of excavation has been completed. Accordingly, using the PWD schedule of rates the value of work turned out was arrived at Rs. 6693. As per the muster rolls 162 person days were required to achieve this work turn out. 90 per cent of the workers were women. Thus the payment per person per day worked out as 6693/162=Rs 41.31 per day.
[10]
“Why did the trickle of migration from these villages become a stream in the early 2000s? The reasons are to be found in two marked changes in the forces and relations of production – the casualisation of labour and the partial mechanisation of production. The casualisation of labour has taken two predominant forms: growing levels of individualised daily casual employment and group-based piece-rate work during times of peak labour demand. These changes in the relations of production have been accelerated by the partial mechanisation of agricultural production, e.g. the adoption of labour-saving rice harvesting machinery between 2002 and 2004.”
(Pattenden: Global Labour Journal 3)
[11]
There exists a lot of technological fetishism concerning UID, seen either as a purely neutral census measure or a technological fix for poverty:
“Poverty has many causes, and no simple cure. But one massive problem in India is that few poor people can prove who they are. Their lack of an identity excludes them from the modern economy. They cannot open bank accounts, and no one would be so foolish as to lend them money. If poor Indians each had an identity number tied to unique biometric markers, it would be much harder for the powerful to rob them.”
“Once recipients have bank accounts, India can follow the likes of Brazil and replace easily stolen benefits in kind, such as rations of cheap food and fuel, with direct cash transfers. Not only do these cut theft, but cash payments also let beneficiaries become mobile-for example so they can leave their state to seek work, while not jeopardising any benefits.”
“Last week Karnataka state claimed that by paying welfare direct to bank accounts it had cut some 2m ghost labourers from a rural public-works project.”
“Microfinance should start to work better, too. It enjoyed a huge boom in recent years, followed by a bust. Many poor people found they could borrow more than they could ever hope to repay by going to several lenders. As a result, some microfinance outfits collapsed. The UID scheme ought to allow for greater control over such small loans.”
(http://www.economist.com/node/21542763)
[12]
The end objective should be ‘Each village maintaining a picture database of job seeking families (or unemployed villagers seeking employment) and the information should be available online creating mirror image of the NREGS implementation process. One of the ways in which the government or the civil society can contribute to further strengthen NREGA is to train Mahila Mandals/SHG Federations/ CBOs/Youths/Individuals/Press etc on how to access these web pages at a local internet café to know about the work that is being proposed and completed in their villages.
IT/state: http://www.nrega.nic.in/netnrega/home.aspx
[13]
Here an example of the discourse:
“The panchayat balance sheets are dominated by grants from the state government and they are the source of funds for the bulk of expenditure on public works in these villages. If there are no clear guidelines on the “hardness” of fiscal budget constraints as they pertain to the flow of funds from higher-level governments to local ones, local governments will have the tendency to spend beyond their means in the expectation that they will be bailed out in times of need. What such “soft” budget constraints also imply is that local governments will slacken their efforts to levy and collect taxes and fees because, in addition to such moves being politically unpopular, they expect that their funding needs will be largely met by flows from higher-level governments.”
http://www.wotr.org/upload/Panchayat_Raj_on_the_Ground.pdf
[14]
A very accurate description of the coalition of local economical and political class:
The wide variety of development schemes launched by the TDP and Congress from the 1990s till today has strongly reinforced local political clientelism and the power of rural leaders, who control and redistribute profits (after taking a substantial percentage). Y.S.Rajasekhara Reddy, the Congress leader from 2004 to 2009, pursued such policies and launched a large number of development schemes related to pension, housing and health. He also pushed ahead with the National Rural Employment Guarantee Act (NREGA). Those are some of the schemes that have deeply reinforced competition and divisions in the village, between political parties as well as within castes. The access to ration cards and other schemes is not a right (as it should be, formally): access is provided through subtle and endless negotiations and manipulations of local micro-hierarchies, from caste to individual levels. To secure access to those programs after months in Hyderabad, migrant labourers have to display their support to the TDP party (who hold power at the village and district level), while henchmen of the party ensure the votes of the caste.
N. Reddy is one such goonda, the grandson of the village’s main moneylender, combining many activities. He is a close associate of the head of the village and the Village Development Officer, mobilises supporters for political meetings, collects migrants’ debts, and is in charge of collecting microcredit group funds at the Cluster level, which his mother directs. Through long-standing docility to the head of the village and a mixture of violence and protection towards the low-castes (Alm 2010), in 2009 he managed not only to become the manager of the shop for subsidized products (petrol, rice, etc.), products which he sells for own profit in the nearby town, but also became a main agent of NREGA. Within NREGA, on average 10 to 15 days of work is carried out per year, in contrast to the 100 days planned and charged. This clearly demonstrates the diversion of money within the scheme and its importance as a source of corruption.
(Migrant Labourers’ Struggles Between Village and Urban Migration Sites: Labour Standards, Rural Development and Politics in South India; David Picherit)
Comments
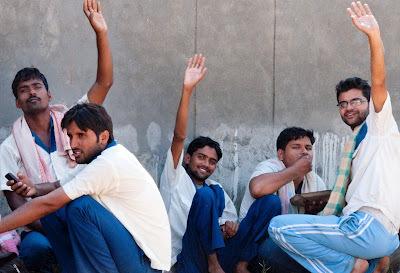
Towards a Workers’ Organisation (Part One)
In this and the following issue of GurgaonWorkersNews we debate the question of ‘workers’ organisations’: how do workers’ bodies formed in the daily struggle relate to ‘political’ coordinations of workers, in continuity with the struggle against the existing social relations?
This debate has to be firmly based on an analysis of a) the actual current workers’ experiences of struggle and the problematic and promising tendencies within; b) the relation between particular struggle and general conditions of the capitalist cycle; c) the changing composition of work-force and the relation of workers to the immediate and social production process – as material basis for self-organisation.
This first part consists of general political theses concerning the question of workers’ organisations and, in relation to this, we present six longer reports on recent struggles in Delhi-Faridabad-Gurgaon industrial areas. The second part will focus on current developments at Maruti Suzuki and its supply chain in relation to the re-composition of workers’ collectivity after the struggle in 2011. On this background we will raise general questions on the relation between workers’ organisations and workers’ inquiry. Please contribute to the debate.
http://www.gurgaonworkersnews.wordpress.com
gurgaon_workers_news@yahoo.co.uk
*** Bullet-Points for Debate on Workers’ Organisation –
The steps towards a workers’ organisation are based on political assumptions – one of them being that the classical distinction in ‘trade union struggle’ and ‘party struggle’, in ‘economical’ and ‘political’ struggle, has become a stumbling block.
*** An Unnecessary Repetition – Struggle at Harsoria Healthcare, Gurgaon –
On 24th of April 2012 workers at Harsoria Healthcare, a manufacturer of cannula and catheters for the medical sector, engaged in a sit-down strike before once more ending up in dead-ends of symbolic and legalistic protest.
*** Lock-Out at Automobile Supplier Senior Flexonics, Manesar –
Workers at multinational Senior Flexonics in Manesar registered a trade union and put forward a demand notice. Subsequently they were locked out from early January till late February 2012.
*** Riots at Orient Craft and Larsen&Tubro Construction Site, Gurgaon –
On 19th of March workers at garment exporter Orient Craft rioted after a work-mate had been attacked by a contractor. On 23rd of March construction workers attacked company property in response to the death of a colleague after a work-accident.
*** Workers’ Sirens at Lakhani Vardan Samuh, Faridabad –
From December 2011 till April 2012 Lakhani workers in Faridabad were engaged in various forms of struggle about delay of wage payments: from direct action on factory grounds to wildcat strikes, to street blockades and demonstrations to governmental institutions.
*** Unrest at Theme Export Garment Factory, Okhla –
Successful direct collective step by garment workers in Okhla on 16th of April about delayed wages, which attracted workers in surrounding factories and workers’ settlements.
*** Revealing Potentials – Struggle at Globe Capacitor, Faridabad –
During April 2012 workers undertook various collectively planned steps to enforce higher wages, which forced management to give concessions. the struggle was influenced workers in the supplying company and by workers in a neighbouring factory.
*** Delhi Calling: Get Involved in Faridabad Majdoor Talmel –
To abolish the global work/war house will take more than informative exercise! If you live in Delhi area, please be welcomed to take part in Faridabad Majdoor Talmel – a workers’ coordination. We distribute around 10,000 copies of Faridabad Majdoor Samachar on ten days each month in various industrial areas around Delhi and try to organise local workers’ meetings.
*** Bullet-Points for Debate on Workers’ Coordinations –
We first present general considerations concerning the question of workers’ organisations. We then turn to the reports on current struggles in Delhi’s industrial area and formulate preliminary conclusions regarding the question of organisation. We finally outline concrete steps towards a workers’ organisation under present conditions.
1) On Workers’ Organisations – General Thoughts
2) On Current Struggles
3) On Concrete Tasks and Steps
1) On Workers’ Organisations – General Thoughts
a) Intro
The proposal for a workers’ organisation is based on political assumptions – one of them being that the classical distinction in ‘trade union struggle’ and ‘party struggle’, in ‘economical’ and ‘political’ struggle, which is still prevalent amongst us, has become a stumbling block. This ‘party/union’-perspective allows ‘tactical’ participation in ‘institutional’ trade union work despite the obvious problematic results for the development of collective workers’ power. The clear shortcomings of ‘institutional’ trade union work can be justified as a problem of the ‘first stage of workers’ struggles’, which will be solved by the party politics waiting in the second stage.
The ‘union/party’-perspective also allows us to abstain from deeper analysis in material conditions and internal tendencies of workers’ struggles which would be necessary in order to explain current limitations. Instead, limitations are ‘explained’ by declaring the struggles as ‘economist’ and lacking ‘political consciousness and leadership’. These are tautological explanations which are meant to give final credit to one’s own ‘external role and position towards workers’ struggle. They are of as little use for the development of workers’ collective power as the general appeals towards workers’ unity. Workers’ unity is not the question of ‘umbrella organisations’, but arises only out of the struggle within the contradictive nature of capitalist production process, which at the same time combines and segments workers. Workers’ have to find forms of organisations which materially undermines the segmentation imposed by the production process – they cannot just step out and ‘generalise externally’.
The following theses won’t say anything new, they are meant to summarise a general position as a background for the debate on current struggles and future tasks – mainly with comrades and friends in Marxist-Leninist organisations, active in the regional industrial areas.
b) Class Composition and Class Movement
The form of social production determines the form of social struggle and the vision of a ‘social alternative’. Although this is generally accepted, most political proposals of ‘how to organise’ and most ‘communist programs’ remain rather unhistoric or attached to the last century. Capitalist social production changes rapidly, the regional centres, dominating industrial sectores and ‘workers figures’ are transformed with each cycle. Within this process ‘the working class’ changes, we have to talk about specific ‘class compositions during specific cycles. The ‘technical class composition’, as the historically dominating form of the social production process, contains the process and potential of ‘political class composition’ – the form of class movement. [1]
By ‘technical composition’ we mean the actual historical form of how workers cooperate within a process of division of labour mediated by machinery and shaped by different levels of development; how the immediate production process relates to the wider social process of (re-)production and forms and levels of consumption; how formal individual skills relate to wider social skills of workers necessary to perform labour; how different categories and sections of workers are brought together and are segmented; how the class conflict is mediated institutionally and culturally.
By ‘political composition’ we mean the process of how ‘working class’ and ‘workers unity’ actually forms out of material conditions and experiences of struggles: the concrete form of organisation of struggle workers develop based on the collective nature of the capitalist production process, overcoming it’s segmenting nature; the concrete demands and wider social critique which springs up from concrete conditions and ‘aspirations of productivity’ – a historically specific relation between living and dead labour; the form of how particular struggles relate to each other and turn into a generalised movement due to the social dimension of production and general conditions within a capitalist cycle; how this generalisation tends to happen through struggles within central industries which can express an advanced stage of conflict between capital and workers; based on this relation between central sectors and wider society, specific forms of ‘economical and political’ organisations (councils, assemblies) of the class movement are formed and can express a specific ‘social alternative’, a historically specific communism.
c) Class Composition and Periodisation
Although historical periodisation contains a certain danger of becoming schematic we can state that, e.g. the cycle of transformation from agricultural labour and small peasantry to urban and industrial work corresponded to formation of ‘communist parties’ as bridge organisations [2], the early stage of skilled industrial manufacturing work gave birth to ‘councilist’ and ‘revolutionary syndicalist’ workers’ organisations, and the period of large-scale ‘Fordist’ industries, which were more integrated into general society brought forth organisational forms of ‘mass workers’, such as general assemblies and wider political coordinations with a quite different ‘communist vision’ from earlier perspectives of ‘self-management’. [3]
In this sense the ‘revolutionary potentials’ of struggles and movements are inscribed within the actual social production process. Communist activities have to relate to the ‘gaps’ between these given material social potentials and the concrete ongoing struggles – last, but not least by referring to the experiences in other regions or of the near past. The challenge obviously lies in the fact that the ‘technical composition’ is in constant change and that a dynamic relation exists between technical and political composition. The overwhelming rapidness and spacial vastness of these changes partly explains the leftist retreat into ‘fixed organisational models’, from ‘parties’ to ‘syndicalism’. What we then have to propose to the living working class today is dead weight of past times.
d) Class Composition and Capitalist Development
The forms of collective power which workers develop based on their combination within the production process is constantly undermined by capital’s attempt to ‘de-compose’: outsourcing, dismantling, introduction of new technologies and production methods requiring new skills, re-location to other regions of the globe, introduction of new categories of workers with different backgrounds etc.. The dynamic character of capitalism and ‘development’ in general is less explained out of ‘market-forces’ or ‘abstract greed for super-profits’, but by this dynamic relation-ship between struggle and changes in production as response. Capitalism contains class conflict through developmental leaps. This entails that the ‘de-composition’ (the segmentation of the working class in the production process) is done in a way which re-composes them on a higher level of social productivity. Capitalism is not merely ‘isolating’ workers in response to their ‘united efforts’ – it is isolating them through specific form of socialisation.
e) Economical – Political Contradiction of Productive Cooperation
Capital is forced to accumulate, less due to ‘internal competition’, but in order to be able to respond to workers’ struggle with an raise of workers’ consumption levels while at the same time increase in their exploitation. In order to ‘de-compose’ workers strong-holds and to re-combine social labour on a higher level, the general costs for machinery increase. The increased use of machinery and its increased share in total production costs is an expression of how capital intends to contain class struggle. Here we find the ‘economical’ and ‘political’ contradiction combined in the production process, in front of workers’ eyes and contained in their experiences: from an ‘economical’ point of view a smooth and close cooperation between workers is necessary in order to increase social productivity. Under given social class relations the ‘productive closeness’ of the social producer contains a ‘political danger’. Despite the fact that it hampers social productivity, which any worker is well aware of, capital has to segment the production process ‘politically’, be it through immediate division of labour, division between intellectual and manual labour, between sectors, between regions, different spheres of production and reproduction, between developed and underdeveloped regions, private and state sector and between nations. This is the sphere of communist theory, understanding and revealing the ‘political systemic forms’ based on workers’ direct experiences.
The ‘political segmentation’ of the social production process is not merely a question of control and domination of the working class. It is also a political requirement for capital in order to obtain its major social legitimation and ‘fetish’: to be seen as pre-condition of social production. Capital brings together individual workers within an industrial production process which cannot be put into motion unless labour is combined. Combination happens ‘under capital’, the resulting social productivity seems the productivity of capital. The fact that millions of new connections of global production are established ‘through capital’ is the major social backbone of exploitation and class system. What seems like cunning tactics of divide-and-rule creates thousands of little hick-ups in the production process, thousands of problems and mis-coordinations. That things run smoothly despite all the imposed barriers largely depends on workers (improvisation, creativity, overcoming problems) – who individually might perceive these problems as problems of ‘mis-management’. Here again workers’ organisations have to reveal the systemic nature.
This ‘capital fetish’ (capital as precondition of production) can only be undermined through revealing the social and political dimension of production process – by interrupting it in struggle. In order to obtain even the most minimal ‘victories’ and economic gains workers are increasingly forced to push beyond their immediate company level. If the daily grind of global supply chains start to stumble, because workers in one link interrupt the flow of production, this gives us a moment to create direct relationships. Communist activities have to refer to the ‘practical existence’ of the ‘collective worker’ – the totality of social cooperation necessary in order to produce, the antagonistic living force within capitalist relation of production. The ‘collective worker’ is necessary reference point in order to gain in power in any struggle for immediate demands and material basis for general radical social transformation on a world-scale. In this sense the ‘collective worker’ is a more historical, material and dynamic concept to analyse the process between particular struggles and political potential of change than the notion of ‘class in and for itself’, which leaves a gap in the transformation, generally filled with vague terms of consciousness.
f) Generalisation and Capitalist Cycle: Boom and Crisis
There has been little historical debate about the relation between class struggle, change of production system and wider capitalist cycle in terms of ‘boom and crisis’. [4] Debates have evolved separately about product or technological cycles, about cycles of ‘expansion’ and financialisation. The question of whether workers face boom or crisis, partly expressed through the conditions on the labour market, obviously impacts on the question of how they can struggle, of how their struggles can generalise and pose the question of a social alternative. Systemic questions mainly arise at times when the working class still contains the structural power and aspirations of a period of ‘expansion’, which also opened space for widespread critique of the ‘alienating and despotic form of expansion’, but faces a crisis which eradicates the hope for ‘a better future’, despite the still blatant potentials of social productivity. The period between 1968 and 1977 is an example, we most likely face a similar situation on a more global scale today.
With the current global crisis it becomes more and more difficult for capital to portray itself as a pre-condition and coordinator of production: capitalist social productive cooperation has to pass through the fragile channels of companies, markets, money. Under condition of crisis the cooperation rips, small links in the chain go bust, millions thrown into unemployment, millions are made to work till total exhaustion. ‘Managers’ supposed to be responsible to ‘coordinate’ the cooperation of billions, but they are increasingly trapped within their ‘small links in the chain’, be it sectorial or regional. Their only answer to the crisis – bail out followed by austerity – aggravates the conditions.
The managers of capital try to enforce austerity against the overt potential for abundance. They can only succeed as long as they are able to separate the social experience of over-productive labour from the poverty of un-/underemployment. Obviously this separation does not take a pure form of ’employed working-class’ on one side, ‘impoverished proletariat’ on the other. This separation appears in its various shades of development and underdevelopment, of high-tech and labour intensity, of regional deprivation and boom centres, of respectable workmen and lumpen, of hire and fire. This separation will appear in all imaginable ethnic colours. With the disappearance of the old buffer-classes, with the social death of peasantry and artisans in the global South, the demise of the self-employed educated middle-classes and petty bourgeoisie, capital has to face up to it’s living self. While being in it’s essence the violent coordinator of social labour – ‘globalisation’, international supply-chains etc. – in this crisis more than ever capital has to hide and segment the global character of social cooperation from the emerging global working class. In the attempt to segment and re-combinate capital becomes a burden to social cooperation. It gets in its own way. Therefore the challenge for working-class communists is to point-out the ‘political separation’ of development (social productivity) and underdevelopment (poverty), the potential of abundance in the face of stark misery. In order to do this we will have to re-consider old concepts used to describe the relation between centre and periphery, e.g. the concept of ‘imperialism’, ‘Third World’ etc., which seem to blunt in order to analyse the emerging global class composition.
g) Union Question
On the background of the process of ‘class de-composition and re-composition’ we can easily see that the problem with trade union struggle is not merely its ‘burocratic undemocratic forms’ or limited ‘economic demands’. The formal and legal framework of trade union organisation does not allow workers to organise on the same level and scope as capital is trying to both combine and disorganise them. While modern companies combine workers beyond categories, company, sector and national boundaries, trade unions can neither reflect this scope nor the rapidness of changes. In addition they have to stick to legally prescribed forms of struggle which by definition will keep workers subjugated to the playing field of state and capital. Amongst communist there will not be much disagreement about these facts.
The disagreement rather concerns the question of the relation between ‘economical’ and ‘political’ struggle, between ‘trade union struggle’ and ‘party or political organisation’. [5] Without going into detail we can state that the position which perceives the ‘economical’ and ‘political’ struggle of the working class as two separate stages – and therefore the ‘party’ as a kind of political complement to the trade unions – has its origins in a historically specific stage of development of capitalist class relations: an early one. The traditional Leninist conception is based on social conditions where industrial production and working class was still marginal, where the state was not majorly involved in industrial relations, where there existed still a major gap between ‘factory and wider social reproduction (schools, science), where the ‘immediate production process could be seen as a mainly ‘economic sphere’ with little connection to the rest of society and ‘politics’.
Since Lenin, with the development of a ‘planning state’ (state industries, direct intervention in industrial planning and relations etc.) as the extension of planning from factory into society, with the extension of ‘scientific’ industrial form of production into all spheres of social life and with the working class becoming a social majority, the question of what is ‘economical’ about the social production process and what is ‘political’ has obviously changed. With these changes also the institutional role of trade unions has transformed drastically. From a ‘school’ of workers in a seemingly gradual process towards ‘political consciousness’, they have been reduced to institutions which – confronted with the vast extension of the social production process – are legally and formally confined to a very narrow social sphere. Their main influence is based on the necessity of capital to control the wage-productivity development. Under these conditions, to maintain Lenin’s classical notion of a rather schematic distinction in economic and political struggle will have negative results.
h) From Workers’ Struggle to Social Transformation
The classical two-stage model of ‘trade union’ and ‘political party’ formation makes it impossible to discover the ‘revolutionary contradictions’ within the social productive cooperation. It is a disjointing, rather then elevating on a higher level of consciousness: limited to the trade union framework workers will not be able to generalise their struggles along the lines of their already existing productive relationships and the ‘political generalisation’ through the party is in most cases happening detached from social production in the ‘political sphere’ (campagnes, mobilisations etc.).
The generalisation within social production itself is the main precondition to materially undermine segmentations and the ‘capital fetish’ (capital as the organiser of society). It is ‘economic struggle’ through which workers have to discover the political nature of capitalist production – the class content of science, technology, institutions. This mass process of discovery cannot be by-passed, the ‘generalisation’ cannot be short-cut through the various channels bourgeois politics have to over: from trade unionism to parliamentarism, from identity politics to regionalism or nationalism.
The class movement will have to develop its organisation along the lines of global productive connections and materially change these connections: in its intensive stage class struggle will simultaneously have to create the (pre-)conditions for ‘the production of communism’. Workers’ struggles will not only ‘attack capital and the state’ by withdrawing social labour – strikes will interrupt social reproduction to an existential degree and thereby force the class movement to re-organise production and circulation while fighting. In this stage of class struggle we will be able to discover not only how social labour is globally integrated, but also that most social labour in capitalism is superfluous – no one will complain about the lack of market research calls or supply of Tata Nanos. A huge mass of human energy and creativity will be set free. At the same time the class movement will face the question of how to re-organise production in a form which not only guarantees effective subsistence, but also extends the ‘self-organisation of struggle’ into a self-organisation of social production: abolishment of hierarchical division of labour and uneven development. The revolution is not only an act of ‘smashing/taking power’, but of revolutionising social relationships, of getting rid of the contradiction between individual and social by materially transforming how we (re-)produce our social existence. In this sense is only logical that the ‘trade union/party’-perspective also disjoints ‘revolution’ from ‘production of communism’ and sees communism rather as a ‘policy’ which can be introduced.
The Leninist conception of ‘trade union’ and ‘party’-struggle was based on a less developed industrial/agricultural society. The practical expression of this notion revealed itself when the new (Bolchevique) state dismantled the Sowjets, the workers’ economical-political organisations, during the first years after the Russian Revolution. [6] The ‘New Economic Policies’ (Fordist industrialisation plus ‘market’ incentives) at the time required to impose ‘a strict centralised regime on factory and society’. We can argue about the ‘historic necessity’ of this policy, e.g. the historic necessity to appease the emerging middle-peasantry or maintain a standing army, fact is that in order to impose this regime the new state forced workers to give up their economical-political power in form of the sowjets. The new state strategically re-introduced a separation: workers were supposed to turn to ‘trade unions’ for their ‘economical needs’ and to ‘the party’ for political direction. In this way workers’ productive collective power was undermined and the driving force of revolution extinct. This was the degeneration.
i) Tasks and Continuity of Workers’ Organisations
On this background we maintain that their is a continuity between ‘economical-political’ organisations today – from the the most minute level of shop-floors and industrial areas – and these future ‘economical-political’ organisations of communist revolution. [7] In a modern capitalist society there can’t be a conceptual-organisational gap between the embryonic and developed forms. Workers’ organisations have to find practical collective answers within daily workers’ struggles in a way which always keeps open the possibility of expansion and generalisation – towards the ‘collective worker’. The coordinated collective steps have to be able to ‘give some relief’ to workers here and now by helping to gain concrete ‘victories’, while at the same time referring organisationally and conceptually to the necessity of social revolution. They have to use the minute scope of ‘anticipation’ (question of which forms of struggles or demands could help catalysing and generalising struggles in concrete time and space) based on the knowledge about current struggles and their position within wider social production. They have to use the current global scope of struggles to build international links which survive the ebb and flow of particular struggles and can come to a truely global perspective and organised practice. Workers’ organisations in that sense are not the ‘organisations through which the working class struggles’, they are rather organisations which support the tendencies towards self-organisation and emancipation in the struggles and movements as they happen.
In the following we will try to refer the questions raised above to the current regional struggles and then formulate some ‘concrete proposals’ concerning steps towards a workers’ organisation.
Footnotes:
[1] For the historical debate about these concepts see:
http://libcom.org/library/renascence-operaismo-wildcat
http://libcom.org/library/storming-heaven-class-composition-struggle-italian-autonomist-marxism-steve-wright
[2] Loren Goldner argues this thesis in his text concerning the general relation between capitalist development and agrarian revolution:
http://libcom.org/library/communism-is-the-material-human-community-amadeo-bordiga-today
[3] Two essential texts on the question of changing class compositions and changing forms of ‘communist movement’:
http://libcom.org/library/class-composition-sergio-bologna
http://libcom.org/library/tribe-of-moles-sergio-bologna
[4] One of the few attempts has been undertaken in ‘Forces of Labor’, by Beverly Silver.
http://www.wildcat-www.de/dossiers/forcesoflabor/fol_preface.htm
http://www.wildcat-www.de/dossiers/forcesoflabor/fol_dossier.htm
[5] Essential text by Mouvement Communiste on the ‘union question’:
http://mouvement-communiste.com/documents/MC/Letters/LTMC0311EN.pdf
[6] On the relation between ‘Bolshevik’ state and workers’ sowjets:
http://en.internationalism.org/ir/1977/08/communist_left
https://files.libcom.org/files/The%20Russian%20revolution%20in%20retreat.pdf
http://libcom.org/library/bolsheviks-workers-control-solidarity-introduction
[7]
The experience of workers’ coordinations in Italy in the 1960s – 1970s illustrate the ‘economic-political’ character and the cohesion between direct struggle and revolutionary organisation:
http://libcom.org/history/porto-marghera-%E2%80%93-last-firebrands
2) On Current Struggles
Concerning the overall ‘class composition’ and ‘conditions for generalisation of struggle’ in Gurgaon area we have published two papers for debate. In the first paper [1] we outlined briefly the main industrial sectors (automobile, garments, IT-related services) and their different degrees of integration into social and global production and ‘market/production’-rhythms. In the second paper [2] in April 2011 we described the general conditions in terms of labour market and inflation, hinting at the possibility of a wider wave of ‘egalitarian wage struggles’ with the potential for generalisation. Since then the struggle at Maruti Suzuki in June – October 2011 has provided us with a vast amount of experiences, which we tried to analyse in various newsletters – the second part of this paper ‘on organisation’ will consist of a ‘balance-sheet’ eight months after the end of the dispute. Regarding the recent struggles at Harsoria, Flexonics, Orient Craft, Theme Export, Lakhani and Globe Capacitor we can only formulate preliminary thoughts:
* First of all we can state a common background of these struggles. The struggles took place in factories with 500 plus workers. Despite the fact that these belong to different sector we think that there exists a certain relation between ‘quantitative concentration’ of workers and their potential to take collective steps under given conditions – or at least collective steps which make themselves known beyond the factory wall. As always the question remains how workers in the ‘centre’ can relate to workers in the ‘periphery’, e.g. in small industries.
* The struggles in the more productively more integrated manufacturing companies – Harsoria, Flexonics and Globe Capacitor – displayed a higher degree of ‘organisation’ in terms of necessary coordination in order to undertake collective steps. Here we can see a difference between two dominating sectors in the area, the automobile and garment sector. It was not by chance that the Maruti struggle (two collective wildcat occupations) took place in the automobile sector and the more ‘impulsive struggles’ tend to shake the garment sector.
* The fact that Harsoria workers opted to stay inside the factory (sit-down strike) is a result of experiences of past defeats. Workers in the area know that they are in a less favourable position towards company and (police) state once they are outside. In this sense the Maruti struggle has entered something like a ‘collective subconsciousness’ of the working class in the area. The fact that the Harsoria workers stayed inside but remained awkwardly attached to the legalistic positions can mainly be explained by the domination of the struggle by permanent workers and their trade union. Similar to Senior Flexonics the dead-ends of trade union form of struggle show themselves very clearly, the tragic element in case of Harsoria is that workers opted to enter the same dead-end twice within a year.
* The struggle at Globe Capacitors reveals some dormant potentials. Workers undertook planned collective steps with direct impacts. They tried to avoid traps of presenting ‘leaders’, who could be bought or crushed. They also avoided the legalistic swamp. The example also demonstrates that the company reacted swiftly after having had to give concessions – management hired new 100 workers through contractor and ‘gave some relieve’ to permanent workers. The short struggles and Superelectro Films and Abhirashi Impex gave an impulse to workers at Globe Capacitor. This was possible due to the mutual dependency with the production system and general similarities in condition in the industrial area. Globe Capacitor workers will have to go a step beyond merely ‘receiving impulses’ from other workers, but form conscious and direct relationships with them – in order to undermine management’s counter-attack on the company ground.
* The Globe Capacitor example also contains the double character of global supply-chains. The company manufactures capacitors for export and for multinationals like L&G or Samsung. Senior Flexonics itself is a multinational company with factories around the globe. In the Gurgaon area, in most cases the global dimension of production has been used against workers, rather than workers having appropriated it for their own collective efforts. In the case of Denso automobile supplier in 2010, management prepared for a lock-out by ordering extra amounts of parts from Denso Thailand plant. When the dispute at automobile supplier in Gurgaon interrupted assembly-lines at general Motors and Ford in the US due to lack of parts the regional representative of the UAW (United Automobile Workers Union – USA) only expressed the hope that ‘the problem at the supplier’ will be solved soon. Neither workers in the US, who were battling with a UAW agreed wage cut ‘for jobs’, nor the Rico workers were able to make conscious use of their productive links.
* It is not by chance that the recent riots at Orient Craft and Larsen&Tubro took place in the textile and construction sector. Garment export workers are subjected to a quick succession of ups and downs of orders from clients, while orders come in they work 12 to 24 hours a day, while orders are down they often have to wait or look for work. The quick wildcat strikes at the time of new orders to enforce higher piece rates have their equivalent in the seemingly spontaneous outbursts after repression. Looking back into history we can see that workers struggles in the garment industry have always been rather violent and to a certain extend erratic. In this sense, regarding the short-term nature of a specific product cycle, the situation of construction workers is not much different.
* The riots at Orient Craft and Larsen&Tubro construction site express a general discontent amongst workers – they also express the general knowledge of workers that the usual ‘grievances channels’, such as trade union protest, legal procedures at labour courts or petitioning of political leaders have become increasingly irrelevant for the majority of workers. The riot is therefore not an ‘unreflected’ reaction of workers. Compared to long-term legalistic efforts within the garment sector, focussing on the illusion of stable agreements and ‘fair trade and jobs’, these outbursts actually have a higher likelihood for workers to force management to ‘give concessions’ – though these concessions will never appear as a ‘formal success’ of negotiations and therefore remain invisible for large sections of the well-meaning left.
* The rather idealistic criticism of many leftist, that workers should focus on ‘true organisation and unity’, instead of engaging in ‘anarchic’ violence is at best helpless. While it is true that riots can at best give an impulse to wider unrest and only open a very limited space to create deeper organisational links, our task is not to condemn them on the basis of our picture book ‘of how workers are supposed to fight’. Rather we have to ask the question of how to imagine an ‘organic’ link between different ‘forms of struggle’ (determined by their position in social production), partly given through the material connection across sectors, mainly due to the mobile character of the modern work-force.
* One of the ‘generalisation of conditions’ between garment and automobile sector in the area is the ongoing transformation from ‘skilled artisan/taylor work’ (full peace production) to chain systems and increased mechanisation (CNC-embroidery), which ‘industrialises’ the sector and introduces a work-force which is less skilled on an individual level, but more integrated on a collective level. The intensifying competition for jobs and the drop in wages in the sector is the current negative outcome. The further introduction of the chain-system takes place at a point where most of the garment export companies are in a severe credit squeeze, which puts further pressure on wages.
* In terms of conditions on the labour market and problems with wage payments we can see a slight gap opening between garment and automobile sector. Many (skilled) garment workers report that it becomes more difficult to find jobs within the sector. Struggles about delayed payment of wages such as those at Theme Export and Lakhani are more pressing in the garment sector than in automobile companies of similar size. Mainly workers in the bigger manufacturing companies are currently able to put forward more offensive demands for less work and more money.
What kind of conclusions can we draw from these struggles regarding potential and necessity of a workers’ organisation? First of all we have to see that the reports themselves, their sketchy and random character, expresses one of the main challenges for future organisational efforts: we have to state honestly that we know too little about what is happening and how. We get to know about ‘official struggles’ or ‘spectacular events’ – in most cases once workers’ are victimised and defeated – but little about workers collective steps in the factories and territory. Our reports and analysis focus more on the role of various political forces (often on the role of our own organisation), than on the material basis of struggles, their internal potentials and limitations.
The lack of insight and analysis is not only a problem of our own limited capacity and lack of ‘contacts’, it is a political problem within the working class itself. Workers’, too, underestimate the importance of their experiences in general and the need for deeper analysis and sharing of these experiences in concrete. Obviously workers will ask and rightly so: how does the exchange of experience change anything, how does it relate to concrete betterment of our situation? This is a question which has to be answered – by turning experience into conclusions for practical coordinated efforts. What could that mean in concrete relating to these recent struggles?
* An organised presence within the struggles at Harsoria and Flexonics armed with a) the experience of struggles which ended in similar situations (individual ‘good conduct’- declarations, lock-out, isolation in front of plant, legalistic traps) and b) practical suggestions how to avoid the dead-ends (expansion of the dispute within area, e.g. through circulating workers’ groups, and along supply-lines) could have shifted things.
* In the case of Harsoria analysis of the wider conditions in companies in the same sector (medical equipment) might open space for generalisation: at the five factories of Eastern Medikit in Gurgaon casuals are under permanent pressure and wages had not been paid for some time. Direct visits and steps independently from the HMS presence in both companies could have increased the pressure on both managements. Harsoria mainly exports to the EU – the current economical crisis will impact in one way or the other on the company and would have to be taken in consideration in the debate with workers.
* In the case of Senior Flexonics direct exchange could have been established to Flexonics workers in the US, UK, France, Germany and Czech Republic. The relationships to workers’ organisations in these countries are weak, but a concrete effort could fortify them. Senior Flexonics is one of the worlds biggest manufacturer for certain diesel engine parts. A more detailed analysis of company strategies and market developments could reveal quite general tendencies and contradictions of the global industrial system – which could re-enter in the proletarian debate.
* In the case of Globe Capacitor a workers’ organisation would suggest to make conscious use of the existing links to workers in other factories, both in the area (Abhirashi Impex) and the supply-chain (Superelectro Films), to make special efforts to relate to the 100 newly hired workers and to re-examine the relationship with the permanents. Additional efforts should be made to find out about current conditions at Orient Fan, L&G etc.
* The cases of Lakhani, Theme Export and to a certain extend the unrest at Orient Craft ask the question of how direct actions around the question of non-payment of wages can be coordinated on a wider industrial area level. Pre-condition is a collective knowledge about where exactly conflicts are brewing at the same time. Common activities of workers of different companies within dense industrial areas will make an impact – management of other companies will put pressure on the ‘non-paying’ management to solve the problem. Additional pressure can be exerted directly on international buyers.
* The riots at Orient Craft ask for a reconsideration of the ‘internal organisation’ of riots. The common view of ‘chaotic violence’ is in most cases superficial and wrong, dealing with social situations like they were natural disasters. Which scope for ‘organised direction’ does exist during situations like at Orient Craft? What can we do and what should we avoid during these situations?
* The fact that all these struggles took place close to each other in terms of space and time raises the question of ‘regular assemblies’ of workers involved in concrete struggles, disregarding specific issues or sectors. The current material conditions of workers (6 to 7 days work per week, 12 hours shifts) will require a special creativity regarding organisation of these assemblies (rotating, mobile). The assembly could also be space to debate current struggle experiences in other regions.
* In the May issue of Faridabad Majdoor Samachar we published the struggle reports in Hindi, introduced by general considerations concerning ‘how to struggle’. the paper will be circulated in Delhi-Faridabad-Gurgaon-Manesar industrial areas. Given our current limited personal capacities we are not able to make the next step towards ‘practical consequences’.
Footnotes:
[1] Paper on class composition in Gurgaon:
https://gurgaonworkersnews.wordpress.com/gurgaonworkersnews-no-925/
[2] Paper on potential for general wage struggle in the area:
https://gurgaonworkersnews.wordpress.com/gurgaonworkersnews-no-937/
3) On Concrete Tasks and Steps
Facing the seemingly gaping abyss between the ‘general role of a communist organisation’ and the ‘mundaneness’ of concrete tasks thrown up by day to day struggles we often confirm the seeming disjuncture in our activity. We either reduce our activities to ‘general debate’ (crisis, communist tradition etc.) or get bogged down in ‘activity’ – losing sight of a wider picture or leaving it to ‘the party leadership’ to re-establish a superficial link between practice and theory in hindsight.
In the following we summarise what ‘workers’ organisation’ could mean in concrete and formulate steps towards it, based on our current stage of practice. The ‘elements’ of a workers’ organisation are put in a seemingly schematic order. We don’t see them as ‘chronological’ or ‘progressive, meaning that we should attempt to see them as a ‘totality’ – the actual limitation of our capacities will nevertheless force us to concentrate on certain aspects.
I) What do we see as the basis of a workers’ organisation
II) Where are we now in this process
III) How could we get further
I) What do we see as the basis of a workers’ organisation
a) Develop Common Understanding
We think that a broad common position towards the following questions is necessary in order to collaborate on a continuous bases:
* ‘what is the main characteristic of the current system’?
* ‘what would be a social alternative’?
* ‘what is the material link between the existing and the alternative’?
* ‘who is the transforming subject’?
* ‘how do we relate to it’?
The answers are never established once and for all – things change. This means to debate things beyond the immediate experience of workers. For that we need ‘new forms’ of internal organisation and debate which do not reproduce the hierarchical devision between ‘educated/uneducated’, between people who have time and resources to read global news and historical texts and those who don’t. In this sense part of the ‘common understanding’ has to relate on the ‘form of how to organise’, e.g. the attempt to abolish formal and informal hierarchies, to remain independent from (non-) state institutions and other social layers who have an interest in the status quo.
b) Relate to Workers’ Experiences
We have already stated that we ourselves know too little about daily conflicts and changes in factories and territory. Workers themselves give little importance to their (individual) experiences – both in terms of daily practice and acts of resistance. It is part of the political debate to challenge this – in order to discover the social nature of individual experiences. The modern industrial system combines labour by individualising it. We have to focus on the question of the social dimension of what appears as isolated labour: which other labour is necessary so that I can perform my work-task, from the direct supply of material I use, to canteen workers, to housework. On a second level we have to ask what similarities and differences in terms of ‘form of work’ and conditions there are within this social cooperation and why. On a third level we have to discuss how state and capital changes this social cooperation and conditions within and how workers could make use of it. This will already go beyond the individual experience. We don’t think that an organisation forms gradually by ‘convincing’ or ‘recruiting’ individual workers. Class struggle develops in leap and bounds and the concept of ‘advanced workers’, who could be ‘organised and conserved’ individually, will turn into an illusion once separated from the actual collective dispute they are/were part of.
c) Debate General Context
Apart from constant conversations and discussions about the situation in companies and wider proletarian life there is a need for relating these experiences to general and historical tendencies. This requires collective debates and empirical research – again a question of time and resources. In the last decades the relation between theoretical and practical efforts have transformed into a social separation between ‘academic research’ and ‘political activities’. A workers’ organisation should try to challenge this separation by putting forward concrete proposals of ‘workers’ inquiry’ as a re-composition of theory and practice.
d) Develop Means of Exchange
Proletarian experiences and reflection on experiences have to circulate. If possible the ‘means of circulation’ itself should become a ‘means of exchange of experiences’ and create the potential for direct relationships. The form itself is political, we have to re-think the means of exchange: leaflets, ‘reports’, newspapers, internet, public meetings, assemblies. The question has to be addressed of who can participate in the production of the means and how.
e) Engage in Concrete Struggles
The actual struggles are the basis and reference-point of any workers’ organisation. We have to fight the tendency of ‘political organisations’ instrumentalising struggles for their ‘own interests’ (which is allegedly in the wider interest of the working class). Not mainly because we think that workers’ could be led astray, but these organisations tend to glorify struggles and turn them into ‘victories’ in order to make them useful for propaganda (with the best intentions). The struggle is the only chance of collective experience and learning. Therefore a deep analysis and sharp criticism is in the actual interest of the wider working class, even if it means to have to pronounce ‘defeats’. We need a political debate of how to analyse struggles – in the appendix [1] you can find a rather naive and preliminary questionaire ‘on struggles’ which could serve as a basis for debate.
The question whether we are able to make practical contributions to struggles depends a) on our insight into the actual situation, the internal organisation of both company and struggle and b) on the question whether we have established close enough relationships within the workers in order to put proposals into practice. Let’s be honest, in many cases neither the first nor the second precondition is given. In some cases this leads us to rather desperate acts, e.g. relating to the workers mainly through their official leaders, hoping that through ‘practical, more radical advice’ – often limited within the terrain of labour law and formal representation politics – the struggle can be ‘influenced’. The results are obvious, but have to be debated.
So what to do instead, accepting our own limitations? Basically we have to check ourselves: do we make our suggestions based on concrete enough knowledge about either the dispute of concern or similar disputes in the recent past? Do the practical suggestions increase a) the tendencies of self-organisation within the struggle; b) the material power/pressure of the struggle towards company and state; c) widens the possibility of generalisation beyond the current sphere? For concrete debate of these questions see the struggle reports in this newsletter and the ‘preliminary conclusions’.
f) Advance Analysis of Strategical Tendencies
As already stated, class struggle does not develop evenly or gradually, instead it mirrors the uneven nature of capitalist production process and cycles. A strategical analysis is therefore of major importance, not in order to find ‘the possible centres’ of future workers’ struggles and power – which would be an easy task – but to anticipate how these centres will relate to the periphery (or other centres) and along which lines struggles will be able to generalise. These lines of generalisation are not necessarily confined to the connections through the social production process, they can be created by certain economical and political developments which impact on wider sections of the class. Here again, debate is necessary about the relation between ‘productive’ and ‘conditional’ links between sections of workers. Our political activities should focus on these potentially generalising sectors and tendencies. In Gurgaon this could mean to focus some activity on the relation between call centre workers and manual industrial workers, between urban experience of workers and conditions in their villages, between Maruti Suzuki and other centres and the wider productive terrain as will be proposed in concrete in the second part. the rapidness of changes in capitalism leave only little scope for ‘preparation’ or ‘anticipation’ – but based on a deeper understanding of production system and proletarian conditions we might be able to push for certain ‘catalysing’ steps during concrete struggles.
g) Relate to / Create Factory Collectives
Prime objective of any workers’ organisation should be the development of collectives (or the establishing of relations to existing collectives) within workplaces, which are able to act. At the current stage of class struggle the question of the relation between ‘shop-floor’ activities and wider ‘political’ coordination seems to be a question of either – or. Without wider struggles workers’ collectives within factories don’t ‘find’ other group of workers outside. For the same reason ‘political groups’ remain small and can chose either to act on the ‘general terrain’ (going from struggle to struggle, publishing general newspapers) or concentrate on building work-place based activities. One reaction to this dilemma is that once we come across active groups of workers, due to lack of time and energy (and may be reflection) we propose quick solutions, such as setting up of company unions – instead of engaging in a common process of analysis as a precondition for more fruitful collective steps. At this point we can only refer to the historic experience of ‘factory activity’ in Faridabad during the 1980s and 1990s as reference for deeper debate.
http://libcom.org/library/self-activity-wage-workers-kamunist-kranti
h) Coordinate Beyond Factory Level
A workers’ organisation cannot be formed on sectorial or professional basis, but the concrete forms of how workers can coordinate their efforts beyond the company boundary differ. Currently within our circles there exists a rather schematic debate whether an ‘area wide union’ would solve the problem of ‘work-placed based isolation’. At this point we can only encourage to base the debate more on the concrete material constitution of the relation between single and wider production sphere:
… in a huge factory like Maruti Suzuki a rotating system of line or department delegation will make sense, which has to relate to a coordination with workers’ in the immediate supply-chain
… living and working conditions in IMT Manesar might be cohesive enough to propose an area wide assembly
… the small-scale nature of certain (home) industries or industrial areas might enforce an area wide delegation system
… the internal productive integration within the garment sector might be too weak in order to base a coordinated steps on direct links, the ‘generalisation’ might happen around the question of ‘wage payments/order overtime’ and take the form of circulating assemblies
… in some areas workers live close to their workplace, there conditions in the living sphere can more easily be raised by factory coordinations, in other areas ‘neighbourhood organisations’ might be necessary
… during certain times struggles will happen in quick succession in a dense space, general ‘struggle assemblies’ might be feasible
Answering these questions would require a very honest re-capitulation of experiences under different conditions, e.g. in the small-scale industry in Ludhiana, the recent anti-eviction movement in slum areas in Kolkota, our own attempts to set up ‘workers’ meeting places’ (see below) etc.. The further challenge will be not to conceptualise these ‘different forms’ as ‘parallel forms’, but as a ‘proletarian continuum’ with a tendency towards generalisation. This will be a constant ‘contradictive balance’: self-organisation of workers is based on their specific productive basis, generalisation which abstracts from this basis without transforming it will lead to undermining workers’ collective power, e.g. many ‘general strikes’ have this feature. In the end it is not the ‘growing organisation’ which generalises, but the emergence of new class movements – again the question of the relation between both. To spell this out a bit more:
As far as possible a workers’ organisation has to make use of regional and global productive interdependence of the labour process. A workers’ organisation would be able to turn this structure into a weapon in the interest of all workers in the chain, disregarding their specific categories. An organisation would make strategical use of the strongest position of workers in the chain (or to find the weakest link), e.g. central suppliers, transport chains etc. and at the same time takes into account the conditions and difficulties of workers in the weakest position. It would use pressure in the strong points to undermine the divisions and differences imposed by management, not due to charity, but need for collective power. A workers’ organisation would be able to coordinate actions disrupting the long chain of production with minimal effort and harm for us and maximal impact on company management. As preparational work we would have to dig out recent historical examples of how workers’ organised such kind of steps, e.g. during the so-called chess-board strikes at FIAT, Italy, during the 1960s and 1970s.
Although workers in automobile (or wider manufacturing sector) and garment are in most cases neither connected through direct productive links nor through ‘immediate demands’ (wage payment), a workers’ organisation will have to explore all possibilities of ‘connections’ apart from rather unsubstantial ‘external unity as proletarians’. Here we have to debate the mobility of a certain section of workers between both sectors, the spacial proximity in dense industrial areas, the increasing similarity in labour process with introduction of chain system, certain general similarities in conditions (12-hours shifts, repressive regime), wider conditions in the reproductive sphere etc.. A workers’ organisation would try to ‘generalise’ from the advanced points, this could mean, e.g. to spread the experience of changing gender relations in ‘mixed industries’ and the different social status of female workers within the more isolated sphere of female labour in the home industry.
i) Understand Relation between Factory and Society
The last decades have transformed those social categories which used to be mobilised as separate elements under the leadership of a ‘political alliance’: ‘worker’, ‘peasant’, ‘student’, ‘women’. Today we can broadly assume a common proletarian existence under very different circumstances – which require not an ‘alliance’, but a sophisticated process of common organisation. Today the probably more challenging separation is the separation between ’employed’ and ‘unemployed’ proletarians, not as fixed categories, but forms of temporary existence – despite the flux and interfaces of migration and informal sector which connects both. A concrete analysis about emerging divisions and re-connections between rural-urban, employed-unemployed proletarians should be in the focus.
j) Organise on a Regional and Global Level
Together with the ‘workers and peasants’-alliance the old form of ‘international solidarity’ between ‘regional/national movements’ has expired. What remains is a rather folkloristic-formal ‘solidarity’ between sister parties. Meanwhile the global character of the system in terms of production chains, export markets, labour migration forces workers’ struggles to relate to the international terrain. As you can read from the struggle reports in this issue, any of the struggles asked the question how to relate to its international dimension, either on the level of ‘international buyers’ or supply-chains. We should make an extra-effort to take this international dimension into account – future international coordinations (or Internationals) between workers’ organisations will mainly be based on the experiences and debates during the collaboration around concrete workers’ struggles. The workers’ struggles themselves will have to re-compose the ‘communist movement’ on a global level. We should nevertheless try to anticipate the necessity and open the debate here and now, e.g. by making the effort of translating or writing regular ‘regional reports’ for the international debate.
II) Where are we now in this process
We briefly summarise the current effort of Faridabad Majdoor Samachar (Faridabad Workers’ News) and GurgaonWorkersNews as an embryonic form of workers’ organisation.
Since the mid-1980s Faridabad Majdoor Samachar – a workers’ newspaper in Hindi – is published once a month and distributed in industrial areas. Currently we distribute 10,000 copies in Faridabad, Okhla, Gurgaon, Manesar and send it to around a hundred people in different parts of India. The paper consists of four pages, most of the content are short workers’ reports concerning the situation in their factories. There are longer struggle reports, workers’ auto-biographies, reports from other regions, thoughts on the systemic nature on common proletarian problems such as (mental) health.
Since 2007 we publish GurgaonWorkersNews as an electronic newsletter in English, mainly consisting of translations from Faridabad Majdoor Samachar plus more general empirical research. The newsletter is sent out to around 4,000 individuals, mainly in the Subcontinent, Europe and the US. We see it as one potential contact-point between workers’ initiatives in Delhi and the ‘international space’.
Under the current conditions of about a dozen people actively involved in Faridabad Majdoor Samachar and GurgaonWorkersNews we just about manage to publish the paper and newsletter and distribute it. There is little scope for other, e.g. specific ‘workplace’ activities. Here we can see a certain contradiction, given that the main backbone of FMS came together as a ‘factory collective’ of permanent workers in the 1980s and 1990s. Today ‘single workplace’ activities have been undermined to a certain degree by the fact that 80 per cent of the work-force is temporary. To build long-term presence in one factory is an organisational challenge. The temporary status and long working hours also means that today only few workers have the time for ‘extra’-political activities, such as publishing a newspaper or organising meetings.
We can see further seeming contradictions. In the 1980s the group underwent a certain period of self-criticism regarding their political premises (‘Leninist’-framework) and relation to workers (‘preach-teach’). The language of the Hindi paper changed from ‘political jargon’ to more common language within the working class. Instead of ‘recruiting cadres’ the emphasise was put on ‘workers self-organisation’. Today we seem to have the problem to explain to younger activists/workers that our efforts aim towards an ‘organisation’ which requires active participation. Without the language and methods of ‘the old mode’ (party) we seem to have difficulties to ‘get people involved’.
What is the motivation and ‘result’ so far?
a) Develop Common Understanding
Most discussions develop ‘informally’ around the front-page articles of the newspaper or in the ‘Workers Library’ in Faridabad. There used to be organised ‘study circles’, but partly due to the format (emphasis on written word, ‘teaching’), partly due to the lack of time of workers these have been stopped. One of the last collectively produced ‘theoretical works’ were reflections of critique of political economy. http://libcom.org/library/refelctions-critique-political-economy
b) Relate to Workers’ Experiences and c) Debate General Context
The newspaper mainly consists of workers’ experiences and emphasises their importance. The front page article hints at the systemic and historical character of seemingly individual problems. In this sense the main content of the newspaper is the relation between workers individual experience, collective steps/struggles and the wider class society. The newspaper portrays a specific class position and position of ‘workers’ autonomy’, which has entered the wider area – the results don’t show up in membership.
d) Develop Means of Exchange
The newspaper cannot be seen as a purely ‘means of information’. It is mainly the maintenance of a potential: it is possible with more or less simple means to create an exchange and possible coordination between workers in a relatively vast industrial area. This does not need major resources or ‘political leaders’. Workers make use of this fact individually and collectively, e.g. by supplying reports for publication. Only rarely workers ask to get in touch with other workers in a specific company through the newspaper – but it remains a possibility open for everyone one’s it is needed.
e) Engage in Concrete Struggles
Over the years and through the regular distribution in various places a vast knowledge of ‘struggles in the area’ is present within the small circle of FMS and expressed in the newspapers. Whenever possible this experience and conclusions are presented to concrete struggles, although given the capacity this happens on a sporadic level. In many articles FMS raises the question ‘what to do, what not to do’ regarding struggles (avoid legal traps, company isolation – inform workers in the area etc.), but it remains a ‘position’. In few cases we manage to create direct contacts between workers engaged in struggles in different areas. In few cases we could make use of international contacts in order to support struggles practically. Focus is therefore also determined by our own strength: critical assessment of struggle experiences and their circulation.
f) Advance Analysis of Strategical Tendencies
Discussions about these tendencies are informal and sporadic. We distributed leaflets to call centre workers knowing that a potential fusion between this section of the working class with ‘traditional’ industrial workers would mean a qualitative shift. We try to emphasise the importance of supply-chain structures in the area and mention these in the workers’ reports.
g) Relate to / Create Factory Collectives
As mentioned there is no scope for systematic ‘work-place activities’ and it has become more difficult due to increased mobility. We try to discuss the potential of workers’ mobility and ‘non-attachment’ to specific jobs and sectors with workers, but this has not expressed itself yet in concrete organisational terms, rather in a general atmosphere of unrest. Sometimes groups of workers come and want to discuss concrete steps in their factories, which we try to debate as concretely as possible dependent on our own understanding.
h) Coordinate Beyond Factory Level
Through years of distribution and presence in the area there is a vast network of contacts, but they rarely ‘collectivise’, result in direct face-to-face meetings of larger groups of workers. In 2010 we undertook an effort to open workers’ meeting places in different locations in Delhi industrial belt. We can say that opening places and announcing them as possible meeting places in the newspaper itself is not enough in order to establish ‘workers’ meetings’. this is partly due to workers’ long working days, but mainly due to an uncertainty regarding ‘what to do’. The relationship between meeting place and individual and collective existence at work was not clear. We lacked time and capacity to organise a closer relationship between these two spheres.
http://www.faridabadmajdoorsamachar.blogspot.in/p/fms-talmel.html
i) Understand Relation between Factory and Society
Focus of the group is the industrial area of Delhi, whenever possible the ‘rural origin’ of workers form part of conversations and show up in articles in the newspaper, so does the situation of students and other workers outside the industry, the living situation (slums) etc. – but on a sporadic level.
j) Organise on a Regional and Global Level
In 1992 FMS comrades undertook an effort to encourage an India wide ‘workers’ newspaper’, which failed due to ‘political differences’ of the various groups. Since then there has been ‘written’ exchange between groups in different regions and countries, which only rarely has direct practical consequences. In some cases the degree of ‘international exchange’ is astonishing, e.g. the translation and publication of letters from inmates in US prisons in FMS. Similar the exchange via GurgaonWorkersNews, which generally happens on individual basis not between ‘active collectives’.
III) How could we get further
Struggles like the one at Maruti Suzuki and the practical experience of ‘political organisations’ within it ask for an open and honest debate within the ‘milieu’ about the current relationship between organisation and workers’ struggle. Groups within the ‘milieu’ can use the chance of re-composing itself around these experiences or they can chose to stick to their particular flags and programs and continue waving them.
For end of May 2012 comrades of Radicalnotes(.com) in Delhi invite to a debate about this question. The first meeting will deal with the attempts of Faridabad Majdoor Samachar during the early 1980s with the classical ‘union/party’-perspective and the development of both industry, class struggle and group politics since then. In the following meetings we will debate the experiences and involvement of different groups during the Maruti Suzuki strike. We hope for a fruitful outcome and will supply material and proposal for a common inquiry in the next GurgaonWorkersNews.
In the mid-term future it would be needed to hold a subcontinental meeting based on precise reports from different industrial and rural areas, relating to common political questions about specific and general tendencies in class struggle. If you are interested in developing ideas concerning such a meeting, please get in touch.
Apart from that we hope for further practical participation in and productive criticism of Faridabad Majdoor Samachar and GurgaonWorkersNews. Please feel free to comment on the general and concrete thoughts in this newsletter and tell us about your collective efforts in your area.
Appendix:
[1]
Questions – Struggles
Interviews and reports can then be circulated and used for further discussions. It is undeniably difficult to write a questionnaire that fits all situations. This one puts emphasis on the struggle in work places but if you want to use it at the university or in the neighbourhood, just change it a bit. Here it is:
The person who is asked / takes part in the conversation
1. What’s your job in the work place? What is your relation to the workers’ in struggle?
2. Do you have a position in the workers representation body (works council…) or the union? If yes, which?
Background
3. What was the starting point of the struggle? (management measures)
4. What happened just before this? (atmosphere amongst the workers, changes to the organisation of work)
5. What other struggles happened earlier, which could have had an influence? (in the same company, in others in the region, after state measures)
6. What are the official demands?
7. Who has made them or put them forward?
Conditions
8. Where exactly does the struggle take place? (company, department)
9. How important is the place of struggle for the company (group), the region? In what kind of ‘economical situation’ was the company? (re-structuring, boom/crisis etc.)
10. What kind of ‘productive connections’ are there to other areas? (suppliers)
11. Who is working in the company? (where are they from, which countries, young/old etc.)
12. What kinds of work contracts exist? (part time, temp work)
13. How do peoples nationalities, work contracts etc. influence the struggle?
Organising
14. Who took the initiative in the struggle? (workers, which kind of workerts, the union)
15. How is the conflict spreading? through which means? (within the company and beyond)
16. What kind of influence do single workers or groups amongst workers have on the struggle? (debates, assemblies)
17. What are the proposals for the forms of struggle? (strikes, blockades)
18. Who puts the suggestions forward?
19. Who gets their own way here and how?
20. Which kinds of attempts are made in order to include other people beyond the department or company? (rallies, demos)
21. Are the means of production being used/appropriated during the strike? (excavator, computer)
22. What role do the relations among the workers, based on the work organisation, play? (cooperation, including with other departments)
23. What kinds of attempts exist to undermine or disturb the struggle? By whom? (scabbing, police repression)
24. What role do organisations from outside play? (unions, parties, supporters)
25. What do these organisations do exactly? (money, leaflets, assemblies)
26. What do the workers say about these organisations?
27. What kinds of organising have the workers tried out? (committees)
28. What kinds of problems did they have with that?
Effects
29. What are the concrete effects of the struggle? (production stops, disturbance of the work in other areas)
30. What do the workers have to say about the effects? (on other workers, clients, patients)
31. What does the media say about the struggle? How does ‘the public’ react? (newspapers, television)
The course of the struggle
32. How can the struggle develop further? (actions, extending the struggleÖ)
33. What is the mood of the workers?
34. What kind of conflicts are there between the workers? (different positions, divisions based on origin or gender)
35. How do people deal with that? (discussions, arguments)
36. How have the conflicts between each other changed during the course of the struggle?
37. What’s the reaction of the bosses towards the struggle? (redundancies, lockouts, pressure)
38. What do the workers say about that?
39. What kinds of attempts of mediation and negotiation are there? How are these organised? (strike committee, works council, union)
40. Is the end of the struggle already in sight? Why?
41. What will or has happen(ed) afterwards? (return to work, more bosses’ measures, new struggles)
Assessment
42. What do the workers have to say about the experiences they are having? (strength, weaknesses)
43. What can be done better or differently next time?
44. What connections do the workers see between their struggle and the general situation of society?
45. What connections do the workers see between struggles in other sectors?
46. Where should reports on the struggle be distributed so people can learn from it?
*** An Unnecessary Repetition – Aborted Sit-Down Strike at Harsoria Healthcare, Gurgaon –
http://www.harsoria.com/
110-111, Phase IV, Udyog Vihar, Gurgaon,
Haryana-122015,
INDIA
On 24th of April 2012 workers at Harsoria Healthcare, a manufacturer of cannula and catheters for the medical sector, engaged in a sit-down strike. We first give a general over-view concerning production and back-ground of the dispute.
The Sector and the Factory
Harsoria mainly produces for export to the European Union via Singapore and South Korea. The annual value of EU imports of syringes, needles and catheters is around 7 billion Euro. Between 2002 and 2007 imports in terms of value increased by 10 per cent annually on average, faster than the production within the EU. Around 20 per cent of the imports come from the US, 9 per cent from Mexico, only a smaller share comes from Asia. The import from Singapore – the channel through which Harsoria markets its products – constituted 0.5 per cent of EU imports. The EU imports from ‘developing countries’ grew faster at a rate of 40 per cent increase per year.
The production at Harsoria in Gurgaon started in 2005. Workers say that the raw material and components come from China. They assemble the product, it is then shipped to Singapore and South Korea. From there the company Neotec exports the medical equipment to Europe, in particular to Denmark, France, Italy. The products are marketed, amongst others, under the name Healflon TM. During the time when the disputed broke out production was running on full steam and the Gurgaon plant is still the only manufacturing unit of Harsoria in India – the attacks of the company therefore are not aiming at downsizing work-force, but at bringing them under tighter control.
The average product, such as cannula with catheter, contains around ten components. Pre-assembling work happens both by hand and with machines. The components are then assembled at a moving conveyor line, around 25 people work at one line. The individual target is around 1050 pieces per hour. If workers don’t meet this target, they are verbally abused and they run danger to not receive payment for that day, according to ‘no work no pay’-rule of the company. Workers say that at least one day’s wage per month is cut that way. Workers are often shifted from one work-station to the other.
The background of the dispute
Workers at Harsoria joined a union in 2010, in March 2011 union and management engaged in a three year agreement. In April 2011 the company provoked workers, which lead to a sit-down strike. After union leaders asked workers to come out they were victimised by police and administration, see GurgaonWorkersNews no.45.
https://gurgaonworkersnews.wordpress.com/2011/12/04/gurgaonworkersnews-no-45-december-2011/#fn4
On 27th of April union and management came to an agreement concerning the dispute, which left nine of the sacked workers outside. many of the formerly ‘company casual workers’, were forced to be re-hired through contractors.
In April 2011 there had been 203 ‘company casuals’, meaning that workers are hired by the company directly, but as casual workers with lower wages and less ‘job security’. After April 2011 the company forced these casuals to sign contracts with a contractor, re-moving them from the company pay-roll. When the current dispute started there were only around 60 casuals left, of whom only 15 were working inside the factory, the rest were fighting cases for re-instatement after having been sacked or suspended.
On 16th of December 2011 the company accused workers to engage in a slow-down and suspended 9 permanent workers on 19th of December 2011. The company claimed that between June 2011 and January 2012 production levels had dropped by 31 per cent. The company reacted by cutting workers’ wages by around 35 per cent during the period from November 2011 to January 2012.
On 1st of January 2012 around 40 casual workers were dismissed by management. At the same time management forced permanents to become ‘staff’, which has a different legal status from being ‘workman’. Around 22 permanent workers accepted the shift, most of them in the tool room. In early 2012 union elections took place and three sacked permanent workers were elected as union leaders. The company refused to accept them. Other permanent workers were lected, the company also refused to recognise them.
The current dispute
On 22nd of April 2012 several workers received letters of termination. On 24th of April workers in A- and B-shift decided to stop work, sit-down in the factory and stay there, while the C-shift established a protest camp in front of the plant. At that time 252 permanent, 15 casuals and 400 to 500 workers hired through six contractors were employed at Harsoria. At the point the workers hired through contractor had not been paid their March wages yet. The demands of the workers included payment of Deepawali bonus and regularisation of the services of casual and contract workers. The workers were also protesting against the frequent change in their departments, delay in payment of salary, increased work intensity and non-payment of loyalty bonus of about Rs. 1500 per month on completion of 4 years with the company.
During the sit-down strike workers did not stop management from coming and going, meaning that 100 management people were inside the factory most of the time. Workers did not block the gates or tried to stop them otherwise – like Maruti Suzuki workers did during the occupation by controling the gates through forming ‘workers’ chains’. Workers hired through contractors who sat inside with their permanent colleagues started to leave the factory one by one. HMS union representatives declared that ‘sit-down strikes can legally only last 72 hours’. Management did not show up for the negotiations at the Labour Commissioner on 27th of April. Instead, at 11:30 pm the same day around 50 – 100 bouncers arrived in cars, armed with hockey bats. Management arrived with them and negotiations started with the factory union leaders. At the time around 200 workers were outside the factory, amongst them the HMS factory union leaders, and 400 workers were inside. The bouncers went inside the factory and threatened the workers. The police arrived one hour after having been called by the workers, but they just watched the scene. The bouncers left the factory shortly after arrival of the police – management sent them out through a back gate. Workers inside called the union leaders outside and asked for advice. They said that workers should not resist and answer to the provocation of the management, but come out peacefully. This is what the workers did, and according to workers there was no debate about the leaders decision. At the same day a court order had been issued that workers are not allowed to stay within 50 metres distance of the factory. On the 27th of April around 37 FIRs had been filed against workers for breaking this court order.
The HMS leaders decided to vacate the protest camp in front of the factory and leave the industrial area, instead stage a sit-down protest at the DLC, a rather isolated spot in the administrative district of old Gurgaon. At the same time management re-started production with 100 management people and 30 to 40 workers newly hired through contractor. On 28th of April a demonstration was organised in Gurgaon, around 600 Harsoria workers and 200 other HMS members took part, amongst others workers from LUMAX company. Another negotiation date on 30th of April lead to no result. On 2nd and 3rd of May, after some confrontation near the factory, FIR were filed by the police against 21 Harsoria workers. By 6th of May the number of suspended workers had increased to around 100 and 18 workers had been sacked. On 6th of May the police threatened workers in front of the DLC office. Workers’ leaders propose to go on hungerstrike.
Missed opportunities
The Harsoria factory is close to the rear-gate of the Maruti Gurgaon plant, there are many factories in the vicinity, also a huge Airtel call centre employing over 1,000 call centre workers. According to their own estimation Harsoria workers did not try to establish contacts with workers in neighbouring factories or tell them about their conflict. They were generally open to the idea of making placards in order to inform and debate with workers who arrive in thousands in Udyog Vihar for the morning shift – but no step was undertaken. One of the neighbouring factories is Anu Auto, an automobile supplier manufacturing parts for Maruti. Mainly young unmarried female workers are employed, they arrive in company buses, which makes communication more difficult. Harsoria workers told that when they started shouting slogans in front of the factory Anu Auto management got nervous and asked Harsoria management to make the workers stop shouting. According to one Harsoria worker, when one of the Anu Auto workers asked management why these workers were outside with a tent and shouting the manager responded that is was something related to the death of a family member of one of the Harsoria workers.
Another linkage both on the basis of sector and current tension could have been established with the many Eastern Medikit workers in the same industrial area. These workers also manufacture medical equipment and face wage delays and dismissals. One may think that the fact that both at Harsoria and Eastern Medikit a HMS union is active should have facilitated the linking up of workers, but it seems that the opposite is the case. At this point we can refer to the union position towards the wildcat strikes of casual workers at Medikit in 2007.
https://gurgaonworkersnews.wordpress.com/gurgaonworkersnews-no911/#fn4
The short report below published in Faridabad Majdoor Samachar in April 2012 nevertheless demonstrated the missed chance.
Eastern Medikit Worker
The company has started to delay wage payments also to the permanent workers of its factories in Gurgaon. The casual workers protest in one form or the other every month in order to get paid. In the factory on Plot 292, Phase II the casual workers laid down tools at 2 pm on 21st of December – by 6 to 7 pm the emergency lights went on and they got their November wages. In order to keep workers under control management in the plant on Plot 196, Phase I called the police inside the factory. Until 24th of December, the November wages were not been paid. Eastern Medikit keeps so-called D-category workers in each factory, they work 12 hours a day, day in day out, but receive no PF. In April 2012 workers reported that the company had sacked many of the casual workers in factories on Plot 195-6 and 205-6 in Udyog Vihar Phase I and Plot 292, Phase II, only 200 to 250 casual workers are left. These workers have not been paid their March wages (27th of April). The permanent workers were paid between 21st and 25th of April. Since 15th of April also the permanent workers have to work on two 12-hours shifts.
*** Lock-Out at Automobile Supplier Senior Flexonics, Manesar –
Plot No.89, Sector 8
IMT Manesar
Gurgaon – 122050 (Haryana)
India
T: +91 124 438 7704
F: +91 124 438 7703
E: sipl@seniorauto.co.in
W: http://www.seniorauto.co.in
http://www.senior-flexonics.com/
Workers at multinational Senior Flexonics in Manesar registered a trade union and put forward a demand notice. Subsequently they were locked out from early January till late February 2012. In the factory workers manufacture parts for silencers used in vehicles of JCB, Tata, and Ashok Leyland. They also produce hose pipes for vehicles for export.
The company
Senior Flexonics (India) Ltd. belongs to the multinational Flexonics group, ‘originally’ based in the UK, a parts manufacturer for aerospace, marine, defence, energy and automobile industry. According to company sources Flexonics is the “largest manufacturer of flexible automotive components in the world, with manufacturing and distribution facilities on six continents.”Automobile parts manufacturing plants are situated, amongst others in/with Bartlett (USA), Blois (France), Canada (Canada), Cape Town (South Africa), Crumlin (UK), Kassel (Germany), New Delhi (India), Olomouc (Czech Republic), Pathway (USA), Sao Paulo (Brazil), Senior Hargreaves (UK). Flexonics manufactures exhaust connectors, decouplers, exhaust gas recirculating tubes generally for exhaust applications in passenger cars, SUV’s and light trucks; and diesel common rails and fuel pipes, for passenger cars and the heavy duty diesel engine market. In 2004, Flexonics workers in the South Wales UK factory engaged in a series of one day strikes over shift patterns. After lengthy negotiation an enhanced sick pay scheme was agreed but the company refused to budge on the shift pattern. The day shift was longer than the morning and afternoon shifts – and workers wanted equal length shifts. In 2004, Flexonics US plant in Tennessee sacked 50 out of 80 workers and shifted the factory to Texas. Workers in Tennessee had been locked out earlier on.
The dispute
Senior Flexonics Worker
(Plot 89, Sector 8, IMT Manesar)
In the factory workers manufacture parts for silencers used in vehicles of JCB, Tata, and Ashok Leyland. They also produce hose pipes for vehicles for export. The shift starts 6 am in the morning, if you arrive later than 5:55 am you are stopped at the gate. meal breaks are 25 minutes, though they say they are 30 minutes. There used to be three 8-hours shifts, since June 2011 there are two 12-hours shifts. They force you to work overtime – they give a call to the gate and tell them not to let you go. The general manager says things like: I hang you up by the feet, I remove your pants. A lot of hands get mutilated by the power-presses, the company does not fill in accident forms, they kick you out and you have to pay for treatment, 30 per cent of the workers don’t have an ESI card. In the factory there are 67 permanent workers, 40 casuals, and 200 workers hired through three different contractors. After working there for 10 years continuously, workers are still ‘temporary’. In February 2009 the factory shifted from Gurgaon Udyog Vihar to Manesar. During this transfer time management said that all temporary workers will be made permanent and that the company will operate buses. Neither happened. But they stopped paying work clothes cleaning allowances to the permanent workers, they stopped paying LTA and incentive bonus. The wages of the permanents are also low, after 15 years you earn only 6,340 Rs. The temporary and casual workers where never paid any bonuses. Yes, they pay double for overtime, but the contractor embezzles at least 400 to 500 Rs per month. Wages are paid delayed and irregularly. The permanent workers started a process to get a union recognised in the factory. The recognition was given on the 23rd of December 2011 – a demand letter had been given to the company already three month earlier. The labour department came to the company for negotiations several times, but stopped doing that in December. Apart from the demand for a wage increase for the permanent workers the list contained the demand that workers should be made permanent after a year of employment, buses should be provided, a canteen. On the 9th of January, after the weekly holiday, the workers found the gates of the company locked. When they asked management said that they should first sign the code of conduct and then they can enter. No worker signed, around 150 workers decided to stay outside. The same in the B-shift, so that 300 workers sat outside. Some went to the labour department. The company said that they will take back all workers except 27 of the permanents. We asked what they had done wrong, but got no answer. On 8th of February at night the company had started to hire new workers. Within 20 days their number increased to 100 to 125, they stayed inside the factory for 24 hours. Around 50 managers and engineers also worked in production. The factory ran on two 12 hours shifts. Middle management was driven from and back to their homes escorted by guards. The company sub-contracted work to Lakki Enterprises, Gurgaon and Ajay Engineering, Faridabad and to other companies. In the Manesar factory now only assembling work was done. During a meeting with the labour department on 11th of January management said that apart from 17 permanent workers they will take everyone back on. On 13th of January they said, everyone but 12 workers, on 16th of January everyone but 4 permanents. On 18th of January they said that these four workers were dismissed, a day later they said that they were only suspended. They repeated that till the 23rd of January. The workers demonstrated in front of the labour commissioners office on 17th of January. The company send letters to workers’ homes saying that they either come to work or they will receive a dismissal letter – this troubled the family at home. The labour official said that big fish will always eat the little fish. The company did not appear to the 27th january date for negotiations. On 30th of January the labour commissioner again said that everyone apart from the four should go inside, but the company also said that they will not take on 40 of the temporary workers, that they will be shifted, On 3rd of February the company representatives did not appear, negotiations happened over the phone. On 8th of February the company said that they will only take back 50 of the temporary workers, they others will be shifted, given that the newly hired workers work more. The labour commissioner did not issue a new date and said that company and workers should sit together and come to an agreement themselves. After complaining on 16th of January the company paid the December wages on19th of January, but two permanent workers were not paid, the company said there was a problem with book-keeping. Unions called for a meeting on 8th of February, around 5 to 6,000 workers from ten different factories gathered in front of the gate. Promises of economic and other forms of support. On 15th of February the union committee will gather in Kamla Nehru Park and think about how to support the Senior Flexonics workers. – On 27th of February we were forced to come to an agreement. Four of the permanents remained suspended, and only 60 out of 109 temporary workers were taken back on. Our own demands were not taken into consideration.
*** Riots at Orient Craft and Larsen and Tubro Construction Site, Gurgaon –
In mid-March 2012 workers’ anger irrupted twice within a week in Gurgaon. On 19th of March workers at garment exporter Orient Craft rioted after a work-mate had been attacked by a contractor. On 23rd of March construction workers attacked company property in response to the death of a colleague after a work-accident.
* Orient Craft
Orient Craft runs 21 factories in India, supplying clients in Europe and the US, such as Tommy Hilfinger, Mark and Spencers, DKNY and GAP. There are five units in Sector 37, Gurgaon and several others in other parts of Gurgaon and nearby IMT Manesar. Around 80 to 90 per cent of Orient Craft workers are hired through contractors. They work 12 to 16 hours shifts, helpers are paid 4,200 Rs, most tailors are employed on piece rate. The contractors take 3 per cent commission from the workers’ piece-rate wages. the company cuts workers wages by using the excuse of bad quality: 20 to 30 per cent pieces are ‘reject’. In this sense Orient Craft is a very normal garment export company in Gurgaon.
On 19th of March a dispute took place between some workers and a contractor inside the factory. Workers had taken the previous day (Sunday) off, which angered the contractor. Workers also complained about delayed wages and embezzlement. the contractor attacked workers with a pair of scissors and injured two of them. When other workers saw the injured they started expressing their anger. There are different versions regarding the question whether 100 workers were subsequently kicked out from the factory by management people or whether they left the factory. After 100 workers were gathered in front of the plant other Orient Craft workers also came out. They were joined by workers from other factories in the vicinity, in total a group of about 2,000 workers came together and started pelting stones at the Orient Craft factory glass-front and also at those of other factories. When management called the police and they arrived, a AASP police car was burnt. Three hours riot of commotion followed, between 12 and 20 bikes were burnt, two trucks, one SUV, another police car and a fire engine on fire. Police arrived in greater numbers and attacked tried to disperse the crowd by lathi (clubs) attack.
In the meantime management had brought the wounded workers to the nearby private Sunrise Hospital. They threatened them and offered money in order to move them to change their official version of the attack through the contractor. In the end the official version claimed that workers were injured by falling onto sharp pieces of glass while trying to flee from the commotion. According to some sources police filed case against 1,000 unknown people and against 9 workers for attempted murder. The contractor was released shortly after is now on bail.
After the riot management tried to appease workers. During the first three days after the riot the factory remained shut, then all workers are allowed to come back to work. According to some sources half of the work-force did not return to work, partly out of fear of the 80 to 100 police who were stationed in front of the factory at least till the 26th of April, one week after the incident. Inside the plant the company tried to normalise the situation. Workers said that for some days the work load was less and supervisors’ behaviour much better. Meanwhile riots are brewing in thousand other factories and hearts…
From: Faridabad Majdoor Samachar, January to March 2012
Minimum Wages (January – February 2012)
Delhi: 6,656 Rs (unskilled) / 8,112 Rs (skilled)
Haryana: 4,847 Rs (unskilled) / 5,497 Rs (skilled)
Orient Craft Worker
(Plot 15, Sector 5, IMT Manesar)
Around six months ago management told workers that they would be given a bicycle. The 3,000 workers hired through contractor were not promised anything. Around 200 permanent workers with over 1 year seniority were supposed to sign a form. They never received their bike. Normally we work from 9 am till 6 pm, on three or four days per week till midnight. They pay double rate overtime, but the management swears a lot at us.
Adigear International Worker
(Plot 189, Sector 4, IMT Manesar)
Around 700 workers manufacture garments for Adidas, Puma, Reebok and others – working from 9:30 am till 1 am every day. Management stops workers from leaving earlier. The general manager takes company cards away from workers who want to leave. After wages of the previous two months had not been paid workers stopped working on 15th of December. This lasted till 1 pm, then the company called goons from PSO Security. All worker left the factory and gathered outside. the company then paid wages in installments.
Astro Fashions Worker
(Plot 69, Sector 4, IMT Manesar)
There are around 150 workers, we work from 9 am till 8 pm and 20 times per months they make us work till 1 am. Wages are delayed every month. On 12th of January 2012 the workers in the finishing department asked for their December wages from the boss. The company management called thugs in cars as response. The workers were finally paid on 21st of January. Money for ESI and PF is cut from workers wages, but they don’t get the benefit.
Shahi Export House Worker
(Pot 1, Sector 28, Faridabad)
There are between 8,000 and 10,000 workers employed, half of them men, half women. In the sewing department there are 47 lines with more than 25 machines each. In the computer embroidery department they run two 12 hours shifts. In the cutting department they also cut the cloth for Shahi factories in NOIDA, Surajpur and Okhla. In the cutting department more than 2,000 workers are hired through contractor. They don’t get ESI or PF and once an inspector comes to the plant, they are kicked out before hand. The wages of the permanent workers are also low, even after 15 years of employment you get only the minimum wage. There is a lot of verbal abuse going on. There is always tension between workers and management – we have to see what we can do. In 2000 the women in the embroidery department were in the first line when we resisted management. During the strike in 2009 the workers in the sampling department were the first.
* Construction Site
Only four days after Orient craft riot, on 23rd of March 2012, as a response to a fatal work accident construction workers in Gurgaon, Sector 58 expressed their anger. From the main-stream media:
“Thousands of labourers went on a rampage on Friday when a worker died after falling from the sixth floor of a building under construction in Sector 58. Angry labourers working in the area torched a police Gypsy, damaged about a dozen more vehicles and demolished a section of the housing project. Labourers alleged that the contractor did not provide them with adequate safety equipment. “Hasan was breathing when he fell. The contractor and the management’s employees kept watching this instead of taking him to hospital,” said labourers Jeetu and Shamsher. As a worker confirmed that the injured labourer had died in hospital, around 4,000 labourers working at different sites in Sector 58 turned violent. They damaged Ireo’s site office and set it on fire. Some others demolished a portion of the housing project while many blocked the road and vandalized several vehicles, including a BMW.
The cops were rescued almost an hour later when a heavy contingent of police force reached the site and resorted to lathi-charge to disburse the crowd. Seven policemen and many labourers were injured. The 28-floor highrise is part of private builder IREO’s Grand Arch residential project. “The construction of the Grand Arch project is being undertaken by L&T Ltd,” the spokesperson said.”
Comrades who have been to the site reported that during the following three days police arrested up to 300 workers from nearby slums, 57 workers were charged with attempted murder – other sources speak of 23 arrests and 200 cases filed. they also said that workers in Beharmpur Sector 58 were aware of the events at Orient Craft some days before. Around ,500 of the construction workers are hired through contractor, one of them Alufit Private Limited. They work seven days a week, 12 to 14 hours a day. The deceased worker had worked without a day off since December 2011.
After the two riots the media has obviously full of reports, looking for reasons, trying to find responsibles, trying to understand this alien force, invisible during most of the time, frequently turning into scary uncontrolled masses…
(sources: Sangharshrat Mehnatkash no.7; Fact Finding by comrades of ‘Majdoor’ and Inqalabi Majdoor Kendra, Mazdoor Bigul, April 2012)
*** Workers’ Sirens at Lakhani Vardan Samuh, Faridabad –
From December 2011 till April 2012 Lakhani workers in Faridabad were engaged in various forms of struggle about delay of wage payments: from direct action on factory grounds to wildcat strikes, to street blockades and demonstrations to governmental institutions.
Lakhani Vardan Samuh Worker
(Plot 265, Sector 24, Faridabad)
The start of the shift at 8 am and at the end of the shift at 4:30 pm is marked by the sound of a hooter siren. The hooter also indicates the meal breaks at 12 and 12:30 pm. One day the hooter went of at 2:30 pm. What happened? the supervisors and managers told workers to gather at the HR department, everyone assembled. Around 1,500 to 2,000 male and female workers chatter amongst each other. A big commotion and noise. the general manager tries to give a speech, there are difficulties with the microphone. Even if one tried to listen attentively one had difficulties to understand what was said and why. It was a speech about fire safety and how to escape from fire. Then he talked about how to put out a fire. The fire officer showed a gas cylinder and asked: “Do you know what kind of gas is in this cylinder?”. None of the workers said a word. “This is CO2 gas,” the officer answered his question. “If the fire is related to electrical faults, if it is burning petrol or thinner, then you can use this gas to put out the fire”. “If cloth or rubber has caught fire, you can douse it with this gas. How does the cylinder work?””Whenever you hear the hooter outside of the normal times, this means fire alarm and you have to leave the factory immediately, come outside and gather here.” The meeting went on for one hour. The next day suddenly the hooter went off at 10 am. It looked like a fire alarm, so workers stopped working and all came outside. Men and women workers gather at the HR department. People looked around, but there was no smoke to be seen. Then workers started to shout: “Give us our wages! Give us our wages!”.
When the hooter went of supervisors, managers and the genertal manager also left the factory. The general called the security guards over the phone. They arrived. the HR manager told the workers: “There is no fire he. Go back to your work now.” The officer who normally pays out the wages tried to scare the workers and shouted: “There is no fire. Move, go now!” The male and female workers just answered: “Pay out the wages!’. The general manager arrived on the scene: “the money will arrive. you will get your wage this evening. Now back tob work, the hooter is faulty, there is no fire.” The wages were not paid that evening. The next day workers stopped work at noon and production kept being halted till 4:30 pm. The wages were not paid. On the third day workers stopped working at 10 am and production did not resume till end of shift. On the fourth day the managers distributed the wages to the workers. At Lakhani Vardan Samuh factory workers don’t receive the complete wages and they receive them with ten days delay.
This hooter incident happened in December 2011. Since then the trouble continued. When February wages were not paid by 22nd of March 2012 the workers in the clothing department of the factory on Plot 265 in Sector 24 went on a slow down on 22nd and 23rd of March and stopped production again on 24th. After the weekly day off the wildcat strike continued on 26th and 27th. On the 28th the managers distributed wages in the factory. the factory manufactures, amongst others PUMA shoes. At the Lakhani Rubber Udyog factory on Plot 131 in Sector 24, 300 workers in the mixing department stopped work after they did not receive their Holi wages, but an advance instead. In this department workers where paid on 7th of March 2012, whereas payments are still outstanding in the other departments.
Again on 21st of April in the Lakhani factory on Plot 265 in Sector 24, when March wages were not paid, workers started to work slower. On 23rd of April workers entered the factory, but did not start work. None of the company officers said a word. Workers started to eat their lunch whenever and wherever they liked. A worker told the general manager: “The landlord asks for the rent. The ration shop-keeper asks for his money. So, pay our wages.” A female worker said: “My mother had an accident. Pay our wages.” The general manager responded: “There is no money. you will be paid within the next days.” Wages were not paid and production lay idle from 24th to 26th of April 2012. Workers started to fool around and on 27th of April a big group of workers went from one department to the other. They kicked around stools, played with the machines, used oil barrels as drums and walked towards the HR department. In order to stop workers the security guards let down the shutter. This game lasted from 8 am till about mid-day. At 3 pm the company put up a notice: “There is holiday from 28th of April till 6th of May. Return to work on 7th of May.” Workers left the factory at 4:30 pm. The night-shift workers found the notice and told the security guard to remove it. Who will pay our wages? The officer of the HR department said that all workers should arrive at 8 am as usual. The next day on 28th of April workers arrived and were not stopped at the gate. Those workers who did not come were called by phone and asked to come. Around 800 to 1,000 male and female workers were inside the factory. No one worked, there was quite some commotion. they went to the HR department, but there was no one, it was locked. Workers caused some disorder in the canteen. Workers from Lakhani factory, Plot 144 arrived at Plot 265 factory at 10 am. A lot of workers were together. Workers left the factory and blocked the street in front of it. Some police arrived. the street remained blocked for two hours, the the workers of 144 left in a demonstration to the labour minister of Haryana. After a negotiation meeting was promised by the labour minister, on 30th of April Lakhani workers found their factory on Plot 265 and 144 locked. Workers blocked the National Highway in response, but police was able to remove them fairly quickly. On 1st of May more demonstrations in town centre, while negotiations remained without result. Labour administration announced that Lakhani will pay the wages by 9th of May, but that till 8th of May the factory will remain closed. More demonstrations in front of administrations on 2nd and 3rd of May, during which demonstrators were attacked by company goons. As far as we know little steps were undertaken to relate to workers in other ‘running’ Lakhani factories or to other factory workers directly.
*** Unrest at Theme Export Garment Factory, Okhla –
Theme Export Worker
(Z-21, PH-2, Okhla Industrial Area, Delhi – 110020)
+(91)-(11)-40547861, 26301269
Worker employed at theme Export do not receive the minimum wage – helpers are paid 5,200 Rs, checkers are paid 6,500 Rs and tailors are paid 250 Rs day wages. None of the 300 workers get ESI or PF. The working hours are from 9:30 am till 1 am, sometimes workers have to work ‘full-nights’ till next day 6 am. Over-time is paid at single rate. The wages are paid with delay – when March wages were not paid by 16th of April workers asked the ‘production incharge’ about it. The incharge said that he will speak to the general manager about it and left. He returned and promised that wages will be paid by 4 pm that day. “If you start handing out the wages by 4 pm, how do you want to finish this task by 5:30 pm”, workers asked. On pay-day workers usually work only till 5:30 pm. Workers told the incharge to speak to the general manager again and he fled the production department. Workers in response started to leave the factory. When the security guards tried to stop them they were pushed aside. The factory on the neighbouring plot also belongs to Theme Export and the Head Office of the company is situated there. When the workers arrived there the security guards locked the gates from inside. People pushed against the gate, some workers jumped over the wall and opened the gate from the inside. The general manager tried to appease the situation and told workers that wages will arrive within the next days. When he saw that the situation was getting out of hand the manager called the police. two police men arrived and tried to get workers out, but during the attempt one of them fell to the ground. From the neighbouring police station two police cars with 20 police arrived. In the meanwhile workers from other factories and inhabitants of the nearby Sanjay Colony had joined the crowd. The street was blocked. People started to pick up stones from road works. the police got afraid and kept outside of the factory. The police chief then said that he will make sure that wages will be paid by 5:30 pm. The managers then went to the bank and started handing out wages by 5 pm, by 8 pm everyone was paid.
*** Revealing Potentials – Struggle at Globe Capacitor, Faridabad –
Globe Capacitor Ltd. Worker
H.O & WORKS: GLOBE CAPACITORS LTD.
Address : 30/8, Industrial Area, N.I.T,
Faridabad ñ 121001 (INDIA)
Ph. : +91-129-4275500
Fax : +91-129-4275555
http://www.globecapacitors.com/
Globe Capacitors production capacity has grown from 1 million pieces in 1987 to 28 million pieces per annum in 2011. The plant and machinery are imported from Korea, Europe, Japan, Taiwan, China. The factory manufactures capacitors from 1 MMD to 150 MMD for L&G, Samsung, GI Motor and Orient Pankha and for export (PSA, MEWE, Alco).
(Plot 30/8, Industrial Area, Faridabad)
The workers have to work 10.5 hours, but only 8 hours show on records and only 8 hours are paid. Out of 500 workers employed here around 50 female workers and 250 male workers don’t get ESI and PF and are not paid the statutory bank holidays. these 300 workers are paid 175 Rs for 8 hours, so their monthly wage for 26 days amounts to only 3,640 Rs. those workers who receive ESI and PF get between 4,644 and 5,650 Rs. the shift times are from 8 am till 8:30 pm and from 8 pm till 8 am. Of 12.5 hours the company calls 2 hours overtime, they pay single rate. On Sunday workers have to work till 6:30 pm. In a month the workers have to work 10 to 12 ‘full nights’, meaning workers have to work from 8 am till next morning 7:30 am, they then have half an hour break and work again from 8 am till 8 pm. The workers talk to each other while working at the line. They talk during the meal breaks. They decide to take a collective step in order to get higher wages, 8 hours working day, double payment for overtime. there are no (union) leaders. From 20th of March workers refuse to work full-nights. After receiving their February wages on 7th of March, workers from then on clock off at 6:30 pm. No worker stays till 8:30 pm – at 7:30 the middle management is forced to load the trucks themselves. All workers take a day off on Sundays. If the company decides to refuse the workers demand the workers will start to clock off at 4:30 pm.
On 8th of April, a Sunday, workers had refused to come to work. On the 9th of April they went inside the factory, went to their respective assembly lines, sat down and did not start work. The company chairman arrived, walked around the plant, but did not address the workers. Supervisors announced that a meeting will take place at 1 pm. At 1 pm, on the third floor in the wiring department all company officers and day shift workers assembled and the chairman talked for one hour: “We have taken loans of 60 crore Rs from the banks. Even our family house is on mortgage. We have to pay taxes. We take the risk of going to foreign countries to find clients and get orders. Give us time to think about the issue, give us time till 23rd of April.” Workers did not reply and went into lunch break. they then went back to the assembly lines, ‘resumed work’, but actually hardly worked at all. Workers left the factory early at 4:30 pm, they passed two gates, but the main gate was locked. The managing director, son of the company chairman arrived and said: “We asked to give time. We will also decide how many hours you will work. No please go back to work.” Workers went back to their work-stations, but hardly worked at all. At 6:30 pm they left the factory. On 10th of April production resumed. Three days later the managing director called workers again and said: “First increase production levels by 25 per cent, then we can think about your wages.” Workers said that there will be no production increase and that they will leave at 4:30 pm as long as their demands are not met: permanent contracts for all casual workers who worked in the factory for more than two years; ESI and PF for all; holiday pay; payment of minimum wages. Next day the same thing happened. Workers said that even now when they work less the work load is too high. “We won’t increase production in fixed percentage.” On 16th of April the company agreed to increase the wages of permanent workers by 1,900 to 2,200 Rs. The wages of the workers was increased from 3,640 Rs to the minimum wage of 4,8560 Rs. Though none of the 350 (company) casual workers have been given ESI and PF and no casual worker has been made permanent. the permanent workers now seem contented with their wage increase. From 23rd of April the managing director started standing at the main gate to see who leaves, also the cameras inside the factory have been made operative again. the company also has hired 100 additional workers through contractor. On the basis of small excuses around 10 to 12 casual workers were fired in April 2012. the shift times are again from 8 am till 8:30 pm and Sundays from 8 am till 6:30 pm.
Before the Globe Capacitor Workers undertook their collective steps production of the factory had been interrupted due to lack of films needed to manufacture capacitors. The film-manufacturing company Superelectro Films in Faridabad, Sector IV, plot 3A – in several kilometres distance from the Globe Capacitor plant – could not deliver the films due to wildcat strike of their workers. These workers were dissatisfied with the fact that, like at Globe Capacitor, the company management paid and documented only 8 hours of work though actually workers worked 10.5 hours. Shortly after the films arrived again, on 2nd of April 2012, 250 female workers at Abhirashi Impex factory right in front of Globe Capacitor plant refused to enter the factory, while 200 of their male work-mates went inside. The same problem: the company paid only 8 hours, while workers worked more than 10 hours. The managing director arrived shortly after and reassured the women workers that they will be paid 5,000 Rs for a 8-hours shift.
Comments
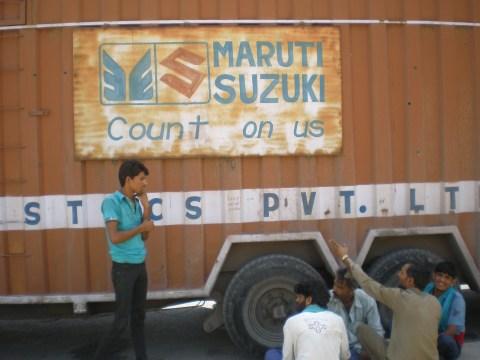
Towards a Workers’ Organisation (Part Two)
/ Material on Struggle at Maruti Suzuki
1) Introduction
2) On Organisation and Inquiry
3) Material on Class Composition at Maruti Suzuki
3.1) State of Workers’ Collectivity one Year after the Occupations (June 2012)
3.2) State and Limitations of the Trade Union at Maruti Suzuki
3.3) Preliminary Thoughts on the Unrest of the 18th of July 2012
3.4) Theses for the Future Armament of Workers’ Struggle at Maruti and Beyond
4) Workers’ Reports
4.1) Reports from Maruti Manesar Workers
4.1.1) Press-Shop Worker
4.1.2) Weld-Shop Workers
4.1.3) Paint-Shop Workers
4.1.4) Bumper-Shop Worker
4.1.5) Final Assembly Workers
4.1.6) Canteen and Housekeeping Workers
4.2) Reports from Suzuki Powertrain Workers (Engine and Gearbox)
4.3) Report from Maruti Gurgaon Worker (Engine-Shop)
4.4) Reports from Maruti Supply-Chain Workers
4.4.1) Asti Electronics Worker
4.4.2) Sanden Vikas Worker
4.5) Report on Life in Aliyar, a Workers’ Village in Manesar Industrial Zone
5) Conversation with Comrade on Practical Engagement during the Maruti Struggle in 2011
6) Comments on and Relevant Parts of “The Maruti Story”, Biography of the Gurgaon Factory by R.C Bhargava, Maruti Chairman
7) Material on situation at Suzuki in Hungary
8) Appendix
8.1) Open Letter on Maruti by Mouvement Communiste to Comrades in Delhi
8.2) Pamphlet by Mouvement Communiste on Maruti Struggle and Leaflet on Struggle at Citroen PSA in France
8.3) Proposal for Critical Debate on ‘Academic Research’
8.4) Phd by Bose on Automobile Industry in Delhi
8.5) Links to Future Readings
1) Introduction
Mobile Tea Stall in Manesar – A Workers’ Meeting Place…
The current repression against Maruti workers is severe – since the unrest on 18th of July 2012 over 150 workers have been arrested, more than 500 permanent workers have been fired, more than 1,500 temporary workers might have lost their – or rather ‘this’ – job and over a thousand state and private cops have been stationed in and around the Maruti factory in order to secure industrial ‘peace’. Repression tends to focus our view and acts on itself – it forces us to react, instead of acting ourselves. These are difficult times for engaging in critical analysis of the struggles of our own class. To criticise our own activities while the enemy attacks seems rather paradox or untimely – but we think it is necessary.
In this newsletter we want to continue the debate about ‘workers’ organisation’, based on what we see as both pre-condition and process of organisation: workers’ self-inquiry into the production process, how it constitutes the working class and how it can be transformed into the basis of self-organised attack on the existing social relations. We present some general and historical thoughts about the relationship between inquiry and workers’ organisation, but our focus is concrete material on the conditions at Maruti after the waves of struggle in 2011 – and a proposal to engage in a process of workers’ inquiry in Manesar.
Between April and June 2012 we asked workers at Maruti and automobile suppliers the following questions: how does your collectivity look like now, a few months after the strike? which changes took places since then, which either weakened or strengthened your collectivity? what did management do in order to undermine your collectivity? what did workers do or can do in order to strengthen and extend the collectivity? which role does the new union play in this process of de- and re-composing workers’ organisational basis?
We summarised a preliminary balance-sheet based on these conversations, which forms the core-part of this newsletter. In addition there is further material: workers’ reports from various departments at Maruti and its suppliers; an interview with a comrade of a Marxist-Leninist group reflecting on his experiences during the 2011 struggles; a summary of ‘The Maruti Story’, written by the Maruti chairman, about the history of the Maruti Gurgaon plant, from the enemy’s perspective. A comrade summarise material on the Suzuki Hungary plant, which supplies the global markets with the same models which are produced in Manesar – and in 2005 workers showed their discontent about the working conditions. To illustrate the newsletter we took some photographs in Manesar and surrounding villages.
Friends of Faridabad Majdoor Samachar distribute the workers’ newspaper every month, both in front of the Maruti Manesar and Maruti Gurgaon plant – we hope you will help out with distribution and/or contribute to the debate. We hope this newsletter provides some instigating material.
Auto Slaves (Graveyard Shift – Stamping Plant)
With automatic movements timed to great
Machines, these metal-workers seem to reel
In some weird dance. Like marionettes they wheel
With some insane music at a maddening rate.
Automatons… What if they learn to hate
Machines whose hungry maws demand a meal
Of metal-piece upon piece of sweat-stained steel?
They work. Monotony and madness wait…
For these are human beings racked with pain,
Grotesquely hued by blue-green mercury lights…
Monotony within this noisy hell
Will breed maggots of madness in the brain
Stop the tongue so it never tell
Of torturing toil through these unending nights
(from: Industrial Worker, IWW Newspaper, 1930)
2) Organisation and Inquiry
Over 2,000 Trucks come and go daily from the Maruti Manesar plant…
The question of communism is the question of collective criticism of the existing state of being, the class power to change it and the social productivity to create an alternative. Answers can only be found in the material process which re-produces at the same time (but contradictively) both society and class relations and the subjective experience of organisation of the working class within. In other words: between potentials and their realisation. The process of organisation of collective power and the process of analysis of these objective and subjective conditions are therefore one.
Most of the leftist balance-sheets of the 2011 Maruti struggle remain on the surface of things. Groups of radical left are caged within their usual categorisation of ‘political and economical’ struggle depending on their own influence on the struggle. Those who had a closer influence on ‘the leadership’ declare that the Maruti struggle was a ‘political advancement’, given that workers’ did not fight primarily for higher wages and other economical demands, but for the political (and ‘constitutional’) right to be organised in a trade union. The historical problem of workers’ struggle and the concrete weak-point of the Maruti dispute – the development of institutionalisation and formalisation of ‘leadership’ – is glorified as ‘political expression of advanced consciousness’, when they claim that after the ‘sell-out’ of the old leadership the new union leadership emerged without major transitional problems. Even less serious are the ways that other groups discard the struggle as ‘economical’ with lack of political leadership. In this way the potentials and limitations of the struggle won’t be understood.
“The extend to which the Maruti struggle should have recomposed the left, it did not. There are some structural limitations for that. The vision of organisation which is distant from workers’ life and struggles inhibits to take lessons from struggles. This cannot be subjectively dissolved, this depends on the development of working class struggle, on reflections on it and the review of Indian left movements. That depends on the fact how we deal with erstwhile successful strategies which now become more and more problematic. The critique of left groups is an internal criticism, a self-critical approach – of the left movement vis-a-vis the working class movement.” (Interview with comrade -see this newsletter)
The underlying motivations and driving forces of the struggle – which surface officially as a common slogan and demand for ‘union’ – are not easily to be categorised as ‘economical or political’, if at all, they have to defined seen as systemical.
a) it was a struggle against the factory system, both against its personal and impersonal disciplinary agents (supervisors and machinery) – under the specific situation of Maruti pushing work-loads to limits before being able to leap into expansion (B- and C-plant), driven by the post-2008 global squeeze and race into over-capacities
b) it was a struggle of workers who felt their collective power of being in the centre of both the current economical regime in India (industrial development, integration into the global market on basis of highly productive cheap labour) and the productive cooperation of hundred thousand workers in the automobile supply-chain
c) it was a struggle about the political question of workers’ consumption: current wage-levels do not allow workers in the most advanced industrial sectors to reproduce themselves and their families and/or to take part in the wider society around them; a claim towards higher wages under these conditions is also a political claim for ‘equality’ and in struggle turns into a measure of class power
d) the struggle was driven by the temporary status of workers, which forms a systemic part of the current regime: temporary not only in terms of employment, but also in terms of the urban-rural status of the workers; workers can not be disciplined anymore with the prospect of a ‘rural petty bourgeois / peasant future’ (small trader, peasant, artisan), but the current set-up does not allow them to ‘save money for a settled urban future’ either; the current state of being is symbolised in the division of the working day into ‘stress of the assembly-line’ and ‘boredom of the dormitory villages’, whose main offer of leisure are cheap multi-media mobile-phones of Chinese brand
e) the struggle created a new collectivity which broke with previous limitations and divisions; in the course of the struggle workers had to confront and break the law; the focus on the official demand of union recognition did not help to realise the potentials of generalisation of the struggle: the general discontent in the area;
Instead of crying about victimisation of workers and the denial of rights we have to analyse the systemic tension – the unability of the current system to offer anything else and the collective power of workers not to accept this. The struggle at Maruti asked systemic questions and through wildcat occupations engaged in practical criticism, but workers did not find a collective language towards other workers beyond Maruti. An organised workers’ inquiry into the current conditions within and beyond Maruti is necessary – see also the contribution and open letter of comrades of the collective Mouvement Communiste from France after a visit in Manesar (appendix).
The Historical Legacy of Workers’ Inquiry
For this effort we can refer to historical experiences within the communist movement, from Marx’s workers’ questionaire to the initiatives of the Italian Operaismo in the early and late 1960s. The comrades back then were confronted with a double crisis of the communist movement. By 1956 it was clear for most workers that the emancipative elements of the ‘old communist movement’ in form of the CPs were finally dead: disarmament of workers after 1945 through the Italian CPI, official party line ‘participation on parliamentary level and national development’, massacre of struggling workers in Berlin 1953 and Hungary 1956 through the ‘workers’ state’. At the same time the material base of the ‘old communist movement’ (peasants and skilled workers in the manufacturing industries) were undermined by social re-structuring. The workers in the north of Italy were confronted with the introduction of assembly line production and the ability of capital to employ peasant-workers from the poorer south. Both unions and political parties had given up the shop-floor as a space of social struggle and provided therefore no answers for the new composition of old skilled workers and seemingly ‘unorganised’ migrant industrial workers. In this situation dissidents of the CPI and PSI (Socialist Party) engaged in a collective effort of workers inquiry, in rounds of workers reporting about the new conditions, trying to formulate political strategies and to circulate it amongst other workers. Following are passages from a longer article on workers’ inquiry and the legacy of Operaismo, we then formulate some practical conclusions for their current relevance at Maruti and in Gurgaon/Manesar area.
“In the introduction to the Italian edition of the Diary of the Renault Worker, Daniel Mothé, Panzieri expanded on the antagonism in the production relation. »The book […] goes beyond the usual testimonies of the conditions of the worker, testimonies that mostly merely express sympathy with the situation of the factory worker (and no more that this). In Mothé’s diary the problems of the working class in a large modern factory, in all their complexities and specific reality, are shown step by step through the keen and thoughtful observations of the everyday life in one department. The book deals with the beginning of the rational organisation of work. There is a contradiction between on the one hand the attempt at a rational organisation of work that isolates the workers more and more; and on the other hand the conditions within which the work has to develop, that themselves lead to the constant breaking of the rules in order that the production can run and has a sense. The worker has to fight against the implementation of these ›rationalisations‹ that have to shut out any human qualified experience in order to be put into practice: even before the legitimate need to connect to the colleague next to him – a need within which appears the value of an unshakeable solidarity – and the experience of work itself which brings the worker to understand his own problems as collective ones. (Panzieri)
The industrial sociological analyses also discover conflicts everywhere. But usually the bourgeois sociologists examine these conflicts as problems that are there to be solved in order to guarantee the smooth functioning of the factory. And the ›critical‹ sociologists expose the conflicts to prove that the factory does not function perfectly. In contrast to this the comrades, schooled on Marx, took the contradiction of the work process as the starting point of the inquiry. Thereby they could understand how conflicts could also be functional for the valorisation and which functions of the hierarchy are there to prevent these conflicts turning into a united struggle.
“From a revolutionary standpoint, the act of gathering this kind of information could enable us to show how a worker fuses with his class and whether his relationship with his social group is different from a petit-bourgeois’ or bourgeois’ relationship with his or her own group. Does the proletarian connect his fate, on all levels of his existence, consciously or not, with the fate of his class? Classic expressions like class consciousness and class behaviour are often too abstract: Can we check them concretely? According to Marx, the proletarian, in contrast to the bourgeois, is not simply member of his class, he is an individual, a member of a community, and he is conscious of the fact that he can only liberate himself collectively. Can we concretely verify this Marxist assumption?” (Lefort)
›Biographical approach‹, ›intensive interviews‹… today everyone from Feminists to left Sociologists practices these inquiry methods. The difference of the ›workers’ inquiry‹ is that they started from a collective dimension: the self-constitution of the class, the detection of communism in the movement of the working class itself. »Porto Marghera [location of the petrochemical industry on the mainland across from Venice] was the laboratory in which we verified the situation with scientific methods. One could not begin to have a political discourse without what we called ›workers’ inquiry‹. We were determined to clarify once again what the workers standpoint was in concrete, because they were the social figures that were strategically relevant in the process towards the ›new‹. (Guido Bianchini)
There was a serious political confrontation within the group around the fundamental question of whether the instrument of sociology could be applied critically. This went from the tendency which reduced Marxism to a mere sociology, through the critical application of sociological instruments up to an attempt at a full abolition [Aufhebung] of the difference between inquirer and the objects of the inquiry, the workers, with the aim of ›workers’ self-inquiry‹. Both the last two positions called their practice ›Conricerca‹, word-for-word meaning; ›with-inquiry‹. Liliana Lanzardo explained in November 1994 in Turin, that today it is much clearer to see the difference between those who wanted to do an academic inquiry and those for whom it was about a political project; at the time there was no terminology at all. A few of their fellow fighters of the time are today recognised industrial sociologies in the worst sense.”
for full text: http://www.wildcat-www.de/en/wildcat/64_65/w64opera_en.htm
Negation of Academic Research
Today, more then ever, a criticism of ‘academic research’ is necessary. There are very apparent problems with academic research: material and formal dependence on state institutions, individualistic academic knowledge production, reproduction of divisions between intellectual professional and working class which leads to instrumentalisation – which applies similarly to other ‘movement professions’ such as trade union organising, labour-NGOs and labour journalism. The challenge will be to go beyond an individualistic criticism of ‘academic comrades’ – which nevertheless remains necessary – in order to ask the question of how the working class movement itself can develop collective intellectual processes and, last but not least, find the material resources for it, independent from the educational state institutions. Since trouble in Gurgaon started the area is flooded with labour NGOs and ‘researchers’. The International Metal Workers Federation (international organisation of the main institutionalised trade unions) offered larger sums of money to the new Maruti workers’ union – at a moment where the influence of the established trade unions was at a low and spaces were opened for independent generalisation of the conflict. There needs to be an open debate ‘within the movement’ about academic work, ‘revolutionary activities’ – the relation between ‘individual aspirations, recognition and wish for material security’ and collective work. Here the ‘academic comrades’ are asked, not to justify, but to explain themselves. For the time being we refer to an older text on the question of ‘union organisers’ and to a ‘letter of questions’ written for the debate with ‘academic comrades’ researching automobile workers in India – see appendix.
http://libcom.org/library/unions-new-grounds-when-work-mate-becomes-client
Towards a Workers’ Inquiry at Maruti and Beyond
The workers’ reports in this newsletter do not reflect the situations from which they emerged. Most of the Maruti workers we spoke to are workers who friends of Faridabad Majdoor Samachar and of Inqualabi Mazdoor Kendra met during the occupations in 2011 – and engaged with in discussions about their struggle. We usually meet after the distribution of Faridabad Majdoor Samachar in Aliyar or other villages in Manesar. Particularly the temporary workers, trainees and apprentices live together, four share a room, forty or more workers share a common backyard, latrine, tap. What bourgeois media describe as ‘miserable living conditions’, we see as potential and actual base-camps of proletarian collectivity. Workers of different departments, of different supplying companies, of different sectors live together. Our conversations take place in groups of five or ten. Most workers have experiences of working in other companies in Manesar or Gurgaon, everyone has friends in other factories. The temporary paint-shop workers have actively taken part in the occupations, they see the need to extend the organisational forms and to strengthen direct contacts between workers. This is the material and organic base for an organisational process.
Since the Maruti struggle in 2011 the atmosphere in Manesar has changed and in some cases workers make active use of their connectedness beyond company walls. A small, but very important example was the direct solidarity action of temporary Maruti workers of various departments for an injured temp workers at Allied Nippon, a supplying company who some of them had shared a room with – see GurgaonWorkersNews no.44/45 – and the spontaneous intervention of Maruti workers during the lock-out at nearby Senior Felxtronics – see GurgaonWorkersNews no.50. In embryonic form workers create an organisational structure – the challenge of a process of workers’ inquiry would be to turn it into a workers’ coordination. We made the following suggestions to the workers we met: put the question ‘what happened to our collectivity since October 2011’ in front of all Maruti workers. What has changed, what did management do, what did we do, how does the union help or not? Answer the questions on the level of your own department or company and invite others to do the same. Find an adequate form to pose this question: leaflet, newspaper, informal meetings. Refer to the experience of the occupations and succesful actions like like at Allied Nippon to demonstrate that the coordination can and must go beyond Maruti and can and must have practical results.
We suggest to working class activists to shift the focus from the sphere of ‘formal representation’ (small union body, negotiations, legal back-and-forth, repression) to this daily form of organisation within the production process and within the wider industrial area. Longer conversations are necessary in order to understand the set-up of Maruti, the management strategies, the potentials and difficulties for workers to form collectives on the shop-floor and to coordinate beyond. We have to see Maruti and Manesar as ‘a workers’ organisation’ in itself, with material and ideological divisions, with regional and international ties, with connections to the rural sphere. This is the organisation we have to work within and to turn into a base of workers’ power – instead of seeing it as a recruitment ground for ‘membership’. Maruti dominates the class relation not only in a material sense, dictating paces of development right into the sphere of slum production, it also dominates the political landscape in its collaboration with Haryana and central state power. The results of workers struggle at Maruti will open or close space for the struggle in the wider industrial landscape, not only in the Delhi industrial belt, but in the whole of the subcontinent. As we have seen, the challenge will be to establish organisational link from this centre of unrest to its productive periphery.
In concrete this would mean to form an initial group of five to ten comrades who are willing to focus on the situation in Manesar for at least half a year to a year, until a structure is established which maintains itself. Rounds of documented conversations with workers from different departments and suppliers are a first step. These conversations have the aim to look for ways to increase collective power and to de-mystify capitalist organisation of work – where it hides its class character behind the seeming neutrality of technology, efficiency, quality, knowledge, science. In the centre of the conversations are the following questions:
* how did you experience the struggle in 2011 and 2012, which internal and informal form of organisation did you experience and how did this relate to the official form of organisation?
* which changes in daily production and life in Manesar do you see since 2011?
* how does the work-step you perform relate to others? on whose work do you depend on and who is dependent on your work-step in order to be able to work?
* in which other departments or companies or sectors do you know workers? how did you get to know them? what do you know about their conditions?
* what kind of experiences do you have of collective forms of resistance on the shop-floor, as little as they might be? what would be ways to extend this collectivity, what would be necessary?
* how could meetings of workers be organised, taking into account both the lack of time and space resources and the question of security
* in case of future conflicts either at Maruti or at other companies in Manesar, how can we support them and/or take part in them in terms of breaking out of isolation and out of the control of institutionalised unions? how can we prepare ourselves at our daily work-place and beyond?
The conversations should be organised and documented in a way which reveals the already existent contacts and knowledge to other workers – face-to-face if possible, through leaflets and newspapers if necessary. General political aim of the process should be:
* making future struggles independent of institutional mediation and making formal leadership unnecessary
* making use of the productive connectedness of production in order to hit the company most and in order to extend the struggle
* find ways of extending the struggle or spread the news about it through the already existing channels of communication that workers have (work-place, life in Manesar)
* develop an understanding of self-organisation (informal committees and coordinations) to plan steps ahead
* be aware of other disputes which go on in other companies and areas at the same time and try to relate to these workers directly
* generalise the issue of the struggle to a wider level: question of more money and less work, general question of existence as proletarians in Delhi area
* establish a political coordination of workers in Manesar which survive single conflicts
* find ways to get in touch with workers outside Delhi region, first of all with those who will play an important role in future disputes, e.g. FIAT workers manufacturing Maruti engines in Maharashtra
Following some preliminary material which can be used as the basis of this process of inquiry…
3) Material on Class Composition at Maruti Suzuki
Trade union flag in front of Suzuki Powertrain – Symbol of institutionalisation…
3.1) Current Situation: State of Workers’ Collectivity one Year after the Occupations (June 2012)
After the occupation in October 2011 Maruti management had to deal with an emerged collective of 3,000 workers in the assembly plant and their extended collective of workers in Suzuki Powertrain and other suppliers. Modern capitalist factory production and this degree of workers’ collectivity don’t go together. Management therefore faces the question how to undermine the collectivity and re-establish control over the shop-floor and the wider productive system. The required control can neither be enforced by brute repression, nor by ‘divide-and-rule’-tactics alone, the material transformation of the production process, the physical change of the cooperation between workers of different departments and productive units is required. From management point of view, concessions given to workers have to contain future potentials of re-division and productivity increase. The productive cooperation – the working side-by-side – was the fundament of workers’ togetherness in 2011, so consequently it has to be changed.
Within the left the understanding of these types of shifts within the productive system are only rarely seen as political measures of re-establishing the rule of capital, focus is on the more obviously ‘political’ measures of management repression against workers. Workers in turn face similar questions. If the Maruti assembly plant and its closest suppliers has been the basis of our collective power so far, and if management is planning strategically to undermine this basis, what can our answer be? These are in noway abstract contemplations, but very concrete facts, moulded in metal: (also) in order to undermine the power of Suzuku Powertrain workers as sole suppliers of diesel engines for the Maruti Gurgaon plant, Suzuki management ordered engines from FIAT factory based in Maharashtra. Since October 2011 the Gurgaon plant is not only supplied by Suzuki Powertrain in Manesar, but also receives 350 engines from FIAT each day, confirming the tendency of capital to react to workers’ struggle by expanding the socialisation and re-division of labour. In their future struggles Maruti workers will have to face up to this fundamental change in their material cooperation, which now includes FIAT workers.
On the background of these questions we have to soberly analyse the role of the newly established unions at Powertrain and Maruti Suzuki. Being structured by the framework of labour law and formal representation, is the union able to counteract the material changes imposed by management? Can the union strengthen workers’ power and expand their collectivity? In the following we will try to draw some preliminary conclusions, based on conversations with workers of different departments and suppliers in April to June 2012. What did management do after October 2011 in order to re-compose the work-force and re-gain control.
Police presence
Management kept around 100 police stationed 24 hours in the Maruti Suzuki assembly plant till December 2011. At Suzuki Castings and Powertrain the police had tents on the factory premises, with 50 to 60 police and 15 police respectively, till at least June 2012. After the riots of the 18th of July a 600-head strong special police battalion was stationed permanently in the industrial zone of Industrial Model Town Manesar. These are the most obvious expressions of the fact that management does not trust their own power in the factory and that for a re-composition this presence of state violence is necessary.
Shifting of workforce
Obviously the management’s attempt of a major shift of work-force was defeated by the workers when they re-occupied the factory in early October 2011 after 1,200 temporary workers were not taken back. This move of re-occupation was not so much due to the ‘political consciousness of unity’ of the union leadership, but due to the enormous (physical) pressure of the temporary workers on their permanent work-mates. After October 2011 management shifted those 800 workers who were hired as ‘scabs’ during the ‘lock-out’ to the new B-plant, which became operational in September 2011. This creates a plant-level division between workers of different histories. In addition management shifted individual workers from A-plant to B-plant, whenever it seemed appropriate and possible to isolate individual workers.
Arbitrary dismissals
Between April and May 2012 management started a campaign against ‘faked’ ITI certificates in all departments. They accused workers who had been employed at Maruti since several years of having presented a faked professional qualification (around 25,000 Rs in UP) and kicked them out. In total only 70 workers became victims of this campaign, but they were employed in nearly all departments, so the campaign created a certain atmosphere throughout the plant. There were only few incidents of collective resistance by workers on line level, see for example workers’ report from the weld-shop. Other workers reported about an increase of dismissals of temporary workers due to minor mistakes and fabricated reasons from April 2012 onwards.
Arbitrary trainee tests
In order to filter the workforce and to give the decision ‘who gets on the company pay-roll and how many’ a seemingly objective touch, companies like Maruti make use of ‘trainee tests’. Workers hired through contractors, after several years of employment, have to pass a test in order to become trainees. Trainees have to go through three years of trainee-status in order to get the chance to become permanents. At Honda HMSI management used the trainee status to re-compose the workforce after the 2005 struggle, Maruti Suzuki in Manesar will very likely modify the trainee status after the unrest 2011/12. A trainee from the bumper department said in June 2012: “Some of us try to become trainees, we have to pass a test. Around 500 questions, mostly on health and safety and quality, also “where have you been during the strike period in 2011″. We have to undergo a medical test, too. In the bumper-shop 24 workers went for the test in early 2012, only 7 were taken on as trainees.”
Uneven work-load distribution
What is common in other big companies, such as neighbouring Honda HMSI, that permanent workers are given ‘better’ jobs (maintenance, quality, supervision) and temporary workers do the main productive work has not been the case yet at Maruti Suzuki Manesar. But things start to change. A permanent worker employed in the weld-shop said in June 2012: “There is a clear policy to divide permanents from temporary workers. Supervisors don’t put any pressure on permanents, you can do your job, you can walk around. Pressure is solely on temporary workers. These workers obviously complain, but they don’t complain in front of the supervisor, they express their anger towards the permanent workers – they in turn tell the temporary workers to shut up and work.”
Increasing wage gap
First reaction of management after the occupation in October 2011 was to give a considerable wage increase to temporary workers and apprentices, without formal agreement or negotiations – see workers’ report from the final assembly department. Since then wage developments were tied to formal negotiations. The wage gap between temporary and permanent workers has increased significantly after the wage agreement settled by the recently established trade union at Suzuki Powertrain. According to permanent workers close to the union leadership, the demand notice put forward at Maruti Suzuki assembly plant puts a strong emphasis on productivity bonus, which is only available for permanent workers. If Maruti wage dynamics follow the general trend, then the wage settlement will most likely result in productivity-related wage increase for permanents and relative wage stagnation for the temporary work-force.
Changes in the supply-chain
We already mentioned the most significant change introduced in October 2011 concerning the supply of 100,000 diesel engine annually from FIAT plant in Ranjangaon, Maharashtra. FIAT India has considerable over-capacities and Maruti Suzuki needs to undermine the position of Suzuki Powertrain workers – Management had to realise in 2011 that two days strike at Powertrain suffices to stop production at the ‘appeased’ Maruti Gurgaon plant. Apart from that the struggle in 2011 forced Maruti to re-think their supply-chain lay-out. While the spacial distance between the assembly plant and most of the suppliers prevented copy-cat effects during the strikes in 2011, workers at companies like Bellsonica, FMI, Krishna Maruti, SKH Metal [], which operate on the Maruti premises, might be too close to the centre. Another major change in the near future will affect hundreds of truck drivers and loaders – some of them took part in the strikes in 2011. With the development of the industrial corridor connecting Delhi industrial area with port-towns in Gujarat and Maharashtra Maruti management intends to increase the finished car transport by rail from currently 5 to 35 per cent. Every day around 500 trucks leave Maruti Gurgaon plant with finished cars, the number will be only slightly smaller in Manesar.
Carrot of the C-Plant – Threat of Gujarat
Maruti management will try to use current investments and fusions in order to undermine workers’ position. In June 2012 Maruti announced the fusion with Suzuki Powertrain, which leaves scope for speculation about future conditions of workers in both companies. Similarly the speculation about the future of assembly work at Gurgaon plant. In March 2012 newspapers announced management decison to reduce the Gurgaon capacity from currently 700,000 cars to 400,000 cars and to increase diesel engine production – production start by mid-2013, around 150,000 units. The new engine-shop will need less workers than the shutting down of the assembly-departments will make redundant. Investments into the C-plant in Manesar and the R&D centre (and expanded Suzuki Motorcycles factory with 4,000 new workers) in ‘the new auto-export-hub’ Rohtak (also in Haryana) and the resulting ‘creation of 1,900 new Maruti jobs’ in the region will be used as a carrot and as a possibility to re-shuffle the workforce – while the construction of the Gujarat plant (estimated production-start 2015) will be instrumentalised as a means of black-mailing against the ‘workers in Haryana’.
These are just some superficial snapshots of current and imminent changes of the conditions at Maruti which will impact on workers’ collectivity and structural power. It is obvious that most of the changes reach beyond the formal boundaries of the trade union frame-work.
3.2) State and Limitations of the Trade Union at Maruti Suzuki
Union demonstration during lock-out at Senior Flexonics automobile supplier…
The question whether workers are able to use the trade union structure as a vehicle to counteract these significant material changes (or attacks) imposed by management depends on objective conditions (who can the union formally represent, what can the union legally do) and subjective factors (how engaged are workers within the union framework).
Most of our conversations with Maruti Manesar workers took place in March 2012 to June 2012, less than a year after an enormously intensive wave of struggle, after a struggle which meant considerable risk and (monetary) sacrifice, but which also created an atmosphere of collective excitement and enthusiasm. Official goal of the struggle was the recognition of an independent trade union. Less than a year after the struggle and after the union got registered in early 2012, the interest and engagement of workers in the trade union seemed close to zero, not only amongst the temporary workers, also amongst the permanents. This reminds us of the participation level in the parliamentary elections in Egypt, which hovered around 20 per cent, after a mass wave of struggle ‘against the dictatorship’, and officially for the right to vote a different government. The union was a symbol of struggle and unity, which brought the Maruti workers together, but also under certain illusions – e.g. many temporary workers were little aware of the fact that they will not be represented – which now come out into the open of ‘normal and formal industrial relations’.
Some of the permanent workers express the hope that a ‘recognition on paper’, either of the union itself or of agreements concerning pay and conditions, will secure the gains now that the immediate pressure of the struggle has decreased.
“We can struggle, we can gain something. But without union recognition the gains are lost, the company will turn back the wheel within three months and we are back at start. Once we have the union we will also take care of the temporary workers”. (Permanent Worker, assembly department, March 2012)
The actual form of organisation excludes the majority of workers. Apprentices, trainees and temporary workers don’t fulfill the official norms as ‘workmen’ and are therefore excluded from membership in the permanent employees union. At Maruti the composition looks like this: 850 permanents (potential union members), 1,000 trainees (no members of union), 300 apprentice (no members of union), over 1,200 workers hired through contractor (no members of union).
“The temporary workers in the paint-shop haven’t seen the demand notice. There are rumours that ‘wage demands for workers hired through contractors’ are included. We heard about 17,000 Rs for non-ITI and 22,000 Rs for ITI workers. Also the permanent workers in the paint-shop haven’t seen the demand notice. There hasn’t been a union general meeting for two months. During the struggle itself we should have put forward our own demands directly: at least 10,000 Rs per month, bus service for everyone and so on.”
(Temporary worker, paint-shop, April and May 2012)
One of the most important questions is obviously whether the form of delegation, which developed during the struggles in 2011 is still intact and alive. During the struggle decisions about the direction of the struggle were announced by line coordinators, one line-coordinator representing around 15 co-workers, in total there were around 150 coordinators. These workers worked together day by day and sat together during the occupations and during the lock-out – it was the basic unit of the struggle. It seemed in hindsight that the line-coordinators were not ‘representing the debate of their co-workers’, but were rather used as disseminators of the decision of the leadership.
“Since October 2011 the line coordinators have no function anymore, apart from being the extended hands of the union body. If any line coordinator talks or acts in a way which does not please the union body, they have ways to shut him up. The demand notice has not been discussed, it is not based on debate. In this sense the whole physical confrontation between union president and HR manager was a show – they suspended the president afterwards, the union guys walked through the plant saying that if the suspension is not withdrawn there will be violence and the HR managers will be beaten up, then the HR withdrew the suspension. We tried to organise Sunday meetings amongst active permanent workers to debate the situation, but these meetings stopped – they had no results.”
(Permanent worker, weld-shop, June 2012)
“The line coordinators in the paint-shop have been elected by everyone, but they had to be permanent workers. They take care of ‘problems’, if the AC does not work or similar things. If they can’t solve it with the supervisor, they go to the ‘union body’. Some line-coordinators are more like the right-hand of the supervisor. Normal workers can also go to the ‘union body members’ on an individual level, that’s no problem.”
(Temporary worker, paint-shop, May 2012)
The usual leftist response to these problems would be to demand more ‘internal democracy’. A permanent worker, union body member since the first hour of the struggle, criticises the attitude of the current union body, but also questions whether union elections would actually benefit workers’ unity.
“The ‘union body’ (eleven members) has not been elected. After the ‘sell-out’ of the 30 union leaders union members initially demanded ‘more control’, for example people said that before an agreement is signed by the union all members should see and sign it; they said to the ‘union body’ that ‘you first have to prove, before we can trust’. After registration of the union in early 2012 the question of elections came up. The constitution requires elections after registration of the union. The eleven member union body tried to avoid having elections, they also asked workers to sign agreements that they don’t wish to have elections at that point. But actually, if there were elections now, it would not have a positive result. It would rather create more divisions between workers due to struggle over posts and votes.”
(Permanent worker, press-shop, June 2012)
At Suzuki Powertrain, where workers refer to the union as the ‘union of the locals’ (workers from Haryana and Rajasthan), as opposed to the ‘outsiders’ (Bihar, UP etc.) it can be seen how quickly ‘the union’ can turn from a symbol of workers’ togetherness in struggle into a medium of ‘managing the status quo’ and therefore managing and re-producing divisions within the work-force. This description of the ‘local workers’ union’ might be superficially true, but does not explain the underlying reasons for why unions tend to represent a smaller or bigger minority of workers. Under the current economic pressure (profit-squeeze, market crisis etc.) and given the legal constrains unions are only able to survive if they offer some benefits to a minoritarian section of the working class, which they have to mobilise every now and then, and manage the division between them and other workers responsibly. Only then management will accept them as ‘representatives’. At Suzuki Powertrain, apart from the division into permanents and temporary workers, the division took regionalistic forms. Following a short summary of the development of the union at Suzuki Powertrain.
“After the joint occupation of Maruti Suzuki and Suzuki Powertrain in October 2011, negotiations took place between Powertrain management and recently established union (HMS) on 19th of October. Three representatives of Suzuki Powertrain were kept separate from the rest of the union leader-ship (HMS) during negotiations. These three leaders had pushed the joint-occupation with the Maruti Suzuki workers. The remaining Powertrain union leadership signed an agreement on 21st of October. The three Powertrain leaders remained suspended and were finally sacked on 17th of April.
On 10th of November 2011 permanent workers at Suzuki Powertrain debated during a general union assembly. Despite having been called several times, the union leadership did not come to the general assembly. The debate had mainly evolved around the issue of the three suspended [more militant] leaders. Workers called for a general union election, and said that no 3-years agreement will be signed with management before the three suspended are taken back. But then it became clear that the union leadership had already signed a three years agreement on the 9th of November. The inquiry against the three suspended was finished on 2nd of December.
In early 2012 around 500 Powertrain workers signed a letter complaining about the agreement settled by the union, one point of conflict was the link of wages to productivity increase. Workers decided last minute not to go forward with this protest in order to ‘keep the unity’. By then the union leadership, in order to deal with the ‘competition’ of the more ‘radical’ suspended leaders turned towards a certain kind of regionalism, presenting themselves as the representatives of the ‘locals’. The fact that Powertrain management announced in June 2012 that in future it will hire only ITI apprentices from ITI’s in Haryana is very likely not by chance.
In order to put pressure on management to take the suspended leaders back on workers refused company tea on 30th and 31st of January 2012 and company canteen food on 1st and 2nd of February 2012. After the food boycot management threatened workers with ‘accusation of undisciplin’ (a formal accusation which can lead to suspensions). On 1st of February 2012 20 to 25 workers were accused of having engaged in physical violence and against two workers a FIR case was filed by police. At the time, around 23rd of March 2012, there were similar protests (food-boycot) at Suzuki Motorcycles in Kherki Dhaula after three leaders had been suspended by management. These conflicts remained isolated from each other.
At Suzuki Motorcycles, the company had revised a new wage settlement for three years around July 2011, but in March 2012 management refused to implement some pending demands. On 21st of March 2012, when a union delegation went and discussed the issues with management, the HR Vice President Anil Munjal and the union General Secretary clashed in the canteen. Next day the three union leaders were suspended without charges. The company called in a large number of police personnel outside the premises.
At Powertrain, the union ordered another a food boycott on 10th and 13th of April, on 17th of April Powertrain management sacked the three leaders. On 17th of April 2012, after having heard that three permanent workers (union leaders) had been sacked, the B- and C-shift gathered at 00:30 am. At 1:30 am one of the union body members (HMS) arrived and said that the union will not be able to support any suspended or sacked (as result of this protest) workers. The B-shift workers went home and the C-shift workers started work. About half of the workers had supported the strike, the other half not. Many of us apprentices joint the strike, although we are not directly concerned, while a lot of the permanents remained passive.
On 21st of April the union leadership removed these three workers from their union posts and gave the posts to new people. On 27th of April HMS regional leadership under leadership of the union president of JCB called for meeting in support for sacked leaders, but the HMS union section from Powertrain did not attend. With Suzuki Powertrain now being ‘under control’ it will be very likely that Maruti Suzuki will try to use the fact that the two companies will fuse by end 2012 in order to ‘import the union agreements and structure’. On 12th of June Powertrain union body members return to work in production department after having mainly been in union office ‘off work’ during the last months. They probably felt the urge to ‘keep in touch’ with the workers as much as the union leadership at Maruti Suzuki felt the need to demonstrate its ‘militancy’, e.g. when the union president slapped a supervisor in mid-June 2012.”
(Based on conversations with Powertrain apprentices and dismissed Powertrain permanent worker, June 2012)
At Maruti Suzuki the MSWU union, though largely absent from the shop-floor, handed over their demand notice on 18th of April 2012. The media reported mainly on a propagandistic level that the union ‘demands a five-fold wage increase’, while most (temporary) workers were largely unaware about the actual content of the demand notice. A large share of the ‘wage hike’ would be linked to production level. “The PPRA (productivity and attendance bonus) forms 50 per cent of our wage. In the current demand notice there is a demand that the bonus should be attached to the amount of cars produced, e.g. if Manesar produces 900 cars per day, the bonus should be 4 Rs per car, if between 900 and 1,200 then 6 Rs, if over 1,200 then 8 Rs.” (Permanent worker, weld-shop, June 2012)
It remained unclear whether this bonus would apply only to the permanent workers wage. The union leadership made an attempt during negotiations to include temporary workers in the long-term agreement and offered to renounce one year of wage increase (for the period from April 2011 to 2012) if the temporary workers would be included. Management did not budge and the ‘preemptive renouncement’ probably also did not help to strengthen the unity between permanents and temporary workers. On 14th of June the union met with HR-head Siddiqui for negotiations about the payment of the annual spare parts bonus. The HR management said that the 53 days of strike in 2011 will be reduced from the bonus, so that permanent workers who took part in the strike get 27,900 Rs bonus, while the non-strikers get 44,000 Rs. The union agreed, which also did not help to build up more pressure for the wage negotiations.
The union was unable to enforce a wage settlement and unwilling or unable to mobilise workers for collective actions (how to mobilise after the main union structure had been paralysed for months? Would the temporary workers have gone on strike for an unclear demand notice? Would the union have been able to call for a legal strike during period of negotiations?) The pressure on the union leadership ‘to prove itself’ and to demonstrate that it is not ‘management-friendly’ increased. That might explain incidences like in mid-May, when a ‘physical’ confrontation between Maruti Suzuki union president and HR manager took place in the final assembly. Workers had complaint about lack of air, faulty cooling system, but there was no reaction from the side of management at all. Only when the union president came out of a meeting, supervisors and managers reacted, there was a back-and-forth and the union president hit a member of staff. Management suspended him, but after a tension grew amongst workers they revoked the measure.
If we return to our initial question whether the union frame work helped to strengthen and expand the workers’ collectivity which emerged out of the 2011 movement we will have to say that the union framework is not sufficient. It focussed the attention of workers onto the sphere of negotiations, suspensions, election politics, while management took material steps to transform the productive cooperation of workers in order to undermine their subversive cooperation. The legal framework of union representation is too narrow in order to organise ourselves on the same level as the company is trying to disorganise us. For the production system, management combines workers of various areas, sectors, companies, categories, from work in slum huts to robot-weldshops, from Delhi to Tokyo, while we are supposed to be organised as the small faction of ‘permanent workers in Manesar’. If we don’t reflect the totality of this productive structure and its constant changes in our coordination of workers (canteen, contracts, suppliers), we will end up in isolation and the paper of agreements and recognition will turn into dust for the majority of workers.
At Honda HMSI it took only two years before a major rupture within the work-force emerged: from the 2005 bloody united struggle for union recognition to the wildcat strike of temporary workers opposed by the union in 2007. Will this process repeat itself at Maruti Suzuki or will both permanent and temporary workers find a different organisational structure to re-compose themselves and re-establish their collectivity on a higher level? These were our questions before the 18th of July 2012…
A valuable weapon in workers’ hands…
3.3) Preliminary Thoughts on the Unrest of the 18th of July 2012
On 18th of July a group of workers and management clashed in the Maruti Manesar factory, a manager got killed and around 100 others were injured by workers using automobile parts. Most Maruti workers fled Manesar after the incident, also as result of severe police raids. Maruti declared a lock-out which continued at least till mid-August.
We are not in the position to ‘provide any evidence’ about what actually happened. The general background of the incident is clear, the living and working conditions of workers in Delhi industrial area produce regular outbursts of ‘violence’. About the specific background and possible outcome of the violence at Maruti there is a controversy within our collective. This is also due to the fact that some of us are currently ‘out of town’ and followed the events from afar, while others are in Faridabad, Manesar and Gurgaon area, distributing Faridabad Majdoor Samachar newspaper amongst workers after the riot took place.
End of July, before the announcement of the mass dismissals, comrades in Faridabad said about the 18th of July incident that “Something new has happened, a shift took place. The management of the entire area is terrorised. Maruti has to announce that it will not use contract labour in the future. The head-manager of Shell had to admit that ‘it is perverse that a top-manager earns 820 times the wage of his worker’. While Maruti CEO has to talk publicly about ‘class-war’, the left keeps on talking about constitutional rights, proper legal inquiry and demand a ‘return to normalcy’. Workers are way ahead of them, they don’t care about their jobs anymore. Maruti will have to re-hire most of the workers, they cannot produce without them. There will obviously be some arrests and some people will be kicked out, but at large the workers have shifted the situation and atmosphere in the area. Management knows that a small trifle like suspensions of two workers can kick off anything now. During distribution, Maruti workers at Gurgaon plant told us that management is shit-scared indeed.”
From afar we raise further questions. In August 2011 a supervisor also attacked a worker inside the plant, but in reaction all workers of the department went on a wildcat strike together and forced the supervisor to apologise in front of them. Soon after police came inside the plant in order to arrest some people, but workers again went on strike and forced the police to return the workers. Since October 2011 the collectivity of workers has suffered. As we have seen, the union leadership was not able to maintain the collectivity and therefore was also not able to enforce themselves against management. In order to prove themselves despite their structurally weak position they resorted to ‘strong men attitude’. Instead of struggling as productive workers as part of a wide industrial network they created a position, mainly amongst permanent workers, that ‘we are 1,000 strong guys’. In mid-May 2012 the union president, who was seen as a ‘softy’, slapped a supervisor on the shop-floor, which has to be seen mainly as a show-act. The desperation of the union leadership of not being able to fulfill the large expectations of workers might have contributed to the ‘show-down’ on the 18th of July. We don’t know how collectively prepared and involved the mass of workers were, but we know that now they are dispersed. As Maruti workers they did not come out stronger out of the incident – although, and this can be true at the same time – the violence might have shifted the general atmosphere in the area in favour of the wider working class. Maruti workers have shown that management is not able to control them, but the difference to the wildcat occupations in 2011 is that a riot leaves less space for generalisation of workers’ autonomy. Maruti will continue to produce and will have no other option but to reproduce the same contradictions which led to the violence.
Two months after the incident the situation looks less bleak. Maruti had to take back a lot of the old workers, but promised better conditions. The 500 sacked workers continue their mobilisation with their family members and form some kind of ‘collective of the discontent’ in various towns in Haryana – the initial dispersion can turn into spreading the conflict. It will have to be seen whether a fruitful relationship can be formed between the situation in Manesar plant, between the ‘sacked workers agitations’ and the Gurgaon plant, where young workers force the union to take some kind of action in support of the Manesar workers – several hundred workers went to the union office to demand steps. Workers and working-class communists have to analyse how the collectivity can be expanded throughout the productive territory around Manesar and how they can hit management the hardest while at the same time keep their own harm at a minimum. The two suspensions at neighbouring Honda HMSI shortly after the 18th of July, which were issued after the Maruti riot, show that not all managers are scared enough yet. Below a very superficial chronology of the events of the 18th of July 2012.
16th of July
The union distributes a document amongst workers which had been handed to them by management, saying that management are not agreeing to union demands, which includes education allowance of 200 Rs for employee’s children.
17th of July
A-shift and B-shift workers boycott their pre-shift meetings with supervisors as protest against management’s non-compromising attitude during the ongoing negotiations about the demand notice.
18th of July
During A-shift a supervisor stopped some workers when they were returning from their tea break and told them to stop boycotting the pre-shift meeting. A dispute took place. The worker alleges that the supervisor engaged in casteist remarks, management alleges that the worker attacked the supervisor and decided to suspend him. B-shift workers continued production while A-shift workers decided to stay back in the plant at the end of their shift. Negotiations took place in the management office. Management alleges that the union leaders called workers in who were armed with auto-parts and who started beating management personnel, destroyed CCTV systems, destroyed parked cars and set control room and offices on fire. The media reports about a 1,200 men strong ‘mob’. One manager died in the fire, 100 others had injuries from being beaten. The union alleges that during the talks management called a group of 100 armed bouncers who started attacking the workers. Later during the night troops of police started raiding the area, but most Maruti workers had already fled from the places where they lived. Police arrested workers randomly, seeing that they were wearing a Maruti uniform. Two company buses with Honda HMSI workers were stopped and searched by the police and held over night.
19th of July
Further arrests, main target are union members. The media repeats management version of events.
21st of July
The company declared a lockout at the Manesar plant. Work at the Gurgaon plant continues. During distribution of Faridabad Majdoor Samachar at gurgaon plant workers say that “management is shit-scared”, similar voices from workers in other companies in Gurgaon and Faridabad. Powertrain reduces work from three to two shifts in engine department. Police conducted raids at various places in Haridwar, Ranchi, Rajasthan and Haryana, a total of 97 workers arrested. Haryana Government announced to permanently deploy a 600-strong police division of the Indian Reserve Battalion (IRB) in Manesar industrial area, 10 acres of land required.
23rd of July
The First Information Report (FIR) issued by Maruti management reportedly names 55 workers and has added 600 others. Reports about local villagares aiding police to find workers and hand them over – comrades deny that this is a mass phenomena.
24th of July
Maruti HR-head Siddiqui announced: “We have received instructions from the parent, Suzuki Motor Corporation, to not compromise on issues of violence. We will derecognise the union at the Manesar plant. All those identified in connection with the incident will be dismissed immediately.Maruti announced to shift supervisors and senior workers from its Gurgaon facility to Manesar and to hire 1,000 new workers for re-start of production. The media circulated reports claiming Maoist infiltration of Maruti workers, a Naxal conspiracy.
25th of July
Union members from Maruti’s Gurgaon plant, Suzuki Powertrain, Suzuki Castings, Suzuki Motocycle, Lumax Auto Technologies, Satyam Auto Components, Endurance Technologies, Hi-Lex India Pvt Ltd, Rico and others attended the memorial meeting of police attack on Honda HMSI workers in 2005 despite imposition of Section 144 at the MSIL plant. The 144 order bars assembly of five or more persons within two km from the boundaries of IMT Manesar. Media reported about gathering of village leaders of 75 villages around Manesar in support of Maruti Suzuki. During the meeting in Dhana, Gurgaon Zila Parishad chairman Rao Abhay Singh said to the press: ” Our local boys could have never done this” and claimed that the ‘mob’ were ‘outsiders’.
26th of July
Maruti declared that they will go ahead with planned investments in Haryana, given that the “immediate arrest of 90-odd workers, shows sincere intentions of the government”. The investments include a Research and Development Centre at Rohtak and a new diesel engine-shop at Gurgaon.
27th of July
Maruti makes an announcement not to use contract labour from March 2013 onwards. they also announce the non-payment of monthly wages for 2,000 workers at Manesar; “No one working at the Manesar plant will be given salary. According to the rule, after the company’s lockout, workers are not paid till the time it (lockout) is revoked.” Siddiqui. Maruti has exhausted the inventory of Swift cars, around 15,000 parked in Manesar and Gurgaon.
30th of July
The price of Maruti shares has fallen by 8.5 percent since the 18th of July. Maruti announced that they expect to fire approximately 500 workers who were involved in the Manesar plant clashes.
31st of july
A tripartite meeting of Maruti officials, workers’ representatives and Government is supposed to “help in creating conditions to restart production at the locked-out plant in Manesar”. Reports claimed 114 arrests so far, a good number among them were apprentices. Accoprding to the press Maruti Suzuki “has sought the help of a vedic astrologer from Bangalore to help sort out the vaastu at the Haryana unit. As part of the vaastu-correction process, “all negative energy” that exists on the land needs to be removed by conducting an extensive puja. Only after two to three weeks from the rituals, the land will be rid of “all negative energy” , an astrologer said.”
3rd of August
Maruti announced to increase production of diesel cars in Gurgaon plant in order to counteract impact of lock-out, which causes a daily loss of Rs 90 crore. Meanwhile, representatives of the workers’ union at Suzuki Powertrain India said with production cut about 30 per cent, many contract workers had been asked to leave. “About 250 contract workers, whose initial tenure came to a end, were asked to leave. The company has decided not to recruit fresh workers at present.”
4th of August
A joint trade union forum met in in Gurgaon, debating the lock-out at Maruti.
7th of August
Tension at Honda Motorcycle & Scooter India’s Manesar facility following suspension of two workers after alleged manhandling of a manager (according to management). Police is stationed at the factory: “We are keeping a close watch,” SHO Manesar Om Prakash Bishnoi.
8th of August
So far 116 workers have been arrested and a list of 162 ‘wanted’ workers is circulated. Police visit homes of these workers and put pressure on their family, threaten them with arrest of family members if the worker is not handed over. Reports on police custody torture of arrested workers are published.
9th of August
Gurgaon police states that the ‘mob’ which ‘rioted’ at Maruti on 19th of July was only 100 people strong, not 1,200 as first claimed and not 650, as claimed later on. Criticism of MUKU Maruti union president, who asks, why the 70 police officers stationed at Maruti Manesar plant were not able to stop the ‘mob’. In the meantime talks on Honda HMSI dispute fail at city labour department in Gurgaon as main company management did not turn up. Unions declare that they will organise a protest during ‘workers’ rights day’ on 17th of August in case no solutions are found for Maruti lock-out and situation of Eastern Medikit workers, who are left without wages since several months.
10th of August
Gurgaon police hastened to add that 100 workers were involved in the incidences inside the office building. but “the violence later spread to the ground floor as well. There were around 2,000 workers armed with metal objects and police priority was to rescue the managerial staff. Even the reports of there being about 1,200 workers are an underestimation of the size of the crowd,” (DCP Daya)l. Their report also states that the ‘violence was not planned’. Further arrests, now a total of 142 workers. Extension of police remand of 17 union leaders.
11th of August
Management announced that the plant might open in the following week. the press wrote about “pressure from vendors to re-open”. A worker said on a mainstream television channel: “Our workers did not have faith in the union body. They were apprehensive about the union cheating them again…. [Yet they wanted that] the management should at least value and listen to the union body.” (NDTV)
16th of August
Maruti announced the dismissal of 546 permanent workers, including the 154 who had been arrested. According to media all workers hired through contractors will remain outside the factory, Maruti will look into re-hiring during mid-September. Maruti deposited 50,000 to 70,000 Rs in sacked workers bank accounts (not in those of the 150 arrested),saying these payments represent the workers’ wages for July plus three months’ salary and an additional 15 days of salary for each year of service.
17th of August
Around 7,000 union members employed at various companies hold a protest-rally in Gurgaon.
19th of August
Maruti announced to employ a security division of retired armymen headed by a top-ranking (retired lieutenant-general rank) ex-officer at the Manesar plant.
20th of August
CPI and CPI(M) announced to make Maruti and the dismissals an issue in parliament and to hold a protest rally in Delhi.
21st of August
The lock-out got lifted. Only few workers entered the Manesar plant, over 1,000 cops in Manesar industrial area. the media claimed that Maruti suffered 250 million USD loss since 18th of July.
22nd of August
Maruti announced to have produced 186 cars, in combined production of A- and B-plant. Other sources claim that only the B-plant started production in the press-shop and weld-shop, while assembly work is done in the Gurgaon plant. Maruti Chairman told during a shareholder general meeting that the conversion of contract workers into permanent workers would increase the labour costs only slightly, “as the starting salary of a permanent worker is only about 10 percent more than a contractor’s pay.” Managers who have been ‘traumatised’ are sent to Brahma Kumaris spiritual centre and to self-defense courses.
30th of August
Maruti announced to re-hire 1,000 out of 1,800 former contract workers, talks to turn them into permanent employees are supposed to take place in early September. Maruti claimed an output of 427 cars per shift, compared to 950 cars before the unrest. Current workforce at Manesar plant allegedly 2,000 workers, compared to 3,000 before. “We’re increasing output on a day-to-day basis, but would need at least 1,000 more people to be closer to full output. Right now, even the 400 supervisors are working on the line and they need to go back to their original roles,” a company official said. “After this, the 3,000 contract workers at the Gurgaon facility will also be given a chance to become permanent at Manesar.”
31st of August
Protest rally in Gurgaon, apart from members of main trade unions around 400 sacked Maruti workers took part.
3rd of September
Maruti announced that monthly sales in August were down by 40 per cent compared to previous year. The company also claimed to increase automation in Manesar: “In over a decade, the company has doubled the number of robots used in its plants to around 1,500. It will add another 50-100 new robots in the older plant at Manesar to increase automation to 99 per cent from the current 90 per cent. [in the press-shop department]”
2nd of September
400 Maruti workers and family members demonstrated in Rohtak, complaining about dismissals, repression and police torture.
4th of September
The main trade unions hold a convention in Delhi, proposed actions only include symbolic and legal protests, no strikes.
6th of September
Maruti announced to manufacture the model Dzire at Gurgaon plant in order to deal with backlog. The Dzire had only been produced in Manesar plant before the unrest.
8th of September
Maruti management acknowledged that they have difficulties finding ‘fresh skilled workers’. Suzuki chairmen announced simultaneously that they don’t intend to abolish the contract system in their plants, but that they will change the ratio and subject contract workers to a more severe check during the hiring process. “About half of the workers at the facility will now be completely fresh hires from vocational schools such as Industrial Training Institutes (ITIs), with another 20 per cent coming from other companies. In all, Maruti expects to have 3,750 workers (earlier 3,300) at the plant, of which about 1,000 permanent workers have already joined. About 20 per cent of the workforce will abe temporary hires who will receive similar pay as permanent workers, but have a limited work contract of 8-9 months.”
11th of September
Haryana government approves hiring 11,000 new police constables, out of which a major share will be placed in Gurgaon.
3.4) Theses for the Future Armament of Workers’ Struggle
Industrial desert IMT Manesar…
The following is a political summary of the workers’ reports…
*** Going beyond formal ‘international solidarity’ – starting from the material connections and divisions of a global working class war
The automobile industry is the most intertwined and integrated global industry and therefore the main organisational base of the emerging global working class. Struggles in the sector take place simultaneously in the global north and south. Some of the the struggles directly impact on each other, but at large the working class has to face up to the fact that the discontinuity of conjunctural cycles and uneven development still enforce a ‘political disjuncture in the direct communication of struggles’. The discontinuity can be described quantitatively: while in the US car production between 2000 and 2009 decreased by 50 per cent and in Japan by 25 per cent, it increased by 700 per cent in China – adding a manufacturing capacity of 2 million cars per year. This geographical shift expresses itself in the form workers’ struggles take: struggles for better conditions and against the factory despotism in the ‘automobile boom regions’ in the south (Honda in China 2010, Suzuki in India 2011), struggles to maintain certain standards achieved during struggles since the 1980s in countries of the ‘second wave’ of automobile expansion (South Korea, Brazil) and struggles against redundancies and severe attacks on conditions in the old centres in the US and Western Europe.
While the struggle is on at Maruti Suzuki we witness mass redundancies (8,000) at PSA-group in Europe and struggles around the closure of the factory in Aulnay (see leaflet by MC in appendix), Renault complains about slump in car sales during the first half of 2012 of nearly 15 per cent, in Italy the car sales decreased by 21.5 per cent during the same period. Since 2007 around 800,000 workers in the European automobile industry lost their job. In 2011, while Maruti was occupied, FIAT enforced a mass deterioration of conditions in collaboration with the main trade unions. General Motors closed its factory in Belgium, in the remaining 12 European factory the number of workers has been reduced by 8.000 workers to now 40.000, currently the General Motors factory in Bochum, Germany is under severe attack. Since 2008 General Motors sacked over 30.000 workers in US factories. On 24th of July 2012, three days after Maruti Suzuki declared lock-out in Manesar, General Motors declared a lock out at São José dos Campos plant in Brasil, undermining the protest of workers against 2,000 redundancies. At the same time production of General Motors in St.Petersburg, Russia is increased from 90.000 to 200.000 cars per year and production units in China are expanded. In July 2012 workers at General Motors in South Korea went on strike for higher wages (demand of a monthly increase of around 100 Euro, 6,500 Rs), together with workers at Hyundai and Kia. In March 2011. workers at General Motors in Halol, India, engaged in struggles with similar characteristics to the Maruti Suzuki dispute. In September 2011, simultaneously to the unrest at Maruti Suzuki, about 4,000 workers at the PT Suzuki Indomobil car and motorcycle assembly plant in West Java, Indonesia, went on strike, demanding year-end bonuses, meal allowances, health expenses and overtime payments. Struggles in the automobile sector in India are permanent and wide-spread, but in most cases we know only superficially about them:
“Among the prominent instances are: Mahindra (Nashik), May 2009 and March 2011; Sunbeam Auto (Gurgaon), May 2009; Bosch Chassis (Pune), July 2009; Honda Motorcycle (Manesar), August 2009; Rico Auto (Gurgaon), August 2009, including a one-day strike of the entire auto industry in Gurgaon; Pricol (Coimbatore), September 2009; Volvo (Hoskote, Karnataka), August 2010; MRF Tyres (Chennai), October 2010 and June 2011; General Motors (Halol, Gujarat), March 2011; Maruti Suzuki (Manesar), June-October 2011; Bosch (Bangalore), September 2011; Dunlop (Hooghly), October 2011; Caparo (Sriperumbudur, Tamil Nadu), December 2011; Dunlop (Ambattur, Tamil Nadu), February 2012; Hyundai (Chennai) April and December 2011, Ford (Chennai) March 2012.” (Rupe) We can add many more examples, e.g. the struggle at Rockman and Satyam Auto in Haridwar in 2011.
In parallel process to these seemingly dis-jointed struggles ‘North and South’, the actual global productive cooperation between these regions is intensified, e.g. the export of car parts manufactured in India, used in the assembly departments in the global north increases much faster than the export of complete cars. At the same time imports of parts manufactured in China to India increased rapidly. We can also see a deeper capital-integration of companies. Maruti Suzuki engaging in engine production with FIAT, which officially has a joint-venture with Tata, the main ‘competitor’ of Maruti Suzuki on the Indian market – the FIAT factory in India runs only on one-third of its capacity, which forced the companies into the collaboration. One of the share-holders of Suzuki are Volkswagen and General Motors, which also enter the Indian car market by expanding their factory base. FIAT subsidiary Magneti Marelli, which supplies Maruti Suzuki from two factories in Manesar recently engaged in a joint-venture with Motherson Sumi, while in early 2012 Continental bought 100 per cent of Rico Auto Ltd. The Rico factory in Gurgaon was engaged in a one month dispute in 2009, which interrupted supply of parts for General Motors and Ford factories in the US, while in those factories a dispute about the introduction of a two-tier wage system (half the entry wage for new workers) was going on.
This quick glance at some of the global developments of the last month demonstrate that obviously ‘formal international solidarity’ and exchange between workers in the sector is necessary, but workers collectives will have to focus on the actual material relations between workers in different regions, which first of all means to analyse how capital in the automobile sector makes use of the global wage cascade and uneven economic cycles in order to re-structure the industry and to undermine the direct solidarity of struggles. In the organisation of actual direct solidarity it will become more and more difficult to rely on the established union federations, what if for example the UAW (main automobile workers’ union in the US) having become a significant share-holder of General Motors since 2008 (17.5 per cent) and unions in Europe being mainly confined to ‘their national framework’, defending ‘national jobs’.
*** Demonstrating the cohesion between global crisis and development of wages and conditions in India – determined by relation of power between capital and workers
Most automobile suppliers and manufactuers faced first a credit squeeze after the 2008 financial crash and since then the devaluation of the Rupee increased costs for import of main raw materials and petrol. With petrol prices increasing (e.g. prices were raised by Rs.7.54 a litre, or 11.5 per cent, to Rs.73.18 in 25 May) and costs for credits expanding, car sales in India slowed down. The diesel price hike by 14 per cent announced by the government in September 2012 will increase the pressure on the industry. Car manufacturers are forced to squeeze the main resource they think they have the control over: the work force. The comrade from Rupe India analysed the relation between wages and productivity increase in the car industry in India, as one of the main determinants for the current unrest:
“Passenger car production has risen from 1.2 million vehicles in 2004-05 to 3 million in 2010-11. Real wages in the auto industry fell 18.9 per cent between 2000-01 and 2009-10. On the other hand, net value added per auto worker has been rising. Each worker added value of Rs 2.9 lakh in 2000-01; this figure rose by 2009-10 to Rs 7.9 lakh. In 2000-01 workers’ wages were 27.4 per cent of value added. By 2009-10, the ratio had fallen to 15.4 per cent. At Maruti workers’ real wages increase by just 5.5% when the consumer price index rose by 50% (2007-11).”
The fact that real wages of workers decline does not mean that company profits automatically increase. Profit margins per manufactured part or car are squeezed. A short glance at the official 2010 Annual Report of Maruti supplier Omax shows that net profits decreased from 2,366 lakh Rs to 2,143 lakh Rs between 2007 and 2011 while capital employed increased from 20,262 lakh Rs to 34,983 lakh Rs. Personnel costs, which includes wages and bonus for managers, was 11,000 lakh Rs in 2010, while general expenses stood at 108,000 lakh.
gwn50_components
In the debates with workers we have to make clear that in their struggles over ‘more money, less work’ they do not mainly face ‘profit greedy (foreign) capitalists’, but a global system and wage [hierarchy]. The wage developments are determined by global developments and also reflect a relation of power between labour and capital. Under these conditions, to tie wages to productivity and to three years agreements – like most of the trade union agreements in Gurgaon area do – can only result in benefits for a small section of workers, and even for them only on a precarious level: “Since May 2012 the production of petrol cars in Gurgaon plant is down. For example there are four engine shops, each of them runs on two shifts. Normally we produce 450 engines per shift, since May 2012 only between 240 and 270. In the assembly department the assembly lines are also stopped for one or one and a half hours everyday, which did not happen before. Some casual workers have been kicked out, due to this overcapacity.”
(Permanent Worker, Engine-Shop, Gurgaon plant)
*** Generalising workers’ organisation on the basis of workers’ wider social existence – turning seeming atomisation into a collective weapon
Modern HR departments obviously have strategical recruitment patterns, e.g. they prefer to hire workers from distant areas in order to cut the ties between shop-floor and sphere of subsistence (patch of land, bigger joint-families) and thereby increase dependency of the worker on the company (wage) – which make long strikes near to impossible; Maruti initially refused to hire workers from other car manufacturers, because they try to avoid importing already made experiences of collective resistance. A deeper analysis of these strategies would be necessary in order to see the potential for turning the seeming weakness of workers into a strength. Historically, organisations which manage to turn the social existence and background of workers into a new form collective power had an enormously fruitful impact on workers’ struggles, such as the early Industrial Workers of the World (IWW), which turned the seeming weakness of seasonal and migrant workers into a mobile, international organisation of direct workers’ action.
Apart from being together on the shop floor the most obvious possibility of turning the social existence into organisation is in the living sphere – see report on life in Aliyar in this newsletter. By cutting workers off from their original villages and families, capital brings them together in new groups, which have the potential of re-creating collective bonds on a more emancipated level. In GurgaonWorkersNews no.48 we reported about a spontaneous solidarity action of several dozen temporary Maruti workers for an injured colleague at Allied Nippon – a connection which were established through living in the same house in a Manesar village. Nevertheless, the fact remains that being away from family and other ties forced many temporary workers, particularly in the suppliers, to leave the area during the Maruti dispute – or they were forced to work: “During the first occupation the 150 housekeeping workers stayed inside with the other workers, but during the one month ‘lock-out’ (good conduct bond dispute in September 2011) around 140 out of 150 went inside and worked. These workers have very little resources to stay without wages and management promised to increase wages if we work.” (Maruti Canteen Worker). Here the relation between ‘locals’ and workers will be crucial in order to survive a longer dispute, and political initiatives will have to break the state and company attempt to buy the consent of the local ex-peasantry.
Maruti needed the strong ties with the ITI sector in order to hire fresh workers in preparation for the ‘lock-out’ in August 2011 – the campus being one of the main pools of skilled industrial reserve army. In May 2012 officially ‘adopted’ 12 ITI’s in Gujarat, promising substantial financial support, as part of their future recruitment strategies for the Gujarat plant. Most of the 1,000 ‘technicians’ hired by Maruti for the expansion of Manesar in 2012 will have come from ITIs. Here again, political initiatives ideally keep in touch with workers already before they get hired. Experiences in this regard – debating and agitating with ITI students – have been made by various comrades, but they have to be thrown in the wider debate.
In the regard of work-force composition the suppliers of electronic parts and electrical harnesses, such as Asti or Motherson Sumi are of particular importance for two reasons. First of all they have the highest level of femal employment in the industrial areas of Delhi, which will in the long run impact on the sexist gender relations within the working class – see report on Asti Electronics. Secondly, at least at Motherson Sumi Gurgaon plant we find a quite exceptional case of manual ‘student workers’. Given the shorter working-hours and the less ‘dirty and heavy’ character of work (electrical wiring) there are many workers at Motherson who study part-time. What is normal in other industrial countries, the mixing of factory and university in workers’ experiences, is quite exceptional in India. A workers organisation should explore whether this situation bears potentials for organic links between the two centres of social unrest.
*** Drawing a battle-map based on the productive cooperation of workers and turning the process of discovering the lines of cooperation into an organisational effort itself
We encourage to read the reports by Maruti workers in this newsletter not as accounts of miserable conditions requiring pity, but as material to draw up future collective strategies of attack. In GurgaonWorkersNews no.50 we wrote:
“As far as possible a workers’ organisation has to make use of regional and global productive interdependence of the labour process. A workers’ organisation would be able to turn this structure into a weapon in the interest of all workers in the chain, disregarding their specific categories. An organisation would make strategical use of the strongest position of workers in the chain (or to find the weakest link), e.g. central suppliers, transport chains etc. and at the same time takes into account the conditions and difficulties of workers in the weakest position. It would use pressure in the strong points to undermine the divisions and differences imposed by management, not due to charity, but need for collective power. A workers’ organisation would be able to coordinate actions disrupting the long chain of production with minimal effort and harm for us and maximal impact on company management. As preparational work we would have to dig out recent historical examples of how workers organised such kind of steps, e.g. during the so-called chess-board strikes at FIAT, Italy, during the 1960s and 1970s, but also during the Gurgaon plant strikes in 2000/2001”
There is nothing new or surprising about the fact that production at Maruti Suzuki depends on a very fragile, spaced-out chain of cooperation between different departments and companies, bridging different categories of workers, wage segments and levels of development. Here the passages of “The Maruti Story” about the setting up of the Gurgaon plant supply-chain – see summary in this newsletter – are quite revealing. The surprising fact is that the local working class so far has not been able to turn this structure against their dead enemy and its representatives.
“Sheet-metal is cut and pressed only ‘one day in advance’, meaning what is pressed today will be assembled tomorrow. The job of the guys in production planning is to make sure that all parts for the next day – around 60,000 different parts – are ready and in right order for the coming production day. A single part missing can cause trouble and production stoppages. If there is an emergency or the sheet-metal cutting machines at the Maruti press-shop cannot supply for ‘over-capacity work’, sheet-metal is cut for Maruti at other companies, such as Manesar Steel Processing” (Permanent Worker, Press-Shop)
“The outer-body press-parts like roof, doors, hood etc. mainly come from Maruti’s own press-shop. The inner-body parts come from about 20 different suppliers, such as JBM, Caparo, Krishna Maruti etc.. Of the bigger parts there is a stock of may be one hour.” (Permanent Worker, Weld-Shop)
“There is a 100 car storage between paint-shop and further assembly.”
(Temp Worker – Paint-Shop)
All parts used at the engine plant at Powertrain arrive more or less on a daily basis, in particular the bigger parts.The raw engine blocks arrive at Powertrain from three different suppliers, one of them is Amtek. Trucks come constantly from Amtek, you probably can fit 100 engines on a truck, daily production is around 1,100 engines, they all go to Maruti Gurgaon plant. There is no proper storage for engines, but in the dispatch area you can store around 200 engines. The engines are used at Maruti more or less immediately, there is no storage on their side either. If they find quality problems with engines they tell Powertrain during the same shift during which the problems occurred.
(Apprentice – Powertrain)
The supplying companies are kept in a relative distance, which might make direct contact between workers a logistical problem. Around 70 per cent of parts are manufactured in the wider Delhi industrial belt, some parts (e.g. like wheel-rims from Patiala, Punjab) come from further away. One potential facilitator in establishing connections between workers at Maruti and those in the supply-chain are workers of suppliers who permanently work in the Maruti Suzuki plant, mainly engaged in logistics and quality check. These workers know the situation at Maruti due to their daily presence on the shop-floor and they know the conditions in their ‘formal companies’, through work-mates, truck-drivers, regular visits. These workers, also due to their everything but privileged conditions, can play a hinge role.
“Suppliers keep workers permanently in the weld-shop, mainly for handling and quality work. Five suppliers jointly keep one worker for handling and one for quality, meaning that per shift there are about eight workers from suppliers on the shop-floor.” (Permanent Worker, Weld-Shop)
“Workers of supplying companies bring parts to the lines, for example the seats from Bharat Seats or Krishna Maruti company. The parts arrive in trucks from the supplying factory, which is in about 2 to 3 km. The workers from Krishna Maruti put the seats at the line and they have to put them in the right sequence of car models. There used to happen occasional problems with supply, but now they keep two trucks with seats extra near the line. The Krishna Maruti workers will get the same wage as we get.”
(Temp – Worker, Final Assembly)
“Some Denso and Lumax workers fit their own parts at the assembly line, but that is an exception.”
(Permanent Worker, Engine-Shop, Gurgaon plant)
“Compressors are assembled at assembly lines, the pipes for the AC’s are dispatched separately. Parts for compressors come from Japan. The pipes come from Korea. The rubber hose pipes come from Bridgestone. There is no storage, trucks leave continuously. The AC-components are delivered directly to the assembly lines at Maruti Suzuki, there is no storage neither at Sanden, nor at Maruti. There are four Sanden Vikas workers permanently employed at Maruti, Manesar, they also live in Manesar. Two for quality check, two for unloading trucks and dispatching AC’s to lines. About six trucks leave Sanden per day, the guys at Manesar plant work 18 hours shifts. Although they work permanently in Maruti they have to pay 30 Rs for a meal at the Maruti canteen. These workers know that there has been a strike at Sanden in 2010 and that there is still trouble. Since March 2012 there have been problems of completing the dispatch to Maruti, not enough or faulty AC’s arrived at Maruti. The problems emerged at a time when a new model was introduced. Maruti made Sanden pay penalties, if dispatches were not complete. In order to find out what the problem was Sanden ordered higher management people to stay during night-shifts and analyse the work process. The situation is that permanent workers only work on A-shift and since 4 permanents have been kicked out in 2009, permanent workers refuse working overtime. So workers hired through contractor employed on B-shift work from 2:30 pm till next morning 6:30 am – this is 16-hours on stretch. While on A-shift they work 8.5 hours. The solution of management for problems of dispatch: B-shift workers must be tired after 15 hours of work, so they changed shift patterns and introduced two 12-hours shifts instead. This also means that when shift changes on Saturday, workers have to work a 24 hours-shift, as ‘compensation’ workers get 50 Rs extra for food and two ‘breakfasts’.”
(Permanent Worker, Sanden Vikas, Faridabad)
Obviously the supply-chain does not stop at this first level of suppliers and it is well known that workers’ conditions deteriorate once we enter second- or third-tier suppliers.
“As an illustration of the three-tiered structure of subcontracting, we can mention that Maruti-Suzuki subcontracts to Munjal Showa which subcontracts to Mod Serap which in turn subcontracts to Modern High Tech Auto. Or, Maruti Suzuki subcontracts to Automax or Mark Exhaust which in turn subcontract to Hema Engineering which in turn subcontracts to Kiran Auto. As an example of first and second level of subcontracting combined, Jay Bharat Maruti, Plant 1 supplies directly to MarutiSuzuki, and indirectly via supplying to Delphi which is a first level subcontractor of Maruti.”
(Bose on Automobile Industry in Delhi – see appendix)
“There are 200 permanents and 400 workers hired through three different contractors. We work 12 hours shifts and manufacture parts for automobile suppliers like Napino, Denso, JNS, Pricol, Delphi. When shift changes on Sunday then workers in the plastic moulding department and in the copper press shop department have to work 20 hours on stretch, from 8 pm Saturday till 4 pm on Sunday. The newly hired helpers hired through contractor get 4,500 Rs.”
(Temporary Worker, Vinay Auto, Manesar)
“Bundy is a fuel-pipe manufacturer for Maruti Suzuki. Bundy has one worker permanently working ‘between’ Bundy and Maruti Suzuki doing quality check and coordination. Bundy itself employs about 550 workers out of which 300 through contractor. The workers are paid on piece rate, there is no basic wage. Workers have to operate bending machines, burring machines etc. and are paid between 10 and 30 paise per piece. daily target is around 3,000 pieces. One truck leaves Bundy for Maruti per day.”
(Bundy Company Worker, Manesar)
“The factory employs 300 workers on two 12-hours shifts. The company manufactures die-casting products for Honda, Hero motorcycles and Maruti Suzuki cars. During the weekly shift change the Saturday night-shift has to work 20 hours on stretch and the Sunday day shift 16 hours. Over-time is paid single rate.”
(Temporary Worker, Kiran Udyog, Manesar)
There are situations when workers can (and are forced) to discover their inter-dependence within the production process: once there is an interruption of part supply. This might be caused by workers’ struggles or other – from the perspective of capital – ‘natural disasters’, e.g. Honda Siel (India) sources several electronic and underbody parts from its Thailand plant, due to floods in Thailand in December 2011 parts supply was irregular. Politically workers were not able to make use of the fact that during the Maruti dispute and the current lock-out since 21st of July most suppliers were effected, many of them shutting down production completely. During this time conscious connections between workers could have been created. On the other way round there are daily conflicts in one of the 800, 900, … suppliers of Maruti, which have the potential to cause ripple-effects. A workers’ collective should make efforts to find out about these conflicts and encourage to develop their potential.
“In the factory 300 workers on two 12-hours shifts manufacture steering locks and keys for Mahindra, Tata Sumo, Toyota Inova and Maruti Suzuki. The overtime is paid at single rate. A first installment of 15 days of overtime payment for December was paid on 15th of February 2012, workers demanded that the rest should be paid by 25th of February – in response the company called the police and one worker was arrested. This worker was sacked and the company refused to pay him the outstanding overtime payment from December to February. The director said that he had to pay the police and that he now won’t pay any money to the worker.”
(Jay Switch Worker, Gurgaon)
In the 1990 the latest hype of ‘capitalist innovation’ which was supposed to overcome the industrial illnesses of the huge factory complexes of the 1970s was the so-called ‘Benetton’-model – a model of outsourcing of textile orders to smallest specialised textile units combined by big garment companies, which was set-up in the north of Italy. In the end it was clear that even with micro-electronics and flexible transport most of the industrial production requires close cooperation and concentration of capital. What was not possible in Western Europe in the 1990s seems a little more realistic in Delhi’s industrial areas in the 2000s. The combination of extremely low wages encouraging labour intensive production, of supply of over-used machinery from the industrial decadence in the global north, a hinterland of slum-production and flexible smallest-scale transport units (self-employed three-wheelers etc.) combined and coordinated by modern logistic management in the bigger plants seem to enable the local industry – at least in times of emergency – to enforce a very flexible exploitation of a network of small manufacturing units. For example during the lock-out at Senior Flexonics supplier – see GurgaonWorkersNews no.50 – management was not only able to hire temp workers within a few days and keep production running. They were also able to outsource within the first two weeks the more skilled work (CNC and power-press operations) to smaller units like Lakki Enterprises, Gurgaon and Ajay Engineering, Faridabad and limited the work in the ‘battled’ factory in Manesar to assembling operations. In this regard, current efforts of organising in the ‘workshop-territory’, such as the strike organised by almond workers in the north of Delhi, using a street-wise delegation system, will become important experiences once they are seen as part of a wider context of centres and productive periphery.
Last, but not least, this type of supply-chain requires a flexible transport organisation. There are at least 2,500 trucks, which enter the Maruti Gurgaon facility everyday with components, and at least 500 leave the factory premises with manufactured vehicles. In addition a similar amount of trucks for the Maruti Manesar plant. Even if we take into account that trucks might go back and forth six to eight times a day and that not all trucks have two drivers, we still speak of another department of several thousand workers.
The conditions of truck-drivers are well known. Two drivers drive three days non-stop from Manesar to ports in Bombay and back. Long-distance workers live in the trucks for weeks. Maruti relies on an army of workers who spend most of their time out of direct control of supervisors and other officials, and a generally volatile sector (strikes against petrol price hikes, road conditions etc.). Currently Maruti tries to deal with the emerging problems by ‘centralisation’ and rationalisation through shifting transport of finished cars onto tracks and by extending the electronic control to the time when workers are on the road. The shift onto tracks is a major infrastructural and therefore political operation – the plans to increase rail-transport from currently 5 to 35 per cent within the next two years seems ambitious. Up to now Haryana State Industrial and Infrastructure Development Corp. Ltd (HSIIDC) hasn’t been able to acquire the land needed to lay dedicated tracks from Patli station in Manesar to the company’s plant 18km away. With a growing importance of export markets the assembly lines of Maruti will catapult over-produced cars from Delhi towards the sea ports in Gujarat and Maharashtra, thereby ploughing an industrial corridor through Rajasthan, connecting existing and emerging industrial centres on the way – see: https://gurgaonworkersnews.wordpress.com/gurgaonworkersnews-no-22/#fn62
The other focus is electronic armament to maintain control over the transport department. Maruti engaged in a contract with US-company Trimble in early 2012. From a company statement:
“Maruti Suzuki India Limited (MSIL) is deploying the Trimble trako Visual Cargo solution in outbound logistics trucks that transport new cars from the factory to Maruti Suzuki dealers across India. Trimble’s trako Visual Cargo is a software as a service solution that provides on-demand visibility — from loading to delivery location — of cargo vehicles using Trimble GPS devices. Trimble applies technology to make field and mobile workers in businesses and government significantly more productive. Solutions are focused on applications requiring position or location — including surveying, construction, agriculture, fleet and asset management, public safety and mapping. In addition to utilizing positioning technologies, such as GPS, lasers and optics, Wireless technologies are utilized to deliver the solution to the user and to ensure a tight coupling of the field and the back office.” Deeper conversations with truck drivers about the actual impact of these technological shackles onto their work have to form part of a militant research of the changing relation between living and dead labour.
*** Destroying the despotism of systemic and strategical uneven technological development
The struggles at the A-plant in 2011 hastened Maruti to take the B-plant into operation, since then management confronts workers not only with a divided workforce – the workers hired during the lockout were shifted to the B-plant – but also with uneven development on plant level. The degree of automation is higher in the B-plant. This creates a cascade of uneven development within Maruti, if we take into account the technological difference between the old plant in Gurgaon and Manesar A-plant. These differences in development are systemic, but used strategically, as Maruti chairman points out in “The Maruti Story”, his account of the development at Maruti.
“A new site was needed for future expansion and Manesar was selected. […] SMC wanted this plant to be very similar to the plant in Kosai, Japan, so that there could be a high level of automation, and the best SMC practice could be established here from the start. Suzuki did not want this plant to become an extension of the Gurgaon plant, which had been built over twenty years and had much more manual operations. He wanted the plants at Gurgaon and Manesar to compete with each other in areas like productivity and quality, with each being a benchmark for the other.”
Workers in the A-plant have to face that in 200 metres distance their job is performed by machinery – they have to face their potential replacement.
“By now the B-plant has started production. There most of the workers are newly hired. The work load is higher, compared to the A-plant. In the A-plant there are 76 workers in the axle department, in the B-plant only 51.”
(Temporary Worker, Final Assembly)
“Since 2006 the numbers of work-stations came down from 16 to 8, to 4 since June 2011 – this happened through increased automation and usage of robots. So far work had been re-distributed in a way that workers numbers did not come down as much as work was replaced (one robot replaces about ten workers). Workers initially operated three hand-welding tools, now one workers operates only one. The work-load has become less in the A-plant.”
(Permanent Worker, Weld-Shop)
It is also important to note that with increasing automation the ratio of temporary workers also increase. This is most prominent in the weld-shop:
“In A-plant around 25 per cent of the workers are permanent, 10 per cent are trainees, 10 per cent are apprentices and 55 per cent are hired through contractor. In the B-plant the ratio is 10 per cent permanent and 70 per cent temporary, while at the same time there the level of automation is much higher. In the A-plant there are still 250 to 300 workers doing spot-welding by hand, in B-plant there is full automation.” We find similar situations in the paint-shop.
The question of when to introduce machinery and to replace living labour is only seemingly an economic question of ‘productivity’. First of all, capitalist productivity is not mainly defined by the question whether running a machine (which still requires living labour for operation) instead of engaging in manual work saves ‘labour-time’ to such an extend that the time to construct and maintain a machine (and to deal with social and ecological consequences) is made up for. Being a society based on wage labour and commodity production, ‘capitalist productivity’ is rather determined by ‘saving labour costs per produced commodity’. Workers directly compete with machines, as long as wages are relatively low enough, workers are employed despite the ‘technological possibility’ to replace their labour. This is the reason why unlike in the global north, the automobile supply-chain in India still reaches into the home-based production of the slum-areas. We can also see that before making the investment into new machinery, capital tries to squeeze living labour as much as possible. The phase before the opening of a new plant at Maruti is characterised by increase in exploitation, again a quote from “The Maruti Story”:
“The work on expanding capacity and establishing a second plant at the same site, started about the end of 1992 and was completed in 1994. With the plant, production rapidly increased to 278,000 in 1995-96, and the need for another plant was obvious. One of the reasons for Maruti being able to keep prices of cars low – and make profits – was the ability to run both these plants at about 140 per cent of the rated capacity. This was achieved by a combination of balancing facilities, innovative practices and full cooperation from the workers.”
During the phase before the B-plant got operational, workers in Manesar had to work double-shifts, there was an ‘off-line’ car assembly section without conveyor belt system, the A-plant was running on similar ‘extra-capacity’ but his time “the full cooperation from the workers” snapped.
This ‘illogical’ use of human energy and creativity creates a constant tension within the production process. Workers not only have to face up to ‘be made into a cog of a machine’ they are also confronted with this ‘political-social’ absurdity. Therefore the other ‘political aspect’ of capitalist use of machinery relates to the question of whether machinery creates a higher degree of productivity by being both means of control/segmentation of workers and means of combination of labour. Without the element of controlling despotism of machinery no capitalist productivity. Within the plant workers can see the contradiction of capitalist use of machinery every day.
“One one side are 12 painting robots. On the other, are workers carrying 25 kilo headloads of used screens up two flights of stairs and returning with a 30 kilo load of clean screens. Each worker has to carry 70-80 screens up and down the stairs, working an extra hour without pay if the job is not done by the end of the shift.”
(Temp Worker – Paint-Shop)
Despite the Manesar plant being a modern plant according to global standards there are still operations which are done manually, which in other plants would be automatised – a potential trump-card in the sleeve of management. It will be part of our work to identify these operations and to be prepared for battle. In a certain way related to this lower degree of automation is another major difference to most passenger car assembly plants in the global north – the fact that the assembly plants in Gurgaon and Manesar don’t run 24 hours, which has become a standard in Europe during the 1980s and 1990s.
“In the A-plant, at the work-station where the chassis meets engine and gearbox, the engine is fitted manually to the chassis. Similarly, the front-shield is put in by hand, not by a robot. At the station where the doors are fitted you get 45 sec for a door. If you are quick you can make it in 30 sec and work ahead. There were occasional night-shifts in the assembly-department, but now night-shifts are only run in the press-, and weld-shop and in the bumper-shop at the machine stations.”
(Temp Worker – Final Assembly)
In these regards the relation between workers and machines express the political power relation between working class and capital, the political contradiction between social potentials and the misery of class society. Alquati claimed that collective ‘workers’ science’ would be able to read machinery like a geology of class struggle, the conflicts of the past and the productive knowledge of workers of the past now moulded into the apparatus – appearing as features of power of capital. A more in depth debate with workers about the changing character of this relation will have to take place. Some have taken place:
“Most workers in the subcontracting chain have 1:1 interface with machines. Where there are U-shaped production lines such as in Clutch Auto, Gabriel, Echlin, BTR Wadco, and Sona Koyo, workers do multi-machining in terms of 1:2 to even 1:10 interface with machines. Gabriel is famous for cellular manufacturing. Tier 2 units such as Sona Okegawa, Sona Somic and Vital Castings have U-shaped cells with multi-machining in terms of 1:4 interface with machines. In some units, workers talk about multi-machining even on straight production lines. Multi-machining causes a lot of stress to the workers.”
(Bose – see appendix)
*** Destroying the veil of capitalist hierarchy: monopoly over machinery and information, fetish of quality and qualification
Obviously a mere technological control of workers is not sufficient, the control has to be maintained through personal hierarchy, which is first of all a hierarchical division of labour. Similar to the attempt to disguise the systemically despotic character of machinery behind ‘technological neutrality’, also the hierarchy between workers and supervisory staff is justified by the fetish of ‘qualification’.
“The promotion system in some of the units is as follows: from senior operator to supervisor in Automax; operator to line supervisor to shift-in-charge at Caparo; semi-skilled to skilled to supervisor at Engineers Combine; associate to section head to supervisor to executive at Motherson Sumi; operator to line monitor to supervisor to junior engineer at QH Talbros; and assistant to operator to senior operator to foreman at Subros.”
(Bose – see appendix)
First of all, a certain position in the production process is less determined by individual seniority, knowledge, skills, but by the hierarchical requirements of the production process: not everyone can become a foreman, department manager or engineer, because by definition a position within a hierarchy is exclusive. Who gets promoted is therefore a process of selection. Capital combines hierarchical functions (control, putting pressure to work etc.) with productive functions: if workers have to ask the supervisor for certain information necessary to perform their tasks, they will be more likely to accept the orders he gives them; if a foreman can criticise the ‘quality’ on ‘objective grounds’, he is more likely to be able to enforce higher levels of quantity. The capitalist production process isolates collective knowledge into individual functions as its material and ideological basis for hierarchy, in particular knowledge about machinery. At the same time ‘general knowledge’ of workers is not formalised and therefore degraded:
“Permanent workers get one day training how to program the robots, the temporary workers don’t get this training.” (Permanent Worker, Weld-Shop)
“Within your area at the assembly-line, which usually includes 5 to 10 work-stations, they change you around on a daily level. Even if you know how to work at five different stations, you might still be paid helper rate.”
(Temp-Worker, Final Assembly)
The capitalist contradiction between quantity and quality, between exchange and use value creates constant frustration. The ‘quality’ of a product is used in order to black-mail workers into accepting company rules and hierarchy, at the same time the requirements of profit-production – output! – undermines any sensible consideration about quality and creative use of humans mental capabilities. This is already felt by workers in their ‘formal’ qualification process, which is mainly a formation process of a certain position within hierarchical division of labour:
“We are 245 apprentices in the factory, coming from different ITIs. We have been sent here to see our trade in practice, to observe it closely, to make experiences and to learn. But here things run according to the will of Suzuki company. According to the needs of the companies we employed in the car engine plant, transmission plant or the two-wheeler engine plant and we have to perform work different from our ITI trade. We work in A, B and C-shift, not in general shift how it is officially said. Instead of observing-learning-making experiences we work as normal production workers. There are no classes for apprentices, neither inside nor outside the plant. The work load is so high that the apprentices have no chance to see the whole plant, they have to stay at their station. ”
(Apprentice – Suzuki Powertrain)
Another hierarchical distinction is created by formal distinction between productive and reproductive labour. In a modern plant the work of housekeeping workers, cleaners, loaders, canteen workers and so on are essential for the workers in the production department to perform their tasks on a continuous basis. With the re-structuring process of the 1980s capital made an effort to segment these essential tasks of the production process as ‘service work’, which degrades the work performed even on a linguistic level. Attached to the segmentation and categorisation of ‘service work’ was an attack on workers’ conditions. At Maruti Suzuki Manesar plant the canteen workers work 12-hours-shifts plus unpaid over-time, they are not paid the minimum wage and are not included in the ‘official struggle – see workers’ report.
4) Workers’ Reports
Gate at Maruti Suzuki Manesar…
4.1) Reports from Maruti Manesar Workers
4.1.1) Press-Shop Worker
4.1.2) Weld-Shop Workers
4.1.3) Paint-Shop Workers
4.1.4) Bumper-Shop Worker
4.1.5) Final Assembly Workers
4.1.6) Canteen and Housekeeping Workers
4.2) Reports from Suzuki Powertrain Workers (Engine and Gearbox)
4.3) Report from Maruti Gurgaon Worker (Engine-Shop)
4.4) Reports from Maruti Supply-Chain Workers
4.4.1) Asti Electronics Worker
4.4.2) Sanden Vikas Worker
4.5) Report on Life in Aliyar, a Workers’ Village in Manesar Industrial Zone
———————
4.1) Reports from Maruti Manesar Workers
4.1.1) Permanent Worker, Press-Shop, Maruti Suzuki Manesar plant (May 2012)
Aliyar auto-stand – New source of income for local ex-peasants…
There are 40 permanents working on one shift in the press-shop – which includes apprentices and trainees – plus 30 workers hired through contractor. The press-shop runs on three shifts. The harder work, such as taking pressed parts out of the machines, is done by workers hired through contractor and apprentices. In general the work in the press-shop is less hard, because most work-stations are machine-stations, meaning that you have a little breathing space while the machine works. In the weld-shop and assembly workers have a harder time.
When the union was formed workers in the press-shop were sure that they would be able to stop work and production, but they were not entirely sure whether workers in other departments – mainly the assembly department where a lot of workers hired through contractors were not informed about the union process – would support them. Six out of eleven current union body members are from the press-shop.
The production sequence changes every day, meaning that every day the ratio between different models changes and therefore supply of different parts is necessary. The supply of the right parts in the right sequence is the job of the PPC (Production Planning and Control) department.
In the press-shop the sheet-metal arrives in big coils. The companies which supply the sheet metal are:
Tata Steel Faridabad
TSPDL is equipped with processing plants at Jamshedpur, Faridabad, Pune, Tada, Pantnagar with a processing capacity of 2.5 Million tones per annum. TSPDL as Tier 1 supplier is using Roll Forming and Stretch Bending technology.
http://www.tspdl.com/
Essar Steel
http://www.essarsteel.com/
Nippon Steel
http://www.nipponsteels.com/contact.html
JP Steel
Sumimoto
Maruti Suzuki keeps a strict ‘no single source’-policy. There is a storage for normal sheet-metal for nearly two month [?!], but certain types of steel, e.g. galvanised steel for export cars like the A-Star is not stored in such volume. The sheet metal is then cut to size. Different parts of the car require different sizes, and parts for different models also vary in size, meaning that there are about 200 different sizes of sheet metal. If there is an emergency or the sheet-metal cutting machines at the Maruti press-shop cannot supply for ‘over-capacity work’, sheet-metal is cut for Maruti at other companies, such as:
Manesar Steel Processing
http://www.mtlo.co.jp/us/news/2010/101115.html
Manesar Steel Procvessing is a joint-venture between Metal One Corporation of Japan and Maruti Suzuki India Limited (MSIL). The company handles and cuts steel coil to carry out slitting, leveling, shearing, blanking, warehousing and supplying to fufil mainly Maruti’s vendor’s requirements. Main facilities: 1 large slitter line, 1 large leveler line, 1 mini leveler line, and 3 shearing lines. Processing capacity 13,000 tonnes per month.
Then there are six lines of power presses. The press-tools of these machines change automatically, according to different form of parts to be pressed. Sheet-metal is cut and pressed only ‘one day in advance’, meaning what is pressed today will be assembled tomorrow. The job of the guys in production planning is to make sure that all parts for the next day – around 60,000 different parts – are ready and in right order for the coming production day. A single part missing can cause trouble and production stoppages. Per shift there is only one guy doing this job – he is an ITI worker and gets 18,000 Rs (24,000 Rs including annual bonuses). They have to count parts, e.g. they have to see that a trolley with 1,000 parts is filled, and then enter the data into the computer system for the weld-shop, which is the next production department in line. Containers with parts are moved by fork-lifts to a storage / warehouse situated between press- and weld-shop.
4.1.2) Permanent Worker, Weld-Shop Maruti Manesar (June 2012)
Empty public housing complex in Aliyar – The rents are too high…
The outer-body press-parts like roof, doors, hood etc. mainly come from Maruti’s own press-shop. The inner-body parts come from about 20 different suppliers, such as JBM, Caparo, Krishna Maruti, Bellsonica etc.. Of the bigger parts there is a stock of may be one hour. In the A-plant you still have a lot of hand-welding work. First the three parts of the underbody are joint by hand-welding, then finally welded by robot at the main line. Similarly the main-body, first manual work, then finalisation by robot. there is also manual assembly happening in the weld-shop, e.g. the two door panels are fixed together by screw-gun operation. Suppliers keep workers permanently in the weld-shop, mainly for handling and quality work. Five suppliers jointly keep one worker for handling and one for quality, meaning that per shift there are about eight workers from suppliers on the shop-floor. Permanent workers get one day training how to program the robots, the temporary workers to get this training.
In A-plant around 25 per cent of the workers are permanent, 10 per cent are trainees, 10 per cent are apprentices and 55 per cent are hired through contractor. In the B-plant the ratio is 10 per cent permanent and 70 per cent temporary, while at the same time there the level of automation is much higher. While in the A-plant there are still 250 to 300 workers doing spot-welding by hand, there is full automation in B-plant. In the A-plant around 200 out of 300 workers are hired through contractor. Since 2006 the numbers of work-stations came down from 16 to 8, to 4 since June 2011 – this happened through increased automation and usage of robots. So far work had been re-distributed in a way that workers numbers did not come down as much as work was replaced (one robot replaces about ten workers). Workers initially operated three hand-welding tools, now one workers operates only one. The work-load has become less in the A-plant.
The PPRA (productivity and attendance bonus) forms 50 per cent of our wage. In the current demand notice there is a demand that the bonus should be attached to the amount of cars produced, e.g. if Manesar produces 900 cars per day, the bonus should be 4 Rs per car, if between 900 and 1,200 then 6 Rs, if over 1,200 then 8 Rs.
There is a clear policy to divide permanents from temporary workers. Supervisors don’t put any pressure on permanents, you can do your job, you can walk around. Pressure is solely on temporary workers. These workers obviously complain, but they don’t complain in front of the supervisor, they express their anger towards the permanent workers – they in turn tell the temporary workers to shut up and work.
At my line there are around 15 temporary workers out of which 6 did not have an original ITI. Last month the contractor said that they should return their gate-pass and that they will not be let to work again. I objected and enforced that the guys can continue working.
4.1.3) Temporary Worker, Paint-Shop, Manesar A-Plant (July 2011)
Entrance to Aliyar Gaon…
I work at the sealer-line, the cars arrive there from the weld-shop. There are about 38 work-stations at the sealer line, two workers at each station. I work with a hand-gun. Most of the workers at the line are temporary or casual workers, trainees. The permanent workers still do the same work here, it is not that they only do the easy work. There is a 100 car storage between paint-shop and further assembly.
One one side are 12 painting robots. On the other, are workers carrying 25 kilo headloads of used screens up two flights of stairs and returning with a 30 kilo load of clean screens. Each worker has to carry 70-80 screens up and down the stairs, working an extra hour without pay if the job is not done by the end of the shift. The lunch-break (30 minutes) and tea break (15 minutes) are not counted as part of the working time on the shift.
The Quality Maintenance Unit employs 95 workers hired through a labour contractor. Their job includes cleaning out the tanks that hold thinners and solvents. They are always on the C-shift – from 12.30 in the night to 8.30 the next morning. Workers on the C-shift work non-stop. There are no breaks for food or tea. The food allowance of Rs.44/- that they used to be given has now been slashed to half. By the end of the shift, they are exhausted, giddy and nauseous from the chemical fumes they inhale. Workers in the Quality Maintenance Unit put in 32 to 192 hours of overtime every month, for which they are paid only Rs.28/- per hour, well short of the legal minimum of 1.5 times the normal wage. For many of these workers, the shift can extend to 17.5 hours of non-stop work without breaks or food.
For A-plant workers there has never been a realistic promise that they will get a permanent job in B- or C-plant. Those workers who had been hired during lock-out still work through contractor in B-plant.
4.1.4) Trainee, Bumper-Shop (June 2012)
The immaculate cold face of capital – Factories bordering Aliyar…
The plastic moulding of bumpers takes place in the department itself, lights and other devices are attached to the bumpers, then ‘bumper-shop’ workers attach the bumper to the car at the assembly line. Out of 250 workers in the department only 20 are permanent, most are trainees and workers hired through contractor. Some of us try to become trainees, we have to pass a test. Around 500 questions, mostly on health and safety and quality, also “where have you been during the strike period”. We have to undergo a medical test, too. In the bumper-shop 24 workers went for the test in early 2012, only 7 were taken on as trainees.
4.1.5) Temporary Worker, Final Assembly (June 2012)
Workers’ rooms in Aliyar – One shared by four, five…
On Situation after Settlement in October 2011
After the first wage increase for workers hired through contractors and apprentices the company pays those workers hired through contractor with ITI qualification 238.38 Rs per day, plus 75 Rs attendance allowance, 4 Rs allowance for cleaning working clothes, 19.62 Rs medical allowance, and 19.62 transport allowance, which sums up to 356.62 Rs per day. Compared to before the dispute this means an average wage increase from 6,500 Rs to about 8,500 Rs per month. The workers hired through contractor without ITI qualification receive 280.93 Rs per day. On bank holidays only the basic wage is paid, without the allowances. Now workers can take two holidays within three months – before the dispute it was only one holiday which also had to be approved by the supervisor – which hardly happened. The permanent workers can take 4 holidays within three months.
You still have to be at your workplace 15 minutes before official start of shift, otherwise you are marked as absent for half of the day.If you go to early into meal break or come back 5 minutes late, the same happens. Now, as before, in case you are ill you are supposed to take medicine and start working immediately – but at least now the worker can go himself and take medicine, before the supervisor came and gave it to you.
During the time when workers occupied the factory – or removed the occupation through the company – there was only the A-plant in operation. By now the B-plant has started production. There most of the workers are newly hired. The work load is higher, compared to the A-plant. In the A-plant there are 76 workers in the axle department, in the B-plant only 51. There are reliefers [replacement workers] in the A-, but not in the B-plant. In both A- and B-plant, out of the 127 workers in the MX department non is permanent, all hired through contractor. Where there should be 8 people employed, you will find 4 workers. The line is still holy, it’s not supposed to stop. Yes, before the dispute they called you ‘Eh, you’, now they call you ‘son’, but the threats continue. Difficulties have not decreased through the fact that there are now two canteens, because with the B-plant the number of workers has increased.
They do nothing for the workers hired through contractors. The new union leaders told us to hold back until 4th of February, until the union will be recognised. Now they say, wait till the 24th of February.
Temporary Worker, Final Assembly, Manesar B-Plant
Within your area at the assembly-line, which usually includes 5 to 10 work-stations, they change you around on a daily level. Even if you know how to work at five different stations, you might still be paid helper rate. You used to have problems with toilet breaks, this got better. If you have to go, the reliever takes over and does your work. The reliever tends to be a permanent worker. If both relievers are busy, the supervisor takes over. Supervisors went through special training at Maruti and they tend to have a diploma.Their behaviour changed a bit after October 2011, they tend to be friendlier.
Workers of supplying companies bring parts to the lines, for example the seats from Bharat Seats or Krishna Maruti company. The parts arrive in trucks from the supplying factory, which is in about 2 to 3 km. The workers from Krishna Maruti put the seats at the line and they have to put them in the right sequence of car models. There used to happen occasional problems with supply, but now they keep two trucks with seats extra near the line. The Krishna Maruti workers will get the same wage as we get.
In general there are not too many stoppages of the line. may be once or twice per day, if at all, and usually not longer than for a minute or two. Sometimes Japanese workers come to the plant in order to fix machinery. There is little to no contact with these workers, also due to language problems.
In the A-plant, at the work-station where the chassis meets engine and gearbox, the engine is fitted manually to the chassis. Similarly, the front-shield is put in by hand, not by a robot. At the station where the doors are fitted you get 45 sec for a door. If you are quick you can make it in 30 sec and work ahead. There were occasional night-shifts in the assembly-department, but now night-shifts are only run in the press-, and weld-shop and in the bumper-shop at the machine stations. The ‘off-line’ [without conveyor-belt system] production in the final assembly has been stopped in October 2011, after the occupation and after the B-plant came into operation.
From a Press Report:
“When I first began working for Maruti, assembly lines used to run right through my dreams,” said a worker with a laugh, “These days I suppose I’m so tired that I don’t get dreams anymore.”
In Manesar, Maruti produces about 180 variants of three basic models. When a car rolls in, the worker looks at a large matrix pasted on the vehicle that indicates if the car is a left or right hand drive, powered by petrol, diesel or compressed natural gas engines intended for the domestic, European or general export market. Depending on his work station the worker chooses from 32 different upholstered seats, 90 tyre and wheel assemblies, and innumerable kinds of wire-harnesses, air conditioning tubes, steering wheels, dashboard trims, gearboxes, switches, locks, and door trims, in an average time of 50 seconds per car. For parts like air conditioning tubes, the worker stands between a set of parts racks. As a particular car variant rolls in, a light above the corresponding parts rack blinks with increasing urgency as the worker runs to it, grabs a part and pulls a cord to acknowledge he has chosen the right part. He then steps onto the conveyor belt, fits the part and rushes back to match the next car to the next blinking parts rack before an alarm rings. If the line halts, signboards across the shop floor light up – flashing the number of the workstation where the line has stopped and the duration of the stoppage. Another board displays the total time ‘lost’ during the shift; a scrolling ticker lists the production targets at a given time of the day, the actual cars produced and the variance. “For every fault, the feedback is recorded and the worker has to sign against it… it goes into his record,” said a worker, speaking on condition of anonymity as every Maruti worker must sign ‘Standing Orders’ that, among 100 other conditions, bar them from slowing down work, singing, gossiping, spreading rumours and making derogatory statements against the company and management. The work record is examined during yearly appraisals. (Gone in 50 seconds, Aman Sethi, The Hindu)
4.1.6) Temporary Worker, Canteen and Housekeeping, A-Plant (May 2012)
Workers’ rooms in Aliyar…
There are now two canteens in the factory, in both of them workers work on two 12-hours shifts. the A-canteen is huge. there are `16 counters to take food, two canteen workers take care of one counter. then there are workers who cut the vegetables, others who cook the food, others who bring it to the counters, who clean the dishes, who clean the canteen, who make tea and who bring the tea to the departments. At 8:30 am workers get tea and snacks, at 10:30 am again tea, at 2:30 pm again tea and biscuits, at 3:30 pm tea and biscuits for the general shift and staff, at 6 pm tea and snacks. For the different shifts and categories of workers one meal-time break follows the other in a constant flow from 11 am till 3 pm. This is the work of the canteen workers of the 8 am to 8 pm shift. the same work is done by the night-shift. the A-Canteen supplies food for the assembly departments of both A- and B-plant, for the paint-shop workers of both plants, for Sand D (drivers and repair workers) and for the 2,500 construction workers of Larsen and Toubro who work on the construction of the third plant. In the A-canteen there are 350 workers for each shift, in the B-canteen more than 150 per shift. The shift of the canteen workers does not change – the night-shift workers work nights constantly. The contractor of the canteen changes frequently, but the canteen workers remain more or less the same. On 1st of March the contractor changed and the new one promised a wage increase. The old contractor paid the chef 19,000 Rs, the new contractor only pays 13,500 Rs. The workers who make samosa, roti and who operate the kneading machines used to be paid 5,000 Rs for 26 days of work of 12 hours each. the rest of the canteen workers used to be paid 4,000 Rs for the same amount of work of which 250 Rs is cut for ESI and PF. Now the new contractor announced that he will pay 4,400 Rs. For the 500 canteen workers per shift there are one general manager, five managers and 30 supervisors in both canteens. None of the canteen workers has an ESI card. Canteen workers don’t receive a pay-slip. When workers are forced to stay two to four hours longer after a 12-hours shift the managers say that they will be paid for this work, but actually they are not. the work load is high. If some workers take a day off you are supposed to take over their work and work at three different places the same time. Expecting trouble and abuses from the manager you run back-and-forth, supplying the production workers with tea. The factory is spread out on 600 acres – it’s quite an effort to supply all production workers with tea. At Suzuki Powertrain canteen the situation is the same, they just start and finish an hour later.
‘During the first occupation the 150 housekeeping workers stayed inside with the other workers, but during the one month ‘lock-out’ (good conduct bond dispute in September 2011) around 140 out of 150 went inside and worked. These workers have very little resources to stay without wages and management promised to increase wages if we work.
4.2) Apprentice, Suzuki Powertrain, Engine-Shop (January 2012)
Shops in Aliyar…
(Plot 1, Sector 8, IMT Manesar)
Maruti Suzuki only started gearbox production in 2007, before that most gears were imported from Japan, because localisation was not seen as profitable as long as production volume was below 700,00 cars. Around 2010 Suzuki Powertrain in Manesar was actually able to produce gears cheaper than the imported gears (landed costs) and Maruti decided to fuse with Powertrain by end of 2012, also partly due the fact that at Powertrain the trouble with the workers now seems under control with the new trade union arrangement.
We are 245 apprentices in the factory, coming from different ITIs. We have been sent here to see our trade in practice, to observe it closely, to make experiences and to learn. This is why we are not given ESI and we are supposed to work only the general shift and go to a nearby ITI for theoretical lessons once a week. But here things run according to the will of Suzuki company. According to the needs of the companies we employed in the car engine plant, transmission plant or the two-wheeler engine plant and we have to perform work different from our ITI trade. We work in A, B and C-shift, not in general shift how it is officially said. Instead of observing-learning-making experiences we work as normal production workers. We are given the normal targets and have to meet them. Some supervisors swear at us a lot. During the 7 am shift you are supposed to be in the department at 6:45 and at the line at 6:58 am. At the work-stations you work standing upright all the time. To do the same job not only for 8 hours, but every day for 8 hours is oppressing. You only endure this because one can joke with the permanent workers, trainees and workers hired through contractor who work next to you. Since the agreement between union and management, which increased wages and production levels, the work load has increased a lot, also for us. Many of the permanent workers don’t find a single minute of time to catch their breath – the assembly line in the transmission plant is one of such places, we consider it as the worst place. There the canteen food is also bad and you have to cue up in six long lines, swallow your food and hurry back – because if you are a minute late you are in trouble. In the factories there are various injustices going on. The wage of the apprentices are cut by 16 Rs a day for food and tea, the wage of the workers hired through contractors is not cut. The permanent workers, trainees and apprentices get a night-shift bonus of 35 Rs in the B-shift and 50 Rs in the C-shift, but the workers hired through contractor does not get this bonus. The permanent workers on C-shift can leave at 7 am, while the apprentices have to work one and a half hours longer till 8:30 am. There are big differences between wages, and also when it comes to the company bus service. There are no classes for apprentices, neither inside nor outside the plant. The work load is so high that the apprentices have no chance to see the whole plant, they have to stay at their station. Eight hours overtime used to be paid 150 Rs, now they pay 240 Rs and you can also take time of in lieu – in order to visit home in your village you accumulate overtime. Now they don’t give you a permanent job after having finished your apprenticeship. Only few are re-hired as trainees or through contractor after finishing the apprenticeship. In the form of apprentices we are very cheap workers for the company.
Normally they give workers hired through contractors a break after six months of employment, which they don’t do at Maruti Suzuki. At Powertrain you might be able to re-apply after three months, but it will be difficult to get the job back. The contractors for Powertrain and Maruti Suzuki are different, at Powertrain there are three main contractors, at Maruti Suzuki there are four. They tend to stand at the Maruti Suzuki gate, they take your resume and ID. You are then invited to one day of safety training, you are not paid for this, then you go to Gate One in order to obtain your gate pass. This is how you get hired, normally you don’t need personal connections.
Before the strike we had to manufacture 500 engines at the short-block line, after the strike this came down to 419 currently. Another change since May 2012 is that Powertrain will only hire apprentices from ITI’s in Haryana, may be that’s a policy developed together with the new union.
Apprentice, Suzuki Powertrain, Engine-Shop (May 2012)
We, five apprentices and a temporary Powertrain worker, share a room in Aliyar. The apprenticeship finishes in August 2012 and we currently try to find jobs for time after apprenticeship. We don’t want to work through contractor, but then most workers hired through contractor are former ITI apprentices, some of them even have a diploma.
Engine plant
Gearbox plant
Two-wheeler engines
Casting plant (aluminum parts for engines)
All parts used at the engine plant at Powertrain arrive more or less on a daily basis, in particular the bigger parts.The raw engine blocks arrive at Powertrain from three different suppliers, one of them is
Amtek.
http://www.amtek.com/
Amtek Auto Group, comprised of Amtek Auto, Amtek India and Ahmednagar Forgings, is one of the largest component manufacturers in India. It has 43 manufacturing facilities located in India (39) and Europe (4).
Trucks come constantly from Amtek, you probably can fit 100 engines on a truck, daily production is around 1,100 engines, they all go to Maruti Gurgaon plant. There is no proper storage for engines, but in the dispatch area you can store around 200 engines. The engines are used at Maruti more or less immediately, there is no storage on their side either. If they find quality problems with engines they tell Powertrain during the same shift during which the problems occurred.
On the long-block assembly -line there are about 200 work-stations, manned by one worker each. For the short-block you need about half the amount of work-stations. After the engine block arrived it is washed. A worker makes use of a crane, clamps the engine block, operates the washing machine, takes the engine out. That’s the job of one worker. Then different data entry has to happen, according to eight different engine models. That’s another work-station. Then you have to attach a bar-code and do the engine number punching. After that you fit the crank-shafts – they are also first checked, then washed, then fitted. The crank-shafts arrive from
Oriental Engine Pvt. Ltd.
The crank-shaft are fitted manually, this is physically the most demanding work, they weigh 15 to 20 kg.
The pistons come from
Sansera
http://www.sanseraindia.com/aboutus.html
Supplier for Maruti, HMSI and Hero, amongst others. Manufacturing facilities at Bangalore, Manesar (New Delhi), Pune and Panthnagar.
Amtek
Subros
http://www.subros.com/
Capacity of the Manesar plant 700,000 Air-Con Kits, total capacity of Subros including Chennai plant 1,5 million.
Sebros
http://www.sebrosgroup.com/website/
At the dressing-line there are around 12 stations, one worker per station. Here ‘attachments’ are fitted, such compressors or starter motors. these parts come from companies like
Bosch
Bolio
The heavy work, such as taking crank-shafts out of the trolley and testing it mechanically is mainly done by casual workers (hired through contractors). The relatively lighter work, such as data entry or final check, is mainly done by permanent workers.
Powertrain stopped producing the Euro V engine, but that did not reduce the total volume of production.
Since October 2011 there are more workers employed, meaning that you have a reliever, if you want to go to the toilet. At the dressing line they increased the number of workers, so the work-load is a little less. Since October 2011 the morning gymnastic to Japanese music has stopped.
4.3) Permanent Worker, Engine Shop, Maruti Gurgaon plant (June 2012)
Workers’ rooms…
In June 2011, when workers occupied the Manesar plant, the atmosphere heated up in Gurgaon. Mainly the young workers (hired through contractors, trainees, apprentices) were agitated and they were also in touch with Manesar workers. The older permanent workers expressed some passive sympathy for the action, the layer of older workers with supervisory functions were largely hostile. younger workers gathered at Maruti Gurgaon parking lot to discuss. They went in groups of 20 to 150 to the MUKU union office in order to press the union to take some form of action. When management sensed the discontent they called for MUKU union election in July, mainly to channel the anger into orderly directions. In 2009 there had been some action and gate meetings of casual workers to demand higher wages, but their leaders were sacked. Since then there had been little open conflict in Gurgaon plant. Workers started to collect money for the Manesar workers. They did this independently from MUKU and they did it secretly – collections were organised on assembly line and department level, a total of 86,000 Rs was collected. Only when in Manesar workers were supposed to vote whether they would accept MUKU Gurgaon union as a representative body in the negotiations for the settlement after the ‘good conduct undertaking’, MUKU sent three buses of Gurgaon workers in order to ‘show’ support and thereby to influence the vote. An independent gate meeting in Gurgaon was planned, but when the shooting happened at Suzuki Cycle-plant the meeting was cancelled. Since then MUKU has been approached by the 1,500 trainees at Gurgaon plant, but MUKU says they can’t do anything for them, not even make them members. Between 1999 and 2007 no worker has been hired on permanent basis in Gurgaon, in 2007 workers were hired as trainees. After three years of being trainee, some of them have been made permanent. These workers were the closest to the Maruti Manesar union.”
“Since May 2012 the production of petrol cars in Gurgaon plant is down. For example there are four engine shops, each of them runs on two shifts. Normally we produce 450 engines per shift, since May 2012 only between 240 and 270. In one shop around 150 workers are employed on two shifts, half of them through contractor.In the assembly department the assembly lines are also stopped for one or one and a half hours everyday, which did not happen before. Some casual workers have been kicked out, due to this overcapacity. Like in Manesar assembly department runs on only two shifts, 16 hours a day. There are rumours that all assembly work will be stopped at Gurgaon plant and that only diesel engines will be produced. they set up a new diesel plant on Gurgaon premises. So far these ‘future plans’ do not impact much on the atmosphere inside the plant. This is also due to the high share of contract workers in most departments, e.g. in the paint-shop on one shift there are eight permanents, four trainees, three apprentices and 59 workers hired through contractor. Some Denso and Lumax workers fit their own parts at the assembly line, but that is an exception.
4.4) Reports from Maruti Supply-Chain Workers
Industrial desert IMT Manesar – In front of the Maruti Suzuki plant…
Ju-Shin Worker
(Plot 4, Sector III, IMT Manesar)
There are 2,500 female [!?] and 500 male workers employed, manufacturing locks for Honda, Suzuki and Hero two-wheelers. The women work from 9 am till 8 pm – they get 75 Rs for the ‘two hours overtime’ as declared by the company. The male workers worl from 9 am till 10 pm, often they are forced to work till 6 am next morning. After three hours of rest they are supposed to start working again at 9 am. They are only paid 17 Rs per hour overtime and that only for 100 hours per months, when people actually have worked 150 to 200 hours. Wages are paid with delay. The company has recently added a floor to the factory building, which has resulted in the whole building becoming unstable. They propped it up with steel pillars, but the situation is unsafe. Eight trucks leave the plant and drive to Maruti per day, four to eight workers are permanently kept at Maruti for loading and quality check. The company has four factories in India, two in Manesar and Gurgaon, two near Chennai.
http://jpmgroup.co.in/milestones.html
Vinay Auto Worker
(Plot 42, Sector 3, IMT Manesar)
There are 200 permanents and 400 workers hired through three different contractors. We work 12 hours shifts and manufacture parts for automobile suppliers like Napino, Denso, JNS, Pricol, Delphi. When shift changes on Sunday then workers in the plastic moulding department and in the copper press shop department have to work 20 hours on stretch, from 8 pm Saturday till 4 pm on Sunday. The newly hired helpers hired through contractor get 4,500 Rs.
Annu Auto Worker
(Plot 52, Sector 3, IMT Manesar)
There are 30 to 35 permanent workers in the factory and 300 workers hired through three different contractors. We manufacture plastic parts for Honda, Hero, Hyundai on 12 hours shifts. Also on Sundays 12 hours shifts. They pay only 18 Rs for an hour overtime. They embezzle 200 to 400 Rs each month. There is no place to take food in the factory. The park is just for show and taking pictures, we are not allowed to sit there. The toilets are dirty.
Shriram Engineers Worker
(Plot 54, Sector 5, IMT Manesar)
Around 250 workers on two 12 hours shifts manufacture parts for Maruti Suzuki four-wheelers and Honda motorbikes. The workers hired through contractors are paid only single rate overtime.
http://shriramengg.trade-india.com/
Indo Autotech Worker
(Plot 338, Sector 24, Faridabad)
Here, around 1,000 workers manufacture parts for Honda, Suzuki and Yamaha motorcycles. In the power-press department workers are employed on two 12-hour shifts, this is where a lot of hands get cut. In the welding department around 50 out of 400 workers have ESI and PF – on the punch card there is neither name nor photo, just a number. Those 50 welders who work on Honda parts work on 12 hours shifts. The other 350 welders work 12, 14, 15 hours a day. The work load is high, you have to stand upright the whole time, they abuse you verbally and make you stay longer after 12 hours of work. Overtime is paid at single rate. There is no canteen or place to eat your food, you have to sit next to the machine and eat. Indo Autotech has other factories in Manesar, Bhiwari, Pune and another one in Faridabad, Sector 24, where they make parts for JCB.
The press-shop has presses from 10-400 tons, there are CNC machines for wire cutting and pipe bending and CAD/CAM facilities. Apart from Maruti and JCB, Indotech supplies Honda, yamaha, Recaro and FCC Rico.
http://www.indoautotech.com/
DS Buhin Worker
(Plot 88, Sector 24, Faridabad)
Workers here work two 12 hours shift, manufacturing parts for Maruti Suzuki, Honda and Tata Nano. Only 35 workers are permanent, 350 workers are hired through five different contractors. There are 30 power-presses in the plant. Fingers get cut, there are a lot of accidents. In a year 150 hands get mutilated. The company does not fill in the accident form. They don’t take workers to an ESI hospital. They sack the injured worker after having brought him to a private clinic. The helpers hired through contractors get 3,600 to 3,800 Rs. Two to three day wages get embezzled each month. Managers swear at us.
DS also manufactures parts for General Motors and Maruti suppliers JBM and Caparo. The press-shop consists of 27 pneumatic and 12 mechanical presses. Most of the hinge components are manufactured by the progressive tools from Nagata Auto Parts Ltd. Japan. The Assembly Shop has 6 Pneumatic Special Purpose Machines for the assembly of hinges with a capacity of 20,000 hinges per day on two shift basis. DS manufactures parts for both Gurgaon and Manesar plant, such as radiator and seat brackets for the Swift.
http://www.dsbuhin.com/clients.html
Omax Worker
(Plot 6, Sector 3, IMT Manesar)
There are 1,000 workers hired through five different contractors employed in the factory, plus 50 casual and 250 permanent workers. In the paint-shop workers work 150 to 200 hours overtime per month, in the weld-shop 115 to 130 hours, in the power press-shop 100 to 125 hours – the payment is single rate and in the paint-shop the contractors embezzle 50 hours each month. ESI and PF contributions are cut from workers wages, but none of the workers hired through contractor get ESI and only few get PF fund when quitting the job. The company declares some Sundays as festival / bank holidays and thereby reduces the statutory paid holidays by 10 to 12 days per year. the wages of the helpers hired through contractor is 4,300 to 4,800 Rs.
Omax runs ten factories in India. The company claims to have the largest sprocket manufacturing capacity (11 Million pa) in South East Asia and the largest welding facility in India with 800 machines (100 Km welding capacity per day). Omax supplies parts to Hero MotoCorp Ltd., Maruti Udyog Ltd., Honda Motorcycle & Scooters India Pvt. Ltd., Honda Siel Cars India Ltd., TVS Motors Ltd. Suzuki Motorcycle Ltd., New Holland Tractors (India) Pvt. Ltd., Yamaha Motors India Pvt. Ltd., Delphi Automotives Denso India Ltd., Indian Railways, Tata Motors Limited, Ashok Leyland Limited, IKEA, Magneti Marelli, Wabco.
In 2004 the company started exporting auto-parts to the US and Europe, amongst others to bigger automobile suppliers like Delphi or Cummins. Since 2009 Omax also supplies IKEA.
http://www.omaxauto.com/contact.htm
Krishna Group Worker
(Plot 47, Sector 3, IMT Manesar)
There are 200 workers employed, they work on 10.5 hours and 13.5 hours shifts, manufacturing parts for Mahindra, Honda, Maruti Suzuki cars and Svaraj mini-buses – mainly roof inner-linings. Workers operate with all kind of chemicals, they develop skin problems. Only 40 to 50 out of 150 workers hired through contractor get ESI or PF.
Krishna Group manufactures seating systems, rear mirrors, door Trims, roofliners & moulded carpets. The weld shop for the seat-frames is equipped with CNC machines, the paint-shop for the seat-frame is fully automatic and conveyorised. Assembly is performed on conveyorised lines using SNIC ‘s technology.
http://www.krishnamaruti.com/gr_prof.html
Jay Switch Worker
(Plot 407, Udyog Vihar Phase 3, Gurgaon)
In the factory 300 workers on two 12-hours shifts manufacture steering locks and keys for Mahindra, Tata Sumo, Toyota Inova and Maruti Suzuki. The overtime is paid at single rate. A first installment of 15 days of overtime payment for December was paid on 15th of February 2012, workers demanded that the rest should be paid by 25th of February – in response the company called the police and one worker was arrested. This worker was sacked and the company refused to pay him the outstanding overtime payment from December to February. The director said that he had to pay the police and that he now won’t pay any money to the worker.
Kiran Udyog Worker
(Plot 23, Sector 3, IMT Manesar)
The factory employs 300 workers on two 12-hours shifts. The factory manufactures die-casting products for Honda, Hero motorcycles and Maruti Suzuki cars. During the weekly shift change the Saturday night-shift has to work 20 hours on stretch and the Sunday day shift 16 hours. Over-time is paid single rate.
Kiran Udyog supplies Maruti Udyog Ltd, Sona Koyo Steering System ltd, Suzuki Motorcycle India (P) Ltd, Tata Motors Ltd, Regal Beloit- U.S.A, Daimler Chrysler – Germany, Koyo Steering Systems – France, Honda Motorcycle & Scooter (I) Pvt Ltd, General Motors India, Nissan, Toyota and Hyundai. They have six plants in Gurgaon and Delhi area. Main products are cylinder blocks, motor frames.
http://www.kiranudyogindia.com/
Bundy Company Worker, Manesar, NH8
A fuel-pipe manufacturer for Maruti Suzuki. Bundy has one worker permanently working ‘between’ Bundy and Maruti Suzuki: quality check, coordination. Bundy itself employs about 550 workers out of which 300 through contractor. The workers are paid on piece rate, there is no basic wage. Workers have to operate bending machines, burring machines etc. and are paid between 10 and 30 paise per piece. daily target is around 3,000 pieces. One truck leaves Bundy for Maruti per day.
JBM Worker, Maruti Suzuki Manesar Premises
There are about 350 permanent and 700 workers hired through contractor, divided up amongst three departments: powerpress-department, axle-shop and paintshop). We manufacture around 30 to 40 smaller press-parts for Maruti and around 1,000 axles per day on two 12-hours shifts. This is a production of axles for 500 cars, meaning that it is not sufficient to cover the full production in Manesar.
JBM is a joint-venture of Maruti Suzuki. JBM has plants in Manesar, Noida and Faridabad, components are also exported to truck manufacturers in Europe. JBM Auto Systems, a sister company, was founded to supply sheet metal components to Ford India and supplies for export to South Africa and Mexico and China. Next door to the JBM Manesar plant Bellsonica-workers operate 2,500 ton presses, imported from Japan. A temporary worker at Bellsonica told us that he went home to his village for a month during the Maruti dispute, he did not have the money to stay in Manesar.
http://www.jbm-group.com/gc-group-jay.asp?lk=gc2d
http://www.bellsonica.co.jp/english/c_subsidiaries.html
Energy Ltd. Worker, Maruti Suzuki Manesar Premises
Since one and a half years Energy Ltd. manufactures plastic-fuel tanks on Maruti premises. There are 64 workers in the production department, working on three shifts and 25 logistics workers. Around 90 per cent of the workers are hired through contractor. Before that Maruti got steel-tanks from a different supplier.
4.4.1) Asti Electronics Worker
Women (House-)Workers…
Asti Electronics Private Ltd.
(IMT Manesar, Sector 8, Plot 402)
Around 600 workers are employed in the factory, out of which 400 are female. Only 100 to 150 out of 600 workers are hired by the company directly, the remaining through three different contractors. Permanent workers basically do the same work, although they tend to do more supervisory jobs, machine setting, quality control. The company manufactures cable harnesses for Maruti Suzuki, Minda and Hero Motorcycles. Harnesses means that the company cuts cables for electrical appliances of the vehicle, joints them with the necessary plugs and connectors and tapes the cables into a bundle which can easily be installed and connected at Maruti Suzuki’s assembly line, mainly at Maruti Manesar plant. There are at least two more companies in IMT Manesar which do this kind of work, Motherson Sumi and JNS.
The production at Asti is divided into different departments (NSK, PCB). One is the machine shop, where cable are cut at length and fitted with plugs, terminals and connectors. The raw material comes from other Asian countries, either Japan or China. There are five automatic and eight manual machines in the machine-shop, all of them of ‘Japanese’ make. With the automatic machines you basically have to enter the right dimensions for the cables, the length of the cable, length of stripped insulation etc. This does not take much longer than 10 minutes. Then you have to supply the machine with the right type of cable. The machine will run for about 20 minutes in order to cut 1,000 cables and strip them. you have to check the quality and tape the cables in bundles of 100. The permanent workers usually show workers how to set the machine, they check the quality. At the manual machine workers mainly fit terminals and plugs onto the cables. The machine-shop runs on three shifts, only in the A-shift there are female workers employed. The A-shift is 9 hours, the B-shift 8 hours and the C-shift (night) is 6 hours. Target for the C-shift is 10,000 pieces at the automatic machines, for the A-shift 18,000. Workers say that targets have increased continuously. In the machine-shop there are around 20 workers and one supervisor. The supervisor reminds workers on a daily basis: “Check the quality, there have been complaints from Maruti”.
Most of the female workers work on the assembly line, which is separated from the machine shop by racks for material. The assembly line runs only on A-shift. Women workers are of all ages, mostly between 18 and 40 years old. The young female workers live with their parents, the older women with their family. Work at the assembly line required speed, the line runs automatically, women workers have to pull cables into a type of frame, other workers then put plugs on their ends, other workers tape the cables into different branches. The assembly line has about 6 to 8 different stations in sequence, then there is a final quality check and dispatch. there is a line leader which is in a hierarchical position between workers and supervisor. There is no storage space, the manufactured goods leave the factory more or less immediately.
In the machine shop workers can talk to each other, work at the assembly line is more rapid, talking is more difficult. If younger male and female workers talk too much to each other, the male worker might be transfered to other work-station. In the canteen male and female workers can sit together, but they often set apart. Workers work A-shift on Sundays, which is called ‘overtime’. Workers also often work B- and C- double-shifts on Sundays, meaning 14 hours on stretch. They are paid 500 Rs for 14 hours. If people take too much holiday, for example a week or two on stretch, they have to ‘re-join’, meaning their seniority is lost. If you take four days holiday in a week you also lose the Sunday pay (normally a day of which is ‘paid’).
Wages are very low at Asti. Machine operators and assembly line workers only get the helper grade. In March 2012 workers hired through contractor got 4,750 Rs per month, plus 1,000 Rs attendance bonus. Workers with ITI received around 7,000 Rs. Women workers on A-shift receive the same amount as workers on B- and C-shift, although they work one hour longer. In March/April 2012 an annual wage increase was given. Those workers who worked at Asti since one to three months got something between 100 and 200 Rs increase, those with three to eigth months 200 to 300 Rs, those over eight months 600 to 800 Rs, only a handful of permanents with long seniority got 1,500 Rs. Workers were rather angry about the miniscule hike.
The ASTI Corporation and Group Companies are located in Japan, China, Vietnam and India. The plant at IMT Manesar was started in October 2005 and at the same time supplies to Suzuki Motorcycle India started. Asti started supplies to Subros Ltd. in May 2006 and since June 2007 to Maruti Suzuki.
http://www.astiindia.com/index_files/groupcompanies.html
4.4.2) Sanden Vikas Worker
Family members of Maruti workers protesting after mass-dismissals…
Sanden Vikas Worker
(Plot 65, Sector A, Faridabad)
There are 60 permanents employed by the company and 950 workers are hired through four different contractors. Sanden Vikas is a major manufacturer of car AC systems in India, together with companies like Delphi or Subros. The factory in Faridabad supplies AC systems mainly to Maruti Suzuki (Nissan, Honda, Mahindra, Tata, Hind Motors)
Parts for compressors come from Japan. The pipes come from Korea. The rubber hose pipes come from
Bridgestone
Other parts come from other companies of the corporate group:
Pranav Vikas
Kenmore Vikas
Sata
RPS
Gele
Compressors are assembled at assembly lines, the pipes for the AC’s are dispatched separately. There is no storage, trucks leave continuously. The AC-components are delivered directly to the assembly lines at Maruti Suzuki, there is no storage neither at Sanden, nor at Maruti. There are four Sanden Vikas workers permanently employed at Maruti, Manesar, they also live in Manesar. Two for quality check, two for unloading trucks and dispatching AC’s to lines. About six trucks leave Sanden per day, the guys at manesar plant work 18 hours shifts. Although they work permanently in Maruti they have to pay 30 Rs for a meal at the Maruti canteen. These workers know that there has been a strike at Sanden in 2010 and that there is still trouble. They know that the dispatch problem of parts, the incomplete dispatch is due to wage trouble and over-work at the Faridabad plant. At Sanden in Faridabad there was no major problem during the Maruti Suzuki struggle, management expanded production for other car companies. The component parts for AC’s can be used for different car models.
Management claims that they the factory runs only 17 hours a day on A- and B- shift, but actually it runs 24 hours – only on Sunday production stops at 7 pm. The work-load is high, every day more than 4,000 AC’s are dispatched. Where their own time study has fixed 500 piece targets, managers ask to produce 1,000 piece
– they employ unskilled workers at CNC bending machines. After accidents workers are sacked, workers hired through contractor have no ESI card.
Since March 2012 there have been problems of completing the dispatch to Maruti, not enough or faulty AC’s arrived at Maruti. The problems emerged at a time when a new model was introduced. Maruti made Sanden pay penalties, if dispatches were not complete. In order to find out what the problem was Sanden ordered higher management people to stay during night-shifts and analyse the work process.
The situation is that permanent workers only work on A-shift and since 4 permanents have been kicked out in 2009, permanent workers refuse working overtime. So workers hired through contractor employed on B-shift work from 2:30 pm till next morning 6:30 am – this is 16-hours on stretch. While on A-shift they work 8.5 hours. The solution of management for problems of dispatch: B-shift workers must be tired after 15 hours of work, so they changed shift patterns and introduced two 12-hours shifts instead. This also means that when shift changes on Saturday, workers have to work a 24 hours-shift, as ‘compensation’ workers get 50 Rs extra for food and two ‘breakfasts’.
4.5) Report on Life in Aliyar, a Workers’ Village in Manesar Industrial Zone
On the way to Aliyar in IMT Manesar…
Living conditions in villages like Aliyar and other villages around IMT Manesar are not worse than those in other places in Delhi region, which is bad enough. Main thing is the isolation, being far away from Gurgaon. There is the huge and sterile industrial zone with hardly any public spaces and there are the small rooms in the villages, nothing more. There is no time and no space for ‘leisure’. A bit of television, if workers have one, and more recently a bit of fiddling with the chinese touch-screen mobile. “What do you do on a Sunday, if you have a day off?” “I go to listen to religious functions in Manesar. Most workers wash clothes and hang out, rest, have a drink, play cards, may be go to the gym. There is nothing to do.” Locals complain about an increase of prostitution in Manesar, but workers say that prices for sex work are mostly out of reach, 50 Rs for a fuck, 200 Rs for an hour.
There are 500 local inhabitants on the vote list in Aliyar, meaning 500 adult original residents, poorer peasant families. Peasants had to sell their land for the industrial development, this started in 2001. At the time Haryana government paid 3.5 lakh Rs per acre compensation. Some years later Haryana state gave permission to private developers to buy land for ‘housing projects’. The private developers paid between 2 and 11 crore per acre. Families who were forced to sell for ‘industrial development’ filed a legal case and demanded higher compensation, a compromise was found and they now get now get 36 lakh. The land deals has created major income differences between the peasant families. Some invest in more land further down the NH8 towards Rajasthan. Others invest the money into ‘education of their sons’. Others buy a three wheeler and get engaged in transport between Manesar and Gurgaon. At least in Aliyar local ex-peasants don’t get engaged in labour contracting, they mainly rent out rooms for workers. They complain that their sons won’t get permanent jobs in the local factories.
These 500 original ‘peasant inhabitants’ built rooms and rent them out to about 10,000 plus workers. Due to the closeness of Aliyar to Maruti Suzuki, due to the rigid ‘punctuality regime’, land-lords in Aliyar can demand higher rents than in other workers housing areas in Gurgaon or Faridabad. While a room rent is 1,600 Rs in Kapashera, in Aliyar you will pay 2,500 Rs to 3,000 Rs. The state built a ‘workers housing colony’ as a show-piece in the early 2000s, but 80 per cent of the 100 or so flats are empty due to high rent of 6,000 Rs per room. Also prices for vegetables and other food items is much higher in Aliyar. Some workers organise collective trips to markets in Gurgaon, but that takes extra-time. Attached to the land-lordism of the locals is also a certain social and patriarchal control. “We wanted to use the roof of our house as a leisure space, to hang out in the evening. The local owner of the neighbouring house said that he does not want to see us on the roof. We had to accept this, otherwise there would have been trouble”. On one floor of an average workers’ house you will find between 40 and 100 workers of different categories (trainees, temps, apprentices), although permanent workers tend to stay in slightly better accommodation apart. Workers from different departments and companies live together they exchange experiences.
During the Maruti Suzuki dispute the media presented the ‘locals’ as supporters of the company, their village council leaders met up and issued a declaration, stating that ‘Maruti did so much for the region and this labour unrest is sparked by outsiders’. Actually there is a lot of discontent amongst the locals, despite their land-lord position. Most of them see that their children have little chance to participate in the ‘boom’, they see the impact of social decomposition, such as drugs and petty crime amongst the local youth. On 22nd of May 2012, for example, local villagers blocked roads within the industrial zone of Manesar in roder to protest against water and electricity shortage. The protest was mainly organised by the BJP, a fair share of the villagers took part. They blocked the main roads towards the Maruti Suzuki plant, but did not block the entrances to the huge car-park, which meant that trucks with parts could still enter the factory and production was not effected. A symbolic protest, also symbolising their helpless and dependent position.
(based on conversations with workers and local inhabitants, May 2012)
5) Conversation with Comrade on Practical Engagement during the Maruti Struggle in 2011 – Recorded June 2012
Workers’ kitchen…
6) Comments on and Relevant Parts of “The Maruti Story”, Biography of the Gurgaon Factory by R.C Bhargava, Maruti Chairman
Workers’ at Maruti supplier…
Below you can find some more relevant passages from “The Maruti Story”, by Maruti chairman R.C Bhargava,published by Collins Business in 2010. The book is obviously annoying, having been written by a top-manager, with the usual arrogance and, which is probably more painful, ignorance of the representatives of capital. But even more painful is the fact that it was a representative of capital and not a revolutionary workers’ collective who wrote a book which, however biased and characterised by blind-spots, analyses the development of a major factory, the problems of getting workers to work, of imposing control on the shop-floor through the production system itself, of organising a fragile supply-chain and actively counter-acting workers’ unrest.
Here we see a parallel to the workers’ historiography in Italy. Initially it were mainly bourgeois sociologist and intelligent factions of capital who got engaged in analysing industrial history and contemporary developments. Only with the re-emergence of workers’ struggles and a dissident communist faction in the early 1960s, workers took the analysis of their material world into their own hands and turned it into a weapon. See Sergio Bologna: ‘The Theory and History of the Mass Worker in Italy’
http://libcom.org/library/theory-history-mass-worker-italy-sergio-bologna
On 350 pages, R.C Bhargava deals with the structure of the early automobile industry in India (Hindustan Motors), with the early attempt of setting up Maruti by Sanjay Gandhi and the close connection between the developmental dictatorship of the State of Emergency and his vision of a people’s car. One has to plough through long passages about the composition of the early management, about the difficult balance-act between being attached to the state and its burocracy and looking for foreign investors. He describes the discussions and negotiations with various international automobile companies and how they chose Suzuki as a partner. For future GurgaonWorkersNews we might type up some historical nuggets, but here we want to concentrate on passages which are relevant for our understanding of the situation today and see them as an incentive to dig deeper from a workers’ perspective as part of workers’ armed struggle.
a) Maruti and Supply-Chain
b) Maruti and Unions
c) Maruti and Expansion of Gurgaon and Manesar
a) Maruti and Supply-Chain
Here we first of all are able to see how capital creates its own fetish. In order to avoid a huge concentration of workers in a single ‘automobile factory’, which would easily need a 100,000 workers, Maruti wants to create the semblance of formally separate units of suppliers around a central ‘Maruti assembly plant’. The reasons they give for this decision are seemingly ‘economic’: aversion of risk, share of investment, competition. Obviously Maruti depends on the smooth cooperation within a production process, so they basically set-up the suppliers with their own engineers, impose clear hierarchy of orders, supply them with necessary capital. It is clear that on the level of ‘use value production’ Maruti and the suppliers are one and that the formal and spacial distinctions are in the end political measures against the working class.
“Chapter 7: Preparing the Vendors
The first 192 cars to roll out of the factory in December 1983 were almost entirely Japanese cars, with only the tyres and the batteries being Indian, supplies coming from Chennai-based MRF and Kolkata-based Chloride India (later renamed Exide Industries). The indigenization percentage was a mere 2.76666 per cent and it stayed at less than 10 per cent till March 1984. […] Maruti had committed to achieving 95 per cent indigenization in five years. […]
At that time [1985], the Indian automobile manufacturers produced close to 50 per cent of the components of a vehicle in-house. SMC, and Japanese manufacturers in general, followed a different policy. In-house production of components was limited to only those that were critical for performance and appearance, like the engine, gearbox and outer body panels. All other components were outsourced to vendors. This reduced investment costs, and thus risk, for the vehicle manufacturer. It also reduced cost of manufacturing components, as vendors could supply to more than one manufacturer, attain higher volumes and derive benefits of scale.[…] Thus the dependence on vendors was to be to the extent of about 75 per cent of the value of all components, excluding steel, paints and similar items.
Interested parties had to submit full information about themselves, including what facilities they had, their experience in manufacturing and management set-up. […] A group of engineers then visited the factories of the applicants to verify the information given and also to judge their capabilities. […] Another difficult decision in respect of each part was to decide when it should be deleted from the CKD kit [kit with imported parts coming from Japan for assembling at Maruti]. The contents of a CKD kit had to be decided and orders placed with SMC five months before the month in which the imported parts would be used on Maruti production lines. Maruti had to anticipate which parts, and in what quantities a vendor would be able to produce six months in advance, in order to decide to delete those parts from the import list. Given the somewhat disorganized state of many vendors, this was not an easy task and often created situations of crisis, as many vendors failed to meet their commitments. […]
Maruti acted virtually as a midwife to a large number of vendors, handholding them at every stage. Maruti was often involved in helping them find the right collaborator, aiding with joint venture agreements and getting approvals and licences, arranging financial assistance and negotiating with financial institutions for providing working capital, persuading state governments to allot land, giving short-term advances to them to pay customs duties and importing tooling, and sending Maruti engineers to help them with their production system. […] As a result, close to forty joint ventures and technical agreements between Indian and Japanese component manufacturers were signed in a short period of time, and this greatly facilitated the process of localization.
Mathur and the late Dr. R.D. Deshpande, who was the first head of engineering, were in charge of developing Maruti vendors. Mathur describes it graphically: “Ensuring that the production line was not disrupted was like feeding a shark which eats around the clock. We were buying 1,200 or 1,300 components. Even if we had a crisis on one of the components every three years, it was still a crisis every day for us”. The crisis could take the form of a quality problem, disruption of production due to shortage of raw materials or imported sub-components, labour unrest or disruption in the transportation system […].
Many vendors would change their manufacturing process in some area, thinking it would not matter. Maruti had to make them realize that the key to quality lay in consistently, without any deviations, following the approved procedures for manufacture […]. If any change was to be made anywhere, it had to be first approved by Maruti.
As a result of all these problems, more parts had to be imported and the indigenization programme had to be revised downward. The target of 31.5 per cent indigenization up to March 1985 was brought down to 23 per cent. […] Maruti then decided to get even more involved with its vendors, forming joint-ventures to manufacture components that were critical to the quality of the vehicles, or were to bulky to transport, or required high technology and large investments, or where the economies of scale dictated a single source. […] Having a stake in the companies enabled Maruti to be involved in all aspects of the establishment of the production facilities and the process of manufacture. […] Initially five joint-ventures were formed. These were to manufacture seats (Bharat Seats), glass (Asahi India Glass), sheet metal parts (Mark Auto), plastic moulding (Machino Plastics) and steering components (Sona Steering) and accounted for 24 per cent of the value of the car.
Three of the joint-ventures – Bharat Seats, Machino Plastics and Mark Auto – were located within the Maruti factory complex, while Asahi Glass and Sona Steering took land nearby. […] Later, to bring in an element of competition and as a fallback arrangement, three more joint ventures were set up – Sona Car Seats (renamed Krishna Maruti) for seats in 1993, and Jay Bharat Maruti and Caparo Maruti for sheet metal components in 1988 and 1994 respectively. […] The management control was with Maruti’s partner, as the company did not want to get involved in the day-to-day management of so many companies. If Maruti had assumed control over the joint ventures, there would soon have been demands from the employees that they should have the same terms and conditions as Maruti employees. […] All this would have diverted attention from the main task of building Maruti and the objective of having vendors would have got defeated. […] to give comofort to the partner, it was provided that for the first seven years or so, pricing would be on a cost plus basis, with an assured return on equity. Maruti had the right to go into details of all costs of manufacture and procurement of materials.
Kumar had to point out to many vendors (other than the joint venture partners)who wanted to persist with the traditional way of using Indian-made tools that they were ignoring the fact that if the components were rejected, they would lose all Maruti business, and suffer a total loss of their investment. Further, since the Maruti pricing policy took into account the tooling cost, buying tooling from Japan would not adversely impact on their profitability. […] The procurement of raw materials and bought-outs had to be from sources who would follow the laid-down processes and systems, […] and no change in the source of procurement should be made without getting Maruti’s approval first.[…] Maruti engineers working in the purchase and vendor development department would spent at least half a day on the shop floor of suppliers.”
By that time Maruti had established a certain competition amongst different suppliers. They imposed a rating system about just-in-time and quality and suppliers were supposed to compete in order to get the next order once a new Maruti model was introduced.
“Logistics posed another headache. […] The rear axles too came by truck from Chennai. This was one of the few cases where Maruti had a single supplier. Trucks would break down or be stranded by floods during the monsoon. […] Truck drivers were not trained to keep Maruti, or even their own management, informed of what was happening. Though they were supposed to call from every major twon on the route, few did this. […] During the 1984 anti-Sikh riots […], several Sikh drivers disappeared and there was no way of knowing whether they were hiding to save themselves or had been killed. On such occasions the rear axleshad to be transported by train […] to ensure they reached the factory in forty-eight hours and production lines could be kept running”.
We added the quote below, which does not directly concern the supply-chain, but the so-called ‘after-service’, the Maruti repair and service work-shops. We can see how the big industry shapes and re-structures the so-called service and informal sector, such as car repairing – through direct intervention, technological impostion and ‘training’ of the work-force.
“As with showrooms, Maruti also provided guidance on how to establish workshops – number of bays, equipment, paint-shop layout, storage and handling of spare parts, among other things. Maruti personnel had to approve the workshop site and the layout (the drawings for which bwere prepared with SMC’s help). […] Some of the equipment – computerised engine diagnostic equipment, wheel alignment systems, and brake tester, to name a few – was a first for dealers in India. […] Workshop practices also needed a major change. Traditionally each mechanic was a specialist who would do work in his area only. […] In addition, each mechanic had one or two helpers, to do the less skilled work like washing and cleaning parts, fetching tools or oil and teightening nuts and bolts. Most of the employees were underutilised and never worked anywhere near eight hours in a shift. The specialist mechanics often sat idlewhen parts were washed and cleaned. […] SMC, quite rightly, did not want these practices to continue.Thei basic principle was that one mechanic should do all the work required for sservicing a car […]. Further he should have to do the entire servicing of a car himself, with no helpers. […] Implementing this was not easy. The older and more experienced mechanics were most unlikely to agree to the change. […] It was decided that , by and large, it would be better to train fresh pass-outs from ITIs […].Thuis a training centre for mechanics was established in the service centre at the Maruti factory, […] regional training centres were established.The young workers from the ITIs were without hang-ups and were quite happy to work in accordance with the new system.”
b) Maruti and Unions
‘The Maruti Story’ contains longer sections about the run-up of the 2000/2001 strike and the subsequent VRS scheme, but most of the details are already provided in GurgaonWorkersNews no.8. Following just some initial quotes concerning the management thought concerning workers’ representation.
“It was realized that continuous training of workers was necessary if their attitude towards work, the company and its management was to be changed. […] Krishnamurthy decided that this could best de done through a union which had a positive approach. […] As a first step, Krishnamurthy promoted a trade union at Maruti before political parties and outsiders could establish one. K.K. Datta, who was a union leader at BHEL [where Krishnamurthy had been a leading manager] was given employment in maruti, and became general secretary of the Maruti Udyog Employees Union (MUEU), which was affiliated with the Indian National trade Union Congress (INTUC). Workers were encouraged to become member of this union […]. But first the credibility of the union had to be established, and this was done by consulting the union and involving it in framing policies and taking decisions in matters affecting the workers. Thus, the policy regarding uniforms, and its colour and design, was settled in consultation with the union. . […] After each union meeting each [union] executive was required to interact with his constituency and share the information with the workers. The management believed that this would be the most effective way of reaching all the workers, and this could not be done successfully by the management trying to interact directly with them.”
Incentive Scheme
“The scheme was notified in November 1989. Productivity levels and sales started to rise rapidly. The bonus pool grew and in a few years the workers were getting a bonus which was approximately one and a half times their basic salary. One benefit of the scheme was that workers never opposed automation or other methods to improve productivity. […] Getting worker cooperation on contentious issues, therefore, became easier, as the management found out in the mid-1990s. The company had a large number of casual/temporary labourers on its rolls and Abraham, who had again become the general secretary of the union, insisted that their service be regularized. Since these people were doing work which was not related to the main activity of the company, like cleaning, sweeping and unpacking crates, and outsourcing was the accepted way to get such tasks done, it would not have been in Maruti’s interest to regularize them. The management talked to other union leaders, and the managers also talked directly to employees on the shop-floor, and pointed out that accepting this demand would lead to a larger number of employees, lesser labour savings and a drop in the bonus pool. The smaller pool would have to be shared between larger numbers. Hence each regular worker would see a big drop in his take-home pay. With the majority of the workers unwilling to let this happen, the union quietly dropped this demand.”
The quite below is actually not from “The Maruti Story”, but from the Phd by Bose – see Appendix. We thought it would be interesting to document the attempt to set up a contract workers union at Maruti Gurgaon plant in the late 1980s.
“Maruti gets license from the Labour Commissioner’s office to use contract labour. We are not given any appointement letter. Initially, Maruti officers used to issue identity cards with their signature on it. But from June 2000 onwards Maruti officers have not been signing on the identity cards, which are changed every six months. Earlier, contractors and Maruti officers used to sit together to pay us wages but now contractors pay on their own within the company. The labour contractors are registered ones and come from local areas, and are well connected to Maruti management. There are now 72 big contractors and many small contractors. They have two yearly agreement with management. Competition among them forces them to quote lower bulk payment so that we do not get even official minimum wages. No equal wages for equal work we do. We do not get any allowance. We have no hospital facility. The entire Maruti Gypsy production line work is subcontracted out. Contract workers are doing the subassembly and final assembly within Maruti premises. We do not get any help from contractors in terms of advance or loan. We are forced to work long hours. We work on Sunday and we do not get any leave. If the worker absents without telling the contractor, they get penalized in terms of no work for three or four days. We face high incidence of injuries and accidents due to too much work pressures and lack of rest. No payment is made. Contractors are told to take us away even as the others are told to clean the blood on the running machines. The permanents look down upon us. Most of us were earlier apprentice workers in this factory. We are doubly f…ed…both management and union exploit us.
In 1989 we struggled with a 9-day strike for our union recognition, and in 1990 we were on a 37-day strike. We are registered as Maruti Contract Workers Union. Our registration number is 1150. We have received no support from Maruti union even as they seek our support which we give in terms of tool down, etc. Both Maruti management and Maruti union have cooperated with the labour contractors to dismiss 20 to 25 activists of our union. We lodge court cases through permanent workers union and the Joint Labour Commissioner wants proof of employment from Maruti or permanent workers but they do not extend any help. Who will save us in this country? Even God is sold out. We have not become criminals. We have not become rapists. Why is the society not grateful to us? Are we not the backbone of this country’s economy? “Note that the President of the Clutch Auto Employees Union has been blessed by the management with press shop subcontract work, and how can he fight for the workers?
c) Maruti and Expansion of Gurgaon and Manesar
We see a parallel here. During the expansion phase of the Gurgaon plant management forced workers to work ‘over-capacity’, and management knew that it depended on workers’ collaboration during this phase. The same thing happened in Manesar in 2011, shortly before the B-plant becoming operational. In order to save investment and to stretch ‘living and dead labour’ as far as possible, the A-plant operated on over-capacity (off-line car assembly etc.) for a long period. Only this time workers were not willing to cooperate.
“The work on expanding capacity and establishing a second plant at the same site, started about the end of 1992 and was completed in 1994. This plant, which was to produce the Zen, had a rated capacity of 100,000 units, like the first plant. In November 1993, the government issued an ad hoc exemption order allowing Maruti to import plant and machinery for the Zen project at nil custom duty on taking an obligation to export 140,000 cars over seven years.The funds were secured through a loan raised in Japan, as well as some internal resources. With the plant, production rapidly increased to 278,000 in 1995-96, and the need for another plant was obvious. One of the reasons for Maruti being able to keep prices of cars low – and make profits – was the ability to run both these plants at about 140 per cent of the rated capacity. This was achieved by a combination of balancing facilities, innovative practices and full cooperation from the workers.”
Here we read about the conception of the Manesar plant: a fresh start without the ‘old labour’ of Gurgaon, a higher degree of automation, a comparable set-up to the already existing plant in Japan. Suzuki wanted Manesar to compete with Gurgaon. It now remains a question for us how to turn this around, from a workers’ perspective. How can the unrest of a young generation at Manesar plant break up the heavy silence in the ‘old core’ Gurgaon?
“There was a history to the establishment of Maruti Suzuki India Ltd. The Gurgaon site had been fully developed with the establishment of the three manufacturing plants. […] A new site was needed for future expansion and Manesar was selected. Khattar was successful in negotiating with the Haryana government to purchase 600 acres of land there, on very reasonable terms. […] SMC wanted this plant to be very similar to the plant in Kosai, Japan, so that there could be a high level of automation, and the best SMC practice could be established here from the start. Suzuki did not want this plant to become an extension of the Gurgaon plant, which had been built over twenty years and had much more manual operations. He wanted the plants at Gurgaon and Manesar to compete with each other in areas like productivity and quality, with each being a benchmark for the other. At the same time, it was always the intention that in areas like human resource management, supply chain and sales and marketing the two plants should work as one.”
7) Material on situation at Suzuki in Hungary
House of an ex-peasant, now landlord in Rampura village near Manesar…
The export of Suzuki passenger cars from Gurgaon to Europe increased over the years both absolutely and relatively. The best-seller Swift is at the same time manufactured in a Suzuki factory in Hungary, which was hailed after the end of the Eastern Block, hailed as the new investment paradise for global car manufacturers, together with the Czech Republic. Both the Suzuki Manesar and the Esztergom plant supply the European market, the different wage levels, levels of general ‘development’ and geographical location will be the objective factors for Suzuki to integrate both plants into their global structure. For workers it will be a challenge to establish a basic form of exchange of experience. A comrade from Hungary summarised following general overview on the Suzuki plant in Esztergom and the workers’ struggle of 2005:
Suzuki Factory in Hungary and International Market
Suzuki accounts for 2.2 per cent of all exports from Hungary in 2008. The factory in Esztergom was built and started production in 1992. Back then it was the only Japanese investment in Hungary. The government and all political forces were promoting the slogan of attracting foreign capital in the country, as there has been a 30 per cent employment loss (with special regard on industry) after the fall of state socialism. Initially most parts for the Suzuki Alto came from the Maruti Suzuki plant in India. In 1993, leaders of Suzuki Corporation and Hungary agreed on settling the production of most car parts (except the engine, gears and wheelwork) in Hungary and/or other countries in the region – but in 1994, when the 25,000th car was made in Hungary, the proportion of european-produced parts was only 60 per cent. From 1994 on, car parts were also made for export to Japan, and whole cars for the Chinese, Dutch and Italian markets. In 1996, the 100,000th car was made, and at the domestic market of new made cars Suzuki had a 20 per cent share in Hungary. In 1999 100,000 cars were sold on the Hungarian market, while total annual production was over 250,000. The integration with other manufacturers continues: the WagonR model consists mainly of parts manufactured by Opel/GM in Poland. The SX4 is, like in India, manufactured in close cooperation with FIAT.
In 2011, Magyar Suzuki Zrt. 171,700 vehicles were made in the factory (+1% compared to 2010), out of which 168,555 were sold abroad (!), out of which 61,123 were Swift, 61,864 were SX4, main export target country is Italy. In 2011 around 3400 people worked directly at Suzuki, total workforce is around 4,200. Exports go not only to Europe but also Japan, Russie, Ukraine, some Middle Eastern and North African countries. There was a significant growth in profits at MS Zrt. (+26.6 million euro). Analysts say it could be because of strengthening the production of own supplies (growth in the value of locally owned supplies: 25 million euro in 2010 to 33.5 million in 2011).
In May 2011 – for a short time (few weeks) only one shift was at work because of “supply problems”, from July on two shifts are working again. Probably because of this, May showed a -0.8% in total industrial output of Hungary compared to April. In November and December 2012, only one shift will work in Esztergom. Management hopes they can restore the 2-shifts setup from January 2013.
Workers’ Struggle
By the end of 2005, tensions arise at Suzuki Esztergom, because of forced overtime, cancelled holidays and weekends (2111 people were given only 7 days instead of 8 days a month; 403 workers didn’t get their 2004 vacations; further 19 were given money instead of their annual leave), additional daily working time “to replace” lunchbreaks, missing toilets in the new facilities. In August, an anonymous letter was sent to the management, describing all these conditions. In December about 150 activists of the “Liga Szakszervezetek” (Unions of “The League”, a lesser trade union confederation) demonstrate at the entrance, also involving workers of the Pét Nitrochemical Works, pedagogues, uniformed officials of armed state bodies. Nationalist separation between slovakian and hungarian workers seems to bleach, although racist resentments towards the “yellow” (japanese management) still present. However, at the handover of the petition and at the distribution of the union flyers the union accepted the restriction given by the management to be no more than 10 persons in action at the gate.
In early 2006 workers of Suzuki Esztergom form a union (Independent Union of Automobile Manufacturers in Esztergom) outside of the fence, but just at the factory gate, in a bus that they rent for this purpose. Since the demonstration in December 2005 they gathered 68 members, 30% of which are slovakian citizens. Some new members join during this first public meeting (held for the election of officials). Police shows up, records the organizers’ data and tries to push them to remove their banner demanding the respect of labour law at Suzuki. In February, a month after forming the union, their leader gets dismissed. The “factory council” [a legally codified but in Hungary very rare form of representation] denies legitimacy of the new union (based on legal formalities) and connection between its leader’s union activity and sacking. The management adds: 70 members are 2% of the total 3200 workers… Based on these points, they don’t admit the union as negotiating partner. The fired union leader made a speech in a TV broadcast that “damaged the good image of the company”. He talks about how the management framed him: some closed bottles of alcohol were found in his locker (which was opened forcefully on the weekend before by an unknown person) – the allegation of having alcohol at the workplace was used for a reason to sack him. Eleven days after he got kicked out, a strike happened: 50 workers walked out spontaneously in protest against unpaid overtime.
In March 2007 the court finds that dismissing the union leader was illegal, although his demand for the wage of the past year is still in question.
In December 2008 management announced that 1200 out of 5523 workers must leave Suzuki from the 8th December on, due to the reduction of orders in the crisis, from 3 shifts only 2 remain. First the outsourced, then those on probation time, then those working there for less than 3 years are to be dismissed. Workers put on “technical leave” get only the basic wage (no “bonus”), this means 20-25’000 HUF less than usual. Those leaving “on their own” by the middle of December are offered to gain 2 more months’ salary instead of the legally prescribed severance pay/compensation of 1 months payment per 3 years spent at work. (About 800 people were tricked by Suzuki again: they left by themselves, only to learn that this compensation offer was meant only for those living out of 30 km radius around the factory. In order to replace these workers leaving in masses, many of those put on “technical leave” were called back to work.) Buses to transport workers to work are cancelled from the 5th January 2009.
8) Appendix
Maruti Wall…
8.1) Open Letter on Maruti by Mouvement Communiste to Comrades in Delhi
8.2) Pamphlet by Mouvement Communiste on Maruti Struggle
8.3) Proposal for Critical Debate on ‘Academic Research’
8.4) Phd by Bose on Automobile Industry in Delhi
8.5) Further readings
8.1) Open Letter on Maruti by Mouvement Communiste to Comrades in Delhi
Workers on their way to shift in Gurgaon industrial area…
Open letter from afar to comrades in India
We went to India some weeks ago and we met many comrades of various tendencies in a friendly and open-minded way. We also met workers in some plants.
The situation of the working class in India, mainly in the automotive industry, shows that a new generation of workers is rising and expressing discontent, not only inside but also outside the factories.
Before the Maruti Suzuki strike (from June to October 2011), other strikes took place, successful or not, with both contract workers and sometimes casual workers, taking part.
We feel that the conditions – both objective and subjective – are ripe for something to happen. There is a hidden potential strength close to emergence. And militants must contribute to the birth of the first stage of workers self-organisation.
Obviously we are writing this letter from a long way away, so we don’t expect you to just follow our recipe – the intention is to open discussion. But if we were militants in India, this would be our proposal.
It is necessary to know more about factory organisation (along with Suzuki operations).
It is necessary to discuss to the greatest possible extent with workers from Suzuki to check that common political goals are both understood and shared.
So, a kind of workers’ inquiry must be launched.
This has to be made visible to other workers, not only to those working for local sub-contractors, but to the workers of the whole Delhi area.
In order to do this, we need “human resources” and basic organisation. This implies clearly advocating for workers autonomy. It does not mean political merger or hiding political differences. But those to which this letter is addressed share, from our point of view, a common will to dedicate their political energy towards working class self-organization, giving it the highest priority.
We are not against any attempt by workers to organise themselves to fight for their interests, even into rank and file unions, but we are very cautious about the evolution of such unions (here we are thinking about what happened at Honda, but not only that). This is a practical point produced by class struggle itself. So a basic point of agreement or disagreement.
There is already an existing medium: FMS (Faridabad Majdoor Samachar). It must become the common political paper. It must be extensively distributed among workers. It must become a tool for workers.
Class struggle never stops, but it often has lower phases and slightly higher ones. We think that now could be the beginning of a higher phase of struggle in the Delhi area, and maybe even other industrial centres across India.
This is an occasion not to be missed. It won’t come again quickly. Taking on the responsibility of this situation is the purpose of this open letter.
Mouvement Communiste/Kolektivn_ proti kapitálu
25th April 2012
About workers’ inquiry
This method was used in Italy, starting in the early 1960’s, by a specific political current, Operaismo.
It was needed to understand Capital’s organisation and Class composition.
A knowledge of the organisation of capital means understanding the production process, not only within factories but also geographically, understanding productive units and their links between factories. The goal is to identify weak points and bottlenecks but above all, capital’s logic and means.
A knowledge of class composition allows the analysis of differences in working class structure between jobs and skill levels, not from a static sociological perspective but from the potentialities and dynamics of struggle. Class composition analysis is intended to discover the underground forces that trigger workers’ struggles and workers’ organisations.
To bring out those key elements, Operaismo brightens up an old method, the workers’ inquiry, in reference to a short questionnaire written by Marx in April 1880.
Workers’ inquiry is both a means of knowledge and a tool for the use and profit of workers themselves.
Workers’ inquiry can be a success only if it gets rid of the static method of bourgeois sociology through common research within factories with workers or, best of all, directly by workers themselves.
8.2) Pamphlet by Mouvement Communiste on Maruti Struggle
Tea stall out of Aliyar…
Pamphlet by Mouvement Communiste on Maruti Struggle
http://mouvement-communiste.com/documents/MC/Booklets/BR5_India_EN_vF_complet.pdf
http://mouvement-communiste.com/documents/MC/Booklets/BR5_India_FR_vF_complet.pdf
8.3) Proposal for Critical Debate on ‘Academic Research’
Public note in IMT Manesar…
Proposal for an Open Debate on ‘Research on Automobile Workers in the Global South Today’
Dear friends,
This proposal goes out to you four, but is not necessarily constricted to this circle. If you can think of comrades who work in a similar field and who might be interested in the exchange, let us know. I assume you have heard from or about each other, nevertheless a short introduction.
L. studies in London, she has done fieldwork at FIAT in Italy and various automobile companies in India.
A. studies in Delhi, engaged in research of automobile industry in India. He is a political activist who has been closely involved with the Maruti Suzuki workers’ strike.
F. studies in London, he researches conditions and struggles in automobile industry in China and Mexico, he has done fieldwork in both places.
T. is at university in Australia, he has written on class formation in India and did fieldwork on automobile industry in Gurgaon.
Let me shortly say something about the background of this proposal. On an individual level we had discussions about ‘research work’/’academic knowledge production’ in relation to industrial changes, the emergence of a new generation of automobile workers and their promising struggles in China 2010 and India 2011 and, last but not least’ the question of ‘political organisational activities’ amongst these workers.
I have to admit that I know very little about research work and the academic mode of production, but it seems clear to me that a more collective debate about ‘research and organisation’ is necessary and could be fruitful. I am not sure how to structure the debate or how to organise it – the questions below have to be seen as a preliminary structure open for comments and changes. What could be the aim of the debate? On one side an exchange of positions about the ‘actual developments’ in research, industry and struggles – on the other side a debate on the current relation and ‘potential/traps’ of ‘academic form of research’ and ‘political organisational activity’. I think this debate is relevant for a wider circle, though unfortunately it is so far often confined to individual and often rhetorical discussions.
Stay tuned
M.
Preliminary Structure / Questions
1) Introduction
* What is your research focussing on and why? Where do you see the ‘political relevance’?
* What empirical sources do you rely on?
* How did the fieldwork look like? Who were you able to talk to and how did this relationship look like?
* What kind of political activity are you engaged in (even on minimalistic level) and how does your research work relate to this?
2) General Condition of the Automobile Sector
* Could you briefly (!) describe the general global trends you see in the automobile sector, the specific relation between the industry in north and south and the concrete relation between your focus of research (region, specific perspective) and these general tendencies?
* What is the current focus of mainstream research into automobile sector and automobile workers mobilisations? How would you describe the current material relation (resources, methods etc.) between the academic apparatus and the research into development of the automobile sector and work-force?
* How do you see the current relation between ‘academic research’ in the sector and the official ‘labour movement’ (trade unions, labour NGOs etc.)?
3) Workers’ Struggles
* Briefly, how do you interpret the recent automobile workers’ struggles in China 2010 and India 2011? Is there a ‘general trend’ in the global south? How do these struggles relate to the situation in the ‘older’ regions? Is there a material basis for generalisation both within the respective regions (India, China) and on a more global scale?
* What impact did recent movements of workers in the automobile sector have on both the ‘official labour movement’ and the academic sphere, in terms of research focus and methods and ‘internal contradictions’?
* Do you see any tendencies of ‘organisational political activity’ in relation to these mobilisations which have the potential to go beyond institutionalisation and immediate conflict?
4) Current Potentials and Limitations of Academic Research
* What could be a ‘fruitful’ relationship between ‘academic research’ and ‘political organisational activities’ within current class movements? Do you see any examples?
* How does your work concretely depend on the academic apparatus (finance, access to resources, debate etc.)?
* What does usually happen with the ‘product’ of your work? How do you and / or the academic apparatus make it public or uses it? Do you get anything out of it, in terms of debate, responses, which lead to ‘clarification’?
* From your own concrete experience: what kind of restrictions does the academic mode of production impose on the relationship between ‘researcher’ and workers or political activities – or between ‘researchers’? How do you deal with these restrictions?
* Why do you think comrades currently try to ‘do research’ through the academic despite these restrictions? Do you see any form of individual or collective alternatives, concrete examples of alternatives?
* How do you see the near future: do you have concrete ideas or projects which bring together ‘research work’ and ‘political activity’?
* Do you have any concrete comments, criticisms and / or suggestions concerning the practice of FaridabadMajdoorSamachar and / or GurgaonWorkersNews?
8.4) Phd by Bose on Automobile Industry and Workers in Delhi area
Maruti truck driver…
Phd thesis by Bose on Delhi automobile industry
Full thesis in PDF
8.5) For further Reading
Workers…
Below a list of relevant further sources on automobile workers struggles and the Maruti Suzuki dispute.
Mainstream news video on 18th of July unrest in Manesar:
http://profit.ndtv.com/videos/india-insight/video-marutis-manesar-plant-the-problems-behind-labour-unrest-240880
Collection on articles concerning Maruti Suzuki from Faridabad Majdoor Samachar in Hindi:
https://docs.google.com/file/d/0B-TeLh1FWjh6WHlQdjFnZzdyWEU/edit?pli=1
Longer journalistic article on ‘workers’ view’ on Maruti Manesar dispute:
http://fountainink.in/?p=2660&all=1
Article by comrades of radicalnotes.com on relevance of Maruti struggle:
http://radicalnotes.com/content/view/171/39/
———————-
Material in GurgaonWorkersNews relating to the local automobile industry:
GurgaonWorkersNews no.3 on the automobile supply chain:
https://gurgaonworkersnews.wordpress.com/gurgaonworkersnews-no3/#fn1
GurgaonWorkersNews no.3 on dispute at Amtek:
https://gurgaonworkersnews.wordpress.com/gurgaonworkersnews-no3/#fn5
GurgaonWorkersNews no.5 on conditions of a truck driver in the supply-chain:
https://gurgaonworkersnews.wordpress.com/gurgaonworkersnews-no5/#fn2
GurgaonWorkersNews no.6 on conditions at supplier Motherson and gender relations on the shop-floor:
https://gurgaonworkersnews.wordpress.com/gurgaonworkersnews-no6/#fn1
GurgaonWorkersNews no.6 Conditions and struggle at supplier Delphi:
https://gurgaonworkersnews.wordpress.com/gurgaonworkersnews-no6/#fn3
GurgaonWorkersNews no.8 reports from workers in the supply-chain:
https://gurgaonworkersnews.wordpress.com/gurgaonworkersnews-no8/#fn1
GurgaonWorkersNews no.8 on wildcat-strike at supplier Delphi:
https://gurgaonworkersnews.wordpress.com/gurgaonworkersnews-no8/#fn4
GurgaonWorkersNews no.8 on struggle at Maruti in 2000:
https://gurgaonworkersnews.wordpress.com/gurgaonworkersnews-no8/#fn5
GurgaonWorkersNews no.11 on struggle at supplier Automax:
https://gurgaonworkersnews.wordpress.com/gurgaonworkersnews-no911/#fn5
GurgaonWorkersNews no.13/14 on struggle at supplier Graziano:
https://gurgaonworkersnews.wordpress.com/gurgaonworkersnews-no913/#fn6
https://gurgaonworkersnews.wordpress.com/gurgaonworkersnews-no914/#fn3
GurgaonWorkersNews no.18 on struggle at supplier Boni:
https://gurgaonworkersnews.wordpress.com/gurgaonworkersnews-no-918/#fn5
GurgaonWorkersNews no.18 on struggle at supplier Mushashi:
https://gurgaonworkersnews.wordpress.com/gurgaonworkersnews-no-918/#fn6
GurgaonWorkersNews no.19 reports from supply-chain workers and worker at Motherson:
https://gurgaonworkersnews.wordpress.com/gurgaonworkersnews-no-919/#fn4
GurgaonWorkersNews no.21 on struggle at Rico and the condition of the automobile sector in India
https://gurgaonworkersnews.wordpress.com/gurgaonworkersnews-no-921/#fn6
GurgaonWorkersNews no.22 on struggle at supplier Rico
https://gurgaonworkersnews.wordpress.com/gurgaonworkersnews-no-22/#fn4
GurgaonWorkersNews no.23 on struggle/lock-out at supplier Denso:
https://gurgaonworkersnews.wordpress.com/gurgaonworkersnews-no-923/#fn5
GurgaonWorkersNews no.24 on lock-out at supplier Denso:
https://gurgaonworkersnews.wordpress.com/gurgaonworkersnews-no-924/#fn5
GurgaonWorkersNews no.26 conditions and struggle at supplier Sanden Vikas:
https://gurgaonworkersnews.wordpress.com/gurgaonworkersnews-no-926/#fn3
GurgaonWorkersNews no.30 on conditions of workers in the supply-chain:
https://gurgaonworkersnews.wordpress.com/gurgaonworkersnews-no-930/#fn2
GurgaonWorkersNews no.31 interview with CNC operator at supplier:
https://gurgaonworkersnews.wordpress.com/gurgaonworkersnews-no-931/#fn4
GurgaonWorkersNews no.32 on situation within the supply chain:
https://gurgaonworkersnews.wordpress.com/gurgaonworkersnews-no-932/#fn1
GurgaonWorkersNews no.33 on the supply-chain mix of welding robots and slum production:
https://gurgaonworkersnews.wordpress.com/gurgaonworkersnews-no-933/#fn1
GurgaonWorkersNews no.35 on the supply-chain of Maruti
https://gurgaonworkersnews.wordpress.com/gurgaonworkersnews-no-935/#fn1
GurgaonWorkersNews no.36 on the supply-chain of Maruti
https://gurgaonworkersnews.wordpress.com/gurgaonworkersnews-no-936/#fn1
GurgaonWorkersNews no.41 on the Maruti occupation in June 2011
https://gurgaonworkersnews.wordpress.com/gurgaonworkersnews-no-941/
GurgaonWorkersNews no.44 on Maruti struggles in 2011
https://gurgaonworkersnews.wordpress.com/gurgaonworkersnews-no-944/
GurgaonWorkersNews no.45 on Maruti struggle update
https://gurgaonworkersnews.wordpress.com/gurgaonworkersnews-no-945/#fn3
GurgaonWorkersNews no.48 on Maruti struggle update
https://gurgaonworkersnews.wordpress.com/gurgaonworkersnews-no-948/#fn1
GurgaonWorkersNews no.50 on lock-out at supplier Senior
https://gurgaonworkersnews.wordpress.com/gurgaonworkersnews-no-950/#fn2
————————–
Article by wildcat car worker on the ‘end of the automobile’:
http://www.wildcat-www.de/en/wildcat/83/w83_auto_en.htm
Article by Marco Revelli on historic strike against layoffs at FIAT Italy:
http://libcom.org/tags/marco-revelli
Article on ‘political assembly’ of workers at Alfa Romeo:
http://libcom.org/history/against-state-boss-autonomous-assembly-alfa-romeo
Article on Lordstown struggle US:
http://libcom.org/library/lordstown-struggle-ken-weller
Comments
Glossary of terms used in Gurgaon Workers News.
Updated version of the Glossary: things that you always wanted to know, but could never be bothered to google. Now even in alphabetical order.
AITUC
BPO
CITU
Casual Workers
Contract Workers
Crore
DA
DC
ESI
Exchange Rate
HSIIDC
ITI
Jhuggi
Lakh (see Crore)
Lay off
Minimum Wage
Panchayat
PF
Ration Card
SP
Staff
Trainees
VRS
Wages and Prices
Workers hired through contractors
AITUC
The All India Trade Union Congress (AITUC) is the oldest trade union federation in India and one of the five largest. It was founded in 1919 and until 1945, when unions became organised along party lines, it was the central trade union organisation in India. Since then it has been affiliated with the Communist Party of India.
BPO
Business Process Outsourcing: for example of call centre work, market research, sales.
CITU
Centre of Indian Trade Unions, a national central trade union federation in India. Politically attached to CPI(M), Communist Party of India (Marxist). Founded in 1970, membership of 2.8 million.
Casual Workers
Workers hired by the company for a limited period of time.
Contract Workers
Workers hired for a specific performance, paid for the performance.
Crore
1 Crore = 10,000,000
1 Lakh = 100,000
DA (Dearness Allowance):
An inflation compensation. Each three to six months the state government checks the general price development and accordingly pays an allowance on top of wages.
DC
Deputy Commissioner, Head of the District Administration.
ESI (Employee’s State Insurance):
Introduced in 1948, meant to secure employee in case of illness, long-term sickness, industrial accidents and to provide medical facilities (ESI Hospitals) to insured people. Officially the law is applicable to factories employing 10 or more people. Employers have to contribute 4.75 percent of the wage paid to the worker, the employee 1.75 percent of their wage. Officially casual workers or workers hired through contractors who work in the factory (even if it is for construction, maintenance or cleaning work on the premises) are entitled to ESI, as well. Self-employment is often used to undermine ESI payment.
Exchange Rate:
1 US-Dollar = 43 Rs (July 2008)
1 Euro = 68 Rs (July 2008)
HSIIDC
Haryana State Industrial and Infrastructure Development Corporation
ITI
Industrial training, e.g. as electrician or mechanic. Two years of (technical school), one year of apprentice-ship in a company. During the two years at school the young workers receive no money, but they have to pay school fees. A lot of the bigger companies ask for ITI qualification.
Jhuggi
Slum Hut
Lakh
see Crore
Lay off
Lay off in the Indian context means that workers have to mark attendance, but they actually do not work and receive only half of the wage.
Minimum Wage:
Official minimum wage in Haryana in June 2007 is 3,510 Rs per month for an unskilled worker, based on an 8-hour day and 4 days off per month. But hardly any workers get this wage.
Panchayat
A locally elected village administrative body in charge of village-level issues.
PF (Employee’s Provident Fund):
Introduced in 1952, meant to provide a pension to workers. Officially applicable to all companies employing more than 20 people. Official retirement age is 58 years. Given that most of the casual workers belong to the regular workforce of a factory, they are entitled to the Provident Fund, as well. So are workers employed by contractors. If workers receive neither PF nor ESI they also do not show up in the official documents, meaning that officially they do not exist.
Ration Card
Officially the so called ‘governmental fair price shops’ are shops were ‘officially poor’ people can buy basic items (wheat, rice, kerosene etc.) for fixed and allegedly lower prices. In order to be able to buy in the shops you need a ration card. The ration card is also necessary as a proof of residency, but in order to obtain the ration card you have to proof your residency. Catch 22. Local politics use the ration depots and cards as a power tool that reaches far into the working class communities. Depot holders’ jobs are normally in the hands of local political leaders. In return they receive this privileged position, which often enable them to make money on the side.
SP
Superintendent of Police, Head of the District Police.
Staff
In India staff includes managers, supervisors, security personnel and white-collar workers.
Trainees
In general trainees work as normal production workers, they might have a six-month up to two-year contract. Depending on the company they are promised permanent employment after passing the trainee period. Their wages are often only slightly higher than those of workers hired through contractors.
VRS (Voluntary Retirement Scheme):
Often a rather involuntary scheme to get rid of permanent workers. Particularly the VRS at Maruti in Gurgaon made this clear, when 35 year olds were sent in early retirement.
Wages and Prices:
When we hear that a cleaner in a call centre in Gurgaon, an industrial worker in Faridabad or a rikshaw-driver in Delhi earns 2,000 Rs for a 70 hour week, which is about the average normal worker’s wage, we have to bear in mind that they often came from West Bengal, Bihar or other remote place in order to get this job. In order to put 2,000 Rs into a daily context here are some prices of goods and services – based on Summer 2006 prices:
Housing:
- Monthly rent for a plastic-tarpaulin hut shared by two people in Gurgaon: 800 Rs
- Monthly rent for a small room in Gurgaon (without kitchen), toilet and bathroom shared by five families: 1,300 Rs
- Monthly rent for a small room in a new building in central Gurgaon, single toilet and bathroom: 4,500 Rs to 8,000 Rs
Food:
- Half a kilo red lentils on the local market: 25 Rs
- Kilo rice on local market: 14 Rs
- 1 Kilo Onions and 1 Kilo carrots on local market: 25 to 30 Rs
- McChicken: 40 Rs
- Bottle (0,7l) of beer at Haryana Wine and Beer shop: 50 to 70 Rs
- Cigarettes (10), cheapest local brand: 25 Rs
- Starbucks Coffee (Latte Medium) in Shopping Mall: 59 Rs
Utensils:
- Faulty shirt on Faridabad local market: 40 Rs
- Single gas cooker plus new 2 litre gas cylinder: 720 Rs
- Re-fill gas (2 litres – once every month and a half): 100Rs
- Second-hand bicycle: 600 to 1,000 Rs
- Two simple steel pots: 250 Rs
Transport and Communication:
- Bus ticket to nearest bigger bus stop in South Delhi: 14 Rs
- Daily Newspaper: 3 Rs
- One hour internet in a cafe: 20 Rs
- Cinema (new) ticket Saturday night: 160 Rs
- Single entry for swimming pool: 100 Rs
- One litre Diesel: 30 Rs
- Driving license in Haryana: 2,000 to 2,500 Rs
- Start package pre-paid mobile phone (without the phone) 300 Rs
- Phone call to other mobile phones: 1 Rs
- One month mobile phone flat rate: 1,500 Rs
Luxuries:
- Minimum dowry poor workers have to pay for the marriage of their daughter: about 30,000 Rs (80,000 Rs more likely)
- Money given to poor labourers for their kidney: about 40,000 Rs
- Compaq Laptop: 50,000 Rs
- Flight Delhi to London: 28,000 Rs
- Cheapest Hero Honda motorbike (150 cc): around 40,000 Rs
- Ford Fiesta: 587,000 Rs
- Four hours on Gurgaon golf course: 800 Rs (info from golf course worker earning 2,400 Rs monthly)
- Two-Bedroom Apartment in Gurgaon: 10,000,000 to 50,000,000 Rs
Workers hired through contractors
Similar to temporary workers, meaning that they work (often for long periods) in one company but are officially employed by a contractor from whom they also receive their wages. Are supposed to be made permanent after 240 days of continuous employment in the company, according to the law. A lot of companies only have a licence for employing workers in auxiliary departments, such as canteen or cleaning. Companies usually find ways to get around these legal restrictions, e.g., workers services are terminated on the 239th day to avoid workers reaching eligibility criteria to become permanent. In many industries contract workers account for 60 to 80 per cent of the work force, their wage is 1/4 to 1/6 of the permanents’ wage.
Comments